
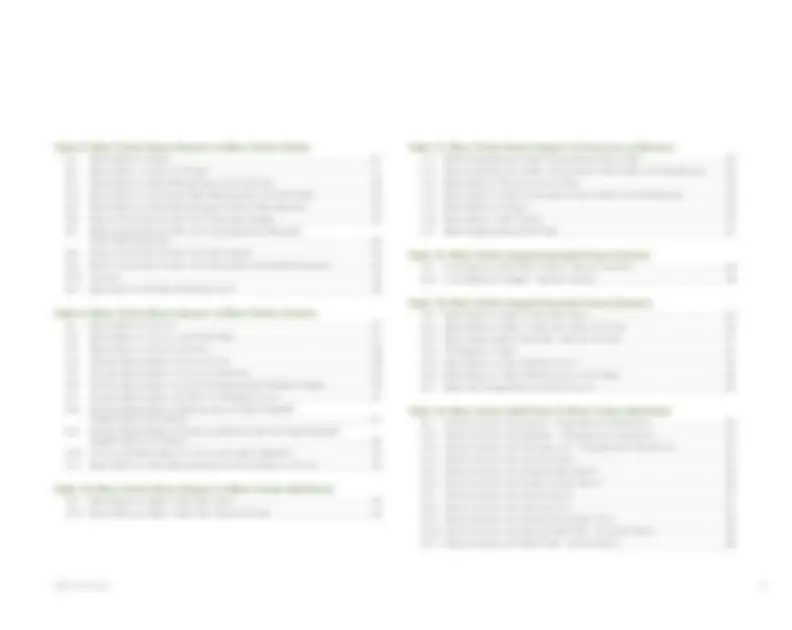
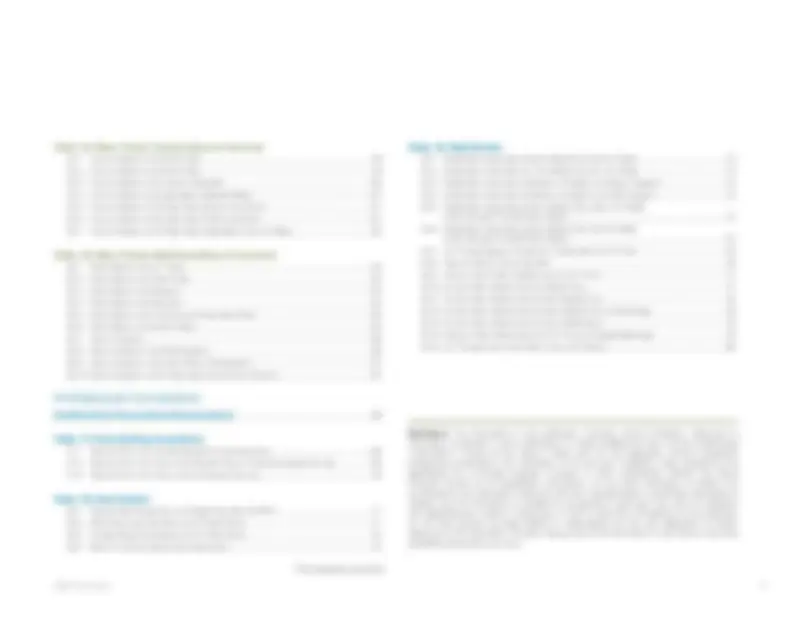
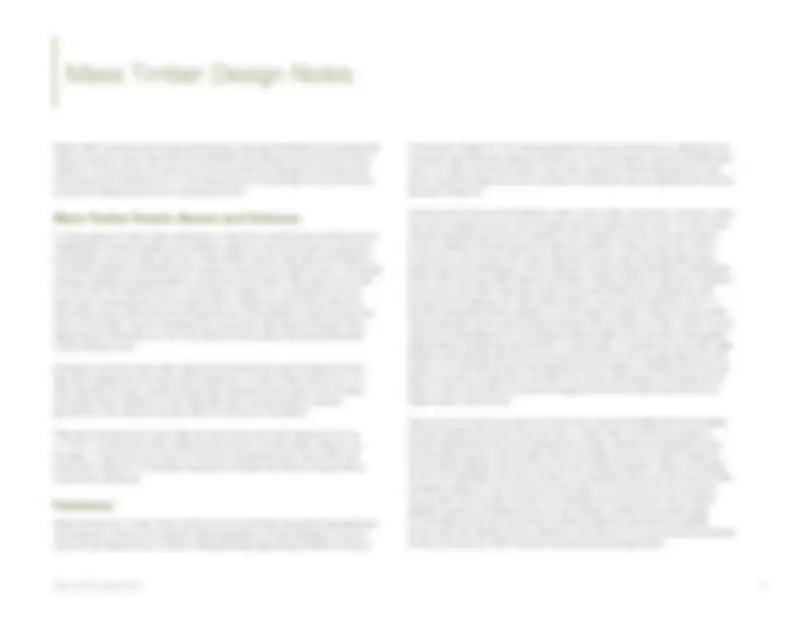
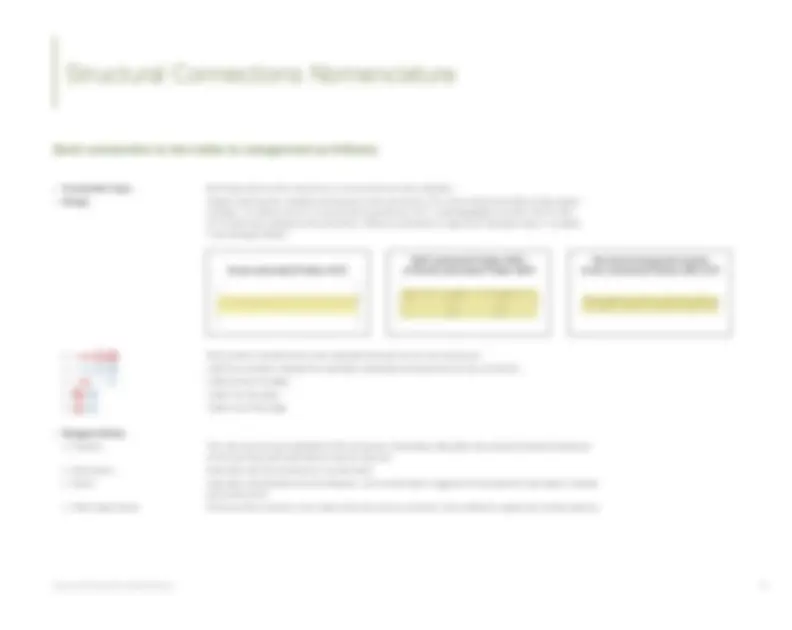
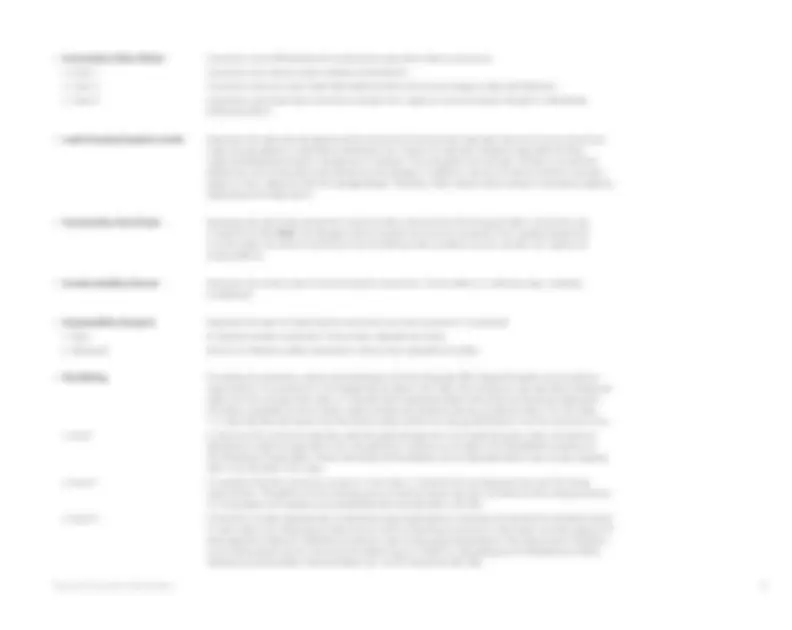
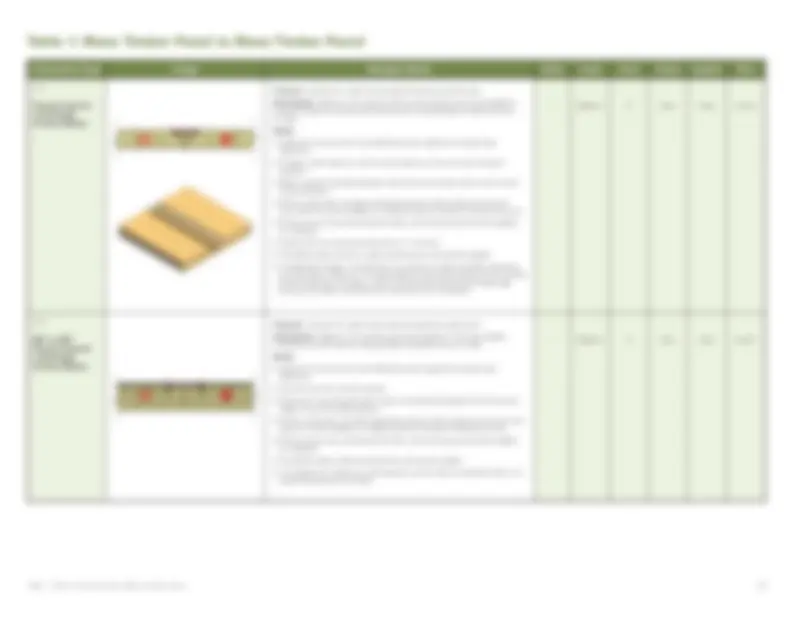
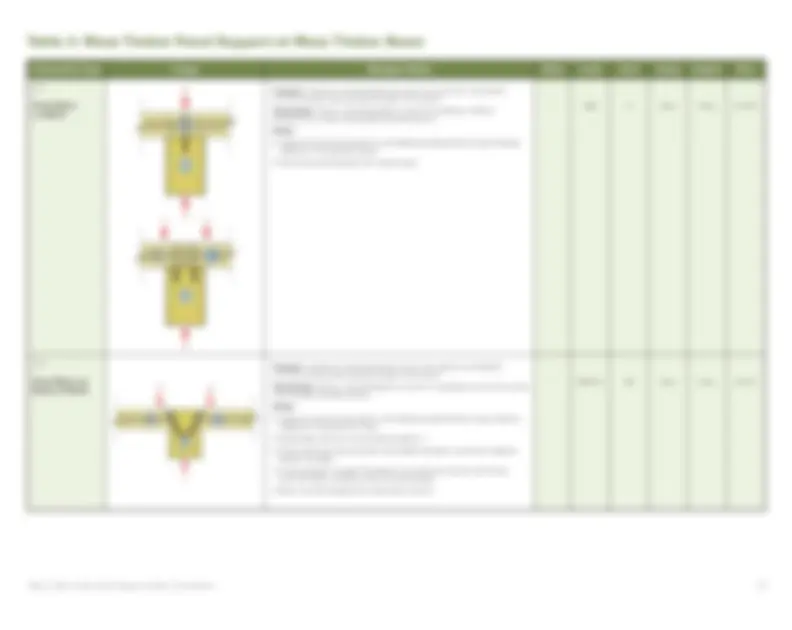
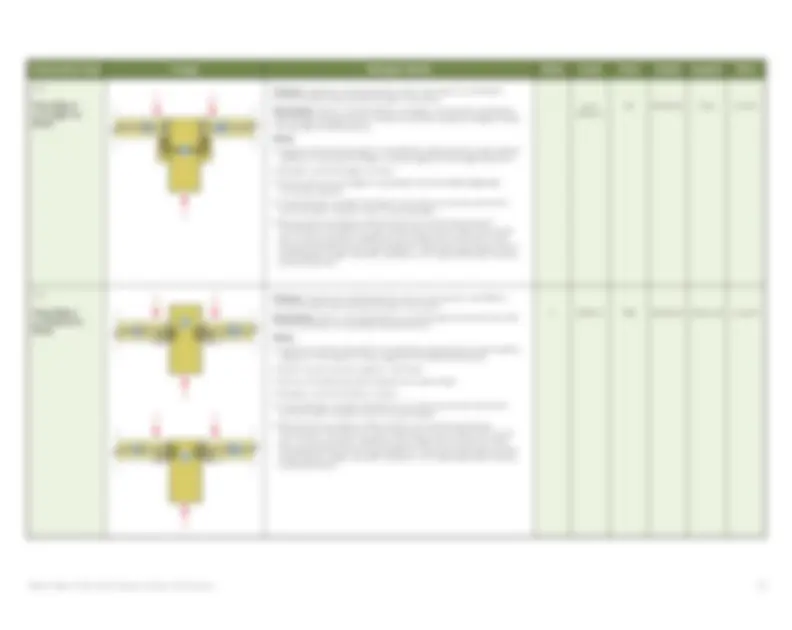
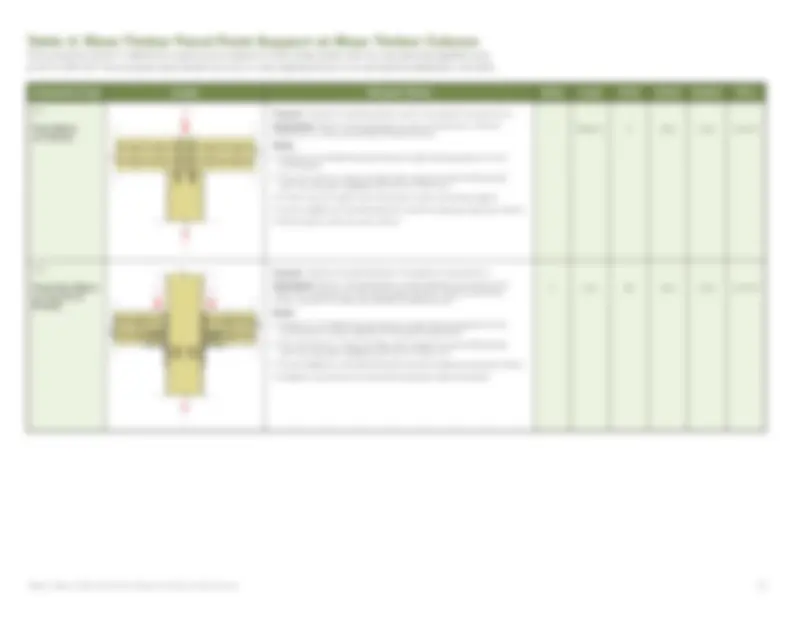
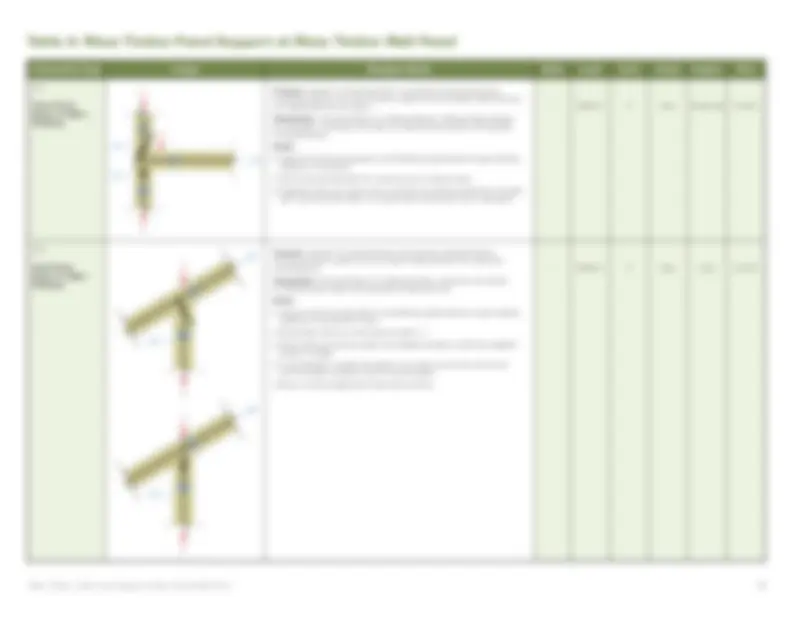
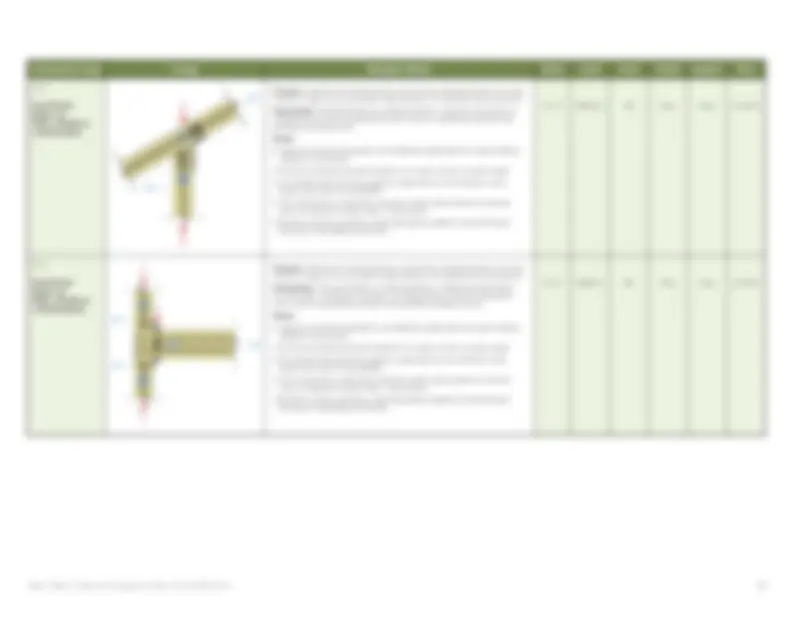
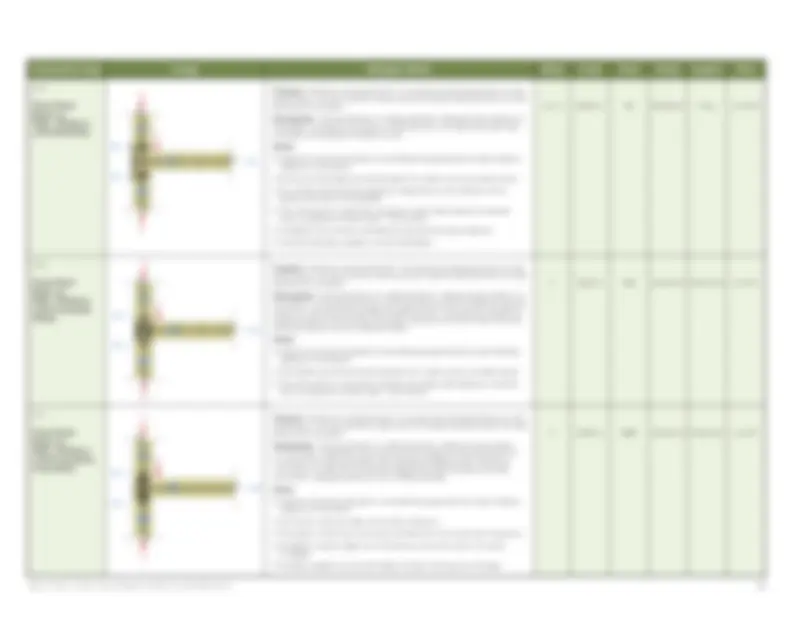
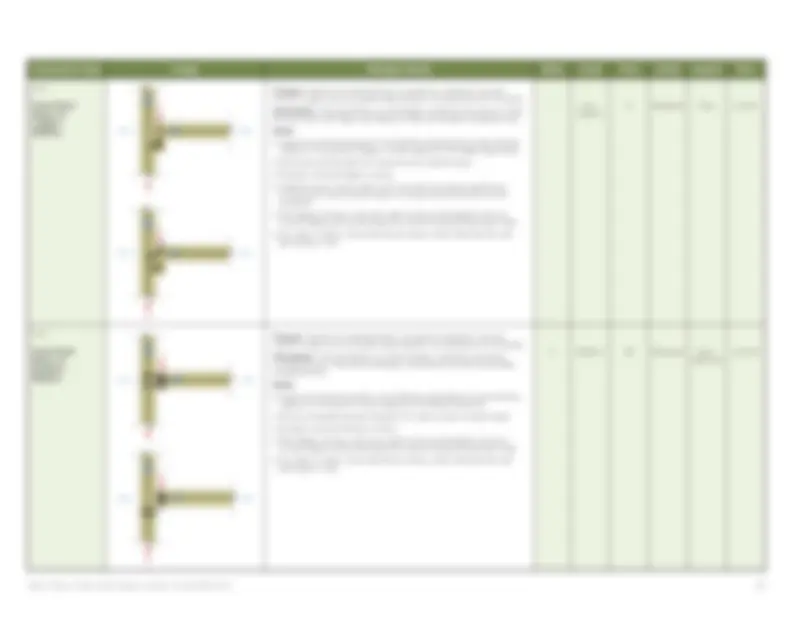
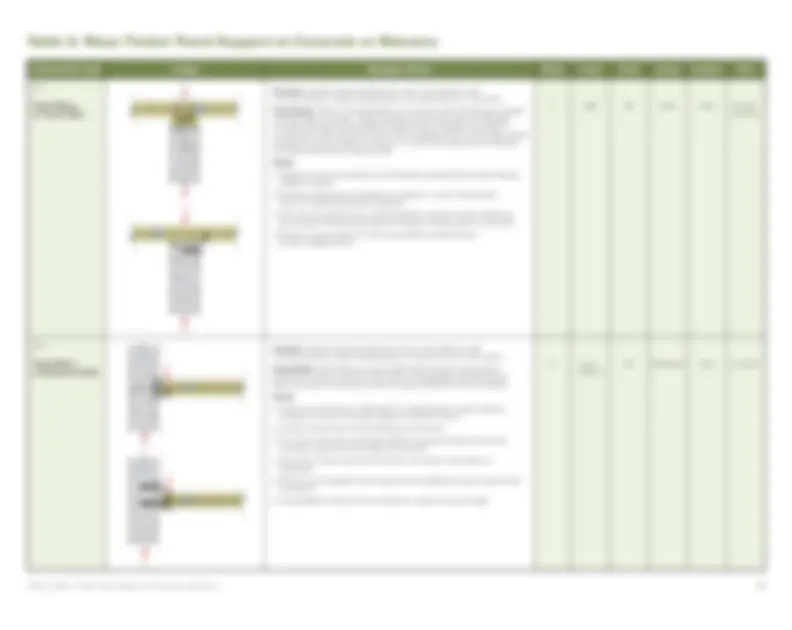
