
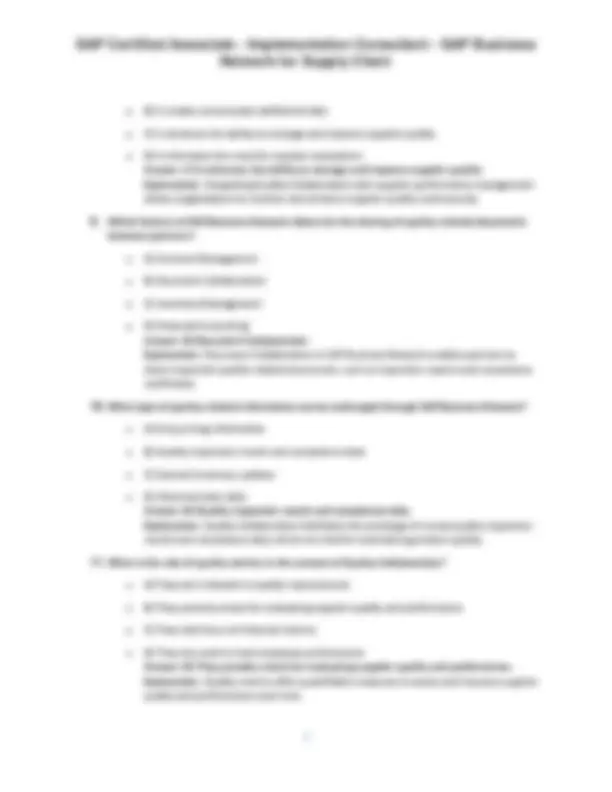
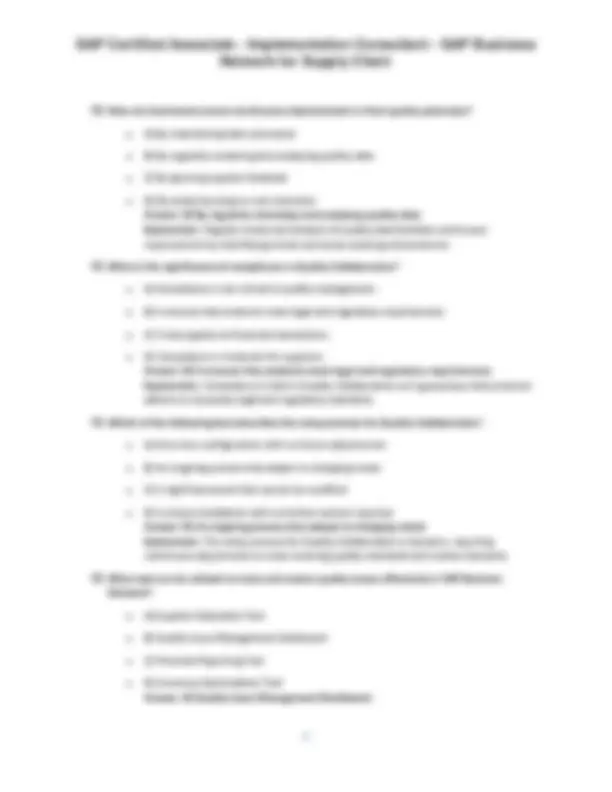
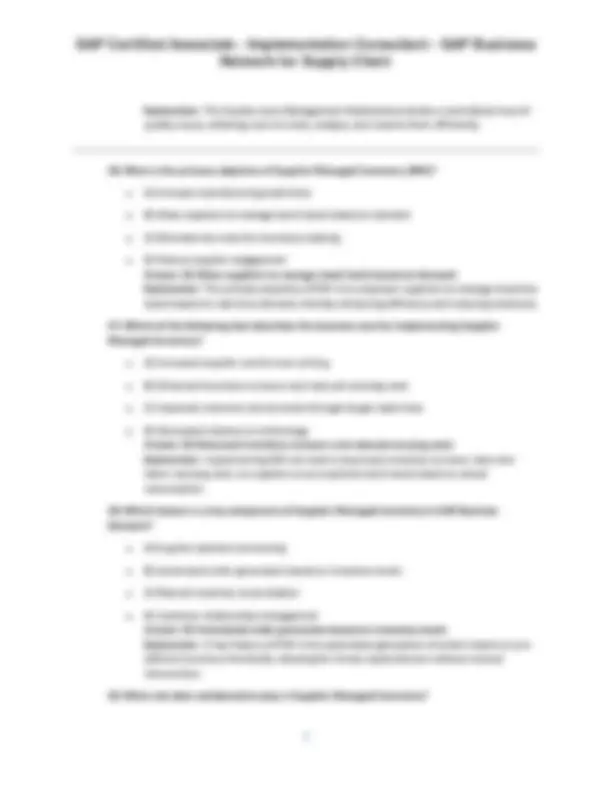
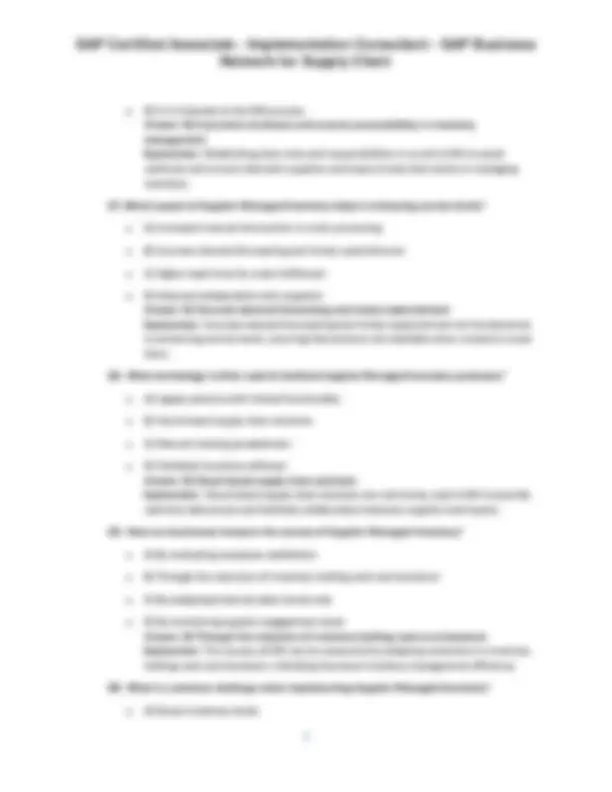
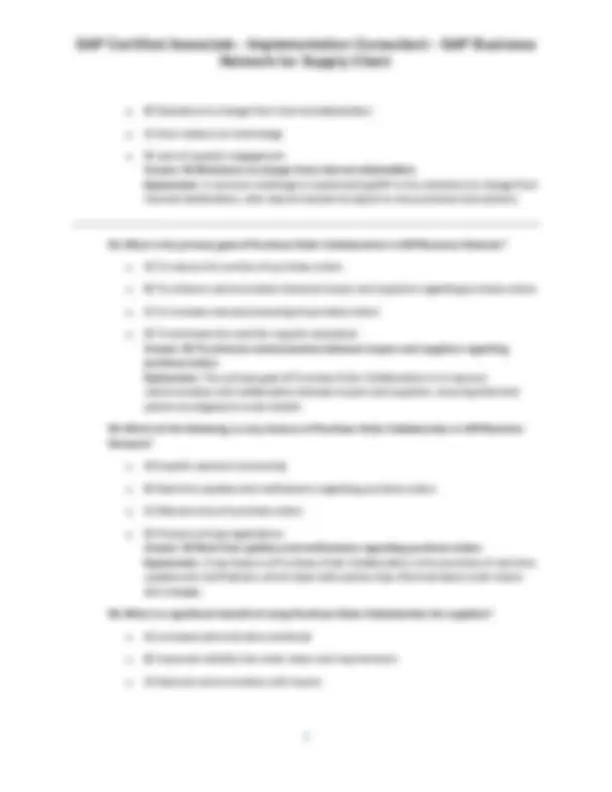
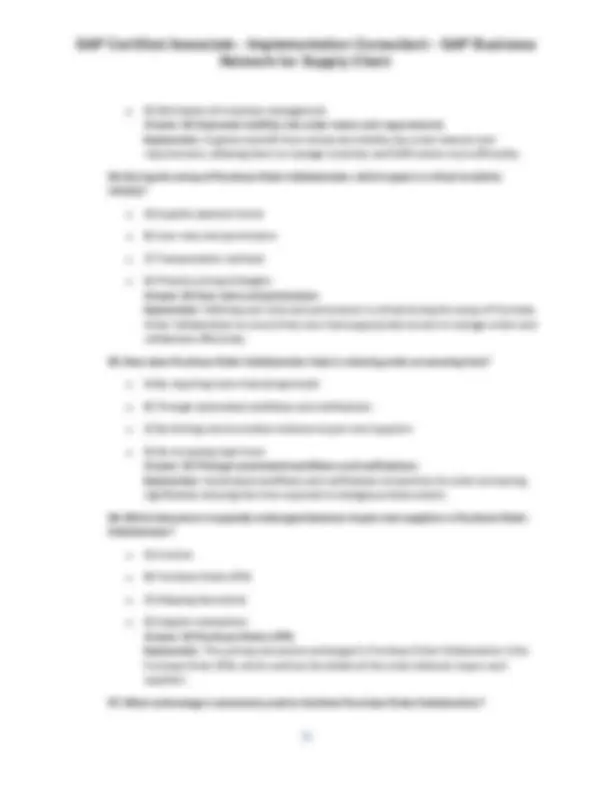
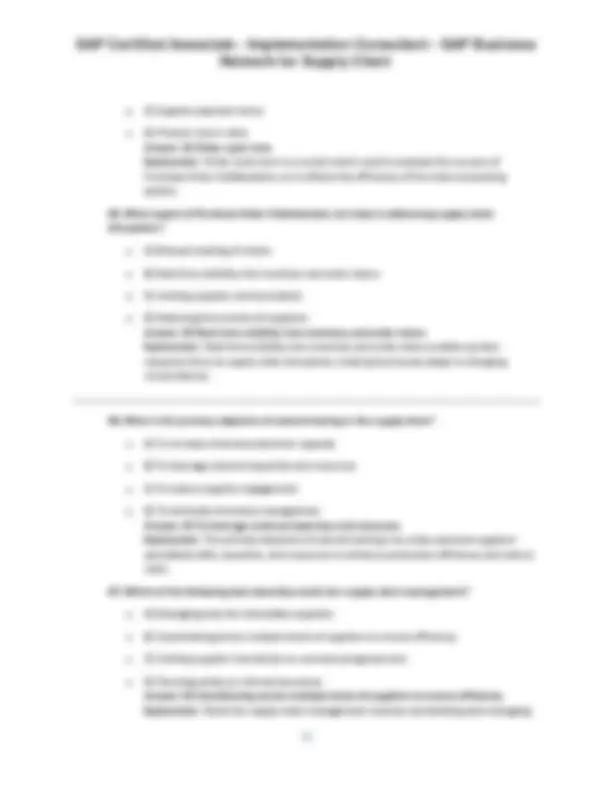
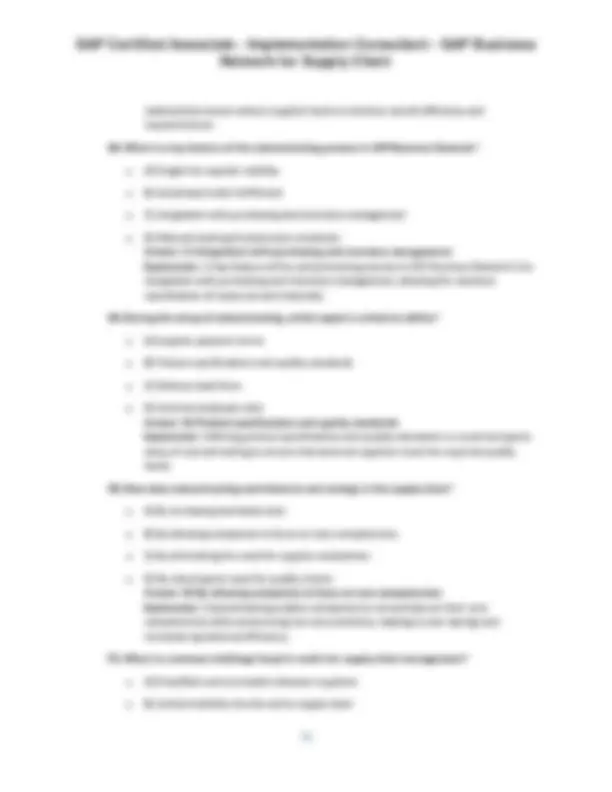
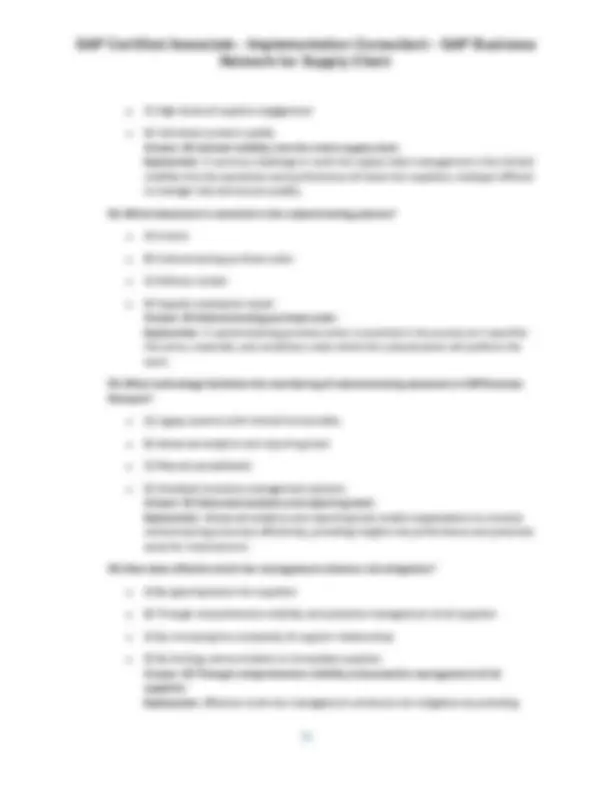

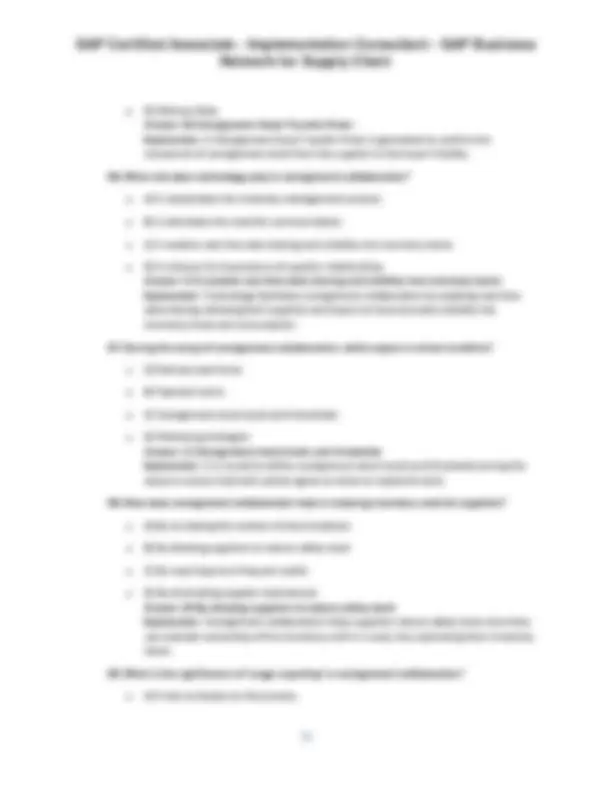
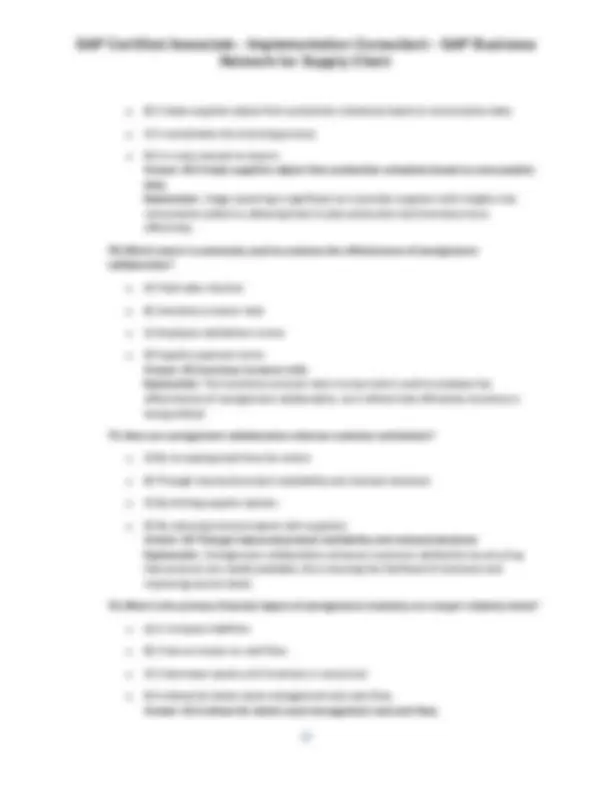
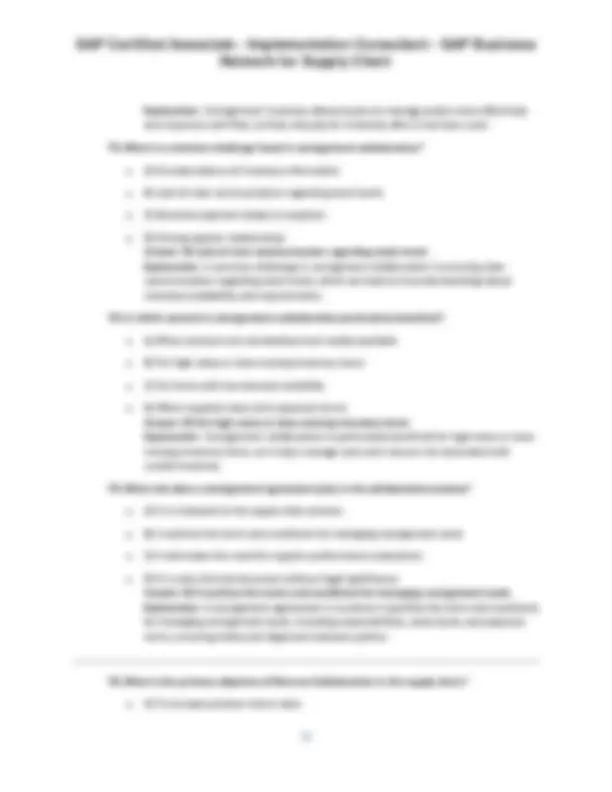
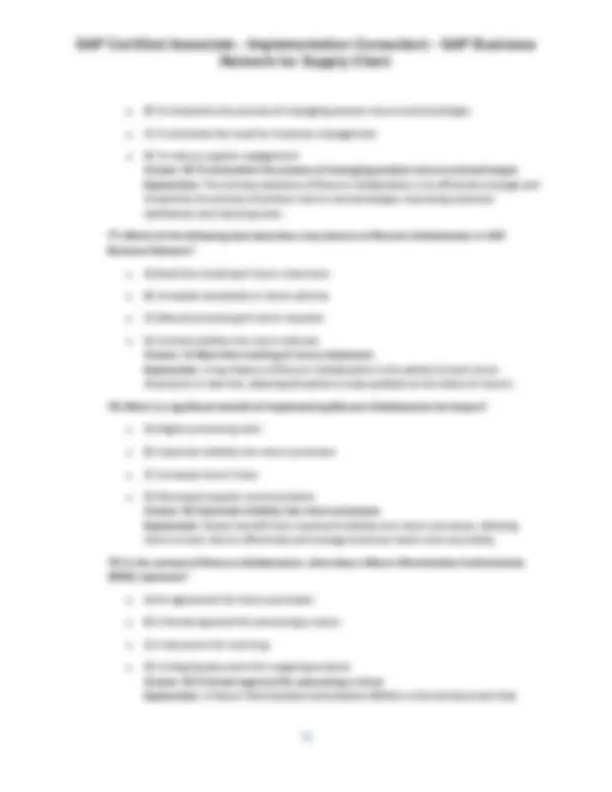
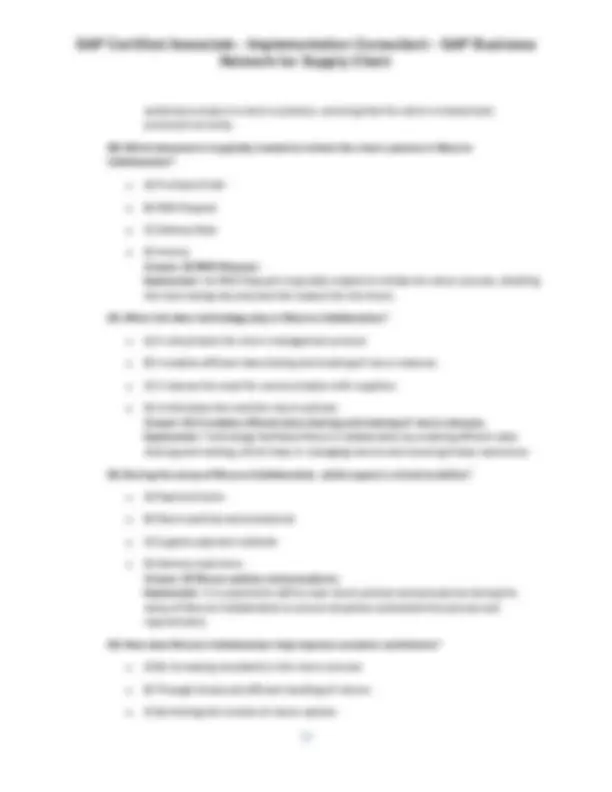
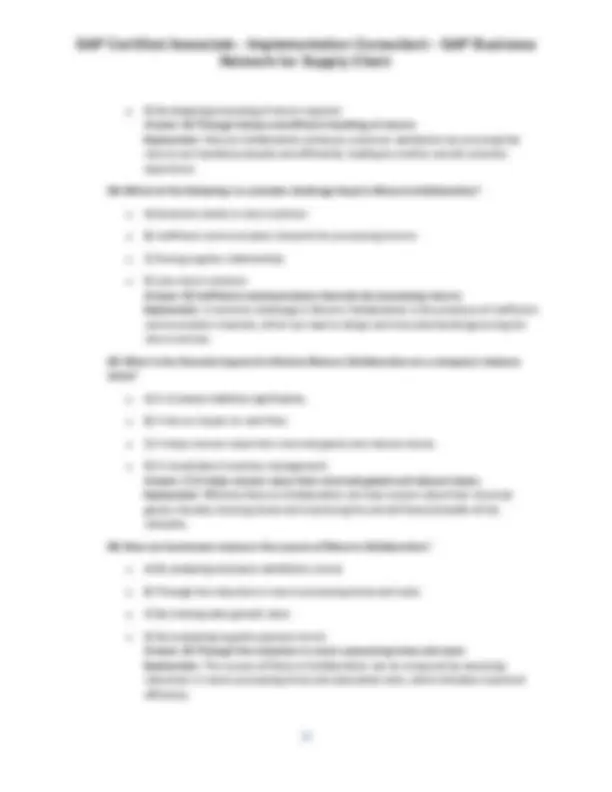
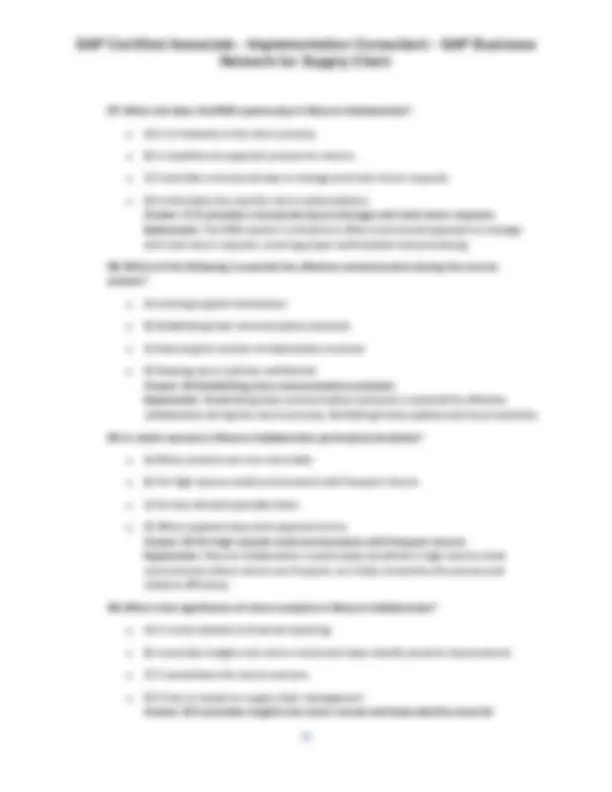
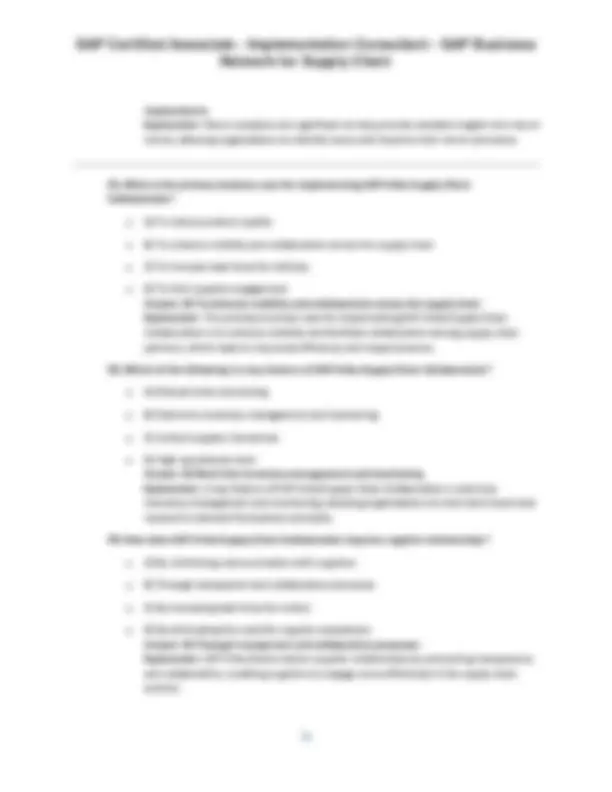
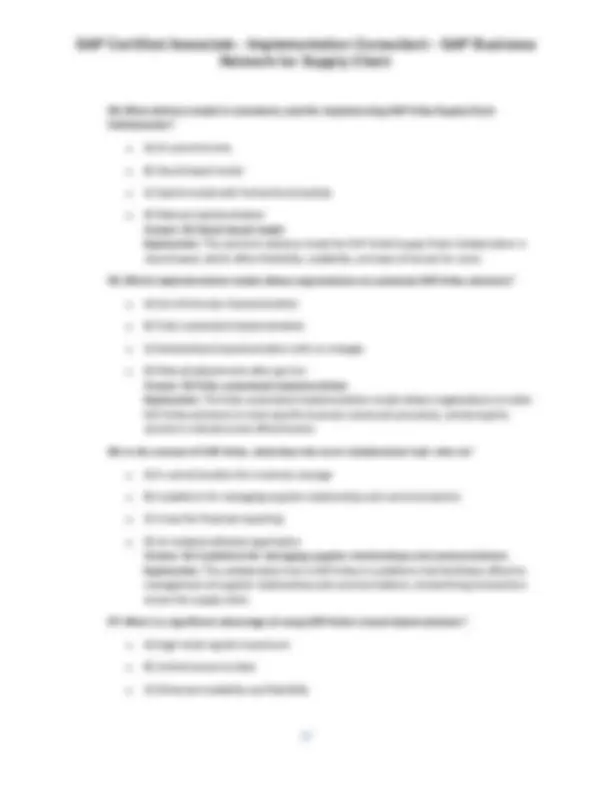
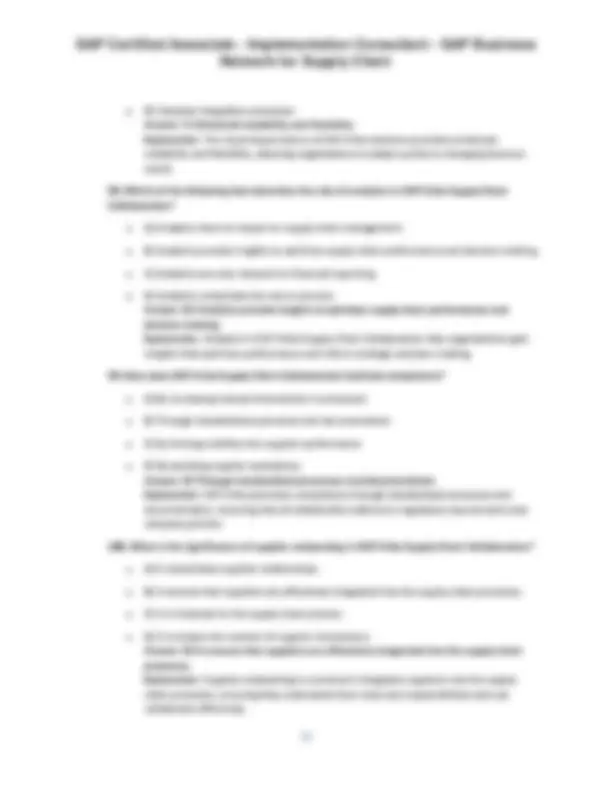
