
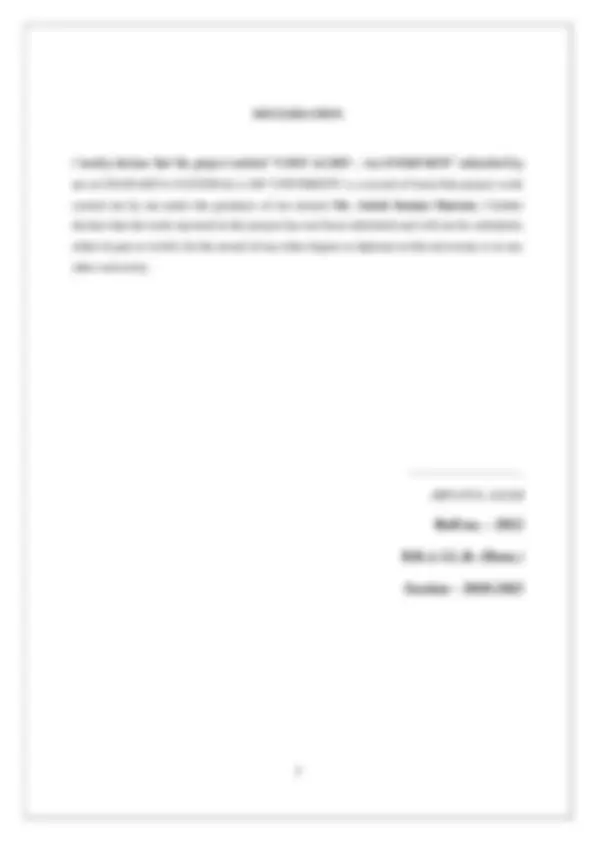
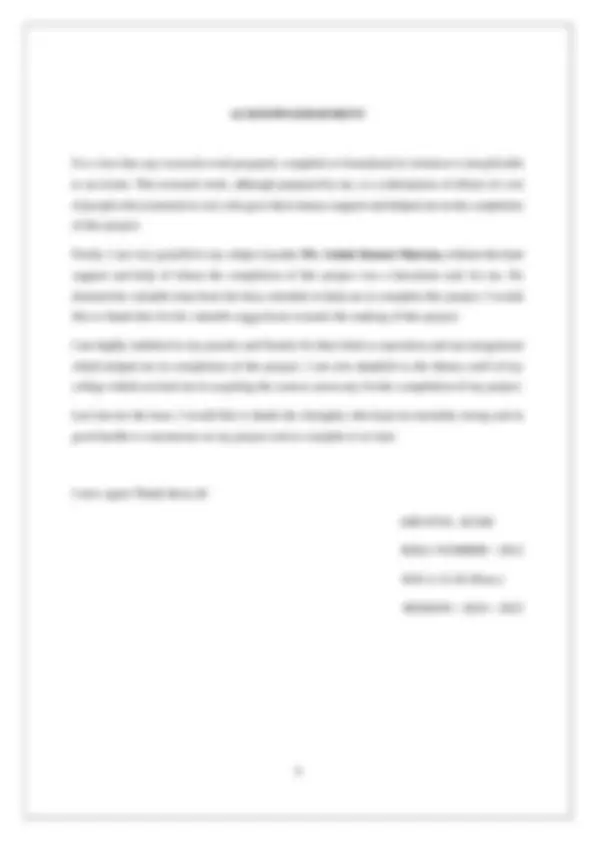
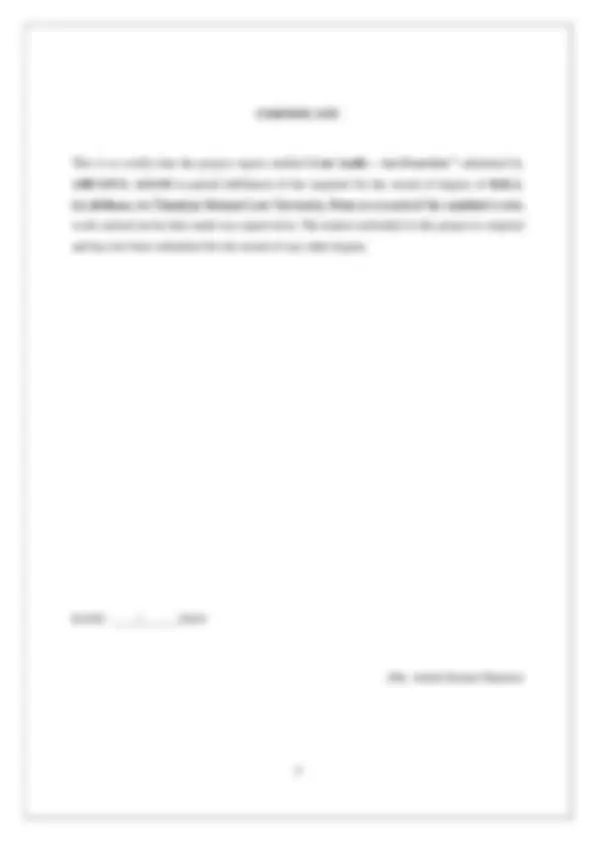
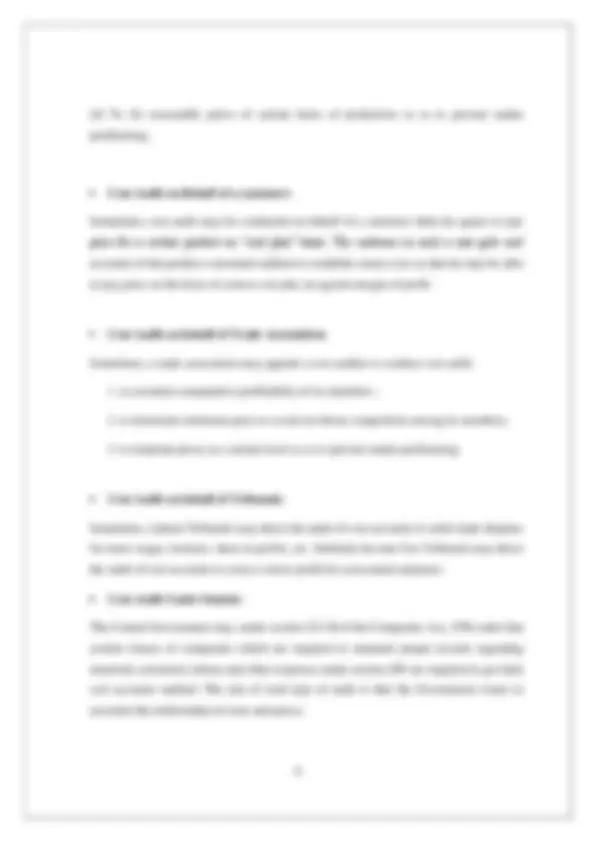
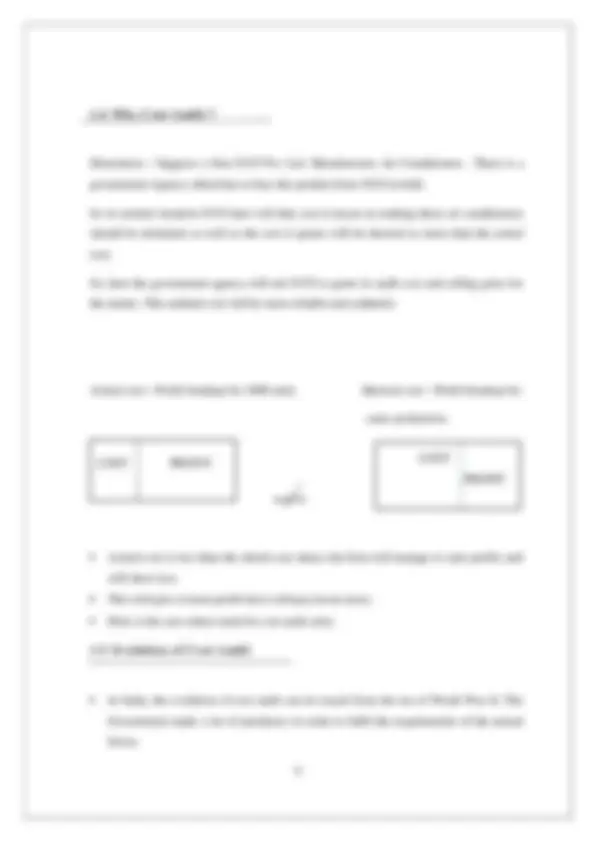
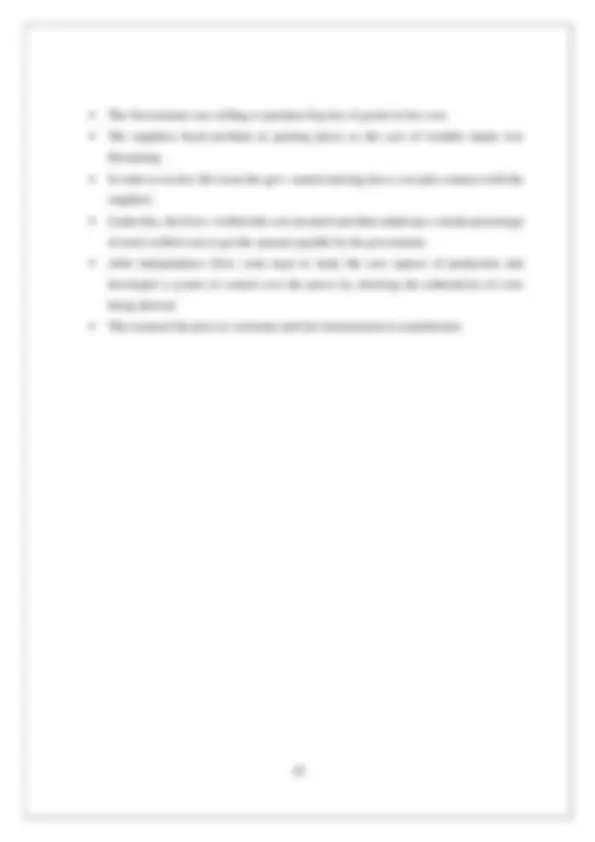
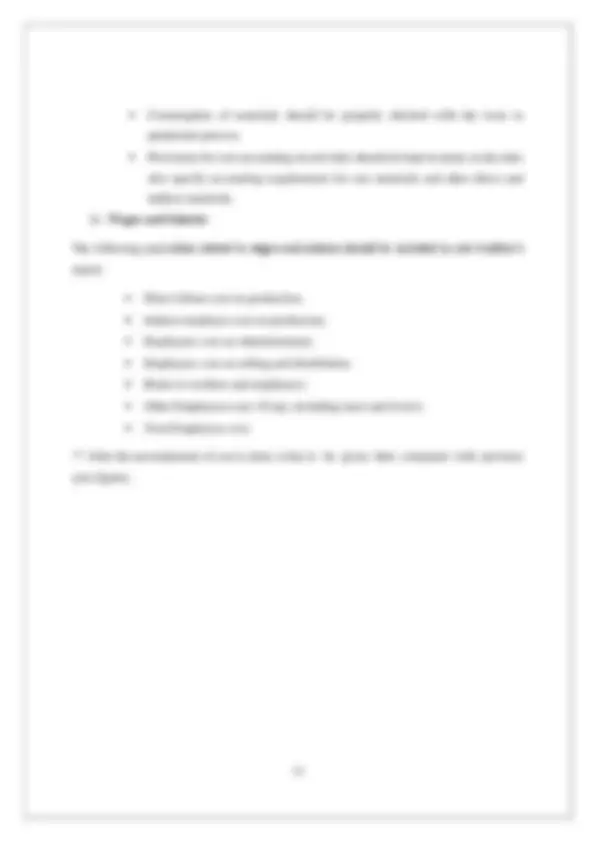
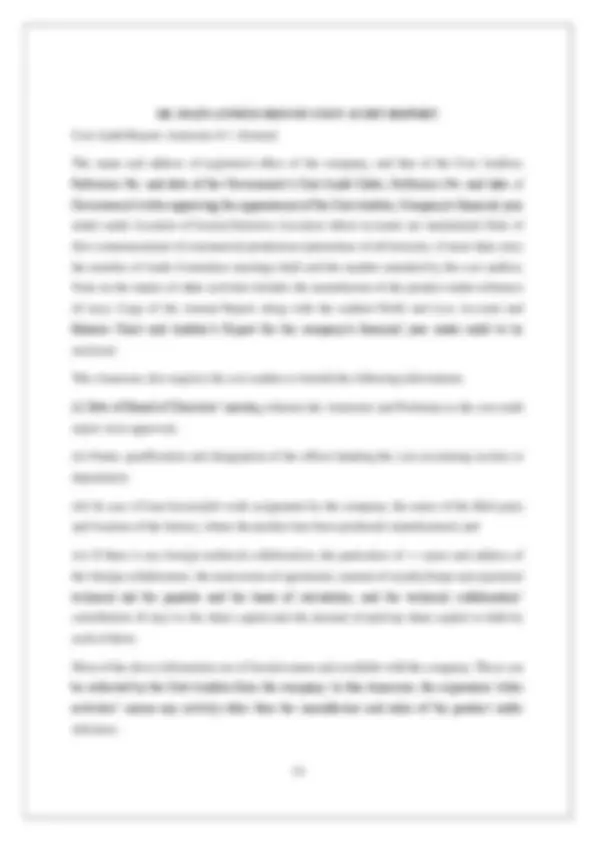