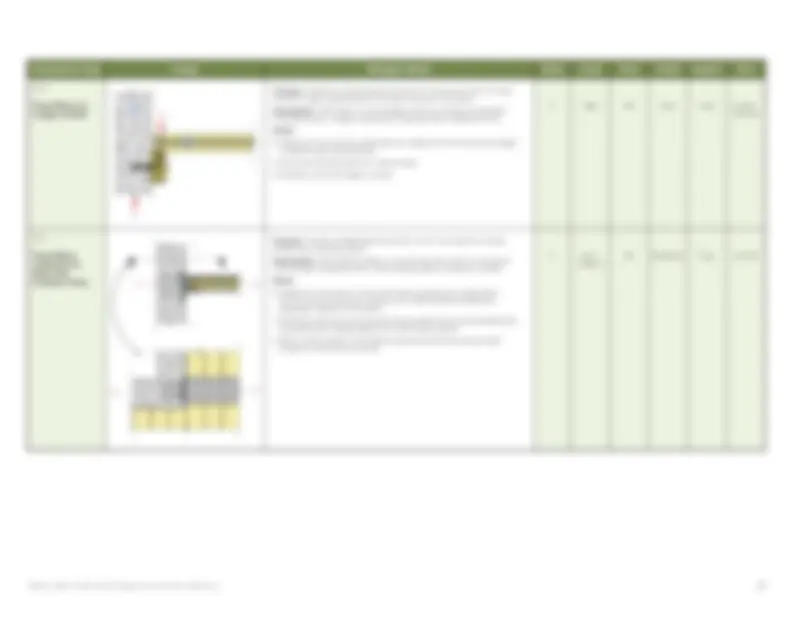
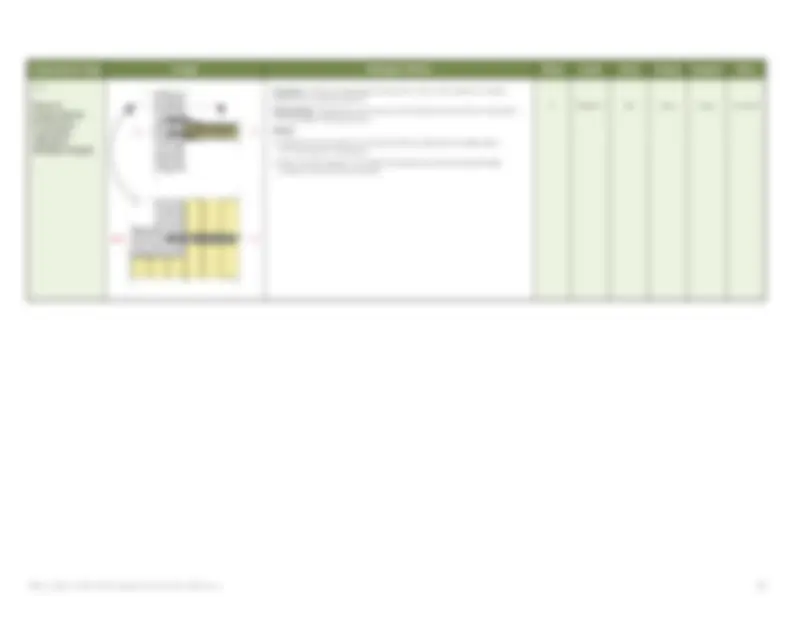
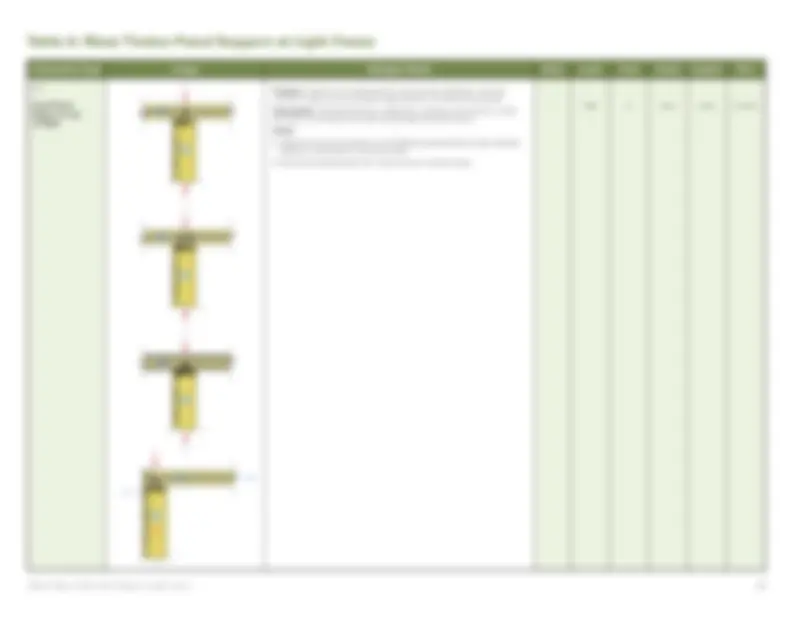
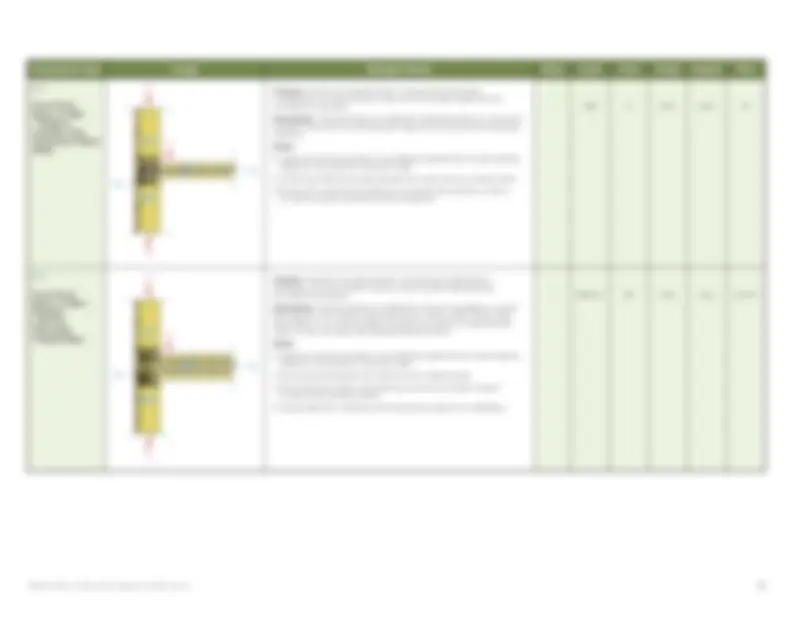
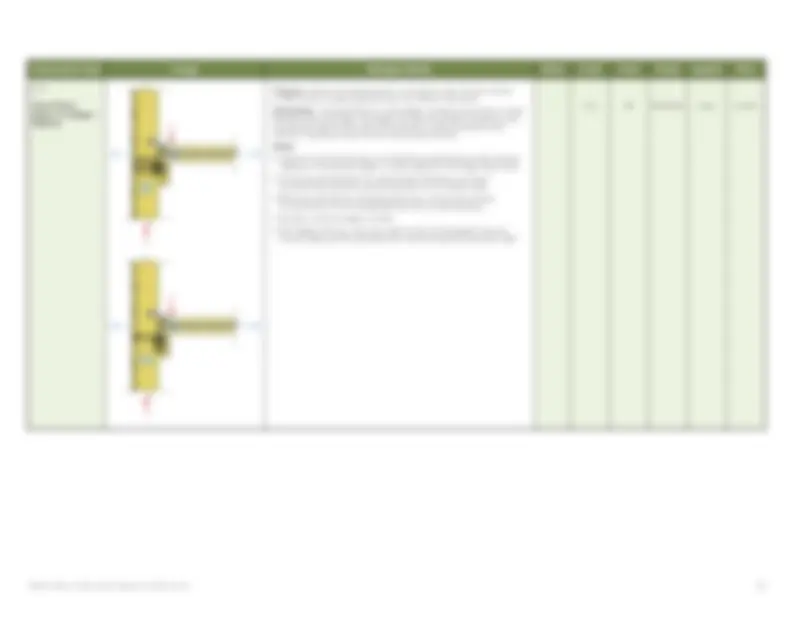
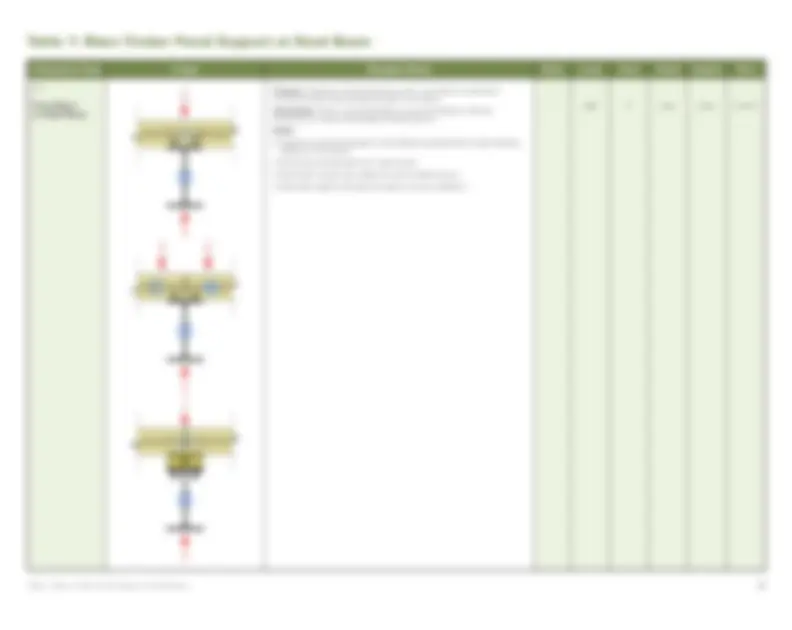
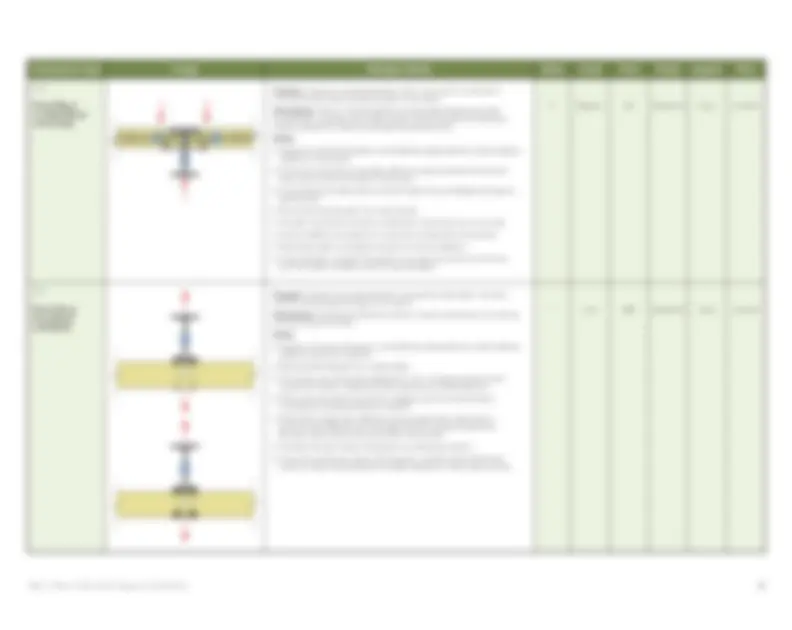
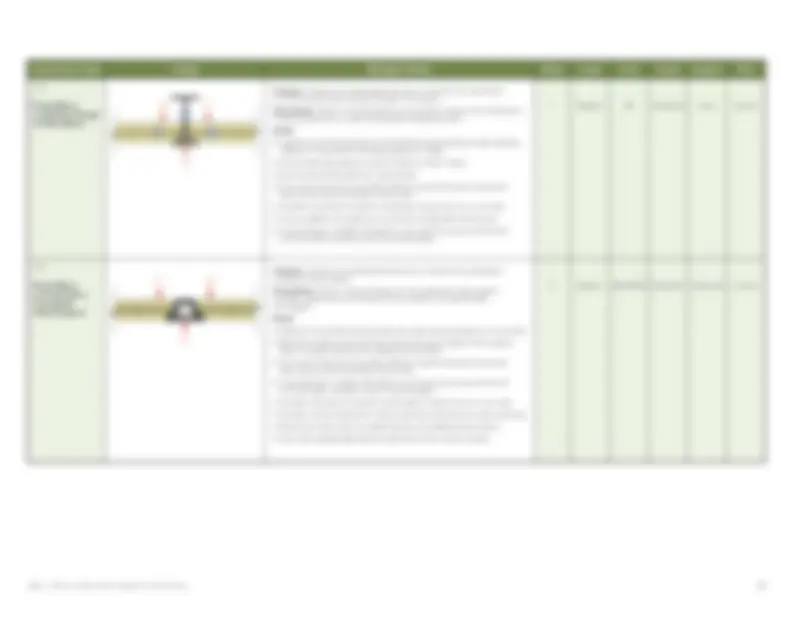
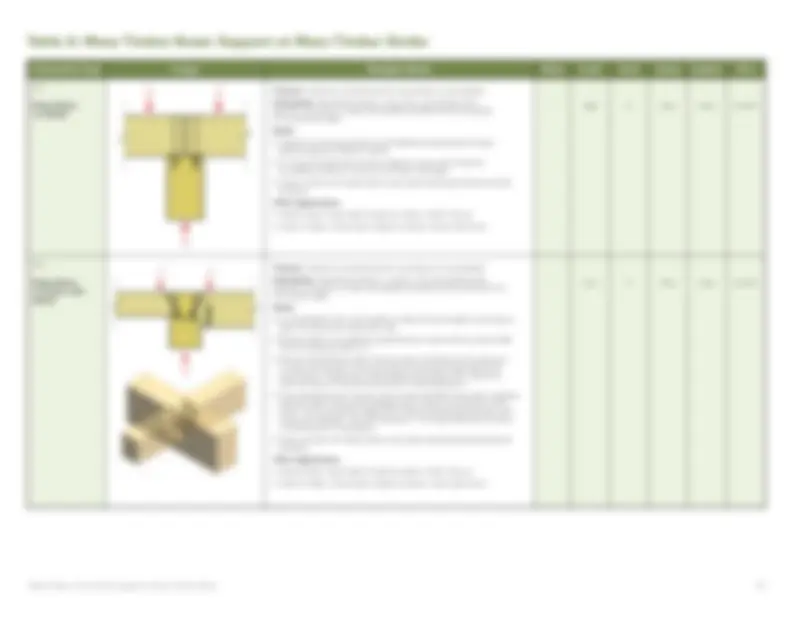
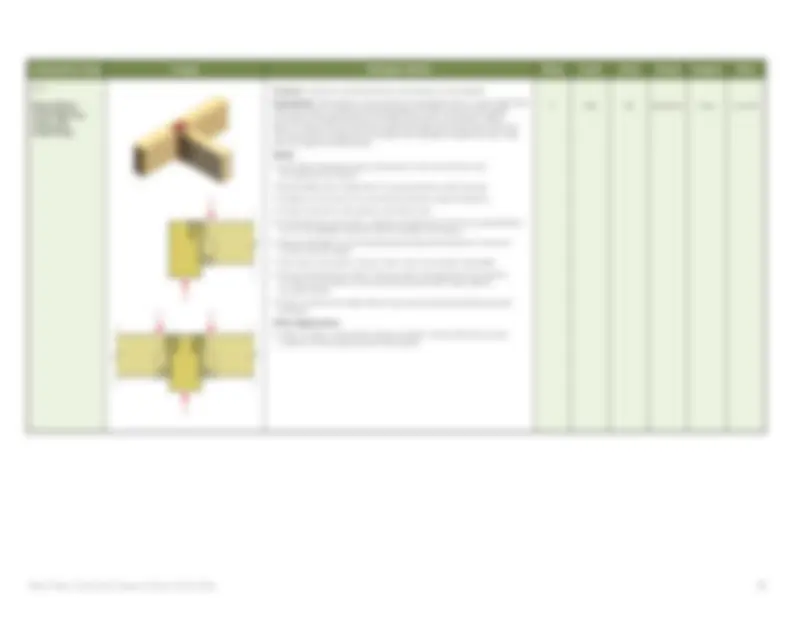
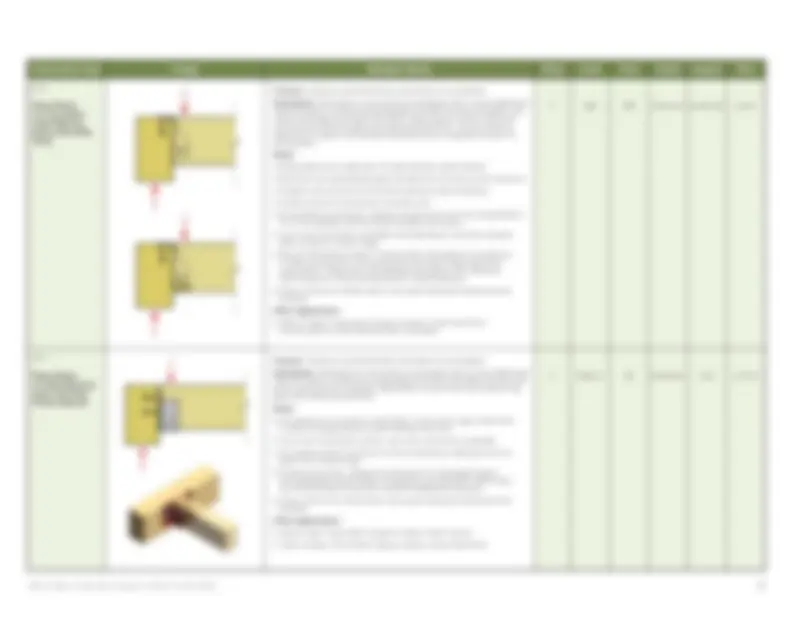
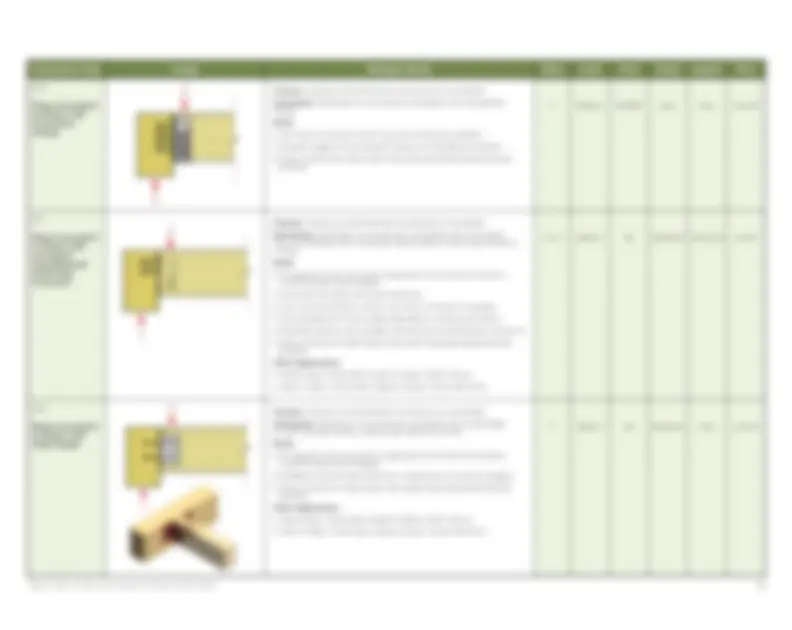
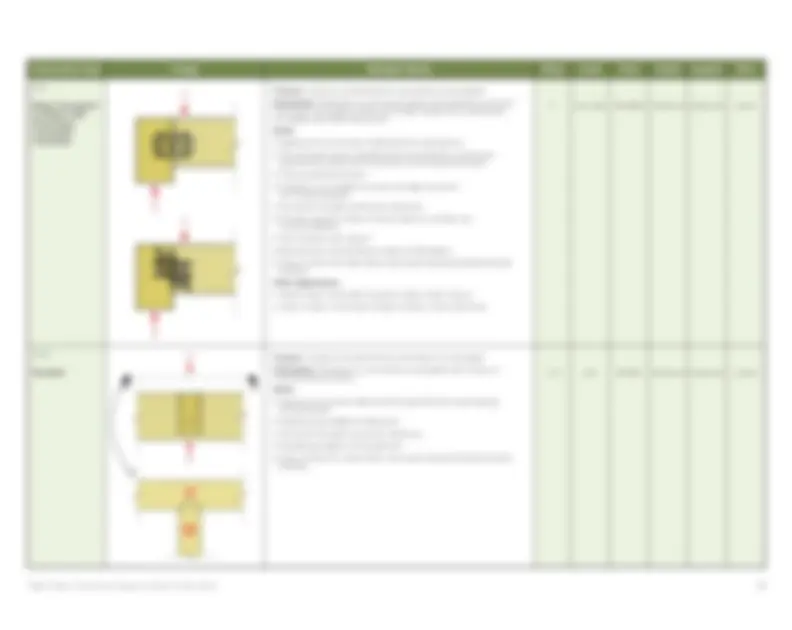
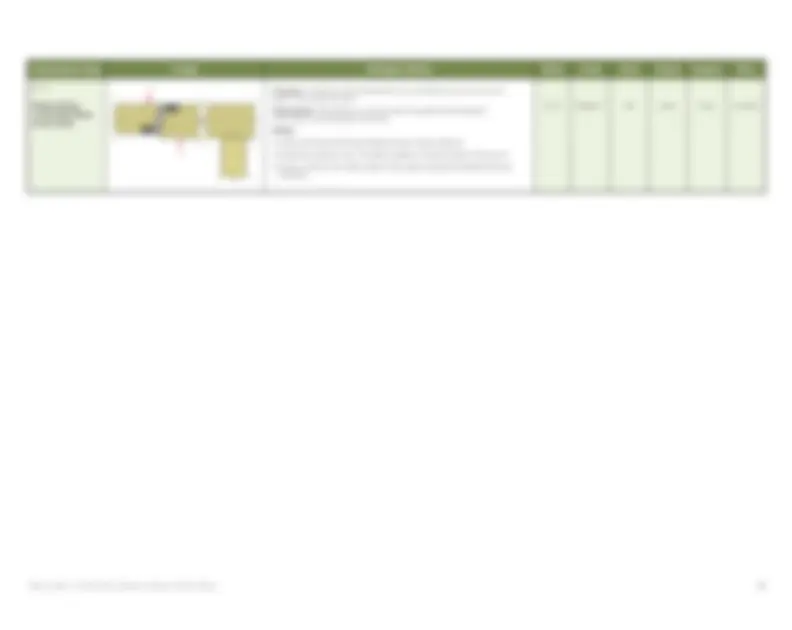