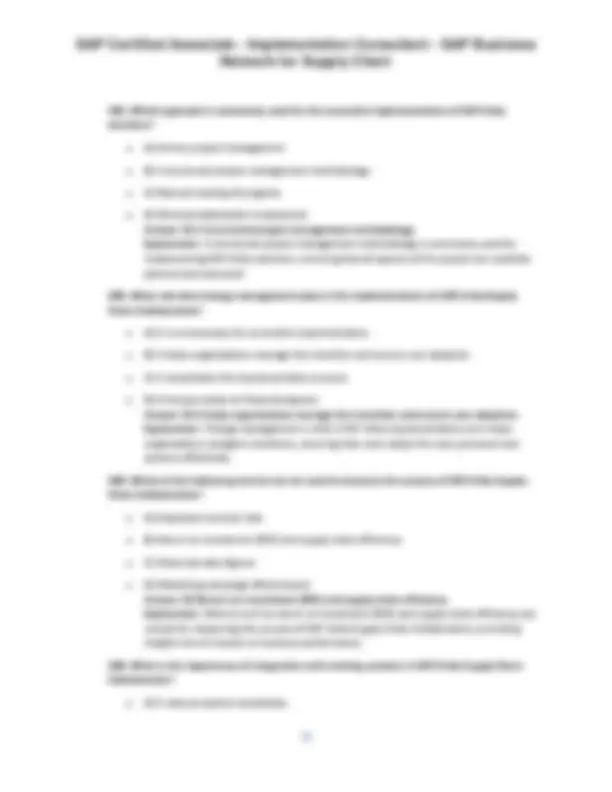
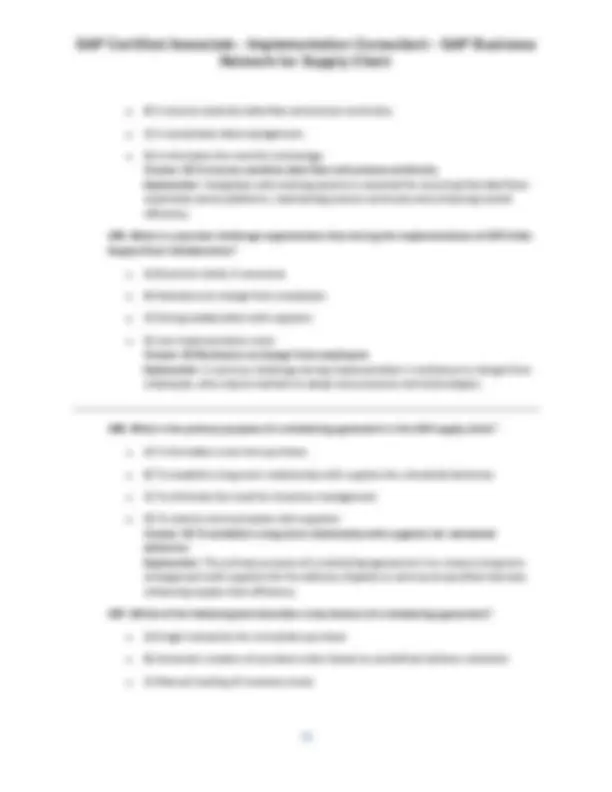
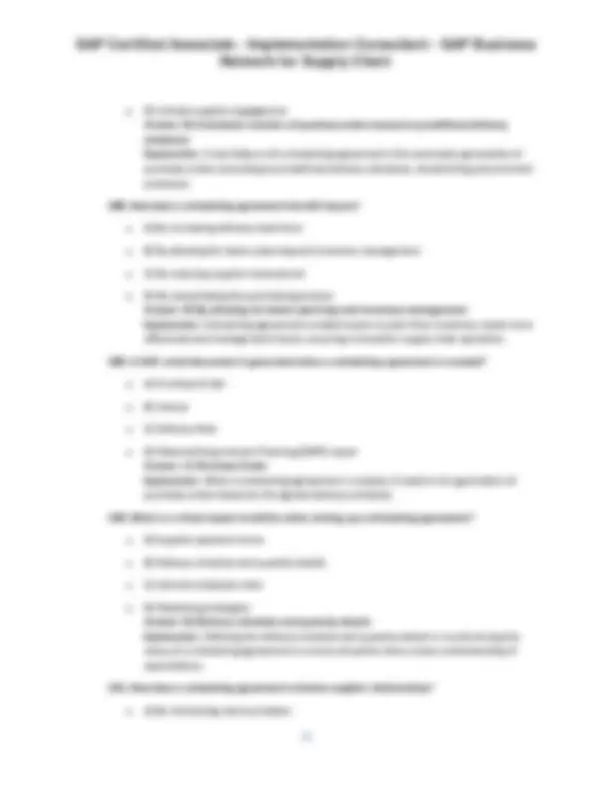

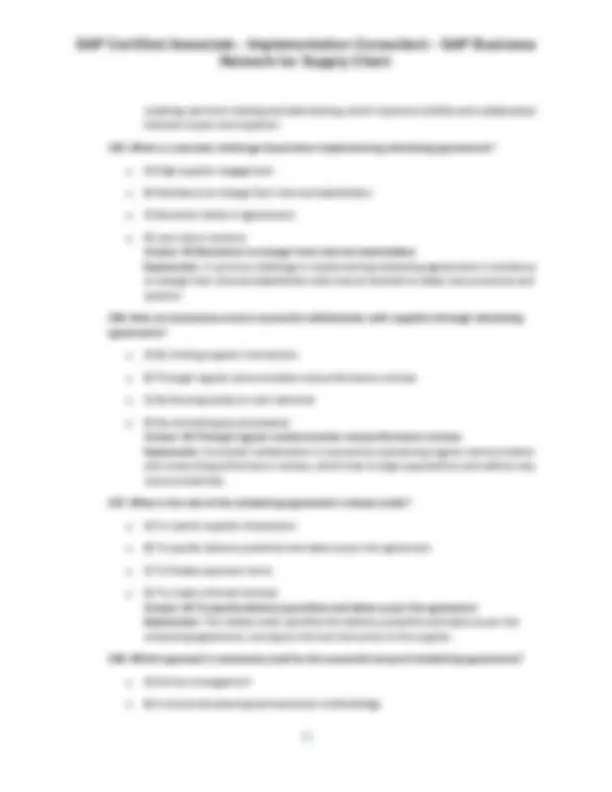
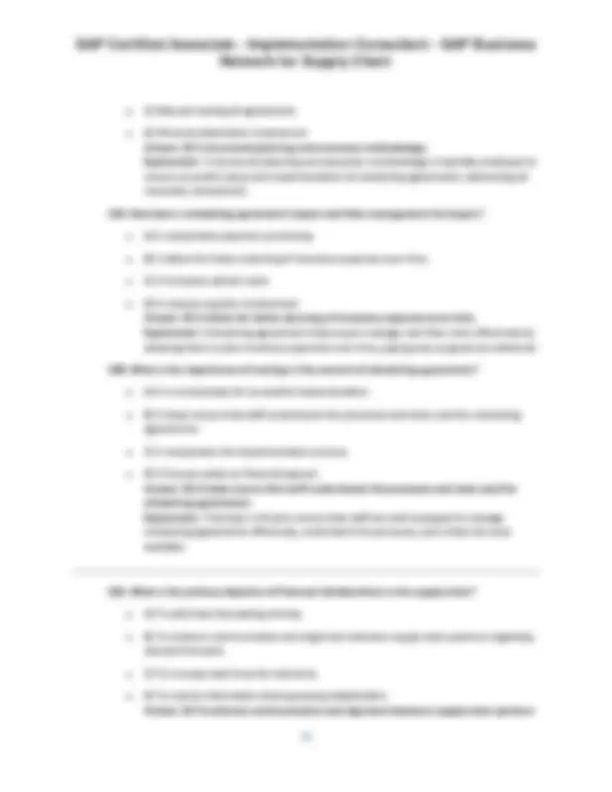
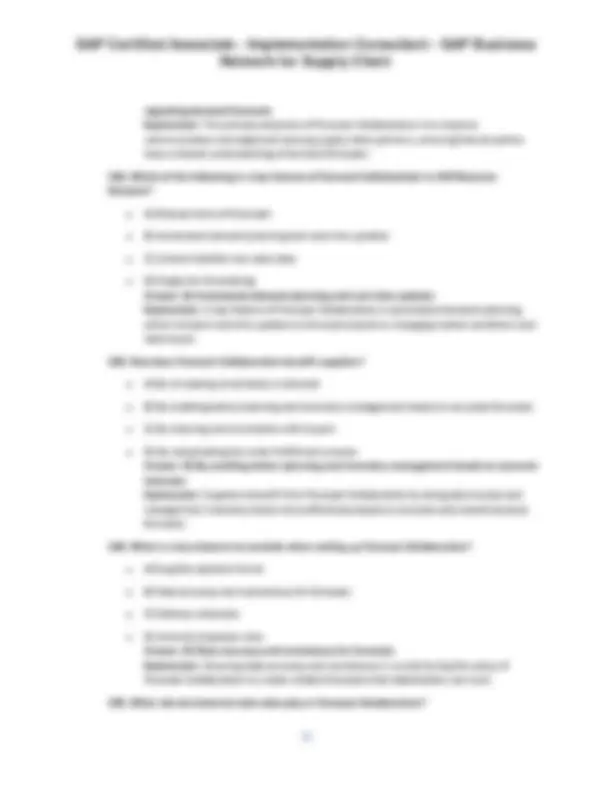
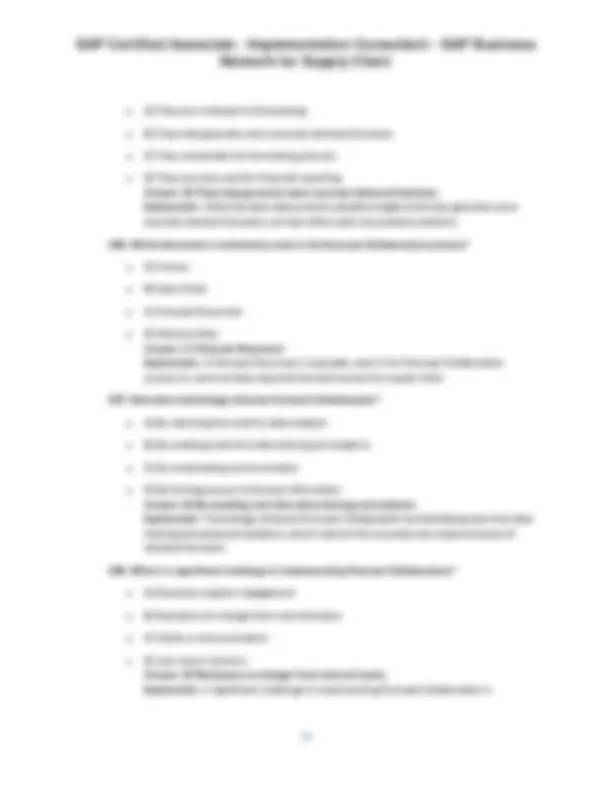
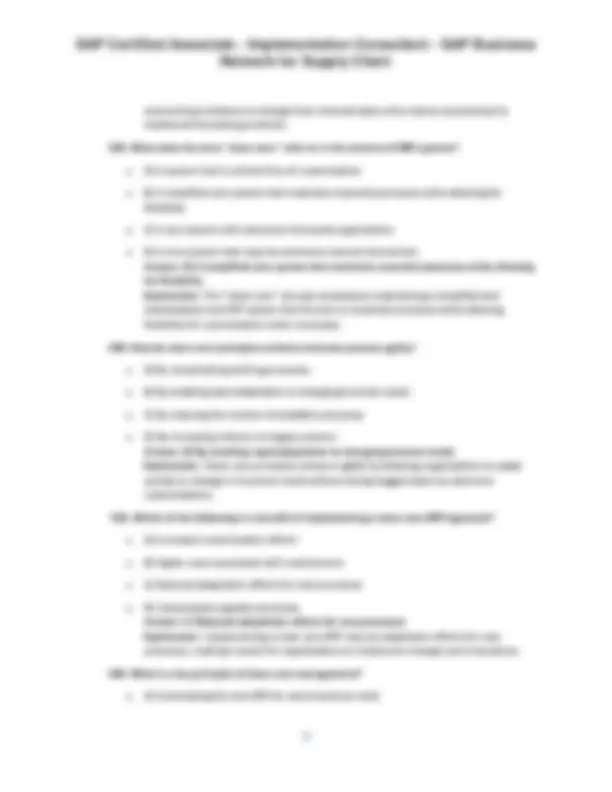
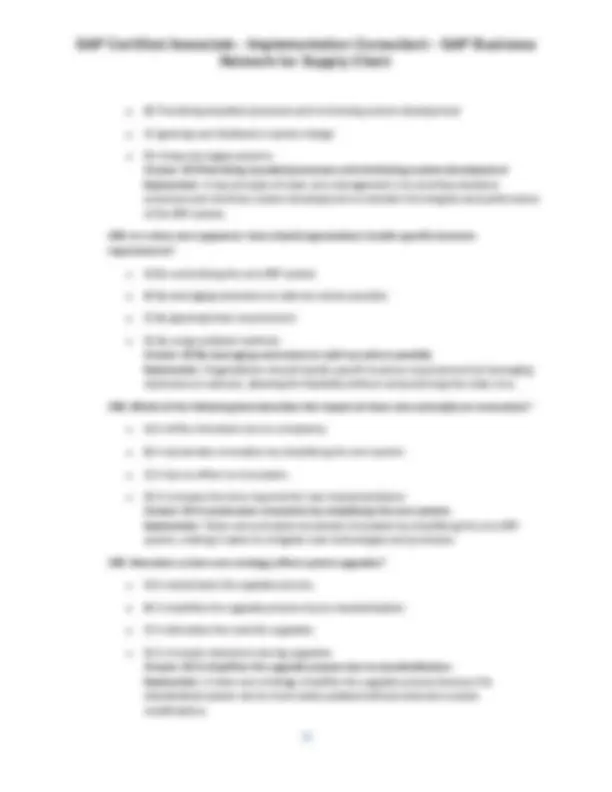
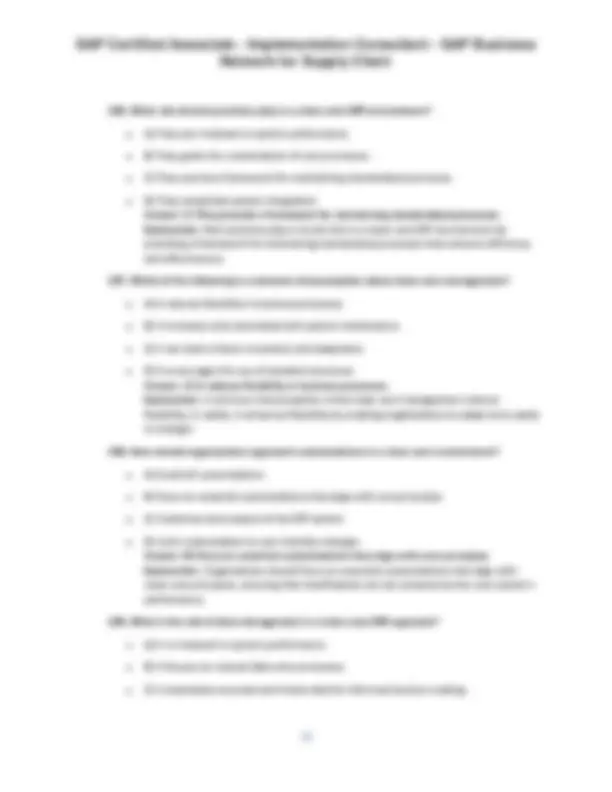
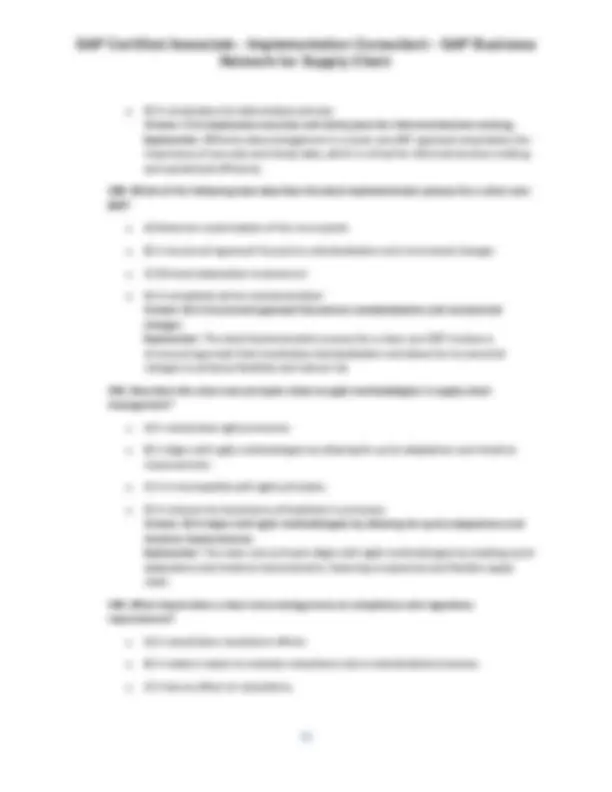
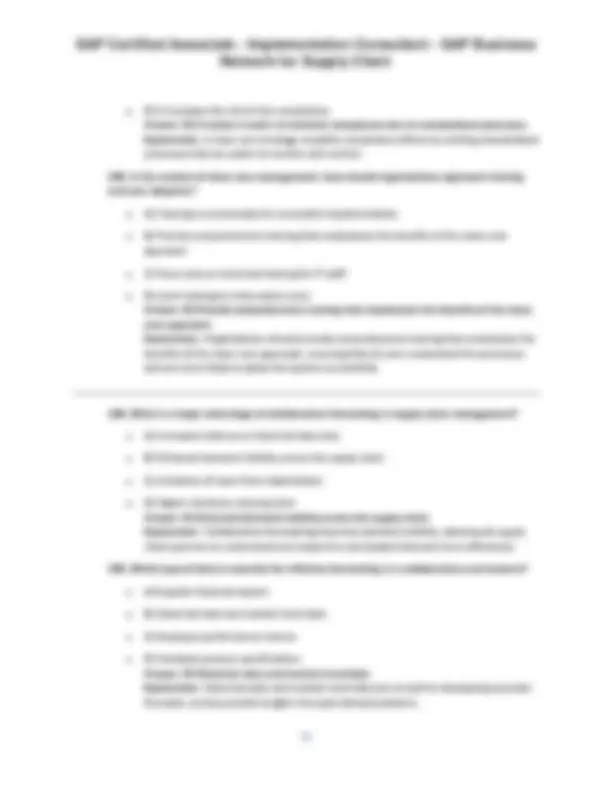
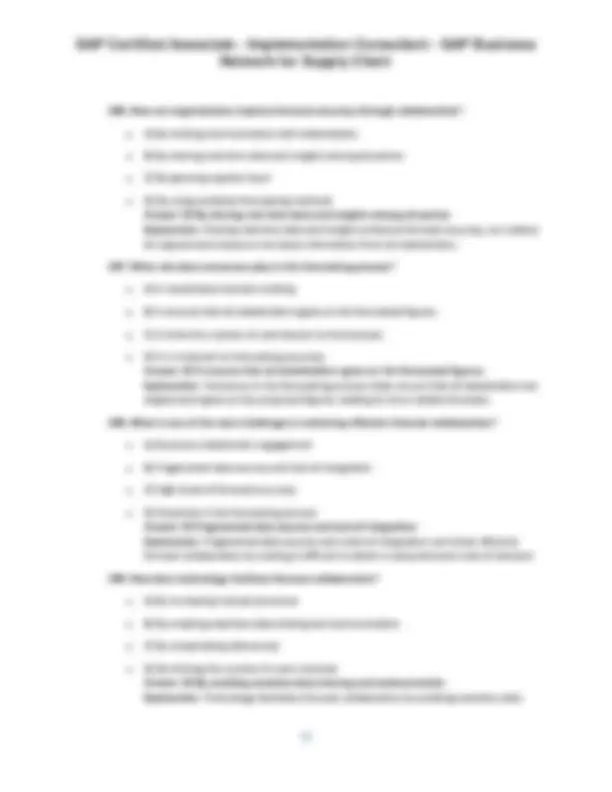
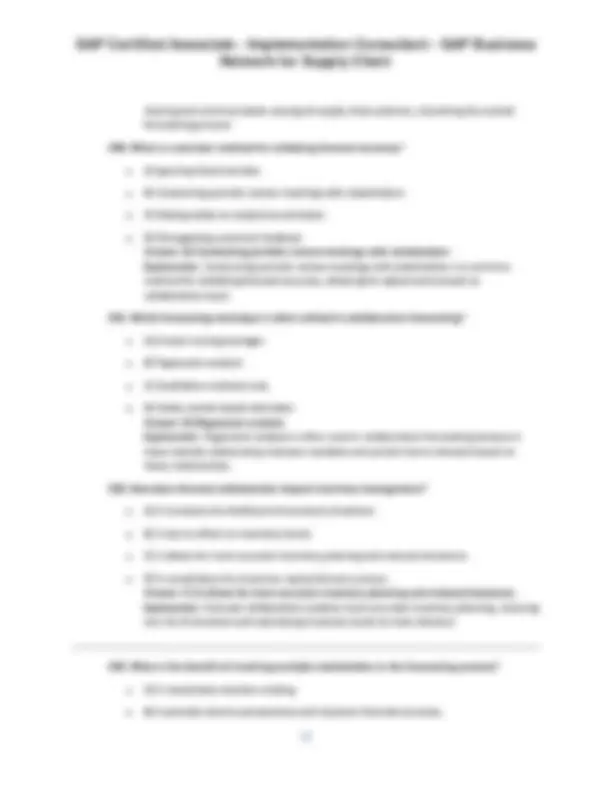
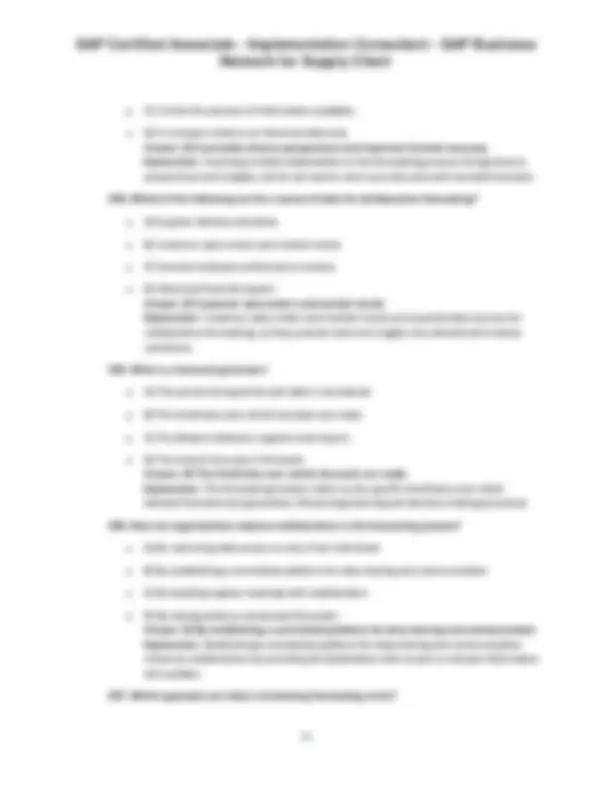

Study with the several resources on Docsity
Earn points by helping other students or get them with a premium plan
Prepare for your exams
Study with the several resources on Docsity
