
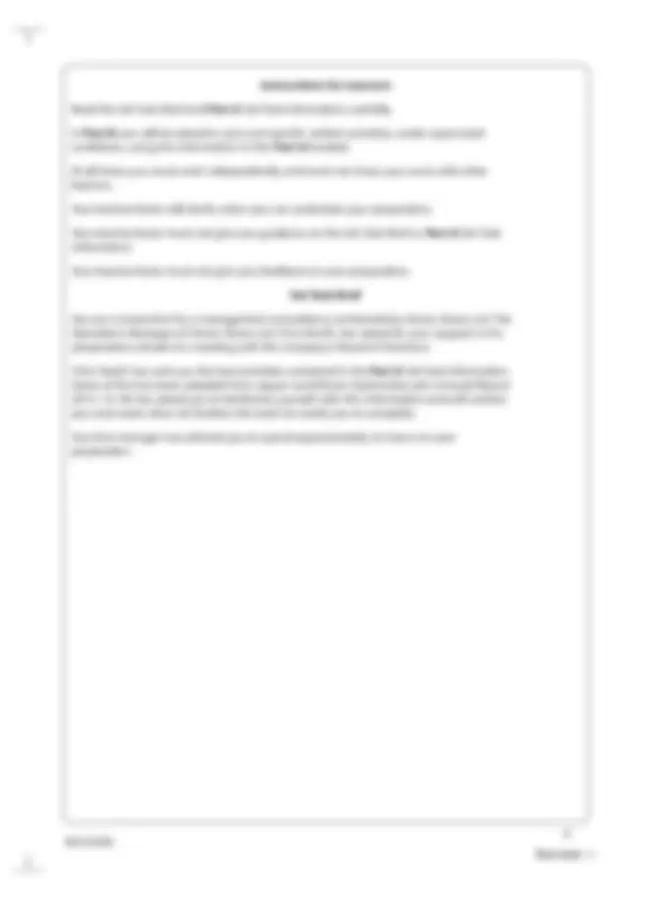
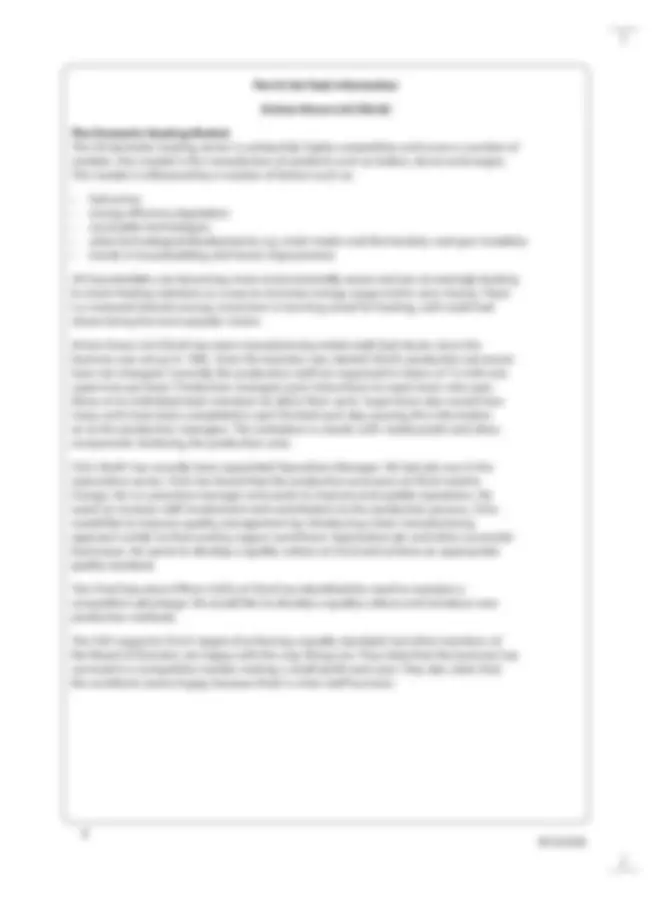
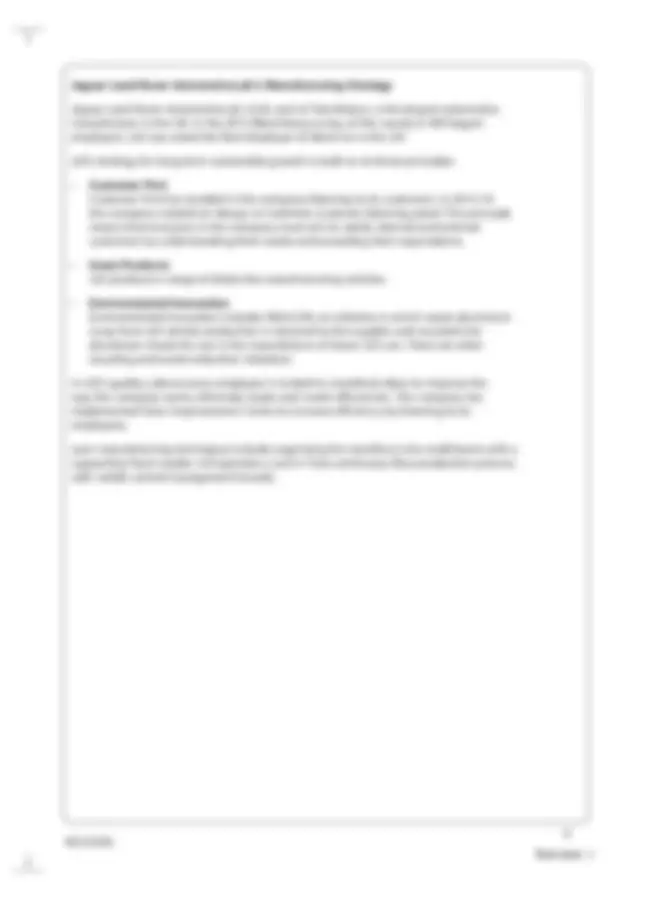
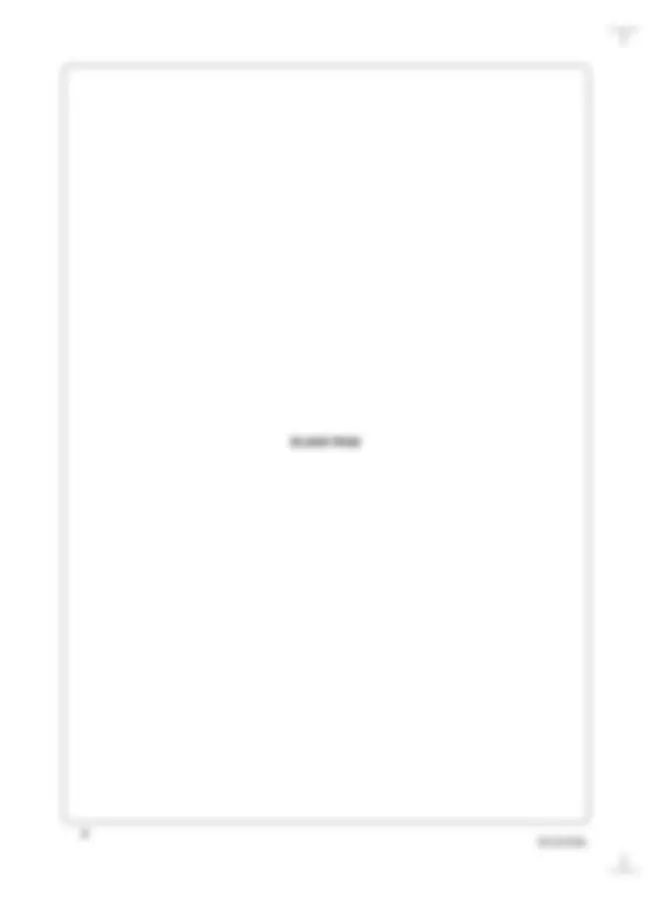
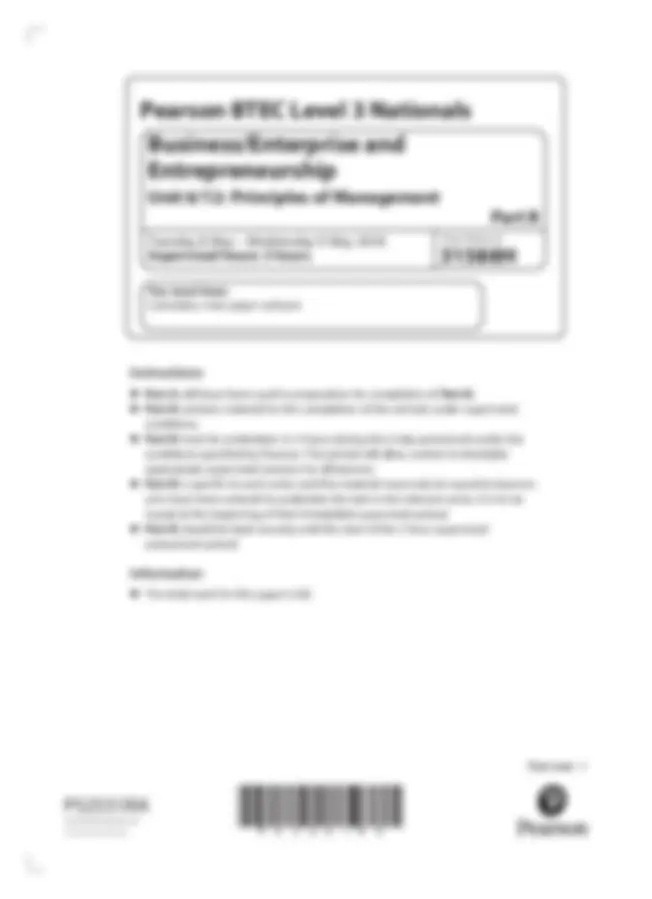
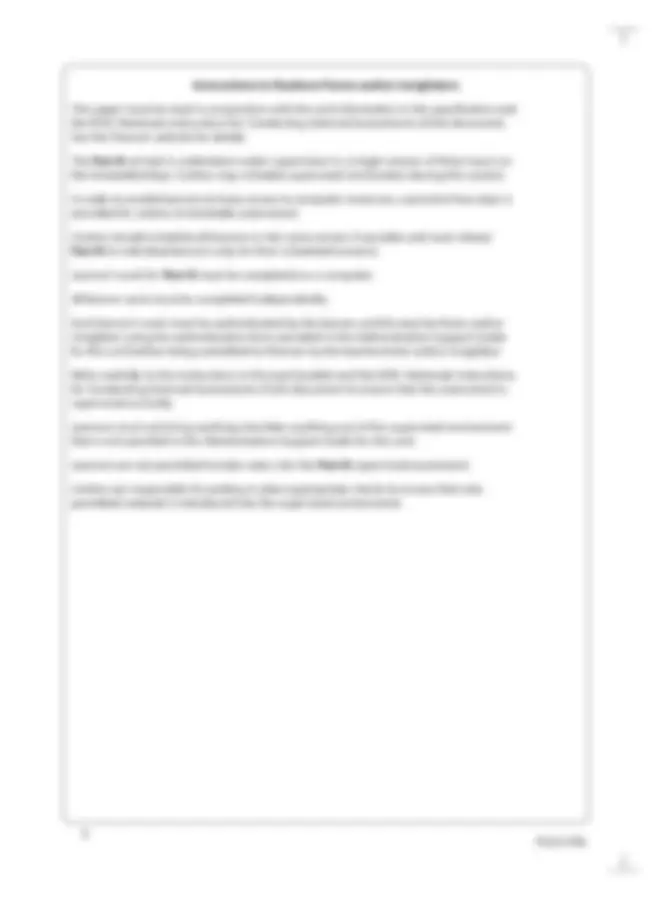
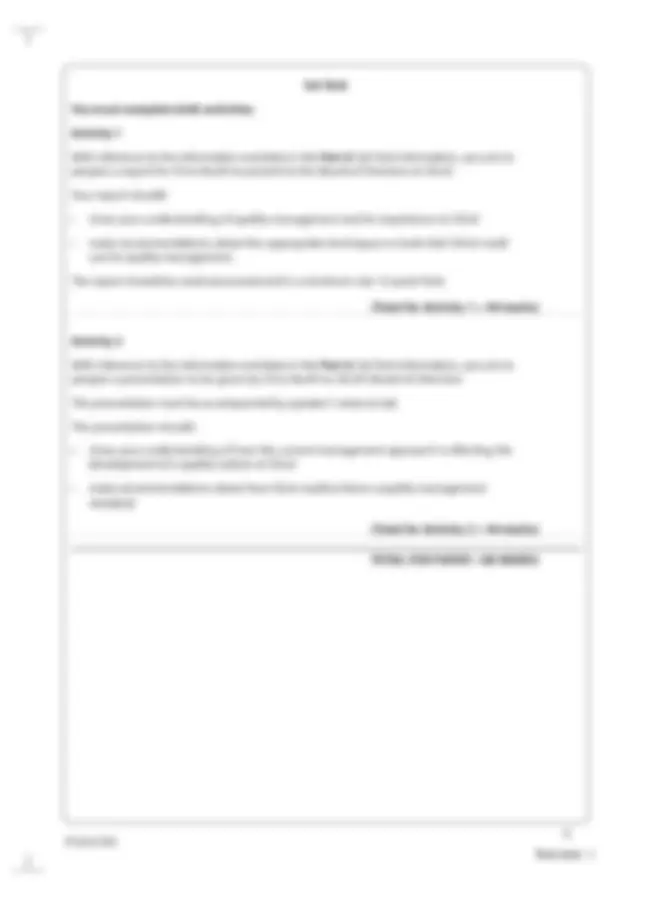
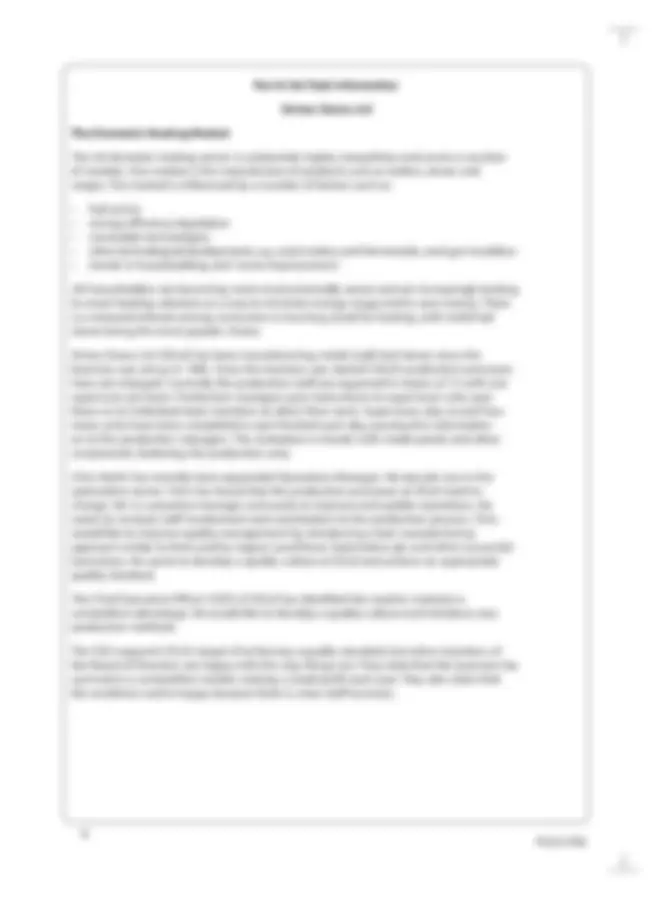
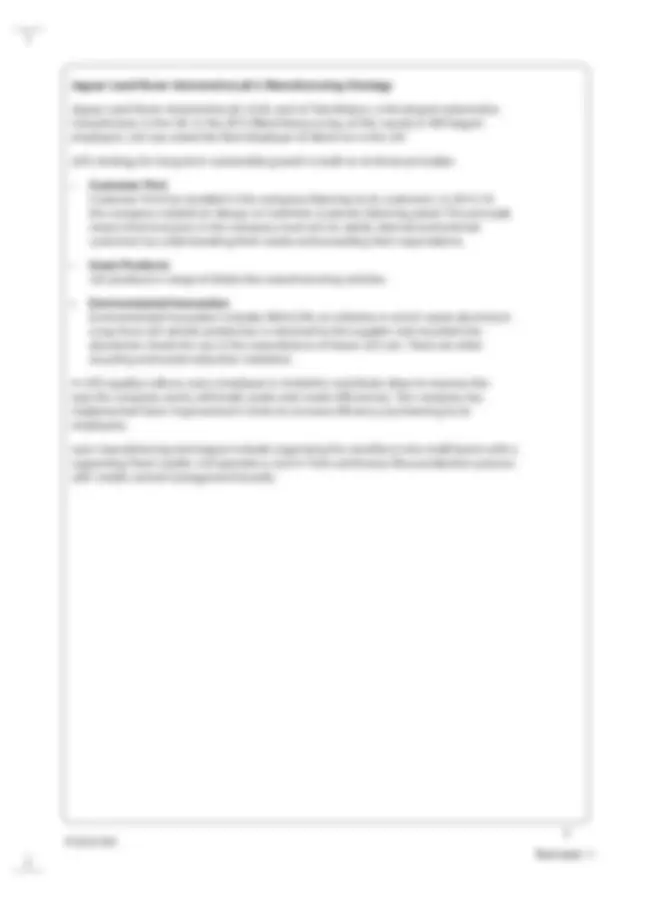
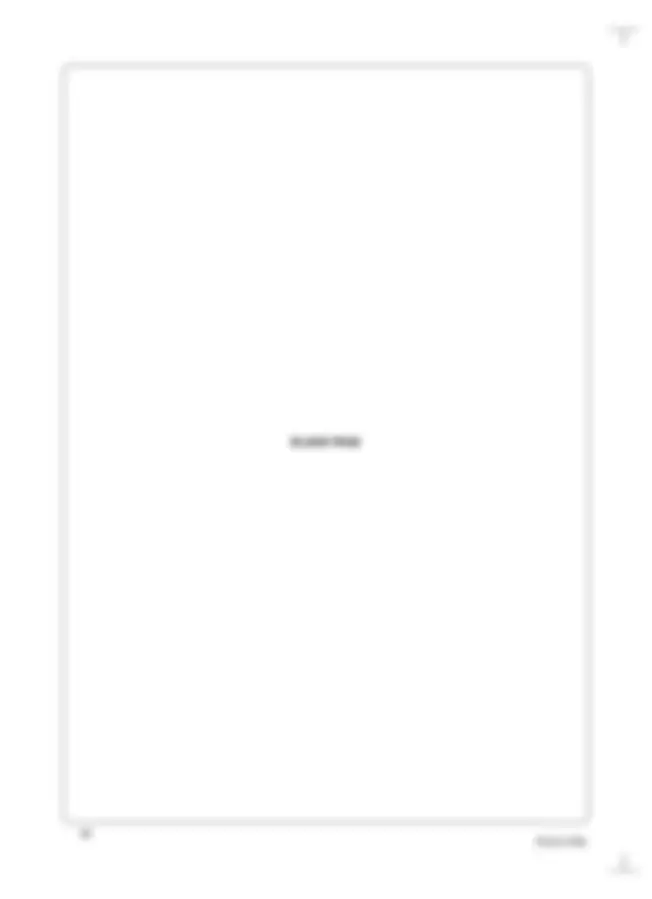
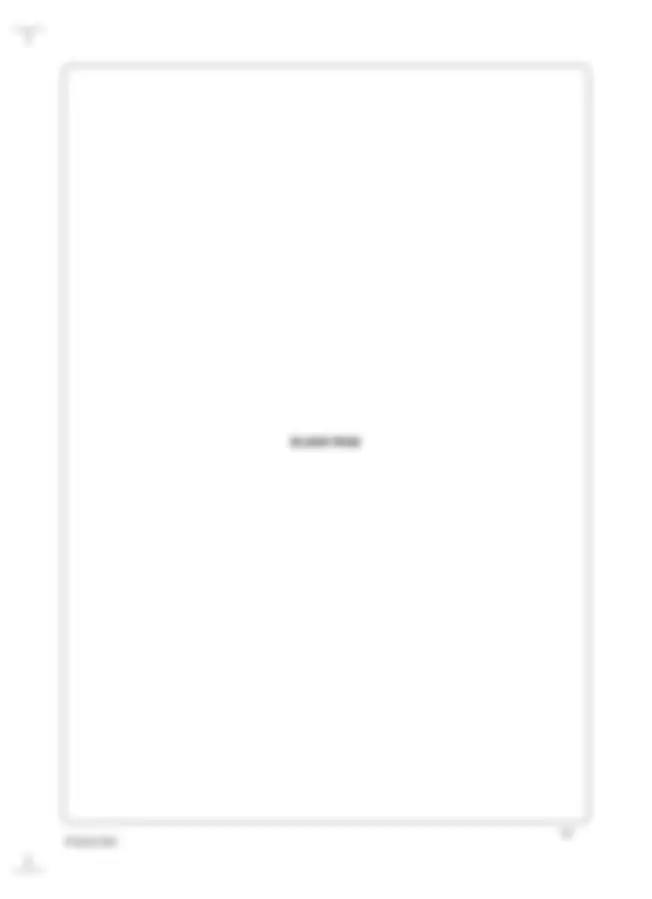
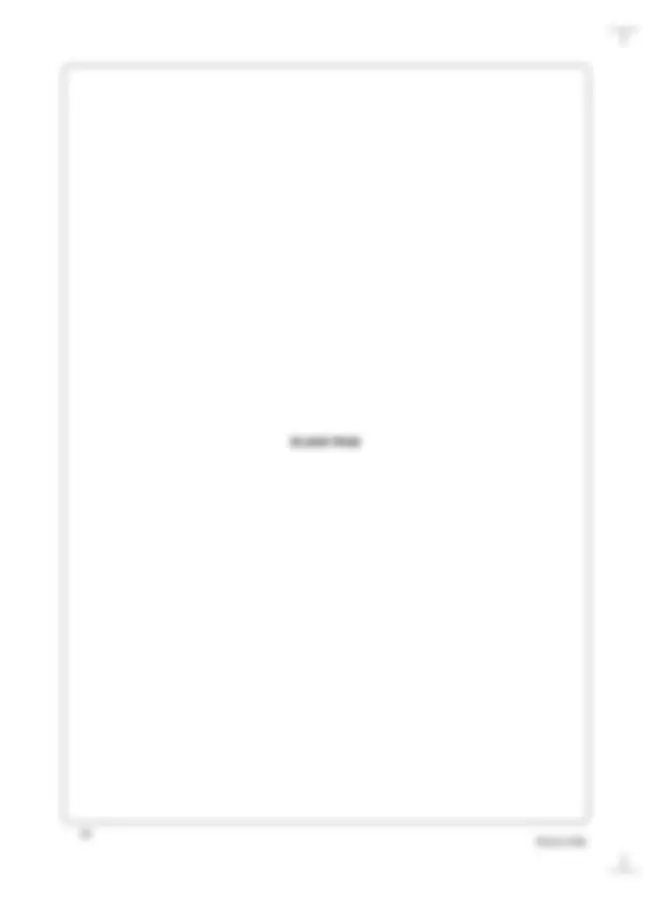