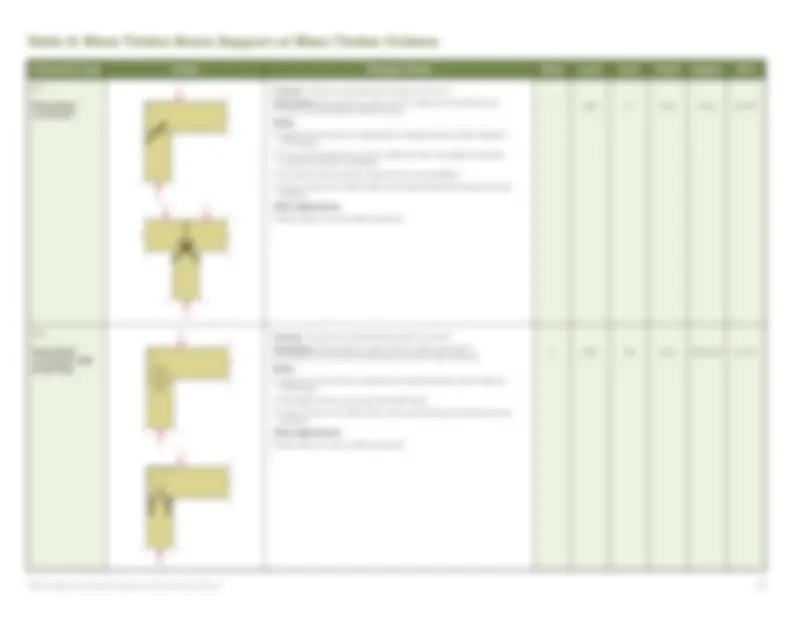
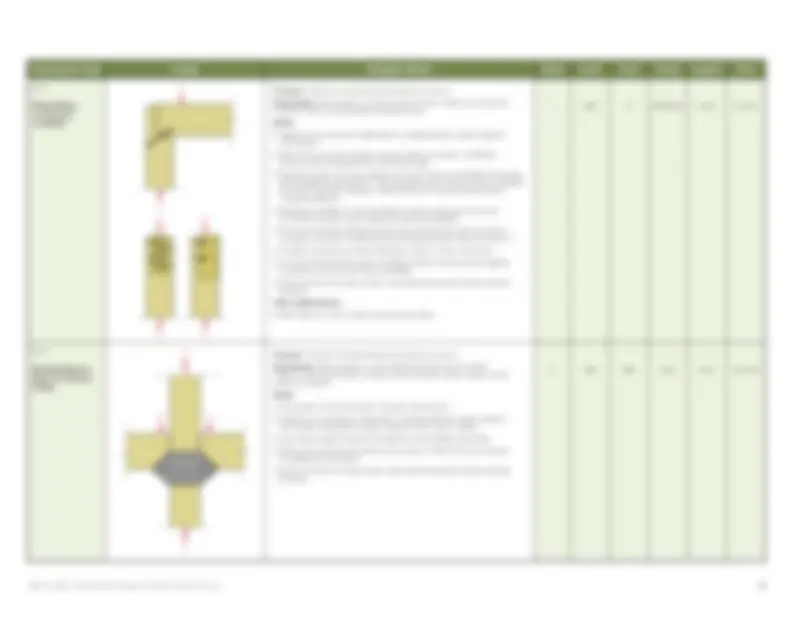
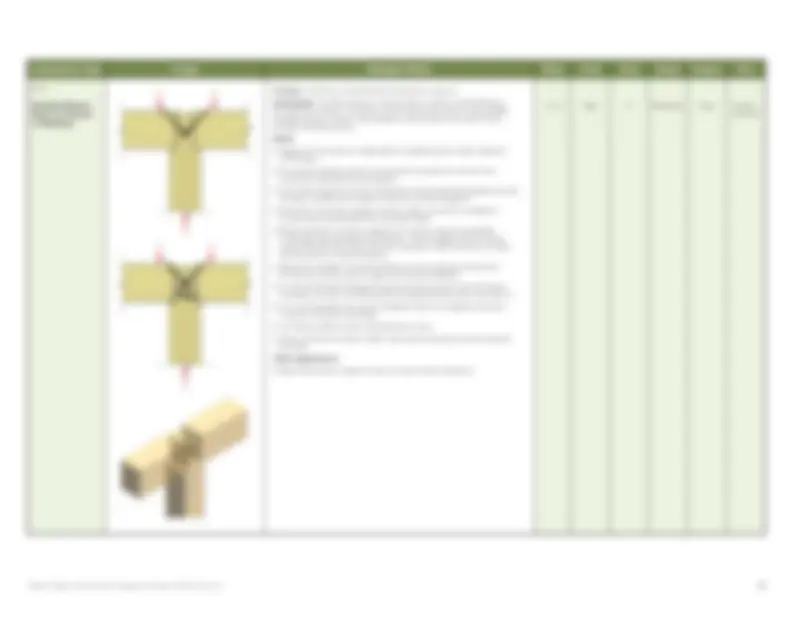
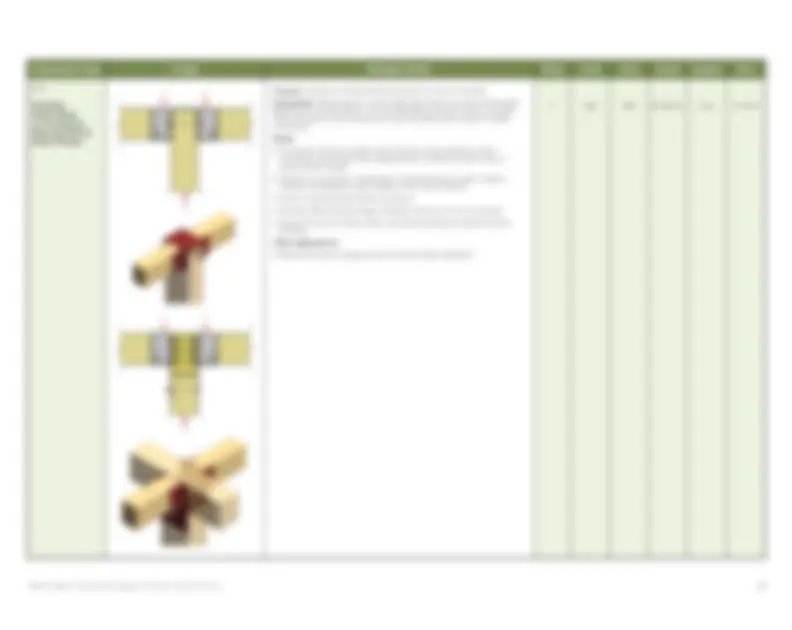
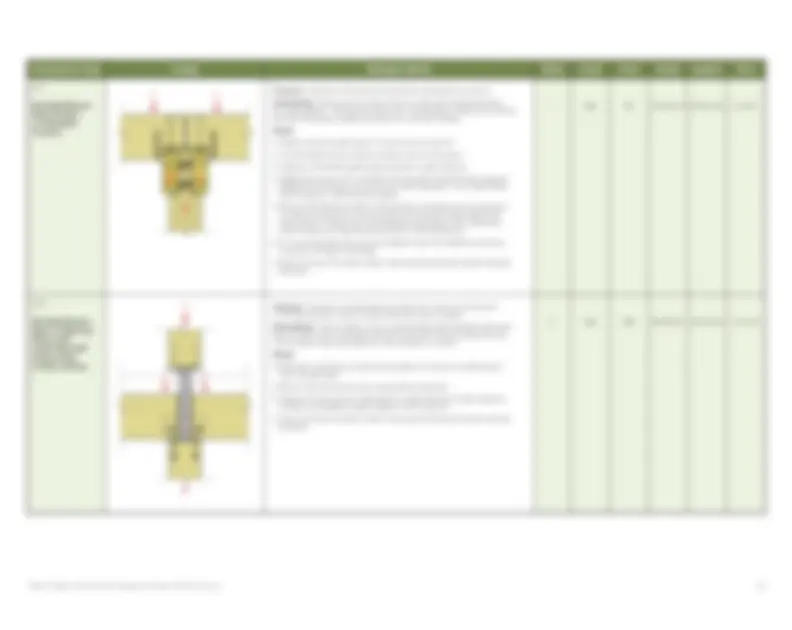
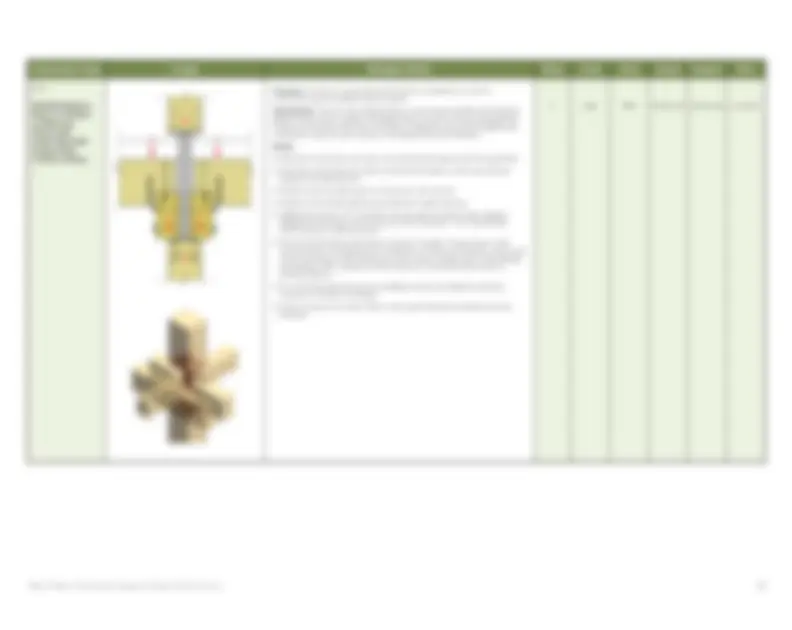
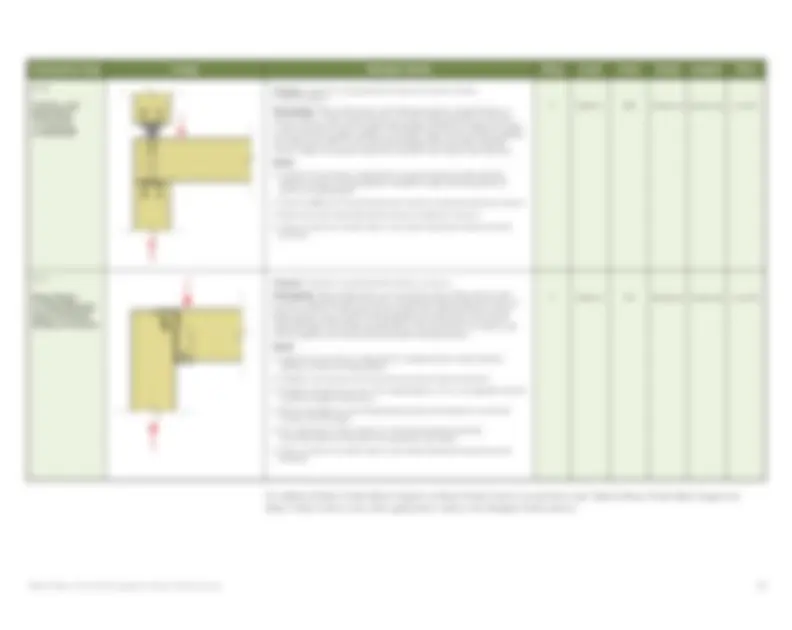
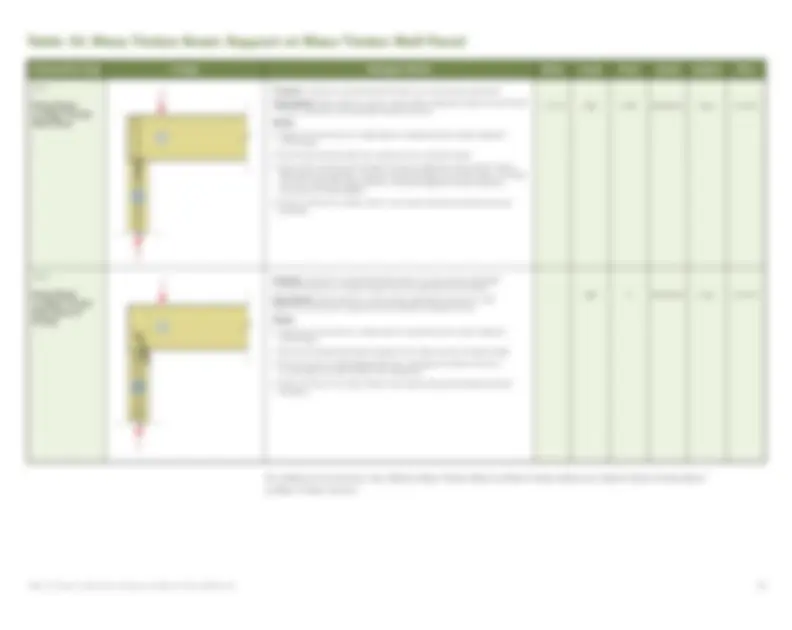
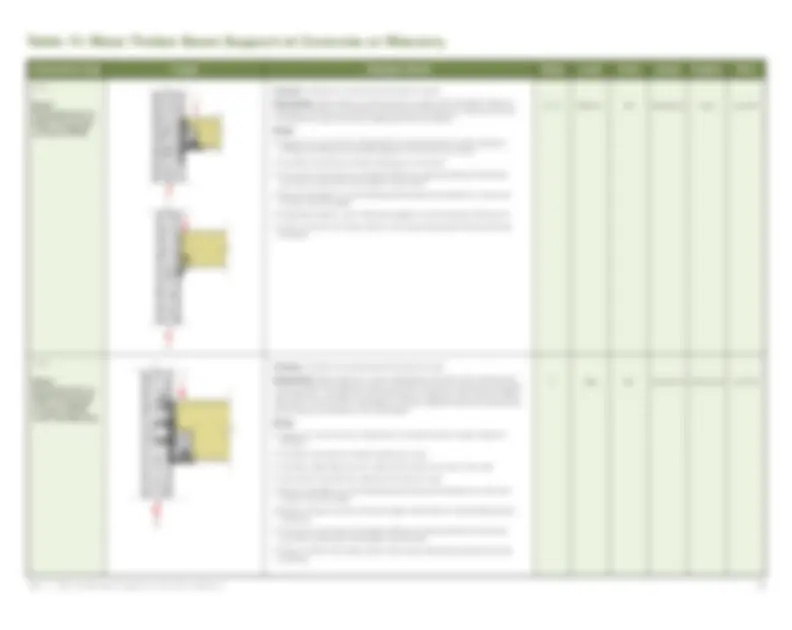
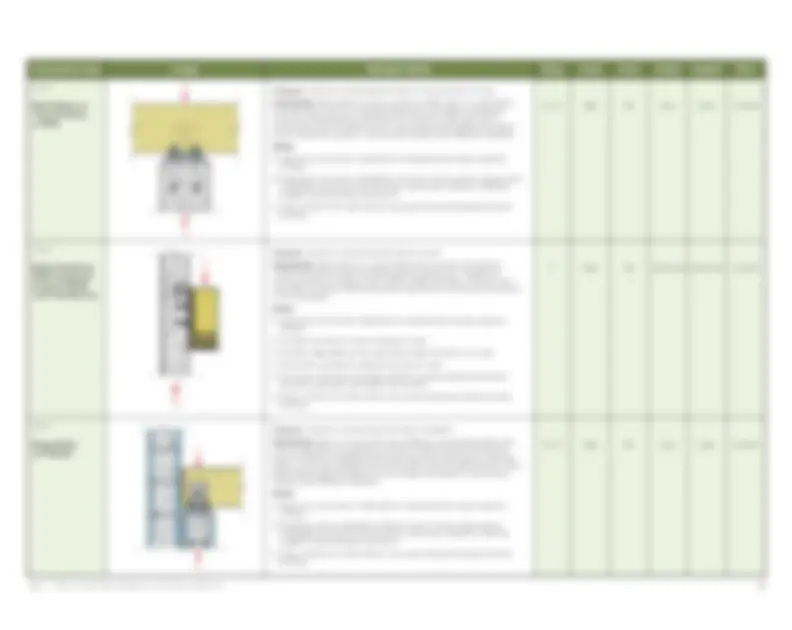
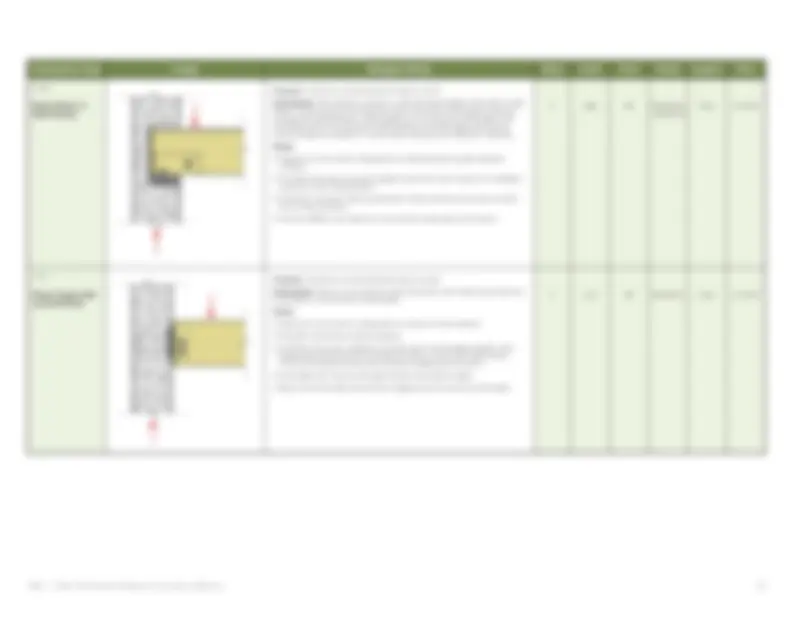
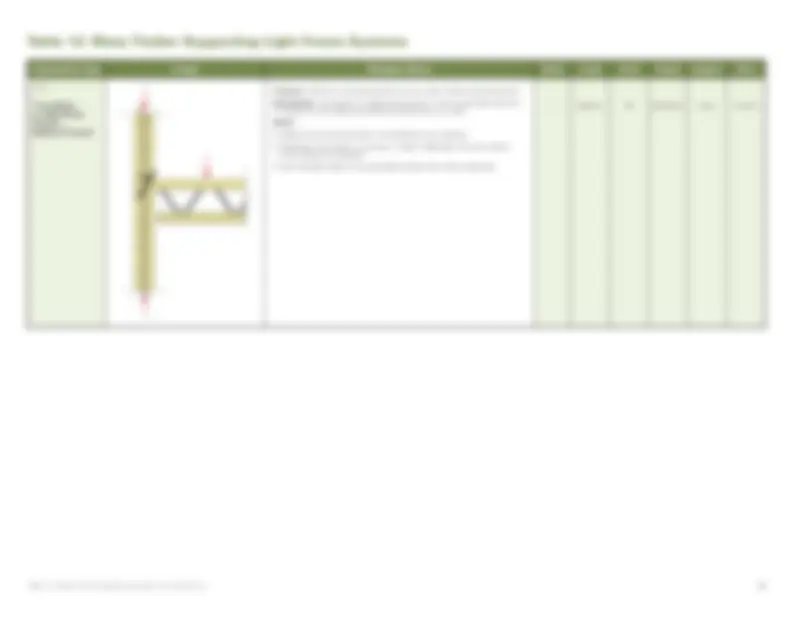
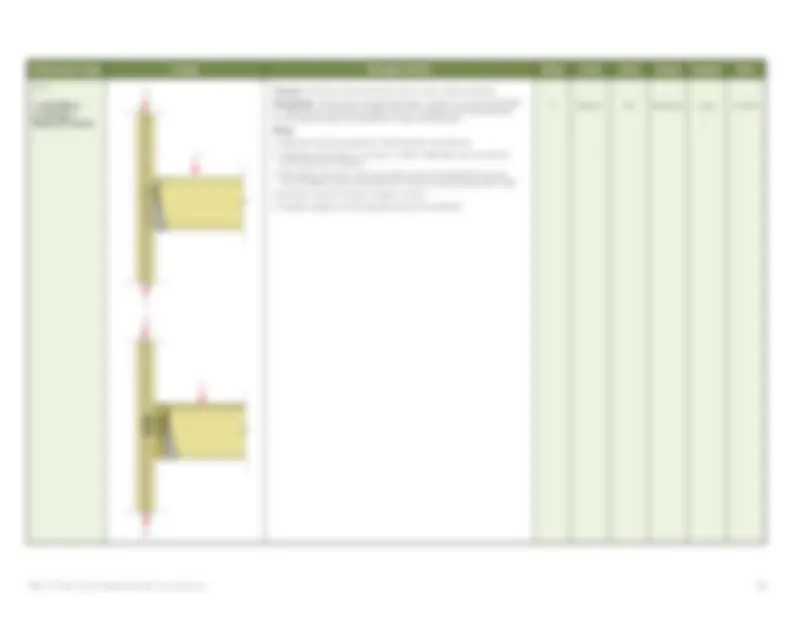
