
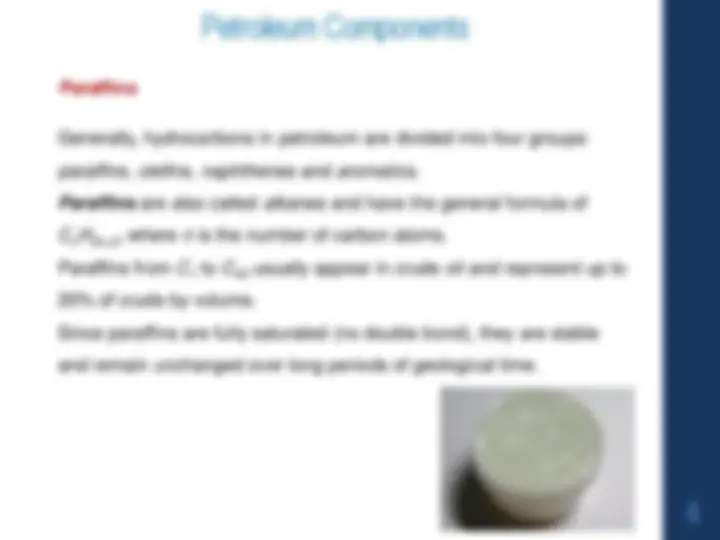
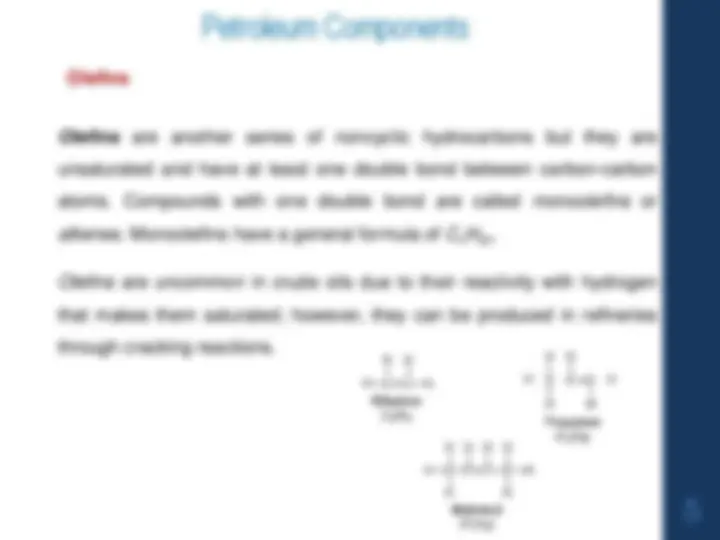
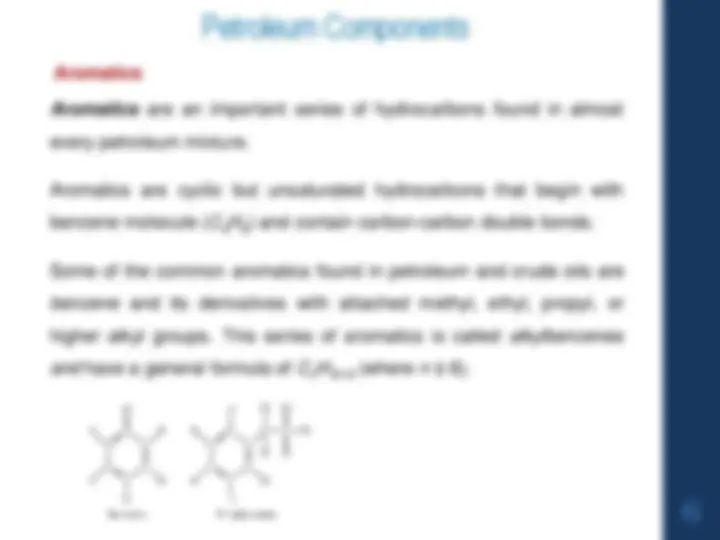
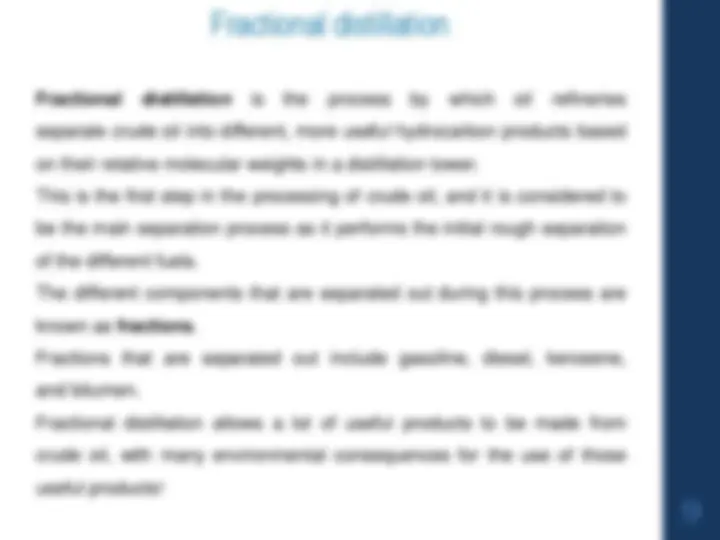
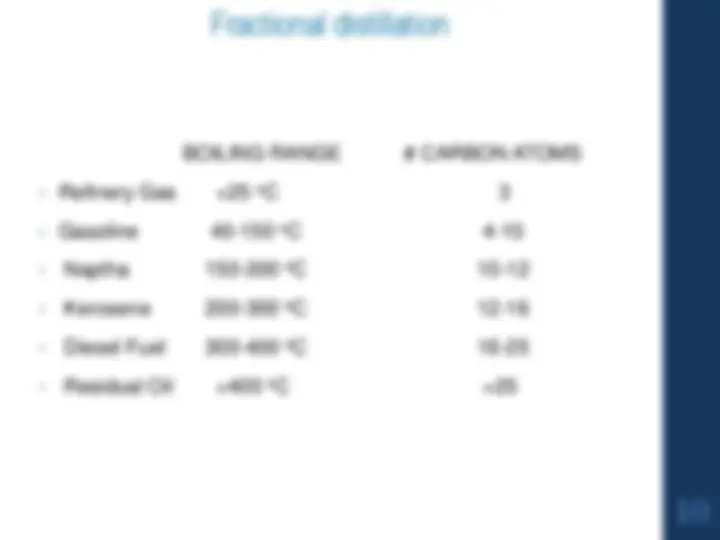
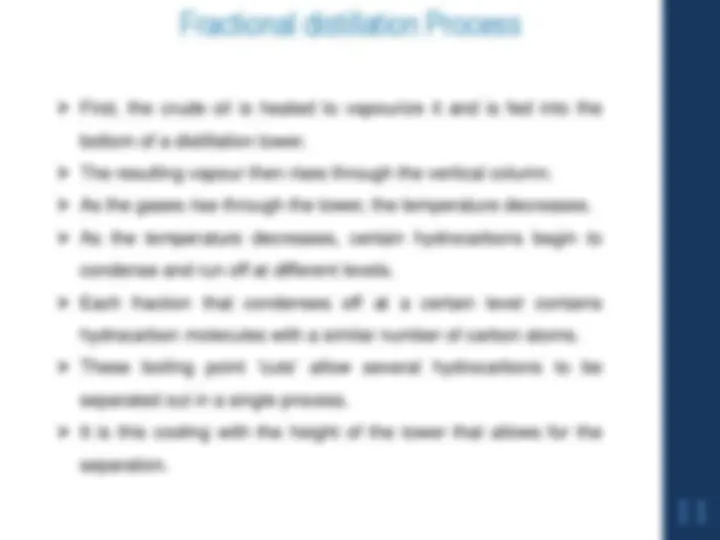
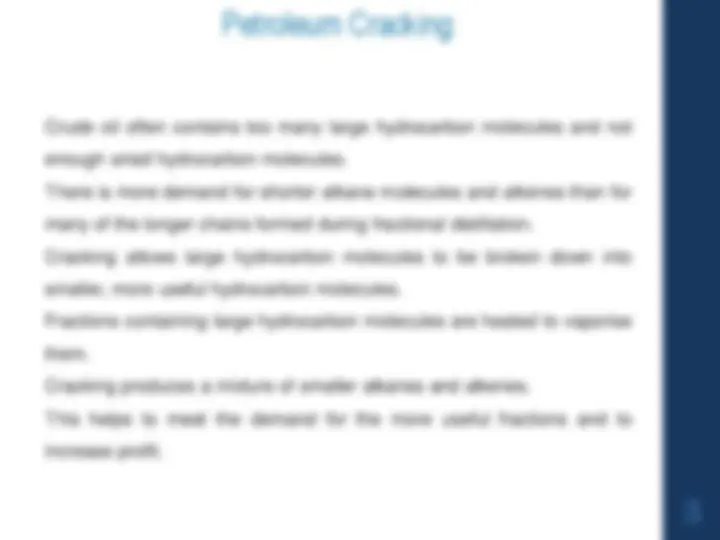
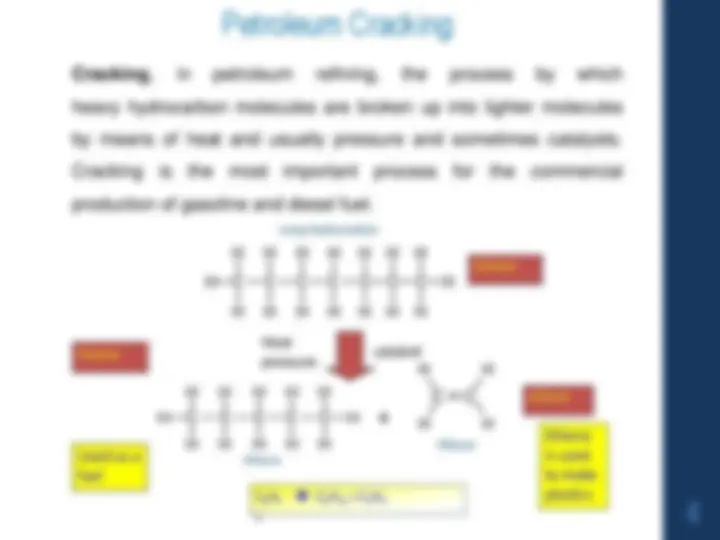
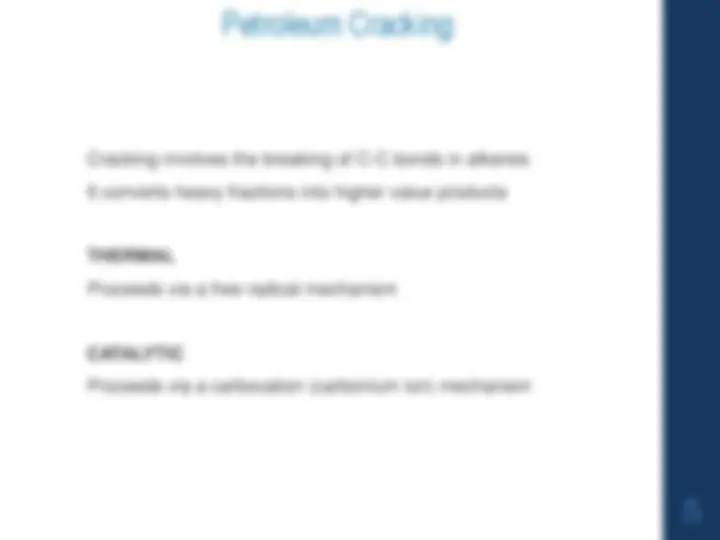
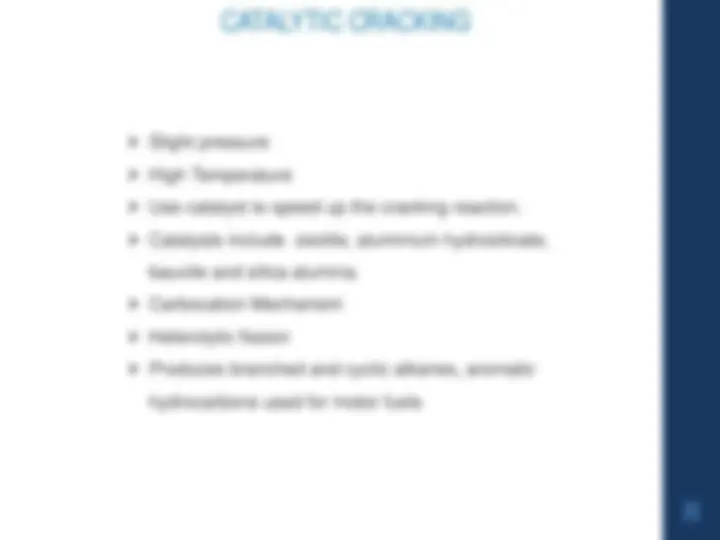
