
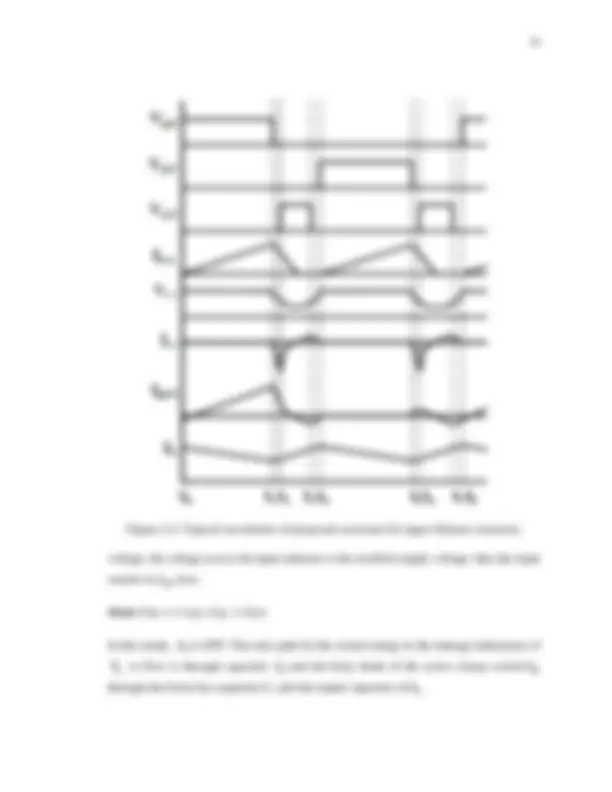
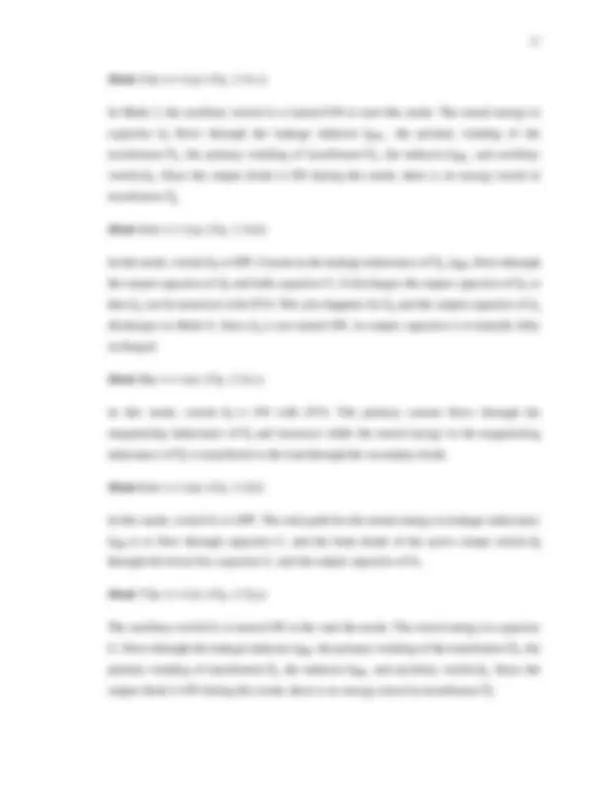
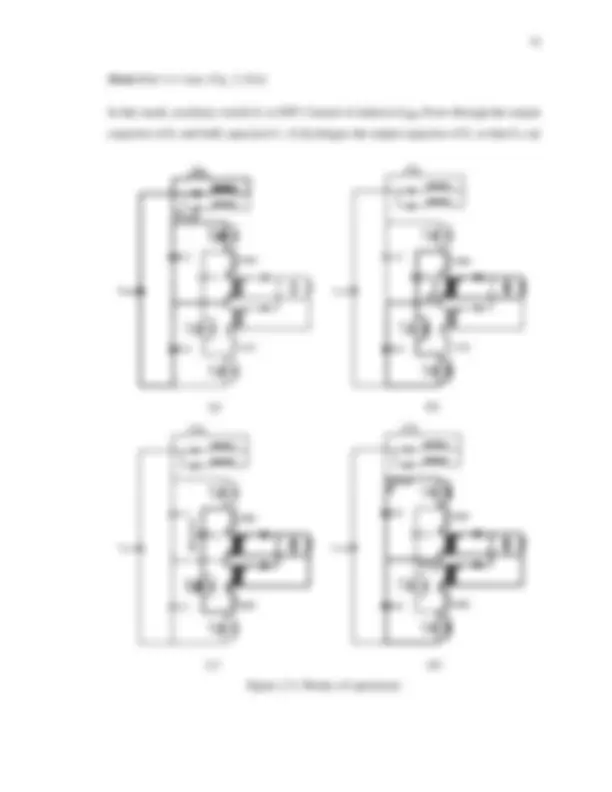
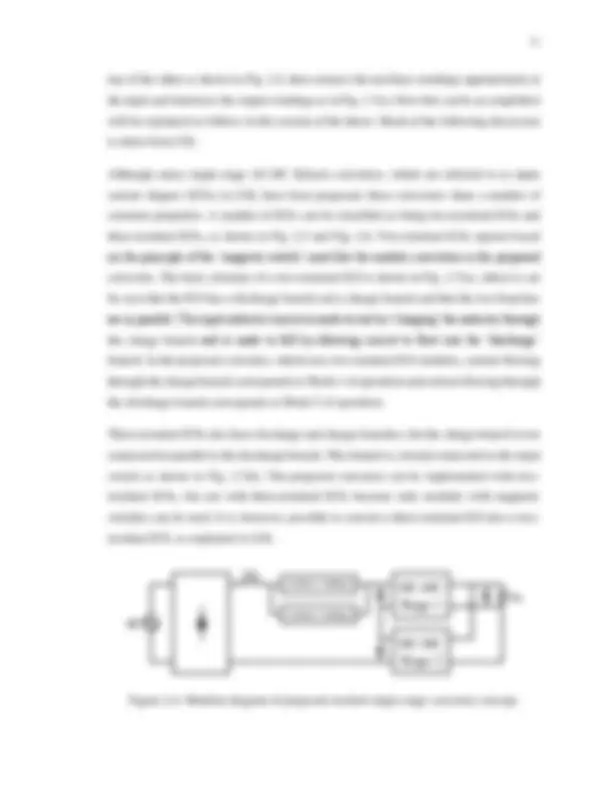
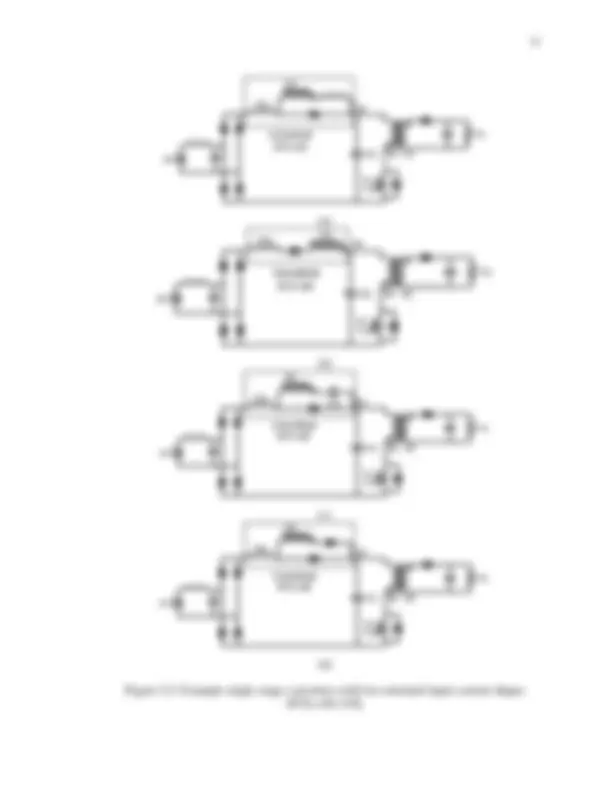
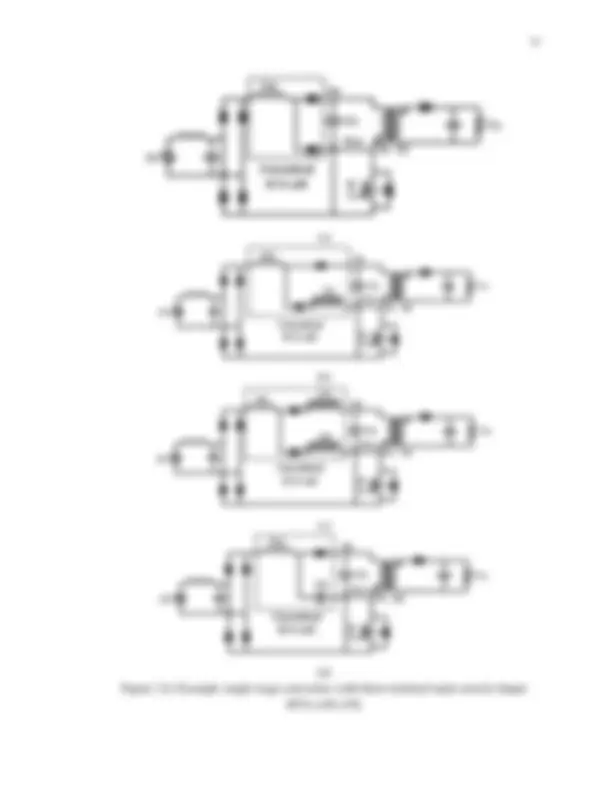
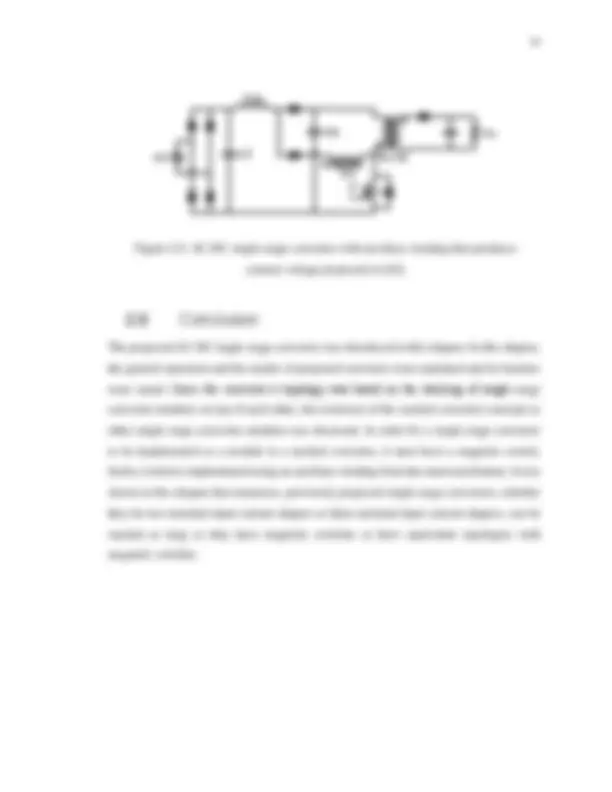
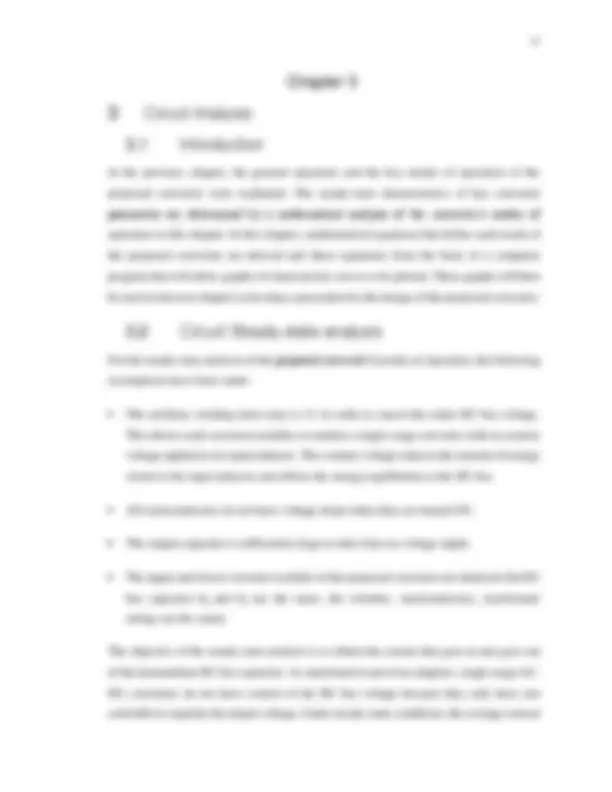
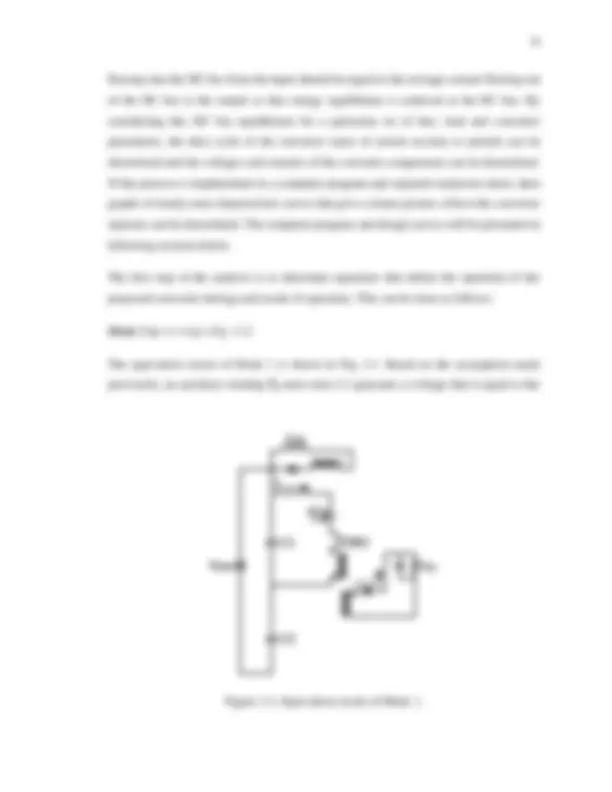
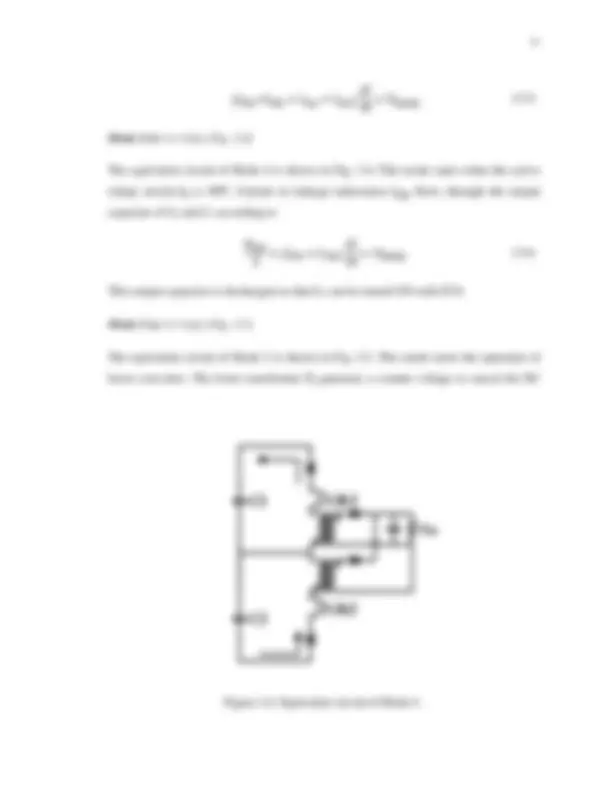
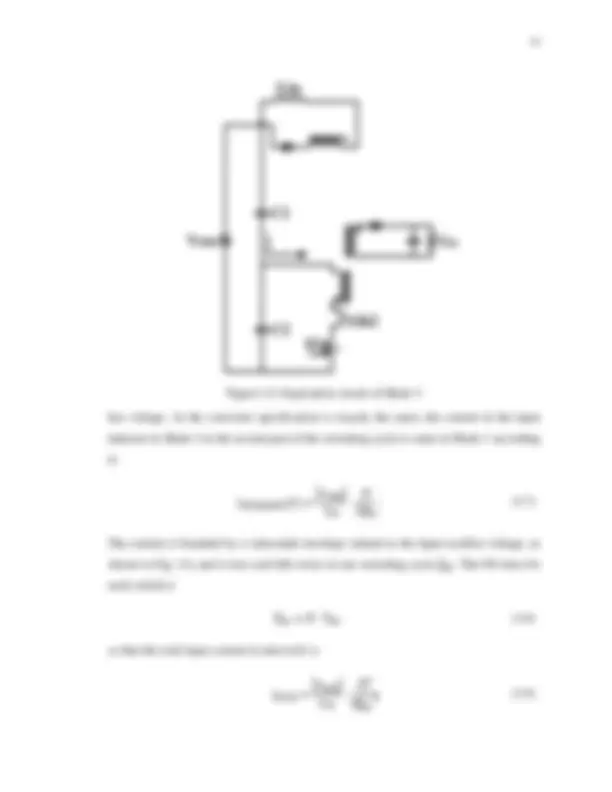
