

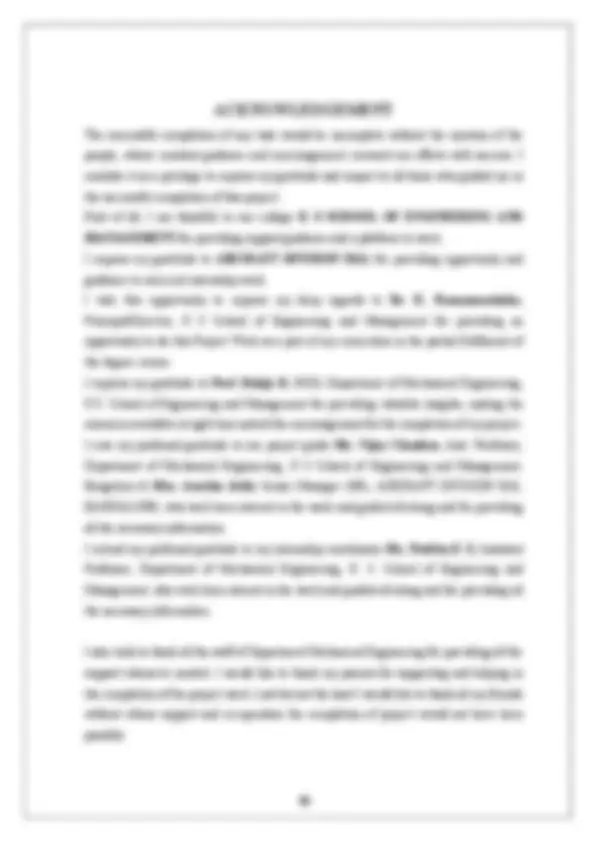
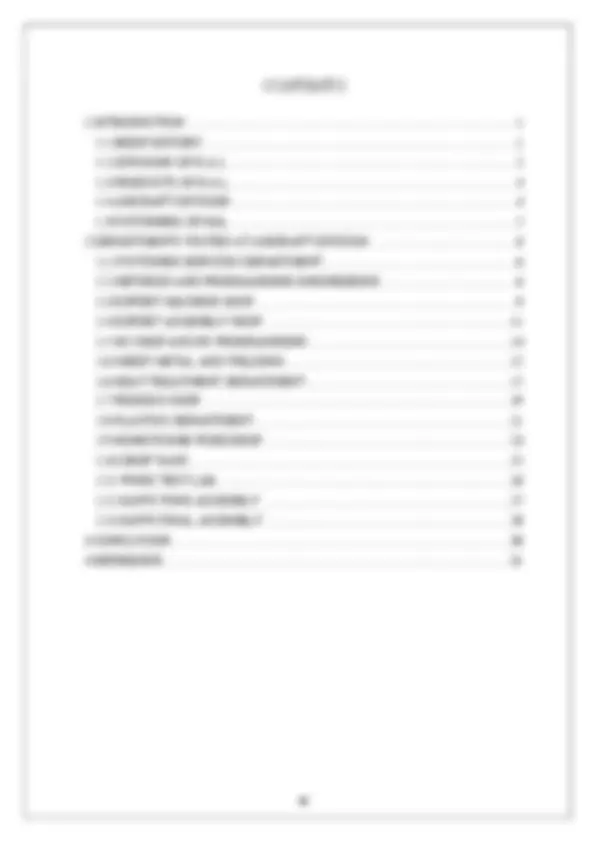
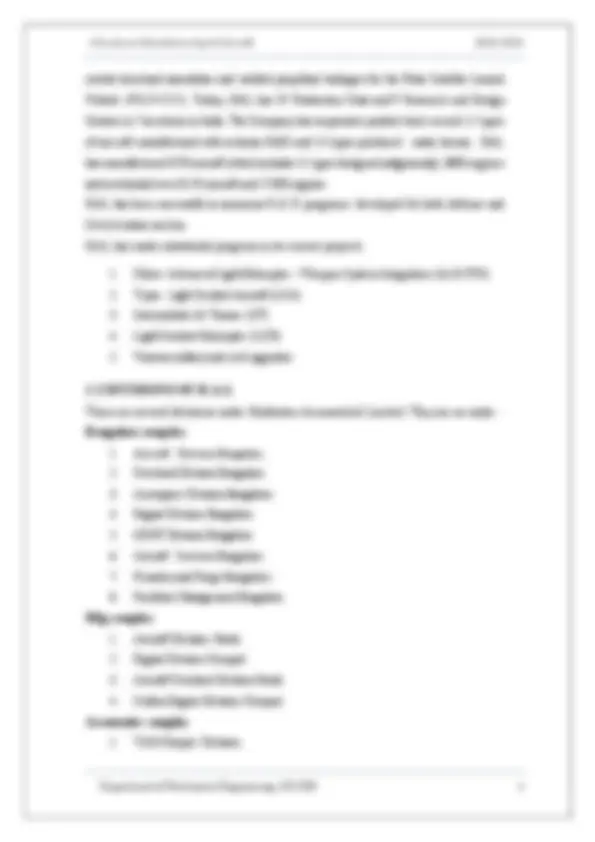
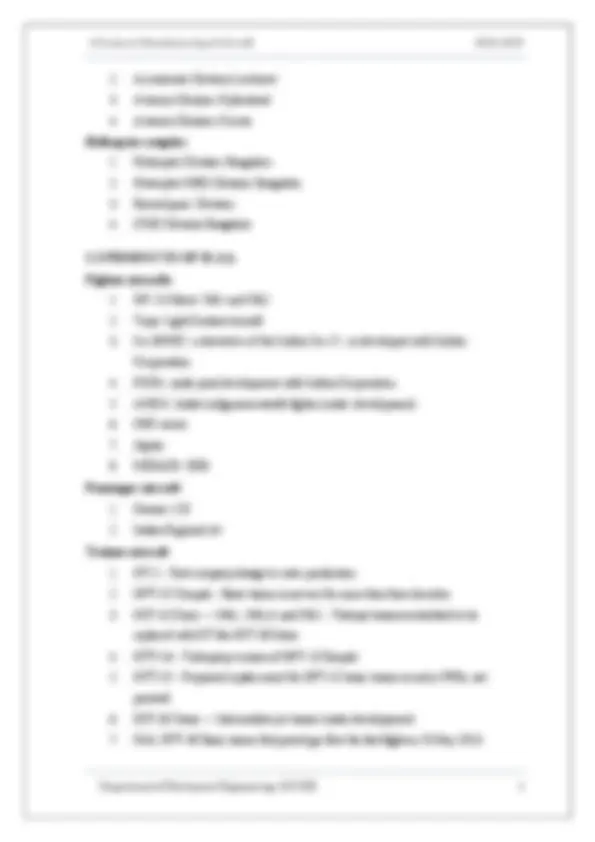
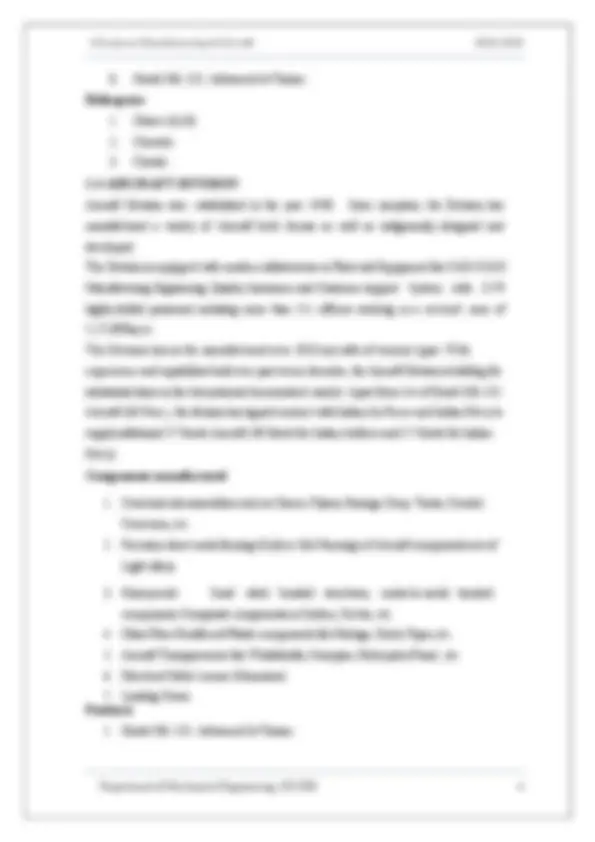
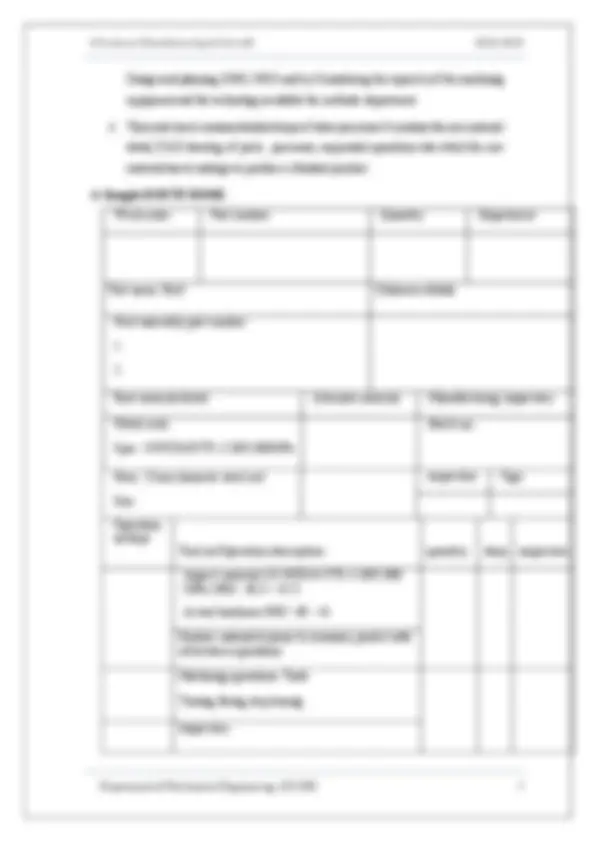
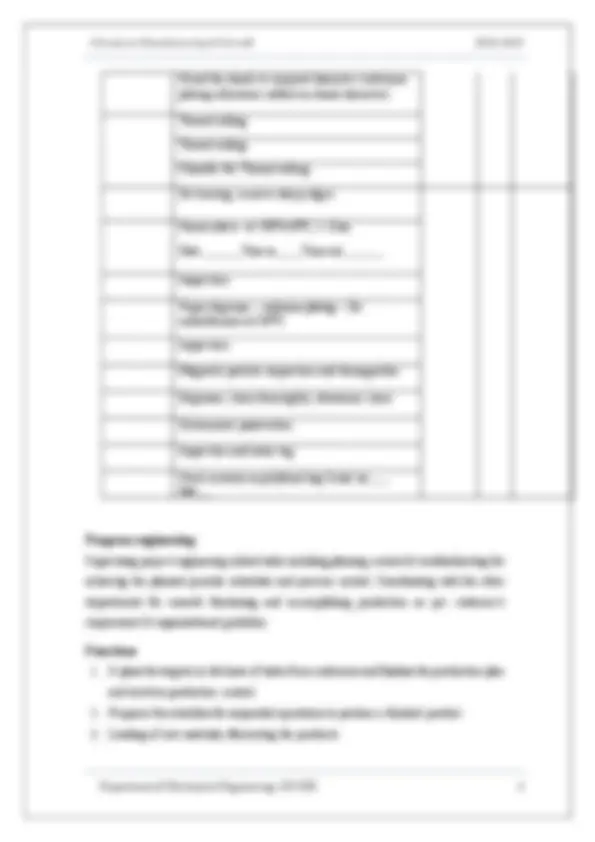
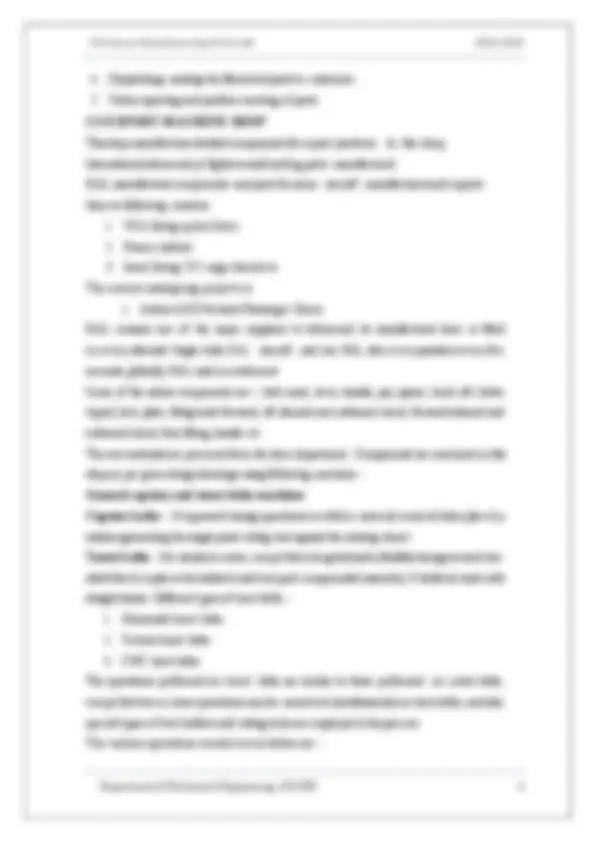
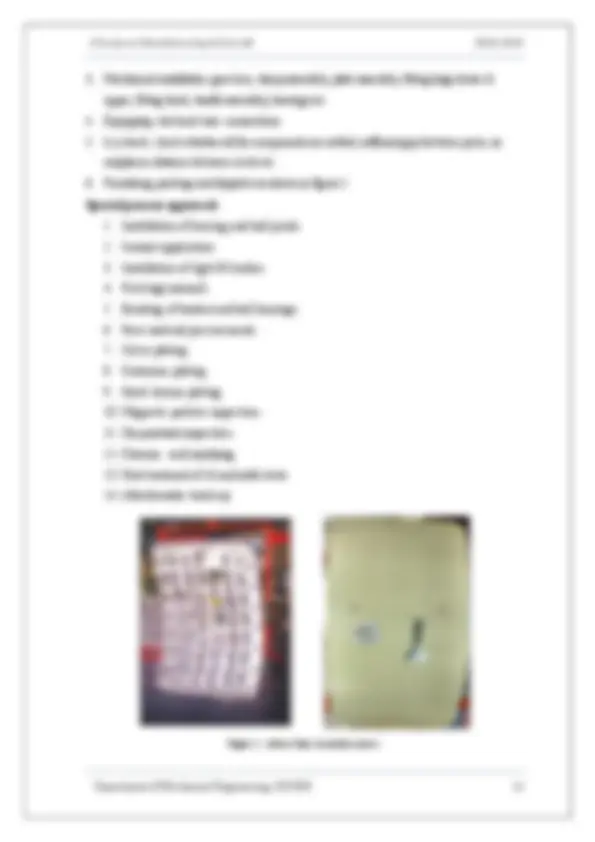
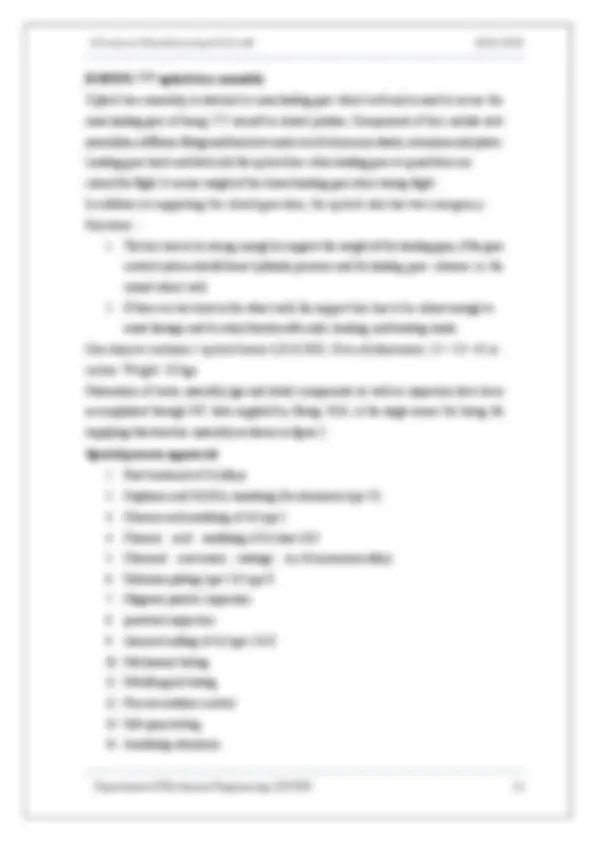
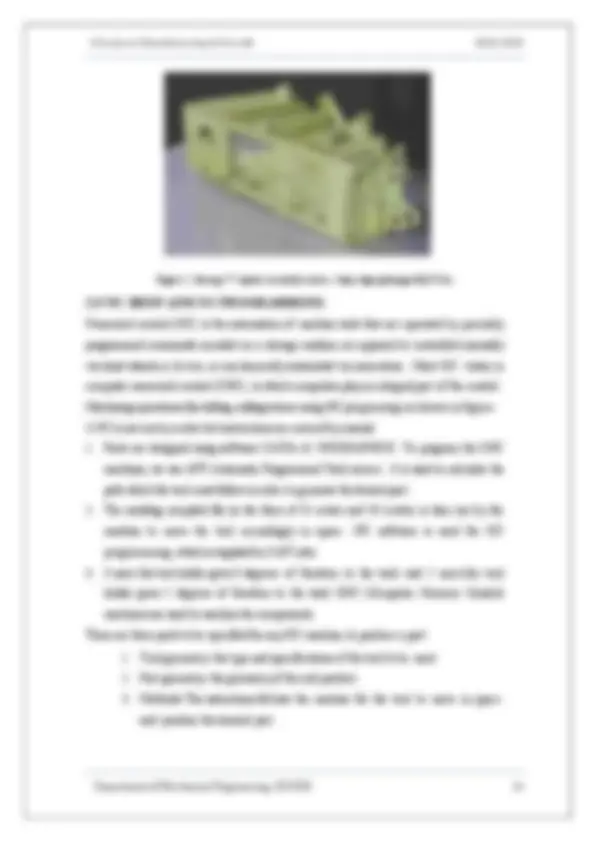
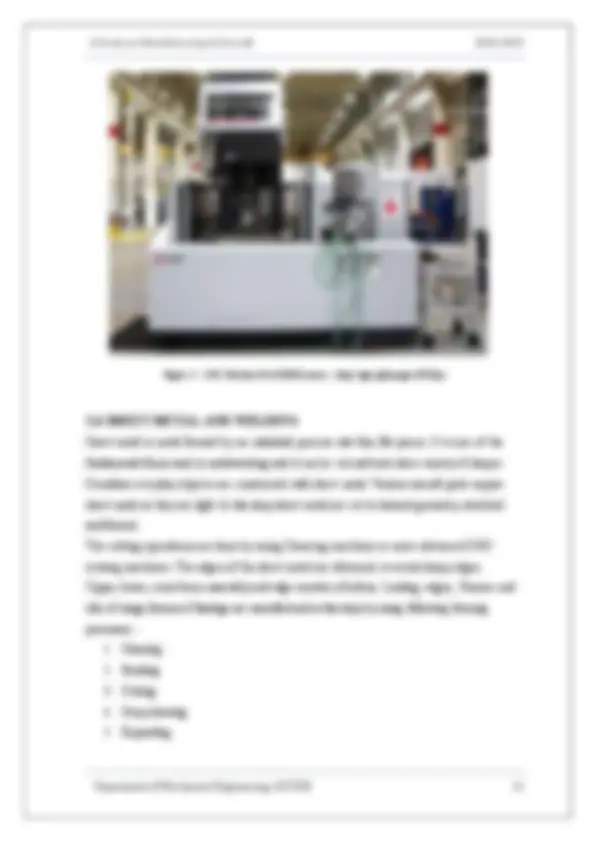
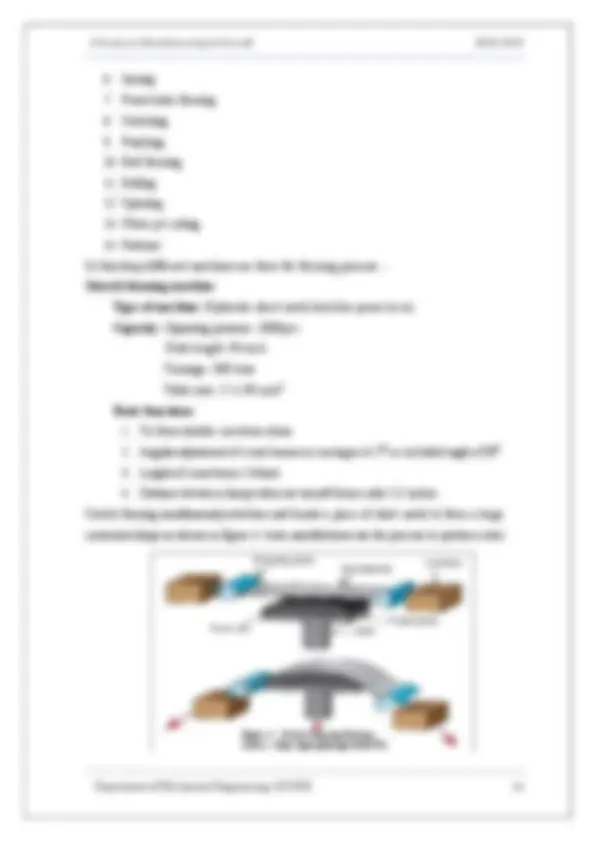
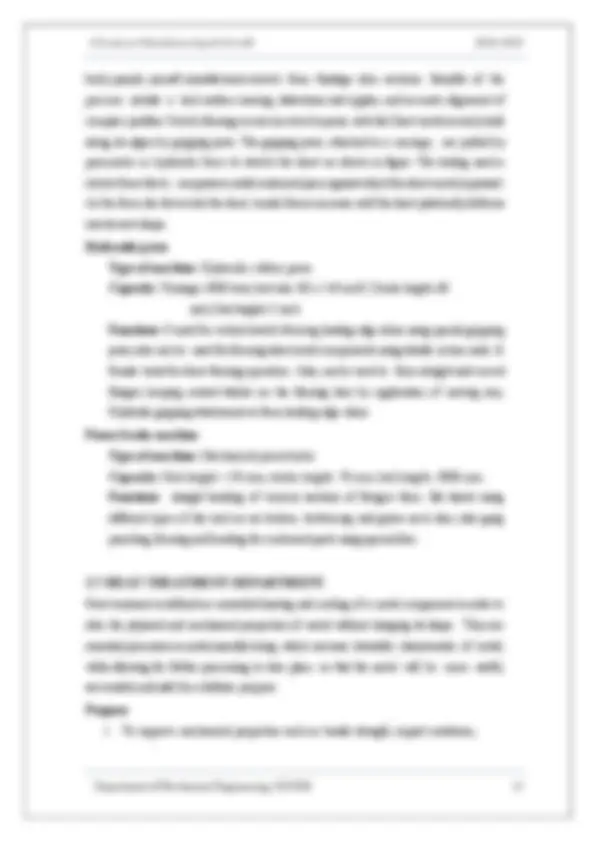
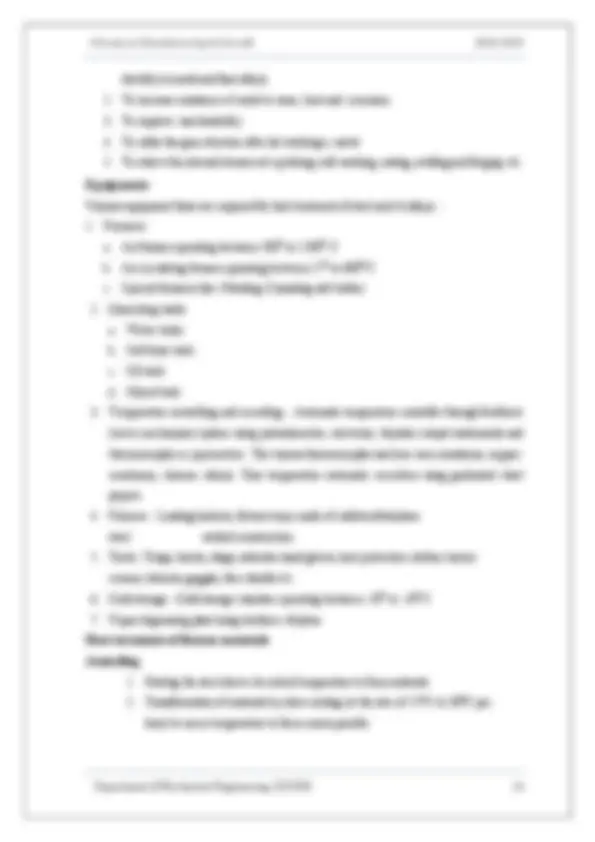
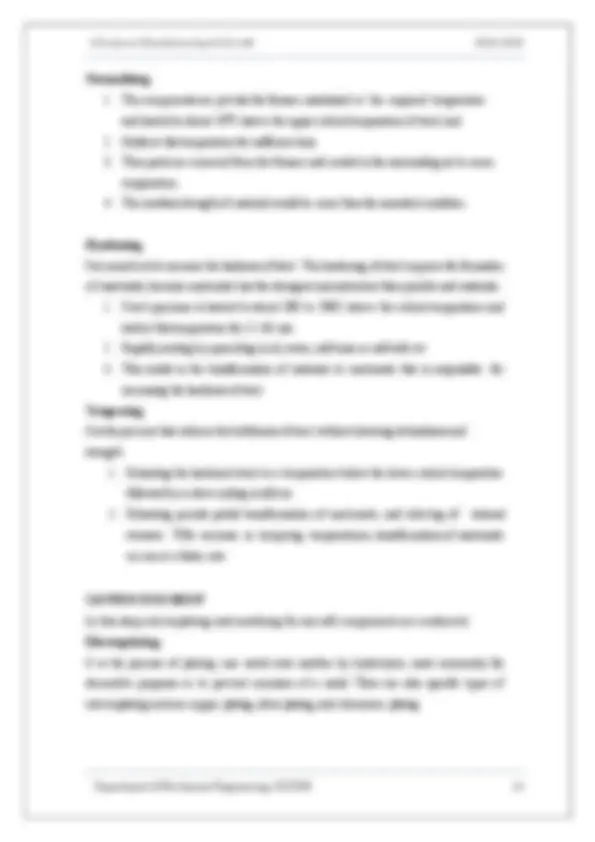