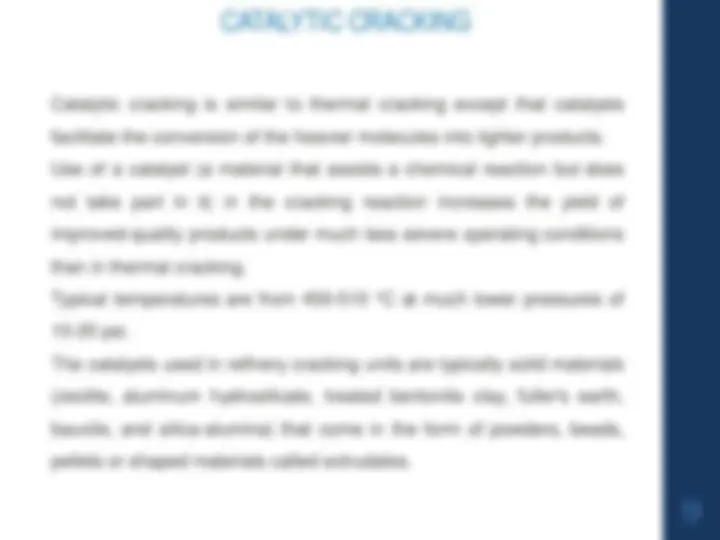
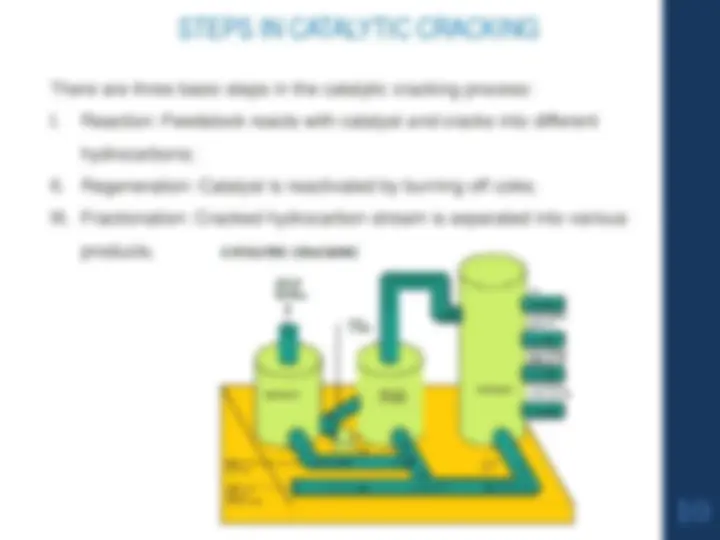
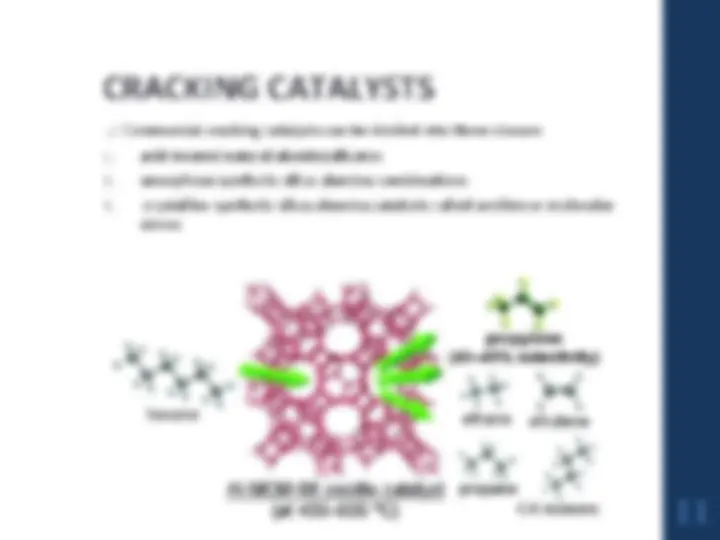
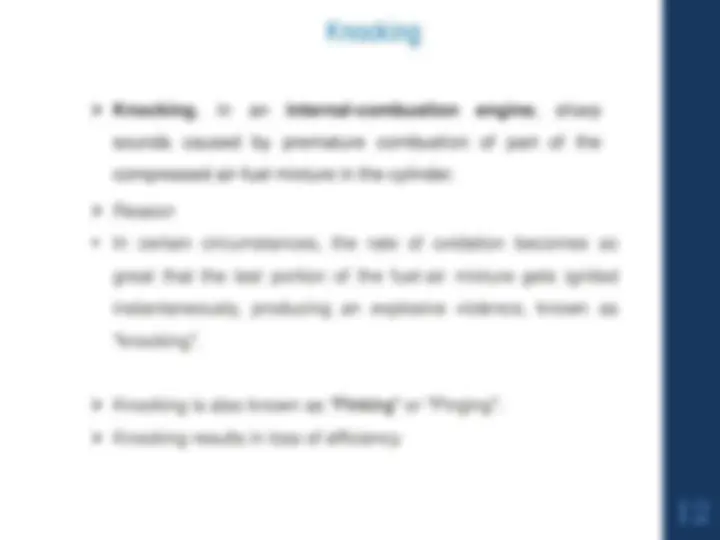
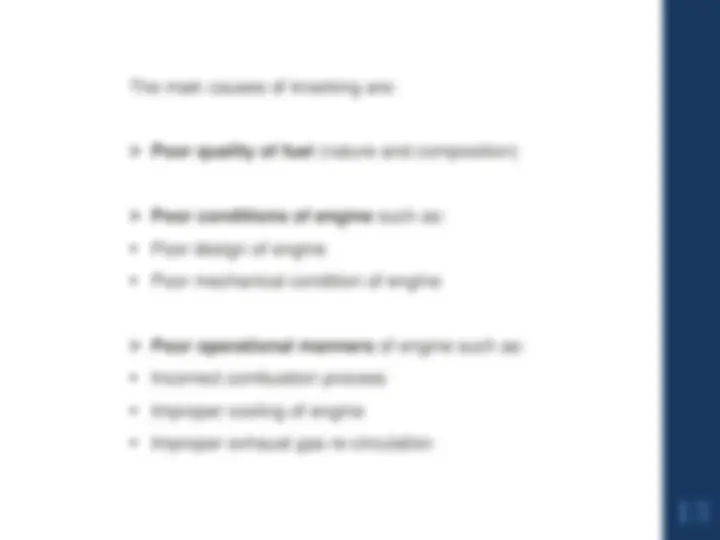
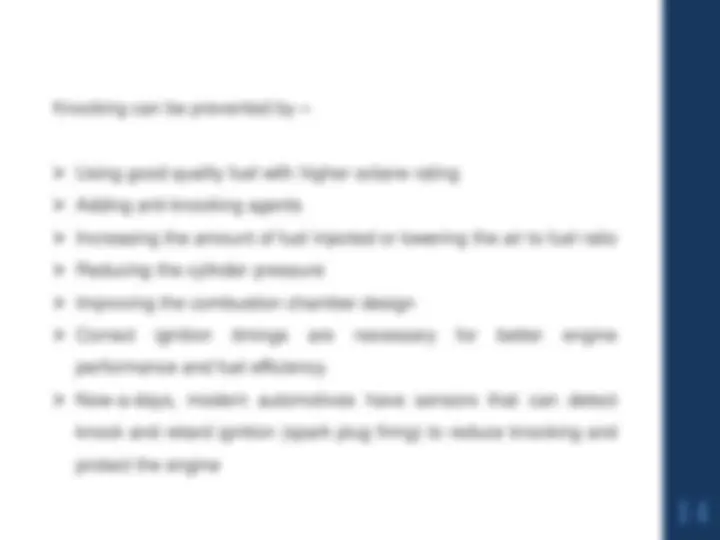

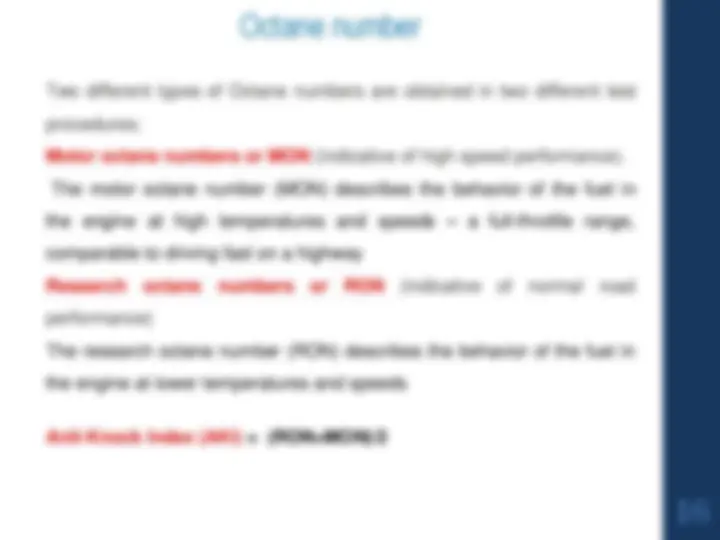
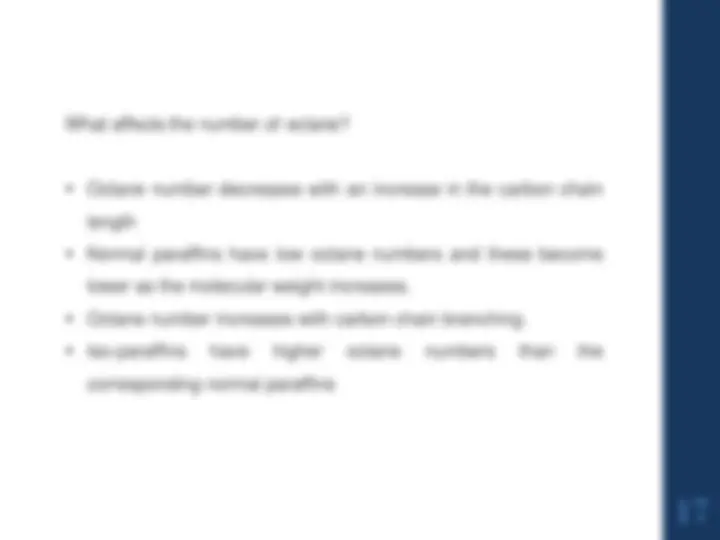
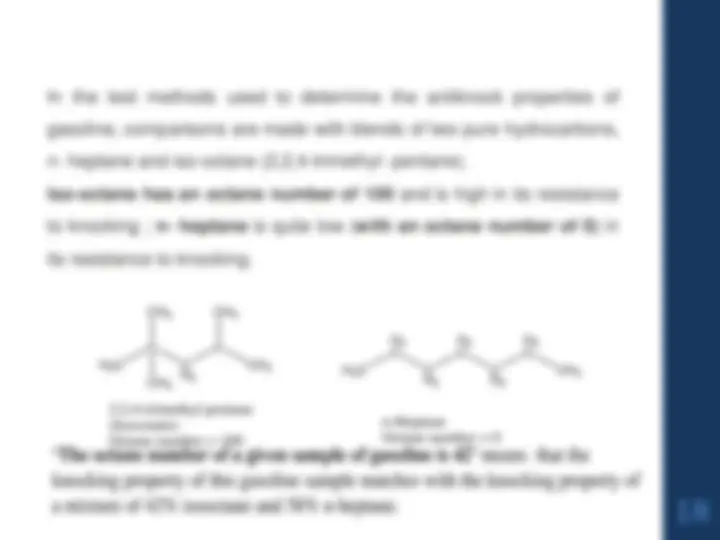
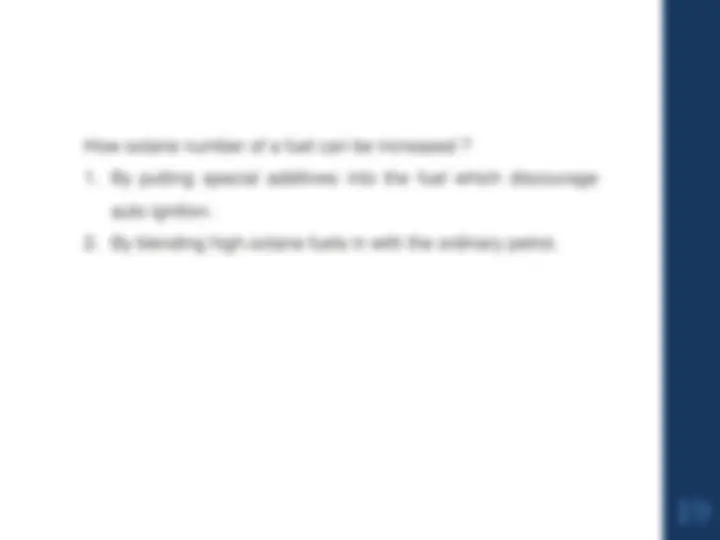
