
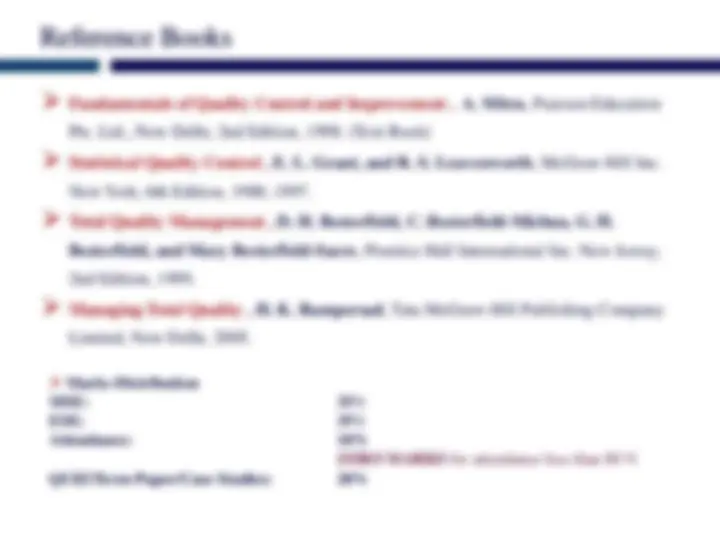
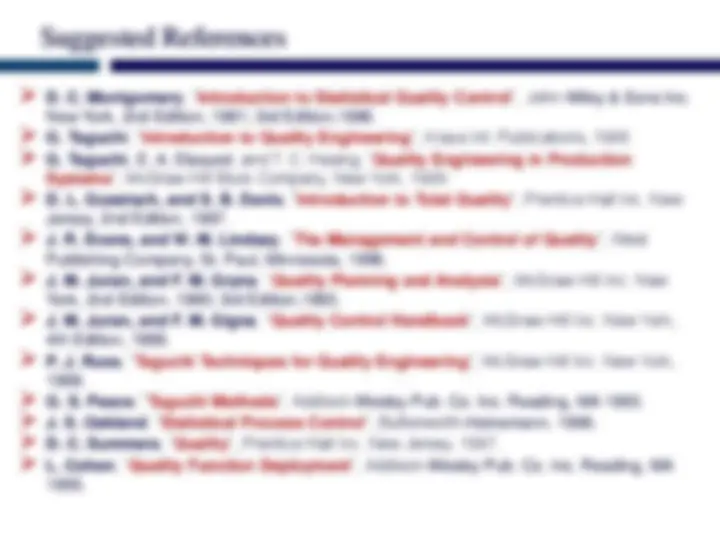
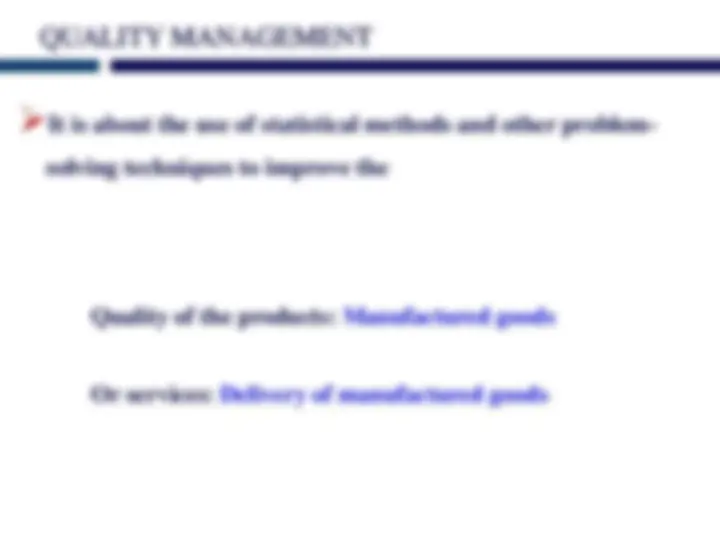
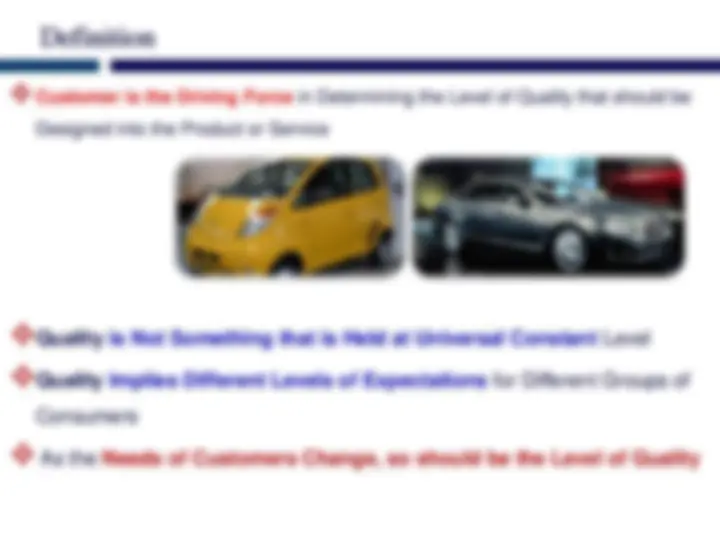
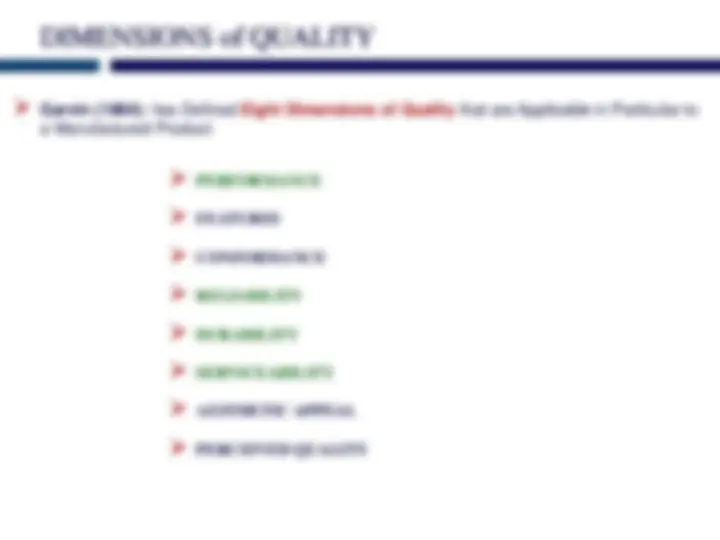
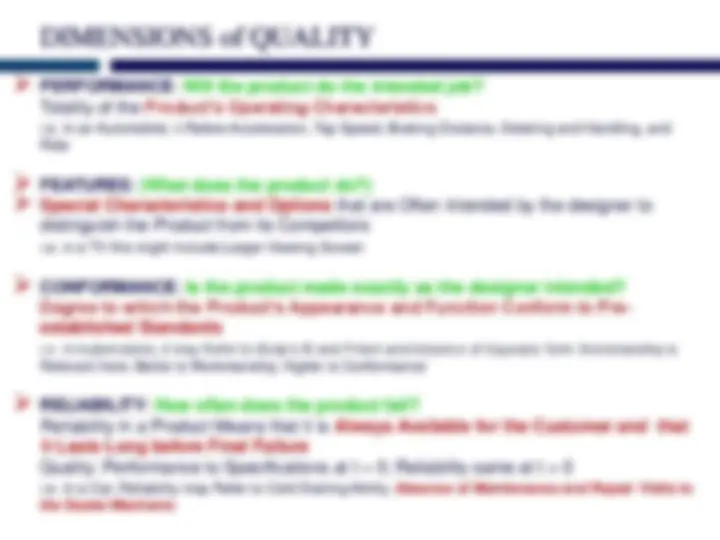
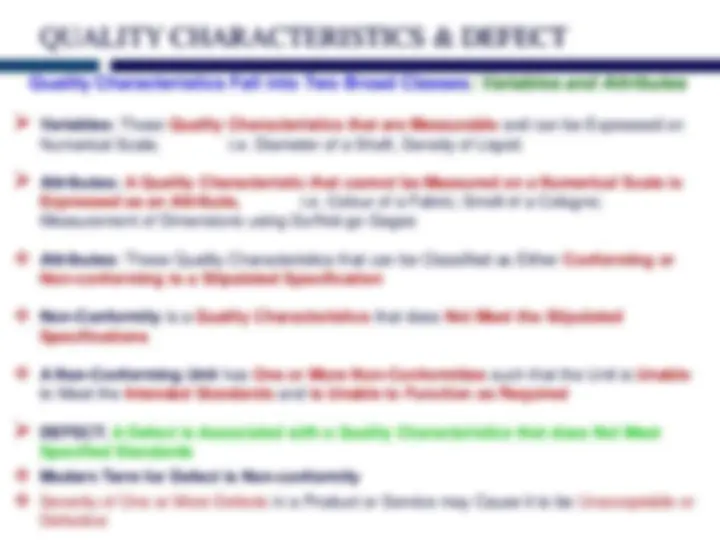
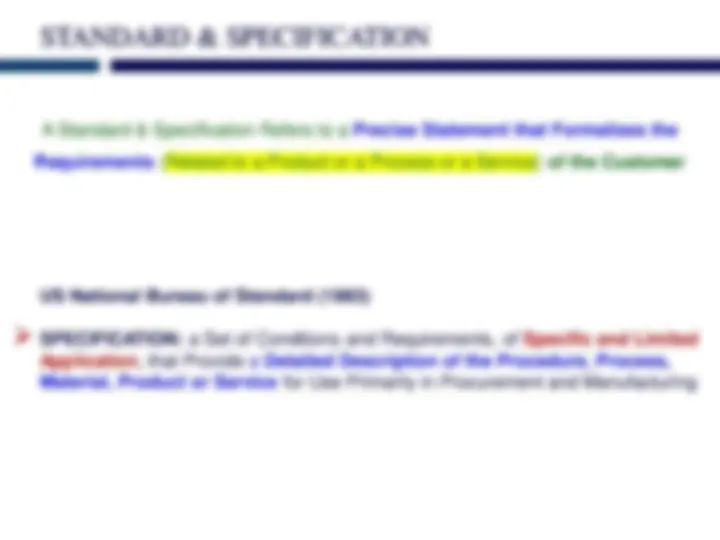
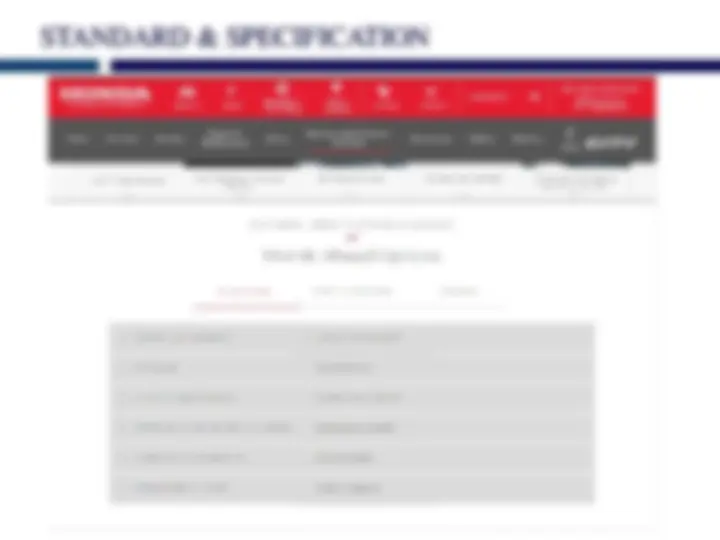
