
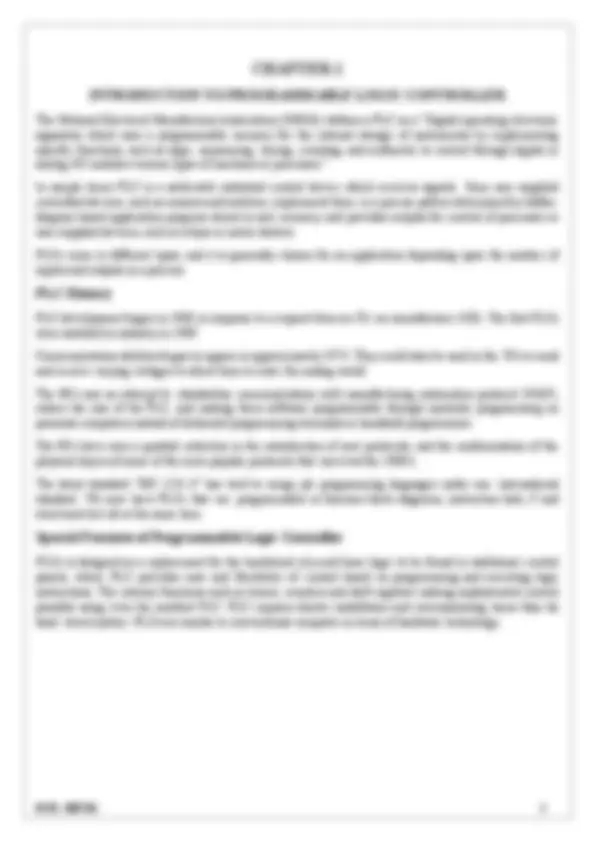
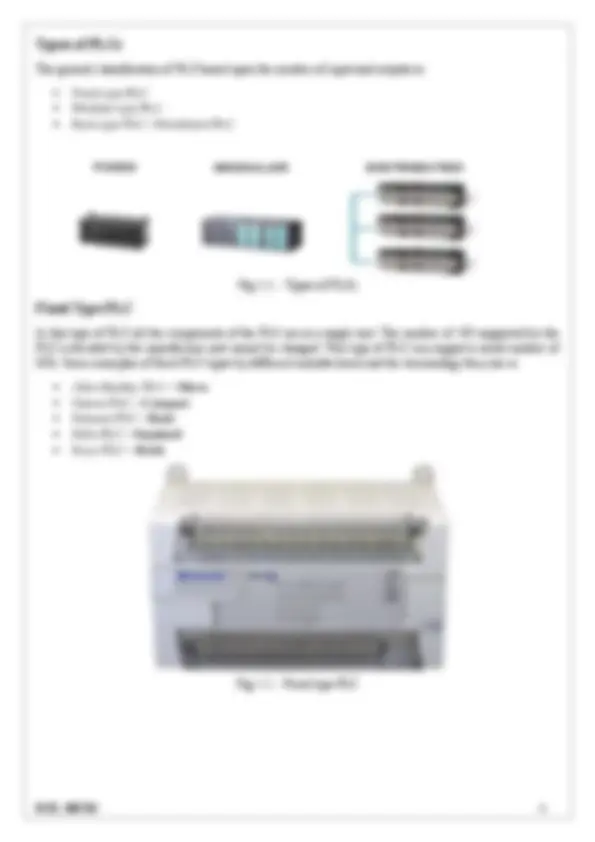
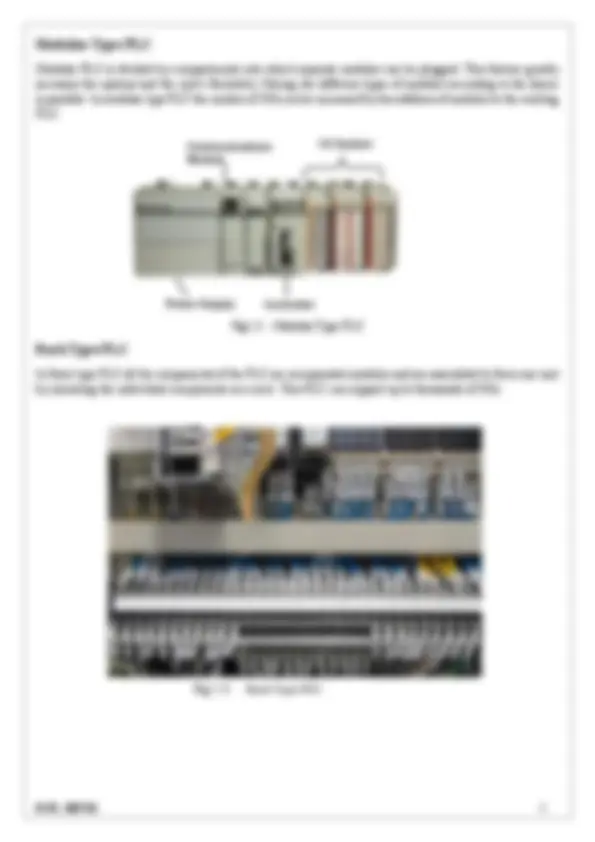
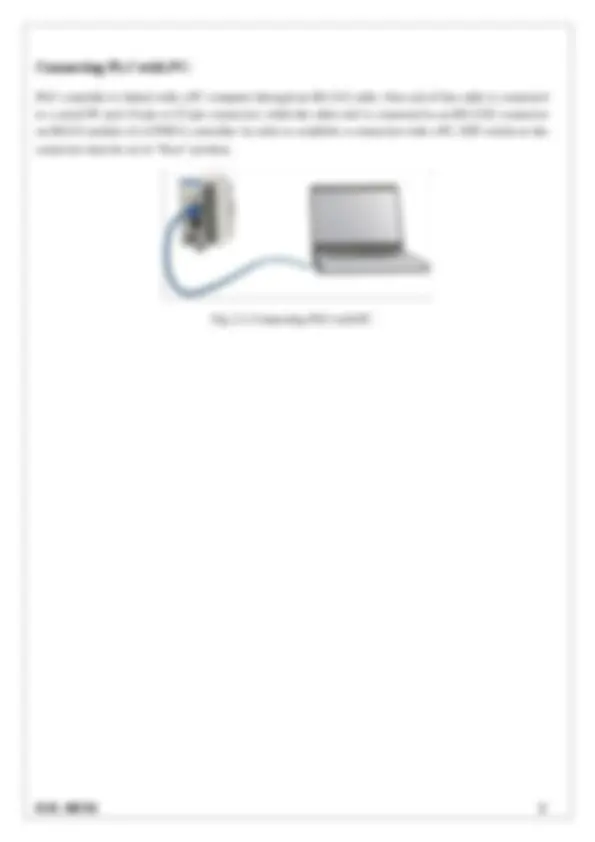
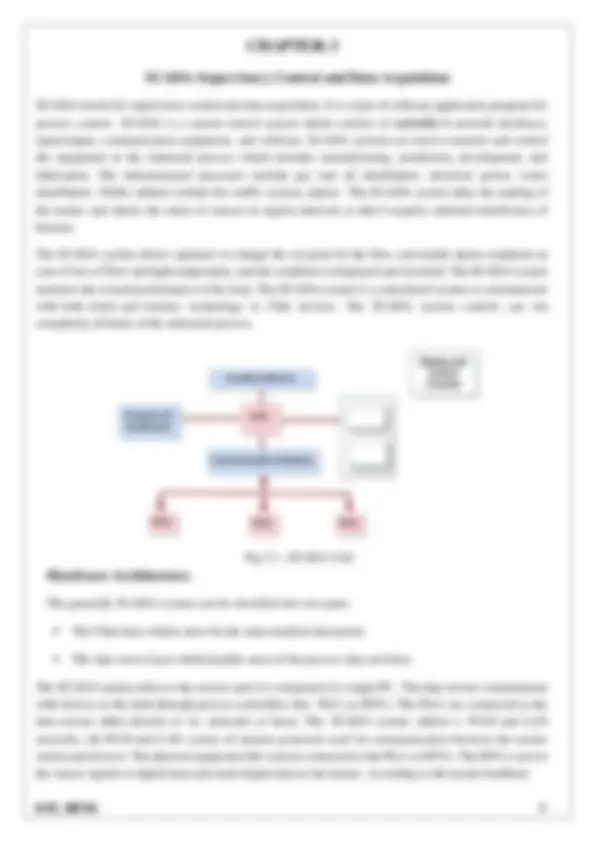
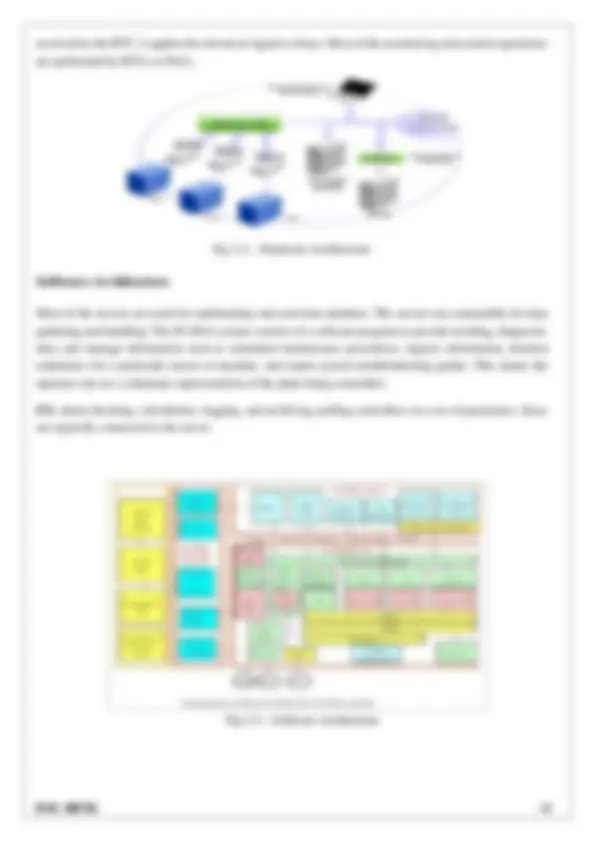
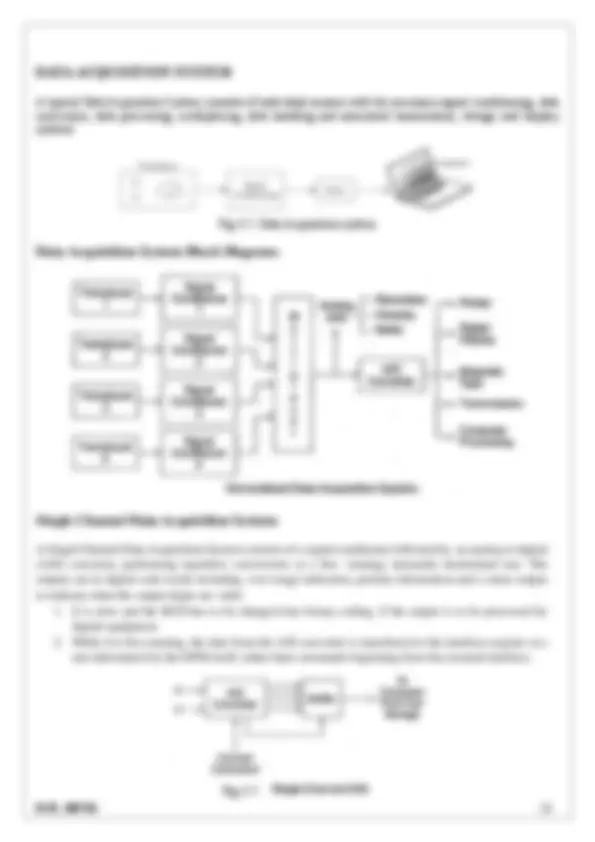
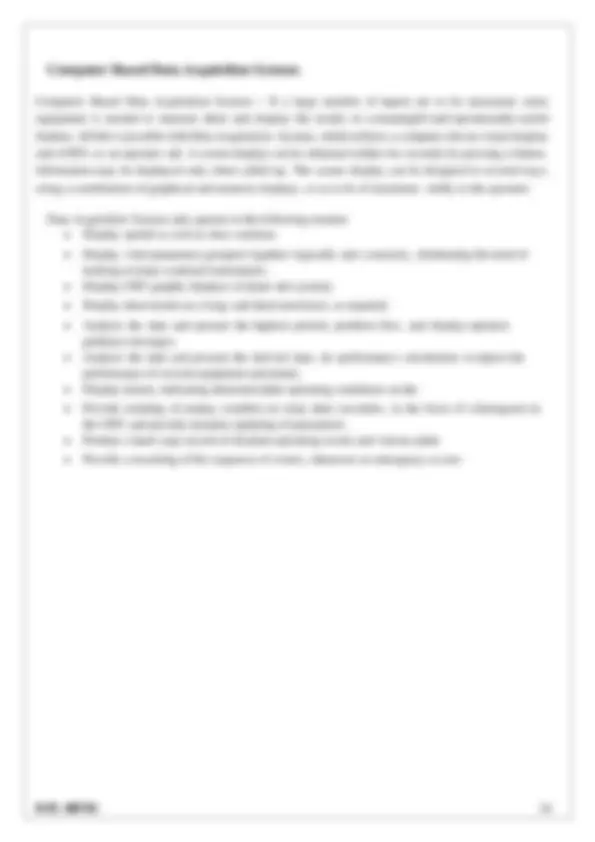