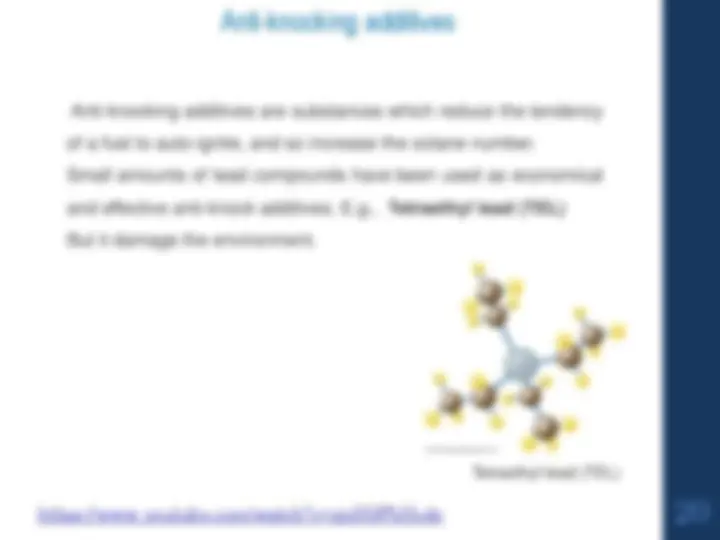
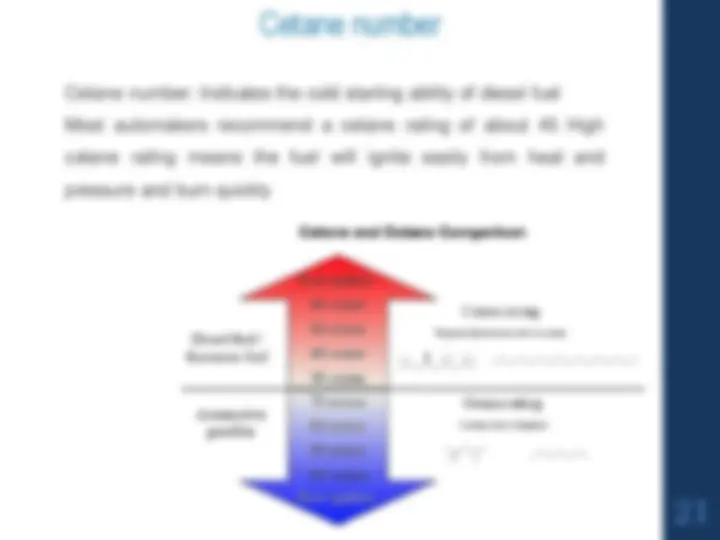
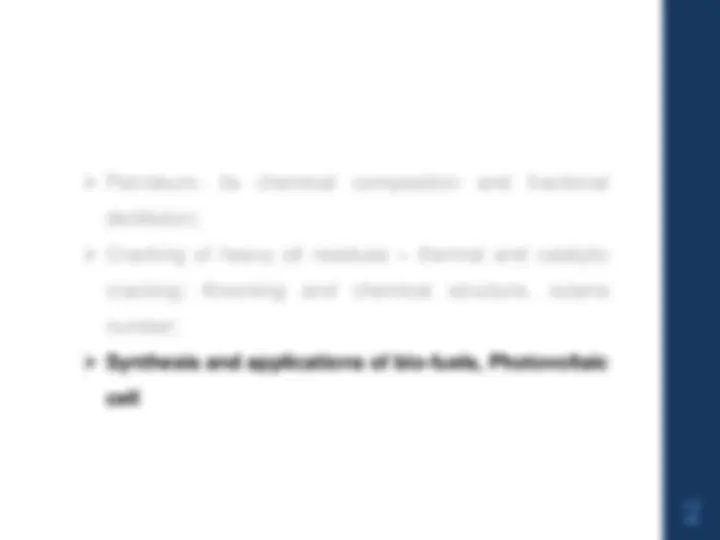
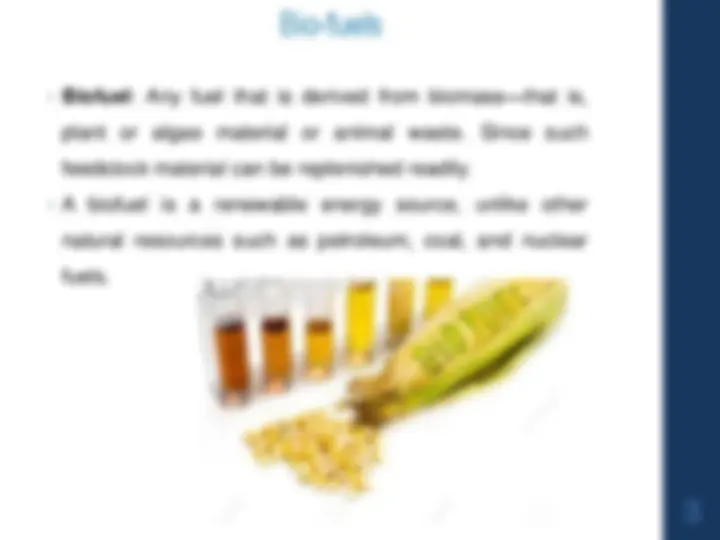
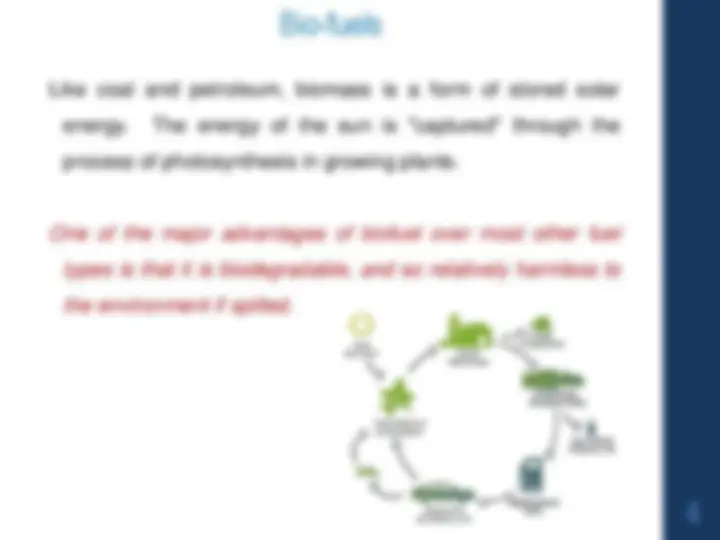
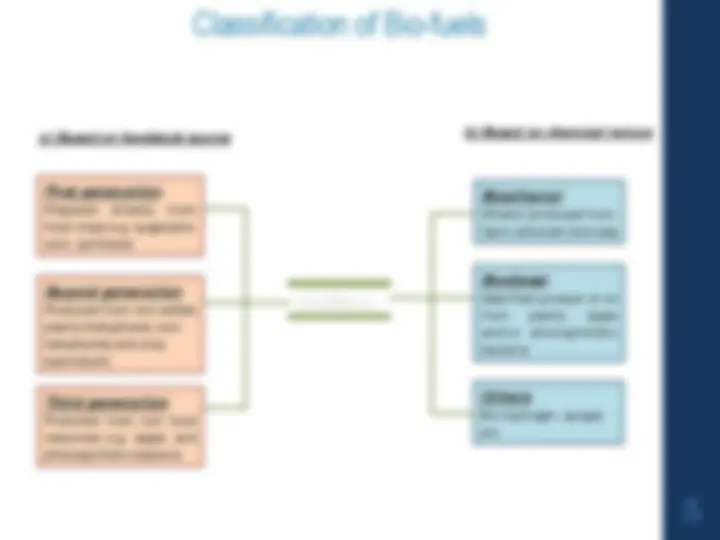
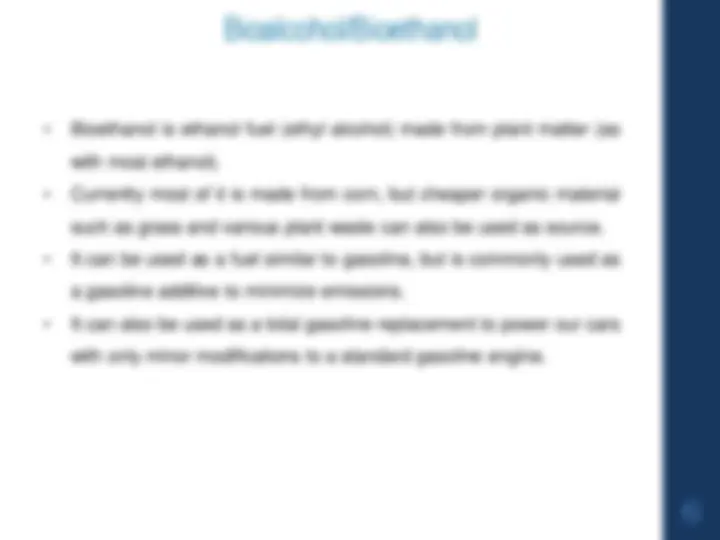
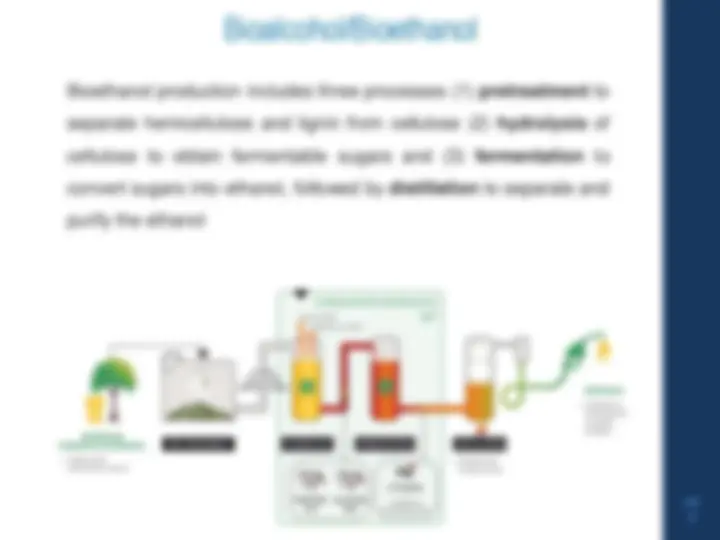
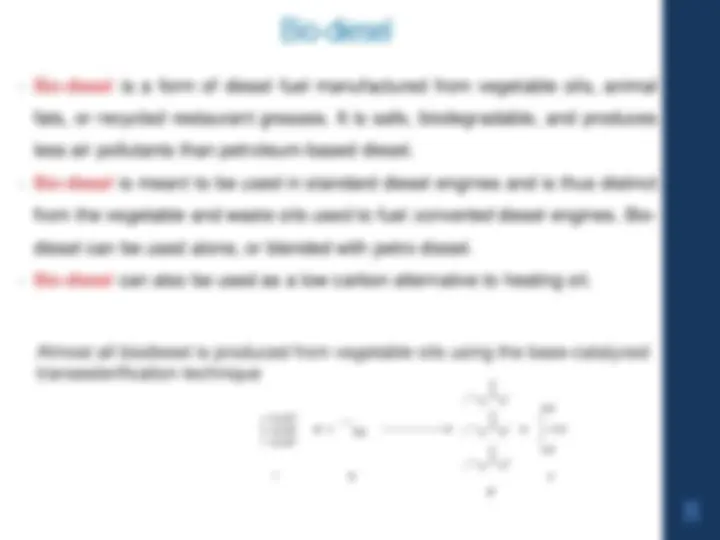
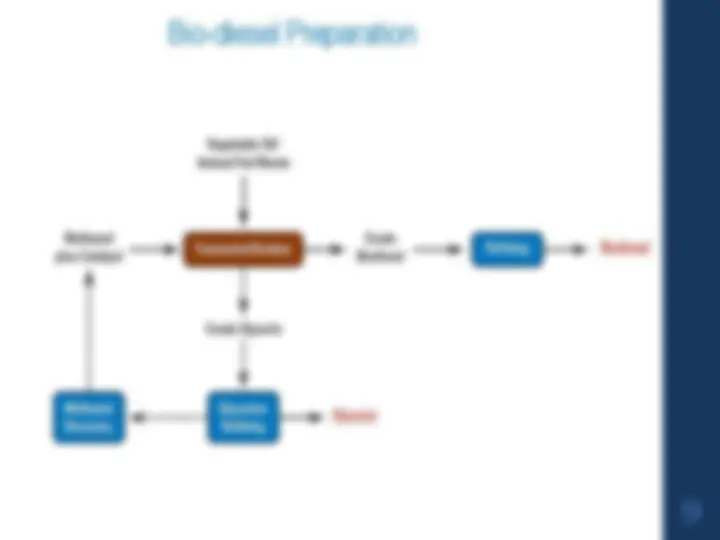
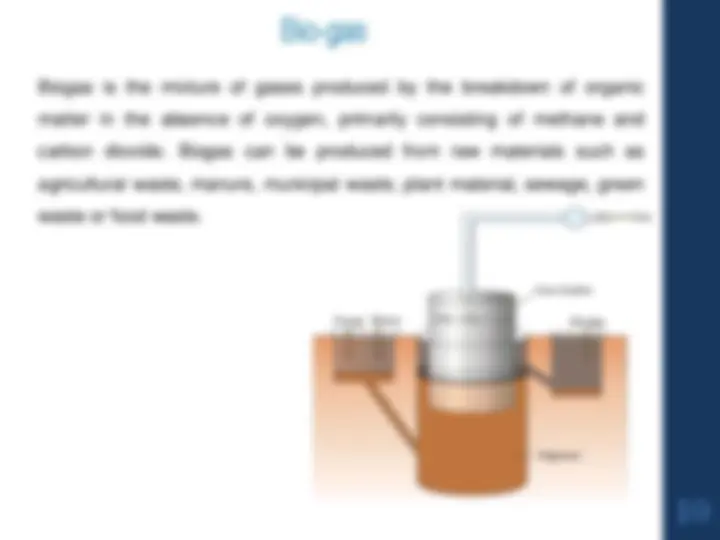
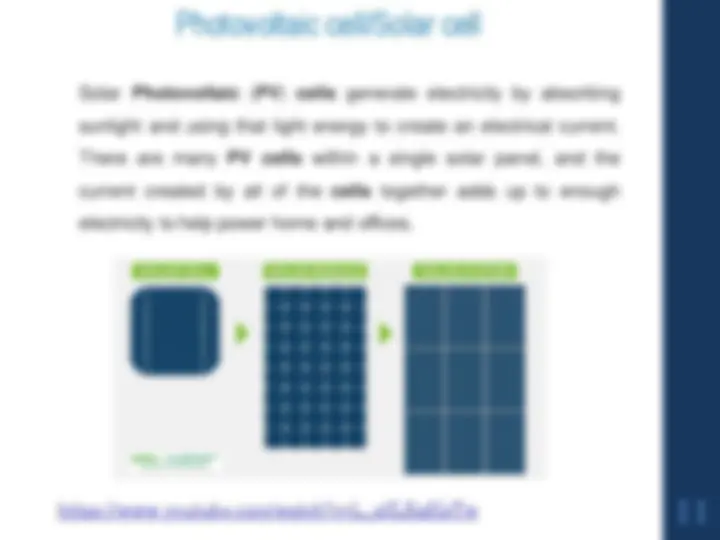
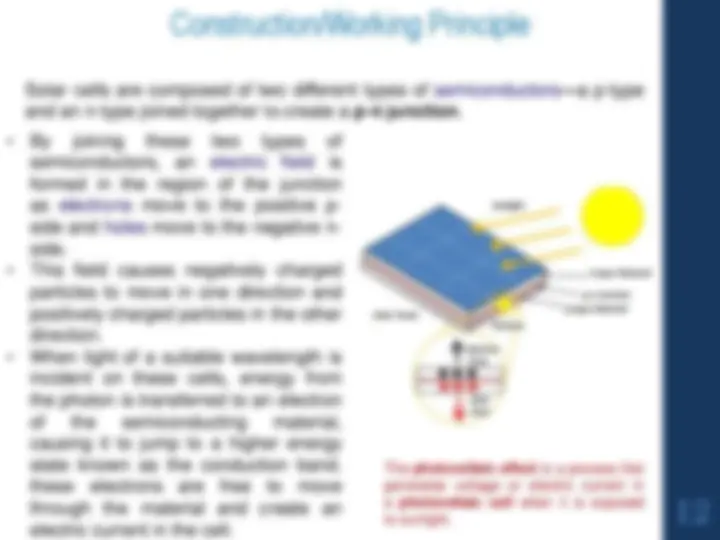
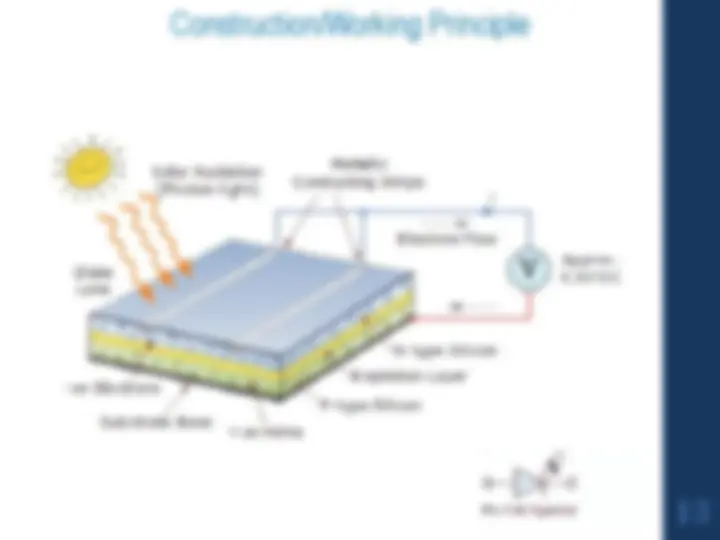
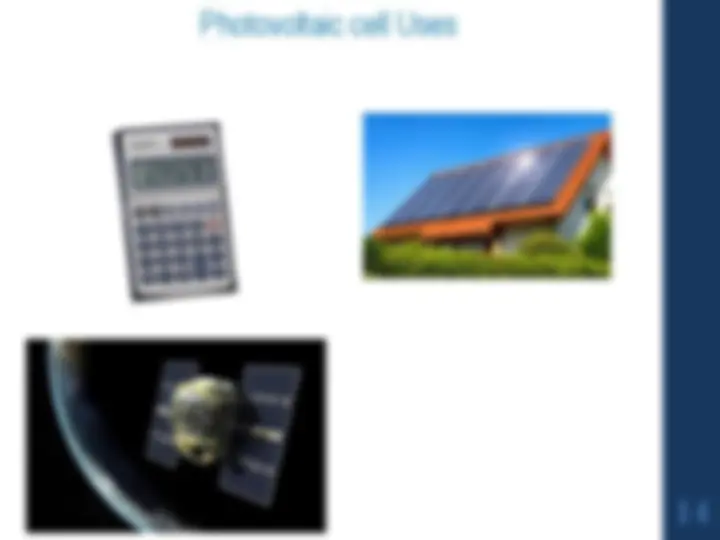
Study with the several resources on Docsity
Earn points by helping other students or get them with a premium plan
Prepare for your exams
Study with the several resources on Docsity
Earn points to download
Earn points by helping other students or get them with a premium plan
Community
Ask the community for help and clear up your study doubts
Discover the best universities in your country according to Docsity users
Free resources
Download our free guides on studying techniques, anxiety management strategies, and thesis advice from Docsity tutors
A comprehensive overview of petroleum, its chemical composition, and the process of fractional distillation. It also delves into the cracking of heavy oil residues, the concept of octane number, and the synthesis and applications of biofuels. The various components of petroleum, including paraffins, olefins, aromatics, and naphthenes, and discusses the role of sulfur in petroleum. It further explores the process of fractional distillation, the importance of boiling point 'cuts', and the environmental consequences of using useful products derived from crude oil. The document also covers the concept of cracking, thermal and catalytic cracking, and the role of catalysts. It discusses the causes and prevention of knocking in engines, the importance of octane number, and the factors affecting it. Lastly, the document introduces biofuels, including bioalcohol/bioethanol, bio-diesel, and biogas, and their production methods.