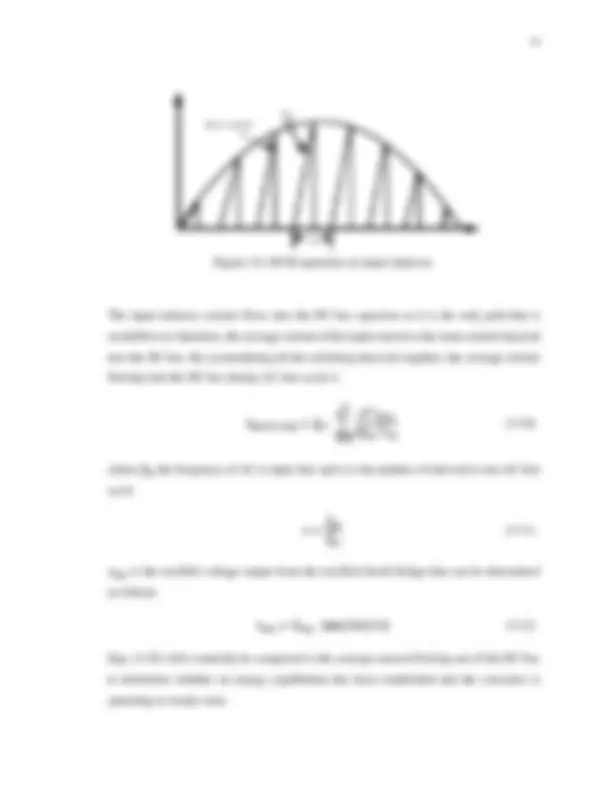
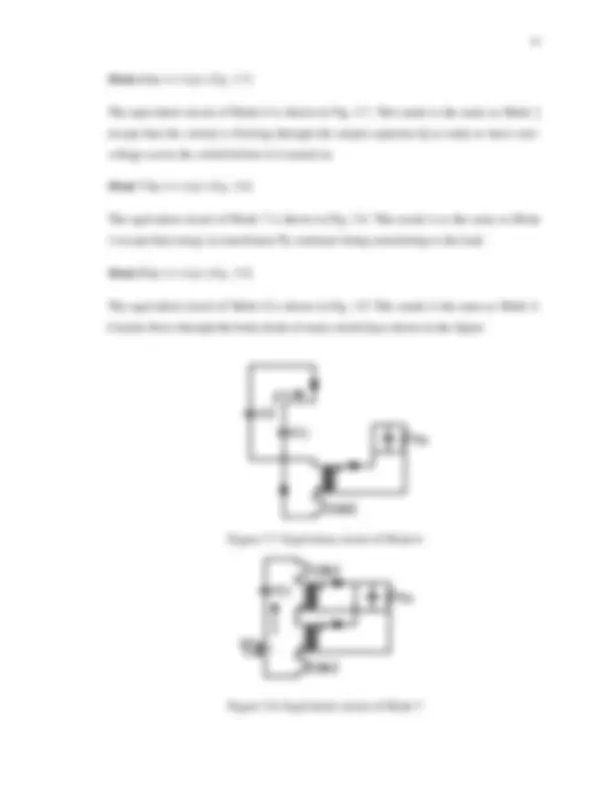
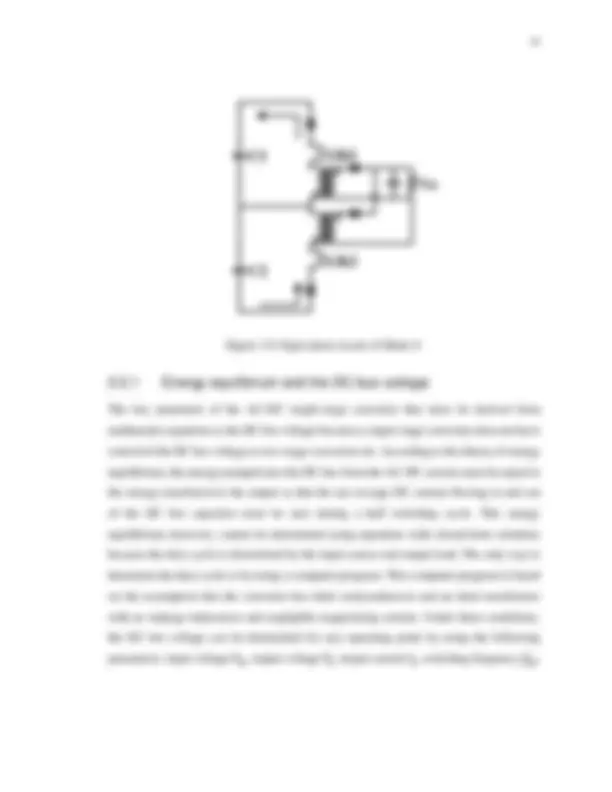
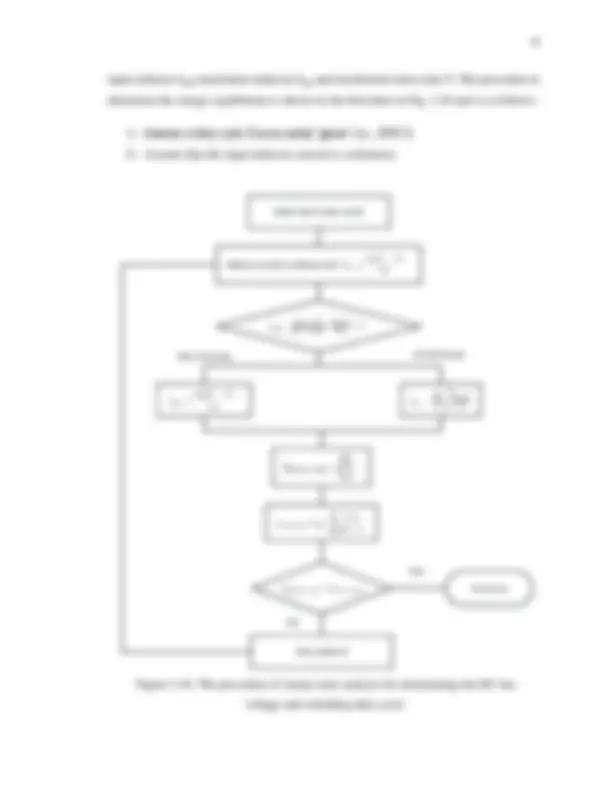
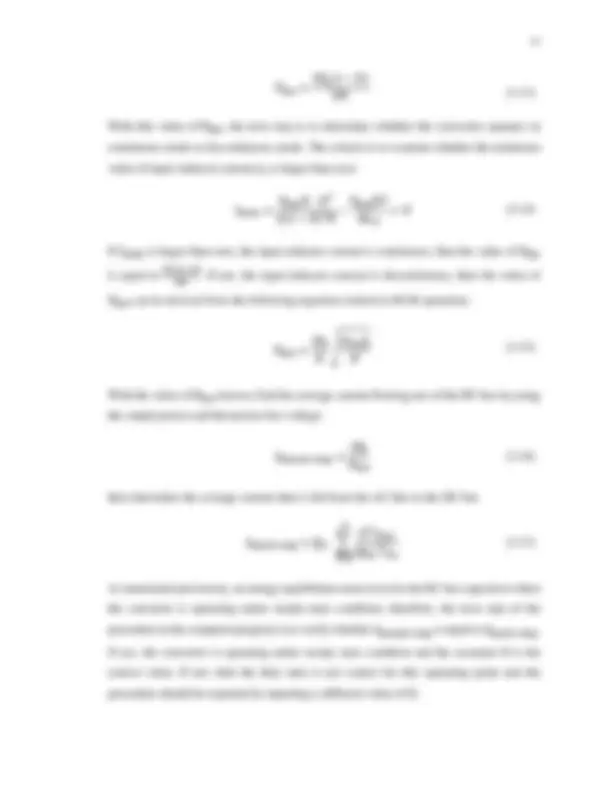
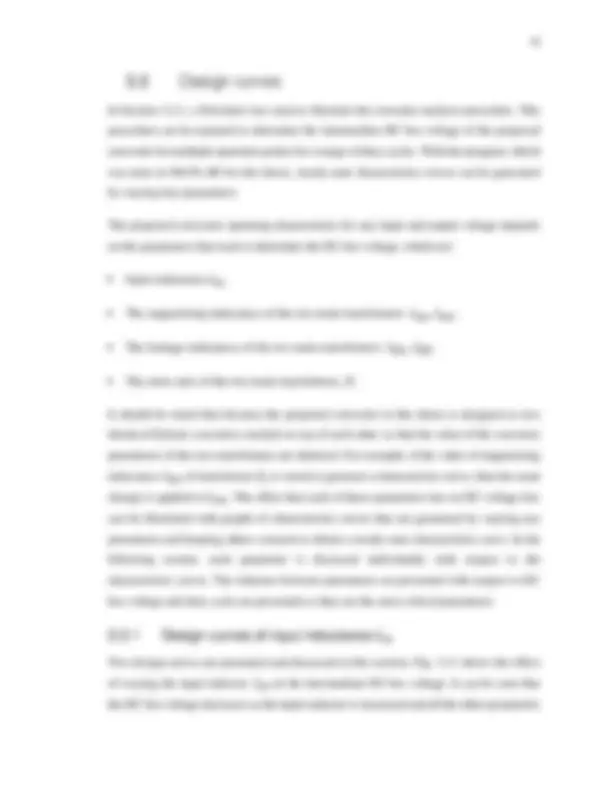
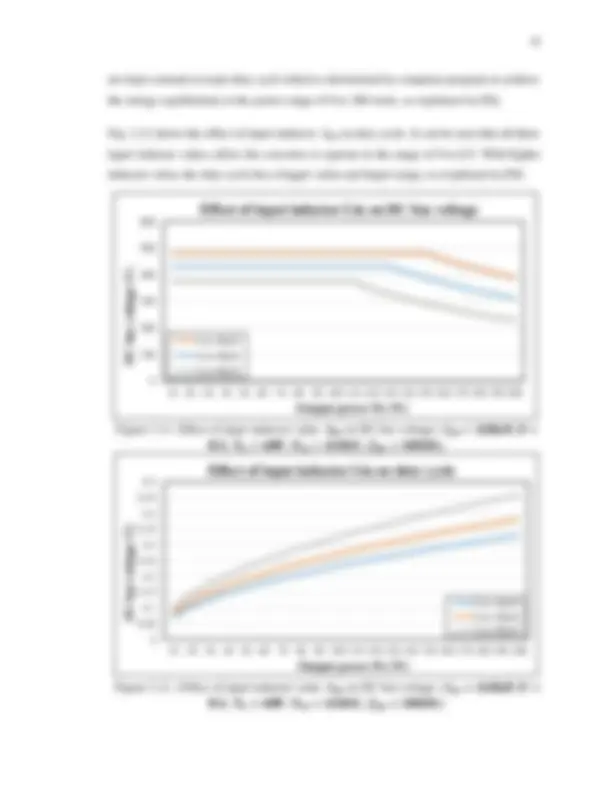
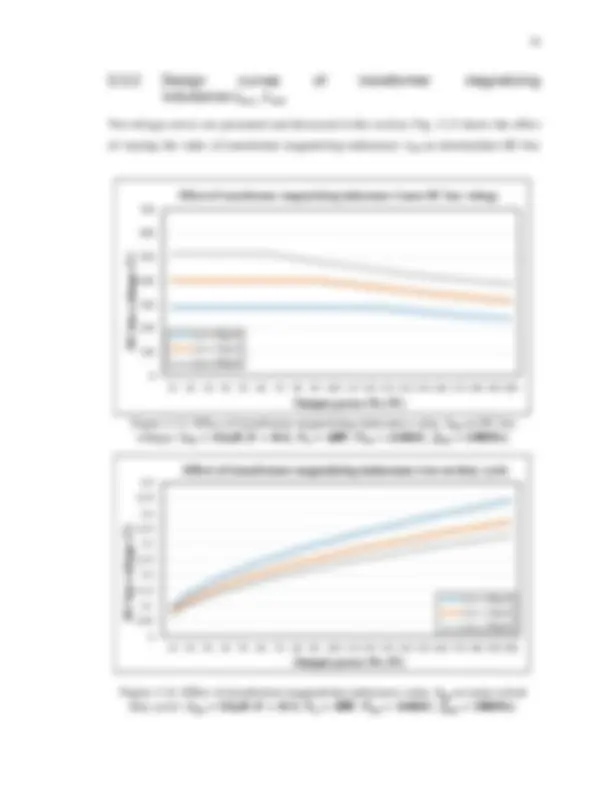
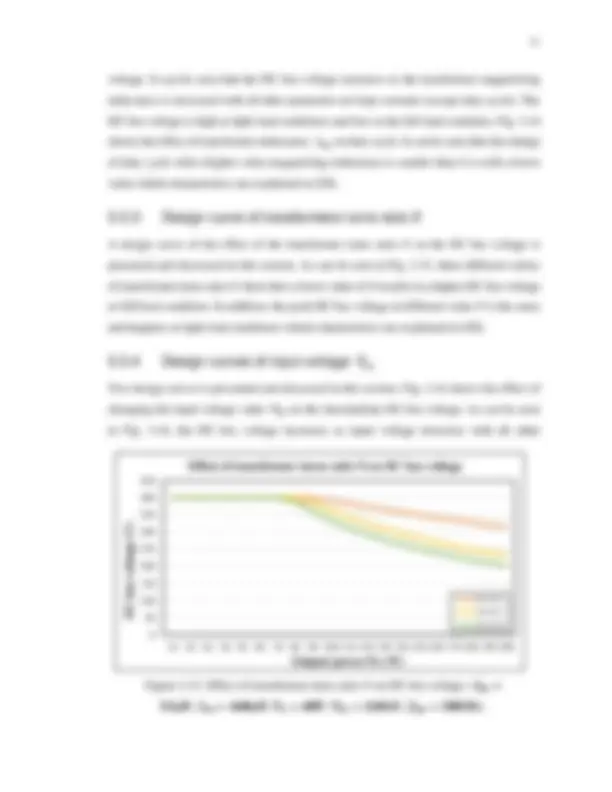
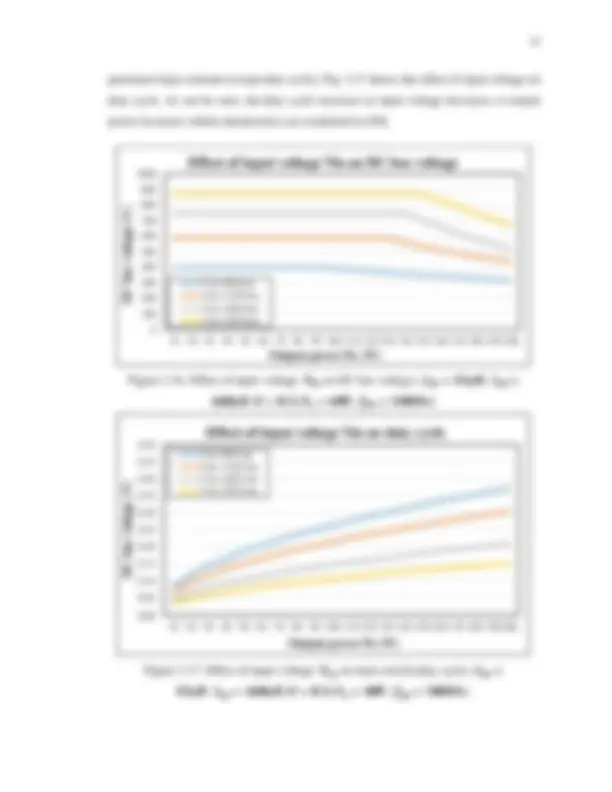
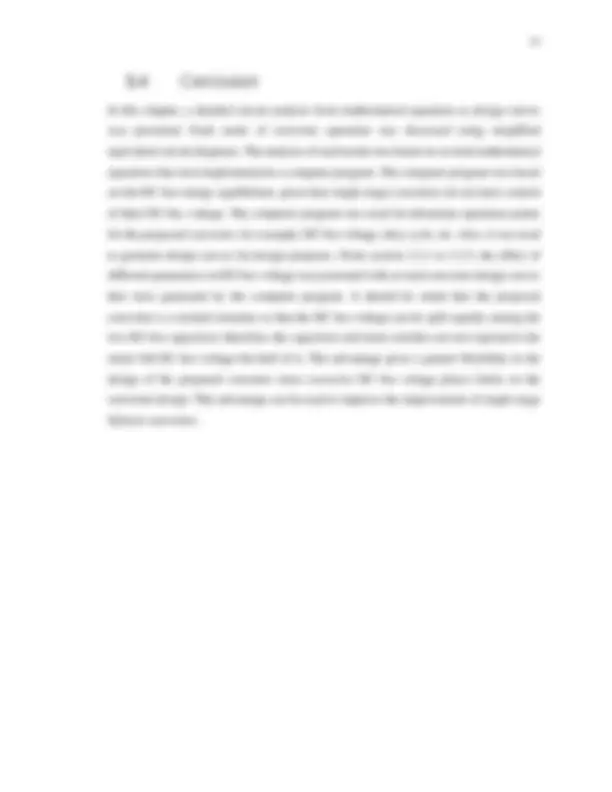