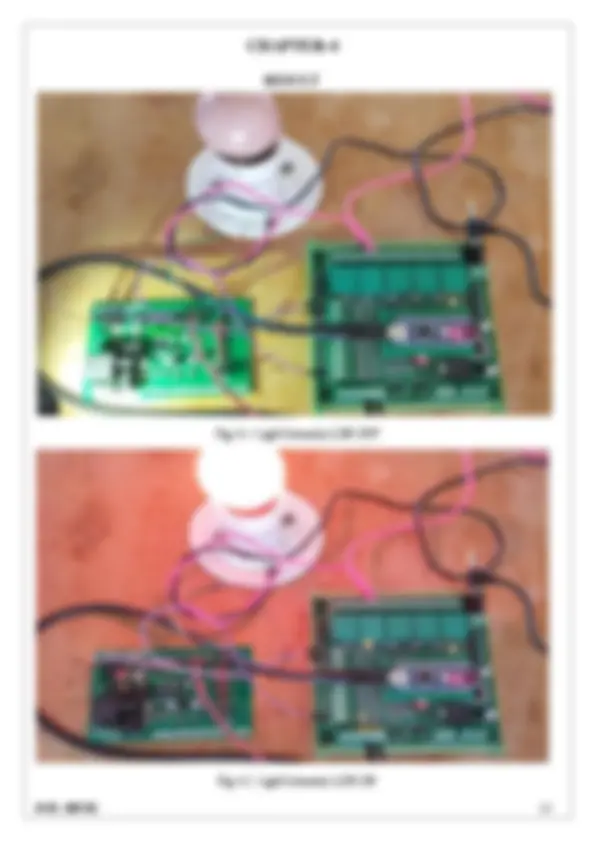
Study with the several resources on Docsity
Earn points by helping other students or get them with a premium plan
Prepare for your exams
Study with the several resources on Docsity
Earn points to download
Earn points by helping other students or get them with a premium plan
Community
Ask the community for help and clear up your study doubts
Discover the best universities in your country according to Docsity users
Free resources
Download our free guides on studying techniques, anxiety management strategies, and thesis advice from Docsity tutors
A comprehensive introduction to programmable logic controllers (plcs) and supervisory control and data acquisition (scada) systems. It covers the history, types, programming languages, architecture, and applications of plcs. The document also explores the scada system's architecture, working procedure, and its role in remote industrial plants. It includes illustrative figures and diagrams to enhance understanding.