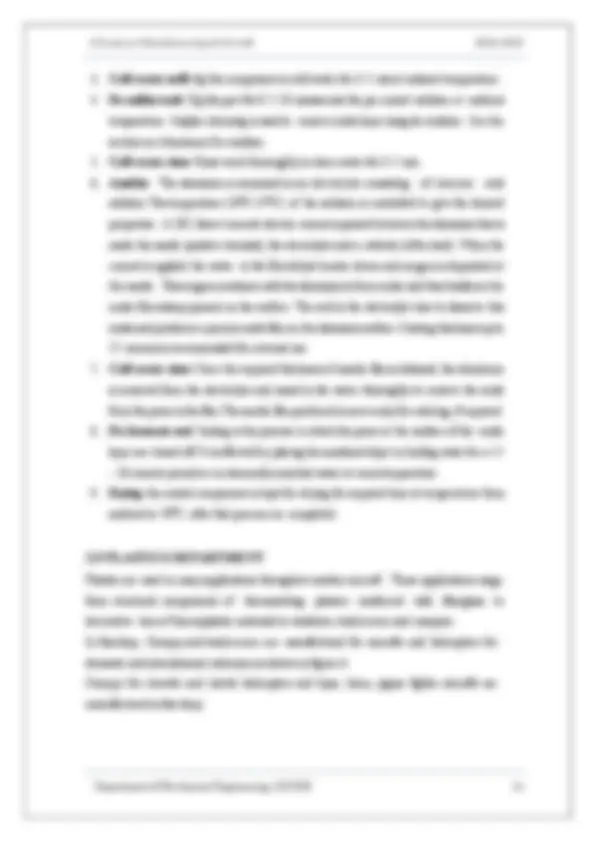
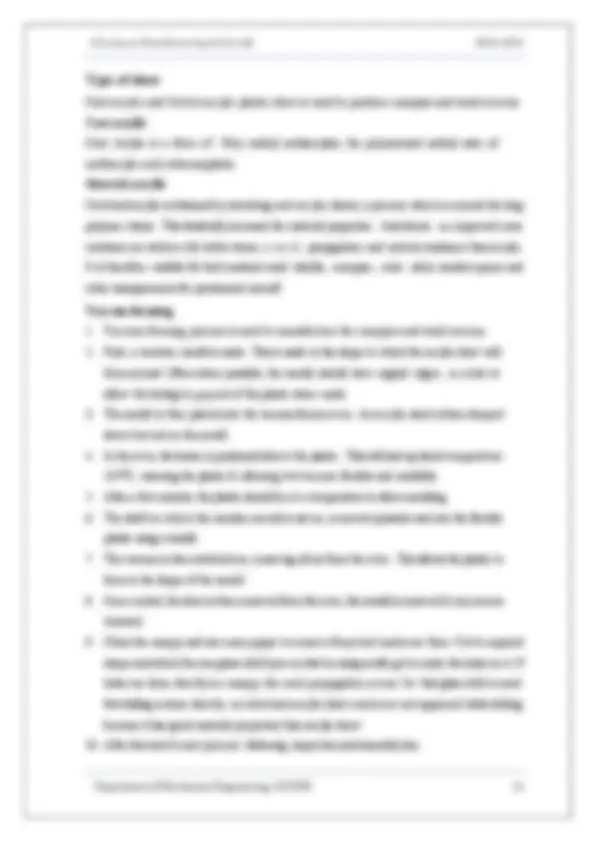
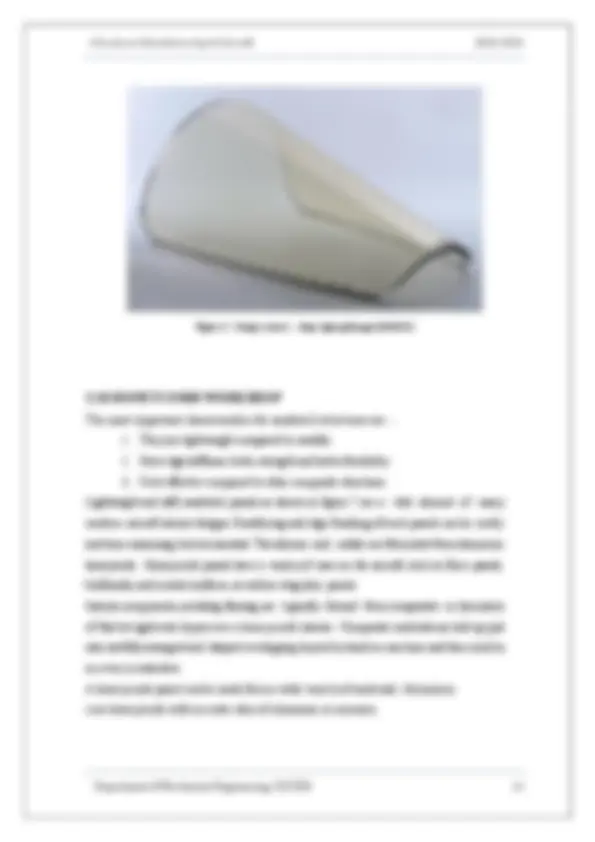
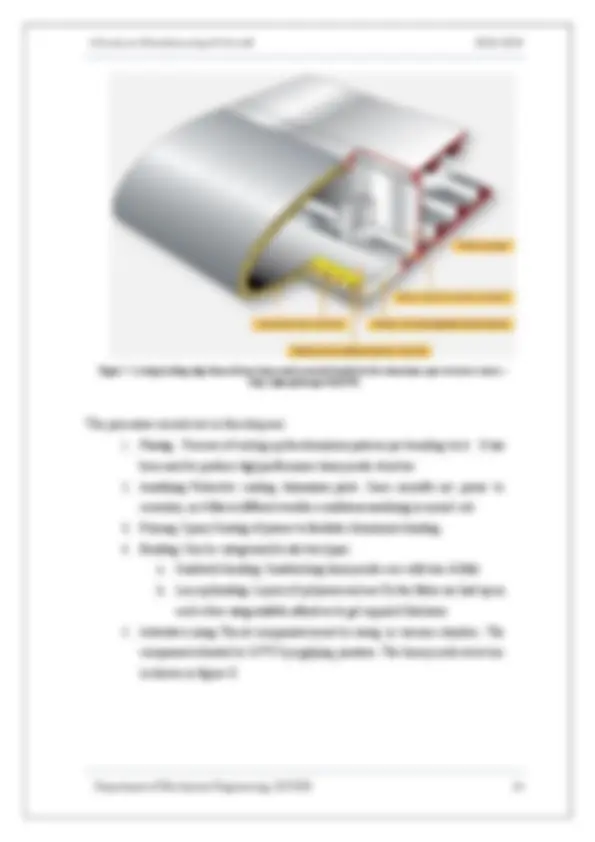
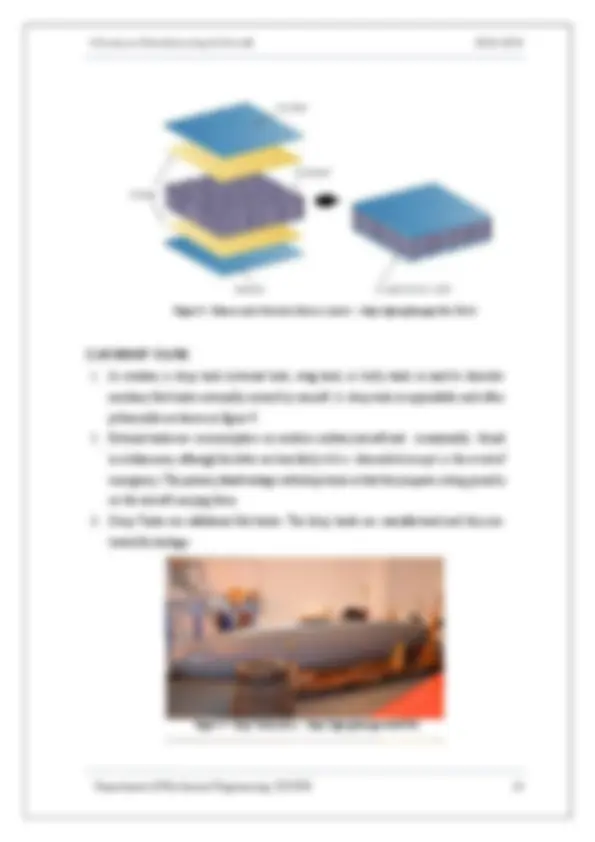
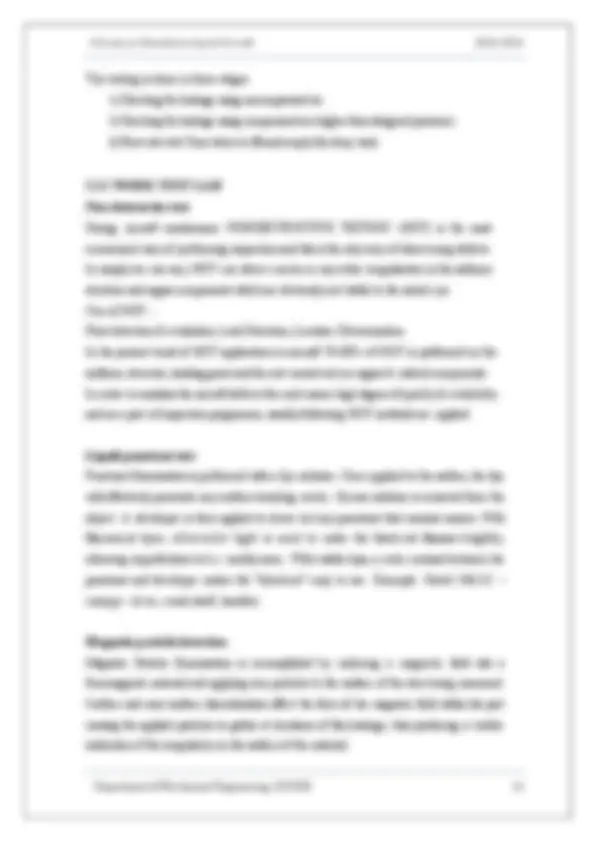
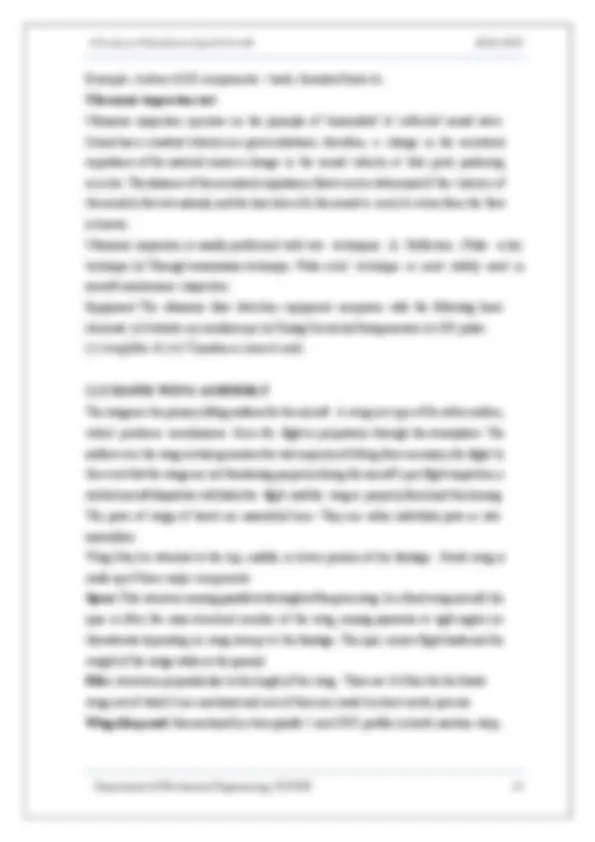
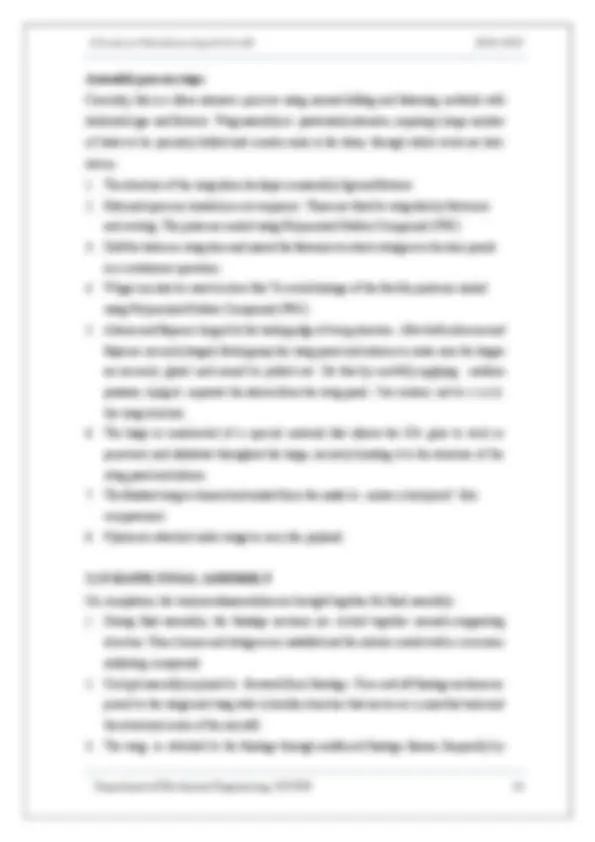
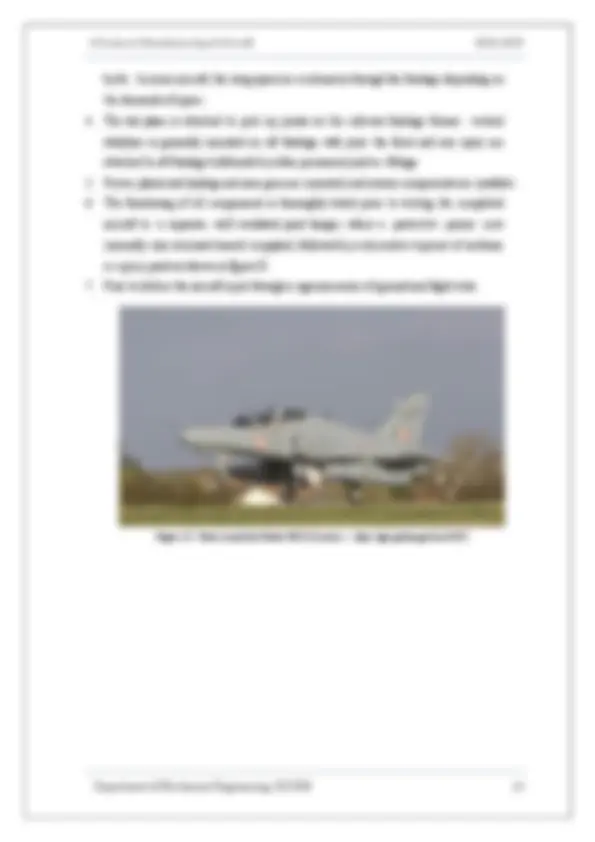
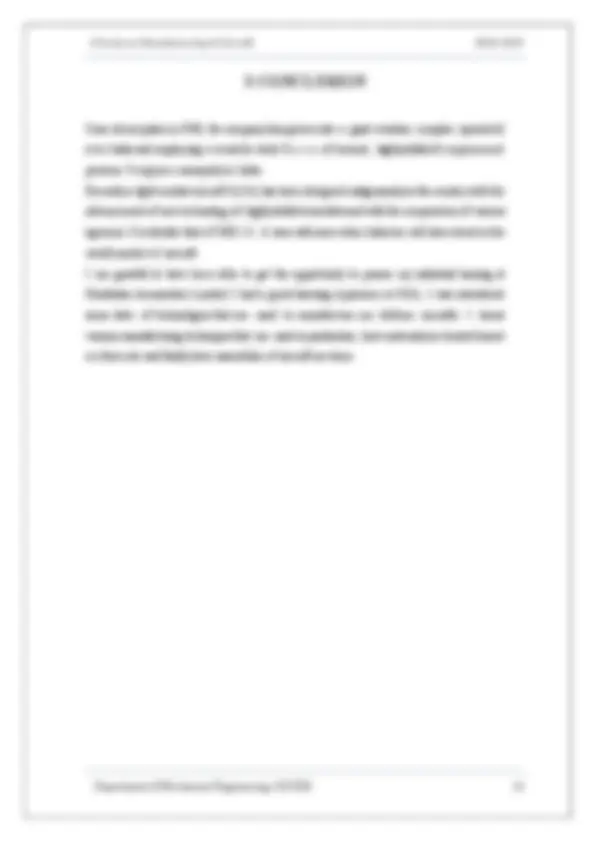
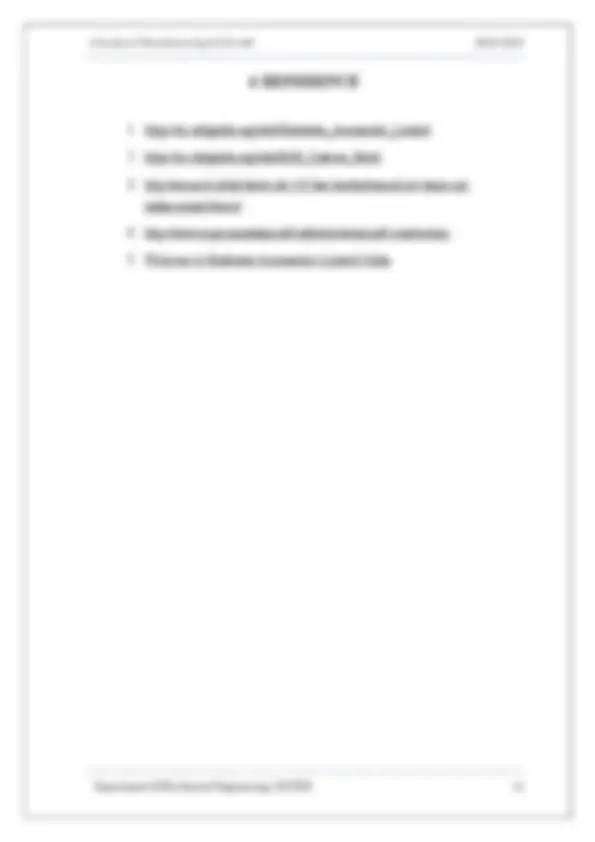
Study with the several resources on Docsity
Earn points by helping other students or get them with a premium plan
Prepare for your exams
Study with the several resources on Docsity
Earn points to download