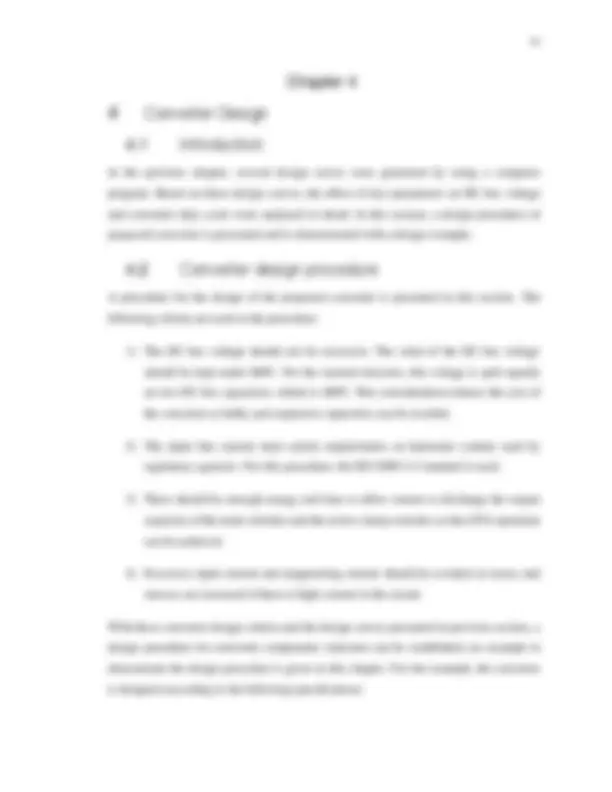
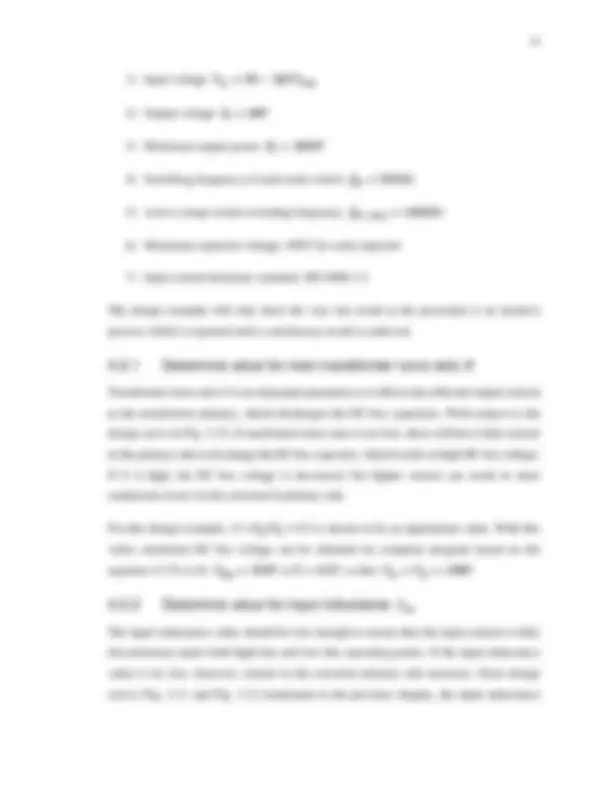
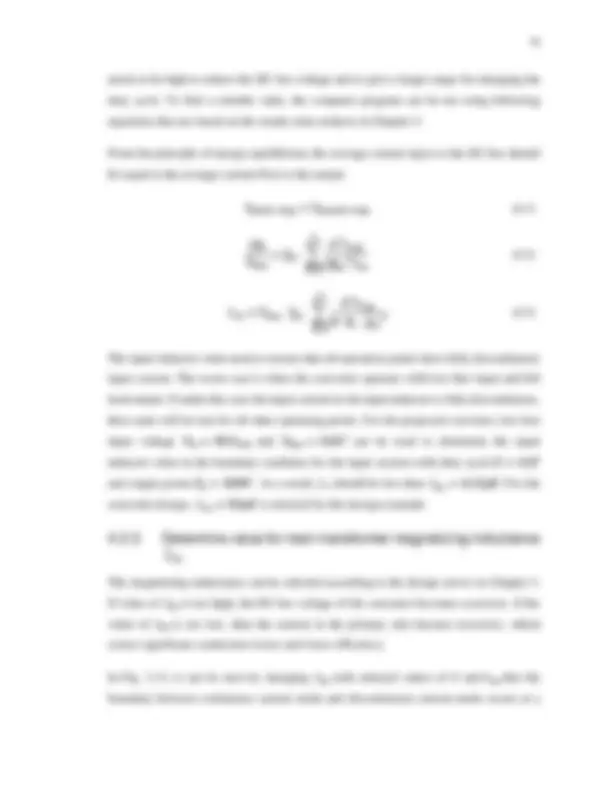
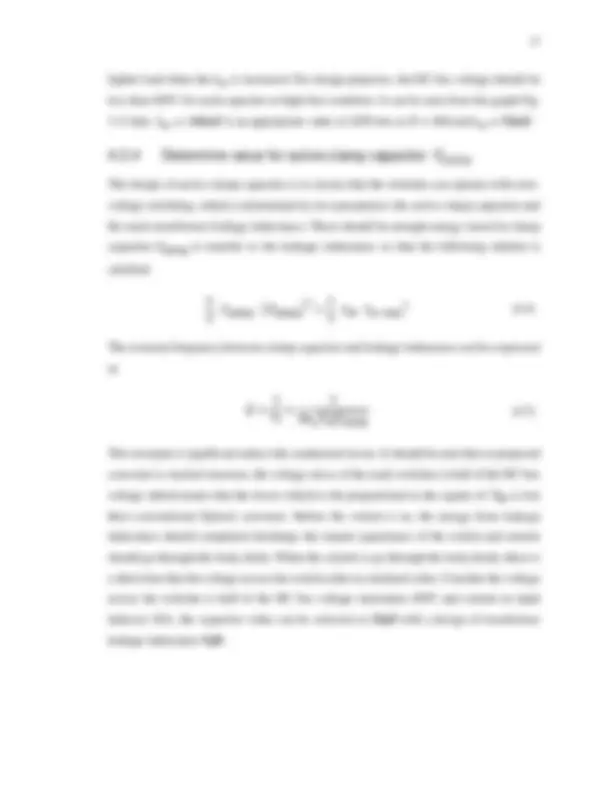
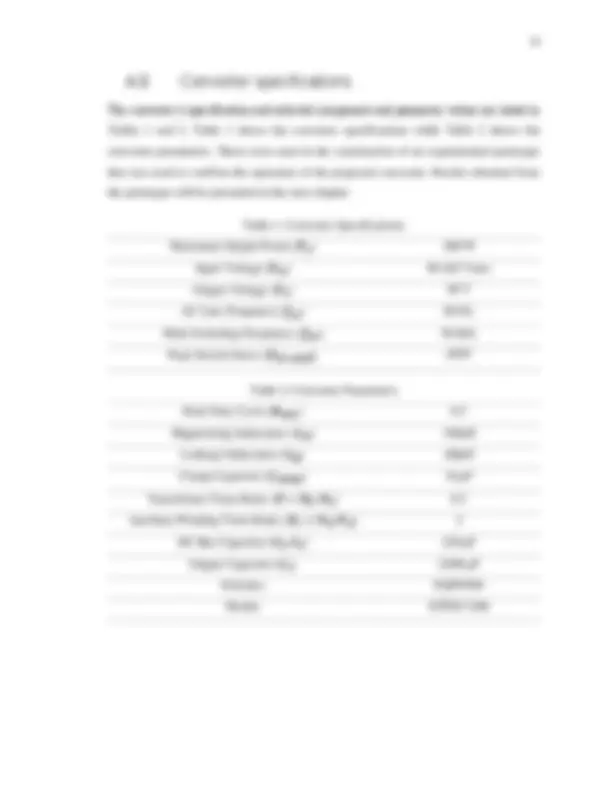
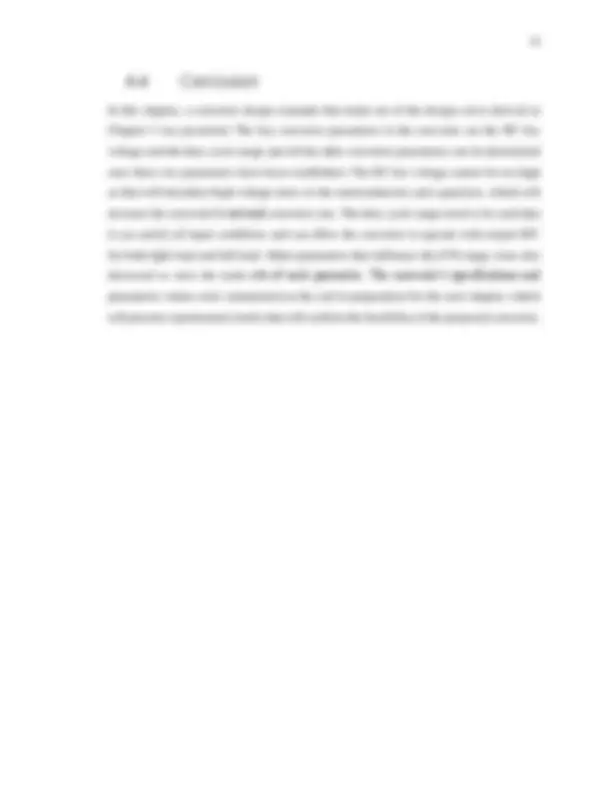
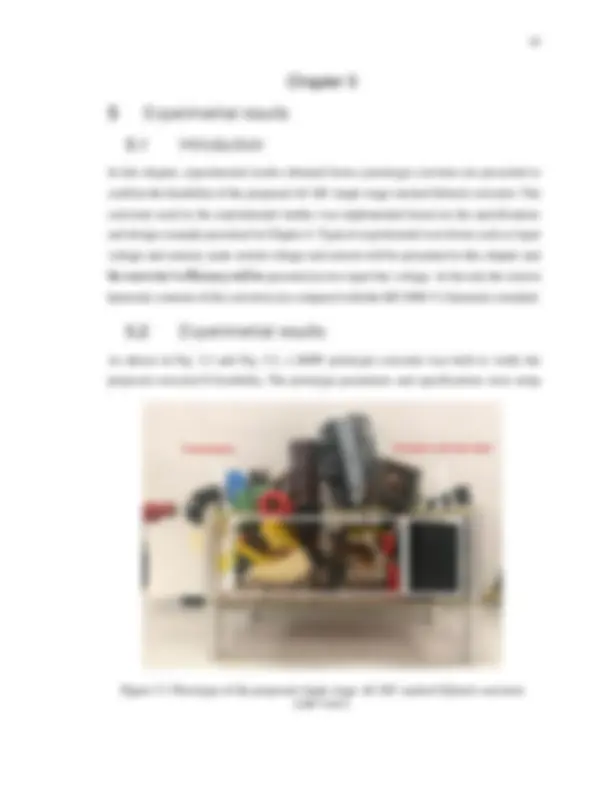
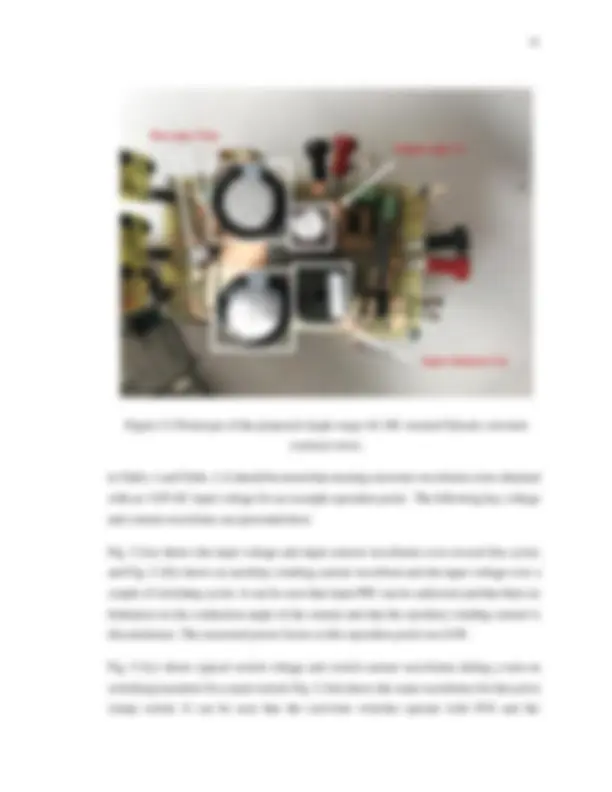
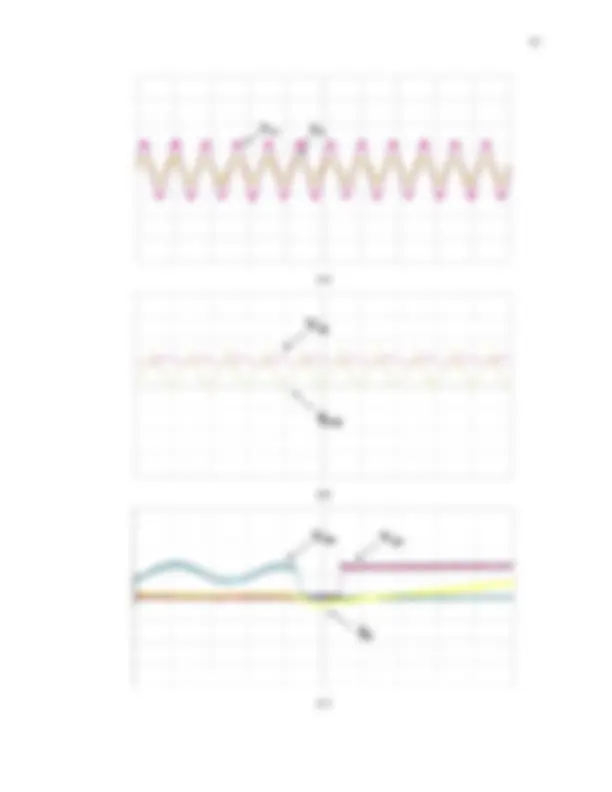
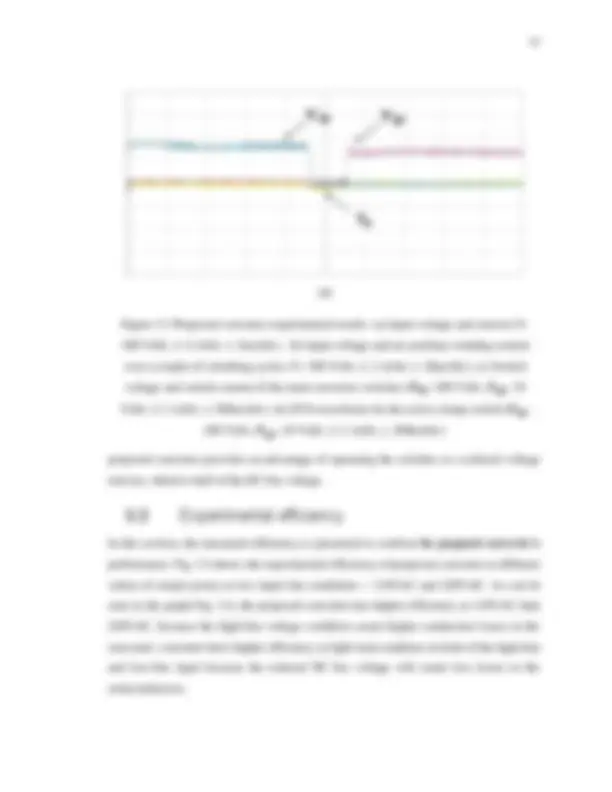
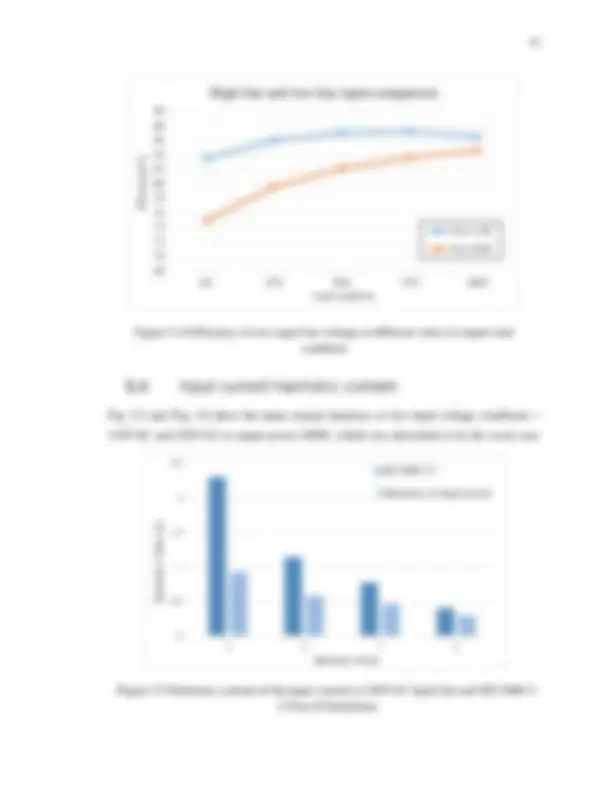
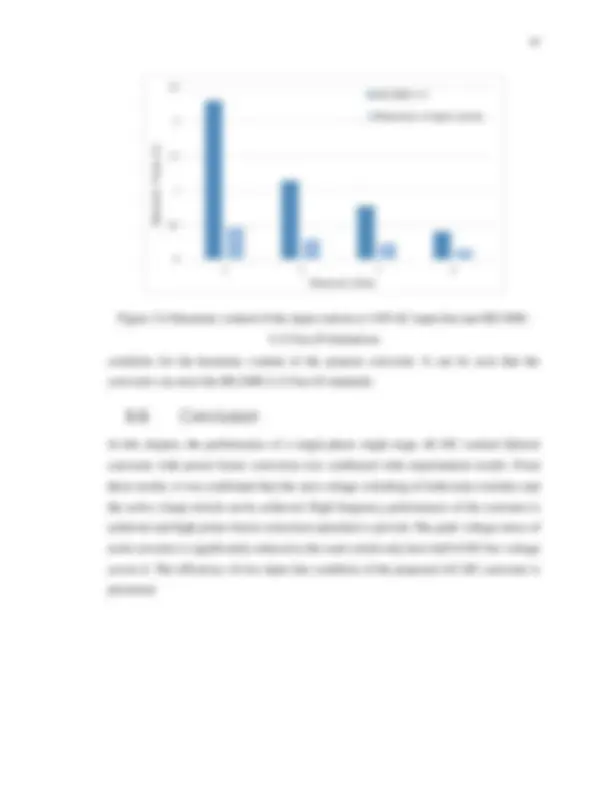