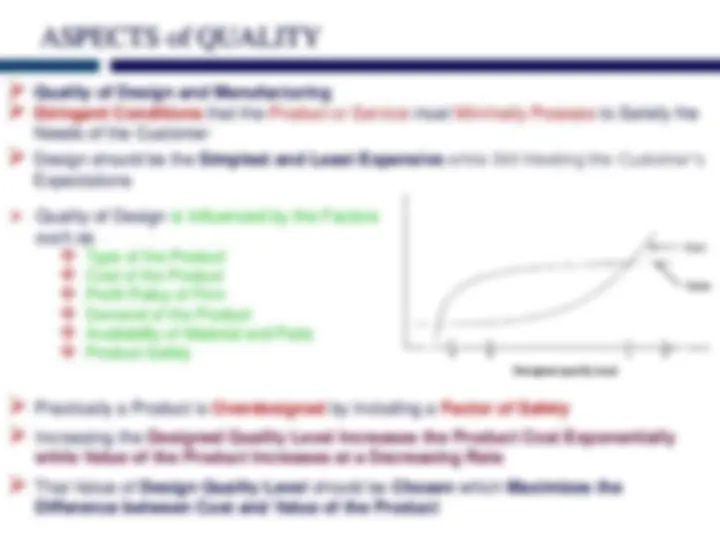
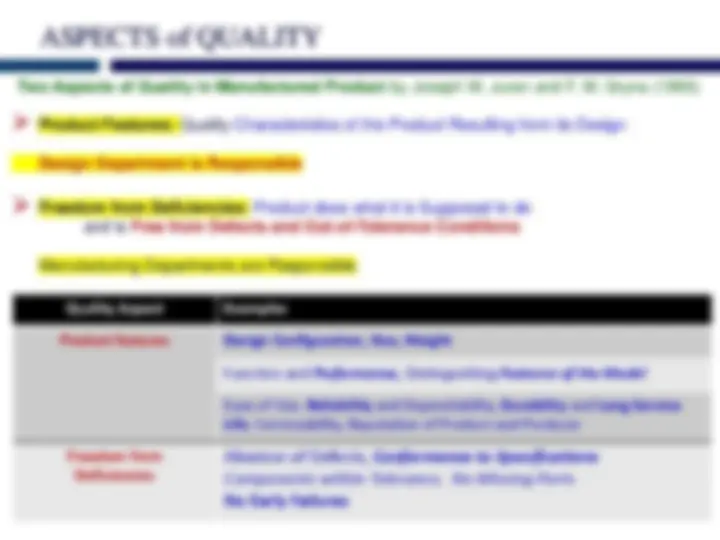
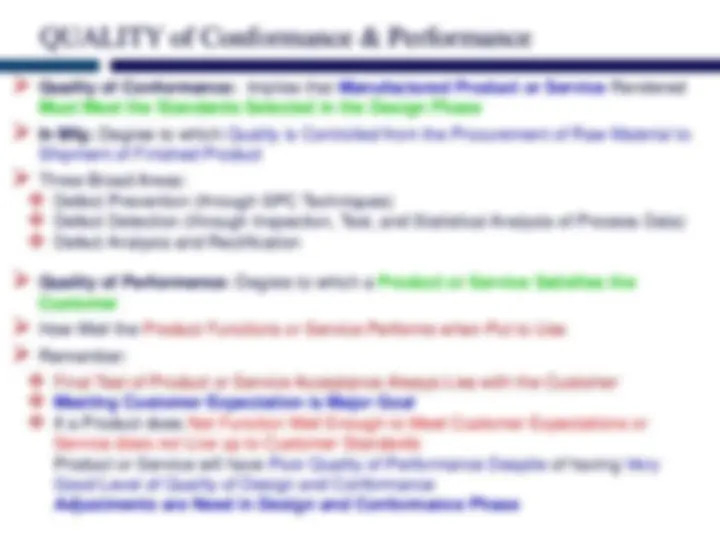
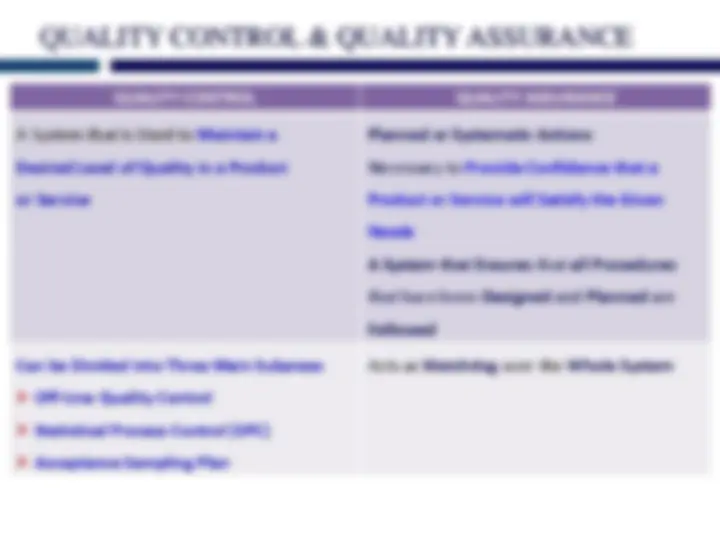
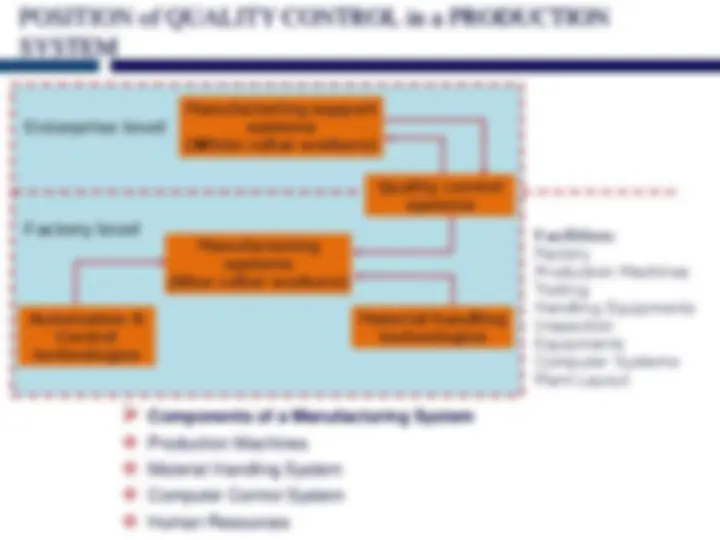
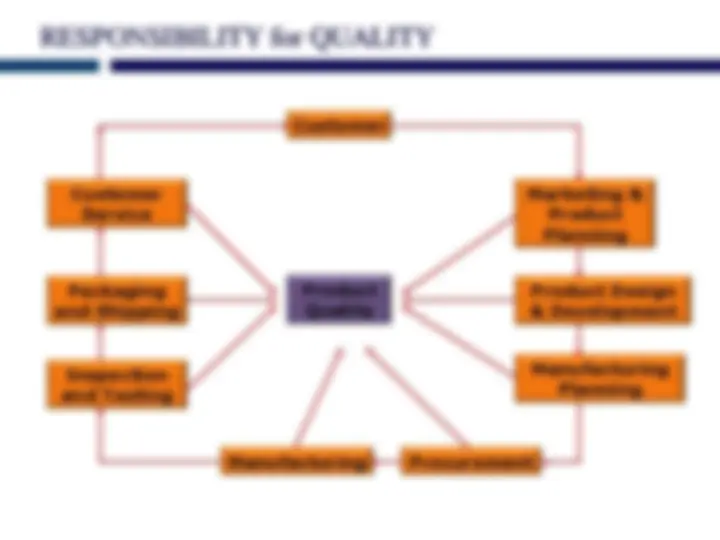
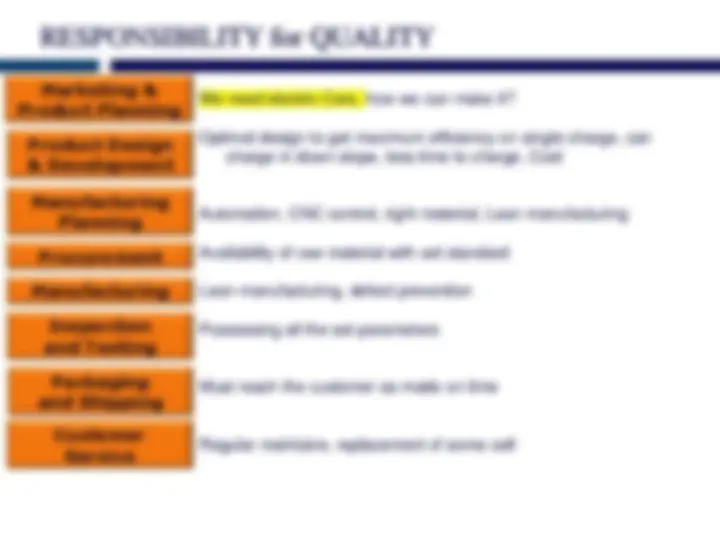
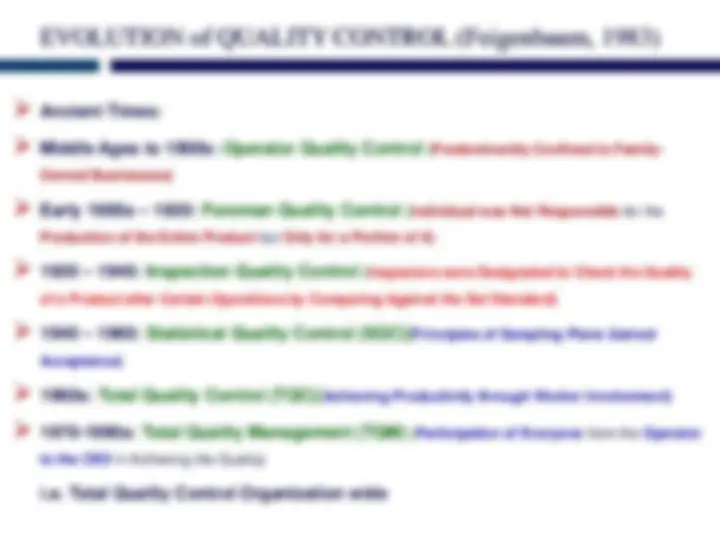
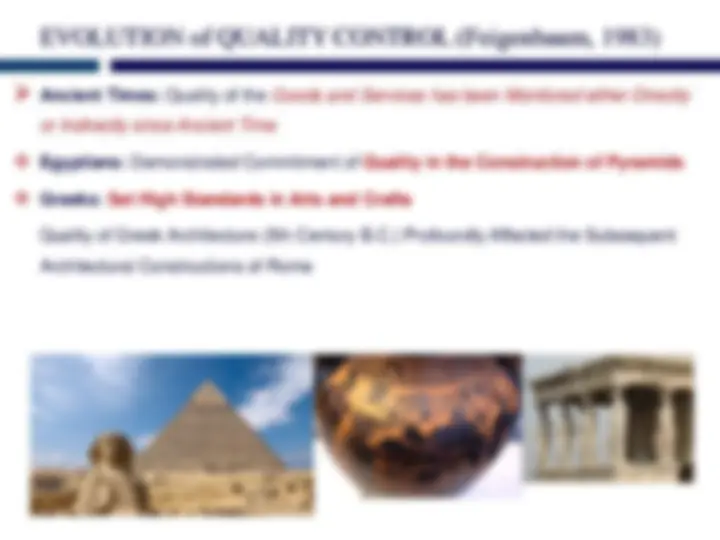
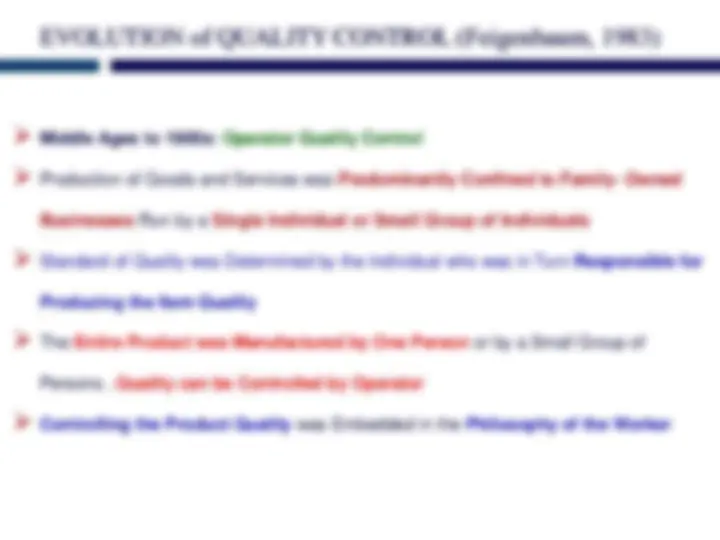