Earn points by helping other students or get them with a premium plan
Community
Ask the community for help and clear up your study doubts
Discover the best universities in your country according to Docsity users
Free resources
Download our free guides on studying techniques, anxiety management strategies, and thesis advice from Docsity tutors
hal observations are been noted fro better speciments
Typology: Papers
1 / 37
This page cannot be seen from the preview
Don't miss anything!
i
# 15, Mallasandra, Off. Kanakapura Road, Bengaluru-
i
This is to certify that the internship work entitled “ A Study on Manufacturing of Aircraft ” is a bonafide work carried out by RAHUL J 1KG15ME
In partial fulfilment for the award of Bachelor of Engineering in Mechanical Engineering of the Visvesvaraya Technological University, Belagavi during the year 2018-19. It is certified that all corrections/suggestions indicated for Internal Assessment have been incorporated in the Report deposited in the departmental library. The internship report has been approved as it satisfies the academic requirements in respect of internship work prescribed for the said Degree.
.. Signature of the Guide Signature of the Guide (External) Mr. VIJAY CHANDAN Mrs. B Arockia Jyothi Asst. Professor Senior Manager (HR) Dept. of Mechanical Engg. Aircraft Division HAL KSSEM, Bengaluru – 109 Bangalore – 560 017 .. Signature of the HOD Signature of the Principal Prof. Balaji. B Dr. K. Ramanarasimha Assoc. Professor and Head Principal/Director Dept. of Mechanical Engg. KSSEM, Bengaluru – KSSEM, Bengaluru – 109
External Viva Name of the Examiners Signature with date
iii
The successful completion of any task would be incomplete without the mention of the people, whose constant guidance and encouragement crowned our efforts with success. I consider it as a privilege to express my gratitude and respect to all those who guided me in the successful completion of this project. First of all, I am thankful to our college K S SCHOOL OF ENGINEERING AND MANAGEMENT for providing support guidance and a platform to work. I express my gratitude to AIRCRAFT DIVISION HAL for providing opportunity and guidance to carry out internship work. I take this opportunity to express my deep regards to Dr. K. Ramanarasimha , Principal/Director, K S School of Engineering and Management for providing an opportunity to do this Project Work as a part of my curriculum in the partial fulfilment of the degree course. I express my gratitude to Prof. Balaji. B , HOD, Department of Mechanical Engineering, K.S. School of Engineering and Management for providing valuable insights, making the resources available at right time and all the encouragement for the completion of my project. I owe my profound gratitude to our project guide Mr. Vijay Chandan , Asst. Professor, Department of Mechanical Engineering, K S School of Engineering and Management, Bengaluru & Mrs. Arockia Jothi , Senior Manager (HR), AIRCRAFT DIVISION HAL BANGALORE, who took keen interest in the work and guided all along and for providing all the necessary information. I extend my profound gratitude to my internship coordinator Mr. Prabhu K S , Assistant Professor, Department of Mechanical Engineering, K. S. School of Engineering and Management, who took keen interest in the work and guided all along and for providing all the necessary information.