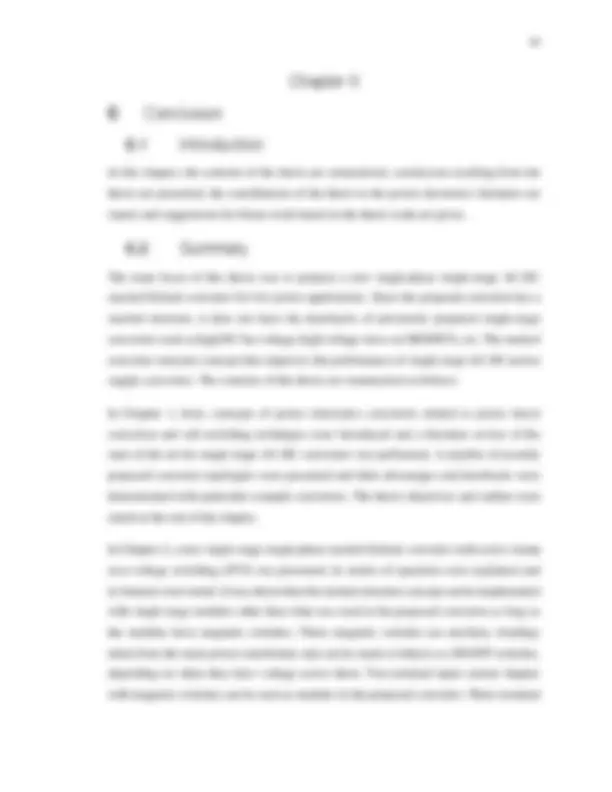
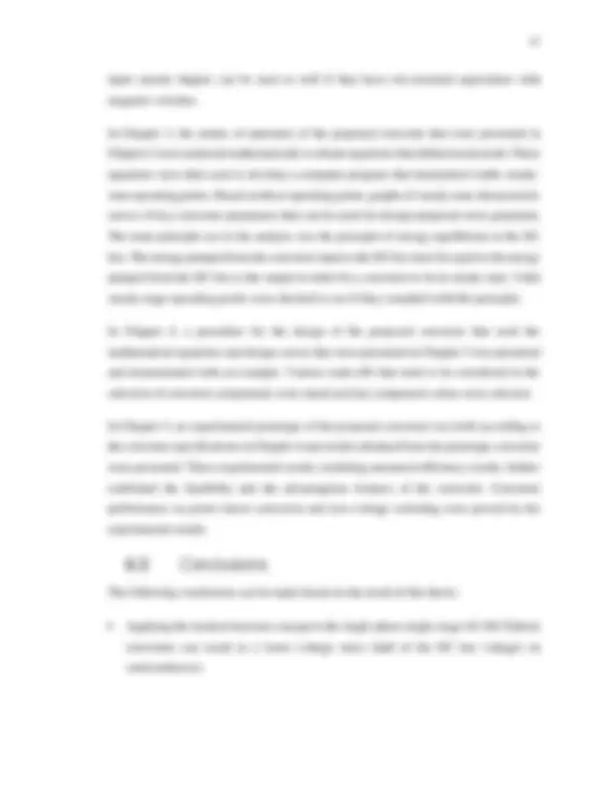
Study with the several resources on Docsity
Earn points by helping other students or get them with a premium plan
Prepare for your exams
Study with the several resources on Docsity
Earn points to download
Earn points by helping other students or get them with a premium plan
Community
Ask the community for help and clear up your study doubts
Discover the best universities in your country according to Docsity users
Free resources
Download our free guides on studying techniques, anxiety management strategies, and thesis advice from Docsity tutors
A detailed circuit analysis and design curves for a single-stage ac-dc converter. The analysis covers the effect of various parameters such as input inductor, transformer magnetizing inductance, and transformer turns ratio on the dc bus voltage and duty cycle of the converter. Design curves are provided to illustrate the relationships between these parameters and the converter's performance. The document also discusses the advantages of the proposed stacked topology, which helps to reduce the voltage stress on the converter components compared to conventional single-stage converters. Overall, this document provides valuable insights into the design and optimization of single-stage ac-dc converters for various power applications.
