
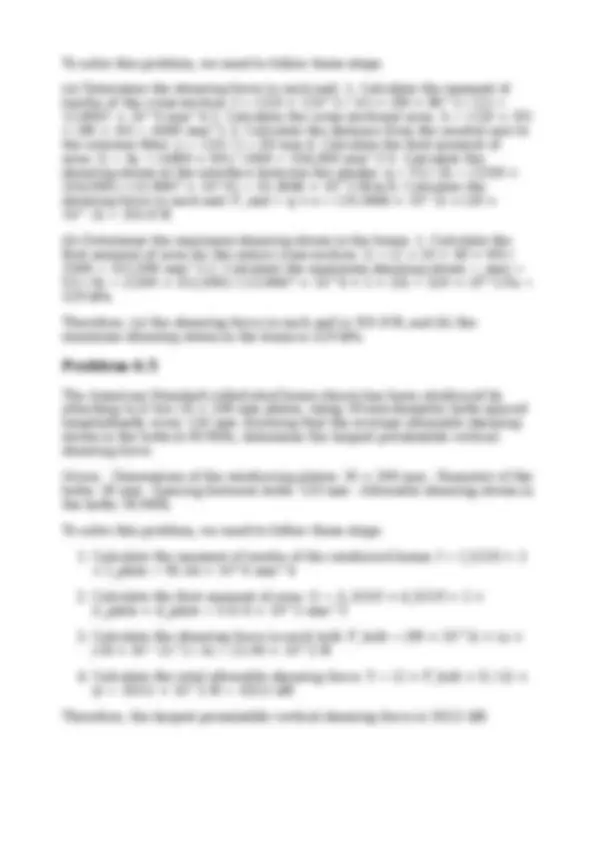
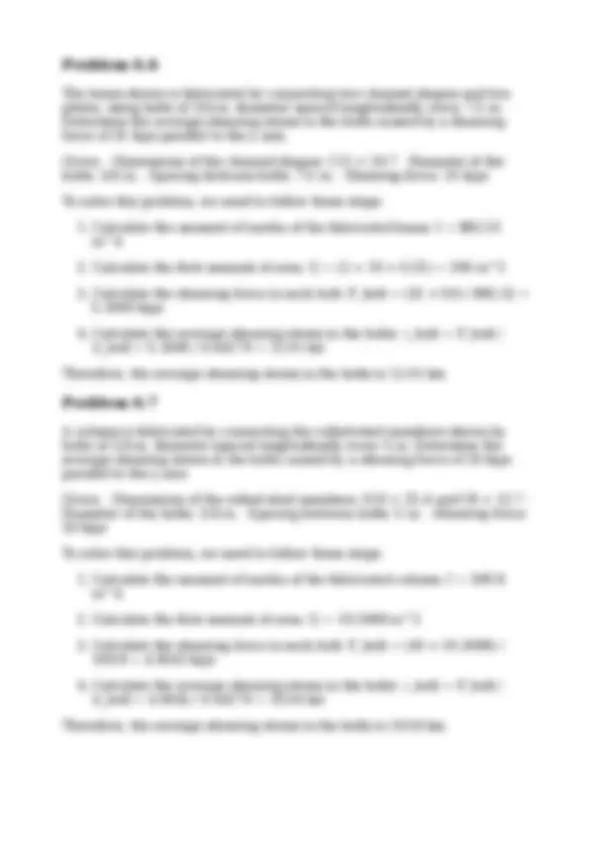
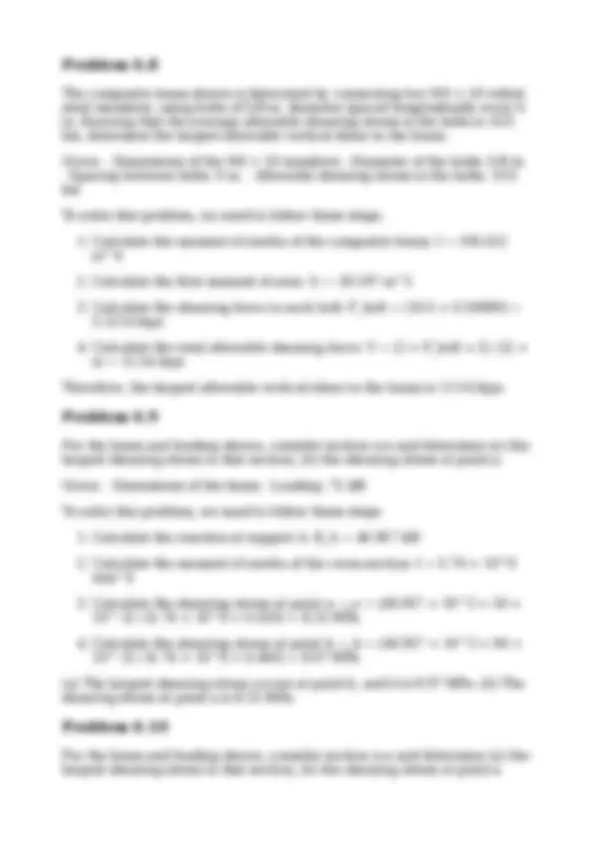
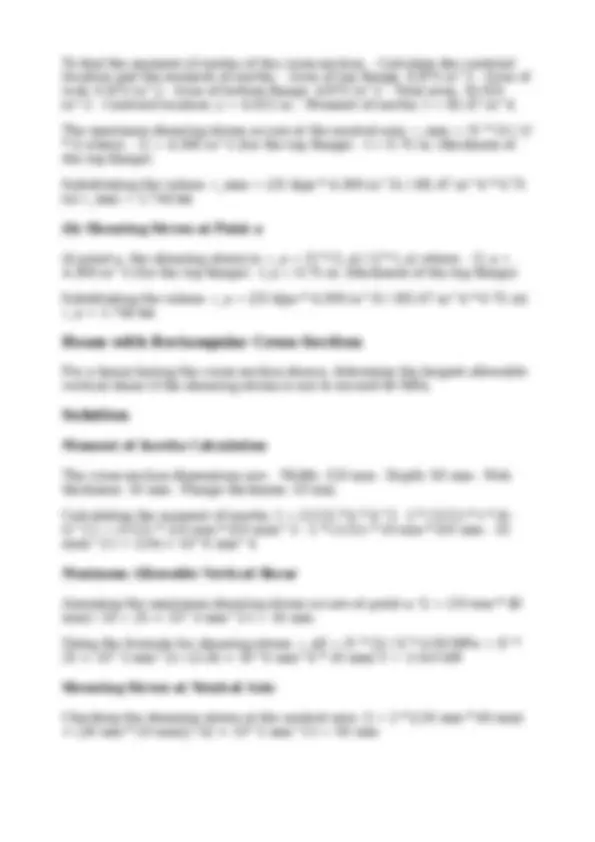
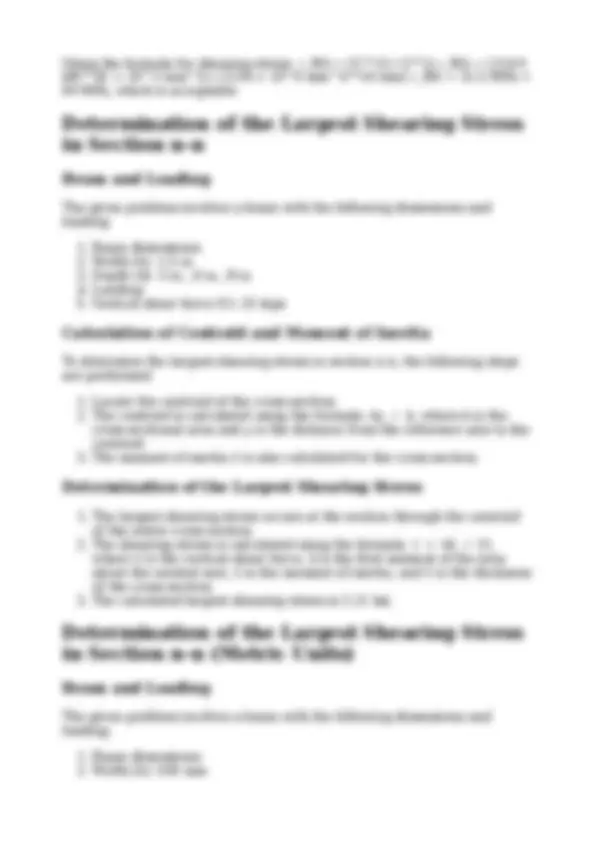
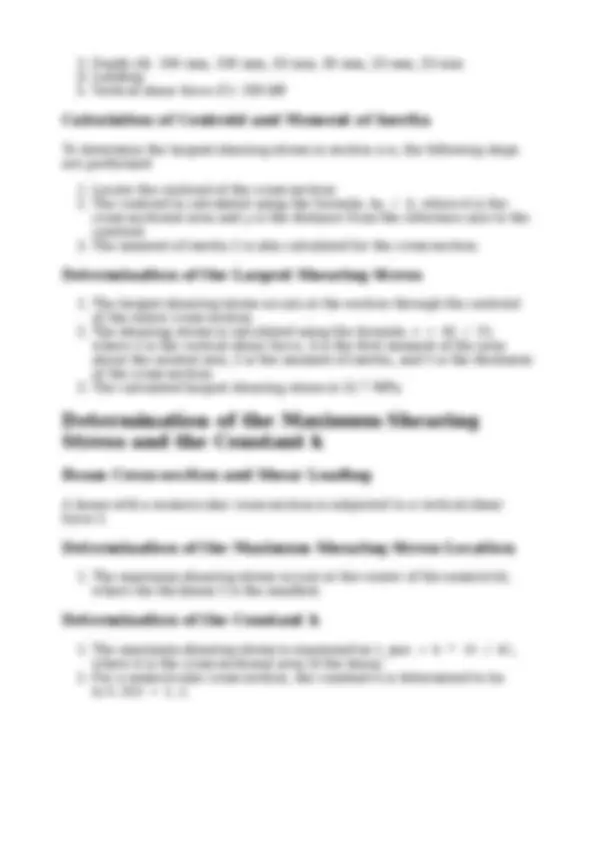
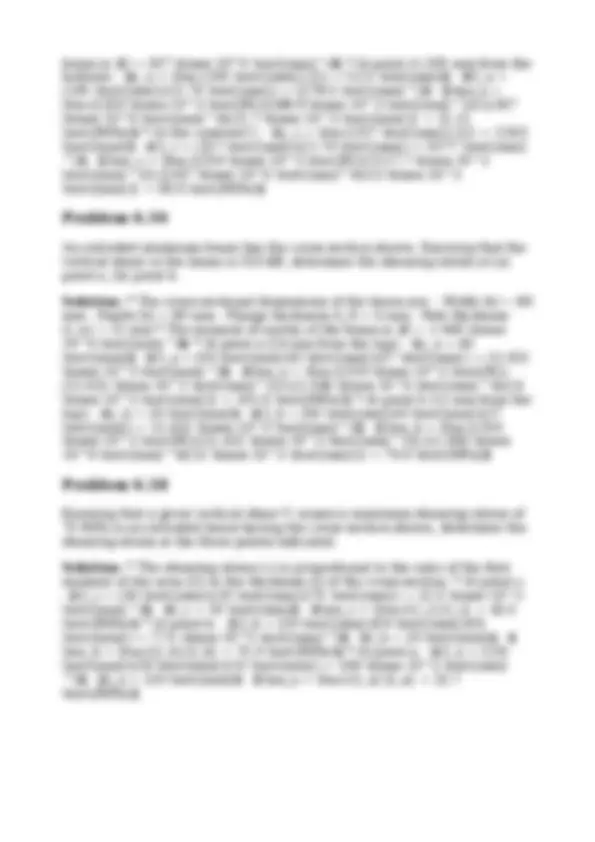
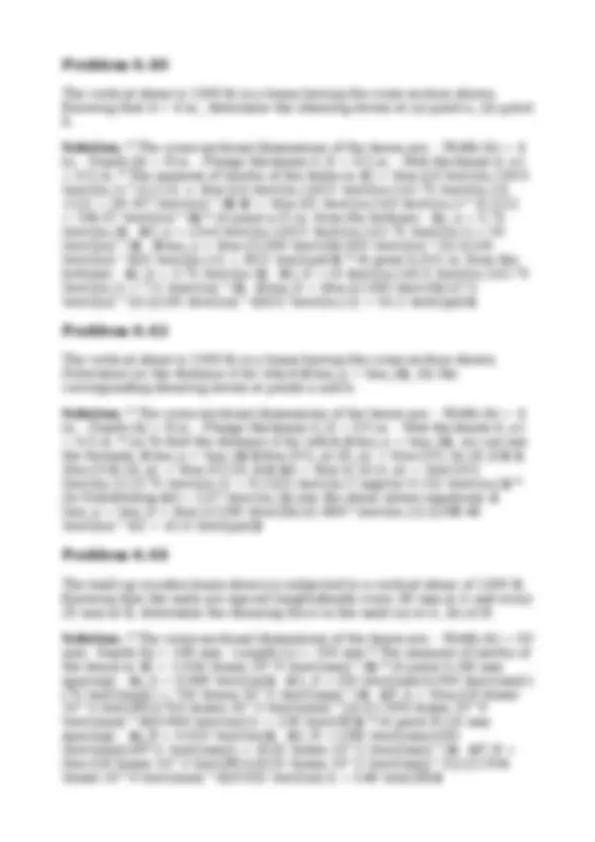
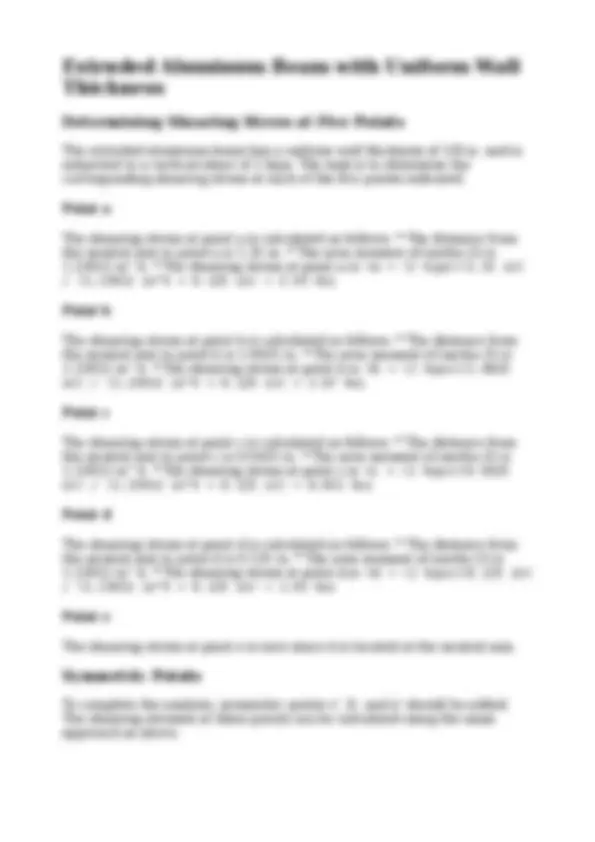
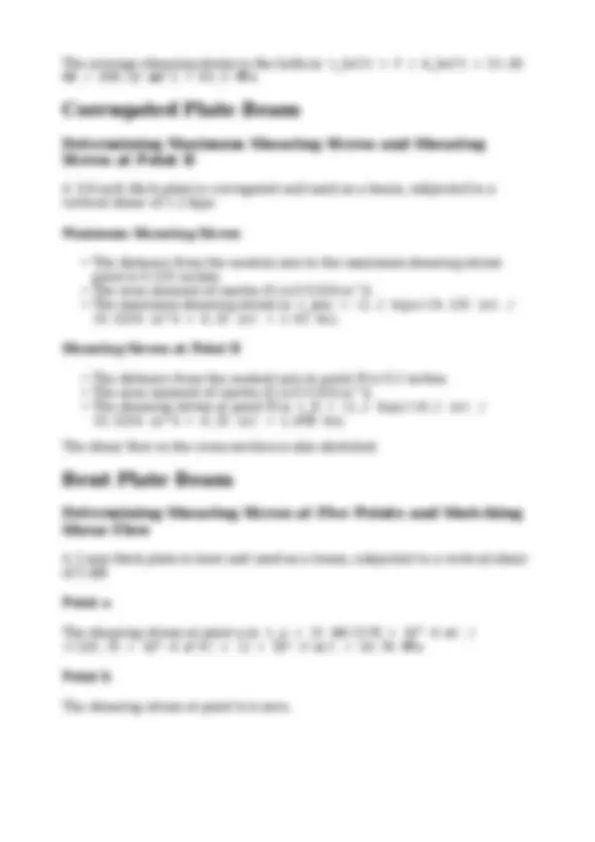
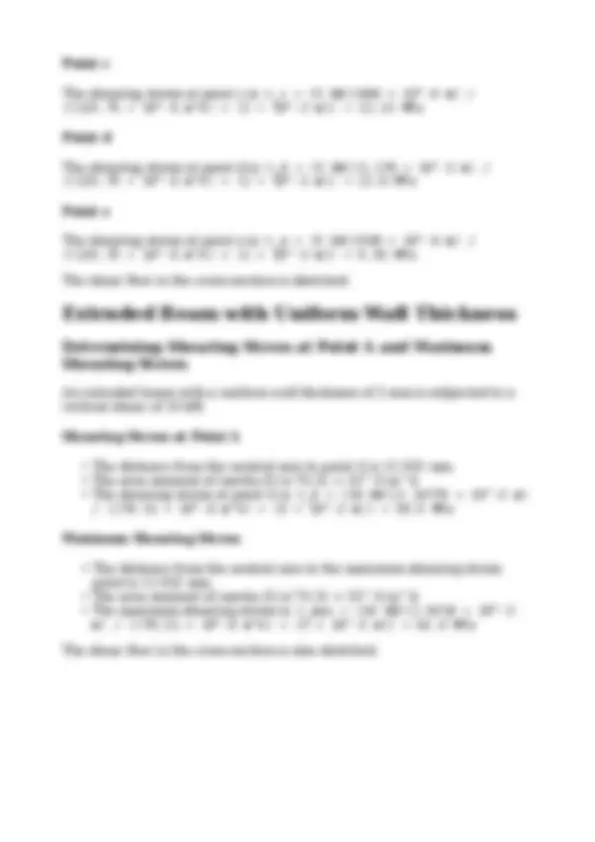
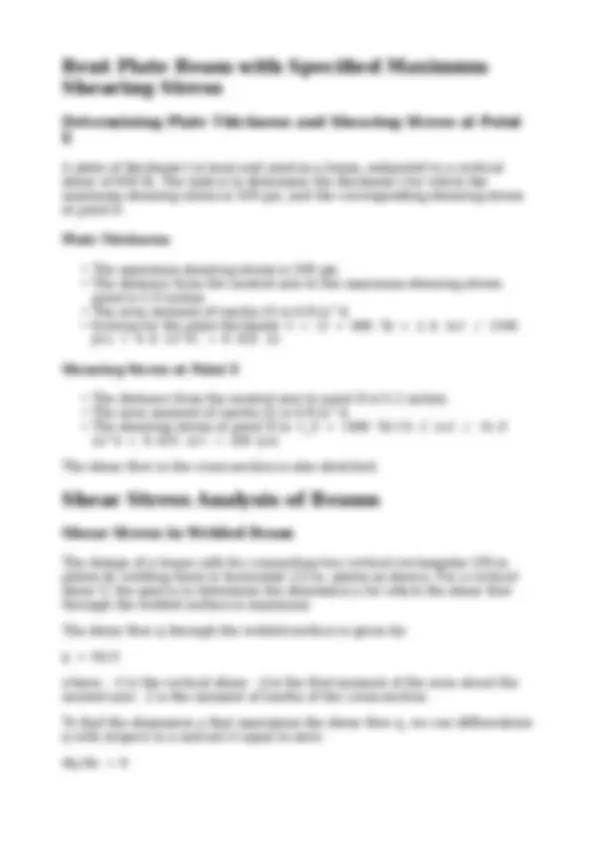
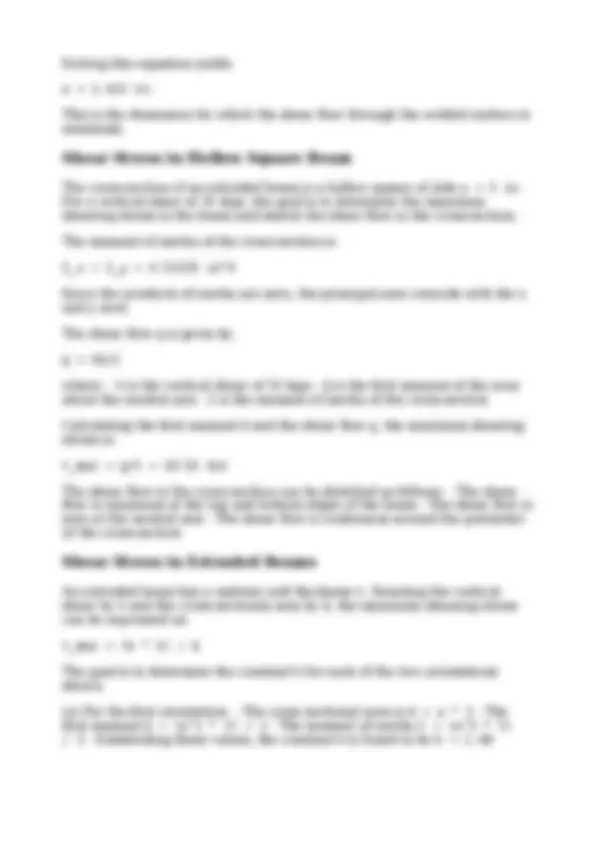
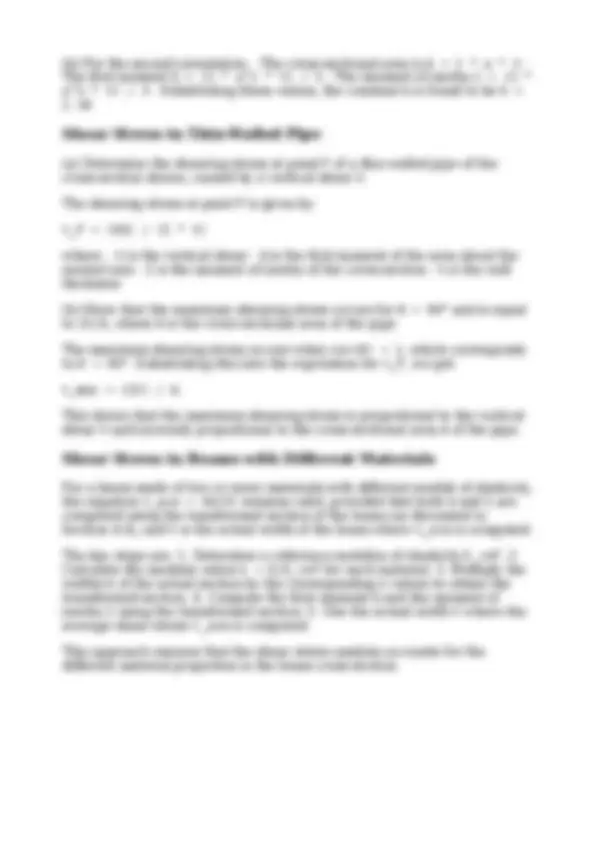
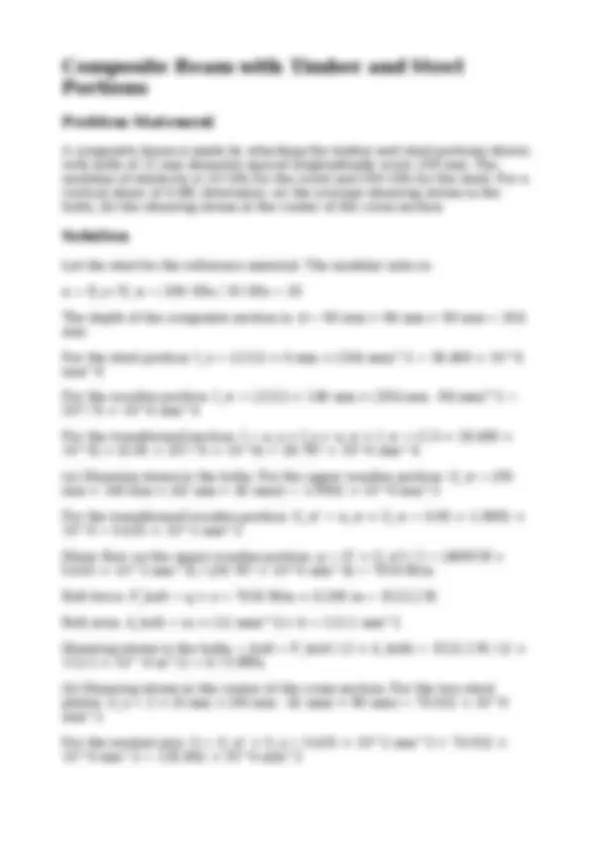
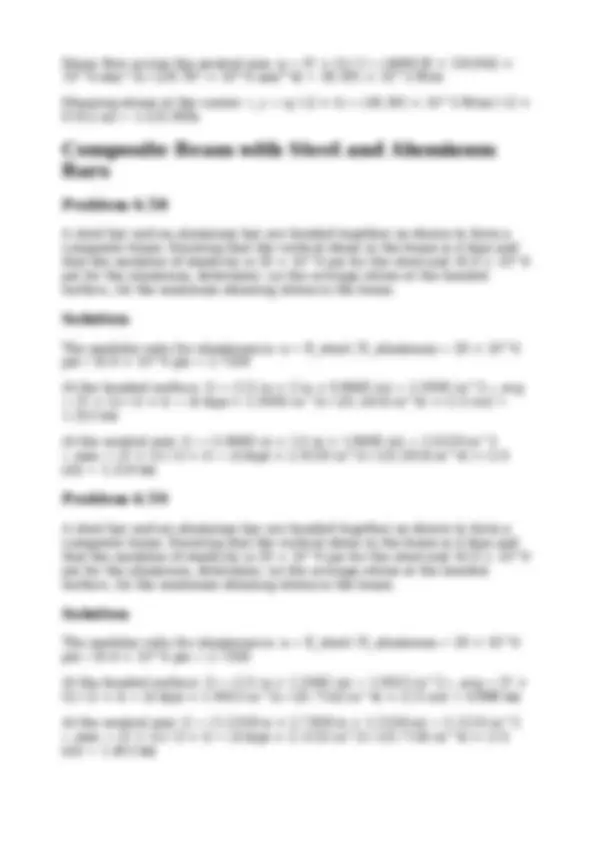
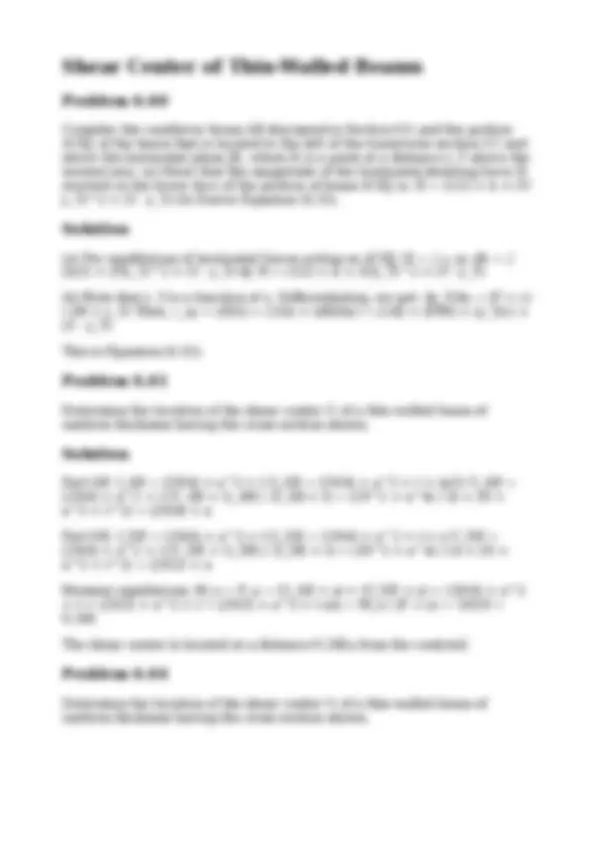
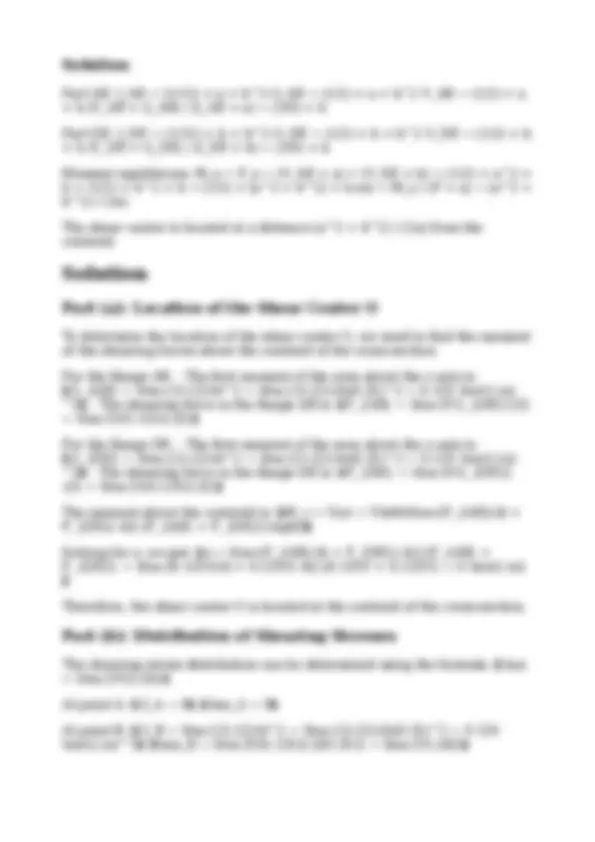
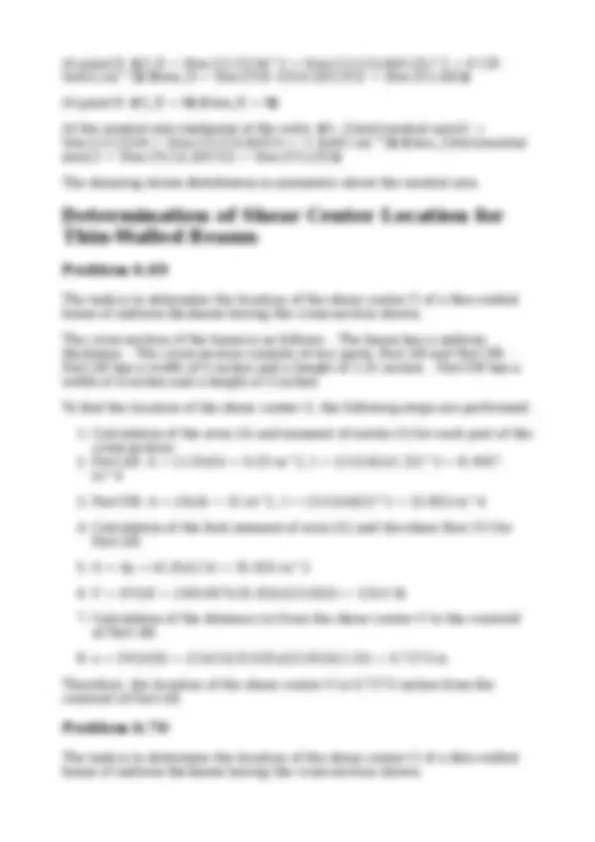
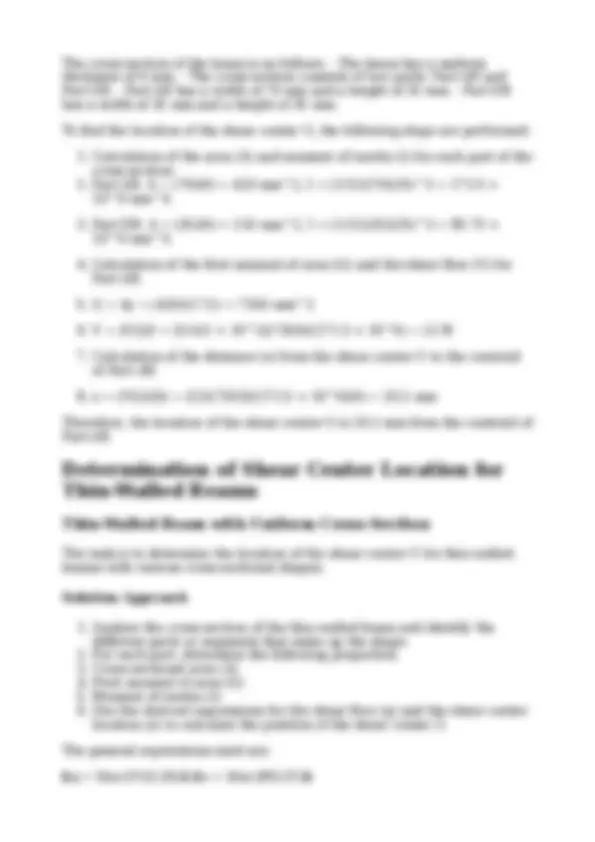
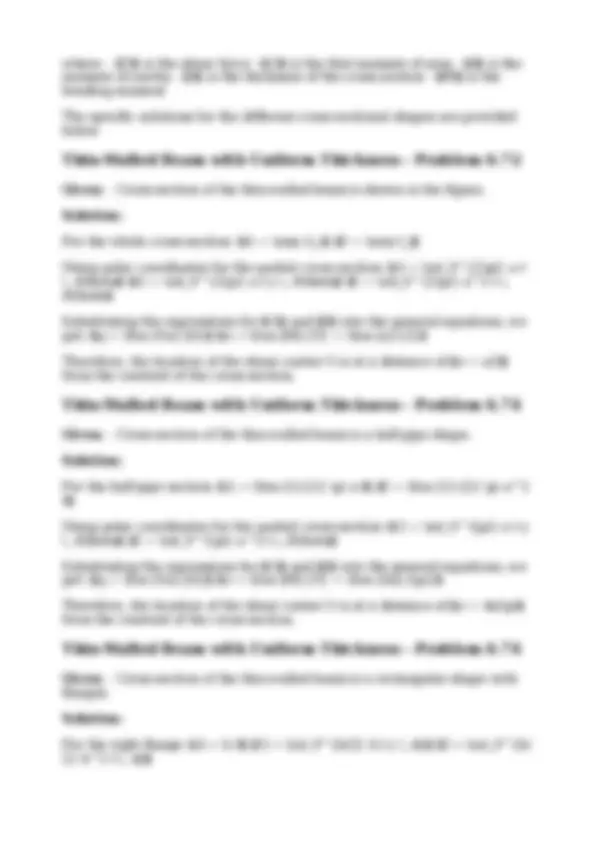
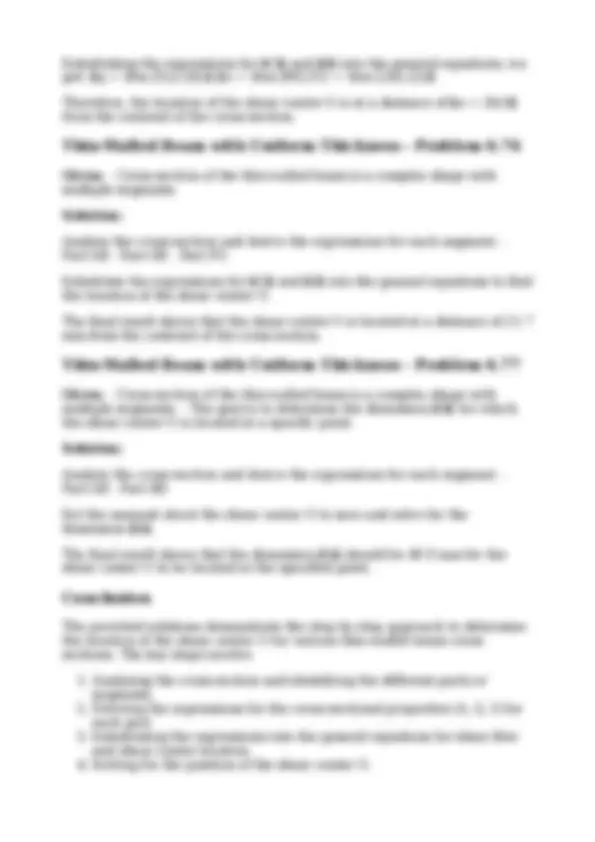
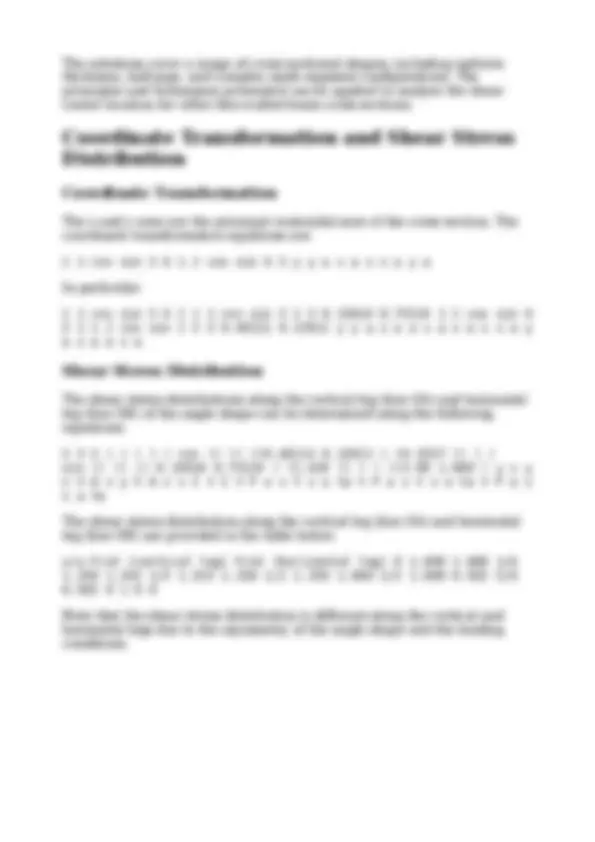
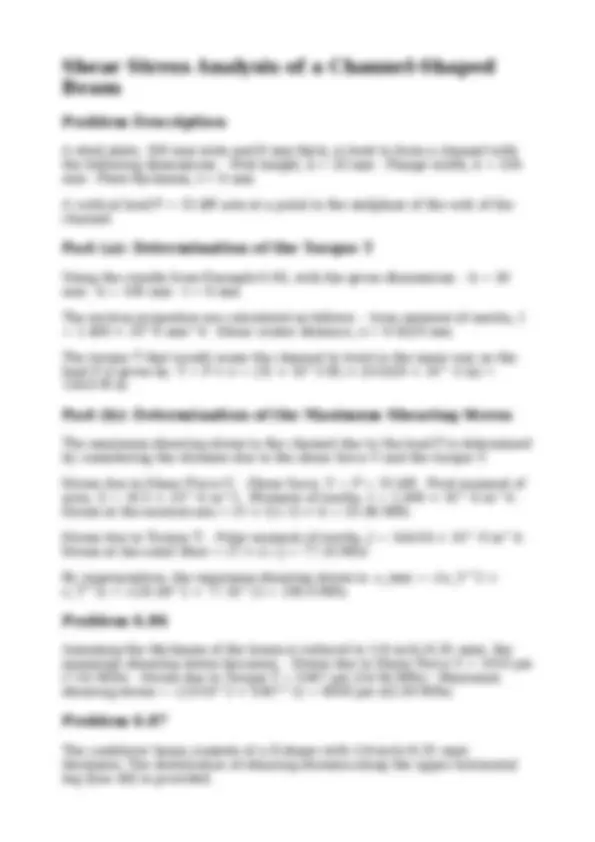
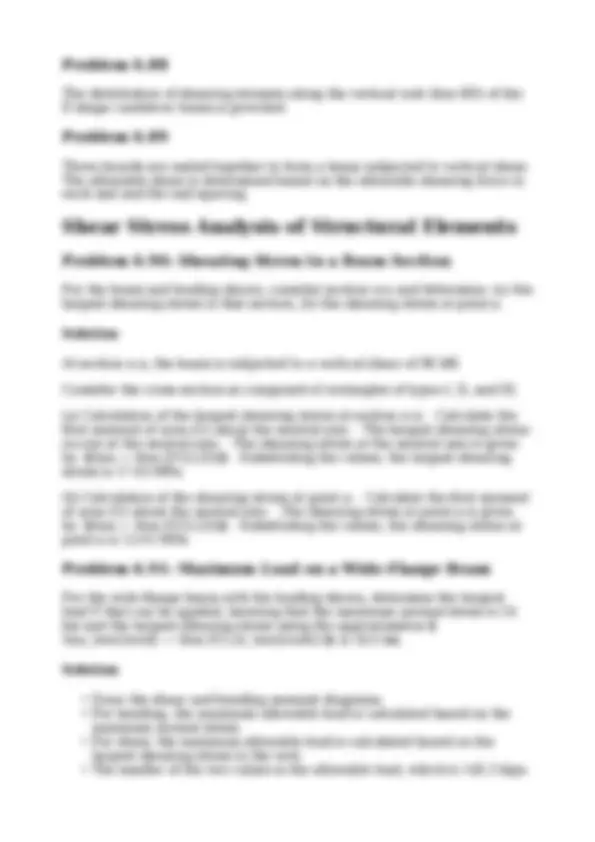
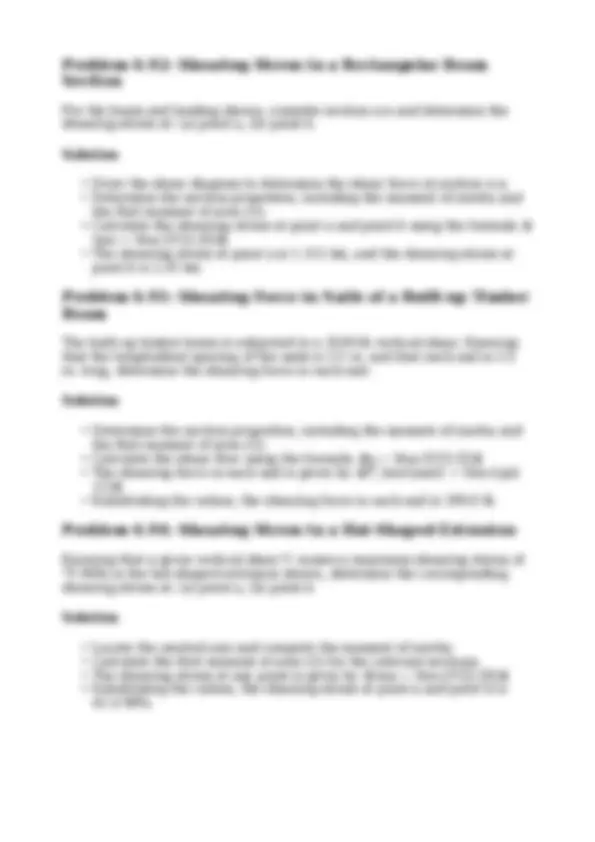
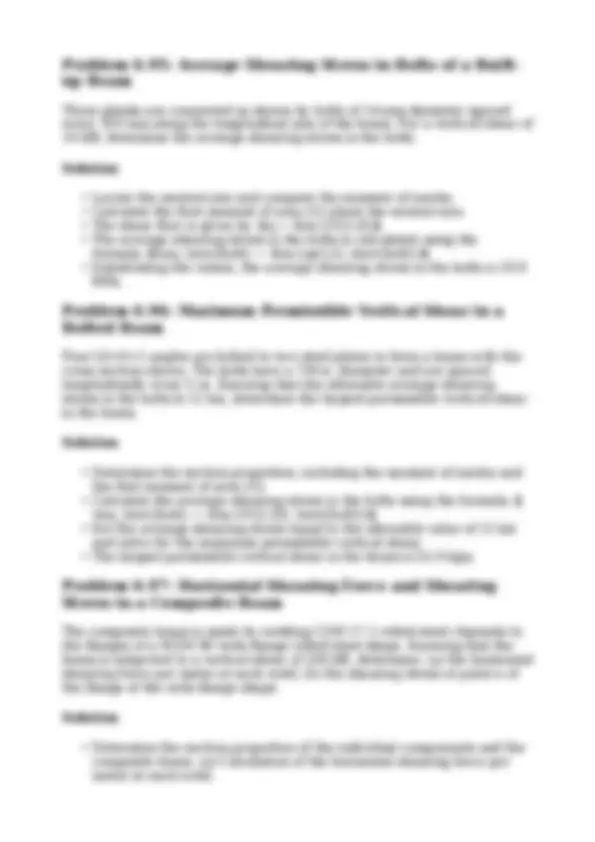
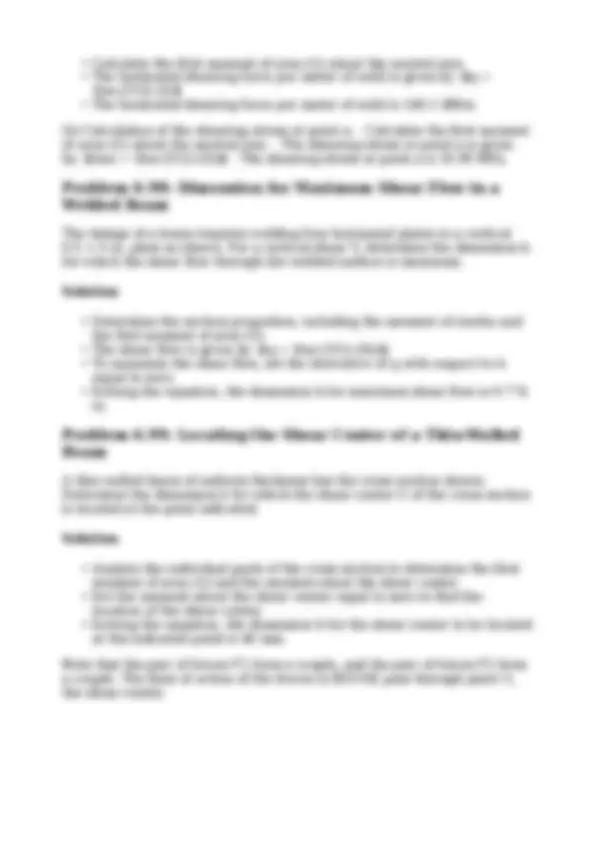
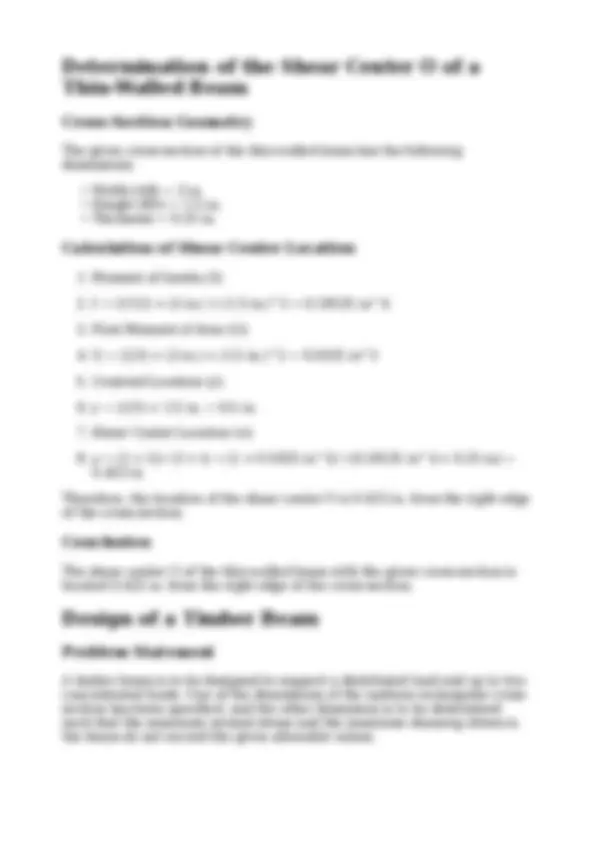