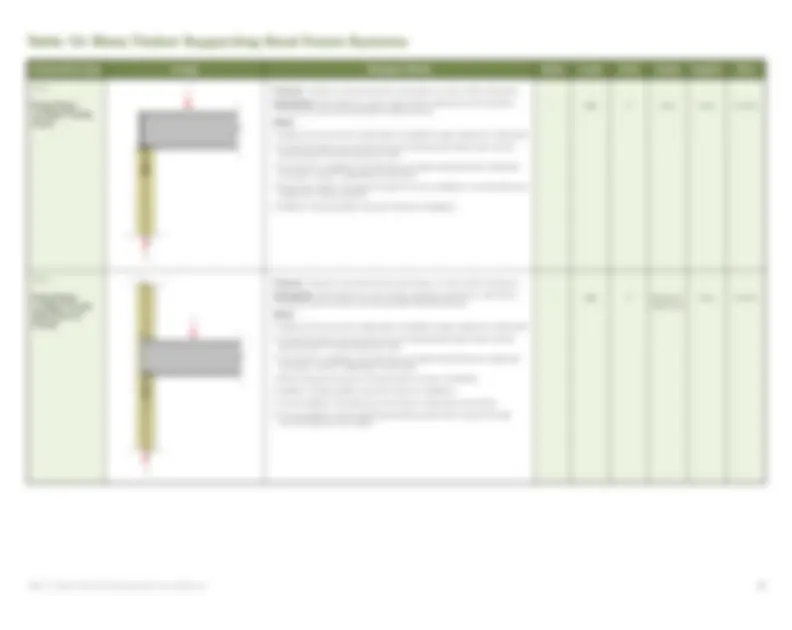
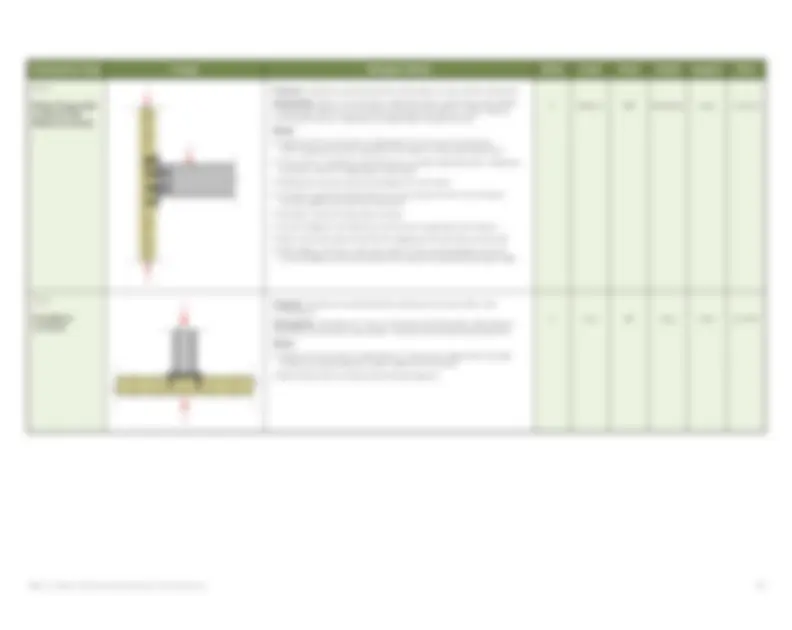
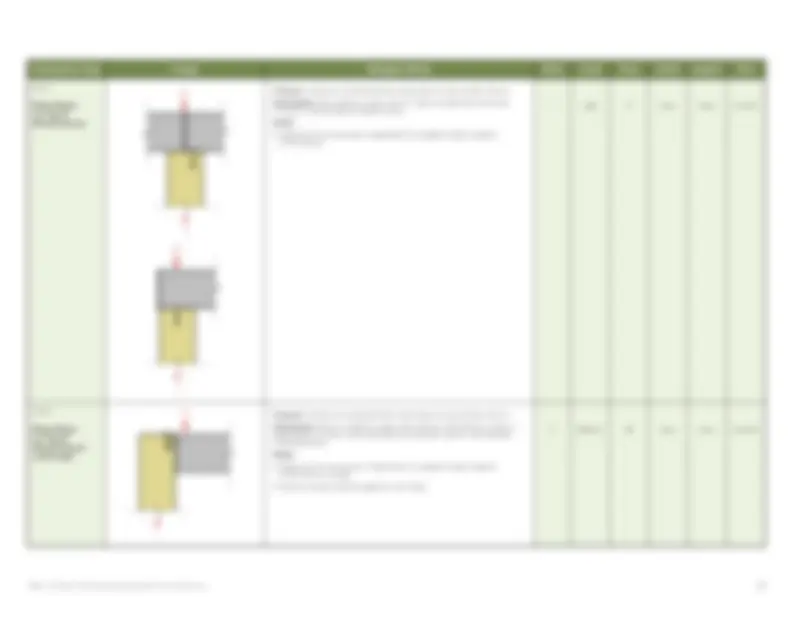
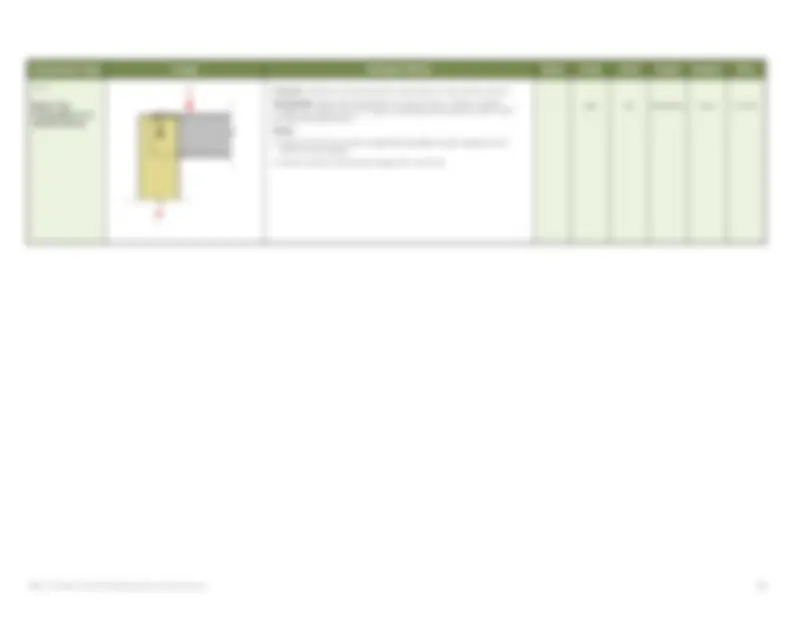
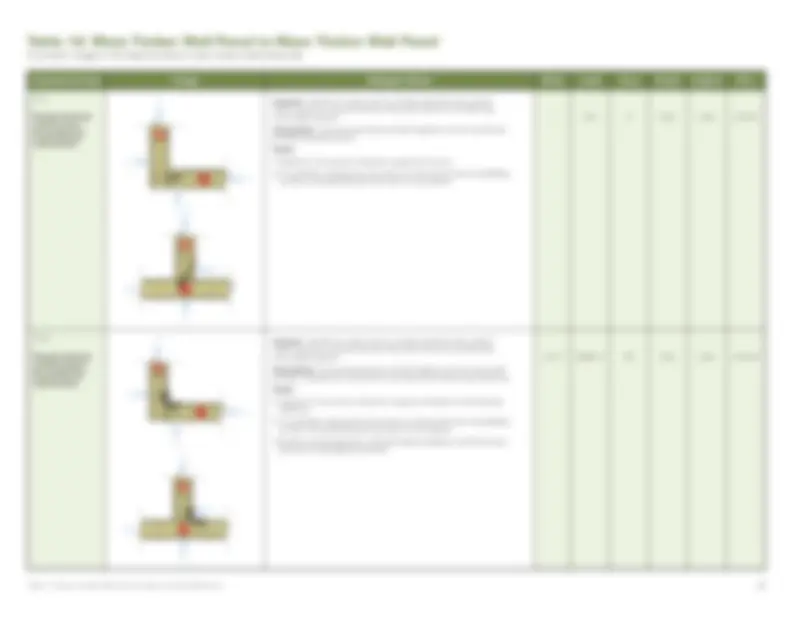
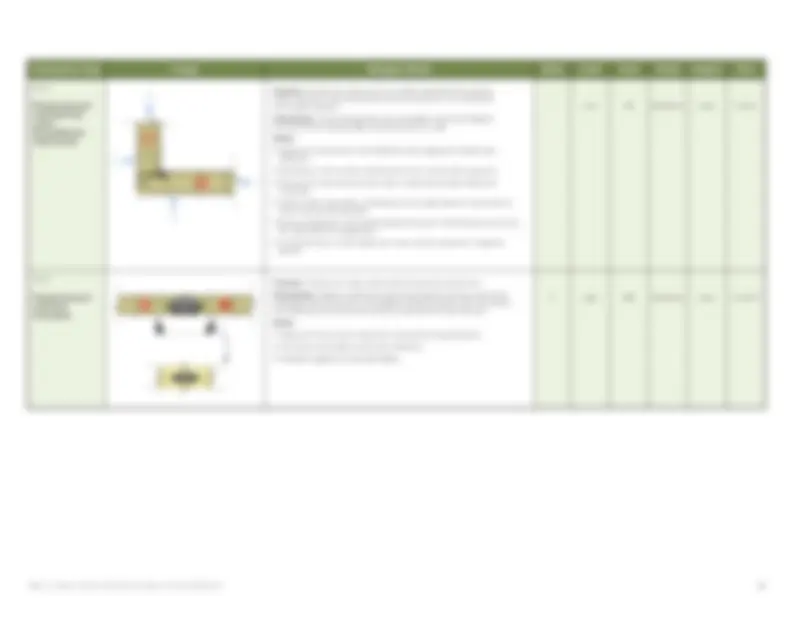
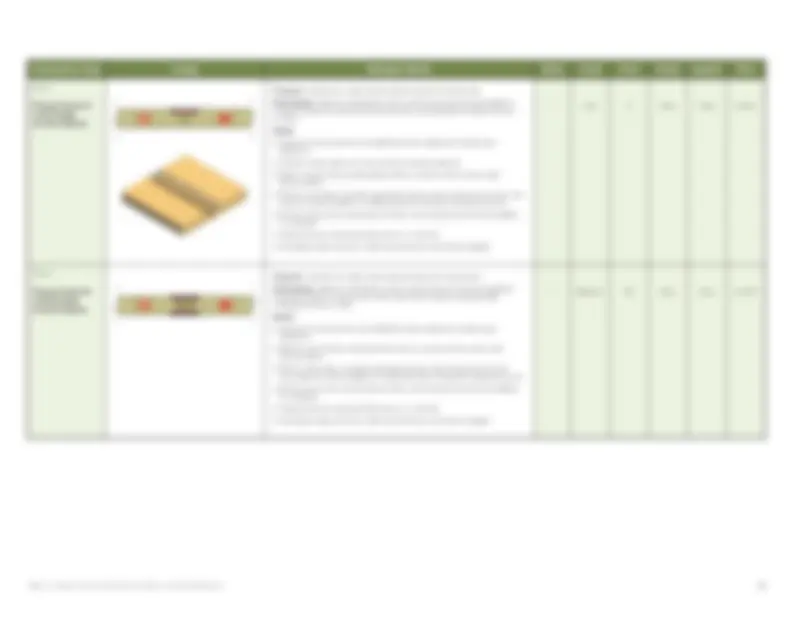
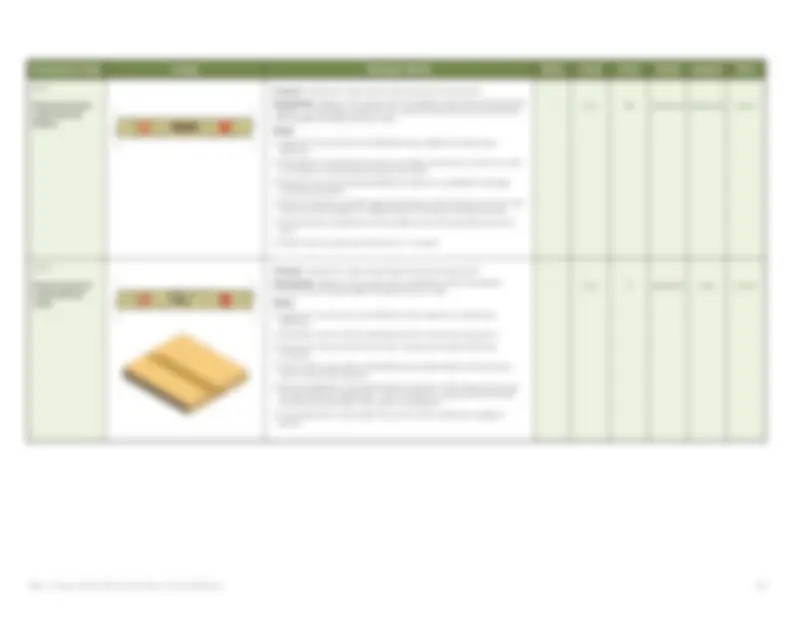
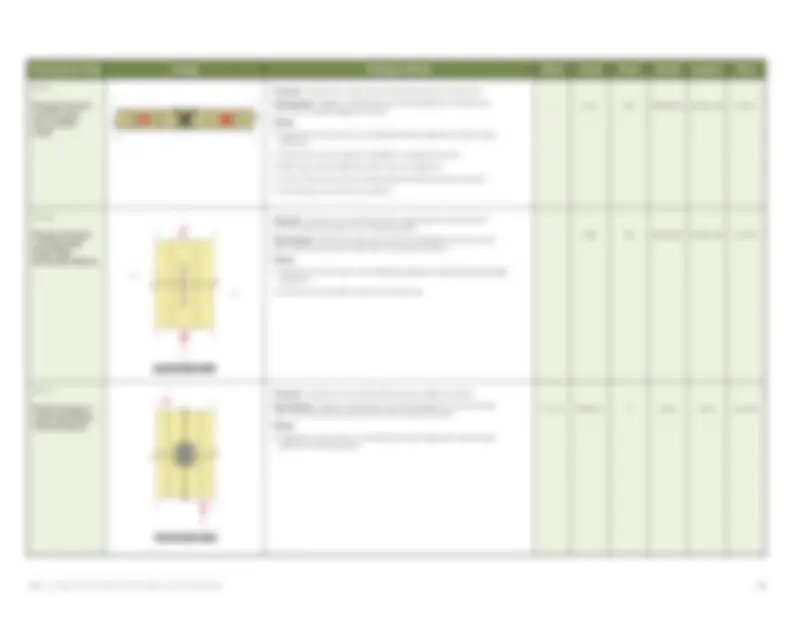
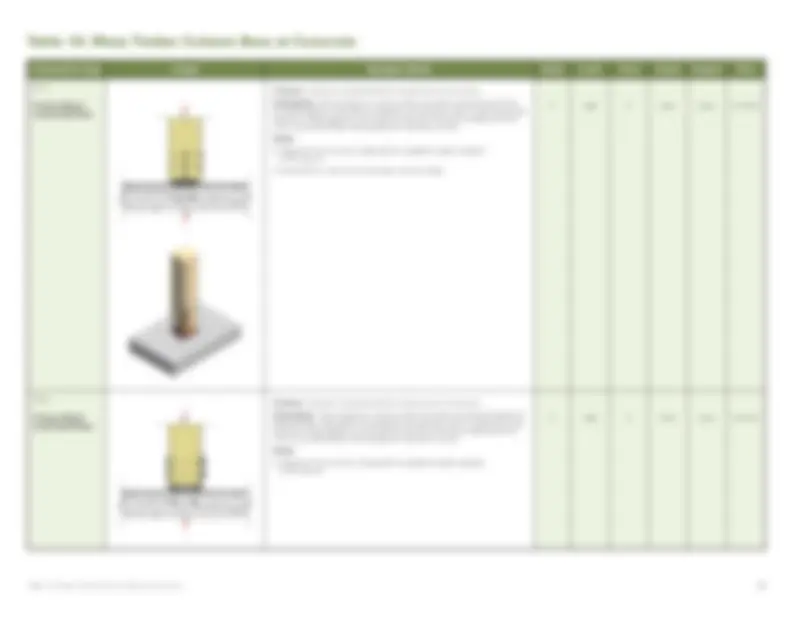
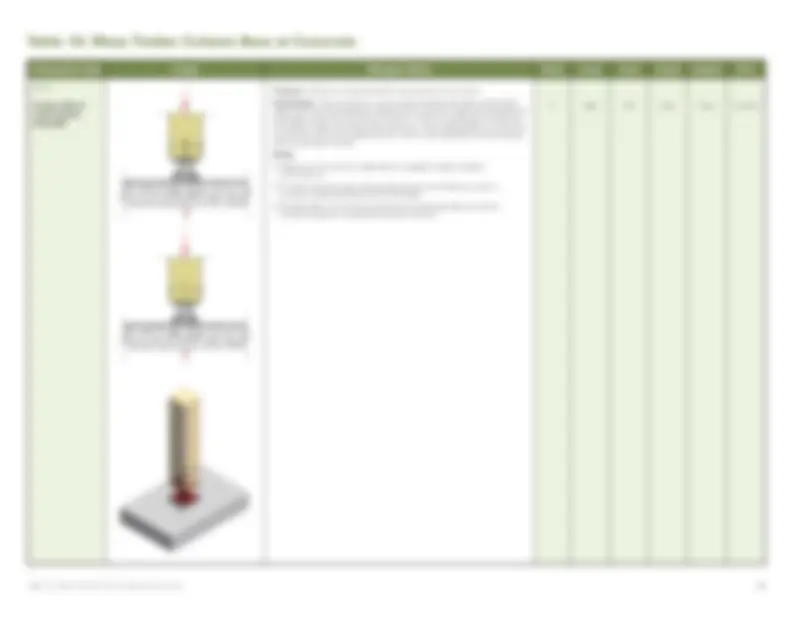
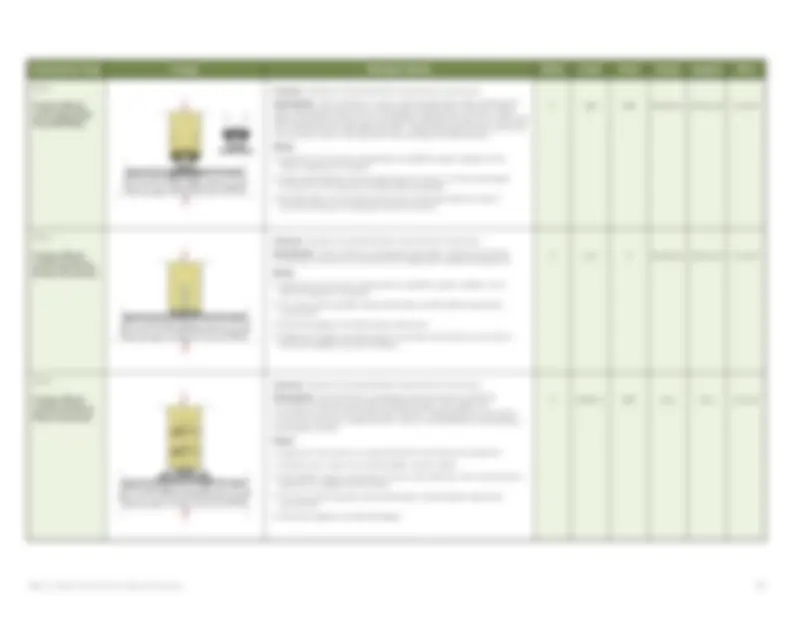
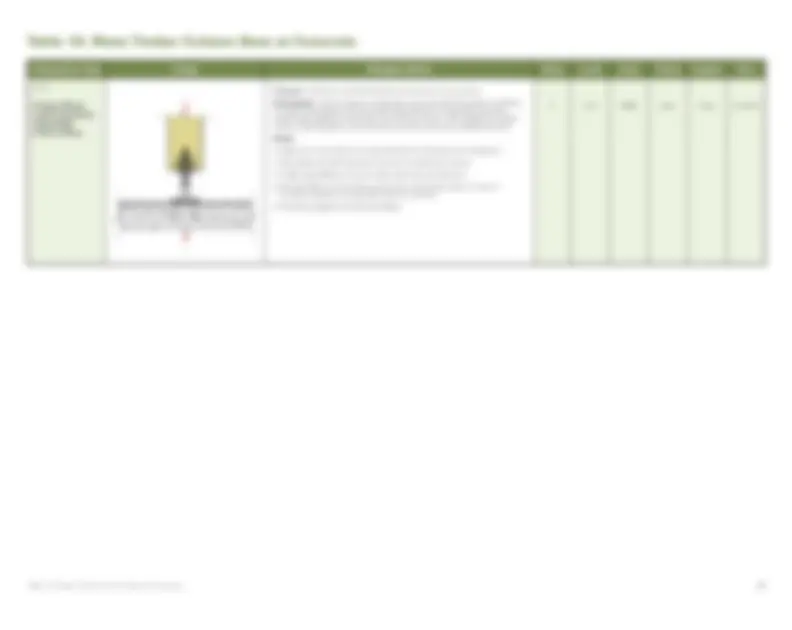
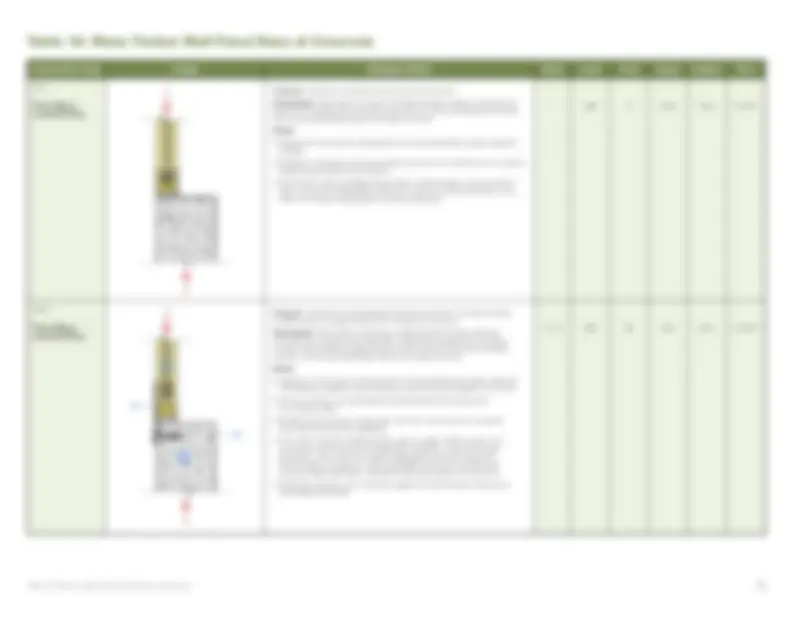
