
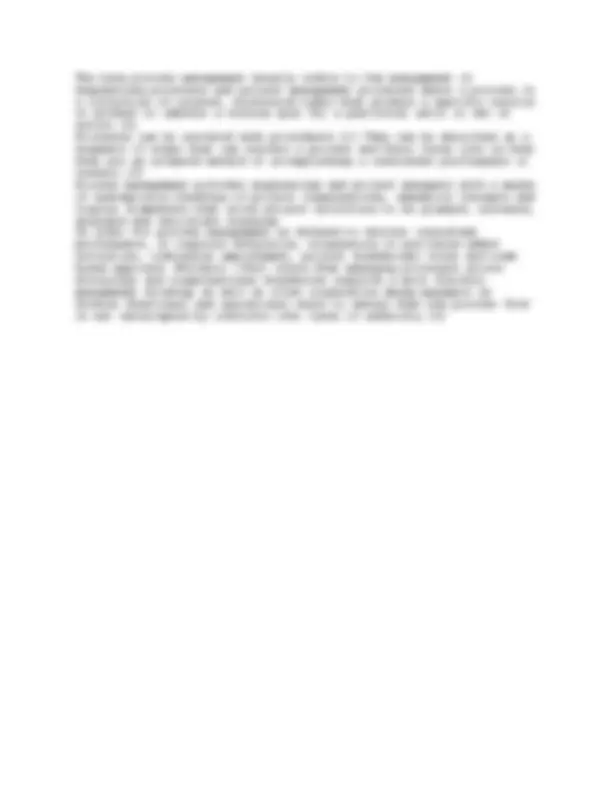
Study with the several resources on Docsity
Earn points by helping other students or get them with a premium plan
Prepare for your exams
Study with the several resources on Docsity
Earn points to download
Earn points by helping other students or get them with a premium plan
Community
Ask the community for help and clear up your study doubts
Discover the best universities in your country according to Docsity users
Free resources
Download our free guides on studying techniques, anxiety management strategies, and thesis advice from Docsity tutors
Useful notes of manufacturing process of engineering department
Typology: Summaries
1 / 2
This page cannot be seen from the preview
Don't miss anything!
Manufacturing process management Manufacturing process management (MPM) is a collection of technologies and methods used to define how products are to be manufactured. MPM differs from ERP/MRP which is used to plan the ordering of materials and other resources, set manufacturing schedules, and compile cost data.[1] A cornerstone of MPM is the central repository for the integration of all these tools and activities aids in the exploration of alternative production line scenarios; making assembly lines more efficient with the aim of reduced lead time to product launch, shorter product times and reduced work in progress (WIP) inventories as well as allowing rapid response to product or product changes. Production process planning Manufacturing concept planning Factory layout planning and analysis work flow simulation. walk-path assembly planning plant design optimization Mixed model line balancing. Workloads on multiple stations. Process simulation tools e.g. die press lines, manufacturing lines Ergonomic simulation and assessment of production assembly tasks Resource planning Computer-aided manufacturing (CAM) Numerical control CNC Direct numerical control (DNC) Tooling/equipment/fixtures development Tooling and Robot work-cell setup and offline programming (OLP) Generation of shop floor work instructions Time and cost estimates ABC – Manufacturing activity-based costing Outline of industrial organization Quality computer-aided quality assurance (CAQ) Failure mode and effects analysis (FMEA) Statistical process control (SPC) Computer aided inspection with coordinate-measuring machine (CMM) Tolerance stack-up analysis using PMI models. Success measurements Overall equipment effectiveness (OEE), Communication with other systems Enterprise resource planning (ERP) Manufacturing operations management (MOM) Product data management (PDM) SCADA (supervisory control and data acquisition) real time process monitoring and control Human–machine interface (HMI) (or man-machine interface (MMI)) In civil engineering and project management, process management is the management of "systematic series of activities directed towards causing an end result such that one or more inputs will be acted upon to create one or more outputs".[1] Process management offers project organizations a means of applying the same quality improvement and defect reduction techniques used in business and manufacturing processes by taking a process view of project activity; modeling discrete activities and high-level processes.[ Distributed control system (DCS)
The term process management usually refers to the management of engineering processes and project management processes where a process is a collection of related, structured tasks that produce a specific service or product to address a certain goal for a particular actor or set of actors.[4] Processes can be executed with procedures.[1] They can be described as a sequence of steps that can execute a process and their value lies in that they are an accepted method of accomplishing a consistent performance or results.[3] Process management provides engineering and project managers with a means of systemically thinking of project organizations, semantics concepts and logical frameworks that allow project activities to be planned, executed, analyzed and facilitate learning. In order for process management as defined to deliver consistent performance, it requires definition, elimination of non-value-added activities, continuous improvement, project stakeholder focus and team based approach. Mitchell (2016) notes that managing processes across divisional and organizational boundaries requires a more flexible management strategy as well as close cooperation among managers in diverse functional and operational units to ensure that the process flow is not interrupted by conflicts over lines of authority.[5]