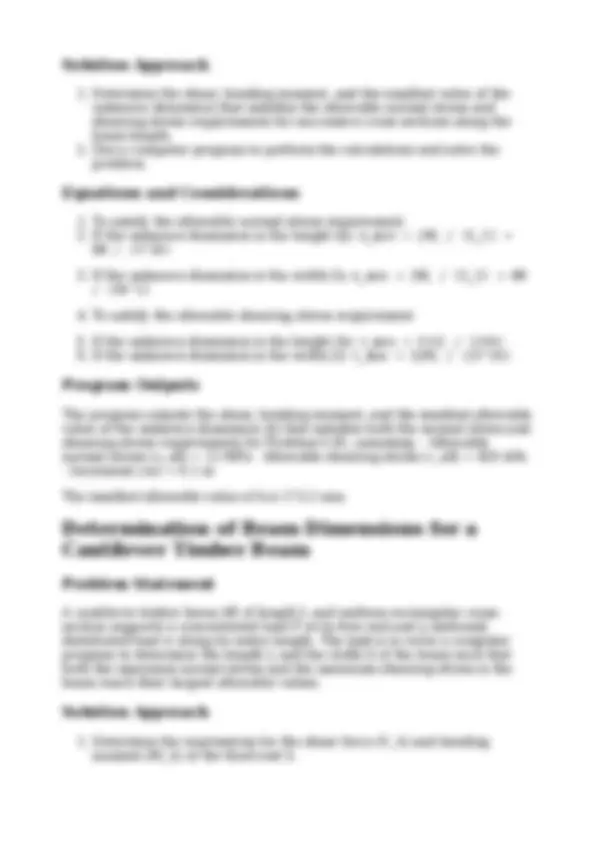
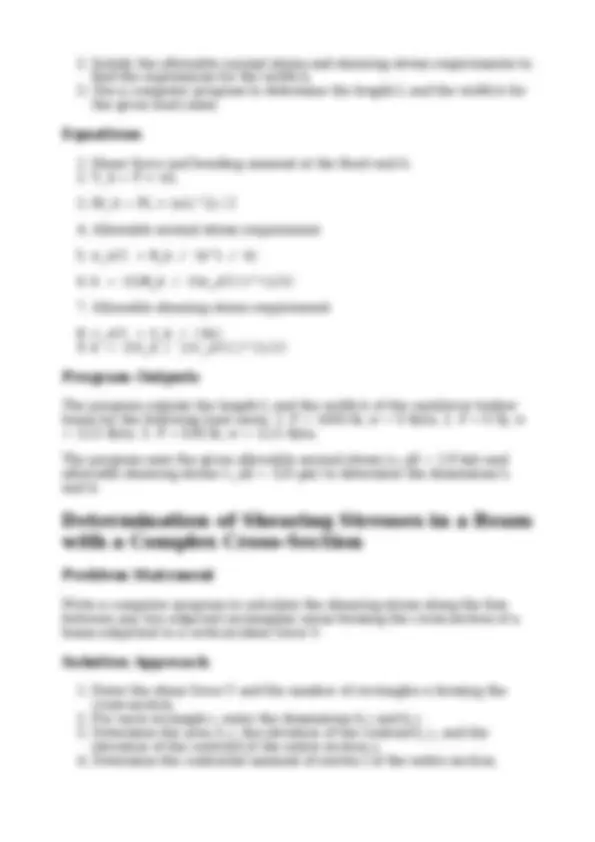
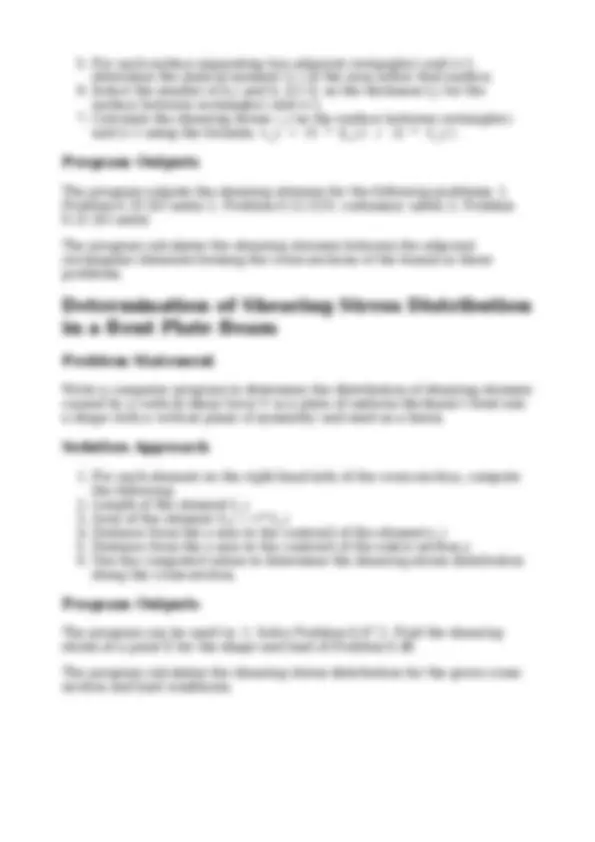
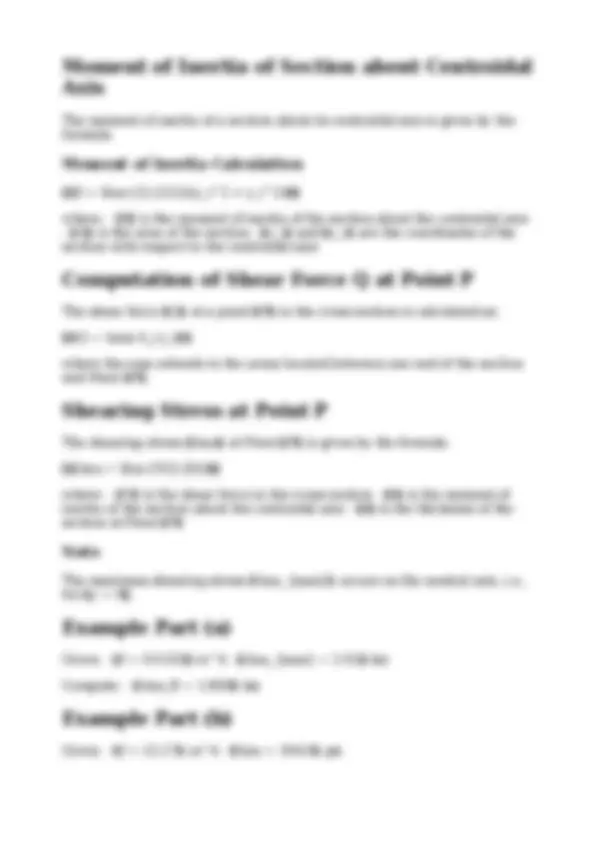
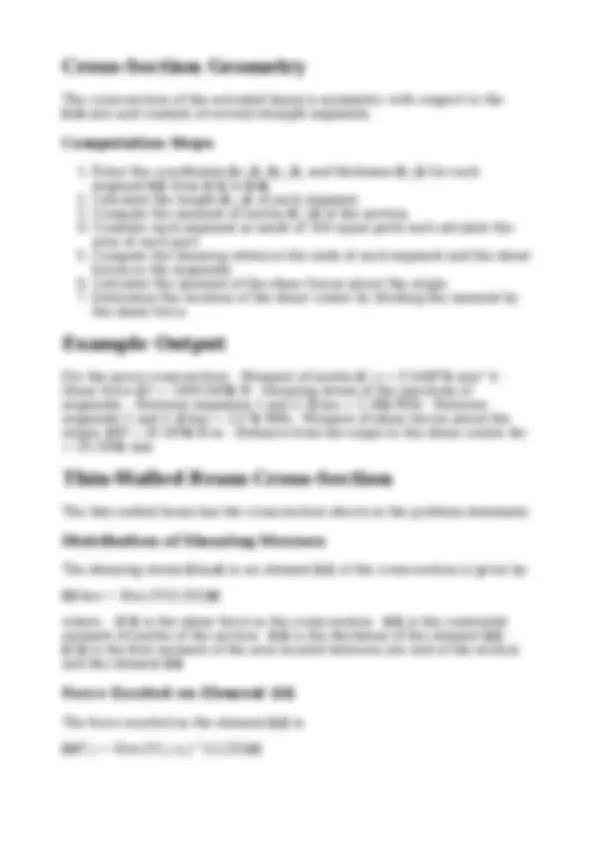
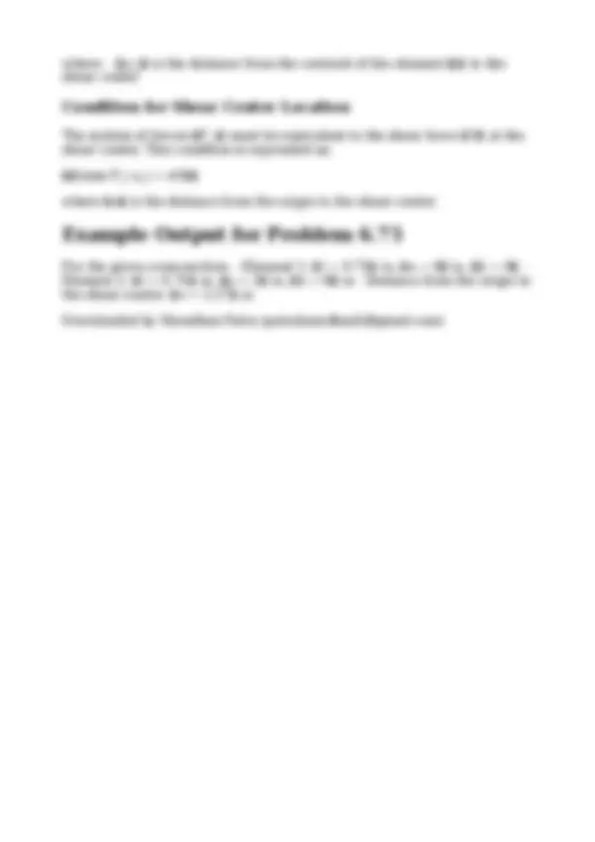
Study with the several resources on Docsity
Earn points by helping other students or get them with a premium plan
Prepare for your exams
Study with the several resources on Docsity
Earn points to download
Earn points by helping other students or get them with a premium plan
Community
Ask the community for help and clear up your study doubts
Discover the best universities in your country according to Docsity users
Free resources
Download our free guides on studying techniques, anxiety management strategies, and thesis advice from Docsity tutors
A detailed structural analysis of a composite beam, including the calculation of various parameters such as the location of the shear center, the distribution of shearing stresses, the stresses due to vertical shearing force and torque, and the analysis of the channel section and the composite beam. The analysis involves the use of various equations and formulas to determine the critical values and ensure the structural integrity of the beam. A comprehensive understanding of the structural behavior of the composite beam and the associated design considerations.