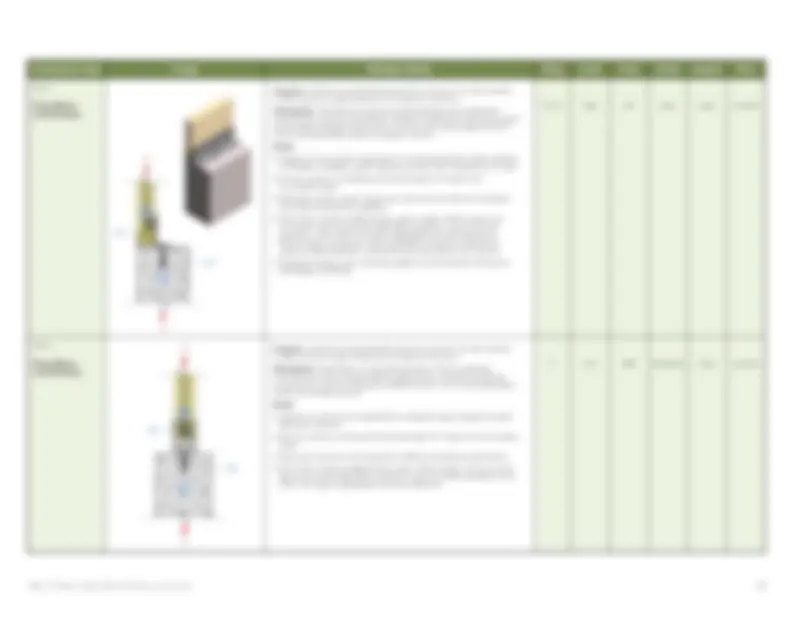
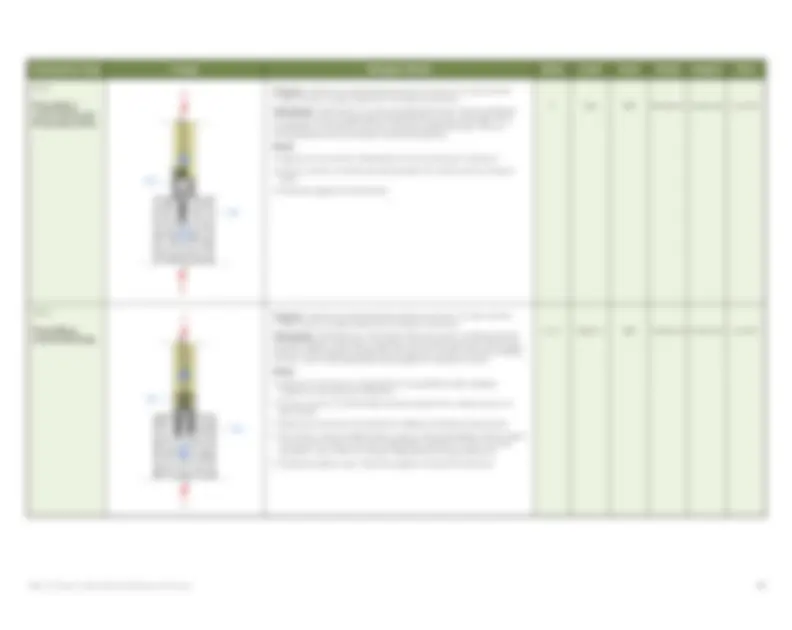
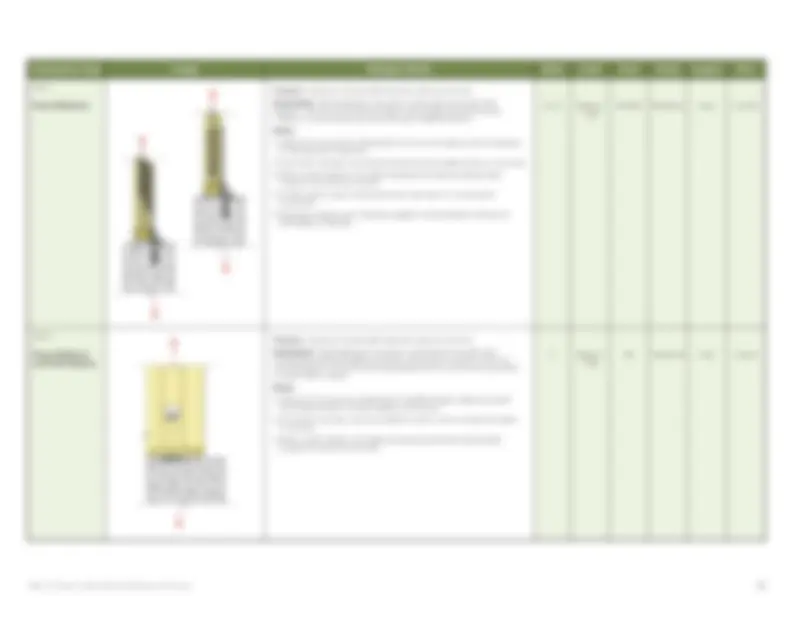
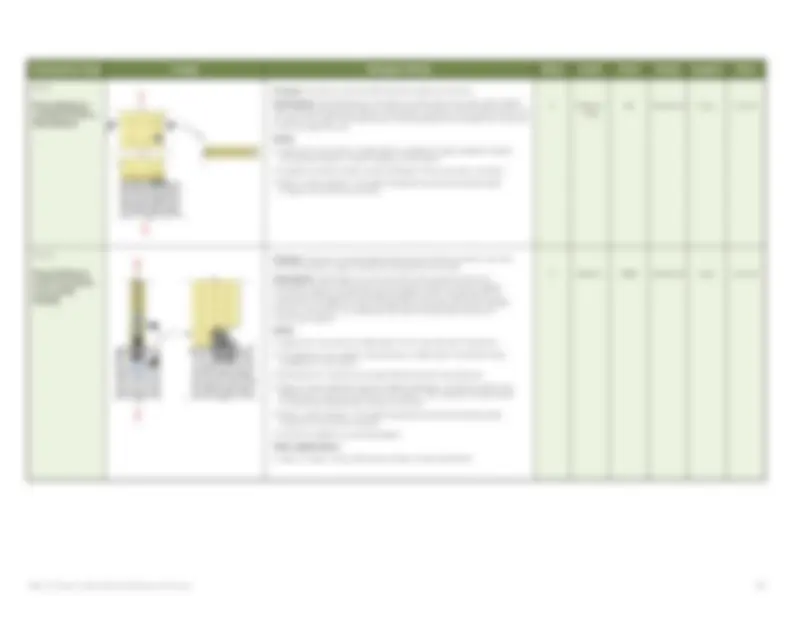
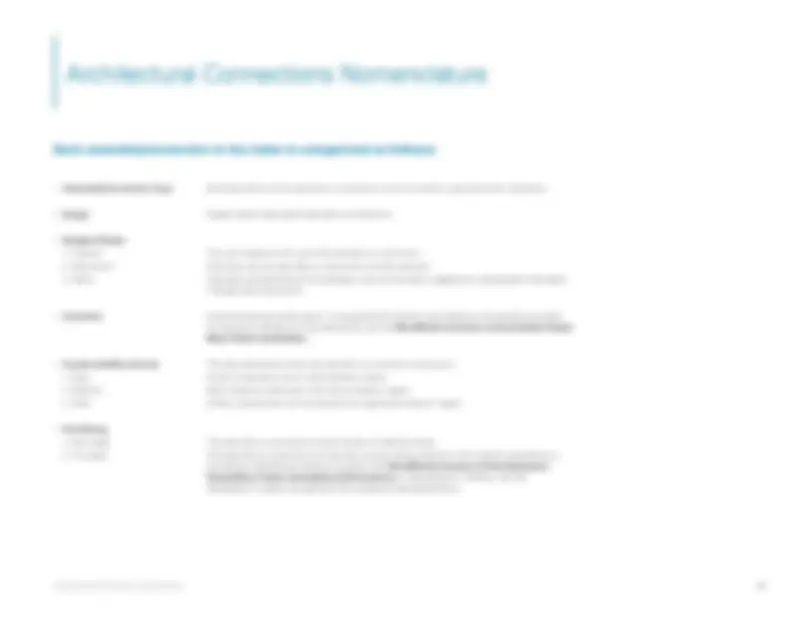
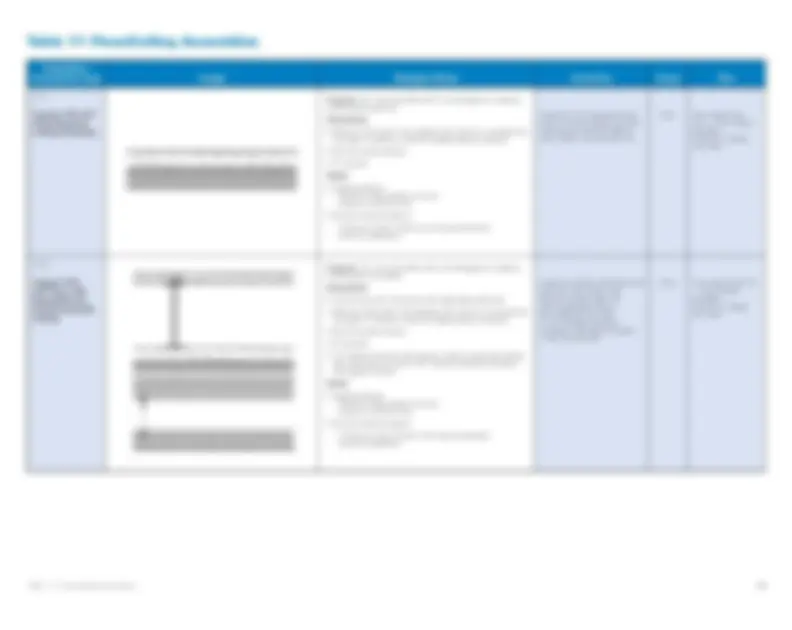
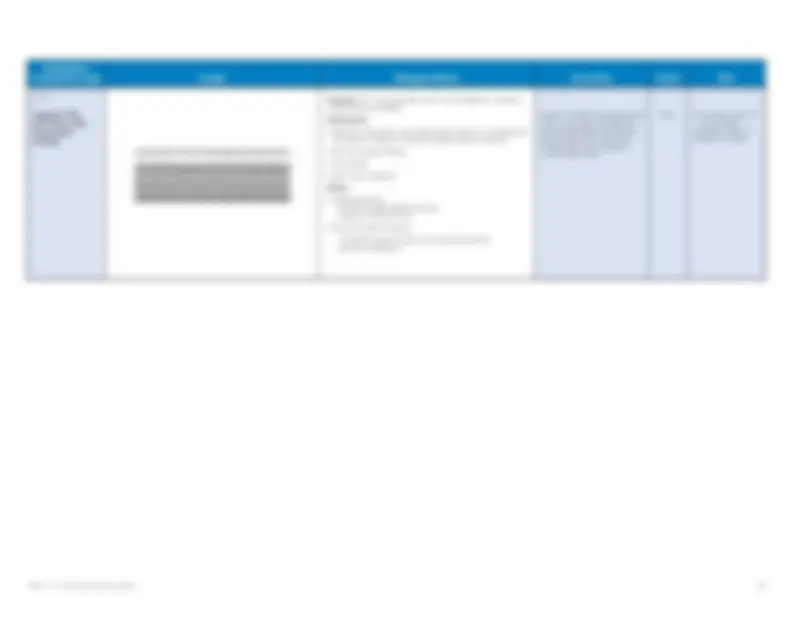
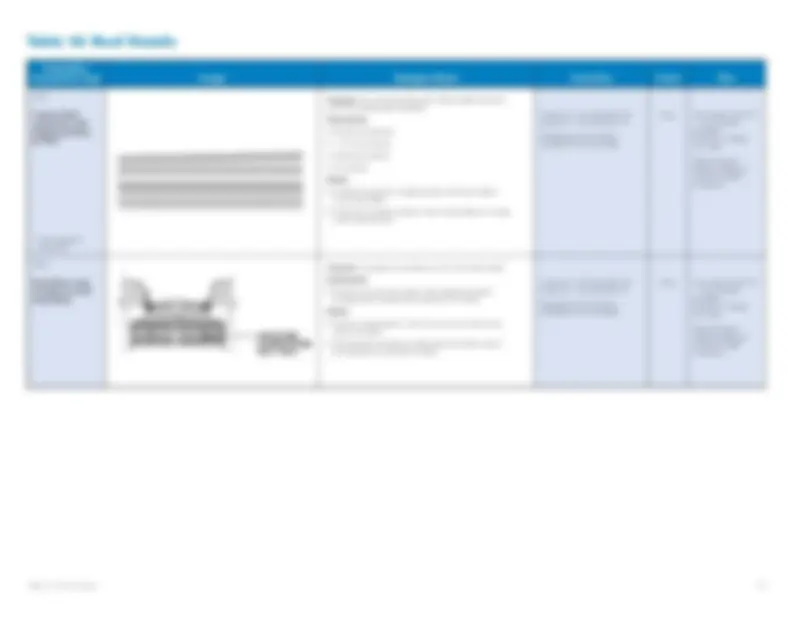
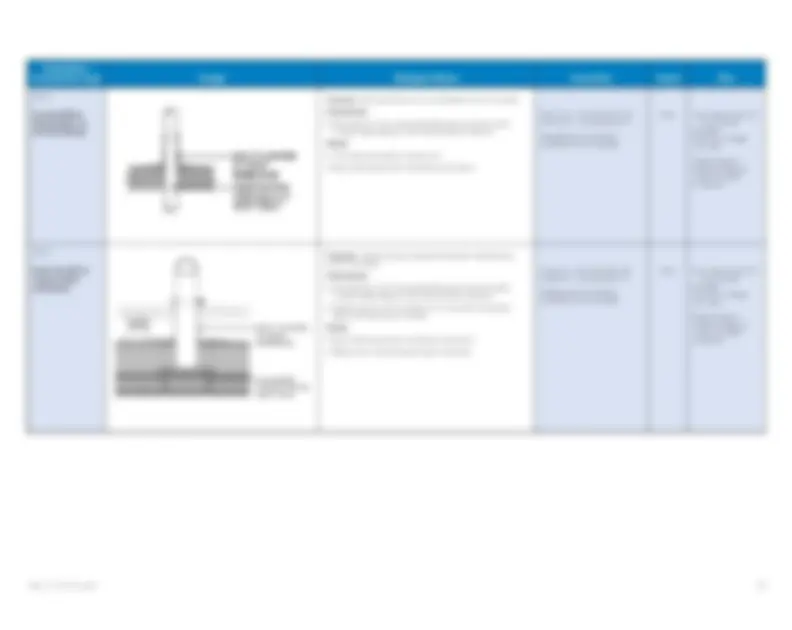
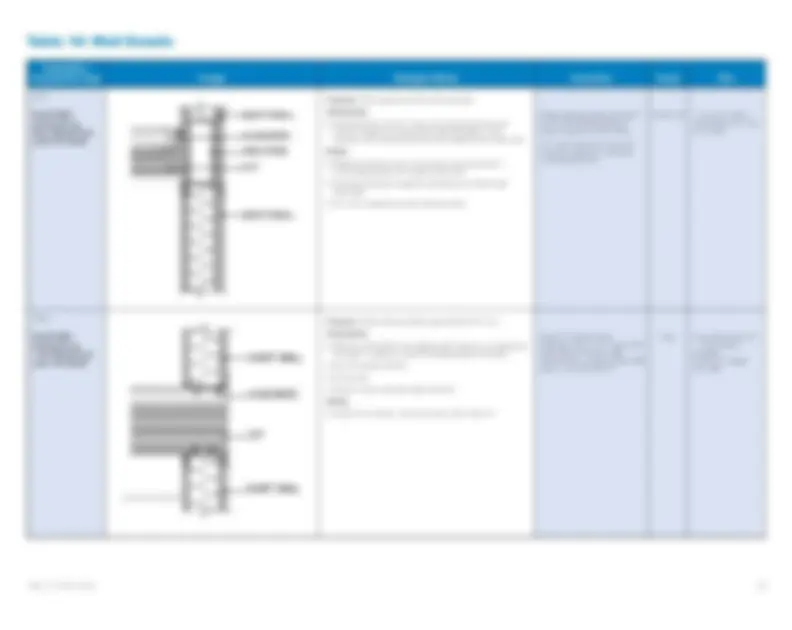
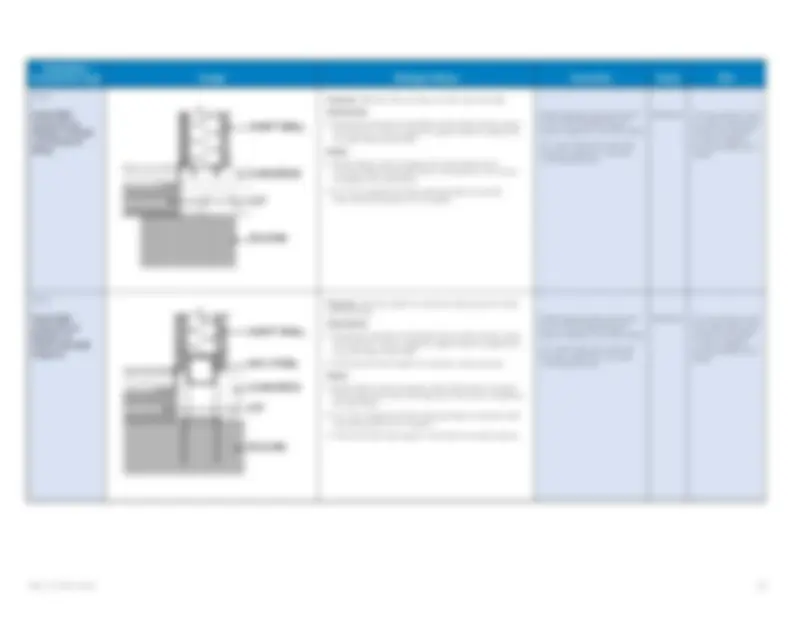
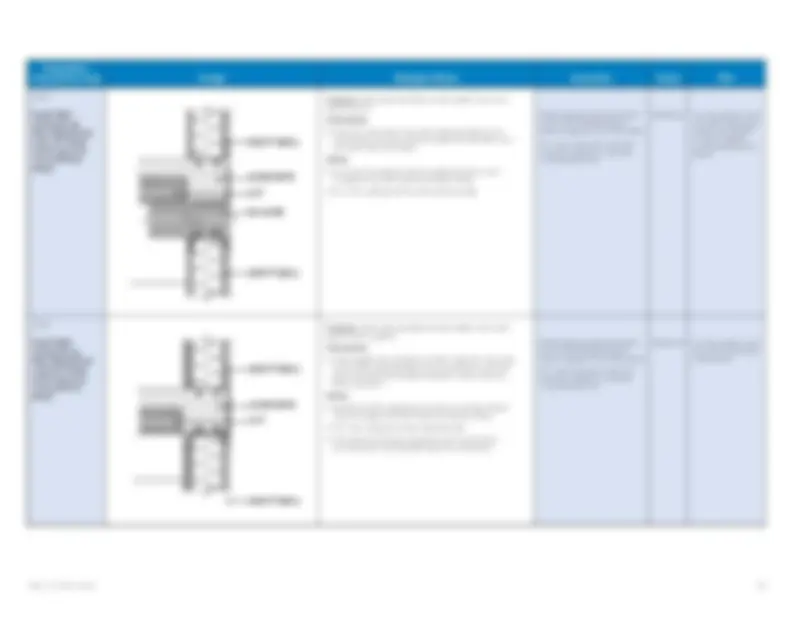
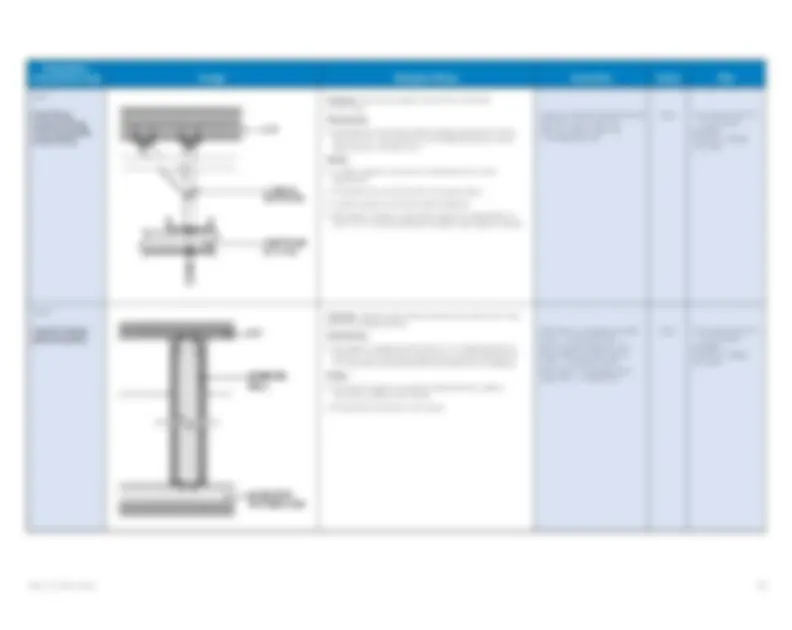
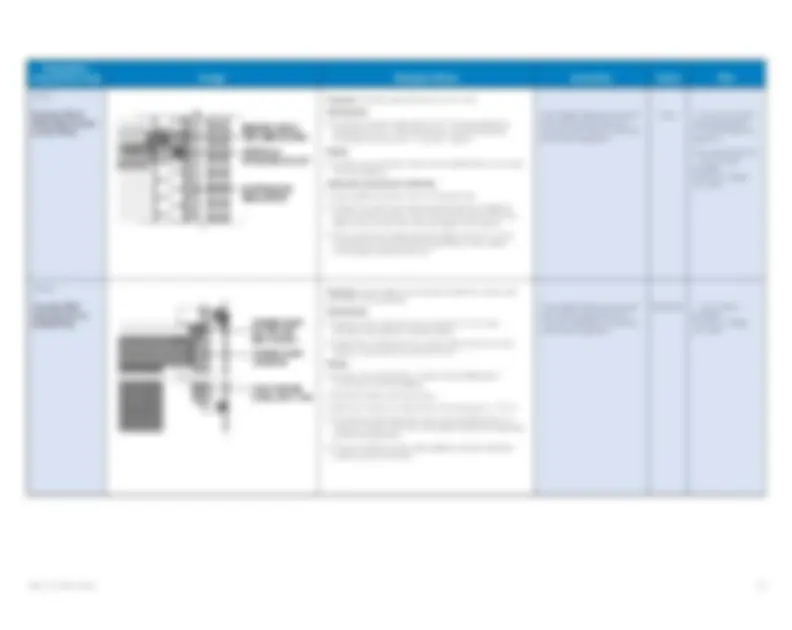
