
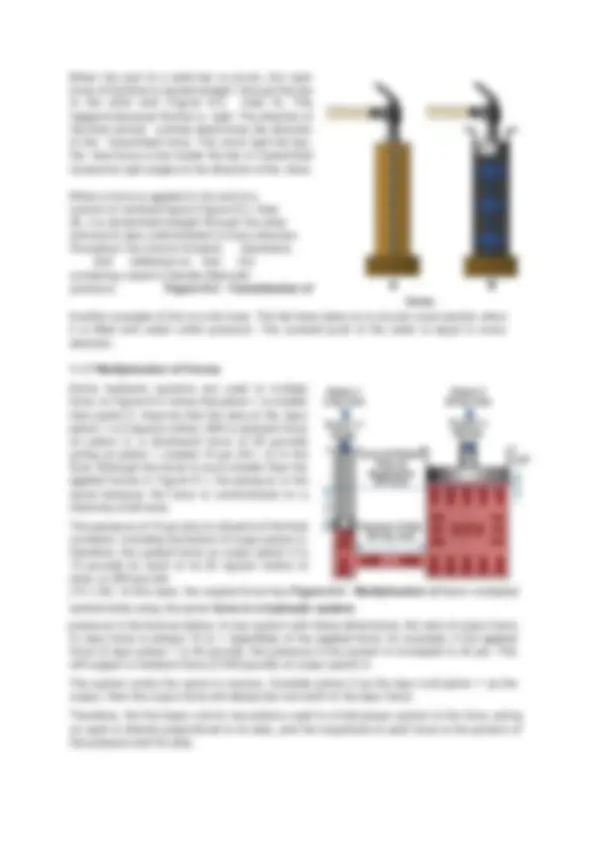
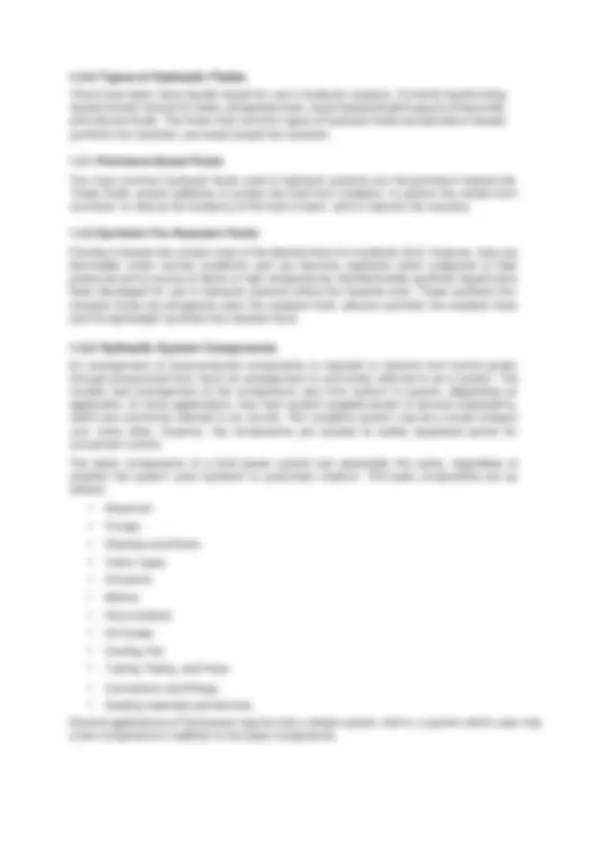
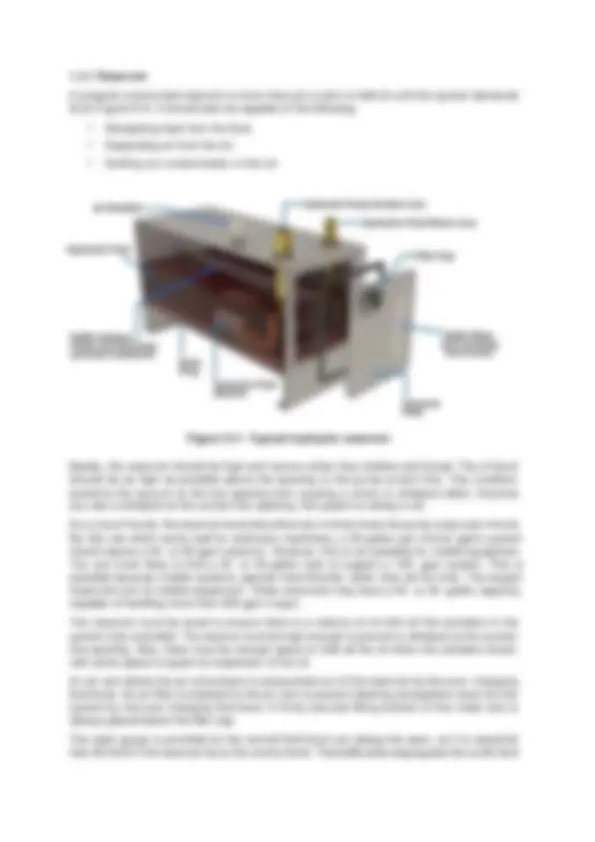
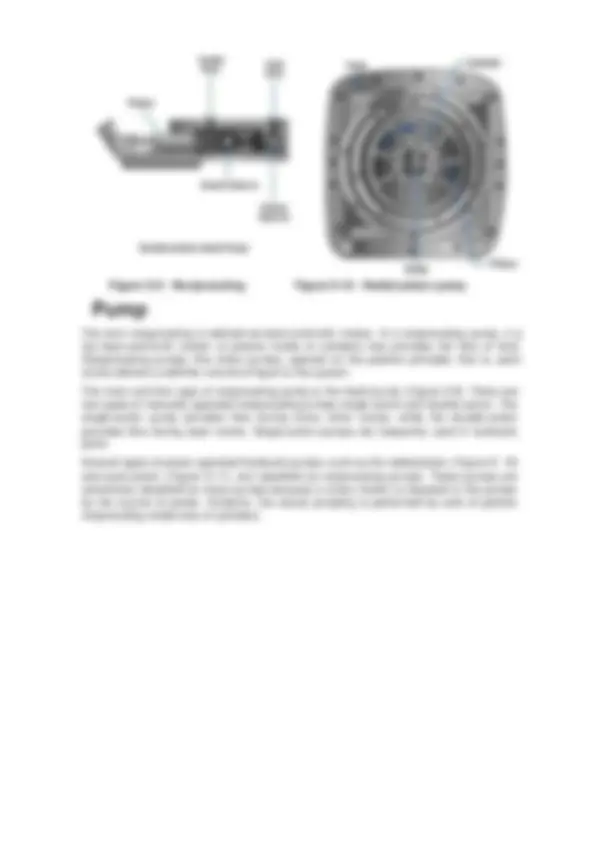
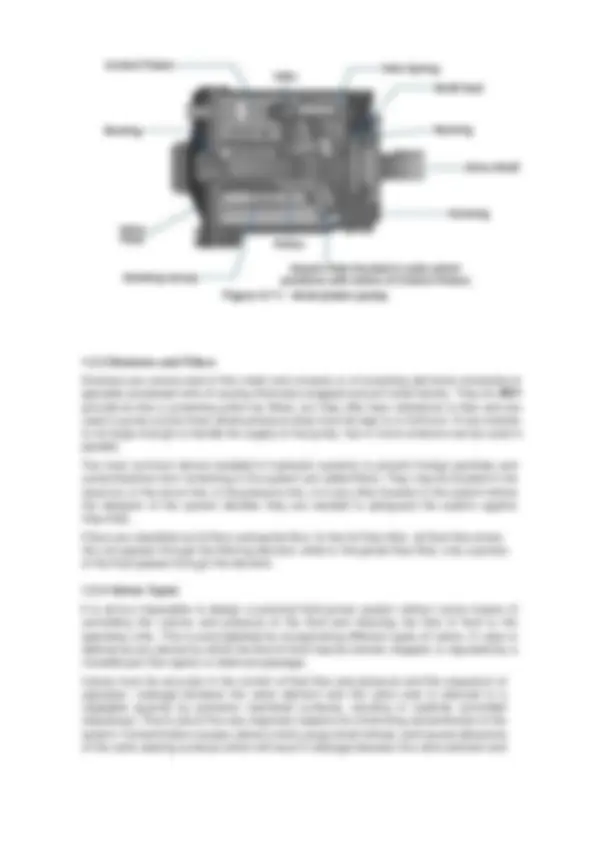

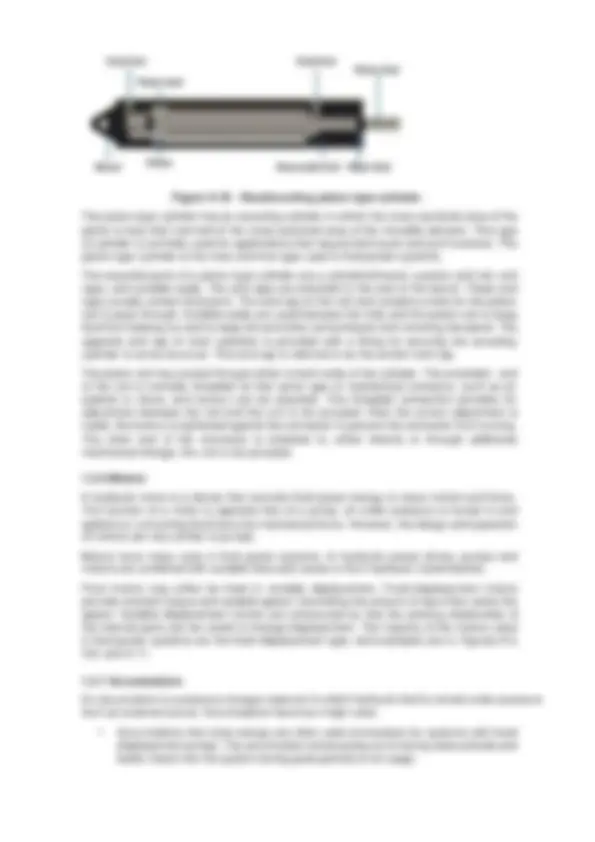
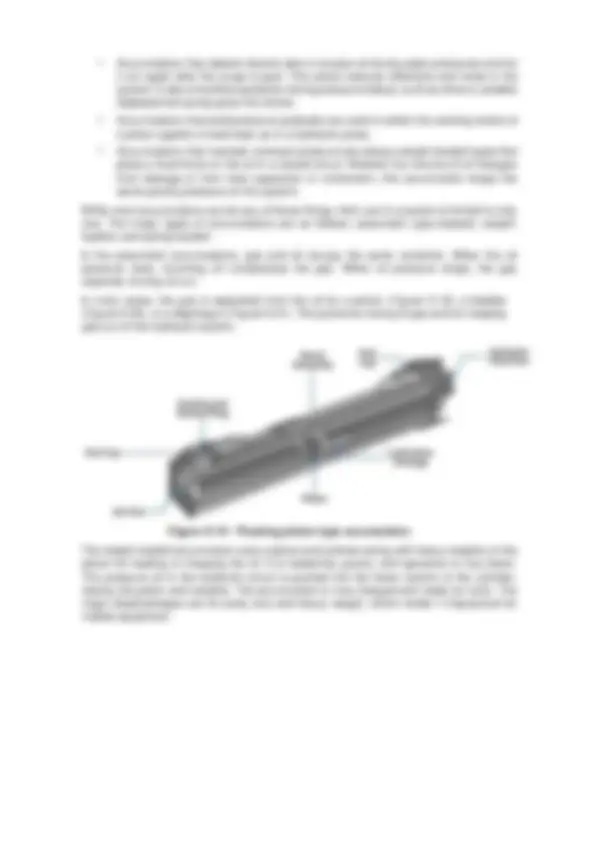
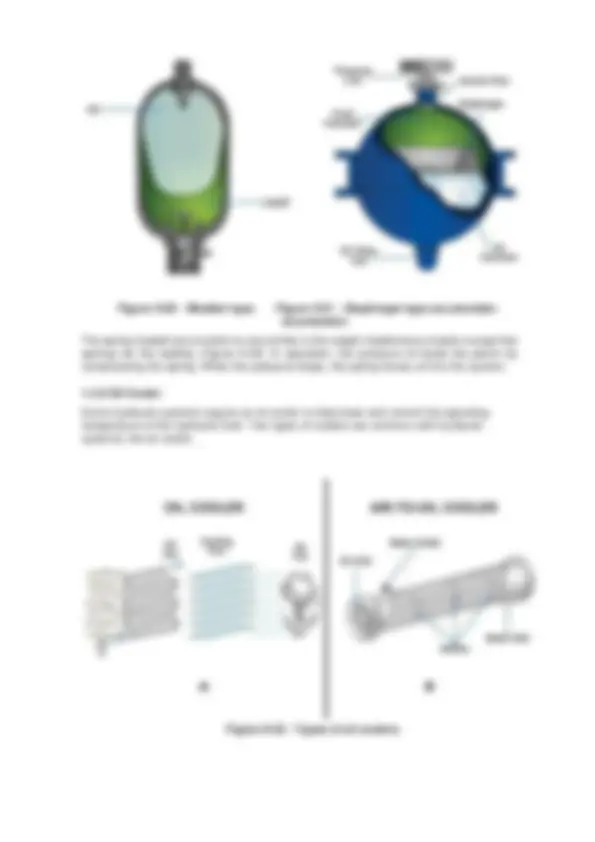
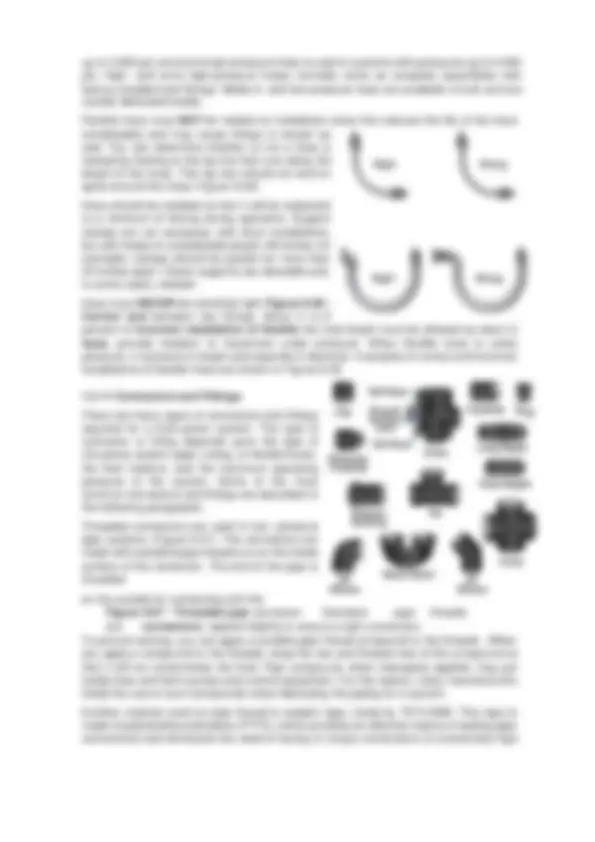
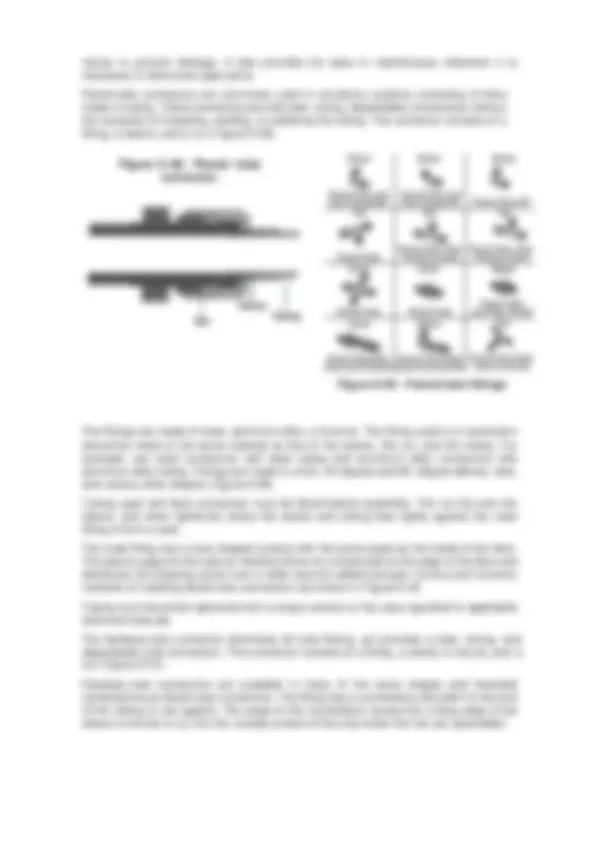
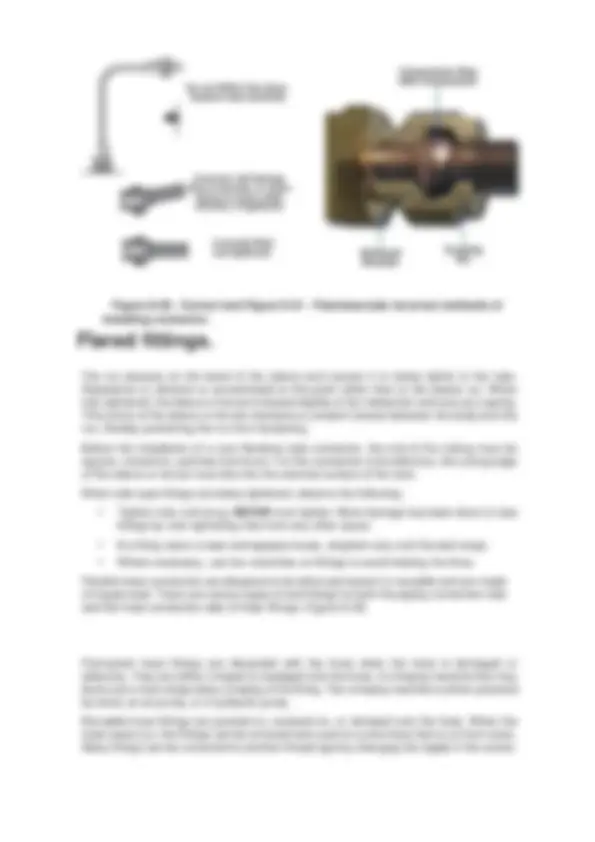
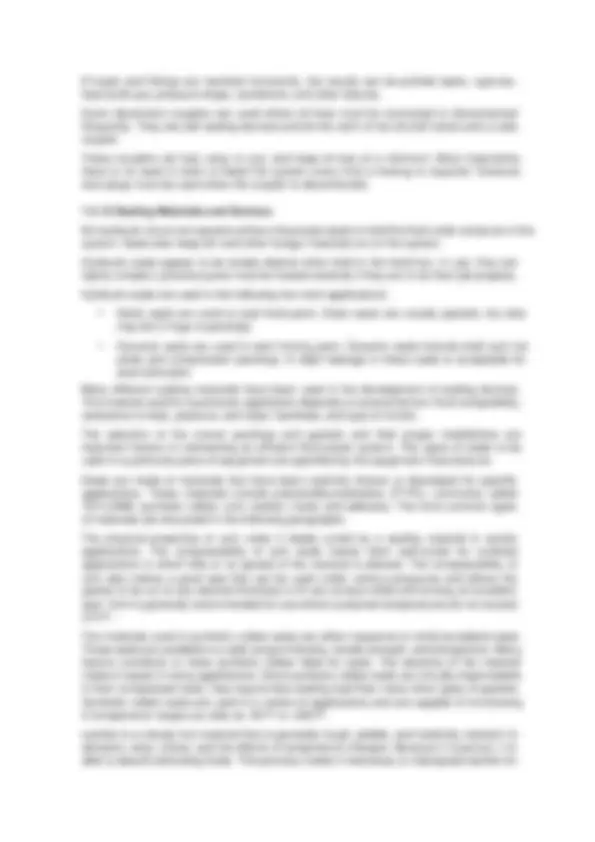
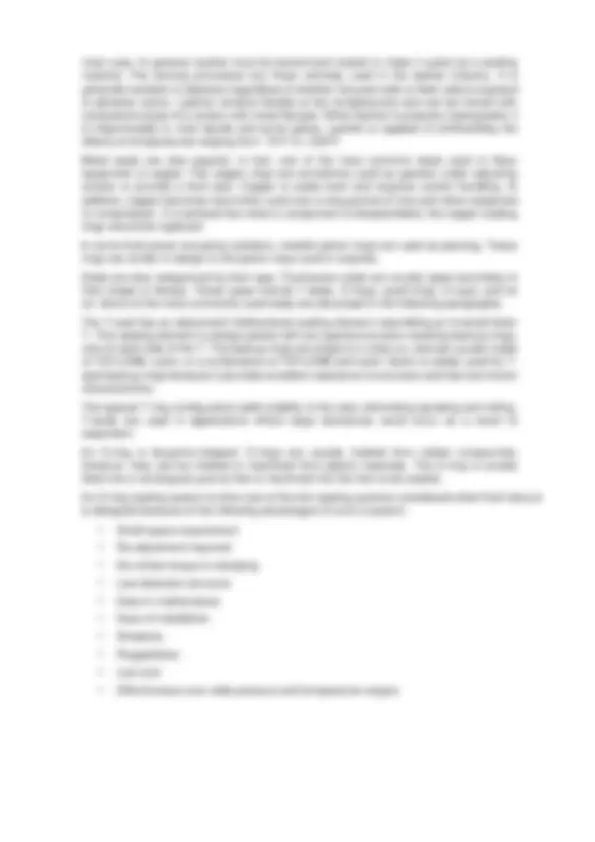
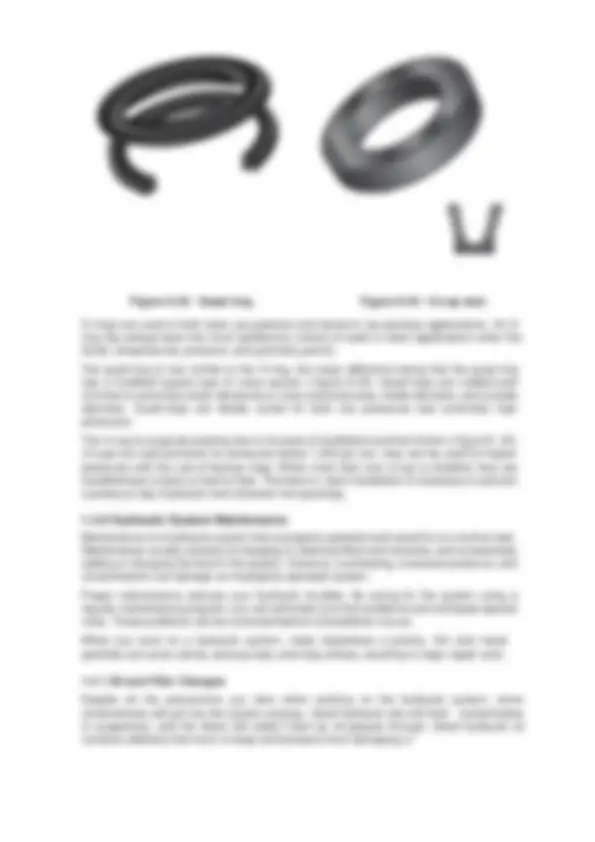
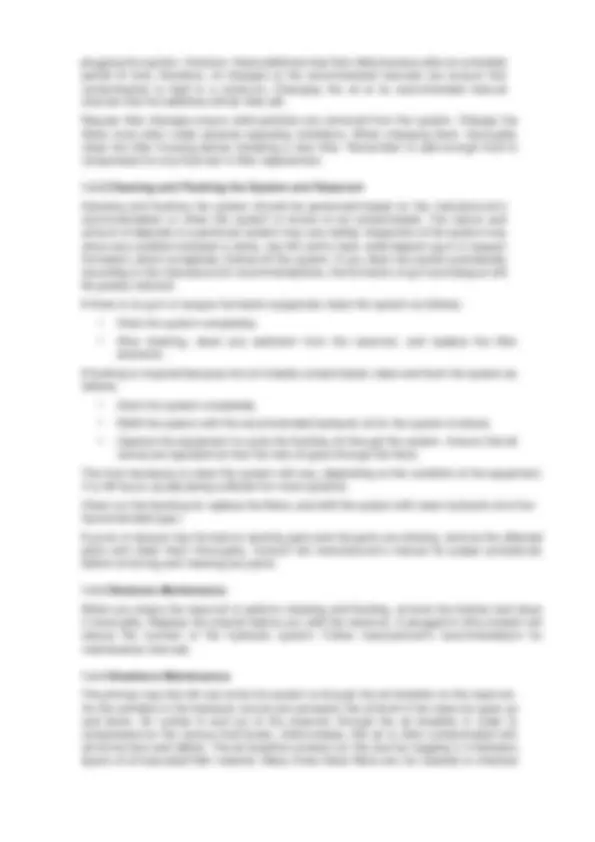
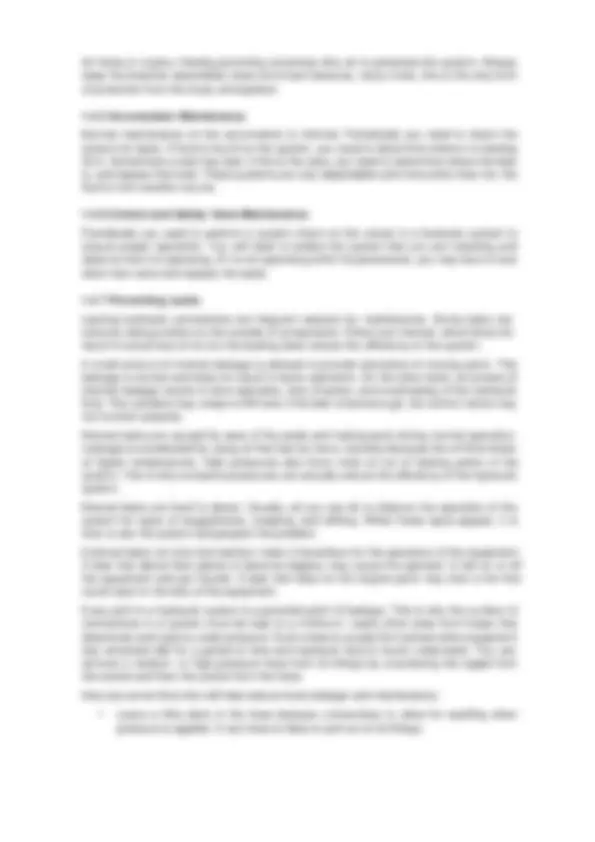
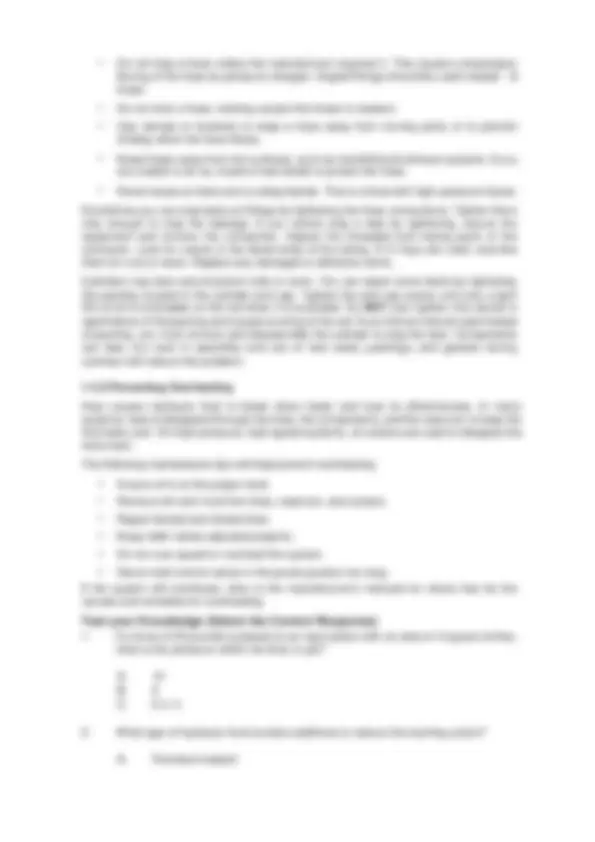
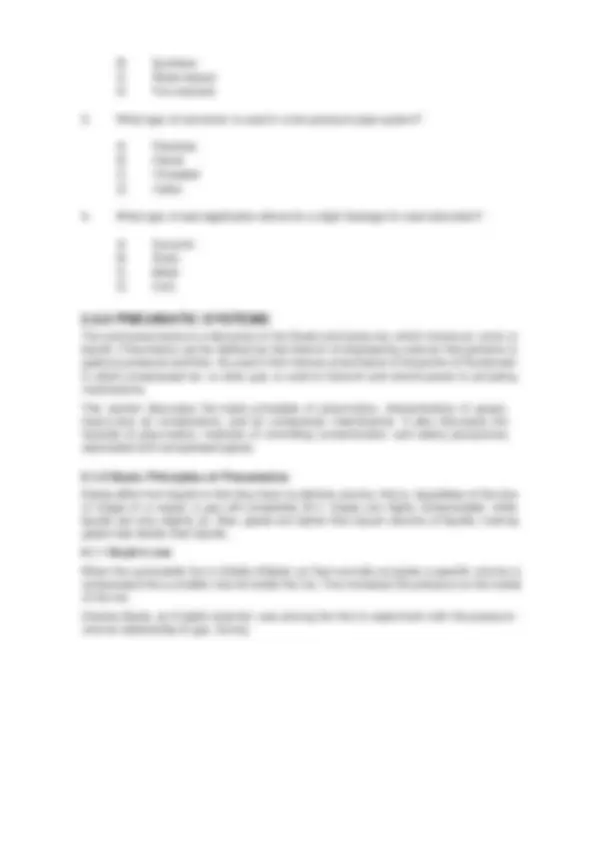
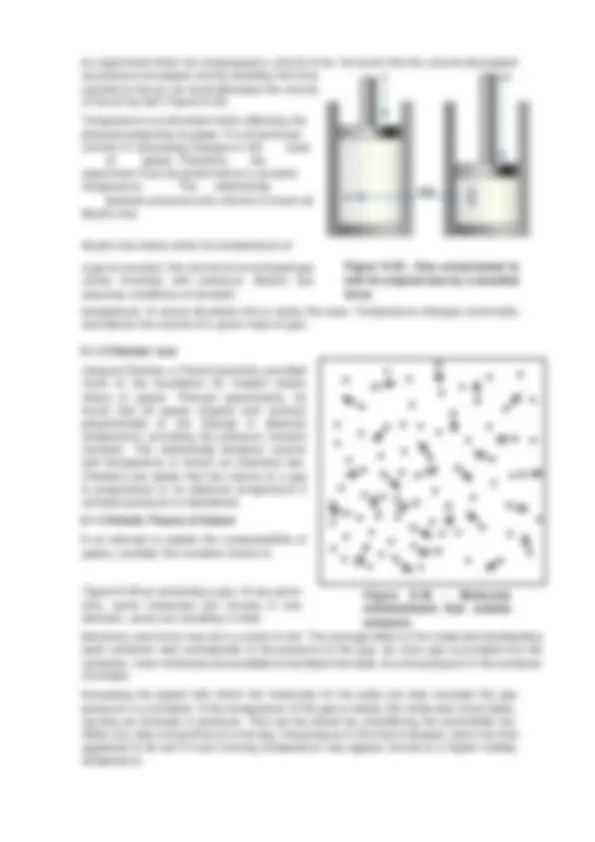
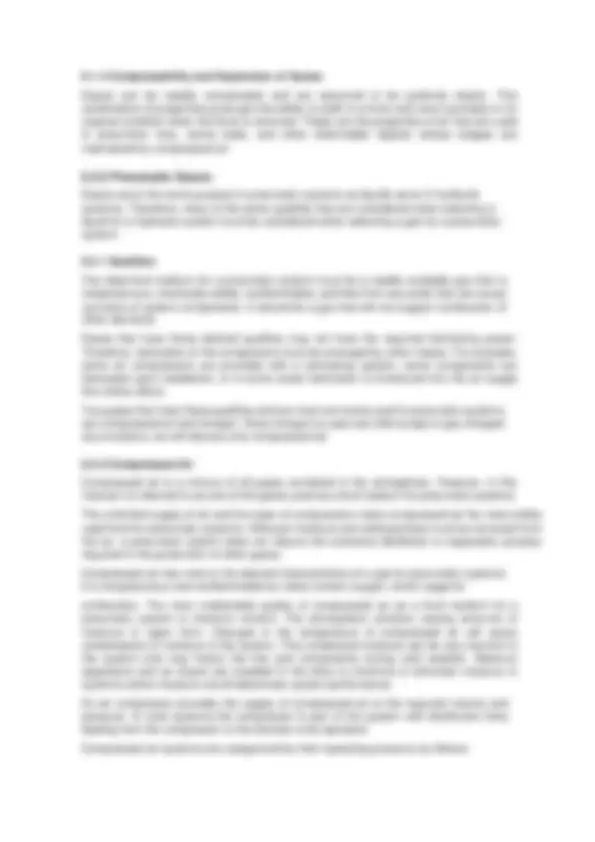
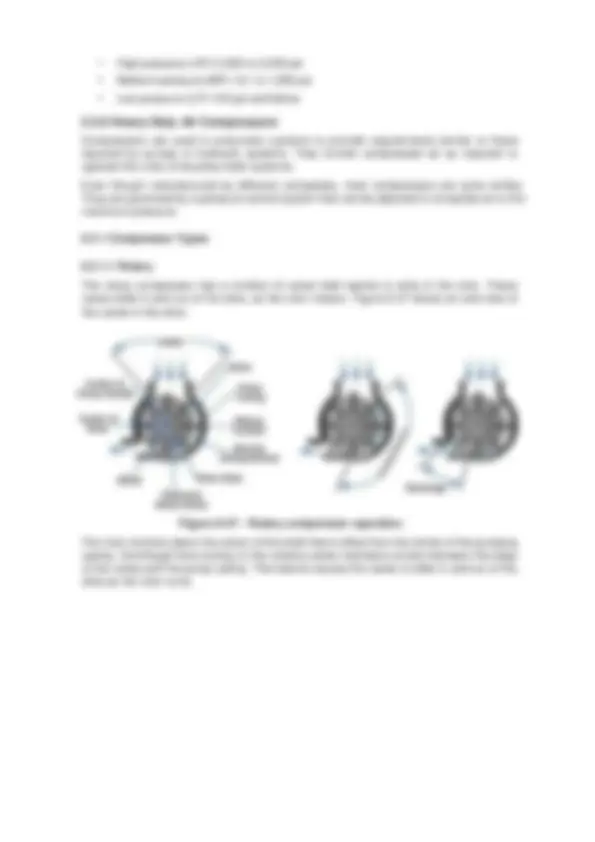
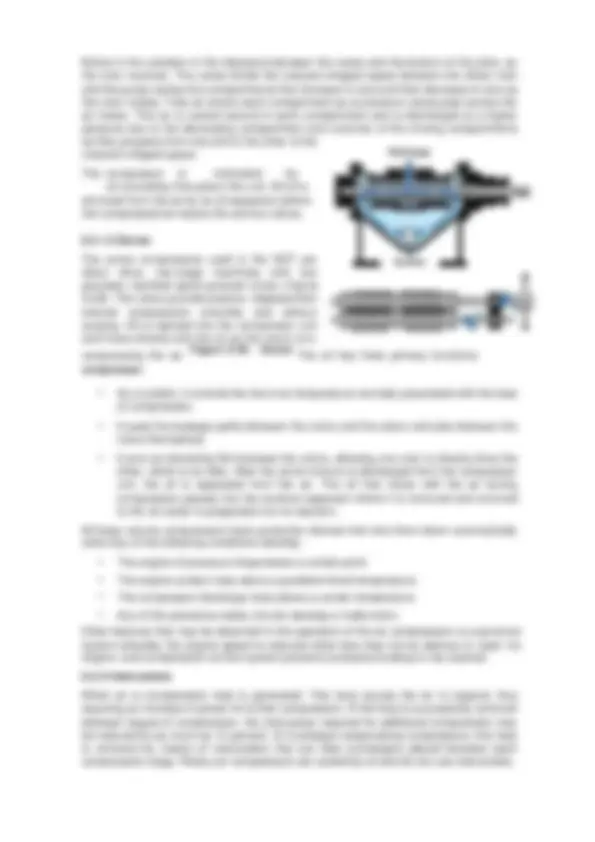
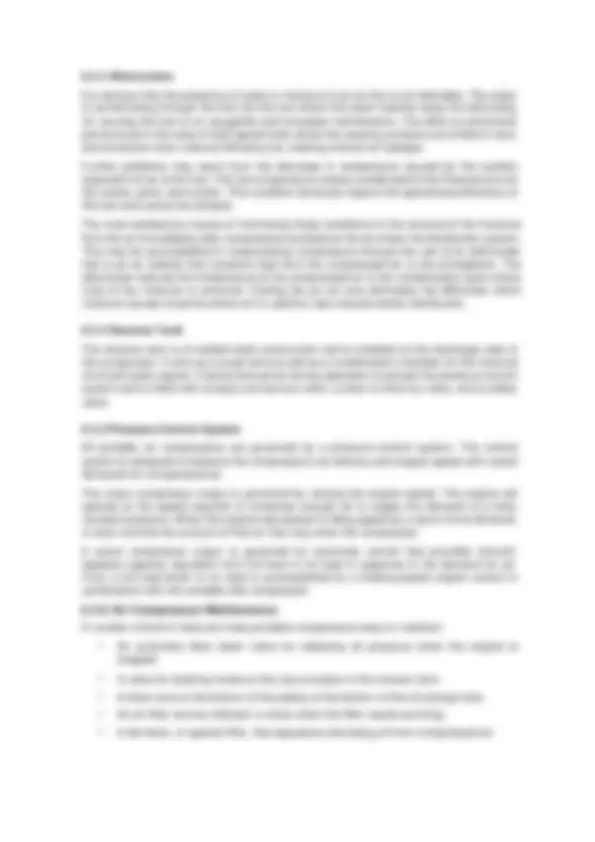