Typology: Study notes
1 / 44
This page cannot be seen from the preview
Don't miss anything!
2 AC-DC Single-Stage Stacked Flyback Converter
The proposed AC-DC single-stage converter is introduced in this chapter. The converter is
based on the concept of stacking single-stage converter modules on top of each other. In
this chapter, the general operation and the modes operation of proposed converter are
explained, the features of the proposed converter are stated and the extension of the stacked
converter concept to other single-stage converter modules is discussed.
The proposed converter is shown in Fig. 2.1. It is made up of two flyback converters that
are stacked on top of each other at the primary and connected in parallel at the output, an
active clamp auxiliary circuit that is used to help the main power switches turn on with
zero-voltage switching (ZVS) and a front-end AC-DC boost section that consists of a diode
Figure 2. 1 : Single-stage single-phase AC-DC stacked flyback converter.
bridge, an input inductor Lin and two auxiliary windings that are each taken from one of
the flyback transformers and that are each connected in series with a blocking diode.
Inductances 𝐿𝑙𝑘 1 and 𝐿𝑙𝑘 2 may be a combination of the transformer leakage inductances
and some external inductances or just the leakage inductances. 𝐿𝑙𝑘 1 and 𝐿𝑙𝑘 2 help in the
ZVS operation of the converter by storing energy that can be later used to discharge the
switch output capacitances before turn-on.
The auxiliary windings act as ‘magnetic switches’ that cancel the DC bus capacitor voltage
so that the voltage that appears at the right-hand side of input inductor 𝐿𝑖𝑛 is zero. When
the upper switch S 1 is on, the primary voltage of the main transformer 𝑇 1 is positive,
auxiliary winding (𝑁𝑎𝑢𝑥 1 /𝑁 1 =2) that cancels out the DC bus voltage so that the currents in
input inductors Lin rise. When the lower switch S 2 is on, the primary voltage of the main
transformer is negative, auxiliary winding (𝑁𝑎𝑢𝑥 2 /𝑁 1 =2) cancels out the DC bus voltage so
that the currents in input inductors Lin rise. When there is no voltage across the main
transformer primary winding, the total voltage across the DC bus capacitors appears at the
output of the diode bridges and the input currents fall since this voltage is greater than the
input voltage. If the input current is discontinuous, it has a sinusoidal envelope and is in
phase with the input voltage.
Typical converter waveforms are shown in Fig. 2.2 and equivalent circuit diagrams that
show the converter’s modes of operation are shown in Fig. 2.3 with the diode bridge output
replaced by a rectified sinusoidal voltage source. The converter has the following modes
of operation during an entire switching cycle.
Mode 1 (t 0 < t < t 1 ): (Fig. 2.3(a))
In this mode, switch S 1 is ON and the energy is stored in the transformer 𝑇 1. At the same
time, since 𝑆 2 is OFF, stored energy in the magnetizing inductance of transformer 𝑇 2 is
transferred to the load. Since the auxiliary winding generates a voltage that is equal to the
total DC bus voltage with opposite polarity, which cancels the total DC bus capacitor
Mode 3 (t 2 < t < t 3 ): (Fig. 2.3(c))
In Mode 3, the auxiliary switch S 3 is turned ON to start this mode. The stored energy in
capacitor 𝐶𝑐 flows through the leakage inductor 𝐿𝑙𝑘 2 , the primary winding of the
transformer 𝑇 2 , the primary winding of transformer 𝑇 1 , the inductor 𝐿𝑙𝑘 1 , and auxiliary
switch 𝑆 3. Since the output diode is ON during this mode, there is no energy stored in
transformer 𝑇 1.
Mode 4 (t 3 < t < t 4 ): (Fig. 2.3(d))
In this mode, switch 𝑆 3 is OFF. Current in the leakage inductance of 𝑇 2 , 𝐿𝑙𝑘 2 , flows through
the output capacitor of 𝑆 2 and bulk capacitor C 2. It discharges the output capacitor of 𝑆 2 so
that 𝑆 2 can be turned on with ZVS. This also happens for 𝑆 1 and the output capacitor of 𝑆 1
discharges in Mode 8. Since 𝑆 1 is not turned ON, its output capacitor is eventually fully
recharged.
Mode 5(t 4 < t < t 5 ): (Fig. 2.3(e))
In this mode, switch 𝑆 2 is ON with ZVS. The primary current flows through the
magnetizing inductance of 𝑇 2 and increases while the stored energy in the magnetizing
inductance of 𝑇 1 is transferred to the load through the secondary diode.
Mode 6 (t 5 < t < t 6 ): (Fig. 2.3(f))
In this mode, switch S 2 is OFF. The only path for the stored energy in leakage inductance
𝐿𝑙𝑘 2 is to flow through capacitor Cc and the body diode of the active clamp switch 𝑆 3
through the lower bus capacitor C 1 and the output capacitor of S 2.
Mode 7 (t 6 < t < t 7 ): (Fig. 2.3(g))
The auxiliary switch S 3 is turned ON at the start the mode. The stored energy in capacitor
Cc flows through the leakage inductor 𝐿𝑙𝑘 2 , the primary winding of the transformer 𝑇 2 , the
primary winding of transformer 𝑇 1 , the inductor 𝐿𝑙𝑘 1 , and auxiliary switch 𝑆 3. Since the
output diode is ON during this mode, there is no energy stored in transformer 𝑇 2.
Mode 8 (t 7 < t < t 8 ): (Fig. 2.3(h))
In this mode, auxiliary switch S 3 is OFF. Current in inductor 𝐿𝑙𝑘 1 flows through the output
capacitor of S 1 and bulk capacitor C 1. It discharges the output capacitor of S 1 so that S 1 can
Vrec
S
C
C
Cc
S
S
Vrec
S
C
C
Cc
S
S
Lin Lin
Llk
Llk
Llk
Llk
(a) (b)
Vrec
S
C
C
Cc
S
S
Vrec
S
C
C
Cc
S
S
Lin
Llk
Llk
Llk
Llk
Lin
(c) (d) Figure 2. 3 : Modes of operations
The proposed converter has the following features:
stacked topology. The converter components on the primary side (i.e. switches) are exposed to just half the DC bus voltage.
stacked single-stage converters, there is greater flexibility in the design of the converter. Most notably, the input current conduction angle does not have to be limited so that input current distortion is reduced and input power factor is increased.
switch instead of having to use two auxiliary switches – one for each switch.
reduced as the converter switches are exposed to only half the DC bus voltage. Most converters with auxiliary circuits for ZVS operation are either ineffective when the converter is operating with light loads or create more losses than they save under these conditions. The proposed converter has superior light-load efficiency.
to around 50% maximum because the converter has two switches instead of one. In conventional single-stage flyback converters, operating with a duty-cycle above 50% means that peak voltage stress of the single switch must be increased considerably or the converter must operate with small duty cycles at high-line voltages. For the proposed converter, the peak voltage stress in the switches is much less because switch duty cycles > 50% are avoided; this reduction is on top of the voltage stress reduction due to the stacked topology. In other words, two lower power rated, cheaper and more widely available devices can be used instead of a very expensive single device.