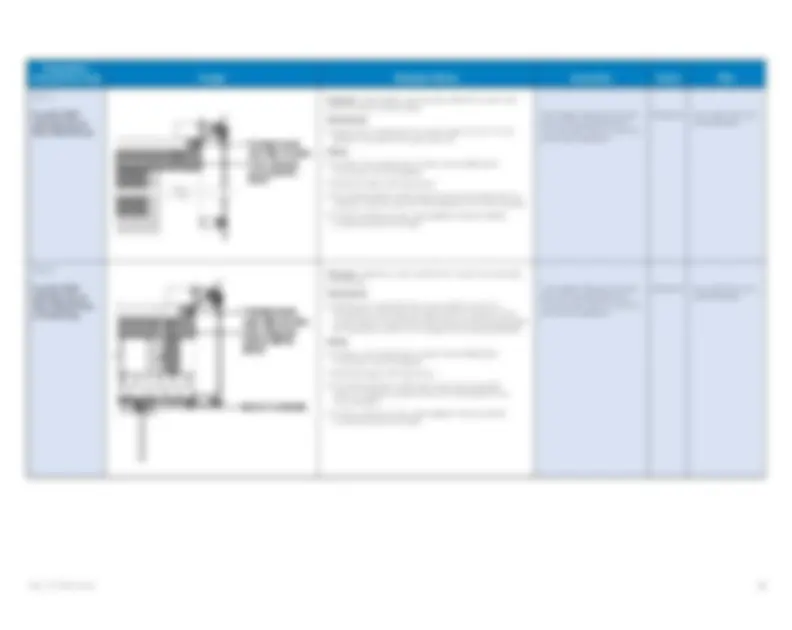
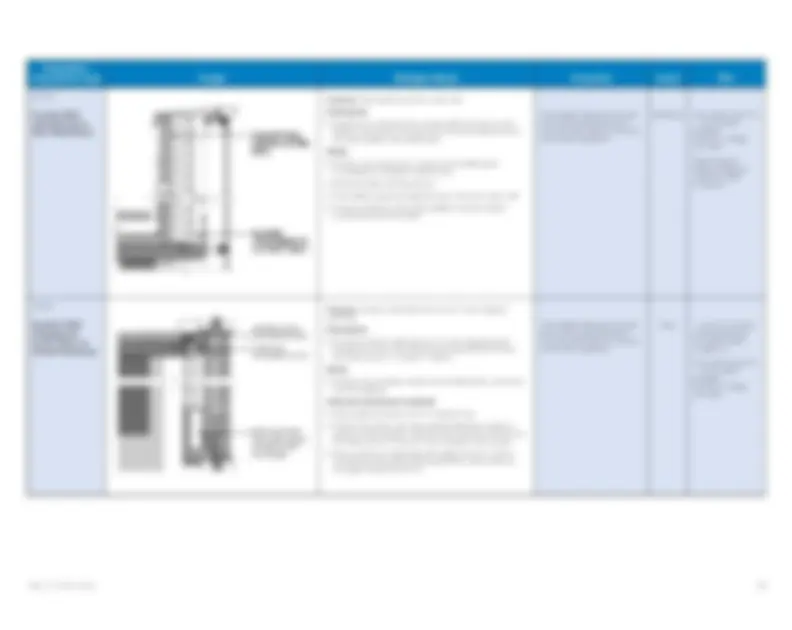
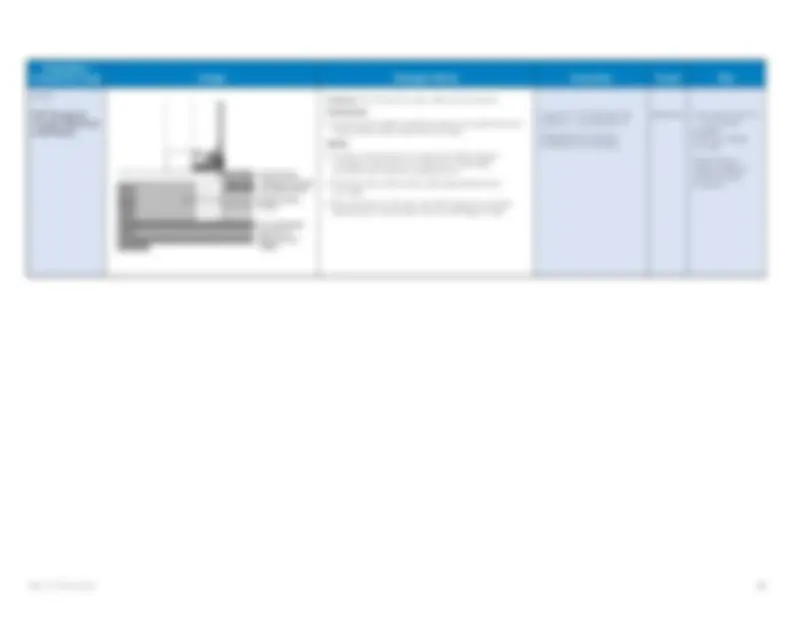
Study with the several resources on Docsity
Earn points by helping other students or get them with a premium plan
Prepare for your exams
Study with the several resources on Docsity
Earn points to download
Earn points by helping other students or get them with a premium plan
Community
Ask the community for help and clear up your study doubts
Discover the best universities in your country according to Docsity users
Free resources
Download our free guides on studying techniques, anxiety management strategies, and thesis advice from Docsity tutors
An in-depth exploration of various connection types for mass timber panels, including structural connections, mass timber panel support at beams and columns, and mass timber panel support at steel beams and walls. It includes designer notes, classes, loads, costs, construction requirements, inspection guidelines, and fire safety considerations for each connection type. The document also lists potential suppliers for proprietary connectors and standoffs.