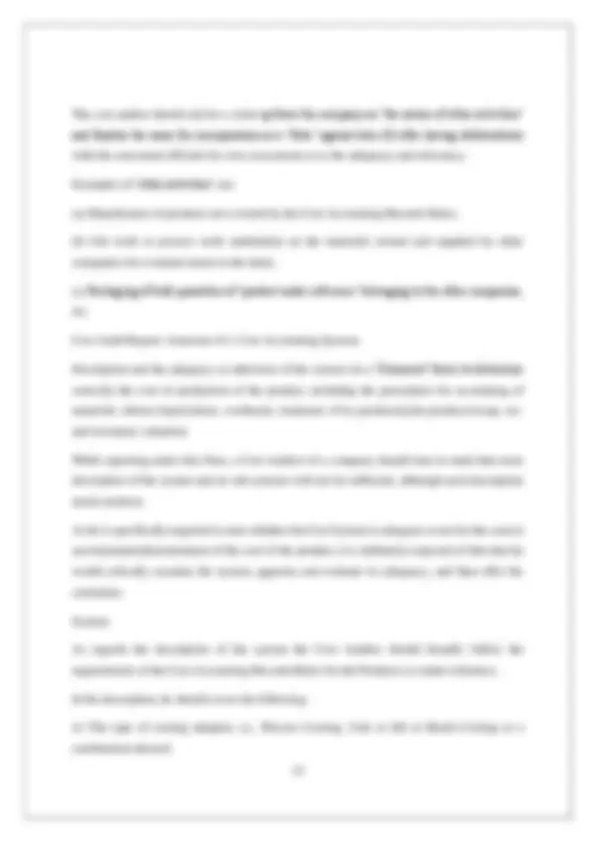
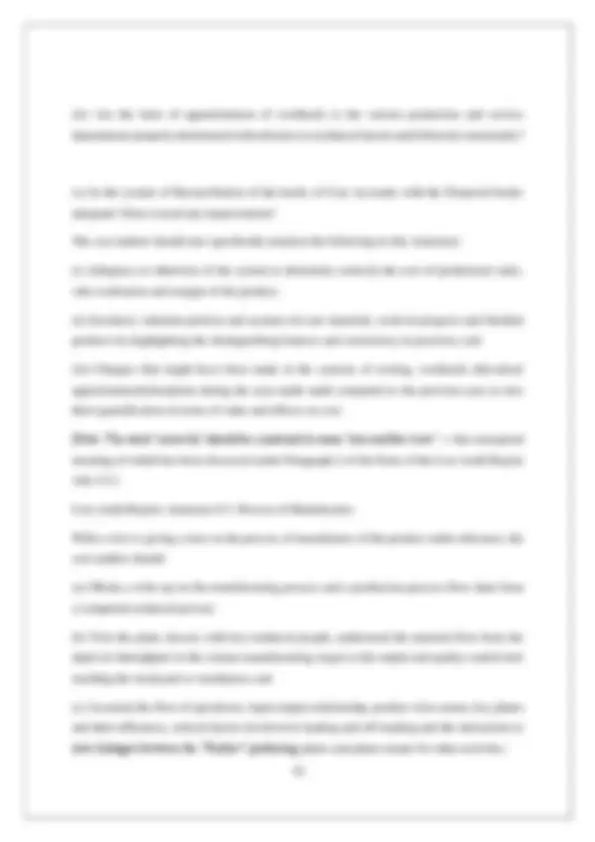
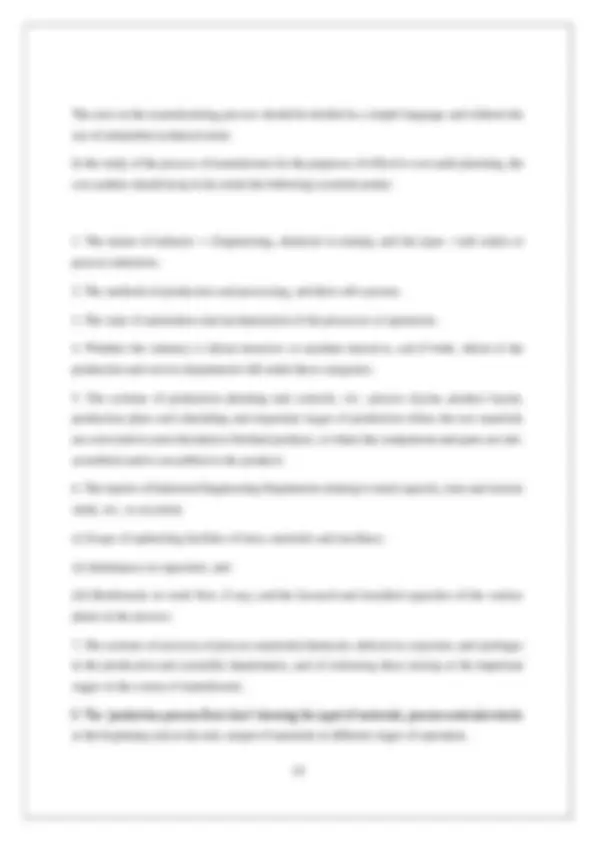
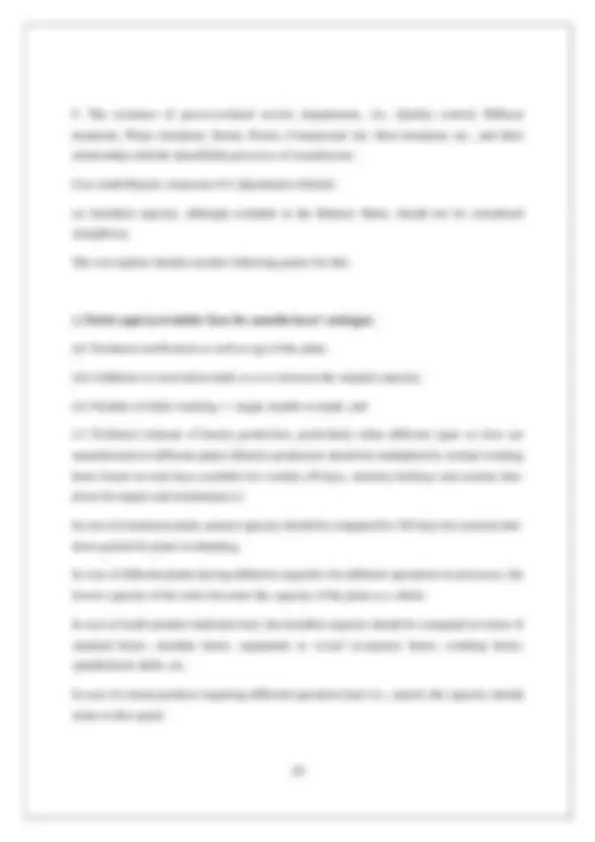
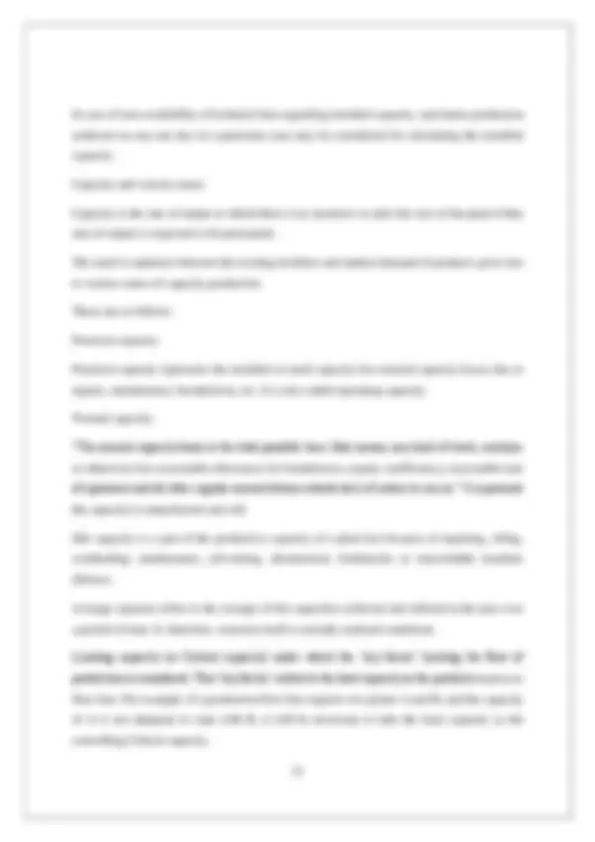
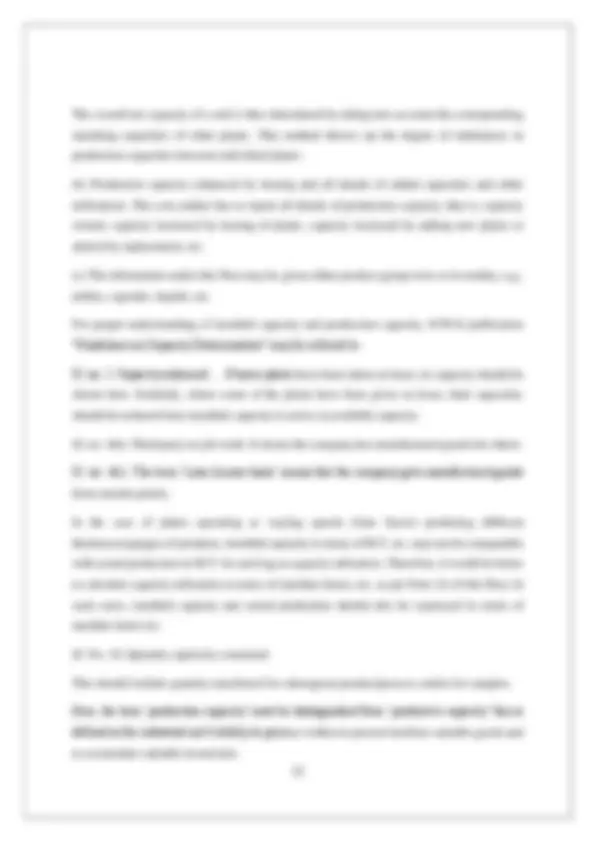
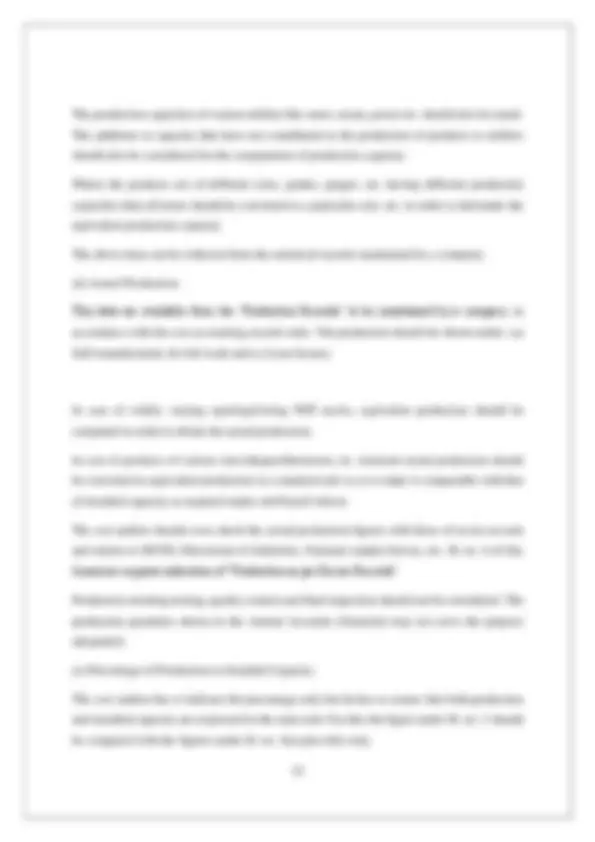
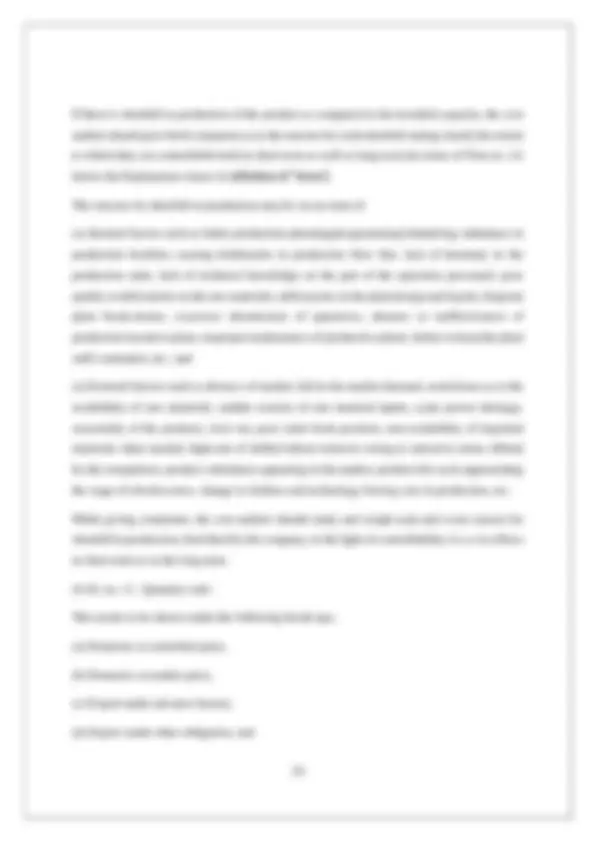
