
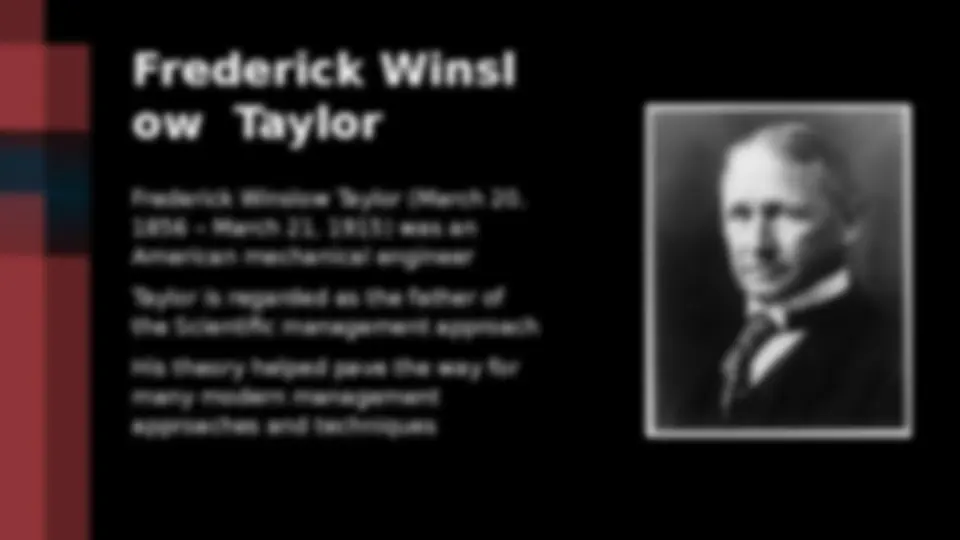
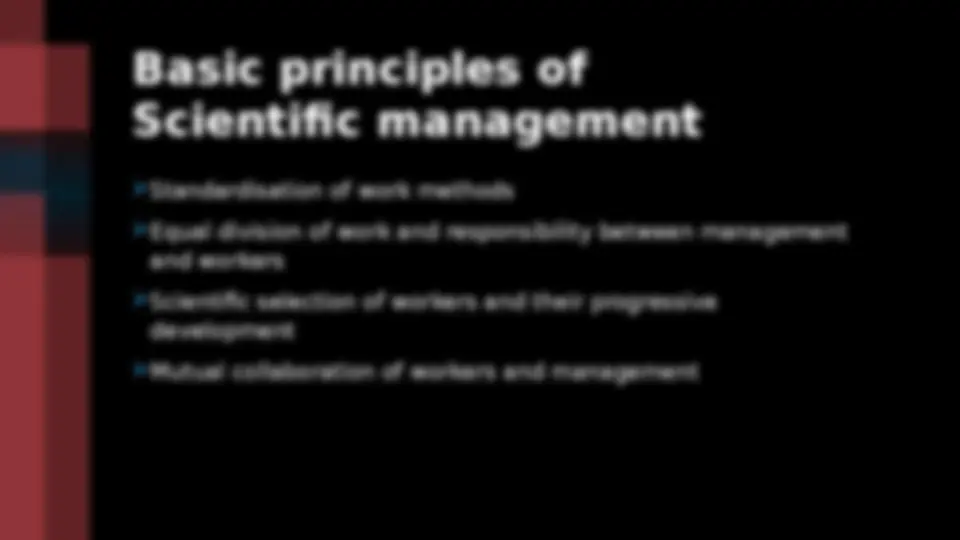
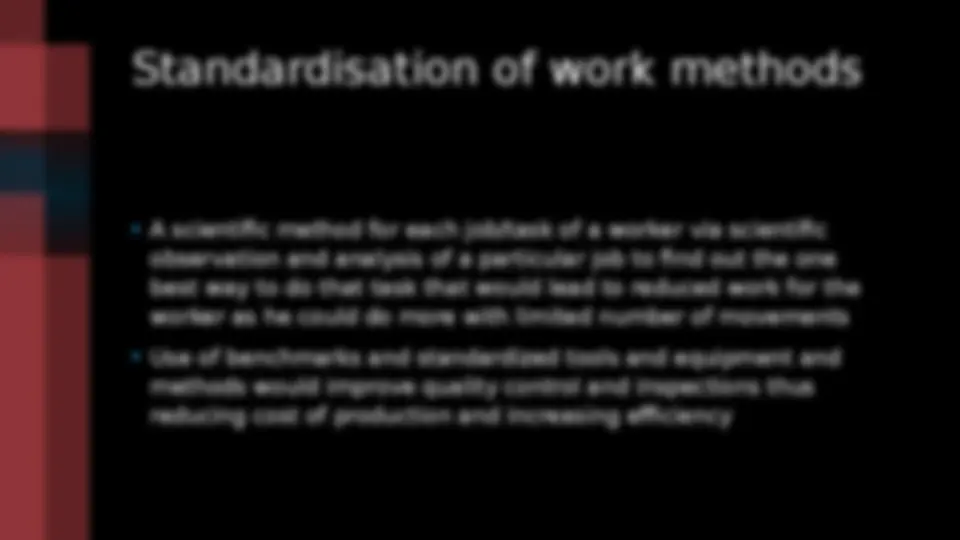
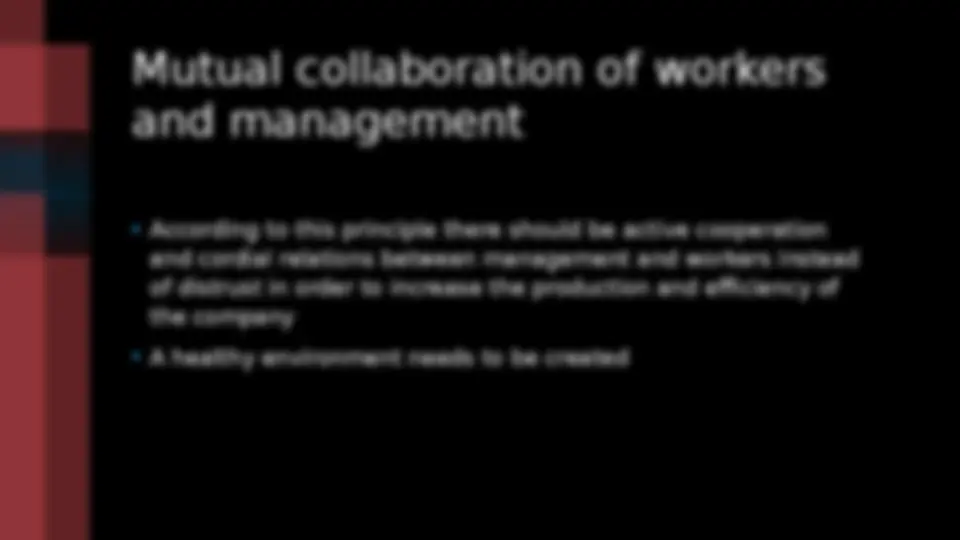
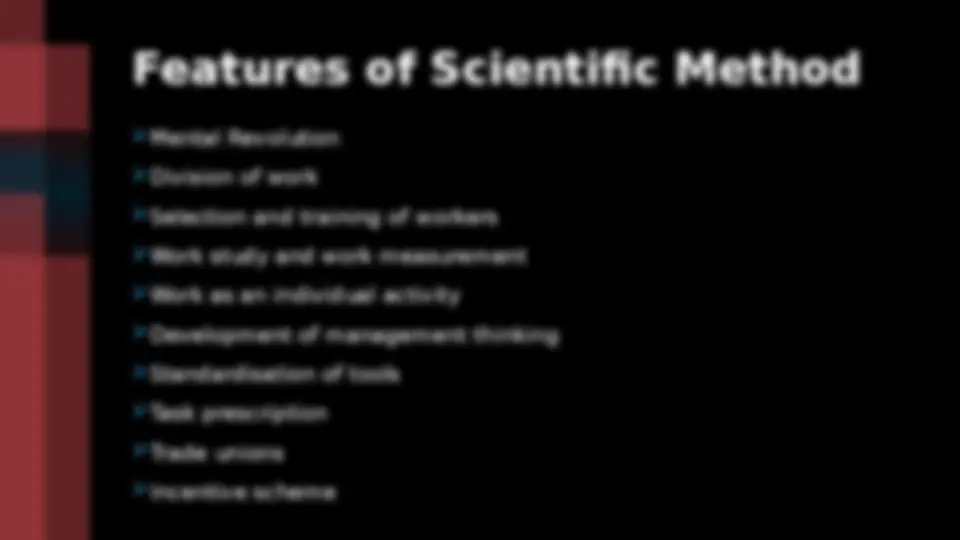
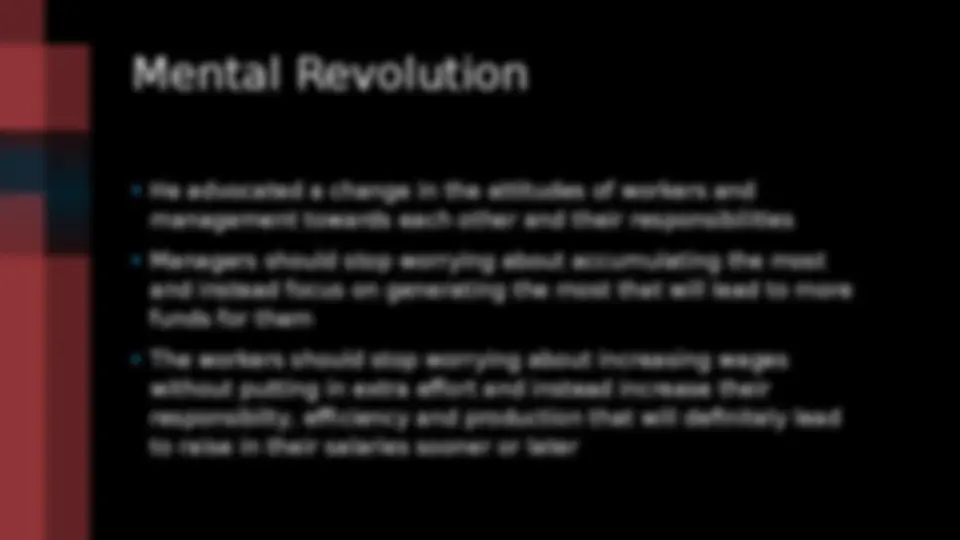
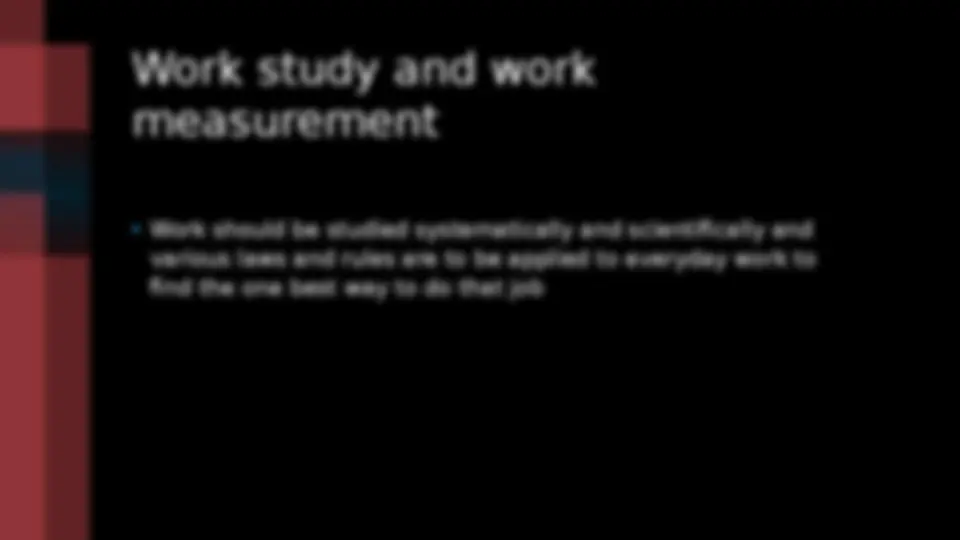
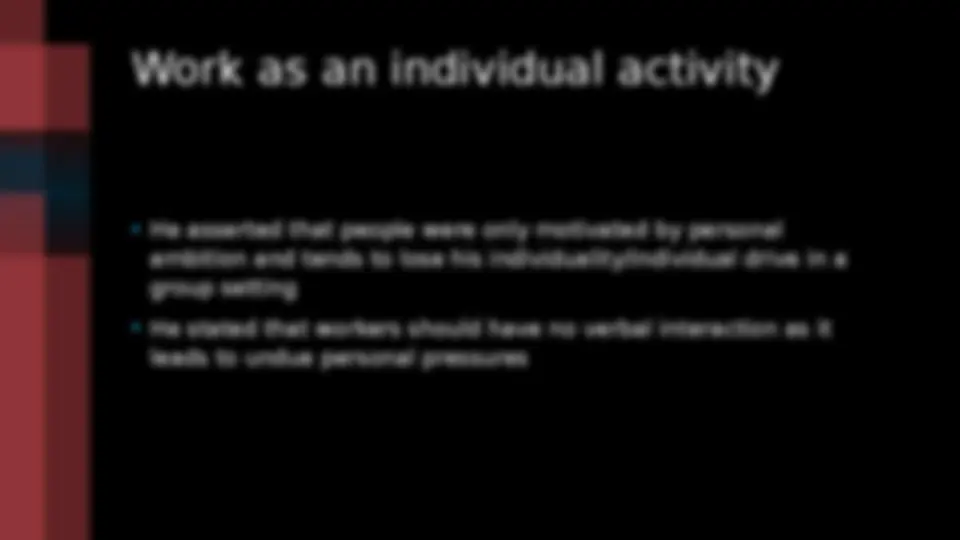
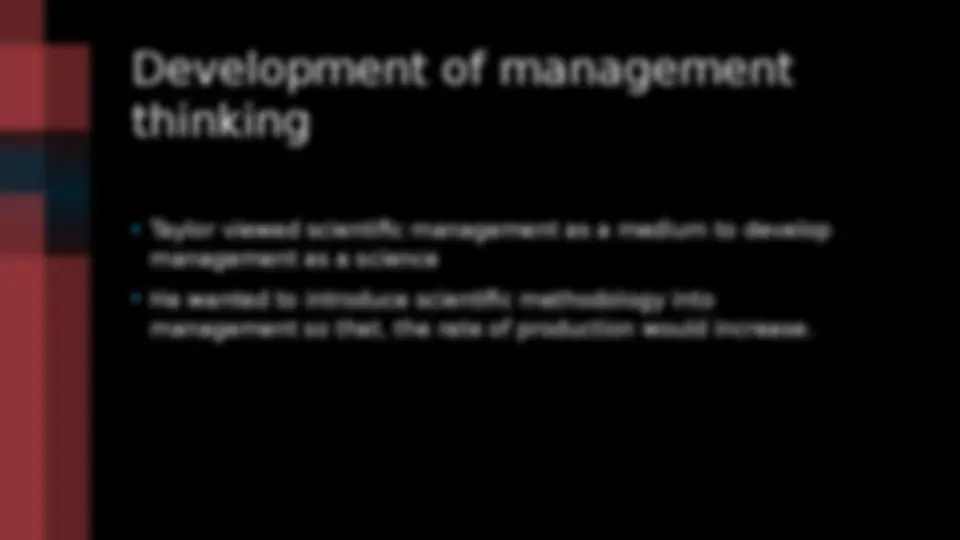
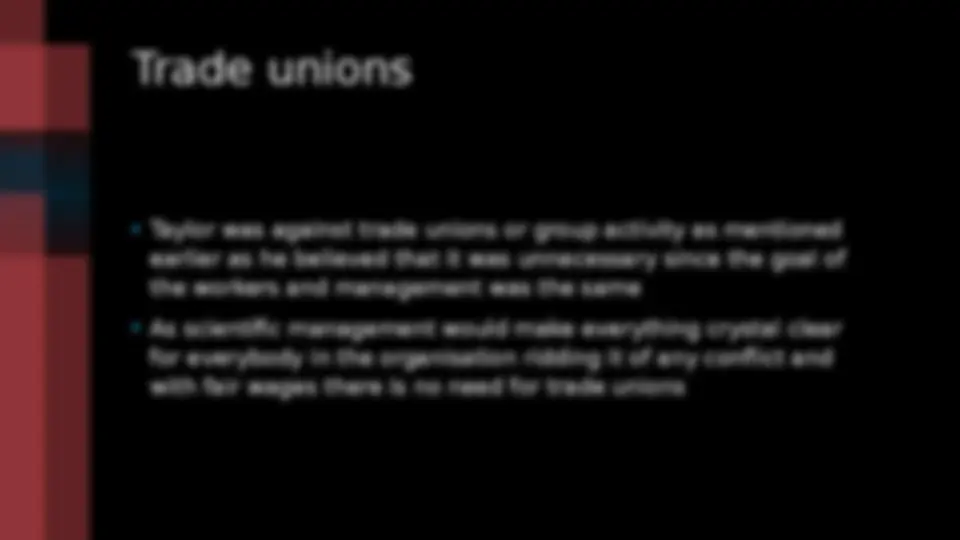
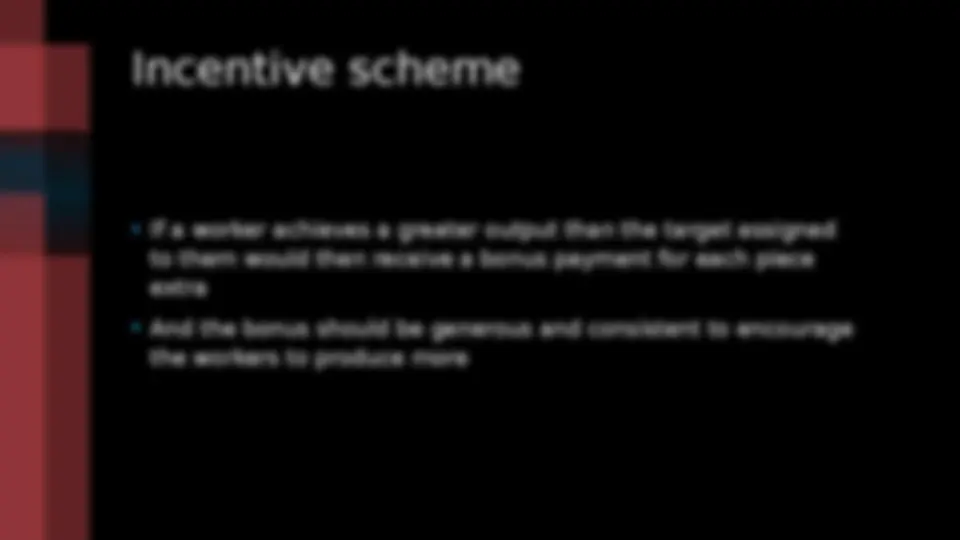

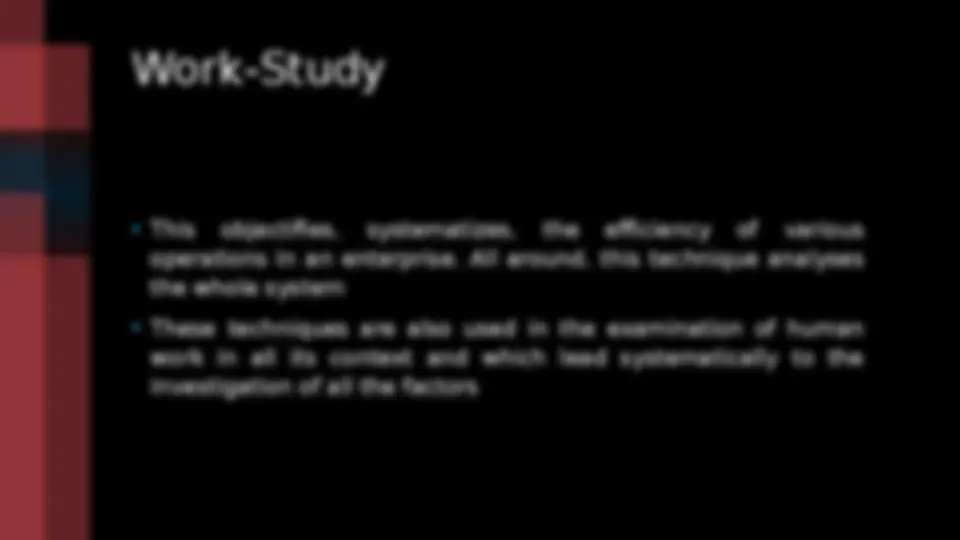
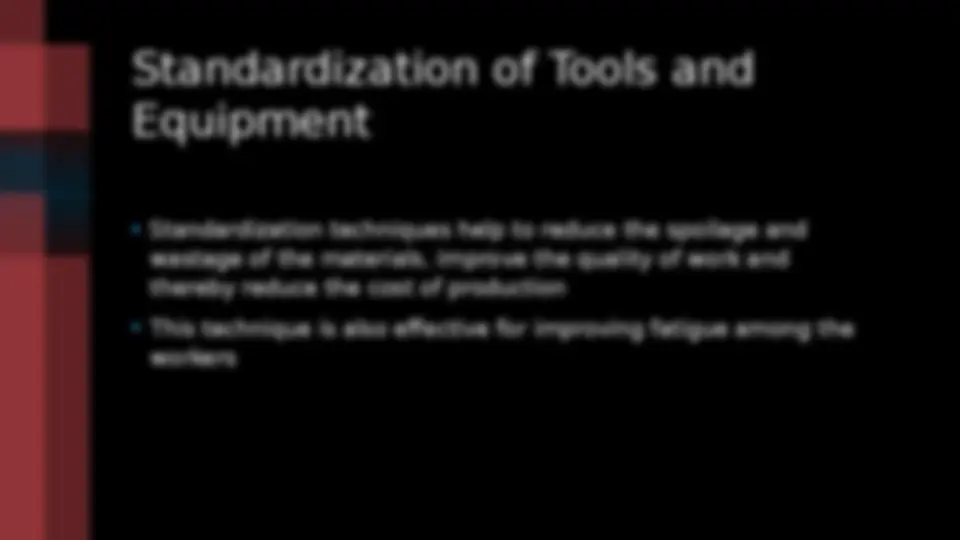
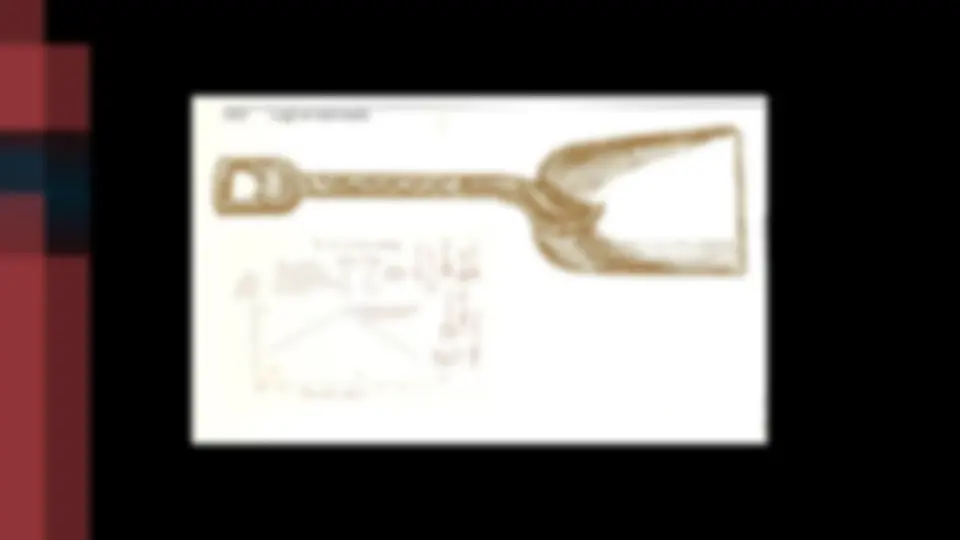
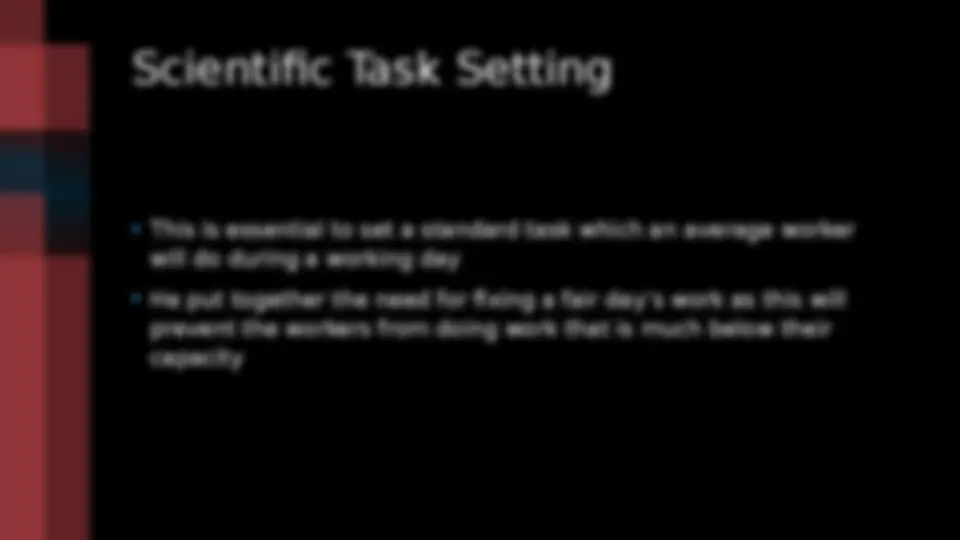
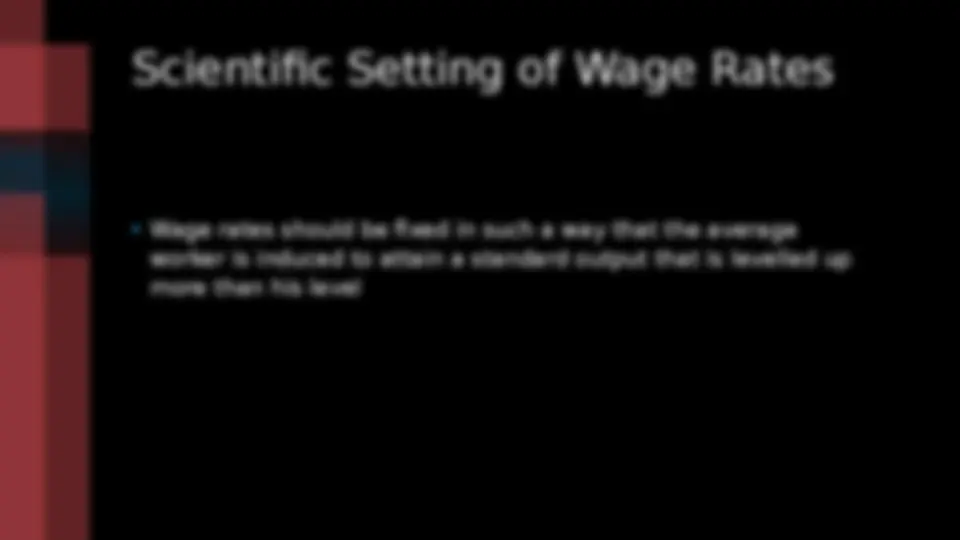
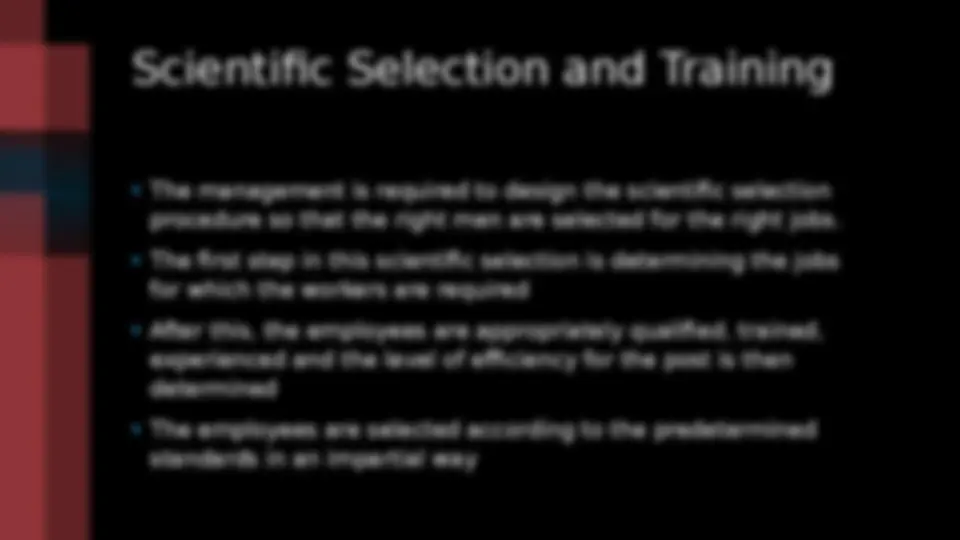
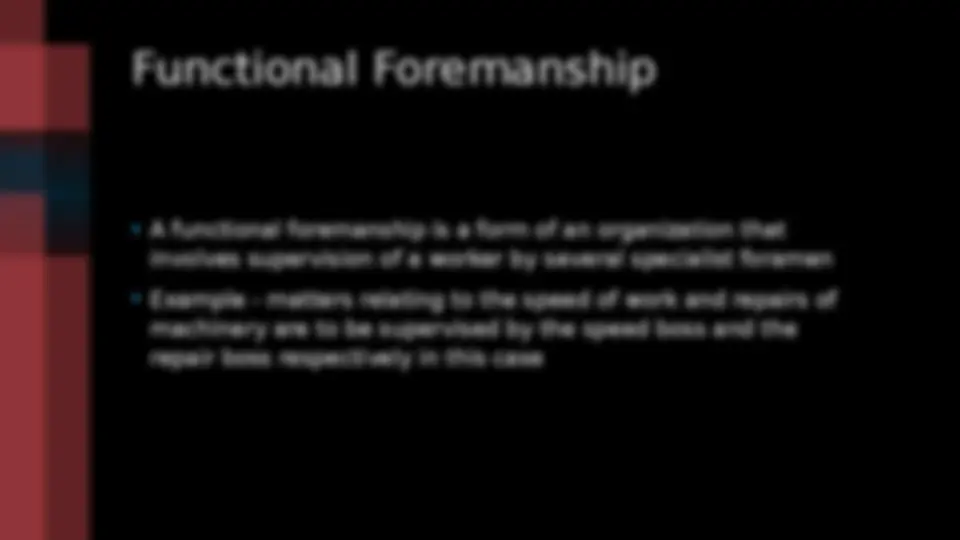
