
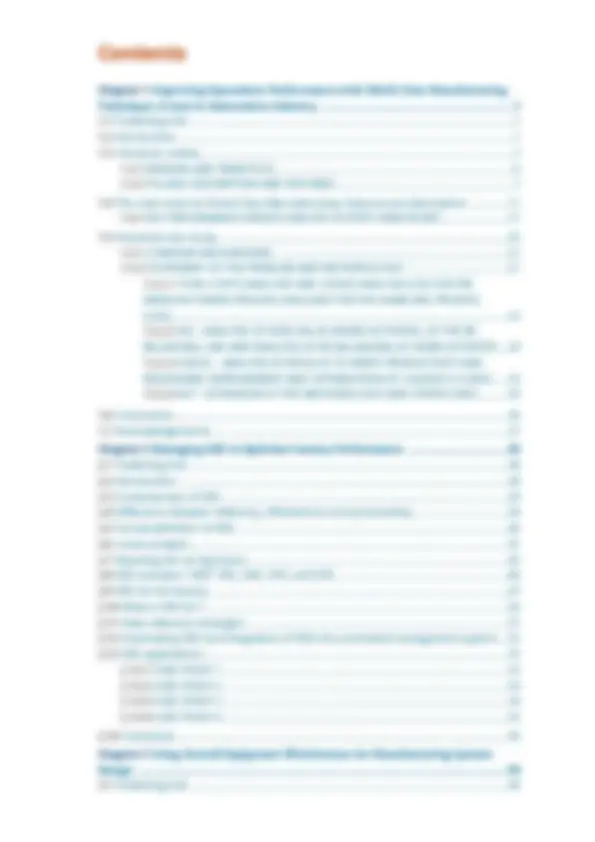
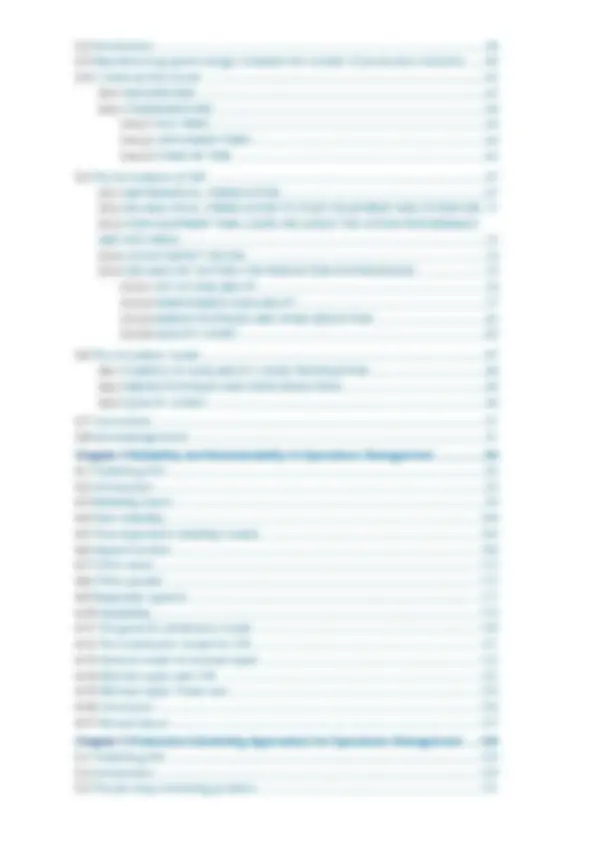
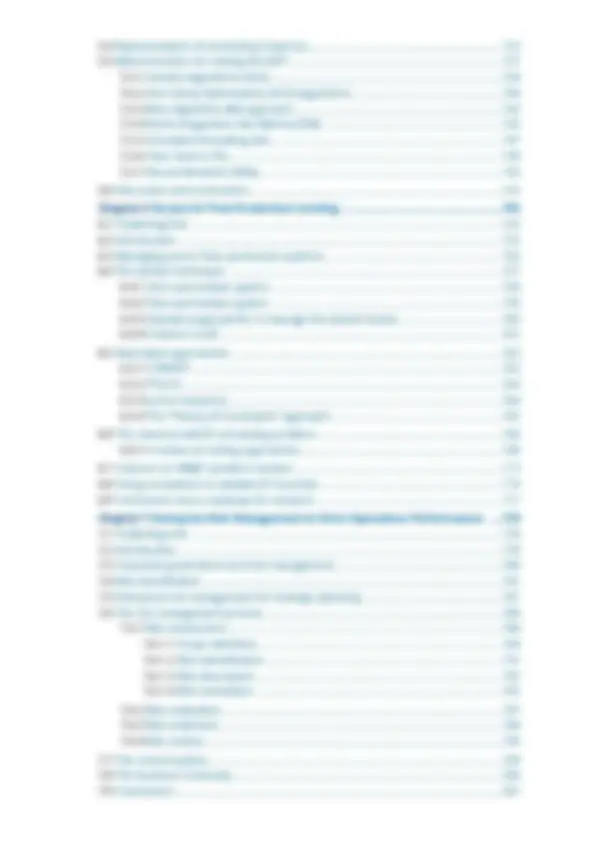
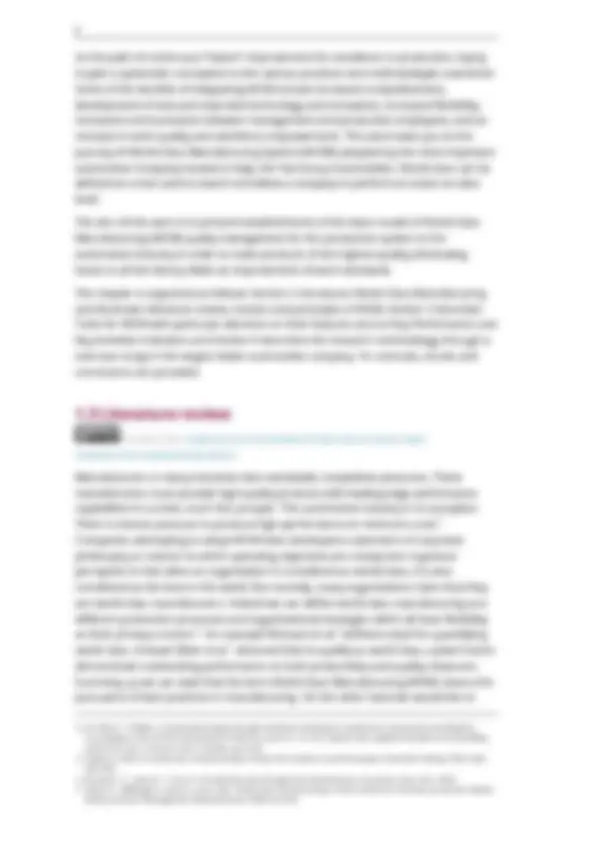
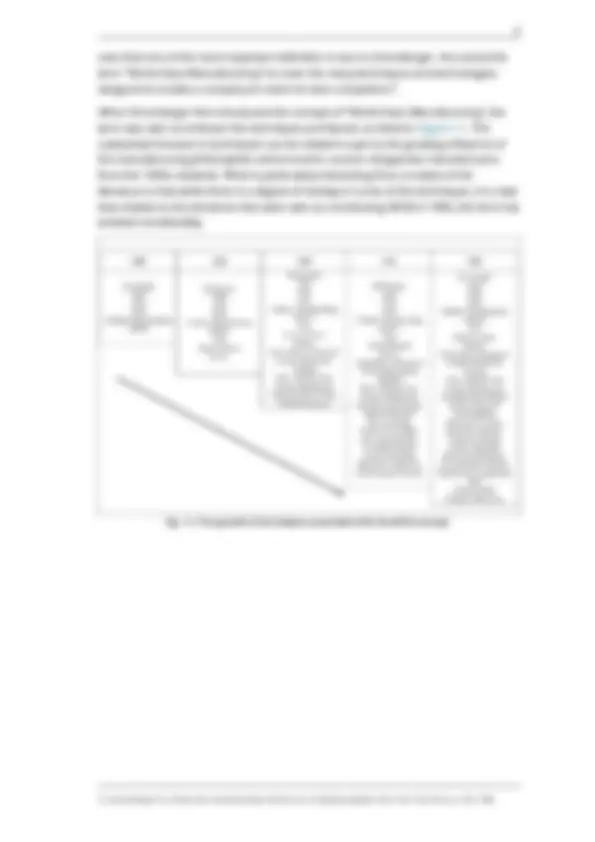
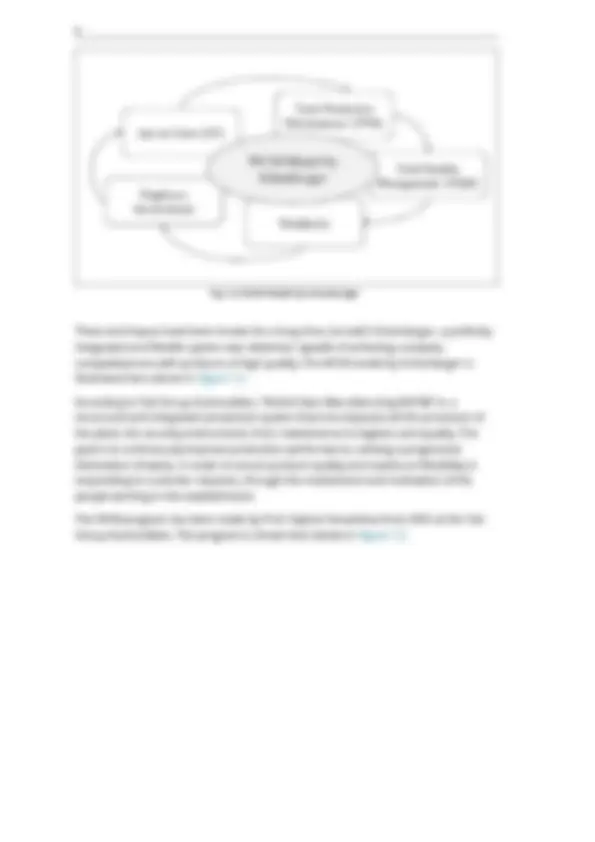
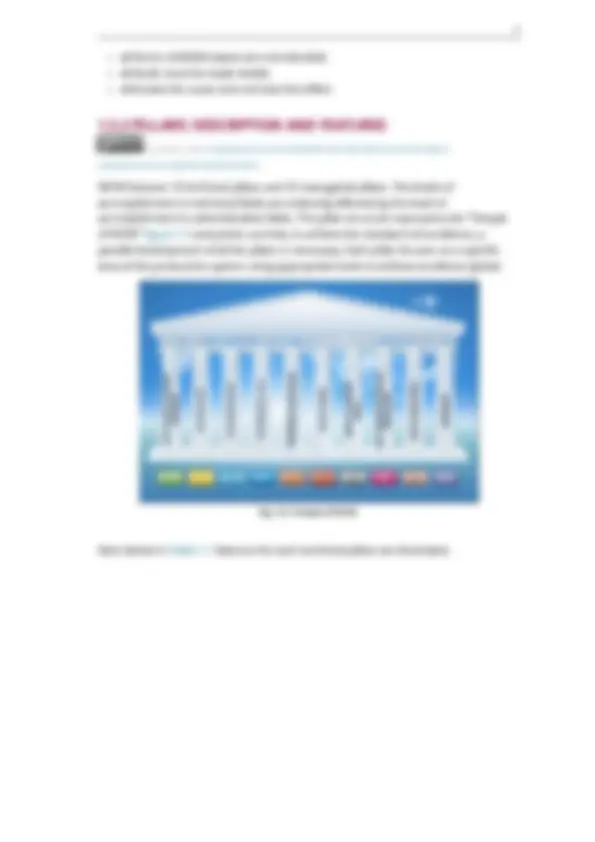
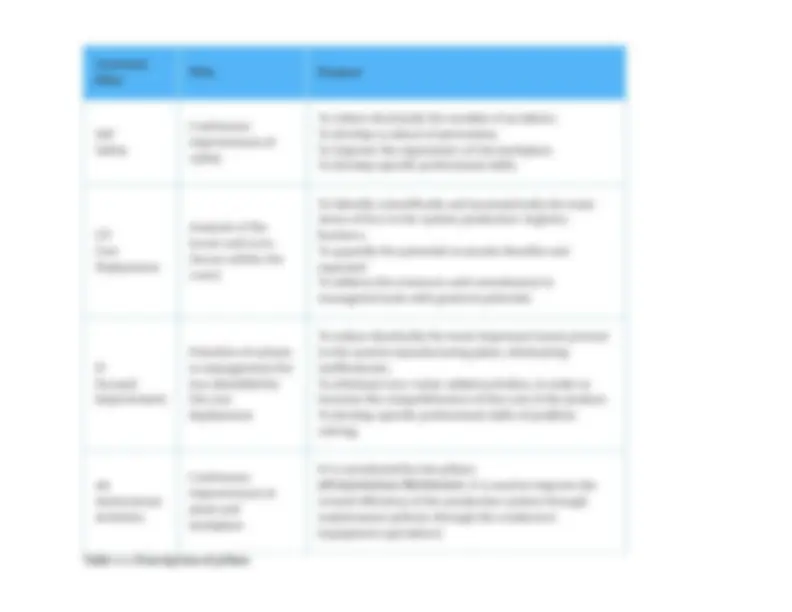
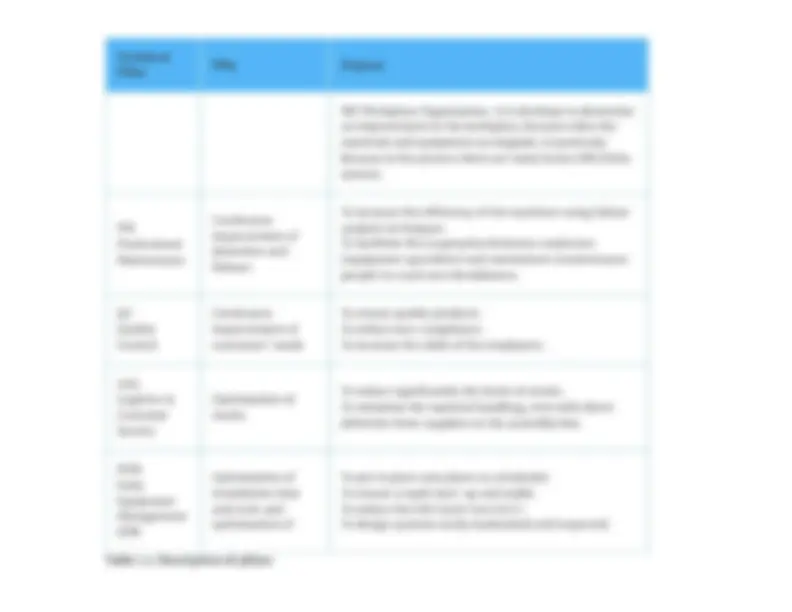
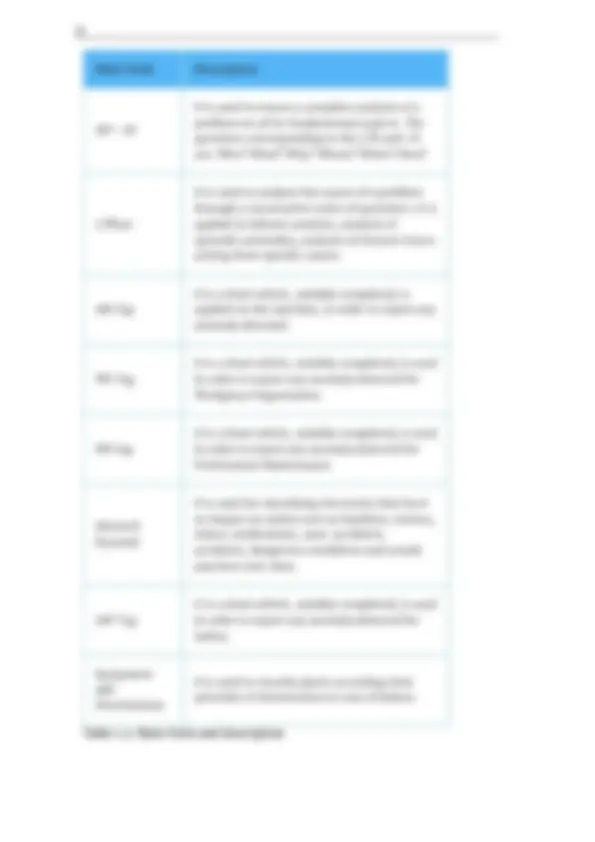
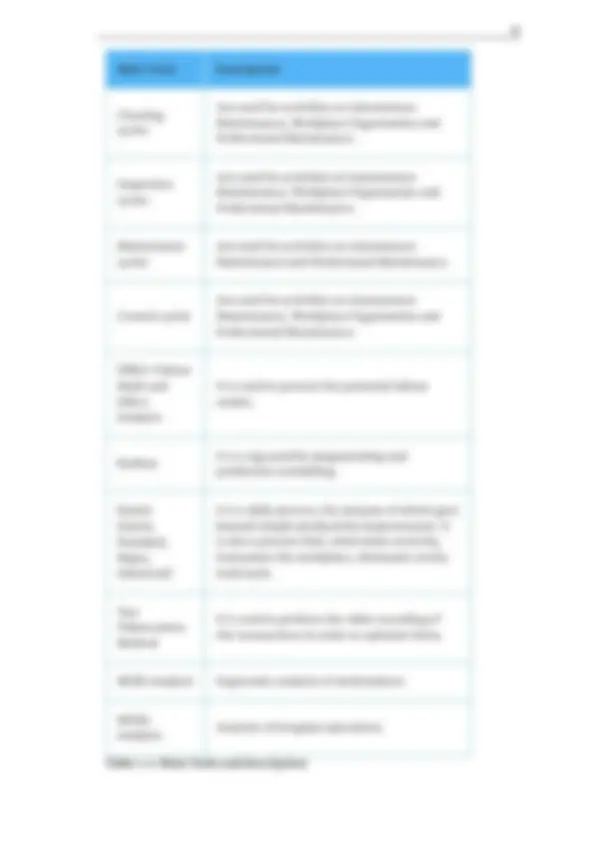
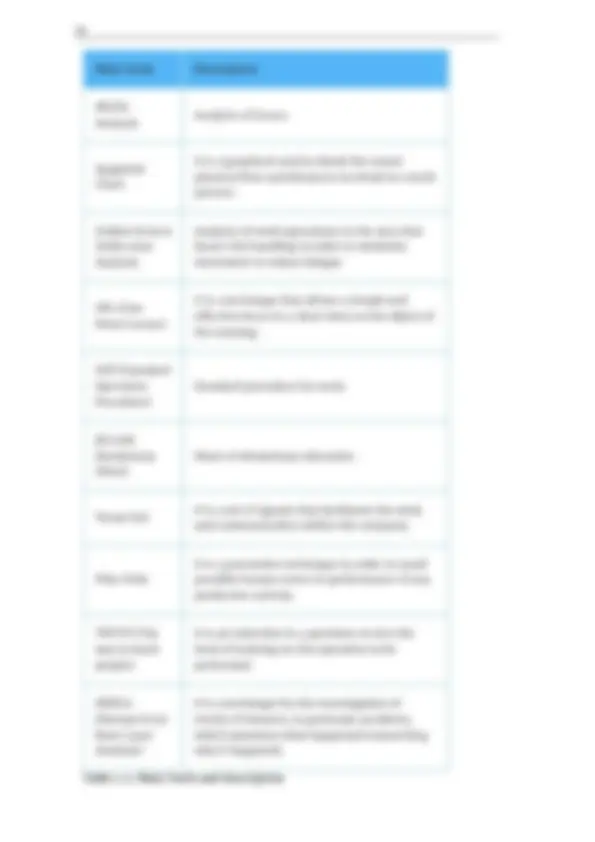
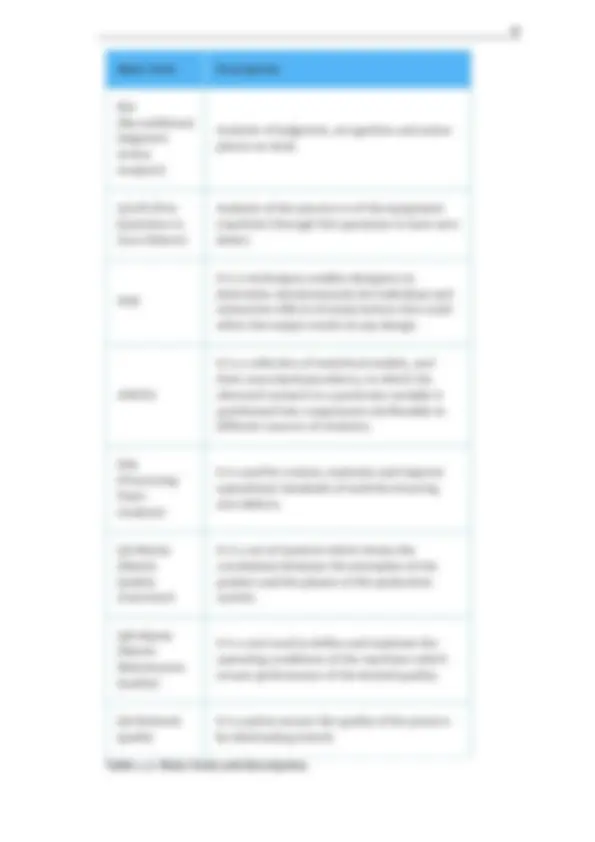
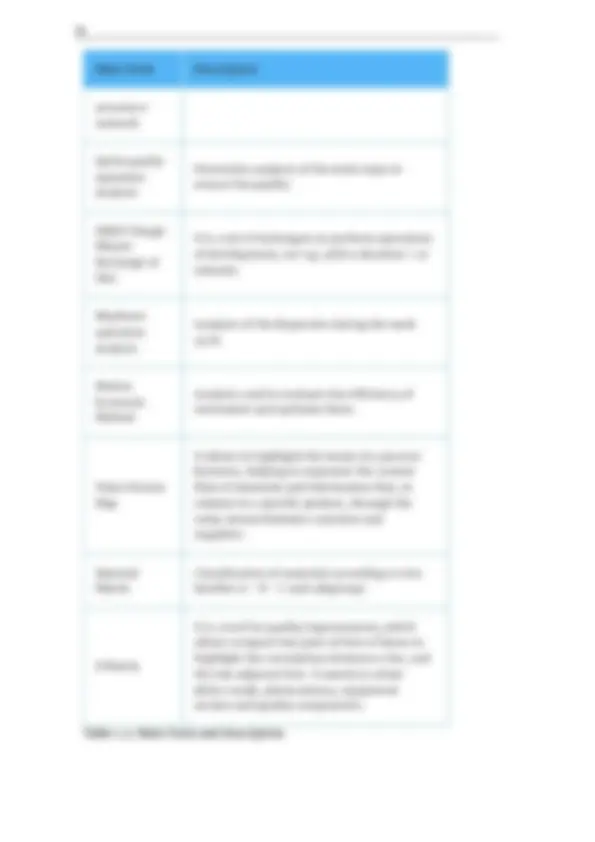
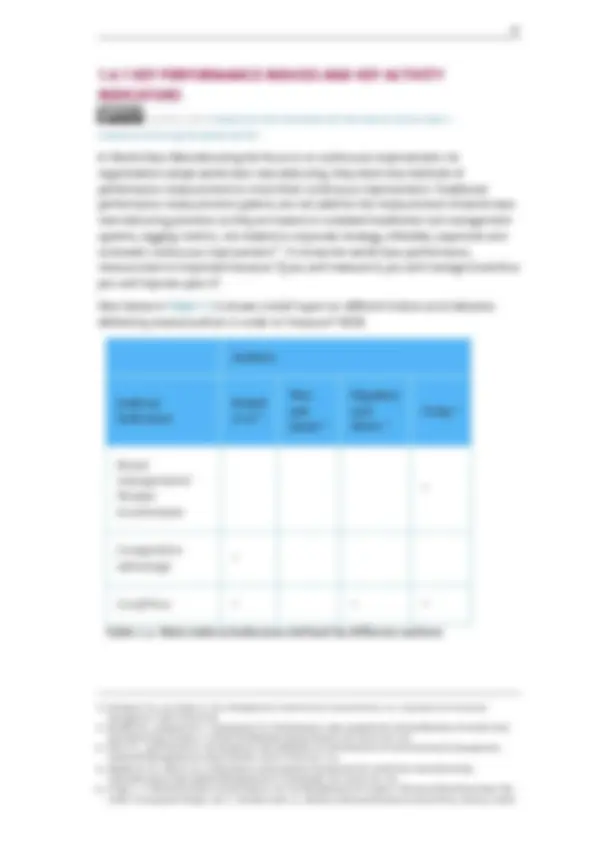
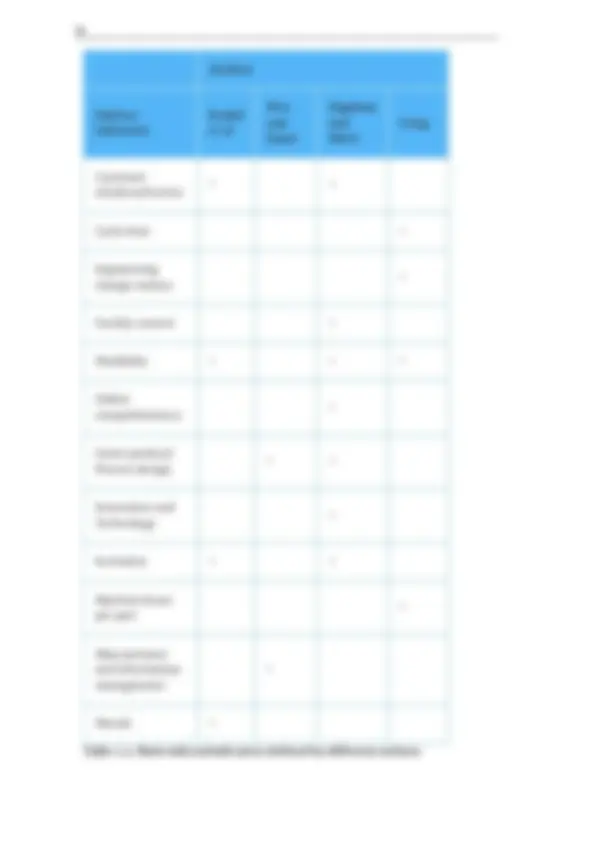
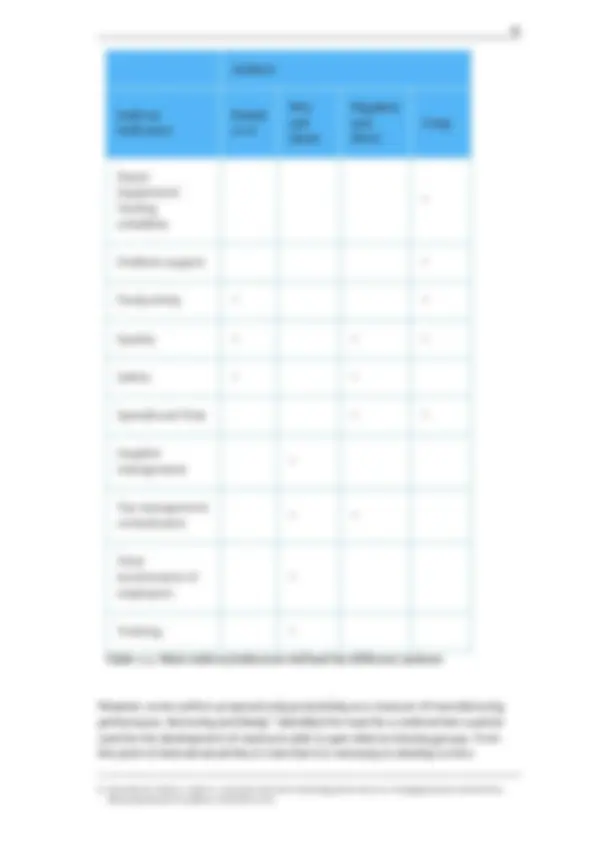
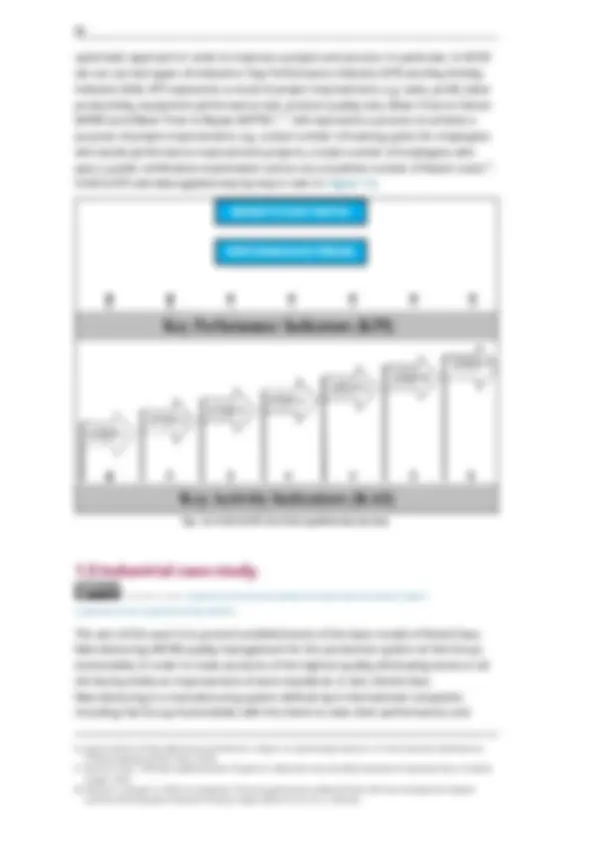
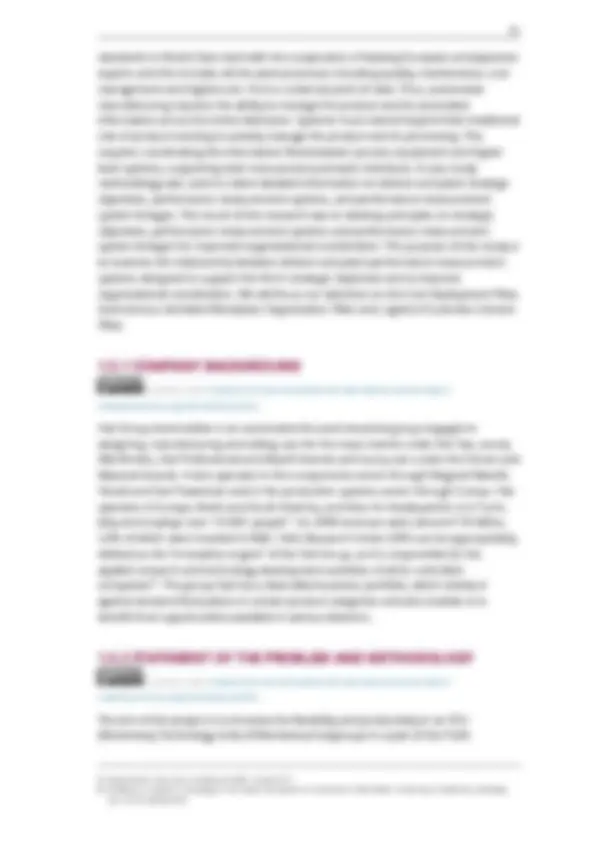
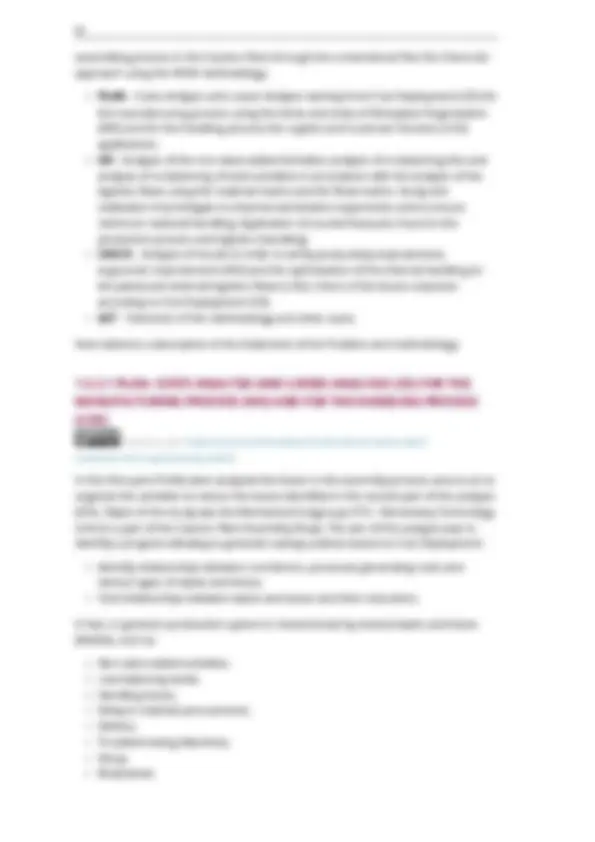
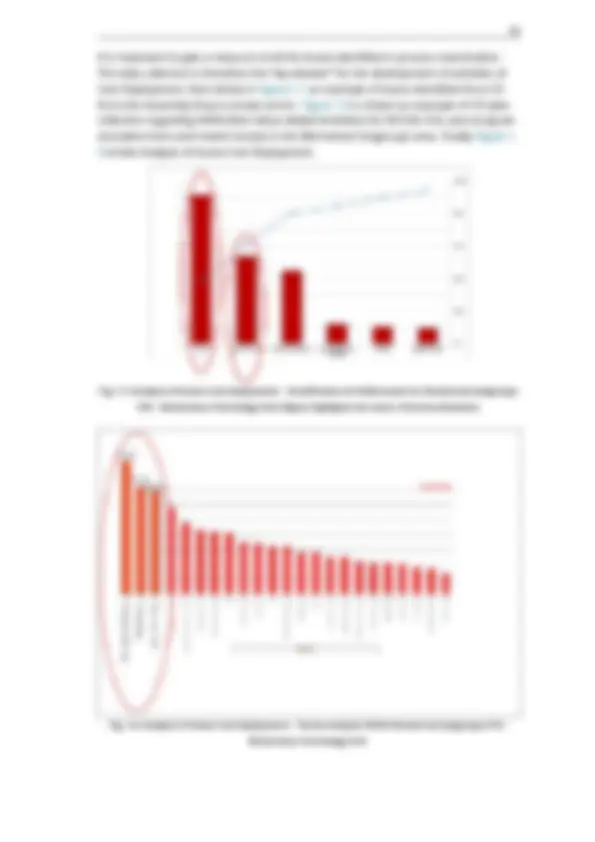
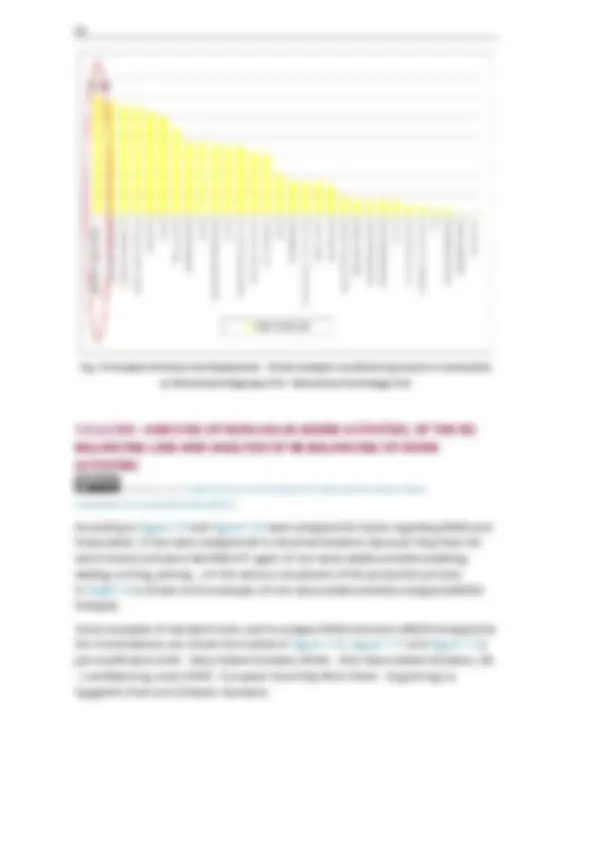
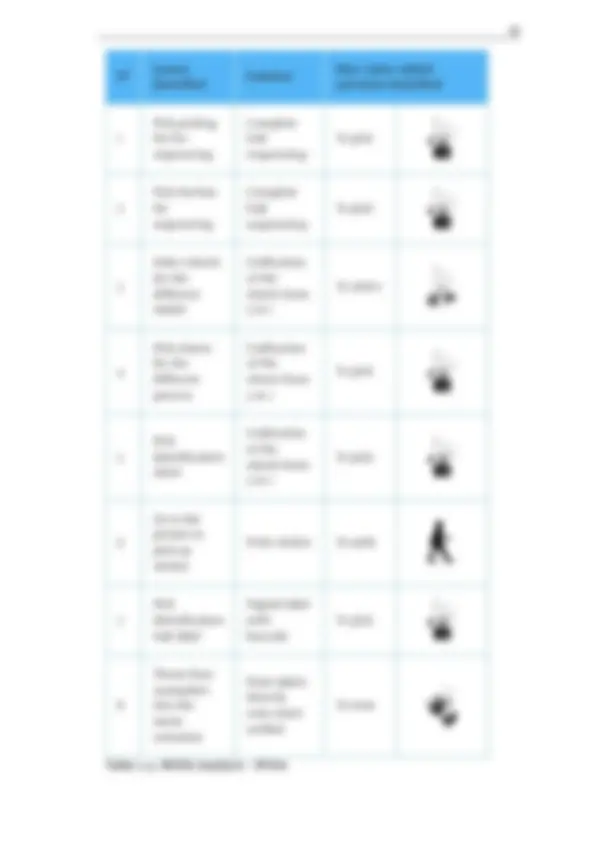
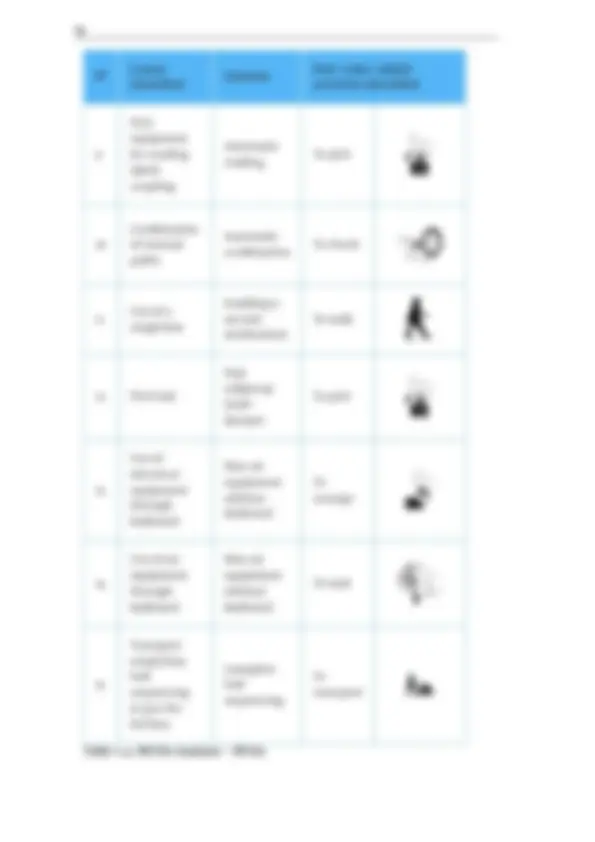
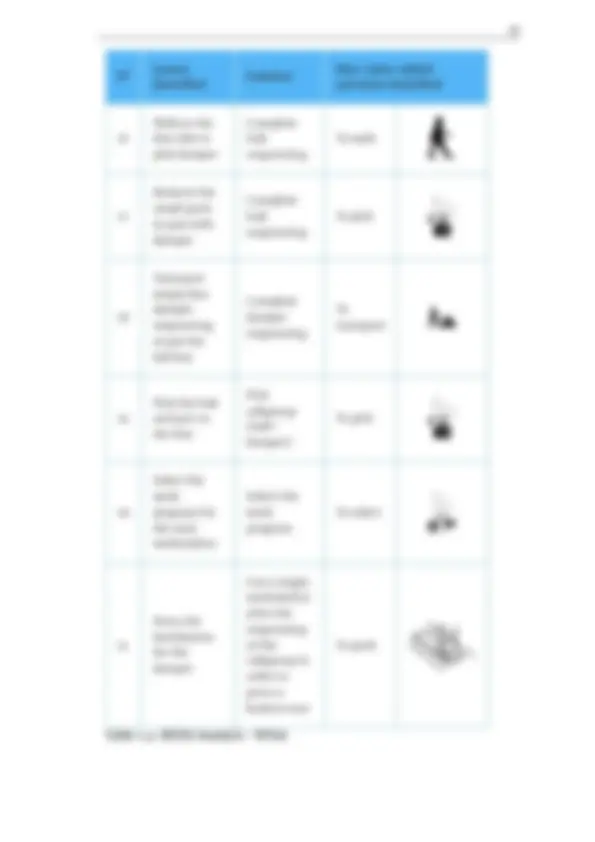
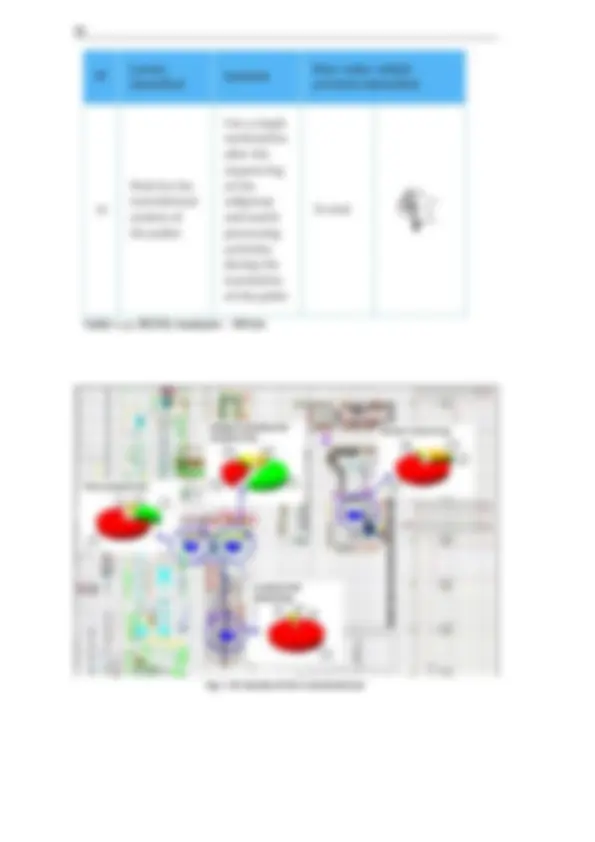
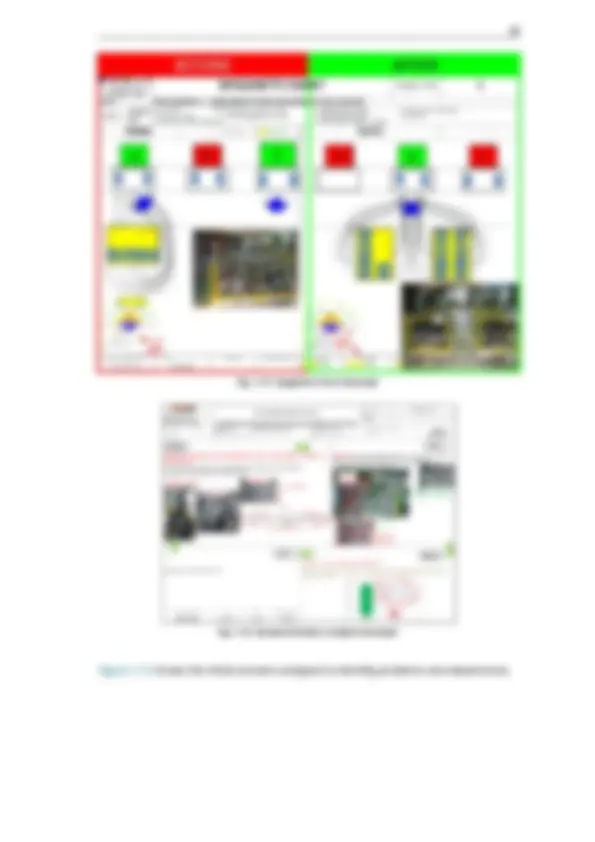
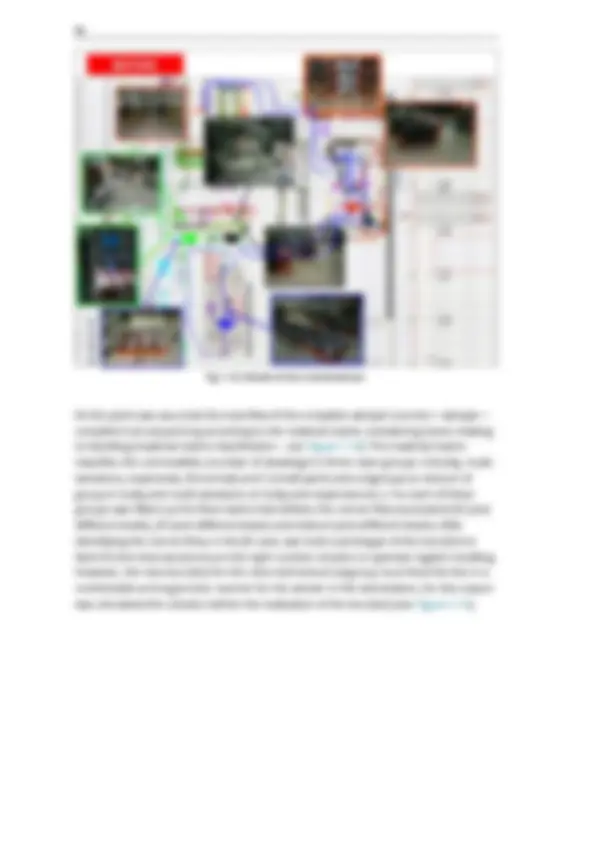
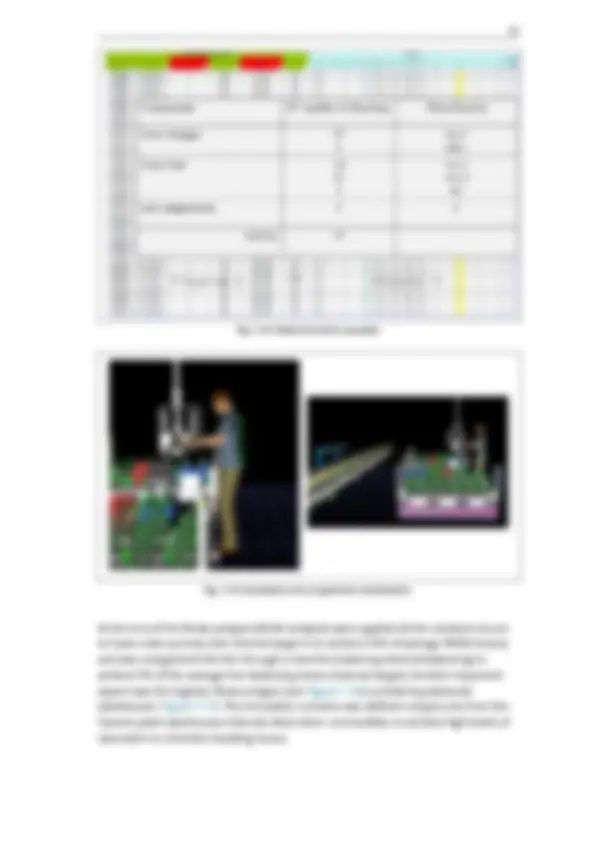
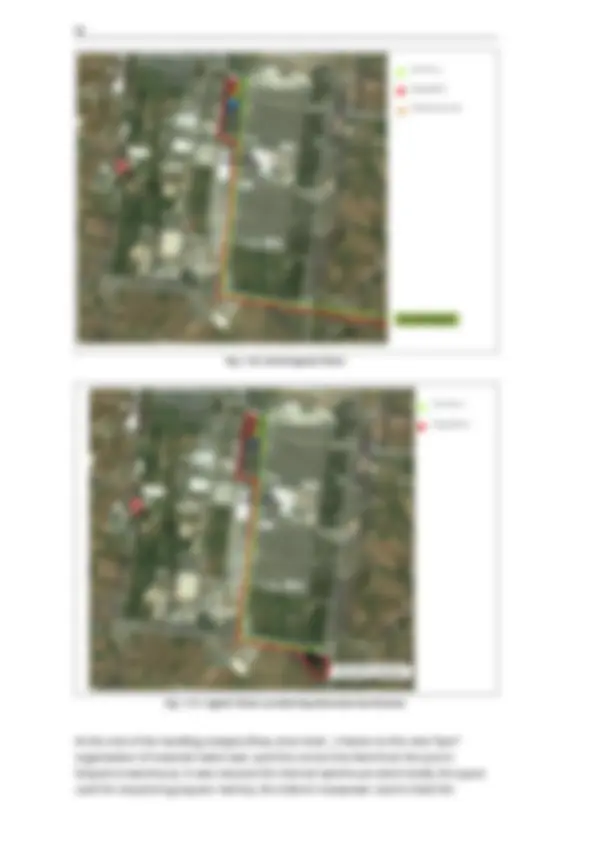
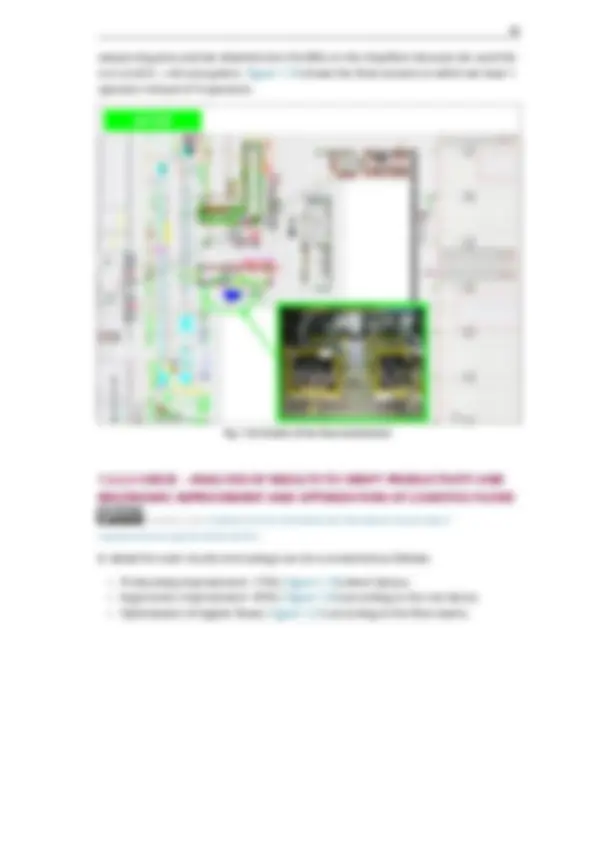
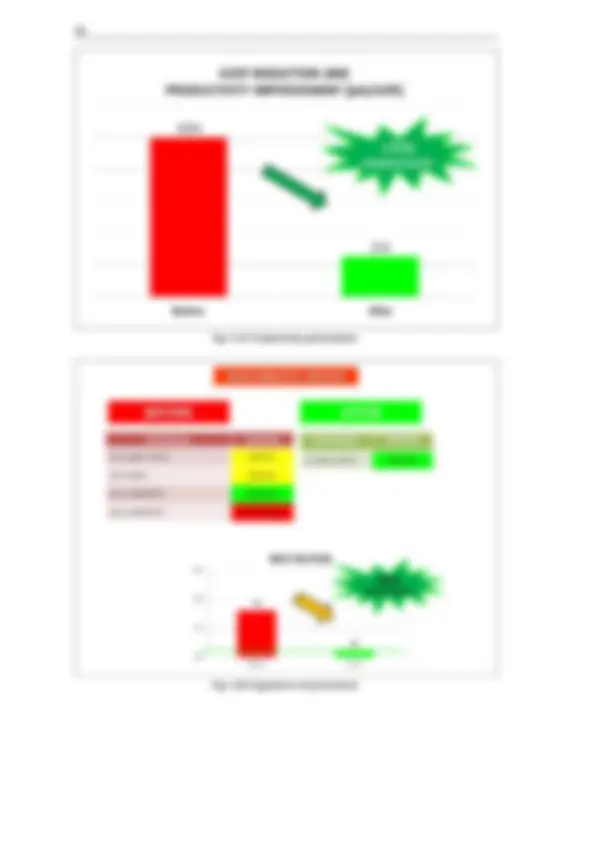
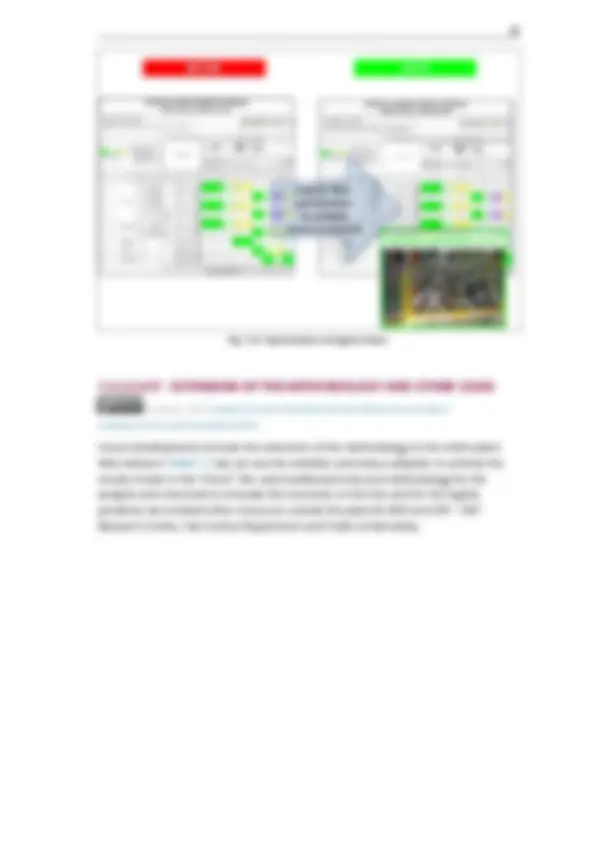
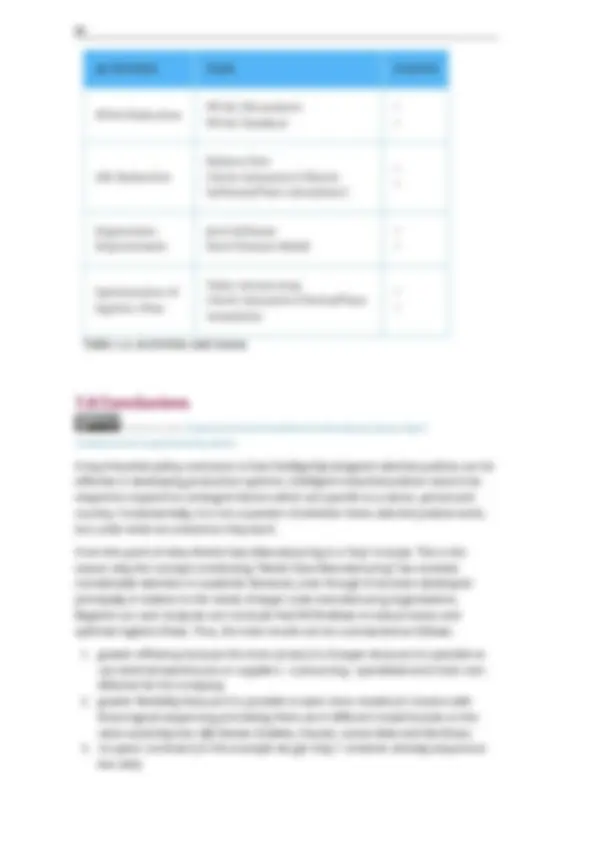
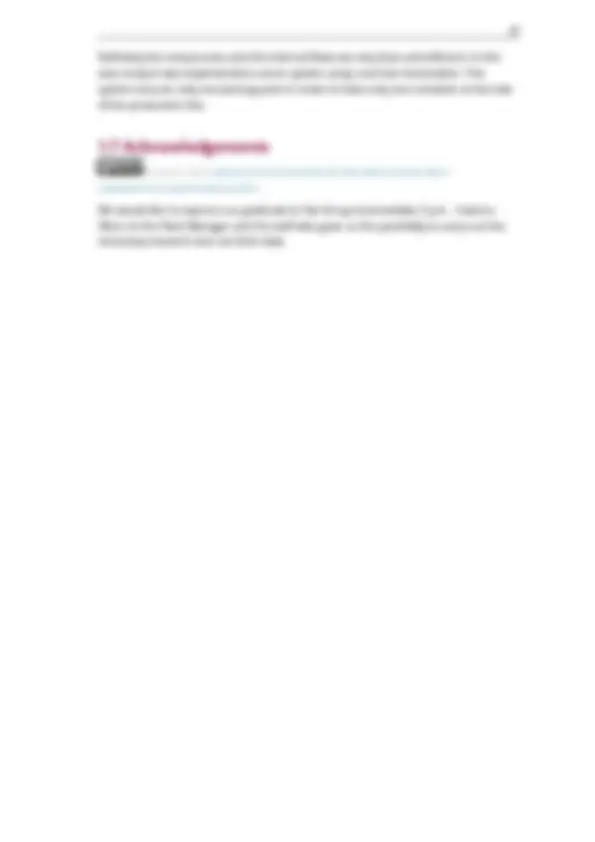
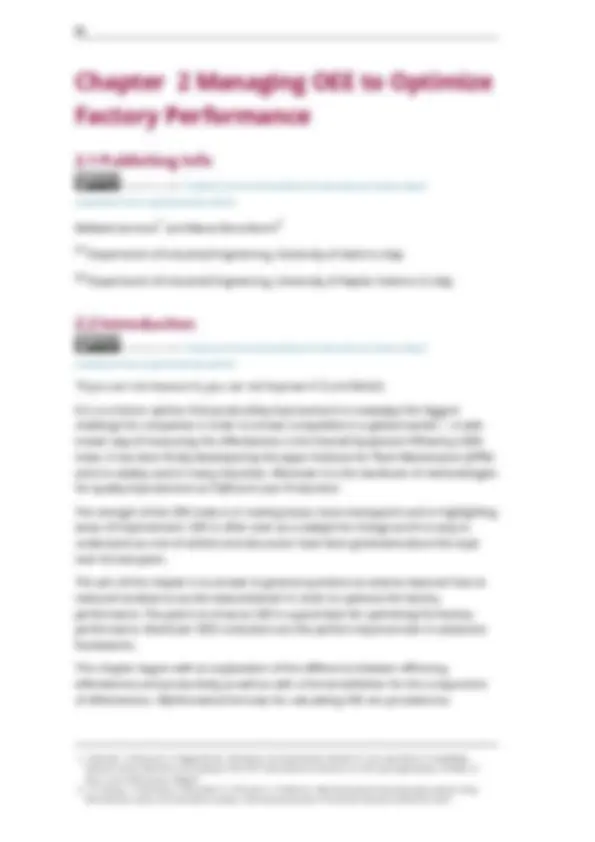
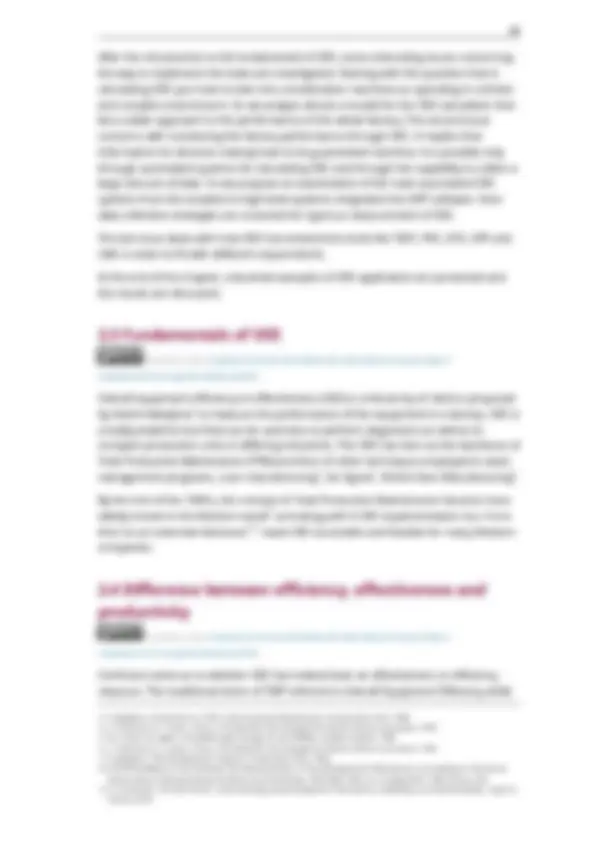
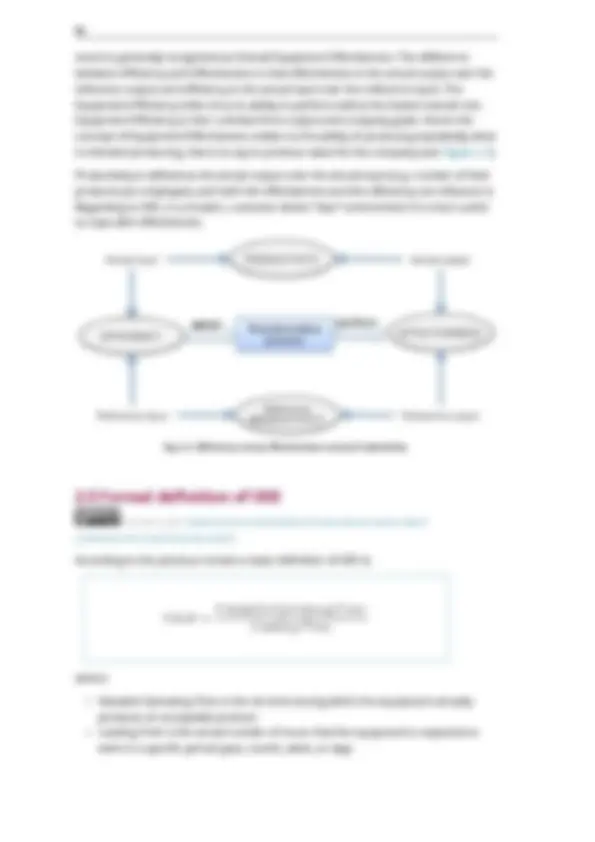
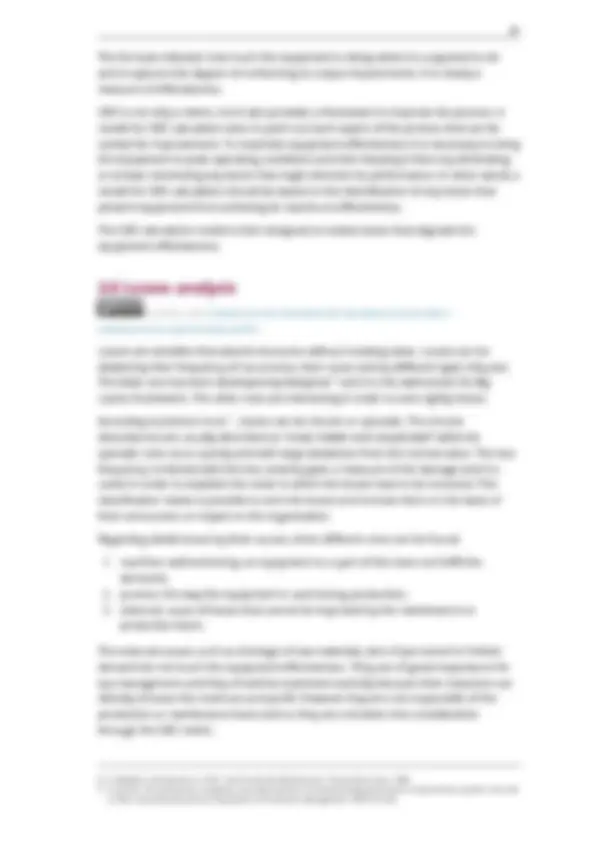
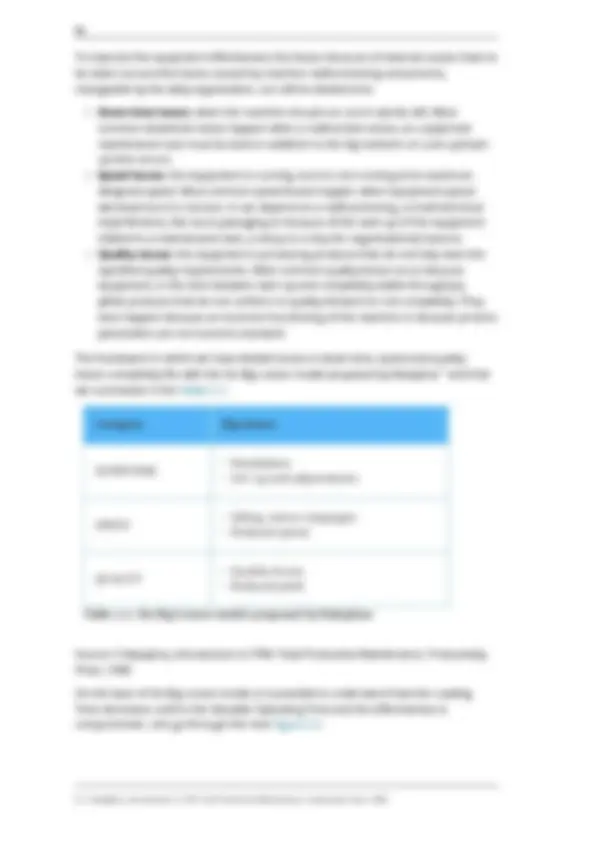
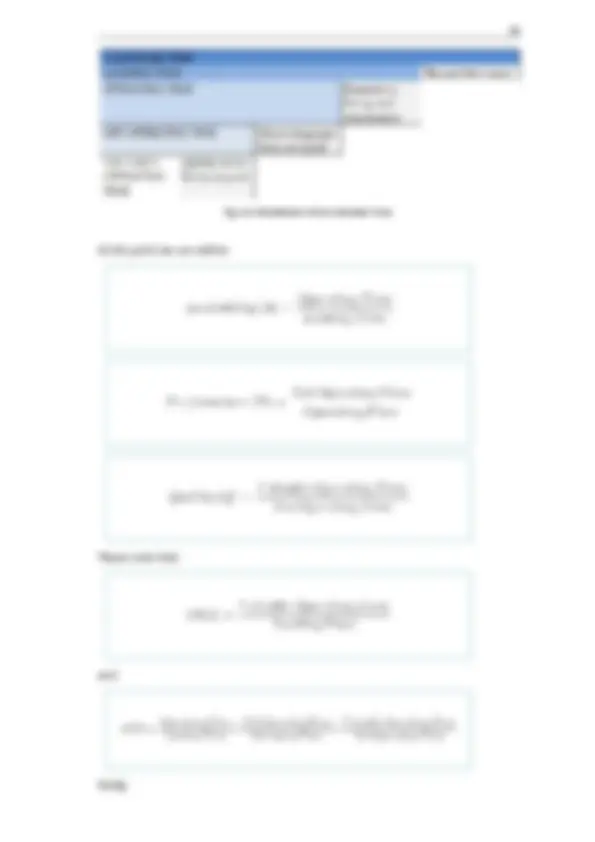
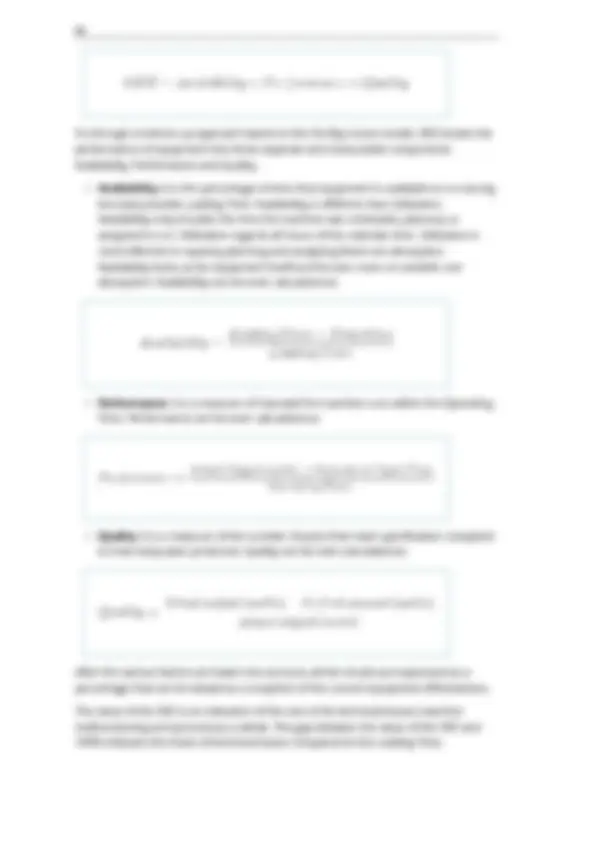
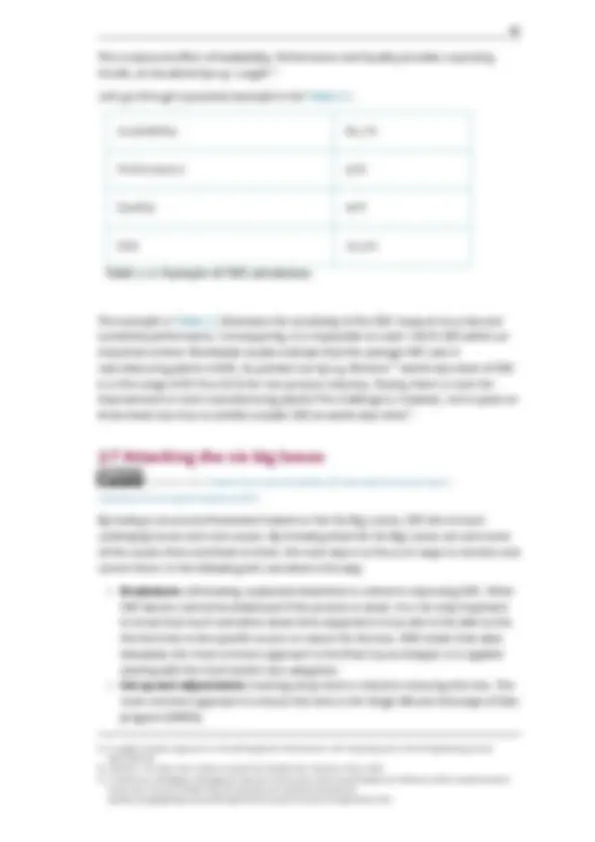
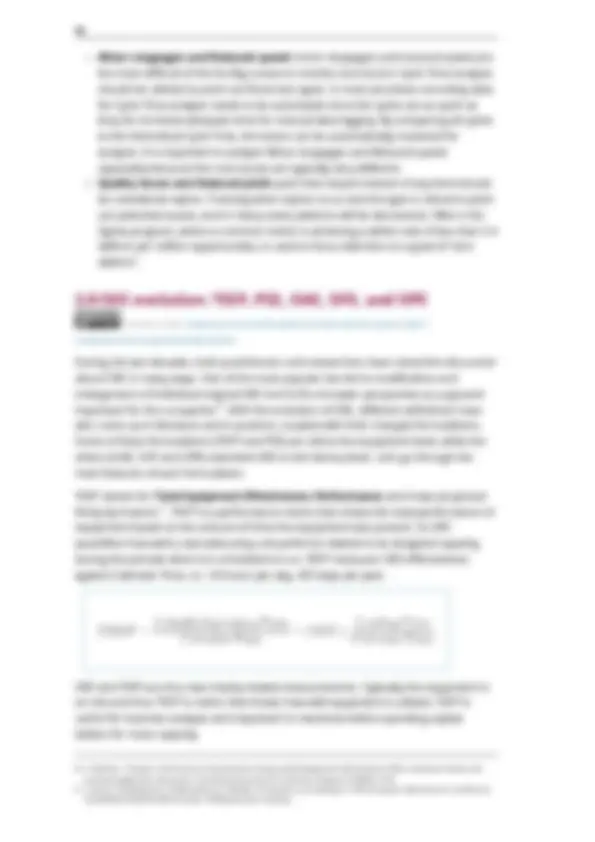
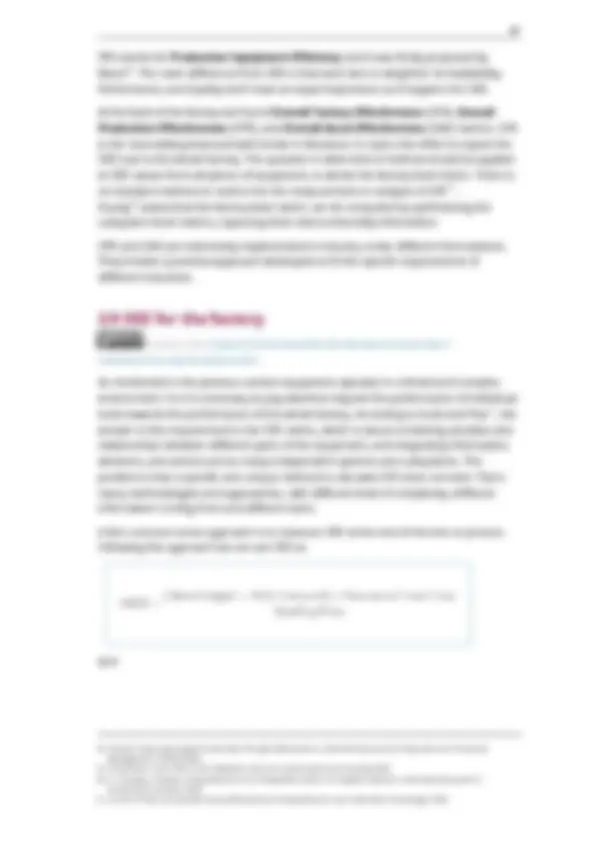
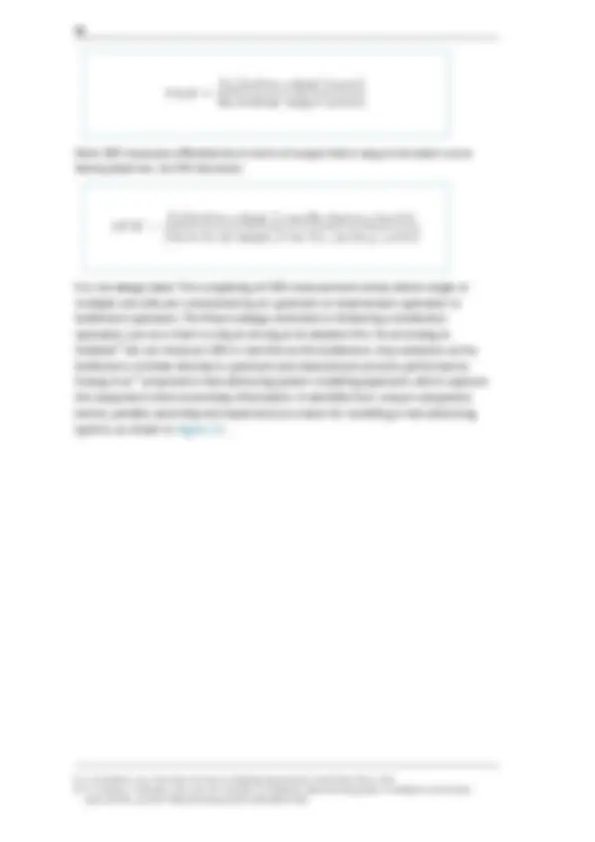
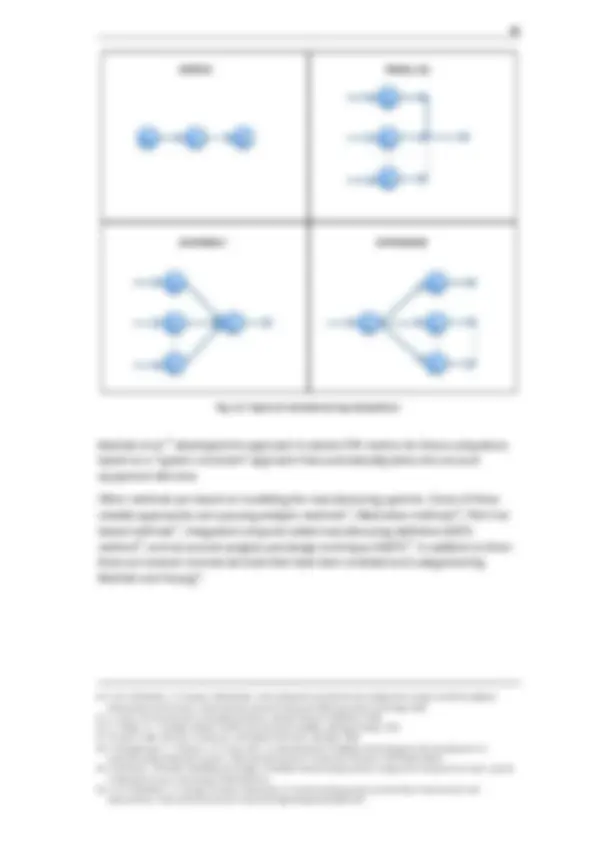
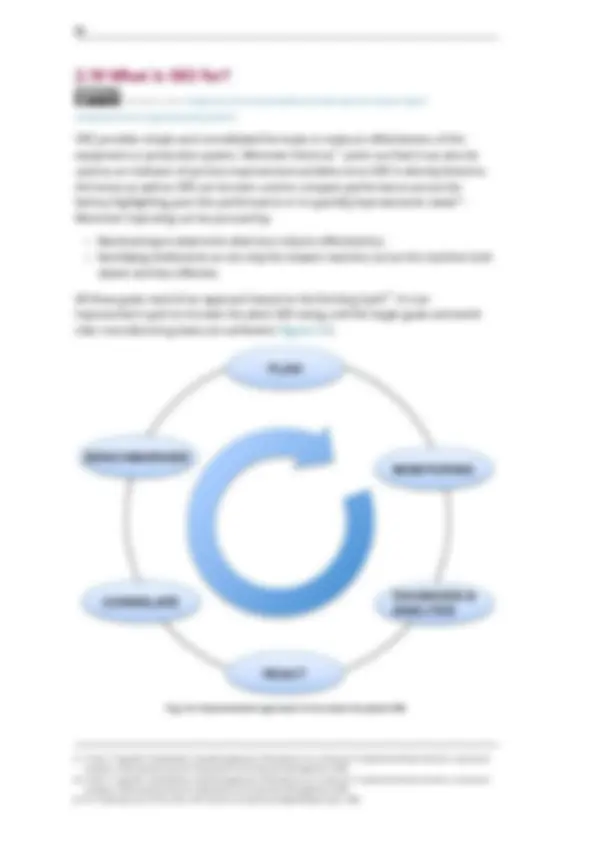
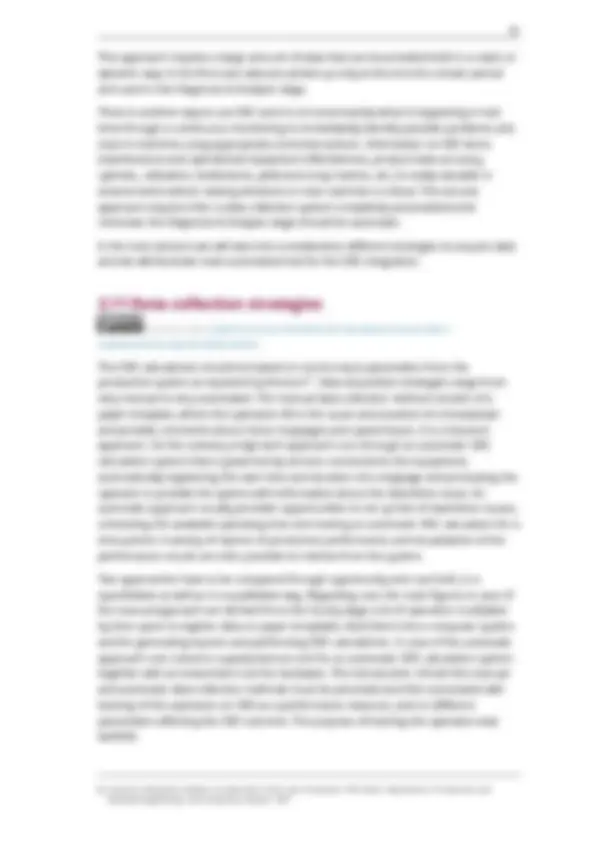
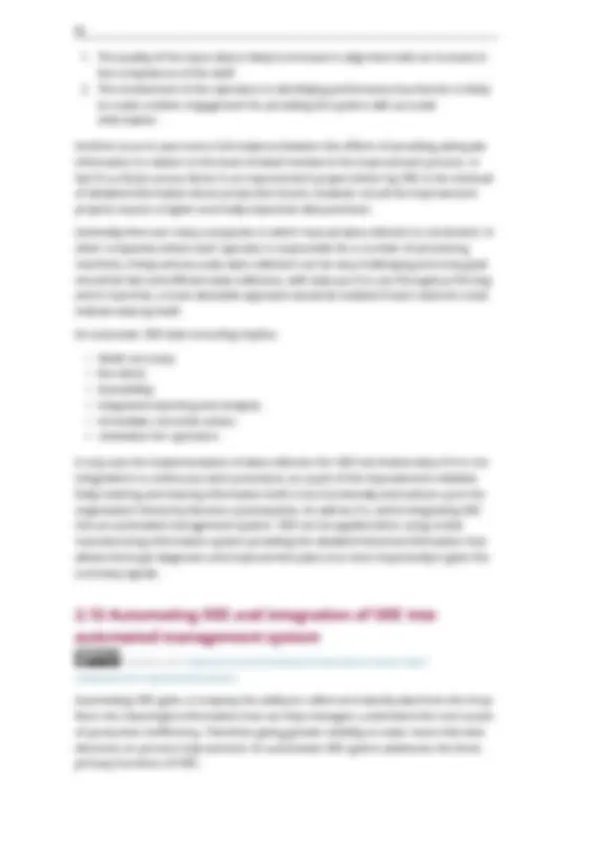
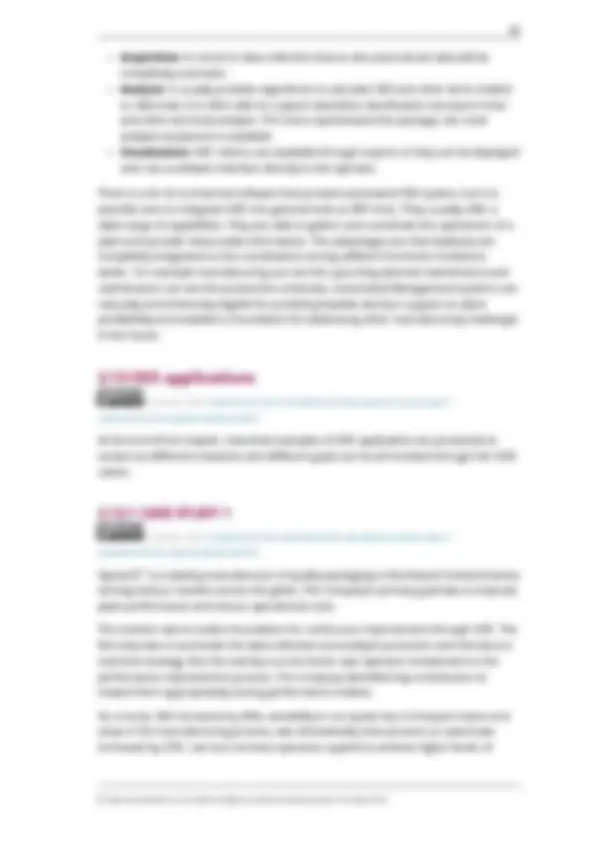
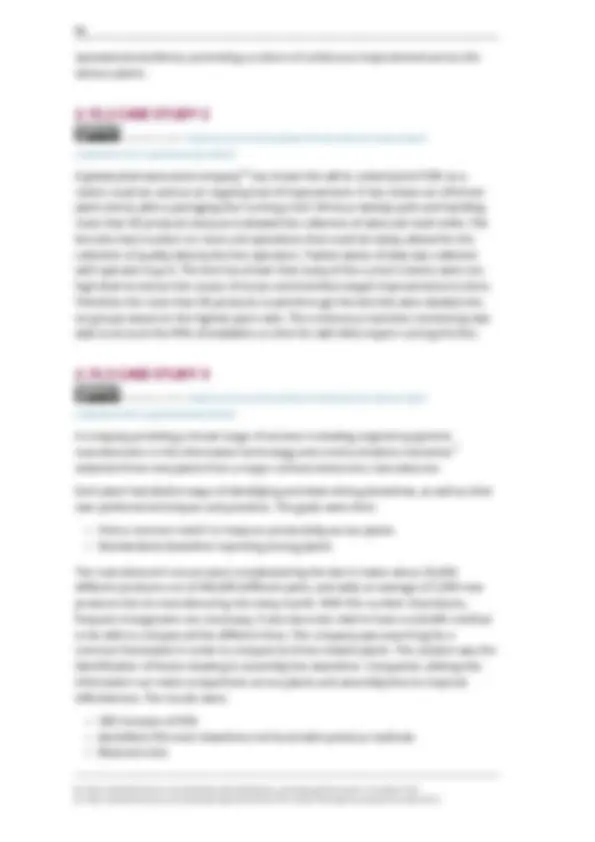
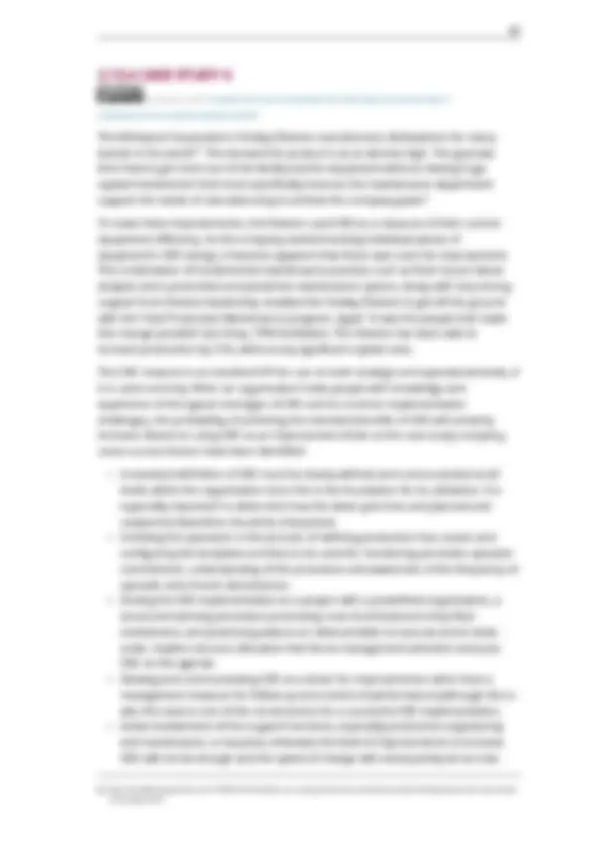
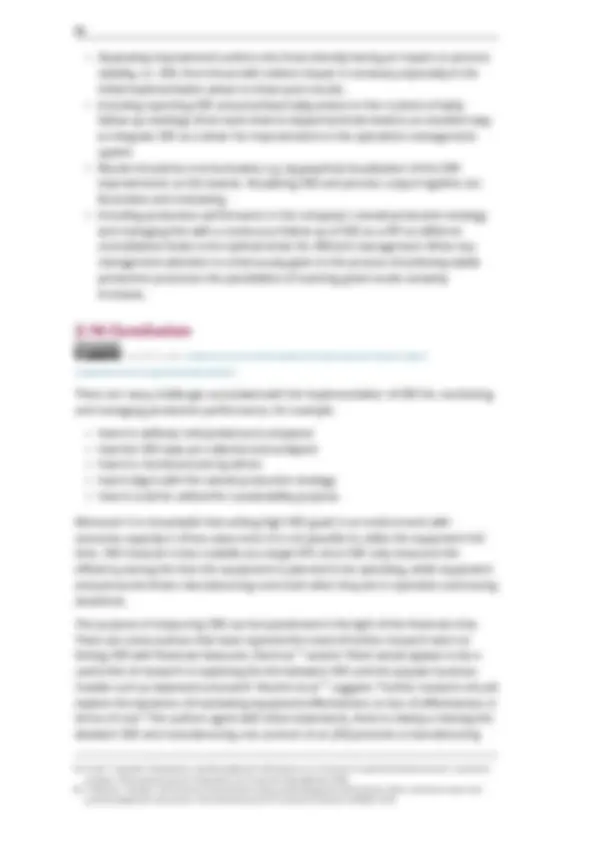
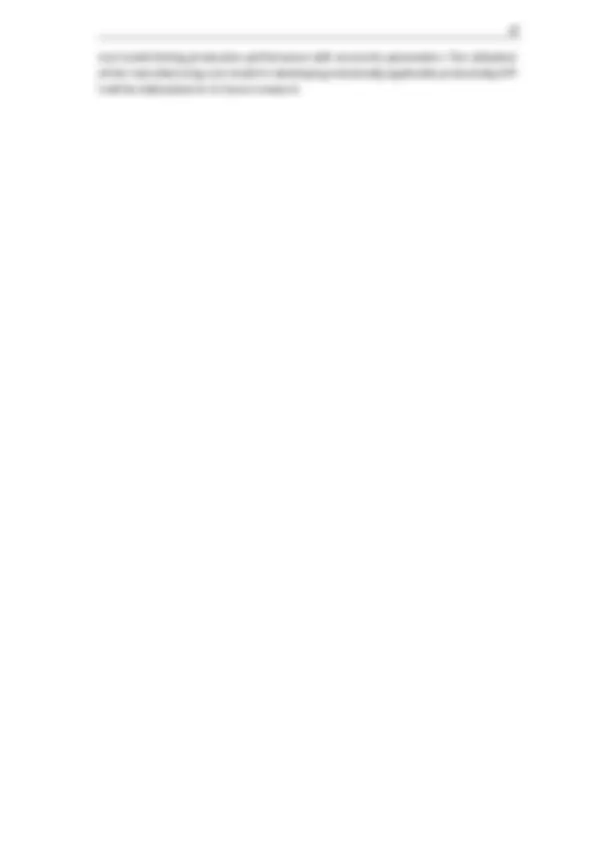
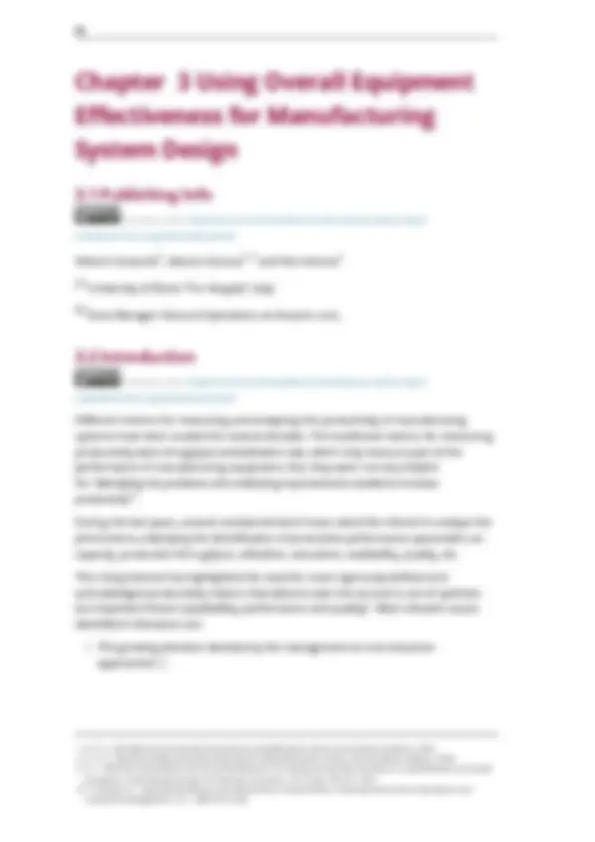
