
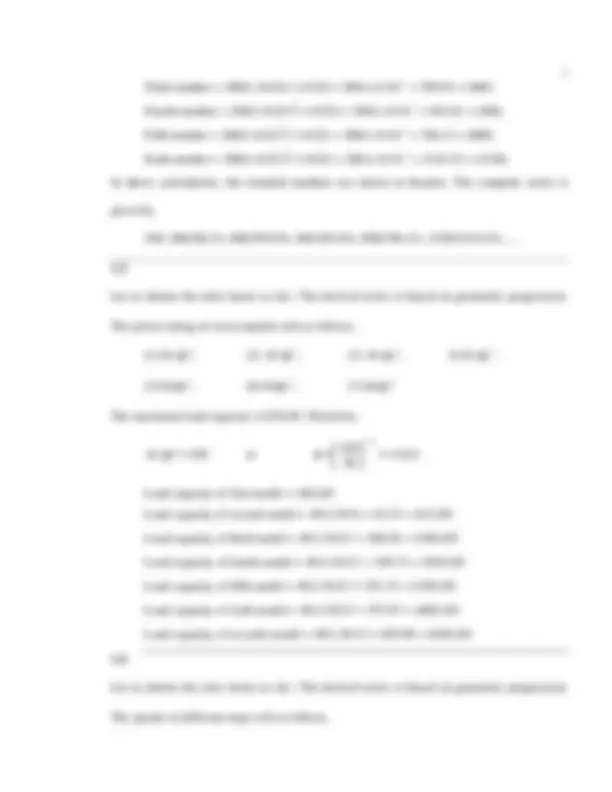
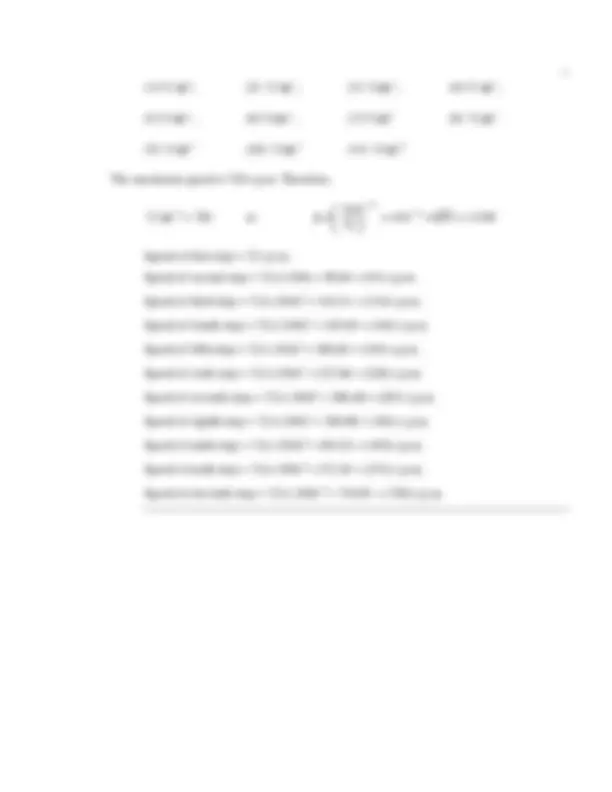
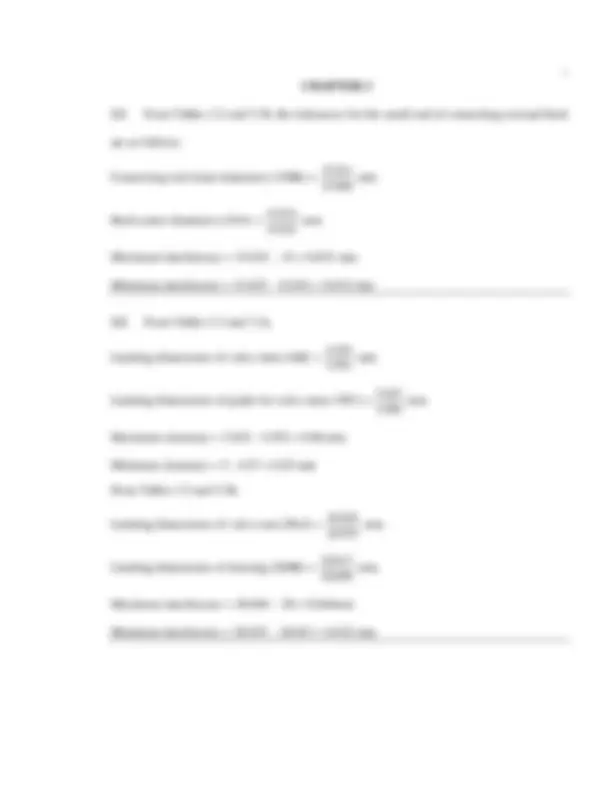
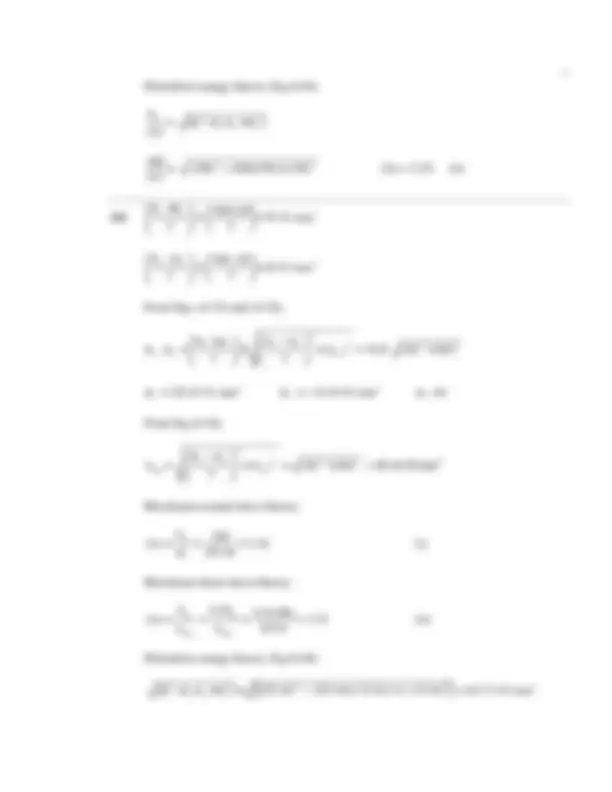
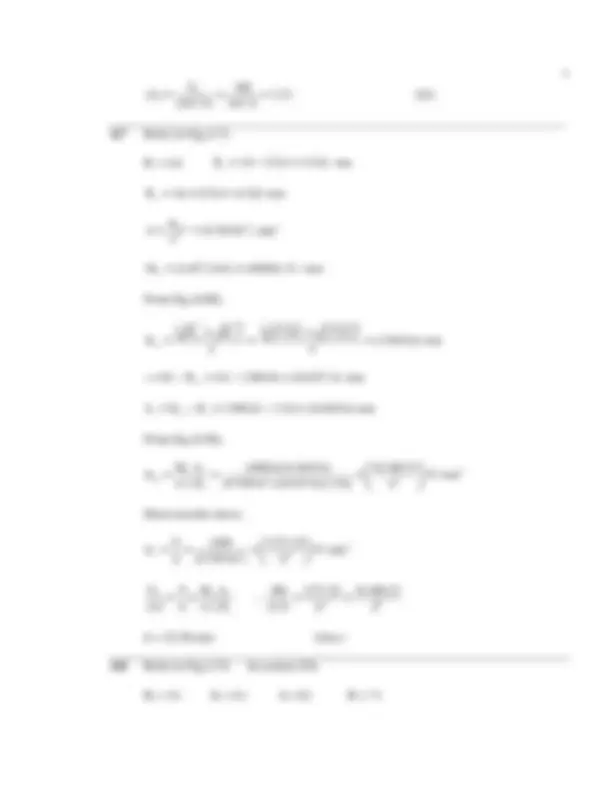
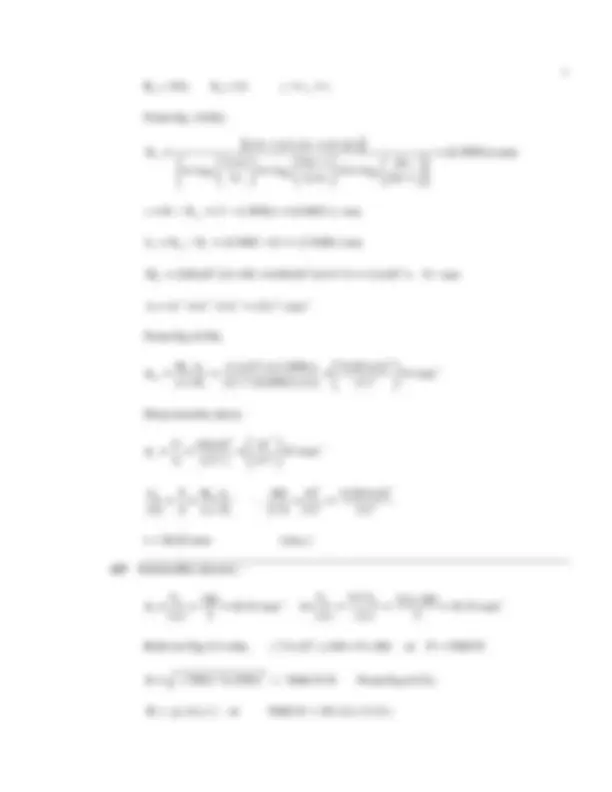
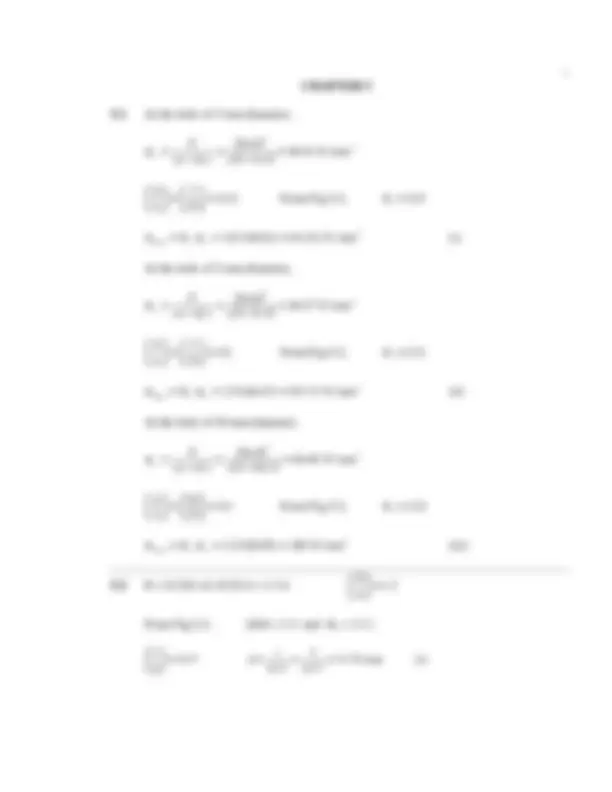
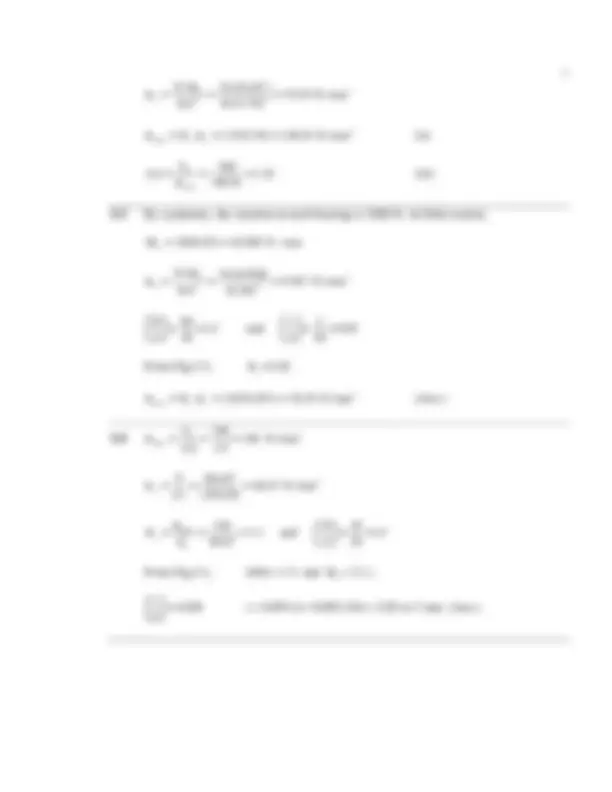
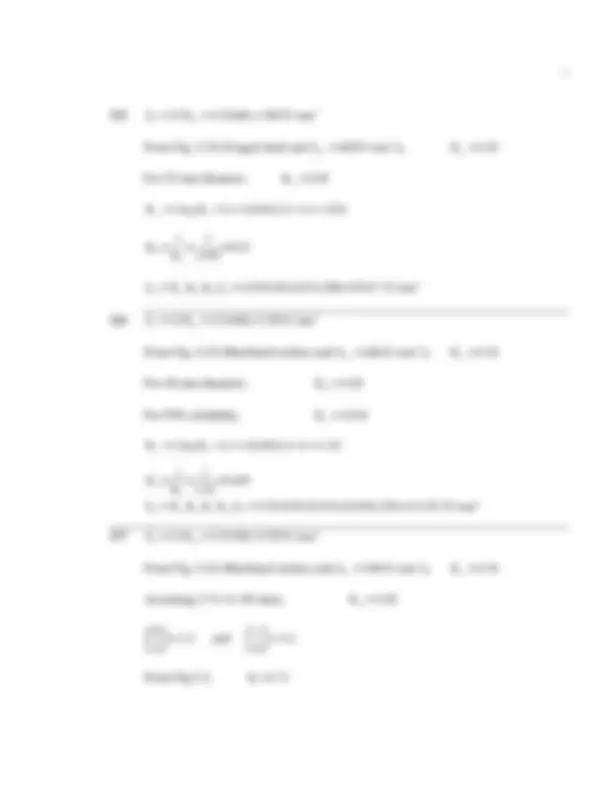

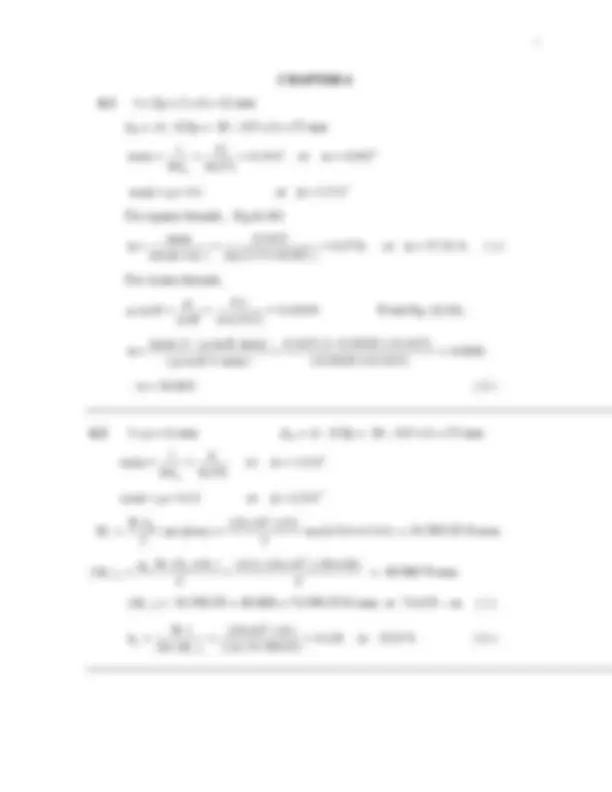
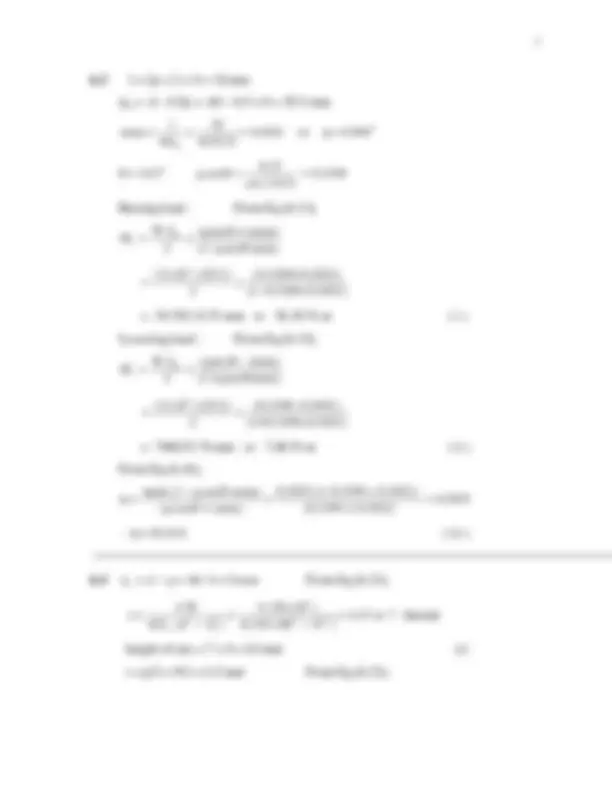
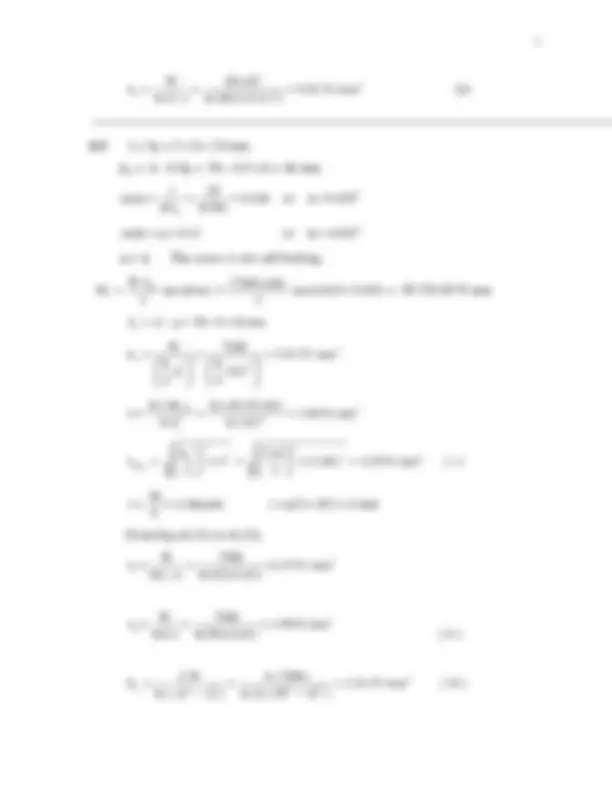
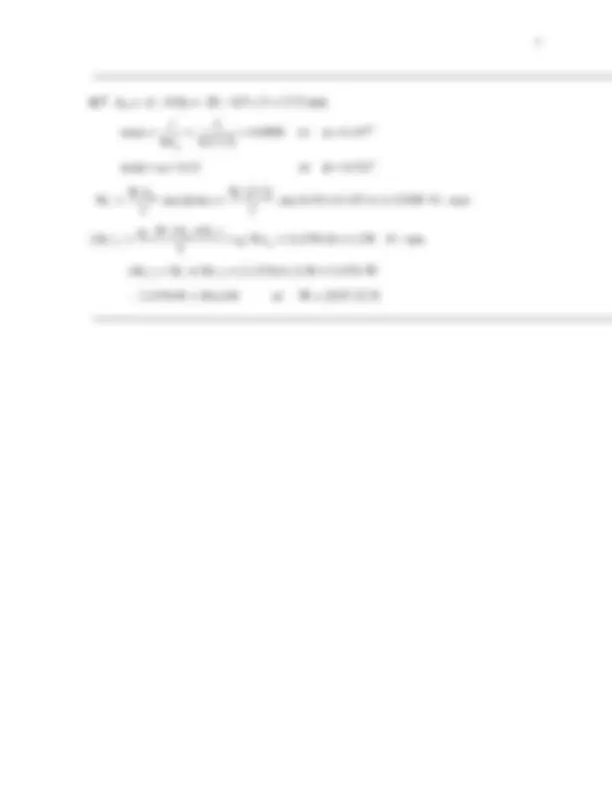
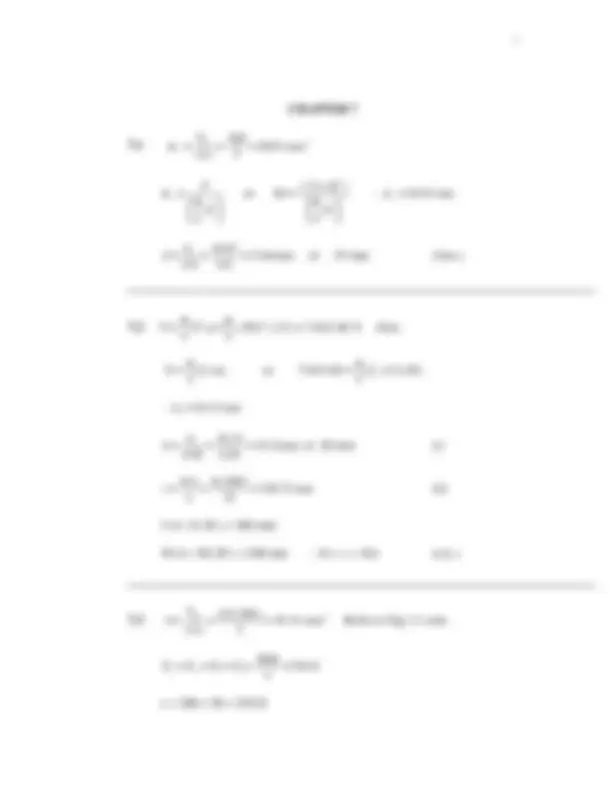
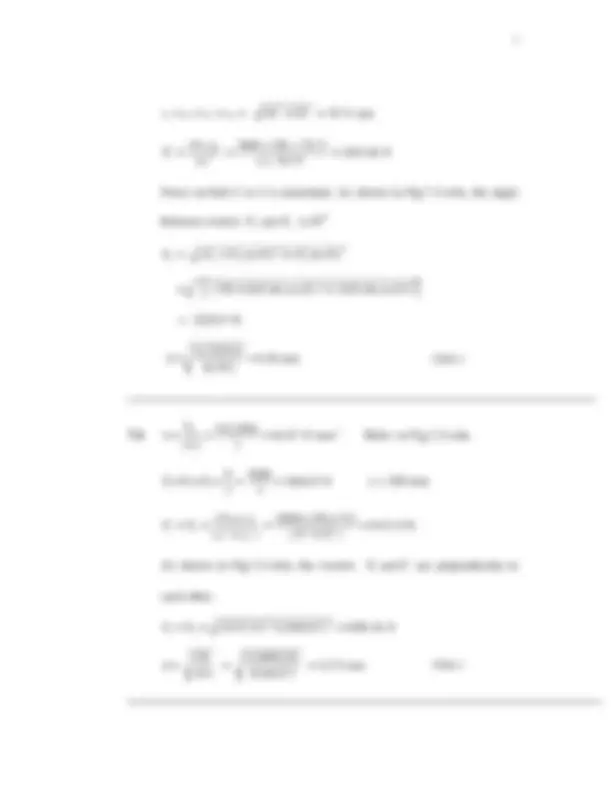
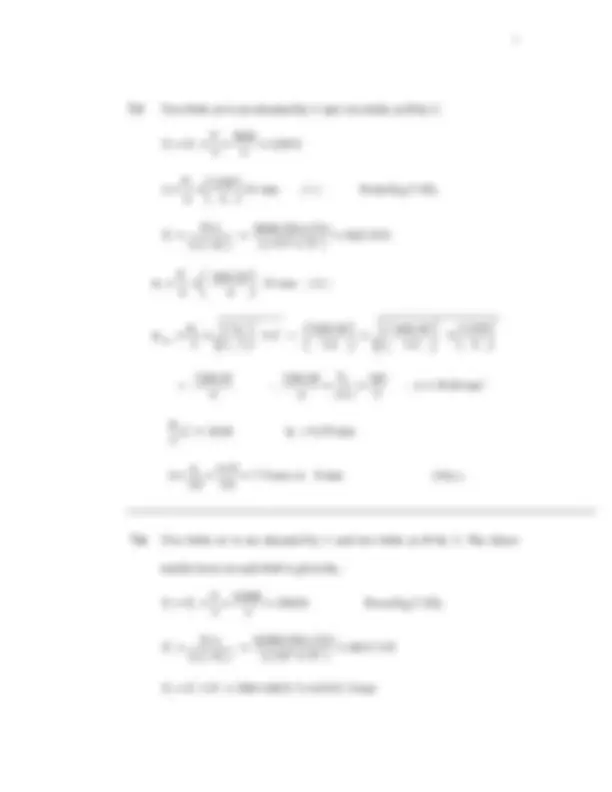
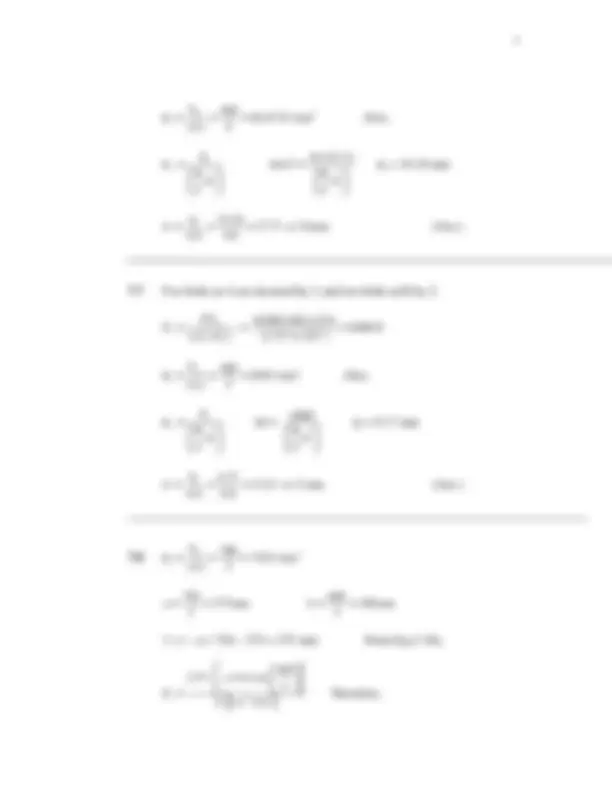
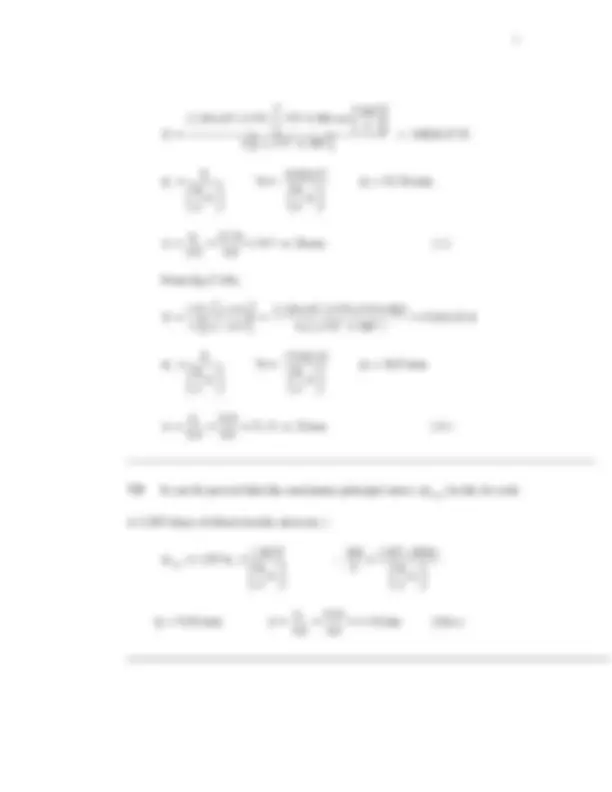
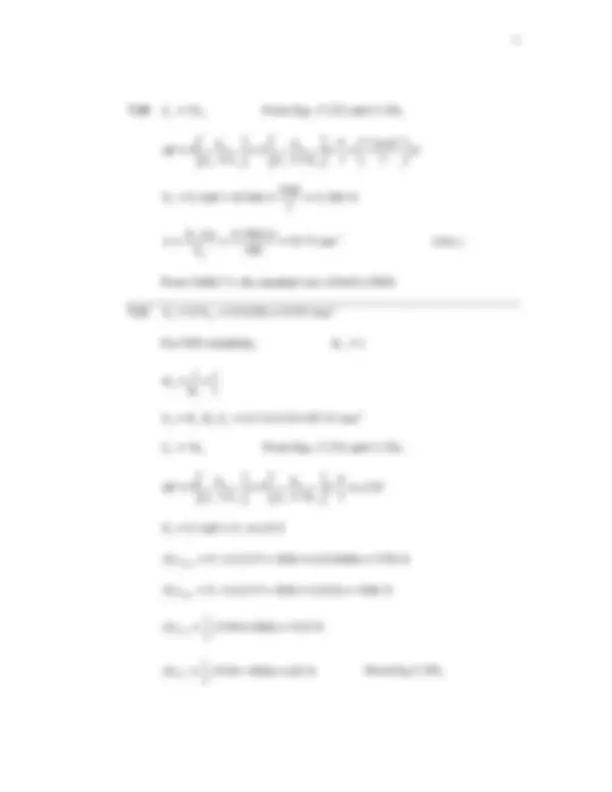
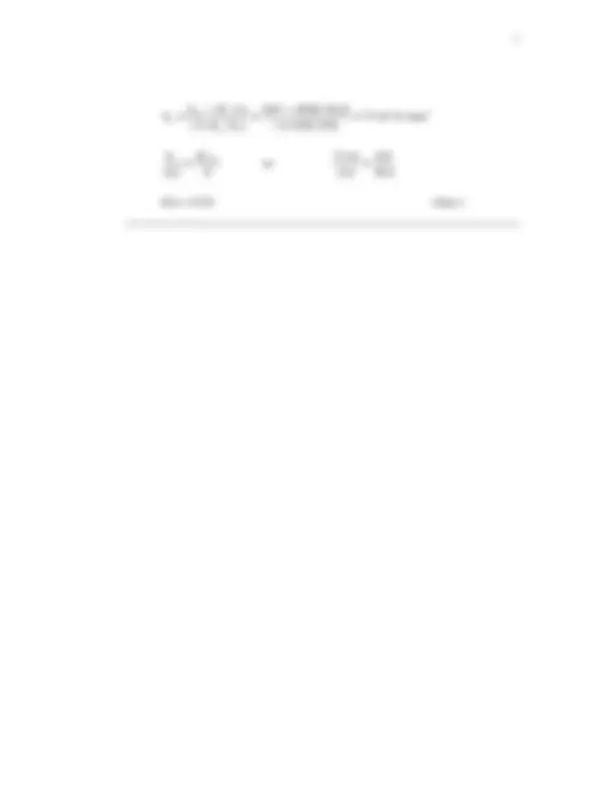
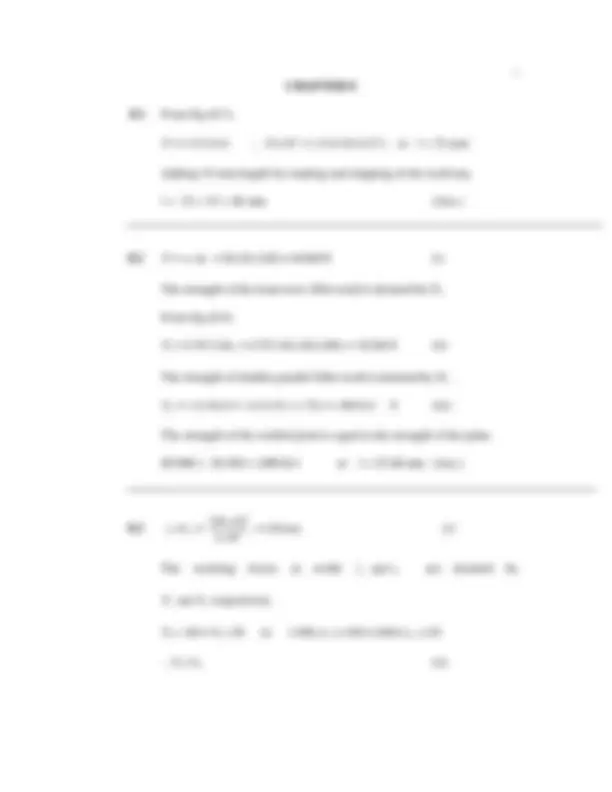
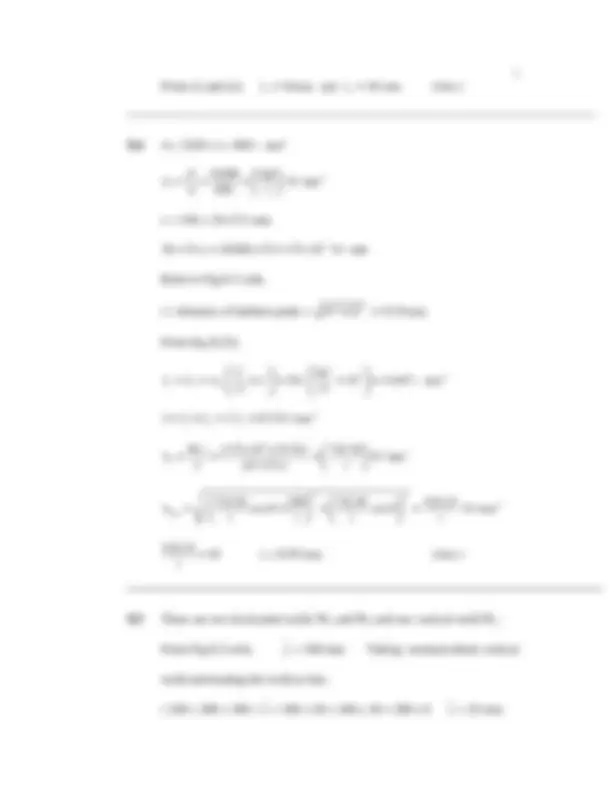
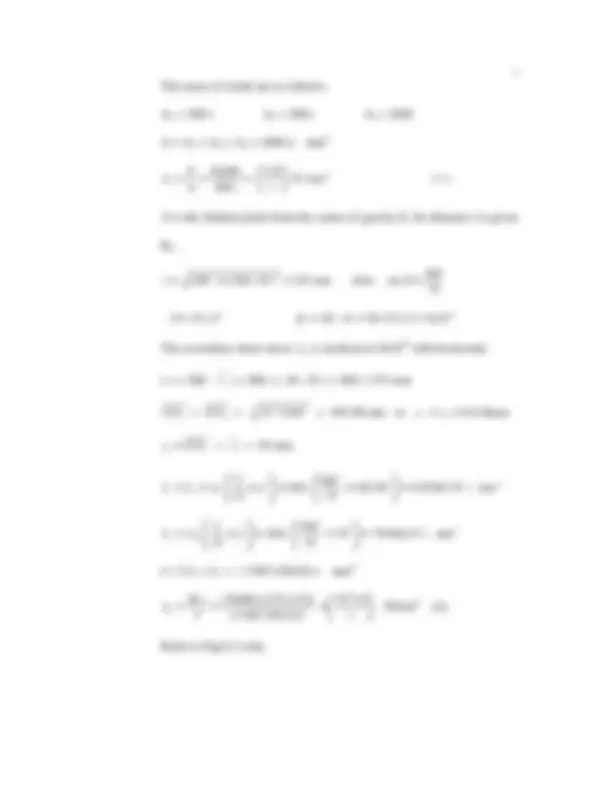
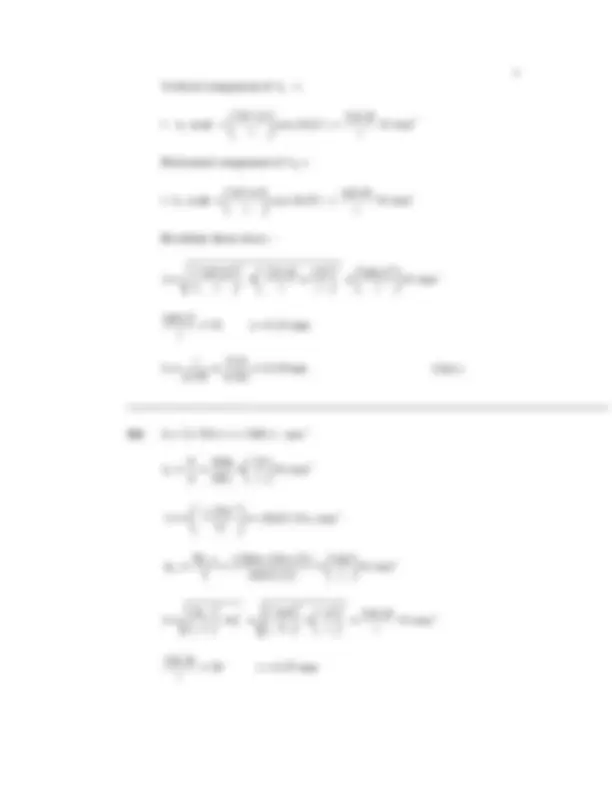
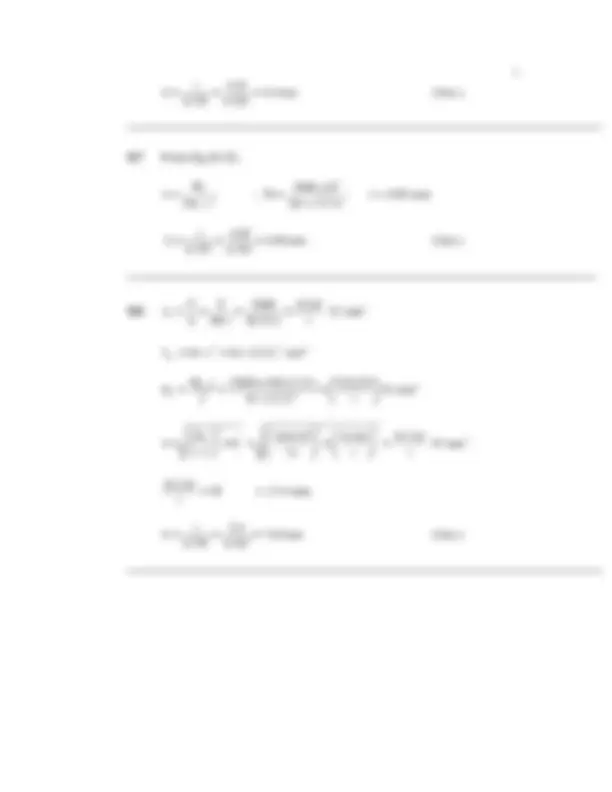
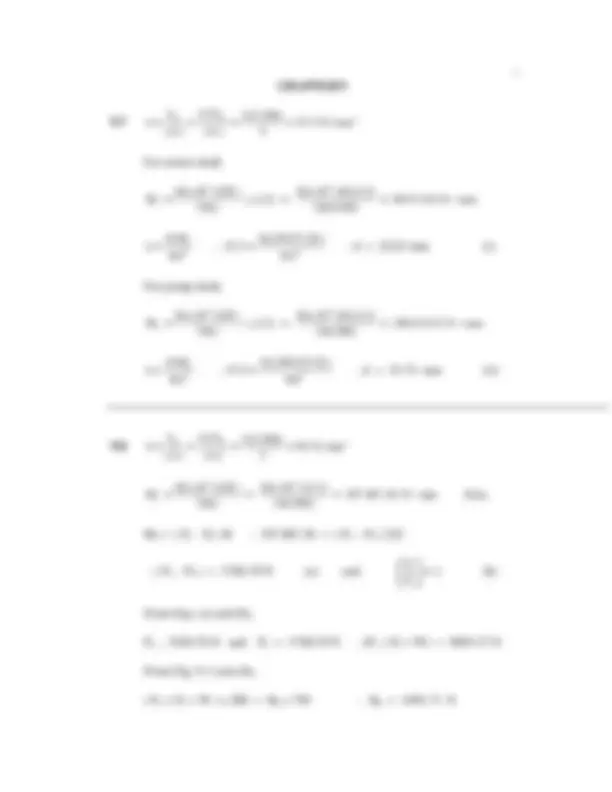