Earn points to download
Earn points by helping other students or get them with a premium plan
Community
Ask the community for help and clear up your study doubts
Discover the best universities in your country according to Docsity users
Free resources
Download our free guides on studying techniques, anxiety management strategies, and thesis advice from Docsity tutors
The business case for implementing supplier managed inventory (smi) and the key features and benefits of this approach. It explains how smi can enhance supplier quality management, improve inventory turnover and reduce carrying costs, and enable automated order generation based on predefined inventory thresholds. The document also covers the setup process for smi, the integration with supply chain management systems, and the measurement of smi success through inventory and usage reports. Additionally, it addresses the challenges of smi, such as ensuring clear communication regarding stock levels, and the benefits of consignment collaboration for high-value or slow-moving inventory items. Insights into the role of sap ariba in fostering better supplier relationships through transparent and collaborative processes, as well as the implementation models and cloud-based advantages of sap ariba solutions.
Typology: Quizzes
1 / 45
This page cannot be seen from the preview
Don't miss anything!
1. What is the primary goal of Quality Collaboration in SAP Business Network? o A) Increase sales revenue o B) Enhance supplier relationships o C) Improve product quality and compliance o D) Reduce manufacturing costs Answer: C) Improve product quality and compliance Explanation: Quality Collaboration aims to ensure that products meet quality standards and compliance requirements, thereby enhancing overall product quality. 2. Which of the following is a key feature of the Quality Collaboration module in SAP Business Network? o A) Real-time inventory tracking o B) Automated purchasing o C) Quality inspection notifications o D) Supplier payment management Answer: C) Quality inspection notifications Explanation: Quality inspection notifications are essential for alerting users about required quality checks, facilitating timely action on quality issues. 3. In the context of Quality Collaboration, what does the term 'quality assurance' refer to? o A) The process of ensuring product availability o B) The proactive measures to prevent defects and ensure quality o C) The strategy for pricing products o D) The method of auditing supplier performance Answer: B) The proactive measures to prevent defects and ensure quality Explanation: Quality assurance involves systematic processes to prevent defects and ensure that products meet specified quality standards. 4. What is the first step in setting up Quality Collaboration in SAP Business Network? o A) Define quality metrics o B) Integrate with supplier systems o C) Create a quality management plan o D) Identify stakeholders Answer: C) Create a quality management plan
Explanation: A quality management plan serves as a foundation for defining quality standards, roles, and responsibilities within the Quality Collaboration setup.
