
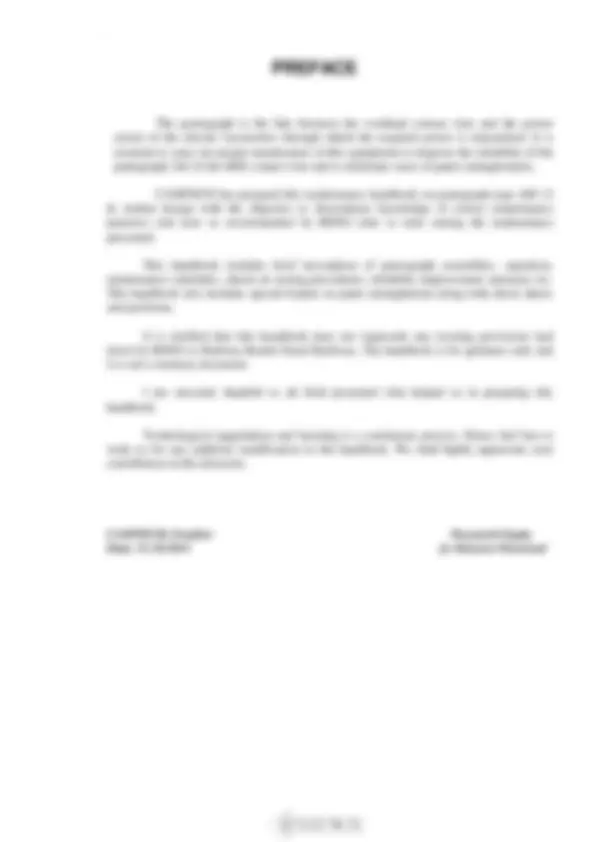
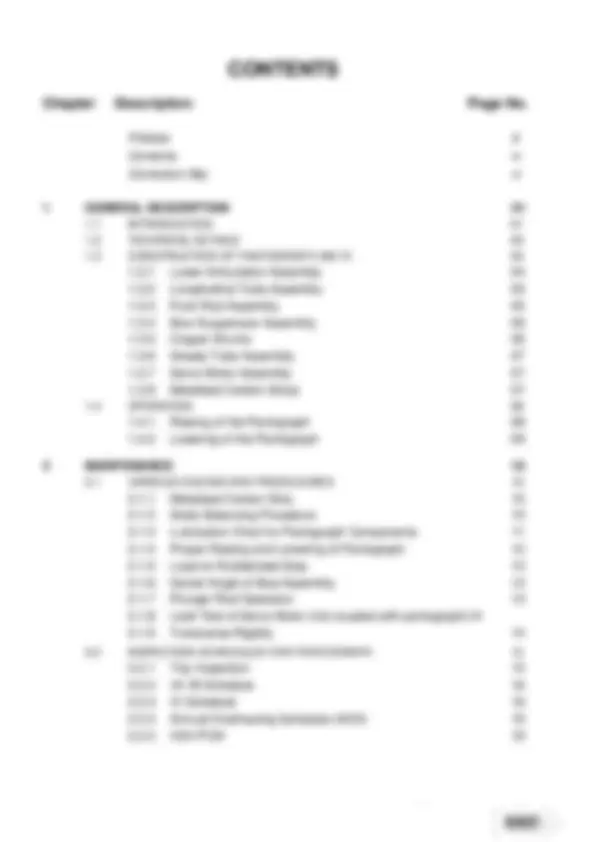
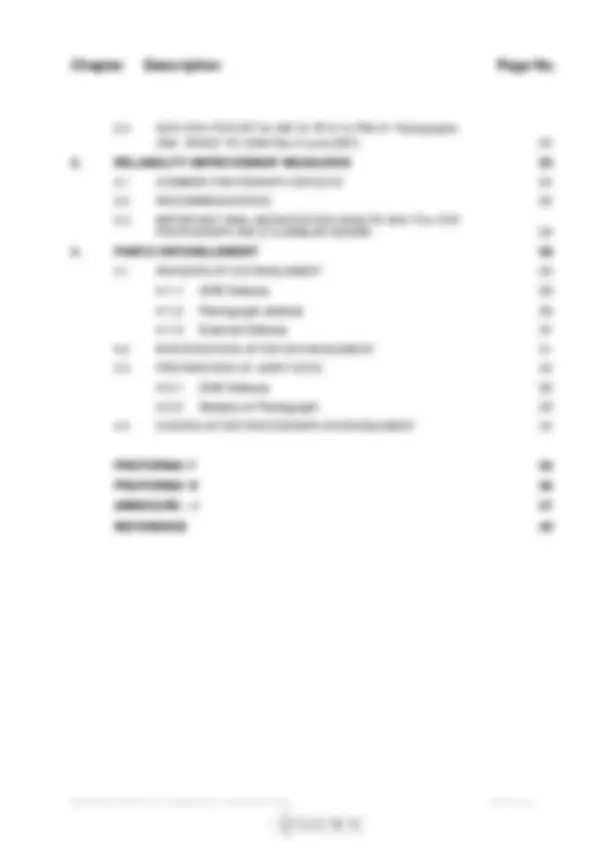
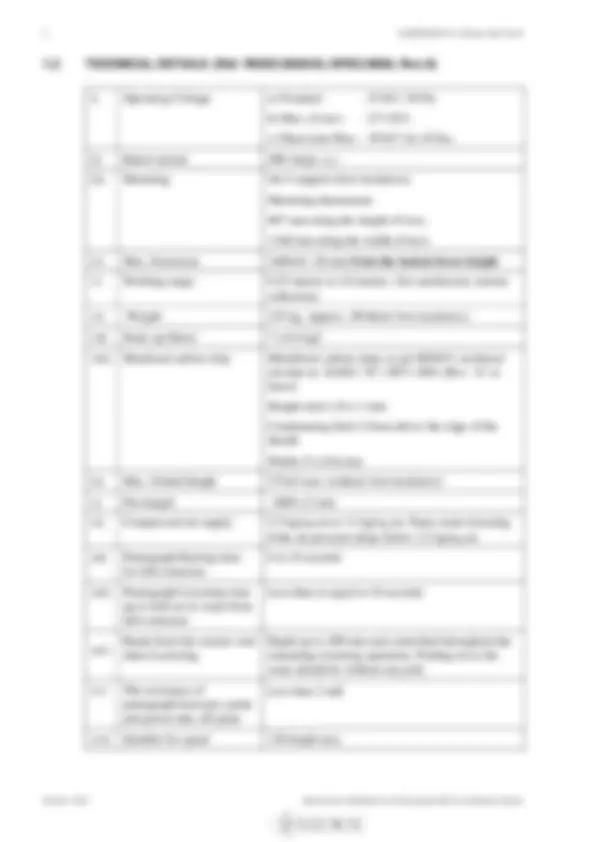
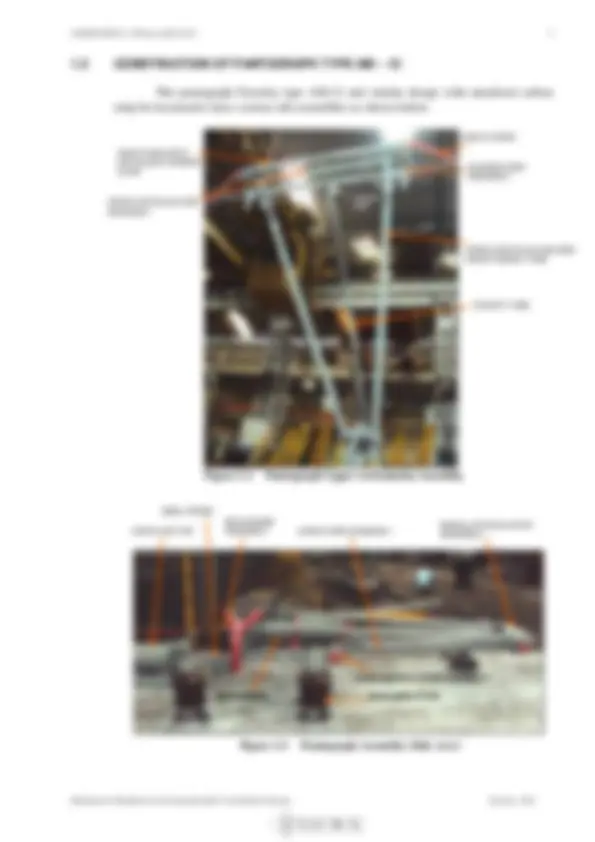
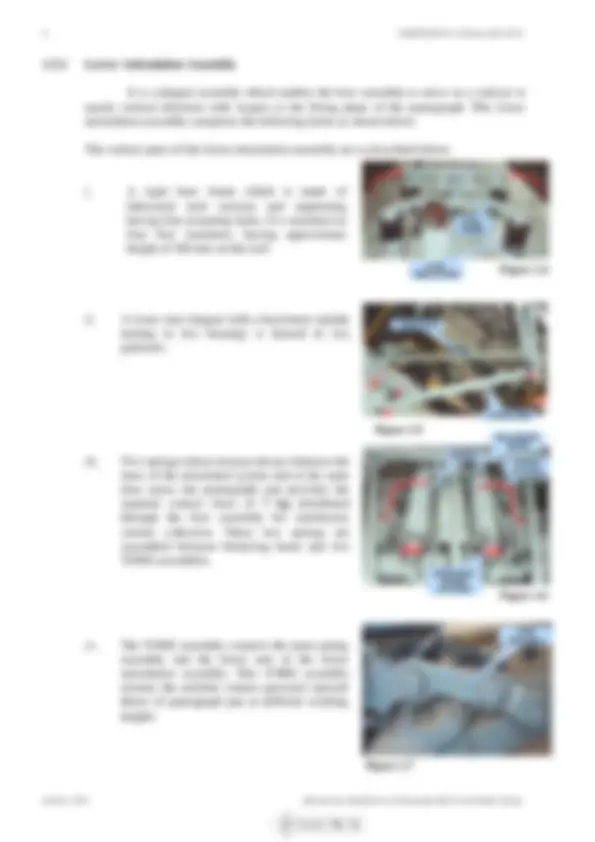
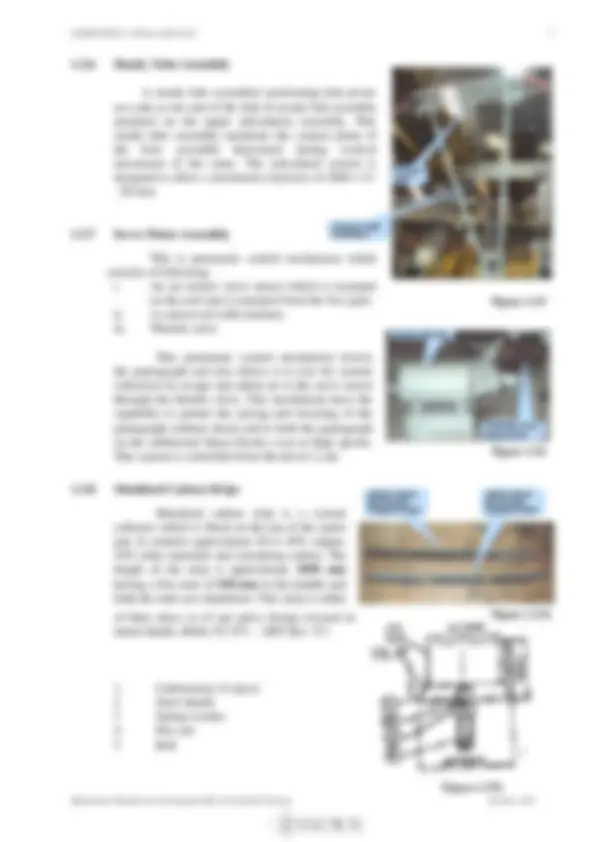
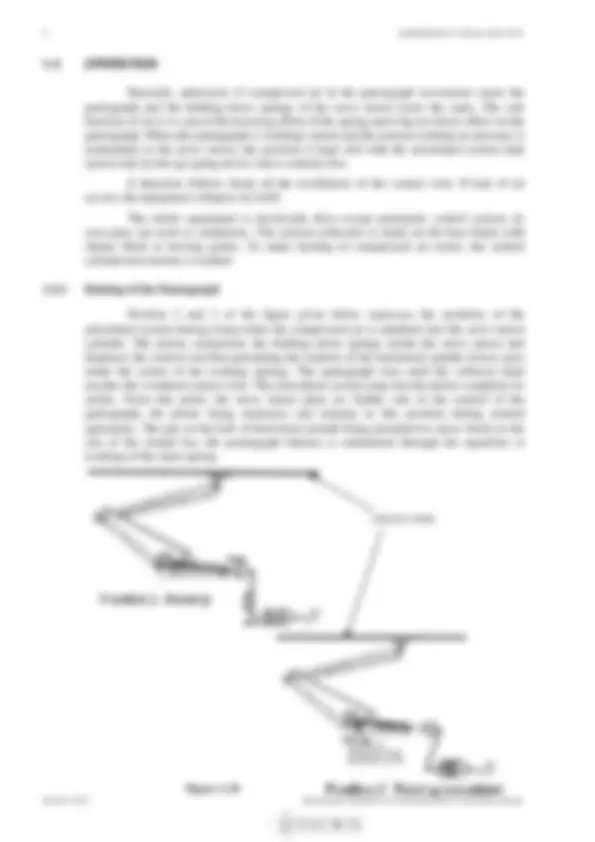
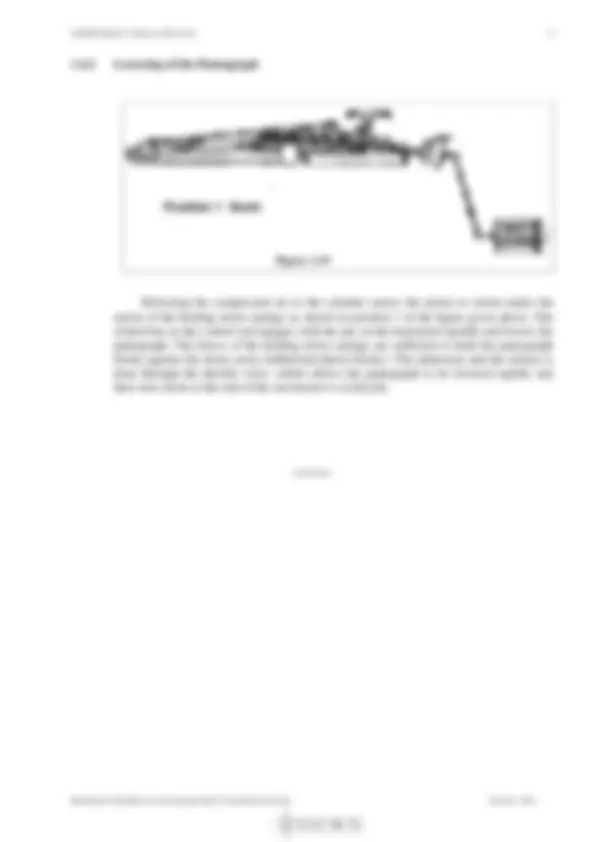
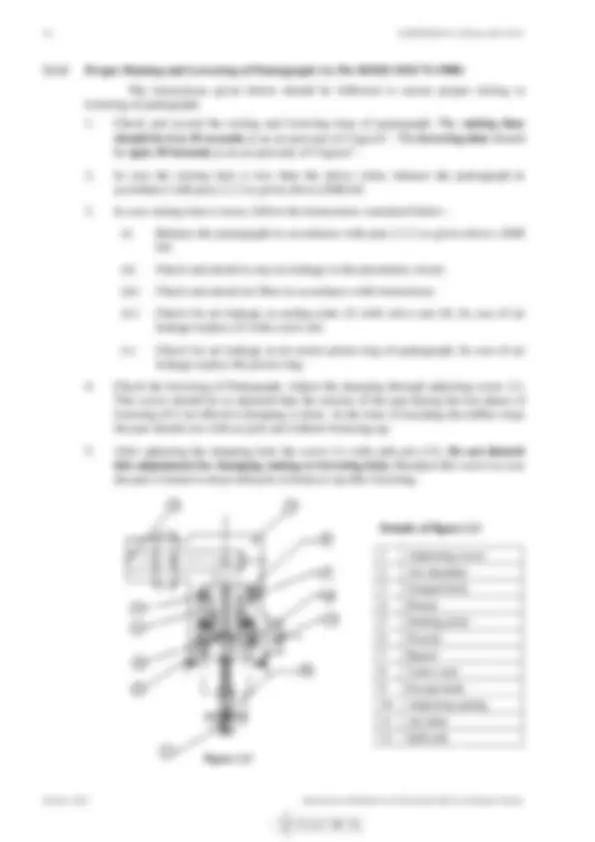

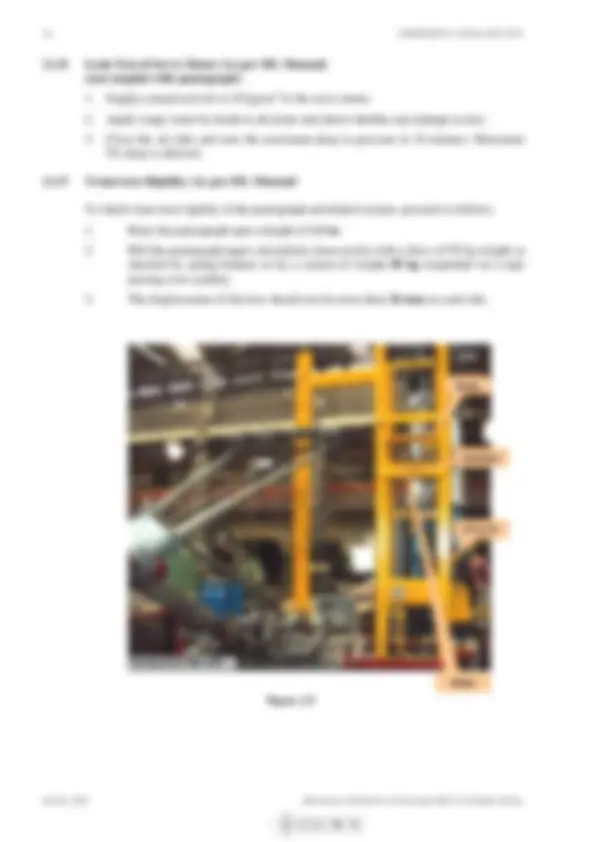
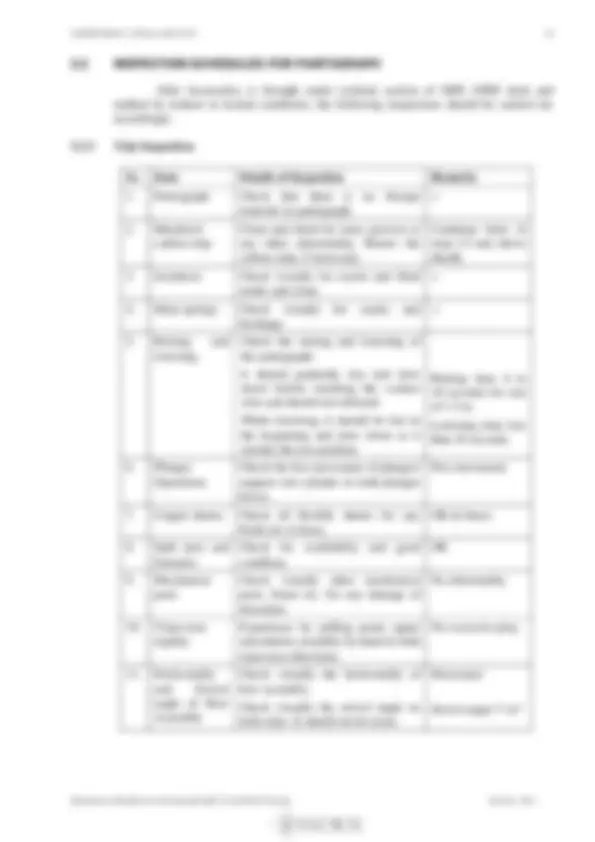
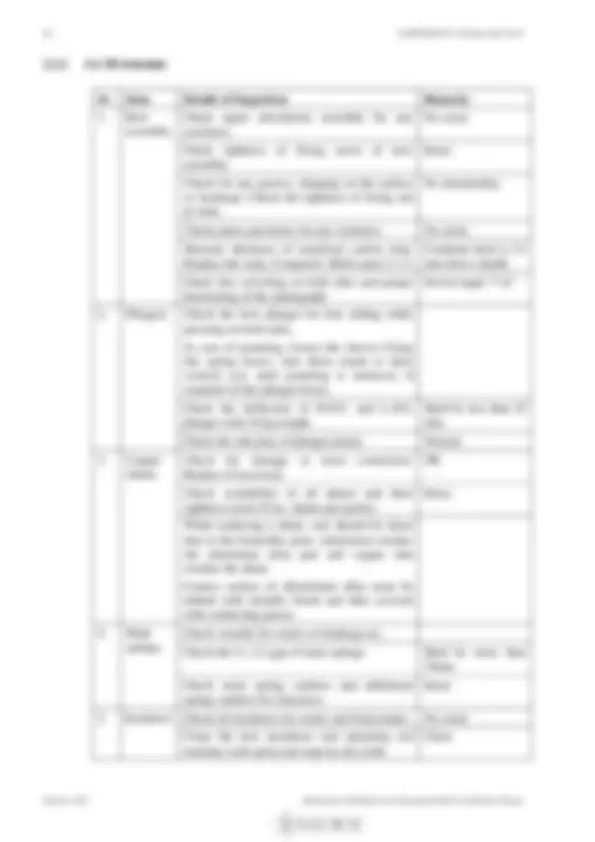
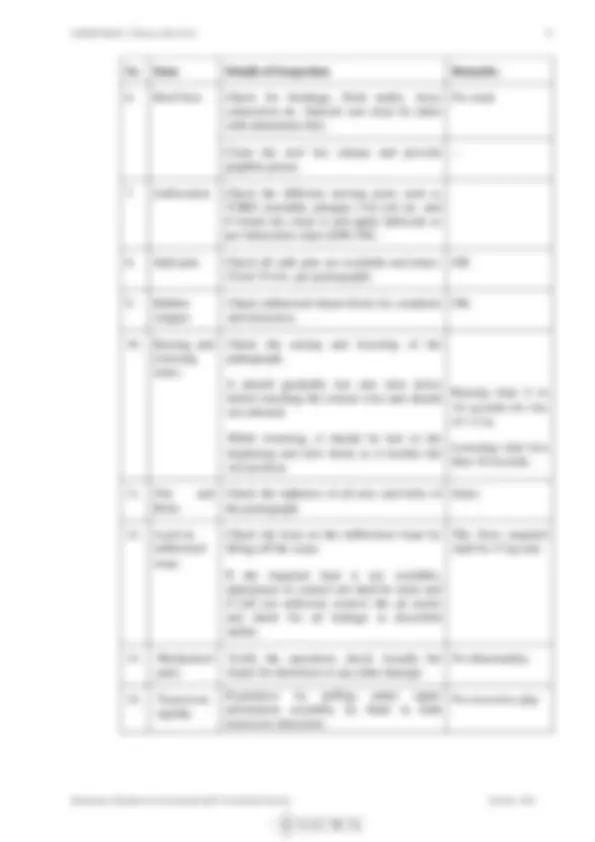
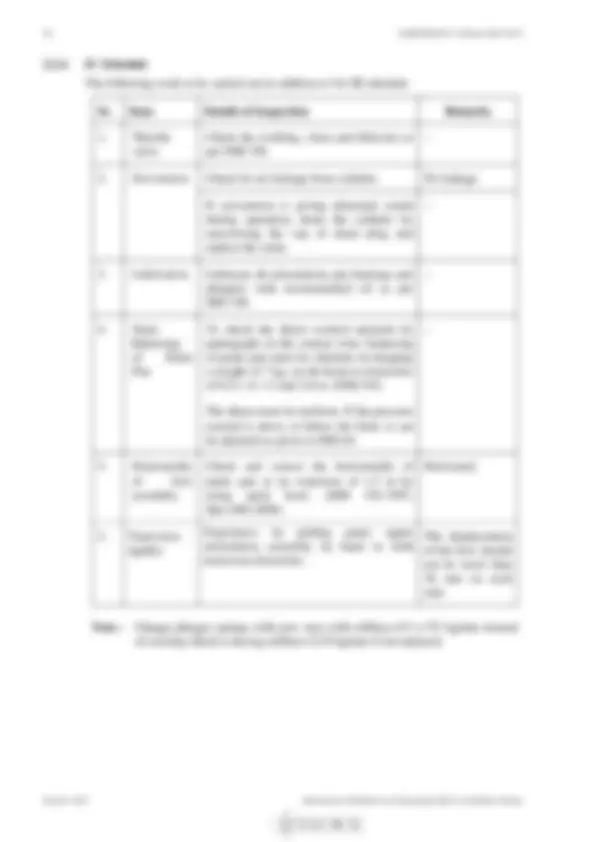
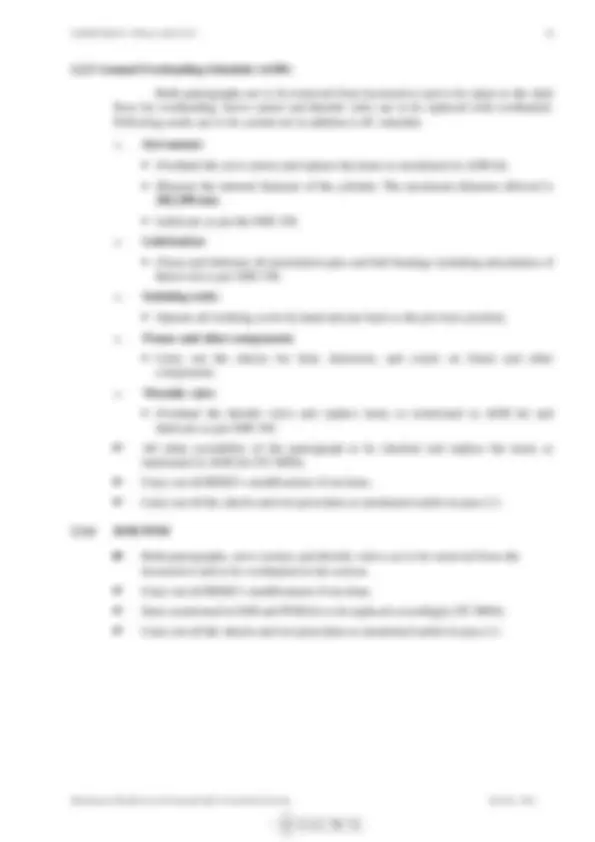
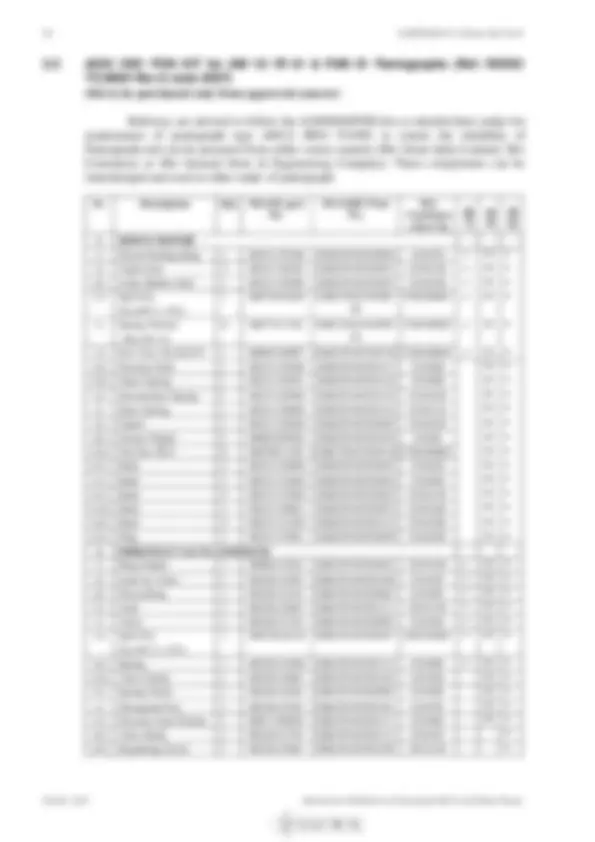
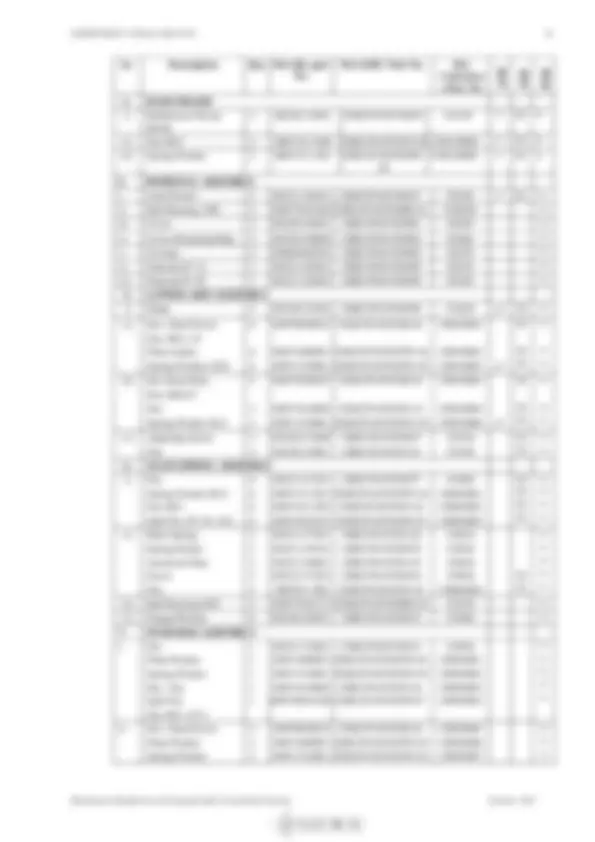
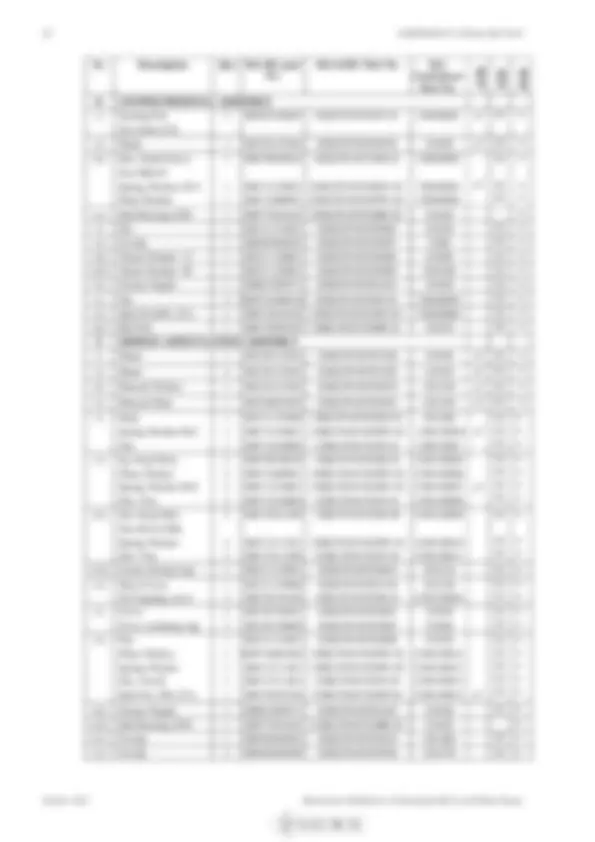
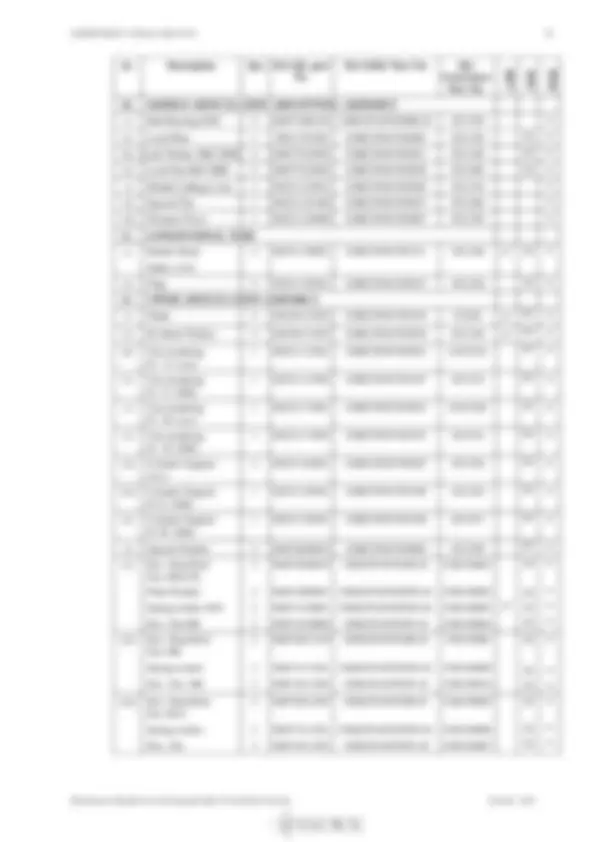
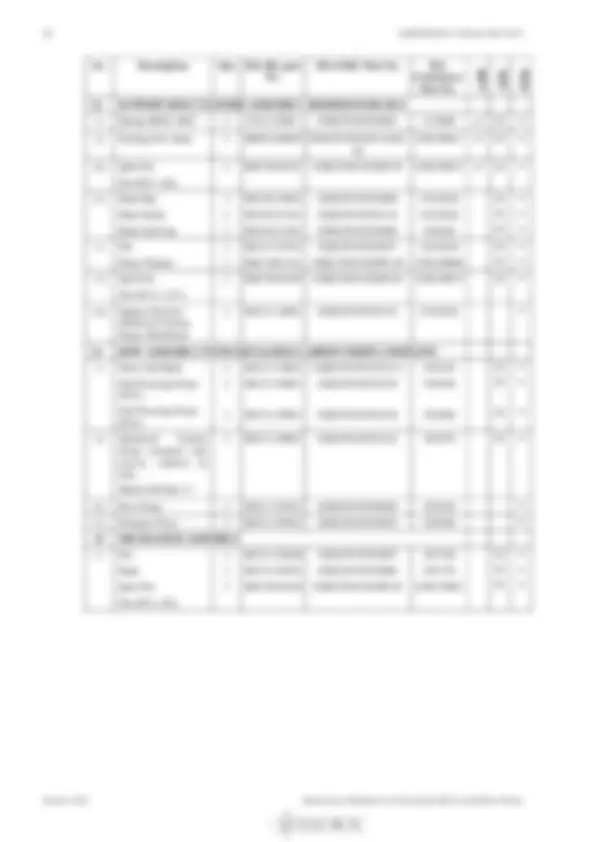
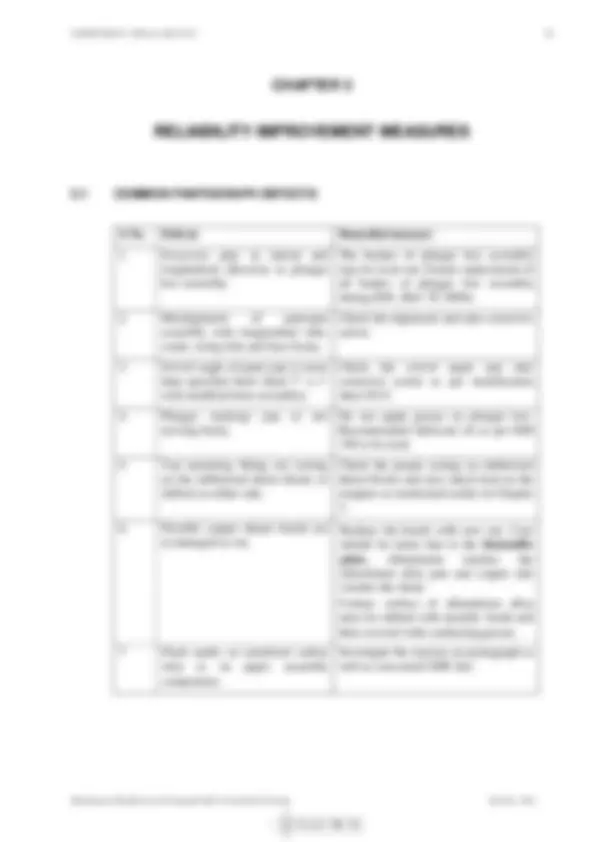