Typology: Thesis
1 / 16
This page cannot be seen from the preview
Don't miss anything!
The general classification of PLC based upon the number of input and outputs is:
In this type of PLC all the components of the PLC are as a single unit. The number of I/O supported by the PLC is decided by the manufacture and cannot be changed. This type of PLC can support a small number of I/Os. Some examples of fixed PLC types by different manufacturers and the terminology they use is:
Modular PLC is divided by compartments into which separate modules can be plugged. This feature greatly increases the options and the unit’s flexibility. Mixing the different types of modules according to the desire is possible. In modular type PLC the number of I/Os can be increased by the addition of modules to the existing PLC. Fig1.3: - Modular Type PLC
In Rack type PLC all the components of the PLC are as separated modules and are assembled to form one unit by mounting the individual components on a rack. This PLC can support up to thousands of I/Os. Fig 1.4:
Fig 2.1: - PLC Architecture
The CPU controls and supervises all operations within the PLC, carrying out programmed instructions stored in the memory. An internal communications highway, or bus system, carries information to and from the CPU, memory and I/O units, under control of the CPU. Virtually all modern PLCs are microprocessor- based, using a 'micro' as the system CPU. Some larger PLCs also employ additional microprocessors to control complex, time-consuming functions such as mathematical processing, three- term PID control, etc. Fig 2.2: PLC – CPU unit
PLC controller is linked with a PC computer through an RS-232 cable. One end of the cable is connected to a serial PC port (9-pin or 25-pin connector), while the other end is connected to an RS-232C connector on RS232 module of a CPM1A controller. In order to establish a connection with a PC, DIP switch on the connector must be set in "Host" position. Fig 2.3: Connecting PLC with PC
received by the RTU, it applies the electrical signal to relays. Most of the monitoring and control operations are performed by RTUs or PLCs. Fig 3.2: - Hardware Architecture
Most of the servers are used for multitasking and real-time database. The servers are responsible for data gathering and handling. The SCADA system consists of a software program to provide trending, diagnostic data, and manage information such as scheduled maintenance procedures, logistic information, detailed schematics for a particular sensor or machine, and expert-system troubleshooting guides. This means the operator can see a schematic representation of the plant being controlled. EX: alarm checking, calculations, logging, and archiving; polling controllers on a set of parameters, those are typically connected to the server. Fig 3.3: - Software Architecture
Working Procedure of SCADA system The SCADA system performs the following functions:
A typical Data Acquisition System consists of individual sensors with the necessary signal conditioning, data conversion, data processing, multiplexing, data handling and associated transmission, storage and display systems Fig 3.5: Data Acquisition system
A Single Channel Data Acquisition System consists of a signal conditioner followed by an analog to digital (A/D) converter, performing repetitive conversions at a free running, internally determined rate. The outputs are in digital code words including over range indication, polarity information and a status output to indicate when the output digits are valid.
Computer Based Data Acquisition System – If a large number of inputs are to be measured, some equipment is needed to measure them and display the results in a meaningful and operationally useful fashion. All this is possible with Data Acquisition System, which utilizes a computer driven visual display unit (CRT) as an operator aid. A screen display can be obtained within two seconds by pressing a button. Information may be displayed only when called up. The screen display can be designed in several ways, using a combination of graphical and numeric displays, so as to be of maximum utility to the operator. Data Acquisition System aids operate in the following manner.