Study with the several resources on Docsity
Earn points by helping other students or get them with a premium plan
Prepare for your exams
Study with the several resources on Docsity
Earn points to download
Earn points by helping other students or get them with a premium plan
Community
Ask the community for help and clear up your study doubts
Discover the best universities in your country according to Docsity users
Free resources
Download our free guides on studying techniques, anxiety management strategies, and thesis advice from Docsity tutors
An analysis of jaguar land rover automotive plc's manufacturing strategy, focusing on its principles of customer first, great products, and environmental innovation. It also discusses the application of lean manufacturing techniques in the service industry, using aldi as an example. Additionally, the document introduces a case study on strines stoves ltd, where the company's production manager, chris, aims to improve quality management by introducing a lean manufacturing approach. Intended for use in a business/enterprise and entrepreneurship unit, specifically for the principles of management, and is to be used for preparation and completion of a set task under supervised conditions.
Typology: Summaries
1 / 20
This page cannot be seen from the preview
Don't miss anything!
Paper Reference
Turn over
set task.
advised to spend approximately six hours on Part A.
who have been entered to undertake the task in the relevant series.
Pearson.
You must have: Calculator, note paper and pen
©2018 Pearson Education Ltd. 1/1/1/1/1/1/1/1/1/1/1/
Turn overTurn over
2 W52550A
Instructions to Teachers/Tutors
This paper must be read in conjunction with the unit information in the specification and the BTEC Nationals Instructions for Conducting External Assessments (ICEA) document. See the Pearson website for details.
Learners should familiarise themselves with the specific case study given in this Part A booklet.
Learners are advised to spend approximately six hours on Part A.
Centres must issue this booklet at the appropriate time and advise learners of the timetabled sessions during which they can prepare. It is expected that scheduled lessons or other timetabled slots will be used for some or all of the preparation.
Learners are not permitted to take notes or any other materials into the supervised Part B assessment period.
