
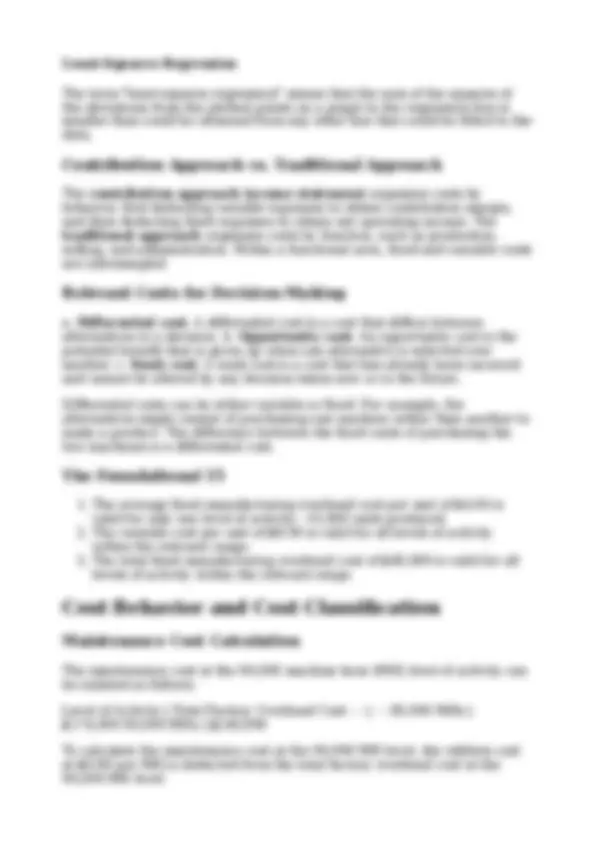
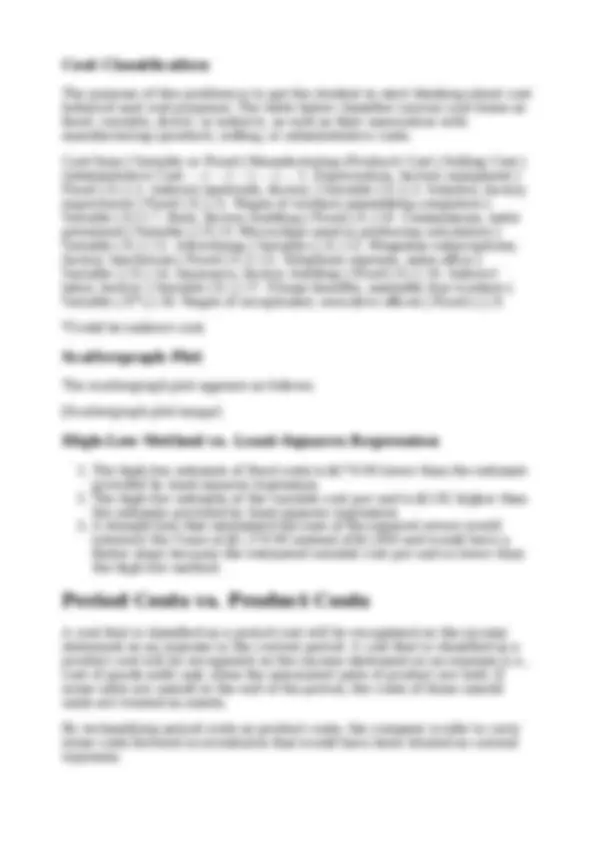
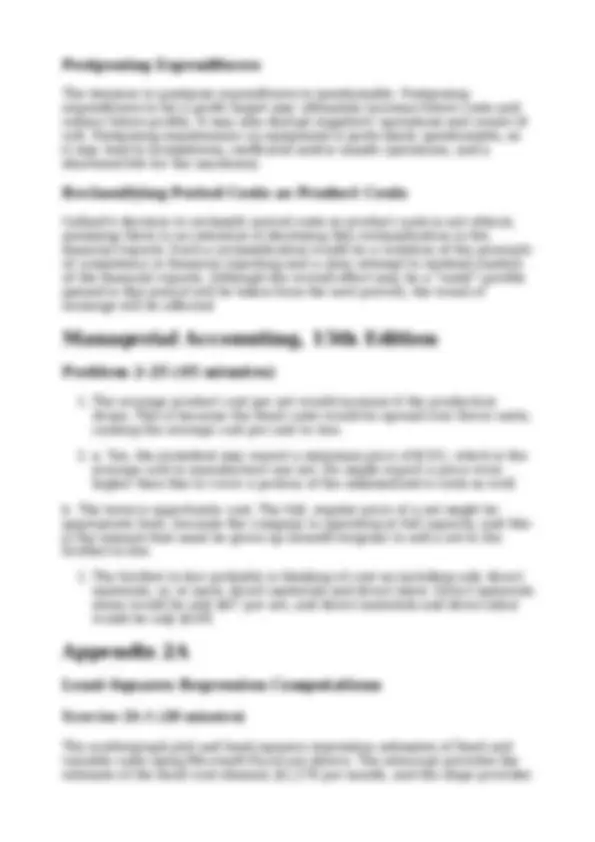
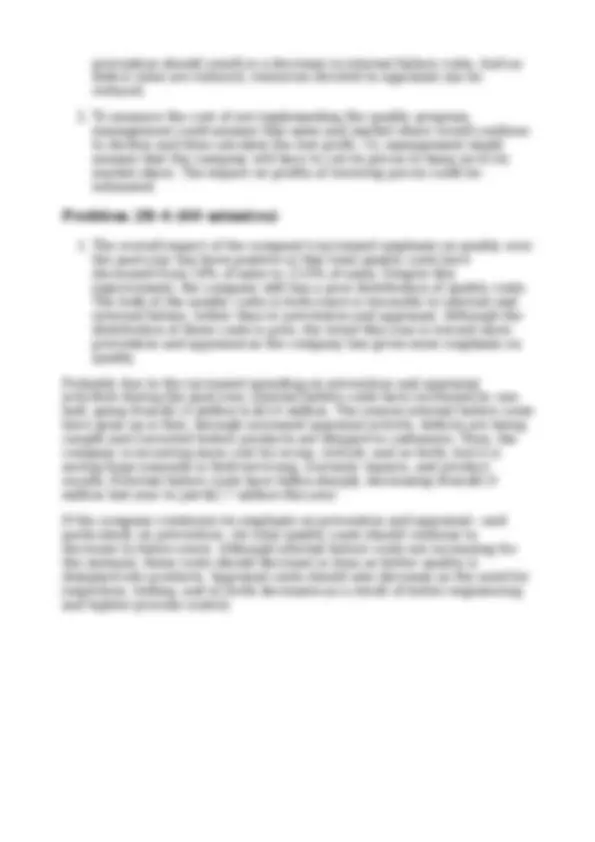
Study with the several resources on Docsity
Earn points by helping other students or get them with a premium plan
Prepare for your exams
Study with the several resources on Docsity
Earn points to download
Earn points by helping other students or get them with a premium plan
Community
Ask the community for help and clear up your study doubts
Discover the best universities in your country according to Docsity users
Free resources
Download our free guides on studying techniques, anxiety management strategies, and thesis advice from Docsity tutors
This document delves into the fundamental concepts of cost behavior in managerial accounting, exploring the classification of costs as variable, fixed, or mixed. It examines the relevant range, activity base, and linear assumption in cost behavior analysis. The document also discusses cost estimation methods, including the high-low method and least-squares regression, and highlights the importance of understanding cost behavior for decision-making. It further explores the contribution approach and traditional approach to income statement preparation, emphasizing the significance of cost behavior in financial reporting.
Typology: Exercises
1 / 8
This page cannot be seen from the preview
Don't miss anything!
The three major elements of product costs in a manufacturing company are: a. Direct materials b. Direct labor c. Manufacturing overhead
Direct and Indirect Costs
a. Direct materials are an integral part of a finished product, and their costs can be conveniently traced to it. b. Indirect materials are generally small items of material that may be an integral part of a finished product, but their costs can be traced to the product only at great cost or inconvenience. c. Direct labor consists of labor costs that can be easily traced to particular products. Direct labor is also called "touch labor." d. Indirect labor consists of the labor costs of janitors, supervisors, materials handlers, and other factory workers that cannot be conveniently traced to particular products. e. Manufacturing overhead includes all manufacturing costs except direct materials and direct labor. Consequently, manufacturing overhead includes indirect materials and indirect labor as well as other manufacturing costs.
Product Costs and Period Costs
A product cost is any cost involved in purchasing or manufacturing goods. In the case of manufactured goods, these costs consist of direct materials, direct labor, and manufacturing overhead. A period cost is a cost that is taken directly to the income statement as an expense in the period in which it is incurred.
