
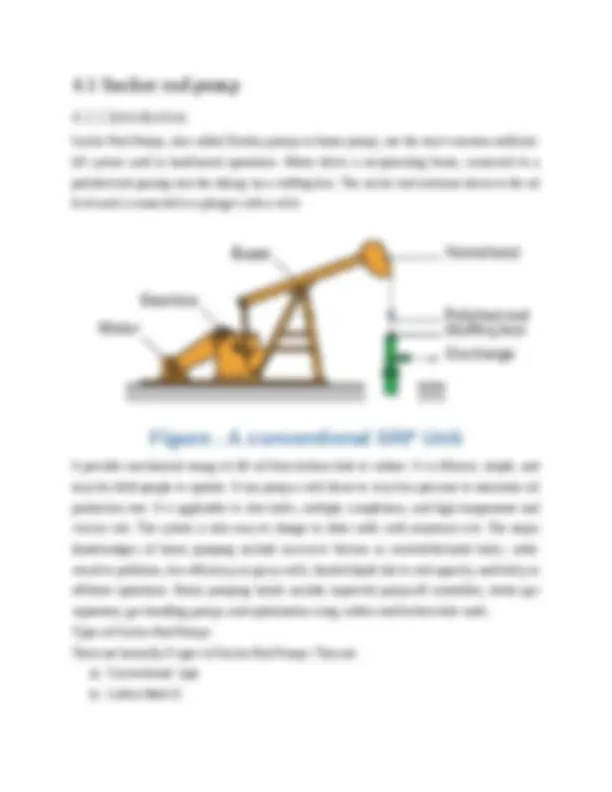
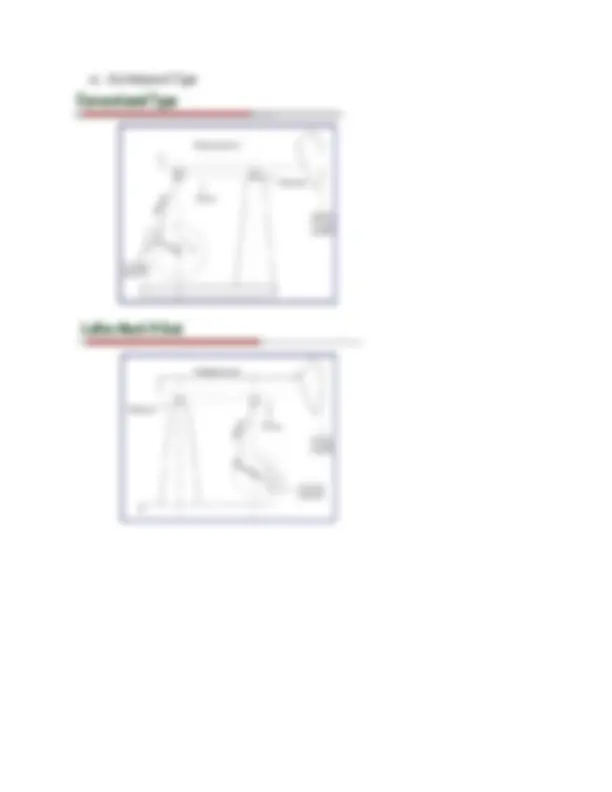
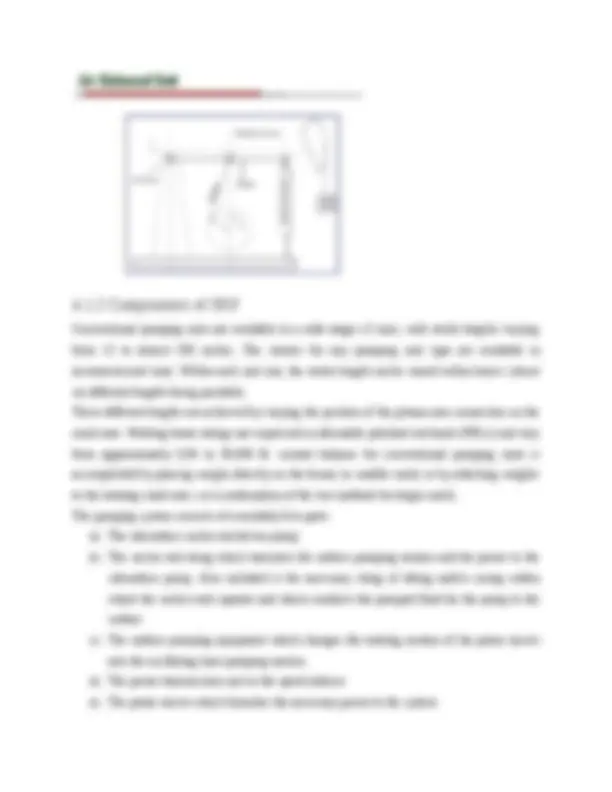
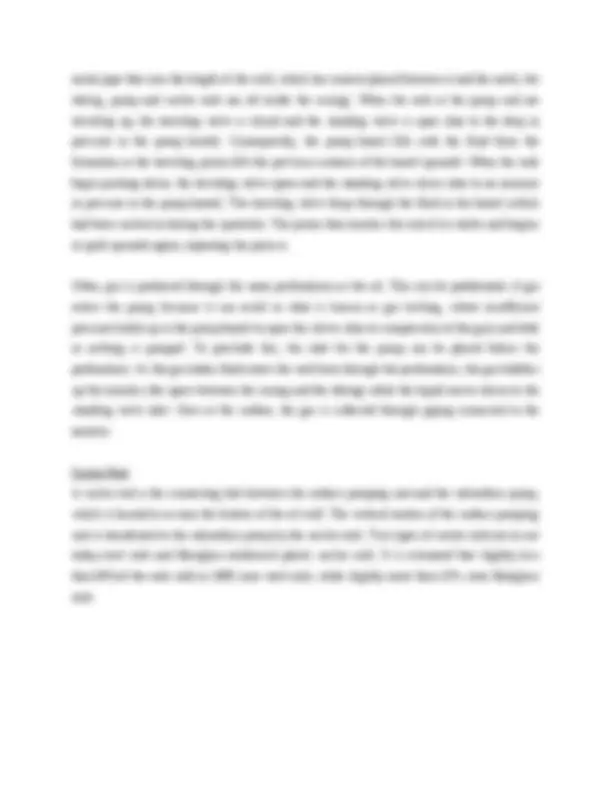
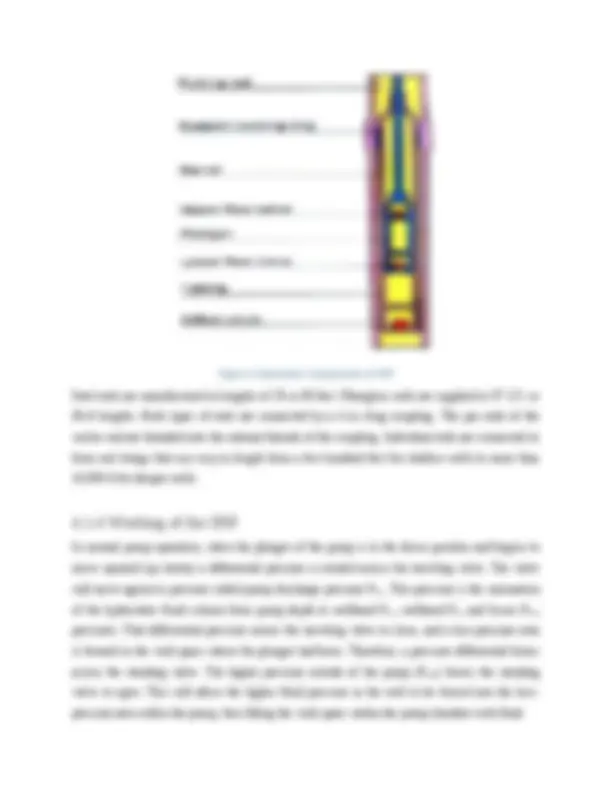
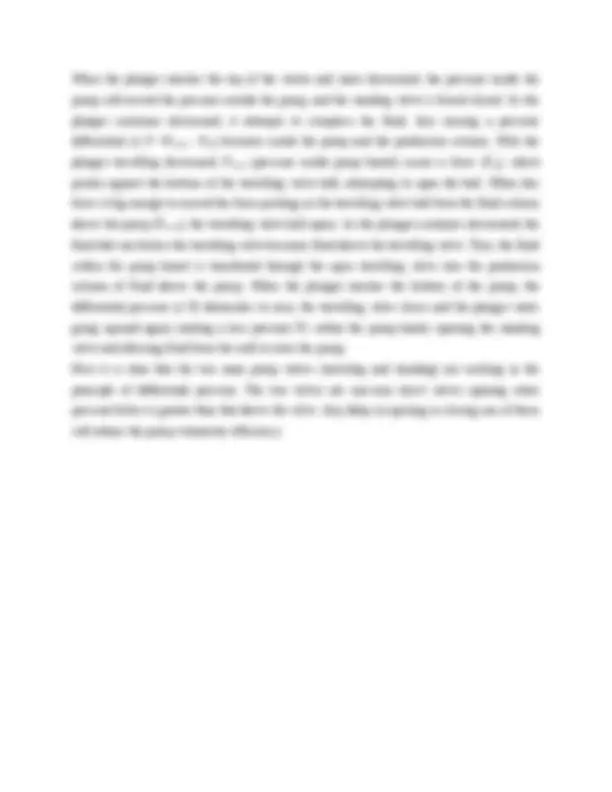
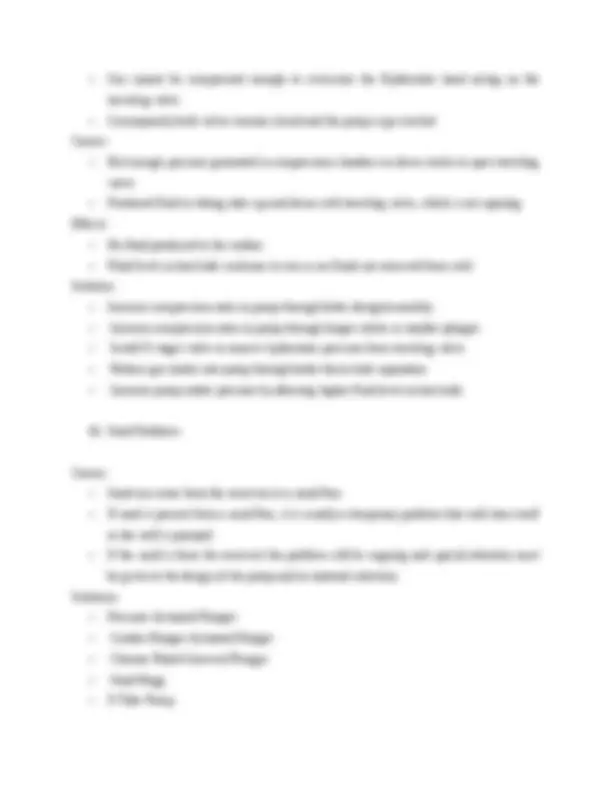
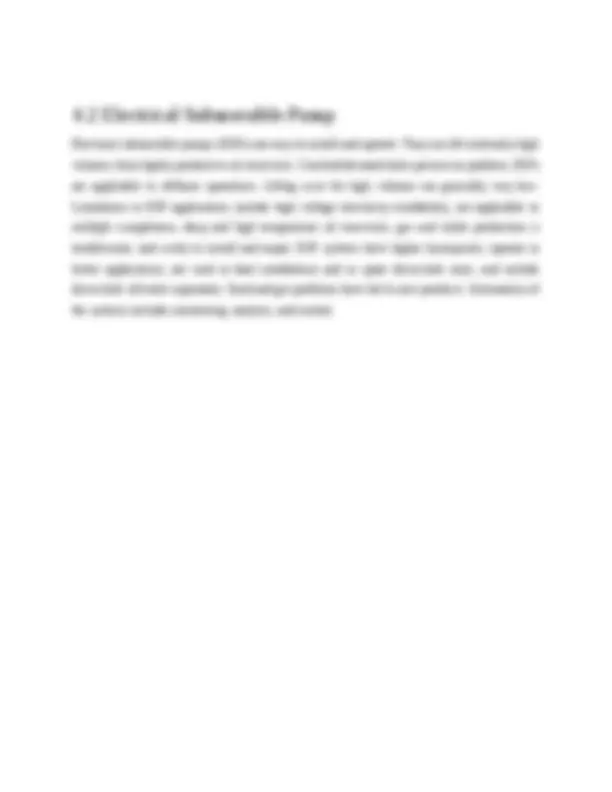
