
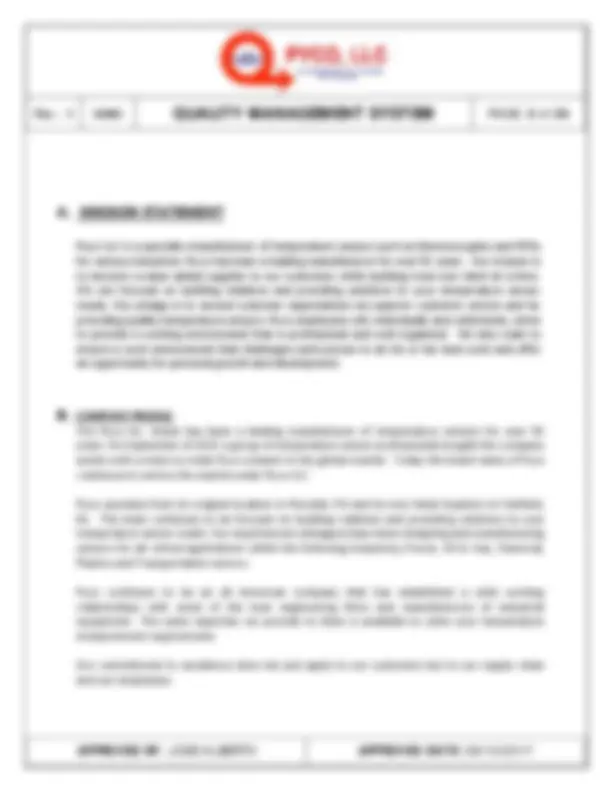
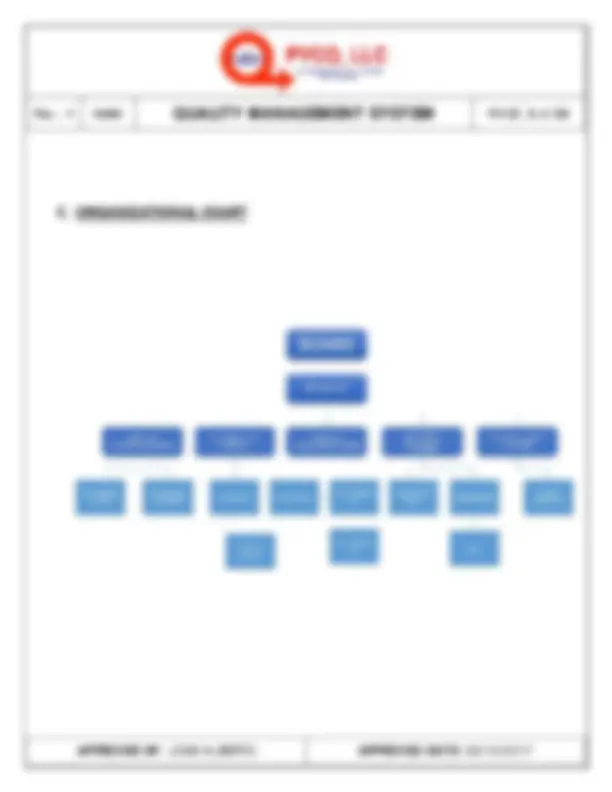
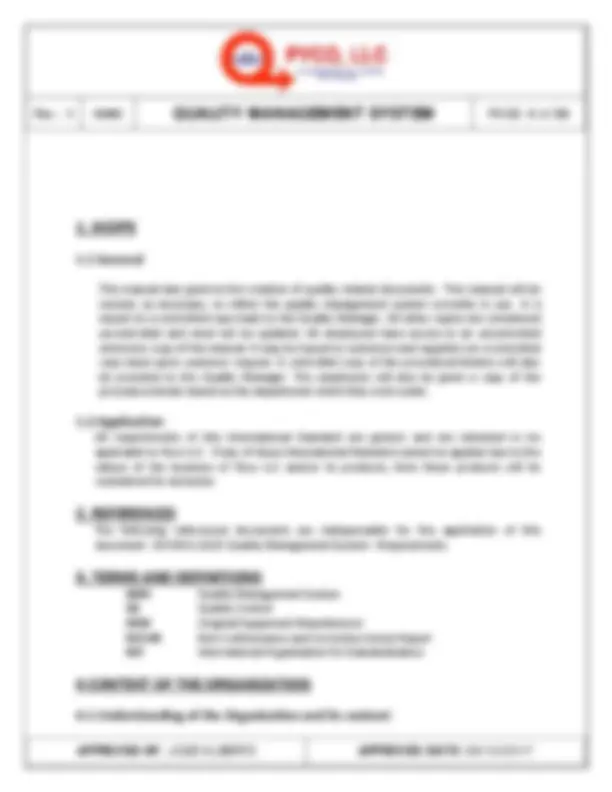
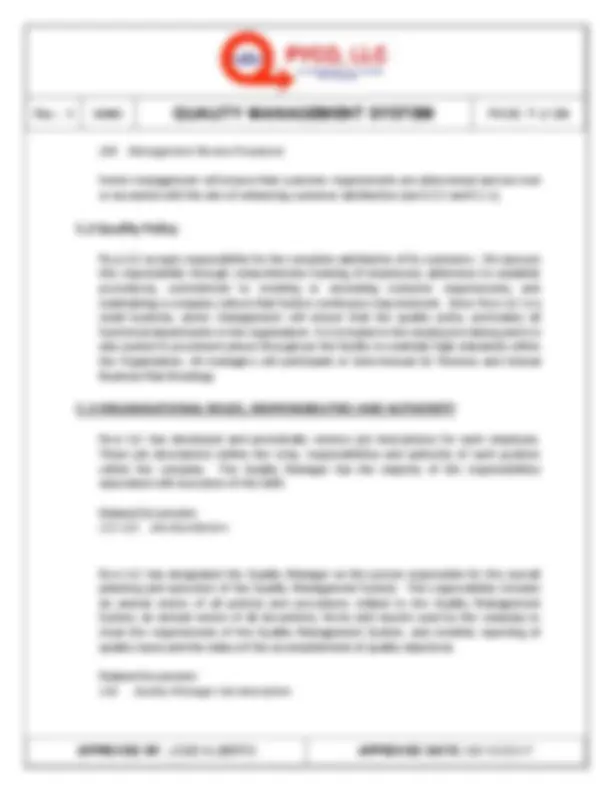
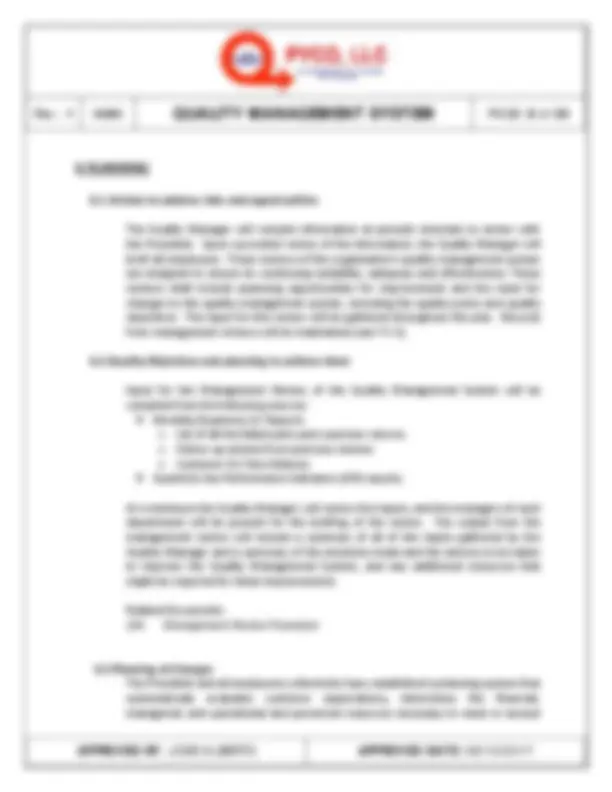
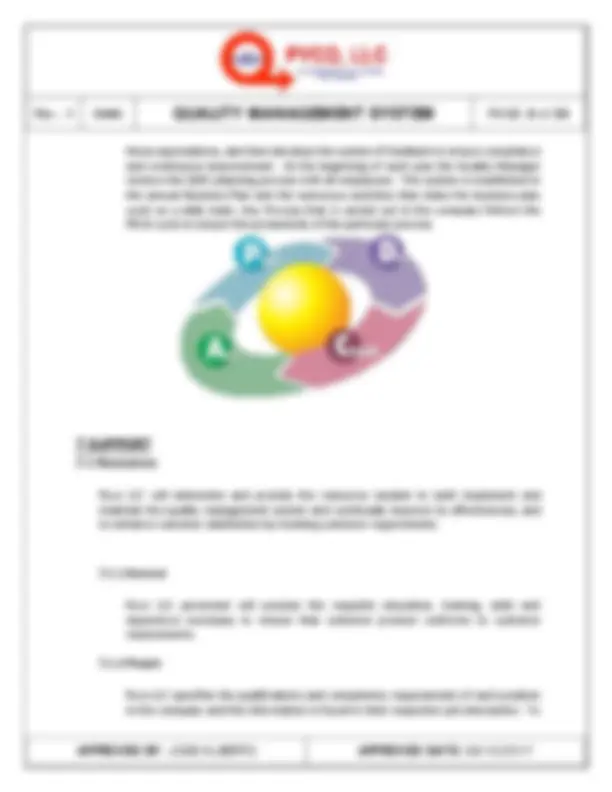
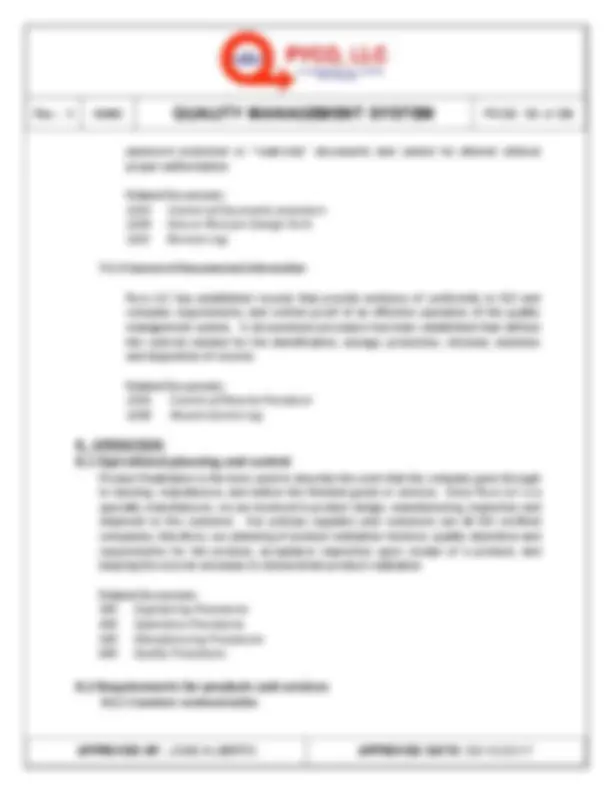
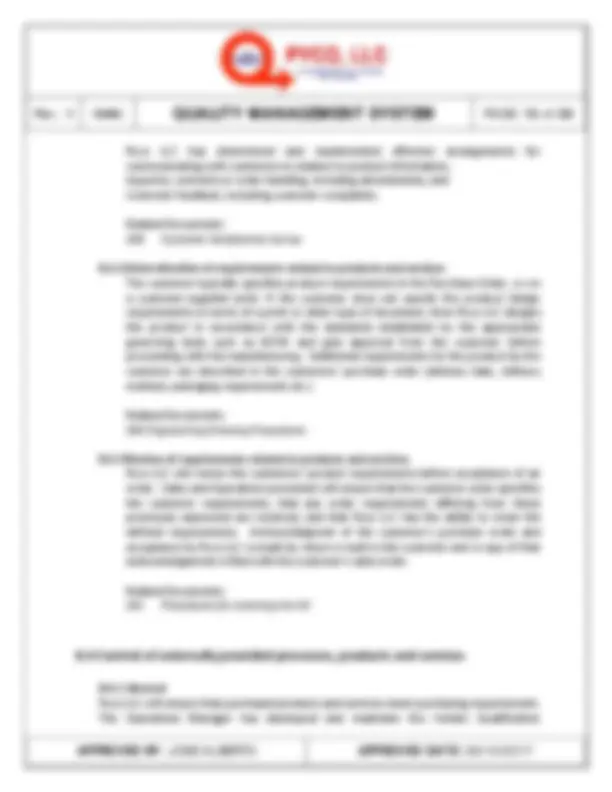
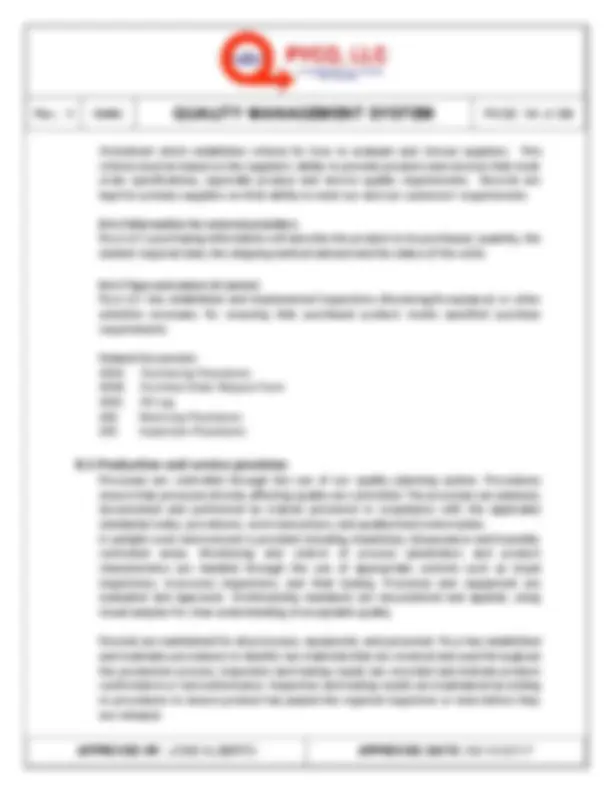

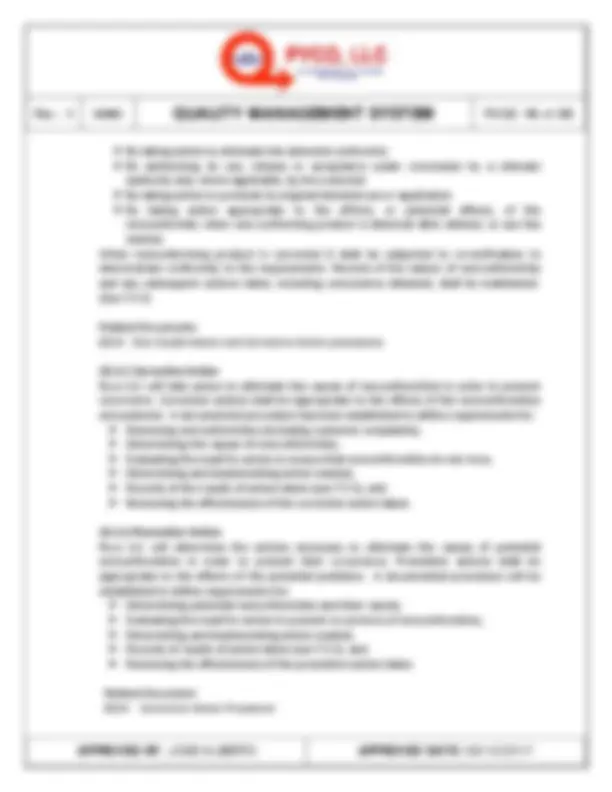
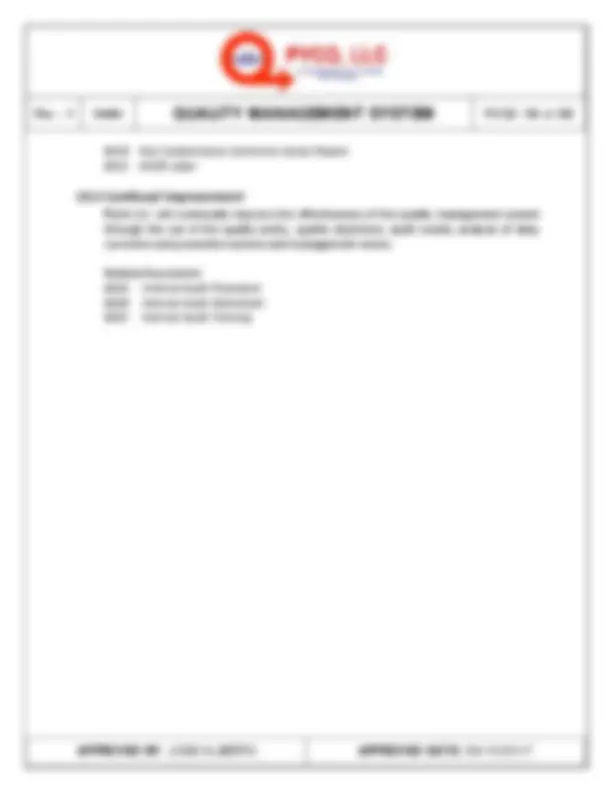
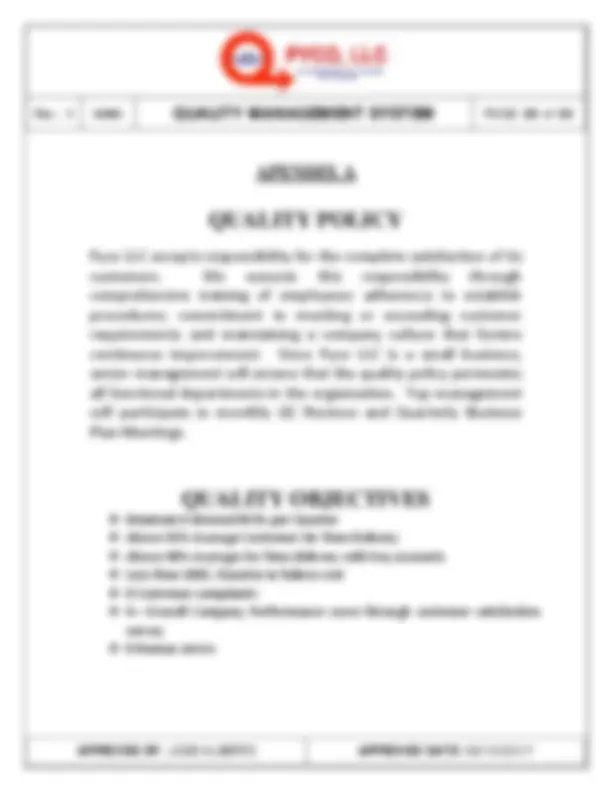
Study with the several resources on Docsity
Earn points by helping other students or get them with a premium plan
Prepare for your exams
Study with the several resources on Docsity
Earn points to download
Earn points by helping other students or get them with a premium plan
Community
Ask the community for help and clear up your study doubts
Discover the best universities in your country according to Docsity users
Free resources
Download our free guides on studying techniques, anxiety management strategies, and thesis advice from Docsity tutors
The Pyco LLC quality management system documentation includes: ➢ A quality manual containing the quality policies and quality objectives. ➢ Documented ...
Typology: Exams
1 / 21
This page cannot be seen from the preview
Don't miss anything!
ISO 9001 QUALITY MANAGEMENT SYSTEM
- Table of Contents SECTION TITLE PAGE
This manual also governs the creation of quality related documents. This manual will be revised, as necessary, to reflect the quality management system currently in use. It is issued on a controlled copy basis to the Quality Manager. All other copies are considered uncontrolled and need not be updated. All employees have access to an uncontrolled electronic copy of the manual. It may be issued to customers and suppliers on a controlled copy basis upon customer request. A controlled copy of the procedural binders will also be provided to the Quality Manager. The employees will also be given a copy of the procedure binder based on the department which they work under.
All requirements of this International Standard are generic and are intended to be applicable to Pyco LLC. If any of these International Standard cannot be applied due to the nature of the business of Pyco LLC and/or its products, then those products will be considered for exclusion.
The following referenced documents are indispensable for the application of this document: ISO 9001:2015 Quality Management System - Requirements.
QMS Quality Management System QC Quality Control OEM Original Equipment Manufacturer NCCAR Non Conformance and Corrective Action Report ISO International Organization for Standardization
4.3.1 Quality Manual
Pyco LLC has established and maintains a Quality Manual. The Quality Manual includes a Table of Contents and eight binders that include procedures, documents and forms necessary to effectively manage the Quality Management System. For Pyco LLC, the Quality Management System encompasses all of the interrelated functions of the company. Interaction with the Administration, Sales, Marketing, IT, Operations Engineering, and Accounting functions of the company have an impact on the quality of the products and services the company provides to our customers, therefore, this management system incorporates all of those functions. The company has a framed diagram posted outside of the office that depicts the relationship between QMS, the Mission, Policies, and Objectives of the QMS and how this all works within the functional departments of the company.
The President of Pyco LLC is dedicated to meeting or exceeding customer expectations by ensuring that company objectives and in-house processes lead toward continual improvement and prevention of issues that reduce our ability to meet customer expectations. Establishment of a Quality Manual and Quality Policy and dedicating the resources necessary to ensure proper implementation of these Policies, coupled with the Goals and Objectives established in the annual Business Plan demonstrates management's commitment. Periodic QC Meetings and Quarterly Reviews ensure that management is effectively monitoring the progress of the various initiatives and objectives of the organization.
Related Documents:
104 Management Review Procedure
Senior management will ensure that customer requirements are determined and are met or exceeded with the aim of enhancing customer satisfaction (see 8.2.2 and 9.1.1).
Pyco LLC accepts responsibility for the complete satisfaction of its customers. We execute this responsibility through comprehensive training of employees; adherence to establish procedures; commitment to meeting or exceeding customer requirements; and maintaining a company culture that fosters continuous improvement. Since Pyco LLC is a small business, senior management will ensure that the quality policy permeates all functional departments in the organization. It is included in the employee training and it is also posted in prominent places throughout the facility to maintain high standards within the Organization. All managers will participate in Semi-Annual QC Reviews and Annual Business Plan Meetings.
Pyco LLC has developed and periodically reviews job descriptions for each employee. These job descriptions define the roles, responsibilities and authority of each position within the company. The Quality Manager has the majority of the responsibilities associated with execution of the QMS.
Related Documents: 111-121 Job descriptions
Pyco LLC has designated the Quality Manager as the person responsible for the overall planning and execution of the Quality Management System. This responsibility includes an annual review of all policies and procedures related to the Quality Management System, an annual review of all documents, forms and reports used by the company to meet the requirements of the Quality Management System, and monthly reporting of quality issues and the status of the accomplishment of quality objectives.
Related Documents: 118 Quality Manager Job description
those expectations, and then develops the system of feedback to ensure compliance and continuous improvement. At the beginning of each year the Quality Manager reviews the QMS planning process with all employees. This system is manifested in the annual Business Plan and the numerous activities that make the business plan work on a daily basis. Any Process that is carried out in the company follows the PDCA cycle to ensure the productivity of the particular process.
Pyco LLC will determine and provide the resources needed to both implement and maintain the quality management system and continually improve its effectiveness, and to enhance customer satisfaction by meeting customer requirements.
7.1.1 General
Pyco LLC personnel will possess the requisite education, training, skills and experience necessary to ensure that customer product conforms to customer requirements.
7.1.2 People
Pyco LLC specifies the qualifications and competency requirements of each position in the company and this information is found in their respective job description. To
ensure currency and on-going competency the company has training in product, sales and procedures throughout the year.
7.1.3 Infrastructure
Pyco LLC will determine, provide and maintain the infrastructure needed to achieve conformity to product and customer requirements. This infrastructure includes the physical facility, manufacturing equipment, inspection equipment and any supporting services that may be required.
7.1.4 Work Environment
Pyco LLC will determine and manage the work environment needed to achieve conformity to product and customer requirements.
7.1.5 Monitoring and measuring resources
Pyco maintains appropriate monitoring and measuring equipment needed to provide evidence of conformity of product to pre-determined requirements. When the customer requests a copy of this evidence (Certificate of Conformance, Dimensional Reports, Material Reports etc.), the requested certificate is prepared and sent to the customer. Pyco also retains a copy of the certificate along with the customer sales order. Additionally, Pyco LLC provides measurement (dimensional inspections) of product upon receipt from suppliers to make sure the items supplied by the vendor has the requested specification. Where necessary to ensure valid results, measuring equipment shall: Be calibrated or verified, or both, at specified intervals, or prior to use, against measurement standards traceable to international or national measurement standards; where no such standards exist, the basis used for calibration or verification shall be recorded (see 7.5.3); Be adjusted or re-adjusted as necessary; Have identification in order to determine its calibration status; Be safeguarded from adjustments that would invalidate the measurement result; Be protected from damage and deterioration during handling, maintenance and storage.
Related Documents: 501 Calibration Procedure
password protected or “read-only” documents and cannot be altered without proper authorization.
Related Documents: 102A Control of Documents procedure 102B New or Revision Change Form 102C Revision Log
7.5.3 Control of Documented information
Pyco LLC has established records that provide evidence of conformity to ISO and company requirements, and written proof of an effective operation of the quality management system. A documented procedure has been established that defines the controls needed for the identification, storage, protection, retrieval, retention and disposition of records.
Related Documents: 103A Control of Records Procedure 103B Record Control Log
Product Realization is the term used to describe the work that the company goes through to develop, manufacture, and deliver the finished goods or services. Since Pyco LLC is a specialty manufacturer, we are involved in product design, manufacturing, inspection and shipment to the customer. Our primary suppliers and customers are all ISO certified companies, therefore, our planning of product realization involves: quality objectives and requirements for the product; acceptance inspection upon receipt of a product; and keeping the records necessary to demonstrate product realization.
Related Documents: 300 Engineering Procedures 400 Operations Procedures 500 Manufacturing Procedures 600 Quality Procedures
8.2.1 Customer communication
Pyco LLC has determined and implemented effective arrangements for communicating with customers in relation to product information; Inquiries, contracts or order handling, including amendments; and Customer feedback, including customer complaints.
Related Documents: 206 Customer Satisfaction Survey
8.2.2 Determination of requirements related to products and services The customer typically specifies product requirements in the Purchase Order, or on a customer-supplied print. If the customer does not specify the product design requirements in terms of a print or other type of document, then Pyco LLC designs the product in accordance with the standards established by the appropriate governing body such as ASTM and gets approval from the customer before proceeding with the manufacturing. Additional requirements for the product by the customer are described in the customers' purchase order (delivery date, delivery method, packaging requirements etc.)
Related Documents: 304 Engineering Drawing Procedures
8.2.3 Review of requirements related to products and services Pyco LLC will review the customers' product requirements before acceptance of an order. Sales and Operations personnel will ensure that the customer order specifies the customer requirements; that any order requirements differing from those previously expressed are resolved; and that Pyco LLC has the ability to meet the defined requirements. Acknowledgment of the customer's purchase order and acceptance by Pyco LLC is made by return e-mail to the customer and a copy of that acknowledgement is filed with the customer's sales order.
Related Documents: 201 Procedures for entering the SO
8.4.1 General Pyco LLC will ensure that purchased products and services meet purchasing requirements. The Operations Manager has developed and maintains the Vendor Qualification
Nonconforming product may be released under authorized concession as stated in Control of Nonconforming Product procedure.
Pyco has established and maintains procedures for preventing damage and deterioration of raw materials and products in all phases of manufacture, storage and delivery.
Team members are provided with training in proper handling methods. Training covers safe handling methods, proper use of handling equipment, and prevention of damage to product.
Packing, packaging, and marking of products are controlled throughout the production process to ensure conformance to customer requirements and prevent damage. The methods of preservation and segregation for preventing damage and deterioration of raw materials and products are controlled through procedures and work instructions. Final product is protected and shipped to maintain the quality of the product.
Related Documents: 101A New Employee Procedures 102A Control of Records procedures 105 Training Procedures 601A Non Conformance and Corrective Action Procedures 407 Shipping Procedures
9.1.1 General Pyco LLC will plan and implement the monitoring, measurement, analysis and improvement processes needed to: Demonstrate conformity to product requirements; Ensure conformity of the quality management system; and Continually improve the effectiveness of the quality management system.
This shall include determination of applicable methods, including statistical techniques, and the extent of their use.
9.1.2 Customer Satisfaction As one of the measurements of the performance of the quality management system, Pyco LLC will monitor information relating to customer perception as to whether Pyco LLC has met customer requirements. The primary method for obtaining and using this information shall be from customer satisfaction surveys.
Related Documents: 206 Customer Satisfaction Survey
9.1.3 Analysis and evaluation Pyco LLC will determine, collect and analyze appropriate data to demonstrate the suitability and effectiveness of the quality management system and to evaluate where continual improvement of the effectiveness of the quality management system can be made. This shall include data generated as a result of monitoring and measurement and from other relevant sources. The analysis of data will provide information relating to: Customer satisfaction (see 8.2.1), Conformity to product requirements (see 8.2.4), Characteristics and trends of processes and products, including opportunities for preventive action (see 8.2.3 and 8.2.4), and Supplier performance (see 7.4.1).
Related Documents: 206 Customer Satisfaction Survey 603A Certificate of Conformance Procedure 601A Non Conformance and Corrective Action Procedure 602B Non Conformance Corrective Action Report 104 Management Review Procedure
Pyco LLC will conduct internal audits at planned intervals to determine whether the quality management system conforms to the planned arrangements (see 6.1), to the requirements of this International Standard and to the quality management system requirements established by the company and is effectively implemented and maintained. The audit criteria, scope, frequency and methods will be defined. The selection of auditors and conduct of audits shall ensure objectivity and impartiality of the audit process. Auditors shall not audit their own work. A documented procedure shall be established to define the responsibilities and requirements for planning and conducting audits, establishing records and reporting results. Records of the audits and their results shall be
By taking action to eliminate the detected conformity By authorizing its use, release or acceptance under concession by a relevant authority and, where applicable, by the customer By taking action to preclude its original intended use or application By taking action appropriate to the effects, or potential effects, of the nonconformity when non-conforming product is detected after delivery or use has started. When nonconforming product is corrected it shall be subjected to re-verification to demonstrate conformity to the requirements. Records of the nature of nonconformities and any subsequent actions taken, including concessions obtained, shall be maintained. (See 7.5.3)
Related Documents: 601A Non Conformance and Corrective Action procedures
10.2.1 Corrective Action Pyco LLC will take action to eliminate the causes of nonconformities in order to prevent recurrence. Corrective actions shall be appropriate to the effects of the nonconformities encountered. A documented procedure has been established to define requirements for: Reviewing nonconformities (including customer complaints), Determining the causes of nonconformities, Evaluating the need for action to ensure that nonconformities do not recur, Determining and implementing action needed, Records of the results of action taken (see 7.5.3), and Reviewing the effectiveness of the corrective action taken.
10.2.2 Preventive Action Pyco LLC will determine the actions necessary to eliminate the causes of potential nonconformities in order to prevent their occurrence. Preventive actions shall be appropriate to the effects of the potential problems. A documented procedure will be established to define requirements for: Determining potential nonconformities and their causes, Evaluating the need for action to prevent occurrence of nonconformities, Determining and implementing action needed, Records of results of action taken (see 7.5.3), and Reviewing the effectiveness of the preventive action taken.
Related Document: 601A Corrective Action Procedure
601B Non Conformance Corrective Action Report 601C NCDR Label
through the use of the quality policy, quality objectives, audit results, analysis of data, corrective and preventive actions and management review.
Related Documents: 602A Internal Audit Procedure 602B Internal Audit Worksheet 602C Internal Audit Training