Variable, Fixed, and Mixed Costs
a. Variable cost : The variable cost per unit is constant, but total variable cost changes in direct proportion to changes in volume. b. Fixed cost : The total fixed cost is constant within the relevant range. The average fixed cost per unit varies inversely with changes in volume. c. Mixed cost : A mixed cost contains both variable and fixed cost elements.
Cost Behavior Characteristics
a. Unit fixed costs decrease as volume increases. b. Unit variable costs remain constant as volume increases. c. Total fixed costs remain constant as volume increases. d. Total variable costs increase as volume increases.
Relevant Range and Activity Base
a. Cost behavior : Cost behavior refers to the way in which costs change in response to changes in a measure of activity such as sales volume, production volume, or orders processed. b. Relevant range : The relevant range is the range of activity within which assumptions about variable and fixed cost behavior are valid. c. Activity base : An activity base is a measure of whatever causes the incurrence of a variable cost, such as units produced, units sold, letters typed, beds in a hospital, meals served in a cafe, service calls made, etc.
Linear Assumption
The linear assumption is reasonably valid, providing that the cost formula is used only within the relevant range.
a. Discretionary fixed cost : A discretionary fixed cost has a fairly short planning horizon—usually a year. Such costs arise from annual decisions by management to spend on certain fixed cost items, such as advertising, research, and management development. b. Committed fixed cost : A committed fixed cost has a long planning horizon—generally many years. Such costs relate to a company's investment in facilities, equipment, and basic organization. Once such costs have been incurred, they are "locked in" for many years.
Yes, as the anticipated level of activity changes, the level of fixed costs needed to support operations may also change. Most fixed costs are adjusted upward and downward in large steps, rather than being absolutely fixed at one level for all ranges of activity.
High-Low Method
The high-low method uses only two points to determine a cost formula. These two points are likely to be less than typical because they represent extremes of activity.
The purpose of this problem is to get the student to start thinking about cost behavior and cost purposes. The table below classifies various cost items as fixed, variable, direct, or indirect, as well as their association with manufacturing (product), selling, or administrative costs.
Cost Item | Variable or Fixed | Manufacturing (Product) Cost | Selling Cost | Administrative Cost --- | --- | --- | --- | --- 1. Depreciation, factory equipment | Fixed | X | | 2. Indirect materials, factory | Variable | X | | 3. Salaries, factory supervisors | Fixed | X | | 5. Wages of workers assembling computers | Variable | X | | 7. Rent, factory building | Fixed | X | | 8. Commissions, sales personnel | Variable | | X | 9. Microchips used in producing calculators | Variable | X | | 11. Advertising | Variable | | X | 12. Magazine subscriptions, factory lunchroom | Fixed | X | | 13. Telephone expense, sales office | Variable | | X | 14. Insurance, factory building | Fixed | X | | 16. Indirect labor, factory | Variable | X | | 17. Fringe benefits, assembly-line workers | Variable | X* | | 18. Wages of receptionist, executive offices | Fixed | | | X
*Could be indirect cost.
The scattergraph plot appears as follows:
[Scattergraph plot image]
The high-low estimate of fixed costs is $170.90 lower than the estimate provided by least-squares regression. The high-low estimate of the variable cost per unit is $1.82 higher than the estimate provided by least-squares regression. A straight line that minimized the sum of the squared errors would intersect the Y-axis at $1,170.90 instead of $1,000 and would have a flatter slope because the estimated variable cost per unit is lower than the high-low method.
Period Costs vs. Product Costs
A cost that is classified as a period cost will be recognized on the income statement as an expense in the current period. A cost that is classified as a product cost will be recognized on the income statement as an expense (i.e., cost of goods sold) only when the associated units of product are sold. If some units are unsold at the end of the period, the costs of those unsold units are treated as assets.
By reclassifying period costs as product costs, the company is able to carry some costs forward in inventories that would have been treated as current expenses.
The decision to postpone expenditures is questionable. Postponing expenditures to hit a profit target may ultimately increase future costs and reduce future profits. It may also disrupt suppliers' operations and create ill will. Postponing maintenance on equipment is particularly questionable, as it may lead to breakdowns, inefficient and/or unsafe operations, and a shortened life for the machinery.
