
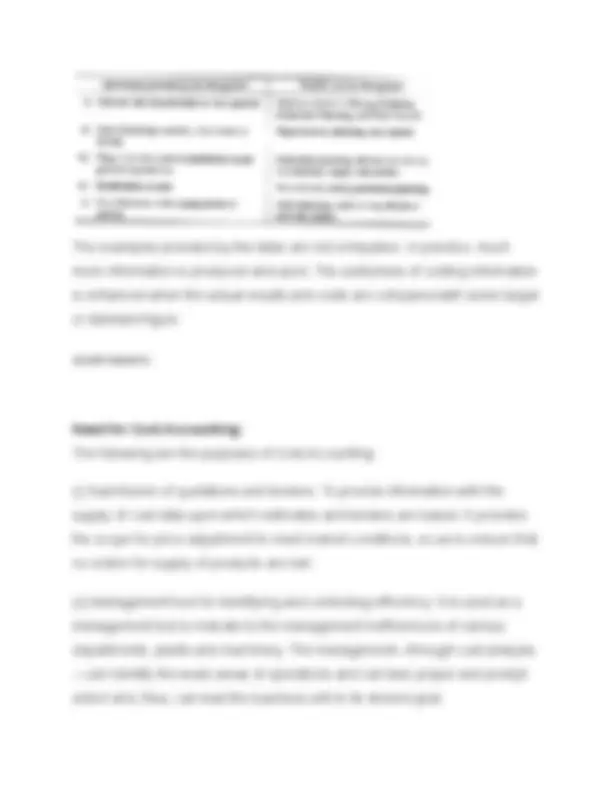
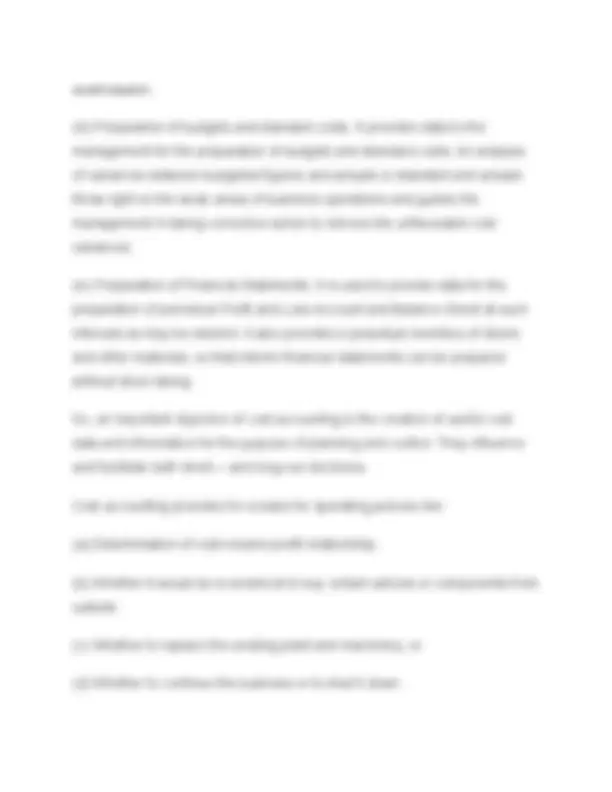
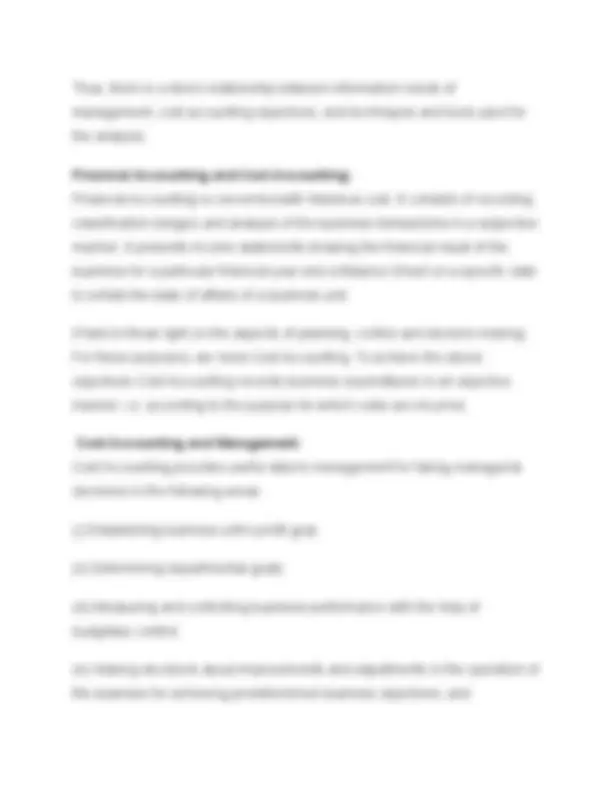
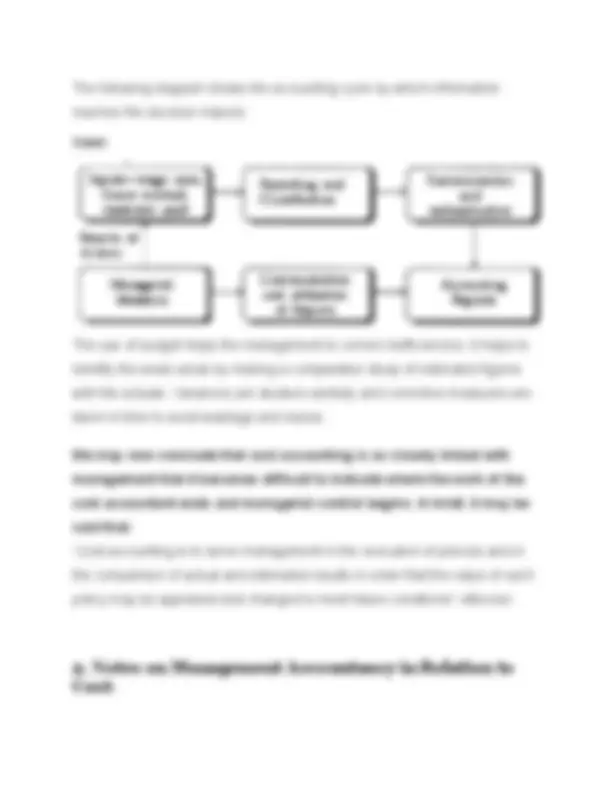
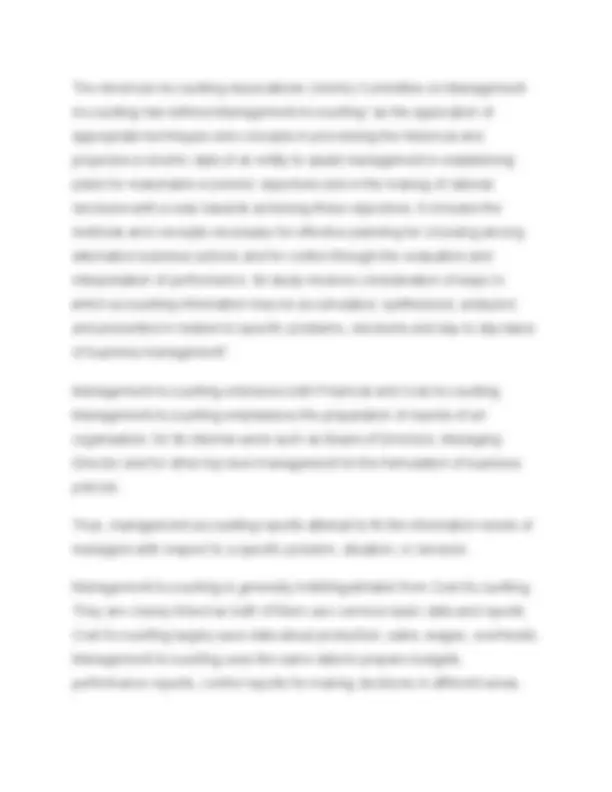
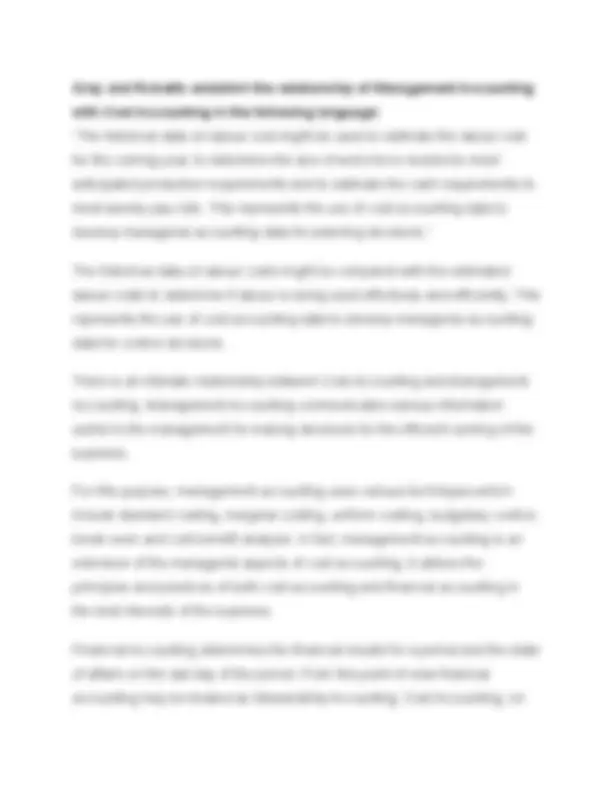
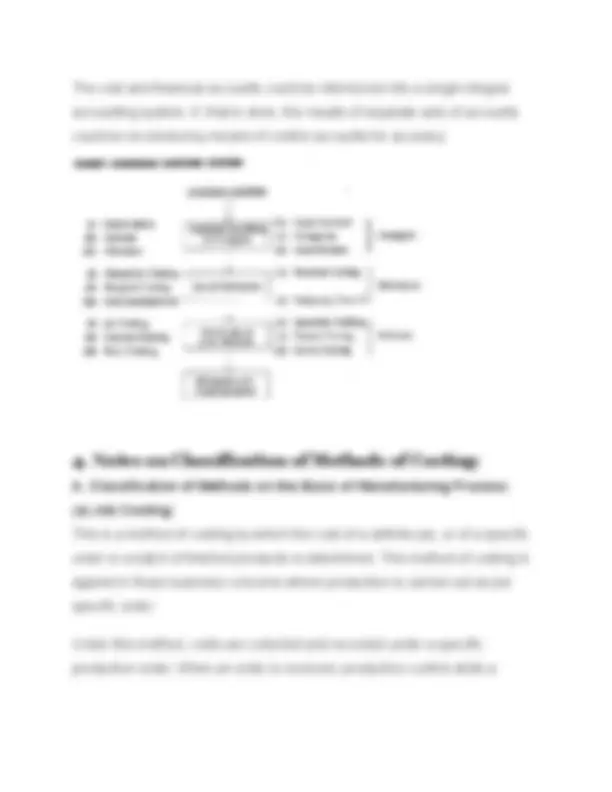
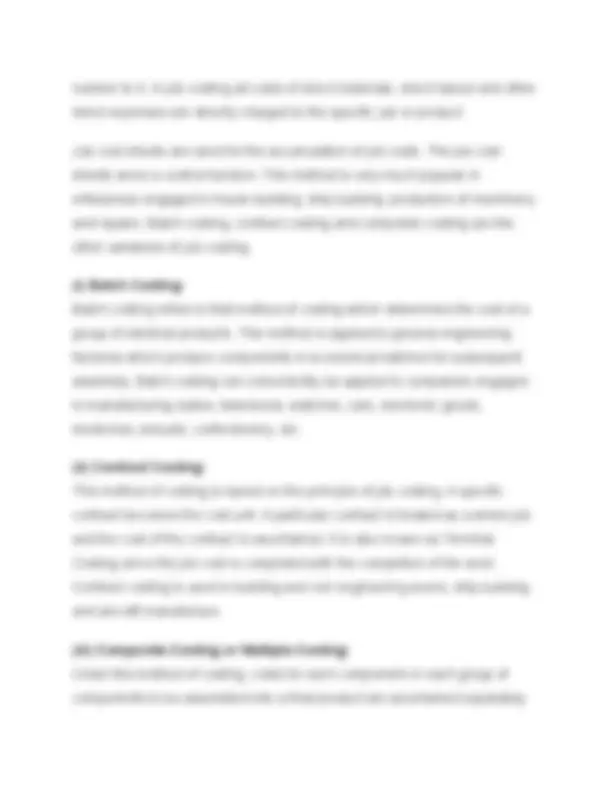
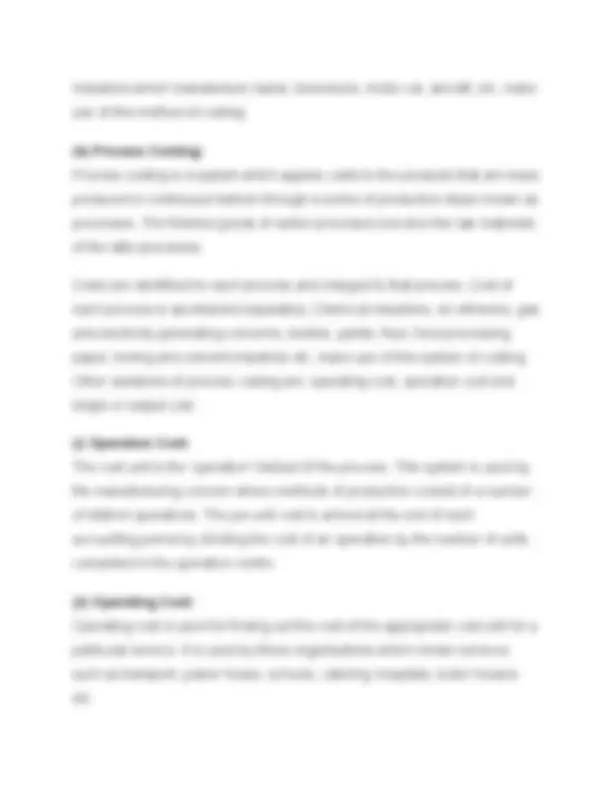
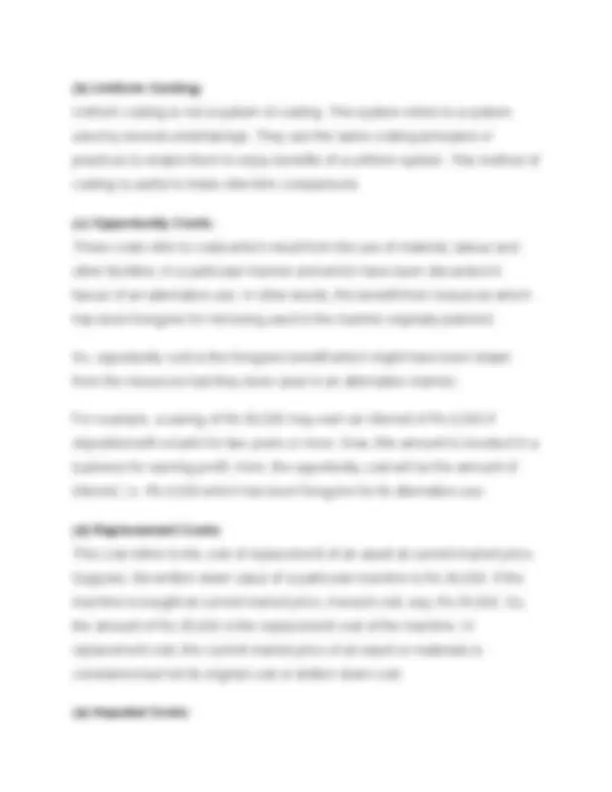
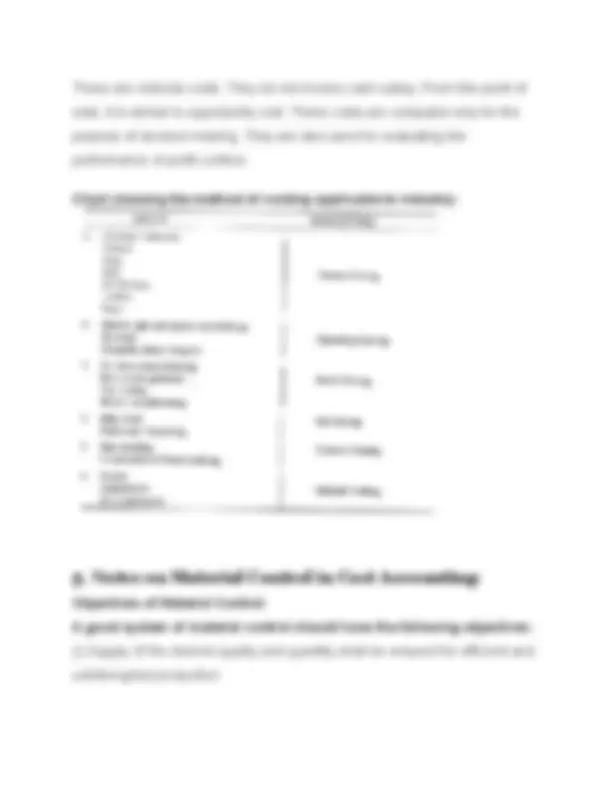
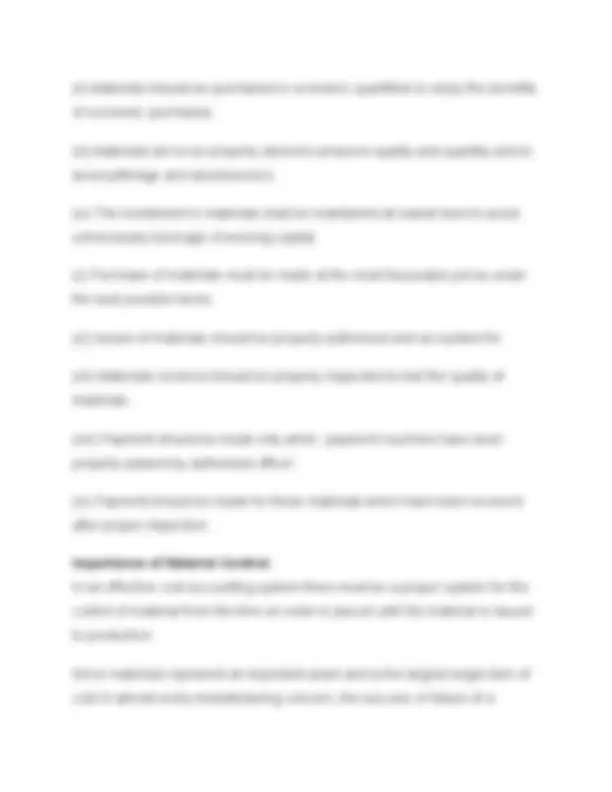
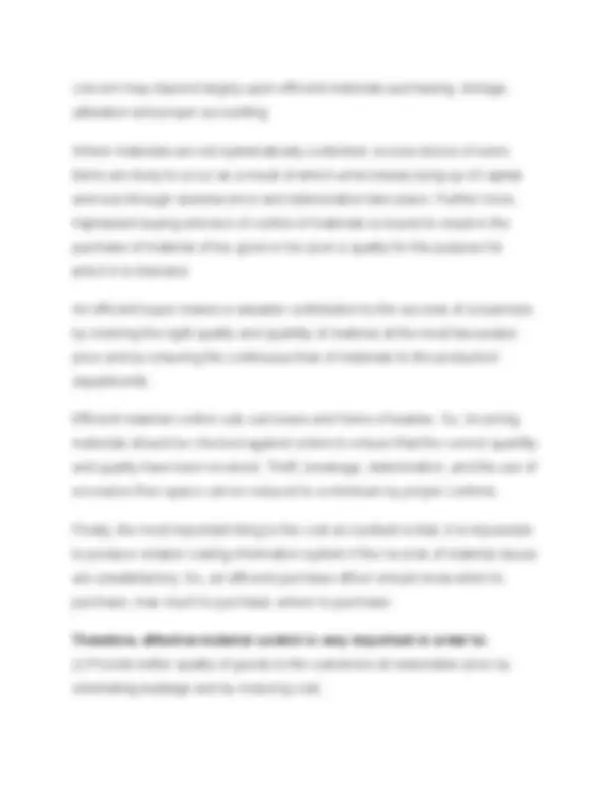
