
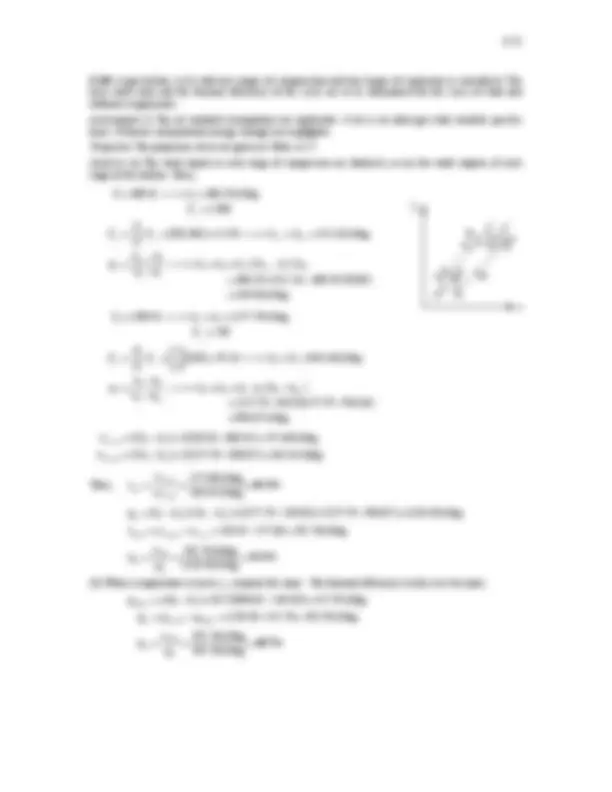
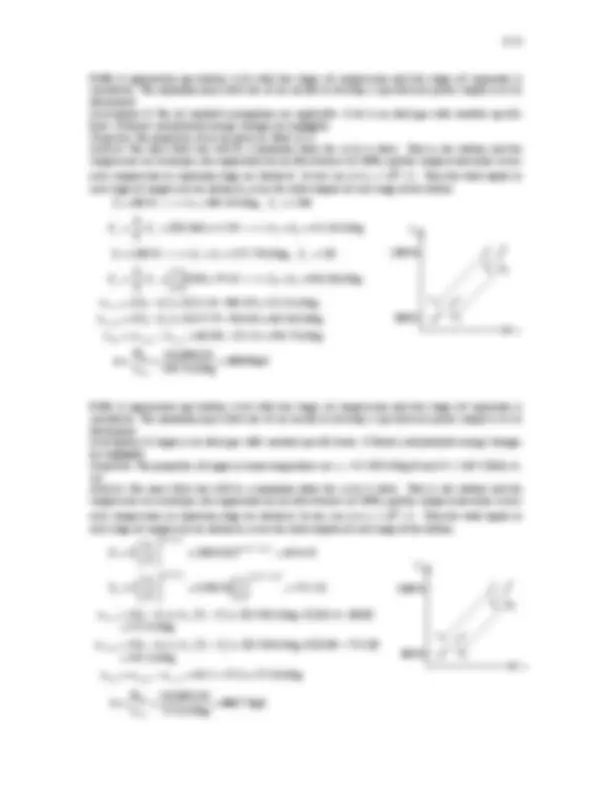
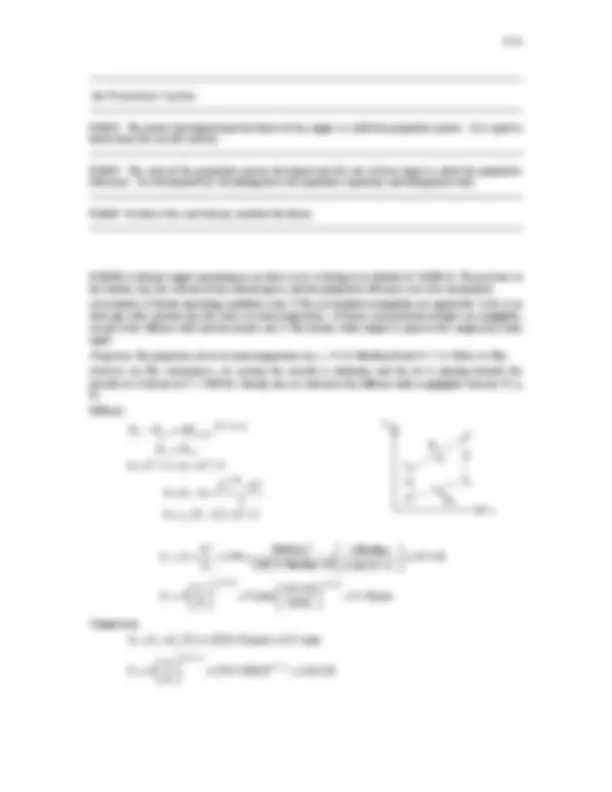
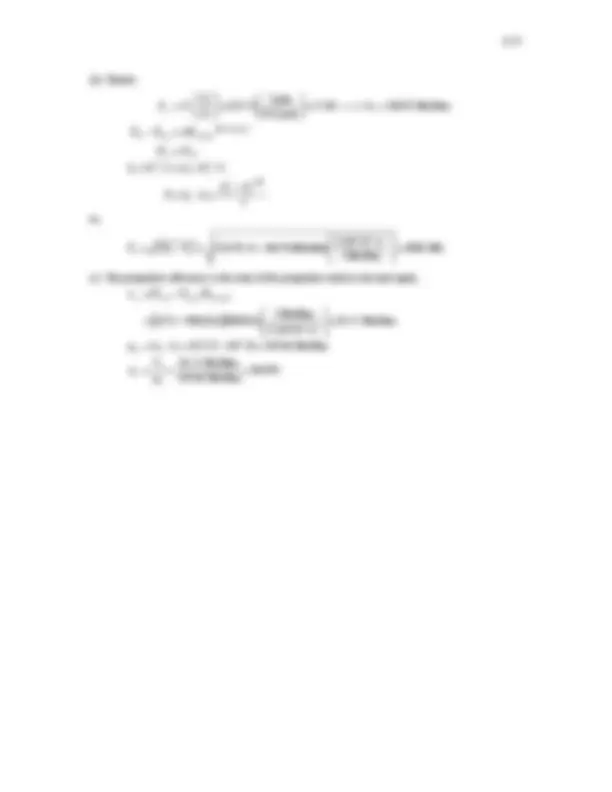
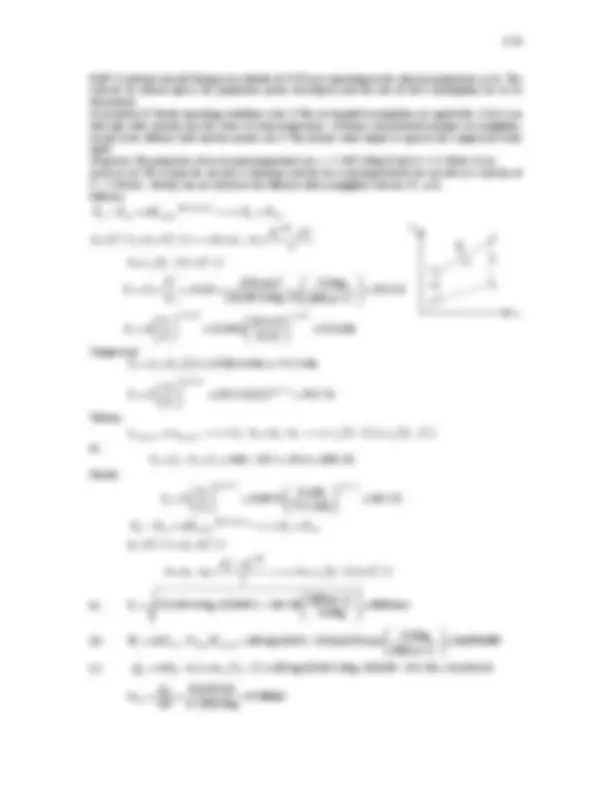
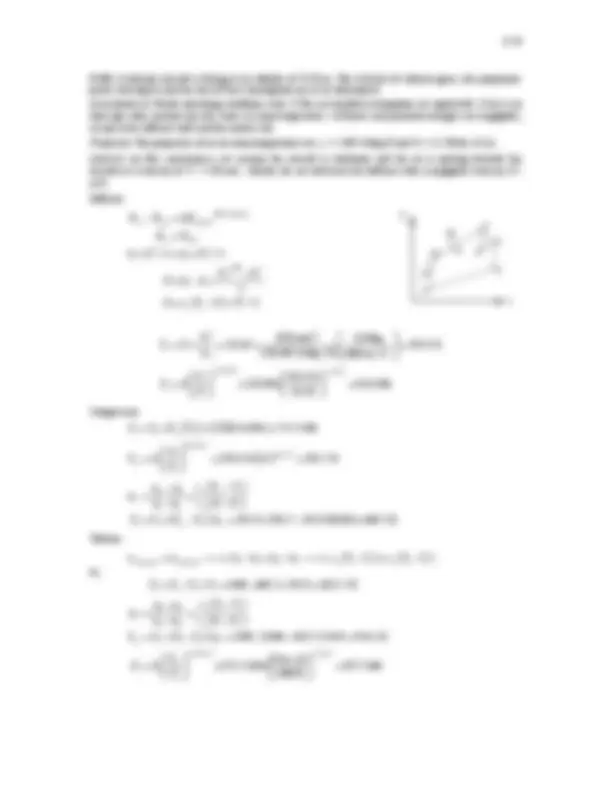

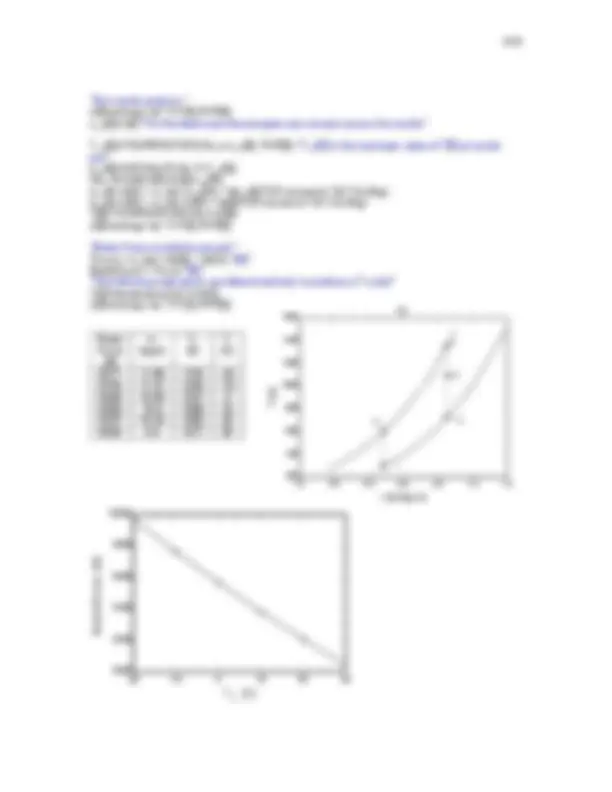
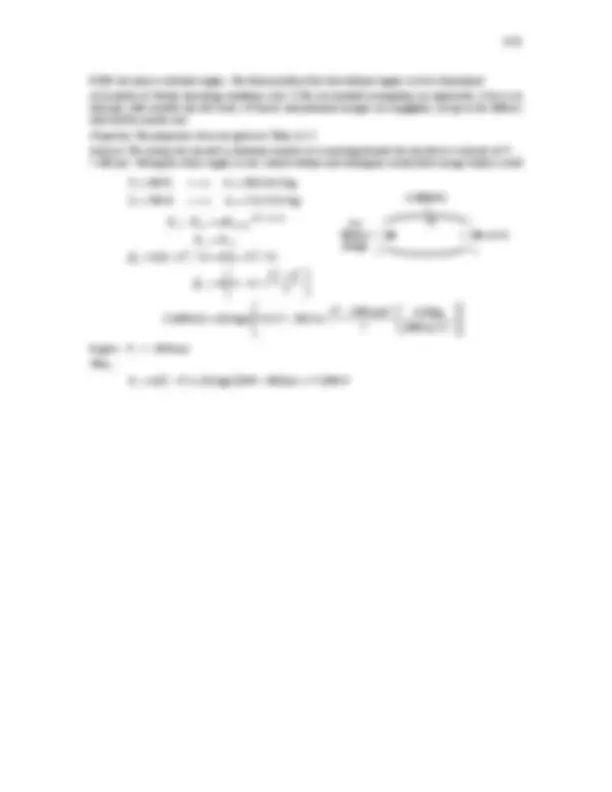
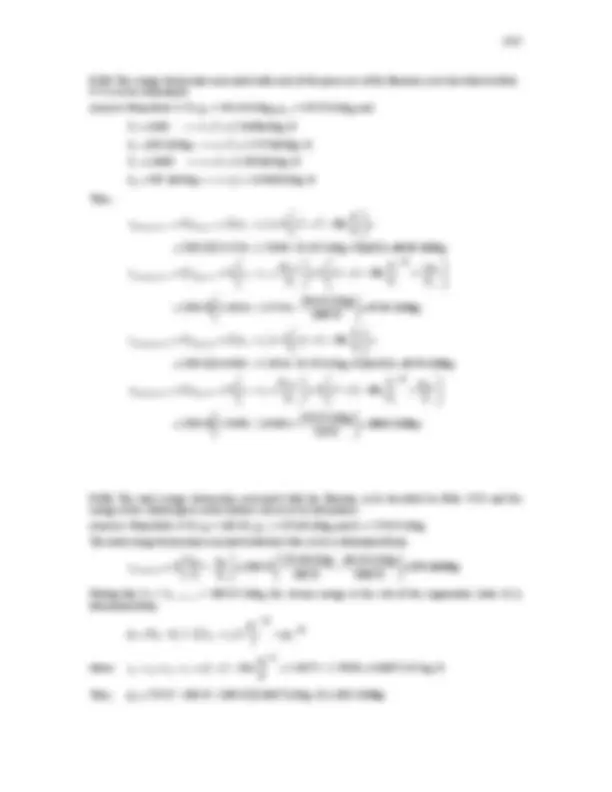
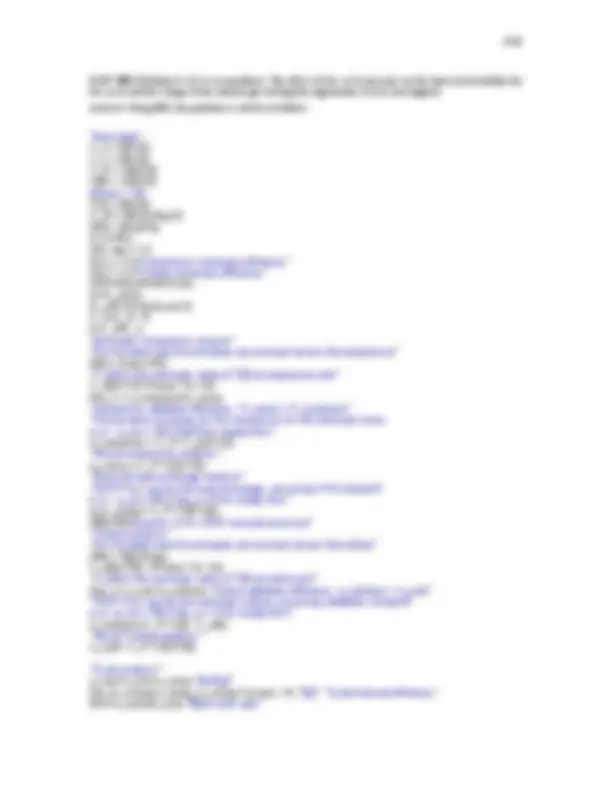
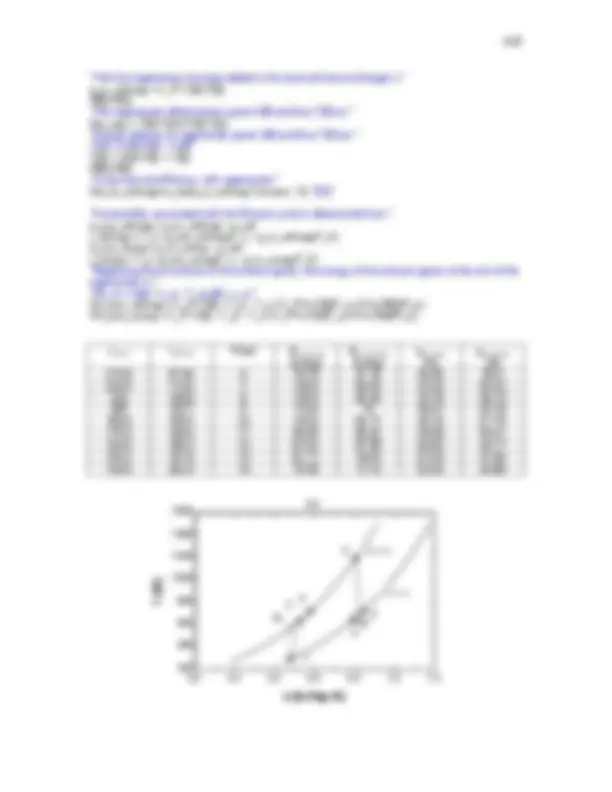
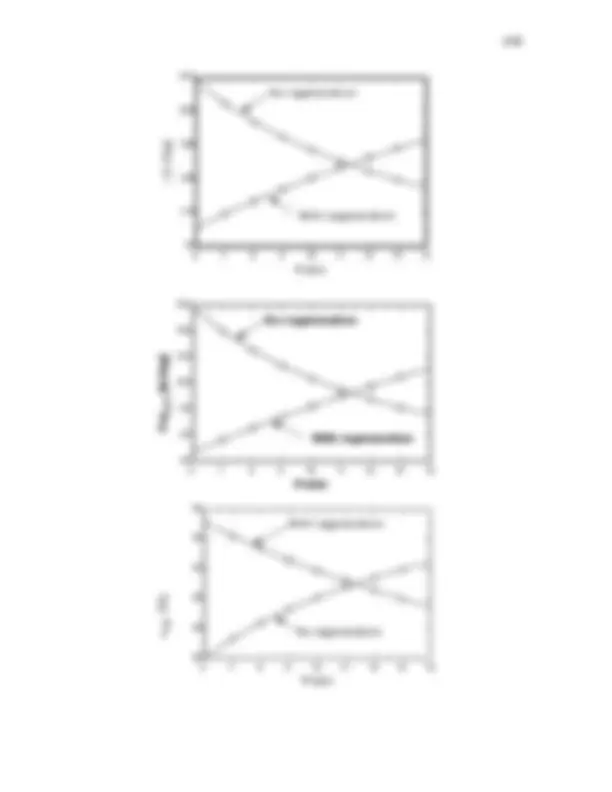
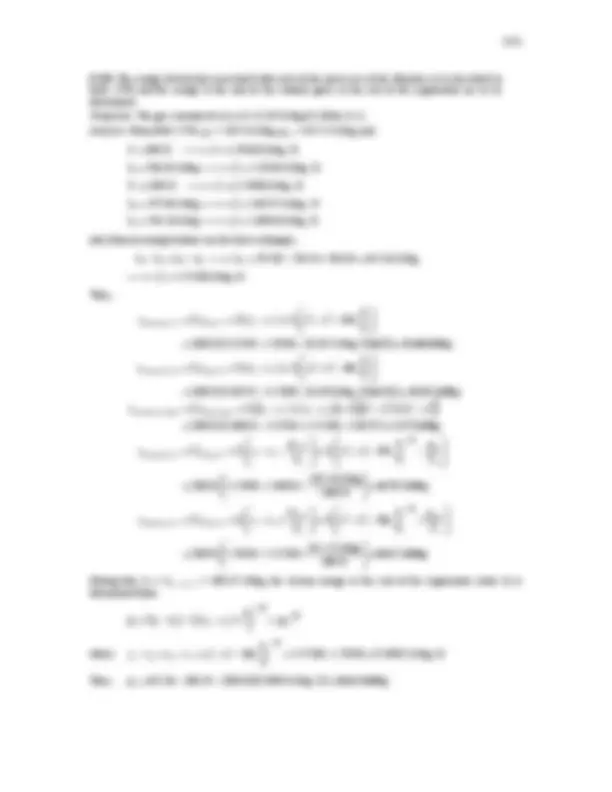
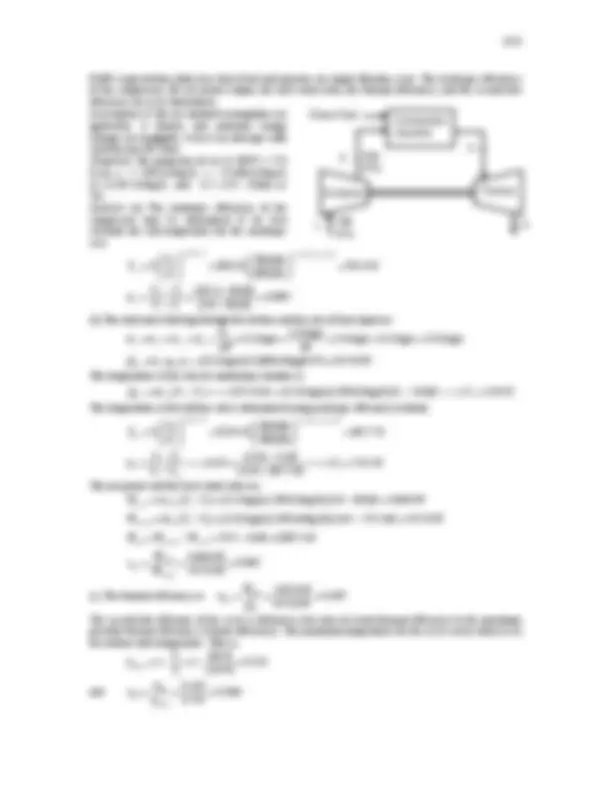
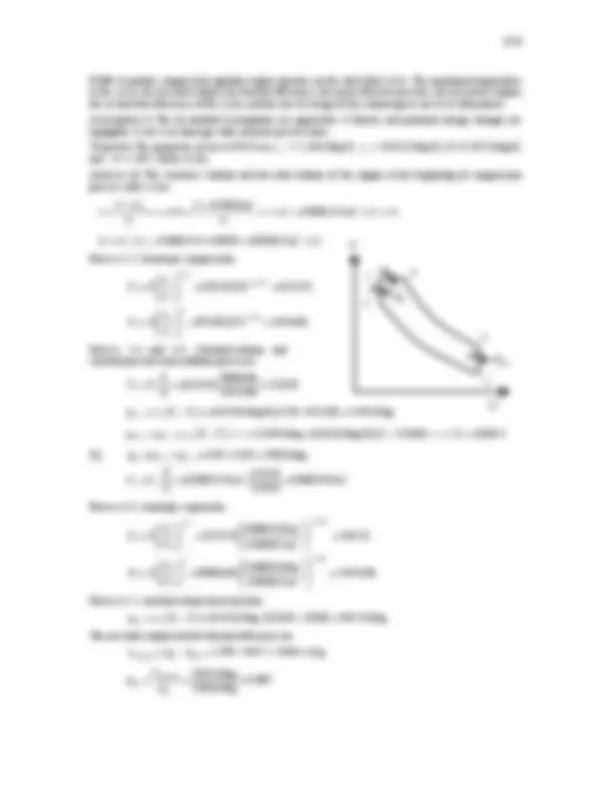
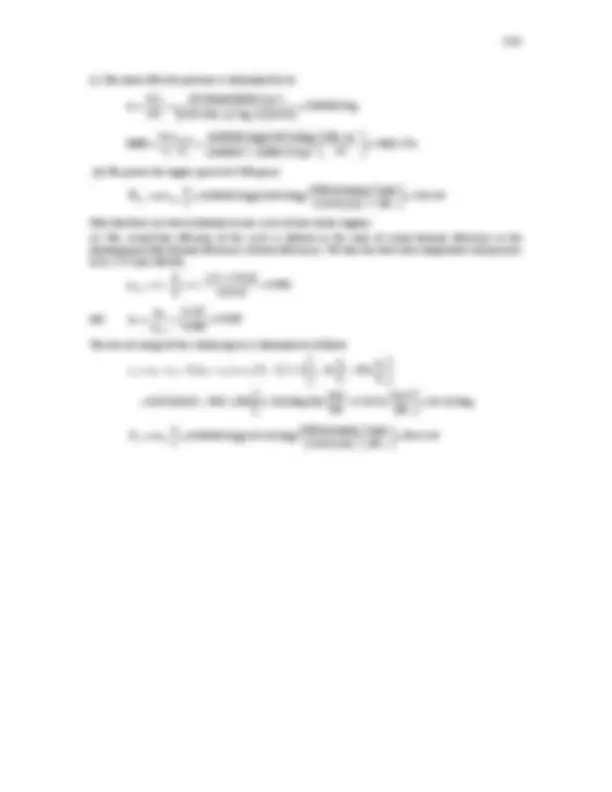
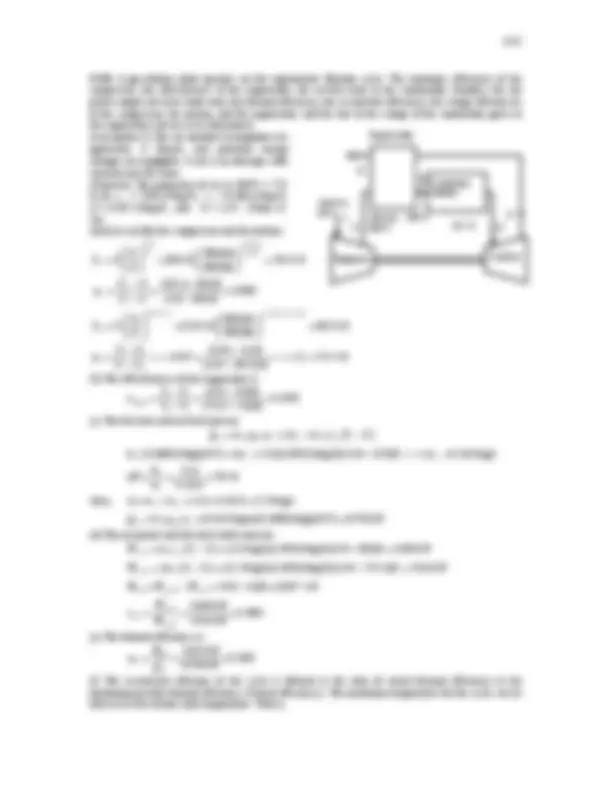
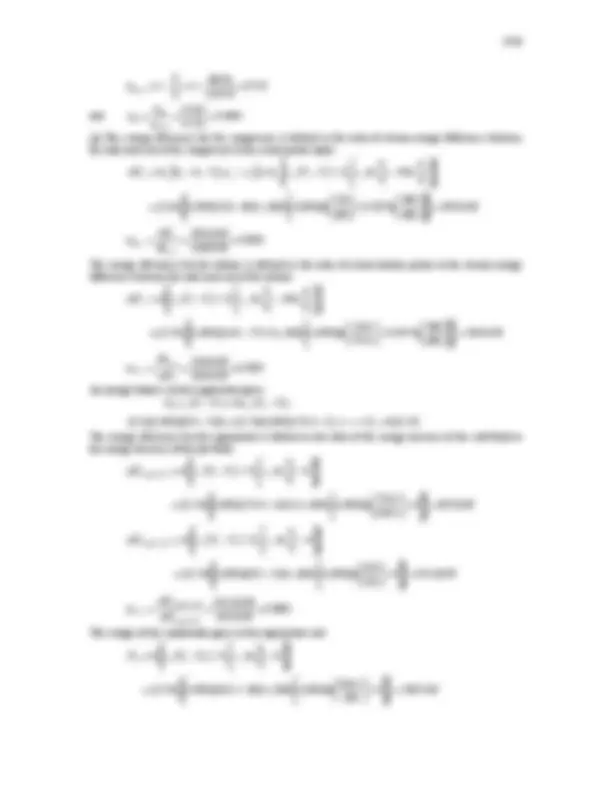
Study with the several resources on Docsity
Earn points by helping other students or get them with a premium plan
Prepare for your exams
Study with the several resources on Docsity
Earn points to download
Earn points by helping other students or get them with a premium plan
Community
Ask the community for help and clear up your study doubts
Discover the best universities in your country according to Docsity users
Free resources
Download our free guides on studying techniques, anxiety management strategies, and thesis advice from Docsity tutors
Full notes for Thermal engineering for all exams questions. And important question
Typology: Exams
1 / 27
This page cannot be seen from the preview
Don't miss anything!
Brayton Cycle with Intercooling, Reheating, and Regeneration
9-101C As the number of compression and expansion stages are increased and regeneration is employed,
the ideal Brayton cycle will approach the Ericsson cycle.
9-102C (a) decrease, (b) decrease, and (c) decrease.
9-103C (a) increase, (b) decrease, and (c) decrease.
9-104C (a) increase, (b) decrease, (c) decrease, and (d) increase.
9-105C (a) increase, (b) decrease, (c) increase, and (d) decrease.
9-106C Because the steady-flow work is proportional to the specific volume of the gas. Intercooling
decreases the average specific volume of the gas during compression, and thus the compressor work.
Reheating increases the average specific volume of the gas, and thus the turbine work output.
9-107C (c) The Carnot (or Ericsson) cycle efficiency.
9-108 An ideal gas-turbine cycle with two stages of compression and two stages of expansion is
considered. The back work ratio and the thermal efficiency of the cycle are to be determined for the cases
of with and without a regenerator.
Assumptions 1 The air standard assumptions are applicable. 2 Air is an ideal gas with variable specific
heats. 3 Kinetic and potential energy changes are negligible.
Properties The properties of air are given in Table A-17.
Analysis ( a ) The work inputs to each stage of compressor are identical, so are the work outputs of each
stage of the turbine since this is an ideal cycle. Then,
2 2411. 26 300. 19 22 2.14kJ/kg
238 79. 33 946.36kJ/kg 3
12 77.79kJ/kg 1200 K
300.19kJ/kg 300 K
T,out 5 6
C,in 2 1
6 8 5
6
5 7 5
2 4 1
2
1 1
6 5
5
2 1
1
w h h
w h h
P h h P
h h T
P h h P
h T
r r
r
r r
r
2
9
10
7
6 8
300 K
1200 K (^) qin
5
1
4
3
T
Thus, = = = 33.5% 662.86kJ/kg
222.14kJ/kg
T,out
C,in bw w
w r
1197.96 kJ/kg
440.72kJ/kg
86 222.14 440.72kJ/kg
79 411. 26 1277. 79 946. 36 1197.96kJ/kg
in
net th
net T,out C,in
in 5 4 7 6
q
w
w w w
q h h h h
( b ) When a regenerator is used, rbw remains the same. The thermal efficiency in this case becomes
796.63 kJ/kg
440.72kJ/kg
96 401. 33 796.63kJ/kg
75 946. 36 411. 26 401. 33 kJ/kg
in
net th
in in,old regen
regen 8 4
q
w
q q q
q h h
9-110 A regenerative gas-turbine cycle with two stages of compression and two stages of expansion is
considered. The minimum mass flow rate of air needed to develop a specified net power output is to be
determined.
Assumptions 1 The air standard assumptions are applicable. 2 Air is an ideal gas with variable specific
heats. 3 Kinetic and potential energy changes are negligible.
Properties The properties of air are given in Table A-17.
Analysis The mass flow rate will be a minimum when the cycle is ideal. That is, the turbine and the
compressors are isentropic, the regenerator has an effectiveness of 100%, and the compression ratios across
each compression or expansion stage are identical. In our case it is rp = 9 = 3. Then the work inputs to
each stage of compressor are identical, so are the work outputs of each stage of the turbine.
= = = 249.6 kg/s
440.72 kJ/kg
110,000kJ/s
2 2 1277.79 946.36 662.86kJ/kg
2 2411. 26 300. 19 222.14kJ/kg
238 79. 33 94 6.36kJ/kg 3
1200 K 1277.79kJ/kg, 238
300 K 3 00.19kJ/kg, 1. 386
net
net
net T,out C,in
T,out 5 6
C,in 2 1
6 8 5
6
5 5 7
2 4 1
2
1 1
6 5
5
2 1
1
w
m
w w w
w h h
w h h
P h h P
T h h P
P h h P
T h P
r r
r
r r
r
2
7
6 8
300 K
1200 K
5
1
4
3
T
9-111 A regenerative gas-turbine cycle with two stages of compression and two stages of expansion is
considered. The minimum mass flow rate of air needed to develop a specified net power output is to be
determined.
Assumptions 1 Argon is an ideal gas with constant specific heats. 2 Kinetic and potential energy changes
are negligible.
Properties The properties of argon at room temperature are c p = 0.5203 kJ/kg.K and k = 1.667 (Table A-
2a).
Analysis The mass flow rate will be a minimum when the cycle is ideal. That is, the turbine and the
compressors are isentropic, the regenerator has an effectiveness of 100%, and the compression ratios across
each compression or expansion stage are identical. In our case it is rp = 9 = 3. Then the work inputs to
each stage of compressor are identical, so are the work outputs of each stage of the turbine.
( )
( )
= = = 404.7 kg/s
−
−
271.8 kJ/kg
110,000kJ/s
444.1kJ/kg
2 2 2 0.5203kJ/kgK 1200 773.2K
172.3kJ/kg
2 2 2 0.5203kJ/kgK 465.6 300 K
net
net
net T,out C,in
T,out 5 6 5 6
C,in 2 1 2 1
1 / 0.667/1.66 7
5
6 6 5
0.667/1.66 7
1 /
1
2 2 1
w
m
w w w
w h h c T T
w h h c T T
p
p
k k
k k
2
7
6 8
300 K
1200 K
5
1
4
3
T
Jet-Propulsion Cycles
9-112C The power developed from the thrust of the engine is called the propulsive power. It is equal to
thrust times the aircraft velocity.
9-113C The ratio of the propulsive power developed and the rate of heat input is called the propulsive
efficiency. It is determined by calculating these two quantities separately, and taking their ratio.
9-114C It reduces the exit velocity, and thus the thrust.
9-115E A turbojet engine operating on an ideal cycle is flying at an altitude of 20,000 ft. The pressure at
the turbine exit, the velocity of the exhaust gases, and the propulsive efficiency are to be determined.
Assumptions 1 Steady operating conditions exist. 2 The air standard assumptions are applicable. 3 Air is an
ideal gas with constant specific heats at room temperature. 4 Kinetic and potential energies are negligible,
except at the diffuser inlet and the nozzle exit. 5 The turbine work output is equal to the compressor work
input.
Properties The properties of air at room temperature are c p = 0.24 Btu/lbm.R and k = 1.4 (Table A-2Ea).
Analysis ( a ) For convenience, we assume the aircraft is stationary and the air is moving towards the
aircraft at a velocity of V 1 = 900 ft/s. Ideally, the air will leave the diffuser with a negligible velocity ( V 2 ≅
0).
Diffuser:
( )
7 psia
25,037ft /s
1 Btu/lbm
2 0.24Btu/lbmR
900 ft/s 470 2
/ (^1) 1.4/0.
1
2 2 1
2 2
2 2 1 2 1
2 2 1 1
2 1
2 0 2 2 1
2 2 2
2 1 1
in out
0 (steady) in out system
k k −
p
p
c
c T T V
h h
h V h V
©
©
6
qout
5
qin
3
4
2
1
Compressor:
( )
13 11.19psia 145.5psia
0.4/1.
1 /
2
3 3 2
3 4 2
k − k
p
P P r P
9-116E A turbojet engine operating on an ideal cycle is flying at an altitude of 20,000 ft. The pressure at
the turbine exit, the velocity of the exhaust gases, and the propulsive efficiency are to be determined.
Assumptions 1 Steady operating conditions exist. 2 The air standard assumptions are applicable. 3 Air is an
ideal gas with variable specific heats. 4 Kinetic and potential energies are negligible, except at the diffuser
inlet and the nozzle exit. 5 The turbine work output is equal to the compressor work input.
Properties The properties of air are given in Table A-17E.
Analysis (a) For convenience, we assume the aircraft is stationary and the air is moving towards the aircraft
at a velocity of V 1 = 900 ft/s. Ideally, the air will leave the diffuser with a negligible velocity ( V (^) 2 ≅ 0).
Diffuser:
470 R 112.20Btu/lbm
1
1 1
=
P r
T h
T
7 psia
128.48Btu/lbm 1. 3698 25,037ft /s
1 Btu/lbm
900 ft/s
1
2
2
2 1
2 2 r
2 2 1 2 1
2 1
2 0 2 2 1
2 2 2
2 1 1
in out
0 (steady) in out system
r
r
h h
h h
h V h V
©
©
6
qout
5
qin
3
4
2
1
Compressor:
13 11.22psia 145.8psia
3 2
3
3 4 2
3 2
P h P
P P r P
r r
p
Turbine: T
6
22 Btu/lbm 2400 R
4
4 4 =
Pr
h
3 2 4 5
comp,in turb,out
h h h h
w w
or,
145.8psia
4
5
5
5 4
5 4 3 2
r
r
r
h h h h P
( b ) Nozzle:
17.66 266.93Btu/lbm 56.6psia
7 psia ( 142. 7 )
2 0 5
2 6 6 5
2 6 6
2 5 5
in out
0 (steady) in out system
6 5
6 6 5
©
©
h h
h V h V
h P
Pr Pr
or,
1 Btu/lbm
25,037ft /s 2 2 ( 478. 14 266. 93 )Btu/lbm
2 2
V 6 h 5 h 6
( c ) The propulsive efficiency is the ratio of the propulsive work to the heat input,
349.66 Btu/lbm
84.55Btu/lbm
84.55Btu/lbm 25,037ft /s
1 Btu/lbm (3252 900)ft/s)(900ft/s)
in
4 3
2 2
exit inlet aircraft
q
w
q h h
w V V V
p p
in
p
9-118 A turbojet aircraft is flying at an altitude of 9150 m. The velocity of exhaust gases, the propulsive
power developed, and the rate of fuel consumption are to be determined.
Assumptions 1 Steady operating conditions exist. 2 The air standard assumptions are applicable. 3 Air is an
ideal gas with constant specific heats at room temperature. 4 Kinetic and potential energies are negligible,
except at the diffuser inlet and the nozzle exit.
Properties The properties of air at room temperature are c p = 1.005 kJ/kg.K and k = 1.4 (Table A-2a).
Analysis ( a ) For convenience, we assume the aircraft is stationary and the air is moving towards the
aircraft at a velocity of V (^) 1 = 320 m/s. Ideally, the air will leave the diffuser with a negligible velocity ( V (^) 2
≅ 0).
Diffuser:
( )
32 kPa
1000 m/s
1 kJ/kg
2 1.005kJ/kgK
320 m/s 241 K 2
/ (^1) 1.4/0.
1
2 2 1
2 2
2 2 1 2 1
2 2 1 1
2 1
2 0 2 2 1
2 2 2
2 1 1
in out
0 (steady) in out system
k k −
p
p
c
c T T V
h h
h V h V
©
©
5
6
5s
Qi
·
3
4
2
1
Compressor:
( )
12 62.6kPa 751.2kPa
0.4/1.
1 /
2
3 3 2
3 4 2
k − k
s
p
P P r P
3 2
3 2
3 2
3 2
s C
p
s p s C
c T T
c T T
h h
h h
Turbine:
or,
comp,in turb,out 3 2 4 5 3 2 4 5
w w h h h h cpT T cpT T
( )
751.2kPa
/ 1 1.4/0.