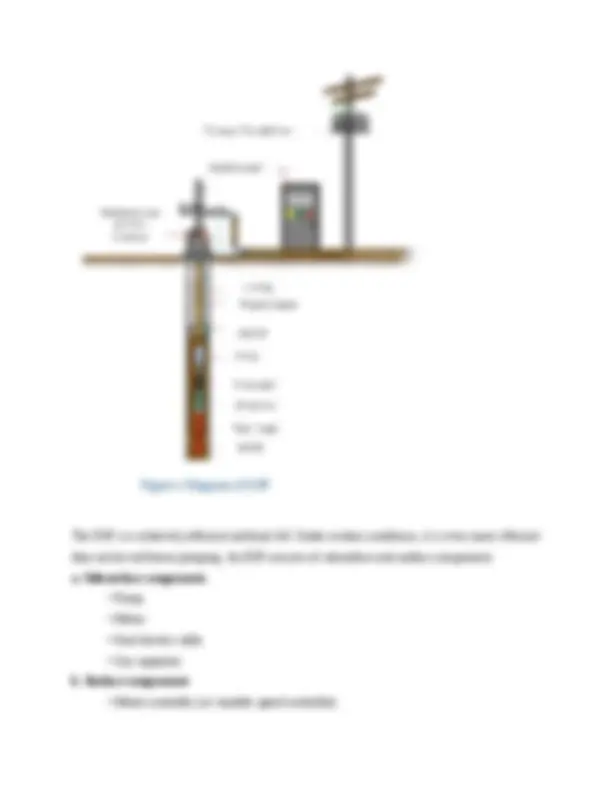
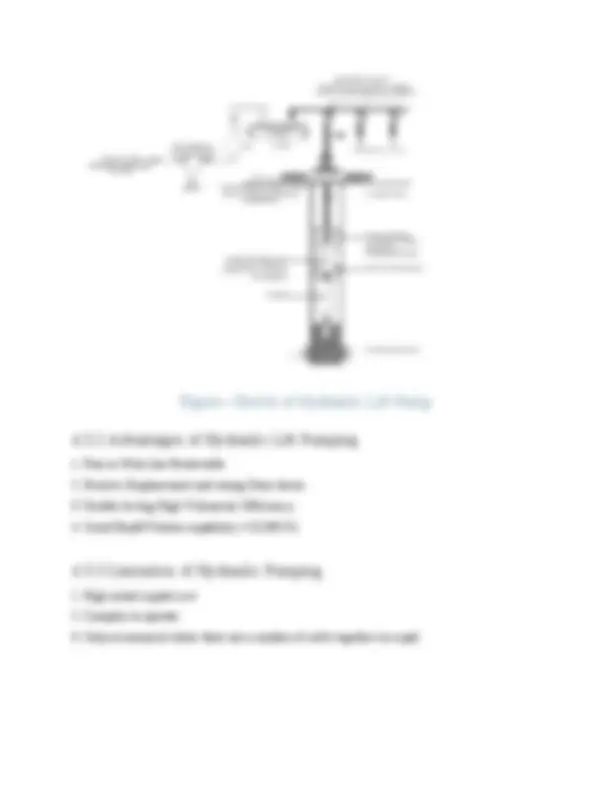
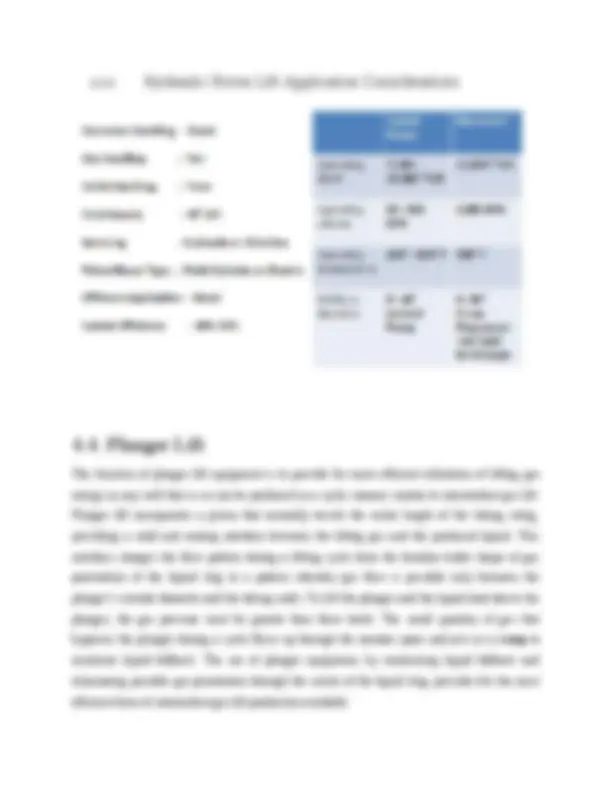
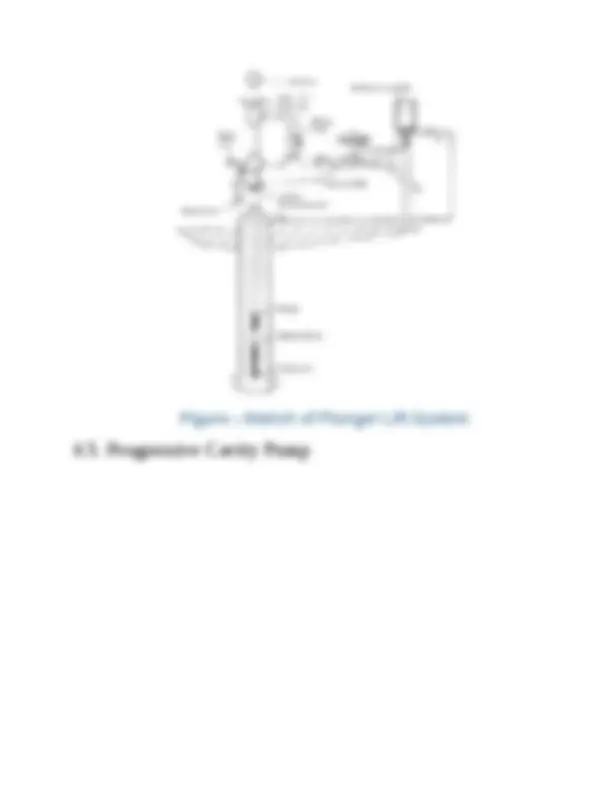
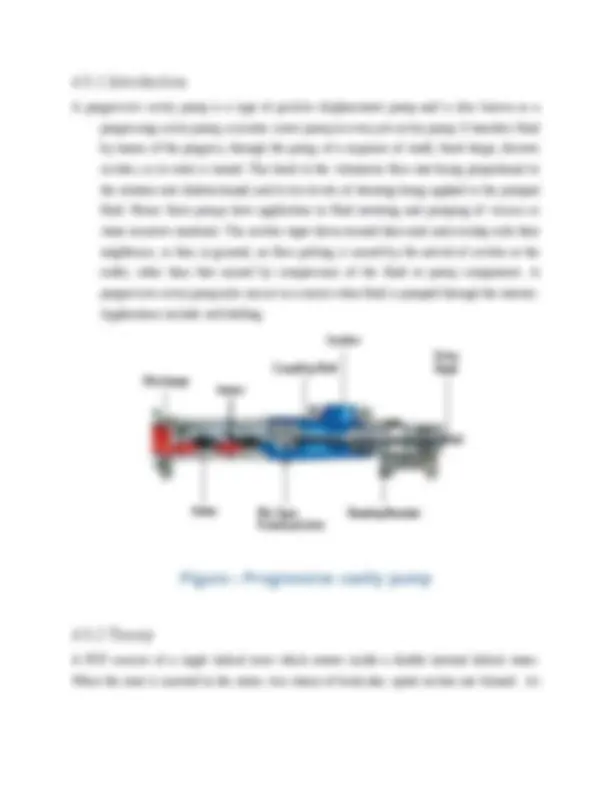
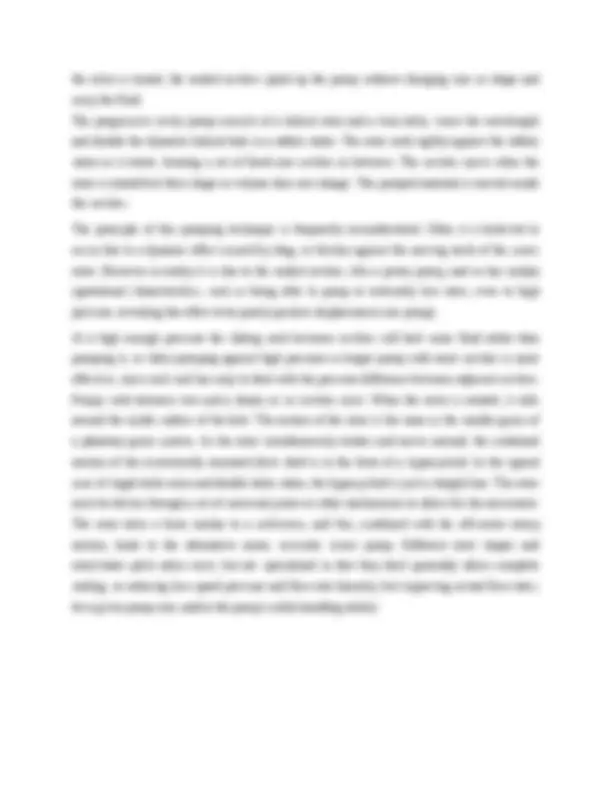
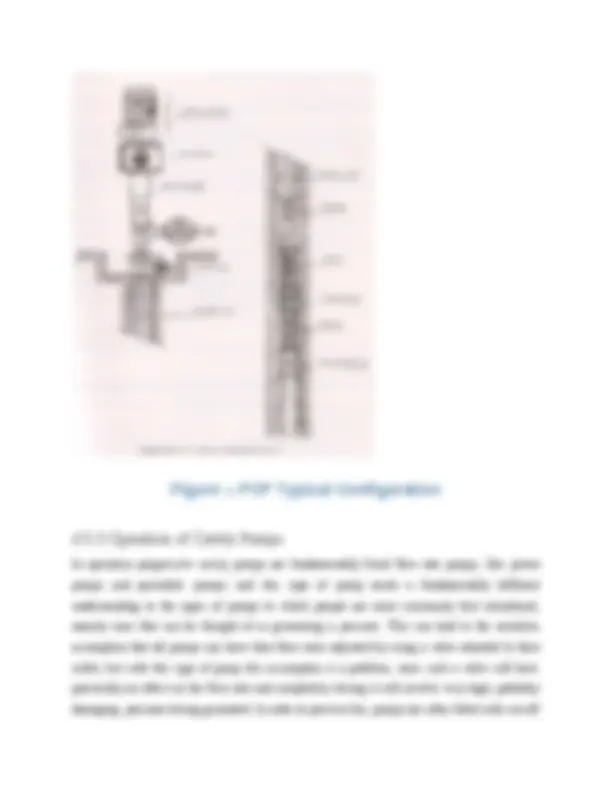
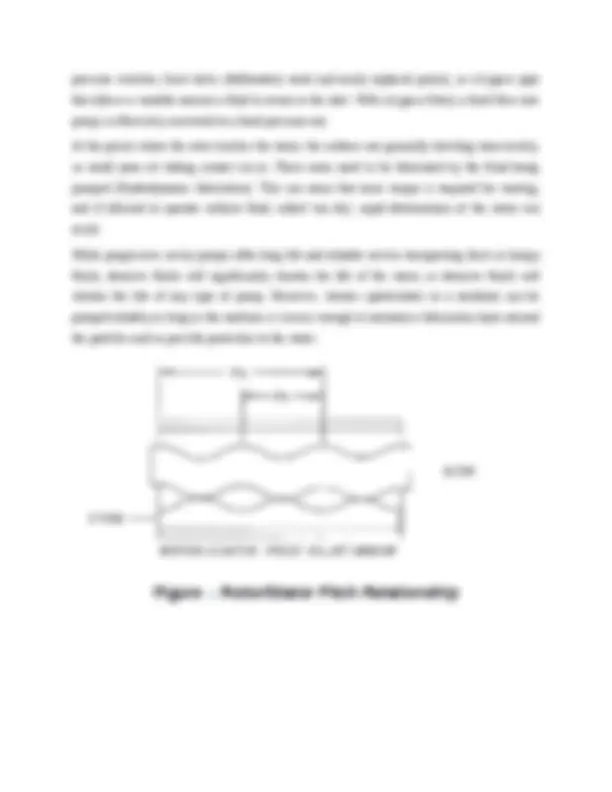