Typology: Study notes
1 / 44
This page cannot be seen from the preview
Don't miss anything!
Petroleum is a naturally occurring complex mixture made up predominantly of organic carbon and hydrogen compounds. It contains significant amounts of nitrogen, sulfur and oxygen together with smaller quantities of nickel, vanadium and other elements. It occurs in the sedimentary rocks in the form of gases (natural gas), liquids (crude oil), semisolids (bitumen), or solids (wax or asphaltite). An underground reservoir that contains hydrocarbons is called petroleum reservoir and its hydrocarbon contents that can be recovered through a producing well is called reservoir fluid.
Olefins are another series of noncyclic hydrocarbons but they are unsaturated and have at least one double bond between carbon-carbon atoms. Compounds with one double bond are called monoolefins or alkenes. Monoolefins have a general formula of CnH 2 n. Olefins are uncommon in crude oils due to their reactivity with hydrogen that makes them saturated; however, they can be produced in refineries through cracking reactions.
Olefins
Aromatics are an important series of hydrocarbons found in almost every petroleum mixture. Aromatics are cyclic but unsaturated hydrocarbons that begin with benzene molecule ( C 6 H 6 ) and contain carbon-carbon double bonds. Some of the common aromatics found in petroleum and crude oils are benzene and its derivatives with attached methyl, ethyl, propyl, or higher alkyl groups. This series of aromatics is called alkylbenzenes and have a general formula of CnH 2 n- 6 (where n ≥ 6 ).
Aromatics
Sulfur is the most important heteroatom in petroleum and it can be found in cyclic as well as noncyclic compounds such as mercaptanes ( R-S-H ) and sulfides ( R-S-R’ ), where R and R’ are alkyl groups. Sulfur in natural gas is usually found in the form of hydrogen sulfide ( H 2 S ). Some natural gas contain H 2 S as high as 30 % by volume. The amount of sulfur in a crude may vary from 0. 05 to 6 % by weight.
Sulfur
Fractional distillation is the process by which oil refineries separate crude oil into different, more useful hydrocarbon products based on their relative molecular weights in a distillation tower. This is the first step in the processing of crude oil, and it is considered to be the main separation process as it performs the initial rough separation of the different fuels. The different components that are separated out during this process are known as fractions. Fractions that are separated out include gasoline, diesel, kerosene, and bitumen. Fractional distillation allows a lot of useful products to be made from crude oil, with many environmental consequences for the use of those useful products!
First, the crude oil is heated to vapourize it and is fed into the bottom of a distillation tower. The resulting vapour then rises through the vertical column. As the gases rise through the tower, the temperature decreases. As the temperature decreases, certain hydrocarbons begin to condense and run off at different levels. Each fraction that condenses off at a certain level contains hydrocarbon molecules with a similar number of carbon atoms. These boiling point 'cuts' allow several hydrocarbons to be separated out in a single process. It is this cooling with the height of the tower that allows for the separation.
Crude oil often contains too many large hydrocarbon molecules and not enough small hydrocarbon molecules. There is more demand for shorter alkane molecules and alkenes than for many of the longer chains formed during fractional distillation. Cracking allows large hydrocarbon molecules to be broken down into smaller, more useful hydrocarbon molecules. Fractions containing large hydrocarbon molecules are heated to vaporise them. Cracking produces a mixture of smaller alkanes and alkenes. This helps to meet the demand for the more useful fractions and to increase profit.
Cracking , in petroleum refining, the process by which heavy hydrocarbon molecules are broken up into lighter molecules by means of heat and usually pressure and sometimes catalysts. Cracking is the most important process for the commercial production of gasoline and diesel fuel.
High Pressure ... 7000 kPa High Temperature ... 400°C to 900 °C Free Radical Mechanism Homolytic fission Produces mostly alkenes ...e.g. ethene for making polymers and ethanol Produces Hydrogen ... used in margarine manufacture Bonds can be broken anywhere in the molecule by C-C bond fission or C-H bond fission THERMAL CRACKING
THERMAL CRACKING
Catalytic cracking is similar to thermal cracking except that catalysts facilitate the conversion of the heavier molecules into lighter products. Use of a catalyst (a material that assists a chemical reaction but does not take part in it) in the cracking reaction increases the yield of improved-quality products under much less severe operating conditions than in thermal cracking. Typical temperatures are from 450 - 510 °C at much lower pressures of 10 - 20 psi. The catalysts used in refinery cracking units are typically solid materials (zeolite, aluminum hydrosilicate, treated bentonite clay, fuller's earth, bauxite, and silica-alumina) that come in the form of powders, beads, pellets or shaped materials called extrudates. CATALYTIC CRACKING
There are three basic steps in the catalytic cracking process: I. Reaction: Feedstock reacts with catalyst and cracks into different hydrocarbons; II. Regeneration: Catalyst is reactivated by burning off coke; III. Fractionation: Cracked hydrocarbon stream is separated into various products. STEPS IN CATALYTIC CRACKING