
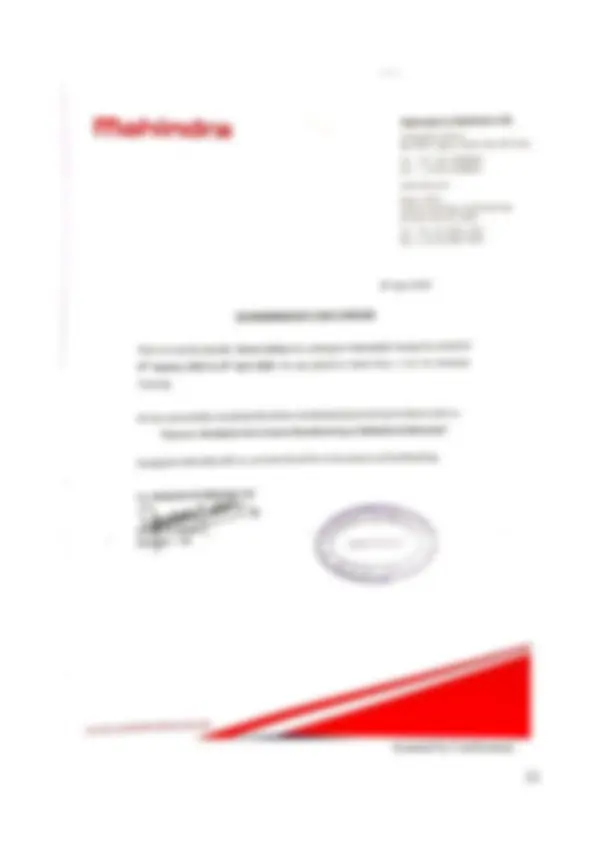
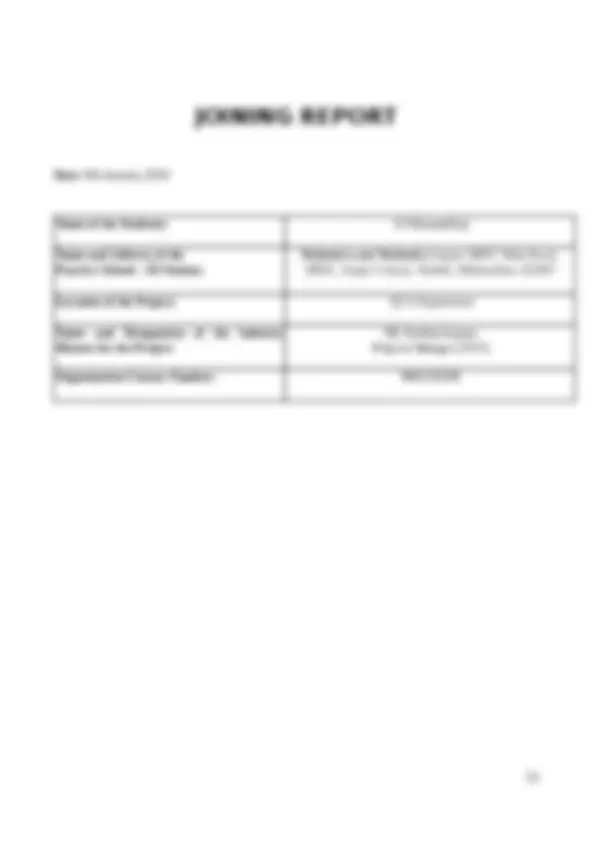
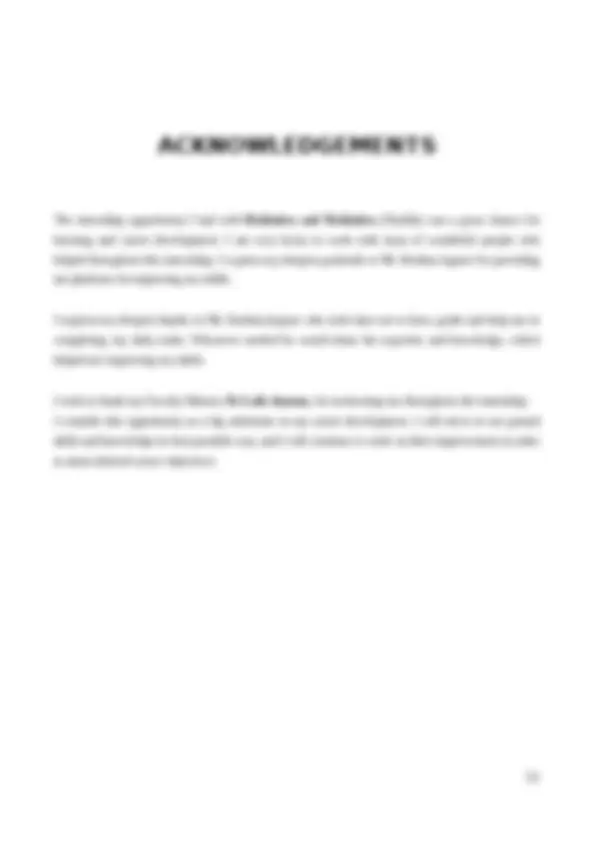
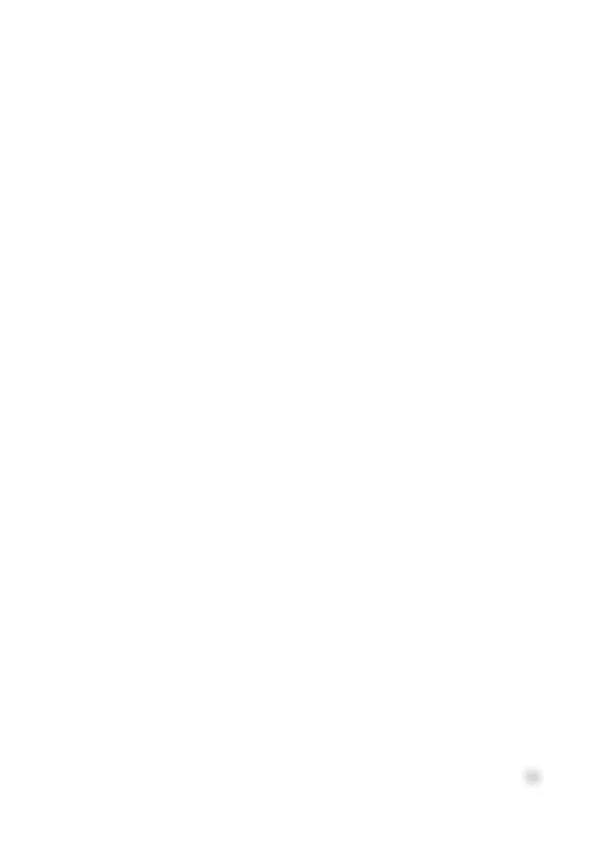
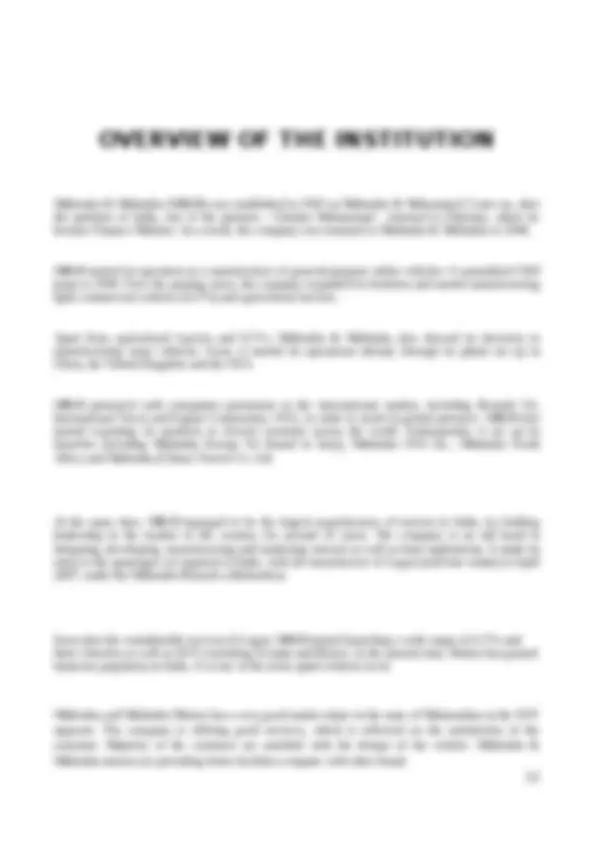
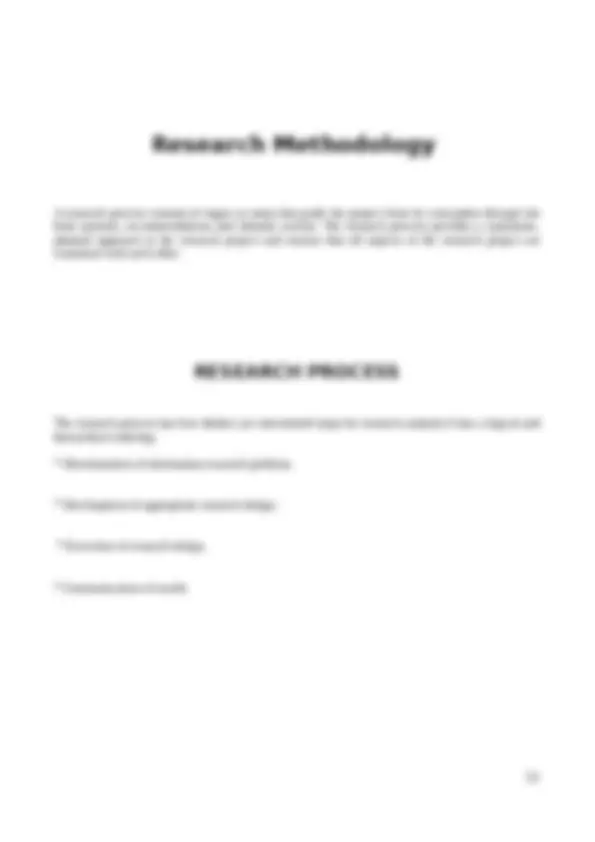
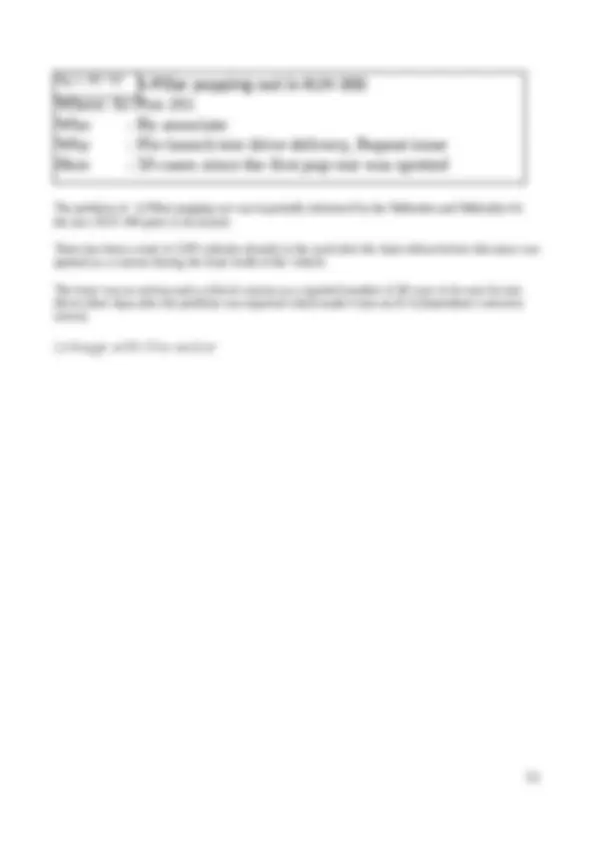
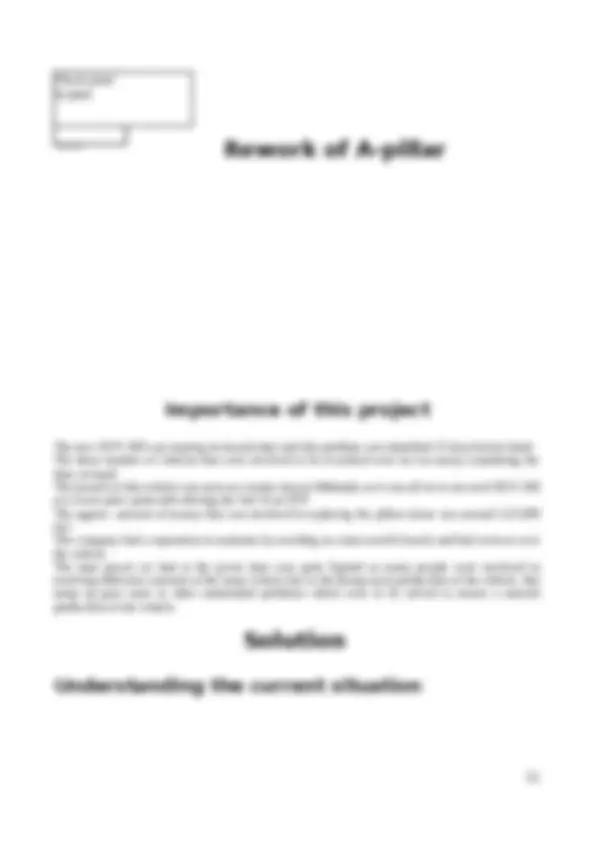