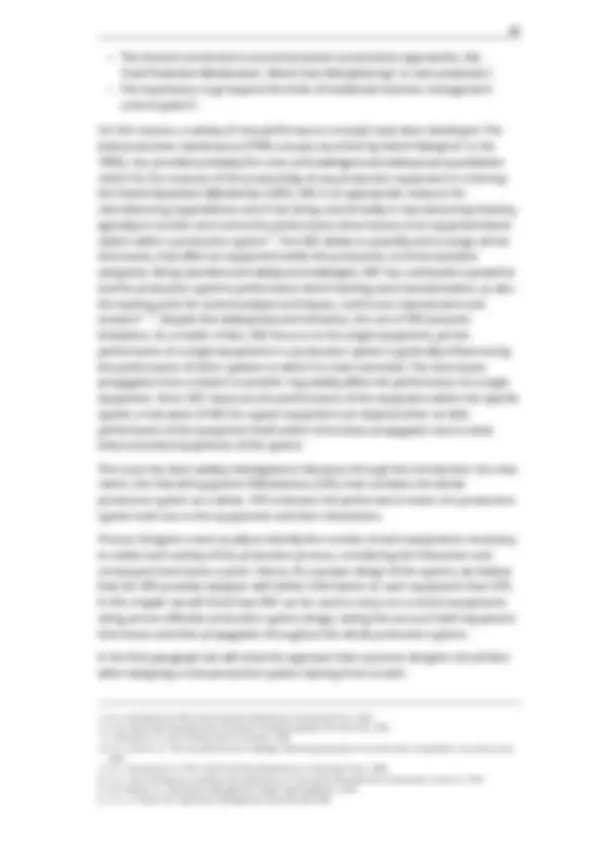
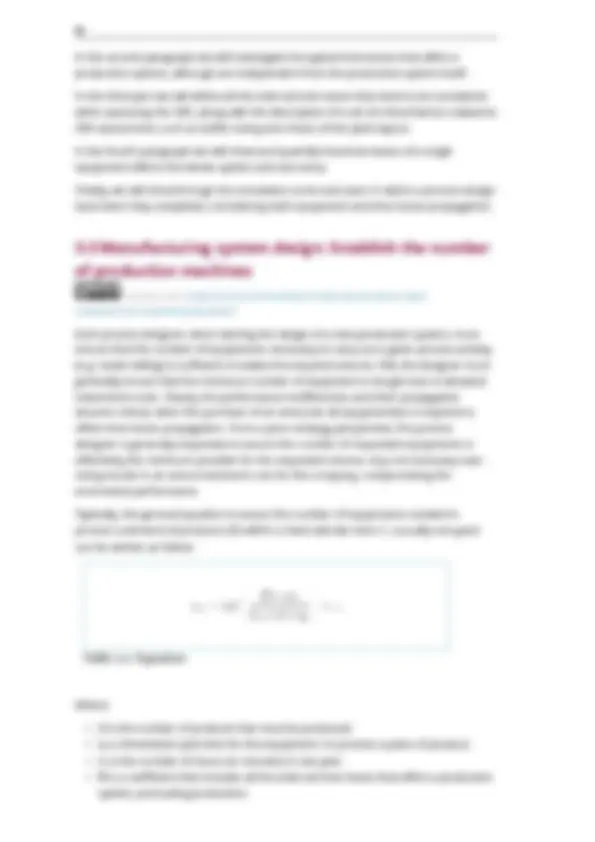
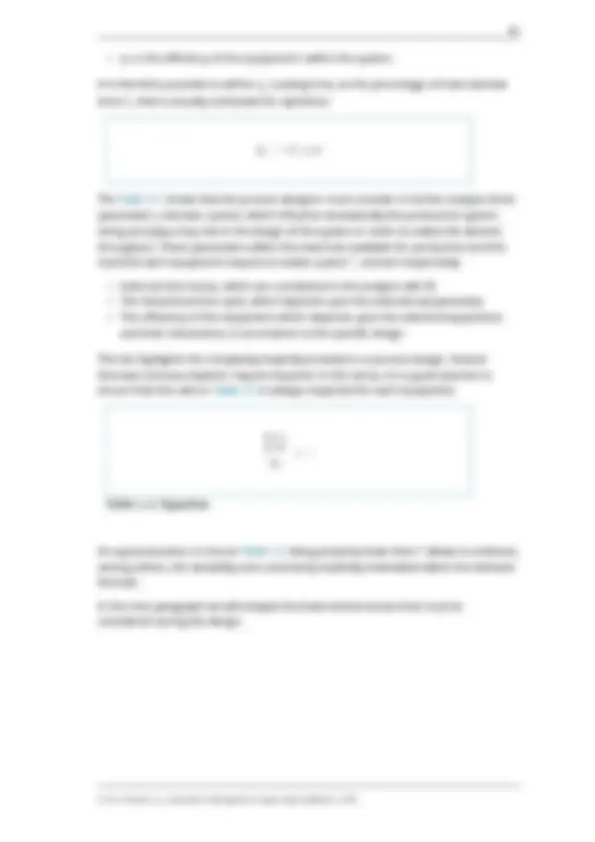
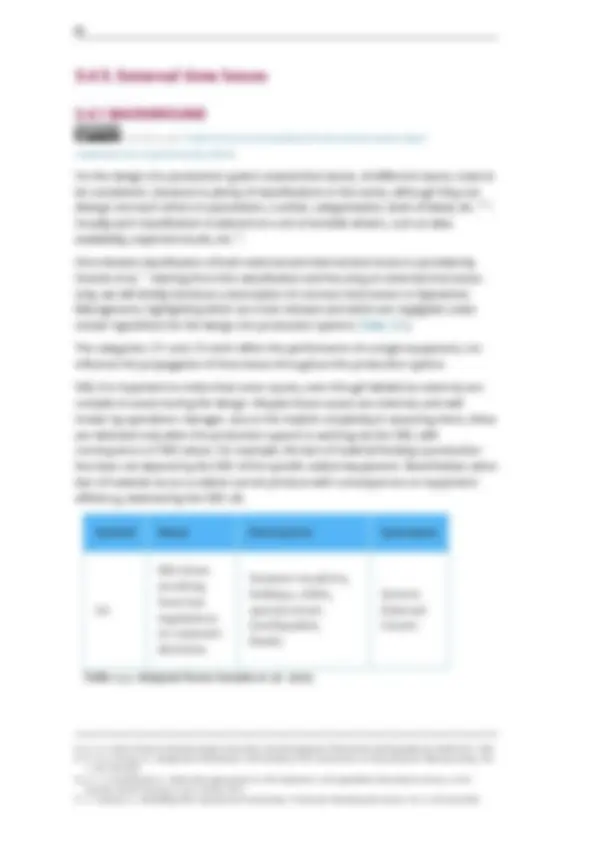
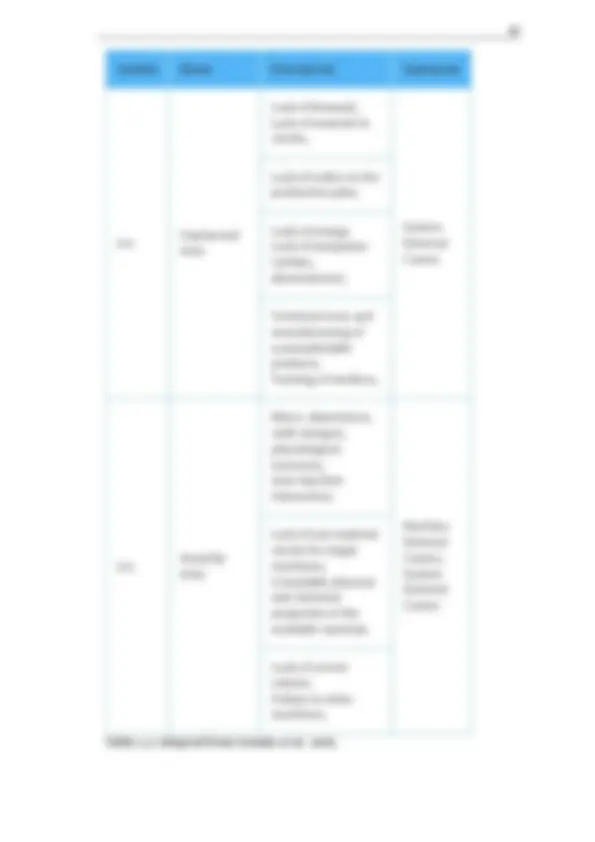
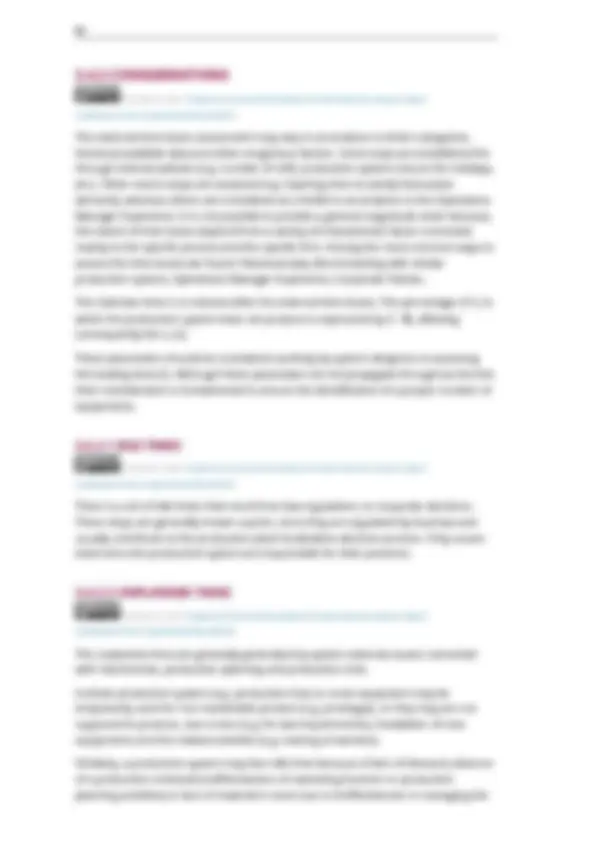
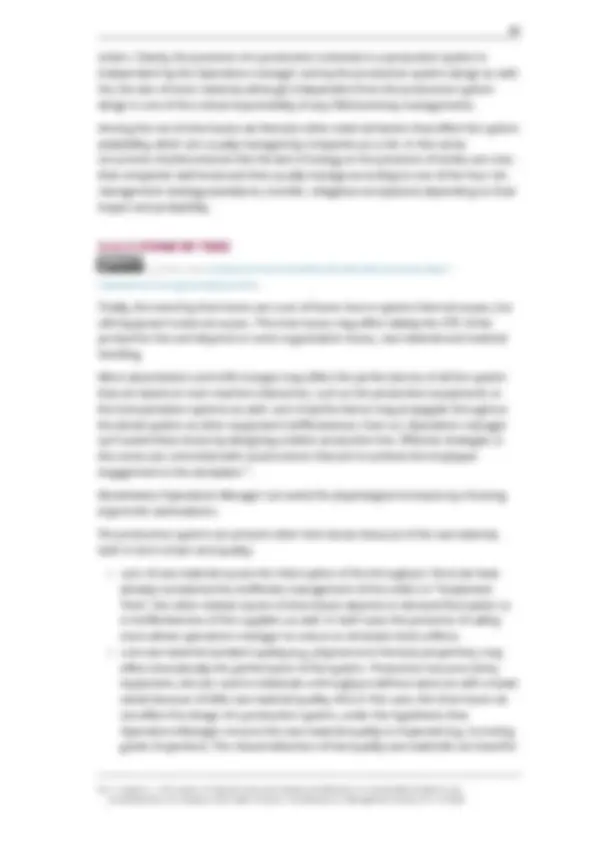
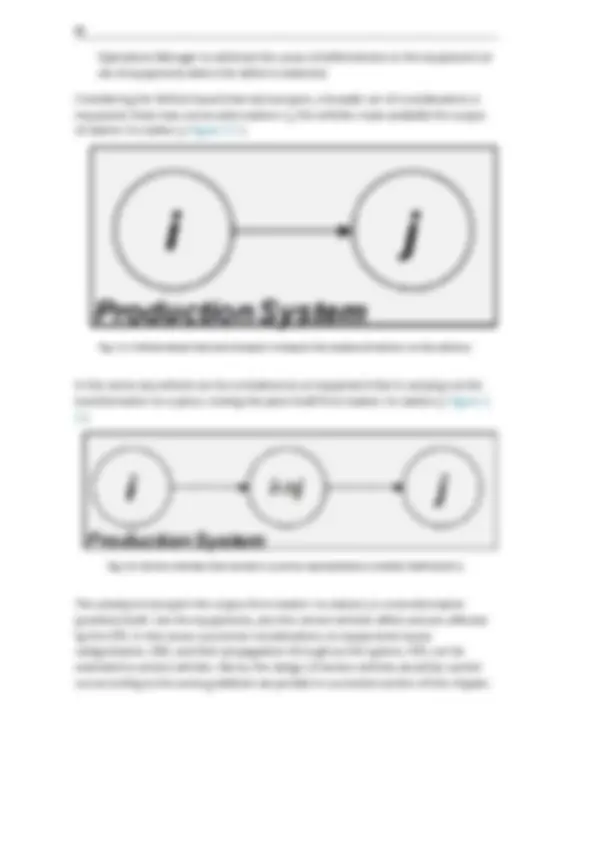
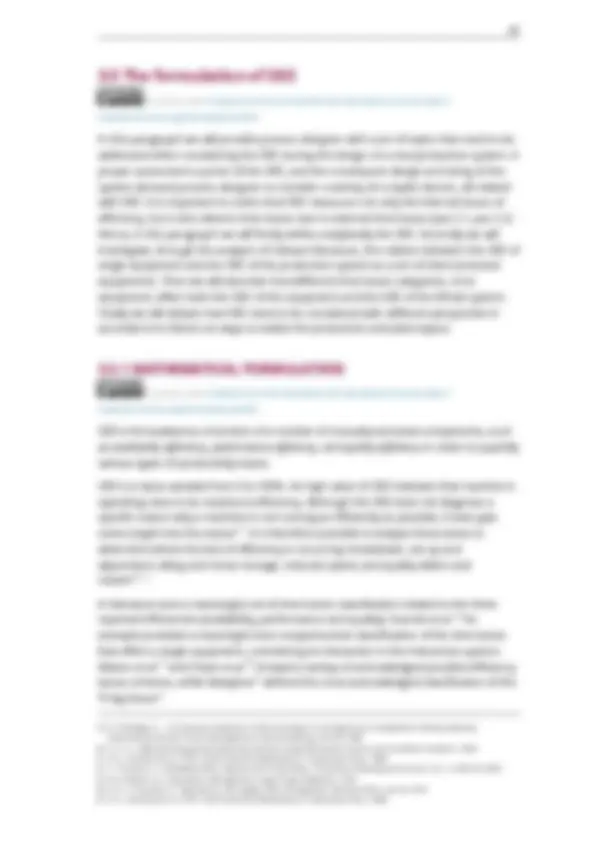
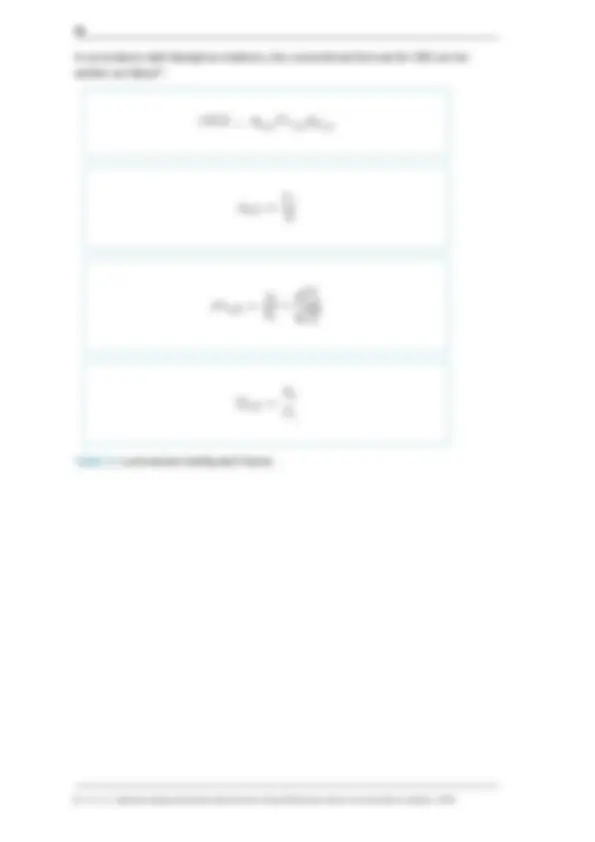
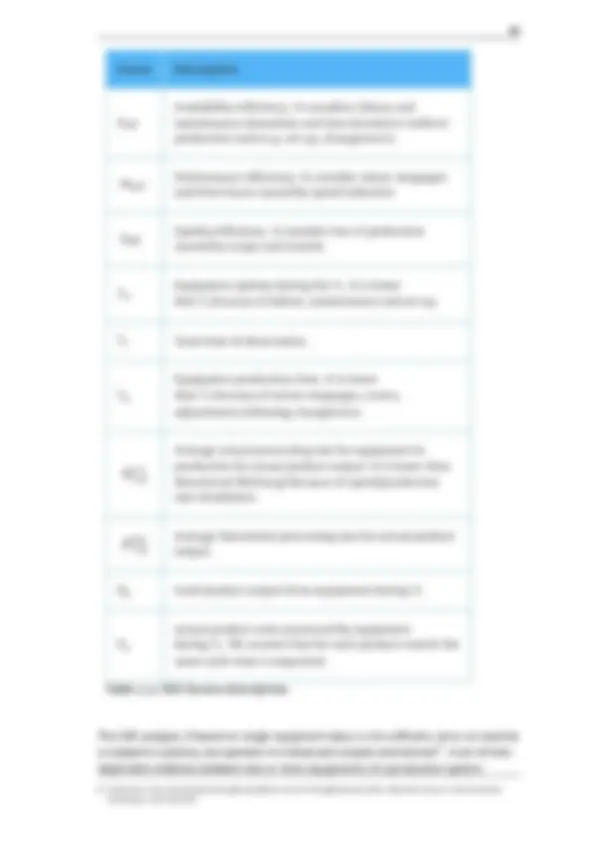
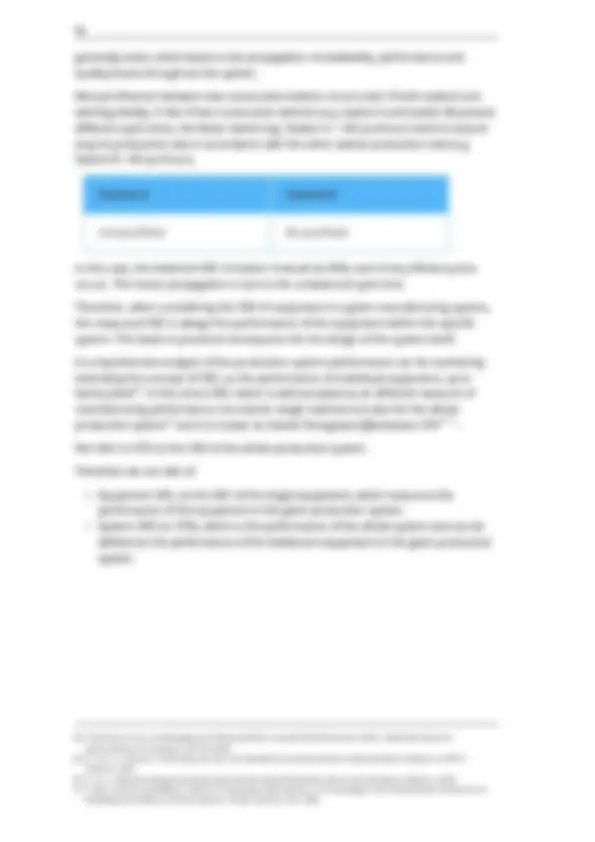
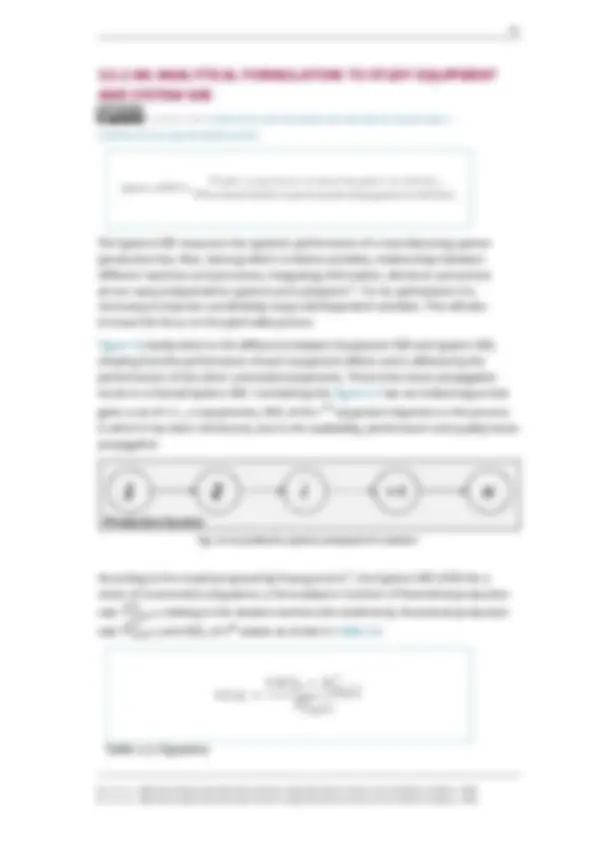
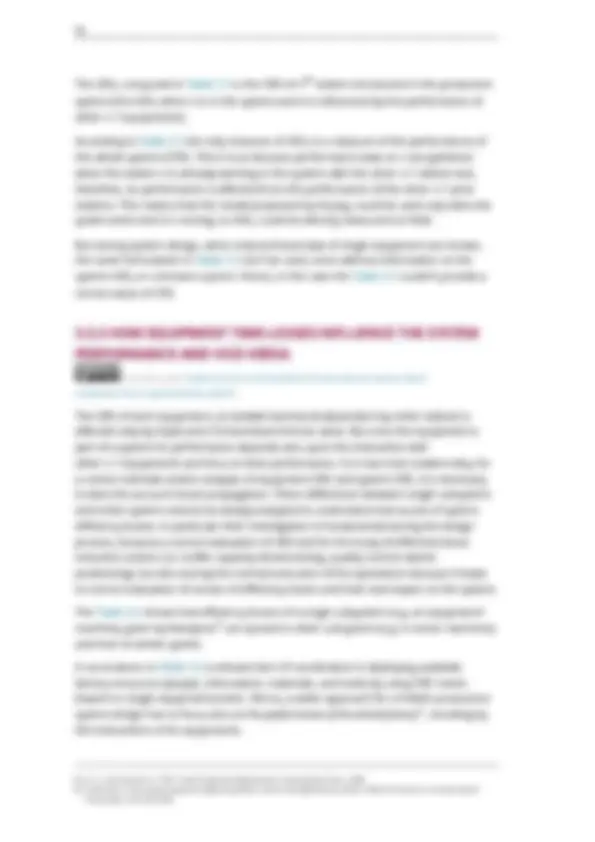
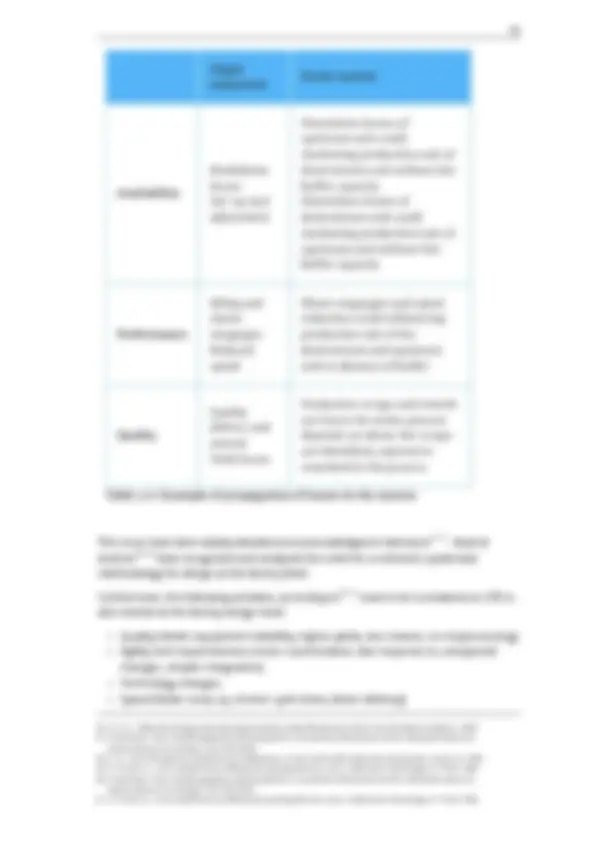
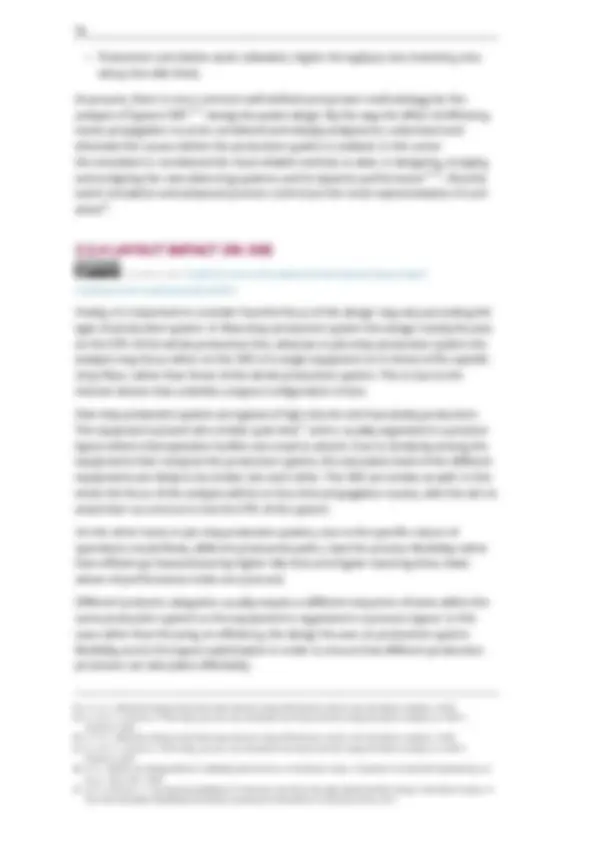
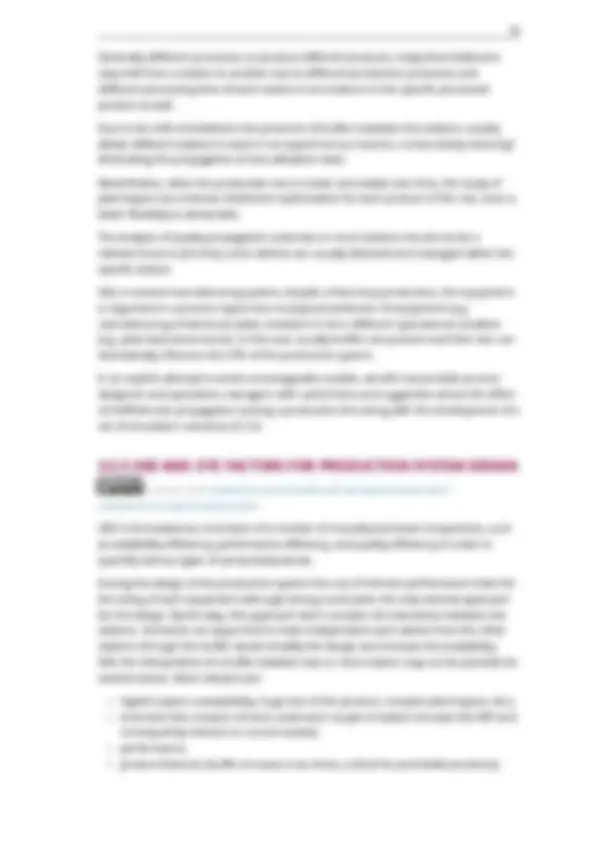
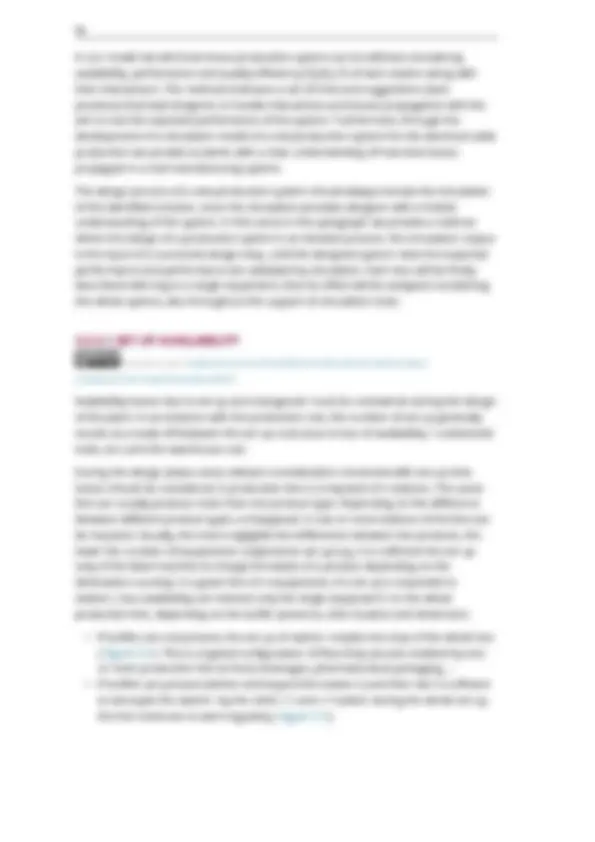

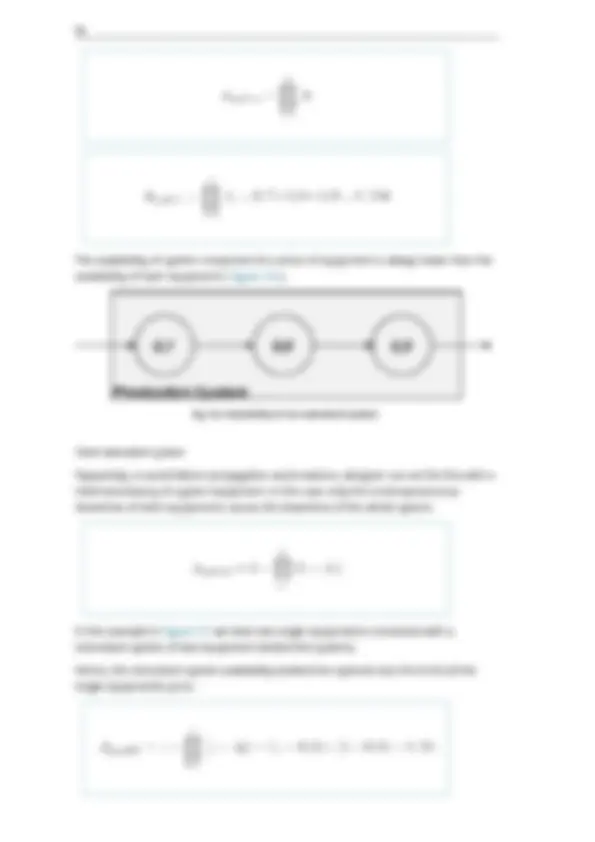
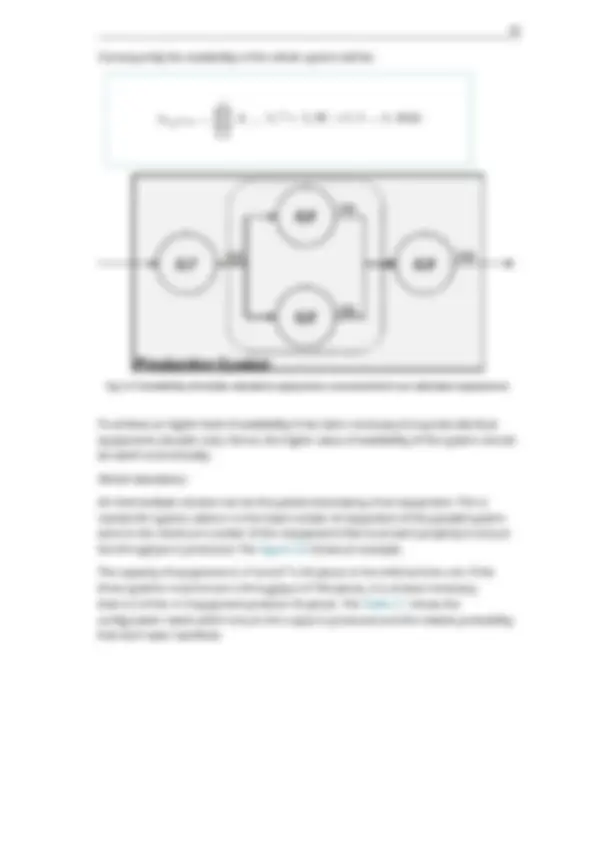
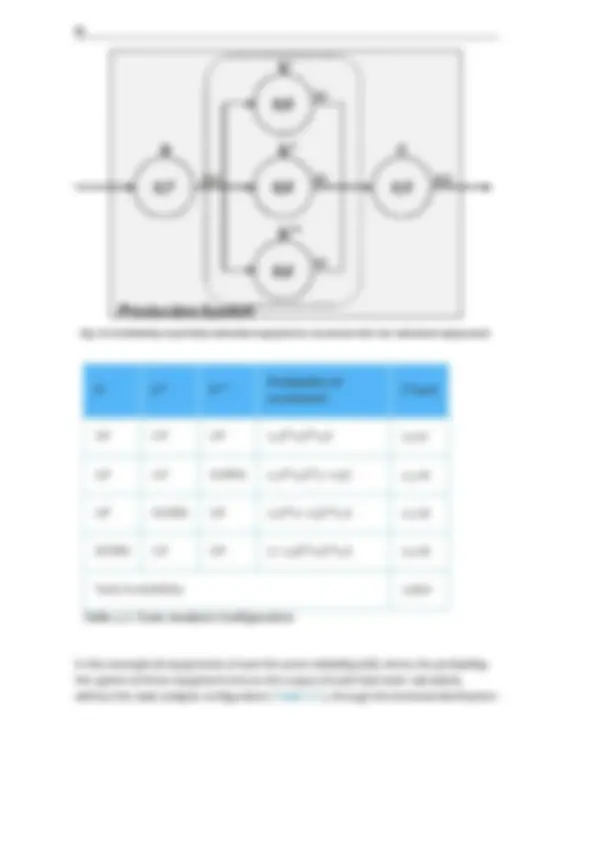
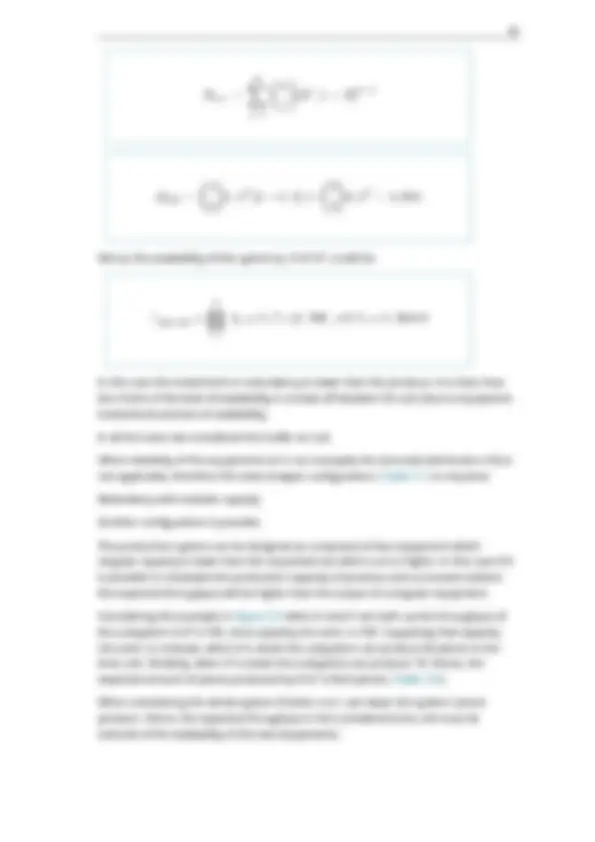
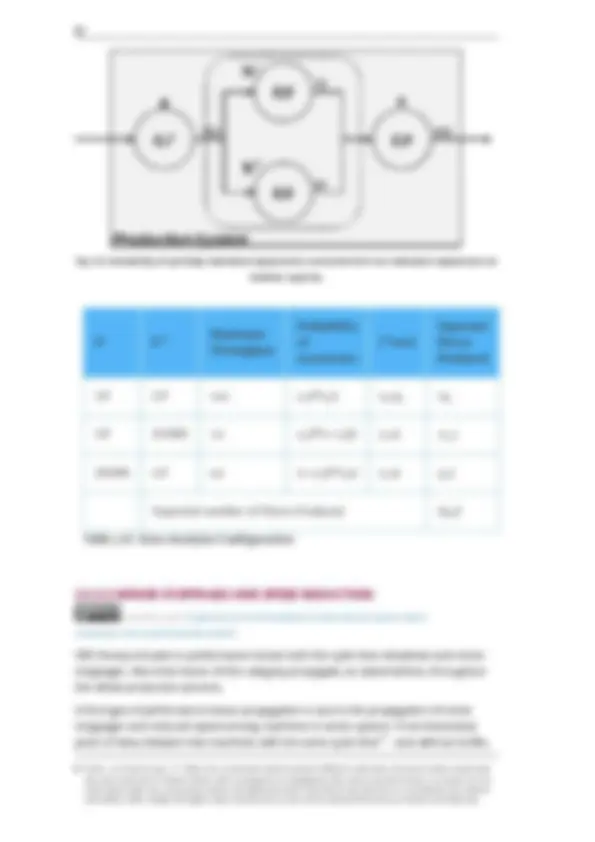
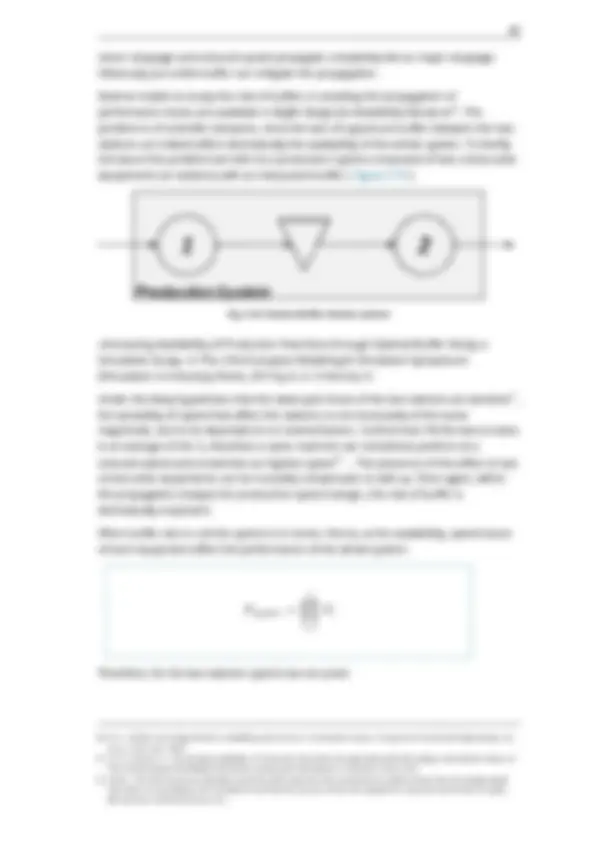
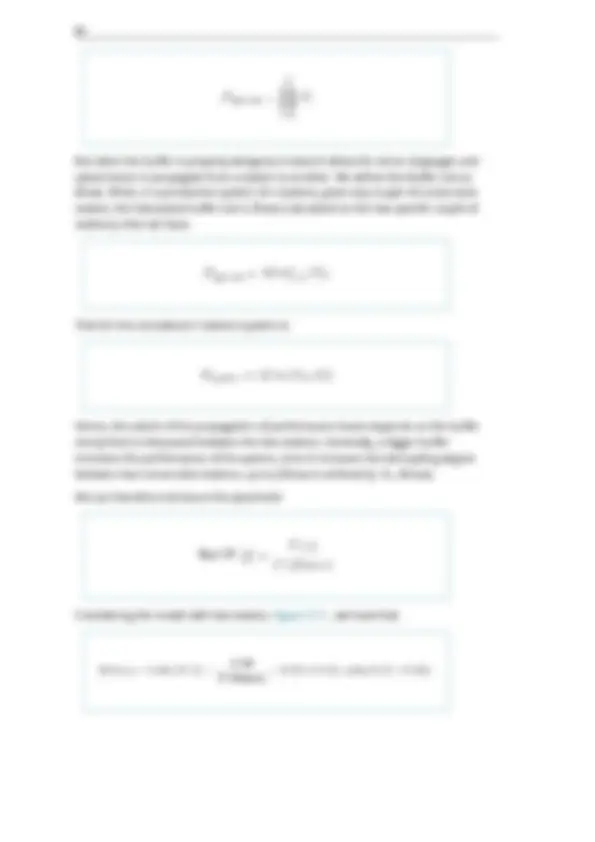
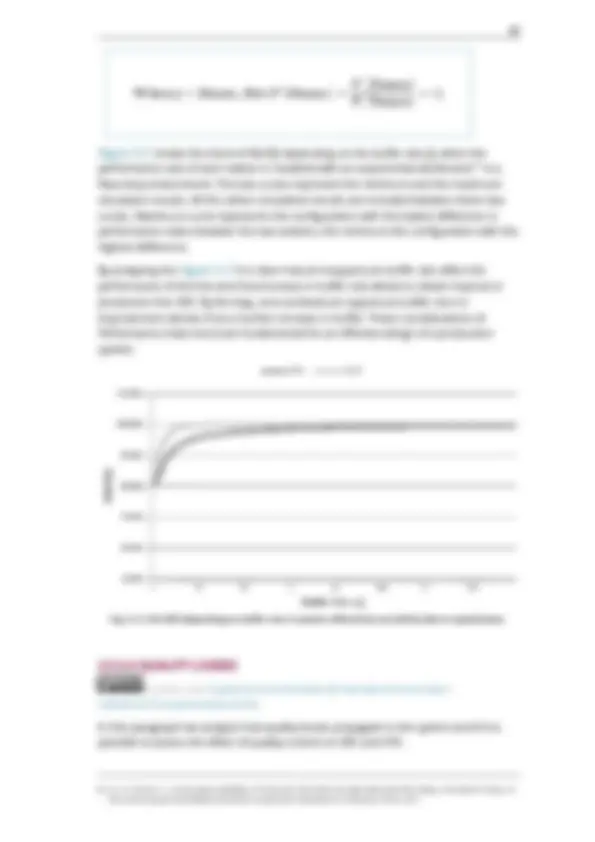
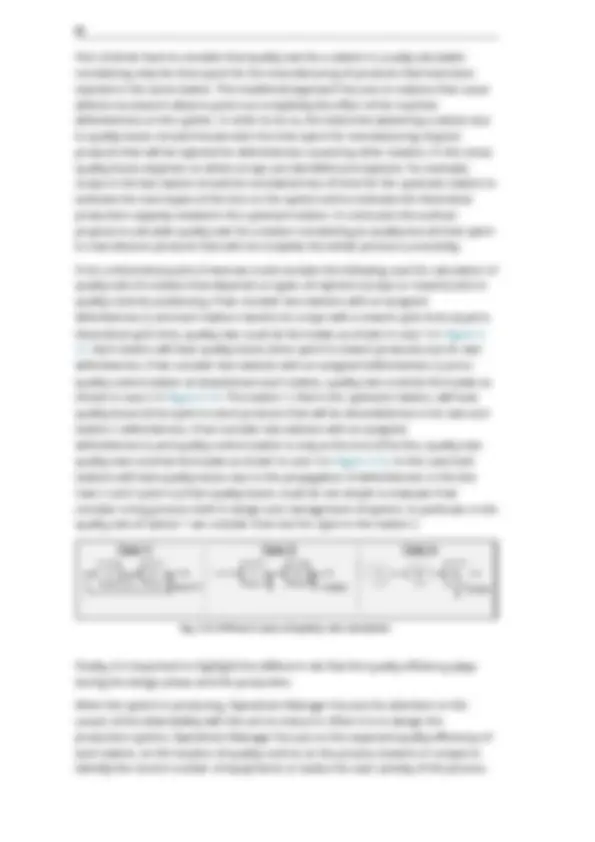
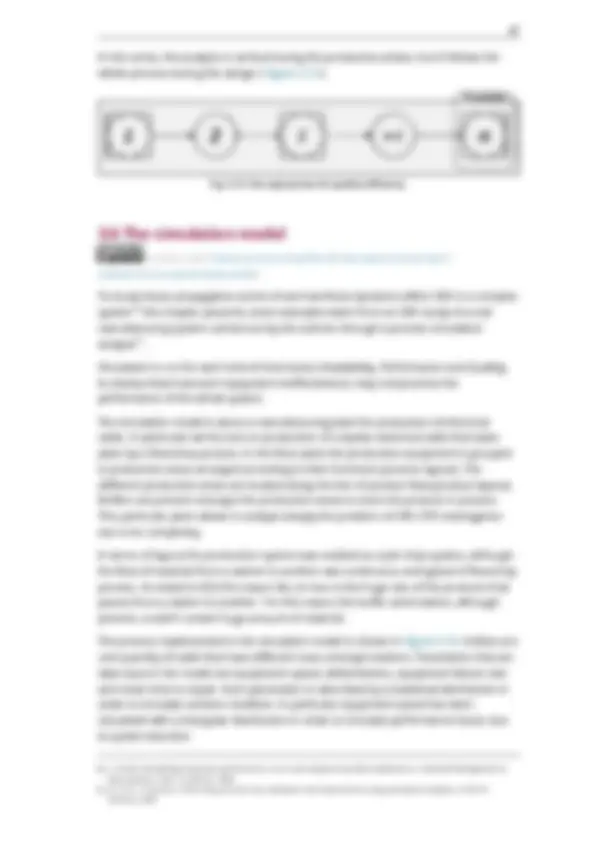
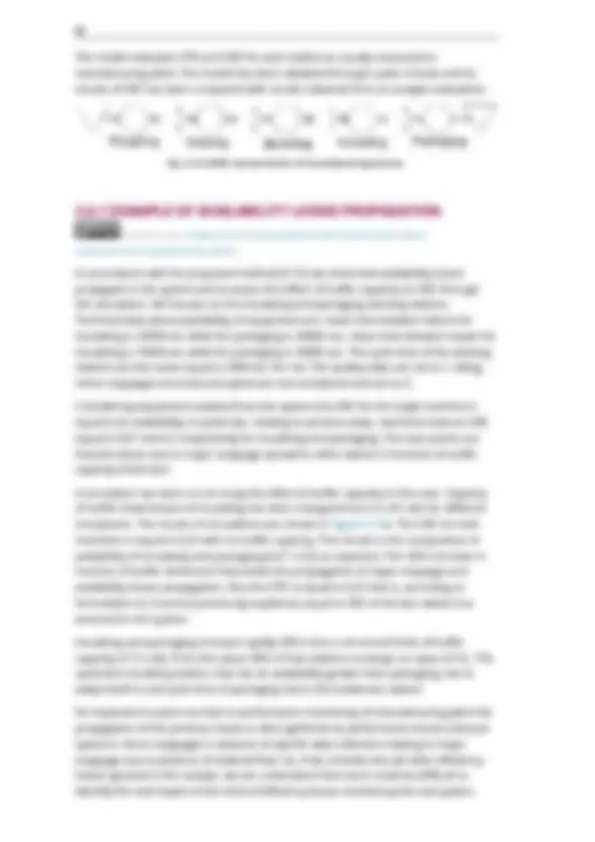
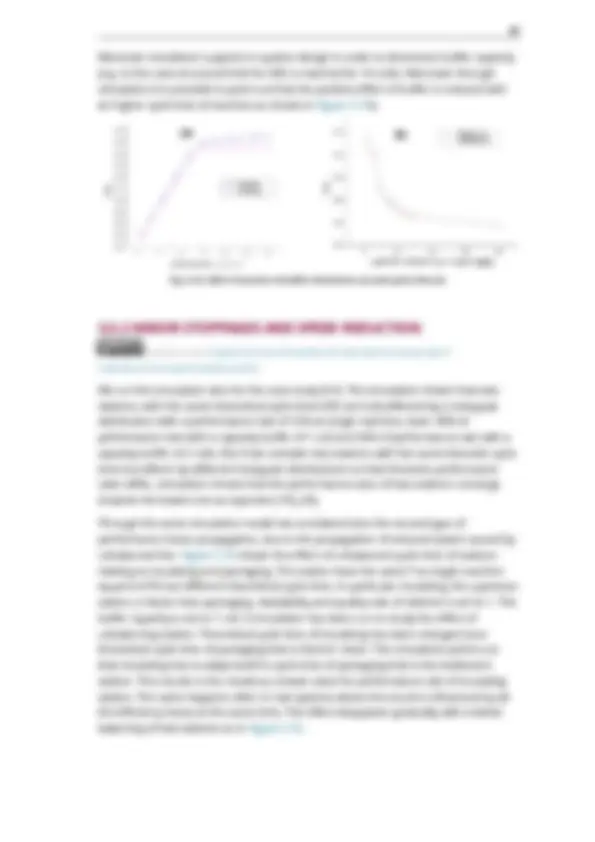
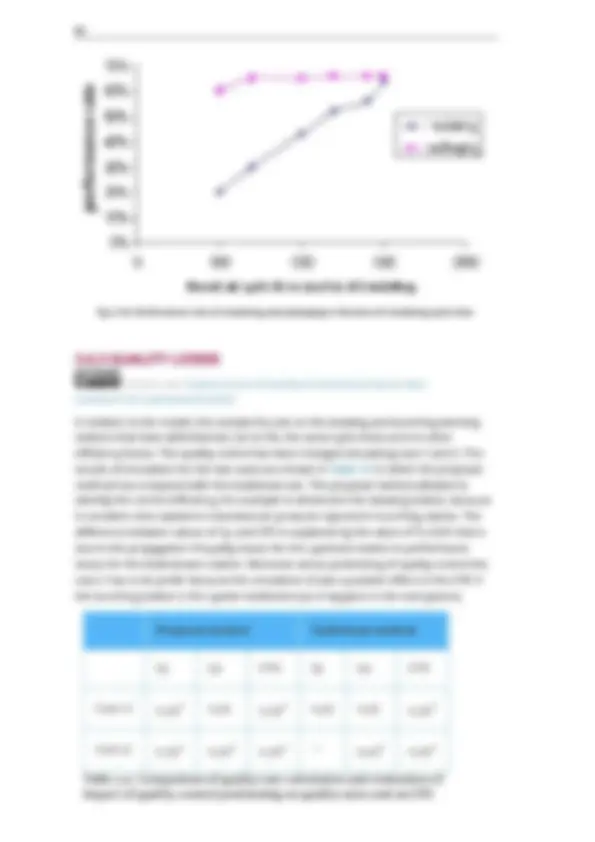
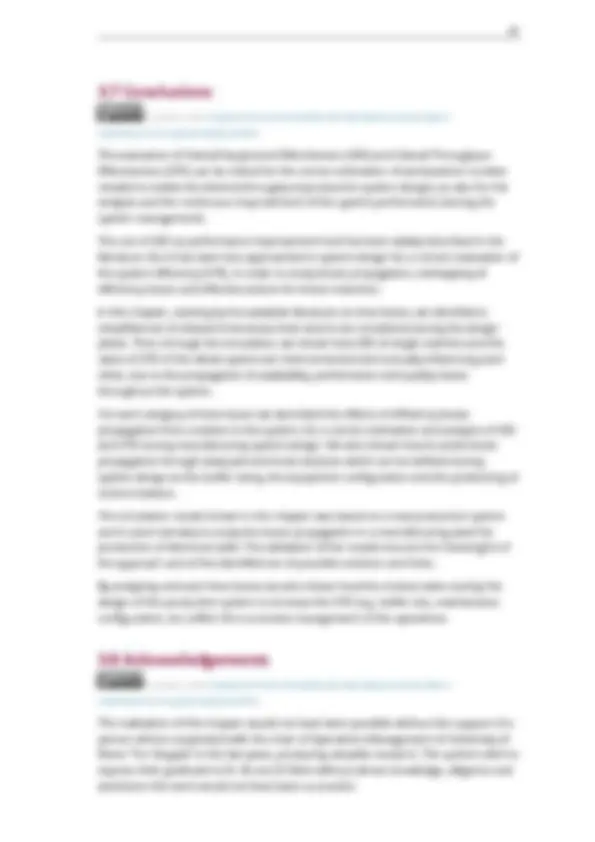
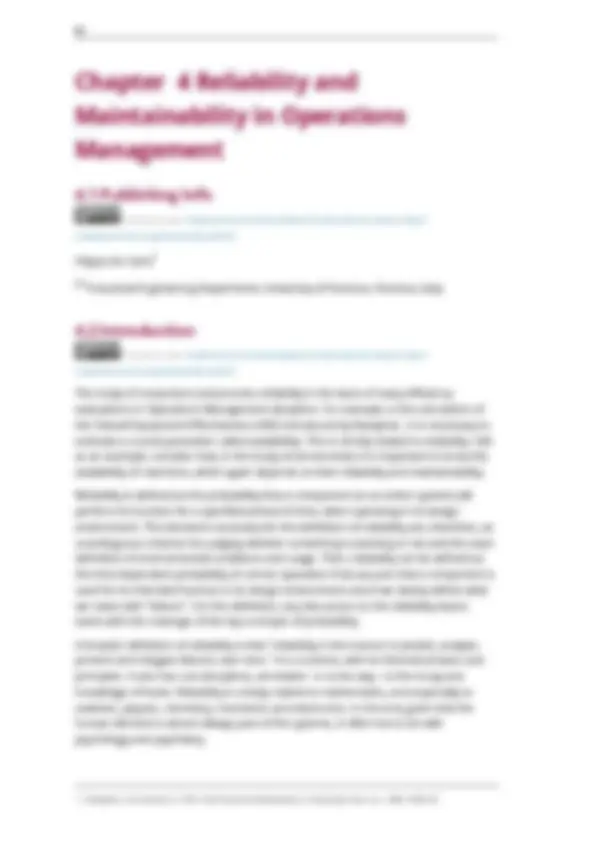
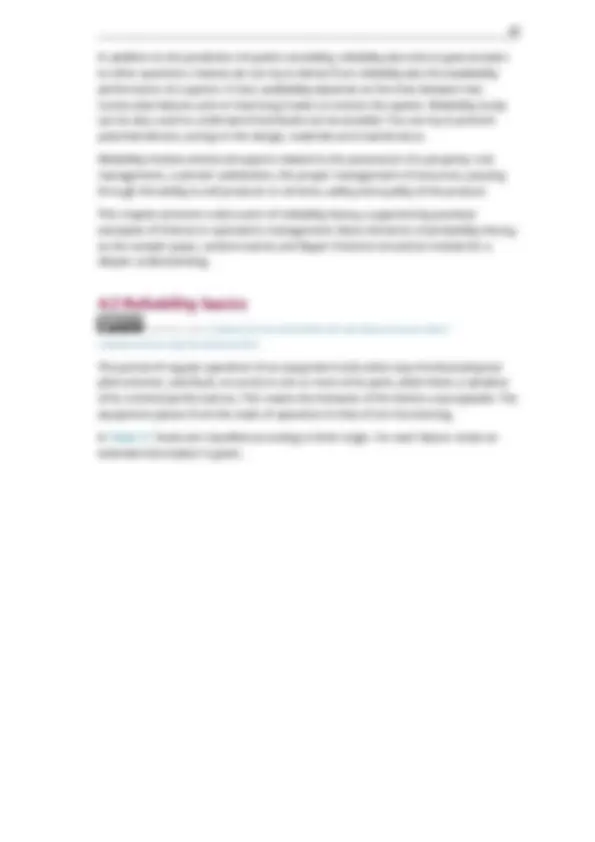
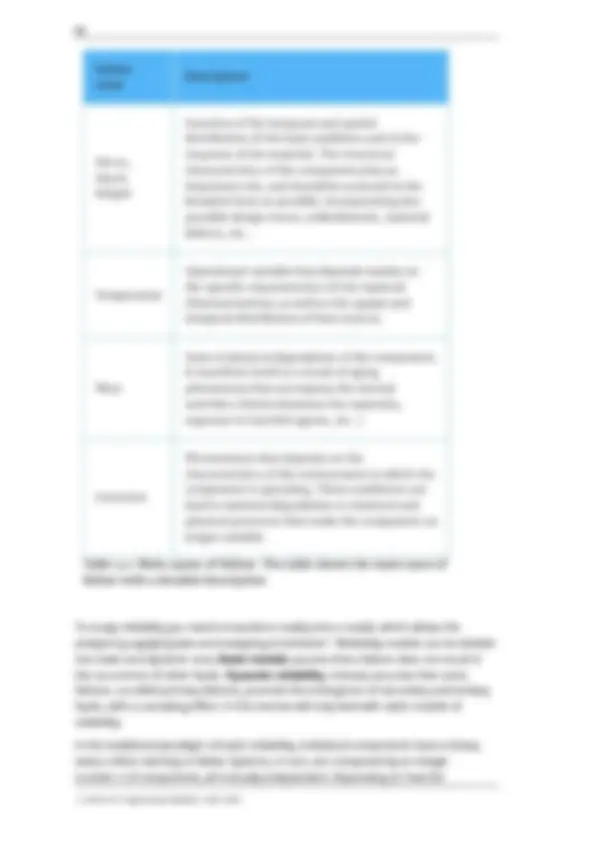
Study with the several resources on Docsity
Earn points by helping other students or get them with a premium plan
Prepare for your exams
Study with the several resources on Docsity
Earn points to download
Earn points by helping other students or get them with a premium plan
Community
Ask the community for help and clear up your study doubts
Discover the best universities in your country according to Docsity users
Free resources
Download our free guides on studying techniques, anxiety management strategies, and thesis advice from Docsity tutors
Ppt for operation management which helps to review notes
Typology: Lecture notes
1 / 278
This page cannot be seen from the preview
Don't miss anything!
© Prof. Fabio De Felice, Dr. Stanislao Monfreda, Dr. Antonella Petrillo, Dr.Ing. Maria Elena Nenni, Prof. Raffaele Iannone, Prof. Vito Introna, Dr. Alessio Giuiusa, Dr. Filippo De Carlo