Gallant's decision to reclassify period costs as product costs is not ethical, assuming there is no intention of disclosing this reclassification in the financial reports. Such a reclassification would be a violation of the principle of consistency in financial reporting and a clear attempt to mislead readers of the financial reports. Although the overall effect may be a "wash" (profits gained in this period will be taken from the next period), the trend of earnings will be affected.
Managerial Accounting, 15th Edition
The average product cost per set would increase if the production drops. This is because the fixed costs would be spread over fewer units, causing the average cost per unit to rise.
a. Yes, the president may expect a minimum price of $153, which is the average cost to manufacture one set. He might expect a price even higher than this to cover a portion of the administrative costs as well.
b. The term is opportunity cost. The full, regular price of a set might be appropriate here, because the company is operating at full capacity, and this is the amount that must be given up (benefit forgone) to sell a set to the brother-in-law.
The brother-in-law probably is thinking of cost as including only direct materials, or, at most, direct materials and direct labor. Direct materials alone would be only $47 per set, and direct materials and direct labor would be only $106.
Appendix 2A
Exercise 2A-1 (20 minutes)
The scattergraph plot and least-squares regression estimates of fixed and variable costs using Microsoft Excel are shown. The intercept provides the estimate of the fixed cost element, $1,378 per month, and the slope provides
Appendix 2B
Exercise 2B-1 (10 minutes)
Quality of conformance Quality costs Quality circles Prevention costs, appraisal costs Internal failure costs, external failure costs External failure costs Appraisal costs Prevention costs Internal failure costs External failure costs Prevention costs, appraisal costs
Prevention costs and appraisal costs are incurred in an effort to keep poor quality of conformance from occurring. Internal and external failure costs are incurred because poor quality of conformance has occurred.
The percentage figures may not add down due to rounding.
From the analysis, it would appear that Mercury, Inc.'s program has been successful. Total quality costs have declined from 16.0% to 12.3% as a percentage of total production cost. In dollar amount, total quality costs went from $670,000 last year to $590,000 this year.
External failure costs, those costs signaling customer dissatisfaction, have declined from 9.8% of total production costs to 2.3%. These declines in warranty repairs and customer returns should result in increased sales in the future.
Appraisal costs have increased from 2.4% to 2.7% of total production cost. Internal failure costs have increased from 2.1% to 4.2% of production costs. This increase has probably resulted from the increase in appraisal activities. Defective units are now being spotted more frequently before they are shipped to customers.
Prevention costs have increased from 1.7% of total production cost to 3.1% and from 10.4% of total quality costs to 25.4%. The $80,000 increase is more than offset by decreases in other quality costs.
The initial effect of emphasizing prevention and appraisal was to reduce external failure costs and increase internal failure costs. The increase in appraisal activities resulted in catching more defective units before they were shipped to customers. As a consequence, rework and scrap costs increased. In the future, an increased emphasis on
prevention should result in a decrease in internal failure costs. And as defect rates are reduced, resources devoted to appraisal can be reduced.
To measure the cost of not implementing the quality program, management could assume that sales and market share would continue to decline and then calculate the lost profit. Or, management might assume that the company will have to cut its prices to hang on to its market share. The impact on profits of lowering prices could be estimated.
The overall impact of the company's increased emphasis on quality over the past year has been positive in that total quality costs have decreased from 16% of sales to 13.6% of sales. Despite this improvement, the company still has a poor distribution of quality costs. The bulk of the quality costs in both years is traceable to internal and external failure, rather than to prevention and appraisal. Although the distribution of these costs is poor, the trend this year is toward more prevention and appraisal as the company has given more emphasis on quality.
Probably due to the increased spending on prevention and appraisal activities during the past year, internal failure costs have increased by one half, going from $2.4 million to $3.6 million. The reason internal failure costs have gone up is that, through increased appraisal activity, defects are being caught and corrected before products are shipped to customers. Thus, the company is incurring more cost for scrap, rework, and so forth, but it is saving huge amounts in field servicing, warranty repairs, and product recalls. External failure costs have fallen sharply, decreasing from $6. million last year to just $2.7 million this year.
If the company continues its emphasis on prevention and appraisal—and particularly on prevention—its total quality costs should continue to decrease in future years. Although internal failure costs are increasing for the moment, these costs should decrease in time as better quality is designed into products. Appraisal costs should also decrease as the need for inspection, testing, and so forth decreases as a result of better engineering and tighter process control.