5. How does SAP Business Network facilitate communication between suppliers and manufacturers regarding quality issues? o A) Through manual emails o B) Via automated notifications and alerts o C) By scheduling regular meetings o D) Using external collaboration tools Answer: B) Via automated notifications and alerts Explanation: Automated notifications and alerts within SAP Business Network streamline communication, ensuring timely resolution of quality issues. 6. Which of the following metrics is commonly used to evaluate quality performance in Quality Collaboration? o A) Return on Investment (ROI) o B) First Pass Yield (FPY) o C) Average Handling Time (AHT) o D) Customer Satisfaction Score (CSAT) Answer: B) First Pass Yield (FPY) Explanation: First Pass Yield (FPY) measures the percentage of products manufactured correctly without rework, making it a critical metric for assessing quality performance. 7. What role do quality audits play in Quality Collaboration? o A) They are optional and not necessary o B) They verify compliance with quality standards and processes o C) They only evaluate supplier performance o D) They focus solely on financial aspects Answer: B) They verify compliance with quality standards and processes Explanation: Quality audits assess adherence to established quality standards and processes, ensuring that both suppliers and manufacturers maintain quality requirements. 8. What is the benefit of integrating Quality Collaboration with supplier performance management? o A) It complicates supplier interactions
12. How can businesses ensure continuous improvement in their quality processes? o A) By maintaining static processes o B) By regularly reviewing and analyzing quality data o C) By ignoring supplier feedback o D) By solely focusing on cost reduction Answer: B) By regularly reviewing and analyzing quality data Explanation: Regular review and analysis of quality data facilitate continuous improvement by identifying trends and areas needing enhancement. 13. What is the significance of compliance in Quality Collaboration? o A) Compliance is not critical to quality management. o B) It ensures that products meet legal and regulatory requirements. o C) It only applies to financial transactions. o D) Compliance is irrelevant for suppliers. Answer: B) It ensures that products meet legal and regulatory requirements. Explanation: Compliance is vital in Quality Collaboration as it guarantees that products adhere to necessary legal and regulatory standards. 14. Which of the following best describes the setup process for Quality Collaboration? o A) One-time configuration with no future adjustments o B) An ongoing process that adapts to changing needs o C) A rigid framework that cannot be modified o D) A simple installation with no further actions required Answer: B) An ongoing process that adapts to changing needs Explanation: The setup process for Quality Collaboration is dynamic, requiring continuous adjustments to meet evolving quality standards and market demands. 15. What tool can be utilized to track and resolve quality issues effectively in SAP Business Network? o A) Supplier Evaluation Tool o B) Quality Issue Management Dashboard o C) Financial Reporting Tool o D) Inventory Optimization Tool Answer: B) Quality Issue Management Dashboard
Explanation: The Quality Issue Management Dashboard provides a centralized view of quality issues, allowing users to track, analyze, and resolve them efficiently.
16. What is the primary objective of Supplier Managed Inventory (SMI)? o A) Increase manufacturing lead times o B) Allow suppliers to manage stock levels based on demand o C) Eliminate the need for inventory tracking o D) Reduce supplier engagement Answer: B) Allow suppliers to manage stock levels based on demand Explanation: The primary objective of SMI is to empower suppliers to manage inventory levels based on real-time demand, thereby enhancing efficiency and reducing stockouts. 17. Which of the following best describes the business case for implementing Supplier Managed Inventory? o A) Increased supplier control over pricing o B) Enhanced inventory turnover and reduced carrying costs o C) Improved customer service levels through longer lead times o D) Decreased reliance on technology Answer: B) Enhanced inventory turnover and reduced carrying costs Explanation: Implementing SMI can lead to improved inventory turnover rates and lower carrying costs, as suppliers ensure optimal stock levels based on actual consumption. 18. Which feature is a key component of Supplier Managed Inventory in SAP Business Network? o A) Supplier payment processing o B) Automated order generation based on inventory levels o C) Manual inventory reconciliation o D) Customer relationship management Answer: B) Automated order generation based on inventory levels Explanation: A key feature of SMI is the automated generation of orders based on pre- defined inventory thresholds, allowing for timely replenishment without manual intervention. 19. What role does collaboration play in Supplier Managed Inventory?
Explanation: SMI enables suppliers to monitor and manage inventory proactively, which helps prevent stockouts and ensures products are available when needed.
23. What type of reporting is typically utilized in Supplier Managed Inventory systems? o A) Historical financial reporting o B) Real-time inventory and usage reports o C) Employee performance reporting o D) Sales forecasting reports Answer: B) Real-time inventory and usage reports Explanation: Real-time inventory and usage reports are essential in SMI systems, providing stakeholders with up-to-date information on inventory levels and consumption patterns. 24. Which of the following is a benefit of Supplier Managed Inventory for suppliers? o A) Increased risk of overstock o B) Reduced visibility into customer demand o C) Improved cash flow through efficient inventory turnover o D) Less engagement with customers Answer: C) Improved cash flow through efficient inventory turnover Explanation: Suppliers benefit from SMI by experiencing improved cash flow, as they can manage inventory more efficiently and reduce excess stock. 25. In SMI, who is primarily responsible for monitoring inventory levels? o A) The purchasing department of the buyer o B) The supplier o C) The finance department of the buyer o D) The customer Answer: B) The supplier Explanation: In Supplier Managed Inventory, the supplier takes responsibility for monitoring and managing inventory levels to meet the buyer’s demand. 26. What is the significance of establishing clear roles and responsibilities in SMI? o A) It reduces supplier engagement. o B) It prevents confusion and ensures accountability in inventory management. o C) It complicates the setup process.
o D) It is irrelevant to the SMI process. Answer: B) It prevents confusion and ensures accountability in inventory management. Explanation: Establishing clear roles and responsibilities is crucial in SMI to avoid confusion and ensure that both suppliers and buyers know their duties in managing inventory.
27. Which aspect of Supplier Managed Inventory helps in enhancing service levels? o A) Increased manual intervention in order processing o B) Accurate demand forecasting and timely replenishment o C) Higher lead times for order fulfillment o D) Reduced collaboration with suppliers Answer: B) Accurate demand forecasting and timely replenishment Explanation: Accurate demand forecasting and timely replenishment are fundamental to enhancing service levels, ensuring that products are available when customers need them. 28. What technology is often used to facilitate Supplier Managed Inventory processes? o A) Legacy systems with limited functionality o B) Cloud-based supply chain solutions o C) Manual tracking spreadsheets o D) Outdated inventory software Answer: B) Cloud-based supply chain solutions Explanation: Cloud-based supply chain solutions are commonly used in SMI to provide real-time data access and facilitate collaboration between suppliers and buyers. 29. How can businesses measure the success of Supplier Managed Inventory? o A) By evaluating employee satisfaction o B) Through the reduction of inventory holding costs and stockouts o C) By analyzing historical sales trends only o D) By monitoring supplier engagement levels Answer: B) Through the reduction of inventory holding costs and stockouts Explanation: The success of SMI can be measured by analyzing reductions in inventory holding costs and stockouts, indicating improved inventory management efficiency. 30. What is a common challenge when implementing Supplier Managed Inventory? o A) Excess inventory levels
o D) Elimination of inventory management Answer: B) Improved visibility into order status and requirements Explanation: Suppliers benefit from enhanced visibility into order statuses and requirements, allowing them to manage inventory and fulfill orders more efficiently.
34. During the setup of Purchase Order Collaboration, which aspect is critical to define initially? o A) Supplier payment terms o B) User roles and permissions o C) Transportation methods o D) Product pricing strategies Answer: B) User roles and permissions Explanation: Defining user roles and permissions is critical during the setup of Purchase Order Collaboration to ensure that users have appropriate access to manage orders and collaborate effectively. 35. How does Purchase Order Collaboration help in reducing order processing time? o A) By requiring more manual approvals o B) Through automated workflows and notifications o C) By limiting communication between buyers and suppliers o D) By increasing lead times Answer: B) Through automated workflows and notifications Explanation: Automated workflows and notifications streamline the order processing, significantly reducing the time required to manage purchase orders. 36. Which document is typically exchanged between buyers and suppliers in Purchase Order Collaboration? o A) Invoices o B) Purchase Orders (PO) o C) Shipping documents o D) Supplier evaluations Answer: B) Purchase Orders (PO) Explanation: The primary document exchanged in Purchase Order Collaboration is the Purchase Order (PO), which outlines the details of the order between buyers and suppliers. 37. What technology is commonly used to facilitate Purchase Order Collaboration?
o A) Legacy on-premise systems o B) Cloud-based collaboration platforms o C) Manual spreadsheets o D) Paper-based communication Answer: B) Cloud-based collaboration platforms Explanation: Cloud-based collaboration platforms enable real-time communication and information sharing, making them essential for effective Purchase Order Collaboration.