Printing History
August 2013: Operations Management
This work is licensed under a Creative Commons-ShareAlike 4.0 International License
Original source: InTech http://www.intechopen.com/books/operations-management
Available under Creative Commons-ShareAlike 4.0 International License (http:// creativecommons.org/licenses/by-sa/4.0/).
Fabio De Felice^1 , Antonella Petrillo^1 and Stanislao Monfreda^2
[1] (^) University of Cassino, Department of Civil and Mechanical Engineering, Cassino,
Italy
[2] (^) Fiat Group Automobiles EMEA WCM Cassino Plant Coordinator, Cassino, Italy
Available under Creative Commons-ShareAlike 4.0 International License (http:// creativecommons.org/licenses/by-sa/4.0/).
Global competition has caused fundamental changes in the competitive environment of manufacturing industries. Firms must develop strategic objectives which, upon achievement, result in a competitive advantage in the market place. However, for almost all manufacturing industries, an increased productivity and better overall efficiency of the production line are the most important goals. Most industries would like to find the formula for the ultimate productivity improvement strategy. Industries often suffer from the lack of a systematic and consistent methodology. In particular the manufacturing world has faced many changes throughout the years and as a result, the manufacturing industry is constantly evolving in order to stay ahead of competition^1. Innovation is a necessary process for the continuous changes in order to contribute to the economic growth in the manufacturing industry, especially to compete in the global market. In addition to innovation as a mode for continued growth and change, there are many other vehicles for growth in the manufacturing industry^2 ,^3. One in particular that has been gaining momentum is the idea of World Class Manufacturing (WCM) developed by Richard J. Schonberger (in the 80s) who collected several cases, experiences and testimonies of companies that had embarked
1
on the path of continuous “Kaizen” improvement for excellence in production, trying to give a systematic conception to the various practices and methodologies examined. Some of the benefits of integrating WCM include increased competitiveness, development of new and improved technology and innovation, increased flexibility, increased communication between management and production employees, and an increase in work quality and workforce empowerment. This work takes you to the journey of World Class Manufacturing System (WCMS) adopted by the most important automotive Company located in Italy, the Fiat Group Automobiles. World class can be defined as a tool used to search and allow a company to perform at a best-on-class level.
The aim of this work is to present establishments of the basic model of World Class Manufacturing (WCM) quality management for the production system in the automotive industry in order to make products of the highest quality eliminating losses in all the factory fields an improvement of work standards.
The chapter is organized as follows: Section 2 introduces World Class Manufacturing and illustrates literature review, mission and principles of WCM, Section 3 describes Tools for WCM with particular attention on their features and on Key Performance and Key Activities Indicators and Section 4 describes the research methodology through a real case study in the largest Italian automotive company. To conclude, results and conclusions are provided.
Available under Creative Commons-ShareAlike 4.0 International License (http:// creativecommons.org/licenses/by-sa/4.0/).
Manufacturers in many industries face worldwide competitive pressures. These manufacturers must provide high-quality products with leading-edge performance capabilities to survive, much less prosper. The automotive industry is no exception. There is intense pressure to produce high-performance at minimum-costs^4. Companies attempting to adopt WCM have developed a statement of corporate philosophy or mission to which operating objectives are closely tied. A general perception is that when an organization is considered as world-class, it is also considered as the best in the world. But recently, many organizations claim that they are world-class manufacturers. Indeed we can define world class manufacturing as a different production processes and organizational strategies which all have flexibility as their primary concern^5. For example Womack et al.^6 defined a lead for quantifying world class. Instead Oliver et al.^7 observed that to qualify as world class, a plant had to demonstrate outstanding performance on both productivity and quality measures. Summing up we can state that the term World-Class Manufacturing (WCM) means the pursuance of best practices in manufacturing. On the other hand we would like to
2
Fig. 1.2: WCM Model by Schonberger
These techniques have been known for a long time, but with Schonberger, a perfectly integrated and flexible system was obtained, capable of achieving company competitiveness with products of high quality. The WCM model by Schonberger is illustrated here above in Figure 1.2.
According to Fiat Group Automobiles, “World Class Manufacturing (WCM)” is: a structured and integrated production system that encompasses all the processes of the plant, the security environment, from maintenance to logistics and quality. The goal is to continuously improve production performance, seeking a progressive elimination of waste, in order to ensure product quality and maximum flexibility in responding to customer requests, through the involvement and motivation of the people working in the establishment.
The WCM program has been made by Prof. Hajime Yamashina from 2005 at the Fiat Group Automobiles. The program is shown here below in Figure 1.3.
4
Fig. 1.3: World Class Manufacturing in Fiat Group Automobiles
Fiat Group Automobiles has customized the WCM approach to their needs with Prof. Hajime Yamashina from Kyoto University (he is also member of the Royal Swedish Academy and in particular he is RSA Member of Engineering Sciences), by redesigning and implementing the model through two lines of action: 10 technical pillars ; 10 managerial pillars.
The definition proposed by Yamashina includes a manufacturing company that excels in applied research, production engineering, improvement capability and detailed shop floor knowledge, and integrates those components into a combined system. In fact, according to Hajime Yamashina the most important thing continues to be the ability to change and quickly^9. WCM is developed in 7 steps for each pillar and the steps are identified in three phases: reactive, preventive and proactive. In Figure 1.4 an example of a typical correlation between steps and phases is shown, but this correlation could change for each different technical pillar; in fact each pillar could have a different relation to these phases. The approach of WCM needs to start from a “ model area ” and then extend to the entire company. WCM “attacks” the manufacturing area. WCM is based on a system of audits that give a score that allows to get to the highest level. The highest level is represented by “ the world class level ”.
5
Available under Creative Commons-ShareAlike 4.0 International License (http:// creativecommons.org/licenses/by-sa/4.0/).
WCM foresees 10 technical pillars and 10 managerial pillars. The levels of accomplishment in technical fields are indirectly affected by the level of accomplishment in administrative fields. The pillar structure represents the “Temple of WCM” Figure 1.5 and points out that, to achieve the standard of excellence, a parallel development of all the pillars is necessary. Each pillar focuses on a specific area of the production system using appropriate tools to achieve excellence global.
Fig. 1.5: Temple of WCM
Here below in Table 1.1 features for each technical pillars are illustrated.
7
PillarTechnical
Why
Purpose
Safety SAF
safetyimprovement ofContinuous
To develop specific professional skills.To improve the ergonomics of the workplace.To develop a culture of prevention.To reduce drastically the number of accidents.
DeploymentCostCD
costs)(losses within thelosses and costsAnalysis of the
managerial tasks with greatest potential.To address the resources and commitment toexpected.To quantify the potential economic benefits andbusiness.items of loss in the system production-logisticsTo identify scientifically and systematically the main
ImprovementFocusedFI
deploymentthe costloss identified byto management thePriorities of actions
solving.To develop specific professional skills of problemincrease the competitiveness of the cost of the product.To eliminate non-value-added activities, in order toinefficiencies.in the system manufacturing plant, eliminatingTo reduce drastically the most important losses present
Activities AutonomousAA
workplaceplant andimprovement ofContinuous
AM Autonomous Maintenance. It is constituted by two pillars:
(^) It is used to improve the
(equipment specialists).maintenance policies through the conductorsoverall efficiency of the production system through
Table 1.1: Description of pillars
PillarTechnical
Why
Purpose
Management Early Product
productsfeatures of new
DevelopmentPeoplePD
and workersskills of employeesimprovement of theContinuous
technologists, specialists such as major staff training.To develop the roles of maintenance workers,correct skills and abilities for each workstation.To ensure, through a structured system of training,
EnergyENE EnvironmentENV
reduce energy wastemanagement andenvironmentalimprovementContinuous
costs and losses.To develop an energy culture and to reduce the energyenvironmental management.To comply with the requirements and standards of
Table 1.1: Description of pillars
As regards the ten Managerial Pillars there are: 1) Management Commitment; 2) Clarity of Objectives; 3) Route map to WCM; 4) Allocation of Highly Qualified People to Model Areas; 5) Organization Commitment; 6) Competence of Organization towards Improvement; 7) Time and Budget; 8)Detail Level; 9) Expansion Level and 10) Motivation of Operators
Available under Creative Commons-ShareAlike 4.0 International License (http:// creativecommons.org/licenses/by-sa/4.0/).
WCM requires all decisions to be made based on objective measured data and its analysis. Therefore, all the traditional data analysis tools such as scatter diagrams, histograms and checklists are used. Thus, from literature survey it is inferred that it is not possible to use the specific single tool to achieve world-class performance and address all the manufacturing components. It is inferred that to address all the components of the manufacturing system the following tools are necessary (see Table 1.2):
Main Tools Description
It is a methodology for the description and the analysis of a loss phenomenon (defects, failures malfunctions...). It based on the facts and the use of the 5 senses
4M or 5M
It is used by the list of possible factors (causes, sub-causes) that give rise to the phenomenon. For the 4M the causes are grouped into 4 categories: Methods; Materials; Machines; Mans. And for the 5M, there are the same 4M more the fifth that is the environment.
It is used to achieve excellence through improvement of the workplace in terms of order, organization and cleanliness. The technique is based on: Seiri (separate and order); Seiton (arrange and organize); Seiso (clean); Seiketsu (standardized); Shitsuke (maintaining and improving).
Table 1.2: Main Tools and description
11
Main Tools Description
Cleaning cycles
Are used for activities on Autonomous Maintenance, Workplace Organization and Professional Maintenance.
Inspection cycles
Are used for activities on Autonomous Maintenance, Workplace Organization and Professional Maintenance.
Maintenance cycles
Are used for activities on Autonomous Maintenance and Professional Maintenance.
Control cycles
Are used for activities on Autonomous Maintenance, Workplace Organization and Professional Maintenance.
FMEA-Failure Mode and Effect Analysis
It is used to prevent the potential failure modes.
Kanban It is a tag used for programming and production scheduling.
Kaizen (Quick, Standard, Major, Advanced)
It is a daily process, the purpose of which goes beyond simple productivity improvement. It is also a process that, when done correctly, humanizes the workplace, eliminates overly hard work.
Two Videocamera Method
It is used to perform the video recording of the transactions in order to optimize them.
MURI Analysis Ergonomic analysis of workstations.
Analysis Analysis of irregular operations.
Table 1.2: Main Tools and description
13
Main Tools Description
Analysis Analysis of losses.
Spaghetti Chart
It is a graphical used to detail the actual physical flow and distances involved in a work process.
Golden Zone & Strike zone Analysis
Analysis of work operations in the area that favors the handling in order to minimize movement to reduce fatigue.
OPL (One Point Lesson)
It is a technique that allows a simple and effective focus in a short time on the object of the training.
SOP (Standard Operation Procedure)
Standard procedure for work.
JES (Job Elementary Sheet)
Sheet of elementary education.
Visual Aid It is a set of signals that facilitates the work and communication within the company.
Poka Yoke
It is a prevention technique in order to avoid possible human errors in performance of any productive activity.
TWTTP (The way to teach people)
It is an interview in 4 questions to test the level of training on the operation to be performed.
(Human Error Root Cause Analysis)
It is a technique for the investigation of events of interest, in particular accidents, which examines what happened researching why it happened.
Table 1.2: Main Tools and description
14