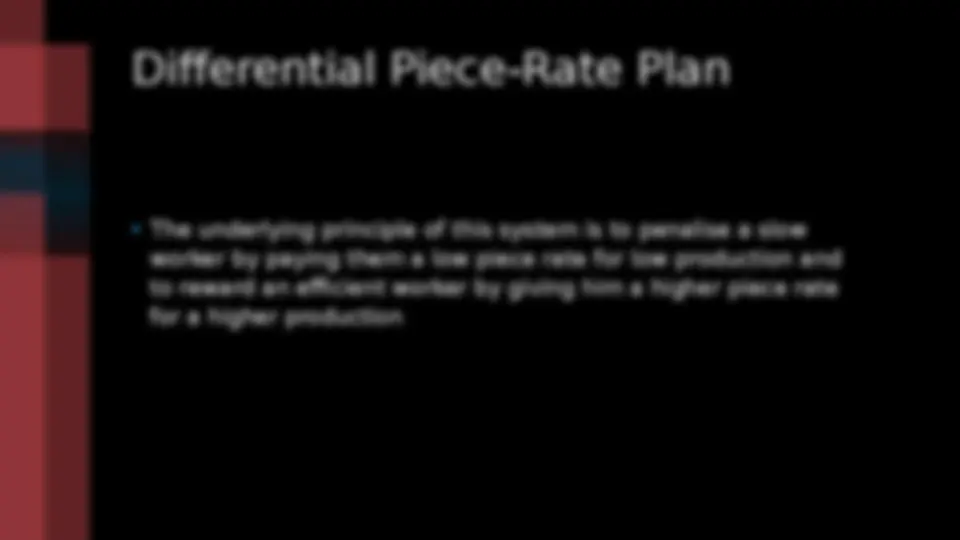
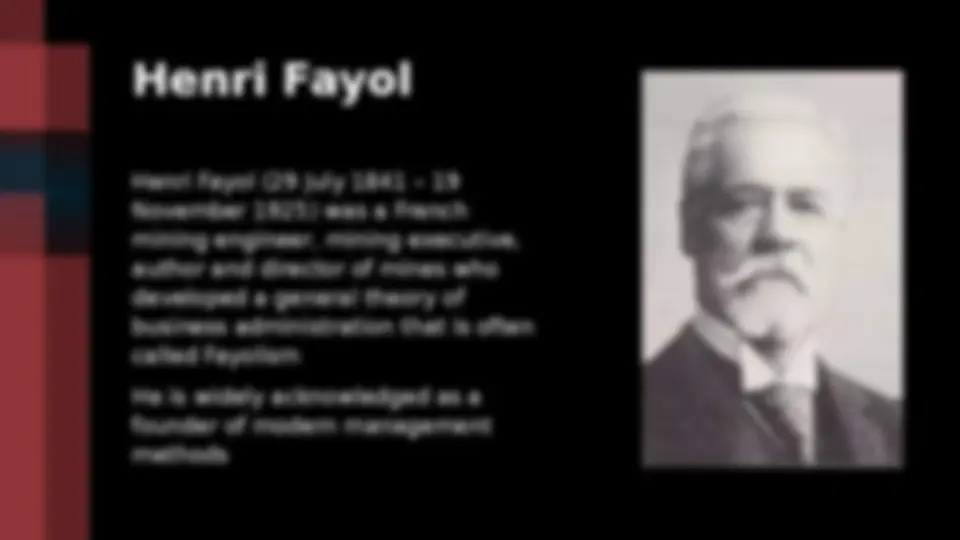
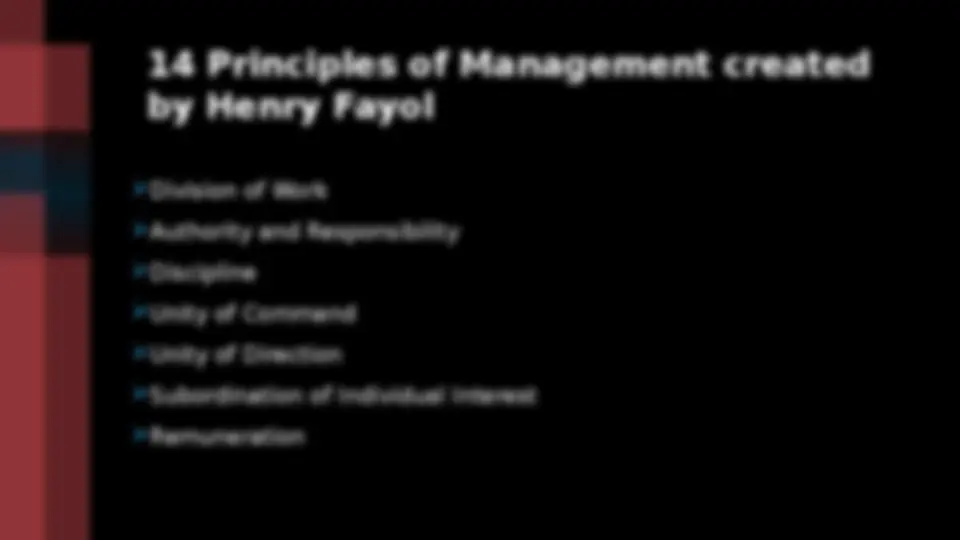

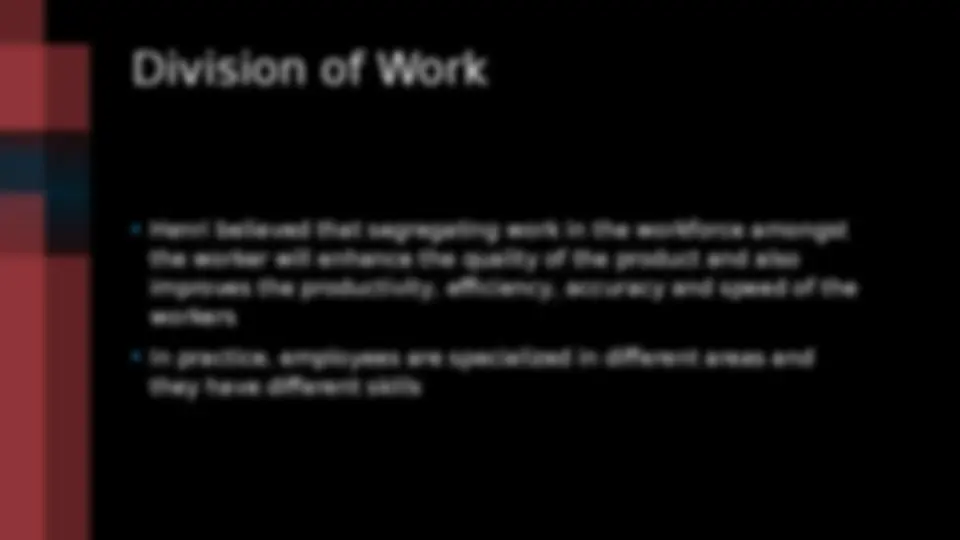
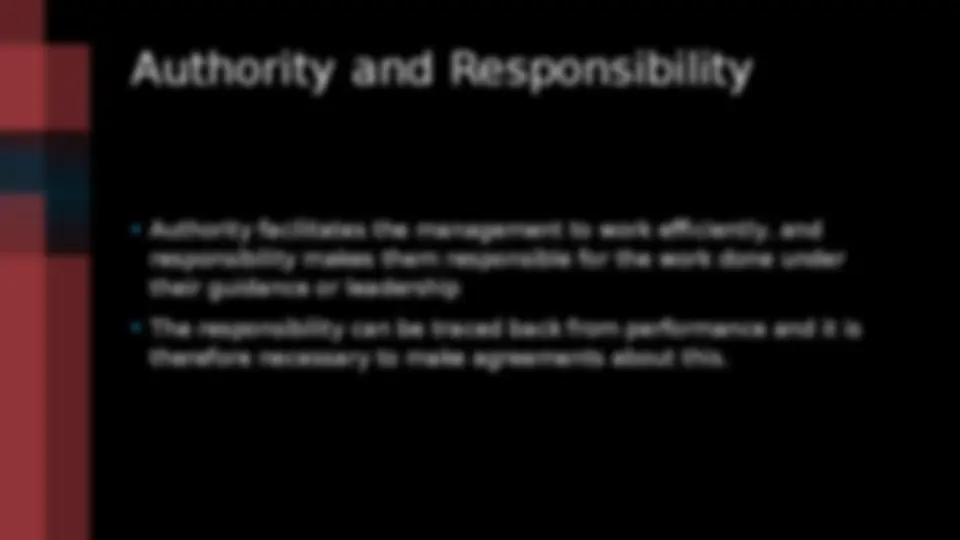
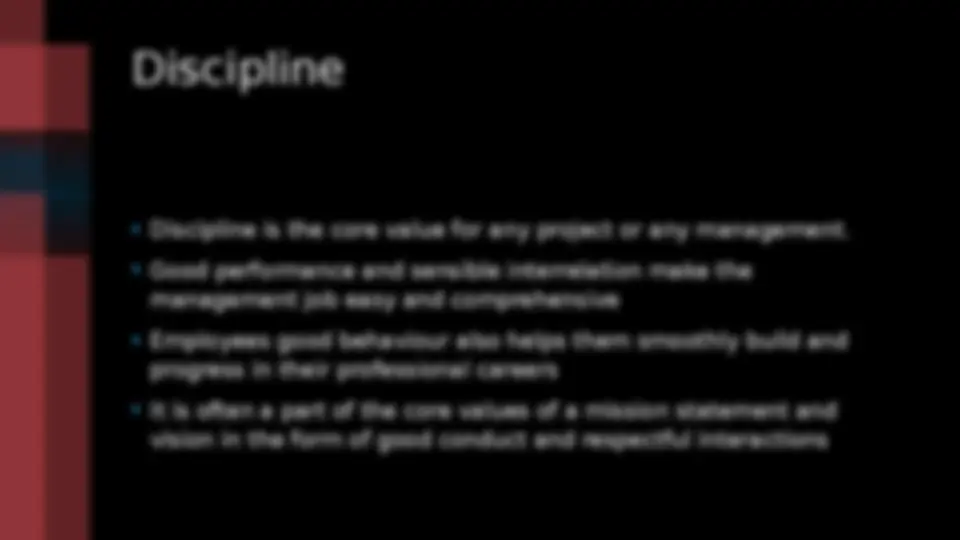
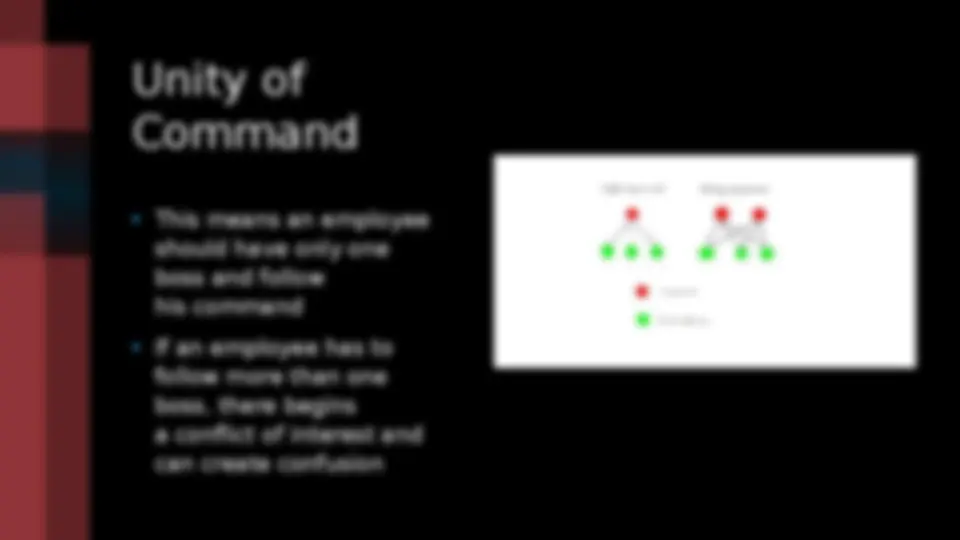
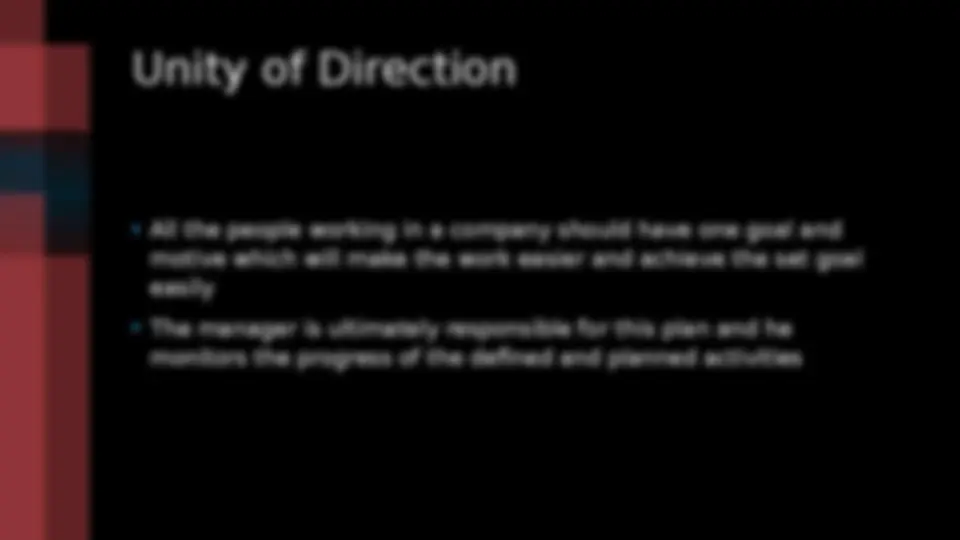

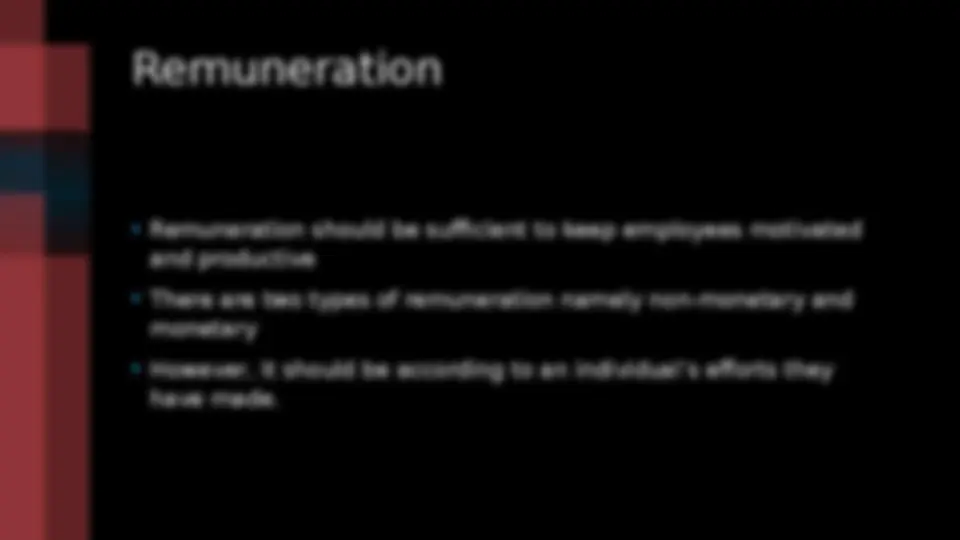

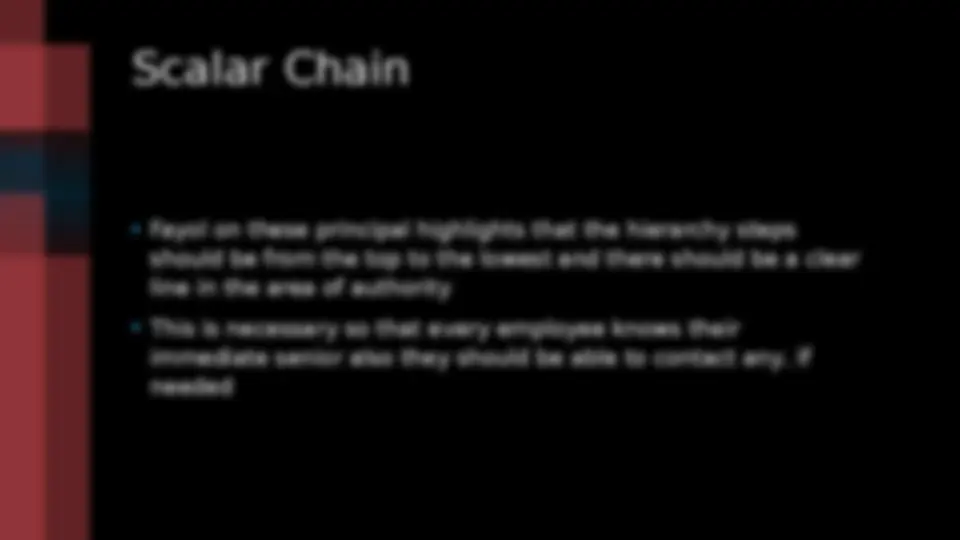
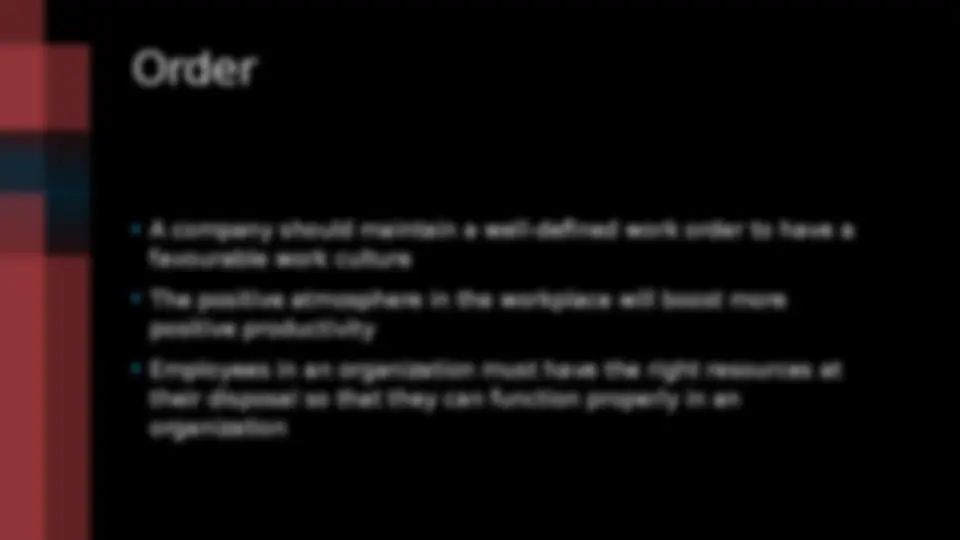
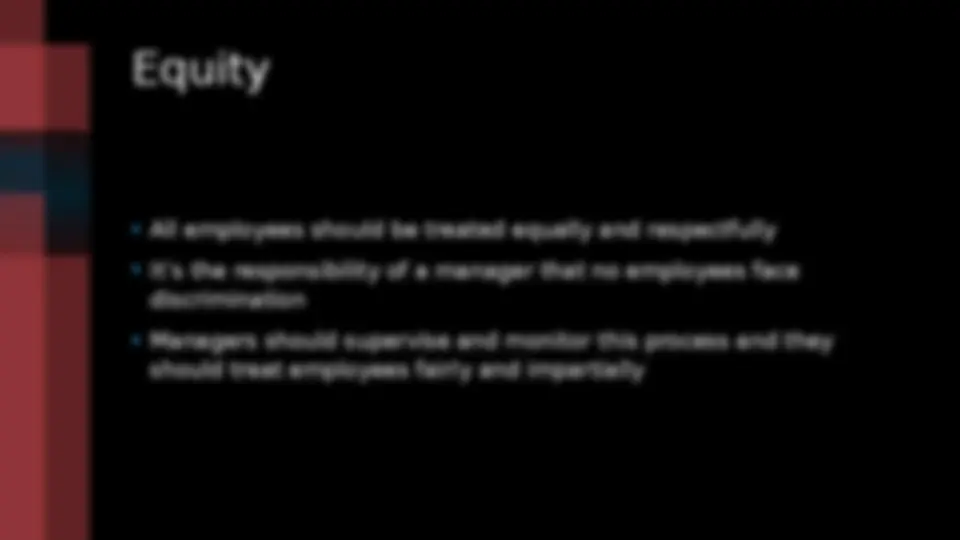
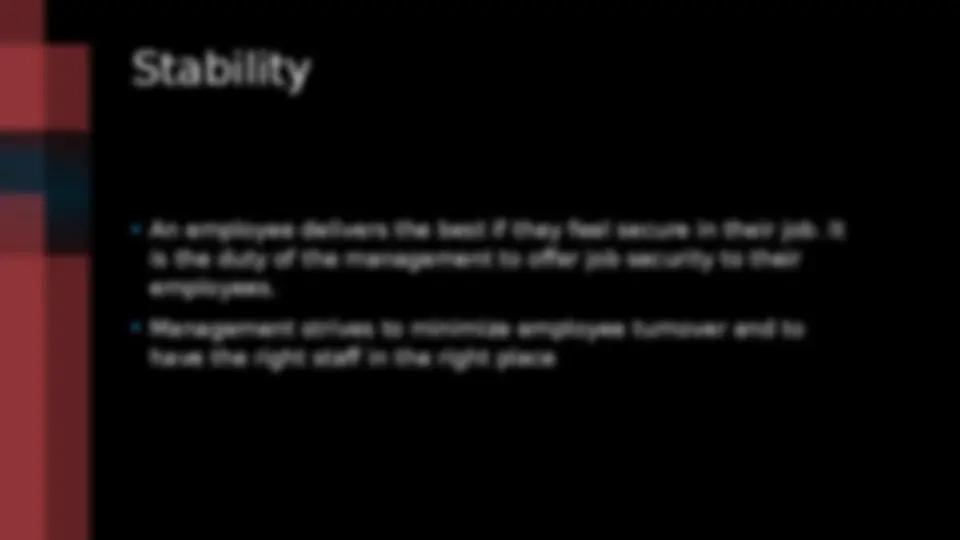
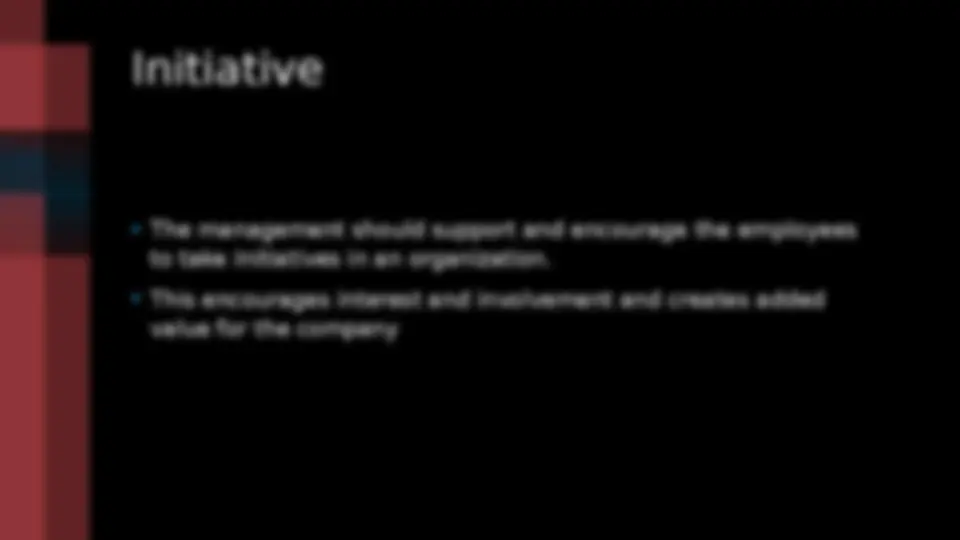
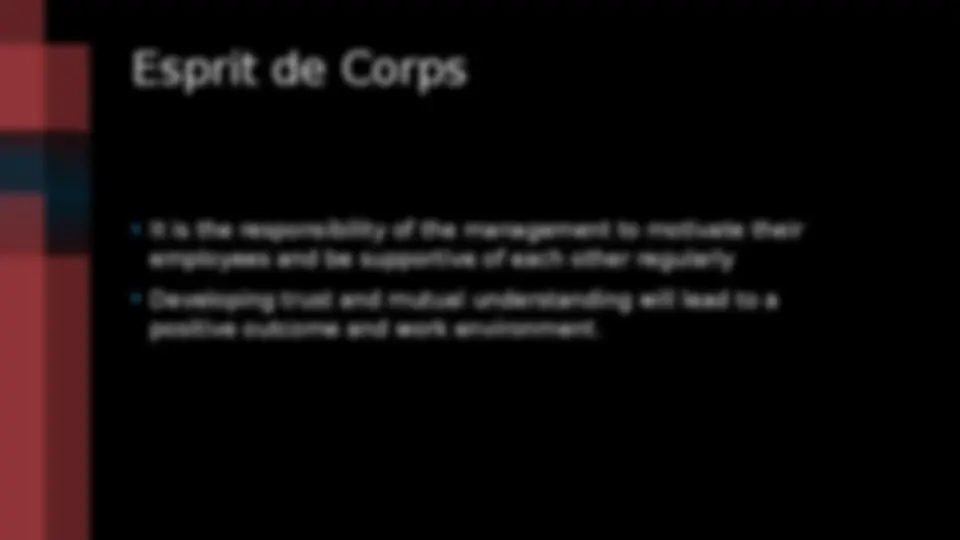
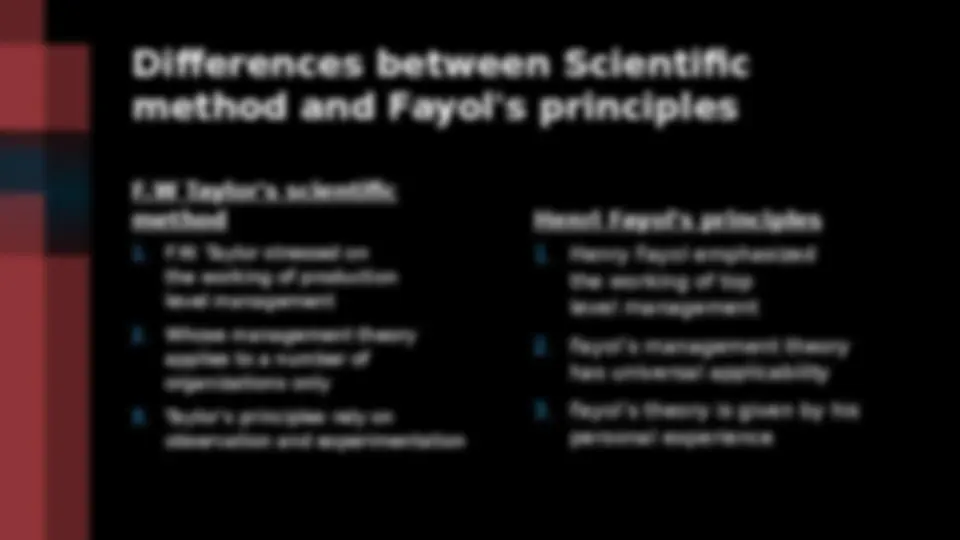
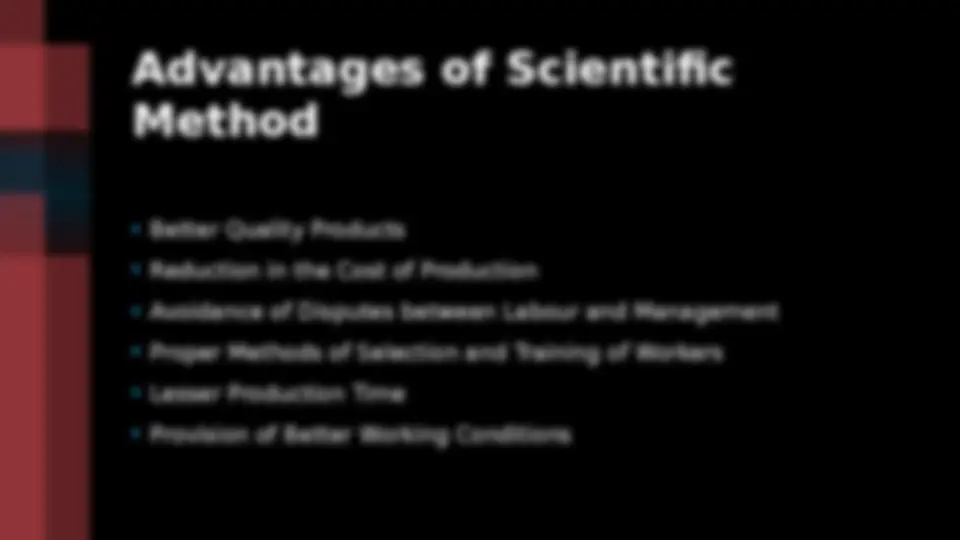
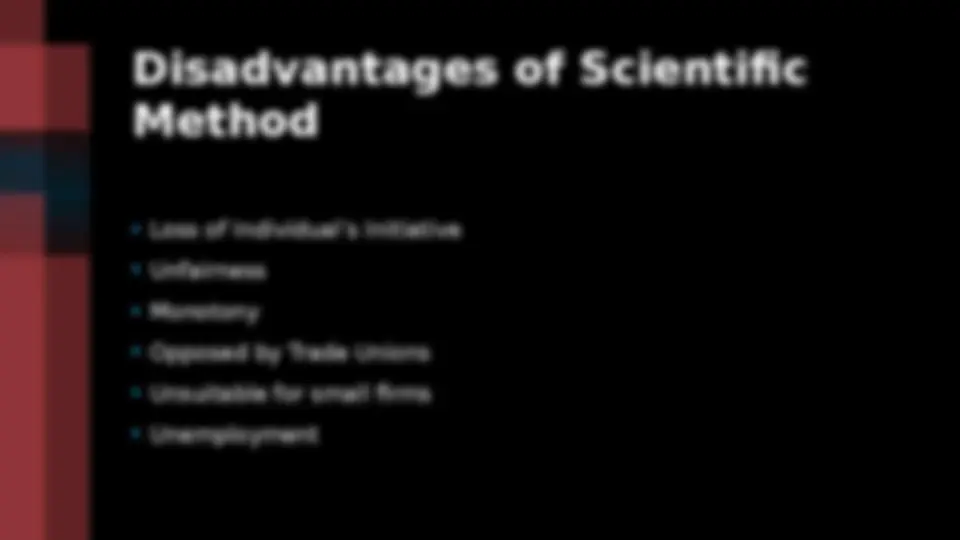