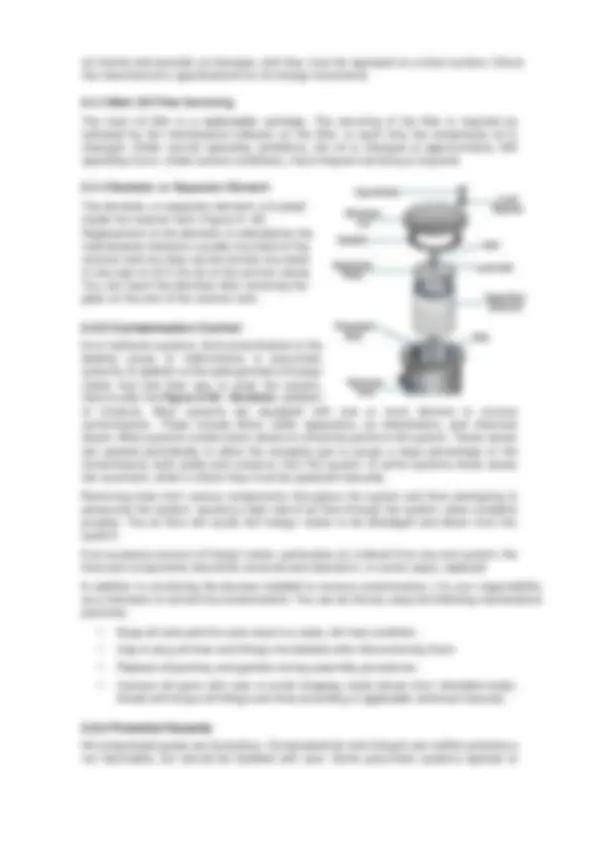
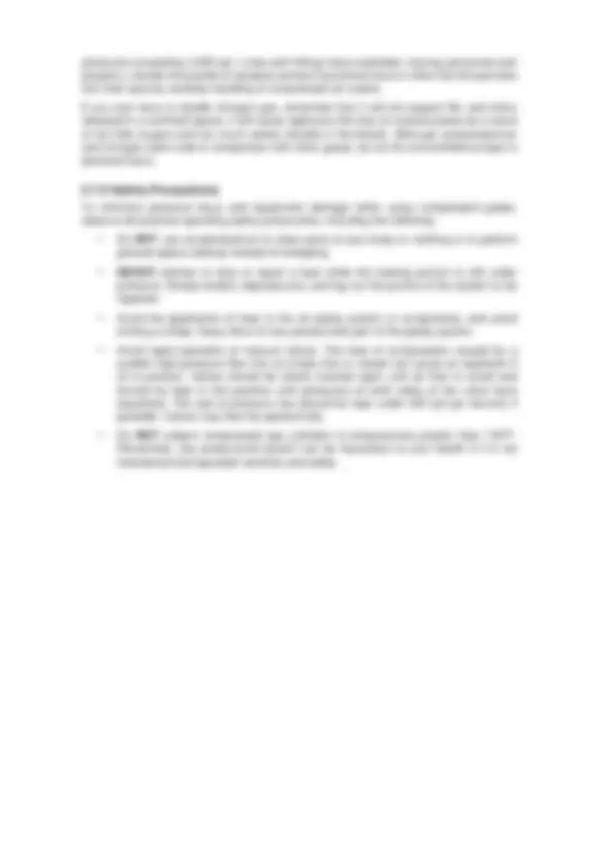
Study with the several resources on Docsity
Earn points by helping other students or get them with a premium plan
Prepare for your exams
Study with the several resources on Docsity
Earn points to download
Earn points by helping other students or get them with a premium plan
Community
Ask the community for help and clear up your study doubts
Discover the best universities in your country according to Docsity users
Free resources
Download our free guides on studying techniques, anxiety management strategies, and thesis advice from Docsity tutors
Principles of Hydraulic and Pneumatic Systems
Typology: Lecture notes
1 / 35
This page cannot be seen from the preview
Don't miss anything!
The extensive use of hydraulics to transmit power is due to the fact that a properly constructed hydraulic system possesses a number of favorable characteristics:
The basic principles of hydraulics are few and simple:
1.1.1.1 Pressure Pressure (P) is the amount of push or pull (force) applied to each unit area of the surface and is expressed in pounds per square inch (psi) or grams per square centimeter (gm/cm 2 ). Pressure may be exerted in one direction, in several directions, or in all directions. 1.1.2 Force Force (F) means a total push or pull. It is push or pull exerted against the total area of a particular surface and is expressed in pounds or grams. 1.1.3 Area Area (A) represents the surface area acted upon by the hydraulic force. 1.1.4 Computing Force, Pressure, and Area The formula used to compute force, pressure, and area in a hydraulic system can be described by force equals pressure times area and is written as: F=PxA. Pressure equals force divided by area. By rearranging the above formula, this statement may be condensed into the following: P=F divided by A or P=F/A. Since the area equals force divided by pressure, the formula for area is written as follows: A=F/P. If the force is 100 pounds and the area of the input piston is 10 square inches, then pressure in the fluid is 10 psi (100 ÷ 10). It must be emphasized that this fluid pressure cannot be created without resistance to flow, which, in this case, is provided by the 100- pound force acting against the top of the output piston 2. This pressure acts on piston 2, so for each square inch of its area, it is pushed upward with the force of 10 pounds. In this case, a fluid column of a uniform cross section is used so the area of output piston 2 is the same as input piston 1, or 10 square inches; therefore, the upward force on output piston 2 is 100 pounds-the same as was applied to input piston 1. All that was accomplished in this system was to transmit the 100 - pound force around a bend; however, this principle underlies practically all mechanical applications of fluid power. 