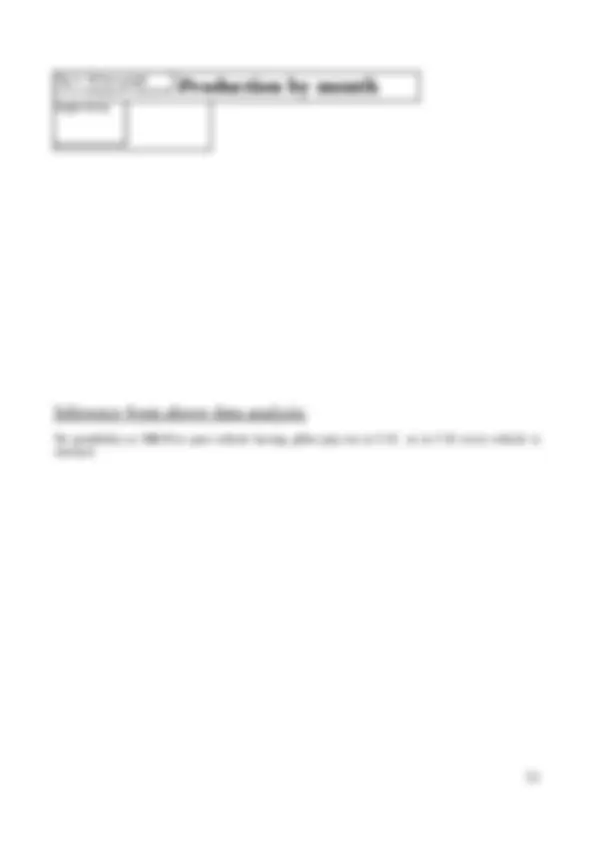
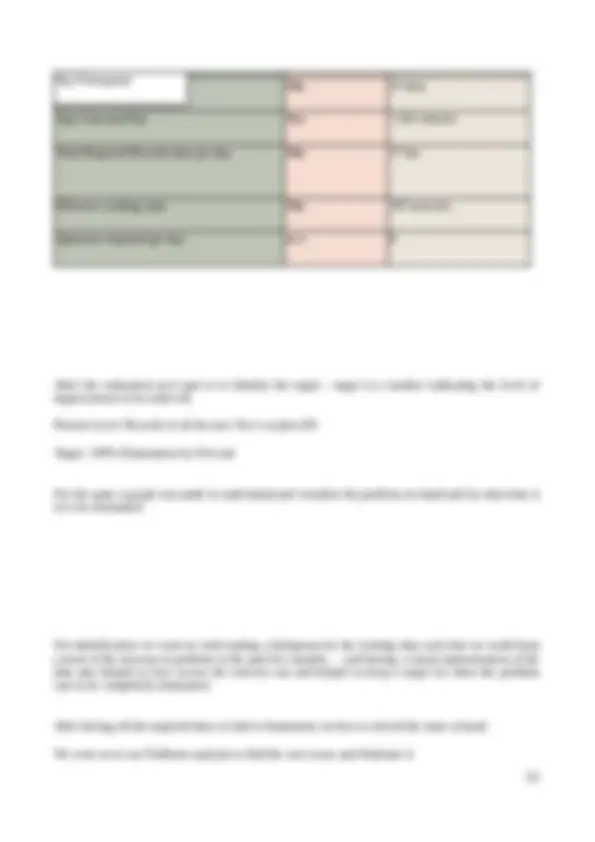
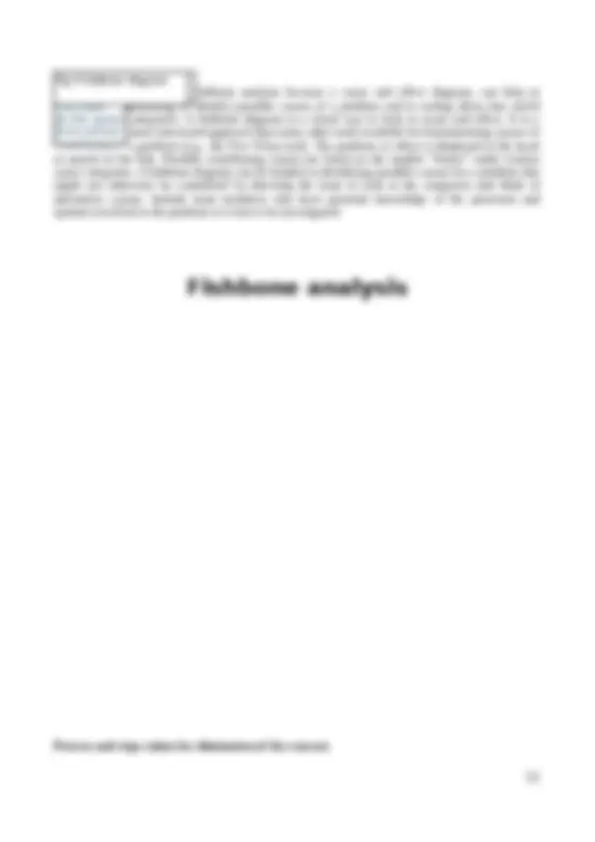
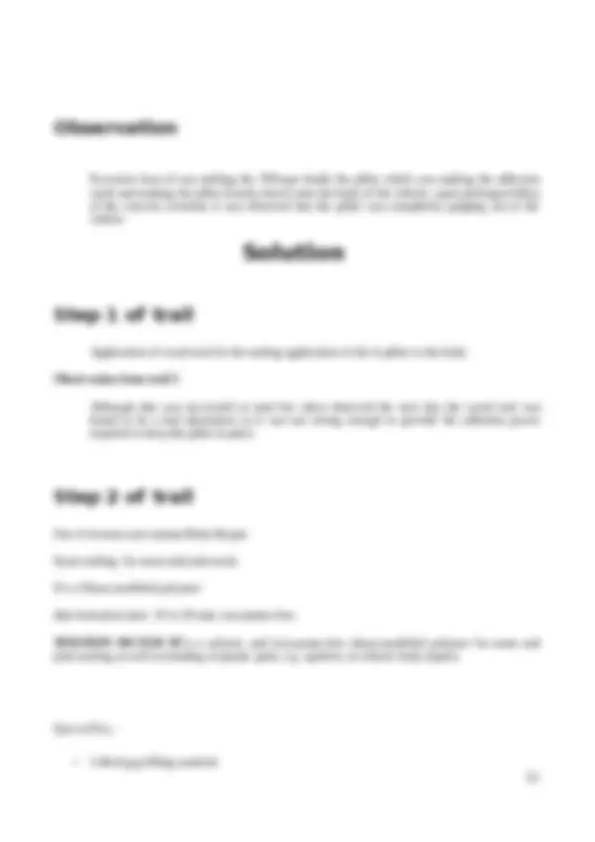
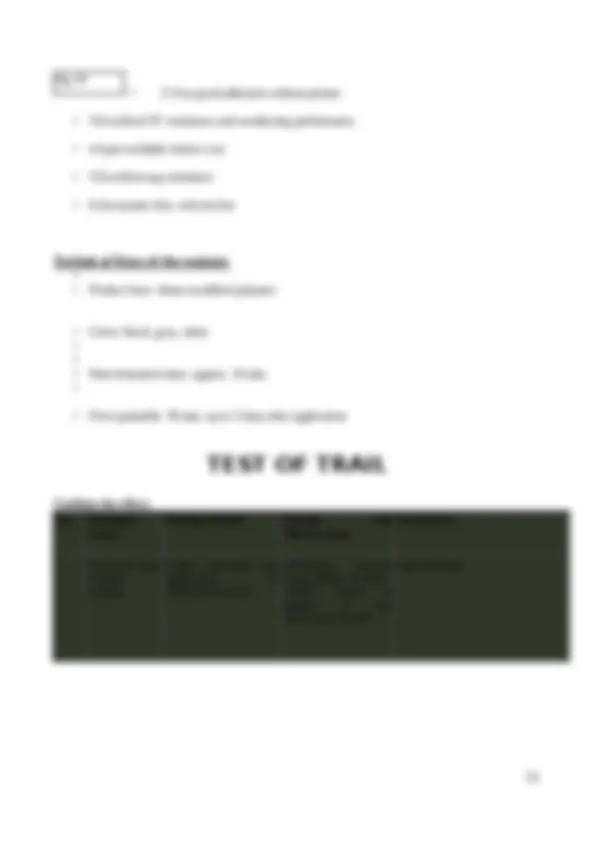
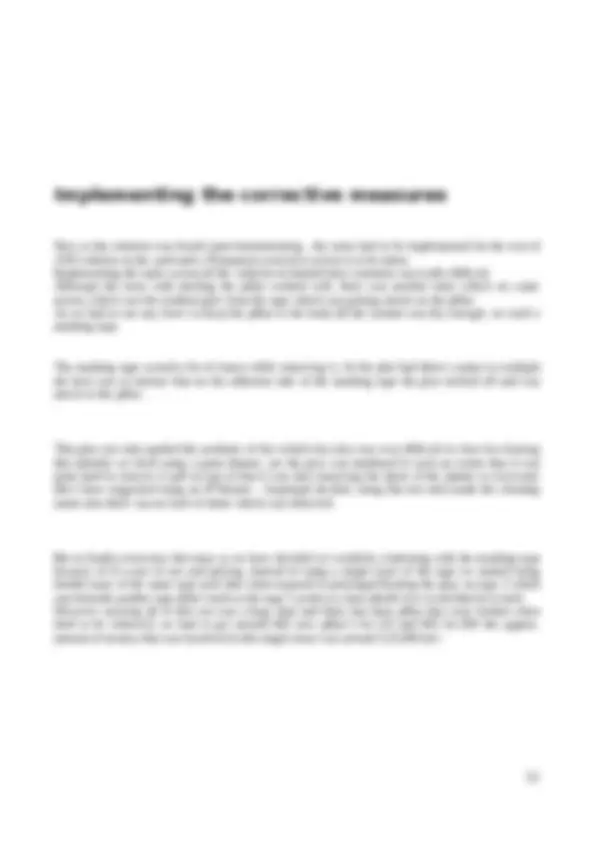
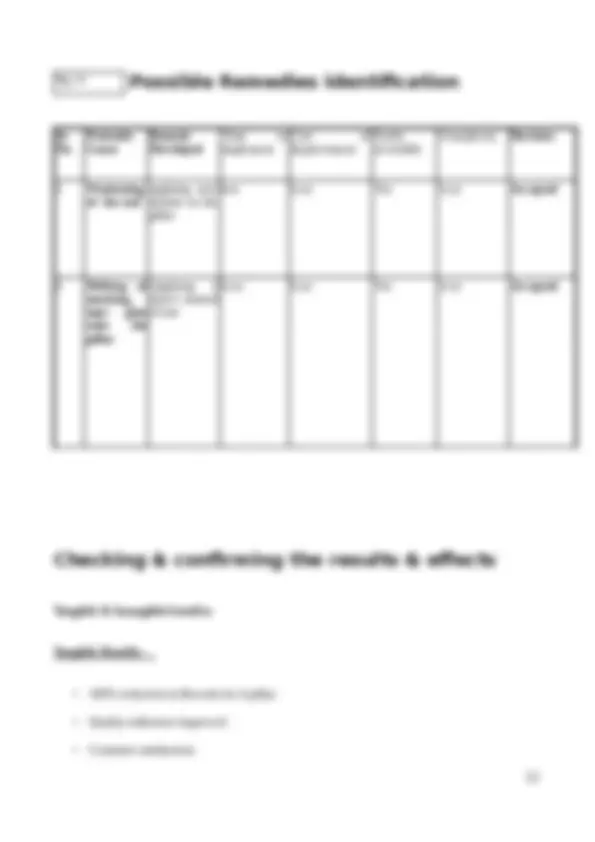
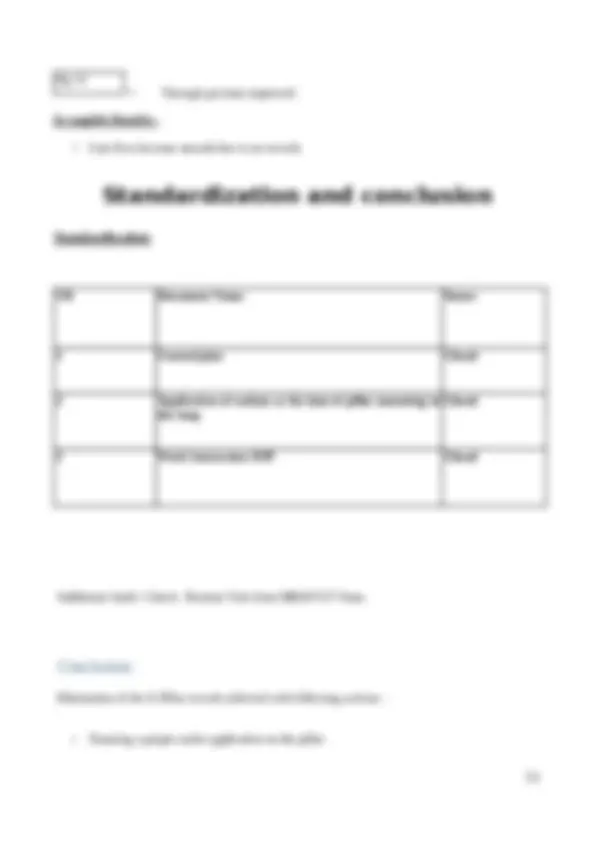