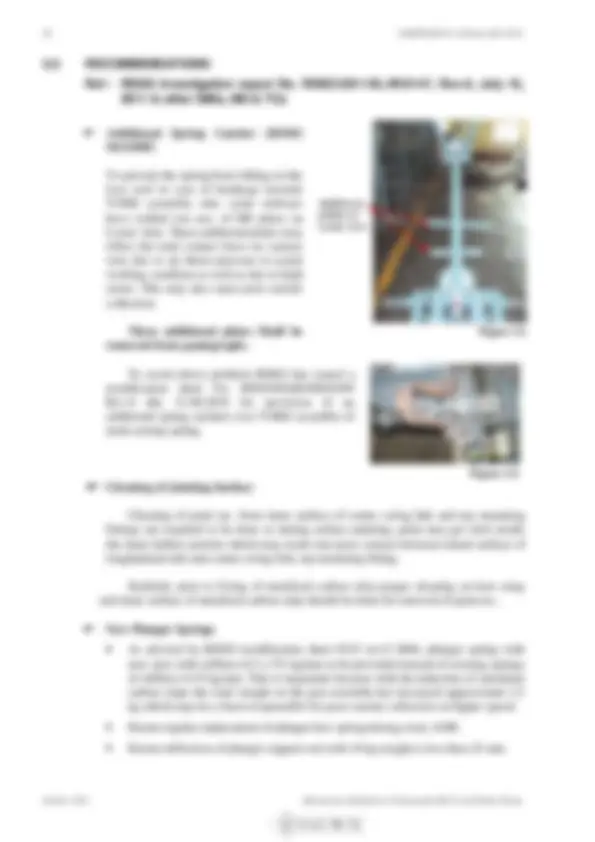
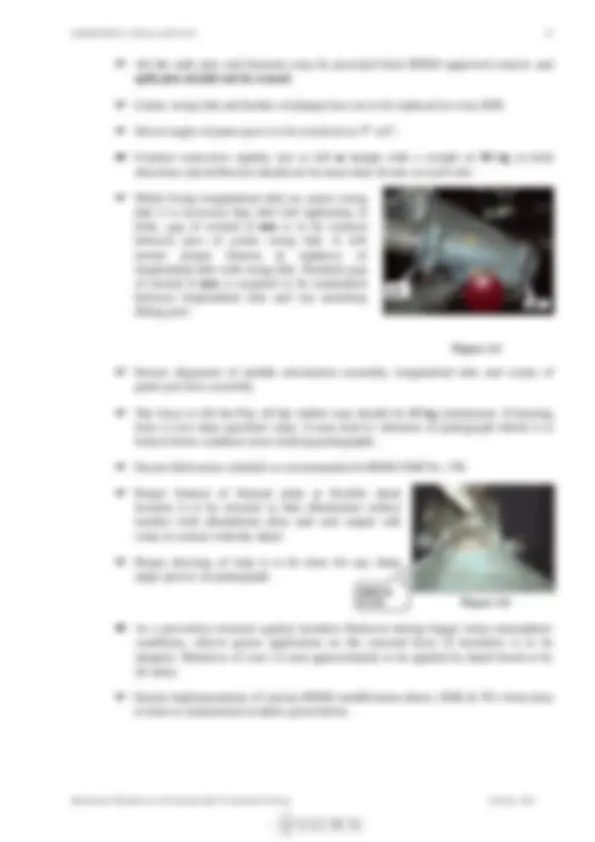
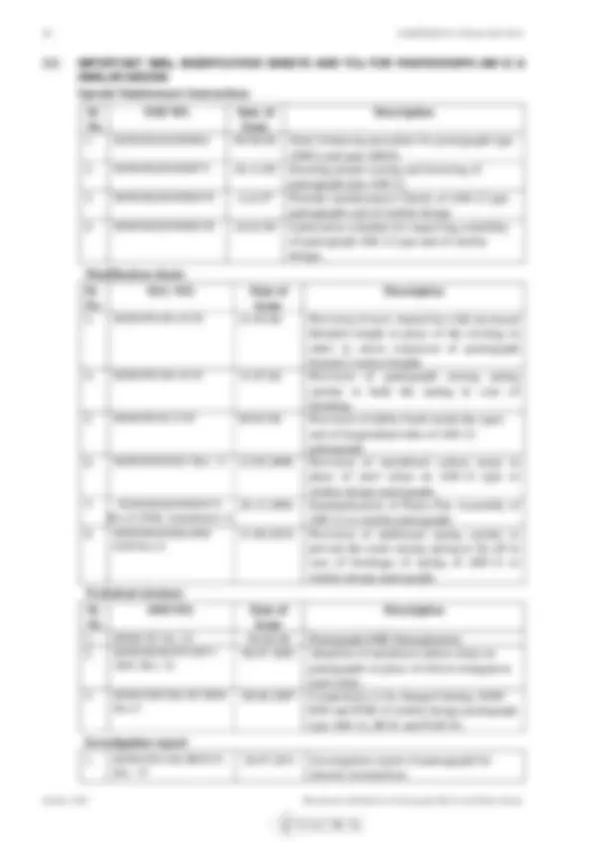
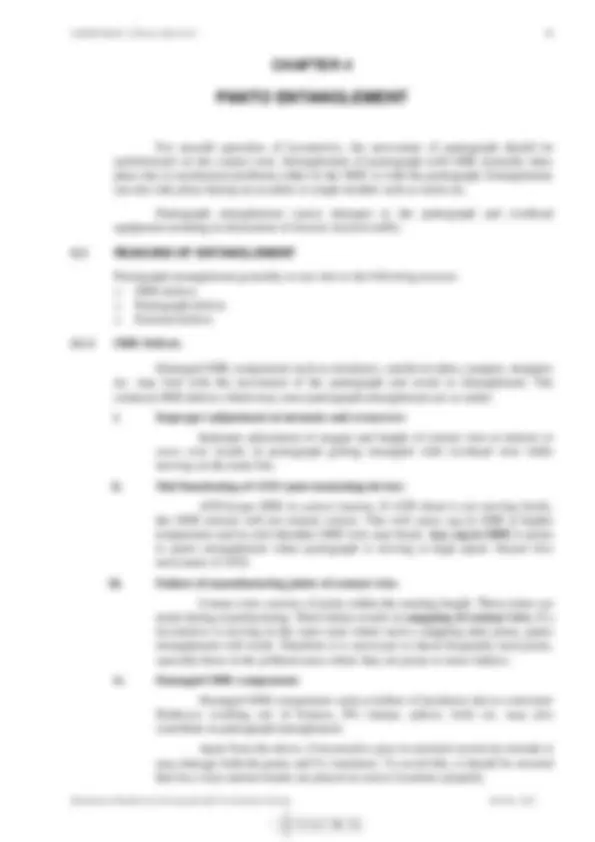
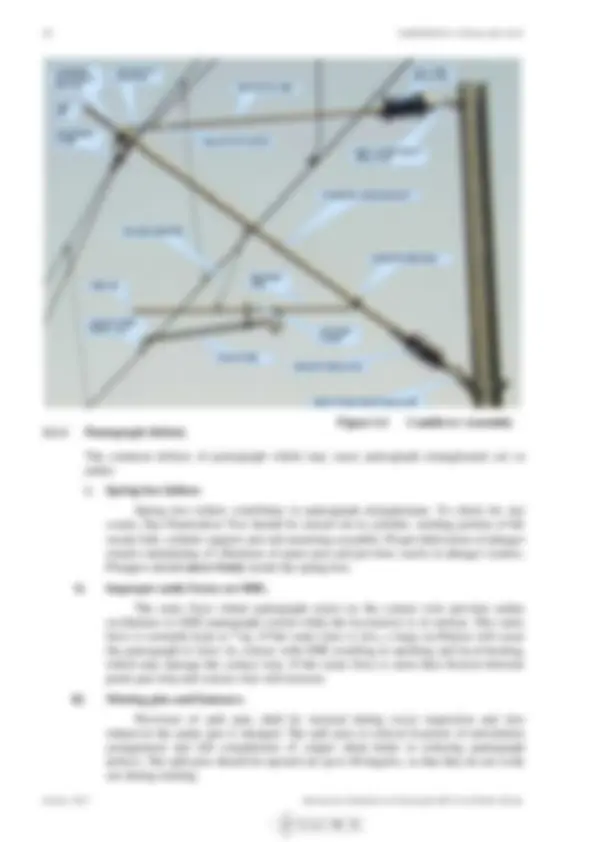
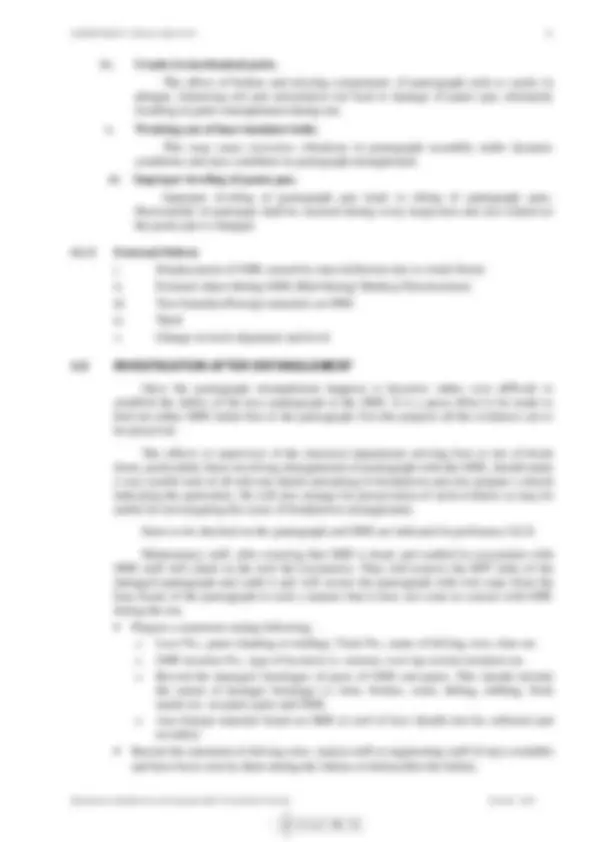
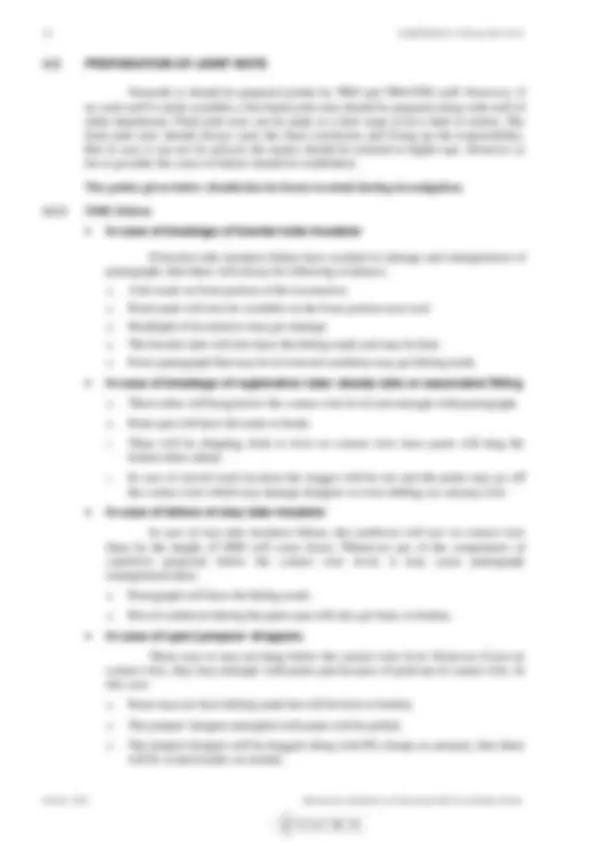
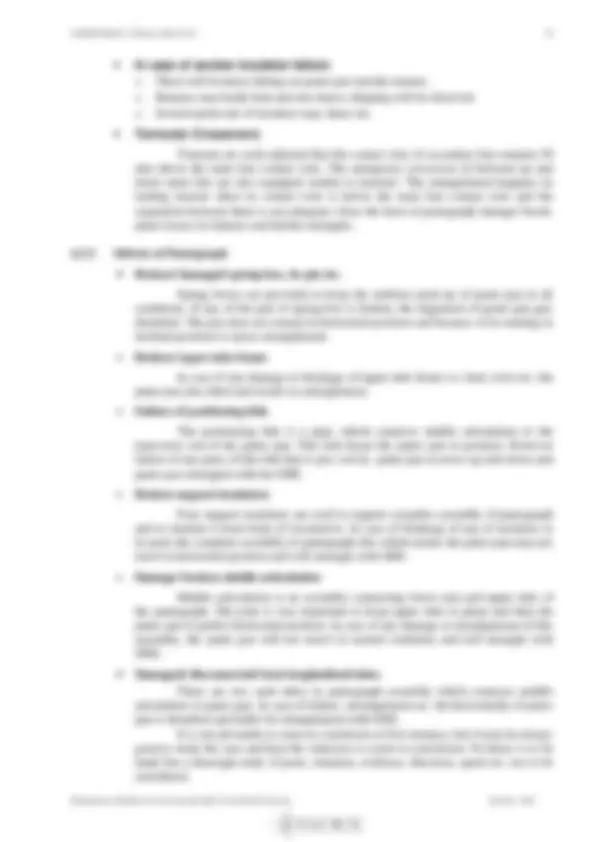
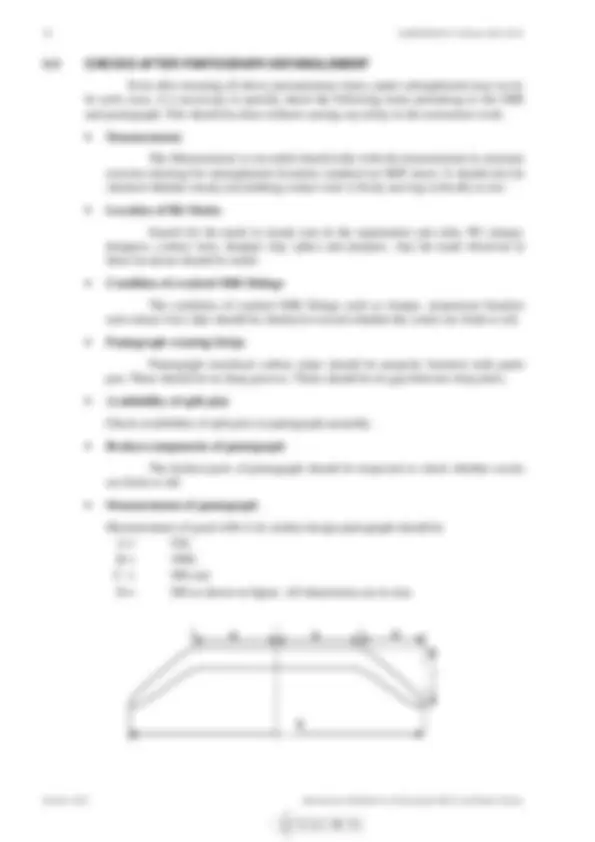
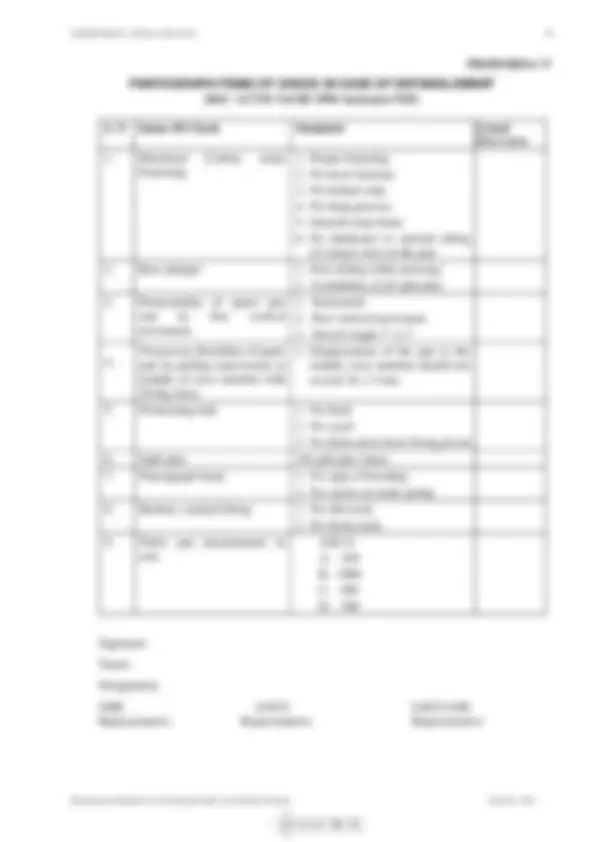
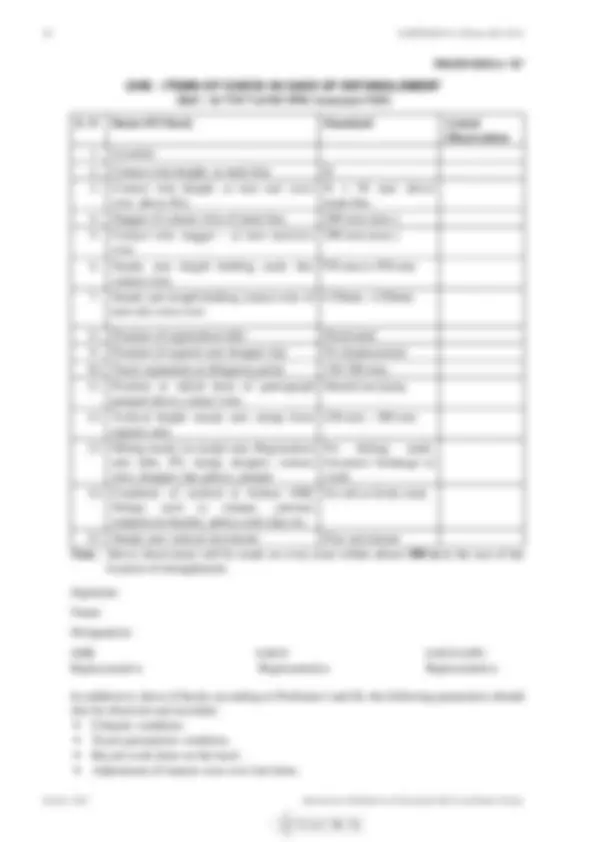
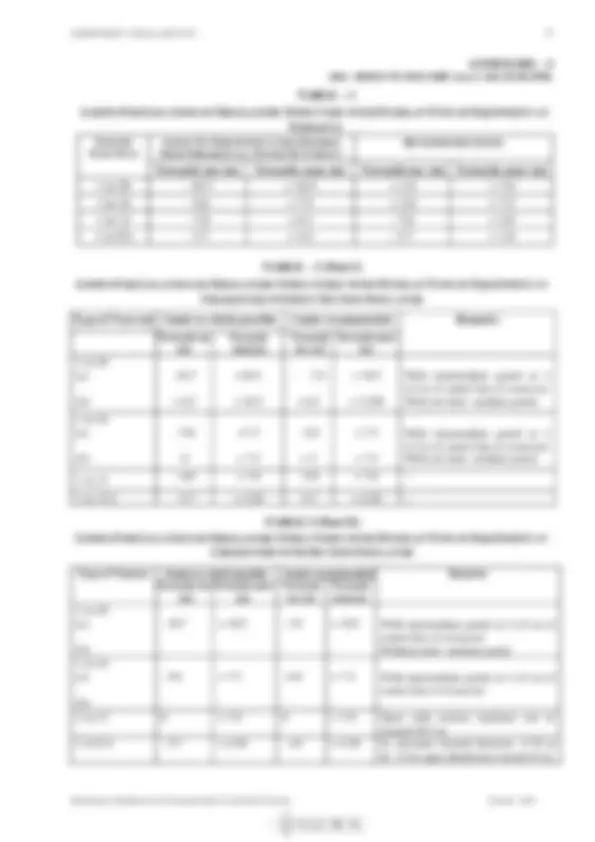
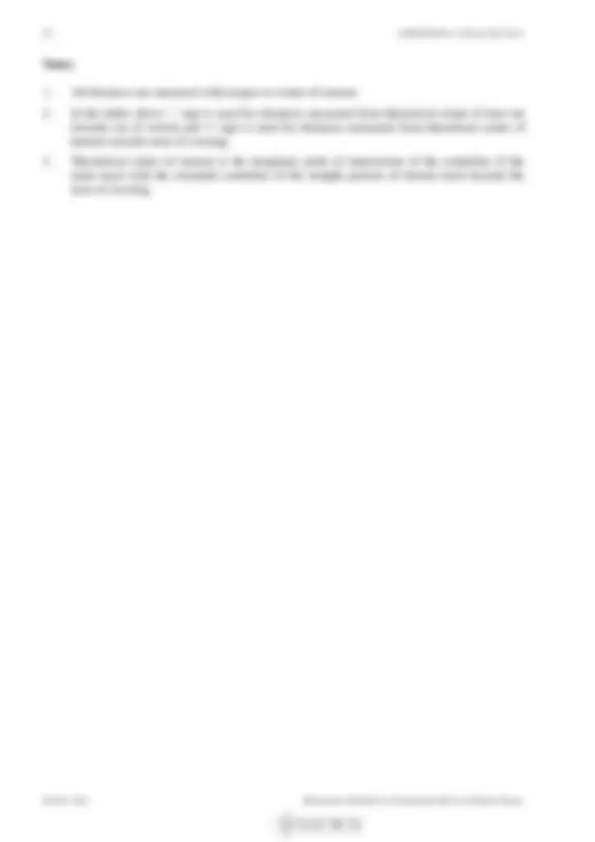
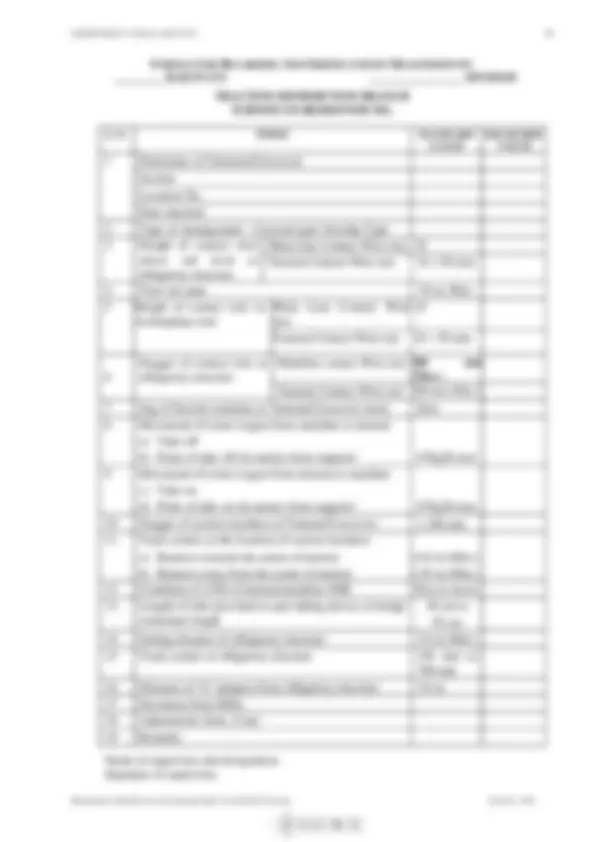
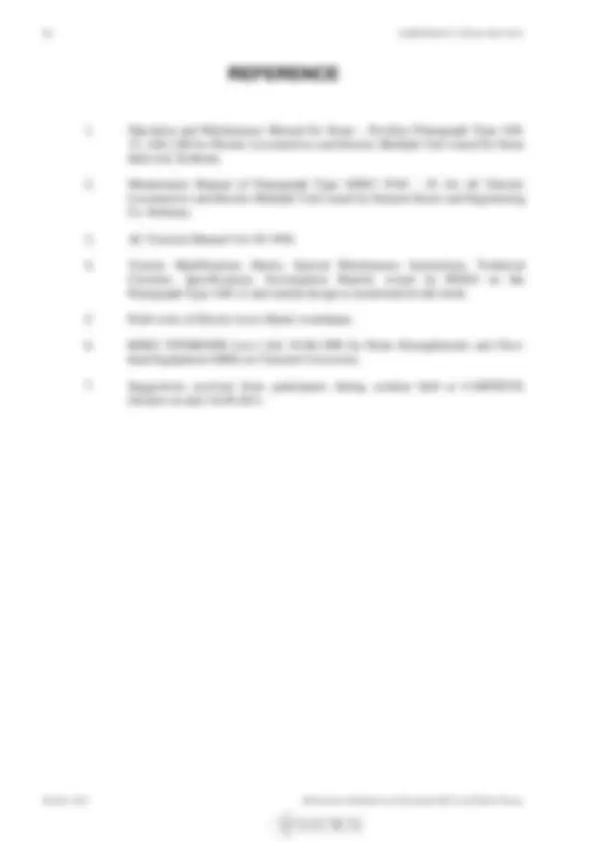
Study with the several resources on Docsity
Earn points by helping other students or get them with a premium plan
Prepare for your exams
Study with the several resources on Docsity
Earn points to download
Earn points by helping other students or get them with a premium plan