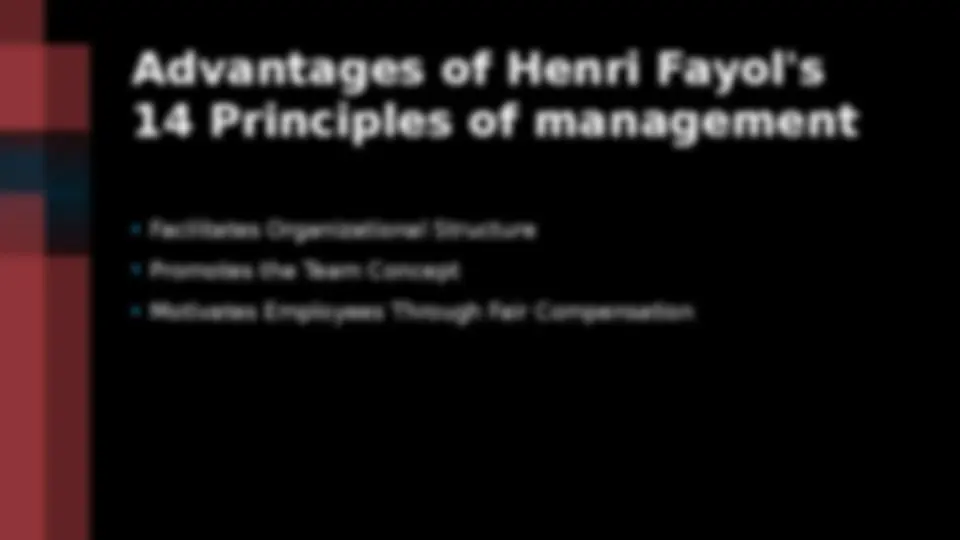
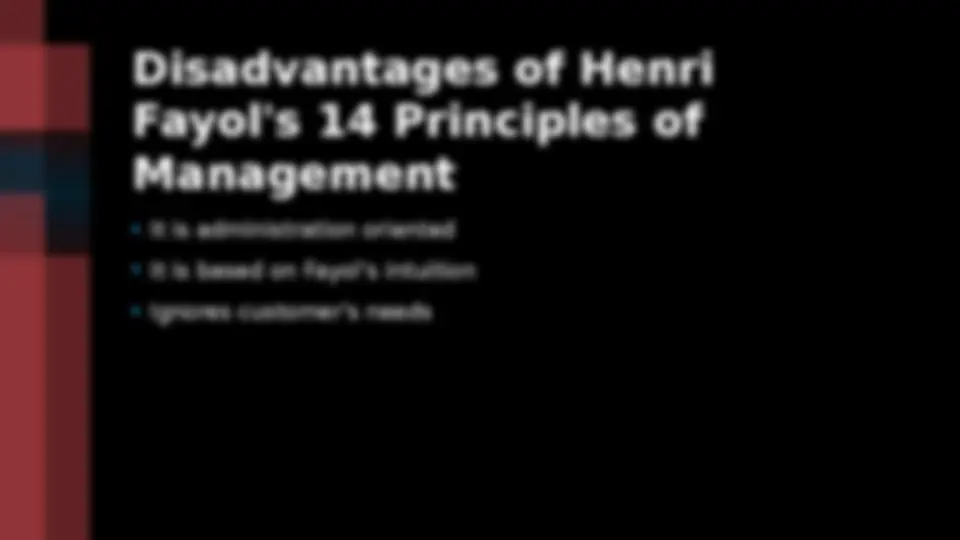
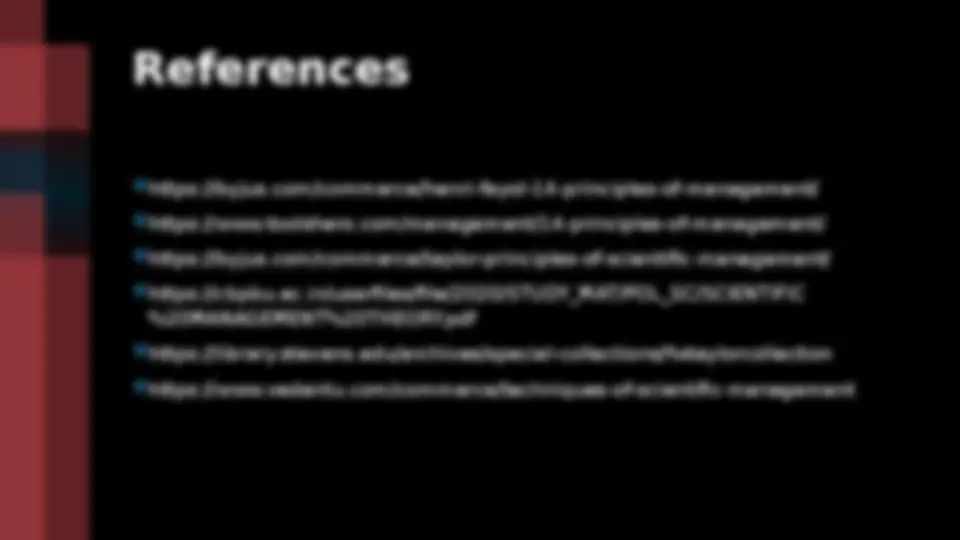
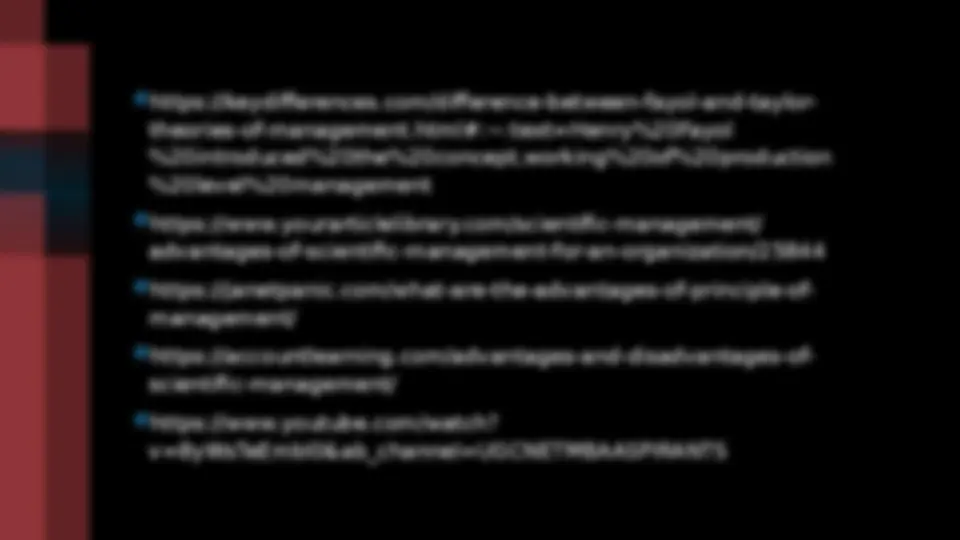
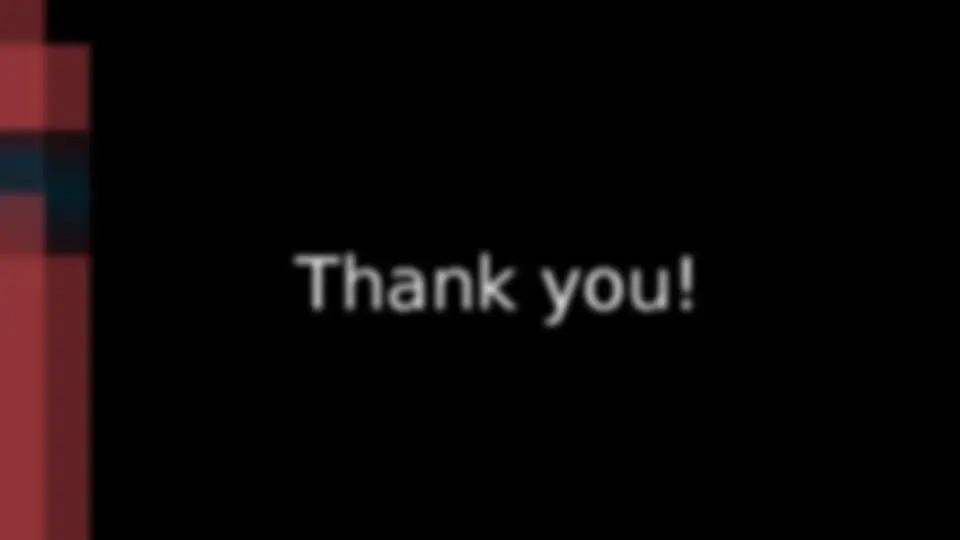
Study with the several resources on Docsity
Earn points by helping other students or get them with a premium plan
Prepare for your exams
Study with the several resources on Docsity
Earn points to download
Earn points by helping other students or get them with a premium plan
Community
Ask the community for help and clear up your study doubts
Discover the best universities in your country according to Docsity users
Free resources
Download our free guides on studying techniques, anxiety management strategies, and thesis advice from Docsity tutors
