
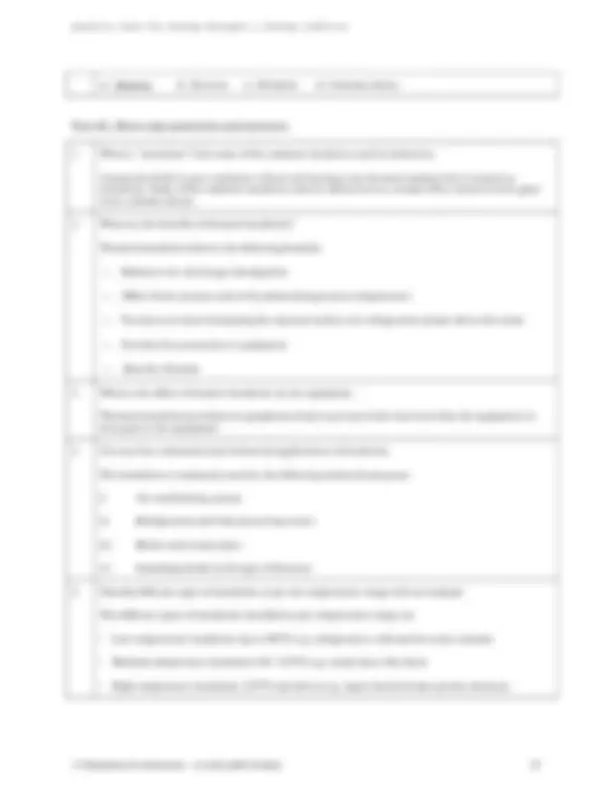
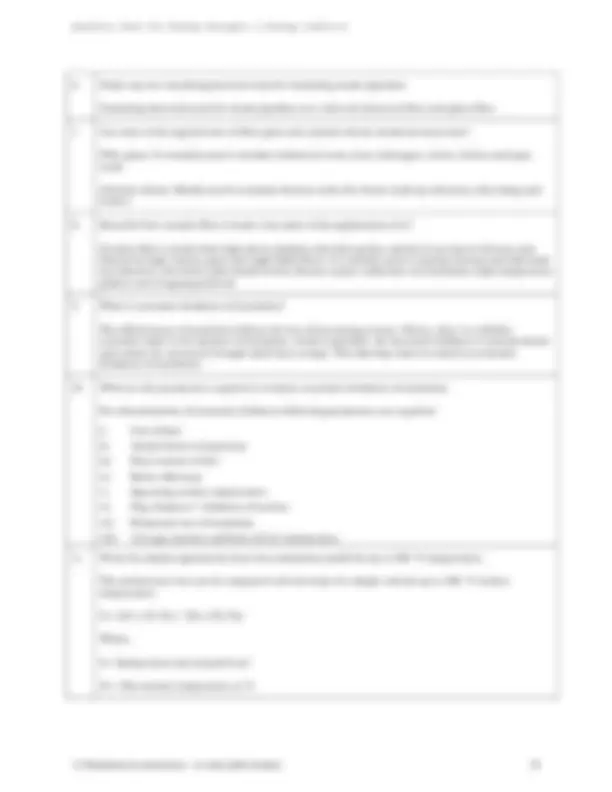
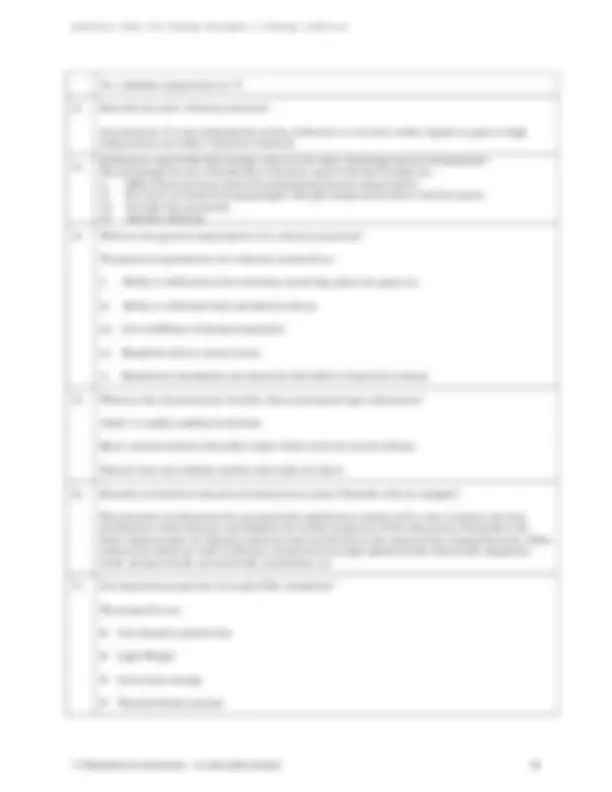
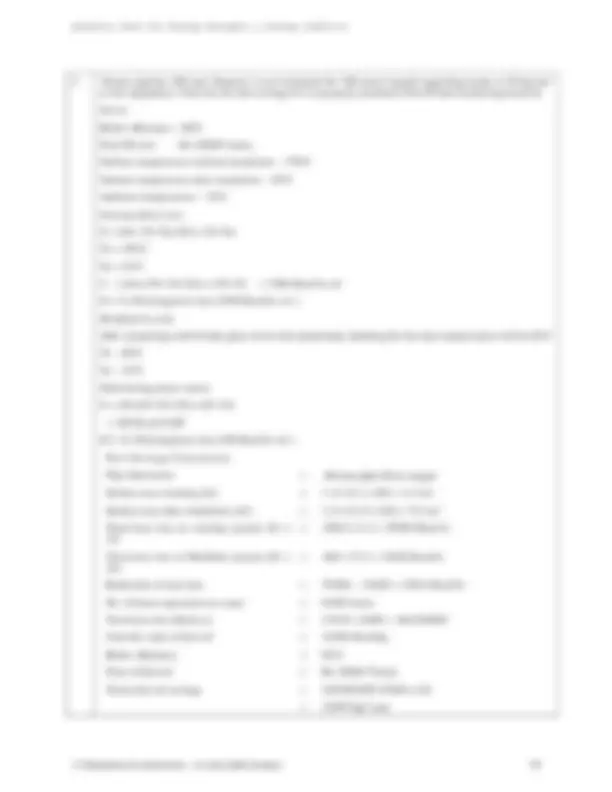
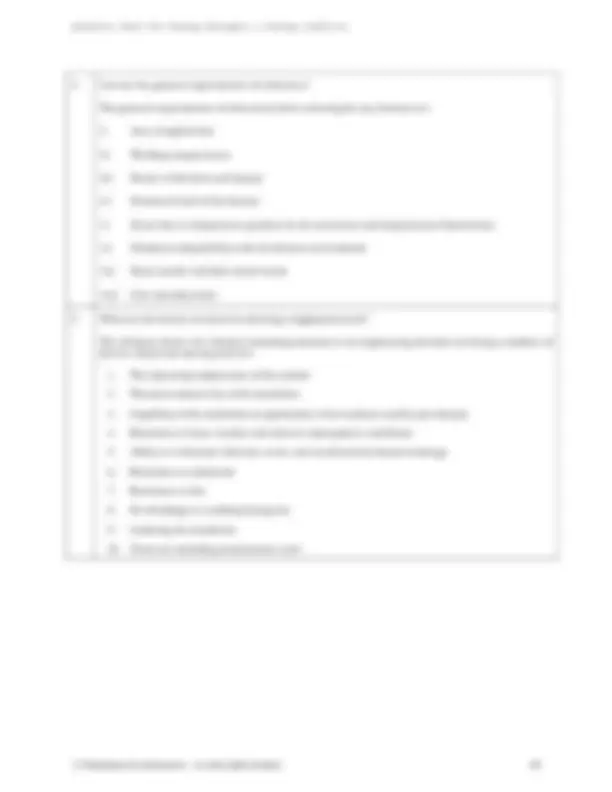
Study with the several resources on Docsity
Earn points by helping other students or get them with a premium plan
Prepare for your exams
Study with the several resources on Docsity
Earn points to download
Earn points by helping other students or get them with a premium plan
Community
Ask the community for help and clear up your study doubts
Discover the best universities in your country according to Docsity users
Free resources
Download our free guides on studying techniques, anxiety management strategies, and thesis advice from Docsity tutors
A question bank for Energy Managers and Energy Auditors, focusing on Chapter 2.5: Insulation & Refractories. It contains objective and short type questions with answers, covering topics such as thermal insulators, insulation materials, refractory materials, and their applications. It also includes a table format revision of Insulation & Refractories.