Community
Ask the community for help and clear up your study doubts
Discover the best universities in your country according to Docsity users
Free resources
Download our free guides on studying techniques, anxiety management strategies, and thesis advice from Docsity tutors
Maintenance handbook of pantograpgh AM12 & similar design(2).pdf
Typology: Thesis
1 / 46
This page cannot be seen from the preview
Don't miss anything!
On special offer
Maintenance Handbook on Pantograph AM-12 and Similar Design October, 2011
CAMTECH/ E/11-12/Panto AM-12/1. October, 2011
dsoy dk;Zky;hu mi;ksx gsrqdsoy dk;Zky;hu mi;ksx gsrq^ dsoy dk;Zky;hu mi;ksx gsrqdsoy dk;Zky;hu mi;ksx gsrq (For Official Use Only)
October, 2011 Maintenance Handbook on Pantograph AM-12 and Similar Design
CONTENTS
Preface iii Contents iv
Maintenance Handbook on Pantograph AM-12 and Similar Design October, 2011
GENERAL DESCRIPTION
In electric locomotives, pantograph acts as mobile current carrying equipment which is mounted on the roof. It collects power from the overhead equipment under both static and dynamic conditions and transfers it to locomotive.
On electric locomotives WAM-4, WCAM-1/AC, WCAM-2/AC, WCAM-3/AC, WAG-5, WAG-7, WAG-9 Faiveley type AM-12 (make of M/s Stone India Ltd.) and similar design pantographs (IR 01 of M/s Contransys & PAN 01 of M/s General stores and engineering) are being used. The whole assembly of pantograph is mounted on the four foot insulators on locomotive roof. It is operated for its raising/ lowering positions with compressed air through servomotor.
Pantograph is an essential fitting of electric locomotives. There are two pantographs mounted on the roof of an electric locomotive. At a time one pantograph is raised and connects the locomotive with the OHE contact