The features, principles, and techniques of F.W. Taylor's scientific management and Henri Fayol's 14 principles of management. It explains how Taylor's approach aimed to increase efficiency and reduce wastage in production by standardizing work methods, equal division of work and responsibility, scientific selection of workers, and mental revolution. Fayol's principles focus on top-level management and include division of work, unity of command, unity of direction, subordination of individual interest, scalar chain, order, equity, stability, initiative, and esprit de corps. The document also highlights the advantages and disadvantages of both approaches.
Typology: Schemes and Mind Maps
1 / 53
This page cannot be seen from the preview
Don't miss anything!
Introduction to F.W.
Taylor's Scientific Management
important theories of traditional public administration formulated
by Frederick Winslow Taylor who was an engineer by profession
and always viewed each and every thing and its aspects
scientifically and since he was into the production field ,he was
to be concerned with increasing efficiency of workers to increase
production within the least possible time with the least possible
resources
the maximum
Standardisation of work methods
Equal division of work and responsibility between management
and workers
Scientific selection of workers and their progressive
development
Mutual collaboration of workers and management
observation and analysis of a particular job to find out the one
best way to do that task that would lead to reduced work for the
worker as he could do more with limited number of movements
Use of benchmarks and standardized tools and equipment and
methods would improve quality control and inspections thus
reducing cost of production and increasing efficiency
management to study the nature and character of each
job/work and then scientifically choose the right worker for the
same who possess the necessary skills for the same
It is also the duty of the management to study the limitations
and possibilities of workers for their development as Taylor
believed that every worker had a definite potential for
development
and cordial relations between management and workers instead
of distrust in order to increase the production and efficiency of
the company
A healthy environment needs to be created
management towards each other and their responsibilities
and instead focus on generating the most that will lead to more
funds for them
without putting in extra effort and instead increase their
responsibilty, efficiency and production that will definitely lead
to raise in their salaries sooner or later
appointed for the same as they have been trained and skilled
for the same and workers to concentrate on completing their
functional task as per the rules and guidelines and methods
planned by the former
various laws and rules are to be applied to everyday work to
find the one best way to do that job
ambition and tends to lose his individuality/individual drive in a
group setting
He stated that workers should have no verbal interaction as it
leads to undue personal pressures
to increase production and efficiency and those after a
successful stint became the benchmark to be used for those
particular jobs
description of what task is to be done by them in clear language
and instructions that is understandable by them by the
management through proper planning
to them would then receive a bonus payment for each piece
extra
And the bonus should be generous and consistent to encourage
the workers to produce more
Work-Study
Standardization of Tools and Equipment
Scientific Task Setting
Scientific Setting of Wage Rates
Scientific Selection and Training
Functional Foremanship
Differential Piece-Rate Plan