I also wish to thank all the staff of Department Mechanical Engineering for providing all the support whenever needed. I would like to thank my parents for supporting and helping in the completion of the project work. Last but not the least I would like to thank all my friends without whose support and co-operation the completion of project would not have been possible.
Hindustan Aeronautic Limited [HAL] a premier Aerospace Company in Asia is engaged in design, development and manufacture of military and civil aircraft for over 75 years. The product r a n g e covers basic piston engine trainer aircraft to helicopters to sophisticated state of the art deep penetration strike aircraft. Hindustan Aeronautic Limited is an organization where integrated air borne weapons platforms are conceived, developed, manufactured and serviced. It is one of the few corporate giants in Asia whose capabilities span the entire range of activities from product conception to after sale support. HAL is also involved in the manufacture and assembly of structures required for India's space programs.
The Company which had its origin as the Hindustan Aircraft Company was incorporated on 23 Dec 1940 at Bangalore by Shri Walchand Hirachand a farsighted visionary in association with the Government of Mysore with an Authorized Capital of Rs.4crores (Paid up capital Rs.40 lakhs) and with the aim of manufacturing aircraft in India. In March 1941, the Government of India became one of the shareholders in the Company holding 1/3 of its paid- up capital and subsequently took over its management in 1942. Hindustan Aeronautics Limited (HAL) came into existence on 1st October 1964. The Company was formed by the merger of Hindustan Aircraft Limited with Aeronautics India Limited and Aircraft Manufacturing Depot, Kanpur. HAL is a fully owned Government of India undertaking under the administrative control of Ministry of Defense, Department of Defense Production. H.A.L is the largest Public Sector Unit (PSU) under the department of Defense production and is a Navaratna Company. The Company takes up maintenance and overhaul services to cover the life cycle requirement of all the old and new products. Presently, 13 types of aircraft/ helicopters and 17 types of engines are being overhauled. In addition, facilities exist for repair/ overhaul of various accessories and avionics fitted on aircraft of Russian, Western and Indigenous designs. HAL is currently meeting the requirements of structures for aerospace launch vehicles and satellites of ISRO t h r o u g h its dedicated Aerospace Division. Infrastructure has also been set up to undertake completed assembly of the strap-on L-40 stage booster. Structures for GSLV Mk III have been produced. HAL has also contributed to Mars mission by supplying
riveted structural assemblies and welded propellant tankages for the Polar Satellite Launch Vehicle (PSLV-C25). Today, HAL has 19 Production Units and 9 Research and Design Centers in 7 locations in India. The Company has impressive product track record-12 types of aircraft manufactured with in-house R&D and 14 types produced under license. HAL has manufactured 3550 aircraft (which includes 11 types designed indigenously), 3600 engines and overhauled over 8150 aircraft and 27300 engines. HAL has been successful in numerous R & D programs developed for both defense and Civil Aviation sectors. HAL has made substantial progress in its current projects:
There are several divisions under Hindustan Aeronautical Limited. They are as under: Bangalore complex
Aircraft Division was established in the year 1940. Since inception, the Division has manufactured a variety of Aircraft both license as well as indigenously designed and developed. The Division is equipped with modern infrastructure in Plant and Equipment like CAD-CAM Manufacturing Engineering, Quality Assurance and Customer support System with 2179 highly skilled personnel including more than 511 officers working in a covered area of 2,25,000sq.m. The Division has so far manufactured over 2010 aircrafts of various types. With experience and capabilities built over past seven decades, the Aircraft Division is bidding for substantial share in the International Aeronautical market. Apart from 1st of Hawk Mk 132 Aircraft (66 Nos.), the division has signed contract with Indian Air Force and Indian Navy to supply additional 57 Hawk Aircraft (40 Hawk for Indian Airforce and 17 Hawk for Indian Navy). Components manufactured
Major customers DEFENCE & SPACE CIVIL Indian Air Force Border Security Force Indian Army Govt. of Karnataka Indian Navy Govt. of Jharkhand Indian Coast Guard Govt. of Maharashtra Indian Space Research Organization Geological Survey of India Defense Research & Development Organization
Oil & Natural Gas Cooperation of India Ordnance Factory Board Bharat Heavy Electricals Ltd.
Minor customers
Design and planning, IMM, MSD and by Considering the capacity of the machining equipment and the technology available the methods department.
A Sample ROUTE BOOK Work order Part number Quantity Department
Part name: Bolt Outsource details
Next assembly part number
Raw material detail Alternate material Manufacturing inspection Metal code: Spec: 35NCD16UTS-1230/1380MPa
Batch no-
Nom: 25mm diameter steel rod Size:
inspection Sign
Operation no/dept Tool no/Operation description quantity shop inspection Inspect material (35 NCD16 UTS-1230/ MPa) HRC: 38.3 – 42. Actual hardness HRC: 40 – 41 Caution: material is prone to corrosion, protect with oil between operations Machining operations- Tools Turning, facing, step turning Inspection
Grind the shank to required diameter (cadmium plating allowance added on shank diameter) Thread rolling Thread rolling Chamfer for Thread rolling De-burring, remove sharp edges
Stress relieve at 190^0 ±10^0 C, 1-3 hrs. Date: Time in: Time out: Inspection Vapor degrease – cadmium plating – De- embrittlement at 1900 C Inspection Magnetic particle inspection and demagnetize Degrease, clean thoroughly, ultrasonic clean Dichromate passivation Inspection and issue tag Stock in stores in polythene bag Serial no: date:
Program engineering Supervising project engineering related tasks including planning, control & troubleshooting for achieving the planned periodic schedules and process control. Coordinating with the other departments for smooth functioning and accomplishing production as per customer’s requirement & organizational guideline.
Functions
Milling machines
CNC machines
HAL’s cost-effective and widespread skills are available to the International Aerospace Community. HAL has proven capabilities and offers collaborative arrangements in the areas of manufacturing of machine components, design and development tasks (Structural analysis, 3D modeling and testing). Parts manufactured in export shop are assembled in this shop with help of nut &bolt, rivets & PRC (used to avoid leakage). The current undergoing projects are: -
Steps for airbus a320 passenger door assembly
BOEING 777 uplock box assembly Uplock box assembly is attached to main landing gear wheel well and is used to secure the main landing gear of being 777 aircraft in closed position. Components of box include web assemblies, stiffness, fittings and brackets made out of aluminum sheets, extrusions and plates. Landing gear hook and latch into the up-lock box when landing gear is up and door are closed for flight. It carries weight of the closed landing gear door during flight. In addition to supporting the closed gear door, the up lock also has two emergency functions: -
Figure 2: -Boeing 777 uplock Assembly (source: -https://goo.gl/images/Ey27UA)
Numerical control (NC) is the automation of machine tools that are operated by precisely programmed commands encoded on a storage medium, as opposed to controlled manually via hand wheels or levers, or mechanically automated via cams alone. Most NC today is computer numerical control (CNC), in which computers play an integral part of the control. Machining operations like drilling, milling is done using NC programing as shown in figure- 3.NC is not run by codes but instructions are entered by manual.