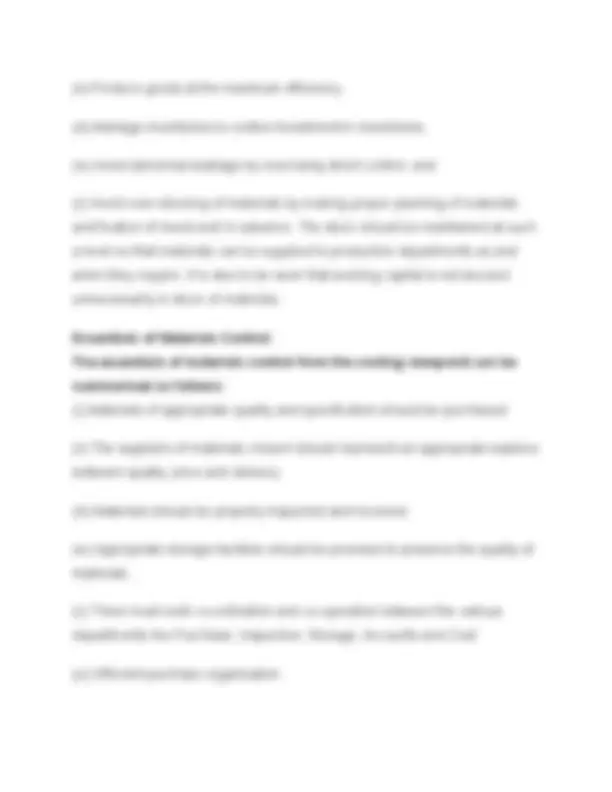
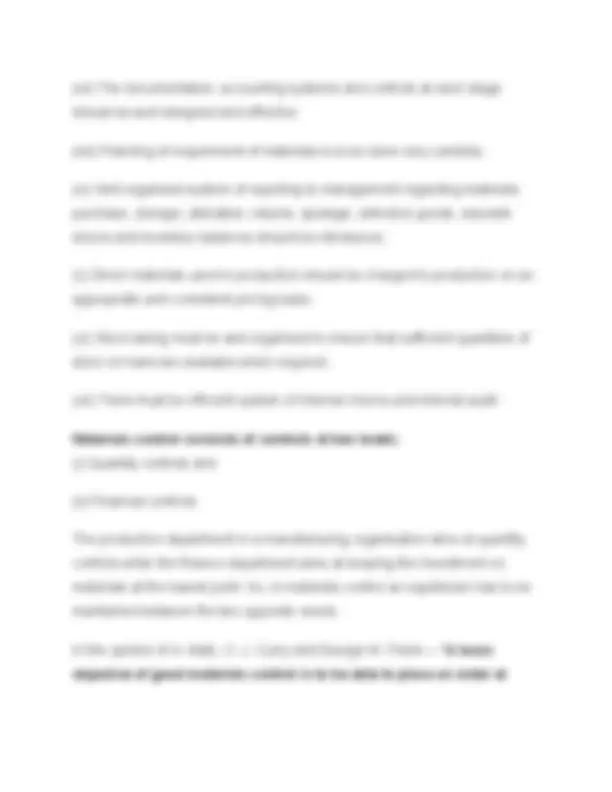
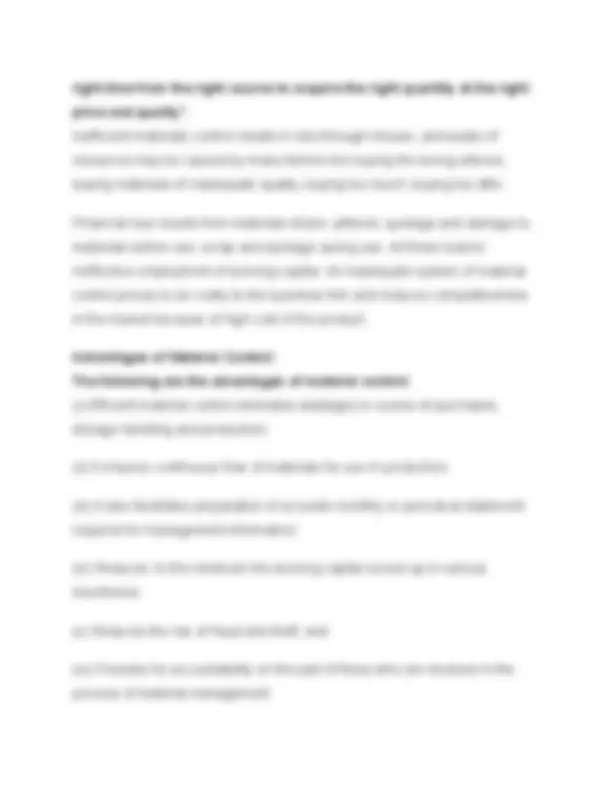
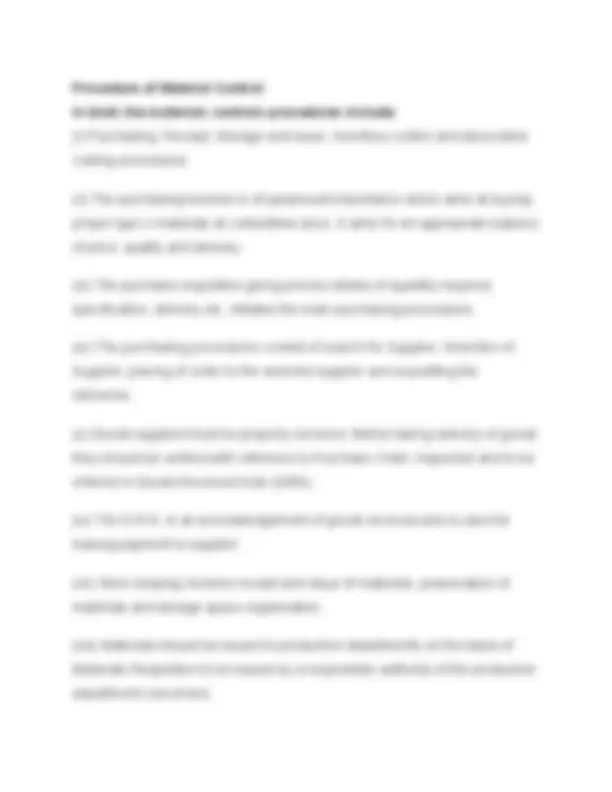
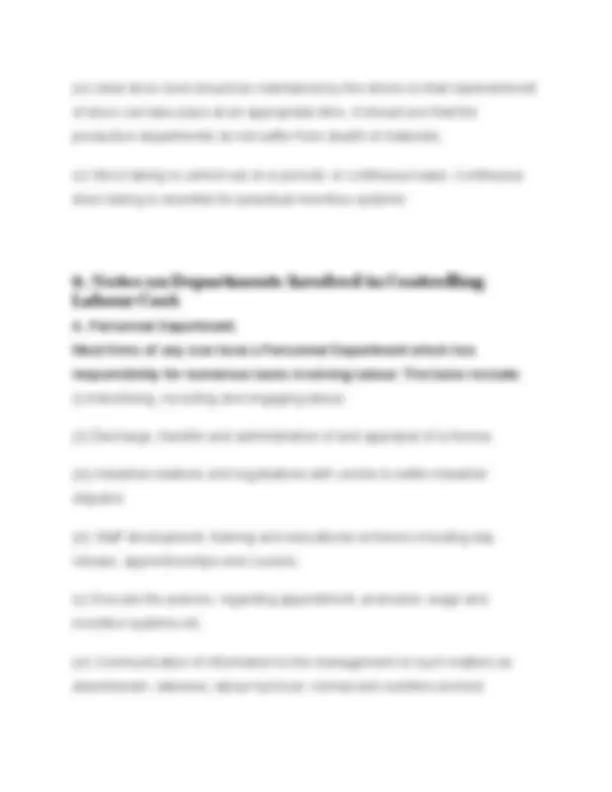
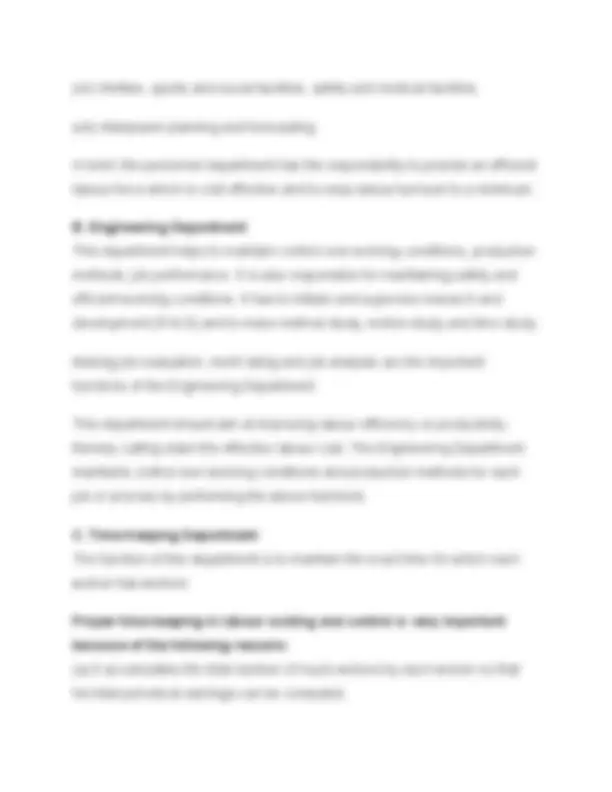
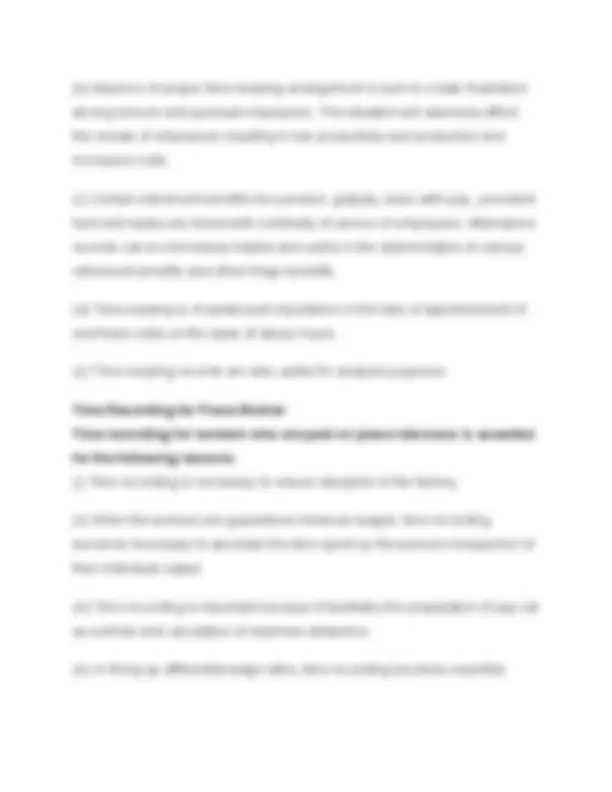
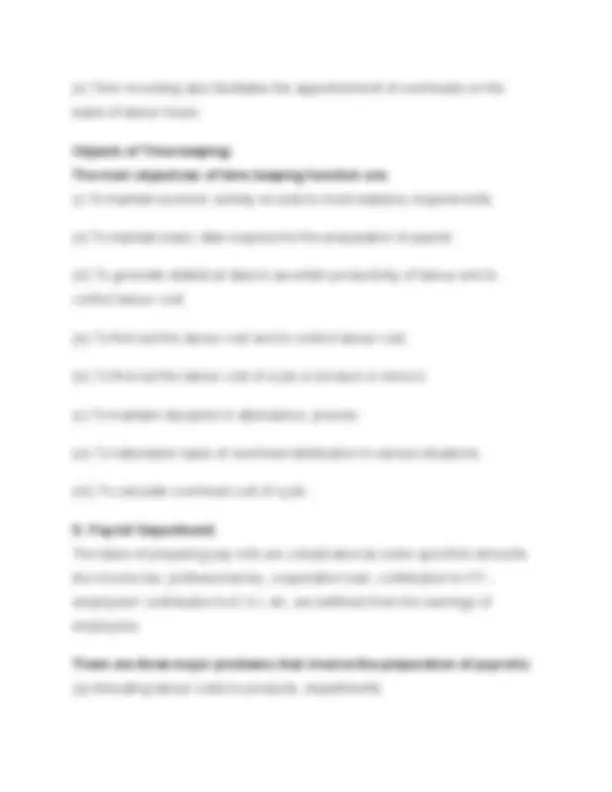
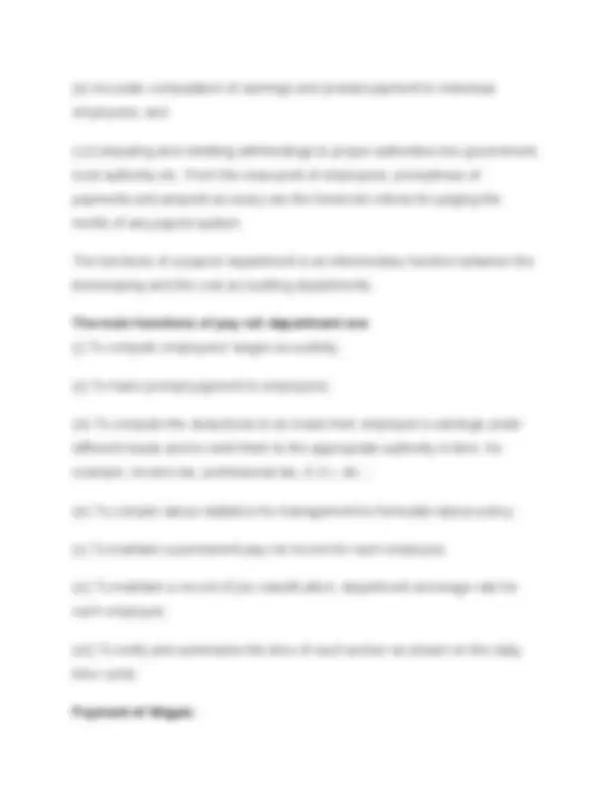
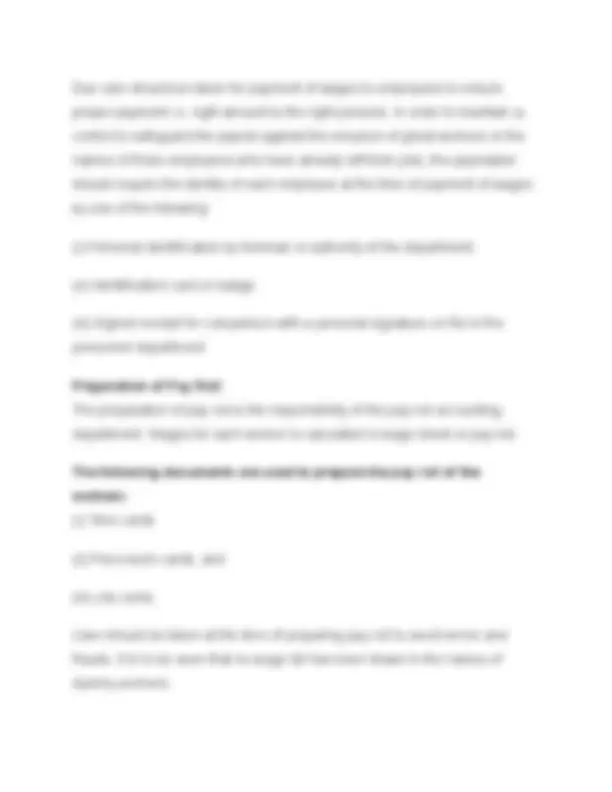
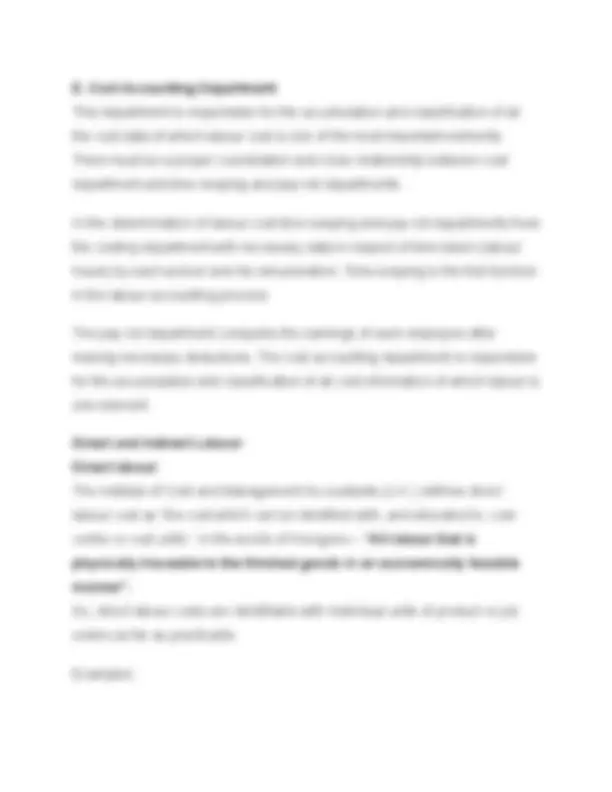
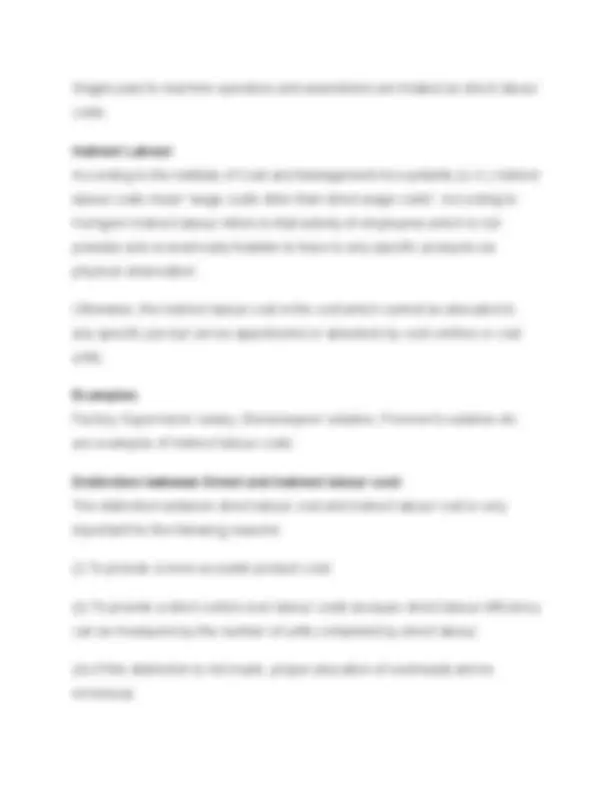