1.1.5 Incompressibility and Expansion of Liquids For all practical purposes, fluids are incompressible. Under extremely high pressures, the volume of a fluid can be decreased somewhat, though the decrease is so slight that it is considered to be negligible except by design engineers. Liquids expand and contract because of temperature changes. When liquid in a closed container is subjected to high temperatures, it expands, and this exerts pressure on the walls of the container; therefore, it is necessary that pressure-relief mechanisms and expansion chambers be incorporated into hydraulic systems. Without these precautionary measures, the expanding fluid could exert enough pressure to rupture the system. 1.1.6 Transmission of Forces through Liquids
There have been many liquids tested for use in hydraulic systems. Currently liquids being tested include mineral oil, water, phosphate ester, water based ethylene glycol compounds, and silicone fluids. The three most common types of hydraulic fluids are petroleum-based, synthetic fire-resistant, and water based fire-resistant. 1.2.1 Petroleum-Based Fluids The most common hydraulic fluids used in hydraulic systems are the petroleum-based oils. These fluids contain additives to protect the fluid from oxidation, to protect the metals from corrosion, to reduce the tendency of the fluid to foam, and to improve the viscosity. 1.2.2 Synthetic Fire-Resistant Fluids Petroleum-based oils contain most of the desired traits of a hydraulic fluid. However, they are flammable under normal conditions and can become explosive when subjected to high pressures and a source of flame or high temperatures. Nonflammable synthetic liquids have been developed for use in hydraulic systems where fire hazards exist. These synthetic fire- resistant fluids are phosphate ester fire-resistant fluid, silicone synthetic fire-resistant fluid, and the lightweight synthetic fire-resistant fluid.