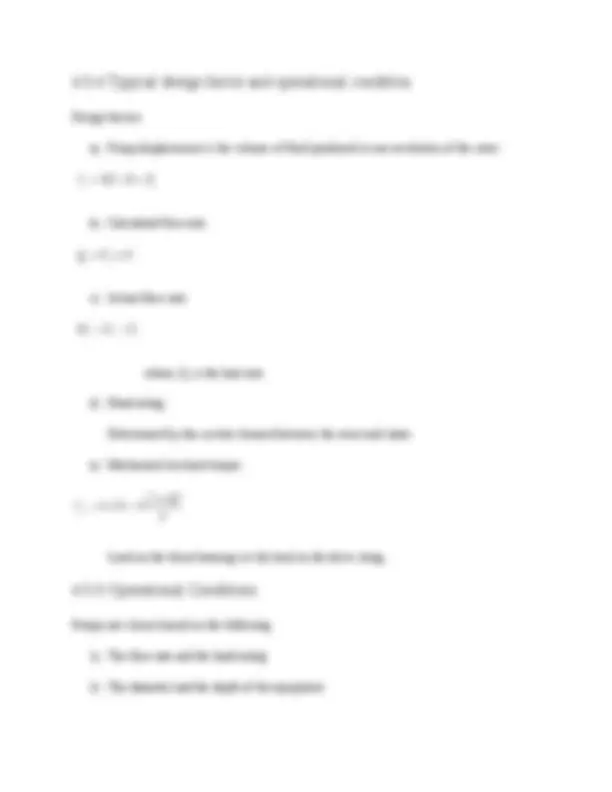
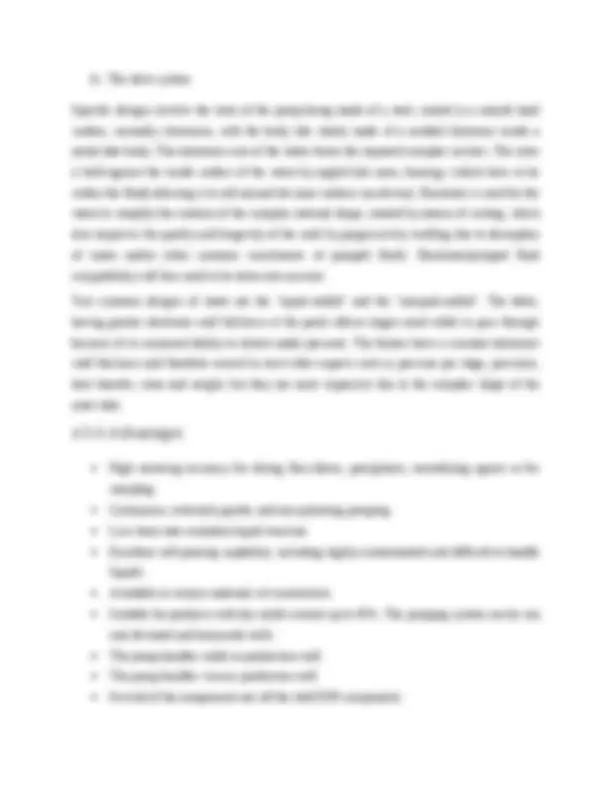
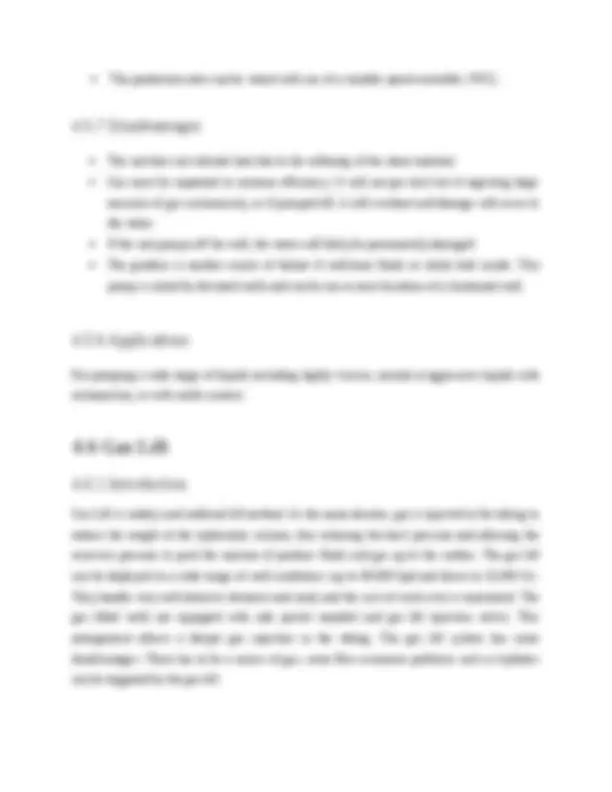
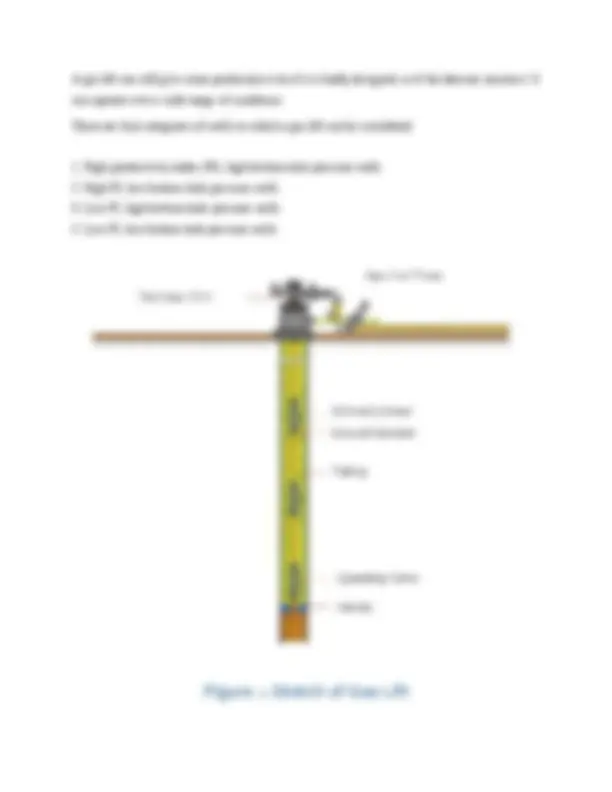
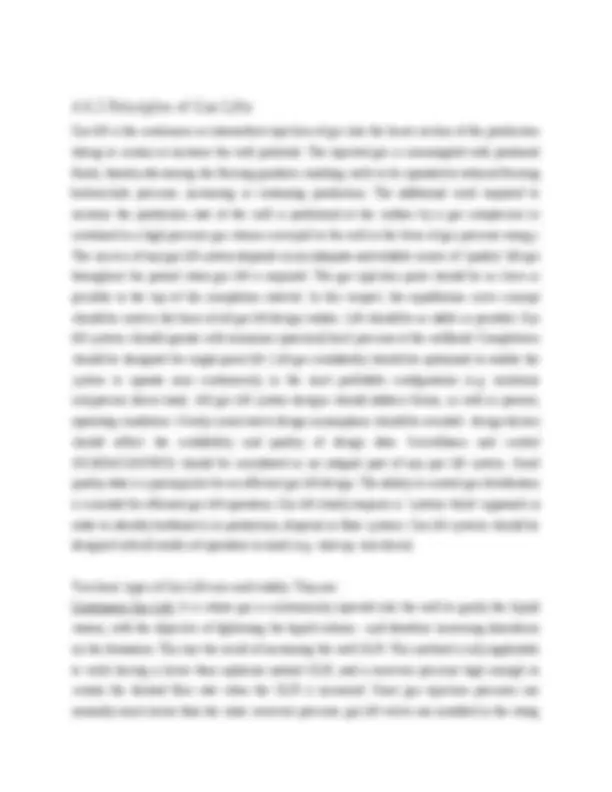
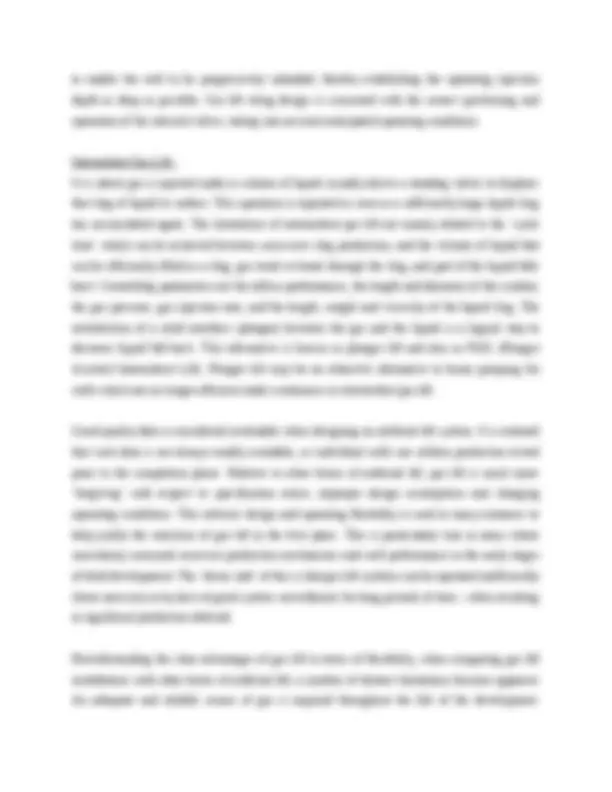
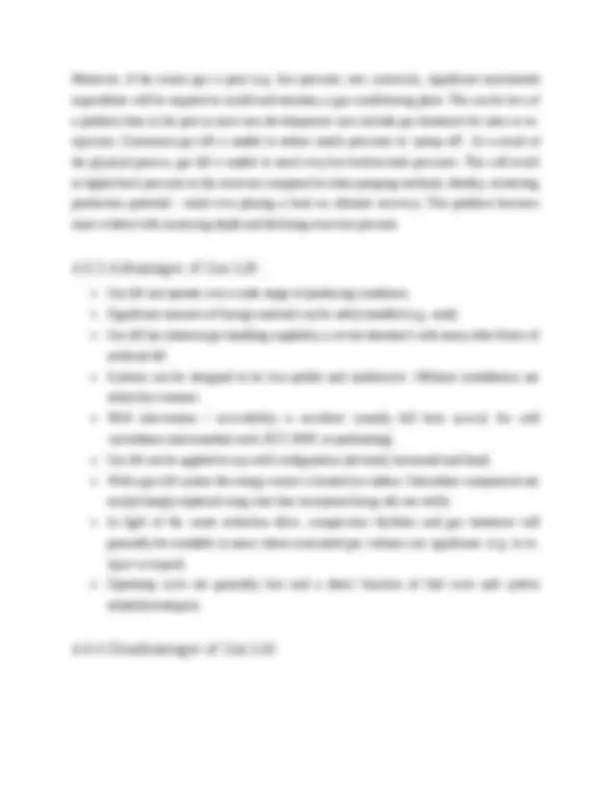
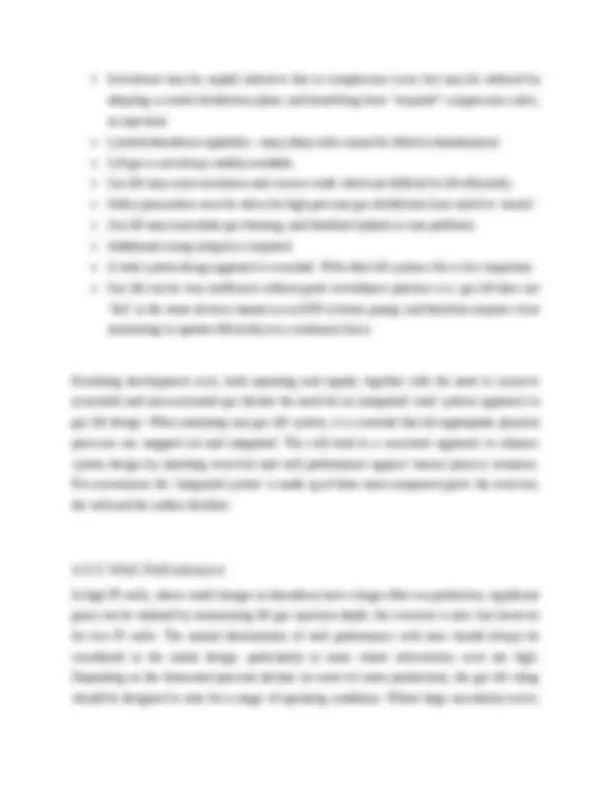
