
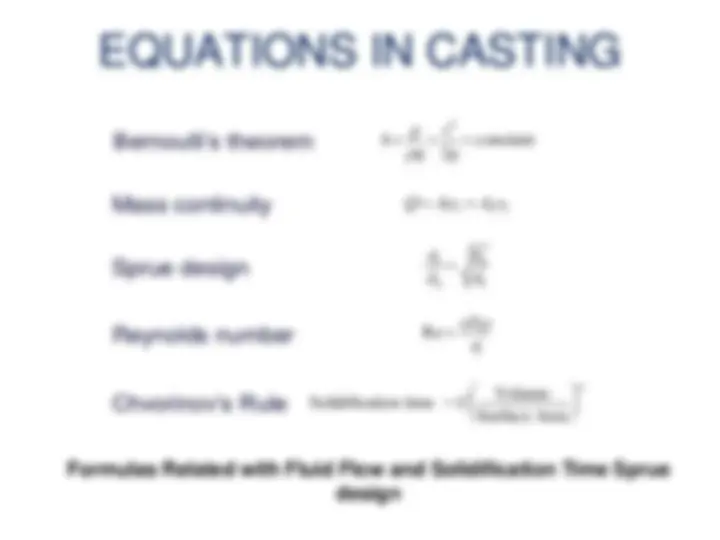
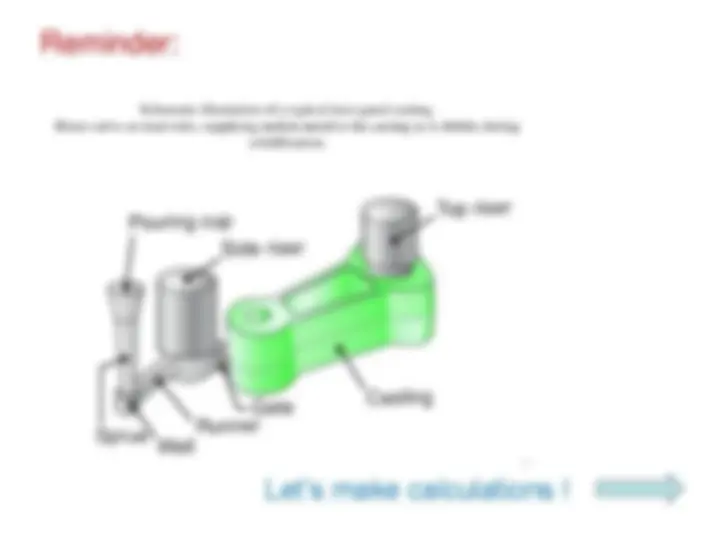
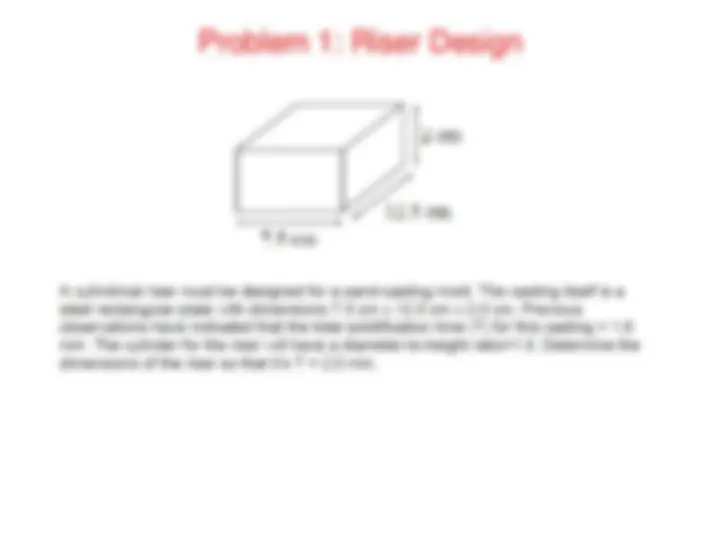
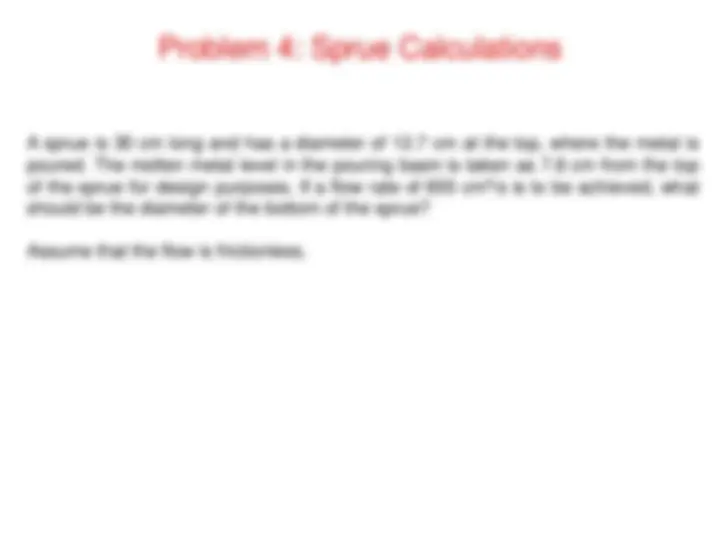
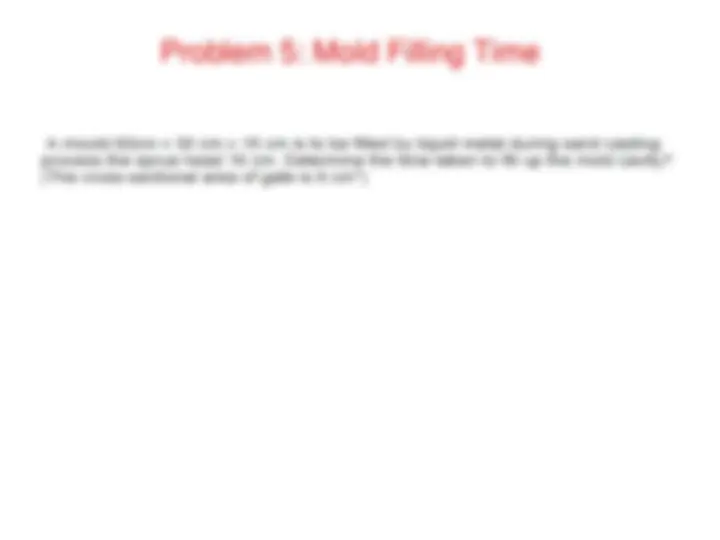
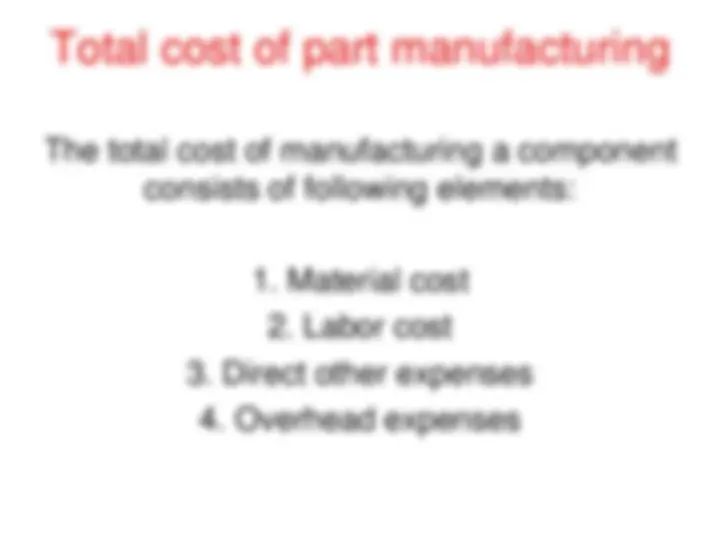
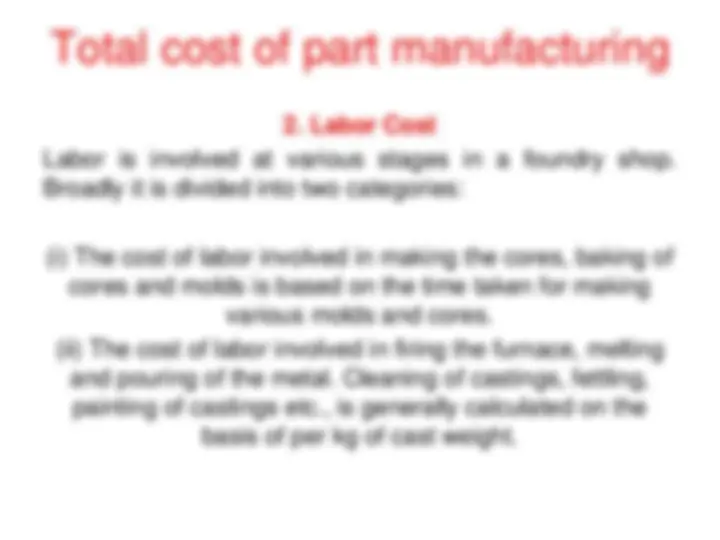

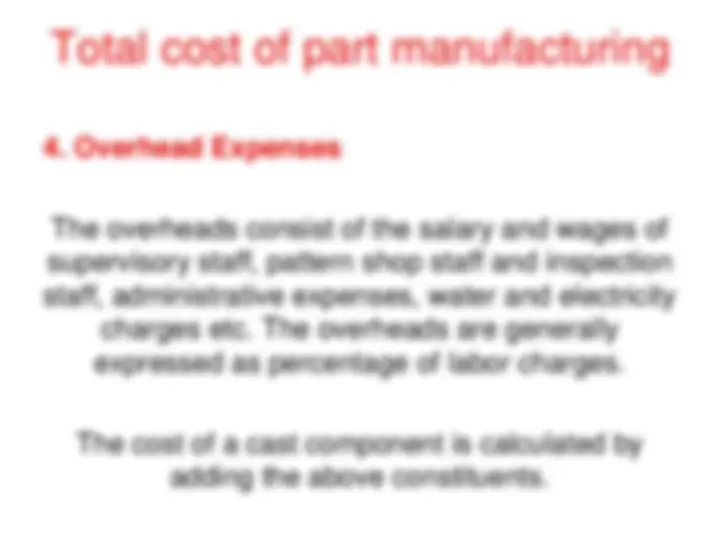
Study with the several resources on Docsity
Earn points by helping other students or get them with a premium plan
Prepare for your exams
Study with the several resources on Docsity
Earn points to download
Earn points by helping other students or get them with a premium plan
Community
Ask the community for help and clear up your study doubts
Discover the best universities in your country according to Docsity users
Free resources
Download our free guides on studying techniques, anxiety management strategies, and thesis advice from Docsity tutors
MAnu İmalat yöntemleri Yıldız tekink üniversitesi