Typology: Study notes
1 / 9
This page cannot be seen from the preview
Don't miss anything!
Part-I: Objective type questions and answers
a) good conductor of heat and has high thermal conductivity
b) poor conductor of heat and has high thermal conductivity
c) good conductor of heat and has low thermal conductivity
d) poor conductor of heat and has low thermal conductivity
a) Mineral fibre b) Fibre glass c) Silica d) polyurethane
a) Asbestos b) Calcium silicate c) Mineral fibre d) All of the above
a) 540 °C b) 1050 °C c) 1430 °C d) 1850 °C
Insulating material Suitable temperature a) Rockwool i) - 178 °C to 4 °C b) Fibre glass ii) -167 °C to 82 °C c) Polystyrene iii) Up to 820 °C d) Polyurethane iv) Up to 540 °C
a-iii); b-iv); c-ii); d-i)
a) calcium silicate b) fibre glass c) rock wool d) Alumina
a) K.cal/m-hr-°C b) K.cal/ m²-hr-°C c) K.cal/m²-°C d) K.cal/ m-°C
a) low b) High c) Medium d) very high
a) acid b) basic c) neutral d) none of the above
a) acid b) basic c) Neutral d) None of the above
The heat conductivity of refractory material should be ___.
a) low b) High c) Medium c) None
a) silica bricks b) Fire brick
c) chrome magnesite d) Calcium silicate blocks
a) low b) high c) medium d) None of the above
a) glass wool b) calcium silicate c) fire bricks d) ceramic fibre
a) Alumina b) Ceramic Fibre c) Fire Brick d) Mineral Fibre
a) Outer surface of furnace b) Refrigeration pipings
c) Inner surface of furnace d) None of the above
a) Al 2 O 3 b) SiO 2 c) ZrO 2 d) All the above
a) Al 2 O 3 b) ZrO 2 c) SiO 2 d) All the above
a) Increases with increased thermal conductivity
b) Decreases with decreased thermal conductivity
c) Decreases with increased thermal conductivity
d) Increases with decreases thermal conductivity
Insulating materials used for steam pipelines are rock wool (mineral fibre) and glass fibre.
Fibre glass: It is mainly used to insulate industrial ovens, heat exchangers, driers, boilers and pipe work.
Calcium silicate: Mainly used to insulate furnace walls, fire boxes, back up refractory, flue lining and boilers
Ceramic fibre is made from high purity alumina and silica grains, melted in an electric furnace and blasted by high velocity gases into light fluffy fibres. It is mainly used to insulate furnace and kiln back up refractory, fire boxes, glass feeder bowls, furnace repair, induction coil insulation, high temperature gaskets and wrapping material
The effectiveness of insulation follows the law of decreasing returns. Hence, there is a definite economic limit to the amount of insulation, which is justified. An increased thickness is uneconomical and cannot be recovered through small heat savings. This limiting value is termed as economic thickness of insulation.
For determination of economic thickness following parameters are required:
i) Cost of fuel ii) Annual hours of operation iii) Heat content of fuel iv) Boiler efficiency v) Operating surface temperature vi) Pipe diameter / thickness of surface vii) Estimated cost of insulation viii) Average exposure ambient still air temperature
The surface heat loss can be computed with the help of a simple relation up to 200 °C surface temperature.