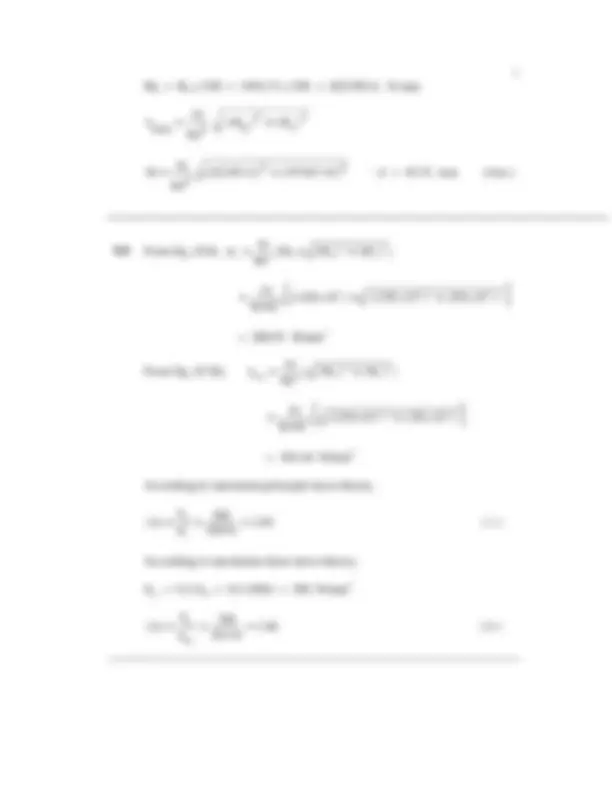
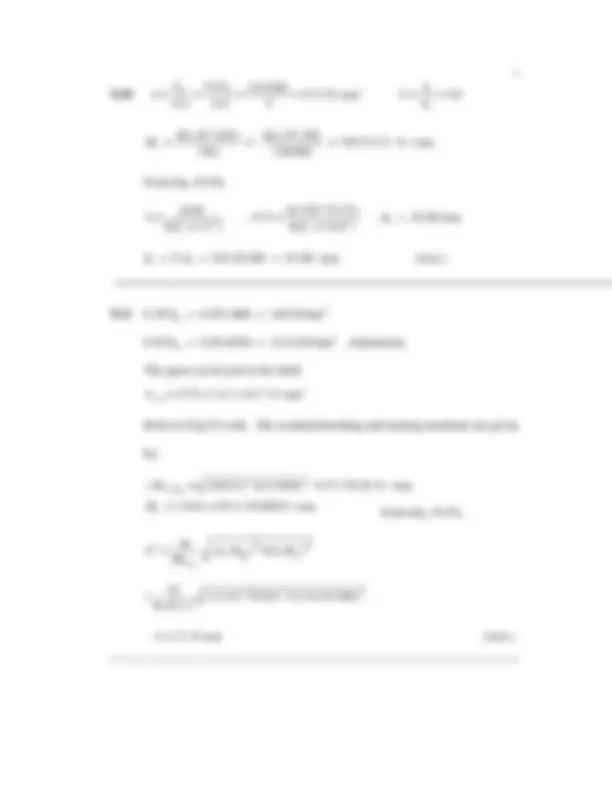
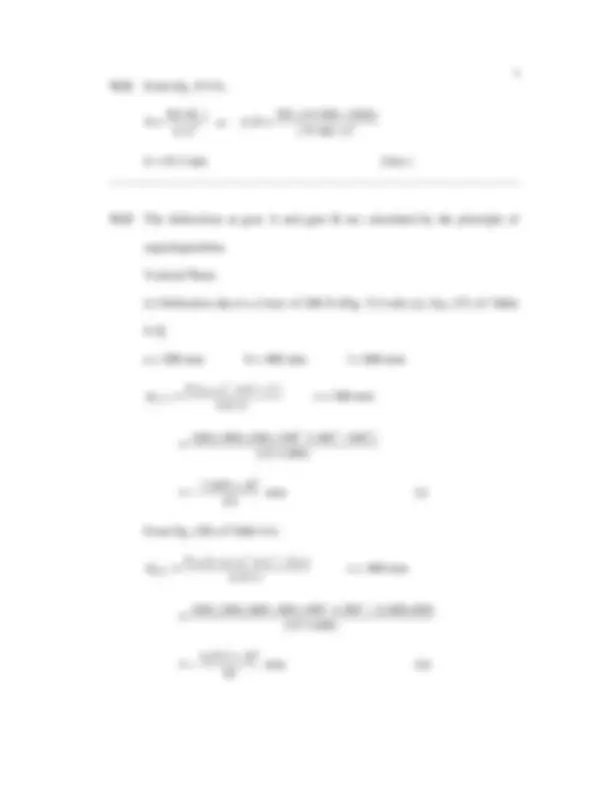
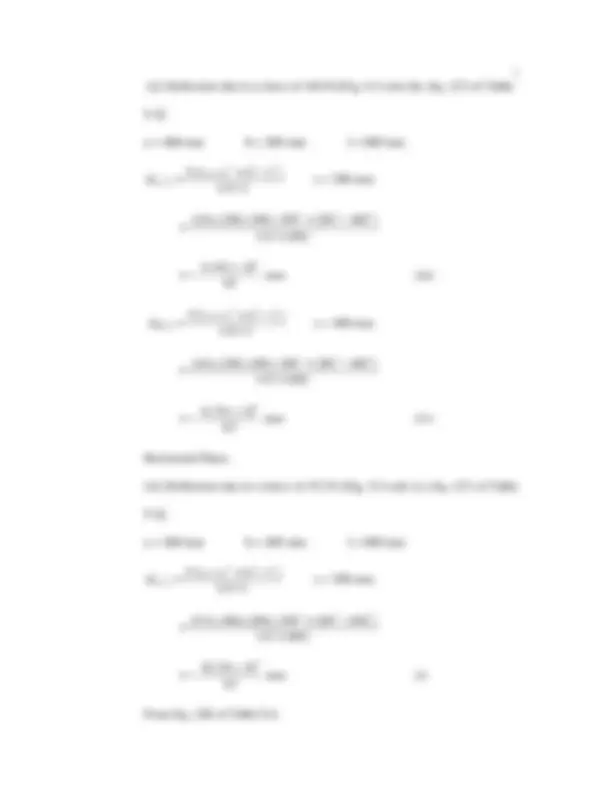
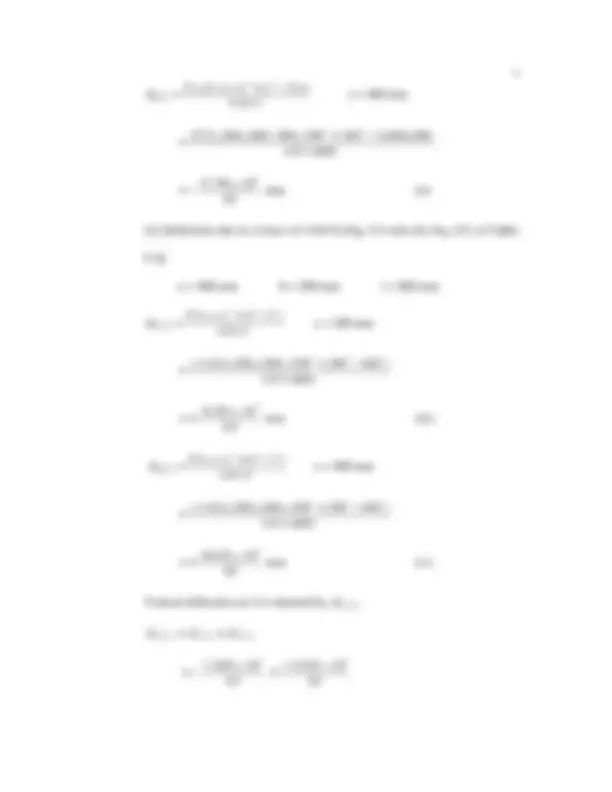
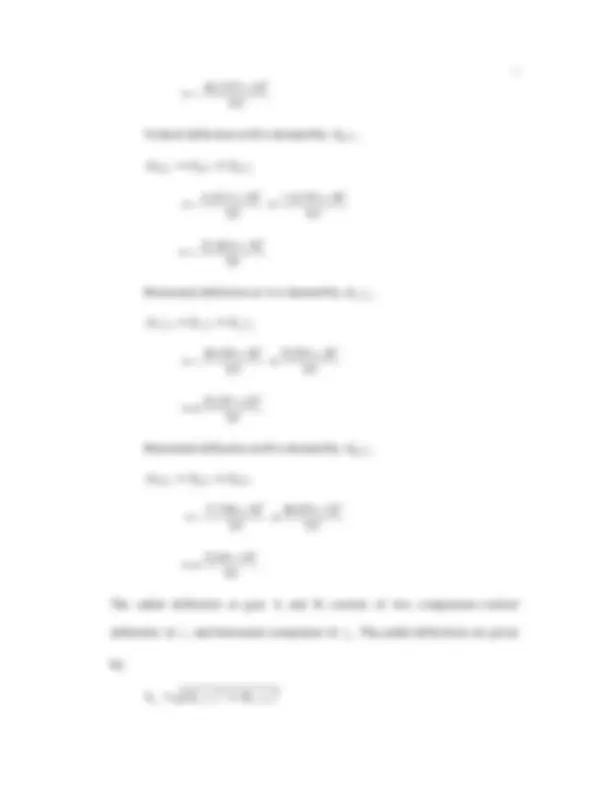
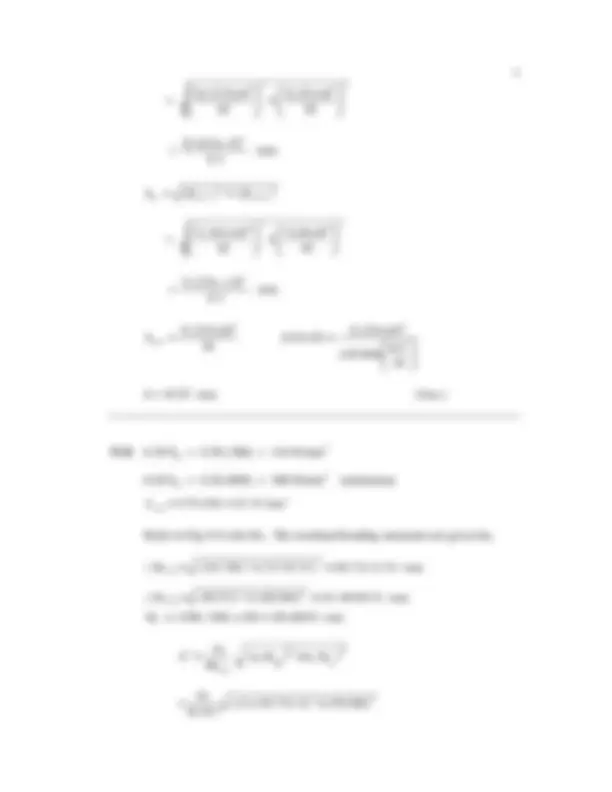
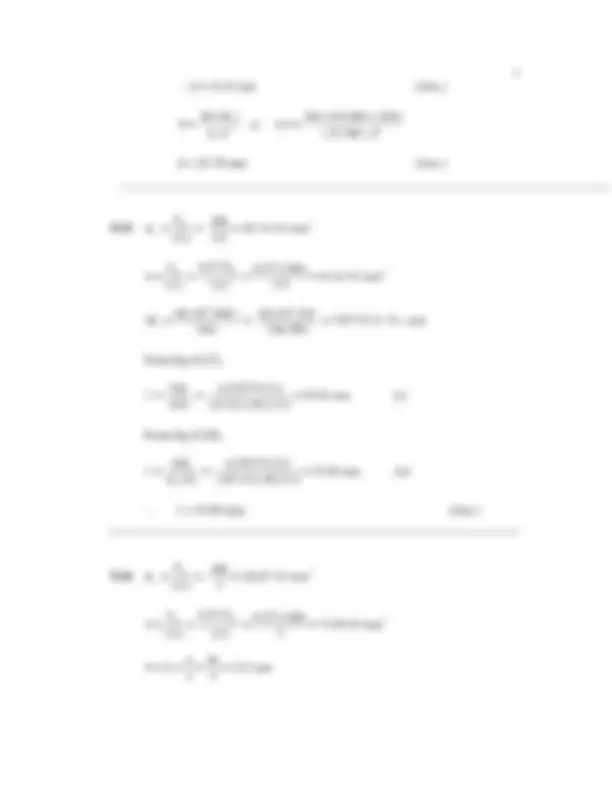
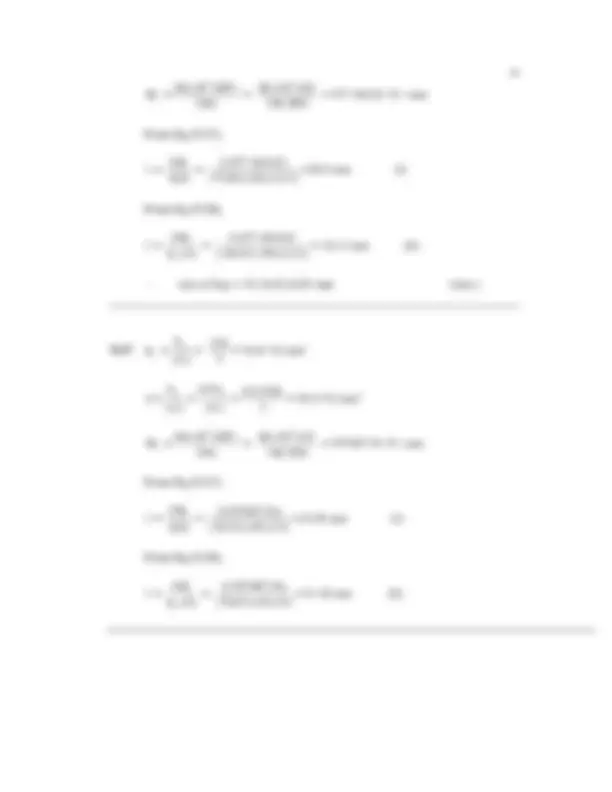
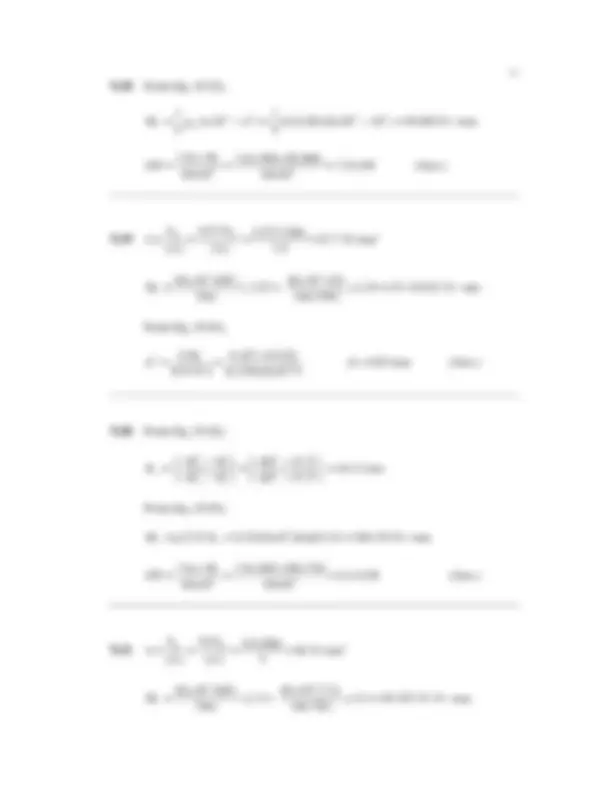
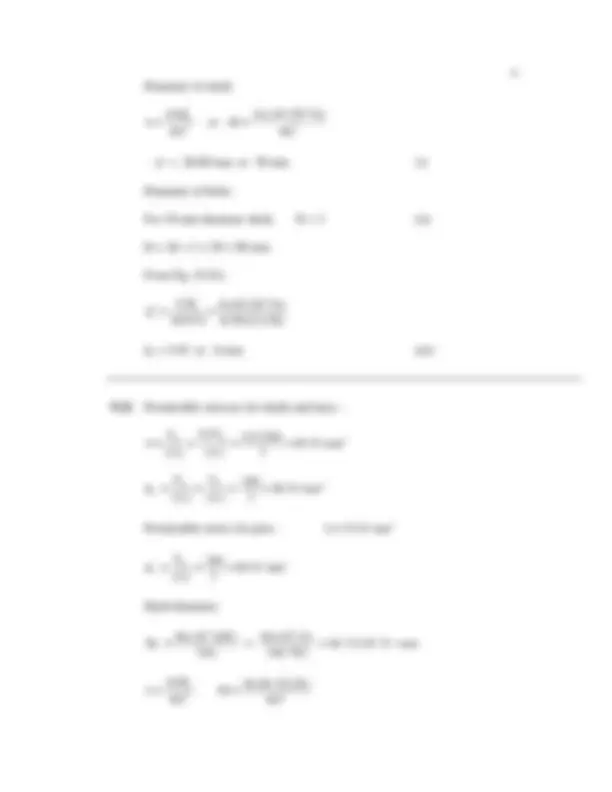
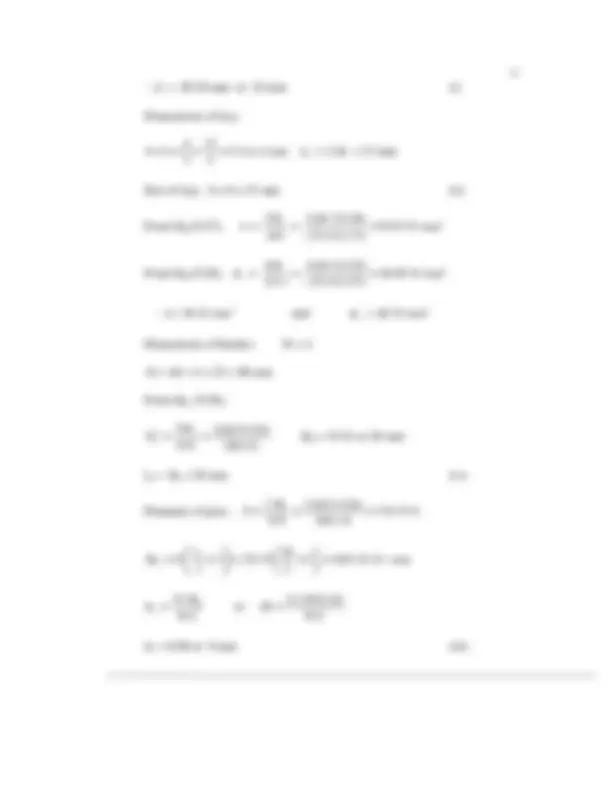
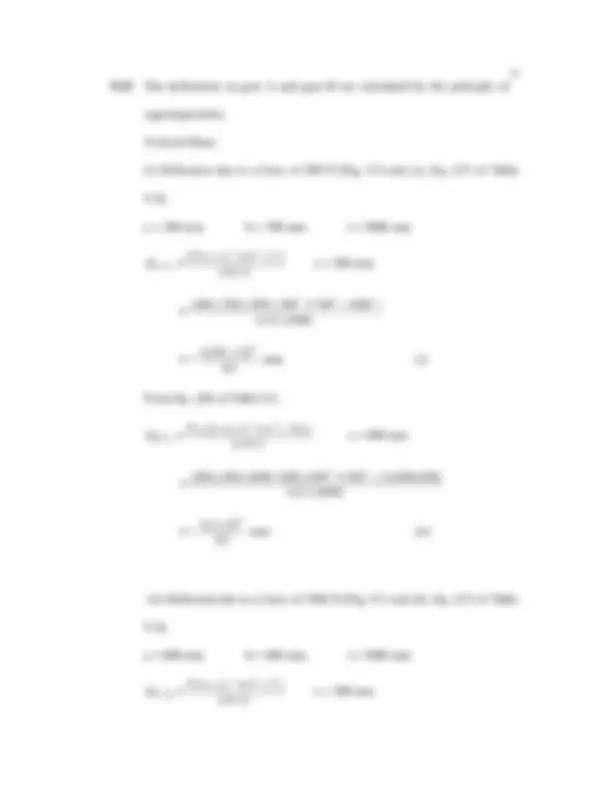
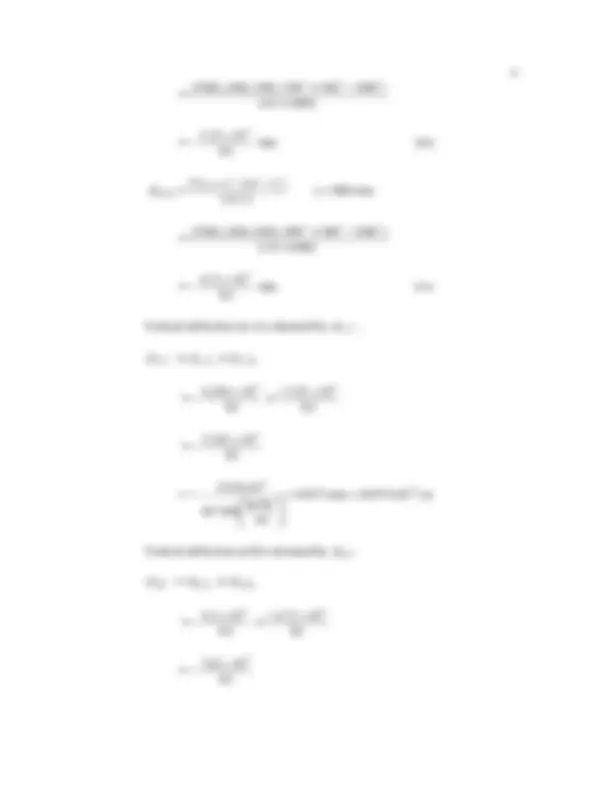
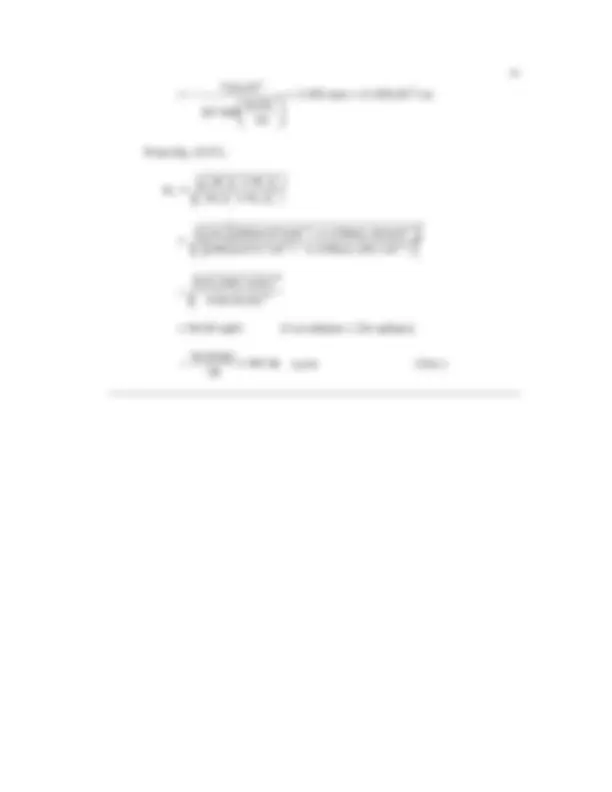
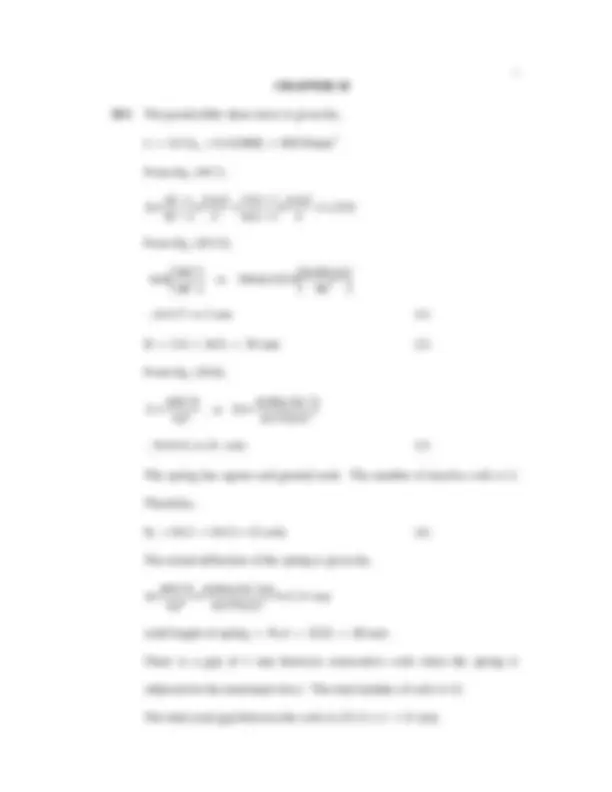
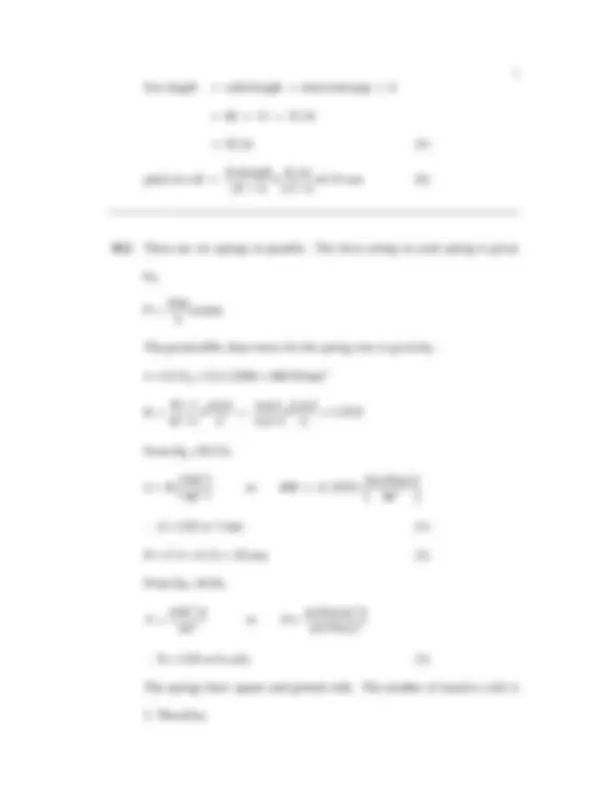
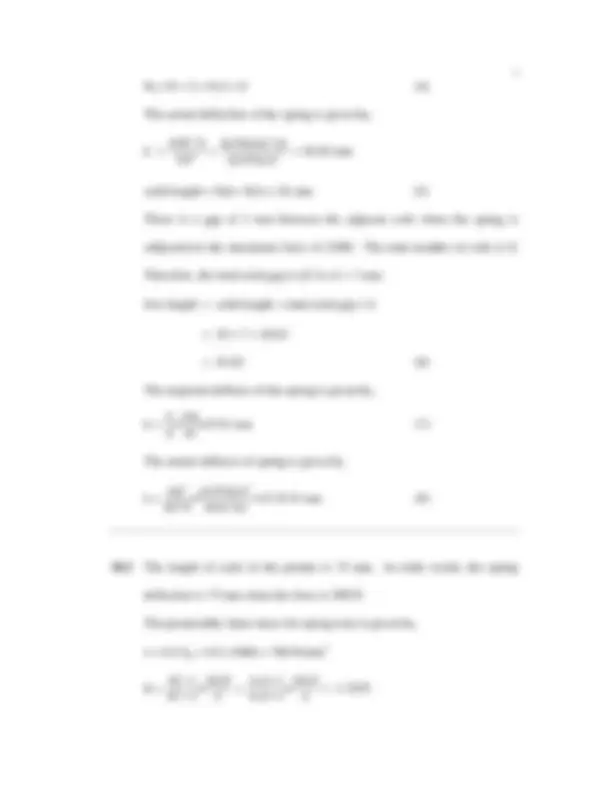
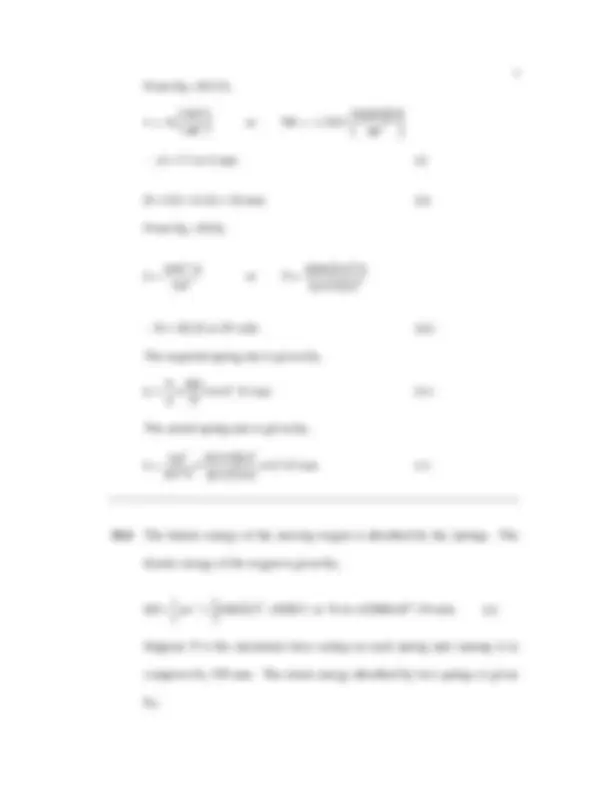
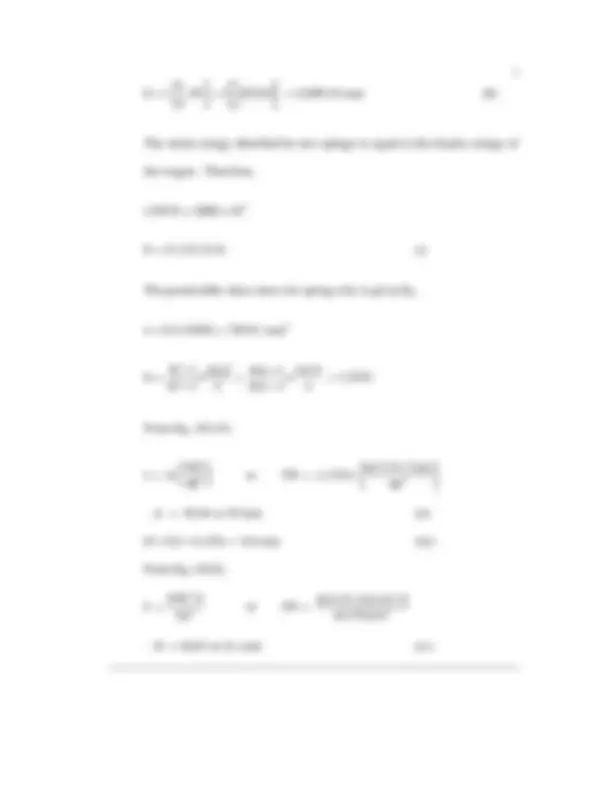
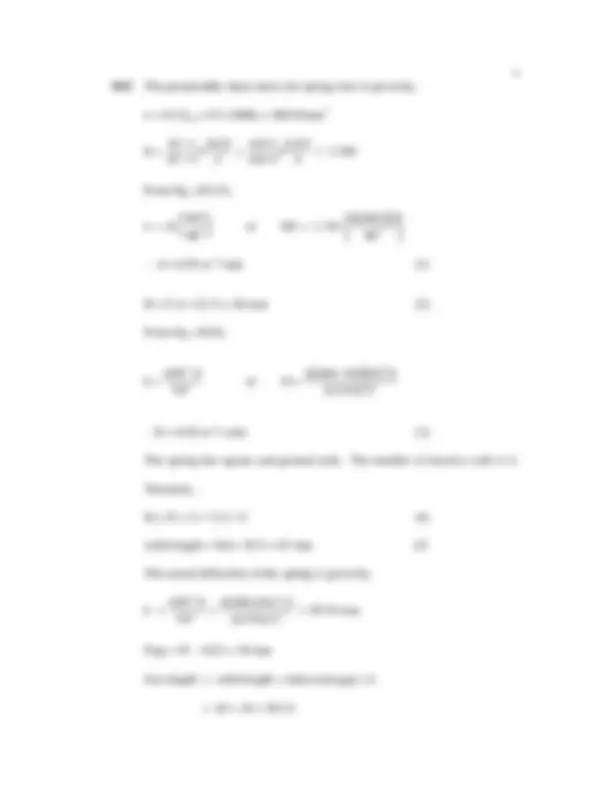
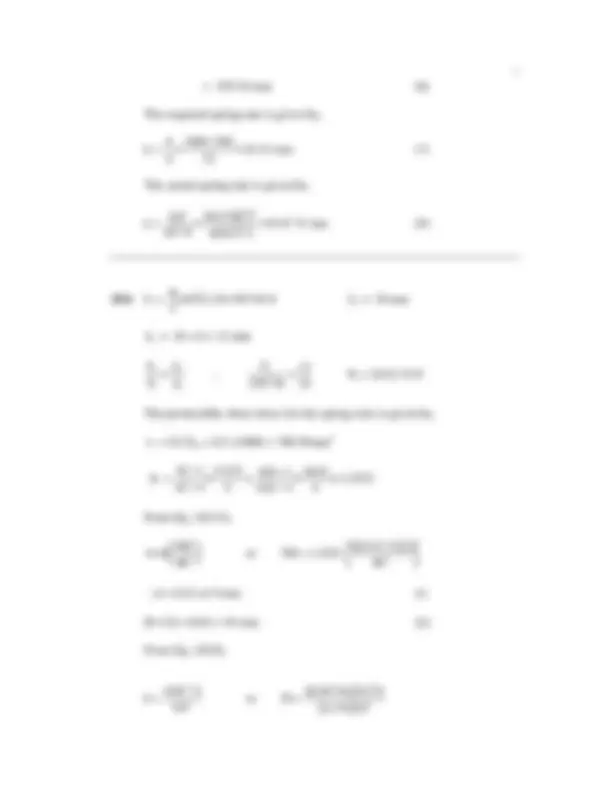
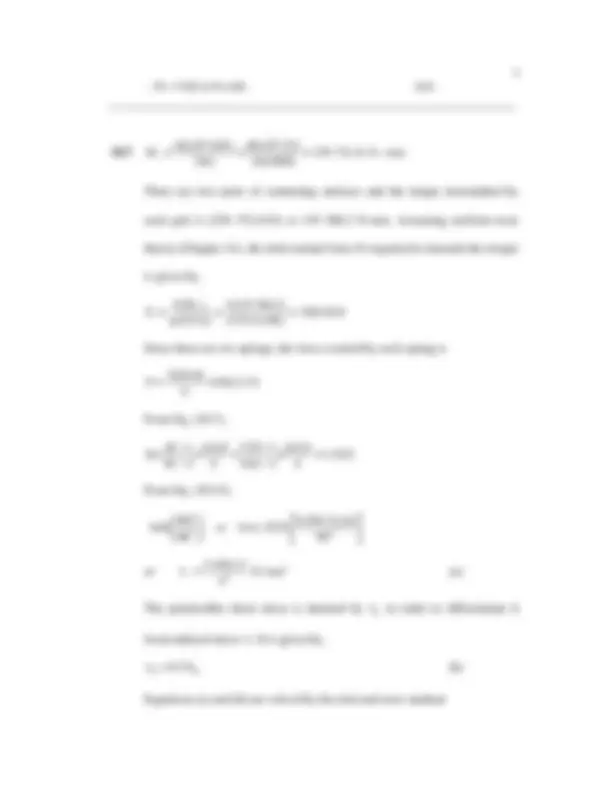
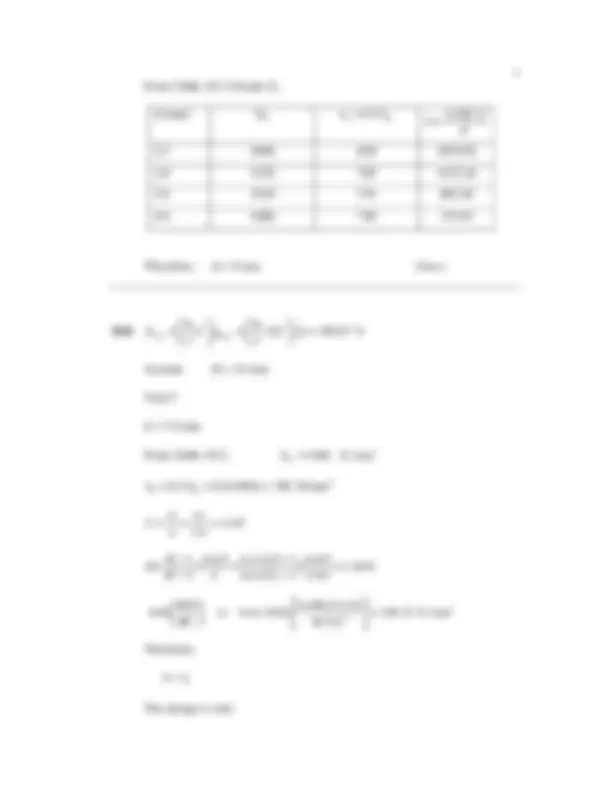
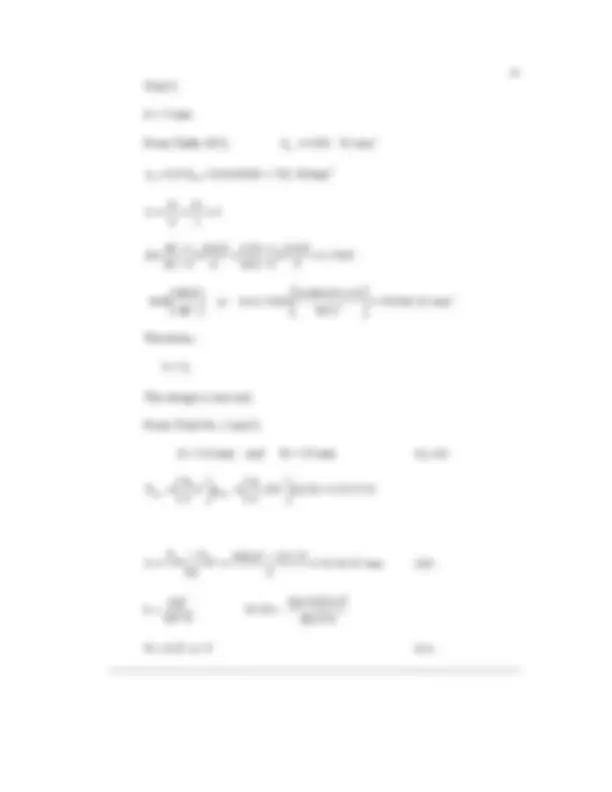
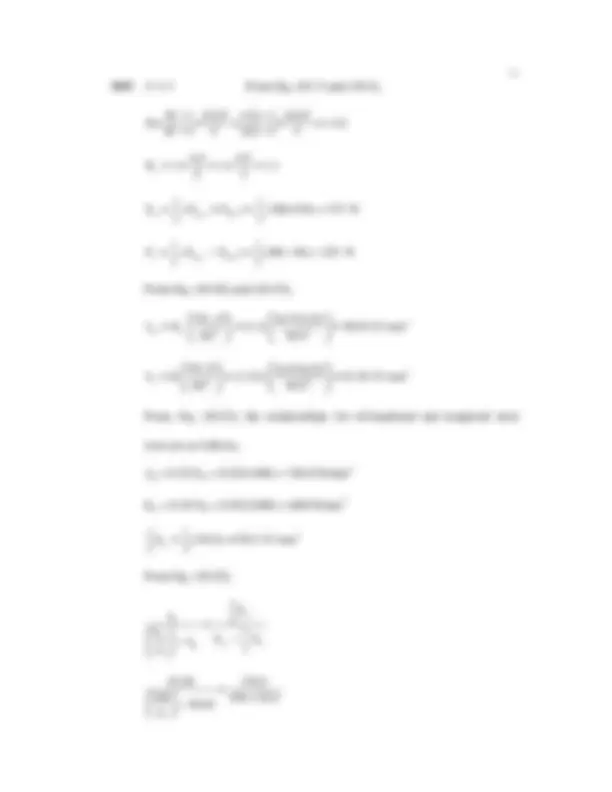
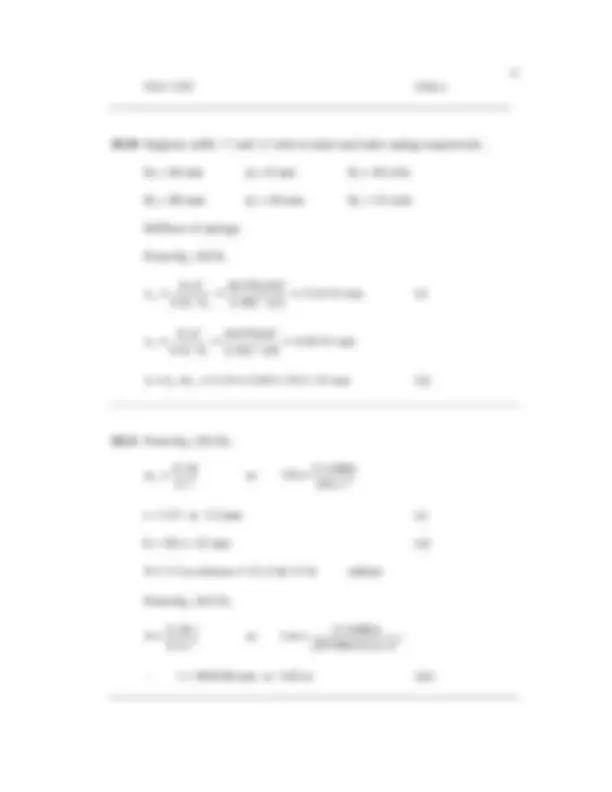
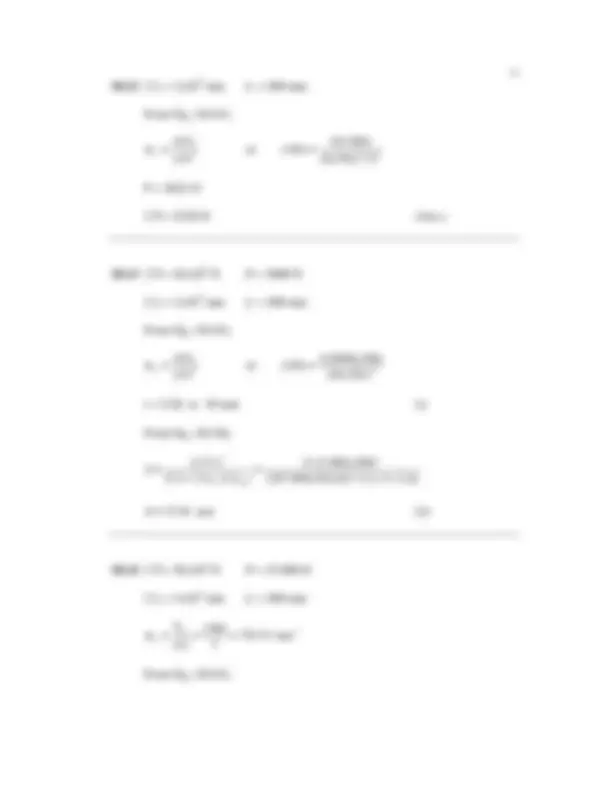
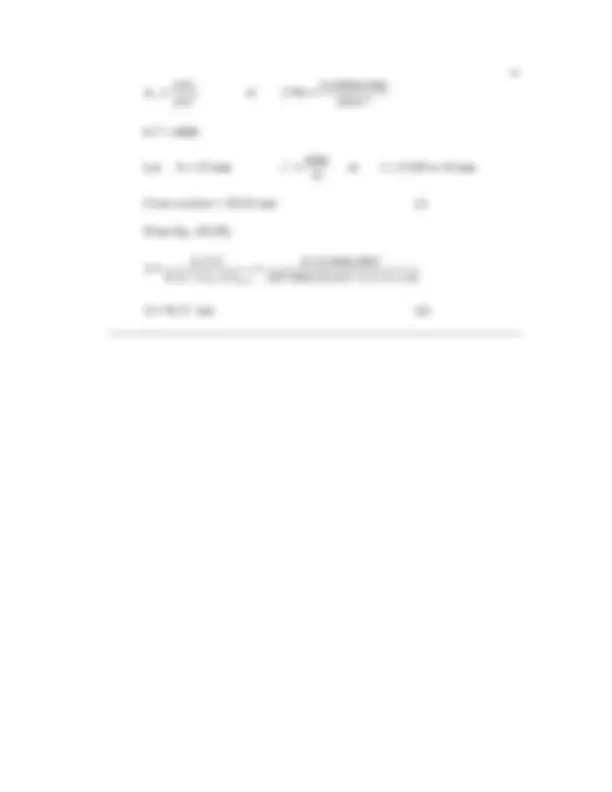
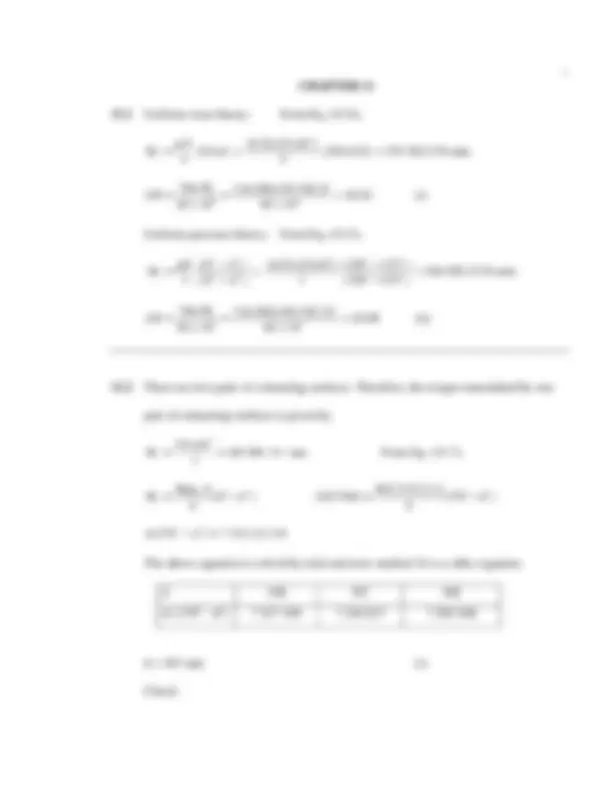
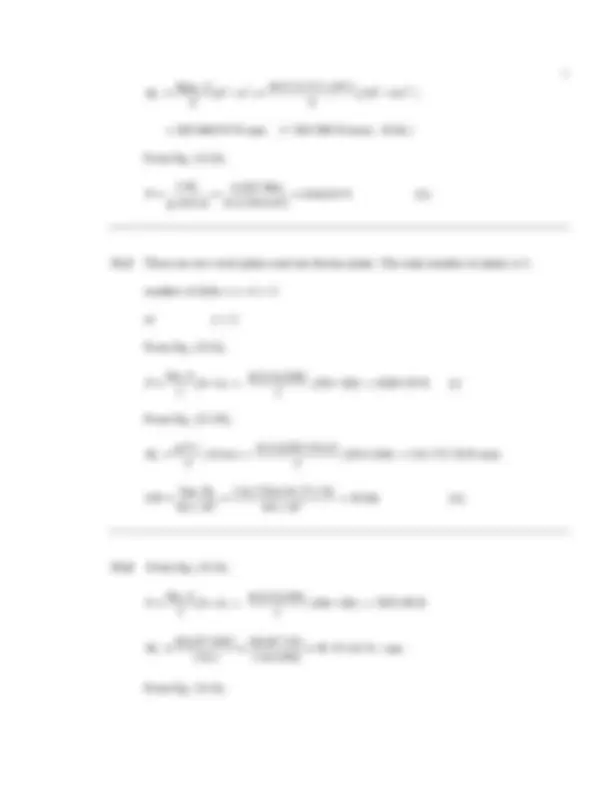
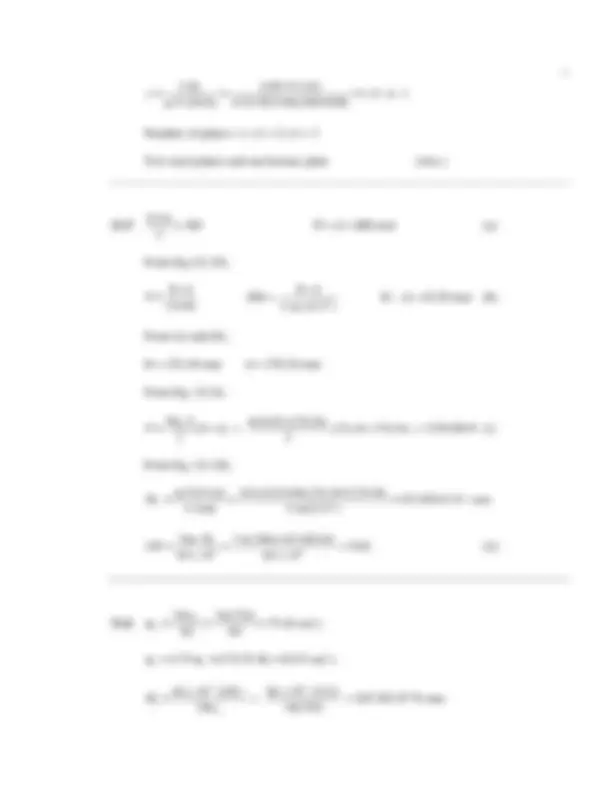
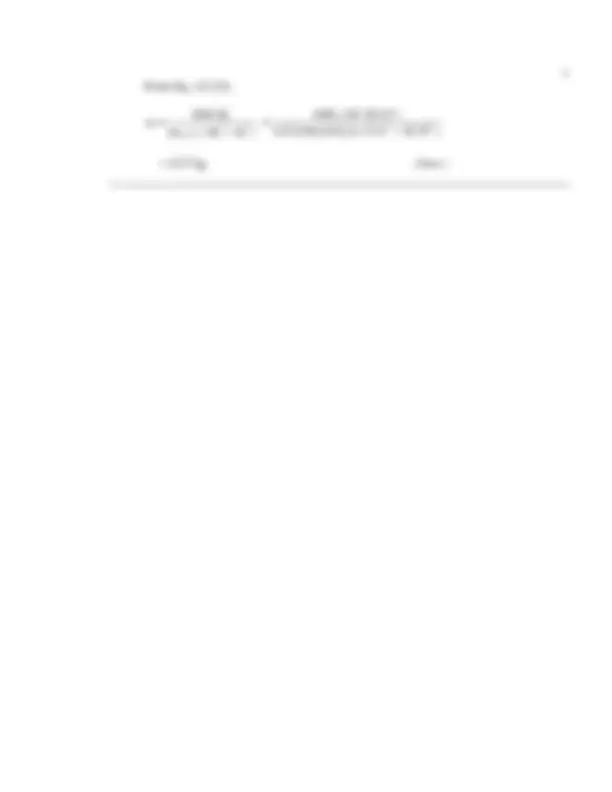
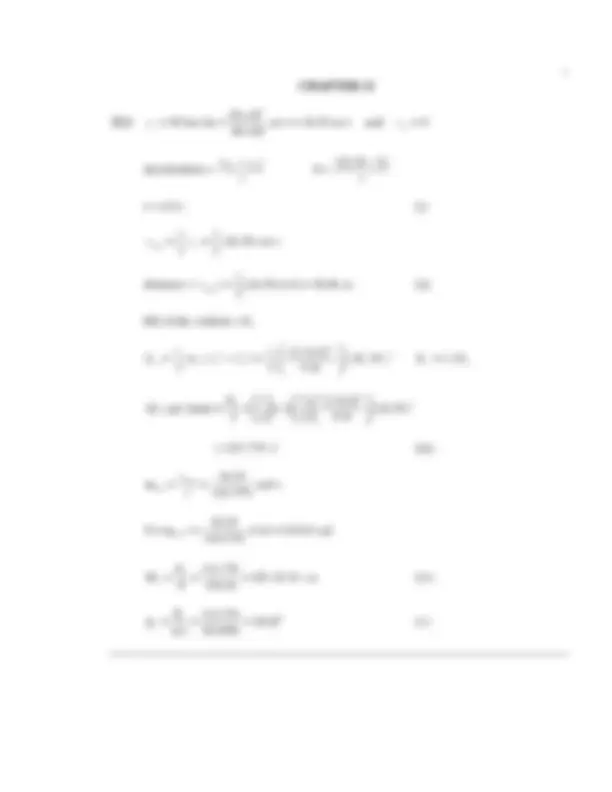
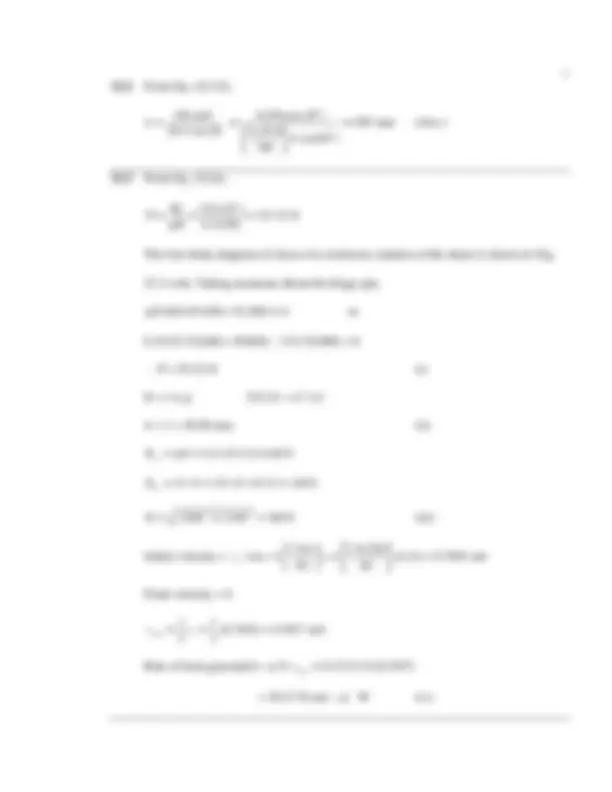
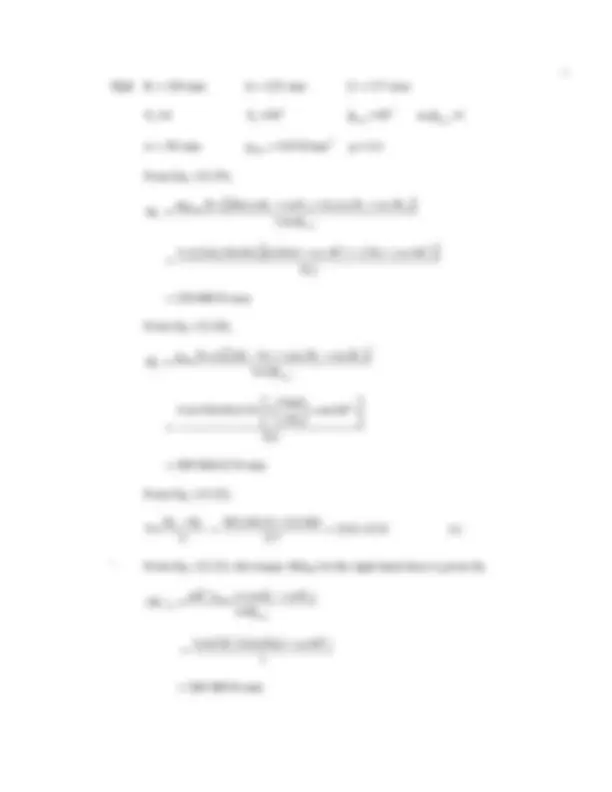
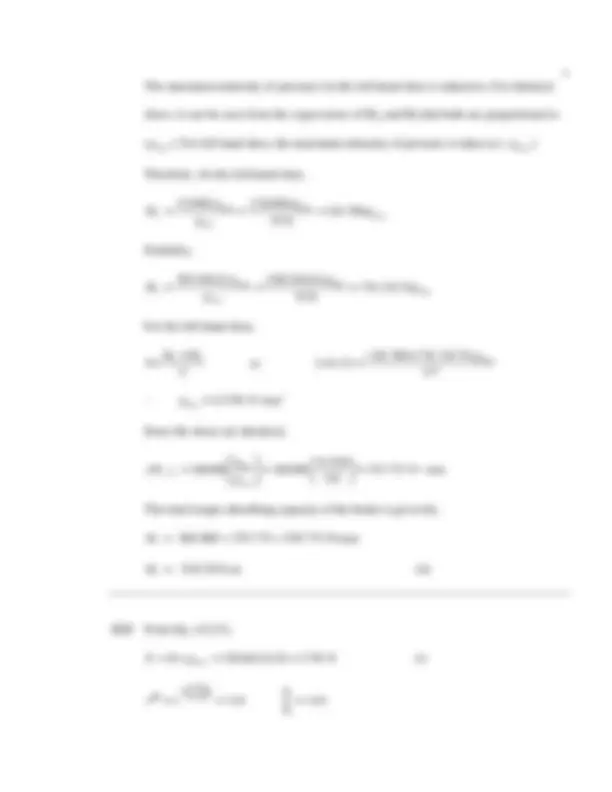
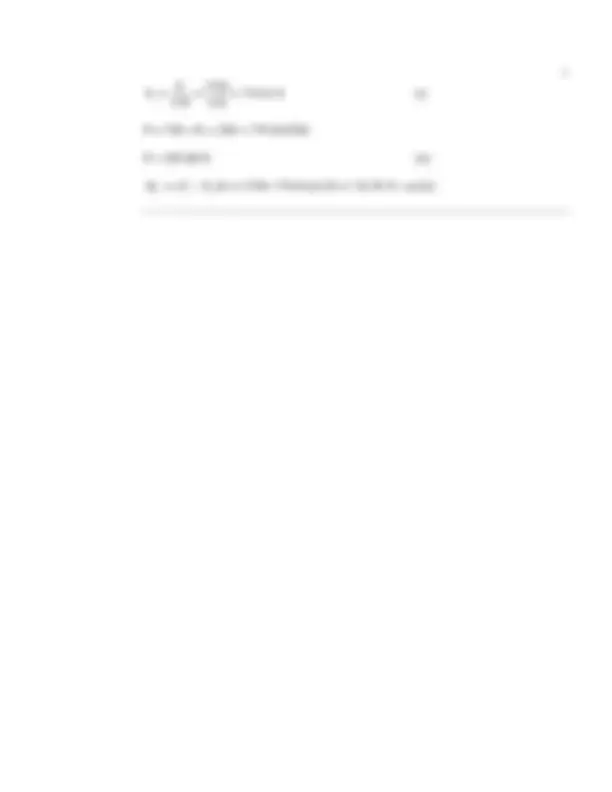
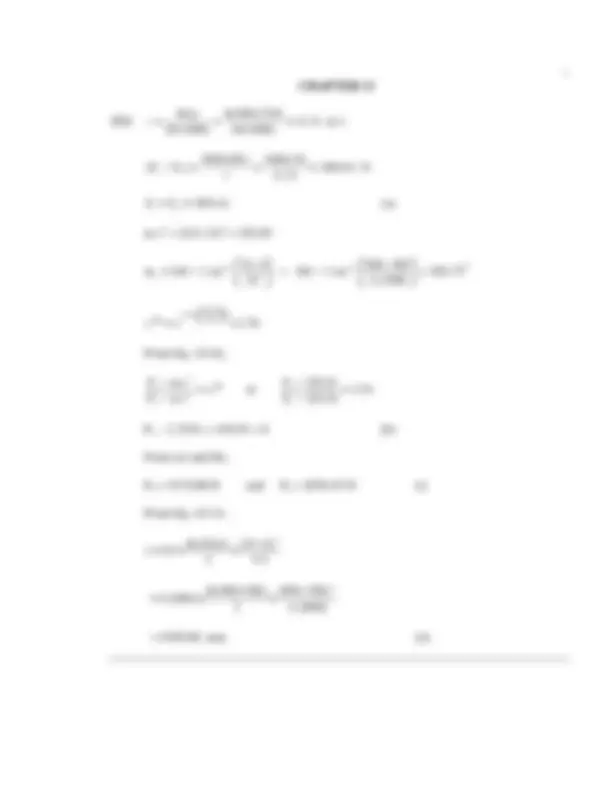
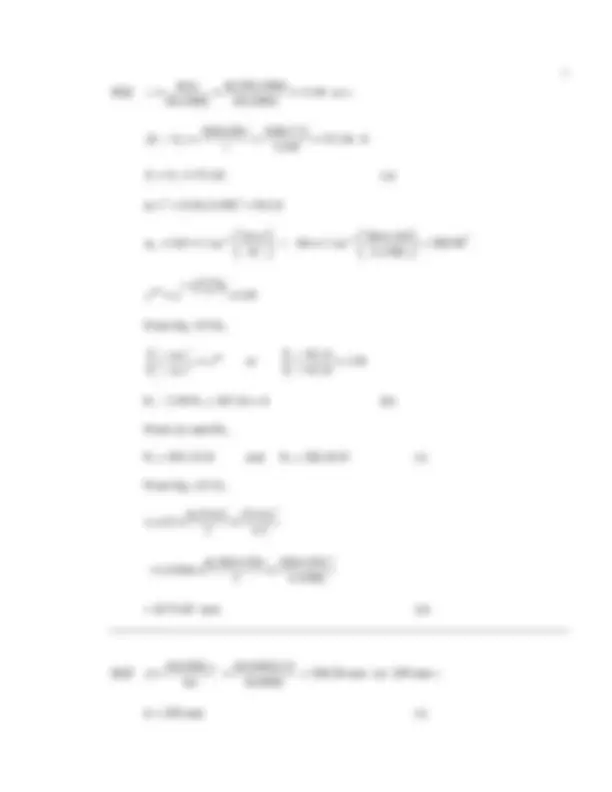
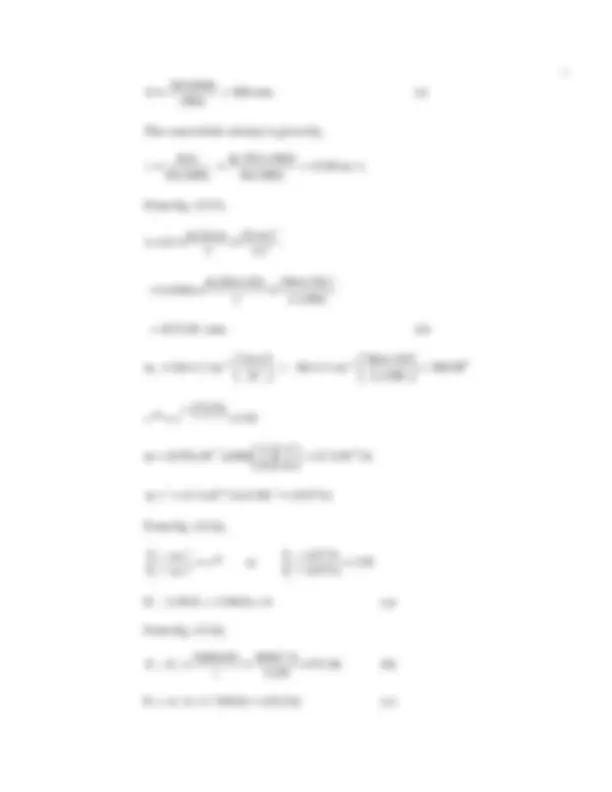
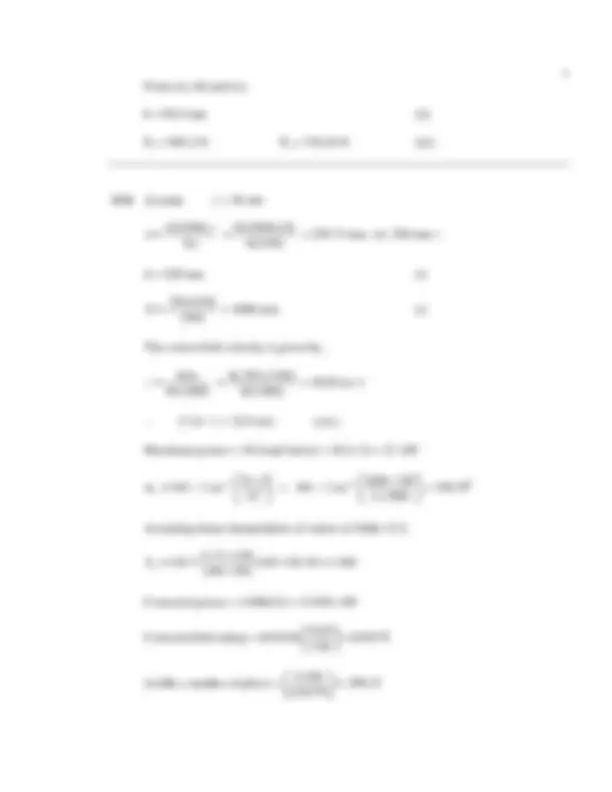
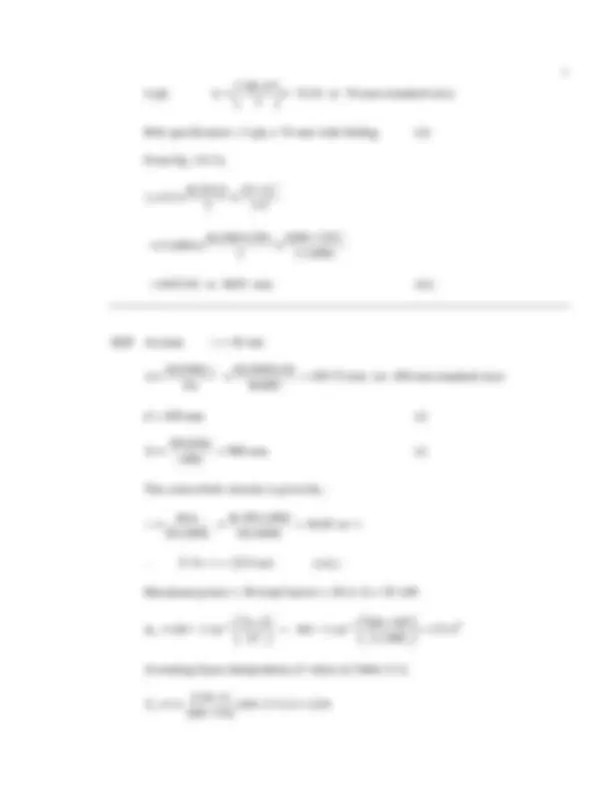
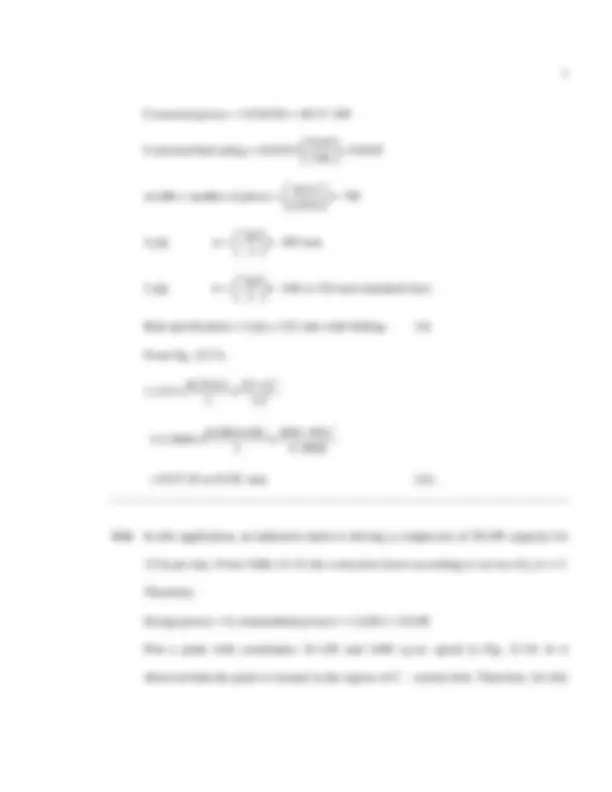
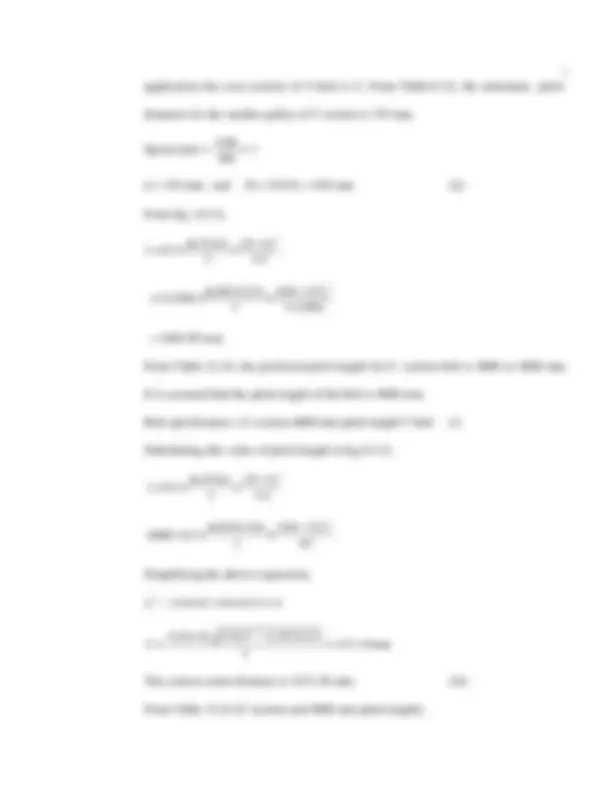
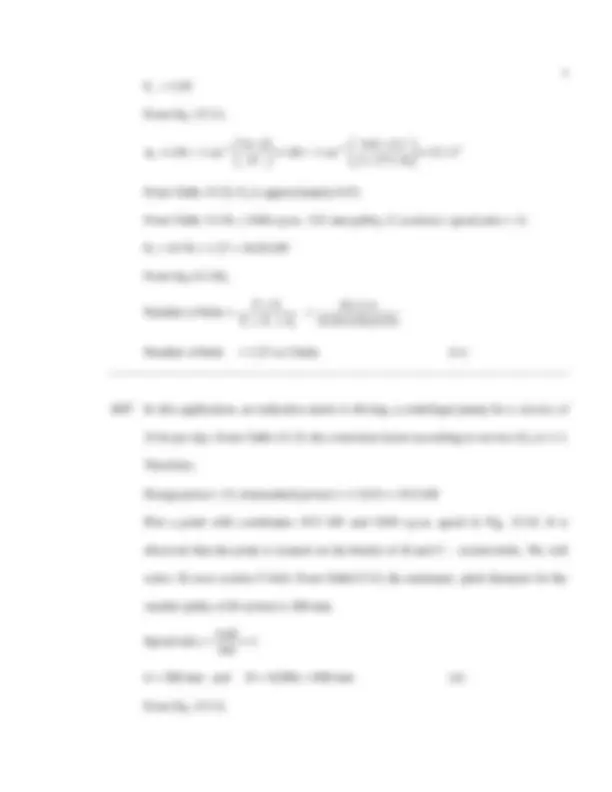
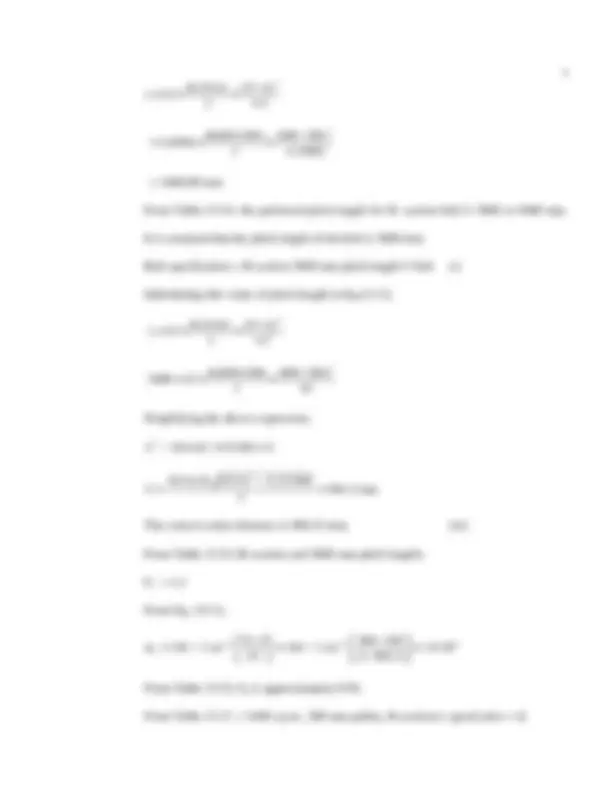
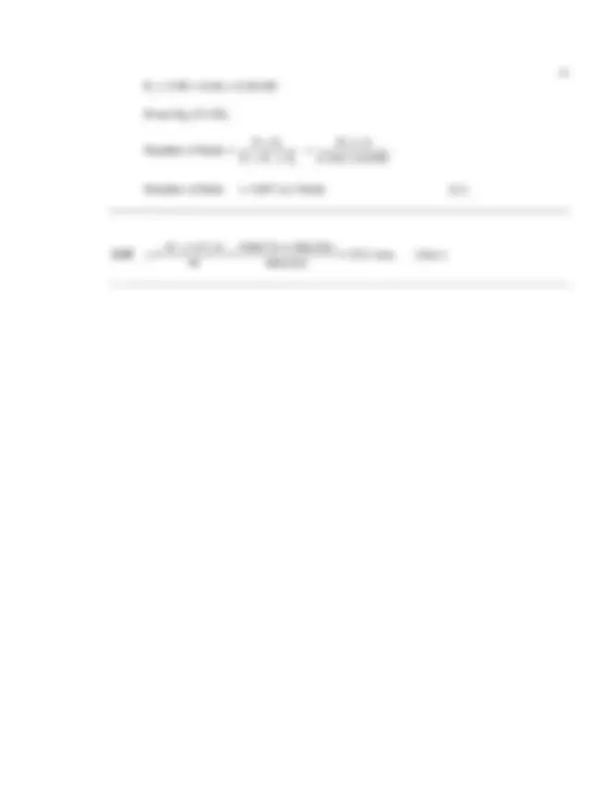
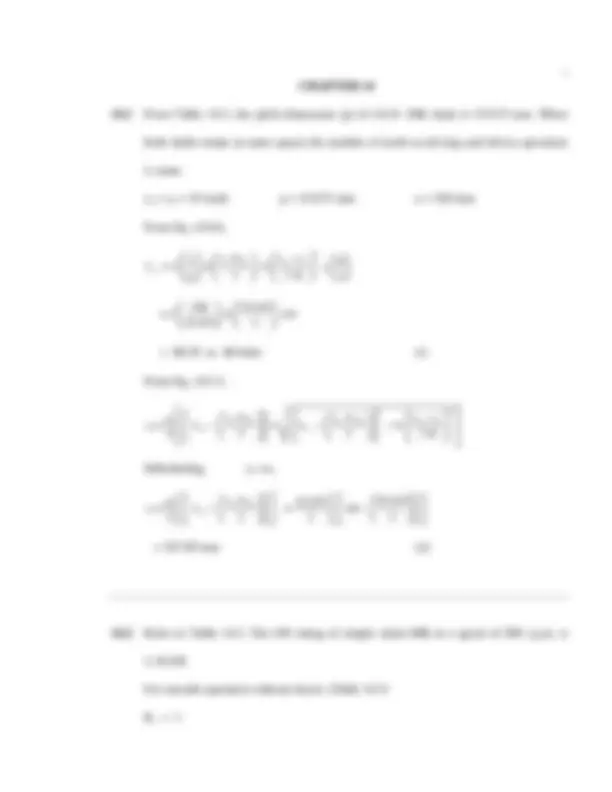
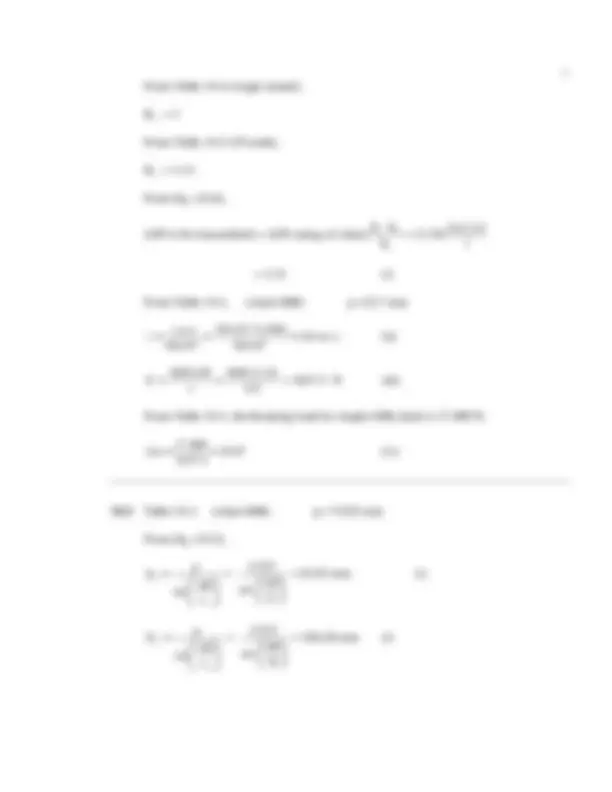
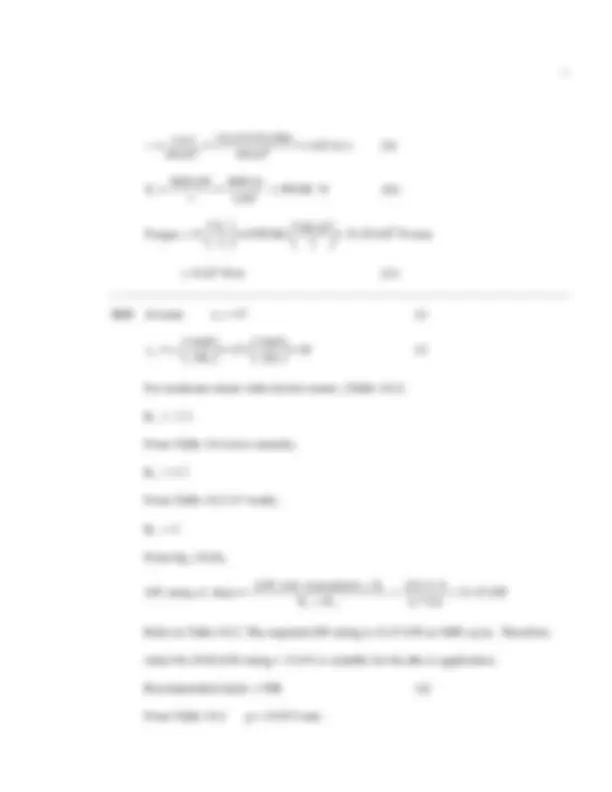
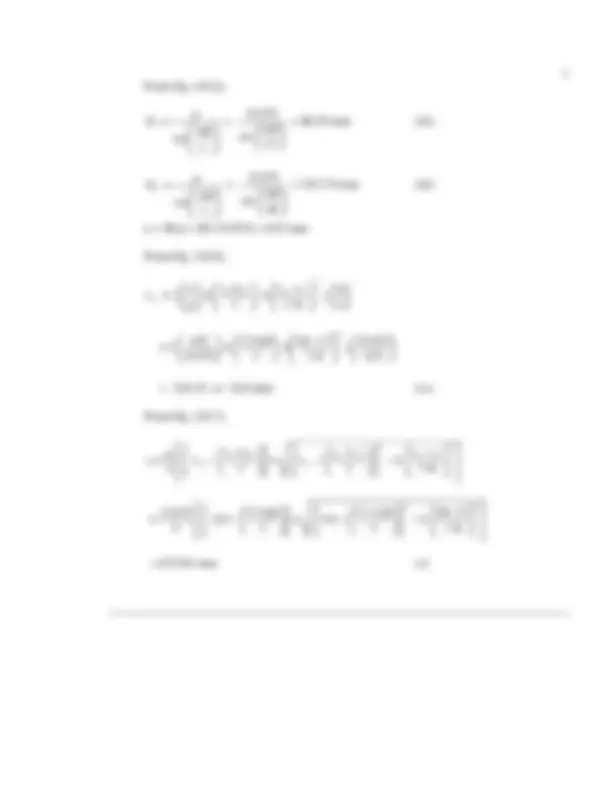
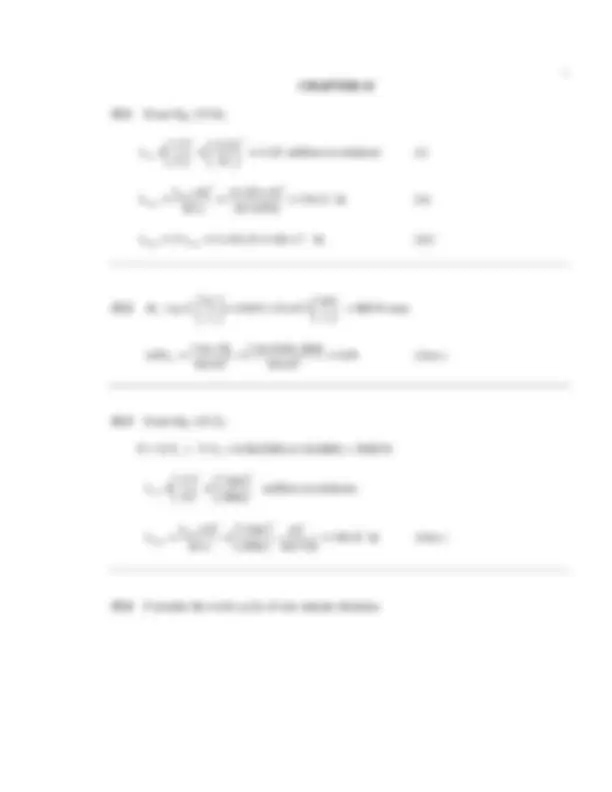
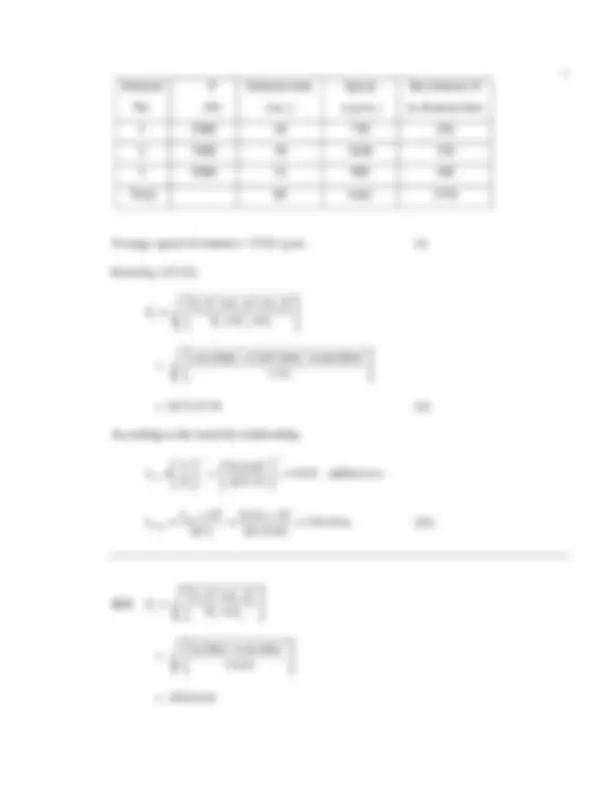
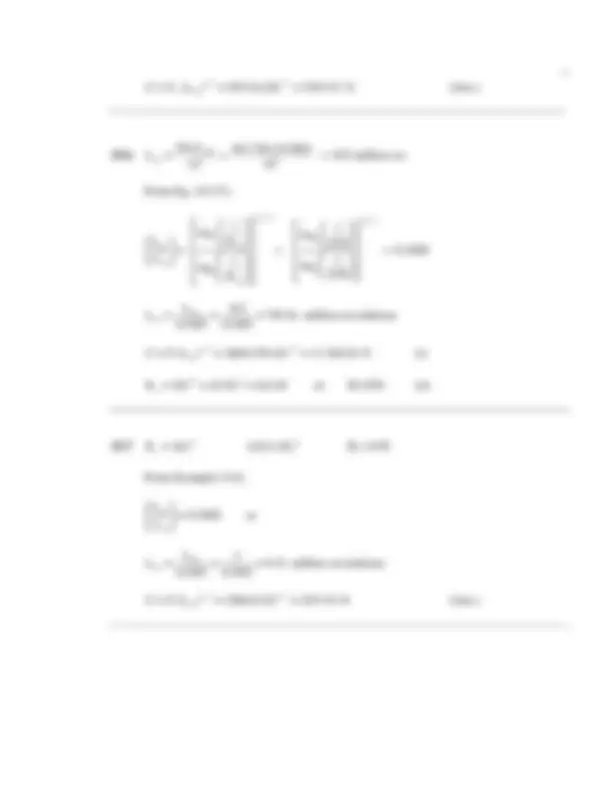
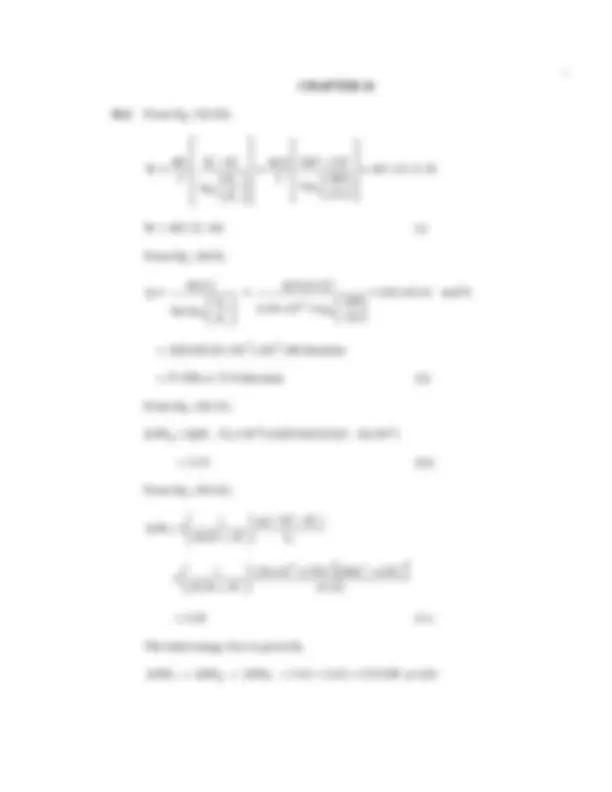
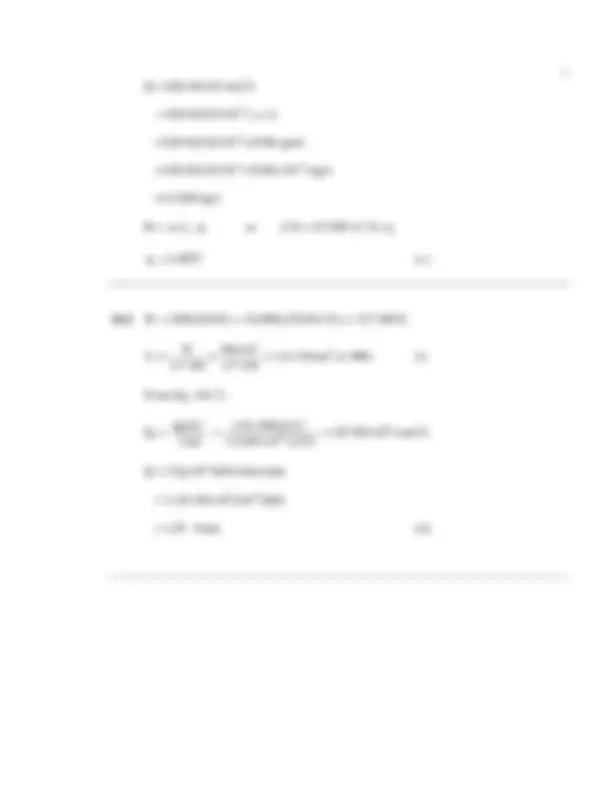
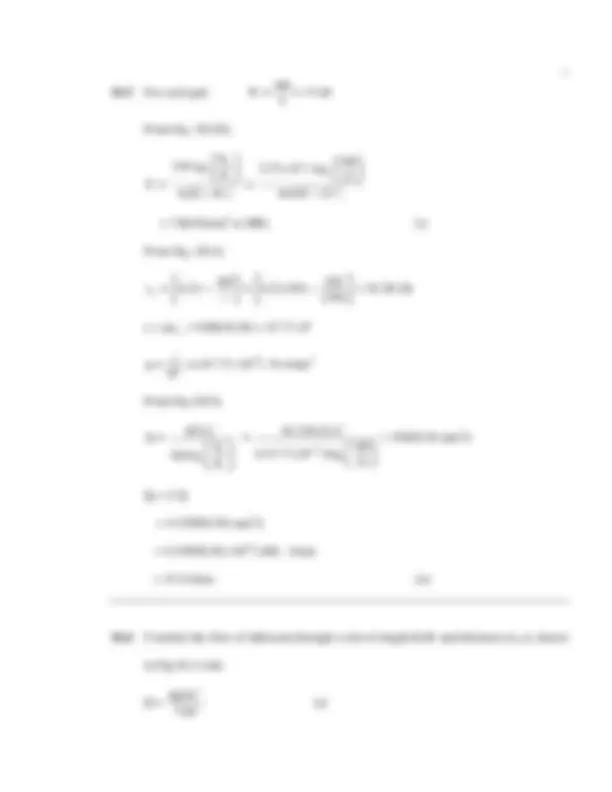
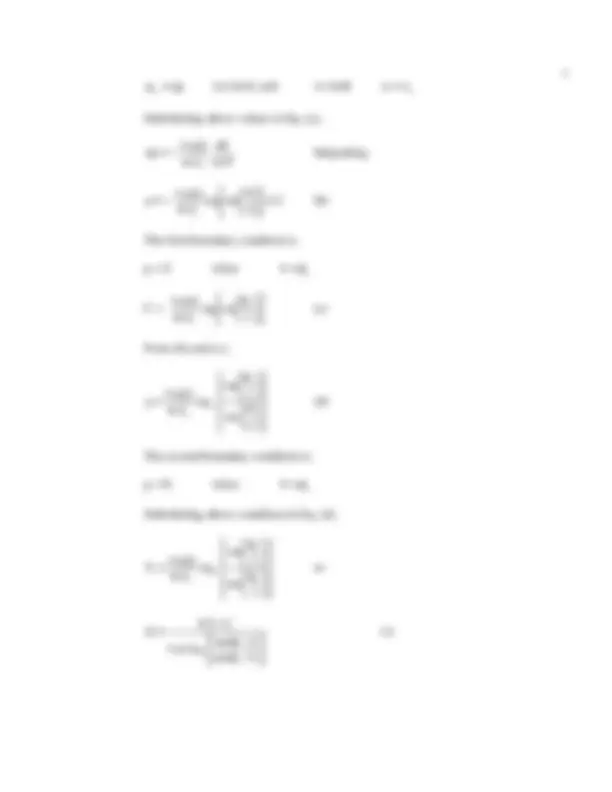
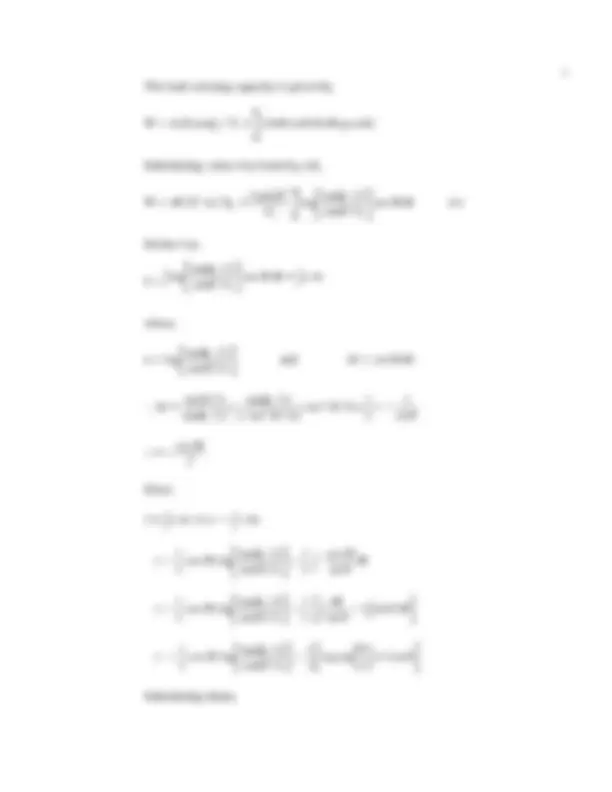
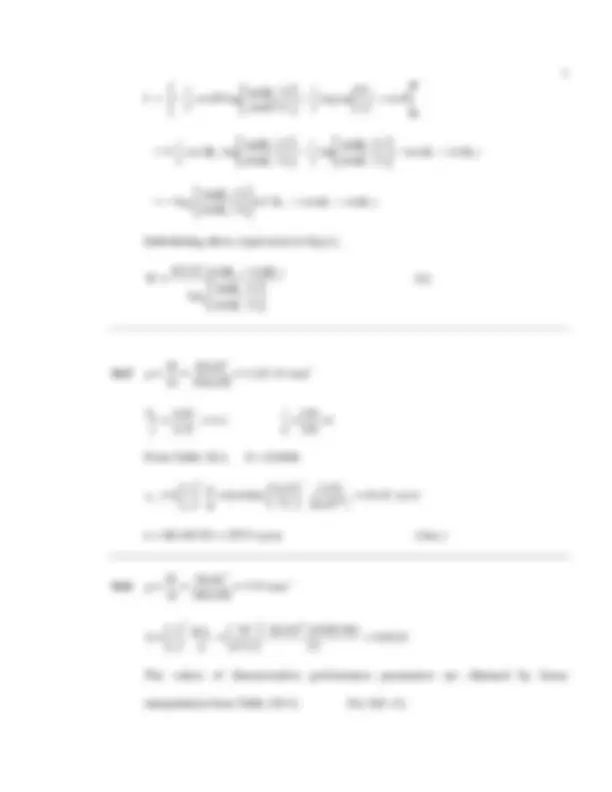
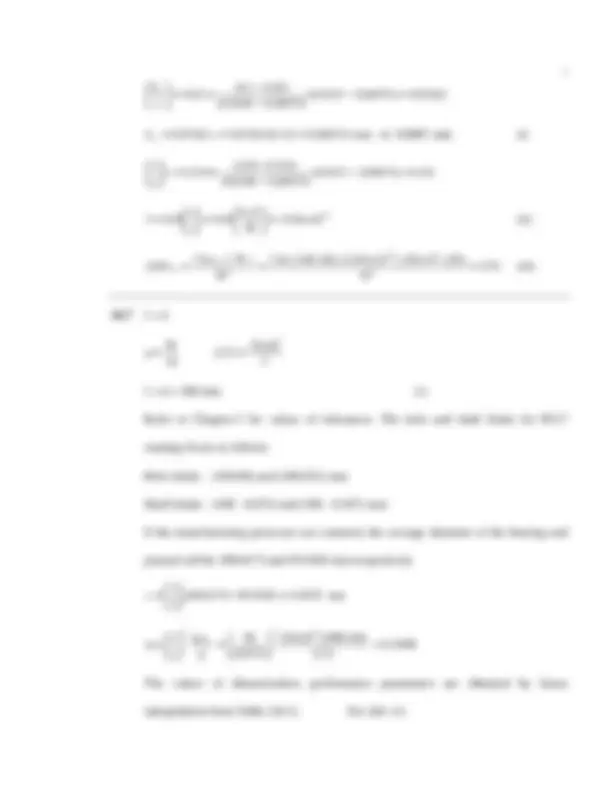
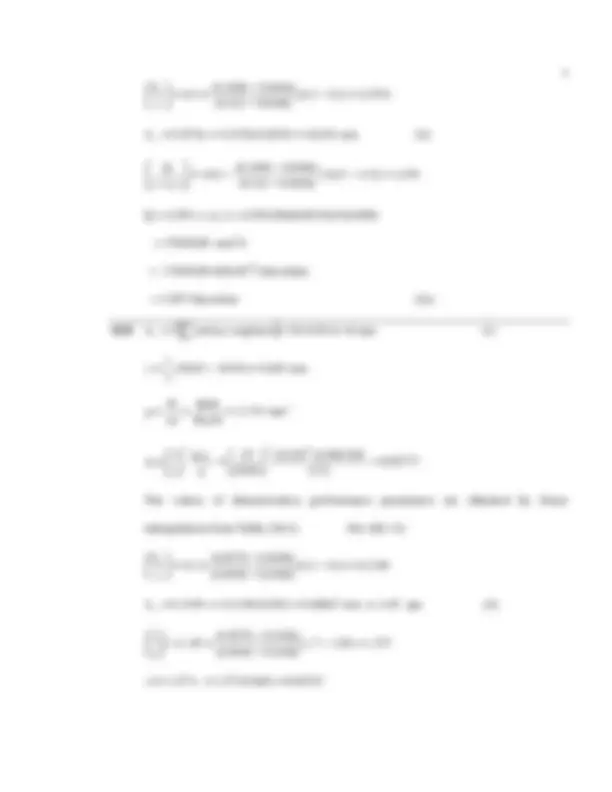
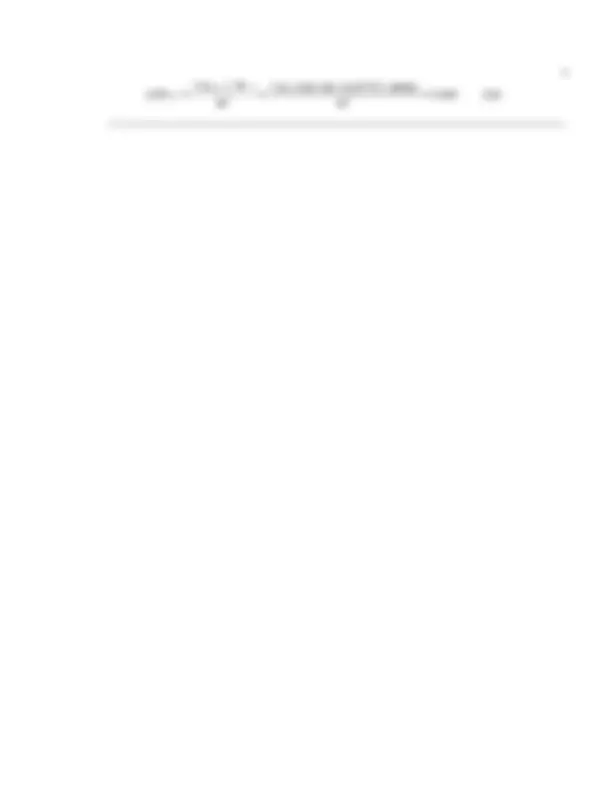
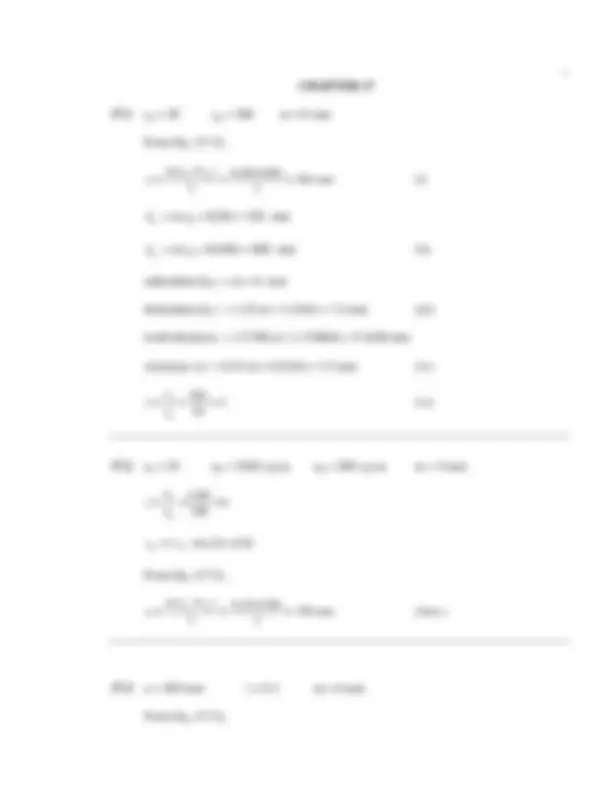
Study with the several resources on Docsity
Earn points by helping other students or get them with a premium plan
Prepare for your exams
Study with the several resources on Docsity
Earn points to download
Earn points by helping other students or get them with a premium plan
Community
Ask the community for help and clear up your study doubts
Discover the best universities in your country according to Docsity users
Free resources
Download our free guides on studying techniques, anxiety management strategies, and thesis advice from Docsity tutors
A detailed technical analysis of various mechanical design concepts and calculations. It covers a wide range of topics including bolt design, shaft design, gear design, flywheel design, and more. Numerous equations, formulas, and numerical examples to illustrate the application of these design principles. It seems to be a comprehensive resource for students or professionals studying mechanical engineering design. The level of detail and mathematical rigor suggests this document could be useful as lecture notes, study materials, or reference material for advanced courses in mechanical design, machine design, or related engineering disciplines.
Typology: Study notes
Uploaded on 09/26/2022
1 document
1 / 154
This page cannot be seen from the preview
Don't miss anything!
2
2
3
3
4
4
5
5
6
6
7
7
8
8
9
9
10
3 φ= =
0
1
2
3
4
5
6
7 72 (φ)
8
9
10 72 (φ)
10
1 / 10
⎟ = =^ = ⎠
φ=
2
3
4
5
6
7
8
9
10
yt 2 t 83.^3 N/mm 3
(fs)
σ = = =
t
2 dr 4
P (^) ⎟σ ⎠
⎛ π
2 r ⎟ ⎠
⎛ π
sy yt 2
(fs)
(fs)
τ= = = =
⎟^ τ ⎠
2 dp 4
P 2 ∴ d ( 41. 67 ) 4
2 p ⎟ ⎠
⎛ π
ut 2 t 120 N/mm
(fs)
σ = = =
2 2 N/mm t
(t)( 5 t)
2 2 3
N/mm t
(t)( 5 t) 12
15000 ( 7. 5 t)( 2. 5 t)
I
P ey ⎟ ⎠
Pey
A
t
t
t
2 ( σ 1 −σ 2 )= 50 N/mm
2
2 ( σ 2 −σ 3 )= 150 N/mm
(fs)
yt
(fs)
( )
2 1 2 2
2 1
yt
(fs)
= σ −σ σ +σ
2 2 ( 200 ) ( 200 )( 150 ) ( 150 ) (fs)
x y 2 70 N/mm 2
⎛ σ +σ
x y 2 30 N/mm 2
⎛ σ −σ
2 xy
2 x y x y 1 2 ( ) 2 2
, + τ ⎟
⎛ σ −σ ± ⎟
⎛ σ +σ σ σ =
2 2 = 70 ± ( 30 ) +( 80 )
2 σ 1 = 155. 44 N/mm
2 σ 2 =− 15. 44 N/mm σ 3 = 0
2 xy
2 x y max ( ) 2
⎛ σ −σ τ =
2 2
2
(fs) 1
yt = = σ
(fs) max
yt
max
sy = = τ
τ
( ) [ ]
2 2 2 2 1 2 2
2 σ 1 −σ σ +σ = ( 155. 44 ) −( 155. 44 )(− 15. 44 )+(− 15. 44 ) = 163. 71 N/mm
[ ]
10 t t
10 t 4 tlog 4 t t
10 t t tlog 4 t
4 t t 4 tlog
t( 4 t t) t( 4 t t) t( 6 t) R
e e e
e =R−RN =( 7 − 6. 3098 )t=( 0. 6902 t)mm
h (^) i =RN−Ri=( 6. 3098 − 4 )t=( 2. 3098 t) mm
M ( 100 x 10 )( 4 t R) ( 100 x 10 )( 4 t 7 t) ( 11 x 10 )t N mm
3 3 5 b = + = + = −
2 2 2 2 2 A = 4 t + 4 t + 4 t =( 12 t )mm
2 2
5
2
5
i
b i bi N/mm 12 t
( 12 t )( 0. 6902 t)( 4 t)
( 11 x 10 t)( 2. 3098 t)
AeR
M h ⎟
σ = = =
2 2
5
2
3
t N/mm 12 t
( 12 t )
100 x 10
A
σ = = =
2
5
2
5
i
ut b i 12 t
12 t
AeR
M h
A
(fs)
yt 2 t 60 N/mm 5
(fs)
σ = = =
sy yt 2 30 N/mm 5
(fs)
(fs)
τ= = = =
3
2 2
2
2 2
( 22. 58 ) 4
d 4
⎛ π
⎛ π
M (^) by
b( 4 b) 12
( 7500 x 100 )( 2 b)
yt 2 t 50 N/mm 4
(fs)
σ = = =
M (^) by
t( 2 t) 12
1166 266. 25 xt
3
t
2
2 2
V t t
2 t
2
3 2
3
t
t
3
2
3
o 60.^61 N/mm ( 25 3 ) 15
20 x 10
(w d)t
σ =
w
d ⎟= ⎠
2
2
3
o 66.^67 N/mm ( 25 5 ) 15
20 x 10
(w d)t
σ =
w
d ⎟= ⎠
2
2
3
o 88.^89 N/mm ( 25 10 ) 15
20 x 10
(w d)t
σ =
w
d ⎟= ⎠
2
d
d
r ⎟= ⎠
r
2 3
3
3
b b 93.^94 N/mm ( 11. 76 )
32 ( 15 x 10 )
d
π
π
σ =
2
(fs) max
ut (^) = = σ
M (^) b = 2500 ( 25 )= 62500 N−mm
2 3 3
b b 9.^947 N/mm ( 40 )
d
π
π
σ =
d
d
r ⎟= = ⎠
2
ut^2 max 140 N/mm
(fs)
σ = = =
2
3
o 66.^67 N/mm ( 30 )( 10 )
20 x 10
dt
σ = = =
o
max t = = σ
σ
d
d
r ⎟= ⎠
K (^) f = 1 +q(Kt− 1 )= 1 + 0. 9 ( 1. 72 − 1 )= 1. 648
f
d = = =
' 2 Se =KaKbKdSe= 0. 78 ( 0. 85 )( 0. 61 )( 270 )= 109. 20 N/mm
e 2 b 54.^6 N/mm 2
(fs)
σ = = =
3
b b d
π
3
d
32 ( 5 x 10 )( 100 )
2 ut
' Se = 0. 5 S = 0. 5 ( 620 )= 310 N/mm
' 2 Se =KaKbKcSe = 0. 89 ( 0. 85 )( 0. 897 )( 310 )= 210. 36 N/mm
2 Sse = 0. 577 Se= 0. 577 ( 210. 36 )= 121. 38 N/mm
se^2 a 60.^69 N/mm 2
(fs)
τ = = =
(M (^) t )max= 400 N− m (M (^) t )min =− 200 N−m
[ ] [( 400 ) ( 200 )] 300 N m 2
(M (^) t )a= t max − t min = − − = −
3
t a a d
π
τ = or (^3)
3
d
16 ( 300 x 10 )
2 xym 17.^5 N/mm 2
τ =
2 xya 17.^5 N/mm 2
τ =
2 xm 7.^5 N/mm 2
σ =
2 xa 22.^5 N/mm 2
σ =
2 2 2 2 xym
2 σm = ( σxm) + 3 (τ ) = ( 7. 5 ) + 3 ( 17. 5 ) = 31. 22 N/mm
2 2 2 2 xya
2 σa = ( σxa) + 3 (τ ) = ( 22. 5 ) + 3 ( 17. 5 ) = 37. 75 N/mm
tan m
a (^) = = σ
σ θ = or
0 θ= 50. 4
S (^) m a
m
a (^) =
2
2 S (^) m = 127. 36 N/mm
(fs) a
a (^) = = σ
2 τ (^) xym = 70 N/mm
2 τxya = 35 N/mm
2 σ (^) xm = 60 N/mm
2 σxa = 80 N/mm
2 2 2 2 xym
2 σm = ( σxm) + 3 (τ ) = ( 60 ) + 3 ( 70 ) = 135. 28 N/mm
2 2 2 2 xya
2 σa = ( σxa) + 3 (τ ) = ( 80 ) + 3 ( 35 ) = 100. 37 N/mm
tan m
a (^) = = σ
σ θ = or
0 θ= 36. 57
m
0
0
0
0
3 m
3 c o i t c
3
t t
m
0
0
m t
3
m t
3
3
2 c
2 b