The proposed converter is just one way of implementing the stacked converter concept. In
general, it can be implemented with any single single-stage converter module that has
auxiliary windings from the main transformer. The basic idea is to stack one module on
top of the other as shown in Fig. 2.4, then connect the auxiliary windings appropriately at
the input and interleave the output windings as in Fig. 1.7(a). How this can be accomplished
will be explained as follows in this section of the thesis. Much of the following discussion
is taken from [10].
Although many single-stage AC-DC flyback converters, which are referred to as input
current shapers (ICSs) in [ 10 ], have been proposed, these converters share a number of
common properties. A number of ICSs can be classified as being two-terminal ICSs and
three-terminal ICSs, as shown in Fig. 2.5 and Fig. 2.6. Two-terminal ICSs operate based
on the principle of the ‘magnetic switch’ must like the module converters in the proposed
converter. The basic structure of a two-terminal ICS is shown in Fig. 2.7(a), where it can
be seen that the ICS has a discharge branch and a charge branch and that the two branches
are in parallel. The input inductor current is made to rise by ‘charging’ the inductor through
the charge branch and is made to fall by allowing current to flow into the ‘discharge’
branch. In the proposed converter, which uses two-terminal ICS modules, current flowing
through the charge branch corresponds to Mode 1 of operation and current flowing through
the discharge branch corresponds to Mode 5 of operation.
Three-terminal ICSs also have discharge and charge branches, but the charge branch is not
connected in parallel to the discharge branch. This branch is, instead connected to the input
switch as shown in Fig. 2.7(b). The proposed converter can be implemented with two-
terminal ICSs, but not with three-terminal ICSs because only modules with magnetic
switches can be used. It is, however, possible to convert a three-terminal ICS into a two-
terminal ICS, as explained in [ 10 ].
Vo
AC
Auxiliary winding 1
Auxiliary winding 2
Lin
Figure 2. 4 : Modular diagram of proposed stacked single-stage converter concept.
Cb (^) Vo
Lin
N1 N
Q
Oc
Osw AC 3-terminal ICS cell
(a)
Cb Vo
Lin
N1 N
Q
N Osw
Oc
3-terminal ICS cell
AC
(b)
Cb Vo
Lin
N1 N
Q
N Osw
N Oc
AC 3-terminal ICS cell
(c)
Cb (^) Vo
Lin
N1 N
Q
Cb Osw
Oc
AC 3-terminal ICS cell
(d) Figure 2. 6 : Example single-stage converters with three-terminal input current shaper (ICS) cells [10].
The general rule is to take a three-terminal ICS cell and add an extra winding as shown in
Fig. 2.8(a). The polarity of the added winding should be such that the equivalent circuit
before and after the translation is the same when the switch is on, as shown in Fig. 2.8(b).
The number of turns of the added winding should equal that of primary winding of the
transformer in the DC-DC converter section if the original three-terminal ICS charge
branch had a direct connection to the main converter switch. If the connection is through
an auxiliary winding that produces a counter voltage to change the energy equilibrium at
the DC bus to a more favorable one like the converter shown in Fig. 2.9 [ 42 ], then the
number of turns of the added winding should be such that the counter voltage is reproduced
Cb Vo
Lin
N1 N
Q
Osw AC 2-terminal ICS cell
Discharge Branch
Charge Branch
(a)
Cb Vo
Lin
N1 N
Q
Osw AC 3-terminal ICS cell
Discharge Branch
Charge Branch
(b)
Figure 2. 7 : Single-stage PFC with generic ICS cell (a) two-terminal (b) three-terminal [10].
The proposed AC-DC single-stage converter was introduced in this chapter. In this chapter,
the general operation and the modes of proposed converter were explained and its features
were stated. Since the converter’s topology was based on the stacking of single-stage
converter modules on top of each other, the extension of the stacked converter concepts to
other single-stage converter modules was discussed. In order for a single-stage converter
to be implemented as a module in a stacked converter, it must have a magnetic switch.
Such a switch is implemented using an auxiliary winding from the main transformer. It was
shown in this chapter that numerous, previously proposed single-stage converters, whether
they be two-terminal input current shapers or three-terminal input current shapers, can be
stacked as long as they have magnetic switches or have equivalent topologies with
magnetic switches.
AC
Cb (^) Vo
Lin
N1 N
S
Cf N
Figure 2. 9 : AC-DC single-stage converter with auxiliary winding that produces counter voltage proposed in [ 42 ].
3 Circuit Analysis
In the previous chapter, the general operation and the key modes of operation of the
proposed converter were explained. The steady-state characteristics of key converter
parameters are determined by a mathematical analysis of the converter’s modes of
operation in this chapter. In this chapter, mathematical equations that define each mode of
the proposed converter are derived and these equations form the basis of a computer
program that will allow graphs of characteristic curves to be plotted. These graphs will then
be used in the next chapter to develop a procedure for the design of the proposed converter.
For the steady-state analysis of the proposed converter’s modes of operation, the following
assumptions have been made:
This allows each converter modules to emulate a single-stage converter with no counter voltage applied to its input inductor. This counter voltage reduces the amount of energy stored in the input inductor and affects the energy equilibrium at the DC bus.
bus capacitor 𝐶 1 and 𝐶 2 are the same, the switches, semiconductors, transformer ratings are the same).
The objective of the steady-state analysis is to obtain the current that goes in and goes out
of the intermediate DC bus capacitor. As mentioned in previous chapters, single-stage AC-
DC converters do not have control of the DC bus voltage because they only have one
controller to regulate the output voltage. Under steady-state conditions, the average current
total DC bus voltage, but with opposite polarity. The input voltage across the input inductor
is thus the rectified supply voltage so that input current in Lin rises according to
where |𝑣𝑖𝑛,𝑘| is the rectified AC input voltage during switching cycle interval k. The input
voltage can be considered to be a constant value in a single switching cycle as the switching
frequency is much higher compared with the AC input line frequency. The current in the
input inductor 𝐿𝑖𝑛 at the end of Mode 1 is
Duty cycle D is defined as the time when main switch 𝑆 1 or 𝑆 2 is ON during the entire
switching cycle (two switches are ON for exactly the same length of time but in alternative
half cycles). The two switches are each operated in during an alternative half switching
cycle 𝑇𝑠𝑤/ 2 or 2 𝑓𝑠𝑤 where 𝑓𝑠𝑤 is the switching frequency of the main switch.
Mode 2 (t 0 < t < t 1 ): (Fig. 3.2)
The equivalent circuit of Mode 2 is shown in Fig. 3.2. Because there is no switch closed
during this mode, the current in the circuit is circulating and energy in the leakage
C
Cc (^) Vo
Llk
Figure 3. 2 : Equivalent circuit of Mode 2.
inductance flows though the active clamp capacitor. Following Kirchhoff’s Voltage Law
(KVL), the following equation can be established:
where the two bus capacitors equally divide the DC bus voltage. 𝐿𝑙𝑘 1 is the leakage
inductance of the upper converter transformer while 𝐿𝑚 1 is the magnetizing inductance of
upper converter transformer. 𝑉𝑐𝑙𝑎𝑚𝑝 is the voltage across the clamp capacitor. During this
mode, the energy in main transformer 𝑇 1 is transferred to the output load until the current
in the transformer goes zero. The output voltage can be expressed as follows:
where N is the transformer turns ratio between the primary and secondary (𝑁 1 /𝑁 2 ).
Mode 3 (t 0 < t < t 1 ): (Fig. 3.3)
The equivalent circuit of Mode 3 is shown in Fig. 3.3. Auxiliary switch S 3 is turned ON
with ZVS. The energy in transformer T 1 is transferred to the output load while the energy
in clamp capacitor is transferred to leakage inductor 𝐿𝑙𝑘 2 , according to
Figure 3. 3 : Equivalent circuit of Mode 3.
bus voltage. As the converter specification is exactly the same, the current in the input
inductor in Mode 5 in the second part of the switching cycle is same in Mode 1 according
to
The current is bounded by a sinusoidal envelope related to the input rectifier voltage, as
shown in Fig. 3.6, and it rises and falls twice in one switching cycle 𝑓𝑠𝑤. The ON time for
each switch is
so that the total input current in interval k is
Vrec
Lin
Llk
Figure 3. 5 : Equivalent circuit of Mode 5
The input inductor current flows into the DC bus capacitor as it is the only path that is
available to it; therefore, the average current of the input current is the same current injected
into the DC bus. By accumulating all the switching intervals together, the average current
flowing into the DC bus during AC line cycle is
𝑛
𝑘= 0
where 𝑓𝑎𝑐 the frequency of AC is input line and n is the number of interval in one AC line
cycle
𝑣𝑟𝑒𝑐 is the rectified voltage output from the rectified diode bridge that can be determined
as follows
𝑣𝑟𝑒𝑐 = 𝑉𝑟𝑚𝑠 ∙ |sin( 2 𝜋𝑘/𝑛)| (3.12)
Equ. (3.10) will eventually be compared to the average current flowing out of the DC bus
to determine whether an energy equilibrium has been established and the converter is
operating in steady-state.
Figure 3. 6 : DCM operation on input inductor.