Typology: Study notes
1 / 43
This page cannot be seen from the preview
Don't miss anything!
Three full-size 50 × 100-mm boards are nailed together to form a beam that is subjected to a vertical shear of 1500 N. Knowing that the allowable shearing force in each nail is 400 N, determine the largest longitudinal spacing s that can be used between each pair of nails.
Given: - Dimensions of the boards: 50 × 100 mm - Vertical shear: 1500 N - Allowable shearing force in each nail: 400 N
To find the largest longitudinal spacing s between each pair of nails, we can use the following steps:
Calculate the moment of inertia of the cross-section: I = bh^3 / 12 = (100 × 50^3) / 12 = 28.125 × 10^6 mm^
Calculate the cross-sectional area: A = bh = 100 × 50 = 5000 mm^
Calculate the distance from the neutral axis to the extreme fiber: y = h / 2 = 50 / 2 = 25 mm
Calculate the first moment of area: Q = Ay = (5000 × 25) / 1000 = 125,000 mm^
Calculate the shearing stress at the interface between the boards: q = VQ / Ib = (1500 × 125,000) / (28.125 × 10^6) = 13.3333 × 10^3 N/m
Calculate the maximum allowable shearing force in each nail: F_nail = 2 × 400 = 800 N
Equate the shearing stress and the maximum allowable shearing force in each nail to find the largest longitudinal spacing s: q = F_nail / (2s) s = F_nail / (2q) = (800) / (2 × 13.3333 × 10^3) = 60.0 mm
Therefore, the largest longitudinal spacing s that can be used between each pair of nails is 60.0 mm.
For the built-up beam of Prob. 6.1, determine the allowable shear if the spacing between each pair of nails is s = 45 mm.
Given: - Spacing between each pair of nails: s = 45 mm - Moment of inertia: I = 28.125 × 10^6 mm^4 - First moment of area: Q = 125,000 mm^3 - Allowable shearing force in each nail: F_nail = 2 × 400 = 800 N
To find the allowable shear, we can use the following equation: V = (F_nail × I) / (Qs)
Substituting the given values: V = (800 × 28.125 × 10^6) / (125,000 × 45 × 10^-3) = 2.00 × 10^3 N = 2.00 kN
Therefore, the allowable shear is 2.00 kN.
Three boards, each 2 in. thick, are nailed together to form a beam that is subjected to a vertical shear. Knowing that the allowable shearing force in each nail is 150 lb, determine the allowable shear if the spacing s between the nails is 3 in.
Given: - Thickness of each board: 2 in. - Spacing between nails: s = 3 in. - Allowable shearing force in each nail: F_nail = 150 lb
To find the allowable shear, we can use the following steps:
Calculate the moment of inertia of the cross-section: I = bh^3 / 12 = ( × 2^3) / 12 = 112 in^
Calculate the cross-sectional area: A = bh = (6 × 2) = 12 in^
Calculate the distance from the neutral axis to the extreme fiber: y = h / 2 = 2 / 2 = 1 in
Calculate the first moment of area: Q = Ay = (12 × 1) = 12 in^
Calculate the shearing stress at the interface between the boards: q = VQ / Ib
Equate the shearing stress and the maximum allowable shearing force in each nail to find the allowable shear: q = F_nail / (2s) V = (F_nail × I) / (Qs) = (150 × 234.67) / (36 × 3) = 326 lb
Therefore, the allowable shear is 326 lb.
A square box beam is made of two 20 × 80-mm planks and two 20 × 120-mm planks nailed together as shown. Knowing that the spacing between the nails is s = 30 mm and that the vertical shear in the beam is V = 1200 N, determine (a) the shearing force in each nail, (b) the maximum shearing stress in the beam.
Given: - Dimensions of the planks: 20 × 80 mm and 20 × 120 mm - Spacing between nails: s = 30 mm - Vertical shear in the beam: V = 1200 N
The beam shown is fabricated by connecting two channel shapes and two plates, using bolts of 3/4-in. diameter spaced longitudinally every 7.5 in. Determine the average shearing stress in the bolts caused by a shearing force of 25 kips parallel to the y axis.
Given: - Dimensions of the channel shapes: C12 × 20.7 - Diameter of the bolts: 3/4 in. - Spacing between bolts: 7.5 in. - Shearing force: 25 kips
To solve this problem, we need to follow these steps:
Calculate the moment of inertia of the fabricated beam: I = 883. in^
Calculate the first moment of area: Q = (2 × 16 × 6.25) = 200 in^
Calculate the shearing force in each bolt: F_bolt = (25 × 50) / 883.33 = 5.3066 kips
Calculate the average shearing stress in the bolts: τ_bolt = F_bolt / A_bolt = 5.3066 / 0.44179 = 12.01 ksi
Therefore, the average shearing stress in the bolts is 12.01 ksi.
A column is fabricated by connecting the rolled-steel members shown by bolts of 3/4-in. diameter spaced longitudinally every 5 in. Determine the average shearing stress in the bolts caused by a shearing force of 30 kips parallel to the y axis.
Given: - Dimensions of the rolled-steel members: S10 × 25.4 and C8 × 13.7 - Diameter of the bolts: 3/4 in. - Spacing between bolts: 5 in. - Shearing force: 30 kips
To solve this problem, we need to follow these steps:
Calculate the moment of inertia of the fabricated column: I = 309. in^
Calculate the first moment of area: Q = 19.2668 in^
Calculate the shearing force in each bolt: F_bolt = (30 × 19.2668) / 309.8 = 4.6643 kips
Calculate the average shearing stress in the bolts: τ_bolt = F_bolt / A_bolt = 4.6643 / 0.44179 = 10.56 ksi
Therefore, the average shearing stress in the bolts is 10.56 ksi.
The composite beam shown is fabricated by connecting two W6 × 20 rolled- steel members, using bolts of 5/8-in. diameter spaced longitudinally every 6 in. Knowing that the average allowable shearing stress in the bolts is 10. ksi, determine the largest allowable vertical shear in the beam.
Given: - Dimensions of the W6 × 20 members - Diameter of the bolts: 5/8 in.
To solve this problem, we need to follow these steps:
Calculate the moment of inertia of the composite beam: I = 195. in^
Calculate the first moment of area: Q = 18.197 in^
Calculate the shearing force in each bolt: F_bolt = (10.5 × 0.30680) = 3.2214 kips
Calculate the total allowable shearing force: V = (2 × F_bolt × I) / (Q × s) = 11.54 kips
Therefore, the largest allowable vertical shear in the beam is 11.54 kips.
For the beam and loading shown, consider section n-n and determine (a) the largest shearing stress in that section, (b) the shearing stress at point a.
Given: - Dimensions of the beam - Loading: 72 kN
To solve this problem, we need to follow these steps:
Calculate the reaction at support A: R_A = 46.957 kN
Calculate the moment of inertia of the cross-section: I = 5.76 × 10^ mm^
Calculate the shearing stress at point a: τ_a = (46.957 × 10^3 × 30 × 10^-3) / (5.76 × 10^6 × 0.030) = 8.15 MPa
Calculate the shearing stress at point b: τ_b = (46.957 × 10^3 × 66 × 10^-3) / (5.76 × 10^6 × 0.060) = 8.97 MPa
(a) The largest shearing stress occurs at point b, and it is 8.97 MPa. (b) The shearing stress at point a is 8.15 MPa.
For the beam and loading shown, consider section n-n and determine (a) the largest shearing stress in that section, (b) the shearing stress at point a.
Q = (2 × 3 in × 7.5 in) × 4.375 in + (4.25 in × 0.25 in) × 2.125 in
Q = 14.96 in^
Maximum Shear Stress (τ_max):
τ_max = (V × Q) / (I × t) τ_max = (25 kips × 14.96 in^3) / (113.8 in^4 × 0.25 in) τ_max = 13.15 ksi
Distance from Neutral Axis to Point a:
Distance = 4.5 in + 8.203 in = 12.70 in
Shear Stress at Point a (τ_a):
τ_a = (V × Q_a) / (I × t) τ_a = (25 kips × 12.70 in^3) / (113.8 in^4 × 0.25 in) τ_a = 11.16 ksi
Conclusion
The analysis of the given beam shows that:
The largest shearing stress in section n-n is 13.15 ksi. The shearing stress at point a is 11.16 ksi.
Shear Stress Analysis of a Beam
For the beam and loading shown, consider section n-n and determine: (a) the largest shearing stress in that section, (b) the shearing stress at point a.
The beam has the following dimensions: - Length: 50 in. (10 in. + 20 in. + 20 in.) - Cross-section: Rectangular - Width: 7.25 in. - Depth: 3.75 in. (1.5 in. + 1.5 in. + 0.75 in.)
The beam is subjected to a concentrated load of 25 kips at the midpoint.
(a) Largest Shearing Stress
By symmetry, the reaction forces at the supports A and B are each 25 kips.
At section n-n, the shear force is: V = 25 kips
To find the moment of inertia of the cross-section: - Calculate the centroid location and the moment of inertia: - Area of top flange: 4.875 in^2 - Area of web: 6.875 in^2 - Area of bottom flange: 4.875 in^2 - Total area: 16. in^2 - Centroid location: y = 4.631 in. - Moment of inertia: I = 83.47 in^
The maximum shearing stress occurs at the neutral axis: τ_max = (V * Q) / (I
Substituting the values: τ_max = (25 kips * 4.366 in^3) / (83.47 in^4 * 0. in) τ_max = 1.744 ksi
(b) Shearing Stress at Point a
At point a, the shearing stress is: τ_a = (V * Q_a) / (I * t_a) where: - Q_a = 4.366 in^3 (for the top flange) - t_a = 0.75 in. (thickness of the top flange)
Substituting the values: τ_a = (25 kips * 4.366 in^3) / (83.47 in^4 * 0.75 in) τ_a = 1.744 ksi
For a beam having the cross section shown, determine the largest allowable vertical shear if the shearing stress is not to exceed 60 MPa.
Moment of Inertia Calculation
The cross-section dimensions are: - Width: 120 mm - Depth: 50 mm - Web thickness: 10 mm - Flange thickness: 10 mm
Calculating the moment of inertia: I = (1/12) * b * h^3 - 2 * (1/12) * t * (h - t)^3 I = (1/12) * 120 mm * (50 mm)^3 - 2 * (1/12) * 10 mm * (50 mm - 10 mm)^3 I = 3.04 × 10^6 mm^
Maximum Allowable Vertical Shear
Assuming the maximum shearing stress occurs at point a: Q = (10 mm * 40 mm) / 16 = 25 × 10^3 mm^3 t = 10 mm
Using the formula for shearing stress: τ_all = (V * Q) / (I * t) 60 MPa = (V * 25 × 10^3 mm^3) / (3.04 × 10^6 mm^4 * 10 mm) V = 114.0 kN
Shearing Stress at Neutral Axis
Checking the shearing stress at the neutral axis: Q = 2 * [(10 mm * 60 mm)
Depth (d): 160 mm, 100 mm, 30 mm, 30 mm, 20 mm, 20 mm Loading: Vertical shear force (V): 180 kN
To determine the largest shearing stress in section n-n, the following steps are performed:
Locate the centroid of the cross-section: The centroid is calculated using the formula: Ay / A, where A is the cross-sectional area and y is the distance from the reference axis to the centroid. The moment of inertia I is also calculated for the cross-section.
The largest shearing stress occurs at the section through the centroid of the entire cross-section. The shearing stress is calculated using the formula: τ = VQ / It, where V is the vertical shear force, Q is the first moment of the area about the neutral axis, I is the moment of inertia, and t is the thickness of the cross-section. The calculated largest shearing stress is 32.7 MPa.
Determination of the Maximum Shearing
Stress and the Constant k
A beam with a semicircular cross-section is subjected to a vertical shear force V.
The maximum shearing stress occurs at the center of the semicircle, where the thickness t is the smallest.
The maximum shearing stress is expressed as τ_max = k * (V / A), where A is the cross-sectional area of the beam. For a semicircular cross-section, the constant k is determined to be 4/3.333 = 1.2.
Determination of the Maximum Shearing
Stress and the Constant k (Thin-Walled
Circular Section)
A beam with a thin-walled circular cross-section is subjected to a vertical shear force V.
The maximum shearing stress occurs at the neutral axis, where the thickness t is the smallest.
The maximum shearing stress is expressed as τ_max = k * (V / A), where A is the cross-sectional area of the beam. For a thin-walled circular cross-section, the constant k is determined to be 2.0.
Determination of the Maximum Shearing
Stress and the Constant k (Rectangular Cross-
section)
A beam with a rectangular cross-section is subjected to a vertical shear force V.
The maximum shearing stress occurs at a distance of h/4 from the neutral axis, where h is the depth of the beam.
The maximum shearing stress is expressed as τ_max = k * (V / A), where A is the cross-sectional area of the beam. For a rectangular cross-section, the constant k is determined to be 1.5.
beam is: $I = 367 \times 10^6 \text{mm}^4$ * At point A (105 mm from the bottom): - $y_a = \frac{105 \text{mm}}{2} = 52.5 \text{mm}$ - $Q_a = (105 \text{mm})(21.70 \text{mm}) = 2278.5 \text{mm}^2$ - $\tau_a = \frac{(250 \times 10^3 \text{N})(388.8 \times 10^3 \text{mm}^3)}{( \times 10^6 \text{mm}^4)(21.7 \times 10^3 \text{mm})} = 12. \text{MPa}$ * At the centroid C: - $y_c = \frac{257 \text{mm}}{2} = 128. \text{mm}$ - $Q_c = (257 \text{mm})(21.70 \text{mm}) = 5577 \text{mm} ^2$ - $\tau_c = \frac{(250 \times 10^3 \text{N})(1117.7 \times 10^ \text{mm}^3)}{(367 \times 10^6 \text{mm}^4)(13 \times 10^ \text{mm})} = 58.6 \text{MPa}$
An extruded aluminum beam has the cross section shown. Knowing that the vertical shear in the beam is 150 kN, determine the shearing stress at (a) point a, (b) point b.
Solution: * The cross-sectional dimensions of the beam are: - Width (b) = 80 mm - Depth (h) = 80 mm - Flange thickness (t_f) = 6 mm - Web thickness (t_w) = 12 mm * The moment of inertia of the beam is: $I = 1.946 \times 10^6 \text{mm}^4$ * At point a (24 mm from the top): - $y_a = 40 \text{mm}$ - $Q_a = (56 \text{mm})(6 \text{mm})(37 \text{mm}) = 31. \times 10^3 \text{mm}^3$ - $\tau_a = \frac{(150 \times 10^3 \text{N}) (31.632 \times 10^3 \text{mm}^3)}{(1.946 \times 10^6 \text{mm}^4)( \times 10^3 \text{mm})} = 101.6 \text{MPa}$ * At point b (12 mm from the top): - $y_b = 20 \text{mm}$ - $Q_b = (56 \text{mm})(6 \text{mm})( \text{mm}) = 12.432 \times 10^3 \text{mm}^3$ - $\tau_b = \frac{( \times 10^3 \text{N})(12.432 \times 10^3 \text{mm}^3)}{(1.946 \times 10^6 \text{mm}^4)(12 \times 10^3 \text{mm})} = 79.9 \text{MPa}$
Knowing that a given vertical shear V causes a maximum shearing stress of 75 MPa in an extruded beam having the cross section shown, determine the shearing stress at the three points indicated.
Solution: * The shearing stress (τ) is proportional to the ratio of the first moment of the area (Q) to the thickness (t) of the cross-section. * At point c:
The vertical shear is 1200 lb in a beam having the cross section shown. Knowing that d = 4 in., determine the shearing stress at (a) point a, (b) point b.
Solution: * The cross-sectional dimensions of the beam are: - Width (b) = 4 in. - Depth (h) = 8 in. - Flange thickness (t_f) = 0.5 in. - Web thickness (t_w) = 0.5 in. * The moment of inertia of the beam is: $I = \frac{(4 \text{in.})(0. \text{in.})^3}{12} + \frac{(4 \text{in.})(0.5 \text{in.})(3.75 \text{in.})} {12} = 28.167 \text{in}^4$ $I = \frac{(5 \text{in.})(4 \text{in.})^3}{12} = 106.67 \text{in}^4$ * At point a (5 in. from the bottom): - $y_a = 3. \text{in.}$ - $Q_a = (2)(4 \text{in.})(0.5 \text{in.})(3.75 \text{in.}) = 55 \text{in}^3$ - $\tau_a = \frac{(1200 \text{lb})(55 \text{in}^3)}{( \text{in}^4)(5 \text{in.})} = 40.5 \text{psi}$ * At point b (0.5 in. from the bottom): - $y_b = 3.75 \text{in.}$ - $Q_b = (4 \text{in.})(0.5 \text{in.})(3. \text{in.}) = 7.5 \text{in}^3$ - $\tau_b = \frac{(1200 \text{lb})(7. \text{in}^3)}{(326 \text{in}^4)(0.5 \text{in.})} = 55.2 \text{psi}$
The vertical shear is 1200 lb in a beam having the cross section shown. Determine (a) the distance d for which $\tau_a = \tau_b$, (b) the corresponding shearing stress at points a and b.
Solution: * The cross-sectional dimensions of the beam are: - Width (b) = 4 in. - Depth (h) = 8 in. - Flange thickness (t_f) = 0.5 in. - Web thickness (t_w) = 0.5 in. * (a) To find the distance d for which $\tau_a = \tau_b$, we can use the formula: $\tau_a = \tau_b$ $\frac{VQ_a}{It_a} = \frac{VQ_b}{It_b}$ $ \frac{Vd}{It_a} = \frac{V}{It_b}$ $d = \frac{t_b}{t_a} = \frac{0. \text{in.}}{3.75 \text{in.}} = 0.1333 \text{in.} \approx 0.133 \text{in.}$ * (b) Substituting $d = 2.67 \text{in.}$ into the shear stress equations: $ \tau_a = \tau_b = \frac{(1200 \text{lb})(2.6667 \text{in.})}{(288. \text{in}^4)} = 41.6 \text{psi}$
The built-up wooden beam shown is subjected to a vertical shear of 1200 lb. Knowing that the nails are spaced longitudinally every 60 mm at A and every 25 mm at B, determine the shearing force in the nails (a) at A, (b) at B.
Solution: * The cross-sectional dimensions of the beam are: - Width (b) = 50 mm - Depth (h) = 100 mm - Length (L) = 150 mm * The moment of inertia of the beam is: $I = 1.504 \times 10^9 \text{mm}^4$ * At point A (60 mm spacing): - $s_A = 0.060 \text{m}$ - $Q_A = (50 \text{mm})(100 \text{mm}) (75 \text{mm}) = 750 \times 10^3 \text{mm}^3$ - $F_A = \frac{(8 \times 10^3 \text{N})(750 \times 10^3 \text{mm}^3)}{(1.504 \times 10^ \text{mm}^4)(0.060 \text{m})} = 239 \text{N}$ * At point B (25 mm spacing): - $s_B = 0.025 \text{m}$ - $Q_B = (300 \text{mm})( \text{mm})(87.5 \text{mm}) = 4125 \times 10^3 \text{mm}^3$ - $F_B = \frac{(8 \times 10^3 \text{N})(4125 \times 10^3 \text{mm}^3)}{(1. \times 10^9 \text{mm}^4)(0.025 \text{m})} = 549 \text{N}$
Thin-Walled Member with Given Cross-Section
A thin-walled member has the given cross-section, and the maximum shearing stress is known to be 50 MPa due to a vertical shear V.
Point a
The shearing stress at point a is calculated as follows: * The distance from the neutral axis to point a is 18 mm. * The area moment of inertia (I) is 49.35 mm^4. * The shearing stress at point a is: τa = (50 MPa)(18 mm) / (49.35 mm^4 × 10 mm) = 18.23 MPa
Point b
The shearing stress at point b is calculated as follows: * The distance from the neutral axis to point b is 12 mm. * The area moment of inertia (I) is 49.35 mm^4. * The shearing stress at point b is: τb = (50 MPa)(12 mm) / (49.35 mm^4 × 10 mm) = 14.59 MPa
Point c
The shearing stress at point c is calculated as follows: * The distance from the neutral axis to point c is 45.6 mm. * The area moment of inertia (I) is 49.35 mm^4. * The shearing stress at point c is: τc = (50 MPa)(45.6 mm) / (49.35 mm^4 × 12 mm) = 46.2 MPa
Beam with Three Planks Connected by Bolts
A beam consists of three planks connected by bolts of 3/8-inch diameter spaced every 6 inches along the longitudinal axis. The beam is subjected to a vertical shear of 2.5 kips.
The average shearing stress in the bolts is calculated as follows: * The moment of inertia (I) of the cross-section is 566.67 in^4. * The distance from the neutral axis to the bolts is 30 inches. * The shear force on each bolt is: F = (2.5 kips)(30 in)(6 in) / 566.67 in^4 = 0.79411 kips * The bolt area is: A_bolt = π(3/8 in)^2 / 4 = 0.110447 in^2 * The average shearing stress in the bolts is: τ_bolt = F / A_bolt = 0.79411 kips / 0.110447 in^2 = 7.19 ksi
Beam with Three Planks Connected by Steel
Bolts
A beam consists of three planks connected by steel bolts with a longitudinal spacing of 225 mm. The vertical shear in the beam is 6 kN, and the allowable average shearing stress in each bolt is 60 MPa.
The smallest permissible bolt diameter is calculated as follows: * The moment of inertia (I) of the cross-section is 75.00 × 10^6 mm^4. * The distance from the neutral axis to the bolts is 37.50 mm. * The shear force on each bolt is: F = (6 kN)(37.50 mm)(0.225 m) / (75.00 × 10^6 mm^4) = 64.286 N * The bolt area is: A_bolt = π(d_bolt^2) / 4 * Solving for the bolt diameter: d_bolt = √(4 × 64.286 N / (π × 60 MPa)) = 9.05 mm Therefore, the smallest permissible bolt diameter is 9.05 mm.
Beam with Five Planks Connected by Steel
Bolts
A beam consists of five planks of 1.5/6-inch cross-section connected by steel bolts with a longitudinal spacing of 9 inches. The vertical shear in the beam is 2000 lb, and the allowable average shearing stress in each bolt is 7500 psi.
The smallest permissible bolt diameter is calculated as follows: * The moment of inertia (I) of the cross-section is 160.2 in^4. * The distance from the neutral axis to the bolts is 4.2 inches. * The shear force on each bolt is: F = (2000 lb)(7.2 in)(9 in) / 160.2 in^4 = 809 lb * The bolt area is: A_bolt = π(d_bolt^2) / 4 * Solving for the bolt diameter: d_bolt = √( × 809 lb / (π × 7500 psi)) = 0.371 in Therefore, the smallest permissible bolt diameter is 0.371 inches.
Beam with Steel Angle Shapes and Plate
A beam is formed by connecting 102 × 9.5 steel angle shapes and a 12 × 400-mm plate using bolts of 22-mm diameter spaced longitudinally every 120 mm. The beam is subjected to a vertical shear of 240 kN.
The average shearing stress in each bolt is calculated as follows: * The moment of inertia (I) of the cross-section is 287.06 × 10^6 mm^4. * The distance from the neutral axis to the bolts is 315.5 mm. * The shear force on each bolt is: F = (240 kN)(315.5 × 10^3 mm) / (287.06 × 10^6 mm^4) = 31.65 kN * The bolt area is: A_bolt = π(22 mm)^2 / 4 = 380.13 mm^2 *
Point c
The shearing stress at point c is: τ_c = (5 kN)(600 × 10^-6 m) / ((133.75 × 10^-6 m^4) × (2 × 10^-3 m)) = 11.21 MPa
Point d
The shearing stress at point d is: τ_d = (5 kN)(1.176 × 10^-3 m) / ((133.75 × 10^-6 m^4) × (2 × 10^-3 m)) = 22.0 MPa
Point e
The shearing stress at point e is: τ_e = (5 kN)(500 × 10^-6 m) / ((133.75 × 10^-6 m^4) × (2 × 10^-3 m)) = 9.35 MPa
The shear flow in the cross-section is sketched.
Extruded Beam with Uniform Wall Thickness
An extruded beam with a uniform wall thickness of 3 mm is subjected to a vertical shear of 10 kN.
Shearing Stress at Point A
The distance from the neutral axis to point A is 11.932 mm. The area moment of inertia (I) is 70.31 × 10^-6 m^4. The shearing stress at point A is: τ_A = (10 kN)(2.14776 × 10^-3 m) / ((70.31 × 10^-6 m^4) × (3 × 10^-3 m)) = 50.9 MPa
Maximum Shearing Stress
The distance from the neutral axis to the maximum shearing stress point is 11.932 mm. The area moment of inertia (I) is 70.31 × 10^-6 m^4. The maximum shearing stress is: τ_max = (10 kN)(2.6318 × 10^- m) / ((70.31 × 10^-6 m^4) × (3 × 10^-3 m)) = 62.4 MPa
The shear flow in the cross-section is also sketched.
Bent Plate Beam with Specified Maximum
Shearing Stress
A plate of thickness t is bent and used as a beam, subjected to a vertical shear of 600 lb. The task is to determine the thickness t for which the maximum shearing stress is 300 psi, and the corresponding shearing stress at point E.
Plate Thickness
The maximum shearing stress is 300 psi. The distance from the neutral axis to the maximum shearing stress point is 2.6 inches. The area moment of inertia (I) is 4.8 in^4. Solving for the plate thickness: t = (2 × 600 lb × 2.6 in) / ( psi × 4.8 in^4) = 0.433 in
Shearing Stress at Point E
The distance from the neutral axis to point E is 5.2 inches. The area moment of inertia (I) is 4.8 in^4. The shearing stress at point E is: τ_E = (600 lb)(5.2 in) / (4. in^4 × 0.433 in) = 180 psi
The shear flow in the cross-section is also sketched.
Shear Stress Analysis of Beams
The design of a beam calls for connecting two vertical rectangular 3/8-in. plates by welding them to horizontal 1/2-in. plates as shown. For a vertical shear V, the goal is to determine the dimension a for which the shear flow through the welded surface is maximum.
The shear flow q through the welded surface is given by:
q = VQ/I
where: - V is the vertical shear - Q is the first moment of the area about the neutral axis - I is the moment of inertia of the cross-section
To find the dimension a that maximizes the shear flow q, we can differentiate q with respect to a and set it equal to zero:
dq/da = 0