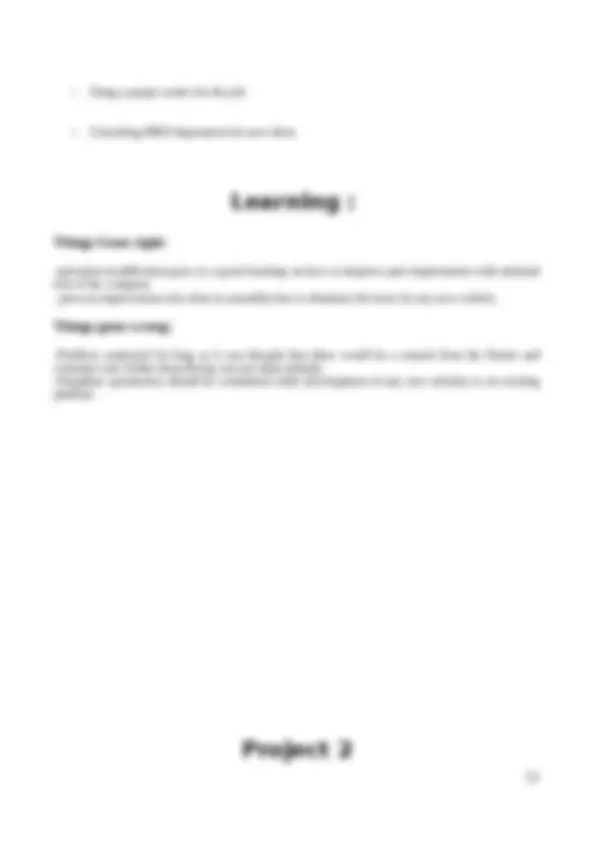
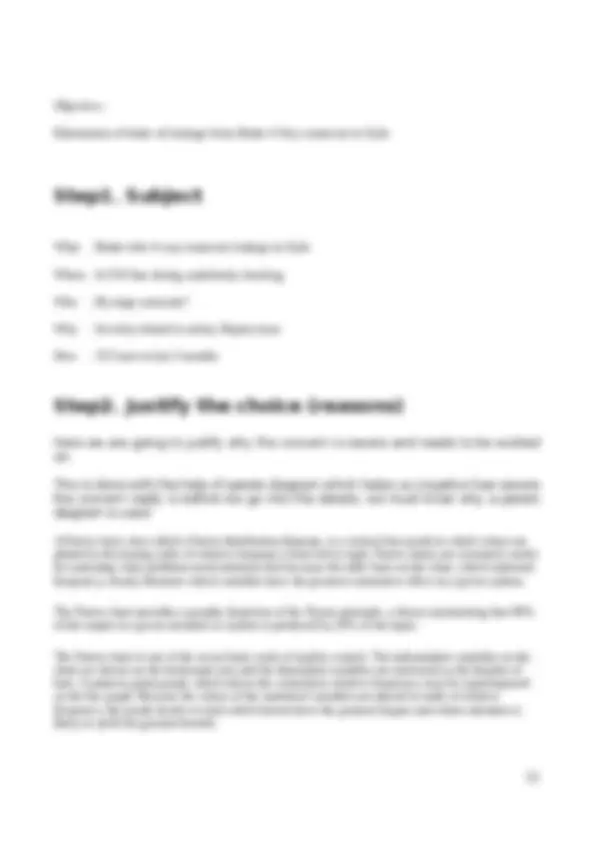
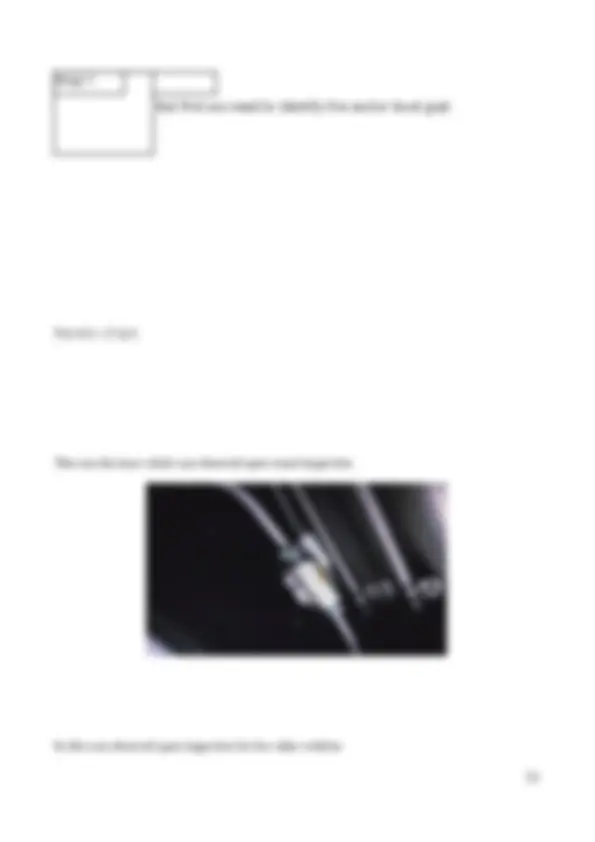
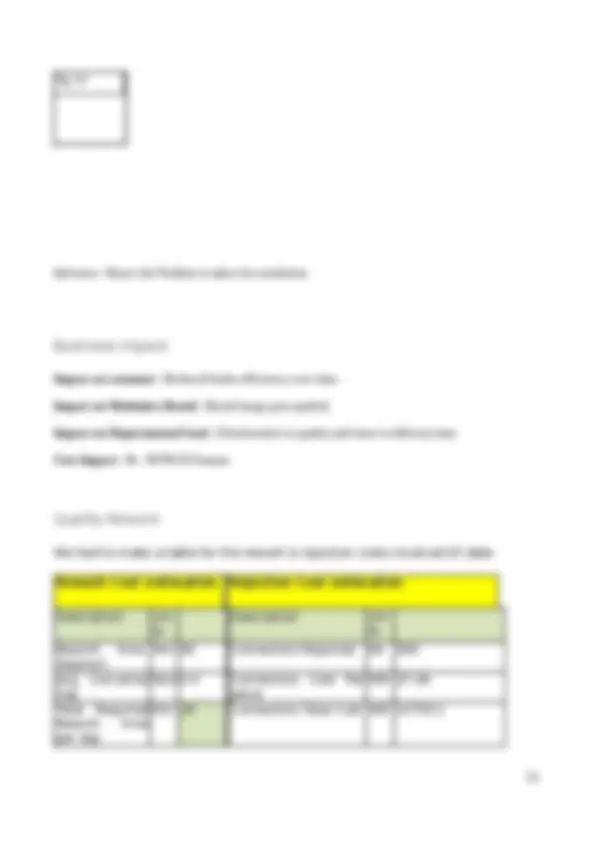
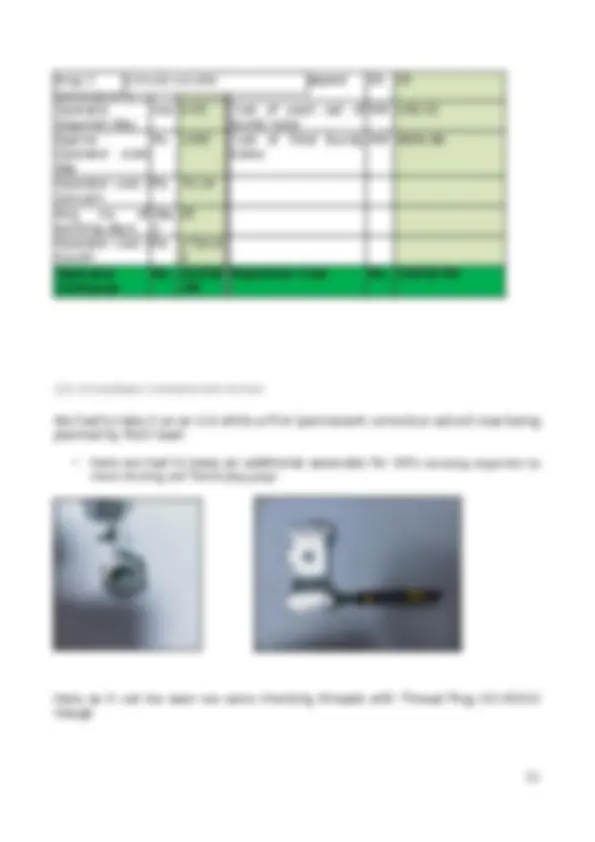
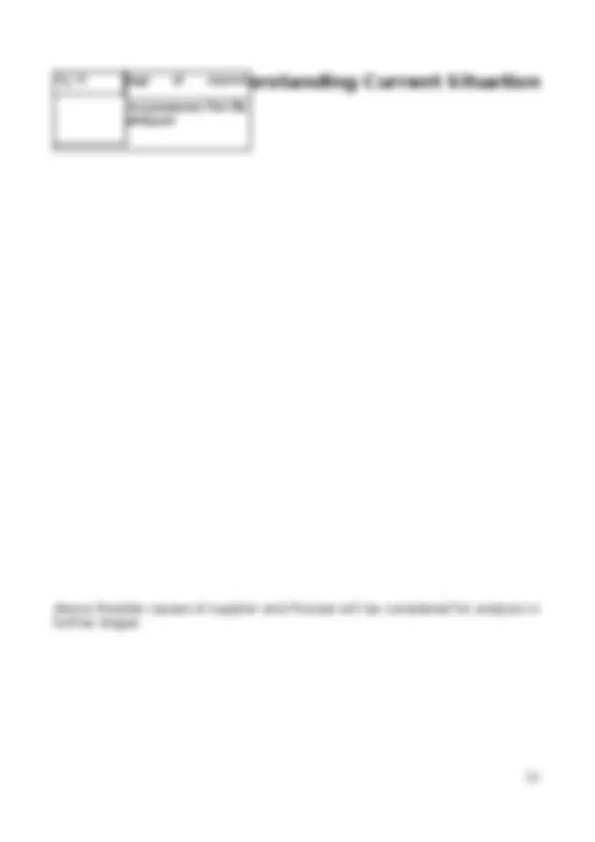
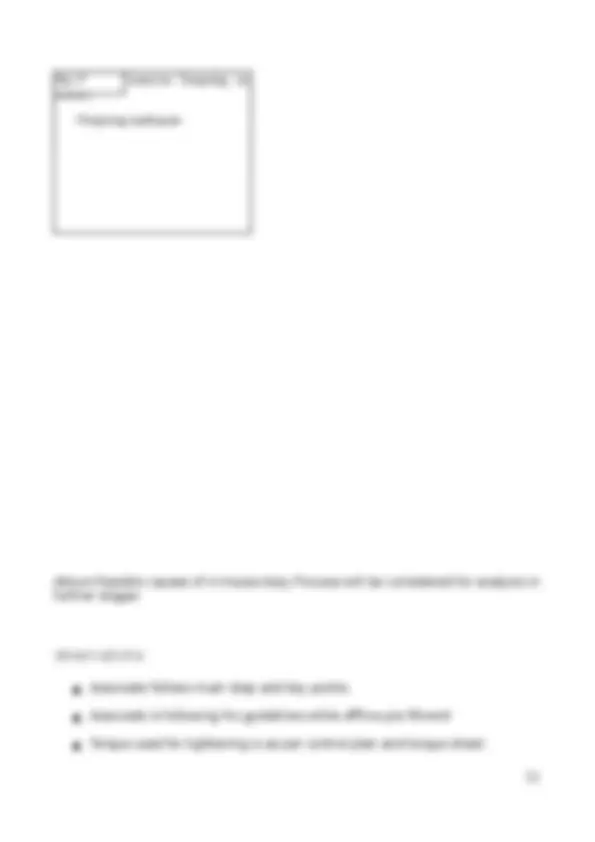
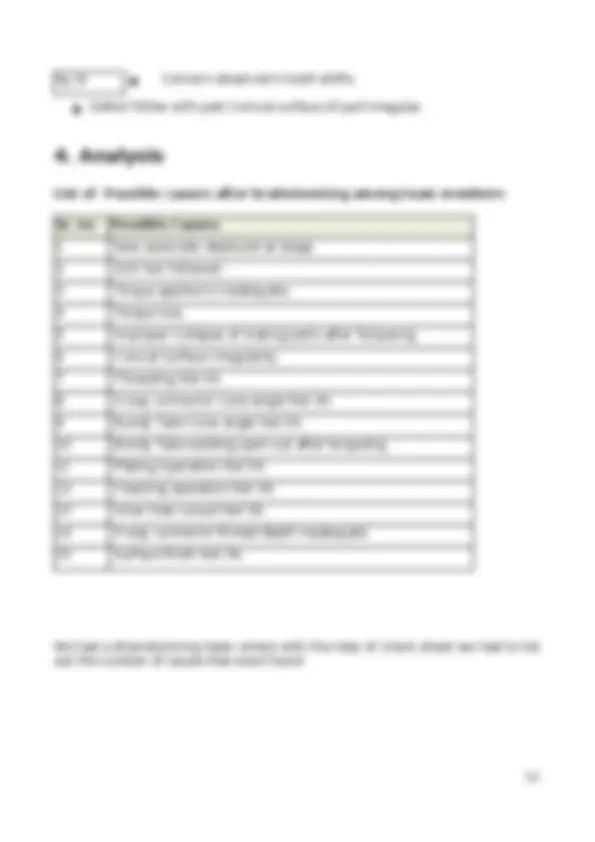
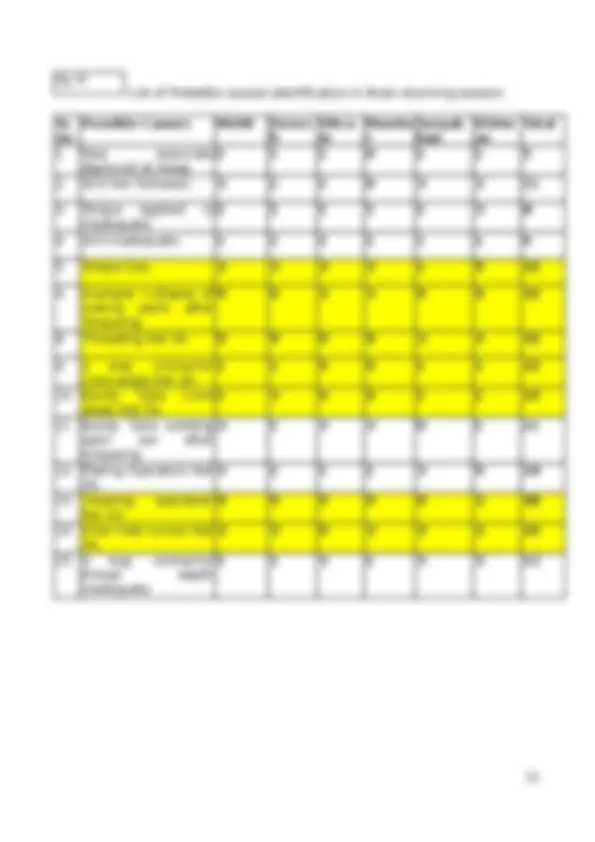
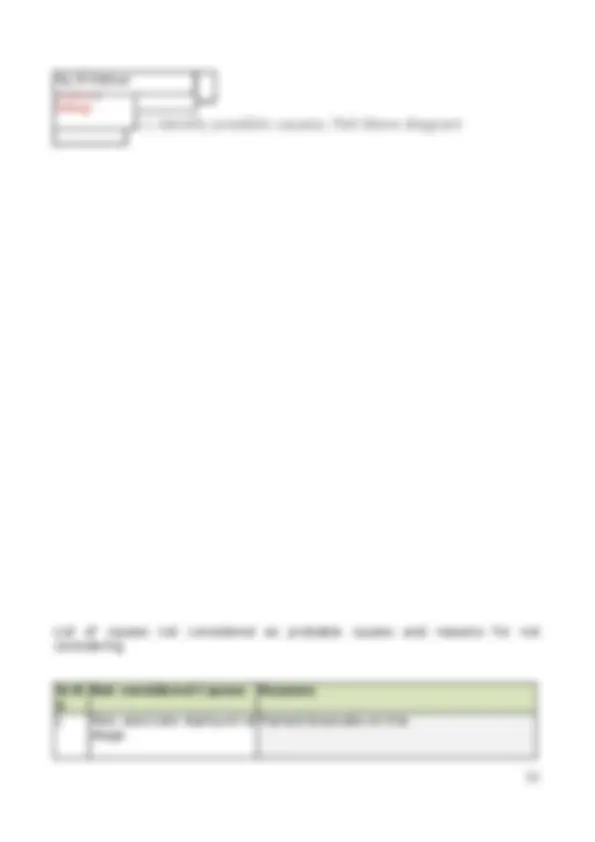
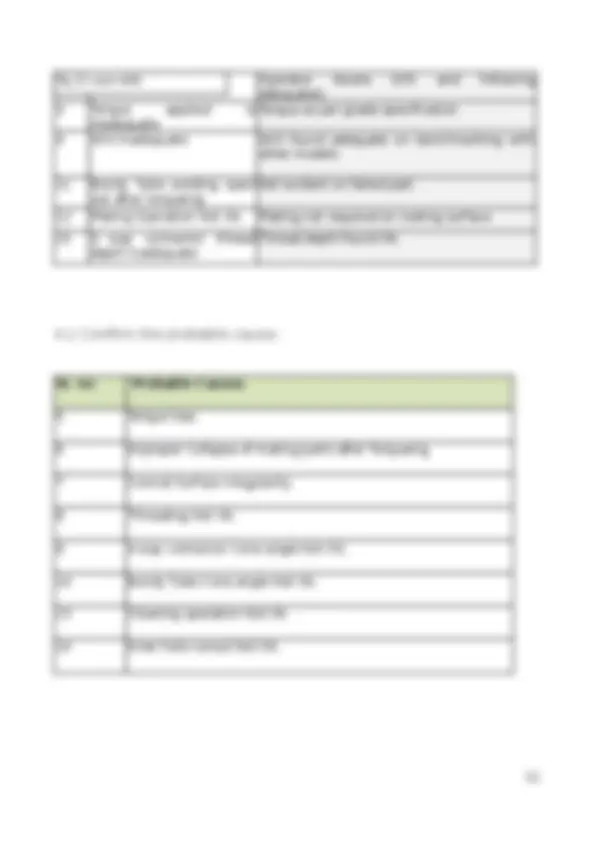
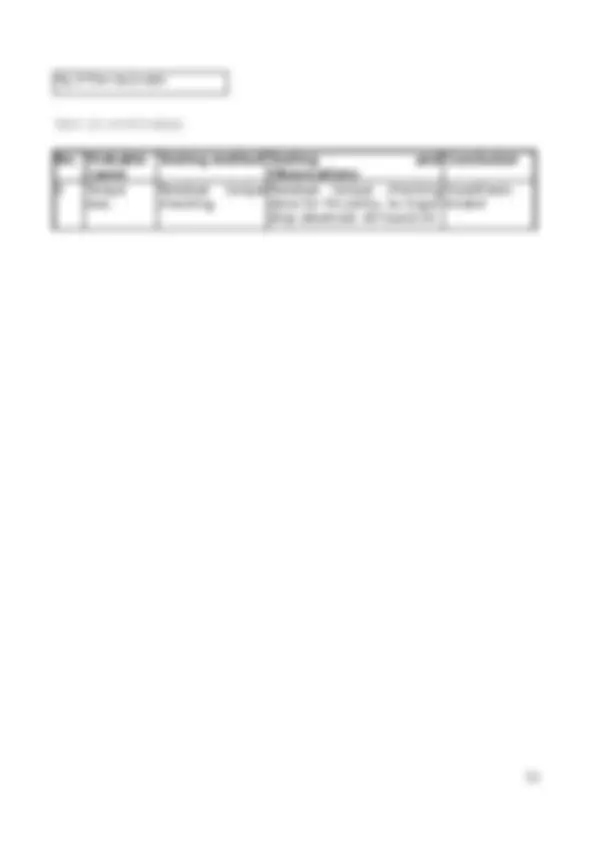
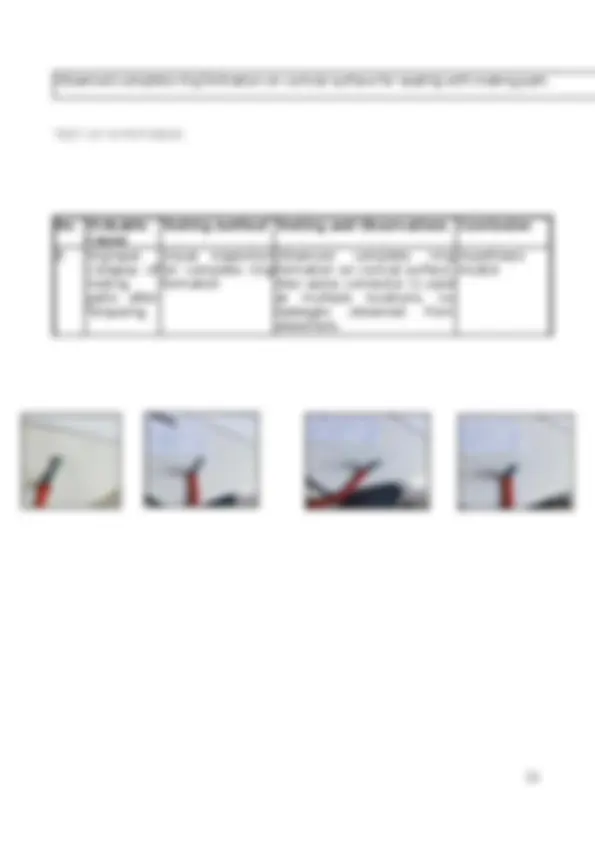
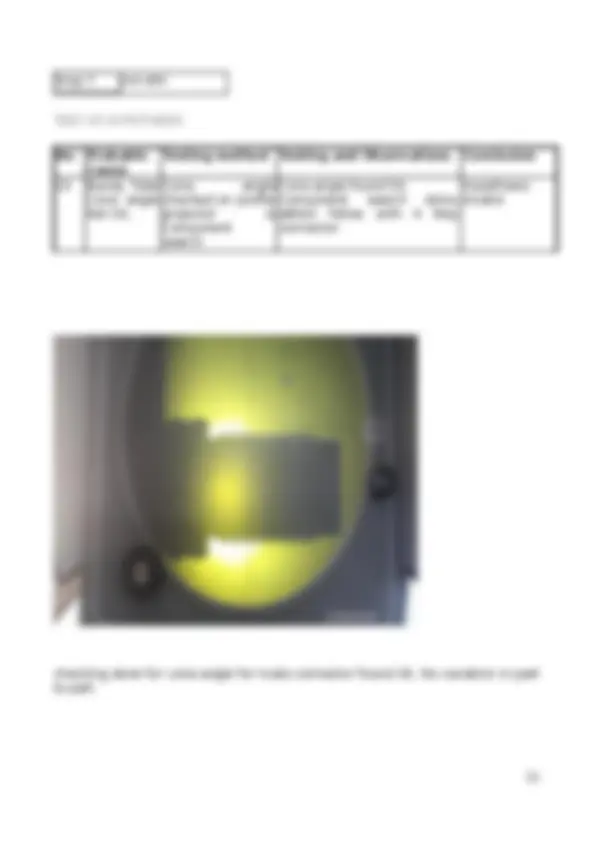
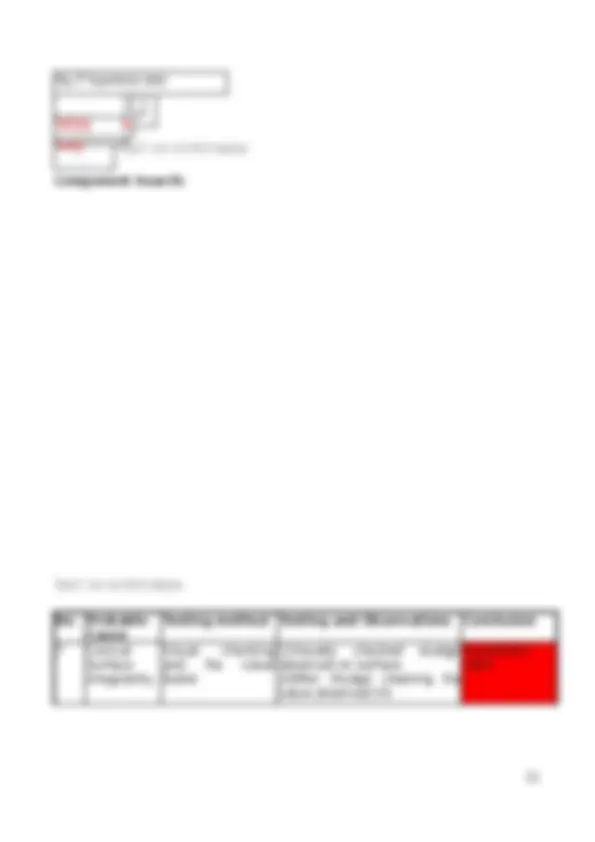
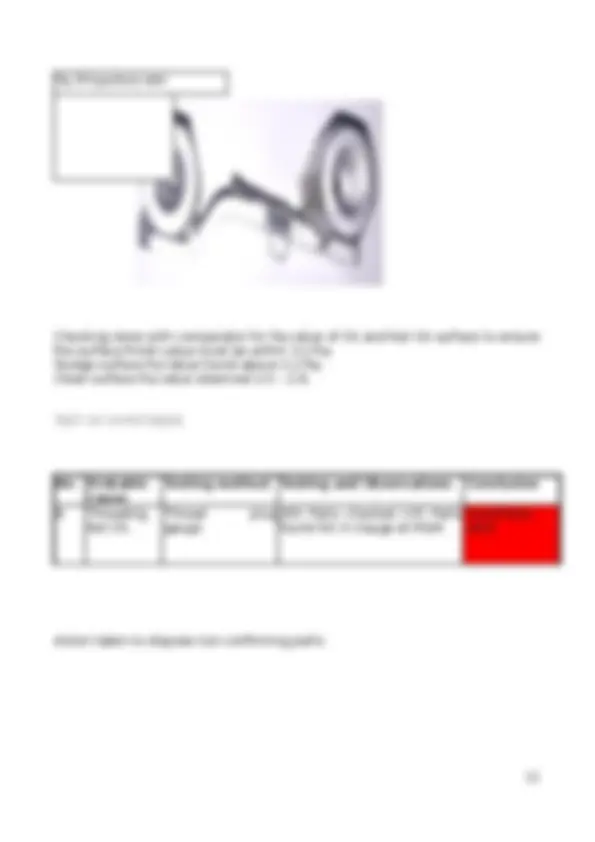

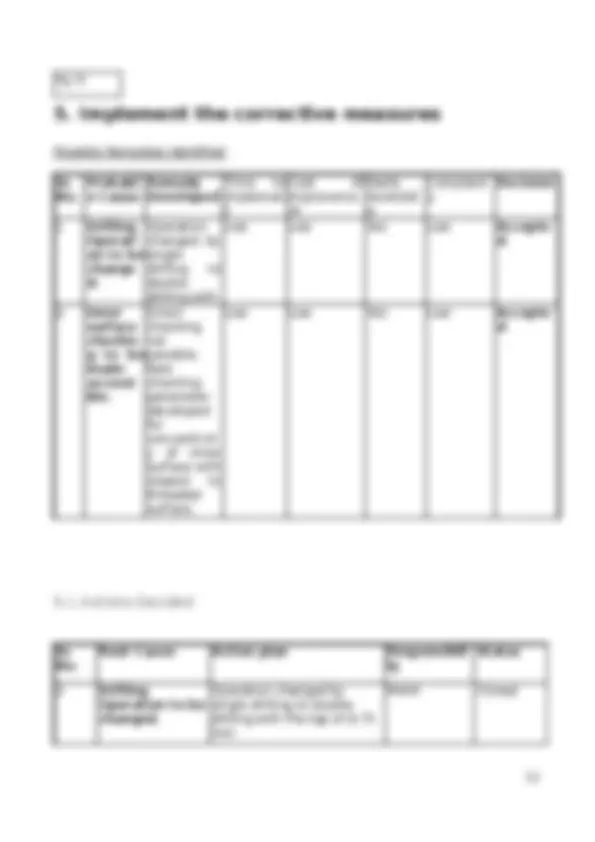
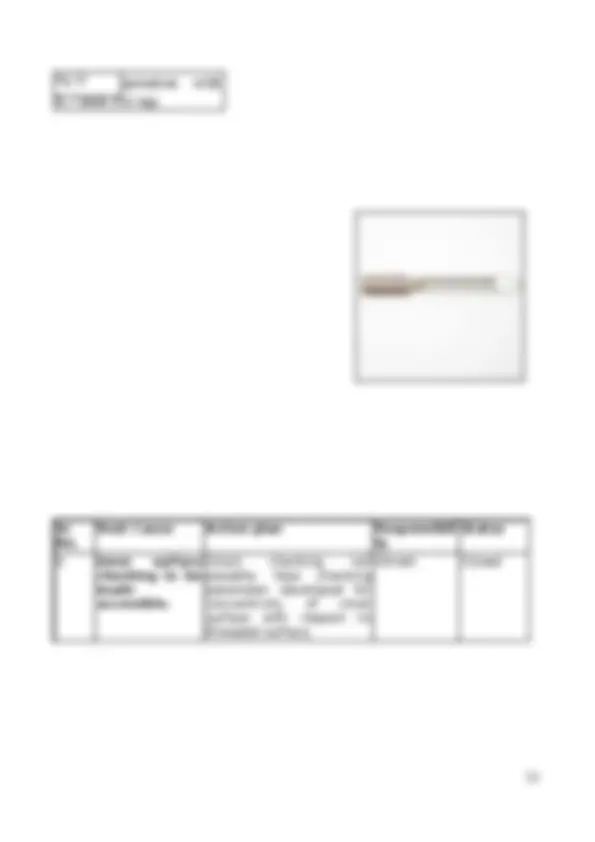
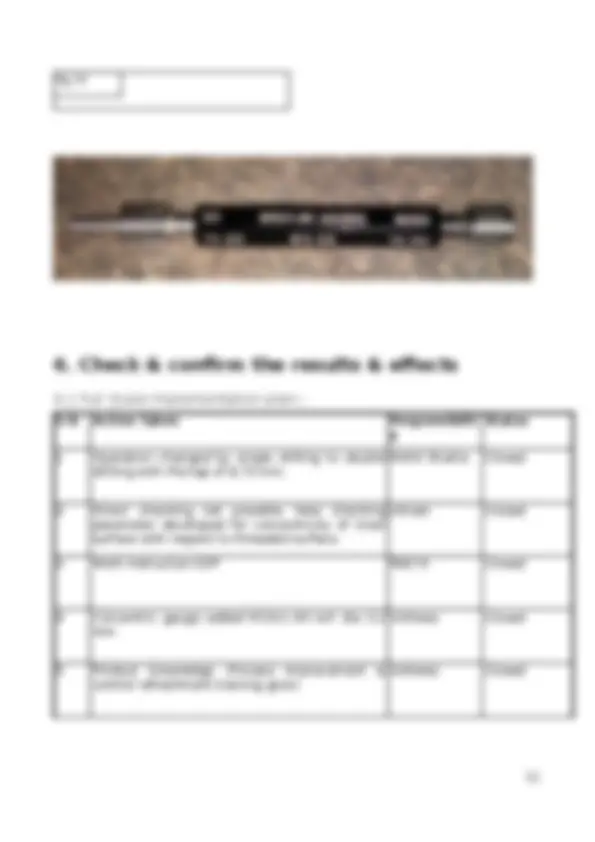
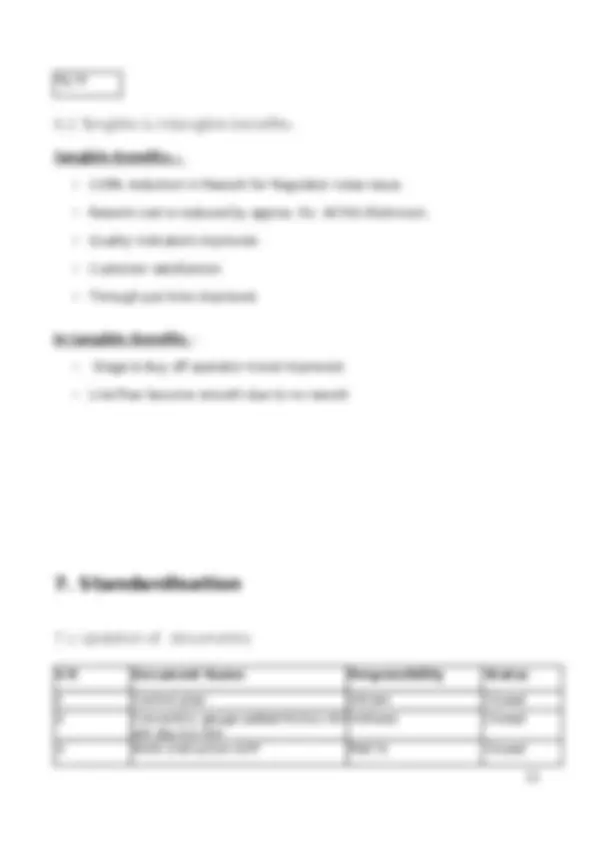
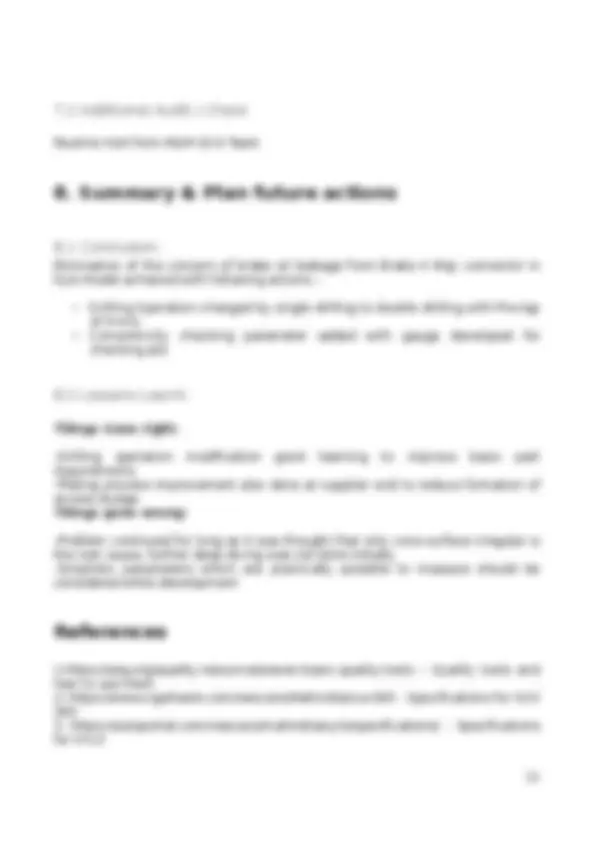
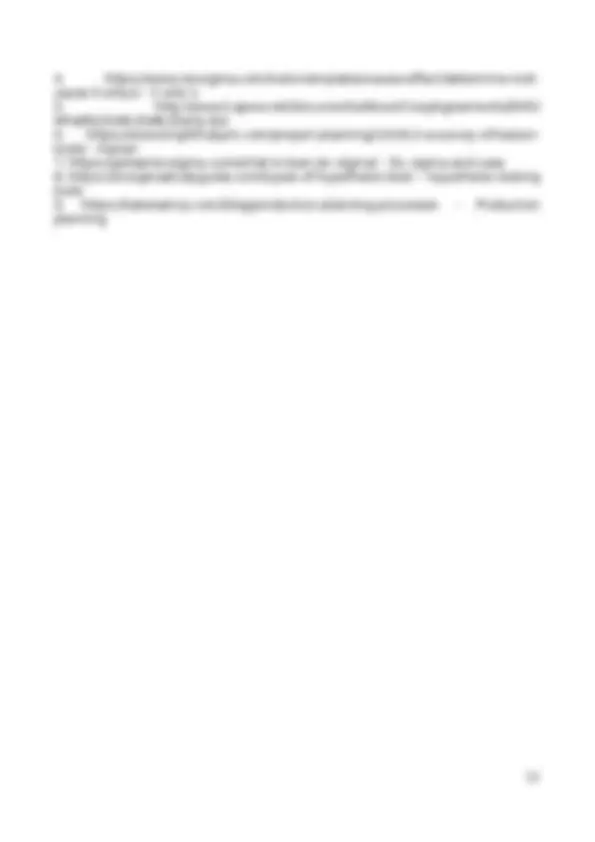
Study with the several resources on Docsity
Earn points by helping other students or get them with a premium plan
Prepare for your exams
Study with the several resources on Docsity
Earn points to download
Earn points by helping other students or get them with a premium plan
Community
Ask the community for help and clear up your study doubts
Discover the best universities in your country according to Docsity users
Free resources
Download our free guides on studying techniques, anxiety management strategies, and thesis advice from Docsity tutors
Eliminating concern of brake oil leakage in Mahindra Xylo and A Pillar pop out of XUV-300
Typology: Study Guides, Projects, Research
1 / 47
This page cannot be seen from the preview
Don't miss anything!
This is to certify that Practice School Project of A.Vikramaditya titled is an original work and that
this work has not been submitted anywhere in any form. Indebtedness to other works/publications
has been duly acknowledged at relevant places. The project work was carried during 9th January
2019 to 8th May 2019 in Mahindra and Mahindra,Nashik.
Signature of PS-III faculty Signature of industry mentor/Supervisor Name: Dr Lalit sharma Name: Mr. Krishna Kapure Designation: Assistant Professor Designation: Projects manager (TCF)
Date: 9th January, 2019
Name of the Students: A.Vikramaditya
Name and Address of the Practice School – III Station:
Mahindra and Mahindra Satpur MIDC Main Road, MIDC, Satpur Colony, Nashik, Maharashtra 422007
Location of the Project: QCA Department
Name and Designation of the Industry Mentor for the Project:
Mr. Krishna kapure Projects Manager (TCF)
Organization Contact Number: 9881130299
The internship opportunity I had with Mahindra and Mahindra (Nashik) was a great chance for
learning and career development. I am very lucky to work with team of wonderful people who
helped throughout this internship. I express my deepest gratitude to Mr. Krishna kapure for providing
me platform for improving my skills.
I express my deepest thanks to Mr. Krishna kapure who took time out to hear, guide and help me in
completing my daily tasks. Whenever needed he would share his expertise and knowledge, which
helped me improving my skills.
I wish to thank my Faculty Mentor, Dr Lalit sharma , for motivating me throughout the internship.
I consider this opportunity as a big milestone in my career development. I will strive to use gained
skills and knowledge in best possible way, and I will continue to work on their improvement in order
to attain desired career objectives.
A research process consists of stages or steps that guide the project from its conception through the final analysis, recommendations and ultimate actions. The research process provides a systematic, planned approach to the research project and ensures that all aspects of the research project are consistent with each other.
The research process has four distinct yet interrelated steps for research analysis It has a logical and hierarchical ordering:
Determination of information research problem.
Development of appropriate research design.
Execution of research design.
Communication of results
Mahindra & Mahindra Limited launched their latest Multi Utility Vehicle (MUV) “Xylo” in India on January 13, 2009. The car boasts of having all the luxurious features that are seen in today’s sedans, with the ample space of a utility vehicle. Xylo's muscular stance contributes to its commanding road presence. Fully packed with the latest features, the MUV is sure to impress Indian consumers and provide a stiff competition to the other vehicles within its class.
Performance Of Mahindra XYLO Under the hood of Mahindra Xylo lies a 4-cylinder turbocharged, diesel engine, which generates a power of 112bhp @ 3800 rpm. The powerful engine is mated to 5- gears manual transmission. The car accelerates from rest to 60 km/h in just 5.8 seconds.
The problem of A-Pillar popping out was reportedly informed by the Mahindra and Mahindra for the new XUV-300 prior to its launch.
There has been a total of 1293 vehicles already in the yard after the final rollout before this issue was spotted as a concern during the final Audit of the vehicle.
The issue was so serious and a critical concern as a reported number of 40 were to be sent for test drives three days after the problem was reported which made it into an ICA (Immediate corrective action)
Fig 1
Fig 2. 4W 1H
The new XUV-300 was nearing its launch date and this problem was identified 15 days before hand The sheer number of vehicles that were involved to be reworked were far too many considering the time on hand The launch of this vehicle was seen as a major step in Mahindra as it was all set to succeed XUV- at a lower price point still offering the feel of an SUV The approx. amount of money that was involved in replacing the pillars alone was around 3,25, inr/- The company had a reputation to maintain by avoiding an unsuccessful launch and bad reviews over the vehicle The man power we had at the given time was quite limited as many people were involved in resolving different concerns of the same vehicle due to the Ramp up in production of the vehicle, this ramp up gave raise to other unintended problems which were to be solved to ensure a smooth
Total number of vehicles to be reworked : 1293
A-Pillar application
A-pillar assy at line
vechicle audit at CAI (customer acceptance inspection)
Pillar checking at CAI
Check point in plant
So once the critical concern was identified, we had to make a process flow for the same for our ease of understanding where did it actually go wrong?
As the vehicle is passed through different stages of assembly, we had to first figure out weather the pop out was happening at the initial stages i.e. The problem with the hole where the pillar was to be fitted or weather the problem was of the pillar itself
Hence having a process flow makes it easier to review and proceed from area to area in a systematic way without missing any specific area where the vehicle passes through.
Activities Responsibilities
Fig 5 pie chart of concernQCA andRoll out logistics
Logistics & dispatch
Drive to vessel side
Storage at port
Unloading atPDI port
Transportatio n to port
PDI ( preLoading dispatch inspection)
Quality checks
Activities
Rework estimation
Description Units
Fig 6 process flow chart
Here we chose Fishbone analysis because a cause and effect diagram, can help in brainstorming to identify possible causes of a problem and in sorting ideas into useful categories. A fishbone diagram is a visual way to look at cause and effect. It is a more structured approach than some other tools available for brainstorming causes of a problem (e.g., the Five Whys tool). The problem or effect is displayed at the head or mouth of the fish. Possible contributing causes are listed on the smaller “bones” under various cause categories. A fishbone diagram can be helpful in identifying possible causes for a problem that might not otherwise be considered by directing the team to look at the categories and think of alternative causes. Include team members who have personal knowledge of the processes and systems involved in the problem or event to be investigated.
Process and steps taken for elimination of the concern
MachineMelting Man of 3M tape when exposed to heat
mating parts
No step for application of the glue onto the pillar before mounting it
No being aware of the issue at the given time period
A pillar pop outMaterialMethodFig 9 fishbone diagram
Excessive heat of sun melting the 3M tape inside the pillar which was making the adhesion weak and making the pillar loosely struck onto the body of the vehicle, upon prolonged delay of the concern overtime it was observed that the pillar was completely popping out of the vehicle
Application of wood seal for the sealing application of the A-pillar to the body
Observation from trail 1
Although this was successful at start but when observed the next day the wood seal was found to be a bad alternative as it was not strong enough to provide the adhesion power required to keep the pillar in place
Use of teroson auto sealant Body Repair
Seam sealing: for seam and joint seals.
It’s a Silane-modified polymer
skin formation time: 10 to 20 min, isocyanate-free.
TEROSON MS 9120 SF is a solvent- and isocyanate-free silane-modified polymer for seam and joint sealing as well as bonding of plastic parts, e.g. spoilers, in vehicle body repairs.