38. How can businesses measure the effectiveness of Purchase Order Collaboration? o A) By analyzing employee satisfaction scores o B) Through the reduction of order discrepancies and processing times o C) By tracking historical sales figures o D) By evaluating supplier payment terms Answer: B) Through the reduction of order discrepancies and processing times Explanation: The effectiveness of Purchase Order Collaboration can be measured by evaluating reductions in order discrepancies and improvements in processing times. 39. Which of the following is a common challenge in implementing Purchase Order Collaboration? o A) High levels of supplier engagement o B) Complexity of integrating with existing systems o C) Simplified communication processes o D) Over-reliance on automated systems Answer: B) Complexity of integrating with existing systems Explanation: A common challenge in implementing Purchase Order Collaboration is the complexity involved in integrating the collaboration tools with existing procurement and ERP systems. 40. What role do alerts and notifications play in Purchase Order Collaboration? o A) They increase manual workloads. o B) They help keep stakeholders informed about order statuses and changes. o C) They are irrelevant to the process. o D) They limit communication with suppliers. Answer: B) They help keep stakeholders informed about order statuses and changes. Explanation: Alerts and notifications are essential in Purchase Order Collaboration as
o C) Supplier payment terms o D) Product return rates Answer: B) Order cycle time Explanation: Order cycle time is a crucial metric used to evaluate the success of Purchase Order Collaboration, as it reflects the efficiency of the order processing system.
45. What aspect of Purchase Order Collaboration can help in addressing supply chain disruptions? o A) Manual tracking of orders o B) Real-time visibility into inventory and order status o C) Limiting supplier communication o D) Reducing the number of suppliers Answer: B) Real-time visibility into inventory and order status Explanation: Real-time visibility into inventory and order status enables quicker response times to supply chain disruptions, helping businesses adapt to changing circumstances. 46. What is the primary objective of subcontracting in the supply chain? o A) To increase internal production capacity o B) To leverage external expertise and resources o C) To reduce supplier engagement o D) To eliminate inventory management Answer: B) To leverage external expertise and resources Explanation: The primary objective of subcontracting is to utilize external suppliers' specialized skills, expertise, and resources to enhance production efficiency and reduce costs. 47. Which of the following best describes multi-tier supply chain management? o A) Managing only the immediate suppliers o B) Coordinating across multiple levels of suppliers to ensure efficiency o C) Limiting supplier interactions to contractual agreements o D) Focusing solely on internal processes Answer: B) Coordinating across multiple levels of suppliers to ensure efficiency Explanation: Multi-tier supply chain management involves coordinating and managing
relationships across various supplier levels to enhance overall efficiency and responsiveness.
48. What is a key feature of the subcontracting process in SAP Business Network? o A) Single-tier supplier visibility o B) Automated order fulfillment o C) Integration with purchasing and inventory management o D) Manual tracking of production schedules Answer: C) Integration with purchasing and inventory management Explanation: A key feature of the subcontracting process in SAP Business Network is its integration with purchasing and inventory management, allowing for seamless coordination of resources and materials. 49. During the setup of subcontracting, which aspect is critical to define? o A) Supplier payment terms o B) Product specifications and quality standards o C) Delivery lead times o D) Internal employee roles Answer: B) Product specifications and quality standards Explanation: Defining product specifications and quality standards is crucial during the setup of subcontracting to ensure that external suppliers meet the required quality levels. 50. How does subcontracting contribute to cost savings in the supply chain? o A) By increasing overhead costs o B) By allowing companies to focus on core competencies o C) By eliminating the need for supplier evaluations o D) By reducing the need for quality checks Answer: B) By allowing companies to focus on core competencies Explanation: Subcontracting enables companies to concentrate on their core competencies while outsourcing non-core activities, leading to cost savings and increased operational efficiency. 51. What is a common challenge faced in multi-tier supply chain management? o A) Simplified communication between suppliers o B) Limited visibility into the entire supply chain
comprehensive visibility into all supplier levels, allowing organizations to identify and address potential risks proactively.
55. What role does collaboration play in the subcontracting process? o A) It complicates communication with suppliers. o B) It is irrelevant to the process. o C) It fosters stronger relationships and aligns expectations between buyers and subcontractors. o D) It limits the number of suppliers involved. Answer: C) It fosters stronger relationships and aligns expectations between buyers and subcontractors. Explanation: Collaboration is essential in subcontracting as it helps build stronger relationships and aligns expectations, ensuring that both parties work towards common goals. 56. Which of the following metrics is commonly used to evaluate the effectiveness of subcontracting? o A) Employee turnover rate o B) Subcontractor performance metrics (e.g., delivery time, quality) o C) Sales growth rate o D) Marketing ROI Answer: B) Subcontractor performance metrics (e.g., delivery time, quality) Explanation: Subcontractor performance metrics, such as delivery time and product quality, are critical for evaluating the effectiveness of the subcontracting process and ensuring alignment with business goals. 57. What is a significant benefit of implementing multi-tier supply chain strategies? o A) Increased reliance on a single supplier o B) Enhanced flexibility and responsiveness to market changes o C) Higher inventory holding costs o D) Reduced supplier collaboration Answer: B) Enhanced flexibility and responsiveness to market changes Explanation: Multi-tier supply chain strategies improve flexibility and responsiveness, allowing organizations to adapt quickly to changes in demand or supply conditions. 58. In the context of subcontracting, what does the term 'reverse logistics' refer to? o A) The process of managing returns and defective products
o B) The forward flow of goods from suppliers to manufacturers o C) The financial transactions between buyers and subcontractors o D) The delivery of finished goods to customers Answer: A) The process of managing returns and defective products Explanation: Reverse logistics in subcontracting involves managing the return of defective products or materials back to suppliers for repair or replacement.
59. Which of the following is essential for successful subcontractor selection? o A) Historical sales data of the subcontractor o B) Supplier risk assessments and performance evaluations o C) The subcontractor's marketing strategy o D) Financial forecasts Answer: B) Supplier risk assessments and performance evaluations Explanation: Conducting supplier risk assessments and performance evaluations is essential for selecting subcontractors who can meet quality and delivery requirements. 60. How does the SAP Business Network facilitate subcontracting and multi-tier management? o A) By providing limited access to supplier information o B) Through real-time data sharing and collaborative platforms o C) By eliminating the need for technology in procurement o D) By focusing solely on internal supply chain processes Answer: B) Through real-time data sharing and collaborative platforms Explanation: The SAP Business Network enhances subcontracting and multi-tier management by enabling real-time data sharing and collaboration, allowing stakeholders to make informed decisions and respond to changes quickly. 61. What is the primary purpose of consignment collaboration in the supply chain? o A) To increase inventory holding costs o B) To allow suppliers to maintain ownership of inventory until it is consumed o C) To eliminate the need for supplier evaluations o D) To reduce communication between suppliers and buyers Answer: B) To allow suppliers to maintain ownership of inventory until it is consumed Explanation: The primary purpose of consignment collaboration is to enable suppliers to
o D) Delivery Note Answer: B) Consignment Stock Transfer Order Explanation: A Consignment Stock Transfer Order is generated to confirm the movement of consignment stock from the supplier to the buyer's facility.
66. What role does technology play in consignment collaboration? o A) It complicates the inventory management process. o B) It eliminates the need for communication. o C) It enables real-time data sharing and visibility into inventory levels. o D) It reduces the importance of supplier relationships. Answer: C) It enables real-time data sharing and visibility into inventory levels. Explanation: Technology facilitates consignment collaboration by enabling real-time data sharing, allowing both suppliers and buyers to have accurate visibility into inventory levels and consumption. 67. During the setup of consignment collaboration, which aspect is critical to define? o A) Delivery lead times o B) Payment terms o C) Consignment stock levels and thresholds o D) Marketing strategies Answer: C) Consignment stock levels and thresholds Explanation: It is crucial to define consignment stock levels and thresholds during the setup to ensure that both parties agree on when to replenish stock. 68. How does consignment collaboration help in reducing inventory costs for suppliers? o A) By increasing the number of stock locations o B) By allowing suppliers to reduce safety stock o C) By requiring more frequent audits o D) By eliminating supplier involvement Answer: B) By allowing suppliers to reduce safety stock Explanation: Consignment collaboration helps suppliers reduce safety stock since they can maintain ownership of the inventory until it is used, thus optimizing their inventory levels. 69. What is the significance of 'usage reporting' in consignment collaboration? o A) It has no impact on the process.
o B) It helps suppliers adjust their production schedules based on consumption data. o C) It complicates the invoicing process. o D) It is only relevant to buyers. Answer: B) It helps suppliers adjust their production schedules based on consumption data. Explanation: Usage reporting is significant as it provides suppliers with insights into consumption patterns, allowing them to plan production and inventory more effectively.
70. Which metric is commonly used to evaluate the effectiveness of consignment collaboration? o A) Total sales revenue o B) Inventory turnover ratio o C) Employee satisfaction scores o D) Supplier payment terms Answer: B) Inventory turnover ratio Explanation: The inventory turnover ratio is a key metric used to evaluate the effectiveness of consignment collaboration, as it reflects how efficiently inventory is being utilized. 71. How can consignment collaboration enhance customer satisfaction? o A) By increasing lead times for orders o B) Through improved product availability and reduced stockouts o C) By limiting supplier options o D) By reducing communication with suppliers Answer: B) Through improved product availability and reduced stockouts Explanation: Consignment collaboration enhances customer satisfaction by ensuring that products are readily available, thus reducing the likelihood of stockouts and improving service levels. 72. What is the primary financial impact of consignment inventory on a buyer’s balance sheet? o A) It increases liabilities. o B) It has no impact on cash flow. o C) It decreases assets until inventory is consumed. o D) It allows for better asset management and cash flow. Answer: D) It allows for better asset management and cash flow.