
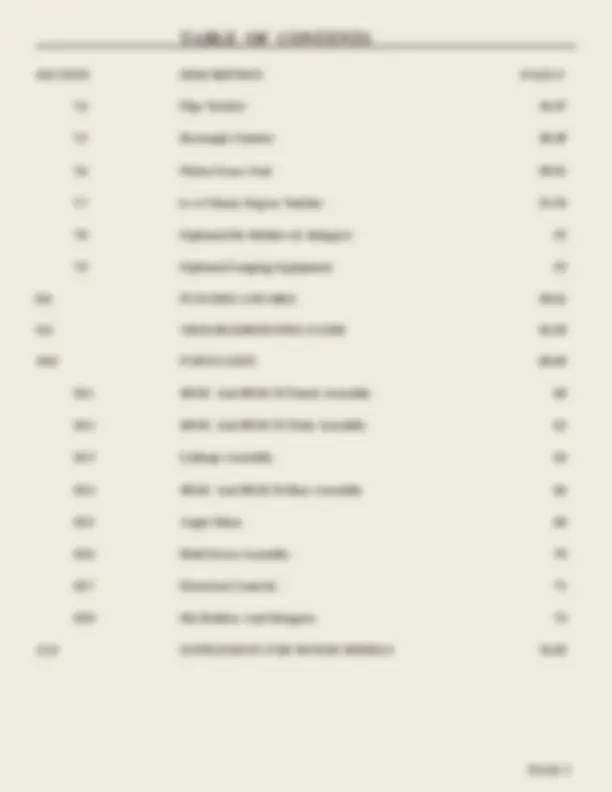
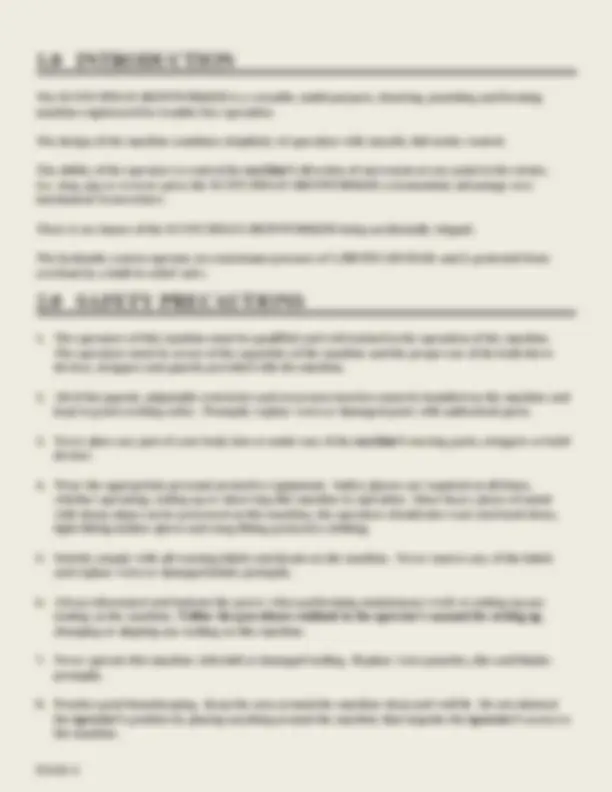
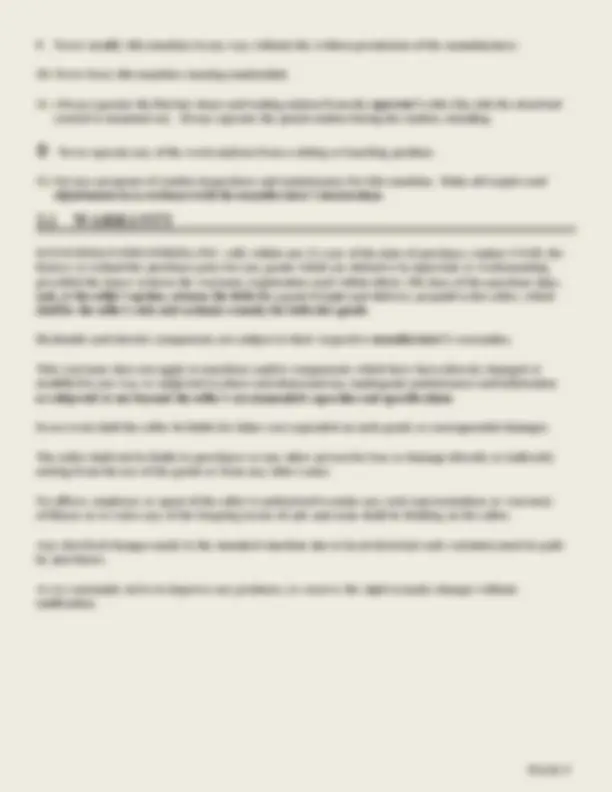
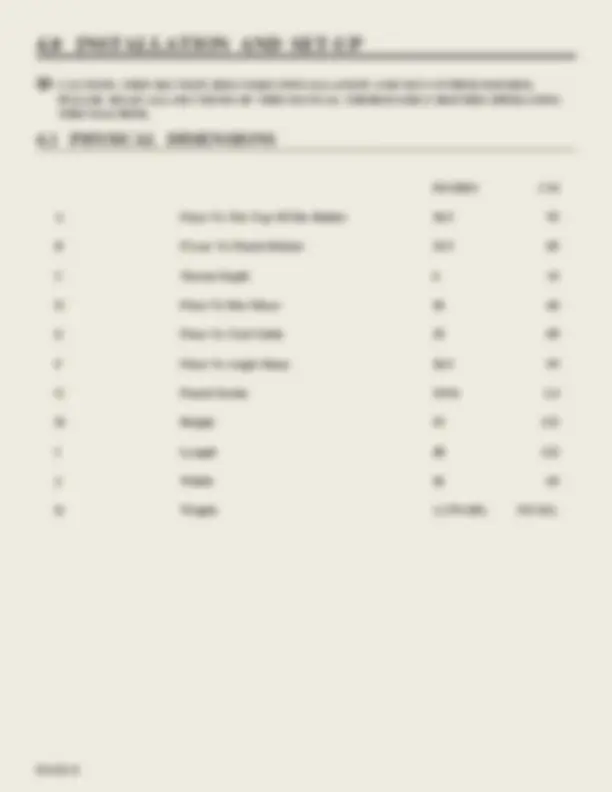
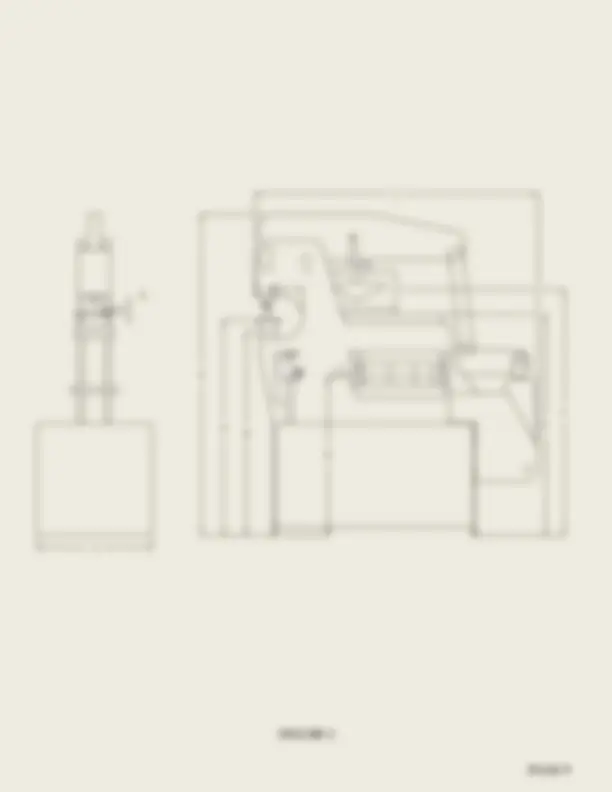
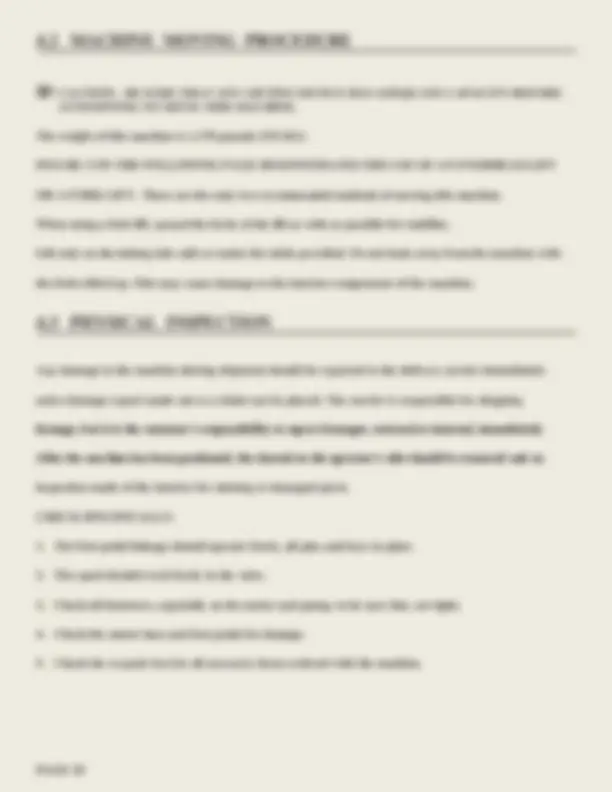
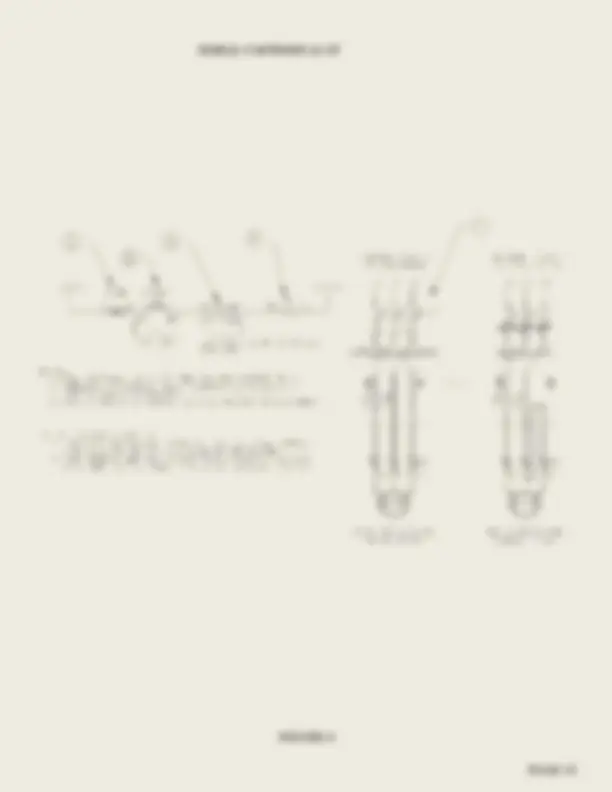
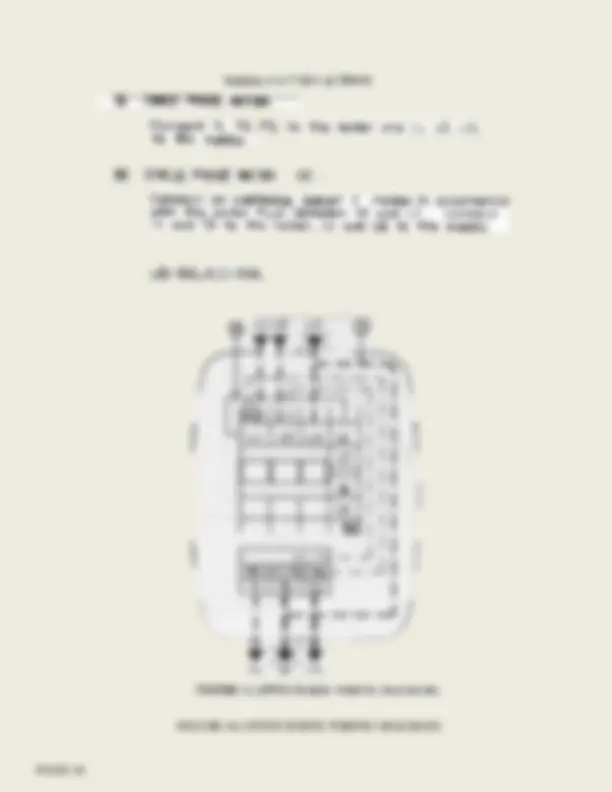
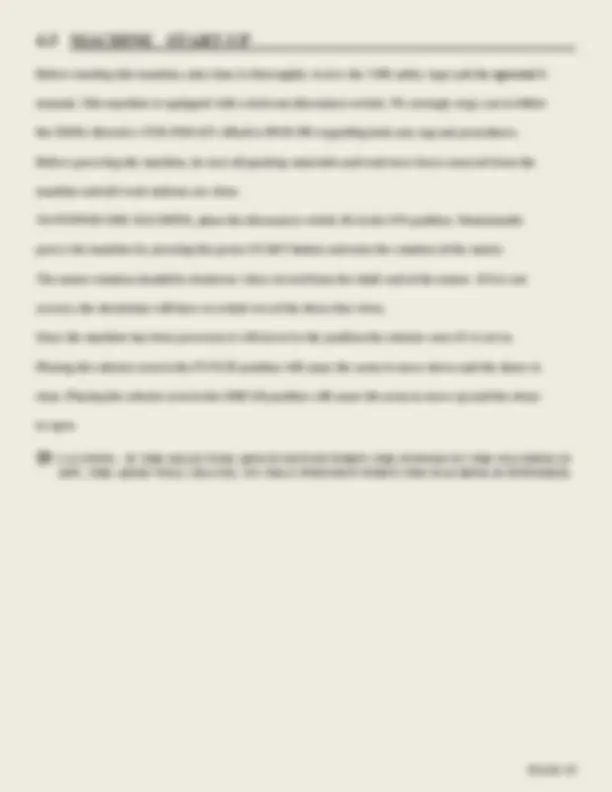
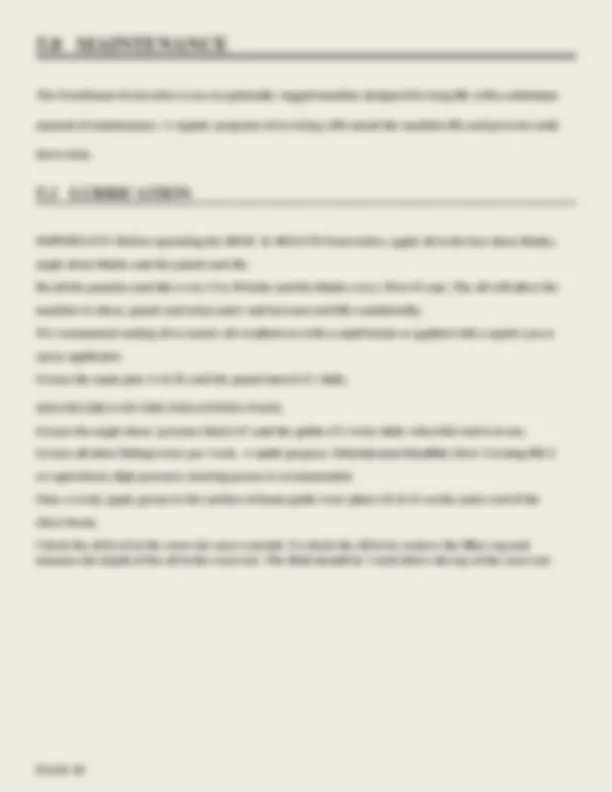
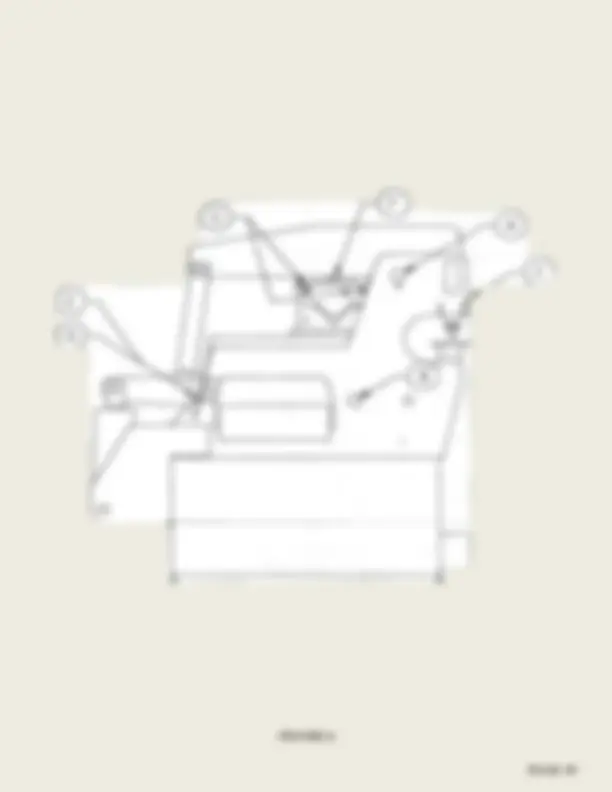

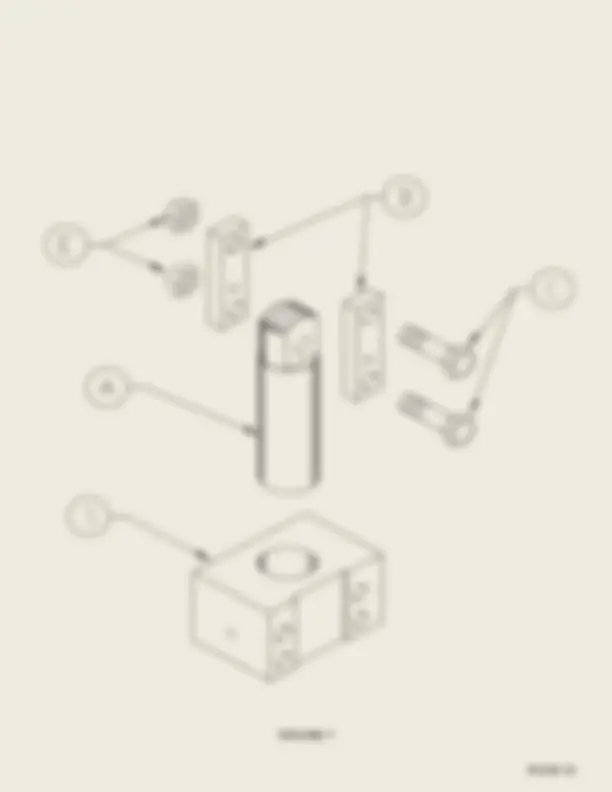
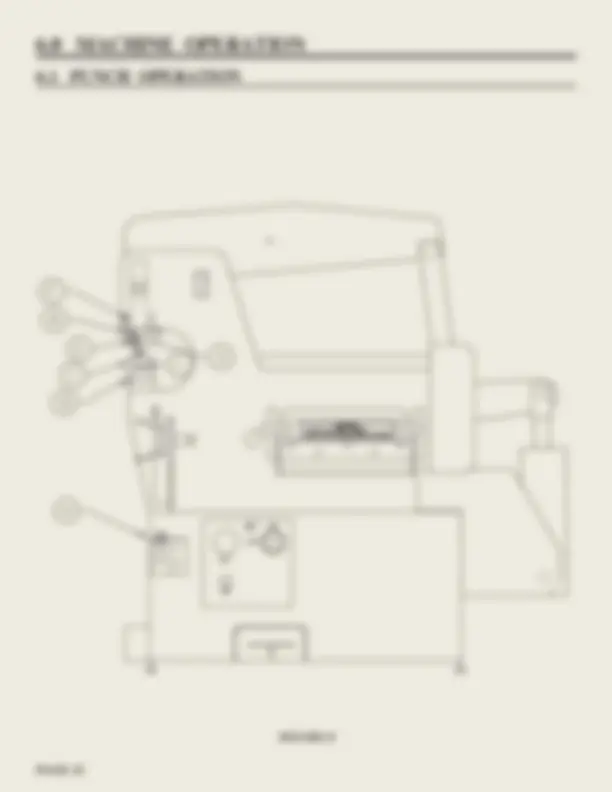
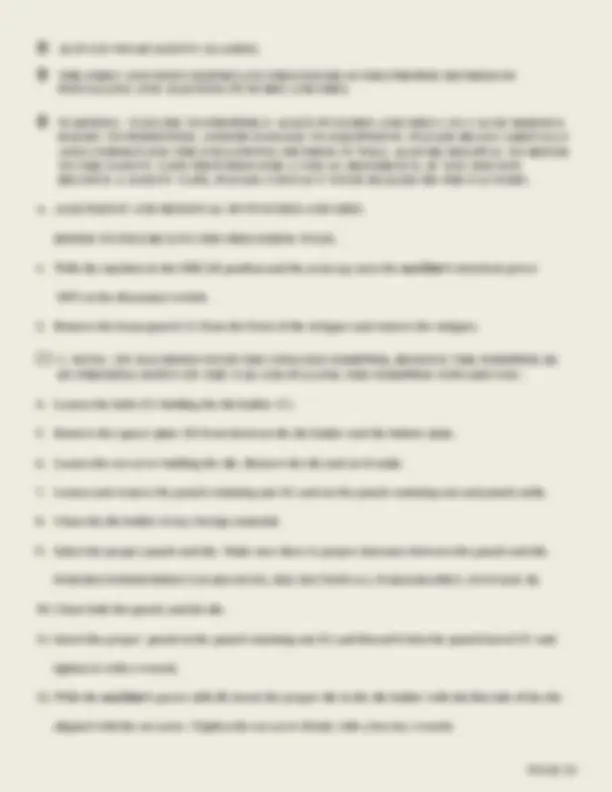
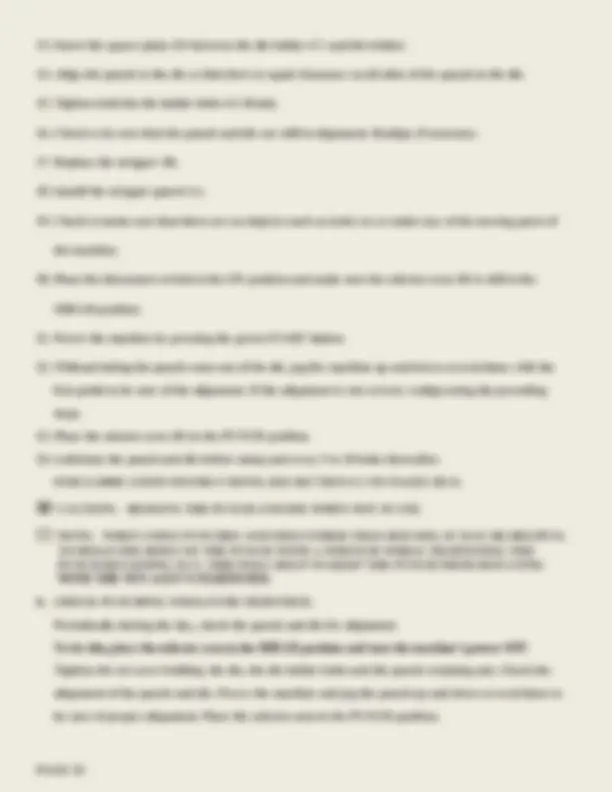
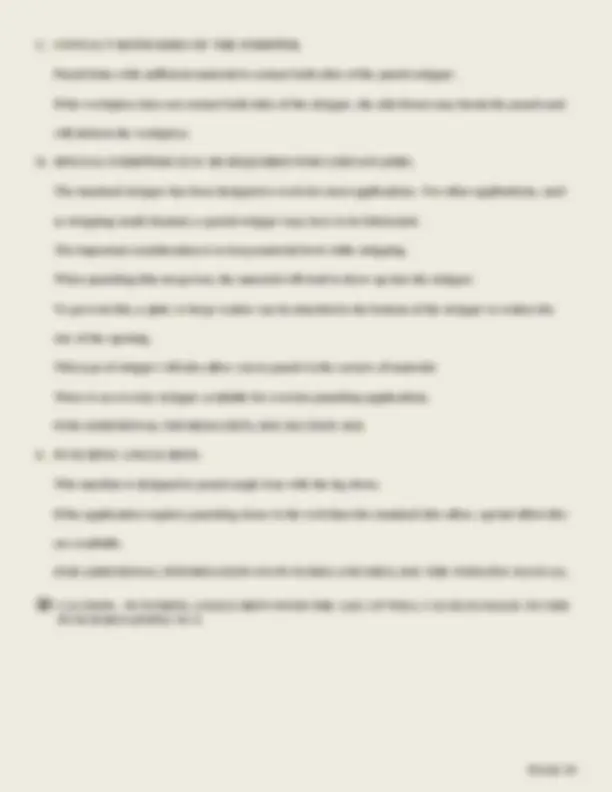
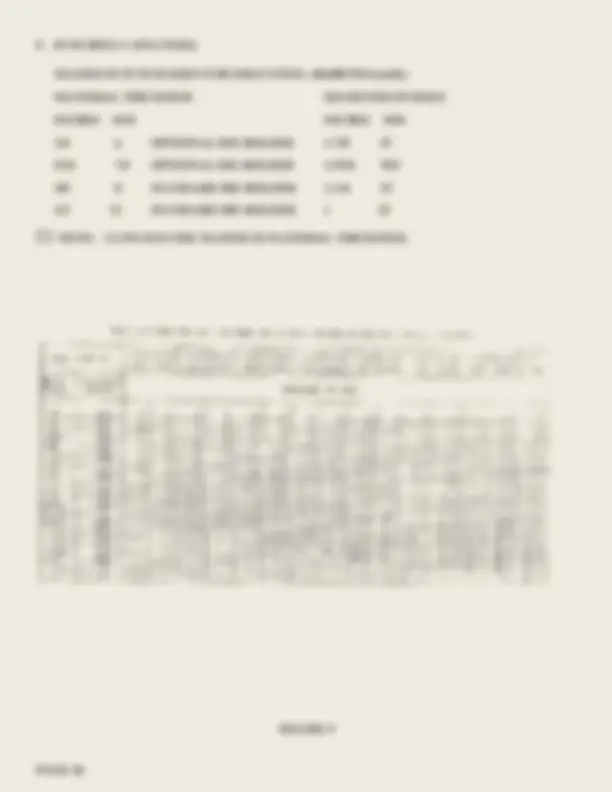
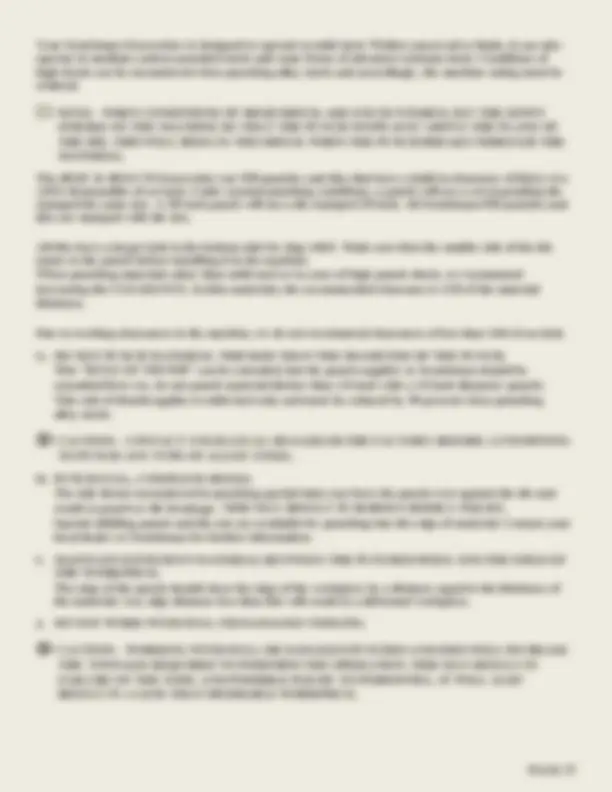
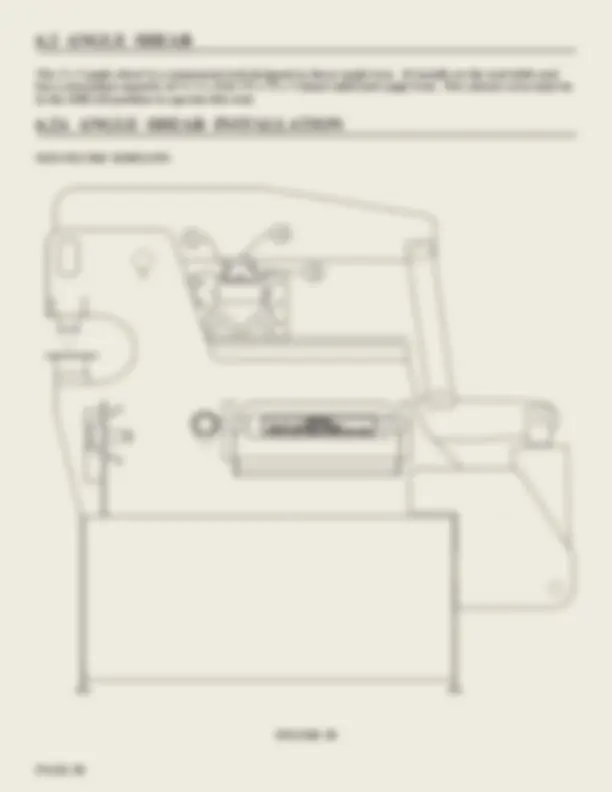
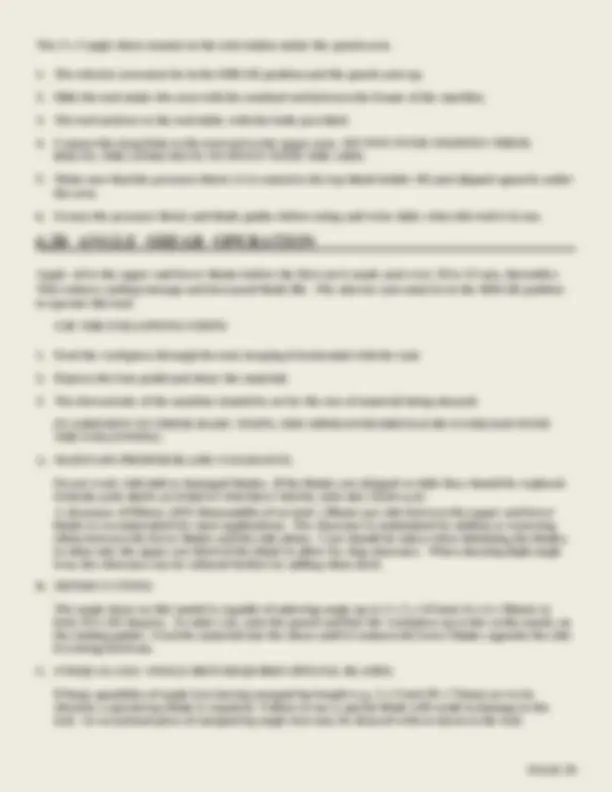
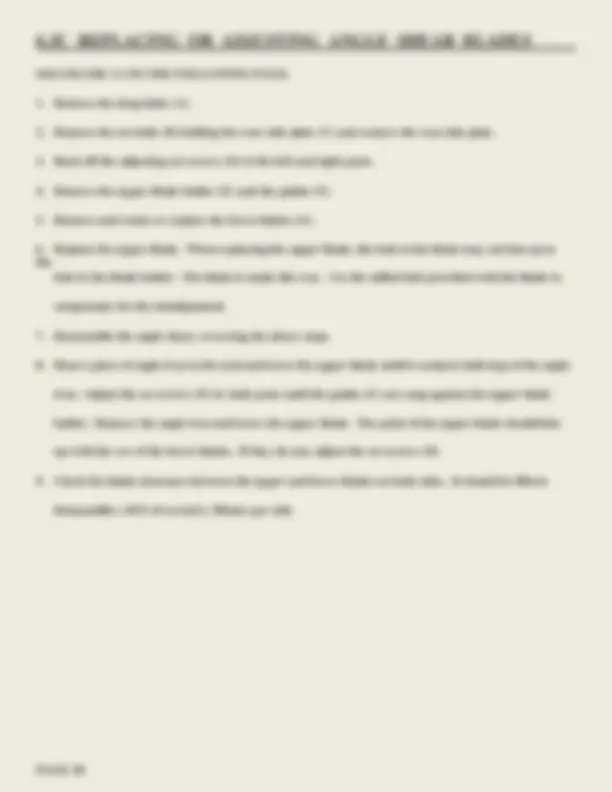
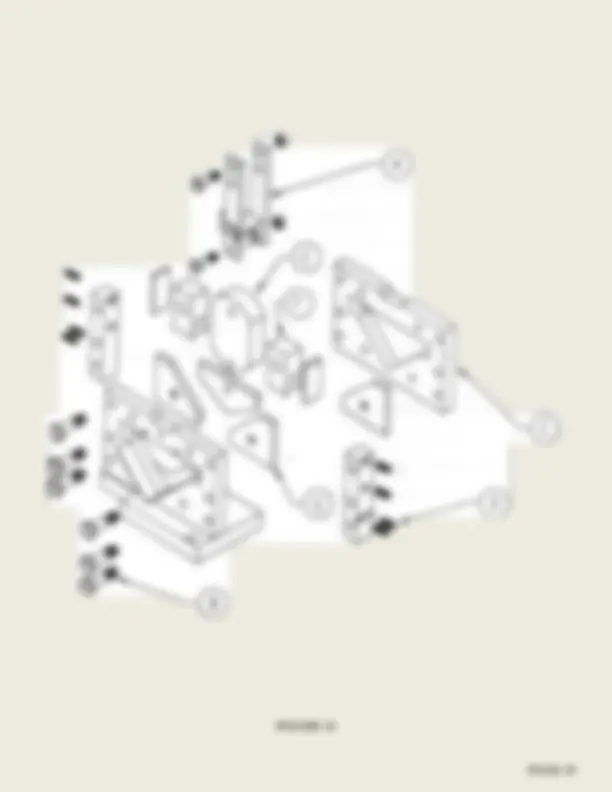
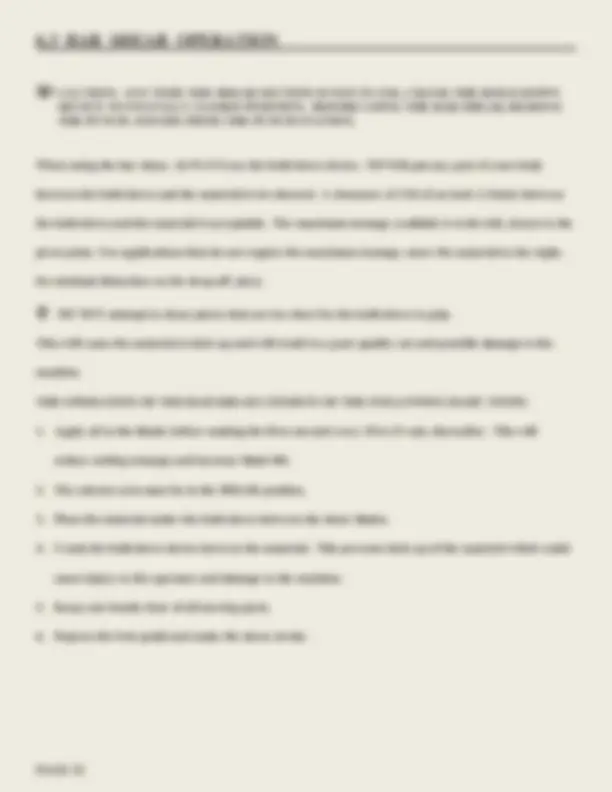
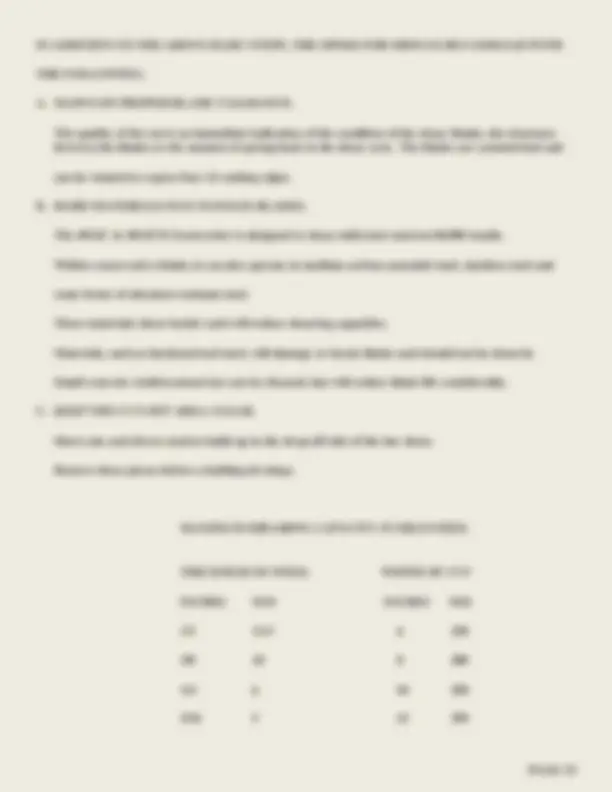
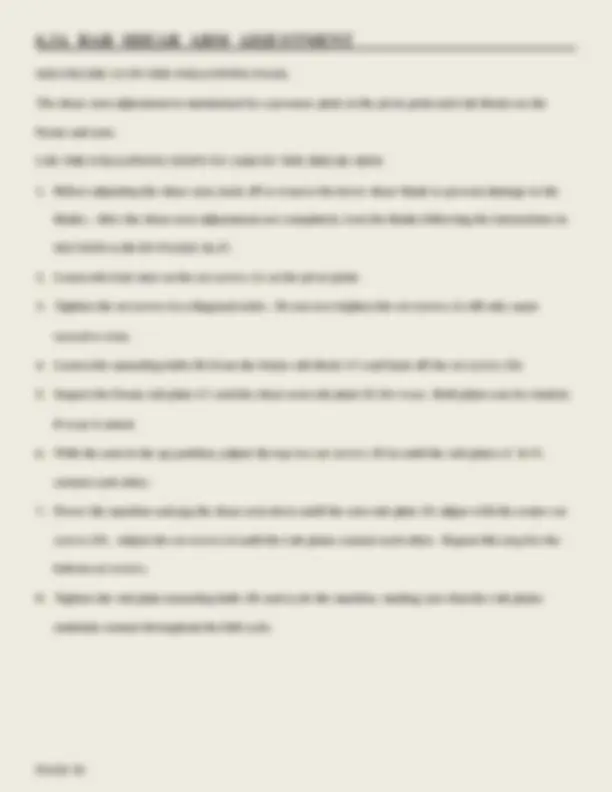

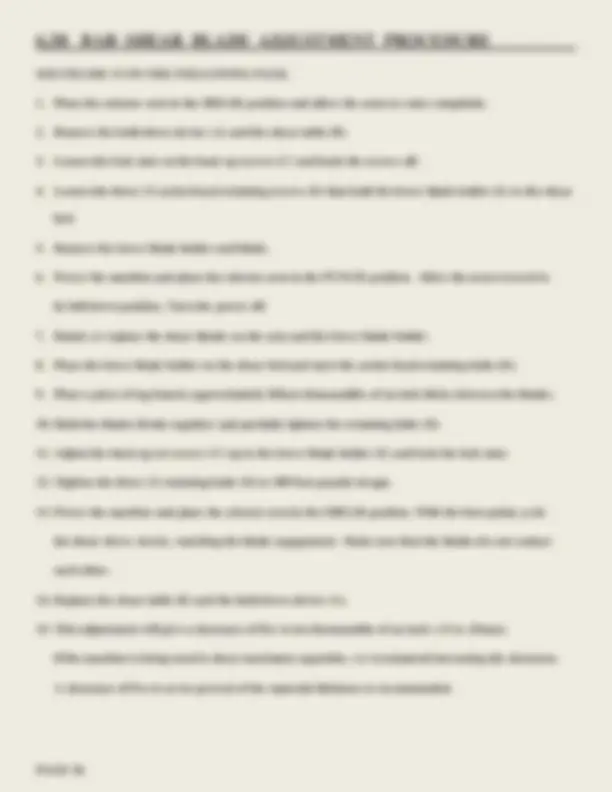
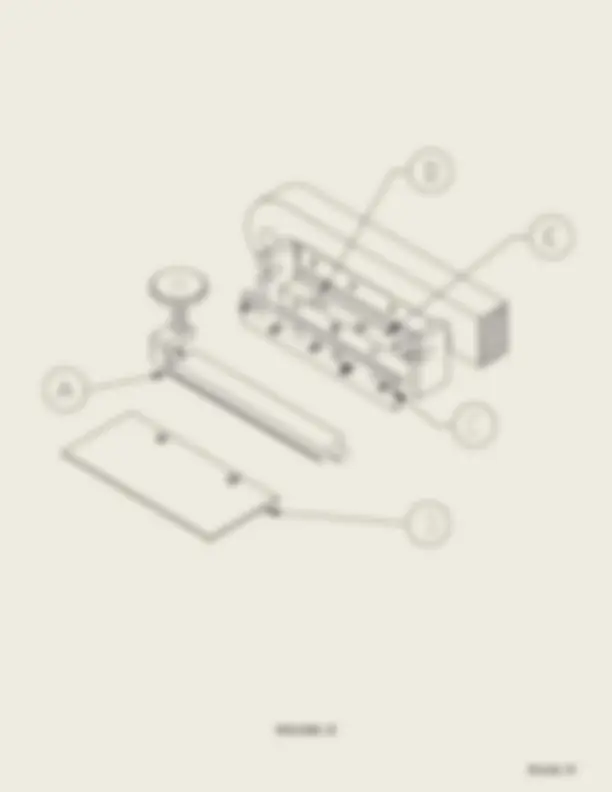
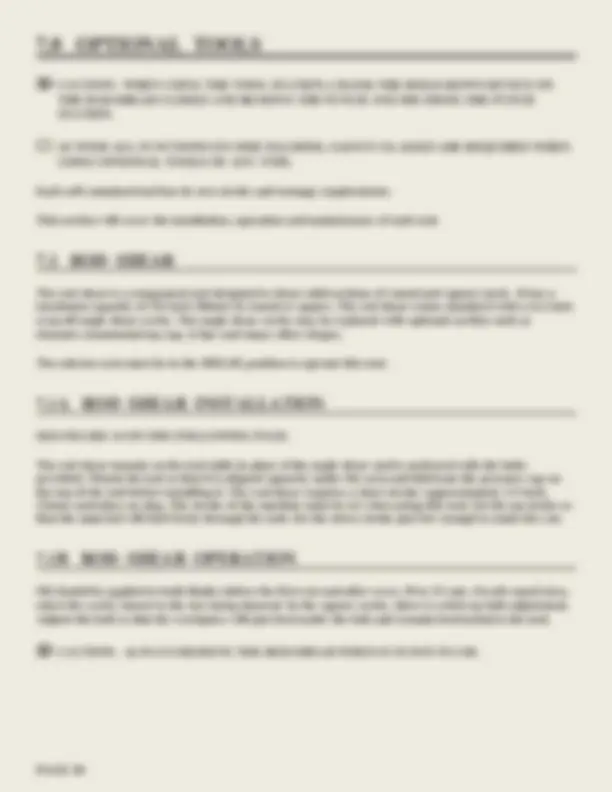
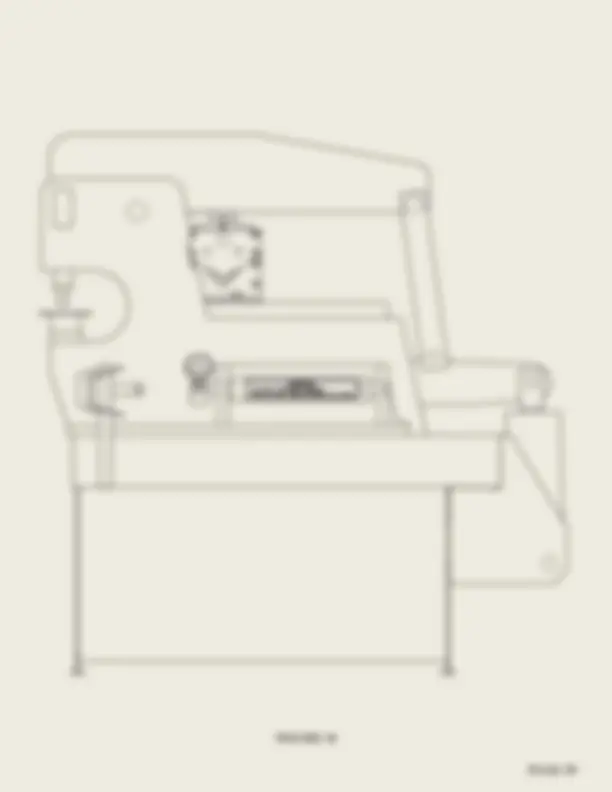
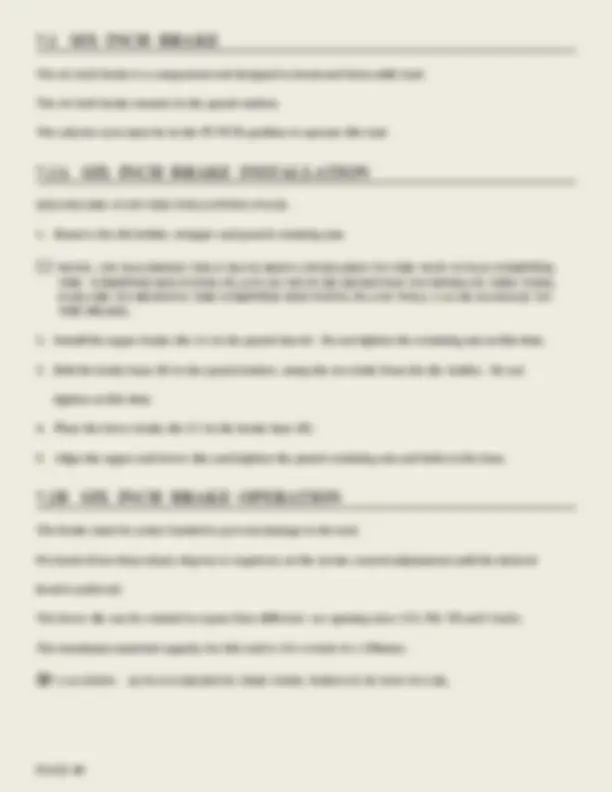
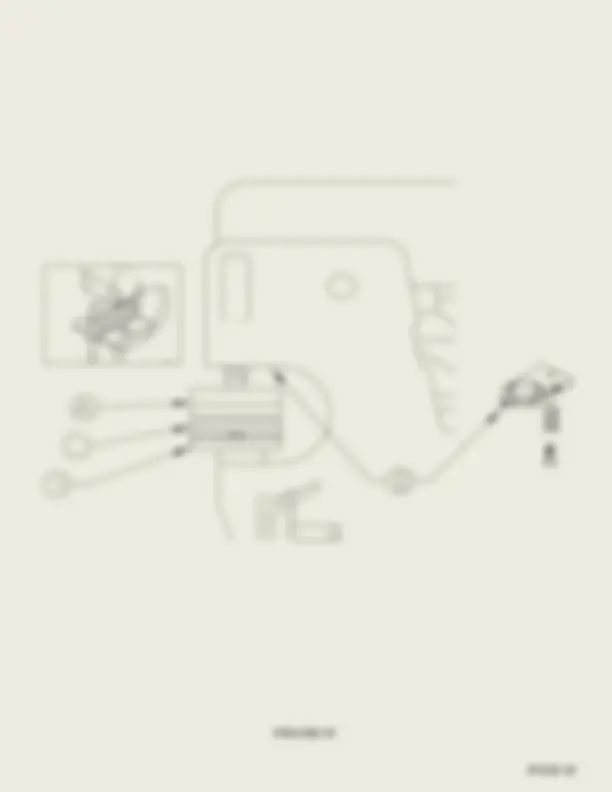
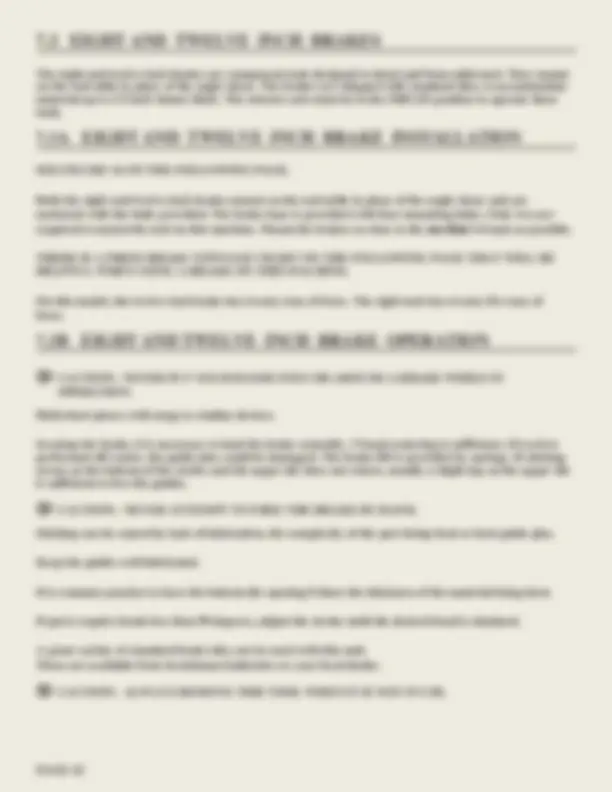
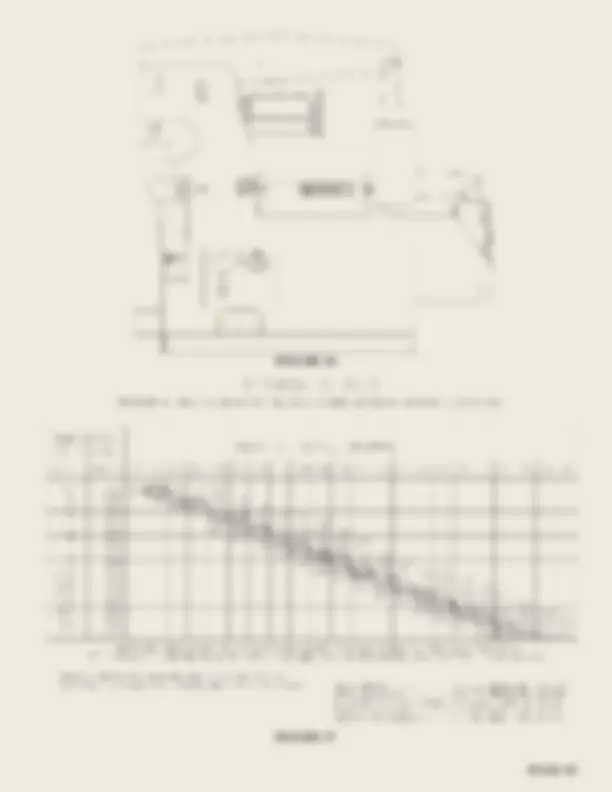

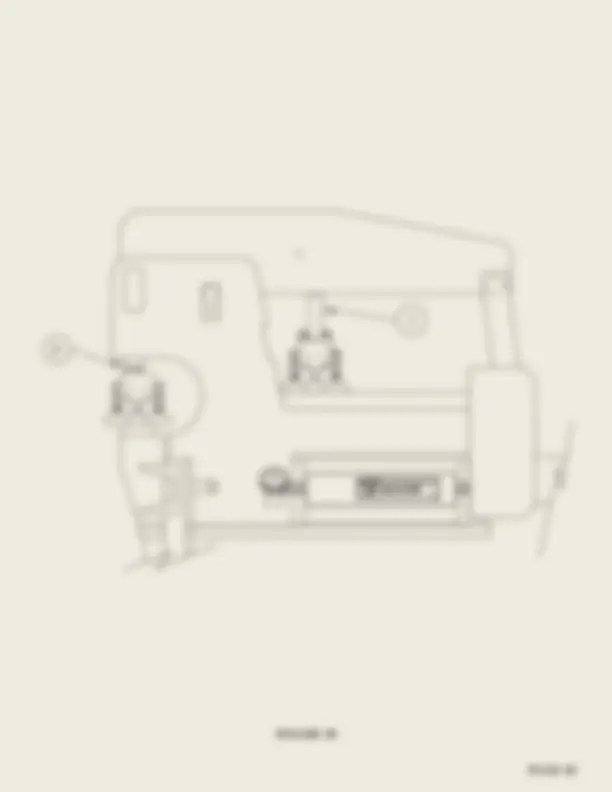

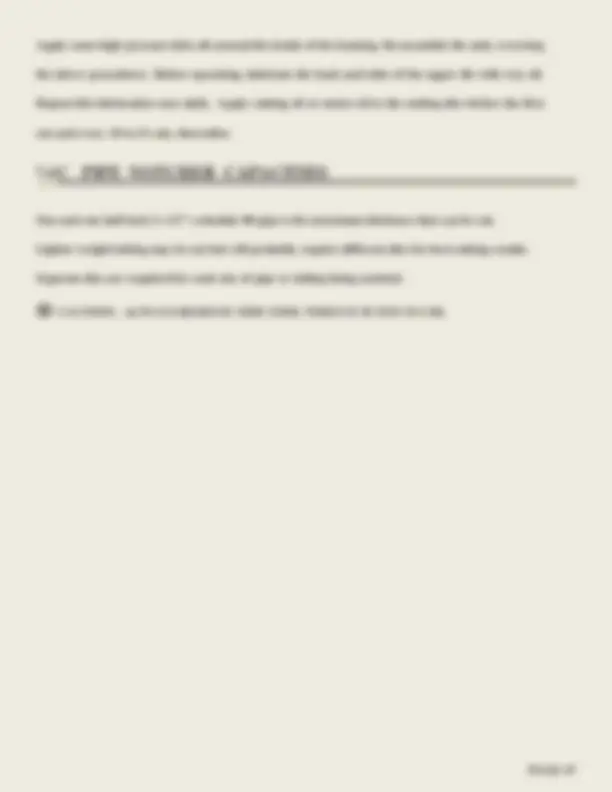
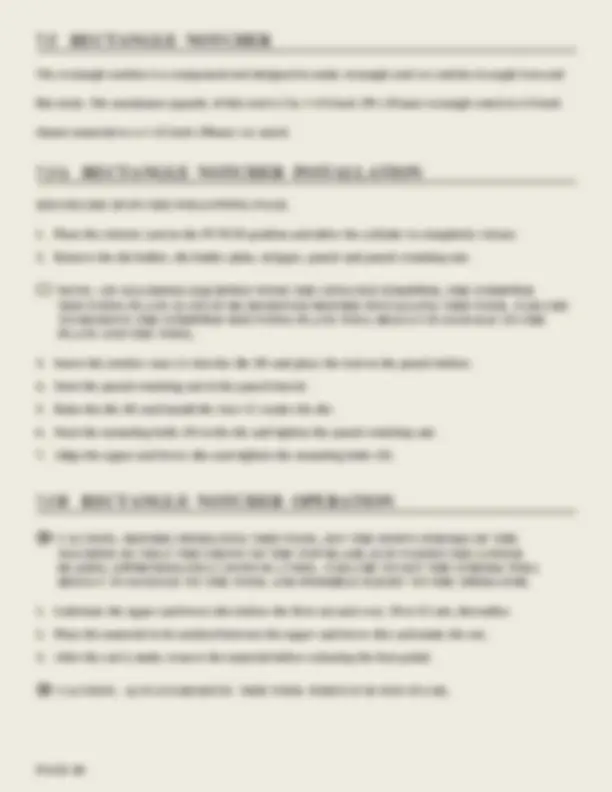
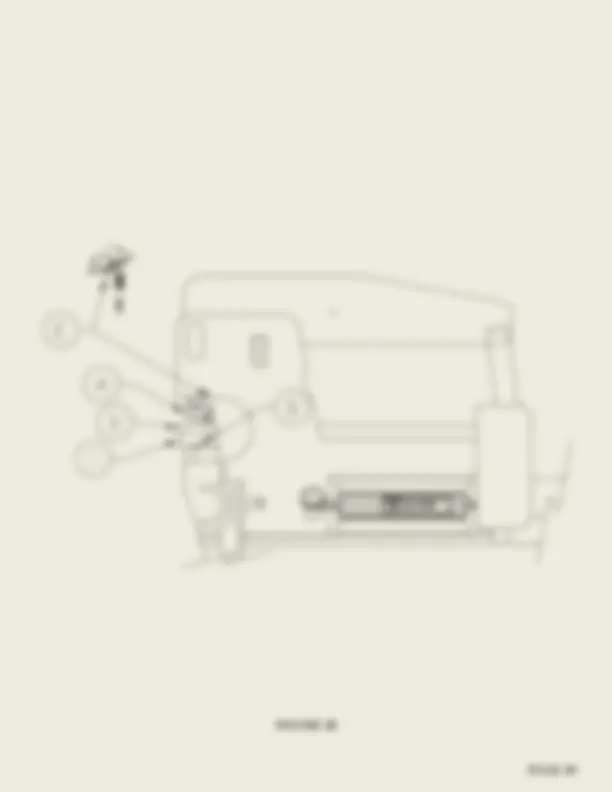
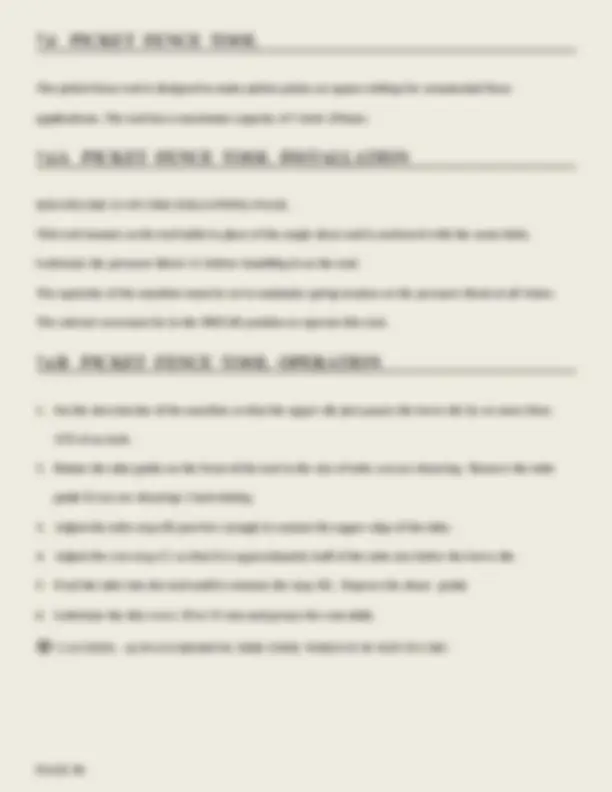
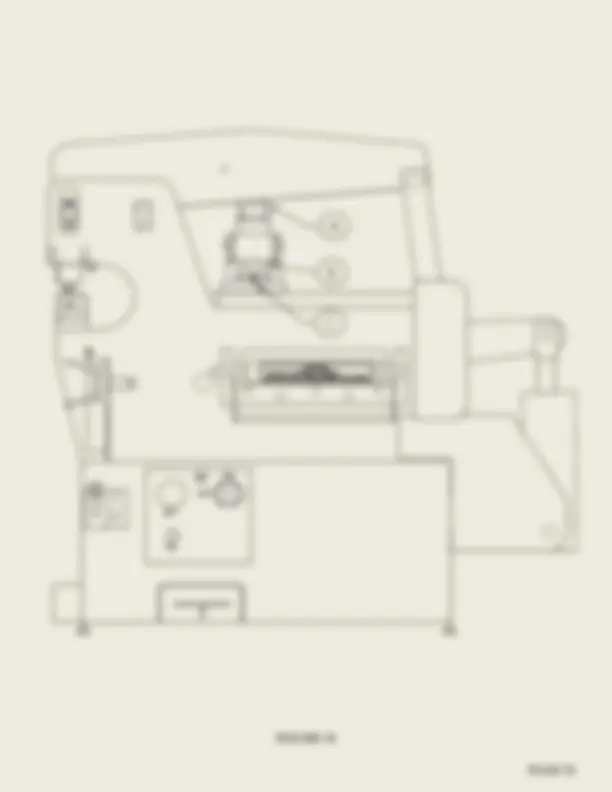
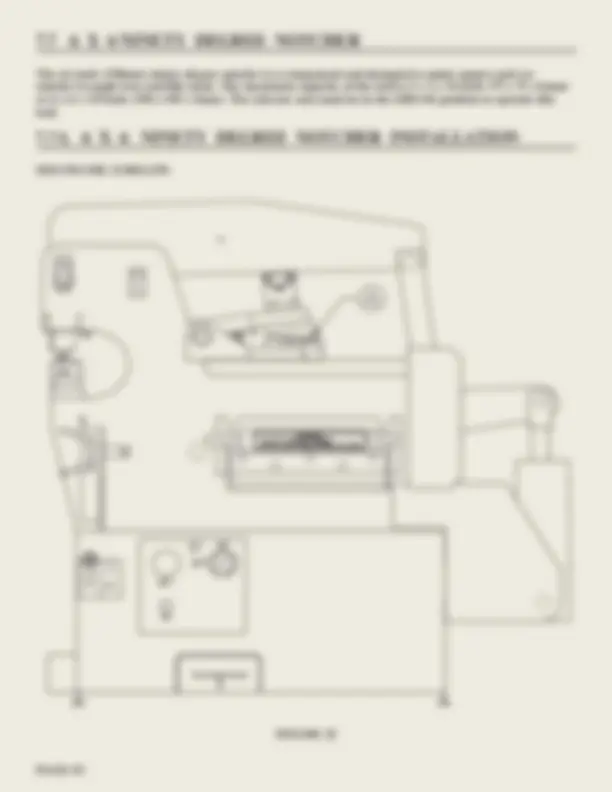
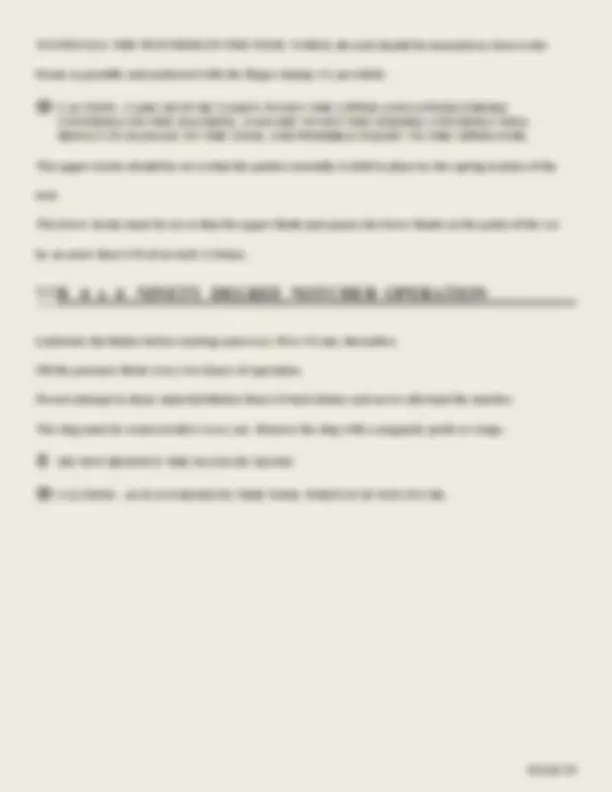
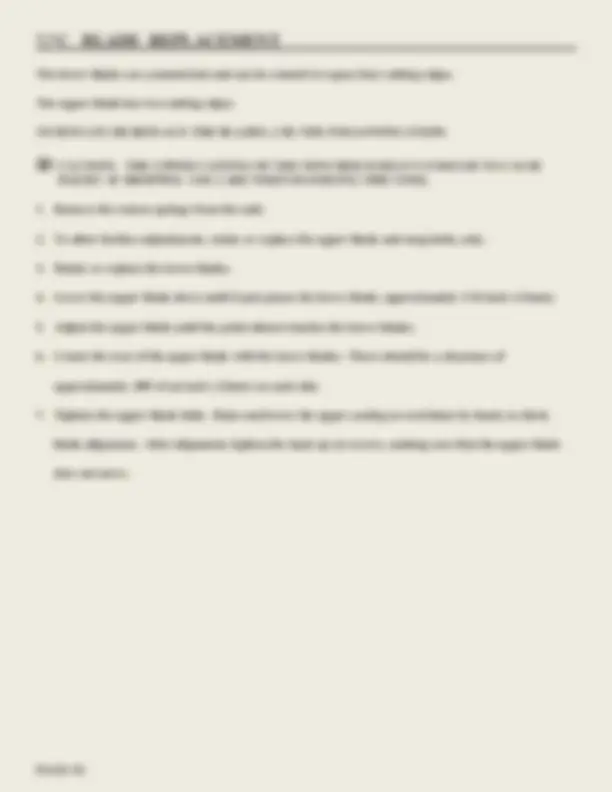
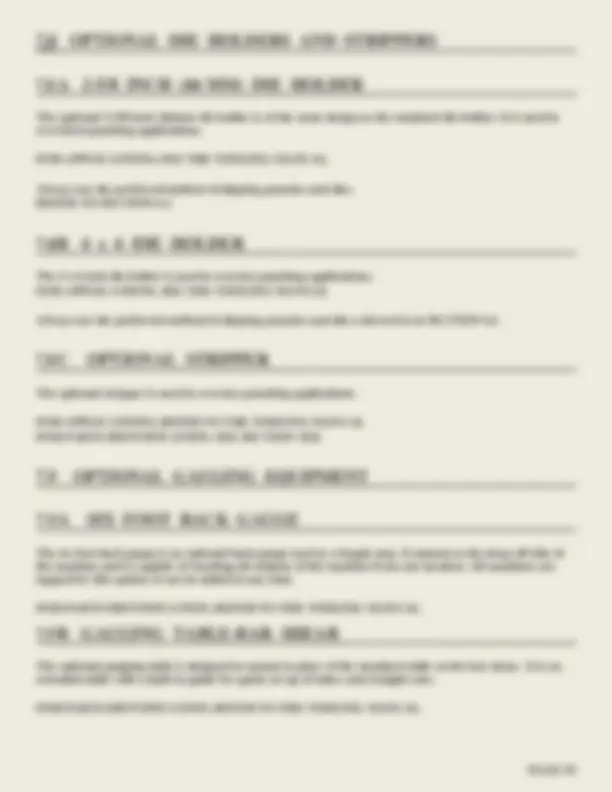
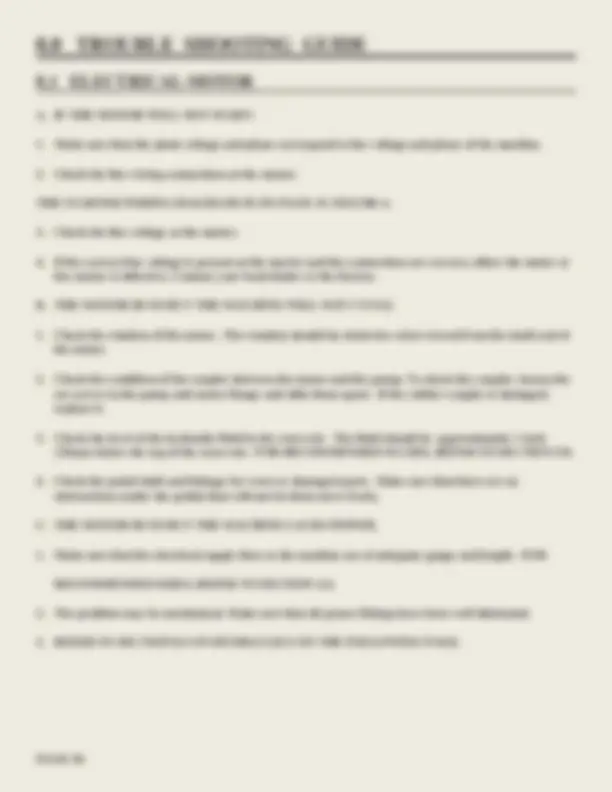
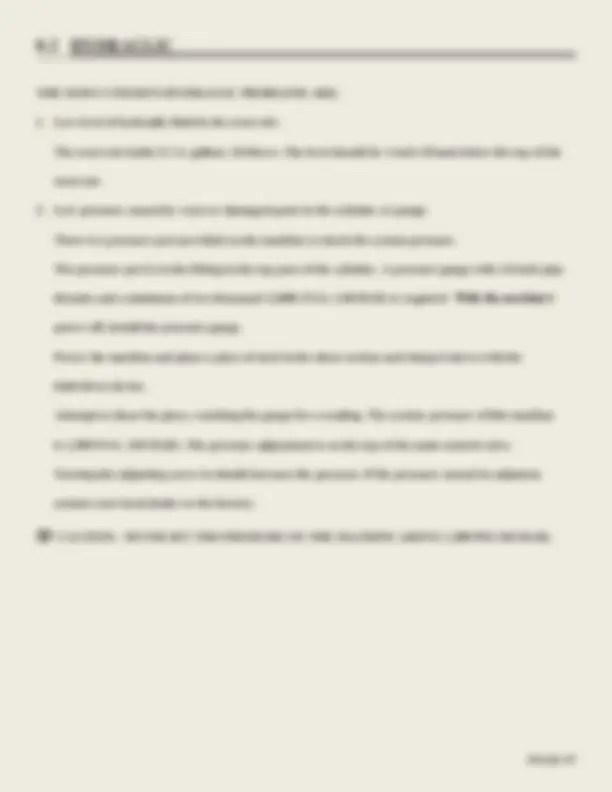
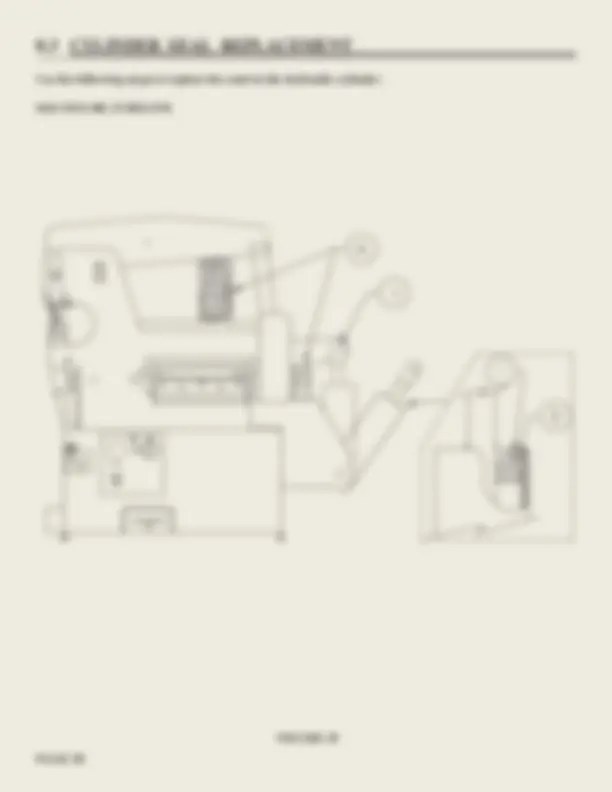
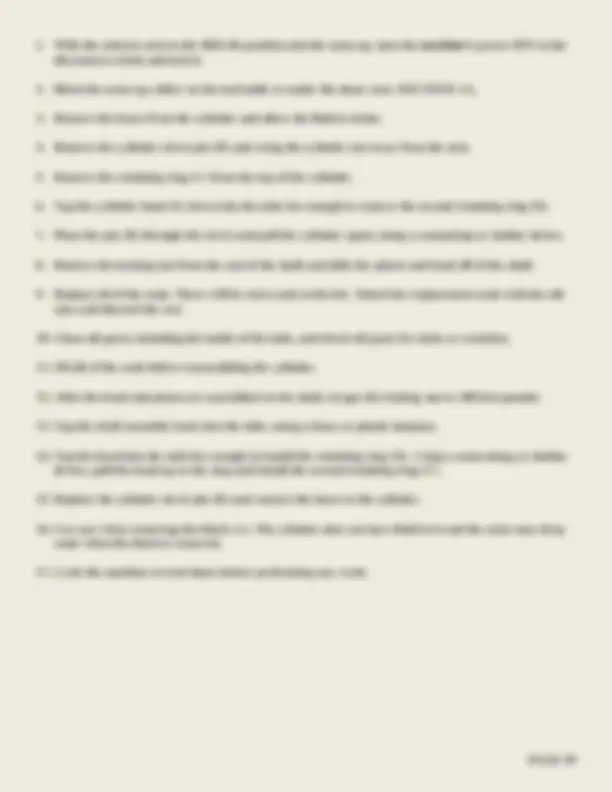
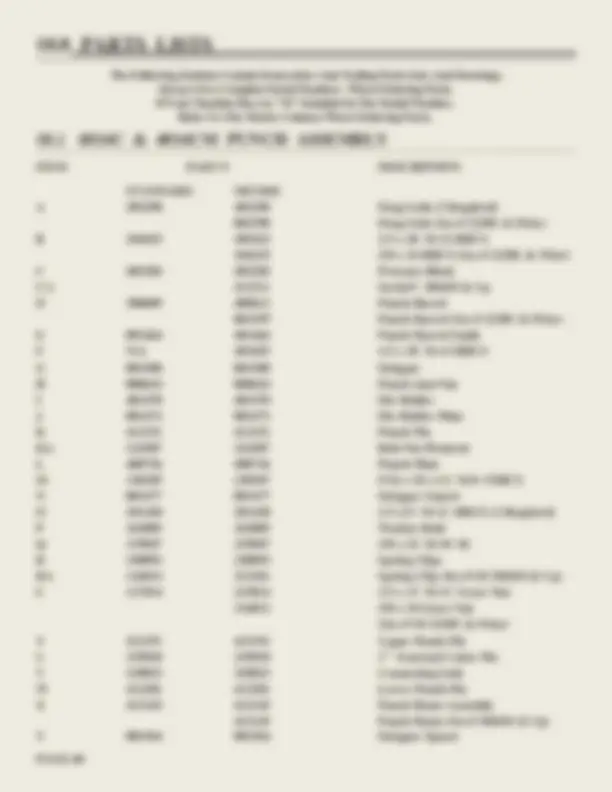
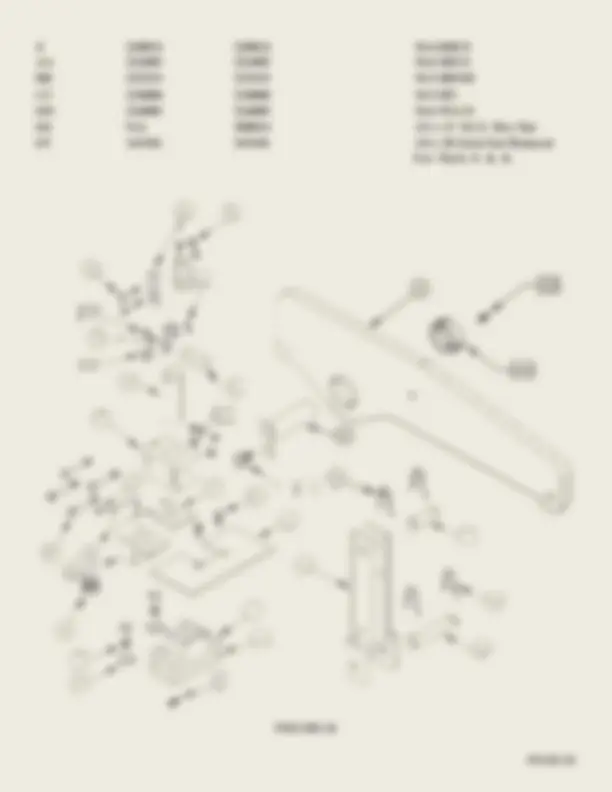
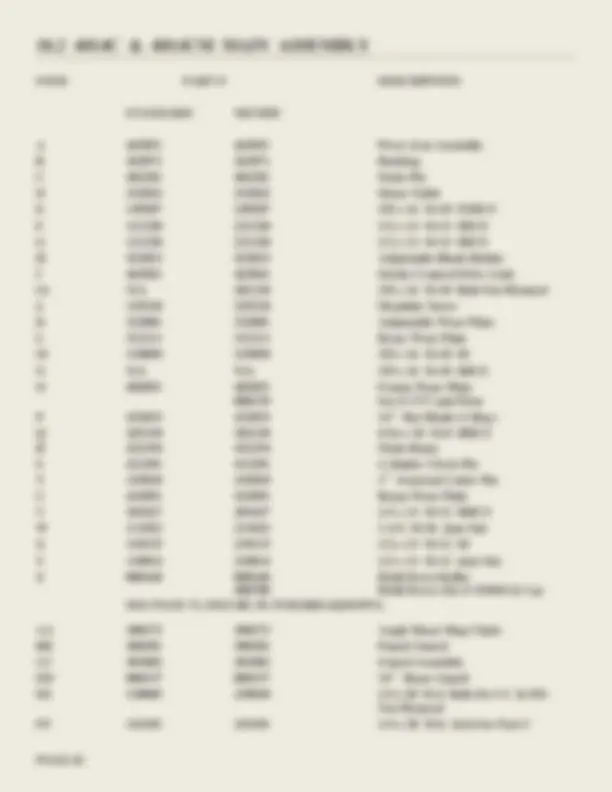
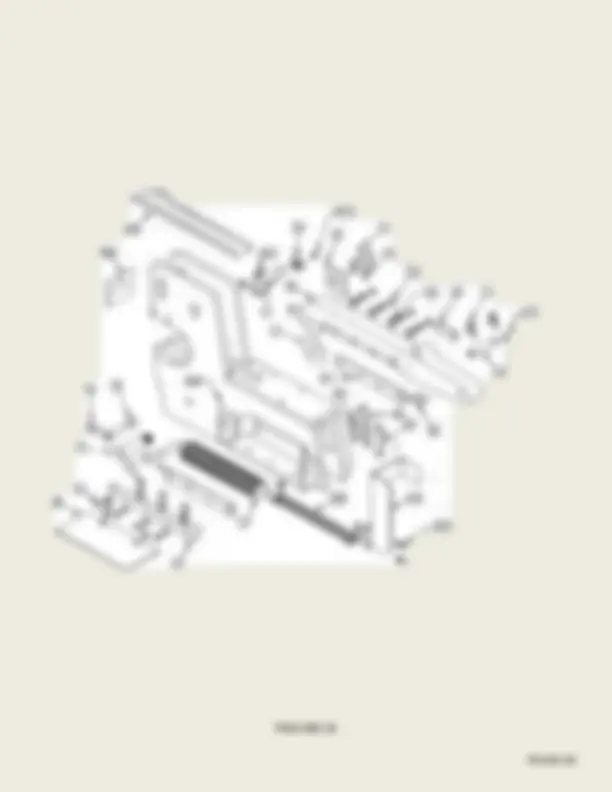
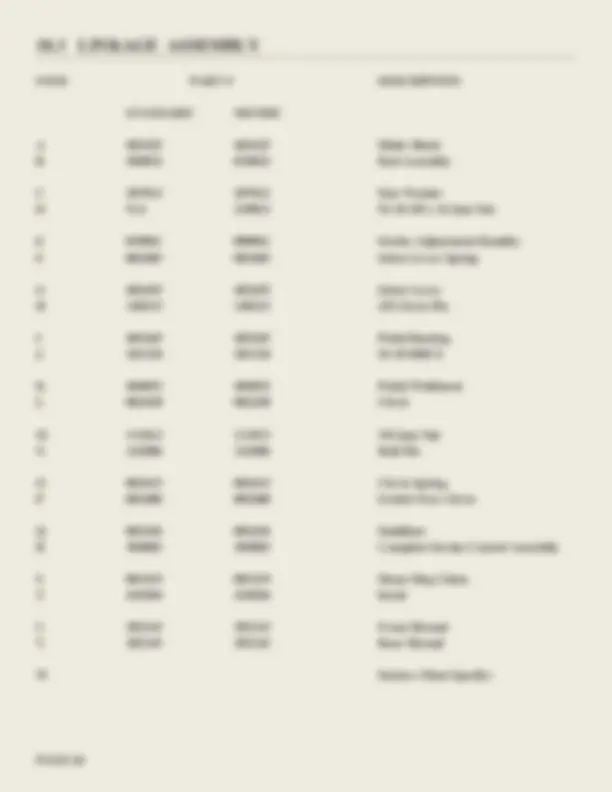
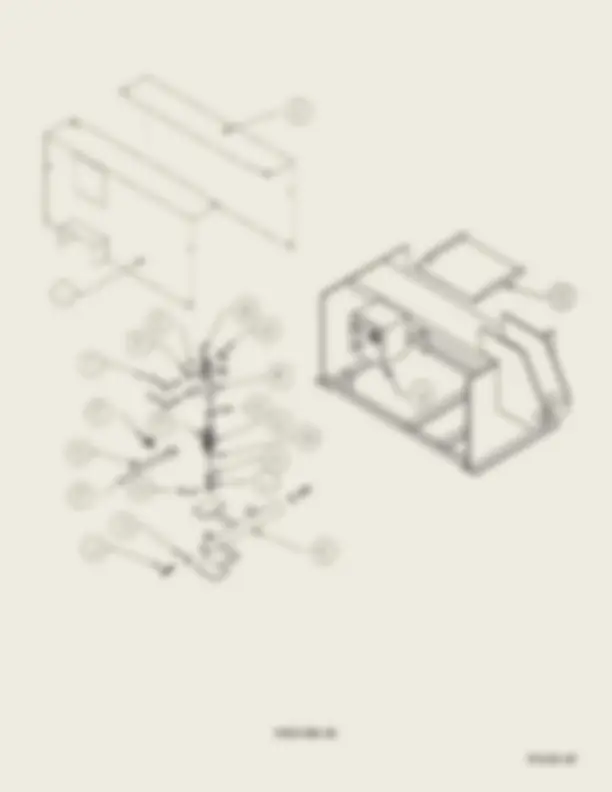
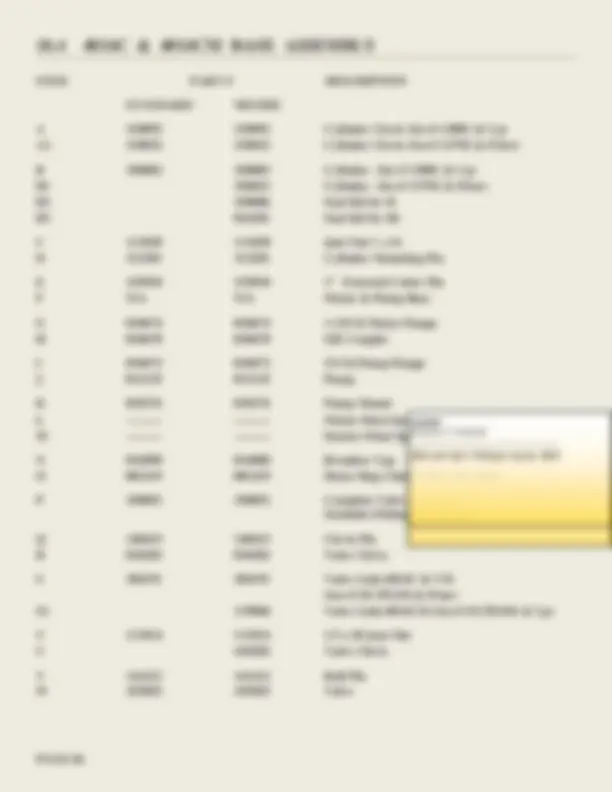
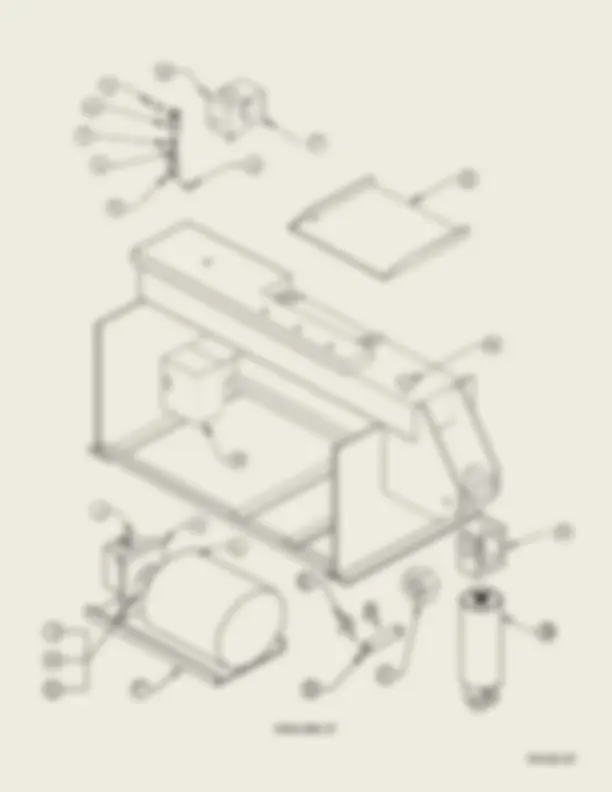
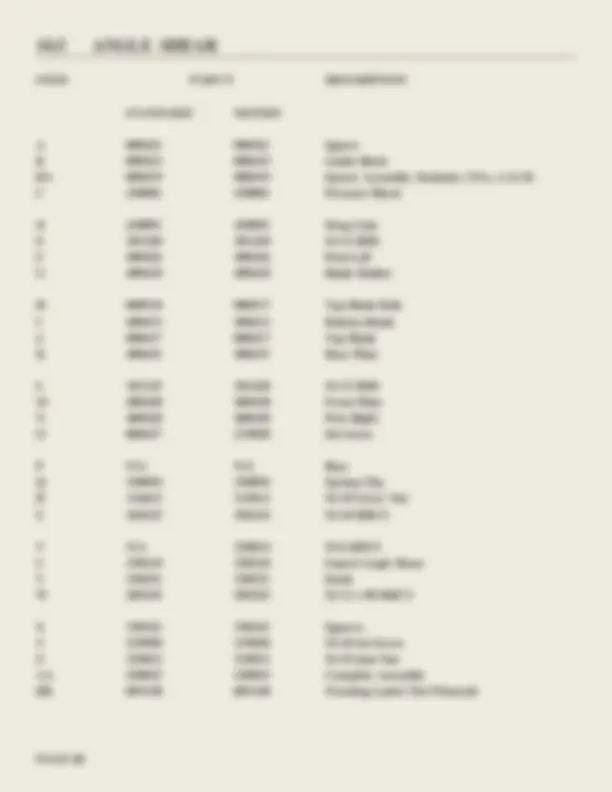
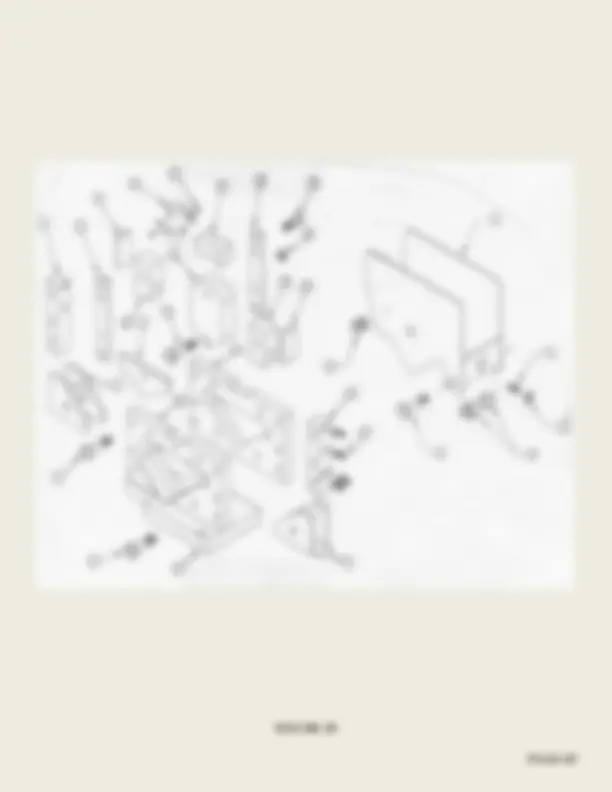
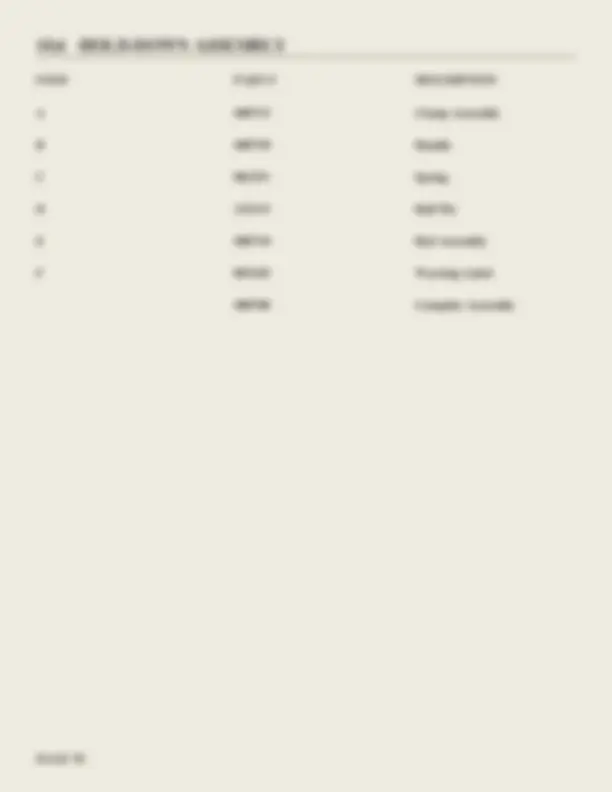
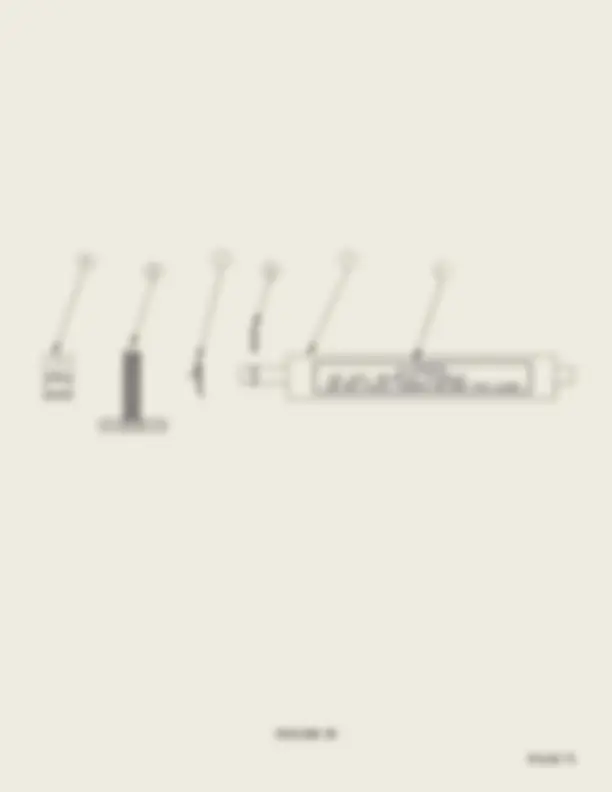
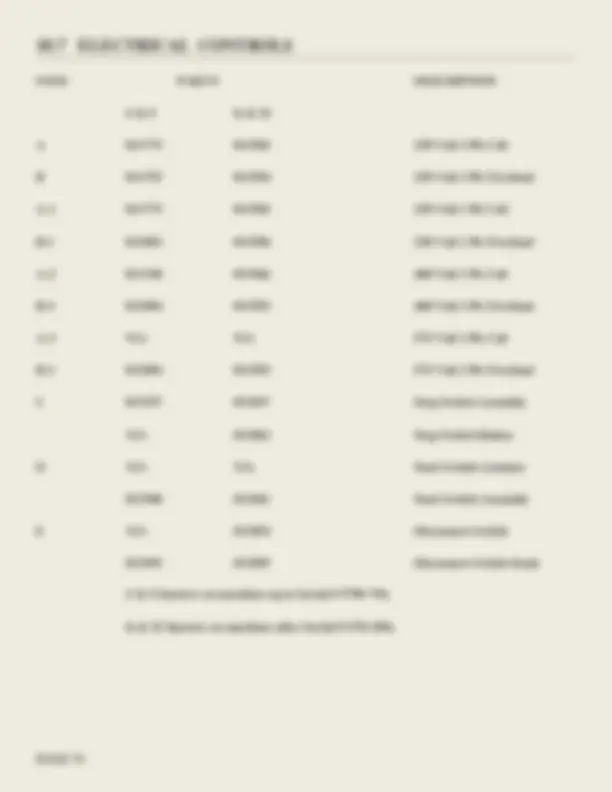
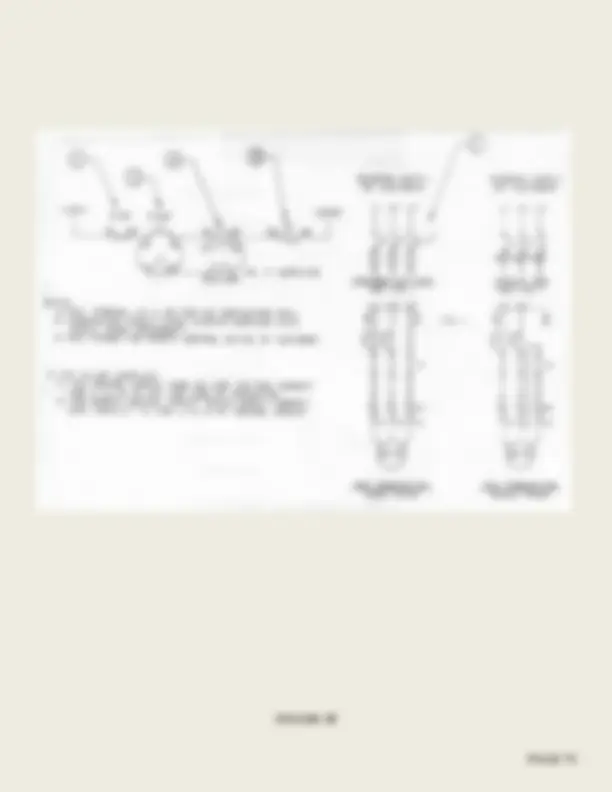
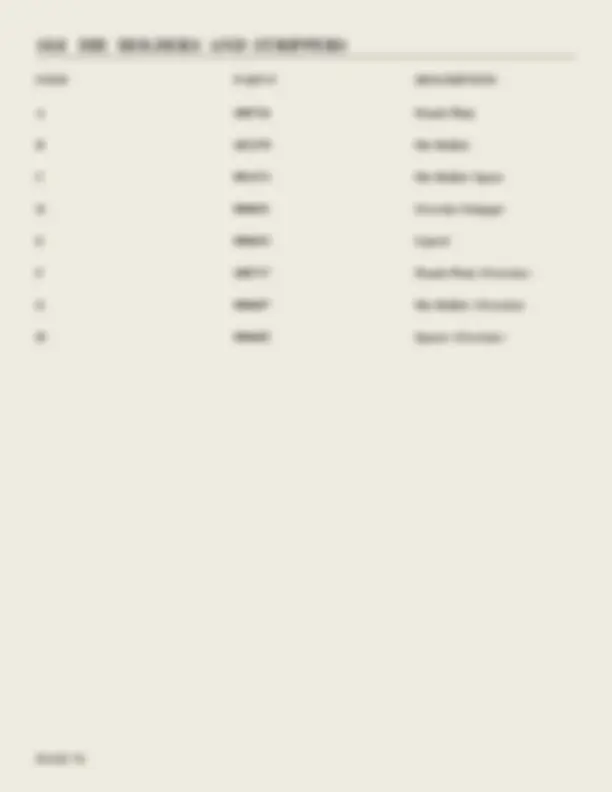
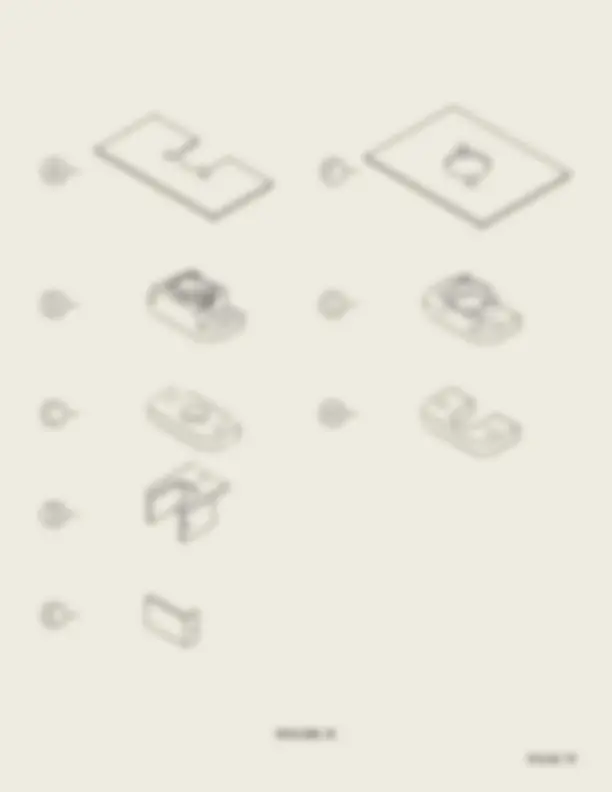
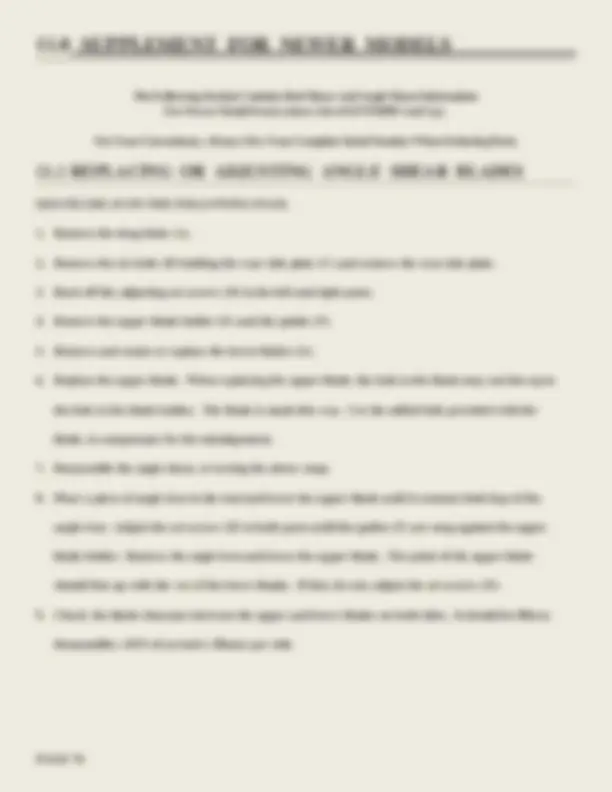
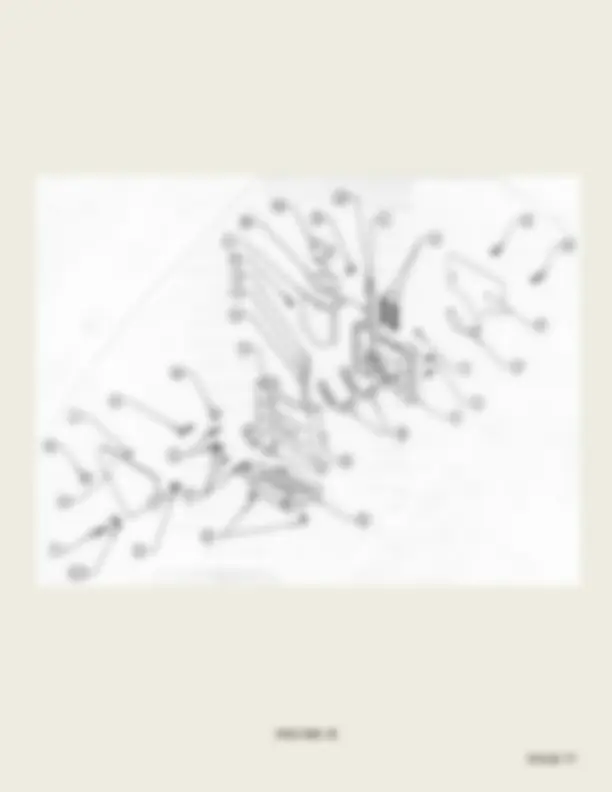
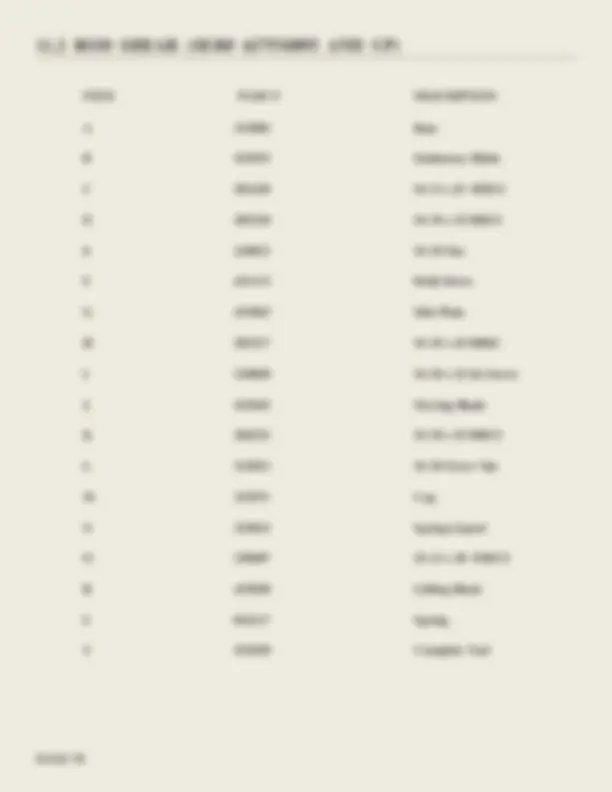
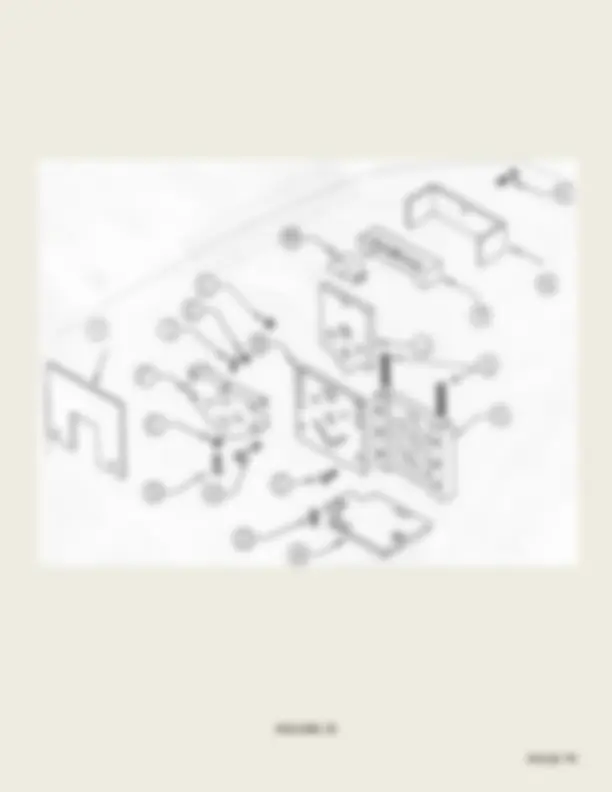
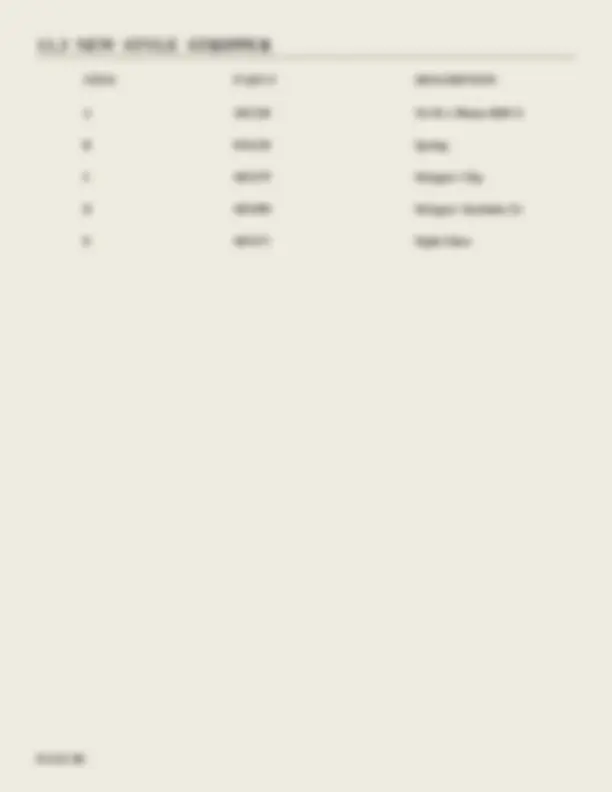
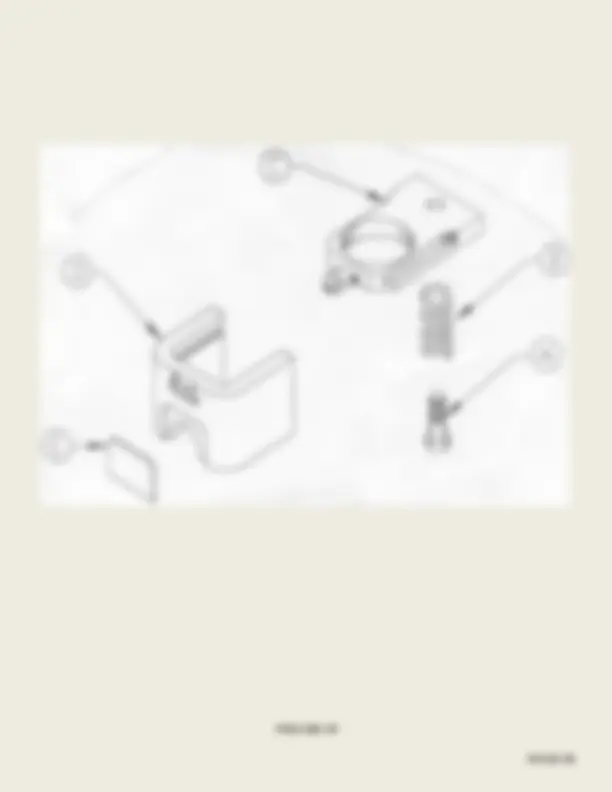
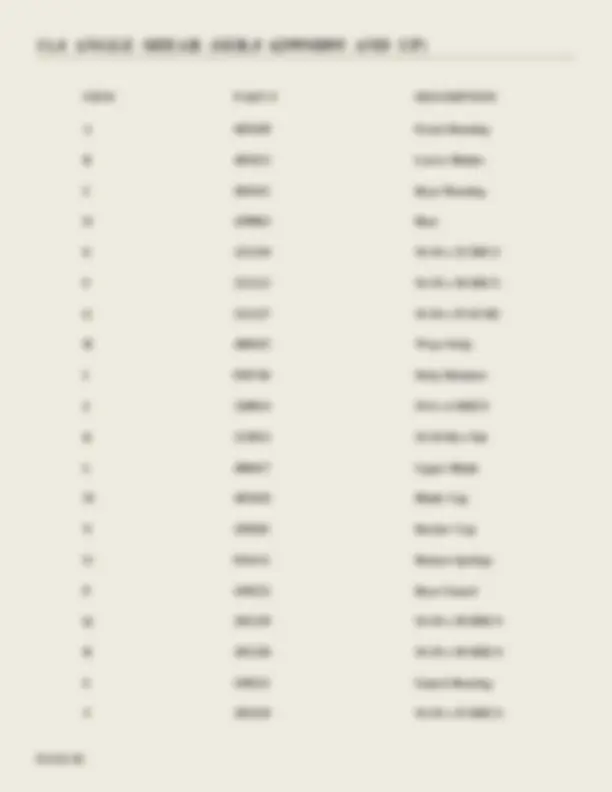
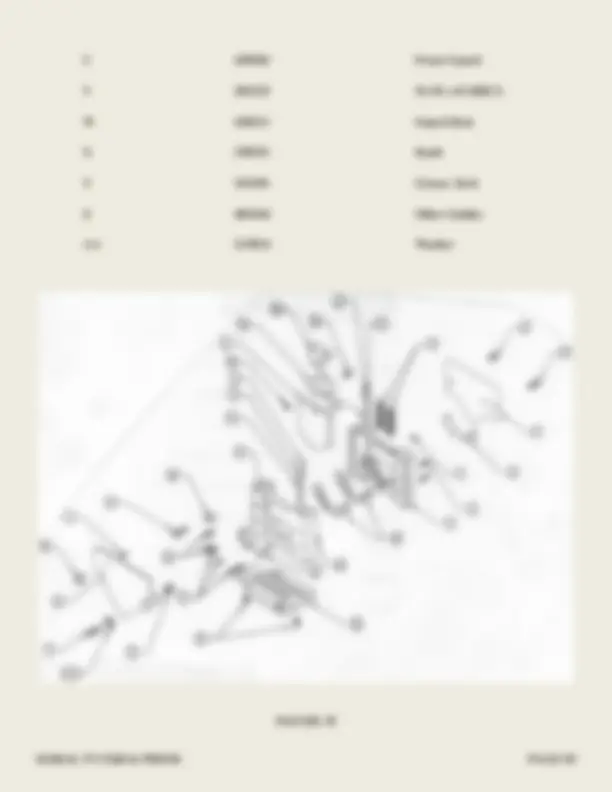
Study with the several resources on Docsity
Earn points by helping other students or get them with a premium plan
Prepare for your exams
Study with the several resources on Docsity
Earn points to download
Earn points by helping other students or get them with a premium plan
Community
Ask the community for help and clear up your study doubts
Discover the best universities in your country according to Docsity users
Free resources
Download our free guides on studying techniques, anxiety management strategies, and thesis advice from Docsity tutors
NCCER Certified Ironworker Study Guide
Typology: Exams
1 / 83
This page cannot be seen from the preview
Don't miss anything!
1.0 INTRODUCTION
The SCOTCHMAN IRONWORKER is a versatile, multi-purpose, shearing, punching and forming machine engineered for trouble free operation.
The design of the machine combines simplicity of operation with smooth, full stroke control.
The ability of the operator to control the machine’s direction of movement at any point in the stroke, (i.e. stop, jog or reverse) gives the SCOTCHMAN IRONWORKER a tremendous advantage over mechanical ironworkers.
There is no chance of the SCOTCHMAN IRONWORKER being accidentally tripped.
The hydraulic system operates at a maximum pressure of 1,500 PSI (103 BAR) and is protected from overload by a built in relief valve.
2.0 SAFETY PRECAUTIONS
SCOTCHMAN INDUSTRIES, INC. will, within one (1) year of the date of purchase, replace F.O.B. the factory or refund the purchase price for any goods which are defective in materials or workmanship, provided the buyer returns the warranty registration card within thirty (30) days of the purchase date, and, at the seller’s option, returns the defecti ve goods freight and delivery prepaid to the seller, which shall be the seller’s sole and exclusive remedy for defective goods.
Hydraulic and electric components are subject to their respective manufacturer’s warranties.
This warranty does not apply to machines and/or components which have been altered, changed or modified in any way or subjected to abuse and abnormal use, inadequate maintenance and lubrication or subjected to use beyond the seller’s recommended capacities and specifications.
In no event shall the seller be liable for labor cost expended on such goods or consequential damages.
The seller shall not be liable to purchaser or any other person for loss or damage directly or indirectly arising from the use of the goods or from any other cause.
No officer, employee or agent of the seller is authorized to make any oral representations or warranty of fitness or to waive any of the forgoing terms of sale and none shall be binding on the seller.
Any electrical changes made to the standard machine due to local electrical code variation must be paid by purchaser.
As we constantly strive to improve our products, we reserve the right to make changes without notification.
4.0 INSTALLATION AND SET-UP
A Floor To The Top Of Die Holder 36.5 93
B FLoor To Punch Bolster 33.5 85
C Throat Depth 6 15
D Floor To Bar Shear 26 66
E Floor To Tool Table 35 89
F Floor To Angle Shear 36.5 93
G Punch Stroke 15/16 2.
H Height 53 132
I Length 48 122
J Width 26 65
K Weight 1,170 LBS. 532 KG.
The weight of this machine is 1,170 pounds (532 KG).
OR A FORK LIFT. These are the only two recommended methods of moving this machine.
When using a fork lift, spread the forks of the lift as wide as possible for stability.
Lift only on the tubing side rails or under the skids provided. Do not back away from the machine with
the forks tilted up. This may cause damage to the interior components of the machine.
Any damage to the machine during shipment should be reported to the delivery carrier immediately
and a damage report made out so a claim can be placed. The carrier is responsible for shipping
damage, but it is the customer’s responsibility to report damages, external or internal, immediately.
After the machine has been positioned, the shroud on the operator’s side should be removed and an
inspection made of the interior for missing or damaged parts.
The stroke adjustment is important for the proper operation of the machine. If the setting has
changed, the machine may over travel and cause the hydraulic cylinder to "bottom out". This
continued condition will cause the starter overload to open. It can also cause the hydraulic oil to
overheat and damage hydraulic system components. A slight change in the setting can result in
inadequate stroke to operate optional tools.
A check of the stroke setting is made at the connecting link pin (D). SEE FIGURE 5 ON PAGE 19.
Turn OFF the power to the machine.
The measurement should be 11-15/16 inches (30 cm).
Turning the clevis clockwise will move the measurement up; turning the clevis counterclockwise will
bring the measurement down.
Turn the machine’s power OFF and recheck the measurement. Repeat, if needed.
A program of scheduled maintenance should be set up and documented according to your application and the frequency you use this machine. The following is a list of important items that should be included in a scheduled maintenance program:
A. Check the clearance between the punch barrel (A) and the punch barrel guide (B). FOR PARTS IDENTIFICATION, SEE FIGURE 7 ON THE FOLLOWING PAGE.
Check the condition of the shear blades, angle shear blades and any component tools for wear. Replace worn parts promptly.
Change the hydraulic oil once a year; more often under adverse conditions.
TO CHANGE THE HYDRAULIC OIL, turn OFF the power to the machine. Remove the drain plug from the bottom of the reservoir. Allow the oil to drain. Replace with 3.5 U.S. gallons (13 liters) of a light weight, nonfoaming, hydraulic oil such as CENEX ROA 200, MOBIL DTE 16, SHELL PELLUS 46, TEXACO RANDO 46 or equivalent.