An arrangement of interconnected components is required to transmit and control power through pressurized fluid. Such an arrangement is commonly referred to as a system. The number and arrangement of the components vary from system to system, depending on application. In many applications, one main system supplies power to several subsystems, which are commonly referred to as circuits. The complete system may be a small compact unit; more often, however, the components are located at widely separated points for convenient control. The basic components of a fluid power system are essentially the same, regardless of whether the system uses hydraulic or pneumatic medium. The basic components are as follows:
1.3.1 Reservoir A properly constructed reservoir is more than just a tank to hold oil until the system demands fluid ( Figure 9- 4 ). It should also be capable of the following:
Figure 9- 5 - Gear-driven Figure 9- 6 - Screw-driven hydraulic pump. hydraulic pump. Rotary pumps are designed with very small clearances between rotating parts and stationary parts to minimize slippage from the discharge side back to the suction side. They are designed to operate at relatively moderate speeds. Operating at high speeds causes erosion and excessive wear, which results in increased clearances. There are numerous types of rotary pumps and various methods of classification. They may be classified by shaft position-either vertically or horizontally mounted; the type of drive-electric motor, gasoline engine, and so forth; their manufacturer's name; or service application. However, classification of rotary pumps is generally made according to the type of rotating element.
Figure 9- 9 - Reciprocating Figure 9- 10 - Radial piston pump.
The term reciprocating is defined as back-and-forth motion. In a reciprocating pump, it is the back-and-forth motion of pistons inside of cylinders that provides the flow of fluid. Reciprocating pumps, like rotary pumps, operate on the positive principle, that is, each stroke delivers a definite volume of liquid to the system. The most common type of reciprocating pump is the hand pump ( Figure 9- 9 ). There are two types of manually operated reciprocating pumps-single action and double action. The single-action pump provides flow during every other stroke, while the double-action provides flow during each stroke. Single-action pumps are frequently used in hydraulic jacks. Several types of power-operated hydraulic pumps, such as the radial piston ( Figure 9- 10 ) and axial piston ( Figure 9- 11 ), are classified as reciprocating pumps. These pumps are sometimes classified as rotary pumps because a rotary motion is imparted to the pumps by the source of power. However, the actual pumping is performed by sets of pistons reciprocating inside sets of cylinders.
valve seat when the valve is closed. Any of these can result in inefficient operation or complete stoppage of the equipment. Valves may be controlled manually, electrically, pneumatically, mechanically, hydraulically, or by combinations of two or more methods. Factors that determine the method of control include the purpose of the valve, the design and purpose of the system, the location of the valve within the system, and the availability of the source of power. Valves are classified according to their use: flow control, pressure control, and directional control. Some of these valves have multiple functions that fall into more than one classification. 1.3.4.1 Pressure Control Valve The safe and efficient operation of hydraulic systems, systems components, and related equipment requires a means of controlling pressure. There are many types of automatic pressure control valves. Some of them Figure 9- 12 - Relief valve. merely provide an escape for pressure that exceeds a set pressure, some only reduce the pressure to a lower pressure system or subsystem, and some keep the pressure in a system within a required range. The most common pressure control valves are relief valves ( Figure 9 - 12 ), pressure regulators, pressure-reducing valves, and counterbalance valves. 1.3.4.2 Directional Control Valve Directional control valves are designed to direct the flow of fluid, at the desired time, to the point in a fluid power system where it will do work, for example, using a directional control valve to drive a ram back and forth in its cylinder. Various other terms are used to identity directional control valves, such as selector valve, transfer valve, and control valve. Directional control valves for hydraulic and pneumatic systems are similar in design and operation. However, there is one major difference. The return ports of a hydraulic valve is ported through a return line to the reservoir, while the similar port in a pneumatic valve, commonly referred to as an exhaust port, is usually vented to the atmosphere. Figure 9- 13 - Poppet control valve. Directional control valves may be operated by differences in pressure acting on opposite sides of the valving element, or they may be positioned manually, mechanically, or electrically. Often two or more methods of operating the same valve will be used in different phases of its action. Directional control valves may be classified in several ways. Some of the different ways are by the type of control, the number of ports in the valve housing, and the specific function of the valve. The most common method is by the type of valving element used in the
construction of the valve. The most common types of valving elements used in a hydraulic system are the poppet ( Figure 9- 13 ), rotary spool ( Figure 9- 14 ), and sliding spool valves ( Figure 9- 15 ). Figure 9- 14 - Rotary spool control valve. Figure 9- 15 - Sliding spool control valve. 1.3.4.3 Volume Control Valve A volume control valve ( Figure 9- 16 ) is a valve that opens by lifting a round or rectangular wedge out of the path of the fluid. The movable object that controls the flow can form a wedge shape or it can be parallel. Typically, these valves should never be used for regulating flow unless they are specifically designed for that purpose. On opening the valve, the flow path is enlarged in a highly nonlinear manner with respect to percent of opening. This means that flow rate does not change evenly with stem travel. Also, a partially open valve disk tends to vibrate from the fluid flow. Most of the flow change occurs near shutoff with a relatively high fluid velocity causing disk and seat wear and eventual leakage if used to regulate flow. Typical volume control valves Figure 9- 16 - Volume control valve.