wire. Normally the pantograph rear to cab used for driving is raised i.e. rear to the direction of movement of the locomotive (if rear is defective or damaged, front can be used to work).
The design of pantograph and its electromechanical interaction with OHE contact wire is very significant. To improve the reliability of the pantograph, life of the OHE contact wire and to reduce the cases of panto entanglements with OHE, RDSO has carried out continuous study and issued various modification sheets, special maintenance instructions and technical circulars etc. time to time, some of them are as under : i. RDSO Modification Sheet no. 0265, Rev. 1 dtd. May, 2000 & Technical Circular no. 071 dtd. July 2001 for adoption of metalised carbon strips. ii. RDSO Modification Sheet no. 0333, dtd. Dec., 2004 for Standardisation of Panto Pan assembly of AM 12 or similar design. iii. RDSO Technical Circular no. 0094 dtd. June 2007 for Components to be changed during AOH/ IOH and POH. iv. RDSO Investigation report No. 0147 Rev.0 dtd. July 2011 for Pantograph for Electric Locomotives.
Figure 1.1 Pantograph Assembly Type AM-
October, 2011 Maintenance Handbook on Pantograph AM-12 and Similar Design
1.2 TECHNICAL DETAILS (Ref: RDSO/2008/EL/SPEC/0066, Rev.0)
i) Operating Voltage a) Nominal - 25 KV, 50 Hz. b) Max. (Cont.) - 27.5 KV. c) Short time Max. - 30 KV for 10 Sec. ii) Rated current 400 Amps. a.c. iii) Mounting On 4 support (foot insulators) Mounting dimensions 807 mm along the length of loco, 1160 mm along the width of loco. iv) Max. Extension 2460+0 /-20 mm from the locked down height v) Working range 0.25 meters to 2.0 meters. (for satisfactory current collection) vi) Weight 235 kg. Approx. (Without foot insulators) vii) Static up-thrust 7 ± 0.4 kgf. viii) Metalised carbon strip Metallised carbon strips as per RDSO’s technical circular no. ELRS / TC / 0071-2001 (Rev. ‘0’ or latest) Height (new) 24 ± 1 mm Condemning limit 3.5mm above the edge of the sheath Width 33 ± 0.6 mm ix) Max. Folded height 275±5 mm. (without foot insulators) x) Pan length 1800 ± 5 mm xi) Compressed air supply 5.5 kg/sq.cm to 11 kg/sq.cm. Panto starts lowering if the air pressure drops below 3.5 kg/sq.cm xii) Pantograph Raising time for full extension
6 to 10 seconds
xiii) Pantograph Lowering time up to fold on its stops from full extension
Less than or equal to 10 seconds
xiv)
Break from the contact wire when Lowering
Rapid up to 200 mm and controlled throughout the remaining lowering operation. Folding on to the stops should be without any jerk. xv) The resistance of pantograph between carrier and power take off point
Less than 2 mΩ
xvi) Suitable for speed 120 kmph max.
October, 2011 Maintenance Handbook on Pantograph AM-12 and Similar Design
1.3.1 Lower Articulation Assembly
It is a hinged assembly which enables the bow assembly to move in a vertical or nearly vertical direction with respect to the fixing plane of the pantograph. This lower articulation assembly comprises the following items as shown below.
The various parts of this lower articulation assembly are as described below:
i. A rigid base frame which is made of fabricated steel sections and supporting having four mounting holes. It is mounted on four foot insulators, having approximate height of 360 mm on the roof.
ii. A lower arm integral with a horizontal spindle turning in two bearings is housed in two pedestals.
iii. Two springs whose tension always balances the mass of the articulated system and at the same time raises the pantograph and provides the required contact force of 7 kg distributed through the bow assembly for satisfactory current collection. These two springs are assembled between balancing beam and two YOKE assemblies.
iv. The YOKE assembly connects the main spring assembly and the lower arm of the lower articulation assembly. This YOKE assembly ensures the uniform contact pressure/ upward thrust of pantograph pan at different working heights.
BASE FRAME
BASE INSULATORS
LOWER ARM
PUSH ROD
SPRING
BALANCING BEAM
ADDITIONAL SPRING CATCHER
YOKE ASSEMBLY
SPRING CATCHER
Figure 1.
Figure 1.
Figure 1.
Figure 1.
Maintenance Handbook on Pantograph AM-12 and Similar Design October, 2011
v. The centre plate assembly helps to balance the pantograph through the main spring assembly with YOKE assembly.
vi. Two rubberized thrust blocks have been provided on the base frame for resting the upper articulation assembly.
vii. A centre pedestal assembly is fixed to the base frame and holds the balancing beam and push rod/ thrust rod assembly.
1.3.2 Longitudinal Tube Assembly
The longitudinal tube assembly consists of two tubes having one end jointed to the extremity of the lower arm assembly through centre swing link of the middle articulation assembly and across braced their upper ends are fixed to the top mounting fitting assembly of upper articulation assembly.
1.3.3 Push Rod Assembly
Push rod/ thrust rod assembly is pivoted at a fixed point on the centre pedestal assembly on one end and at its opposite end on the centre swing link of the middle articulation assembly. This rod ensures the positioning of the longitudinal tube assembly as the lower arm rotates.
RUBBERISED THRUST BLOCK
CENTRE PLATE ASSEMBLY
LONGITUDINAL TUBE ASSEMBLY
CENTRE PEDESTAL ASSEMBLY
PUSH ROD ASSEMBLY
Figure 1.
Figure 1.
Figure 1.
Figure 1.
Figure 1.
Maintenance Handbook on Pantograph AM-12 and Similar Design October, 2011
1.3.6 Steady Tube Assembly
A steady tube assembly/ positioning link pivots on a pin at one end of the link of steady link assembly mounted on the upper articulation assembly. This steady tube assembly maintains the contact plane of the bow assembly horizontal during vertical movement of the same. The articulated system is designed to allow a maximum extension of 2460 + 0 /
1.3.7 Servo Motor Assembly
This is pneumatic control mechanism which consists of following: i. An air motor/ servo motor which is mounted on the roof and is insulated from the live parts. ii. A control rod with insulator. iii. Throttle valve
This pneumatic control mechanism lowers the pantograph and also allows it to rise for current collection by escape and admit air to the servo motor through the throttle valve. This mechanism have the capability to permit the raising and lowering of the pantograph without shock and to hold the pantograph on the rubberized thrust blocks even at high speeds. This system is controlled from the driver’s cab.
1.3.8 Metalised Carbon Strips
Metalised carbon strip is a current collector which is fitted on the top of the panto pan. It contains approximate 20 to 30% copper, 10% other materials and remaining carbon. The length of the strip is approximate 1050 mm having a flat zone of 520 mm in the middle and both the ends are chamfered. This strip is either of three piece or of one piece design encased in metal sheath. (Refer TC 071 – 2001 Rev ‘0’)
STEADY LINK
STEADY TUBE ASSEMBLY
SERVO MOTOR
CONTROL ROD INSULATOR
SINGLE PIECE METALISED CARBON STRIP
THREE PIECE METALISED CARBON STRIP
Figure 1.
Figure 1.
Figure 1.17a
Figure 1.17b
October, 2011 Maintenance Handbook on Pantograph AM-12 and Similar Design
Basically, admission of compressed air in the pantograph servomotor raises the pantograph and the holding down springs of the servo motor lower the same. The sole function of air is to cancel the lowering effort of the spring and it has no direct effect on the pantograph. When the pantograph is working/ raised and the normal working air pressure is maintained in the servo motor, the position is kept still with the articulated system kept raised only by the up-spring device and is entirely free. It therefore follows freely all the oscillations of the contact wire. If lack of air occurs, the equipment collapses by itself. The whole equipment is electrically alive except pneumatic control system, its own parts are used as conductors. The current collection is made on the base frame with shunts fitted at moving points. To make feeding of compressed air easier, the control cylinder/servomotor is earthed.
1.4.1 Raising of the Pantograph
Position 2 and 3 of the figure given below expresses the positions of the articulated system during rising when the compressed air is admitted into the servo motor cylinder. The piston compresses the holding down springs inside the servo motor and displaces the control rod thus permitting the rotation of the horizontal spindle (lower arm) under the action of the working springs. The pantograph rises until the collector head reaches the overhead contact wire. The articulated system stops but the piston completes its stroke. From this point, the servo motor plays no further role in the control of the pantograph, the piston being stationary and remains in this position during normal operations. The pin on the fork of horizontal spindle being permitted to move freely in the slot of the slotted bar, the pantograph balance is maintained through the operation or working of the main spring.
Figure 1.
CLEARANCE PERMITTING FREE MOVEMENT OF PIN (^) AIR INLET
AIR INLET
CONTACT WIRE
October, 2011 Maintenance Handbook on Pantograph AM-12 and Similar Design
MAINTENANCE
2.1.1 Metalised Carbon Strip (As per TC 071 Rev.’0’-2001, & MS/0265 Rev.1/2000)
Fill up the gaps between ends of carbon strips and end wearing strip, with suitable sealing material (M-seal etc.), in case of three piece design, fill the gaps between the carbon strips with suitable adhesive to avoid corrosion of the metal sheath and ingress of water between carbon and sheath. Check the smoothness of the current collector surface and swiveling angle. It should be 7° ± 1° on both sides. Measure the thickness of carbon strip above sheath. The condemning limit is 3.5 mm above the edge of the sheath. However, in schedule inspection, if the height of the carbon above the sheath is found in between 3.7 to 4.4 mm the strip may be allowed for another 10,000 km run before replacement. If carbon strip is required to be replaced, fix it on the panto pan with a torque value of 2.5 kg-m.
2.1.2 Static Balancing Procedure (As Per RDSO SMI 64-1980)
Carry out static balancing of pantograph according to the following sequence of operations to obtain correct force at various heights: i. Place a weight of 7 kg. for AM-12 and similar design pantograph on the pantopan. ii. Feed the pantograph with air at pressure 5 kg/cm^2.
7 KG WEIGHT
Figure 2.1 Static Balancing Procedure
Figure 2.
Maintenance Handbook on Pantograph AM-12 and Similar Design October, 2011
iii. Loosen lock nuts on the regulating screws C, D, E and F. iv. Screw down all the four regulating screws C.D.E and F. v. Balance the pantograph at a height of 2.0 metres by tensioning the main springs A and B with the help of adjusting nuts G and H. vi. Balance the pantograph at a height of 1.75 meters by using regulating screw F (top screw on left hand side viewing the pantograph from servo motor end). vii. Balance the pantograph at a height of 1.5 metres by using regulating screw D (top screw on right-hand side). viii. Balance the pantograph at a height of 1.0 metres by using regulating screw C (bottom screw on right-hand side). ix. Balance the pantograph at a height of 0.5 metres by using regulating screw E (bottom screw on left-hand side). x. Re-check the balancing of pantograph at heights of 2.0, 1.75, 1.5, 1.0 and 0. meters. xi. Lock regulating screws with the help of Lock nuts after obtaining the balance.
2.1.3 Lubrication Chart for Pantograph Components (As per RDSO/SMI/198-1998)
Ensure proper lubrication of the components of the pantograph as per the details given below. This will help in reducing the cracks/ breakage of moving components & will also minimize the cases of panto OHE entanglement.
SL No.
Parts to be lubricated
Recommended Lubricants
Substitute Lubricant Frequency of lubrication
Alvania- Grease (Shell)
Thuban K(Caltex)
Maintenance Handbook on Pantograph AM-12 and Similar Design October, 2011
2.1.5 Load on Rubberised Stop (As per SIL Manual)
2.1.6 Horizontality & Swivel Angle of Bow Assembly (Ref: RDSO/SMI 192, 1997 & RDSO/MS/0333–2004 Amendment 1 dtd. 21.04.2005)
2.1.7 Plunger Rod Operation (RDSO/MS/0333 Rev.0/ 2004)
The difference of gap ‘X’ available in the plunger rod height before and after installing a 10 kg. weight at each end of bow assembly above the plunger rod cylinder assembly should be less than 25 mm.
This deflection limit is for new plunger springs with stiffness 0.5 ± 5% kg per mm.
Deflection
Figure 2.4 Plunger Rod Operation
October, 2011 Maintenance Handbook on Pantograph AM-12 and Similar Design
2.1.8 Leak Test of Servo Motor (As per SIL Manual) (not coupled with pantograph)
2.1.9 Transverse Rigidity (As per SIL Manual)
To check transverse rigidity of the pantograph articulated system, proceed as follows:
50 Kg Wt.
Pully
Indicator
Slider
Courtesy ELS CNB/ NCR
Figure 2.