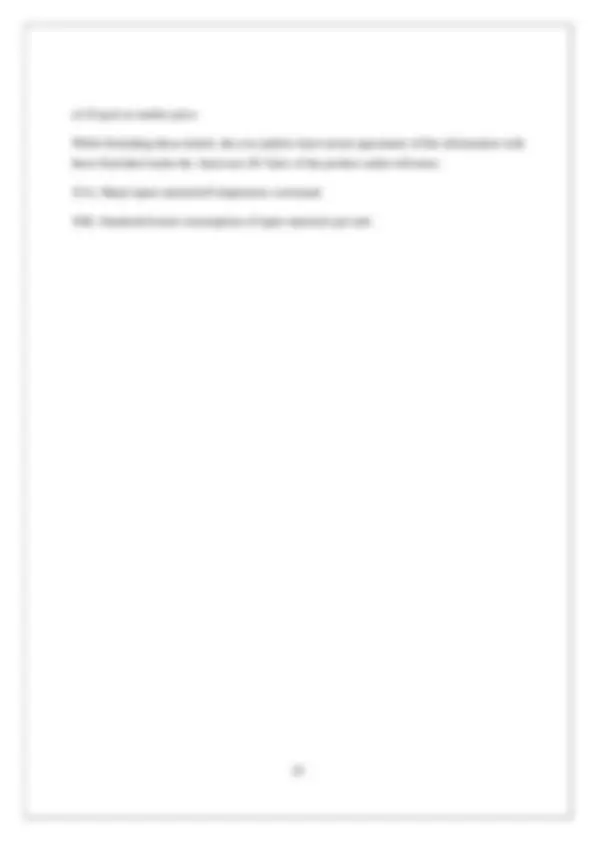


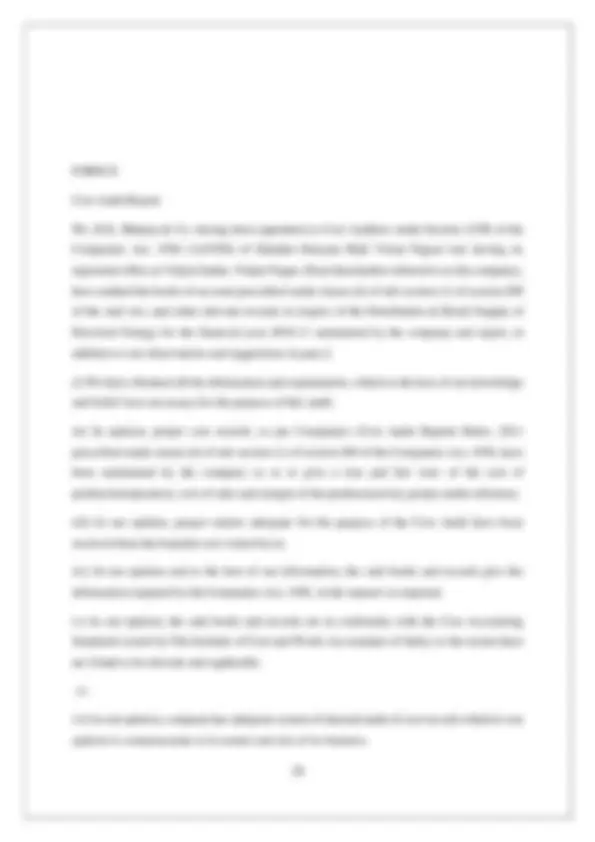
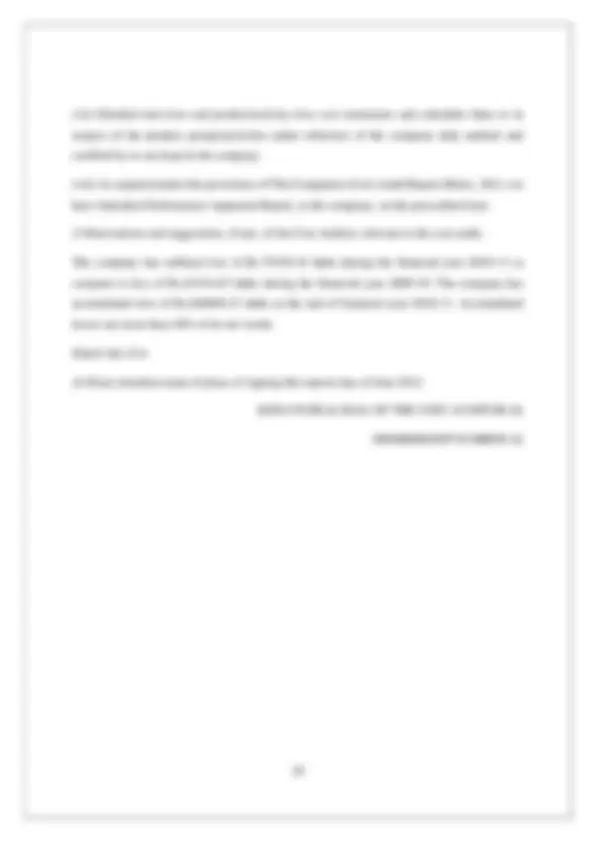
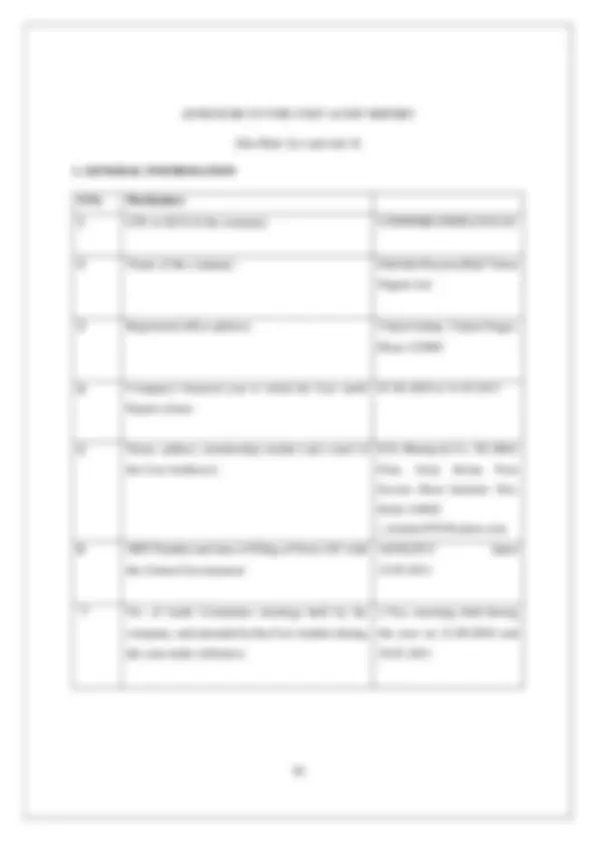
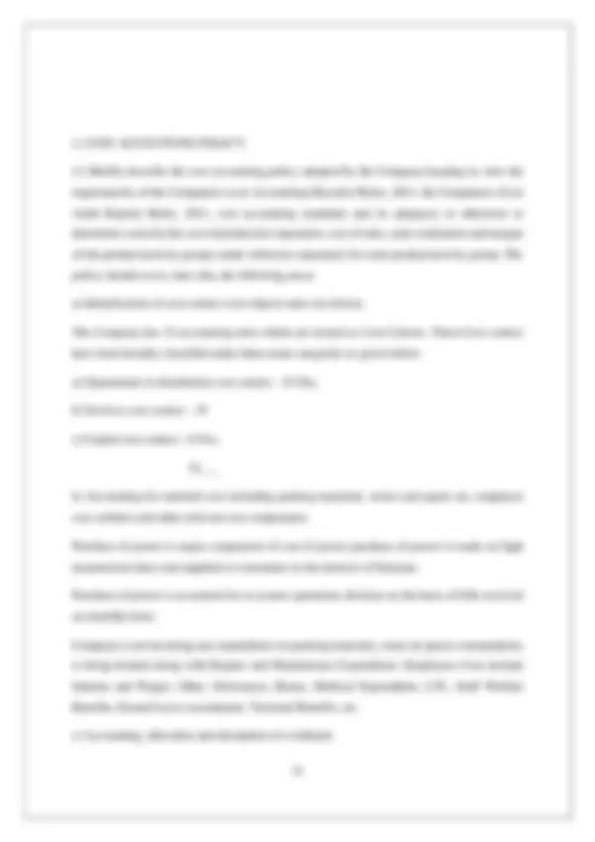
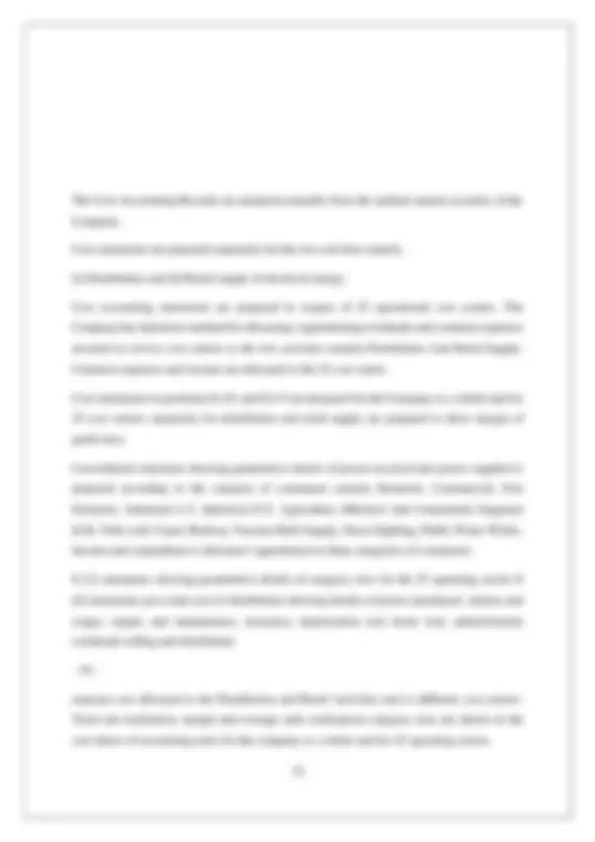
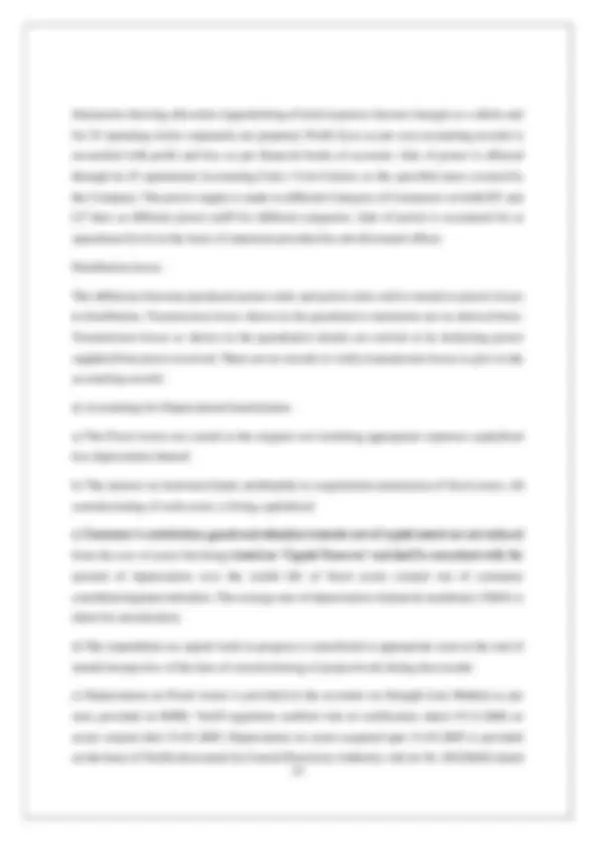
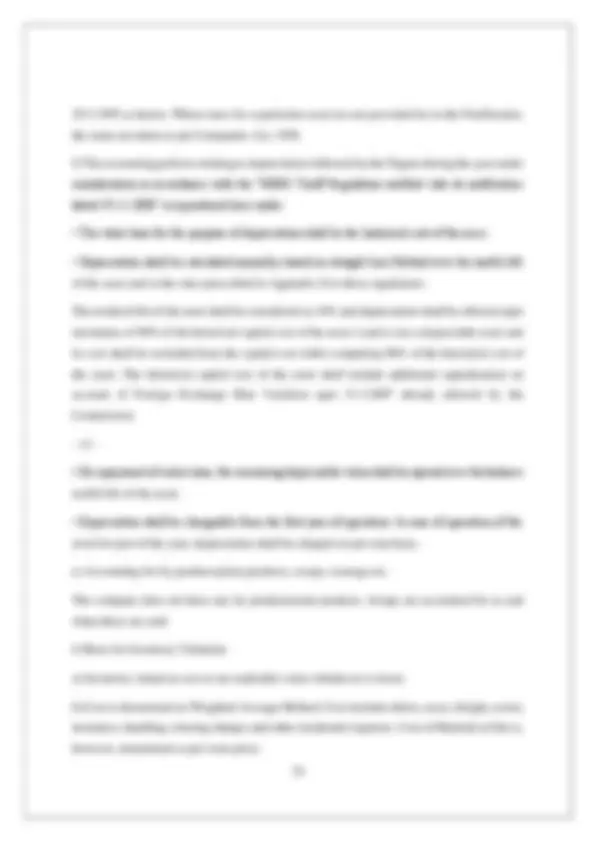
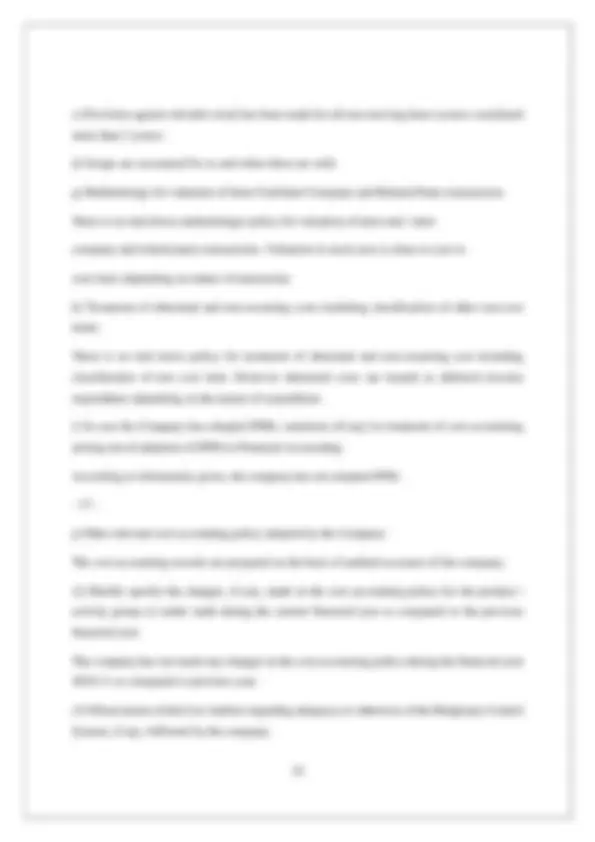