The supervised assessment for Part B will take place in a timetabled period specified by Pearson.
Centres should schedule all learners at the same time or supervise cohorts to ensure there is no opportunity for collusion.
Learner work for Part B must be completed on a computer.
Refer carefully to the instructions in this Part A booklet and the BTEC Nationals Instructions for Conducting External Assessments (ICEA) document to ensure that the preparatory period is conducted correctly and that learners have the opportunity to carry out the required activities independently.
4 W52550A
Part A Set Task Information
Strines Stoves Ltd (SSLtd)
The Domestic Heating Market The UK domestic heating sector is substantial, highly competitive and covers a number of markets. One market is the manufacture of products such as boilers, stoves and ranges. This market is influenced by a number of factors such as:
UK householders are becoming more environmentally aware and are increasingly looking to smart heating solutions as a way to minimise energy usage and to save money. There is a renewed interest among consumers in burning wood for heating, with multi-fuel stoves being the most popular choice.
Strines Stoves Ltd (SSLtd) has been manufacturing metal multi-fuel stoves since the business was set up in 1985. Since the business was started SSLtdās production processes have not changed. Currently the production staff are organised in teams of 15 with one supervisor per team. Production managers give instructions to supervisors who pass these on to individual team members to direct their work. Supervisors also record how many units have been completed or part finished each day, passing this information on to the production managers. The workplace is chaotic with metal panels and other components cluttering the production area.
Chris North has recently been appointed Operations Manager. His last job was in the automotive sector. Chris has found that the production processes at SSLtd need to change. He is a proactive manager and wants to improve and update operations. He wants to increase staff involvement and contribution to the production process. Chris would like to improve quality management by introducing a lean manufacturing approach similar to that used by Jaguar Land Rover Automotive plc and other successful businesses. He wants to develop a quality culture at SSLtd and achieve an appropriate quality standard.
The Chief Executive Officer (CEO) of SSLtd has identified the need to maintain a competitive advantage. He would like to develop a quality culture and introduce new production methods.
The CEO supports Chrisās target of achieving a quality standard, but other members of the Board of Directors are happy with the way things are. They state that the business has survived in a competitive market, making a small profit each year. They also claim that the workforce seems happy because there is a low staff turnover.
5 Turn over
Jaguar Land Rover Automotive plcās Manufacturing Strategy
Jaguar Land Rover Automotive plc (JLR), part of Tata Motors, is the largest automotive manufacturer in the UK. In the 2016 Bloomberg survey of the countryās 400 largest employers, JLR was voted the āBest Employer to Work For in the UKā.
JLRās strategy for long-term sustainable growth is built on its three principles:
In JLRās quality culture every employee is invited to contribute ideas to improve the way the company works, eliminate waste and create efficiencies. The company has implemented Team Improvement Circles to increase efficiency by listening to its employees.
Lean manufacturing techniques include organising the workforce into small teams with a supporting Team Leader. JLR operates a Just in Time continuous flow production process with visible control management boards.
7 W52550A
Lean Manufacturing Techniques in the Service Industries
Lean manufacturing techniques have been adapted for use in the service industries. The supermarket chain, Aldi, applies a lean approach to its business operations, including:
8 W52550A
2 P52551RA
Instructions to Teachers/Tutors and/or Invigilators
This paper must be read in conjunction with the unit information in the specification and the BTEC Nationals Instructions for Conducting External Assessments (ICEA) document. See the Pearson website for details.
The Part B set task is undertaken under supervision in a single session of three hours on the timetabled days. Centres may schedule supervised rest break(s) during this session.
In order to enable learners to have access to computer resources, a period of two days is provided for centres to timetable assessment.
Centres should schedule all learners in the same session if possible and must release Part B to individual learners only for their scheduled sessions.
Learnerās work for Part B must be completed on a computer.
All learner work must be completed independently.
Each learnerās work must be authenticated by the learner and the teacher/tutor and/or invigilator using the authentication form provided in the Administrative Support Guide for this unit before being submitted to Pearson by the teacher/tutor and/or invigilator.
Refer carefully to the instructions in this task booklet and the BTEC Nationals Instructions for Conducting External Assessments (ICEA) document to ensure that the assessment is supervised correctly.
Learners must not bring anything into/take anything out of the supervised environment that is not specified in the Administrative Support Guide for this unit.