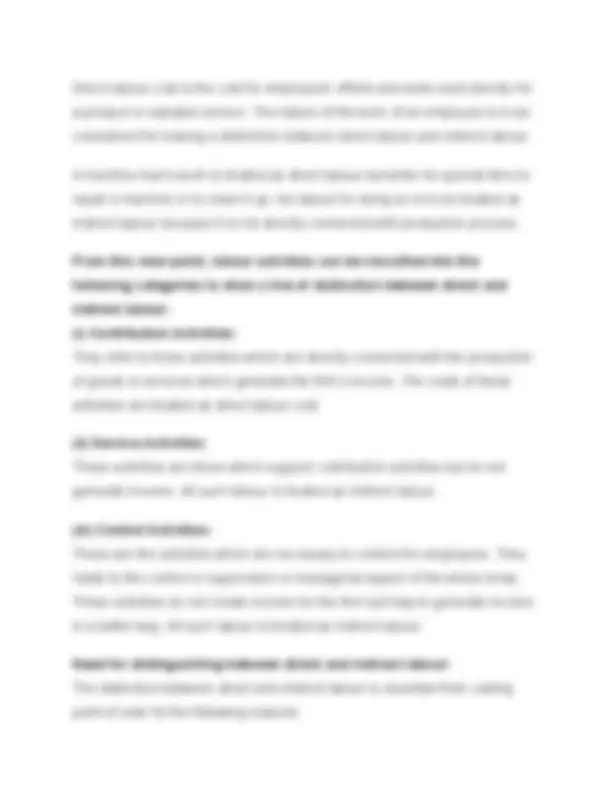
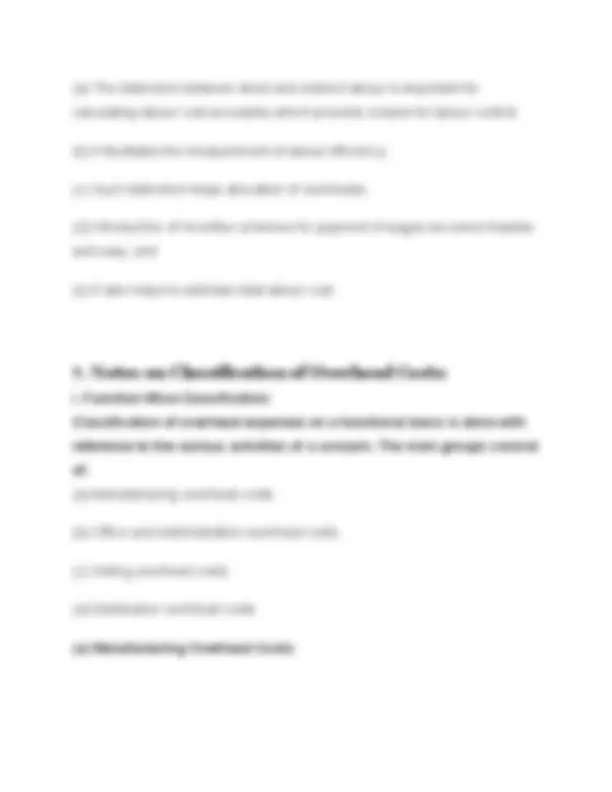
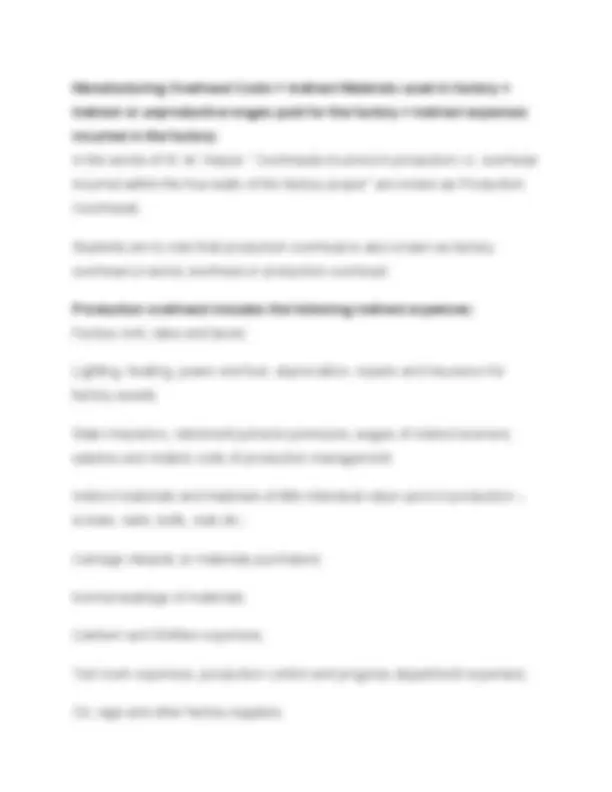
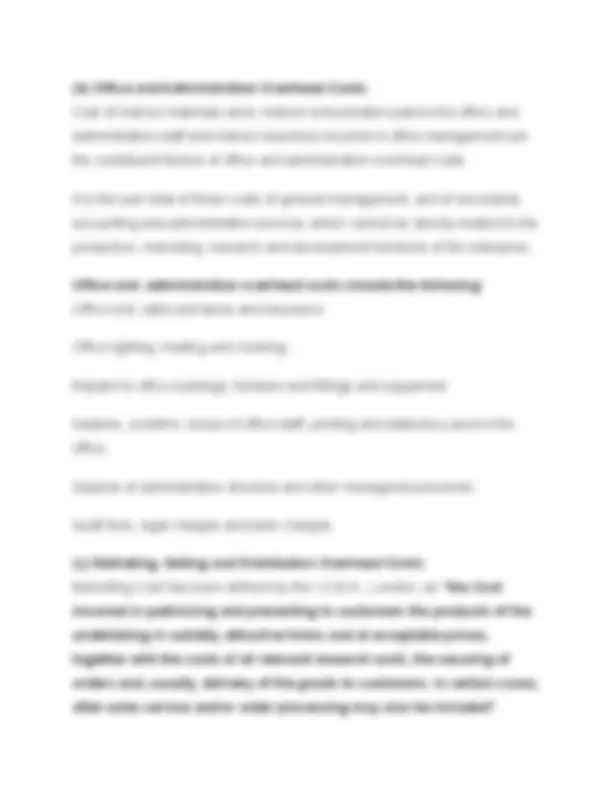
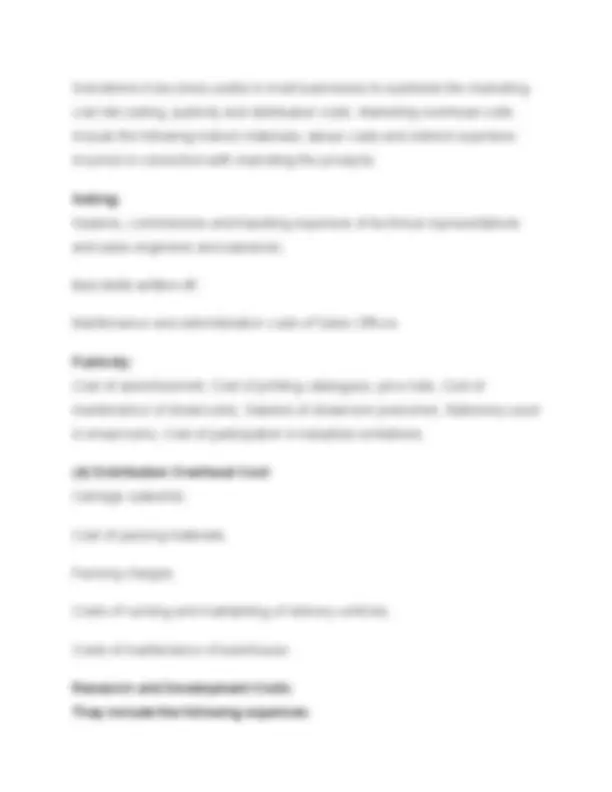
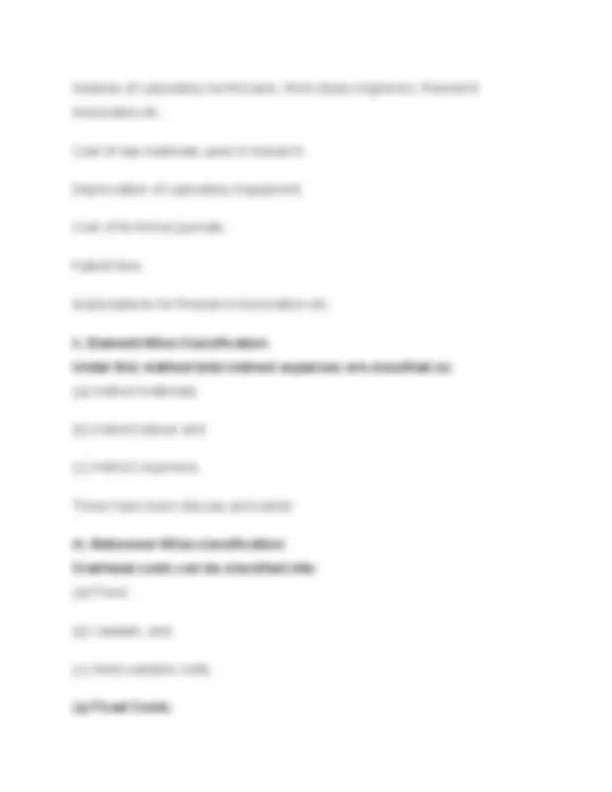
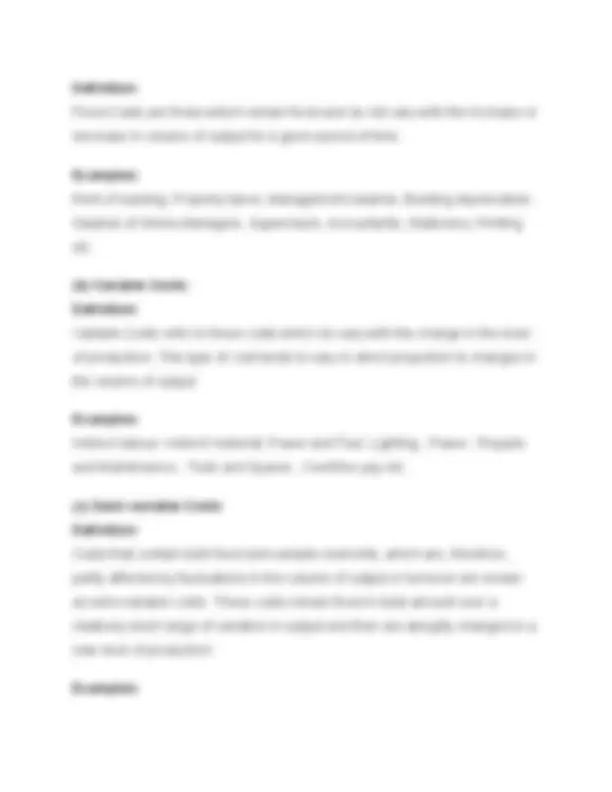
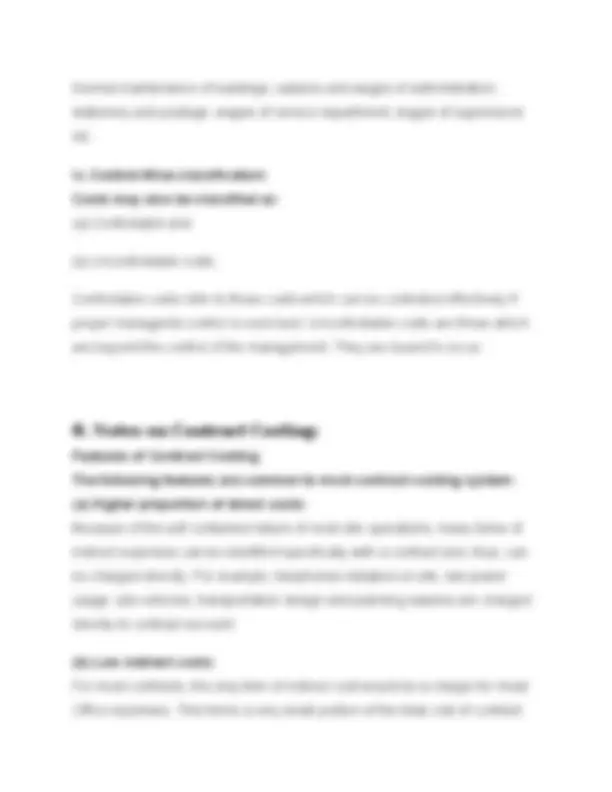
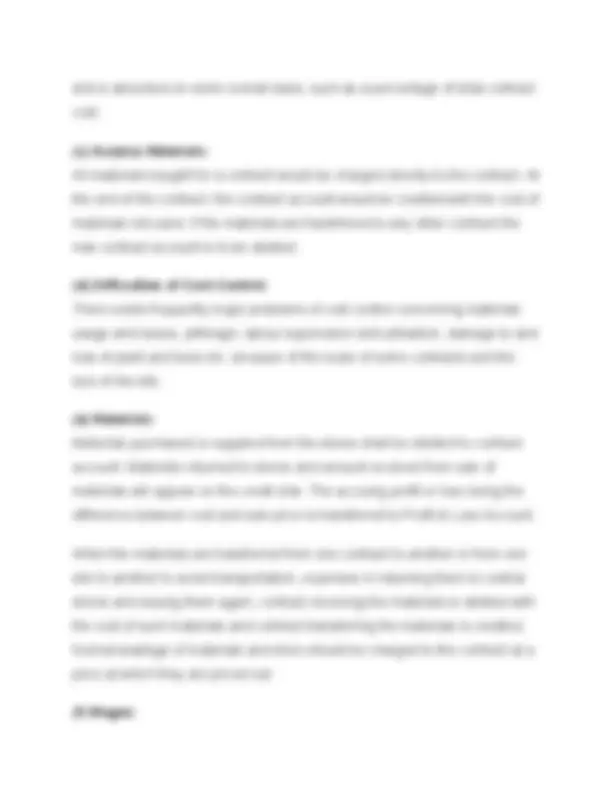
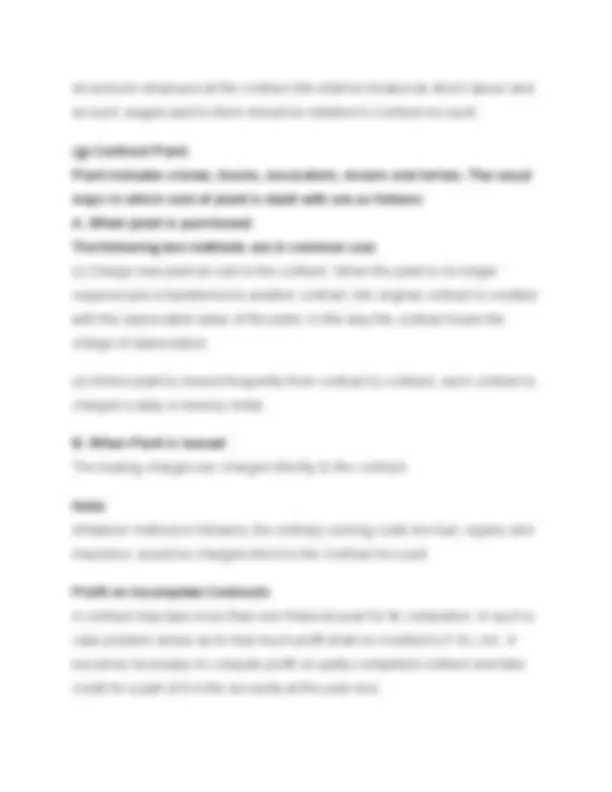
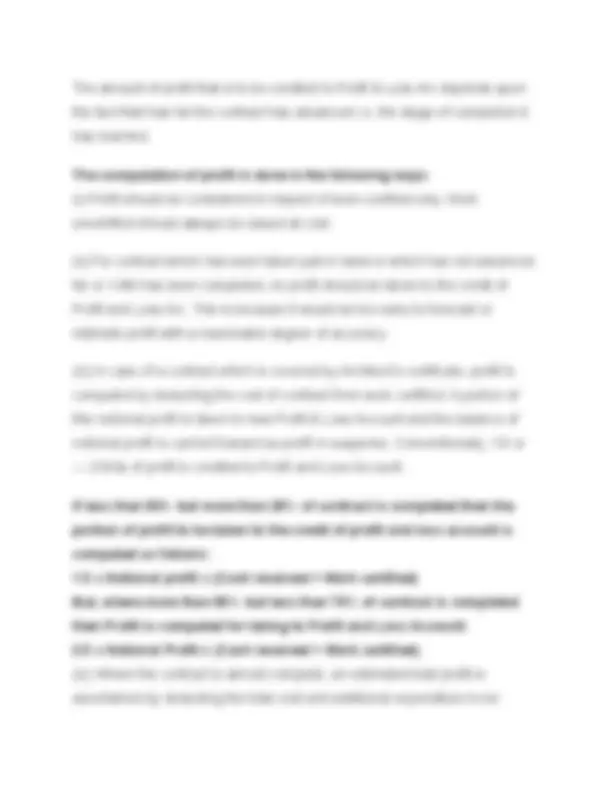
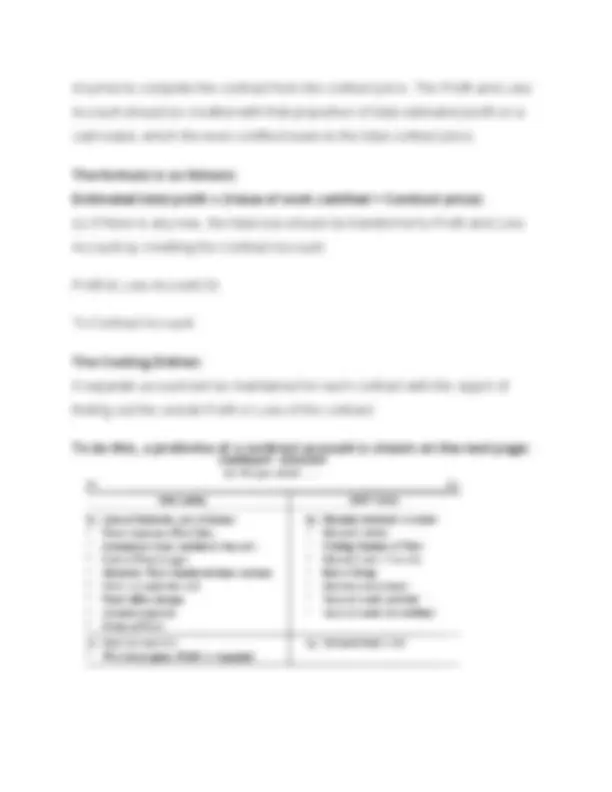
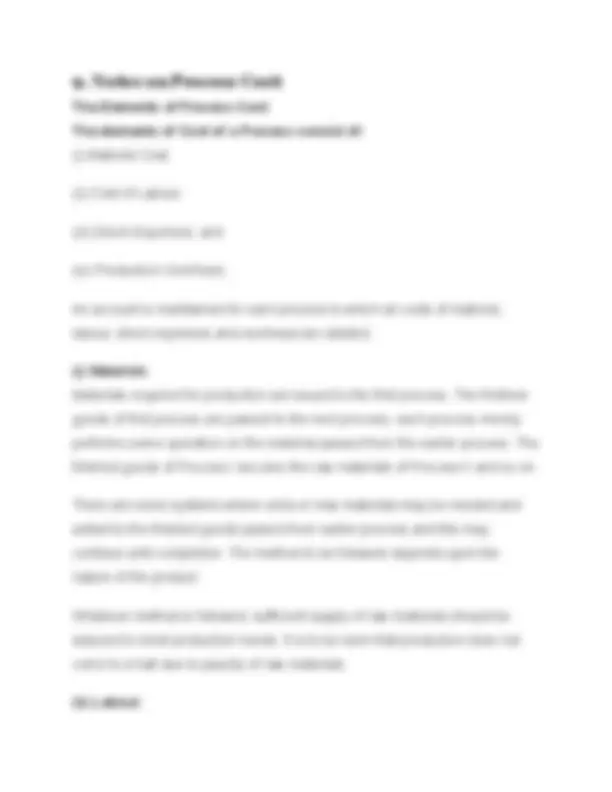
