
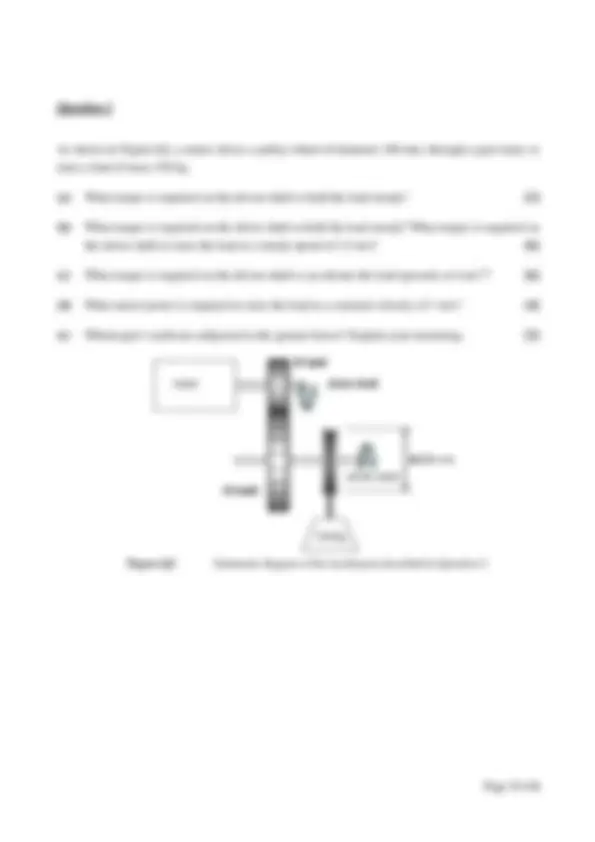
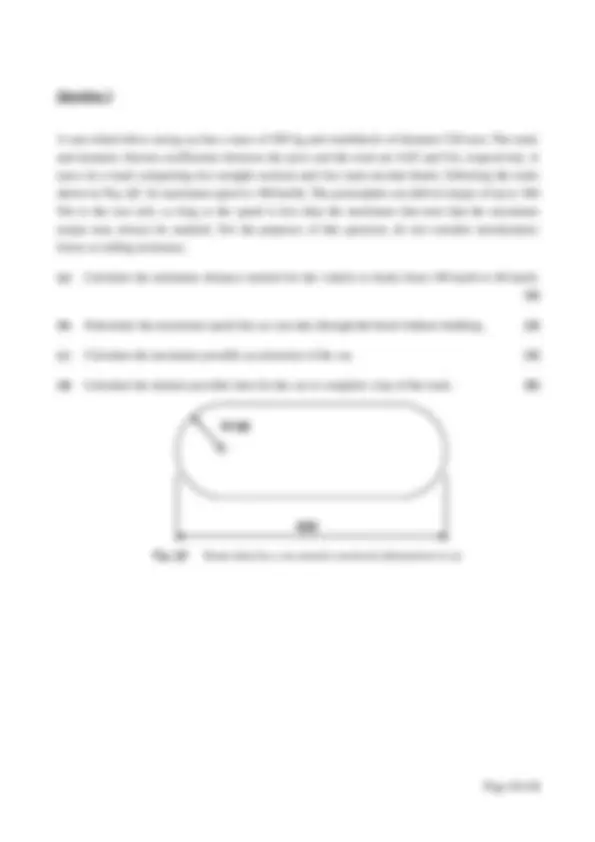
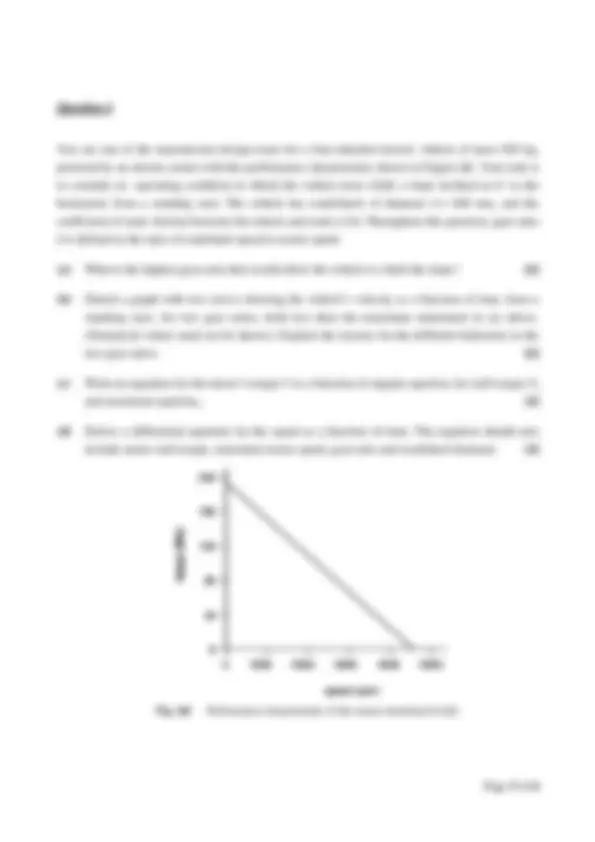
Study with the several resources on Docsity
Earn points by helping other students or get them with a premium plan
Prepare for your exams
Study with the several resources on Docsity
Earn points to download
Earn points by helping other students or get them with a premium plan
Community
Ask the community for help and clear up your study doubts
Discover the best universities in your country according to Docsity users
Free resources
Download our free guides on studying techniques, anxiety management strategies, and thesis advice from Docsity tutors
Information about the examinations held in semester 2 of the 2011/2012 academic year for the mechanical, electrical and electronic engineering courses. It includes exam codes, modules, question papers, instructions, and requirements. Topics such as wind tunnel testing for cars, torque calculations, and vehicle dynamics.