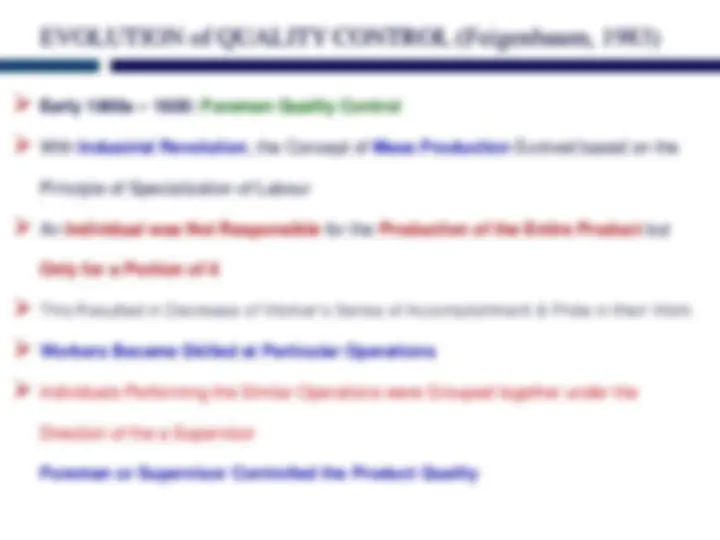
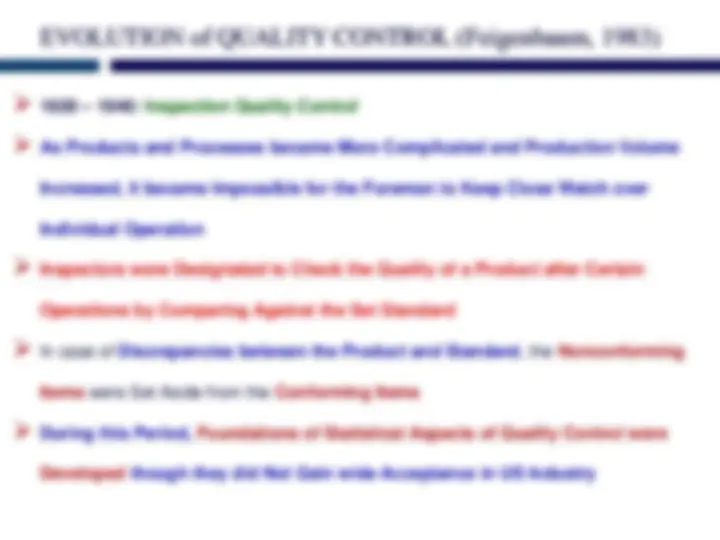
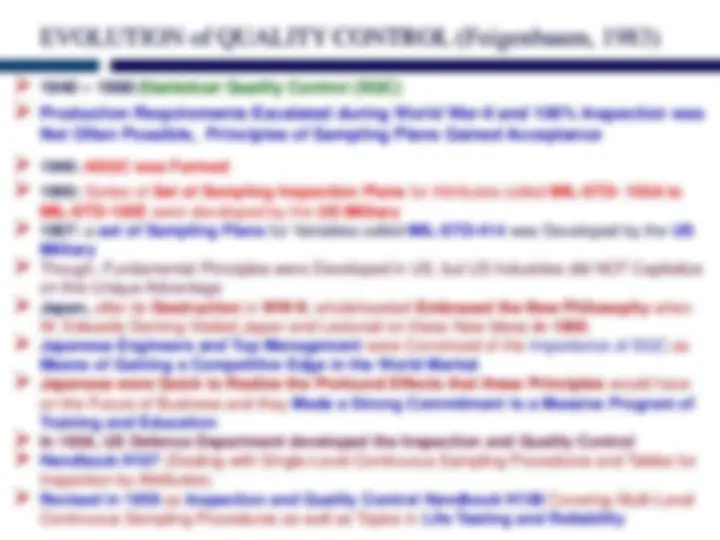
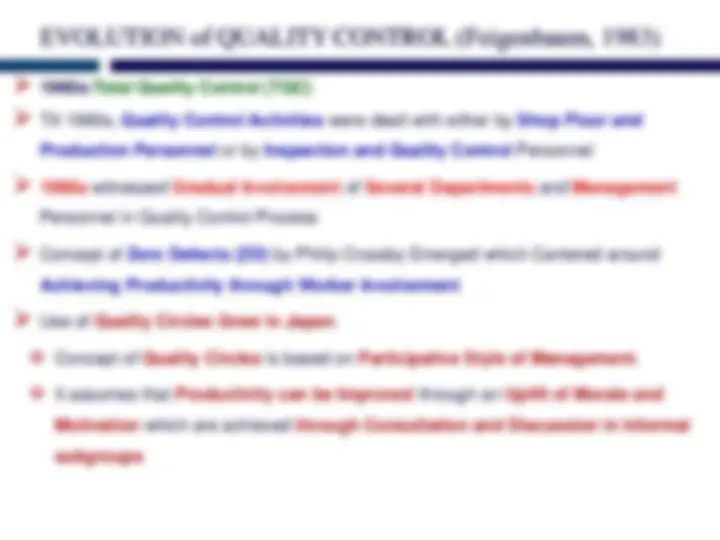
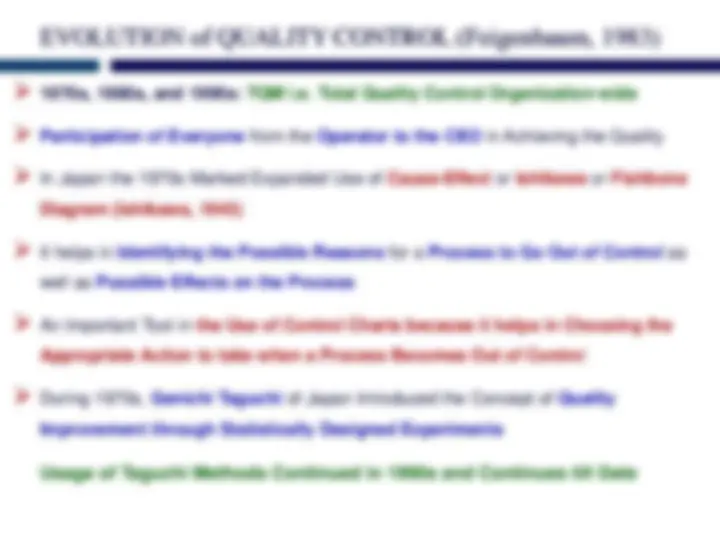
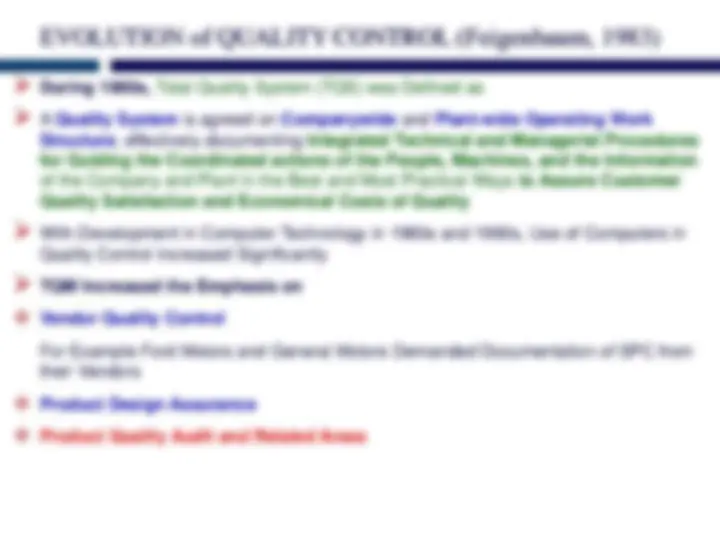
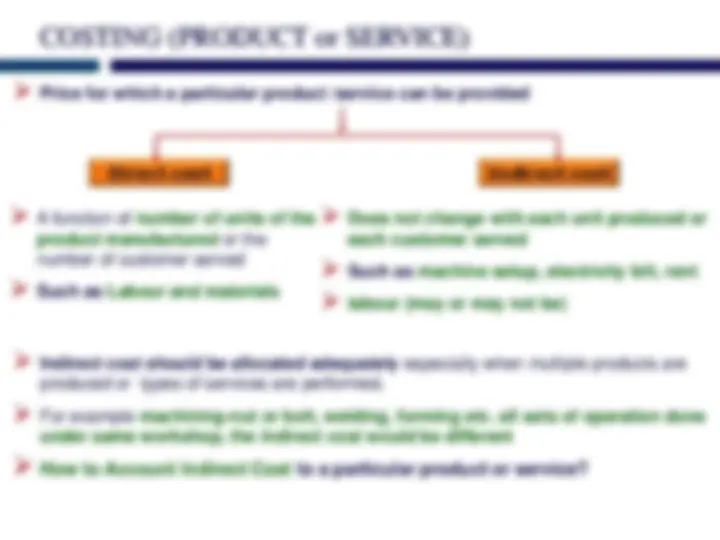
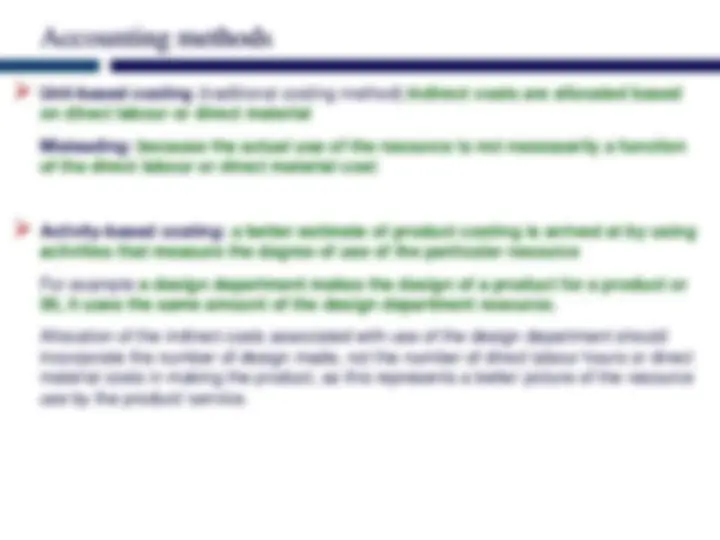
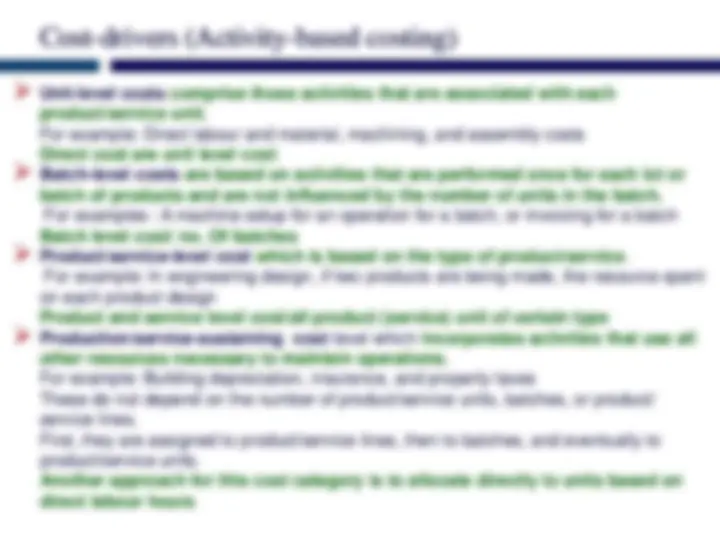
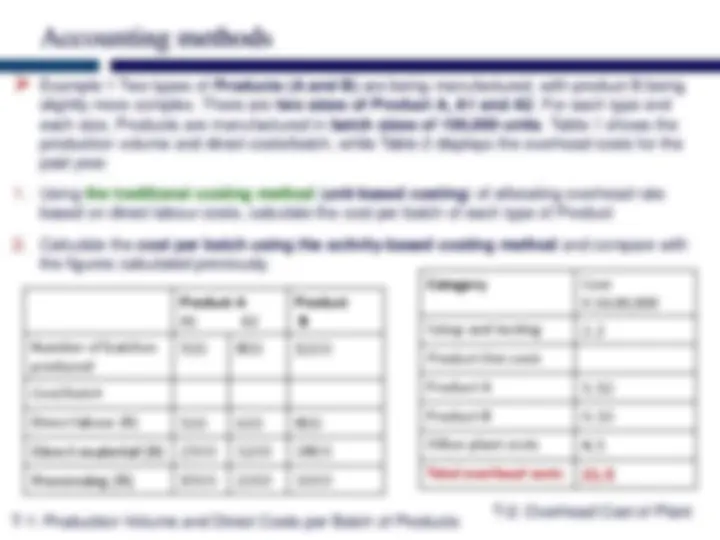
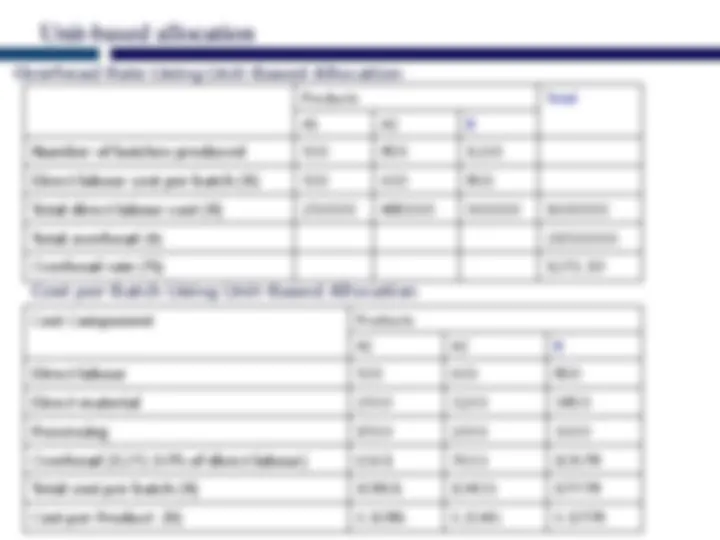
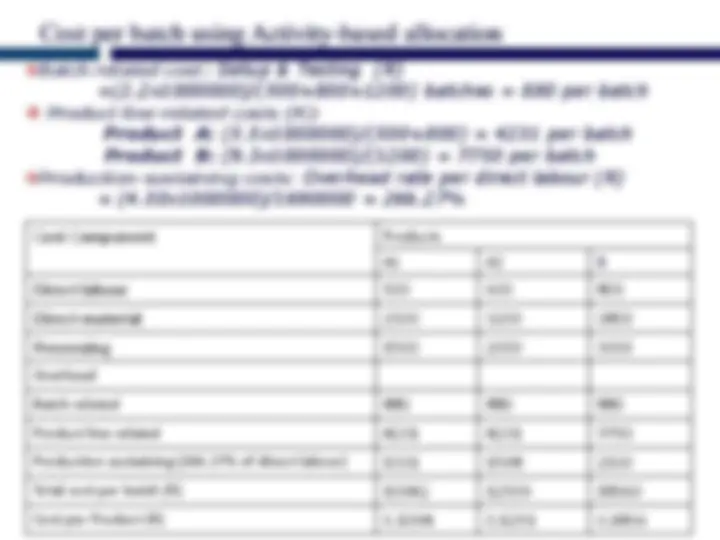
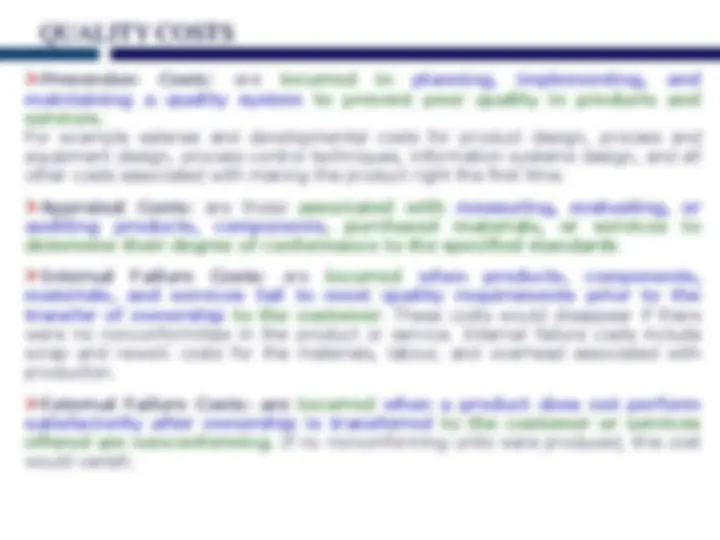
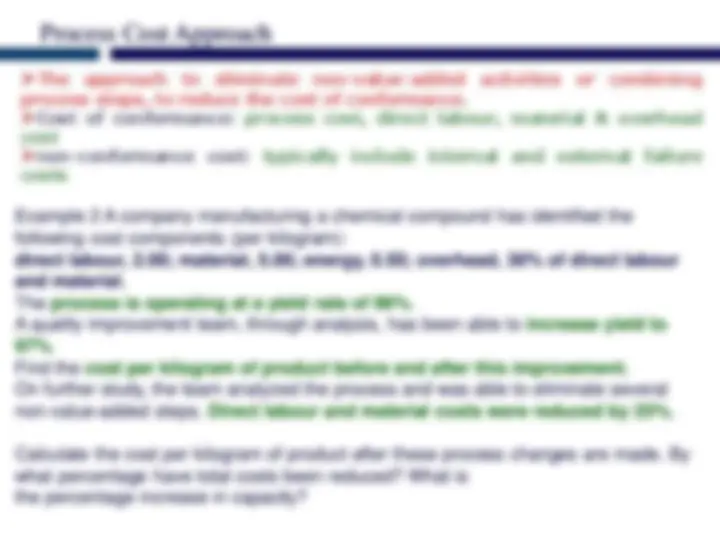
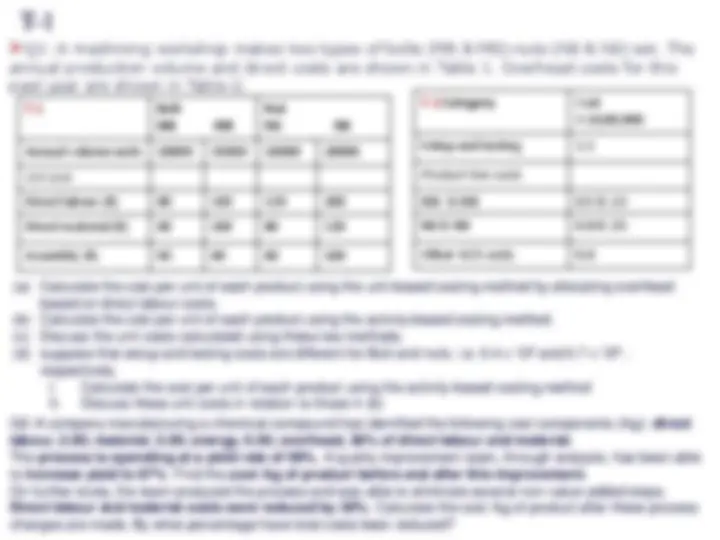
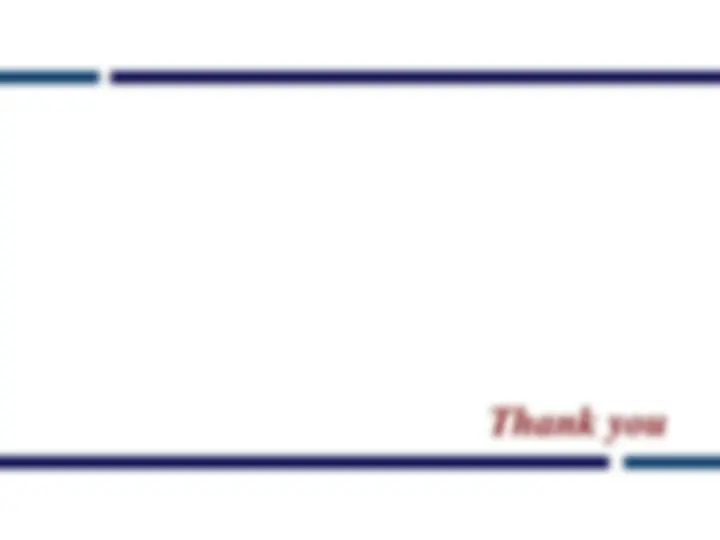
Study with the several resources on Docsity
Earn points by helping other students or get them with a premium plan
Prepare for your exams
Study with the several resources on Docsity
Earn points to download
Earn points by helping other students or get them with a premium plan
Community
Ask the community for help and clear up your study doubts
Discover the best universities in your country according to Docsity users
Free resources
Download our free guides on studying techniques, anxiety management strategies, and thesis advice from Docsity tutors
qaity jotes of quality management
Typology: Lecture notes
1 / 43
This page cannot be seen from the preview
Don't miss anything!
Topic ~ No. of Lectures 1 Introduction: Different definitions, dimensions, aspects of quality, Traditional and modern view of Quality Control, Different Philosophies by Quality Gurus
2 Modern Quality Control Technologies: Quality engineering using Taguchi Methods, Off-line and On-line quality control, Concepts of Robust Design, Taguchi Loss Function, Quality Function Deployment (QFD)
3 Statistical Process Control (SPC): Manufacturing process variability, manufacturing process capability, and tolerances; Tools/methods used in SPC: Control Charts, Pareto charts, Fishbone diagram, etc. Implementation of SPC.