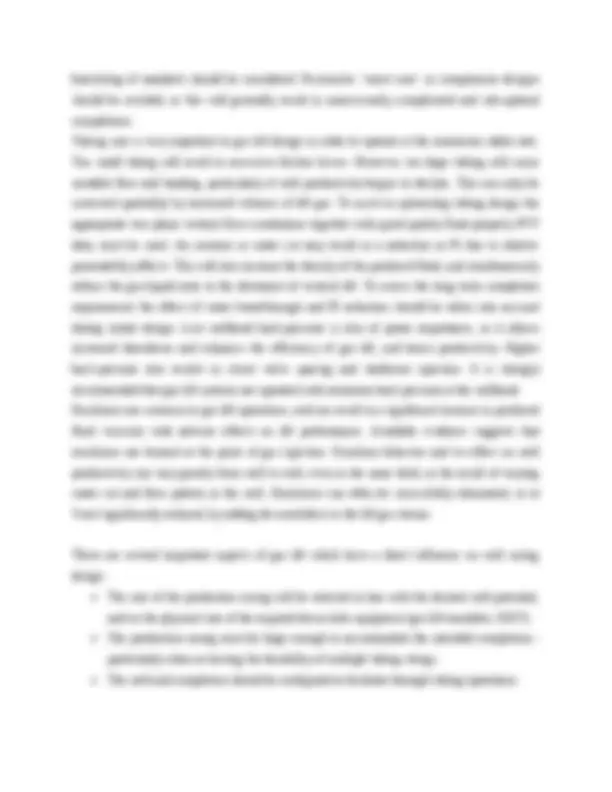
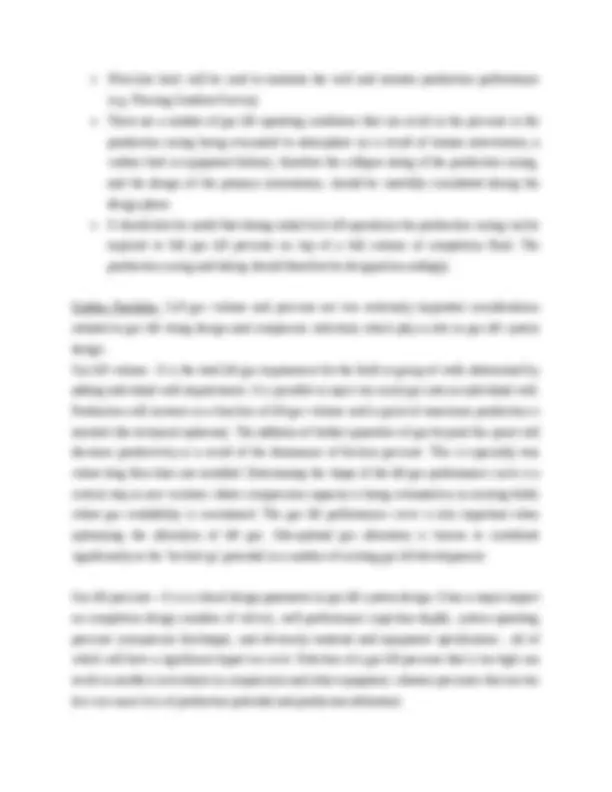
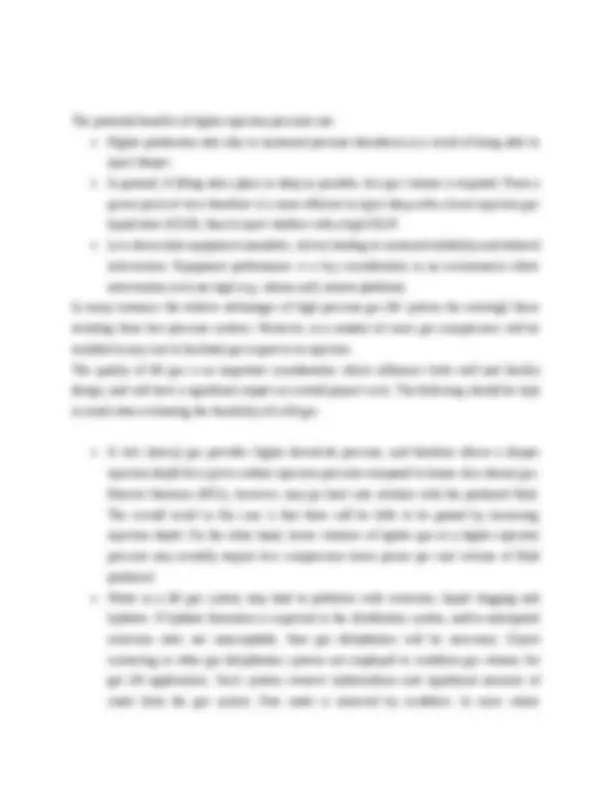
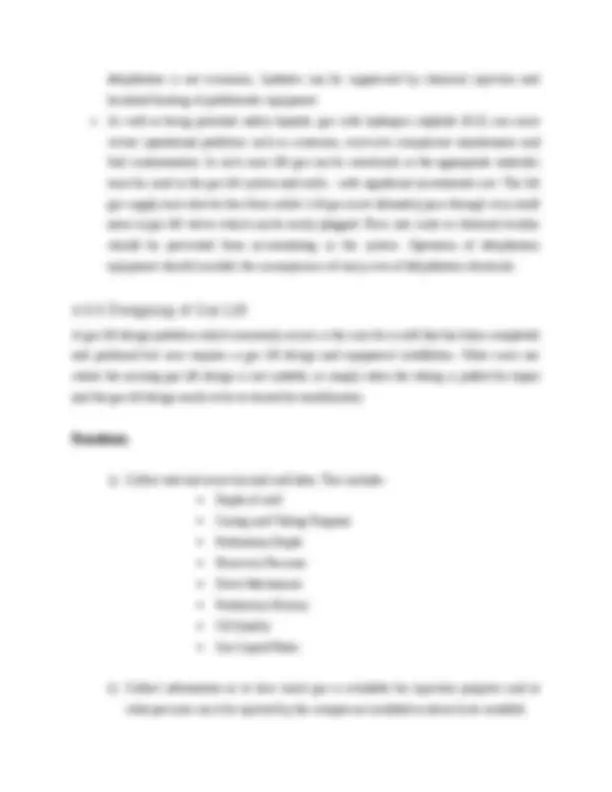
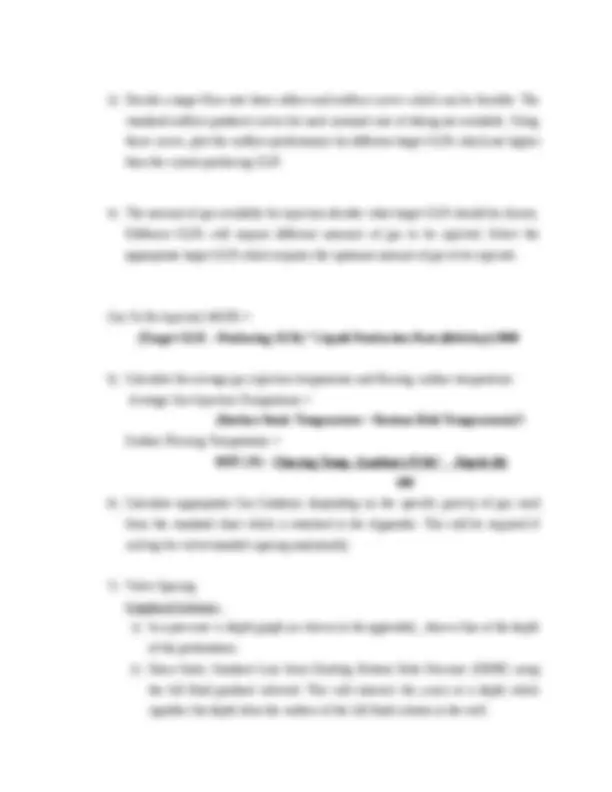
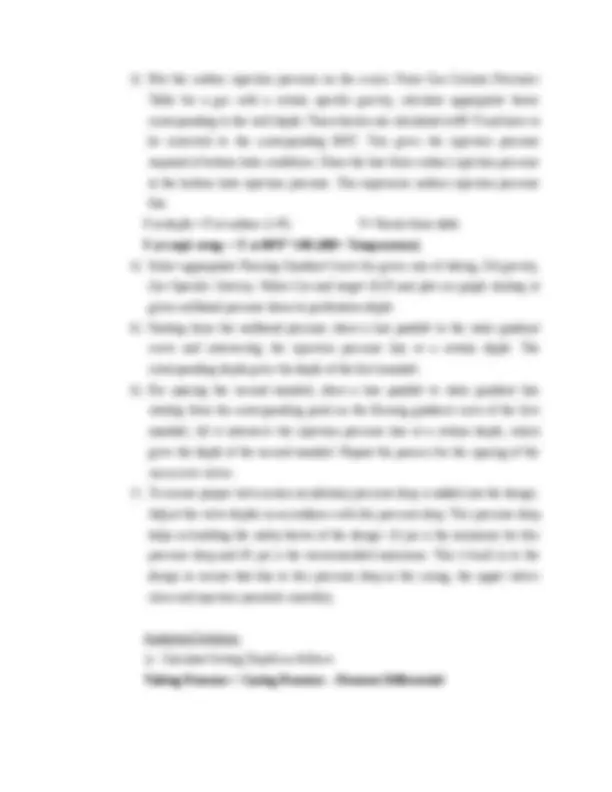
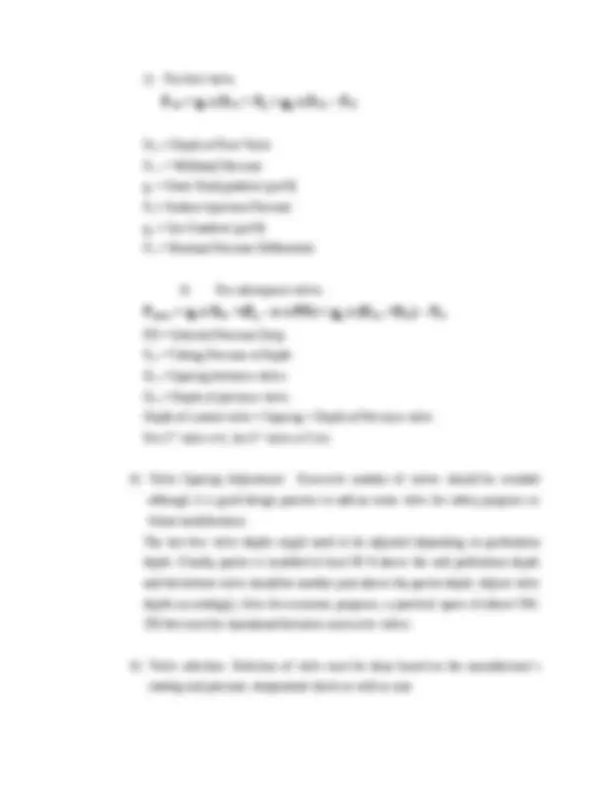
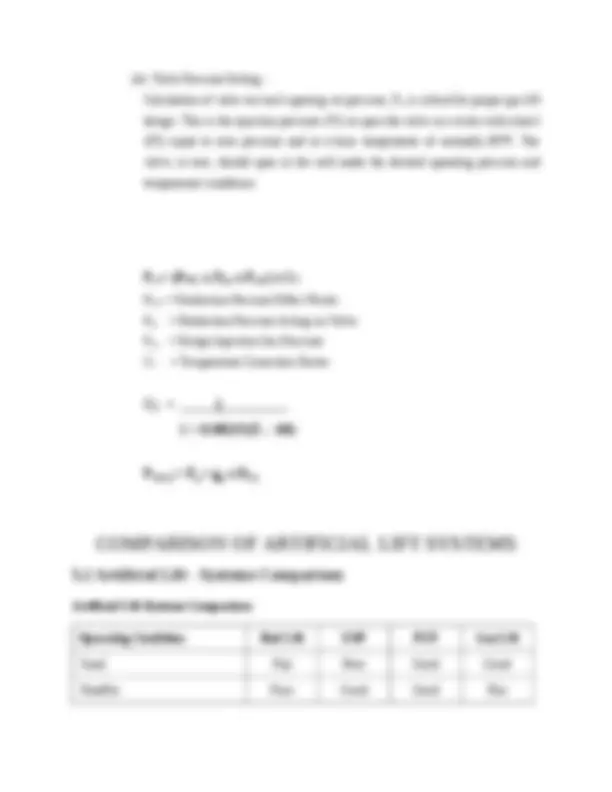
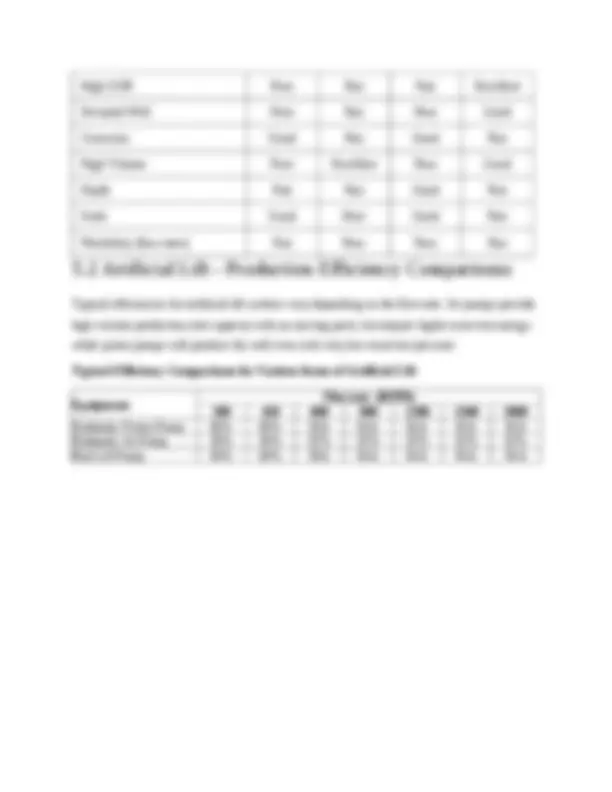
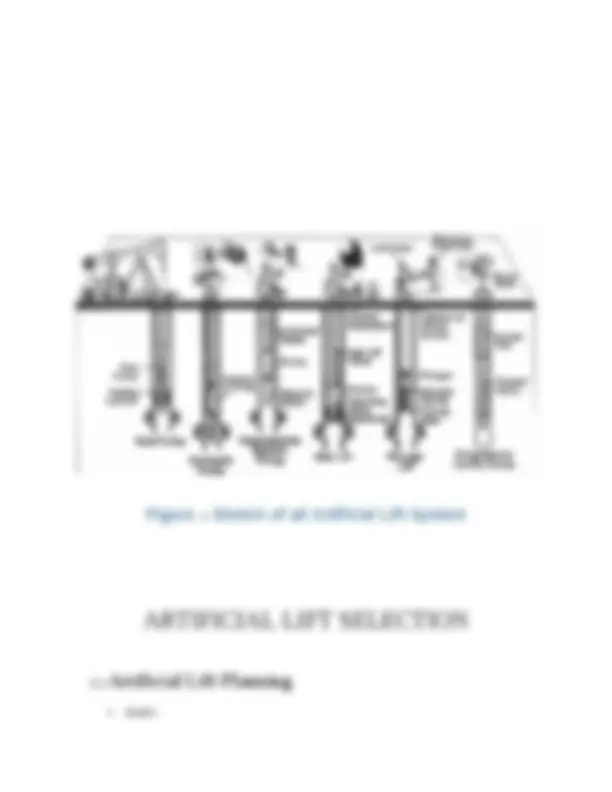
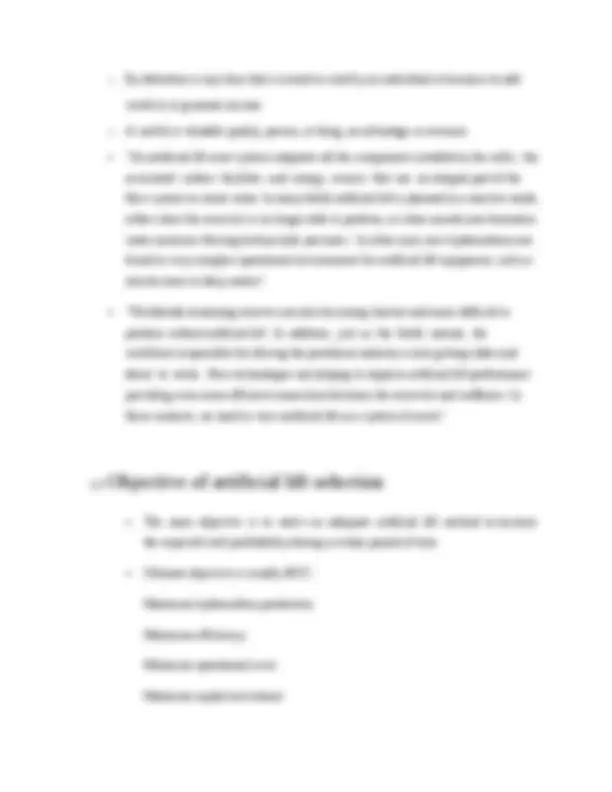
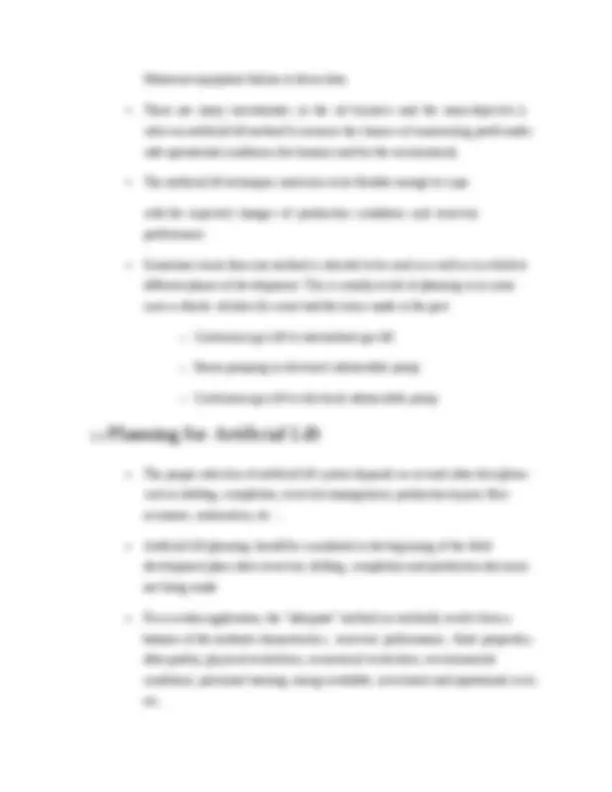
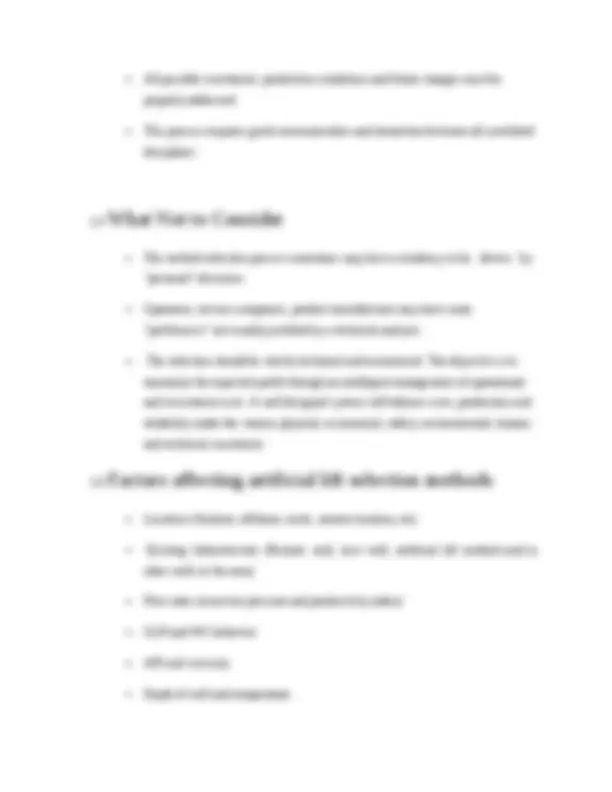
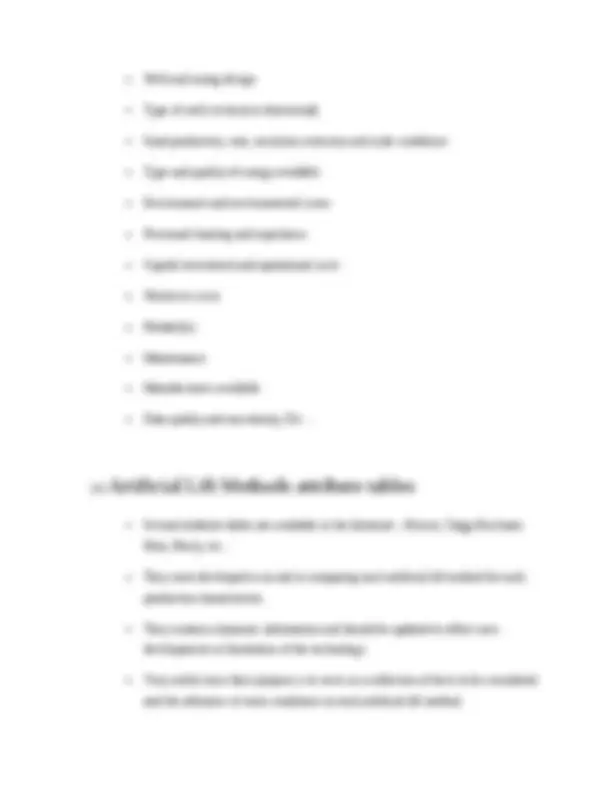
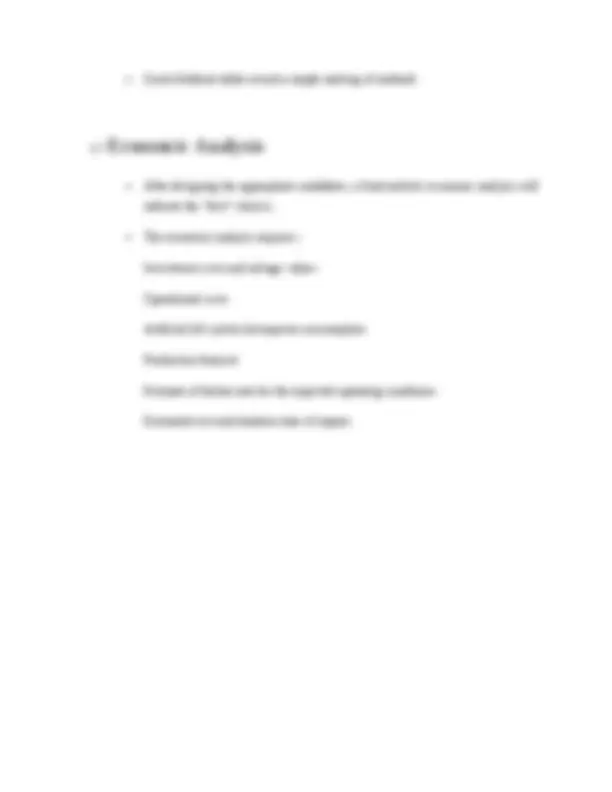
Study with the several resources on Docsity
Earn points by helping other students or get them with a premium plan
Prepare for your exams
Study with the several resources on Docsity
Earn points to download
Earn points by helping other students or get them with a premium plan
Community
Ask the community for help and clear up your study doubts
Discover the best universities in your country according to Docsity users
Free resources
Download our free guides on studying techniques, anxiety management strategies, and thesis advice from Docsity tutors
overview of artificial lift to enhance the productivity of oil well
Typology: Study notes
1 / 47
This page cannot be seen from the preview
Don't miss anything!