What you will learn
Typology: Study notes
1 / 80
This page cannot be seen from the preview
Don't miss anything!
F R E E P R O J E C T S U P P O R T | E D U C AT I O N | R E S O U R C E S For free technical assistance related to mass timber connections, or any aspect of the design, engineering or construction of a commercial or multi-family wood building in the U.S., visit woodworks.org to contact the WoodWorks Regional Director nearest you or email help@woodworks.org.
Table of Contents 4 Table 15: Mass Timber Column Base at Concrete 15-1 Column Bears with Knife Plate ............................................................................ 59 15-2 Column Bears with Side Plates ........................................................................... 59 15-3 Column Bears with Custom Standoff .................................................................. 60 15-4 Column Bears with Adjustable Standoff Base ..................................................... 61 15-5 Column Bears with Proprietary Dowel Connector ............................................... 61 15-6 Column Bears with Proprietary Plate Connector ................................................. 61 15-7 Column Bears with Proprietary Adjustable Column Base................................... 62 Table 16: Mass Timber Wall Panel Base at Concrete 16-1 Panel Bears with Sill Plate ................................................................................... 63 16-2 Panel Bears with Side Plate ................................................................................. 63 16-3 Panel Bears with Bracket ..................................................................................... 64 16-4 Panel Bears with Buckets .................................................................................... 64 16-5 Panel Bears with Continuous Proprietary Shoe .................................................. 65 16-6 Panel Bears with Knife Plates .............................................................................. 65 16-7 Panel Holdown ..................................................................................................... 66 16-8 Panel Holdown with Rod System ........................................................................ 66 16-9 Panel Holdown with Multi-Story Rod System ..................................................... 67 16-10 Panel Holdown with Proprietary Connection System ......................................... 67 Architectural Connections Architectural Connections Nomenclature ............................................................ 68 Table 17: Floor/Ceiling Assemblies 17-1 Typical 3-Ply CLT Floor/Exposed Ceiling Assembly ............................................ 69 17-2 Typical 5-Ply CLT Floor with Raised Plenum Floor/Concealed Ceiling ................ 69 17-3 Typical 5-Ply CLT Floor with Concealed Ceiling ................................................... 70 Table 18: Roof Details 18-1 Typical Roof Assembly with Rigid Insulation & TPO* .......................................... 71 18-2 Roof Drain and Overflow at CLT Roof Deck ......................................................... 71 18-3 Conduit/Pipe Penetration at CLT Roof Deck ........................................................ 72 18-4 Roof Tie-Off at Typical Roof Assembly ................................................................ 72 *Thermoplastic polyolefin Table 19: Wall Details 19-1 Shaft Wall Assembly at Non-Rated Floor & 2-Hr Shaft........................................ 73 19-2 Shaft Wall Assembly at 1-Hr-Rated Floor & 1-Hr Shaft ....................................... 73 19-3 Shaft Wall Assembly at Bottom of Shaft with Beam Support ............................. 74 19-4 Shaft Wall Assembly at Bottom of Shaft with HSS Support ............................... 74 19-5 Shaft Wall Assembly at Non-Rated Floor and 1-Hr Shaft with Concrete Turned Down Beam ...................................................................... 75 19-6 Shaft Wall Assembly at Non-Rated Floor & 2-Hr Shaft with Concrete Turned Down Beam ...................................................................... 75 19-7 CLT Hung Support Hung from Underside of CLT Floor ........................................ 76 19-8 Typical Interior Demising Wall .............................................................................. 76 19-9 Exterior Brick Wall Attachment to CLT Floor ....................................................... 77 19-10 Curtain Wall Attachment to Rated Floor.............................................................. 77 19-11 Curtain Wall Attachment to Non-Rated Floor....................................................... 78 19-12 Curtain Wall Attachment to Non-Rated Floor at Overhang .................................. 78 19-13 Curtain Wall Attachment to Non-Rated Roof ....................................................... 79 19-14 Exterior Wall Attachment to CLT Floor at Glazed Openings ................................ 79 19-15 CLT Terrace at Curtain Wall Curb with Pavers..................................................... 80 Disclaimer: The information in this publication, including, without limitation, references to information contained in other publications or made available by other sources (collectively “information”) should not be used or relied upon for any application without competent professional examination and verification of its accuracy, suitability, code compliance and applicability by a licensed engineer, architect or other professional. Neither the Wood Products Council nor its employees, consultants, nor any other individuals or entities who contributed to the information make any warranty, representative or guarantee, expressed or implied, that the information is suitable for any general or particular use, that it is compliant with applicable law, codes or ordinances, or that it is free from infringement of any patent(s), nor do they assume any legal liability or responsibility for the use, application of and/or reference to the information. Anyone making use of the information in any manner assumes all liability arising from such use.
Mass Timber Design Notes 5 Mass timber structures are a unique building type requiring consideration of concepts that may be unique to mass timber and not considered in the design of connections for other materials. The following is an overview of some of these considerations, but should not be considered an exhaustive list. It is the responsibility of the designer to ensure that the connection design accounts for all necessary criteria. Mass Timber Panels, Beams and Columns: A unique aspect of mass timber construction is that some materials and members are not standardized. Products available from different suppliers may vary by species, geometry and available maximum fabrication size. These factors may be important constructability, cost and/or aesthetic considerations for a project. Selection of a supplier early in the design process, although not always feasible, can be extremely helpful. Panel types can include CLT, DLT, NLT, GLT and SCL-CLT. In most cases, a supplier will manufacture only one panel type. Conversations with the supplier early in design can also help to determine optimal grid sizes, preferred connection geometries, and methods to reduce construction costs. For example, in panel manufacturing, a connection that requires the panel to be flipped during manufacture will be more expensive than a panel that can be fabricated without flipping it over. Discussions with the mass timber supplier and contractor are useful to determine their fabrication capabilities and construction preferences. In mass timber construction, it is often desirable for holes, notches and any other alterations to be made in the member during fabrication instead of on site. Many fabricators can also produce complex geometries in the shop that could be difficult to achieve on the jobsite. Fabrication tolerances for mass timber are extremely precise and might be as low as +/- 1/16-in. Tolerances for other materials such as steel, concrete and/or masonry can be larger. In most structures, there will be some interface between mass timber and these other materials. It is therefore important to consider the effects of these relative construction tolerances. Fasteners: Many connections in mass timber construction are connected using dowel-type fasteners, including bolts, screws, nails and pins. Detailed guidance on these fasteners is found in the American Wood Council's (AWC's) National Design Specification®^ (NDS®) for Wood Construction , Chapter 12. The required fastener for a given connection will depend on the connection geometry and loading conditions, as well as contractor, architect and fabricator input. For many connections shown in the index, especially those distributed over long joints, connection capacity can be increased or decreased simply by adjusting the size and spacing of fasteners. Screws are the most common fastener used in mass timber connections. However, where nails work instead of screws, they are easier and less expensive to install. It is also worth considering specifying nail gun-compatible nails instead of common nails and collated screws instead of individual screws for ease of installation. Where screws are used in a connection, they can be either lag or proprietary screws, and many fabricators have preferred screw manufacturers. Screw suppliers include Simpson Strong-Tie, Rothoblaas, MiTek, MTC Solutions, GRK Fasteners and others. Requirements for lag screw installation are covered in the NDS. Proprietary screws are as specified by the manufacturer and are typically self-tapping. For mass timber projects, screw sizes are generally 1/4-in. in diameter and greater and are available in a wide range of lengths. Installers tend to prefer smaller-diameter screws where possible because they are easier to install. Smaller screws may also be advantageous for the designer because larger screw diameters have greater edge distance and spacing requirements. In many cases, it is possible to use smaller edge distances and spacing when screw holes are pre-drilled, but this can add expense to the project. It is important to ensure that fasteners are not loaded in withdrawal from the end grain of members, as specified in the NDS. This can be challenging on the edges of CLT panels, where every other ply presents end grain and there are tight constraints due to edge distance requirements. There are two primary screw types to choose from: partially-threaded and fully-threaded. Partially-threaded screws are more common in mass timber construction and have a smooth shaft between the screw head and the threads, whereas fully-threaded screws have threads along their entire length. Partially-threaded screws are used for fastening two members together, and work to pull the two members together. Ideally, the threads will be fully embedded in the main member. Fully-threaded screws are used where thread withdrawal capacity is required either on both sides of a connection joint or a possible failure plane within a single member. Fully-threaded screws do not pull two members together as partially-threaded screws do, and improper installation can create a gap. Fully-threaded screws can also restrain members differently than partially-threaded screws when the member shrinks. Additional information on fully versus partially-threaded screws can be found in MTC Solutions' Structural Screw Design Guide. Mass Timber Design Notes
Connection Design Resources 7 The following resources may be useful in mass timber connection design:
Structural Connections Nomenclature 8 Each connection in the index is categorized as follows:
- Connection Type : Brief description of the connection in terms of the primary load path. - Image: Graphic showing the members and pieces of the connection. For most connections that include a panel member, it is shown as CLT. In most of the connections, CLT is interchangeable with DLT, NLT or SCL- CLT without any change to the connection. Where a connection is specific to the panel type, it is stated in the Designer Notes. Structural Connections Nomenclature Cross-Laminated Timber (CLT) Nail-Laminated Timber (NLT) or Dowel-Laminated Timber (DLT) Structural Composite Lumber Cross-Laminated Timber (SCL-CLT) o Red symbols indicate the primary load path and direction for the connection. o Light blue symbols indicate the secondary load paths and directions for the connection. o Loads across the page. o Loads into the page. o Loads out of the page. - Designer Notes: o Purpose The main function and load path of the connection. Secondary load paths may also be present and analysis of the resulting load combinations may be required. o Description Describes how the connection is constructed. o Notes Important considerations for the designer, such as alternates, suggestions and potential challenges in design and construction. o Other Applications Points to other sections in the index where the same connection with a different supporting member applies.
Table 1: Mass Timber Panel to Mass Timber Panel 10
Panels Connect with Single Surface Spline Purpose : Transfer of in-plane shear along the panel-to-panel joint. Description : Adjacent floor panels with routed surfaces are butted together. A plywood spline is fastened to both panels using partially-threaded screws or nails. Notes :
Table 1: Mass Timber Panel to Mass Timber Panel 11
Panels Connect with Steel Surface Spline Purpose : Transfer of in-plane shear along the panel-to-panel joint. Description : Adjacent floor panels are butted together. A steel spline is fastened to both panels using partially-threaded screws or nails. Notes :
Table 2: Mass Timber Panel Support at Mass Timber Beam 13
Panel Bears on Beam Purpose : Transfer of vertical loads from roof or floor panel to wood beam. Can also transfer shear along the length of the beam. Description : Roof or floor panel bears on top of wood beam. Positive attachment is made with partially-threaded screws. Notes :
Table 2: Mass Timber Panel Support at Mass Timber Beam 14
Panel Bears on Ledger at Beam Purpose : Transfer of vertical load from roof or floor panel to wood beam. Can also transfer shear along the length of the beam. Description : Roof or floor panel bears on ledgers connected to wood beam with partially-threaded screws. Positive connection of panel to ledger is made with partially-threaded screws. Notes :
Table 3: Mass Timber Panel Point Support at Mass Timber Column 16
Floor Panel Bears on Column at Standoff Purpose : Transfer of vertical load from floor panels and upper column to wood column below. Description : Upper column and panels bear on standoff. Standoff bears on column below. Standoff consists of an upper bearing plate welded to an alignment guide and a lower bearing plate welded to a standoff. The alignment guide nests inside the standoff. Positive connection of bearing plates is made to columns with epoxied threaded rods or partially-threaded screws. Positive connection of panel to bearing plate is made with welded threaded rods. Notes :
Table 3: Mass Timber Panel Point Support at Mass Timber Column 17
Floor Panel Bears on Column at Proprietary Standoff Purpose : Transfer of vertical load from floor panels and upper column to wood column below. Description : Proprietary connector is composed of an oversized bearing assembly and upper post, which fits into a larger lower post and bearing plate. The upper column bears on the oversized bearing assembly which then bears on the floor panels. The floor panels bear on the lower bearing plate. Positive connection is made between the connector and panels and between the connector and columns with screws. Notes :
Table 4: Mass Timber Panel Support at Mass Timber Wall Panel 19
Roof Panel Bears on Wall – Platform with Bracket Purpose : Transfer of vertical load from roof panel to wall panel below. Can also transfer in-plane and out-of-plane loads between the wall panel and roof panel. Description : Roof panel bears on wall panel below. A positive connection is made between roof and wall panels with custom or proprietary bracket with partially-threaded screws. Notes :
Table 4: Mass Timber Panel Support at Mass Timber Wall Panel 20
Floor Panel Bears on Wall – Platform with Side Plate Purpose : Transfer of vertical load from floor panel and wall panel above to wall panel below. Can also transfer in-plane and out-of-plane loads between the wall panels and floor panel. Description : Floor panel bears on wall panel below. Wall panel above bears on floor panel. A positive connection is made between floor panel and walls with side plate with partially-threaded screws. Notes :