Typology: Lecture notes
1 / 15
This page cannot be seen from the preview
Don't miss anything!
Reminder: Let’s make calculations!
Problem 1: Riser Design
Problem 3: Sprue Calculations
Problem 4: Sprue Calculations A sprue is 30 cm long and has a diameter of 12. 7 cm at the top, where the metal is poured. The molten metal level in the pouring basin is taken as 7. 6 cm from the top of the sprue for design purposes. If a flow rate of 655 cm 3 /s is to be achieved, what should be the diameter of the bottom of the sprue? Assume that the flow is frictionless.
1. Material Cost (a) Cost of material required for casting is calculated as follows : (i) From the component drawing, calculate the volume of material required for casting. This volume multiplied by density of material gives the net weight of the casting. (ii) Add the weight of process scrap i.e. weight of runners, gates and risers and other material consumed as a part of process in getting the casting. (iii) Add the allowance for metal loss in oxidation in furnace, in cutting the gates and runners and over runs etc. (iv) Multiply the total weight by cost per unit weight of the material used. (v) Subtract the value of scrap return from the amount obtained in step (iv), to get the direct material cost. Note: The casting drawing is made by adding various allowances like- shrinkage, draft and machining allowance, etc., to the dimensions of finished component.
2. Labor Cost Labor is involved at various stages in a foundry shop. Broadly it is divided into two categories: (i) The cost of labor involved in making the cores, baking of cores and molds is based on the time taken for making various molds and cores. (ii) The cost of labor involved in firing the furnace, melting and pouring of the metal. Cleaning of castings, fettling, painting of castings etc., is generally calculated on the basis of per kg of cast weight.