Hydrocarbons will normally flow to the surface under natural flow when the discovery well is completed in a virgin reservoir. The fluid production resulting from reservoir development will normally lead to a reduction in the reservoir pressure, increase in the fraction of water being produced together with a corresponding decrease in the produced gas fraction. All these factors reduce, or may even stop, the flow of fluids from the well. The remedy is to include within the well completion some form of artificial lift. Artificial lift adds energy to the well fluid which, when added to the available energy provided “for free” by the reservoir itself, allows the well to flow at a (hopefully economic) production rate. Figure 1 : Sketch of a well The purpose of artificial lift is to maintain a reduced producing bottom-hole pressure so the formation can give up the desired reservoir fluids a well may be capable of performing this task under its own power. In its later stages of flowing life, a well is capable of producing only a portion of the desired fluids. During this stage of a wells flowing life and particularly after the
well dies, a suitable means of artificial lift must be installed so the required flowing bottom-hole pressure can be maintained. Maintaining the required flowing bottom-hole pressure is the basis for the design of any artificial lift installation; if a predetermined drawdown in pressure can be maintained, the well will produce the desired fluids. The commonly used artificial lift methods include the following:
c) Air balanced Type
Conventional pumping units are available in a wide ranges if sizes, with stroke lengths varying from 12 to almost 200 inches. The strokes for any pumping unit type are available in increments(unit size). Within each unit size, the stroke length can be varied within limits ( about six different lengths being possible). These different lengths are achieved by varying the position of the pitman arm connection on the crank arm. Walking beam ratings are expressed in allowable polished rod loads (PRLs) and vary from approximately 3,00 to 35,000 lb. counter balance for conventional pumping units is accomplished by placing weighs directly on the beam( in smaller units) or by attaching weights to the rotating crank arm ( or a combination of the two methods for larger units). The pumping system consists of essentially five parts: a) The subsurface sucker rod driven pump b) The sucker rod string which transmits the surface pumping motion and the power to the subsurface pump. Also included is the necessary string of tubing and/or casing within which the sucker rods operate and which conducts the pumped fluid fro the pump to the surface c) The surface pumping equipment which changes the rotating motion of the prime mover into the oscillating liner pumping motion. d) The power transmission unit or the speed reducer e) The prime mover which furnishes the necessary power to the system
In the early days, pumps were actuated by rod lines running horizontally above the ground to an eccentric wheel in a mechanism known as a Central Power. The Central Power itself, which might operate a dozen or more pumps, was powered by a steam or internal combustion engine or by an electric motor. Among the difficulties with this scheme was keeping the system balanced as individual well loads changed. Modern pumps are powered by a prime mover. This is commonly an electric motor, but combustion engines are used in isolated locations without economic access to electricity. Common off-grid pumpjack engines run on casing gas produced from the well, but pumps have been run on many types of fuel, such as propane and diesel. In harsh climates such motors and engines may be housed inside a shack to protect them from the elements. The prime mover of the pumpjack runs a set of pulleys to the transmission which in turn drives a pair of cranks, generally with counterweights on them to assist the motor in lifting the heavy string of rods. The cranks in turn raise and lower one end of an I-beam which is free to move on an A-frame. On the other end of the beam, there is a curved metal box called a Horse Head or Donkeys Head, named so due to its appearance. A cable made of steel (or, occasionally, fiberglass) called a bridle, connects the horse head to the polished rod, a piston that passes through the stuffing box. The polished rod has a close fit to the stuffing box, letting it move in and out of the tubing without fluid escaping. (The tubing is a pipe that runs to the bottom of the well through which the liquid is produced.) The bridle follows the curve of the horse head as it lowers and raises to create an almost completely vertical stroke. The polished rod is connected to a long string of rods called sucker rods, which run through the tubing all the way to the down- hole pump, usually positioned near the bottom of the well. Downhole At the bottom of the tubing is the down-hole pump. This pump has two ball check valves: a stationary valve at bottom called the standing valve, and a valve on the piston connected to the bottom of the sucker rods that travels up and down as the rods reciprocate, known as the traveling valve. Reservoir fluid enters from the formation into the bottom of the borehole through perforations that have been made through the casing and cement (the casing is a larger
metal pipe that runs the length of the well, which has cement placed between it and the earth; the tubing, pump and sucker rods are all inside the casing). When the rods at the pump end are traveling up, the traveling valve is closed and the standing valve is open (due to the drop in pressure in the pump barrel). Consequently, the pump barrel fills with the fluid from the formation as the traveling piston lifts the previous contents of the barrel upwards. When the rods begin pushing down, the traveling valve opens and the standing valve closes (due to an increase in pressure in the pump barrel). The traveling valve drops through the fluid in the barrel (which had been sucked in during the upstroke). The piston then reaches the end of its stroke and begins its path upwards again, repeating the process. Often, gas is produced through the same perforations as the oil. This can be problematic if gas enters the pump, because it can result in what is known as gas locking, where insufficient pressure builds up in the pump barrel to open the valves (due to compression of the gas) and little or nothing is pumped. To preclude this, the inlet for the pump can be placed below the perforations. As the gas-laden fluid enters the well bore through the perforations, the gas bubbles up the annulus (the space between the casing and the tubing) while the liquid moves down to the standing valve inlet. Once at the surface, the gas is collected through piping connected to the annulus. Sucker Rod A sucker rod is the connecting link between the surface pumping unit and the subsurface pump, which is located at or near the bottom of the oil well. The vertical motion of the surface pumping unit is transferred to the subsurface pump by the sucker rods. Two types of sucker rods are in use today-stcel rods and fiberglass-reinforced plastic sucker rods. It is estimated that slightly less than 90%of the rods sold in 1985 were steel rods, while slightly more than 10% were fibreglass rods.
When the plunger reaches the top of the stroke and starts downward, the pressure inside the pump will exceed the pressure outside the pump, and the standing valve is forced closed. As the plunger continues downward, it attempts to compress the fluid, thus causing a pressure differential (∆ P =Pcomp - Pdis) between inside the pump and the production column. With the plunger travelling downward, Pcomp (pressure inside pump barrel) causes a force (Fup), which pushes against the bottom of the travelling valve ball, attempting to open the ball. When this force is big enough to exceed the force pushing on the travelling valve ball from the fluid column above the pump (Fdown), the travelling valve ball opens. As the plunger continues downward, the fluid that was below the travelling valve becomes fluid above the travelling valve. Thus, the fluid within the pump barrel is transferred through the open travelling valve into the production column of fluid above the pump. When the plunger reaches the bottom of the pump, the differential pressure (∆ P) diminishes to zero, the travelling valve closes and the plunger starts going upward again creating a low pressure P1 within the pump barrel, opening the standing valve and allowing fluid from the well to enter the pump. Now it is clear that the two main pump valves (traveling and standing) are working in the principle of differential pressure. The two valves are one-way check valves opening when pressure below is greater than that above the valve. Any delay in opening or closing one of them will reduce the pump volumetric efficiency.
Electrical submersible pumps (ESPs) are easy to install and operate. They can lift extremely high volumes from highly productive oil reservoirs. Crooked/deviated holes present no problem. ESPs are applicable to offshore operations. Lifting costs for high volumes are generally very low. Limitations to ESP applications include high voltage electricity availability, not applicable to multiple completions, deep and high temperature oil reservoirs, gas and solids production is troublesome, and costly to install and repair. ESP systems have higher horsepower, operate in hotter applications, are used in dual installations and as spare down-hole units, and include down-hole oil/water separation. Sand and gas problems have led to new products. Automation of the systems includes monitoring, analysis, and control.
Hydraulic piston pumping systems can lift large volumes of liquid from great depth by pumping wells down to fairly low pressures. Crooked holes present minimal problems. Both natural gas and electricity can be used as the power source. They are also applicable to multiple completions and offshore operations. Their major disadvantages include power oil systems being fire hazards and costly, power water treatment problems, and high solids production being troublesome. As shown in Figure a hydraulic piston pump (HPP) consists of an engine with a reciprocating piston driven by a power fluid connected by a short shaft to a piston in the pump end. HPPs are usually double-acting, that is, fluid is being displaced from the pump on both the upstroke and the down stroke. The power fluid is injected down a tubing string from the surface and is either returned to the surface through another tubing (closed power fluid) or commingled with the produced fluid in the production string (open power fluid).
The function of plunger lift equipment is to provide for more efficient utilization of lifting gas energy in any well that is or can be produced in a cyclic manner similar to intermittent gas lift. Plunger lift incorporates a piston that normally travels the entire length of the tubing string, providing a solid and sealing interface between the lifting gas and the produced liquid. This interface changes the flow pattern during a lifting cycle from the familiar bullet shape of gas penetration of the liquid slug to a pattern whereby gas flow is possible only between the plunger’s outside diameter and the tubing walls. To lift the plunger and the liquid load above the plunger, the gas pressure must be greater than these loads. The small quantity of gas that bypasses the plunger during a cycle flows up through the annular space and acts as a sweep to minimize liquid fallback. The use of plunger equipment, by minimizing liquid fallback and eliminating possible gas penetration through the centre of the liquid slug, provides for the most efficient form of intermittent gas lift production available.