4 Control Charts: Theory and applications of control charts; Controls charts for variables: charts averages, ranges, and standard deviation; Control charts for attributes: p and c charts; Fraction defective and number of defects per unit; Different adaptation of control charts
5 Acceptance Sampling: Concept of acceptance sampling; Sampling by attributes: Single and double sampling plans, Use of Dodge Romming and Military standard sampling tables, Construction and use of OC curves; Sampling by variables: Continuous sampling plans
6 Total Quality Management (TQM): Concept and philosophy, Scope, Applications, Implementation, Quality Circles: Objectives, Structures, Techniques
7 Reliability: Concept and definition, Measurement and test of reliability, Design for reliability (DFR), Concepts of Maintainability and Availability
Total 42
Suggested References ➢ D. C. Montgomery , “ Introduction to Statistical Quality Control ”, John-Wiley & Sons Inc. New York, 2nd Edition, 1981; 3rd Edition,1996. ➢ G. Taguchi , “ Introduction to Quality Engineering ”, Kraus Int. Publications, 1986. ➢ G. Taguchi , E. A. Elsayed, and T. C. Hsiang, “ Quality Engineering in Production Systems ”, McGraw Hill Book Company, New York, 1989. ➢ D. L. Goestsch, and S. B. Davis , “ Introduction to Total Quality ”, Prentice Hall Inc. New Jersey, 2nd Edition, 1997. ➢ J. R. Evans, and W. M. Lindsay , “ The Management and Control of Quality ”, West Publishing Company, St. Paul, Minnesota, 1996. ➢ J. M. Juran, and F. M. Gryna , “ Quality Planning and Analysis ”, McGraw Hill Inc. New York, 2nd Edition, 1980; 3rd Edition,1993. ➢ J. M. Juran, and F. M. Gigna , “ Quality Control Handbook ”, McGraw Hill Inc. New York, 4th Edition, 1988. ➢ P. J. Russ , “ Taguchi Techniques for Quality Engineering ”, McGraw Hill Inc. New York,
➢ G. S. Peace , “ Taguchi Methods ”, Addison-Wesley Pub. Co. Inc. Reading, MA 1993. ➢ J. S. Oakland , “ Statistical Process Control ”, Butterworth-Heinemann, 1996. ➢ D. C. Summers , “ Quality ”, Prentice Hall Inc. New Jersey, 1997. ➢ L. Cohen , “ Quality Function Deployment ”, Addison-Wesley Pub. Co. Inc. Reading, MA
Definition of QUALITY
Definition ❖ Customer is the Driving Force in Determining the Level of Quality that should be
Consumers
DIMENSIONS of QUALITY ➢ PERFORMANCE : Will the product do the intended job?
i.e. In an Automobile, it Refers Acceleration, Top Speed, Braking Distance, Steering and Handling, and Ride ➢ FEATURES : (What does the product do?) ➢ Special Characteristics and Options that are Often Intended by the designer to
i.e. in a TV this might Include Larger Viewing Screen ➢ CONFORMANCE : Is the product made exactly as the designer intended?
i.e. In Automobiles, it may Refer to Body’s fit and Finish and Absence of Squeaks Term Workmanship is Relevant here. Better is Workmanship, Higher is Conformance ➢ RELIABILITY : How often does the product fail?
i.e. In a Car, Reliability may Refer to Cold Starting Ability, Absence of Maintenance and Repair Visits to the Dealer/Mechanic
DIMENSIONS of QUALITY ➢ DURABILITY : How long does the product last?
➢ SERVICEABILITY : How easy is it to repair the product?
➢ AESTHETIC APPEAL : What does the product look like?
➢ PERCEIVED QUALITY : What is the reputation of the company or its product?
QUALITY CHARACTERISTICS & DEFECT
➢ Variables: Those Quality Characteristics that are Measurable and can be Expressed on Numerical Scale, i.e. Diameter of a Shaft, Density of Liquid. ➢ Attributes: A Quality Characteristic that cannot be Measured on a Numerical Scale is Expressed as an Attribute, i.e. Colour of a Fabric; Smell of a Cologne; Measurement of Dimensions using Go/Not-go Gages ❖ Attributes: These Quality Characteristics that can be Classified as Either Conforming or Non-conforming to a Stipulated Specification ❖ Non-Conformity is a Quality Characteristics that does Not Meet the Stipulated Specifications ❖ A Non-Conforming Unit has One or More Non-Conformities such that the Unit is Unable to Meet the Intended Standards and is Unable to Function as Required ➢ DEFECT: A Defect is Associated with a Quality Characteristics that does Not Meet Specified Standards ❖ Modern Term for Defect is Non-conformity ❖ Severity of One or More Defects in a Product or Service may Cause it to be Unacceptable or Defective
STANDARD & SPECIFICATION
➢ SPECIFICATION: a Set of Conditions and Requirements, of Specific and Limited
STANDARD & SPECIFICATION ➢ STANDARD: A Prescribed Set of Conditions and Requirements , of General or
➢ Acceptable Bounds on Individual Quality Characteristic are Known as
➢ The Document that Addresses the Requirements of All Quality characteristics
ASPECTS of QUALITY ➢ Quality of Design and Manufacturing:
➢ Quality of Conformance: Implies that
➢ Quality of Performance: Degree to which a
➢ Three aspects of Quality
➢ Two aspects of Quality ➢ Design quality: deliver
➢ Conformance quality: how
ASPECTS of QUALITY Two Aspects of Quality in Manufactured Product by Joseph M. Juran and F. M. Gryna (1993) ➢ Product Features: Quality Characteristics of the Product Resulting from its Design Design Department is Responsible ➢ Freedom from Deficiencies: Product does what it is Supposed to do and is Free from Defects and Out-of-Tolerance Conditions Manufacturing Departments are Responsible Quality Aspect Examples Product features Design Configuration, Size, Weight Function and Performance, Distinguishing Features of the Model Ease of Use, Reliability and Dependability, Durability and Long Service Life , Serviceability, Reputation of Product and Producer Freedom from Deficiencies
QUALITY of Conformance & Performance ➢ Quality of Conformance: Implies that Manufactured Product or Service Rendered
➢ In Mfg: Degree to which Quality is Controlled from the Procurement of Raw Material to
➢ Three Broad Areas: ❖ Defect Prevention (through SPC Techniques) ❖ Defect Detection (through Inspection, Test, and Statistical Analysis of Process Data) ❖ Defect Analysis and Rectification ➢ Quality of Performance: Degree to which a Product or Service Satisfies the
➢ How Well the Product Functions or Service Performs when Put to Use ➢ Remember: ❖ Final Test of Product or Service Acceptance Always Lies with the Customer ❖ Meeting Customer Expectation is Major Goal ❖ If a Product does Not Function Well Enough to Meet Customer Expectations or