
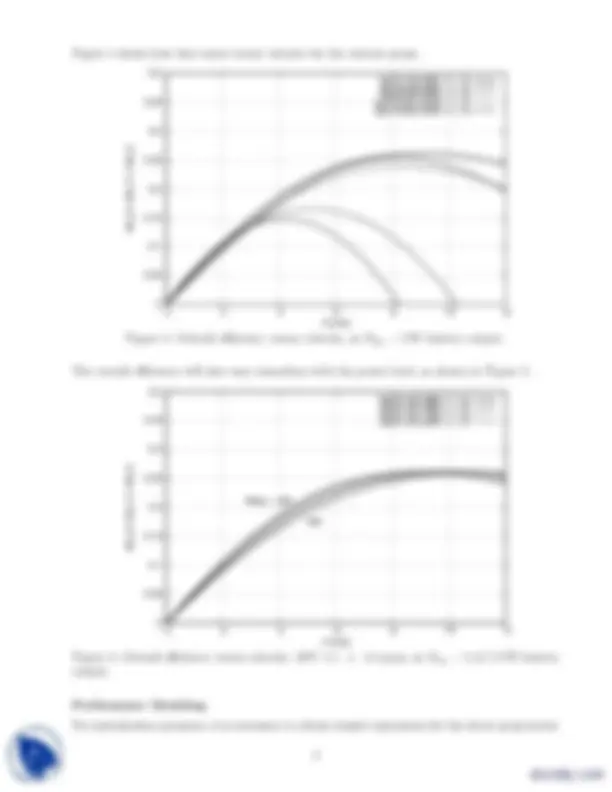

Study with the several resources on Docsity
Earn points by helping other students or get them with a premium plan
Prepare for your exams
Study with the several resources on Docsity
Earn points to download
Earn points by helping other students or get them with a premium plan
Community
Ask the community for help and clear up your study doubts
Discover the best universities in your country according to Docsity users
Free resources
Download our free guides on studying techniques, anxiety management strategies, and thesis advice from Docsity tutors
This is lab report and manual for Design Analysis and Aeronautical Engineering course lab. It was submitted to Dr. Aadhunik Joshi at Bidhan Chandra Krishi Viswa Vidyalaya. It includes: Propeller, Performance, Motor, Tests, Power, Levels, Thrust, Simulation, Model, Torque, RPM
Typology: Exercises
1 / 4
This page cannot be seen from the preview
Don't miss anything!
Propellers tested Tests were performed on a Speed-280 motor driving the following propellers:
APC 5.1 x 4. APC 5.5 x 4. APC 6.0 x 4. APC 7.0 x 4.0 (narrowed) APC 7.0 x 5.0 (narrowed)
The tests were performed over a range of air velocities and motor power levels, the latter controlled via motor voltage. Measurements consisted of thrust, torque, RPM, current, voltage. This allowed the calculation of all relevant operating parameters and efficiencies. Figure 1 shows typical thrust performance measurements for four applied voltages, together with predictions from the motor/prop simulation model.
0
1
0 5 10 15 20 25
T [N]
3 Volt
4 Volt
5 Volt
7 Volt
V [m/s] Figure 1: Measured thrust versus velocity (symbols), for APC 5.1x4.5 prop, Speed-280 motor. Lines are motor/prop numerical model predictions.
The intent here is to validate the numerical model, which is used to generate all the subsequent performance curves.
Maximum-Power Thrust Figure 2 shows the thrust of the propellers for the maximum available battery rest voltage of 7.4 Volts (the actual battery voltage is reduced somewhat by battery’s internal resistance). Figure 3 shows the corresponding maximum thrust power. Pmax ≡ TmaxV = ηm ηp ηb (Pelec)max
1
"apc51x45.74vb" u 1: "apc55x45.74vb" u 1: "apc60x40.74vb" u 1: "apc70x50n.74vb" u 1: "apc70x40n.74vb" u 1:
T [N]
0 0 5 10 15 20 25 V [m/s] Figure 2: Maximum thrust versus velocity, for 7.4 Volt, 0.30 Ohm battery.
0
1
2
3
4
5
6
7
8
9
0 5 10 15 20 25
TV [W]
"apc51x45.74vb" u 1: "apc55x45.74vb" u 1: "apc60x40.74vb" u 1: "apc70x50n.74vb" u 1: "apc70x40n.74vb" u 1:
V [m/s] Figure 3: Maximum thrust power versus velocity, for 7.4 Volt, 0.30 Ohm battery.
Cruise-Power Efficiency
For a given thrust or power, the propeller efficiency ηp varies substantially with velocity. The motor and battery efficiencies may vary as well. It is convenient to lump these into one overall efficiency. η = ηm ηp ηb
� �
performance curves. For the three best props in Figure 2, the maximum thrust is closely approximated by the simple linear curve-fit function
Tmax(V ) ≃ T 0 + T 1 V (1) T 0 = 0 .86 N (2) T 1 = − 0 .027 N/(m/s) (3)
If performance calculations are to be performed in terms of thrust power rather than thrust, the performance of the best props in Figure 3 is then approximated by the following curve fit.
Pmax(V ) ≃ Tmax V = (T 0 + T 1 V )V (4)
The overall efficiency in Figure 5 is closely approximated by the curve fit
η
η(V ) ≃ η 0 1 − (V /Vη 0 − 1)^2 (5) 0 =^0.^26 (6) Vη 0 = 9 .0 m/s (7)
This Vη 0 value gives the best fit to the Pelec = 6 W curve. It can be adjusted slightly if necessary.