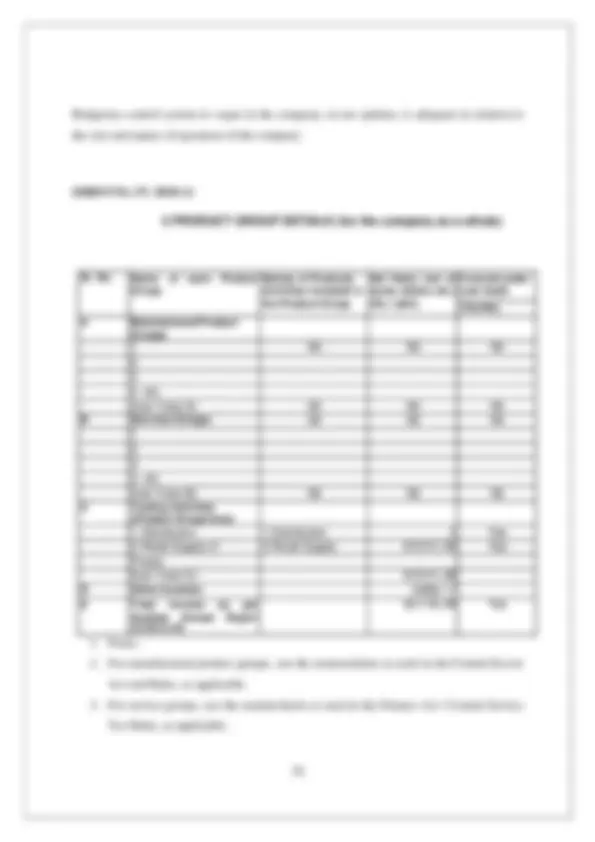
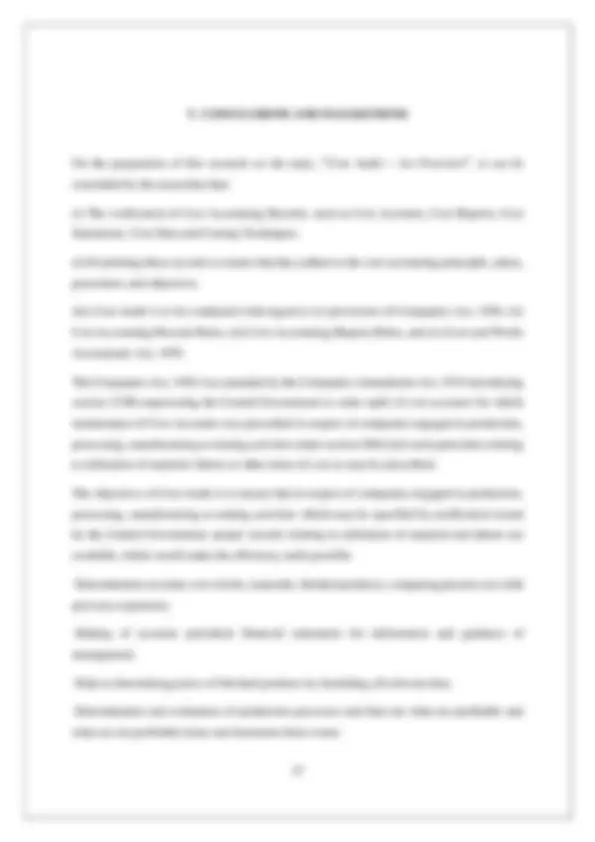
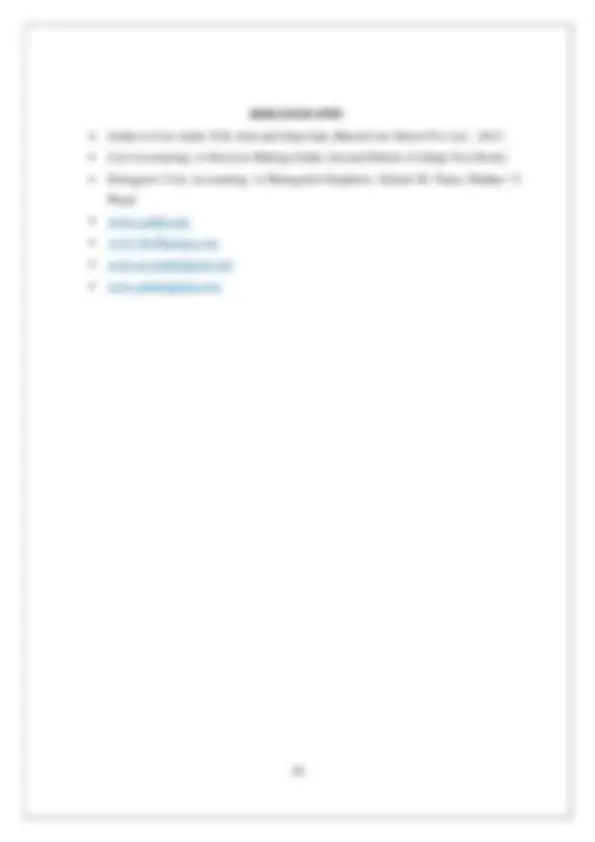
Study with the several resources on Docsity
Earn points by helping other students or get them with a premium plan
Prepare for your exams
Study with the several resources on Docsity
Earn points to download
Earn points by helping other students or get them with a premium plan
Community
Ask the community for help and clear up your study doubts
Discover the best universities in your country according to Docsity users
Free resources
Download our free guides on studying techniques, anxiety management strategies, and thesis advice from Docsity tutors
An overview of Cost Audit, the process of verifying cost accounting records in production organizations in India. It covers the importance of cost audits, the evolution of cost auditing, and the elements of cost auditing. The document also includes examples of industries and products subject to cost audits, as well as the performing of cost audits and the cost audit report of DHBVNL, Hisar.
Typology: Assignments
1 / 38
This page cannot be seen from the preview
Don't miss anything!
NYAYA NAGAR, MITHAPUR, PATNA – 800001. SUBMITTED TO; SUBMITTED BY; MR. ASHOK KUMAR SHARMA ARFATUL AZAM FACULTY OF ACCOUNTING B.B.A. LL.B (Hons.) ROLL NUMBER – 2012.
