
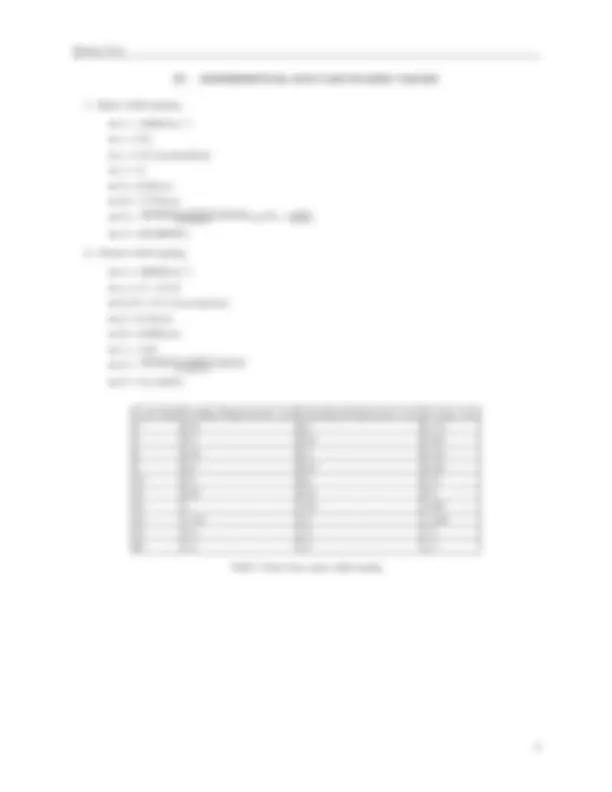
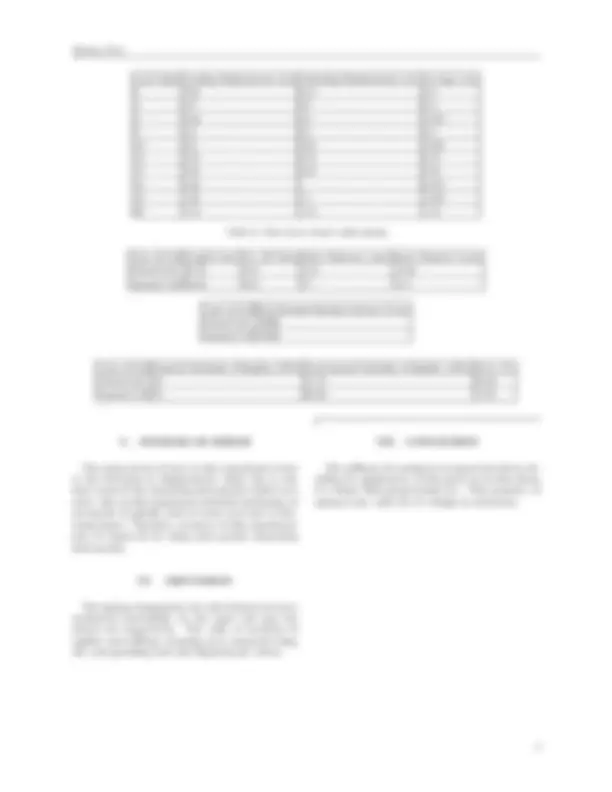
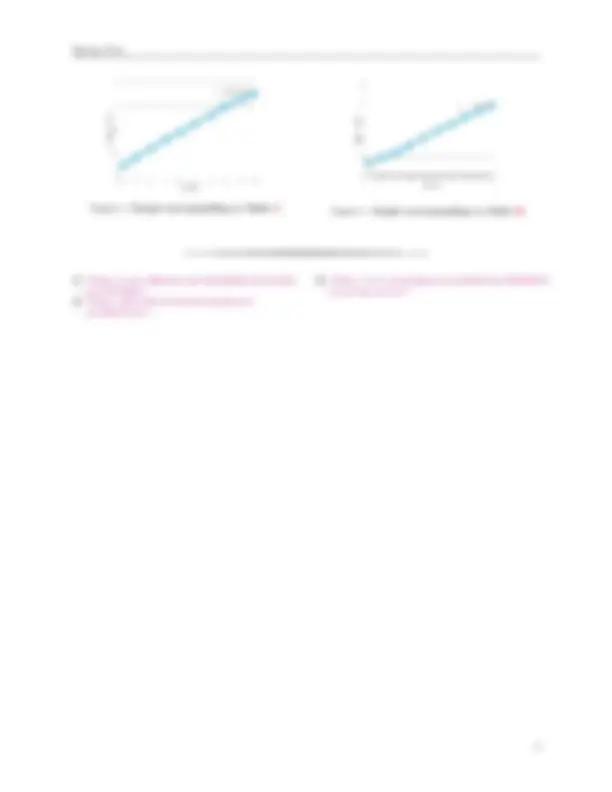
Study with the several resources on Docsity
Earn points by helping other students or get them with a premium plan
Prepare for your exams
Study with the several resources on Docsity
Earn points to download
Earn points by helping other students or get them with a premium plan
Community
Ask the community for help and clear up your study doubts
Discover the best universities in your country according to Docsity users
Free resources
Download our free guides on studying techniques, anxiety management strategies, and thesis advice from Docsity tutors
In this report we found the value of stiffness constant
Typology: Lab Reports
1 / 5
This page cannot be seen from the preview
Don't miss anything!
Shiva Yadav
Aerospace Engineering, 3 rd^ Sem (Dated: August 10, 2022)
This report is a summary of the experiment known as the Spring Test used to determine the Modulus of rigidity of a given spring. The values of the Stiffness and Modulus of Rigidity are successfully obtained. The value of rigidity of a material obtained through such experiment is very useful in determining possible applications of the material in various industries such that the products are less prone to mechanical failure.
I. INTRODUCTION
Springs are an integral part of a vast array of prod- ucts and devices, from automotive and aerospace to medical devices and consumer products. From key- boards to cars, it’s virtually impossible to spend a day in the modern world without interacting with many springs. Springs are designed around spe- cific types of mechanical motion, including tension, compression, and torsion, and they cover a range of forces from fractions of a pound to hundreds of thou- sands of pounds. Any change in a spring, whether size, shape, or material, will impact the mechanical properties and therefore performance of the device. Mechanical performance needs to be carefully mea- sured during product design and development as well as monitoring in a production environment. Equip- ment designed to test springs must have the appro- priate mechanical motion control and force measure- ment. capability.
II. THEORY
The spring constant of a spring is the change in force it experiences per unit change in extension or compression. It is a constant that depends upon the length, radius of turns, number of turns and material of spring. When force is applied spring is compressed or elongated but the deformation comes due to the bending deformation of the spring wire. Hooke’s Law is the law which gives the mathematical relationship between the applied force on the spring and the elongation or compression in the spring’s length. It states that within the elastic limit of the material the change produced in the length of the spring will be directly proportional to the applied tensile or compressive force on the spring. Generally, the Hooke’s Law condition is satisfied well for length changes which are small in comparison to the natural length of the spring.
Mathematically,
F = −kx
Where, F is applied force, k is the spring constant, x is the change in the length of the spring.
Angle of Helix (α)
It is the ratio of the pitch of the spring to the mean circumference of the helix and is given by the relation,
tan α = (^2) πRNL
Where, L= Length of the spring R= Mean radius of the spring, N=number of turns in the spring.
Helical Springs are very helpful for practical pur- poses due to their shock absorbing and load bearing properties. There are two types of helical springs when distinguished in terms of their load bearing capacity, the Open Coiled and Closed Coiled Helical Springs.
A. Open coiled Helical spring
The open coiled helical springs are designed to re- sist compression and hence are also known as com- pression springs. These are not wound tightly and thus have a higher pitch. For these springs, the mod- ulus of rigidity can be found by the equation below.
G = 64 kR
(^3) nsec α d^4 (cos
(^2) α + sin^2 α 1+μ )
Figure 1. The open coiled spring
Where,
G is Modulus of Rigidity, K is Spring Constant, n= N - 1 where N is the number of turns in the coil. μ =Poisson’s Ratio
d = (OuterDiameter− 2 InnerDiameter)
R = (outerdiameter+ 4 Innerdiameter)
B. Closed coiled Helical spring
Figure 2. The closed coiled spring
The closed coiled helical springs are designed to resist stretching and twisting and hence are also known as tension/extension springs. These springs are wounded vey tightly and thus have a very small pitch. Modulus of rigidity for them can be found using the equation below.
G = 64 kR
(^3) nsec α d^4
III. PROCEDURE
Figure 3. Apparatus used
Load (Kgf) Loading Displacement (cm) Unloading Displacement (cm) Average (cm) 2 0.25 0.15 0. 4 0.3 0.3 0. 6 0.35 0.4 0. 8 0.5 0.5 0. 10 0.6 0.65 0. 12 0.75 0.75 0. 14 0.85 0.85 0. 16 0.95 1 0. 18 1.05 1.1 1. 20 1.15 1.15 1.
Table II. Data from closed coiled spring
Type of Coil Length (mm) No. Of Turns Outer Diameter (mm) Inner Diameter (mm) Closed Coil 45.72 14.5 17.3 11. Opened Coil 49.64 10.5 17 11.
Type of Coil Experimental Spring Constant (N/m) Closed Coil 16000 Opened Coil 15092
Type of Coil Standard Modulus of Rigidity (GPa) Experimental Modulus of Rigidity (GPa) Error (%) Closed Coil 78 51.14 34. Opened Coil 78 68.89 11.
V. SOURCES OF ERROR
The main source of error in this experiment is due to the deviation in displacement values due to the least count of the measuring instruments which were used. Also as this experiment included mechanism of movement of spindle, there is some error due to fric- tional losses. Therefore, accuracy of this experiment may be improved by using more precise measuring Instruments.
VI. DISCUSSION
The spring compression test and tension test were conducted successfully on the open coil and the closed coil respectively. The value of modulus of rigidity and stiffness of spring were measured using the corresponding load and displacement values.
VII. CONCLUSION
The stiffness of a spring is an important factor de- ciding it’s application. It also gives us an idea about it’s elastic limit,proportional etc. This property of spring is key value for it’s design in structures.
Figure 4. Graph corresponding to Table I (^) Figure 5. Graph corresponding to Table II
[1] “https://www.slideshare.net/shamjithkeyem/spring- test-37713980,”. [2] “https://idoc.pub/documents/spring-test- ylyxd9yd7vnm,”.
[3] “https://www.researchgate.net/publication/ thespringscaletest,′′^.