Learners are not permitted to take notes into the Part B supervised assessment.
Centres are responsible for putting in place appropriate checks to ensure that only permitted material is introduced into the supervised environment.
3 Turn over
Maintaining security
Outcomes for submission
Each learner will submit:
- a report on quality management - a presentation about quality culture and quality standards.
A fully completed authentication sheet must be submitted by each learner.
5 Turn over
Set Task
You must complete both activities.
Activity 1
With reference to the information and data in the Part A Set Task Information, you are to prepare a report for Chris North to present to the Board of Directors at SSLtd.
Your report should:
The report should be word processed and in a minimum size 12-point font.
(Total for Activity 1 = 44 marks)
Activity 2
With reference to the information and data in the Part A Set Task Information, you are to prepare a presentation to be given by Chris North to SSLtdās Board of Directors.
The presentation must be accompanied by speakerās notes/script.
The presentation should:
- show your understanding of how the current management approach is affecting the development of a quality culture at SSLtd
(Total for Activity 2 = 44 marks)
6 P52551RA
Part A Set Task Information
Strines Stoves Ltd
The Domestic Heating Market
The UK domestic heating sector is substantial, highly competitive and covers a number of markets. One market is the manufacture of products such as boilers, stoves and ranges. This market is influenced by a number of factors such as:
UK householders are becoming more environmentally aware and are increasingly looking to smart heating solutions as a way to minimise energy usage and to save money. There is a renewed interest among consumers in burning wood for heating, with multi-fuel stoves being the most popular choice.
Strines Stoves Ltd (SSLtd) has been manufacturing metal multi-fuel stoves since the business was set up in 1985. Since the business was started SSLtdās production processes have not changed. Currently the production staff are organised in teams of 15 with one supervisor per team. Production managers give instructions to supervisors who pass these on to individual team members to direct their work. Supervisors also record how many units have been completed or part finished each day, passing this information on to the production managers. The workplace is chaotic with metal panels and other components cluttering the production area.
Chris North has recently been appointed Operations Manager. His last job was in the automotive sector. Chris has found that the production processes at SSLtd need to change. He is a proactive manager and wants to improve and update operations. He wants to increase staff involvement and contribution to the production process. Chris would like to improve quality management by introducing a lean manufacturing approach similar to that used by Jaguar Land Rover Automotive plc and other successful businesses. He wants to develop a quality culture at SSLtd and achieve an appropriate quality standard.
The Chief Executive Officer (CEO) of SSLtd has identified the need to maintain a competitive advantage. He would like to develop a quality culture and introduce new production methods.
The CEO supports Chrisās target of achieving a quality standard, but other members of the Board of Directors are happy with the way things are. They state that the business has survived in a competitive market, making a small profit each year. They also claim that the workforce seems happy because there is a low staff turnover.
8 P52551RA
Revenue (Ā£m)
Profit pre-tax (Ā£m)
(Source: figures adapted from JLR Annual Report 2015ā16)
Figure 1
JLR Sales by Region 2015ā16^1
UK N America (^) China 2 Europe Rest of the world
Sales (%) 20 19 19 24 18
Change in sales from 2014ā15 (%)
(^1) 521 571 units sold in 2015ā (^2) Adverse impact of slowdown in the Chinese economy
(Source: figures adapted from JLR Annual Report 2015ā16)
Figure 2
JLR ā Other Highlights 2015ā
1 Voted Number 1 in Bloombergās āBest Employers UK 2016ā
2 Exported 80% of all vehicles produced
Employed 3 000 new recruits (including 600 graduates) increasing workforce to 38 000 worldwide
4 Won 150 awards including the Queenās Award for Sustainable Development
5 Invested £3.1bn in the company
Figure 3
9 P52551RA
Lean Manufacturing Techniques in the Service Industries
Lean manufacturing techniques have been adapted for use in the service industries. The supermarket chain, Aldi, applies a lean approach to its business operations, including:
- Just in Time approach to stock control - staff trained to carry out a range of different tasks/jobs in the store - stocking fewer variations of each product compared to other UK supermarkets - trolleys having a £1 deposit system - rejecting 24 hour a day opening - sourcing the majority of its fruit and vegetables locally - customers packing shopping away from the check-out - pallet-based displays - replacing standard practices such as shelf stacking by topping up individual products using display-ready consignments.
11 P52551RA
12 P52551RA