It is a fact that any research work prepared, compiled or formulated in isolation is inexplicable to an extent. This research work, although prepared by me, is a culmination of efforts of a lot of people who remained in veil, who gave their intense support and helped me in the completion of this project. Firstly, I am very grateful to my subject teacher Mr. Ashok Kumar Sharma, without the kind support and help of whom the completion of this project was a herculean task for me. He donated his valuable time from his busy schedule to help me to complete this project. I would like to thank him for his valuable suggestions towards the making of this project. I am highly indebted to my parents and friends for their kind co-operation and encouragement which helped me in completion of this project. I am also thankful to the library staff of my college which assisted me in acquiring the sources necessary for the compilation of my project. Last but not the least, I would like to thank the Almighty who kept me mentally strong and in good health to concentrate on my project and to complete it in time. I once again Thank them all. ARFATUL AZAM ROLL NUMBER – 2012 B.B.A. LL.B (Hons.) SESSION – 2018 – 2023
This is to certify that the project report entitled Cost Audit – An Overview ” submitted by ARFATUL AZAM in partial fulfilment of the required for the award of degree of B.B.A. LL.B(Hons.) to Chanakya National Law University, Patna is a record of the candidate’s own work carried out by him under my supervision. The matter embodied in this project is original and has not been submitted for the award of any other degree. DATE - ____/______/2019. (Mr. Ashok Kumar Sharma)
The researcher would be relying on doctrinal form of research which would include different works of writers in this matter and different articles. The researcher would also be justifying his research through a cost audit report of a company. 1.3 TYPES OF COST AUDIT Following are the main types of Cost Audit:
(d) To fix reasonable prices of certain items of production so as to prevent undue profiteering.
Statutory Provisions included in: 209 (1) (d) of Companies Act (Amended) 1965, sec. deals with provisions related to cost records. Sec. 233B (Amended in 1988) deals with the specific cases where cost audit is applicable. Maintenance of books of accounts under sec. 209 (1):- As per the provisions of this section, every company is required to maintain the following: a) All receipts and disbursements of money and matters in respect of which the receipts and disbursements take place. b) All sales and purchases of goods of the company. c) The assets and liabilities of the company. Section 209 (1) (d) :- It provides that in case the company is engaged in any of the following activity i.e. a) Mining b) Production c) Processing d) Manufacturing Then the company will have to prepare a detail of labour and material cost being involved as well as the other elements of cost being involved. As according to the section 209 (1) (d) the government has prescribed rules as regards maintenance of cost accounts separately, for the following industries.. ( 33 Industries).
Cost Audit Report: Annexure # 1. General: The name and address of registered office of the company, and that of the Cost Auditor; Reference No. and date of the Government’s Cost Audit Order; Reference No. and date of Government’s letter approving the appointment of the Cost Auditor; Company’s financial year under audit; Location of factory/factories; Location where accounts are maintained; Date of first commencement of commercial production (particulars of all factories, if more than one); the number of Audit Committee meetings held and the number attended by the cost auditor; Note on the nature of other activities besides the manufacture of the product under reference (if any); Copy of the Annual Report along with the audited Profit and Loss Account and Balance Sheet and Auditor’s Report for the company’s financial year under audit to be enclosed. This Annexure also requires the cost auditor to furnish the following information: (i) Date of Board of Directors’ meeting wherein the Annexure and Proforma to the cost audit report were approved; (ii) Name, qualification and designation of the officer heading the cost accounting section or department; (iii) In case of loan license/job work assignment by the company, the name of the third party and location of the factory, where the product has been produced/ manufactured; and (iv) If there is any foreign technical collaboration, the particulars of — name and address of the foreign collaborators, the main terms of agreement, amount of royalty/lump-sum payment/ technical aid fee payable and the basis of calculation, and the technical collaborators’ contribution (if any) to the share capital and the amount of paid-up share capital so held by each of them. Most of the above information are of factual nature and available with the company. These can be collected by the Cost Auditor from the company. In this Annexure, the expression ‘other activities’ means any activity other than the manufacture and sales of the product under reference.
(ii) Raw Materials; (iii) Process Materials; (iv) Consumable stores, tools, machinery spares, etc.; (v) Salaries and wages, including basis of differentiation of Direct and Indirect Labour; (vi) Depreciation; (vii) Overheads including classification procedure; (viii) Departmentalisation — Production and Service department expenses; system of apportionment, reapportionment of services’ expenses to production; (ix) Method of recovery of costs to the products; (x) Valuation of work-in-progress inventories; (xi) Valuation of items captivity consumed; (xii) System of preparation of different Cost Statements as required under the relevant Cost Accounting Record Rules; (xiii) System followed for the reconciliation of Cost Accounts Records with the Financial Books of Account; (xiv) The determination of value of joint-products, by-products, own manufactured components; (xv) System of Standard costing, if any, in operation and a reference as to whether the cost accounting is done on a historical basis. In this Para, the Cost Auditor need not describe the accounting procedures that the company follows in respect of ‘Materials’ and ‘Stores and Spare Parts’, but should give a reference to the other paras of the Annexure where these have been discussed. Adequacy or Otherwise of the System: The Cost Auditor should critically analyse and evaluate the following so as to draw conclusions for offering his comments:
(i) Whether the type of costing adopted by the company is appropriate to the industry; (ii) Whether the standards — physical and monetary — fixed by company are reasonable; how have these standards been set? What are the criteria taken into consideration? Whether the standards are realistic and workable under the present operating conditions, if a standard costing system is in existence, of course; (iii) Whether the distinction made between direct and indirect labour is reasonable to meet the requirements of the costing system; (iv) Whether the allocation of salaries and wages is appropriately made. What could be the possible limitations in the system? (v) Whether the classification and codification of materials facilitate easy identification. Are these adequate? (vi) Whether the system is reasonably flexible for collection of significant data on wastages, spoilages, defectives, rejections, etc. Whether it provides for generation of data on non-moving, slow-moving and obsolete items. How are the fast-moving items and sundry materials treated? (vii) How is the system of overheads classification? Is the classification procedure understood and applied consistently? Is there any Standard Chart of Accounts? Is it rational under the present set-up? Is the system of Standing Order Numbers adequate and appropriate? How is the inter-relationship between the Profit and Loss Account and the Cost Accounts (since the relevant Cost Accounting Rules state that details of all such overhead expenses are to be collected from the Financial Accounts)? (viii) How are the different overhead rates (i.e., Machine hour rate, Labour hour rate, Prime cost percentage rate, Direct wages rate, etc.) determined? Are the numerator and denominator — contents to find out the rates proper and being applied consistently? What is the length of the period considered for computation of rate? Does the system provide for computation of pre-determined rates? If so, how are the under- and over- absorption of overheads treated for adjustments in Cost Accounts? Are the absorption rates periodically studied by the management? Does the management enquire into the fluctuations thrown up by the adoption of predetermined rates?
The note on the manufacturing process should be drafted in a simple language and without the use of unfamiliar technical terms. In the study of the process of manufacture for the purposes of effective cost audit planning, the cost auditor should keep in his mind the following essential points: