
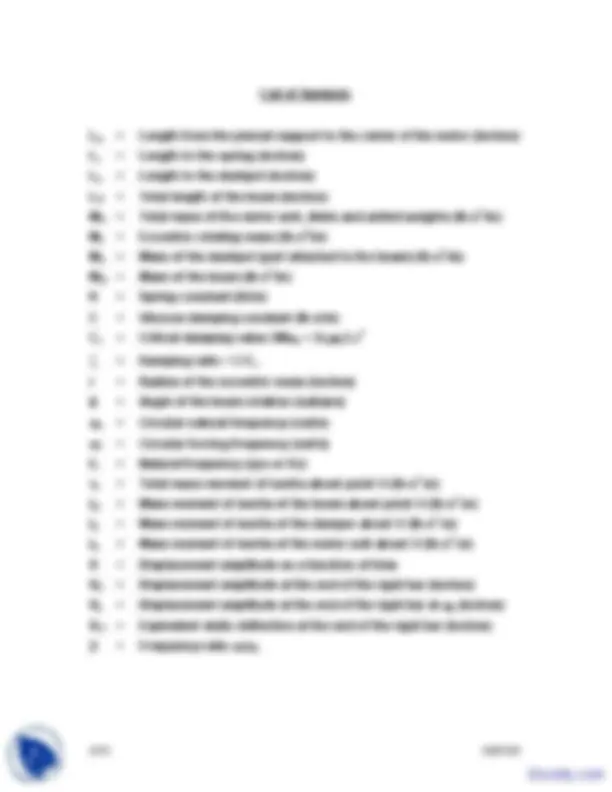
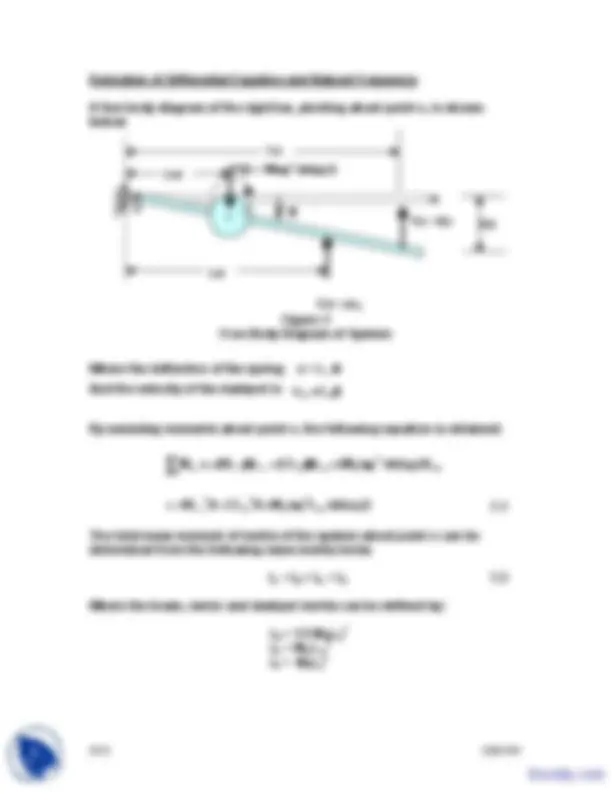
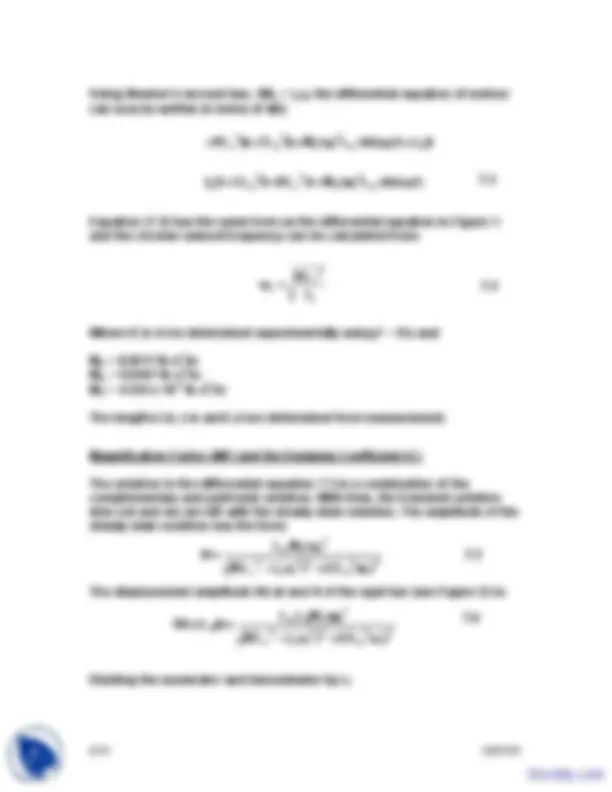
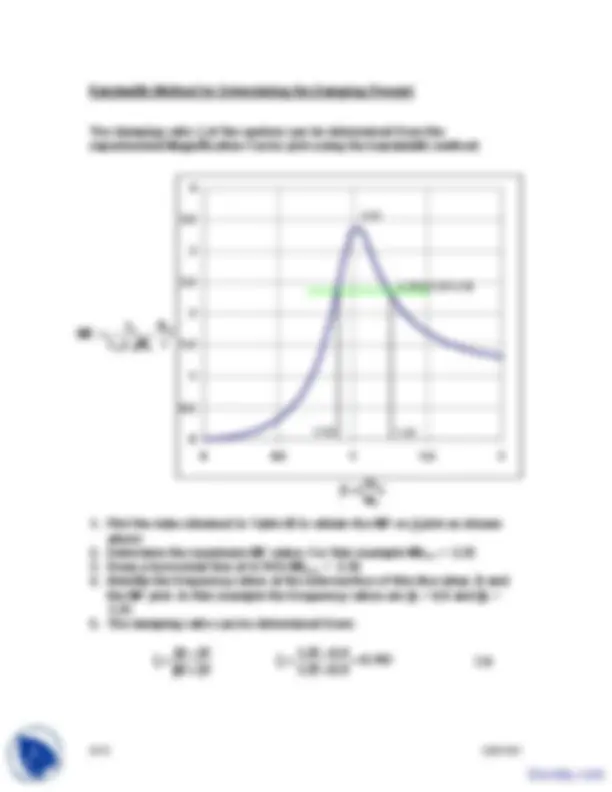
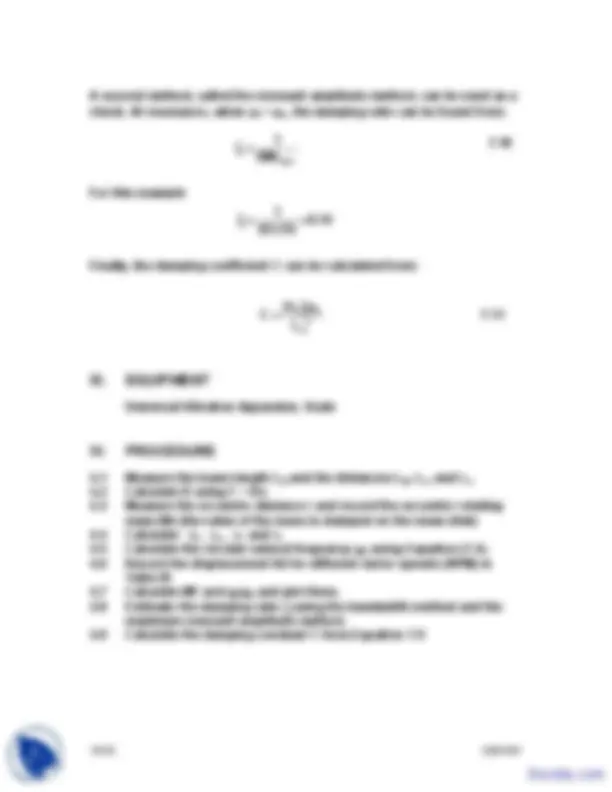
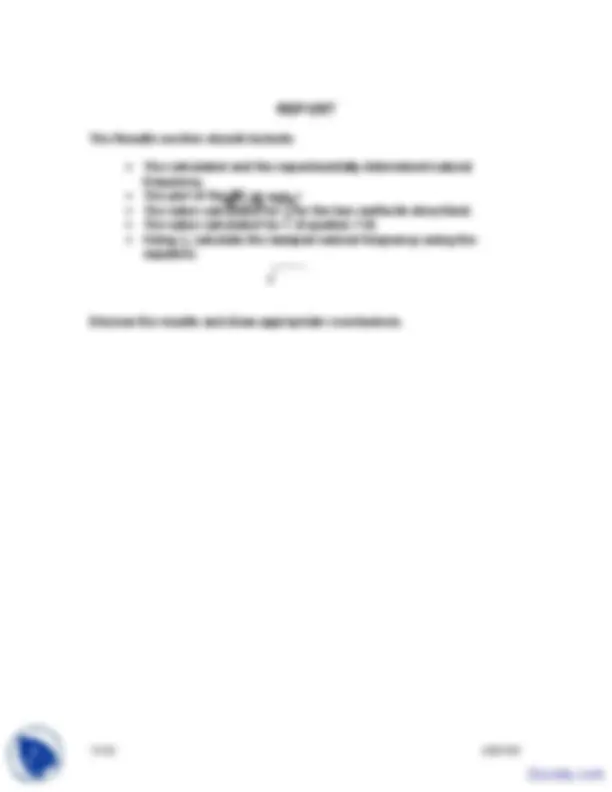
Study with the several resources on Docsity
Earn points by helping other students or get them with a premium plan
Prepare for your exams
Study with the several resources on Docsity
Earn points to download
Earn points by helping other students or get them with a premium plan
Community
Ask the community for help and clear up your study doubts
Discover the best universities in your country according to Docsity users
Free resources
Download our free guides on studying techniques, anxiety management strategies, and thesis advice from Docsity tutors
The main points in the lab notes of mechanics are: Mechanical System, Damping Ratio, Damping Coefficient, Stiffness, Mass, Exchange, Potential Energy, Energy Loss, Dashpot, Oil
Typology: Study notes
1 / 12
This page cannot be seen from the preview
Don't miss anything!
2/13 03/01/
1.1 To determine the undamped and damped natural frequency of a single degree of freedom system.
1.2 To obtain a plot of the magnification factor versus the frequency ratio.
1.3 To determine the damping ratio ζζζζ and the damping coefficient C of the system.
Any mechanical system that has mass and stiffness can vibrate. Vibration results when there is an energy exchange between the mass, which stores kinetic energy and the spring, which stores potential energy. In such a system, the mass will oscillate with periodic motion. The energy loss in a vibrating system is modeled as a dashpot or viscous damper. The dashpot is comprised of a cylinder filled with a viscous fluid, such as oil and a piston. The force produced by a dashpot Fd is proportional to the velocity of the mass. The constant of proportionality is the viscous damping constant C which has units of N-s/m or Lb-s/in.
For a damped system, the ratio of the damping constant C to the critical damping value is a dimensionless parameter which represents a meaningful measure of the amount of damping present. This damping
Differential equation:
Circular natural frequency:
Critical damping value:
Damping ratio:
Figure 1 Single Degree of Freedom System
Mx &&++++ Cx&++++Kx====F(t)
Cc (^) ==== 2 Mωωωω n
ωωωωn ====
ζζζζ====C /Cc ====C/ 2 Mωωωω n
Fs ==== Kx Fd ====Cx&
x(t )
F(t)
3/13 03/01/
More complicated mechanical systems can be modeled using the same differential equation theory. The system considered for study here is a viscously damped single degree of freedom system which is excited by and external harmonic force.
Figure 2 EXPERIMENTAL SET-UP
The rigid bar OA shown in Figure 3 pivots about point O when subjected to the harmonic force. This harmonic force is produced by a rotating mass Me driven by a motor.
DASHPOT
BEAM PIVOT
SPEED CONTROL
MOTOR ECCENTRIC SPRING ROTATING MASS
5/13 03/01/
Derivation of Differential Equation and Natural Frequency
A free body diagram of the rigid bar, pivoting about point o, is shown below:
Figure 3 Free Body Diagram of System
Where the deflection of the spring x = Ls θθθθ
And the velocity of the dashpot is
By summing moments about point o, the following equation is obtained:
The total mass moment of inertia of the system about point o can be determined from the following mass inertia terms
I (^) o = IB + Im + Id 7.
Where the beam, motor and dashpot inertia can be defined by:
I B = 1/3 MBLB^2 I m = Mm Lm^2 I d = Md Ld^2
vd ==== L d θθθθ&
KL CL M r L sin( t)
M (KL )L (CL )L (Mr sin( t)L
m f
2 e f
2 d
2 s
f m
2 o s s d d e f
====−−−− θθθθ−−−− θθθθ++++ ωωωω ωωωω
Ld
Ls
Lm
Fd = cvd
Fs = Kx
F(t) = Meωωωωf^2 sin(ωωωωf t)
οοοο (^) θθ θθ
A
Xd
6/13 03/01/
Using Newton’s second law, ΣΣΣΣMo = I oαααα, the differential equation of motion can now be written in terms of θθθθ(t):
Equation (7.3) has the same form as the differential equation in Figure 1 and the circular natural frequency can be calculated from:
Where K is to be determined experimentally using F = Kx and
Mb = 0.0217 lb-s 2 /in Mm = 0.0447 lb-s 2 /in Md = 4.534 x 10 -3^ lb-s 2 /in
The lengths Lb, Lm and Ld are determined from measurement.
Magnification Factor (MF) and the Damping Coefficient (C)
The solution to the differential equation 7.3 is a combination of the complementary and particular solution. With time, the transient solution dies out and we are left with the steady state solution. The amplitude of the steady state solution has the form:
The displacement amplitude Xd at end A of the rigid bar (see Figure 2) is:
Dividing the numerator and denominator by I o
CL KL M r L sin( t)
KL CL Mr L sin( t)
m f
2 e f
2 s
2 o d
m f o
2 e f
2 d
2 s
ΙΙΙΙ θθθθ++++ θθθθ++++ θθθθ==== ωωωω ωωωω
−−−− θθθθ−−−− θθθθ++++ ωωωω ωωωω ====ΙΙΙΙ θθθθ
o
2 s n
ωωωω ====
2 f
2 d
2 2 o f
2 s
2 m e f (KL ) (CL )
L Mr
−−−−ΙΙΙΙ ωωωω ++++ ωω ωω
ωωωω θθθθ====
2 f
2 d
2 2 o f
2 s
2 m B e f B (KL ) (CL )
L L M r Xd L −−−−ΙΙΙΙ ωωωω ++++ ωωωω
ωωωω ==== θθθθ====
8/13 03/01/
Plotting the right hand side of Equation 7.8 versus the frequency ratio ββββ = ωωωωf/ωωωωn , the following plot is obtained for different damping ratios.
Figure 4 Magnification factor versus the frequency ratio. Large amplification occurs when the forcing frequency ωωωωf is near the natural frequency (^) ωωωωn
0
1
2
3
4
0 1 2 3 4
zeta = 0 zeta = 0. zeta = 0. zeta = 0. zeta = 1
r
MF d m B e
==== ΙΙΙΙo
n
f ωωωω
ωωωω ββββ====
9/13 03/01/
Bandwidth Method for Determining the Damping Present
The damping ratio ζζζζ of the system can be determined from the experimental Magnification Factor plot using the bandwidth method:
ββββ ++++ ββββ
ββββ −−−−ββββ ζζζζ====
0
1
2
3
4
0 0.5 1 1.5 2
r
MF d m B e
==== ΙΙΙΙo
n
f ωω ωω
ωωωω ββββ====
0.707x3.33=2.
ζζζζ====
11/13 03/01/
The Results section should include:
Discuss the results and draw appropriate conclusions.
2 ωωωωd ====ωωωωn 1 −−−−ζζζζ
12/13 03/01/
COMPONENT MASS (lb-s^2 /in) LENGTH (in) CALCULATION BEAM Mb = Lb = I b = MOTOR Mm = Lm = I m = DASHPOT Md = Ld = I d = ROTATING MASS Me = r = STIFFNESS (lb/in) I o = SPRING K = Ls = K Ls^2 = ωωωωn =
o
2 s n
ωωωω ====