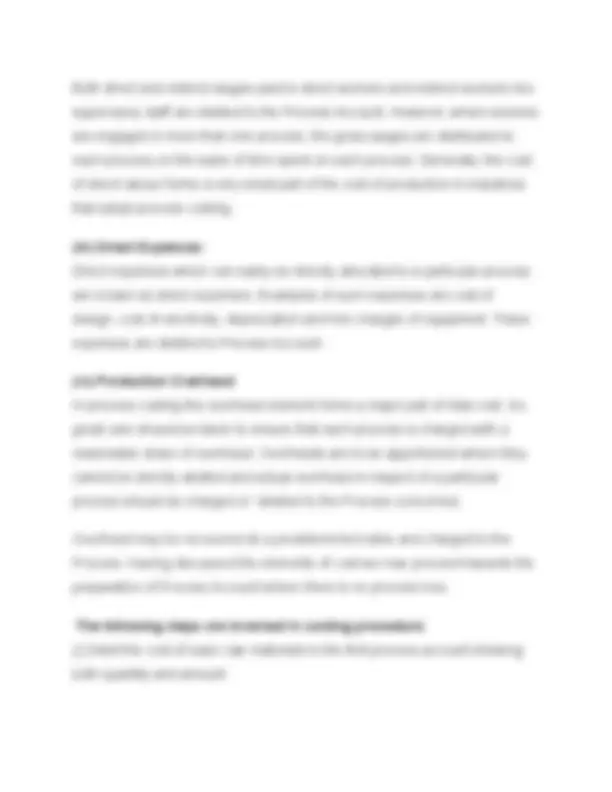
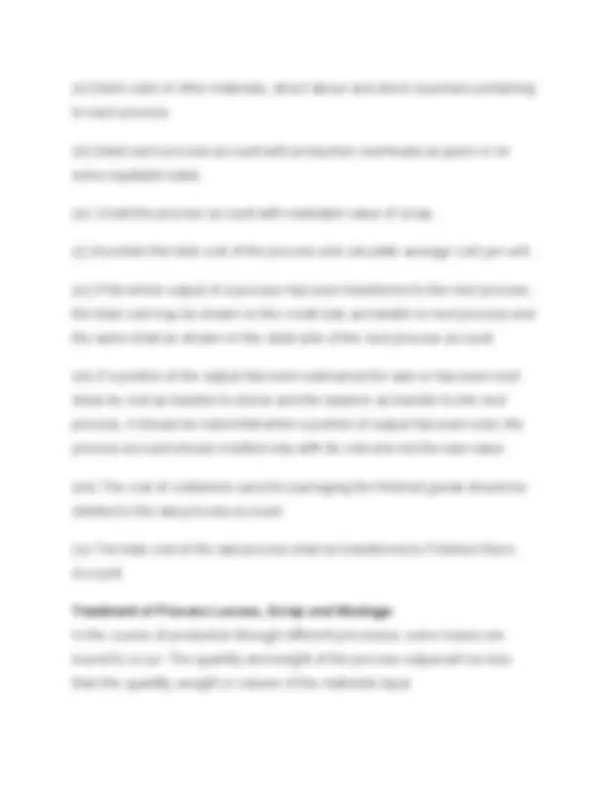
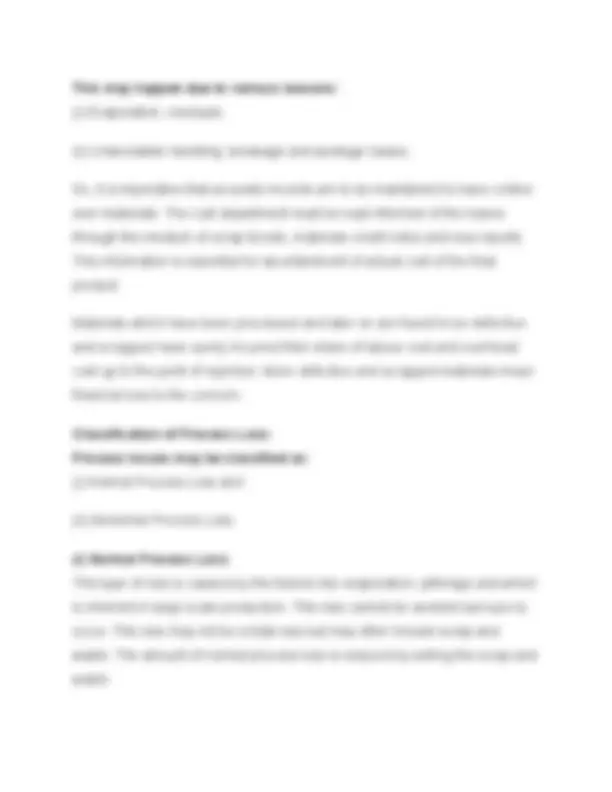
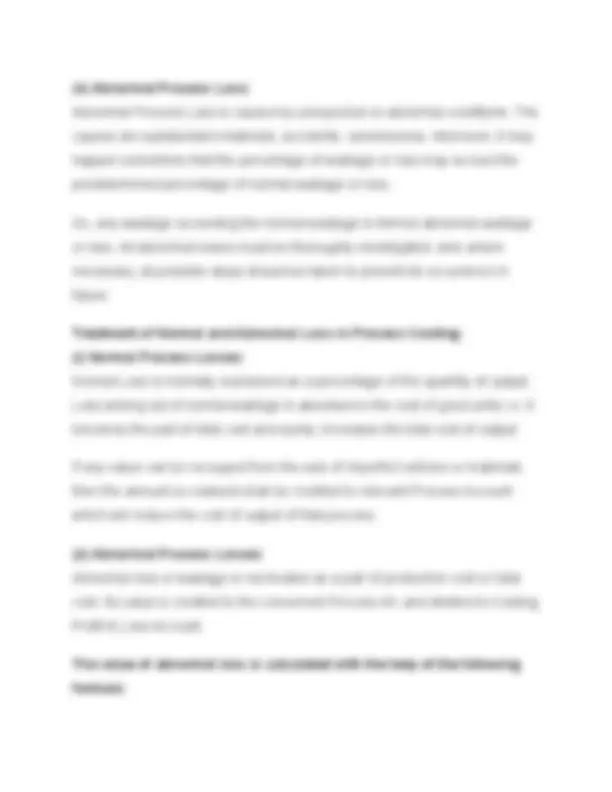
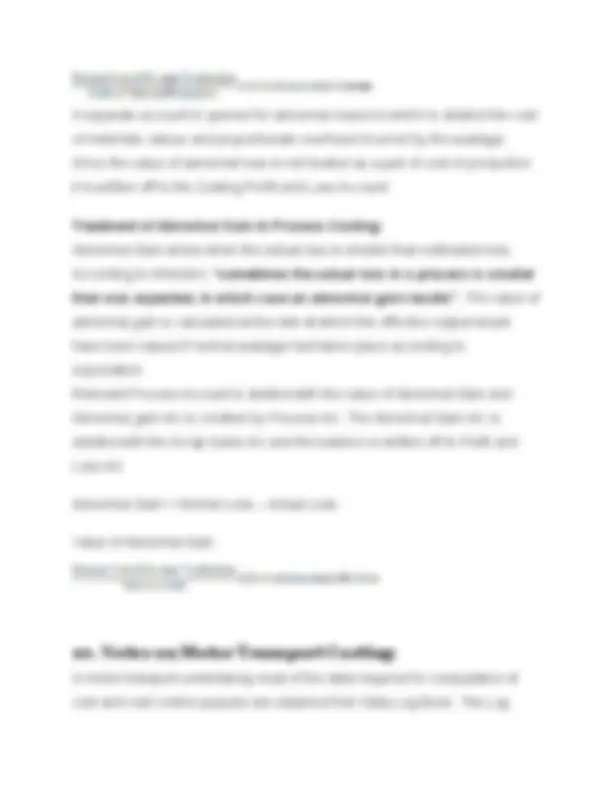
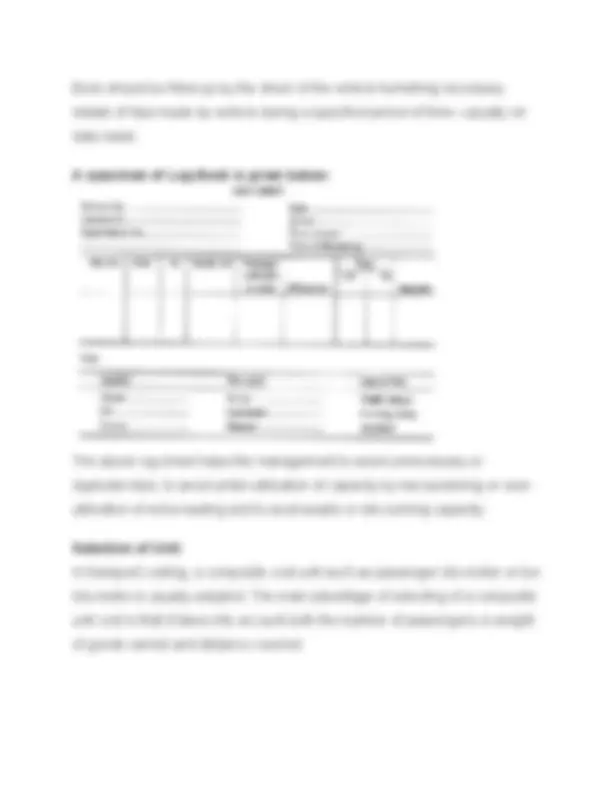
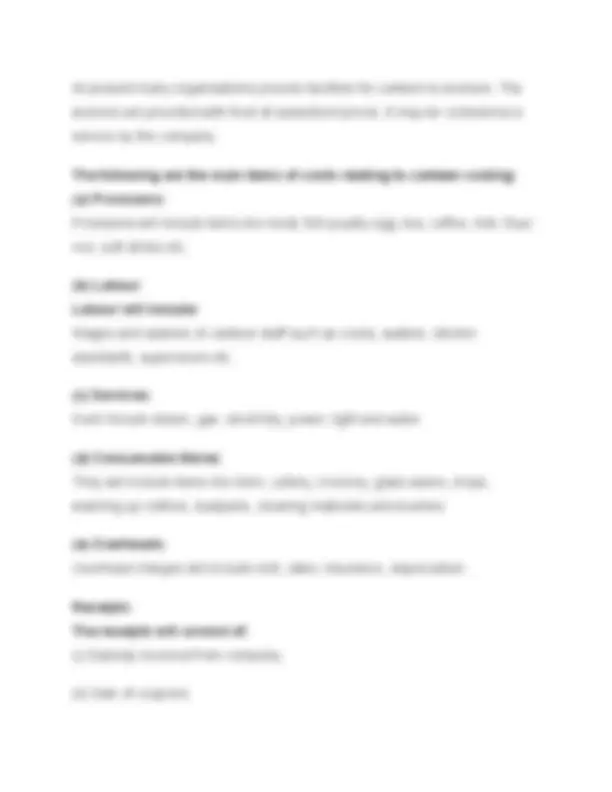
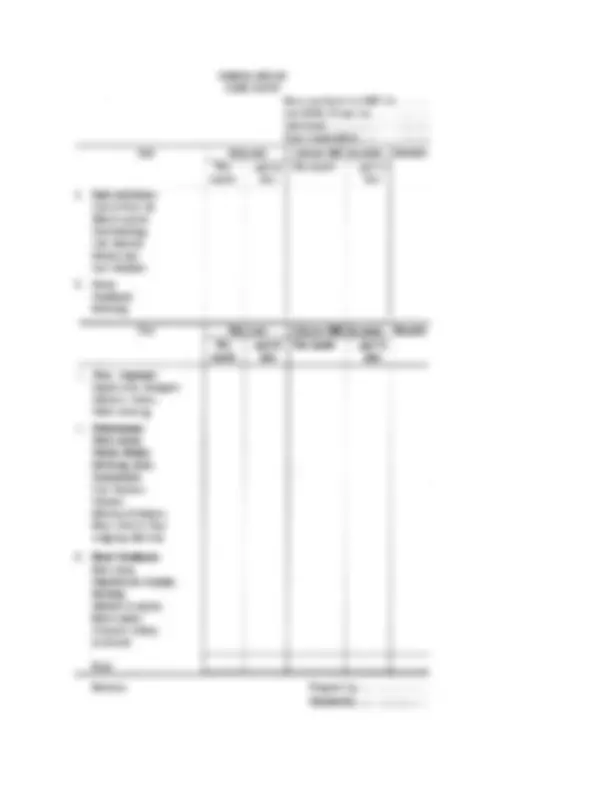
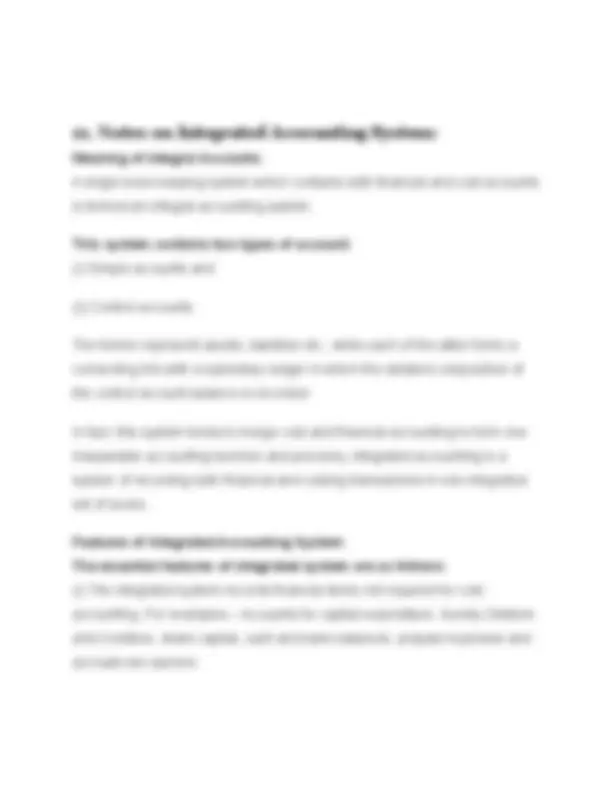
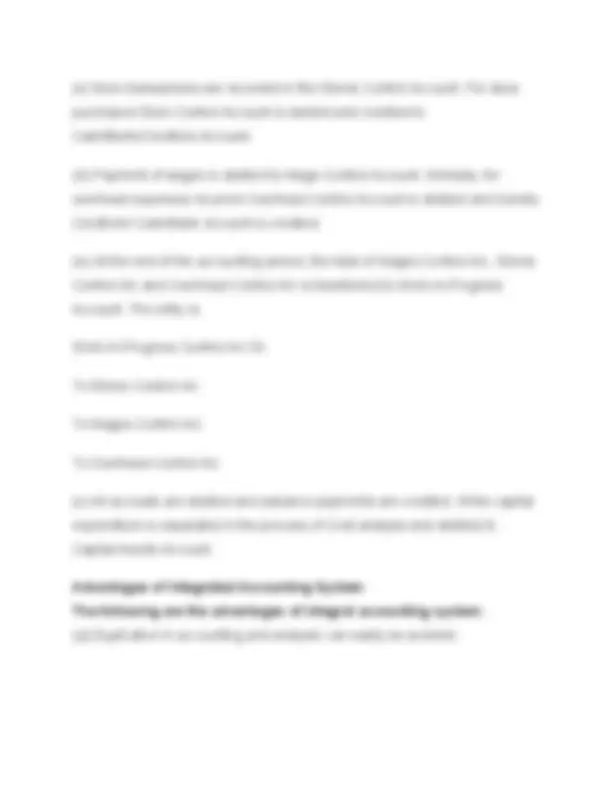
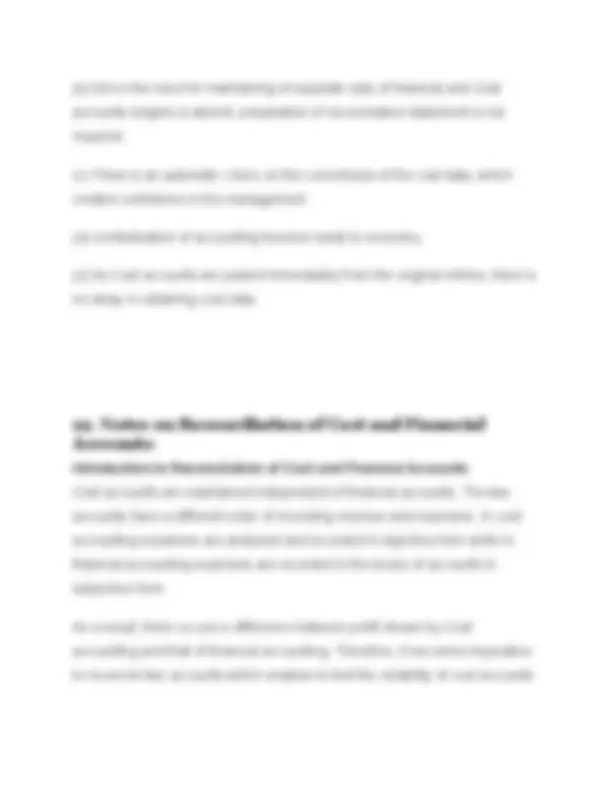
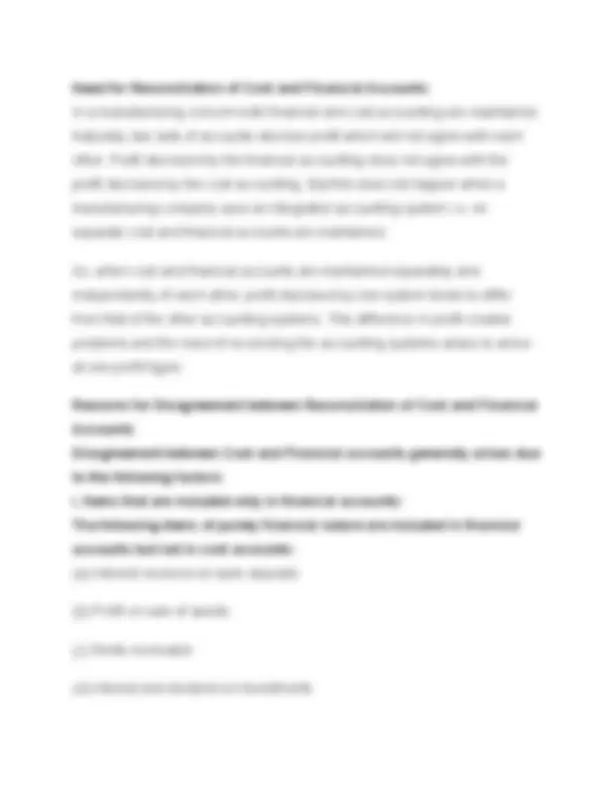
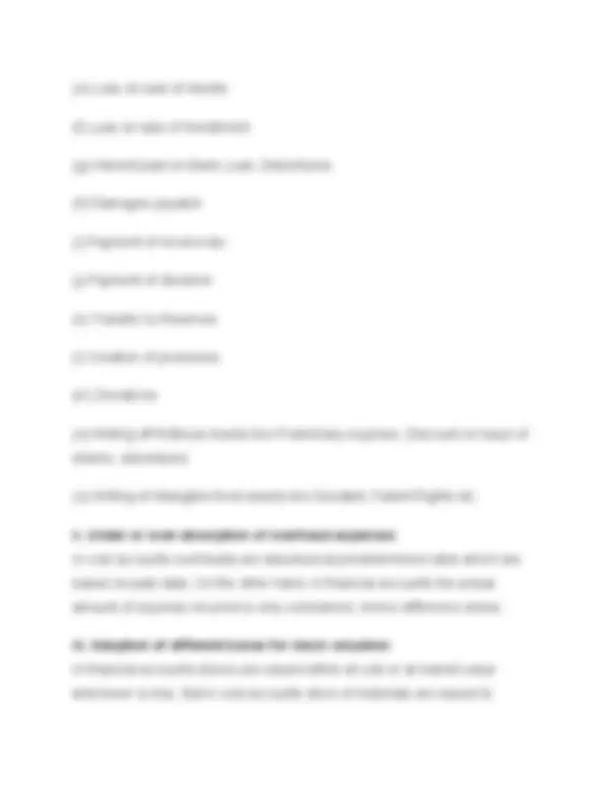
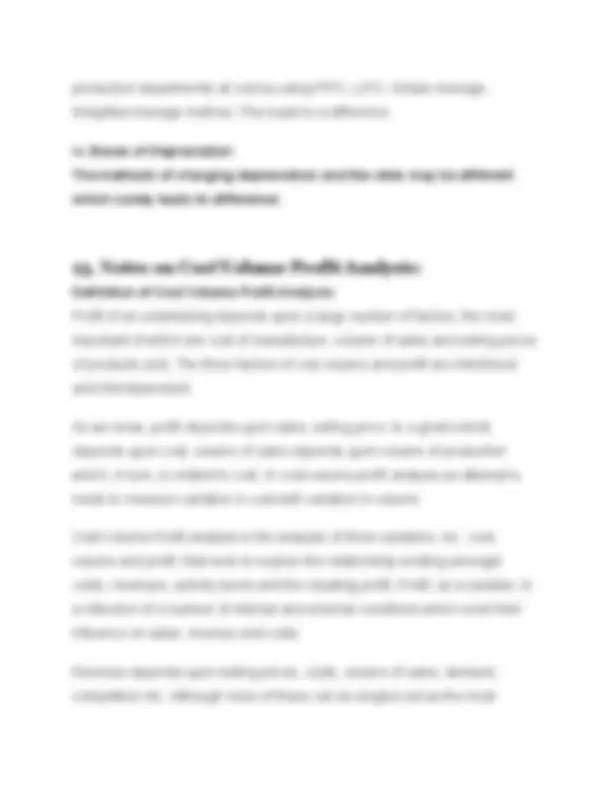
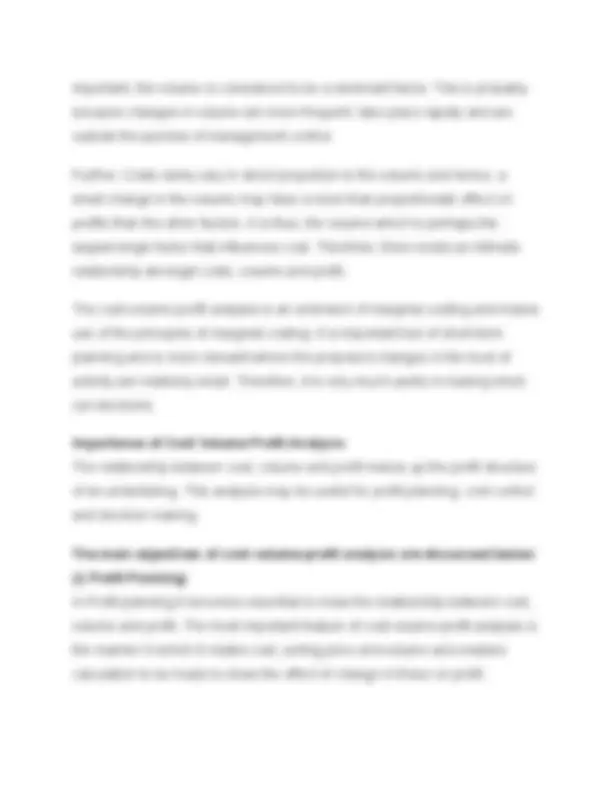
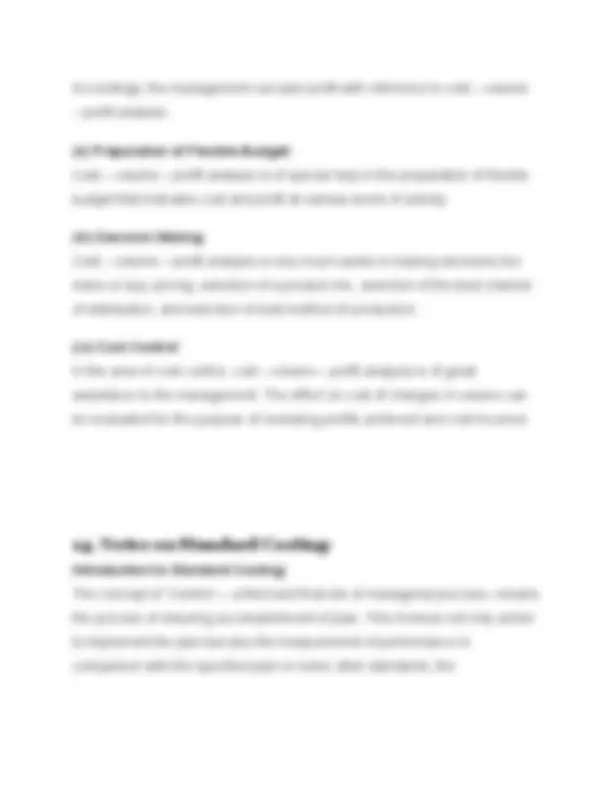
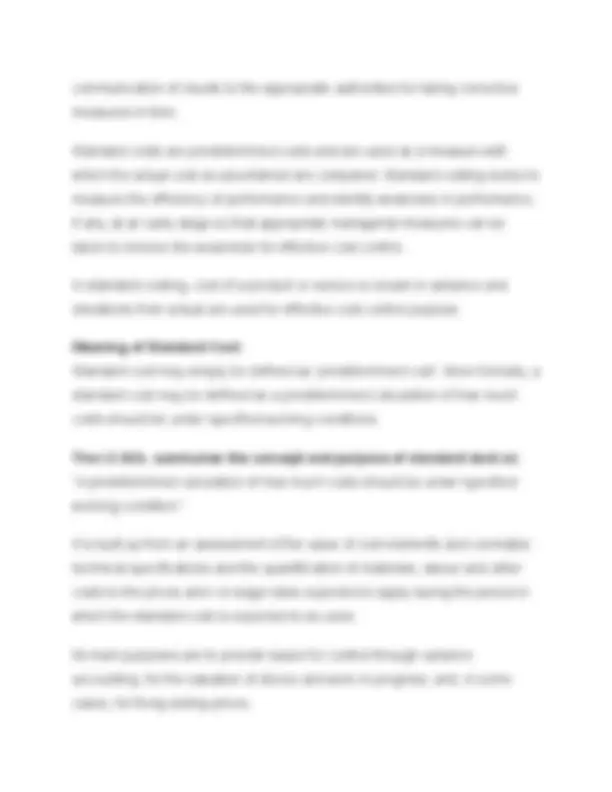
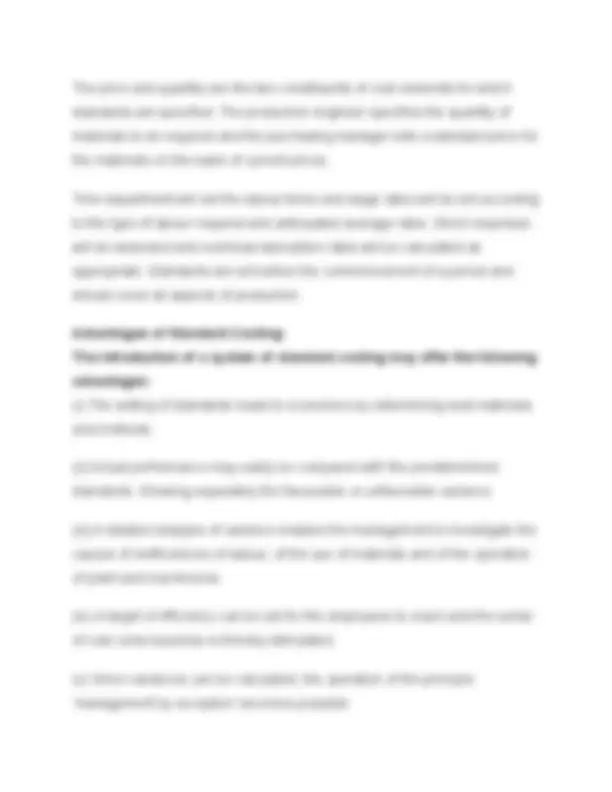
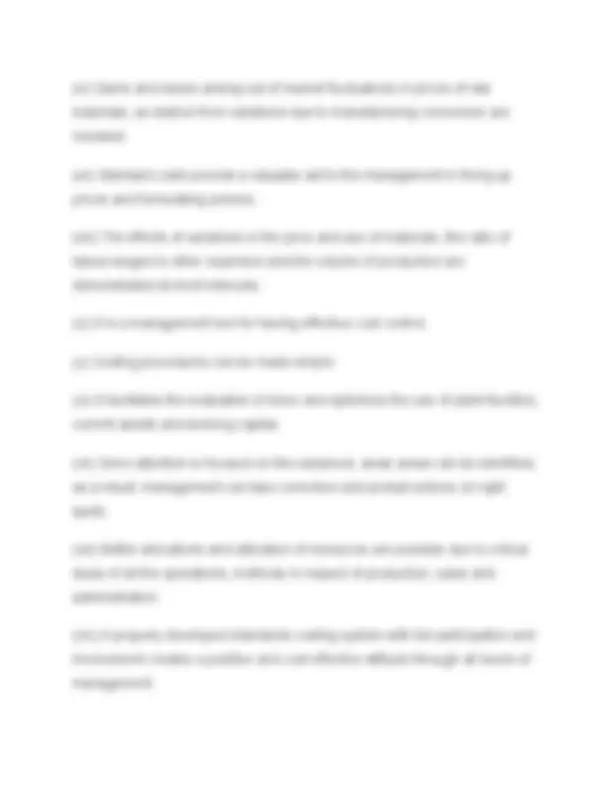
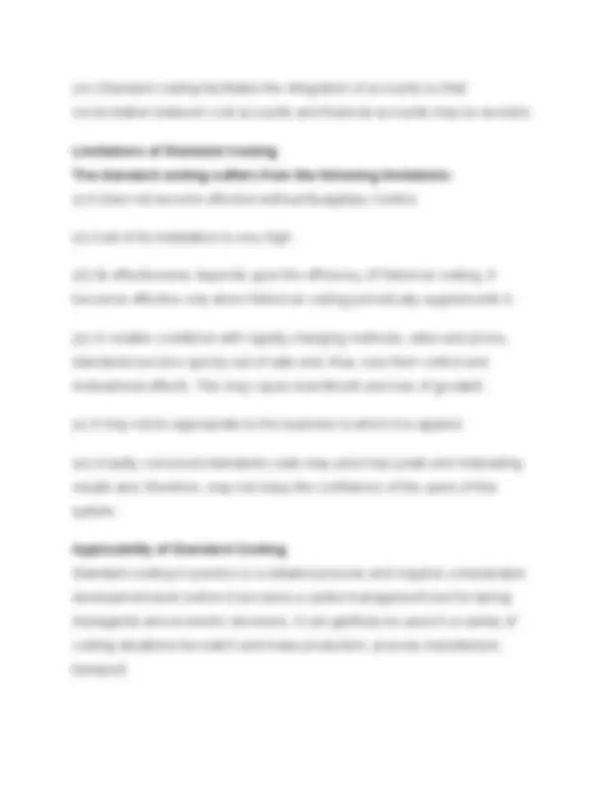
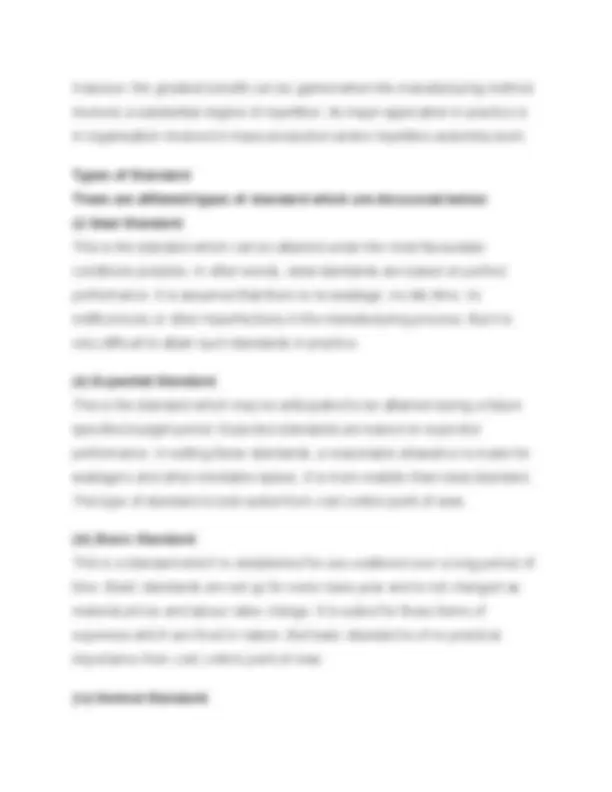
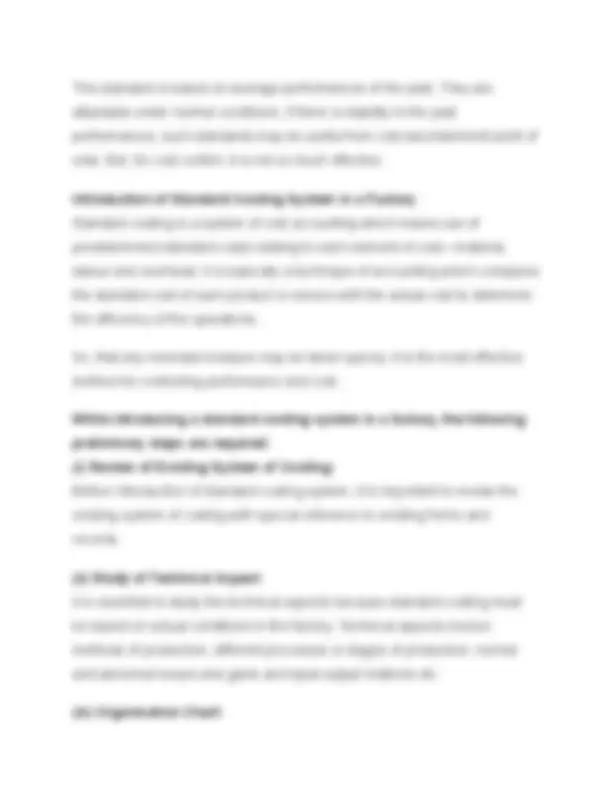
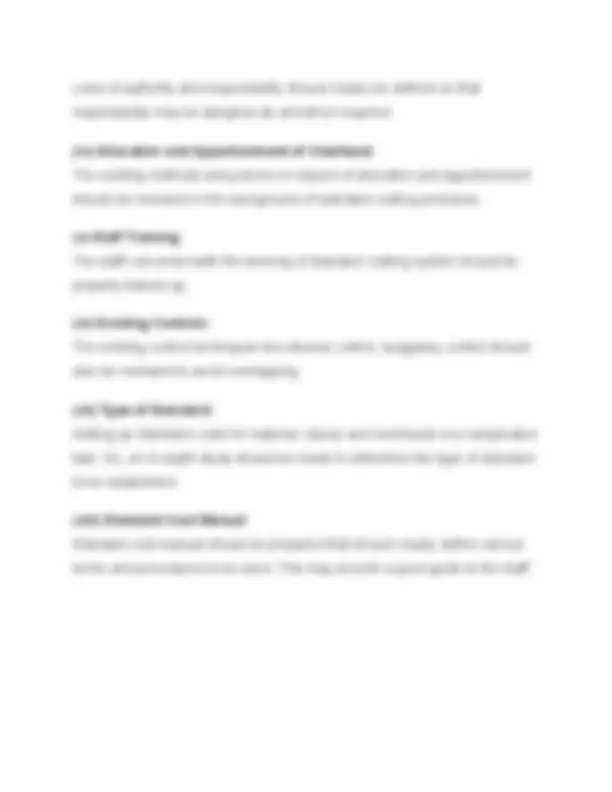
Study with the several resources on Docsity
Earn points by helping other students or get them with a premium plan
Prepare for your exams
Study with the several resources on Docsity
Earn points to download
Earn points by helping other students or get them with a premium plan
Community
Ask the community for help and clear up your study doubts
Discover the best universities in your country according to Docsity users
Free resources
Download our free guides on studying techniques, anxiety management strategies, and thesis advice from Docsity tutors
Notes on Cost and Cost Accounting 2. Notes on Management Accountancy in Relation to Cost 3. Notes on Prerequisites of Costing System 4. Notes on Classification of Methods of Costing 5. Notes on Material Control in Cost Accounting 6. Notes on Departments Involved in Controlling Labour Cost 7. Notes on Classification of Overhead of Costs 8. Notes on Contract Costing 9. Notes on Process Cost 10. Notes on Motor Transport Costing 11. Notes on Integrated Accounting System 12. Notes on Reconciliation
Typology: Lecture notes
1 / 69
This page cannot be seen from the preview
Don't miss anything!
Article shared by Compilations of study notes from different chapters of cost accounting! The below given notes will help you for prepare for various competitive examination. If you are preparing for Civil Service Examination, these notes will definitely help you to get an overall idea about the subject. Contents:
Aspects of Cost: Costs may be ascertained: ADVERTISEMENTS:
(i) Historically; i.e. after they have been incurred; or (ii) By predetermined standards combined with subsequent analysis of variances between these standards, and the actual cost incurred; and (iii) By the use of marginal methods of presentation for either (a) or (b), involving the differentiation between “fixed” and “variable” costs. ADVERTISEMENTS: In the light of the above definitions we may define Cost Accounting as a process or mechanism by means of which costs of products and services are ascertained with a reasonable degree of accuracy. In a broader view, cost accounting is concerned with the field of responsibility for advising the management in both historical and future costs and, thereby, helping managerial planning, control and decision making. It provides the management with a variety of information to plan, control and make decisions. The following table gives us the examples of the information provided by a typical costing system and how it is used for different purposes by the management.
ADVERTISEMENTS: (iii) Preparation of budgets and standard costs: It provides data to the management for the preparation of budgets and standard costs. An analysis of variances between budgeted figures and actuals or standard and actuals throw light on the weak areas of business operations and guides the management in taking corrective action to remove the unfavorable cost variances. (iv) Preparation of Financial Statements: It is used to provide data for the preparation of periodical Profit and Loss Account and Balance Sheet at such intervals as may be desired. It also provides a perpetual inventory of stores and other materials, so that interim financial statements can be prepared without stock taking. So, an important objective of cost accounting is the creation of useful cost data and information for the purpose of planning and control. They influence and facilitate both short— and long-run decisions. Cost accounting provides for a basis for operating policies like: (a) Determination of cost-volume-profit relationship, (b) Whether it would be economical to buy certain articles or components from outside, (c) Whether to replace the existing plant and machinery, or (d) Whether to continue the business or to shut it down.
Thus, there is a direct relationship between information needs of management, cost accounting objectives, and techniques and tools used for the analysis. Financial Accounting and Cost Accounting: Financial Accounting is concerned with historical cost. It consists of recording, classification (ledger) and analysis of the business transactions in a subjective manner. It presents income statements showing the financial result of the business for a particular financial year and a Balance Sheet on a specific date to exhibit the state of affairs of a business unit. It fails to throw light on the aspects of planning, control and decision making. For these purposes, we need Cost Accounting. To achieve the above objectives Cost Accounting records business expenditures in an objective manner, i.e. according to the purpose for which costs are incurred. Cost Accounting and Management: Cost Accounting provides useful data to management for taking managerial decisions in the following areas: (i) Establishing business unit’s profit goal; (ii) Determining departmental goals; (iii) Measuring and controlling business performance with the help of budgetary control; (iv) Making decisions about improvements and adjustments in the operation of the business for achieving predetermined business objectives; and
In many industries higher costs and lower profits arise due to seasonal changes in activities. The cost accountant may make an attempt to alleviate the situation by presenting figures showing costs and losses that result from irregular employment of labour, plant and machinery. The cost reports can exhibit the idle time of workers and machinery, cost of storing raw materials and finished products, unabsorbed overhead costs and general decay in the morale of personnel that result from subnormal operations. The use of budgetary control combined with cost accounting may go a long way to bring about stability in industrial activity which will ultimately benefit the shareholders, employers and the society at large. (d) Cost Accounting and expansion policy: Every business unit has to face national and international changes that occur frequently due to changes in governments’ political and economic policies. These changes have considerable effect on costs. Moreover, the management has to adopt policies to face the ever growing competition, to develop new markets for its products. The cost accountant is required to investigate and to prepare reports to keep the management abreast of the relative advantages and profitability of one policy as compared to others. (e) Budgeting: Participation of cost accounting in the formulation and execution of budgets and standards: Cost information for managerial decision making and planning is the most important justification of a sound cost accounting system.
The following diagram shows the accounting cycle by which information reaches the decision makers: The use of budget helps the management to correct inefficiencies. It helps to identify the weak areas by making a comparative study of estimated figures with the actuals. Variances are studied carefully and corrective measures are taken in time to avoid wastage and losses. We may now conclude that cost accounting is so closely linked with management that it becomes difficult to indicate where the work of the cost accountant ends and managerial control begins. In brief, it may be said that: “Cost accounting is to serve management in the execution of policies and in the comparison of actual and estimated results in order that the value of each policy may be appraised and changed to meet future conditions” – Blocker.
Gray and Ricketts establish the relationship of Management Accounting with Cost Accounting in the following language: “The historical data on labour cost might be used to estimate the labour cost for the coming year, to determine the size of work-force needed to meet anticipated production requirements and to estimate the cash requirements to meet weekly pay rolls. This represents the use of cost accounting data to develop managerial accounting data for planning decisions.” The historical data on labour costs might be compared with the estimated labour costs to determine if labour is being used effectively and efficiently. This represents the use of cost accounting data to develop managerial accounting data for control decisions. There is an intimate relationship between Cost Accounting and Management Accounting. Management Accounting communicates various information useful to the management for making decisions for the efficient running of the business. For this purpose, management accounting uses various techniques which include standard costing, marginal costing, uniform costing, budgetary control, break even and cost benefit analysis. In fact, management accounting is an extension of the managerial aspects of cost accounting; it utilizes the principles and practices of both cost accounting and financial accounting in the best interests of the business. Financial Accounting determines the financial results for a period and the state of affairs on the last day of the period. From this point of view financial accounting may be treated as Stewardship Accounting. Cost Accounting, on
the other hand, generates information for controlling operations with a view to maximising efficiency and profit. So, it may be termed as Control Accounting. Since Management Accounting communicates necessary information to the management for efficient running of the business, it is known as Decision Accounting.
(i) Determination of objectives: The objectives for which the costing system is installed are to be determined. In fact, if the objectives are not predetermined and well defined, the costing system will fail to accomplish the desired goal. (ii) Size layout and nature of the business: A close study of the size, layout and nature of the business is very much essential to design the costing system. The choice of method of costing largely depends upon the nature of the business. (iii) Production stages: Every costing system should follow the production stages because the cost at each stage of production is to be determined. The costing system should be designed in a way so that it can determine the cost at each significant stage. (iv) Organizational structure of the business: The organizational set up of the business is to be closely studied. The methods of purchase, receipt of materials, issue and storage of materials should be examined and changes, if required, are to be made so that these
The cost and financial accounts could be interlocked into a single integral accounting system. If, that is done, the results of separate sets of accounts could be reconciled by means of control accounts for accuracy.
A. Classification of Methods on the Basis of Manufacturing Process: (a) Job Costing: This is a method of costing by which the cost of a definite job, or of a specific order or a batch of finished products is determined. This method of costing is applied in those business concerns where production is carried out as per specific order. Under this method, costs are collected and recorded under a specific production order. When an order is received, production control allots a
number to it. In job costing all costs of direct materials, direct labour and other direct expenses are directly charged to the specific job or product. Job cost sheets are used for the accumulation of job costs. The job cost sheets serve a control function. This method is very much popular in enterprises engaged in house building, ship building, production of machinery and repairs. Batch costing, contract costing and composite costing are the other variations of job costing. (i) Batch Costing: Batch costing refers to that method of costing which determines the cost of a group of identical products. This method is applied to general engineering factories which produce components in economical batches for subsequent assembly. Batch costing can conveniently be applied to companies engaged in manufacturing radios, televisions, watches, cars, electronic goods, medicines, biscuits, confectionery, etc. (ii) Contract Costing: This method of costing is based on the principle of job costing. A specific contract becomes the cost unit. A particular contract is treated as a whole job and the cost of the contract is ascertained. It is also known as Terminal Costing since the job cost is completed with the completion of the work. Contract costing is used in building and civil engineering works, ship building and aircraft manufacture. (iii) Composite Costing or Multiple Costing: Under this method of costing, costs for each component or each group of components to be assembled into a final product are ascertained separately.
(iii) Single or Output Cost: This method is employed where production is uniform and consists of a single product or two or three types of similar products. The per unit cost is obtained by dividing the total cost by the total number of units manufactured. B. Classification on the Basis of Time: (a) Historical Cost: These costs represent the cost of actual operational performance. It is a method of costing under which costs are determined after they have been incurred. Historical costs are ‘post-mortem’ costs. Historical data are considered for predicting estimated costs of the alternative actions under consideration. By making comparisons, one of these alternative actions is selected and the decision is translated into action. So, in a decision-making process, historical costs play an important role. (b) Predetermined Cost: (i) Standard Costing: It is a technique where standard costs are prepared in advance and used. Standard costs are fixed on the historical data. After the production, actuals are compared with the standard costs and variances are identified. Once the variances are determined, the management finds out the reasons for such variances for taking remedial measures. So, it is a tool in the hands of the management to control cost and ensures accountability, as also efficiency in the use of factors of production. It is an extension of budgetary
control. This system of costing is useful in repetitive industries and jobbing industries. I.C.M.A.’s definition of standard costing summarizes its concept and purposes: “A pre-determined calculation of how much costs should be under specified working conditions. It is built up from an assessment of the value of cost elements and correlates technical specifications and the qualification of materials, labour and other costs to the prices and/or wage rates expected to apply during the period in which the standard cost is expected to be used. Its main purposes are to provide bases for control through variance accounting, for the valuation of stocks and work-in-progress, and in some cases, for fixing selling prices”. C. Classification for Making Managerial Decisions: (a) Marginal Costing: In marginal costing, costs are classified into fixed and variable costs. The fundamental approach of marginal costing is to relate variable costs to cost units; while fixed costs are attributed to the business in general. Variable costs are charged to production; fixed costs will be written off in full in the period to which they are attributable. Marginal costing assumes that the excess of sale price over variable cost contributes to a fund which will cover the fixed costs and provide the undertaking’s profit. In other words, fixed overhead is not allocated to cost units.
These are notional costs. They do not involve cash outlay. From this point of view, it is similar to opportunity cost. These costs are computed only for the purpose of decision making. They are also used for evaluating the performance of profit centres. Chart showing the method of costing applicable to industry:
Objectives of Material Control: A good system of material control should have the following objectives: (i) Supply of the desired quality and quantity shall be ensured for efficient and uninterrupted production.
(ii) Materials should be purchased in economic quantities to enjoy the benefits of economic purchases. (iii) Materials are to be properly stored to preserve quality and quantity arid to avoid pilferage and obsolescence. (iv) The investment in materials shall be maintained at lowest level to avoid unnecessary blockage of working capital. (v) Purchase of materials must be made at the most favourable prices under the best possible terms. (vi) Issues of materials should be properly authorised and accounted for. (vii) Materials received should be properly inspected to test the quality of materials. (viii) Payment should be made only when .payment vouchers have been properly passed by authorised officer. (ix) Payment should be made for those materials which have been received after proper inspection. Importance of Material Control: In an effective cost accounting system there must be a proper system for the control of material from the time an order is placed until the material is issued to production. Since materials represent an important asset and is the largest single item of cost in almost every manufacturing concern, the success or failure of a