4
5 5 4
5 4 4 5
4 5
4 5
4 5
4 5
k k − s
s T
p s
p
s
T
c T T
c T T
h h
h h
Nozzle:
( )
197.7kPa
32 kPa 1022.7K
2 6 5 6
2 0 5
2 6 6 5
2 6 6
2 5 5
in out
0 (steady) in out system
1 / 0.4/1.
5
6 6 5
c T T V
h h
h V h V
p
k k
−
©
©
or,
1 kJ/kg
1000 m /s 2 1.005kJ/kgK 1022.7 607.8K
2 2
V 6
= 11,390 kW
2 2
exit inlet aircraft
1000 m/s
1 kJ/kg 60 kg/s913.2 320 m/s 320 m/s
W & (^) p m & V V V
= = = 1.03 kg/s
42,700 kJ/kg
44,067kJ/s
60 kg/s1.005kJ/kgK 1400 669.2K 44,067kJ/s
in fuel
in 4 3 4 3
m
Q mh h mcpT T
9-120 EES Problem 9-119 is reconsidered. The effect of compressor inlet temperature on the force that
must be applied to the brakes to hold the plane stationary is to be investigated.
Analysis Using EES, the problem is solved as follows:
P_ratio = 12
T_1 = 27 [C]
T[1] = T_1+273 "[K]"
P[1]= 95 [kPa]
P[5]=P[1]
Vel[1]=0 [m/s]
V_dot[1] = 9.063 [m^3/s]
HV_fuel = 42700 [kJ/kg]
m_dot_fuel = 0.2 [kg/s]
Eta_c = 1.
Eta_t = 1.
Eta_N = 1.
"Inlet conditions"
h[1]=ENTHALPY(Air,T=T[1])
s[1]=ENTROPY(Air,T=T[1],P=P[1])
v[1]=volume(Air,T=T[1],P=P[1])
m_dot = V_dot[1]/v[1]
"Compressor anaysis"
s_s[2]=s[1] "For the ideal case the entropies are constant across the compressor"
P_ratio=P[2]/P[1]"Definition of pressure ratio - to find P[2]"
T_s[2]=TEMPERATURE(Air,s=s_s[2],P=P[2]) "T_s[2] is the isentropic value of T[2] at
compressor exit"
h_s[2]=ENTHALPY(Air,T=T_s[2])
Eta_c =(h_s[2]-h[1])/(h[2]-h[1]) "Compressor adiabatic efficiency; Eta_c =
W_dot_c_ideal/W_dot_c_actual. "
m_doth[1] +W_dot_c=m_doth[2] "SSSF First Law for the actual compressor, assuming:
adiabatic, ke=pe=0"
"External heat exchanger analysis"
P[3]=P[2]"process 2-3 is SSSF constant pressure"
h[3]=ENTHALPY(Air,T=T[3])
Q_dot_in = m_dot_fuel*HV_fuel
m_doth[2] + Q_dot_in= m_doth[3]"SSSF First Law for the heat exchanger, assuming W=0,
ke=pe=0"
"Turbine analysis"
s[3]=ENTROPY(Air,T=T[3],P=P[3])
s_s[4]=s[3] "For the ideal case the entropies are constant across the turbine"
{P_ratio= P[3] /P[4]}
T_s[4]=TEMPERATURE(Air,h=h_s[4]) "Ts[4] is the isentropic value of T[4] at turbine exit"
{h_s[4]=ENTHALPY(Air,T=T_s[4])} "Eta_t = W_dot_t /Wts_dot turbine adiabatic efficiency,
Wts_dot > W_dot_t"
Eta_t=(h[3]-h[4])/(h[3]-h_s[4])
m_doth[3] = W_dot_t + m_doth[4] "SSSF First Law for the actual compressor, assuming:
adiabatic, ke=pe=0"
T[4]=TEMPERATURE(Air,h=h[4])
P[4]=pressure(Air,s=s_s[4],h=h_s[4])
"Cycle analysis"
W_dot_net=W_dot_t-W_dot_c"Definition of the net cycle work, kW"
W_dot_net = 0 [kW]
"Exit nozzle analysis:"
s[4]=entropy('air',T=T[4],P=P[4])
s_s[5]=s[4] "For the ideal case the entropies are constant across the nozzle"
T_s[5]=TEMPERATURE(Air,s=s_s[5], P=P[5]) "T_s[5] is the isentropic value of T[5] at nozzle
exit"
h_s[5]=ENTHALPY(Air,T=T_s[5])
Eta_N=(h[4]-h[5])/(h[4]-h_s[5])
m_doth[4] = m_dot(h_s[5] + Vel_s[5]^2/2*convert(m^2/s^2,kJ/kg))
m_doth[4] = m_dot(h[5] + Vel[5]^2/2*convert(m^2/s^2,kJ/kg))
T[5]=TEMPERATURE(Air,h=h[5])
s[5]=entropy('air',T=T[5],P=P[5])
"Brake Force to hold the aircraft:"
Thrust = m_dot*(Vel[5] - Vel[1]) "[N]"
BrakeForce = Thrust "[N]"
"The following state points are determined only to produce a T-s plot"
T[2]=temperature('air',h=h[2])
s[2]=entropy('air',T=T[2],P=P[2])
Brake
Force
[N]
m
[kg/s]
4.5 5.0 5.5 6.0 6.5 7.0 7.
200
400
600
800
1000
1200
1400
1600
s [kJ/kg-K]
T [K]
95 kPa
1140 kPa
Air
1
2s
3
4s
5s
-20 -10 0 10 20 30
9000
9200
9400
9600
9800
10000
1
BrakeForce
Second-Law Analysis of Gas Power Cycles
9-122 The total exergy destruction associated with the Otto cycle described in Prob. 9-34 and the exergy at
the end of the power stroke are to be determined.
Analysis From Prob. 9-34, q in = 750, q out = 357.62 kJ/kg, T 1 = 300 K, and T 4 = 774.5 K.
The total exergy destruction associated with this Otto cycle is determined from
750 kJ/kg
357.62kJ/kg 300 K
out in destroyed 0 L T H
q
q x T
Noting that state 4 is identical to the state of the surroundings, the exergy at the end of the power stroke
(state 4) is determined from
where
2 .6823 1.70203 0.287kJ/kgKln
ln ln ln
357.62kJ/kg
1
4 4 1 1 4
4 1 4 1 1
4 4 0 4 1 4 1
4 0 4 1
4 0 4 1 out
s s R T
s s R P
s s s s s s R
u u u u q
o o o o o o
Thus,
9-123 The total exergy destruction associated with the Diesel cycle described in Prob. 9-47 and the exergy
at the end of the compression stroke are to be determined.
3
= 0.906 / 12 = 0.0566 m
3 /kg.
The total exergy destruction associated with this Otto cycle is determined from
1019.7kJ/kg
445.63kJ/kg 300 K
out in destroyed 0 L T H
q
q x T
Noting that state 1 is identical to the state of the surroundings, the exergy at the end of the compression
stroke (state 2) is determined from
= 348.6 kJ/kg
3
3
2 1 0 2 1 0 2 1
2 2 0 0 2 0 0 2 0
1 kPa m
1 kJ 643.3 214.07 0 95 kPa 0.0566 0.906m/kg
u u T s s P
9-124E The exergy destruction associated with the heat rejection process of the Diesel cycle described in
Prob. 9-49E and the exergy at the end of the expansion stroke are to be determined.
T 1 )/2 = (1420.6 + 540)/2 = 980.3 R, we have c v,avg = 0.180 Btu/lbm·R. The entropy change during process
4-1 is
ln ln 0.180Btu/lbmRln
0
4
1
4
1 1 − 4 = + = ⋅ =− ⋅
©
s s cv
Thus,
158.9Btu/lbm 540 R 0.1741Btu/lbm R
, 41 destroyed, 41 0 1 4 R
R
T
q x T s s
Noting that state 4 is identical to the state of the surroundings, the exergy at the end of the power stroke
(state 4) is determined from
where
0.1741Btu/lbm R
4 0 4 1
4 0 4 1
4 0 4 1 out
s s s s
u u u u q
Thus,
Discussion Note that the exergy at state 4 is identical to the exergy destruction for the process 4-1 since
state 1 is identical to the dead state, and the entire exergy at state 4 is wasted during process 4-1.
9-127 EES Problem 9-126 is reconsidered. The effect of the cycle pressure on the total irreversibility for
the cycle and the exergy of the exhaust gas leaving the regenerator is to be investigated.
Analysis Using EES, the problem is solved as follows:
"Input data"
T_o = 300 [K]
T_L = 300 [K]
T_H = 1400 [K]
T[3] = 1200 [K]
{Pratio = 10}
T[1] = 300 [K]
C_P=1.005 [kJ/kg-K]
P[1]= 100 [kPa]
P_o=P[1]
Eta_reg = 1.
Eta_c =1.0"Compressor isentorpic efficiency"
Eta_t =1.0"Turbien isentropic efficiency"
MM=MOLARMASS(Air)
R=R_u/MM
R_u=8.314 [kJ/kmol-K]
C_V=C_P - R
k=C_P/C_V
"Isentropic Compressor anaysis"
"For the ideal case the entropies are constant across the compressor"
P[2] = Pratio*P[1]
"T_s[2] is the isentropic value of T[2] at compressor exit"
T_s[2]=T[1]*(Pratio)^((k-1)/k)
Eta_c = w_compisen/w_comp
"compressor adiabatic efficiency, W_comp > W_compisen"
"Conservation of energy for the compressor for the isentropic case:
e_in - e_out = DELTAe=0 for steady-flow"
w_compisen = C_P*(T_s[2]-T[1])
"Actual compressor analysis:"
w_comp = C_P*(T[2]-T[1])
"External heat exchanger analysis"
"SSSF First Law for the heat exchanger, assuming W=0, ke=pe=
e_in - e_out =DELTAe_cv =0 for steady flow"
q_in_noreg = C_P*(T[3]-T[2])
P[3]=P[2]"process 2-3 is SSSF constant pressure"
"Turbine analysis"
"For the ideal case the entropies are constant across the turbine"
P[4] = P[3] /Pratio
T_s[4]=T[3]*(1/Pratio)^((k-1)/k)
"T_s[4] is the isentropic value of T[4] at turbine exit"
Eta_t = w_turb /w_turbisen "turbine adiabatic efficiency, w_turbisen > w_turb"
"SSSF First Law for the isentropic turbine, assuming: adiabatic, ke=pe=
e_in -e_out = DELTAe_cv = 0 for steady-flow"
w_turbisen=C_P*(T[3] - T_s[4])
"Actual Turbine analysis:"
w_turb= C_P*(T[3]-T[4])
"Cycle analysis"
w_net=w_turb-w_comp "[kJ/kg]"
Eta_th_noreg=w_net/q_in_noreg*Convert(, %) "[%]" "Cycle thermal efficiency"
Bwr=w_comp/w_turb "Back work ratio"
"With the regenerator the heat added in the external heat exchanger is"
q_in_withreg = C_P*(T[3]-T[5])
P[5]=P[2]
"The regenerator effectiveness gives h[5] and thus T[5] as:"
Eta_reg = (T[5]-T[2])/(T[4]-T[2])
"Energy balance on regenerator gives h[6] and thus T[6] as:"
"h[2] + h[4]=h[5] + h[6]"
T[2] + T[4]=T[5] + T[6]
P[6]=P[4]
"Cycle thermal efficiency with regenerator"
Eta_th_withreg=w_net/q_in_withreg*Convert(, %) "[%]"
"Irreversibility associated with the Brayton cycle is determined from:"
q_out_withreg = q_in_withreg - w_net
i_withreg = T_o*(q_out_withreg/T_L - q_in_withreg/T_H)
q_out_noreg = q_in_noreg - w_net
i_noreg = T_o*(q_out_noreg/T_L - q_in_noreg/T_H)
"Neglecting the ke and pe of the exhaust gases, the exergy of the exhaust gases at the exit of the
regenerator is:"
"Psi_6 = (h[6] - h_o) - T_o(s[6] - s_o)"
Psi_exit_withreg = C_P(T[6] - T_o) - T_o(C_Pln(T[6]/T_o)-Rln(P[6]/P_o))
Psi_exit_noreg = C_P(T[4] - T_o) - T_o(C_Pln(T[4]/T_o)-Rln(P[4]/P_o))
inoreg iwithreg Pratio (^) Ψexit,noreg
[kJ/kg]
Ψexit,withreg
[kJ/kg]
ηth,noreg
[%]
ηth,withreg
[%]
270.8 97.94 6 157.8 47.16 40.05 58.
244.5 113.9 7 139.9 56.53 42.63 56.
223 128.8 8 125.5 65.46 44.78 54.
205 142.7 9 113.6 74 46.61 53.
189.6 155.9 10 103.6 82.17 48.19 51.
176.3 168.4 11 95.05 90.02 49.58 50.
164.6 180.2 12 87.62 97.58 50.82 49.
154.2 191.5 13 81.11 104.9 51.93 47.
144.9 202.3 14 75.35 111.9 52.94 46.
4.5 5.0 5.5 6.0 6.5 7.0 7.
200
400
600
800
1000
1200
1400
1600
100 kPa
1000 kPa
Air
2s
1
2
5
3
4 4s 6