S = [10 + (Ts-Ta) / 20] x [Ts-Ta]
Where,
S = Surface heat loss in kcal/hr m^2
Ts = Hot surface temperature in °C
Ta = Ambient temperature in °C
Any material, if it can withstand the action of abrasive or corrosive solids, liquids or gases at high temperatures are called ‘refractory’ material.
In furnaces, apart from fuel savings, what are the other advantages by use of insulation? The advantages by use of insulation in furnaces, apart from fuel savings are: i) Offers better process control by maintaining process temperatures ii) Prevents corrosion by keeping higher flue gas temperatures above acid dew point. iii) Provides fire protection iv) Absorbs vibration
The general requirements of a refractory material are
i) Ability to withstand action of molten metal slag, glass, hot gases etc.
ii) Ability to withstand load and abrasive forces
iii) Low coefficient of thermal expansion
iv) Should be able to conserve heat
v) Should not contaminate the material with which it comes into contact
Acidic: it readily combines with base
Basic: consists mainly of metallic oxides which resist the action of bases
Neutral: does not combine neither with acids nor bases
The selection of refractories for any particular application is made with a view to achieve the best performance of the furnace, and depends on certain properties of the refractories. Firebrick is the most common form of refractory material used extensively in the construction of small furnaces. Other refractories which are used in furnace construction are high alumina brick, silica brick, magnesite brick, chromite brick, zirconia brick, monolithics etc.
The properties are
¾ Low thermal conductivity
¾ Light Weight
¾ Lower heat storage
¾ Thermal shock resistant
ii. Pipe diameter/thickness of surface
iii. Estimated cost of insulation.
Average exposure ambient still air temperature.
Determine:
i) The heat loss per m^2 area of the furnace wall.
Consider K1 (brick) = 1.1 W/m-°C
K2 (steel) = 39 W/m-°C
h 0 (outside heat transfer coefficient) = 68 W/m^2 -°C
Considering unit surface area
R (^) brick =
R steel =
0
RTotal = Rbrick + Rsteel + Rcov = 0.
ii) Q (heat loss per m^2 area) = Total
i a
7 .5 mm L
6.4 mm L 2
Ti = 647 °C
Ta = 27 °C
Given:
Boiler efficiency – 80%
Fuel Oil cost - Rs.15000/tonne
Surface temperature without insulation – 170oC
Surface temperature after insulation – 65oC
Ambient temperature – 25oC
Existing Heat Loss
S = [10+ (Ts-Ta)/20] x (Ts-Ta)
Ts = 170oC
Ta = 25oC
S = [10+(170-25)/20] x (170-25) = 2500 Kcal/hr-m^2
S1 = S =Existing heat loss (2500 Kcal/hr-m^2 )
Modified System
After insulating with 65 mm glass wool with aluminium cladding the hot face temperature will be 65oC
Ts – 65oC
Ta – 25oC
Substituting these values
S = [10+(65-25)/20] x (65-20)
= 480 K.cal/hrM^2
S2 = S =Existing heat loss (480 Kcal/hr-m^2 )
Fuel Savings Calculation
Pipe dimension = (^) 100 mm φ & 100 m length
Surface area existing (A1) = 3.14 x 0.1 x 100 = 31.4 m^2
Surface area after insulation (A2) = 3.14 x 0.23 x 100 = 72.2 m^2
Total heat loss in existing system (S1 x A1)
= 2500 x 31.4 = 78500 Kcal/hr
Total heat loss in Modified system (S2 x A2)
= 480 x 72.2 = 34656 Kcal/hr
Reduction in heat loss = 78500 – 34656 = 43844 Kcal/hr
No. of hours operation in a year = 8400 hours
Total heat loss (Kcal/yr) = 43844 x 8400 = 368289600
Calorific value of fuel oil = 10300 Kcal/kg
Boiler efficiency = 80%
Price of fuel oil = Rs.15000/Tonne
Yearly fuel oil savings = 368289600/10300 x 0.
= 44695 kg//year