Typology: Exams
1 / 6
This page cannot be seen from the preview
Don't miss anything!
Exam Code(s) 1BM, 1BG, 1BLE, 1BP, 1EG, 1BSE, 1BEI, 1BEE Exam(s) 1 st^ Engineering: Mechanical Biomedical Electrical and Electronic Electronic and Computer Undenominated Energy Systems Engineering Innovation – Electronic, Sports and Exercise)
Module Code(s) ME Module(s) Fundamentals of Mechanical Engineering
Paper No. 1
External Examiner(s) Prof. Robin Clarke Internal Examiner(s) Prof. Sean Leen *Dr. Nathan Quinlan
Instructions: (^) Answer 3 questions. All questions carry equal marks.
No. of Pages 6 Department(s) Mechanical and Biomedical Engineering Course Co-ordinator(s) Dr. Nathan Quinlan
Requirements:
Statistical/ Log Tables Mathematical tables Release to Library: Yes
A 1/5 scale model of a racing car is tested in a wind tunnel with a rolling road at airspeed of 22 m/s. Without wings attached, the aerodynamic downforce on the car is measured as 6.4 N. With front and rear wings attached, the downforce is 38.4 N. Drag on the model car without wings and with wings is 24.0 N and 31.2 N, respectively. On the full-scale car, the planform area of the bare car is 4.62 m^2 , frontal area is 1.65 m^2 , and the wings have planform area of 0.72 m^2 each. The front and rear wings are identical.
(a) Explain the method of wind tunnel testing for cars, with at least one sketch, including arrangements for the measurement of downforce and drag. [4]
(b) Find the coefficients of lift of the car body and the wings. [4]
(c) Calculate the total downforce and drag on the full-scale car at a speed of 250 km/h. [4]
(d) Calculate the minimum engine power required for the full-scale car at 250 km/h. [4]
(e) Estimate the percentage increase in fuel consumption (in terms of fuel burned per unit distance travelled) when a car increases its speed from 100 km/h to 120 km/h. [4]
A rear-wheel-drive racing car has a mass of 450 kg and roadwheels of diameter 520 mm. The static and dynamic friction coefficients between the tyres and the road are 0.85 and 0.6, respectively. It races on a track comprising two straight sections and two semi-circular bends, following the route shown in Fig. Q3. Its maximum speed is 190 km/hr. The powerplant can deliver torque of up to 360 Nm to the rear axle, as long as the speed is less than the maximum (but note that the maximum torque may always be needed). For the purposes of this question, do not consider aerodynamic forces or rolling resistance.
(a) Calculate the minimum distance needed for the vehicle to brake from 190 km/h to 80 km/h. [4]
(b) Determine the maximum speed the car can take through the bend without skidding. [4]
(c) Calculate the maximum possible acceleration of the car. [4]
(d) Calculate the shortest possible time for the car to complete a lap of the track. [8]
Fig. Q3 Route taken by a car around a racetrack (dimensions in m).
You are one of the transmission design team for a four-wheeled electric vehicle of mass 920 kg, powered by an electric motor with the performance characteristic shown in Figure Q4. Your task is to consider an operating condition in which the vehicle must climb a slope inclined at 6° to the horizontal, from a standing start. The vehicle has roadwheels of diameter d = 640 mm, and the coefficient of static friction between the wheels and road is 0.8. Throughout this question, gear ratio k is defined as the ratio of roadwheel speed to motor speed.
(a) What is the highest gear ratio that would allow the vehicle to climb the slope? [6]
(b) Sketch a graph with two curves showing the vehicle’s velocity as a function of time, from a standing start, for two gear ratios, both less than the maximum mentioned in (a) above. (Numerical values need not be shown.) Explain the reasons for the different behaviour in the two gear ratios. [6]
(c) Write an equation for the motor’s torque T as a function of angular speed , for stall torque T 0 and maximum speed 0. [4]
(d) Derive a differential equation for the speed as a function of time. The equation should also include motor stall torque, maximum motor speed, gear ratio and roadwheel diameter. [4]
200
160
120
80
40
torque (Nm)
0 1000 2000 3000 4000 5000
0
torque (Nm)
speed (rpm)
0
200
160
120
80
40
torque (Nm)
0 1000 2000 3000 4000 5000
0
torque (Nm)
speed (rpm)
0
Fig. Q4 Performance characteristic of the motor mentioned in Q4.