Figure 9- 18 - Double-acting piston type cylinder. The piston-type cylinder has an actuating cylinder in which the cross-sectional area of the piston is less than one half of the cross-sectional area of the movable element. This type of cylinder is normally used for applications that require both push and pull functions. The piston-type cylinder is the most common type used in fluid power systems. The essential parts of a piston-type cylinder are a cylindrical barrel, a piston and rod, end caps, and suitable seals. The end caps are attached to the end of the barrel. These end caps usually contain fluid ports. The end cap on the rod end contains a hole for the piston rod to pass through. Suitable seals are used between the hole and the piston rod to keep fluid from leaking out and to keep dirt and other contaminants from entering the barrel. The opposite end cap of most cylinders is provided with a fitting for securing the actuating cylinder to some structure. This end cap is referred to as the anchor end cap. The piston rod may extend through either or both ends of the cylinder. The extended end of the rod is normally threaded so that some type of mechanical connector, such as an eyebolt or clevis, and locknut can be attached. This threaded connection provides for adjustment between the rod and the unit to be actuated. After the correct adjustment is made, the locknut is tightened against the connector to prevent the connector from turning. The other end of the connector is attached to, either directly or through additional mechanical linkage, the unit to be actuated. 1.3.6 Motors A hydraulic motor is a device that converts fluid power energy to rotary motion and force. The function of a motor is opposite that of a pump; oil under pressure is forced in and spilled out, converting fluid force into mechanical force. However, the design and operation of motors are very similar to pumps. Motors have many uses in fluid power systems. In hydraulic power drives, pumps and motors are combined with suitable lines and valves to form hydraulic transmissions. Fluid motors may either be fixed or variable displacement. Fixed-displacement motors provide constant torque and variable speed. Controlling the amount of input flow varies the speed. Variable displacement motors are constructed so that the working relationship of the internal parts can be varied to change displacement. The majority of the motors used in fluid power systems are the fixed-displacement type, and examples are in Figures 9-5, 9 - 8, and 9 - 11. 1.3.7 Accumulators An accumulator is a pressure storage reservoir in which hydraulic fluid is stored under pressure from an external source. Accumulators have four major uses:
The water cooler has water flowing through the center of the capsule and the hydraulic fluid is flowed into a series of tubes that surround the water jacket. The cool water removes the heat of the hydraulic fluid as it returns to the reservoir. 1.3.9 Cooling Fan The cooling fan is run off an electrical circuit that blows across the tubes of the heat exchanger. This air circulation cools the hydraulic fluid before returning it to the reservoir. 1.3.10 Tubing, Piping, and Hose The three types of lines used in fluid power systems are tubing (semi rigid), pipe (rigid), and hose (flexible). A number of factors are considered when the type of line is selected for a particular system. These factors include the type of fluid, the required system pressure, and the location of the system. For example, heavy pipe might be used for a large stationary system, but comparatively lightweight steel tubing is used in the automotive brake system. Flexible hose is required in installations where units must be free to move relative to each other. The choice between pipe and tubing depends on system pressure and flow. The advantages of tubing include easier bending and flaring, fewer fittings, better appearance, better reusability, and less leakage. However, pipe is cheaper and will handle large volumes under high pressures. Pipe is also used where straight-line hookups are required and for more permanent installations. In either case, the hydraulic lines must be compatible with the entire system. Pressure loss in the line must be kept to a minimum for an efficient system. Pipes for hydraulic systems should be made of seamless cold-drawn mild steel. Galvanized pipe should NOT be used because the zinc coating could flake or scale, causing damage to the valves and pumps. Tubing used in fluid power systems is commonly made from steel, copper, aluminum, and, in some instances, plastic. Each of these materials has its own distinct advantages or disadvantages in certain applications. The use of copper is limited to low-pressure hydraulic systems where vibration is limited. Copper has high resistance to corrosion and is easily drawn or bent. However, it is unsatisfactory for high temperatures and has a tendency to harden and break due to stress and vibration. Tubing constructed of cold-drawn steel is the accepted standard in hydraulics where high pressures are encountered. Steel is used because of its strength, stability for bending and flanging, and adaptability to high pressures and temperatures. Its chief disadvantage is its comparatively low resistance to corrosion. There are two types of steel tubing: seamless and electric welded. Aluminum is limited to low-pressure use, yet it has good flaring and bending characteristics. Plastic tubing lines are made from a variety of materials; nylon is the most suitable for use in low-pressure hydraulic applications ONLY. There are three important dimensions of any tubular product: outside diameter (OD), inside diameter (ID), and wall thickness. Sizes of pipe are listed by the nominal (or approximate) ID and wall thickness. Sizes of tubing are listed by the actual OD and the wall thickness. The material, the inside diameter, and the wall thickness are the three primary considerations in the selection of lines for the circulatory system of a particular fluid power system. The manufacturers of tubing and pipe usually supply charts, graphs, or tables which aid in the selection of proper lines for fluid power systems. These tables and charts use different methods for deriving the correct sizes of pipe and tubing.
Line should normally be kept as short and free of bends as possible. However, tubing should NOT be assembled in a straight line because a bend tends to eliminate strain by absorbing vibration and it compensates for thermal expansion and contraction. Bends are preferred to elbows because bends cause less of a power loss. A few of the incorrect and correct methods of installing tubing are shown in Figure 9-24. Figure 9- 24 - Correct and incorrect methods of installing tubing. Flexible hose is used in fluid power systems where there is a need for flexibility, such as connection to units that move while in operation or to units attached to a hinged portion of the equipment. It is also used in locations that are subjected to severe vibration. Flexible hose is usually used to connect the pump to the system. The vibration that is set up by the operating pump would ultimately cause rigid tubing to fail. Flexible hose is designated by a dash number, which is the ID of the hose expressed in 16ths of an inch and is stenciled on the side of the hose. For example, the inside of a - 16 hose is 1 inch. For a few hose styles, this is approximate and is not a true ID. Rubber hose is designed for specific fluid, temperature, and pressure ranges and is provided in various specifications. Flexible hydraulic hose is composed of three basic parts ( Figure 9- 25 ): The inner tube is a synthetic rubber layer that is oil-resistant. It must be smooth, flexible, and able to resist heat and corrosion. Figure 9- 25 - Flexible rubber hose construction. The reinforcement layers vary with the type of hose. These layers (or plies) are constructed of natural or synthetic fibers, braided wire, or a combination of these. The strength of this layer depends upon the pressure requirement of the system. The outer cover protects the reinforcement layers. A special rubber is most commonly used for the outer layer because it resists abrasion and exposure to weather, oil, and dirt. Flexible hose is provided in four pressure ranges. Low-pressure hose is used in a low- pressure system and for the exhaust lines of high-pressure systems. Medium-pressure hose is used in systems with pressures up to 1,200 psi; high-pressure hose is used with pressures
values to prevent leakage. It also provides for ease in maintenance whenever it is necessary to disconnect pipe joints. Flared-tube connectors are commonly used in circulatory systems consisting of lines made of tubing. These connectors provide safe, strong, dependable connections without the necessity of threading, welding, or soldering the tubing. The connector consists of a fitting, a sleeve, and a nut ( Figure 9- 28 ). Figure 9- 29 - Flared-tube fittings. The fittings are made of steel, aluminum alloy, or bronze. The fitting used in a connection should be made of the same material as that of the sleeve, the nut, and the tubing. For example, use steel connectors with steel tubing and aluminum alloy connectors with aluminum alloy tubing. Fittings are made in union, 45-degree and 90- degree elbows, tees, and various other shapes ( Figure 9- 29 ). Tubing used with flare connectors must be flared before assembly. The nut fits over the sleeve, and when tightened, draws the sleeve and tubing flare tightly against the male fitting to form a seal. The male fitting has a cone-shaped surface with the same angle as the inside of the flare. The sleeve supports the tube so vibration does not concentrate at the edge of the flare and distributes the shearing action over a wider area for added strength. Correct and incorrect methods of installing flared-tube connectors are shown in Figure 9- 30. Tubing nuts should be tightened with a torque wrench to the value specified in applicable technical manuals. The flareless-tube connector eliminates all tube flaring, yet provides a safe, strong, and dependable tube connection. This connector consists of a fitting, a sleeve or ferrule, and a nut ( Figure 9- 31 ). Flareless-tube connectors are available in many of the same shapes and threaded combinations as flared tube connectors. The fitting has a counterbore shoulder for the end of the tubing to rest against. The angle of the counterbore causes the cutting edge of the sleeve or ferrule to cut into the outside surface of the tube when the two are assembled.
Figure 9- 30 - Correct and Figure 9- 31 - Flareless-tube incorrect methods of installing connector.
The nut presses on the bevel of the sleeve and causes it to clamp tightly to the tube. Resistance to vibration is concentrated at this point rather than at the sleeve cut. When fully tightened, the sleeve or ferrule is bowed slightly at the midsection and acts as a spring. This action of the sleeve or ferrule maintains a constant tension between the body and the nut, thereby preventing the nut from loosening. Before the installation of a new flareless-tube connector, the end of the tubing must be square, concentric, and free from burrs. For the connection to be effective, the cutting edge of the sleeve or ferrule must bite into the external surface of the tube. When tube-type fittings are being tightened, observe the following: