
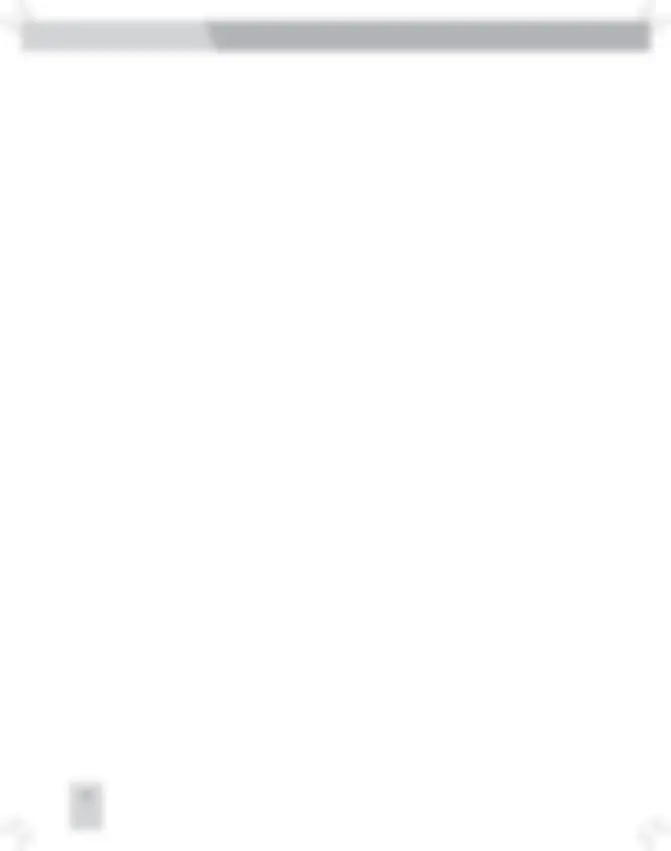
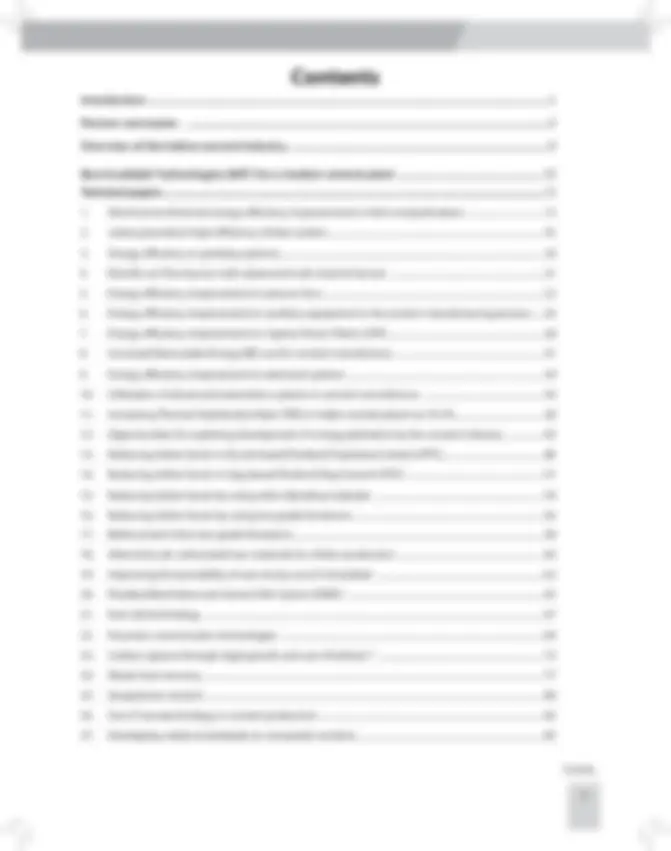
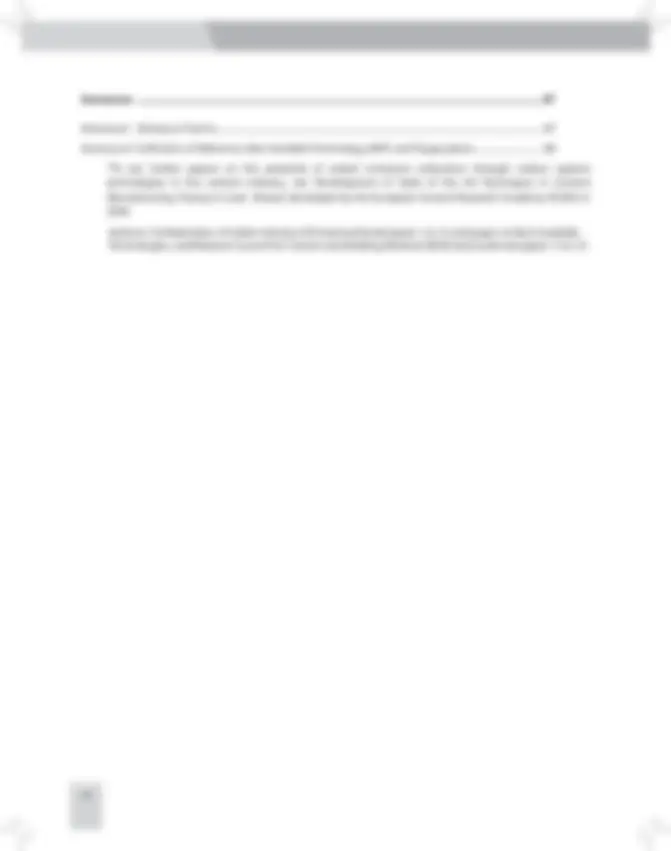
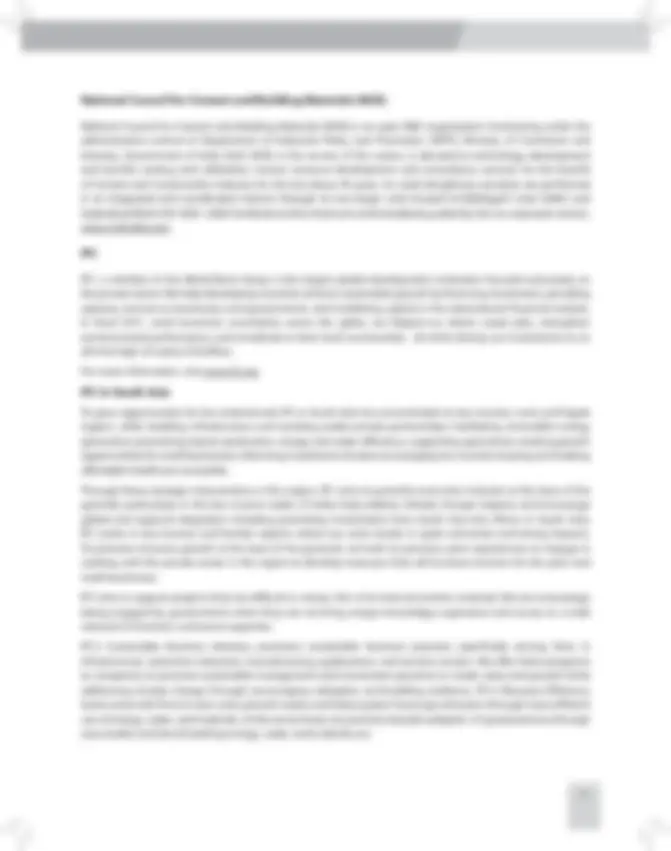
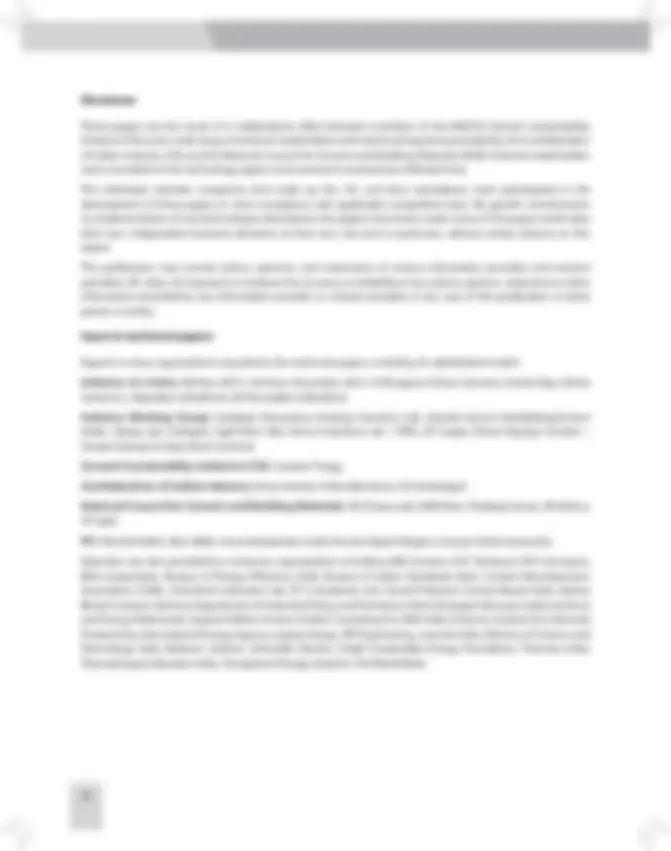
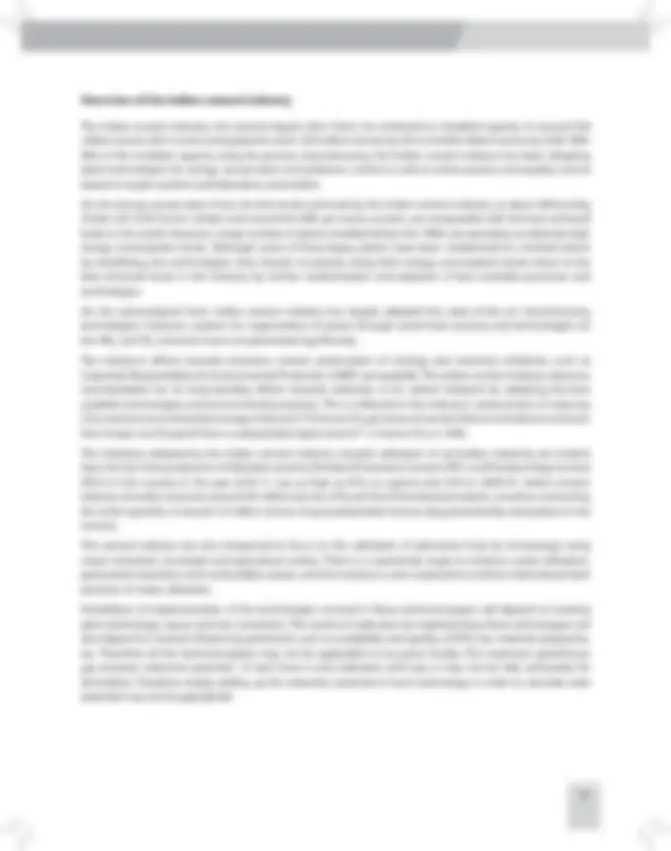
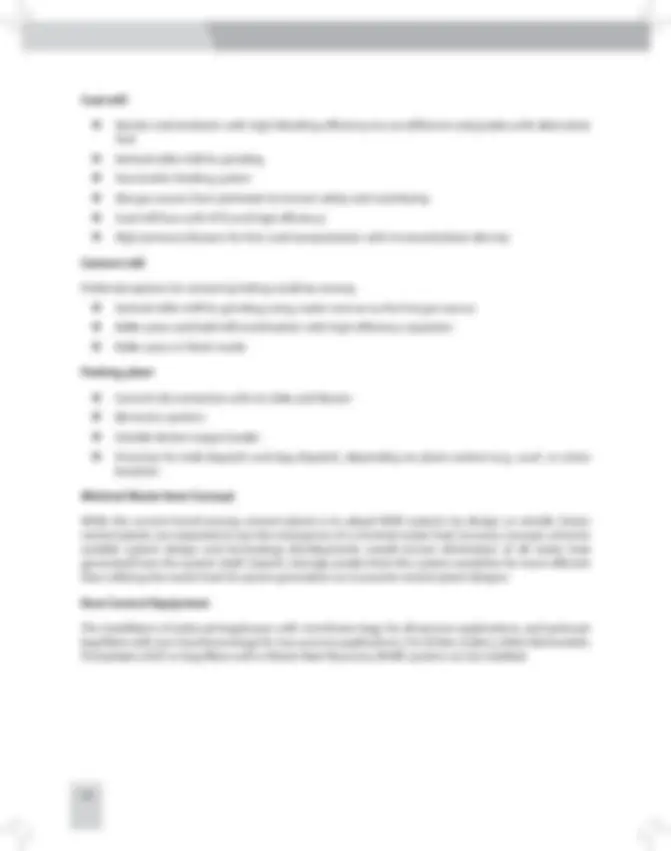
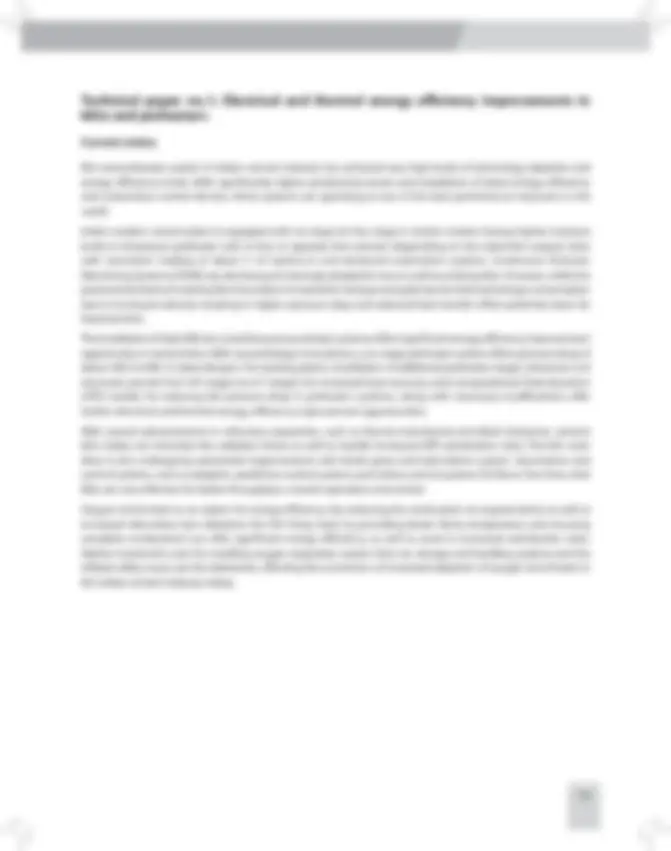

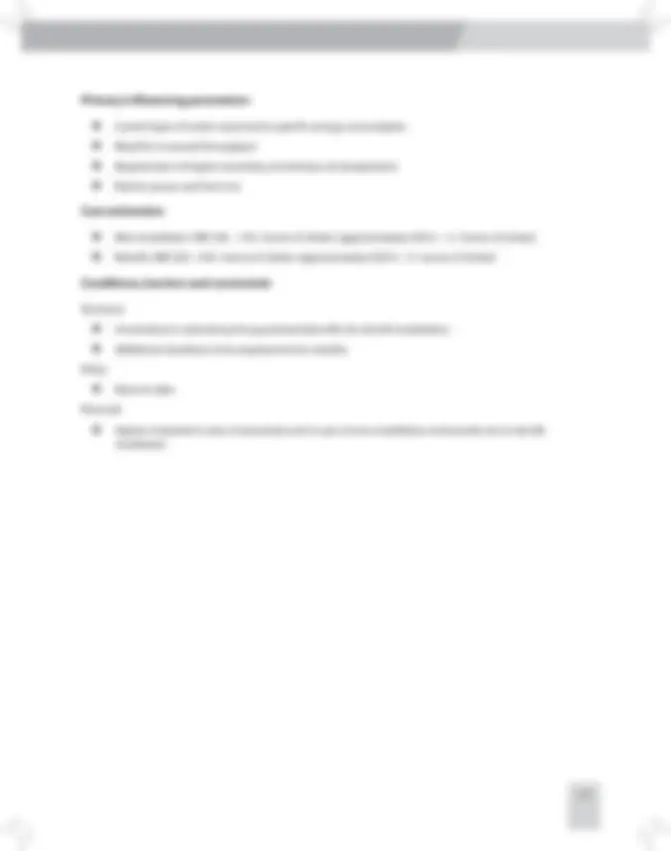
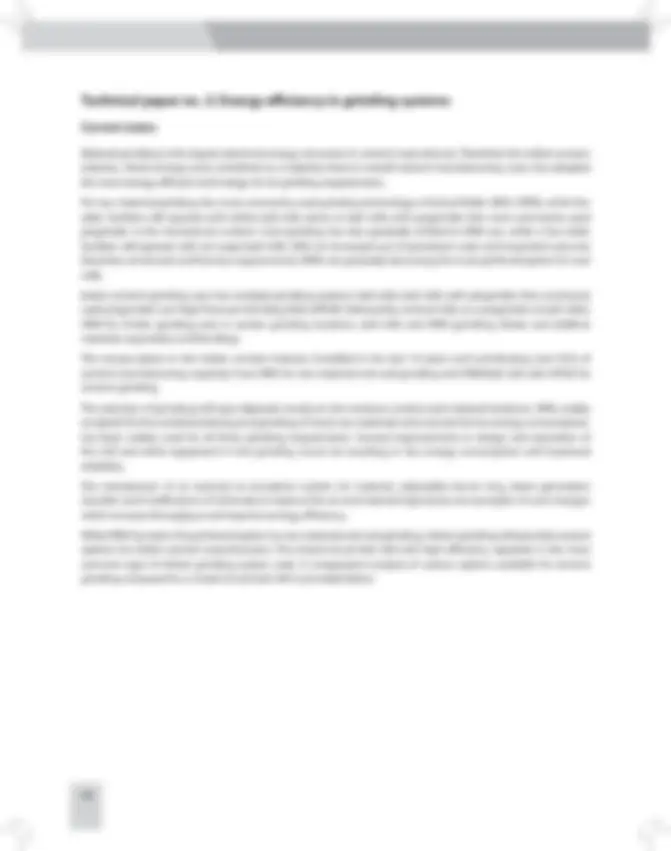
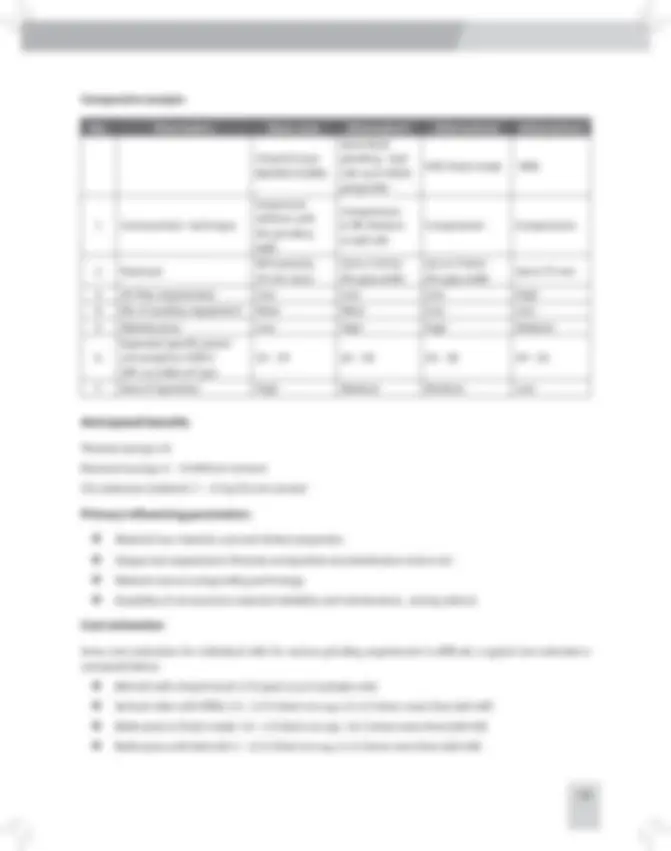
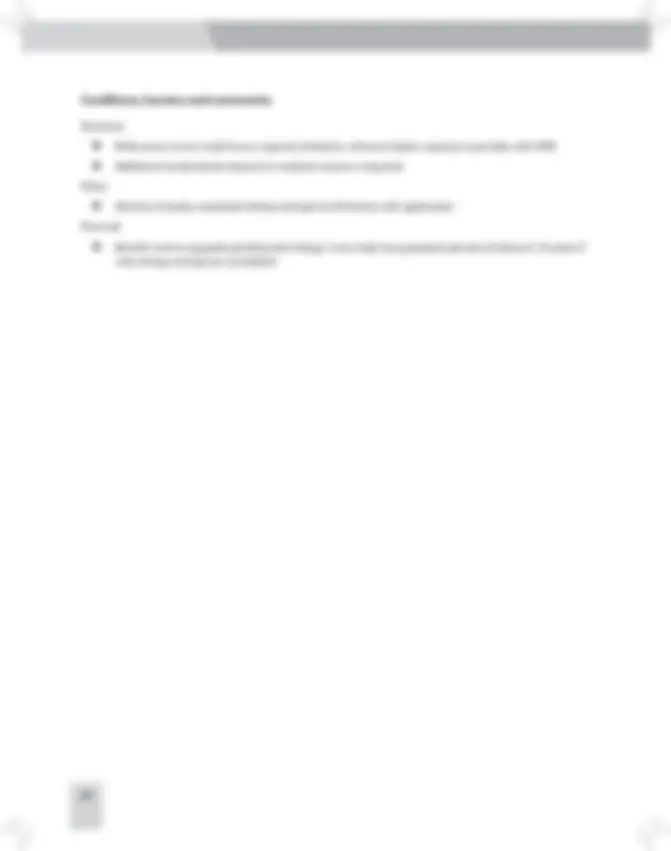
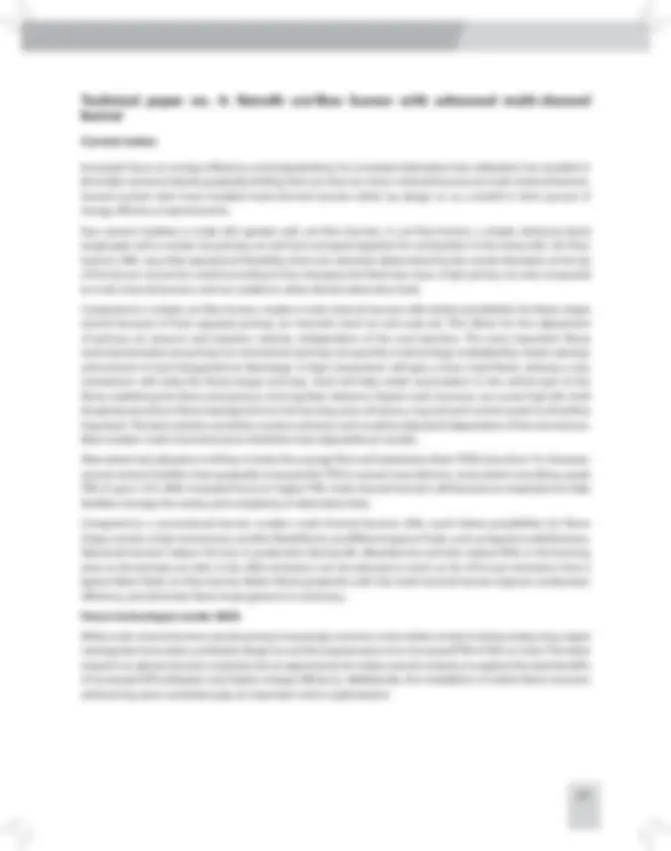
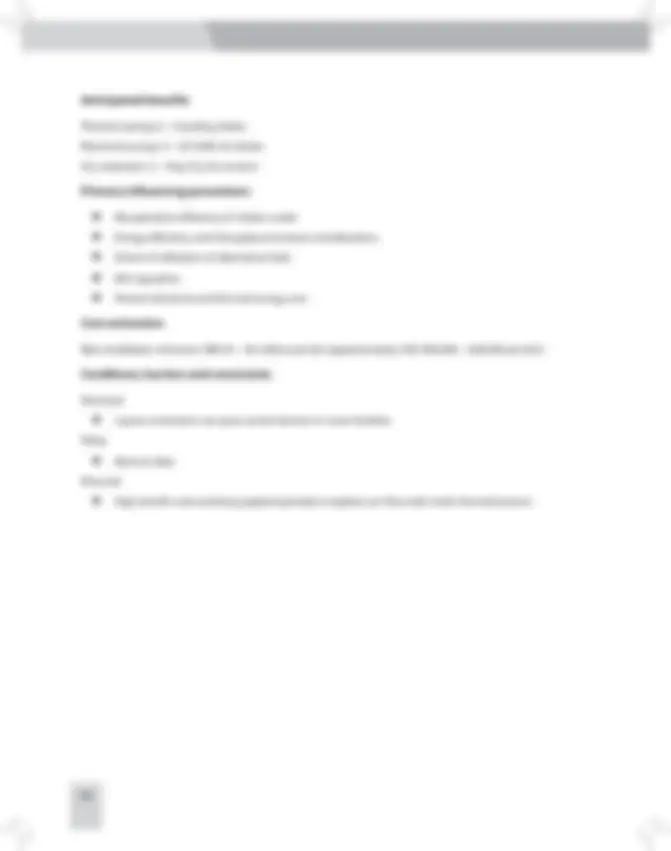
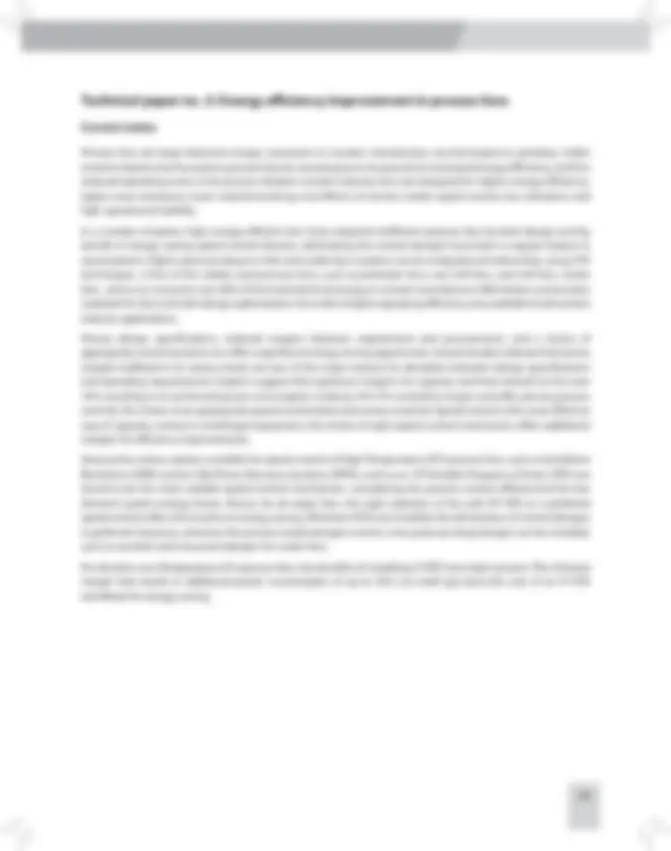
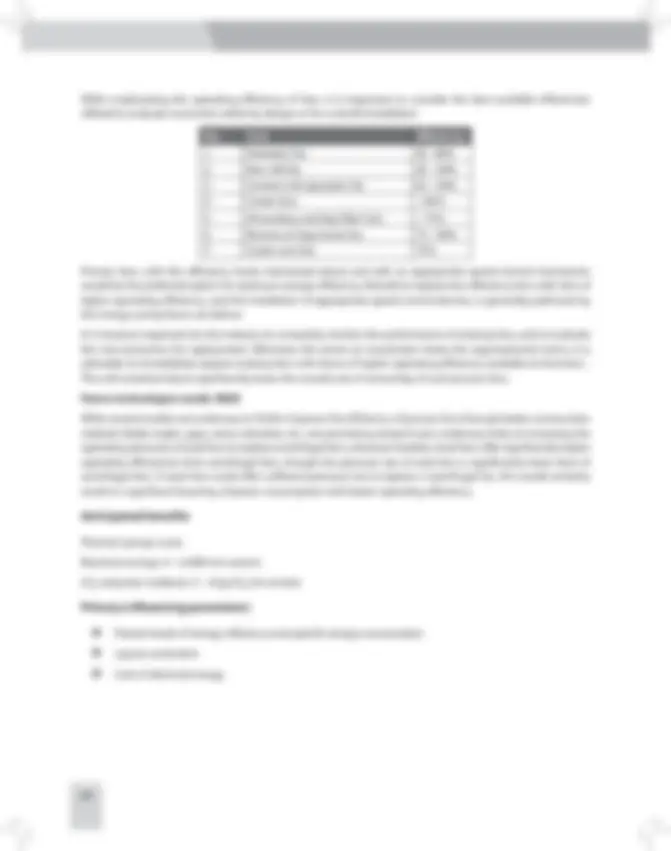
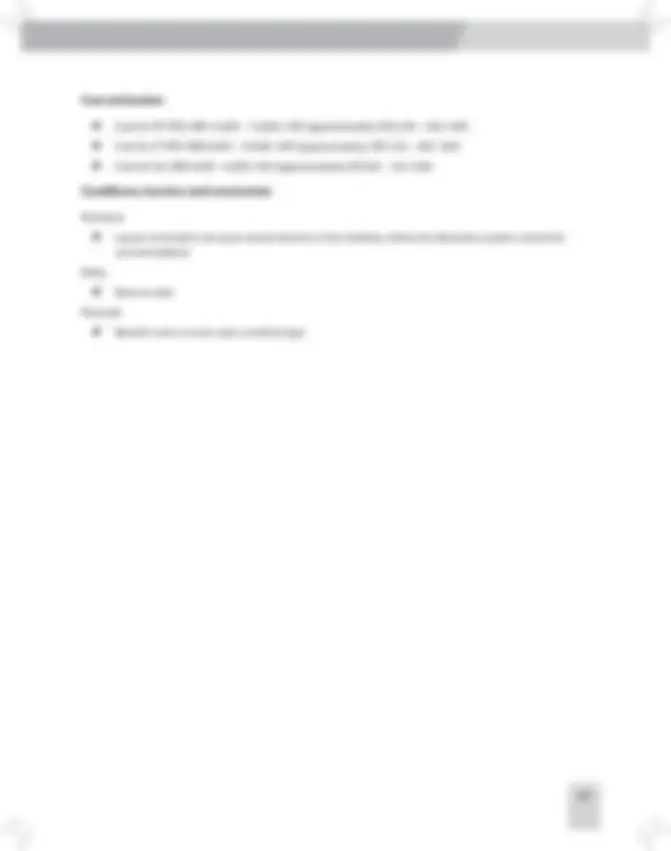
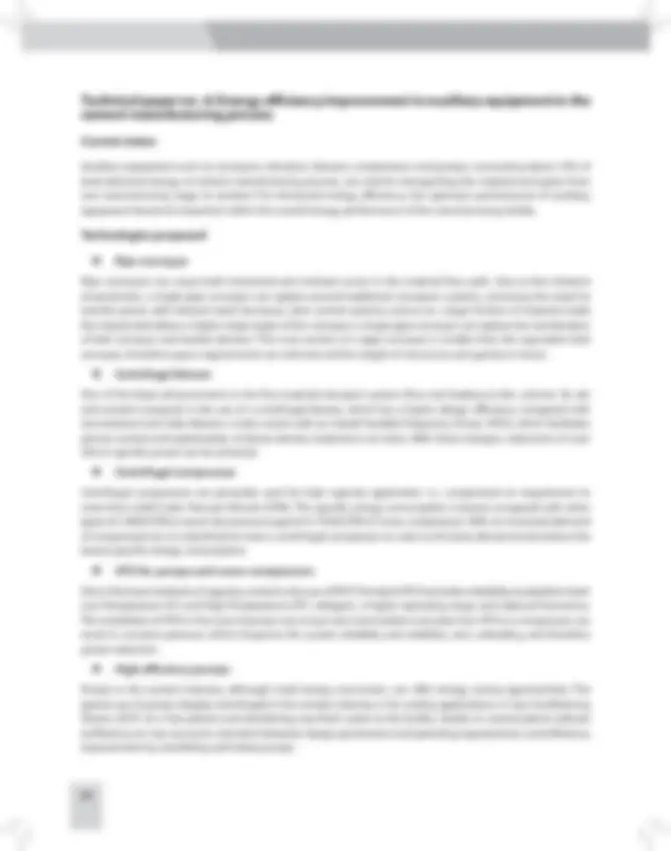
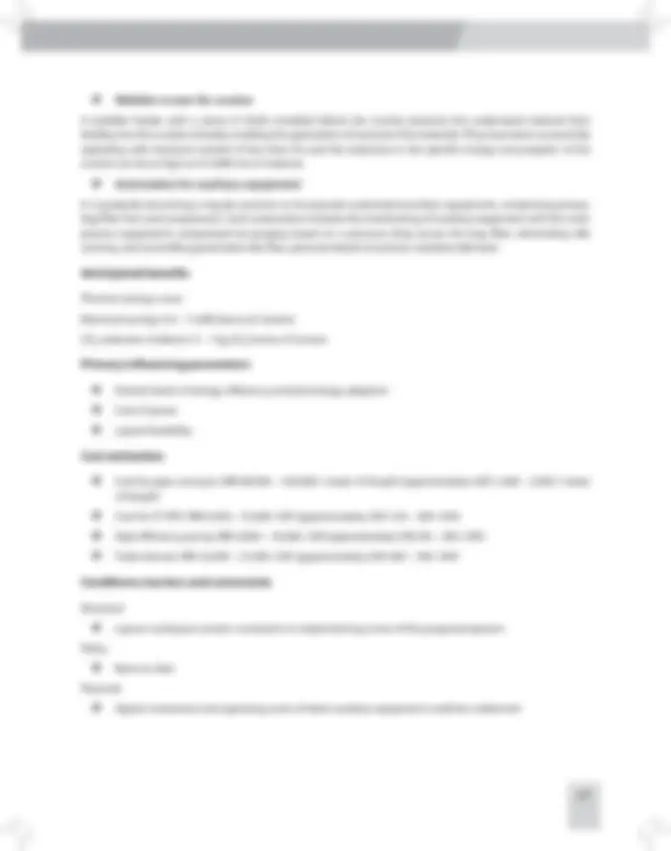
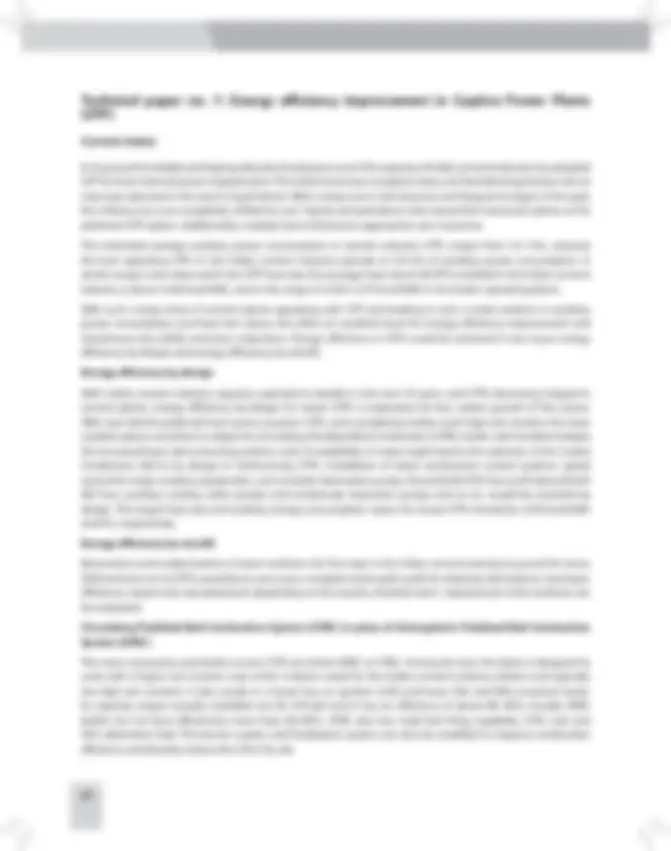
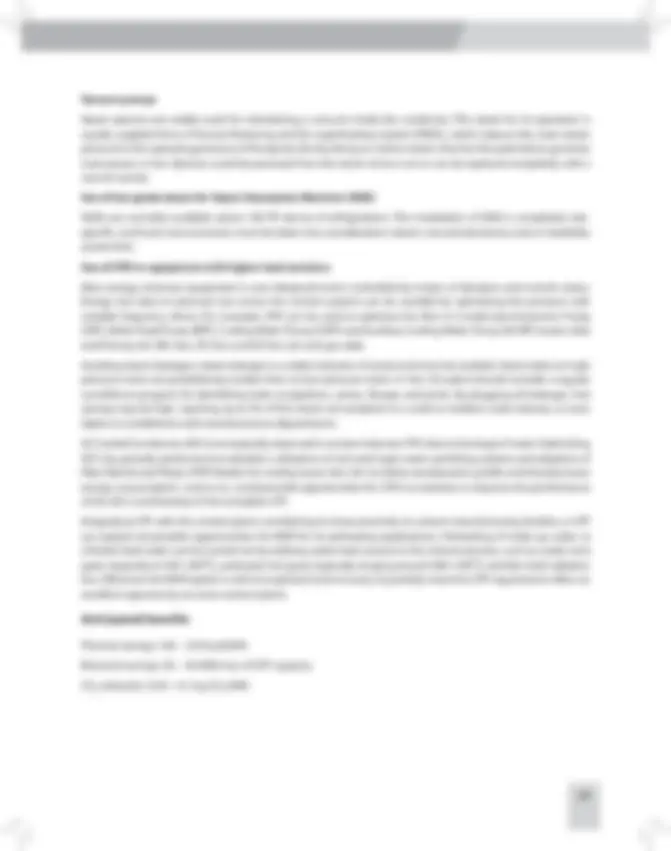
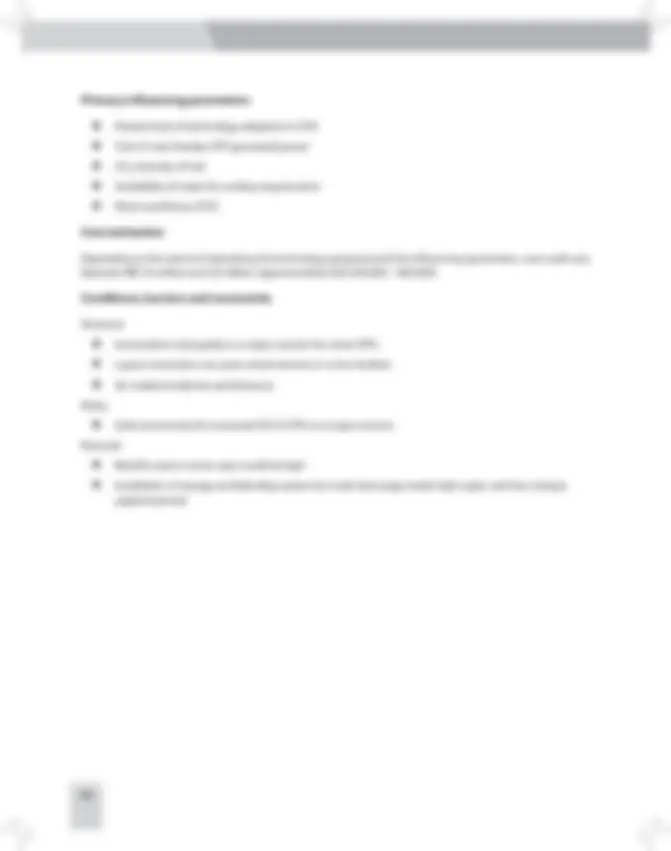
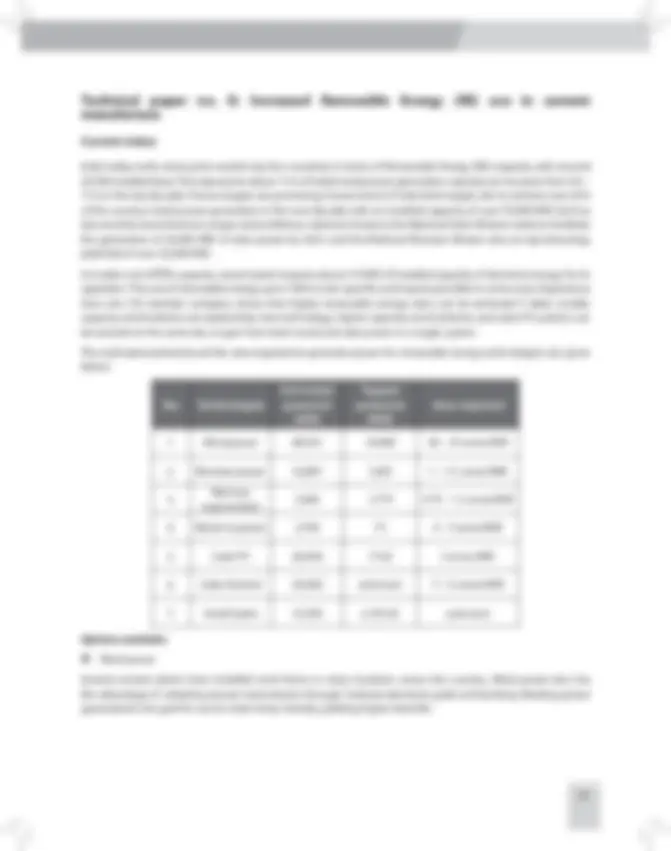
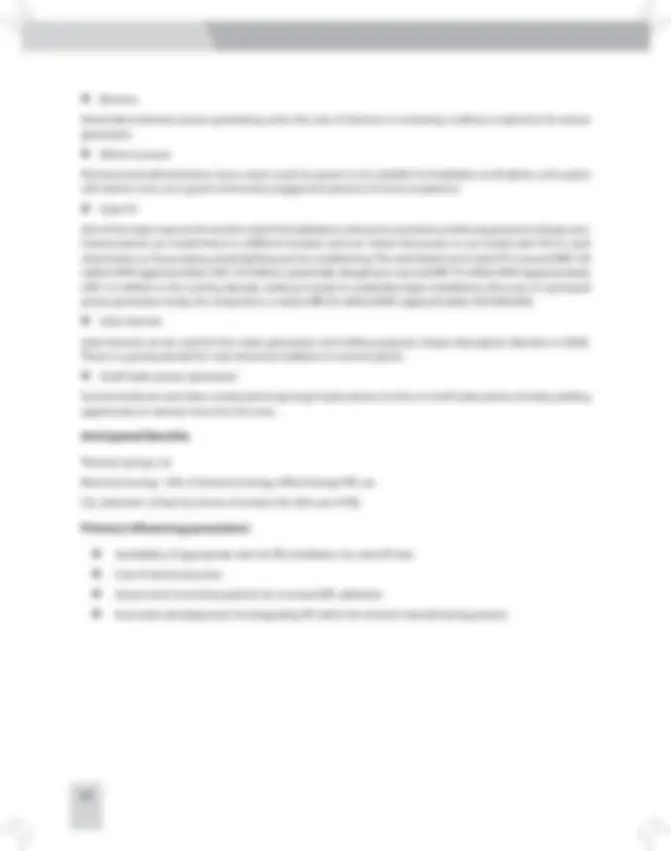
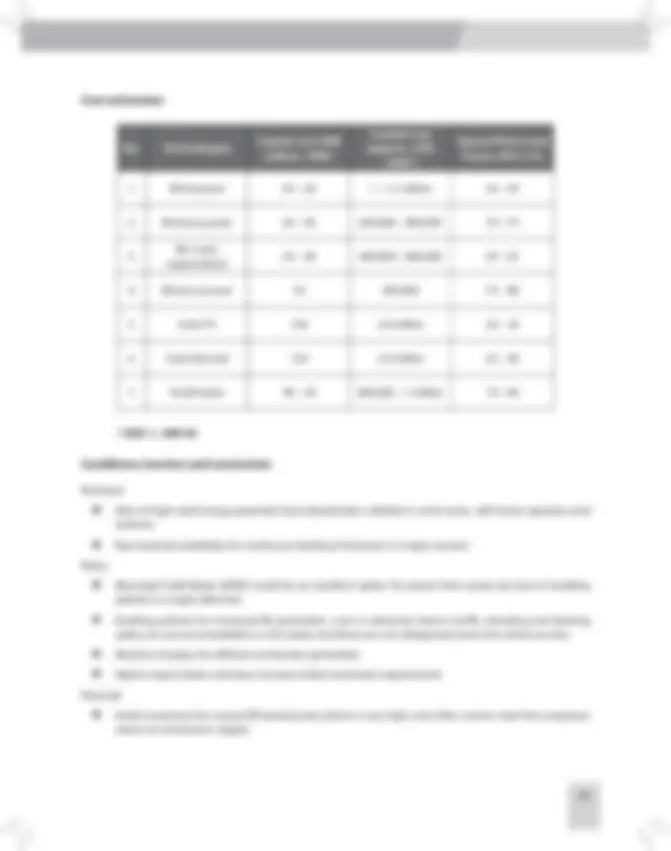
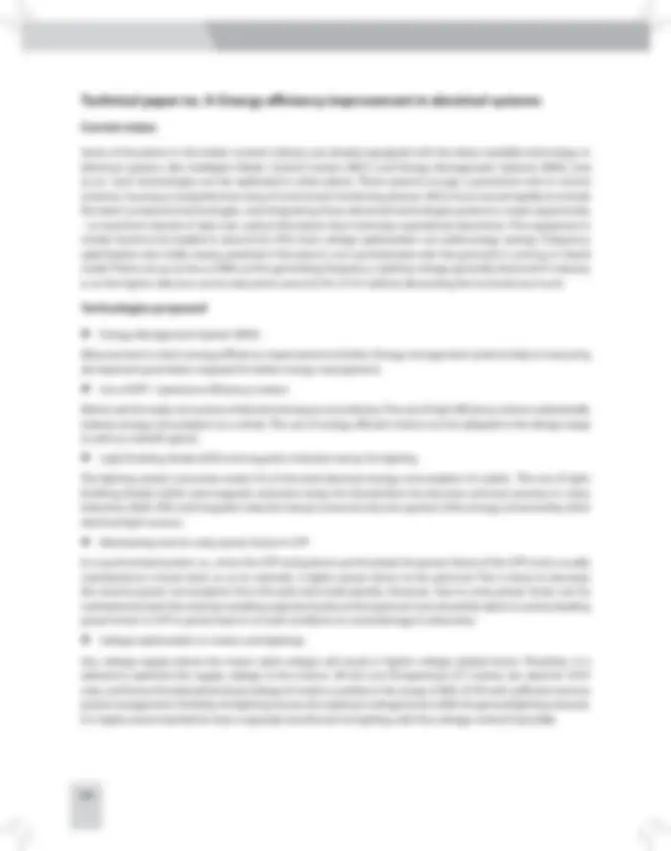
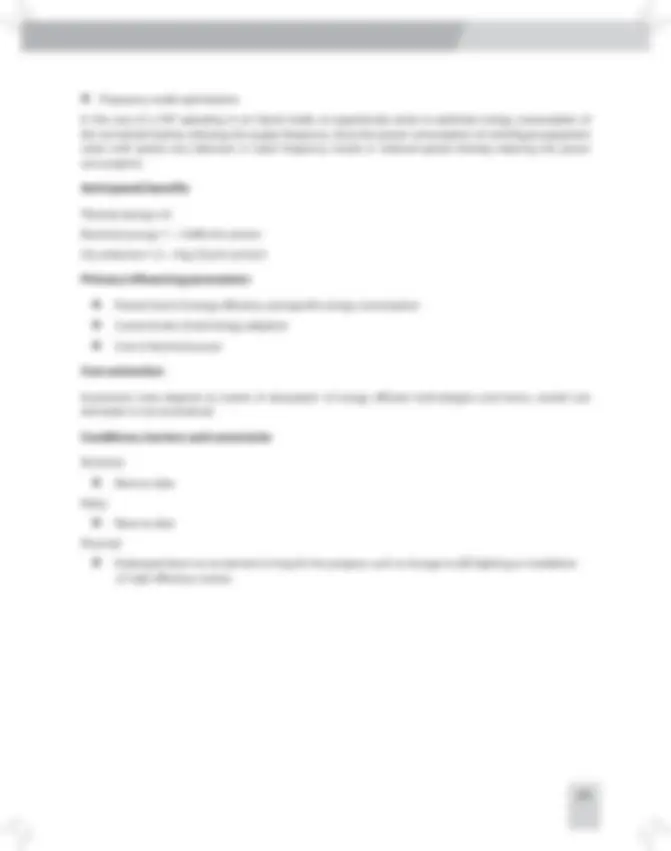
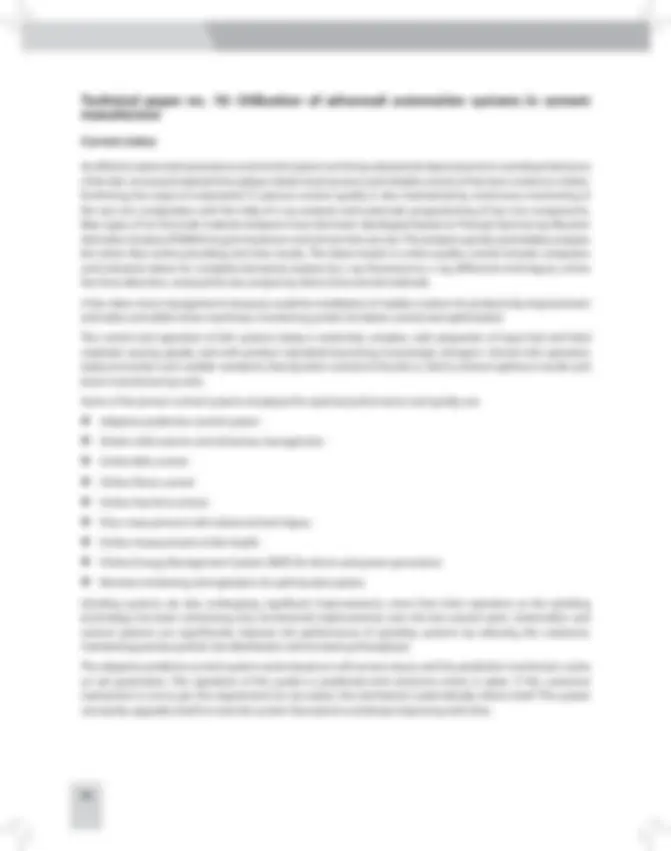
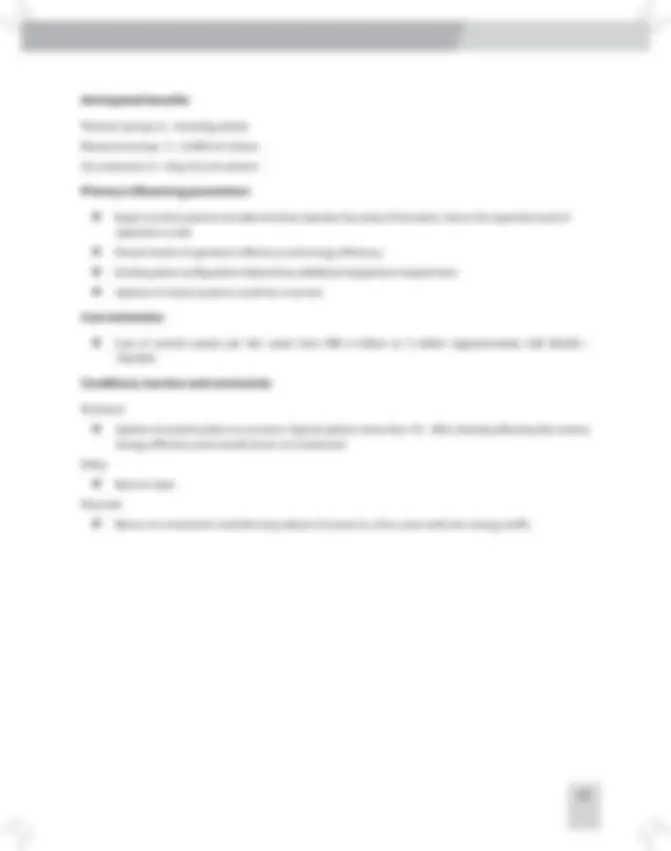
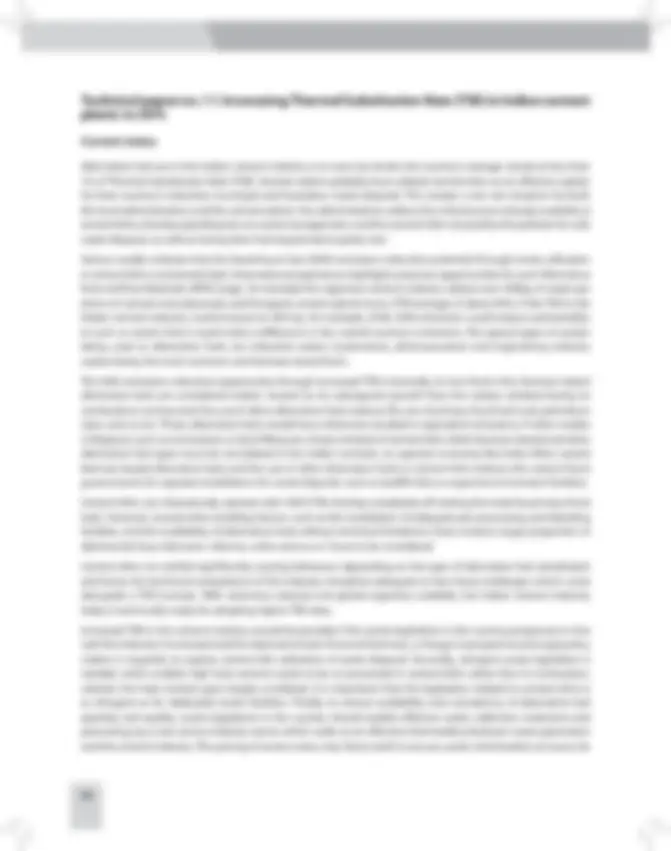
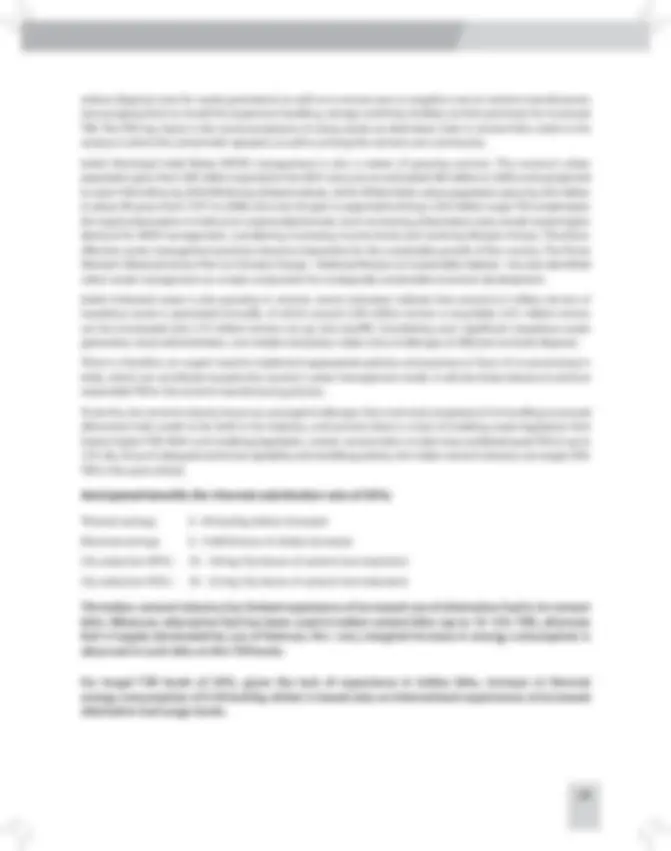
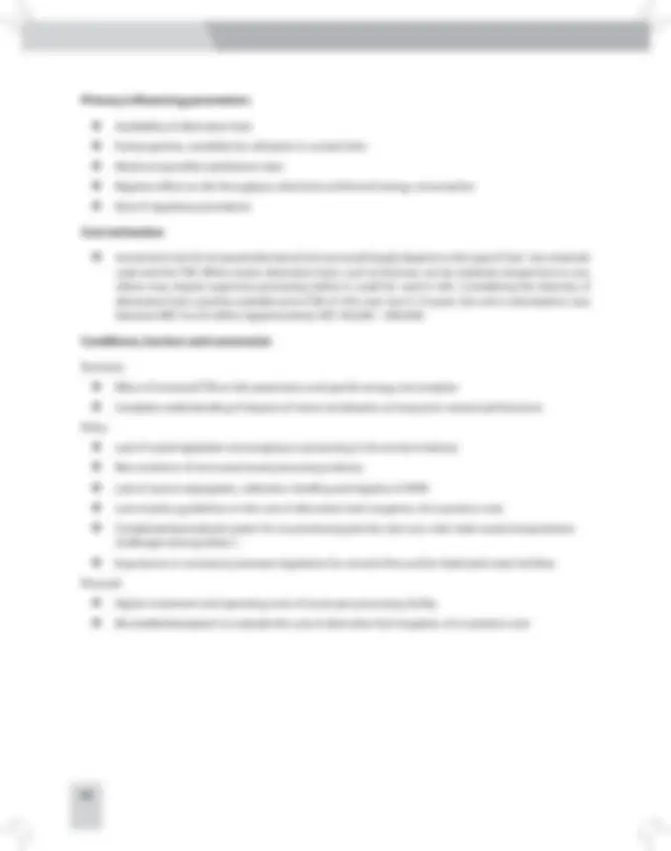
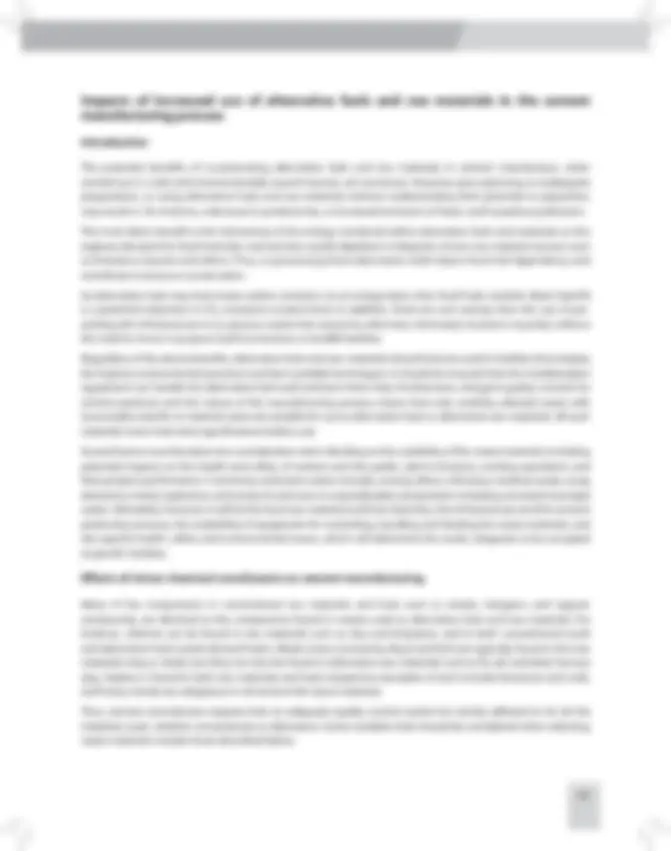
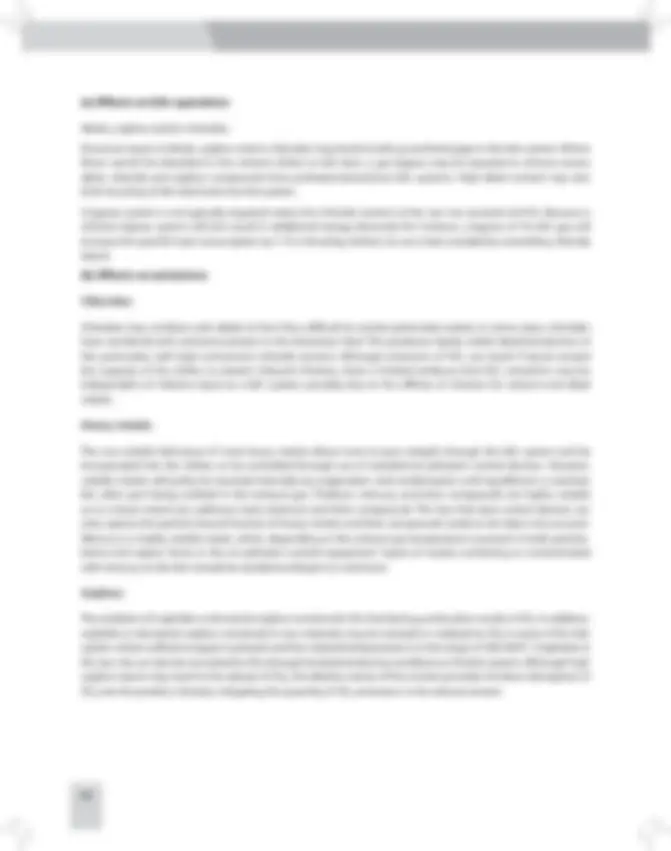
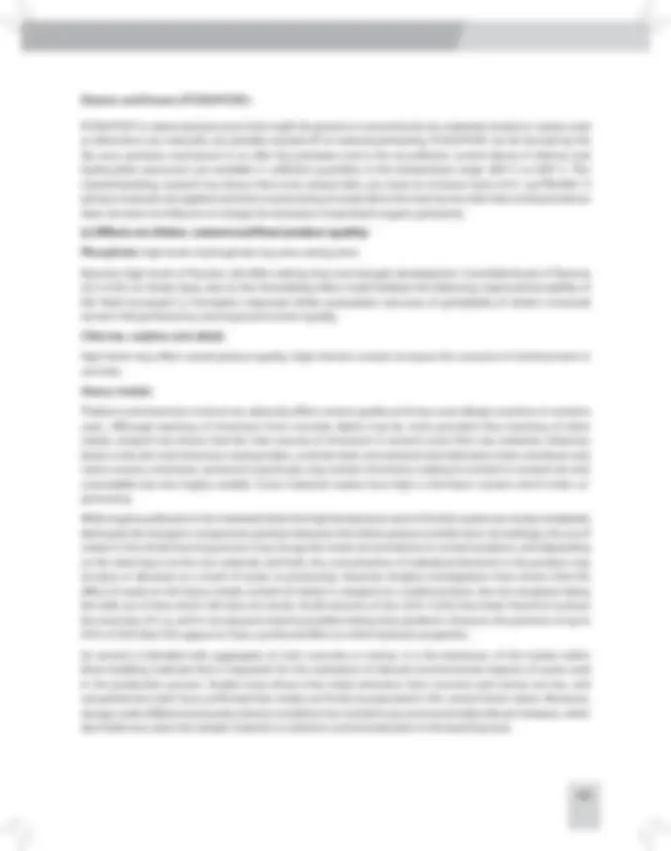
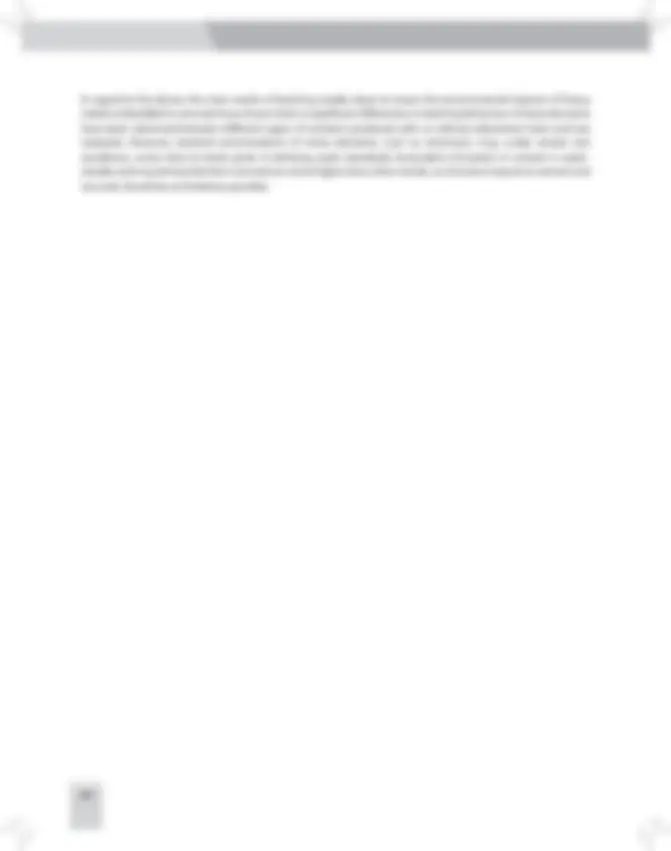

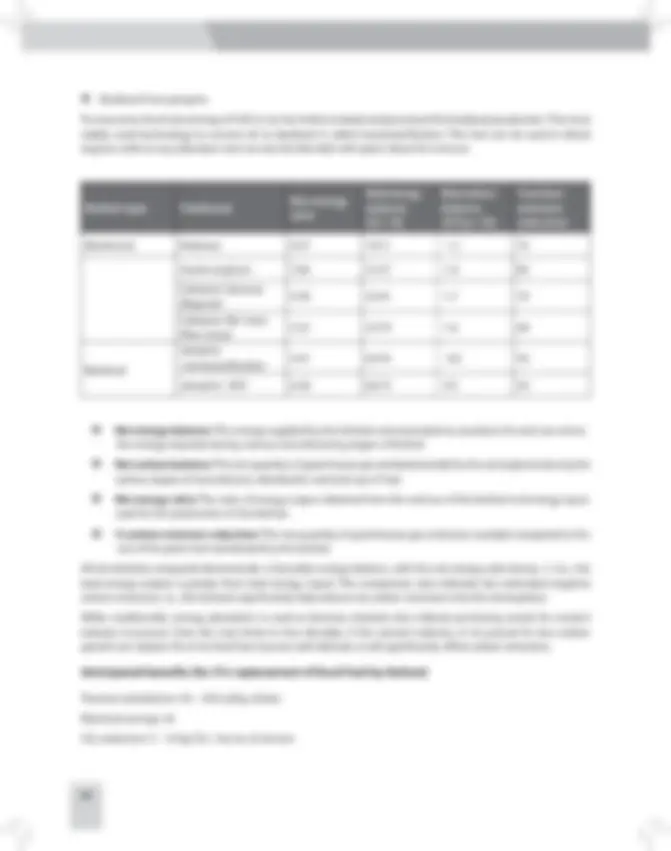
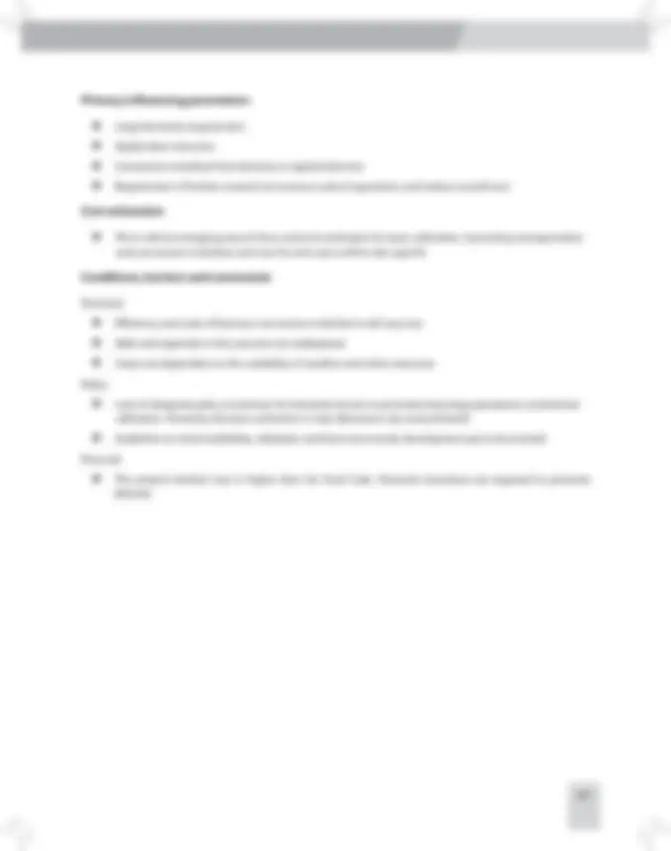
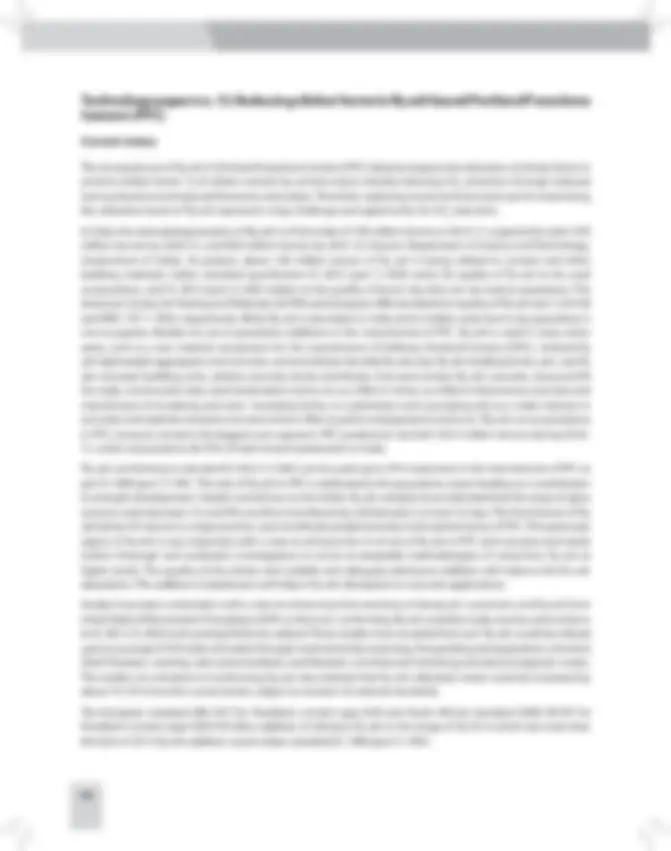
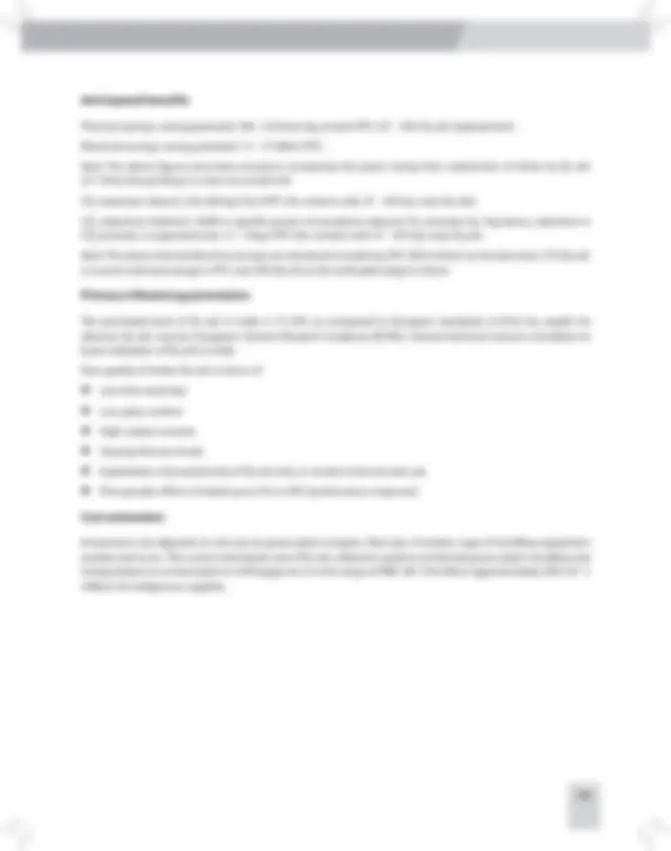
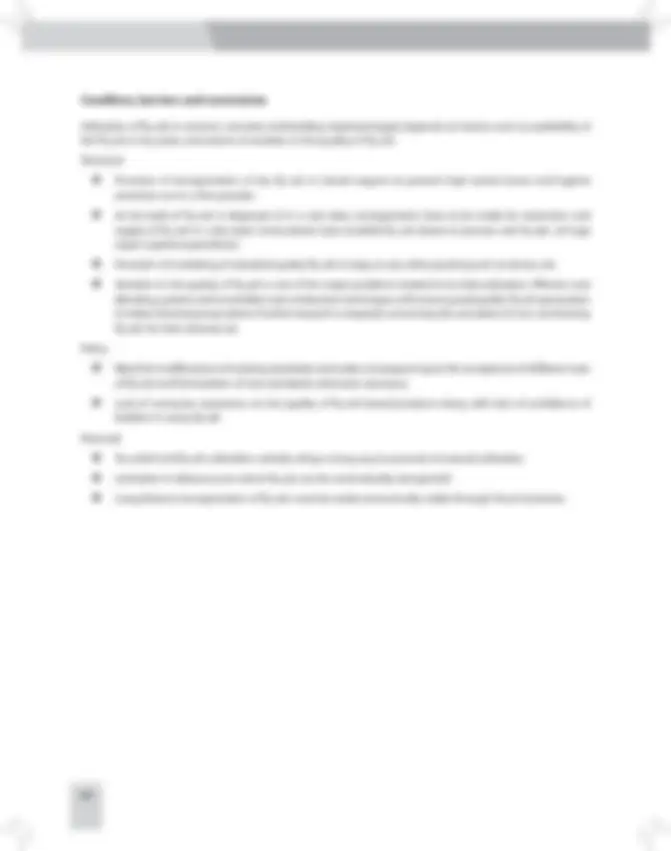
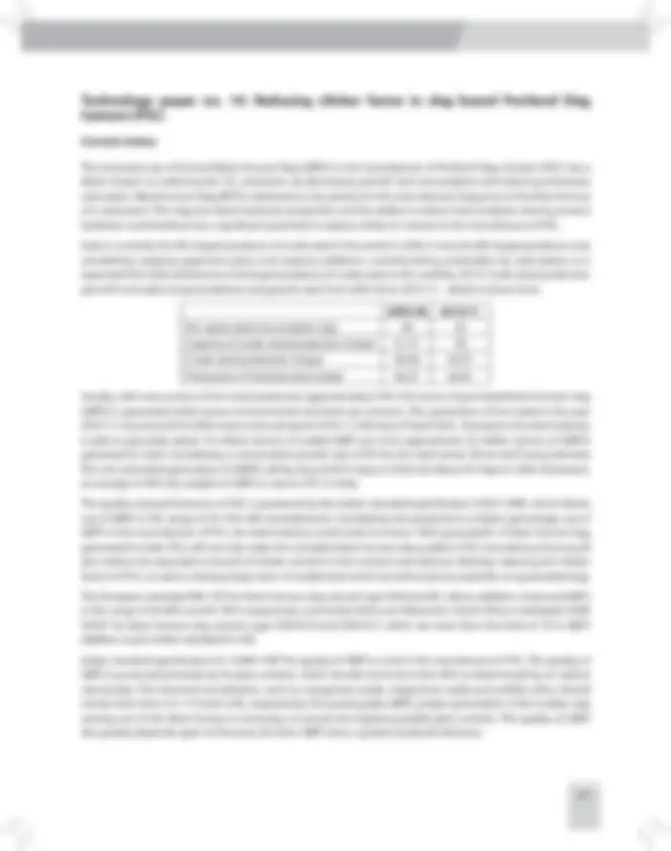
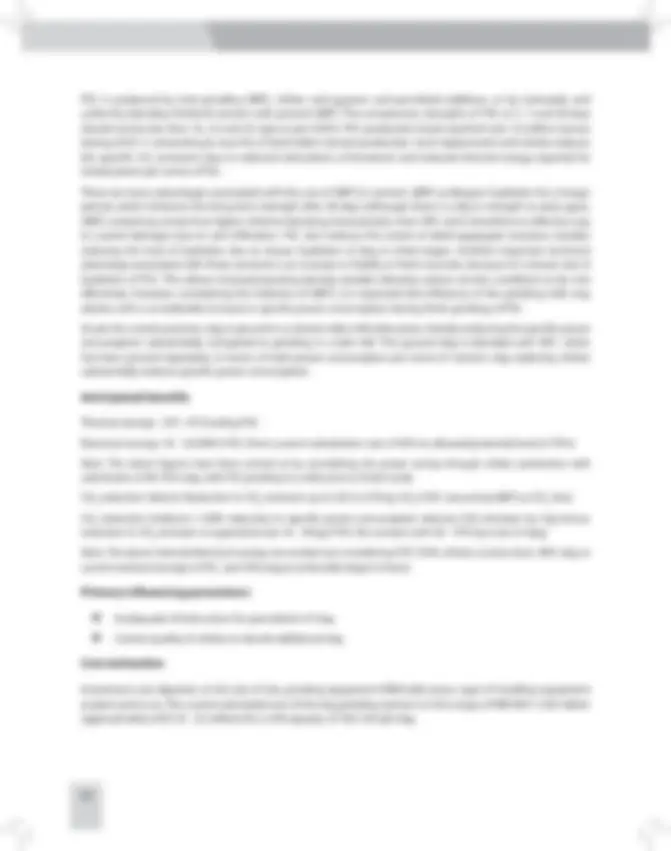
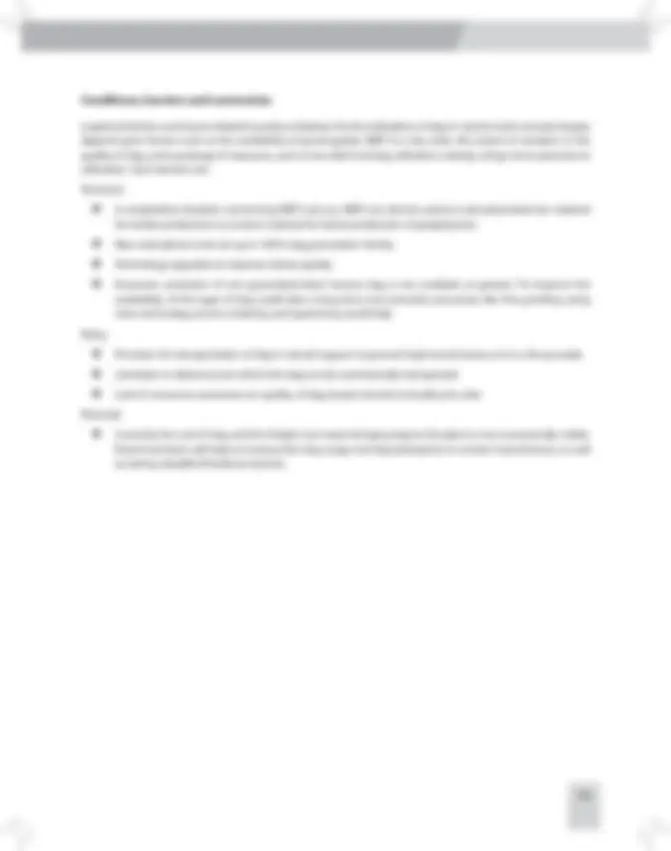
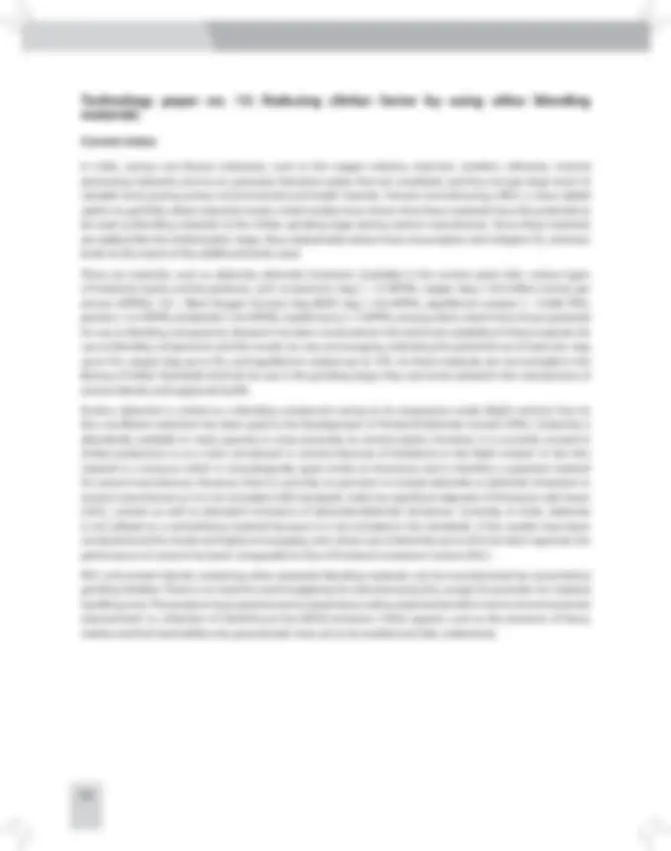
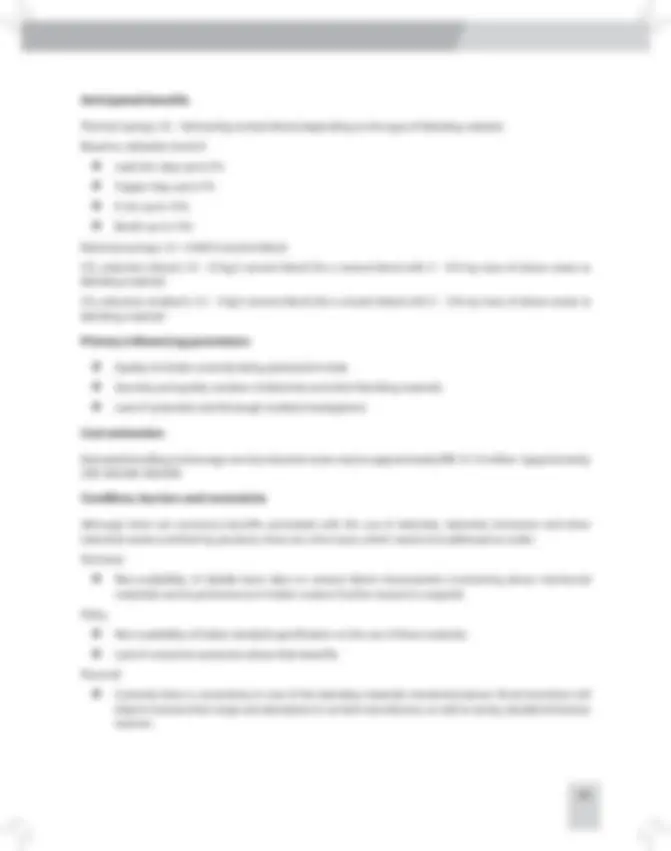
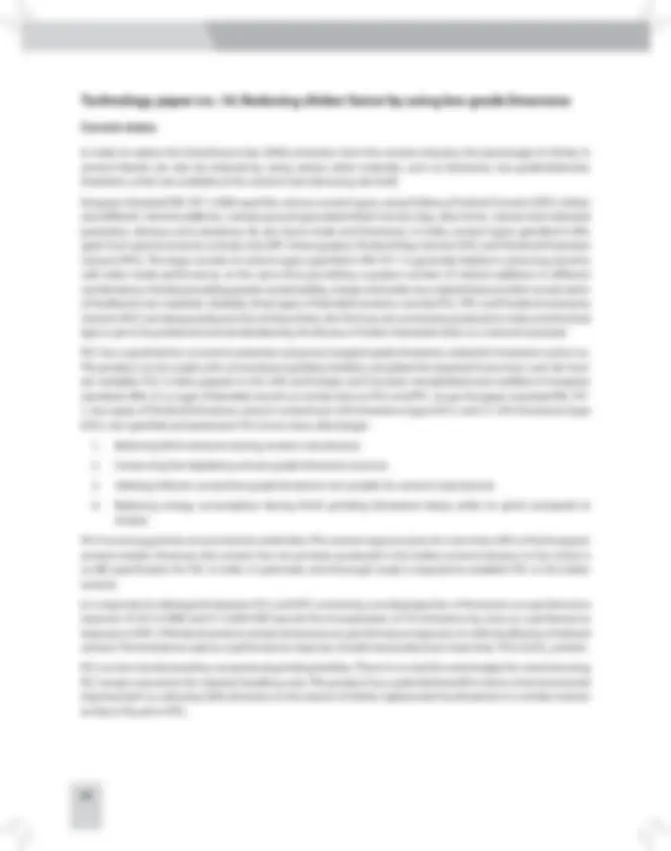
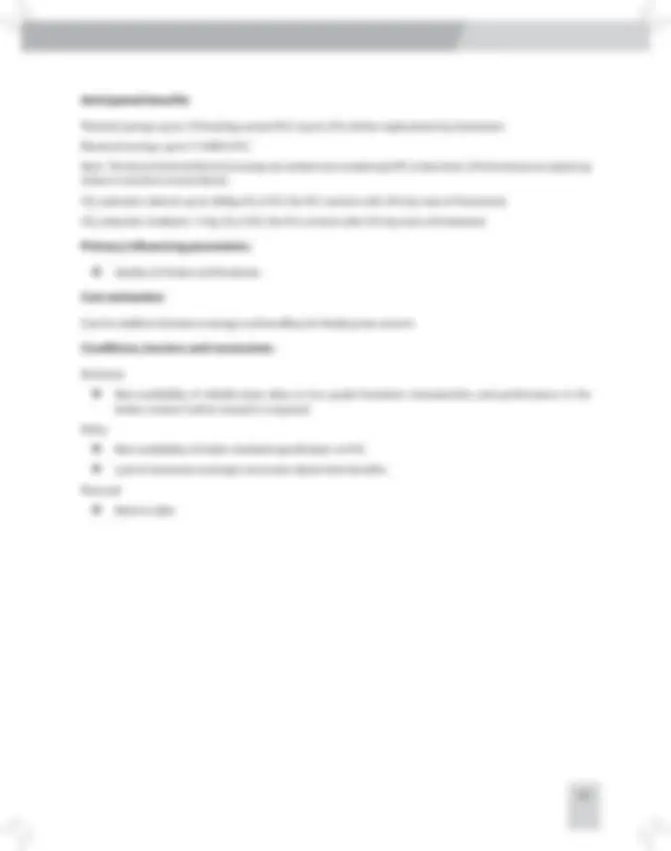
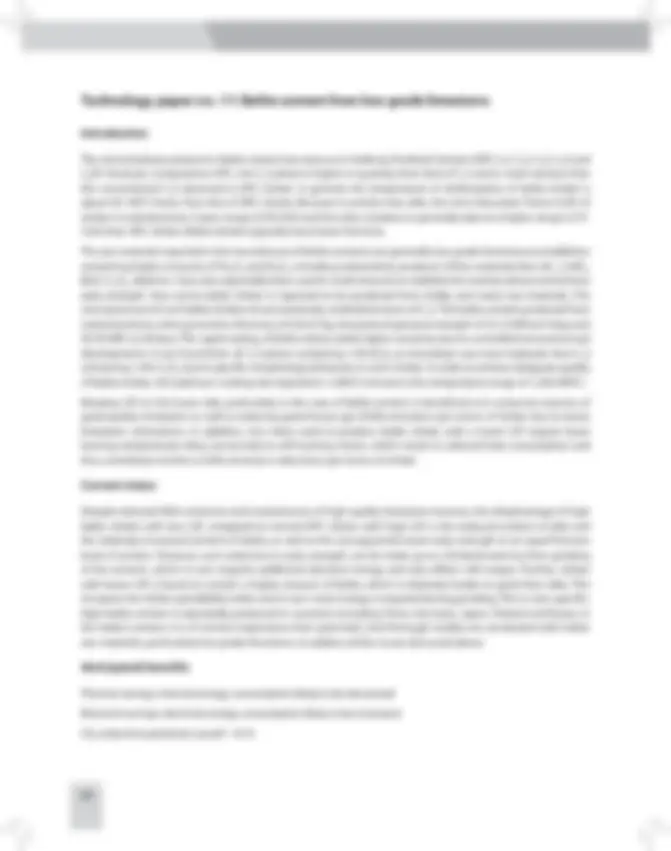
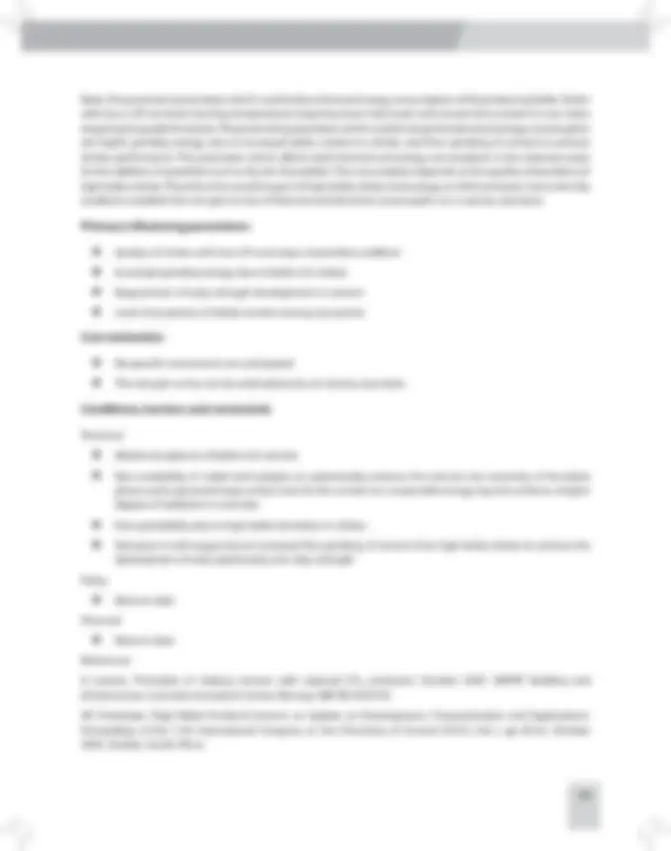
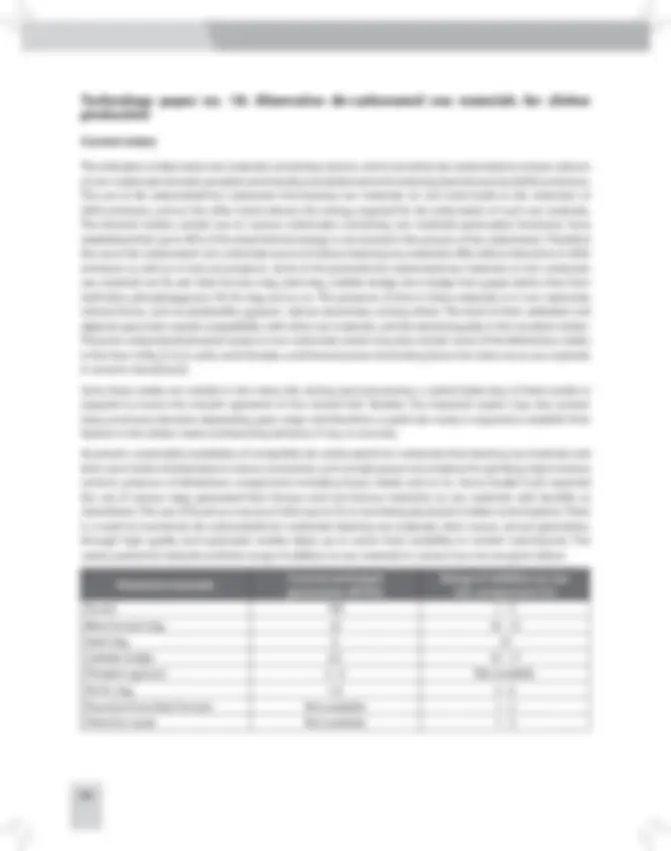
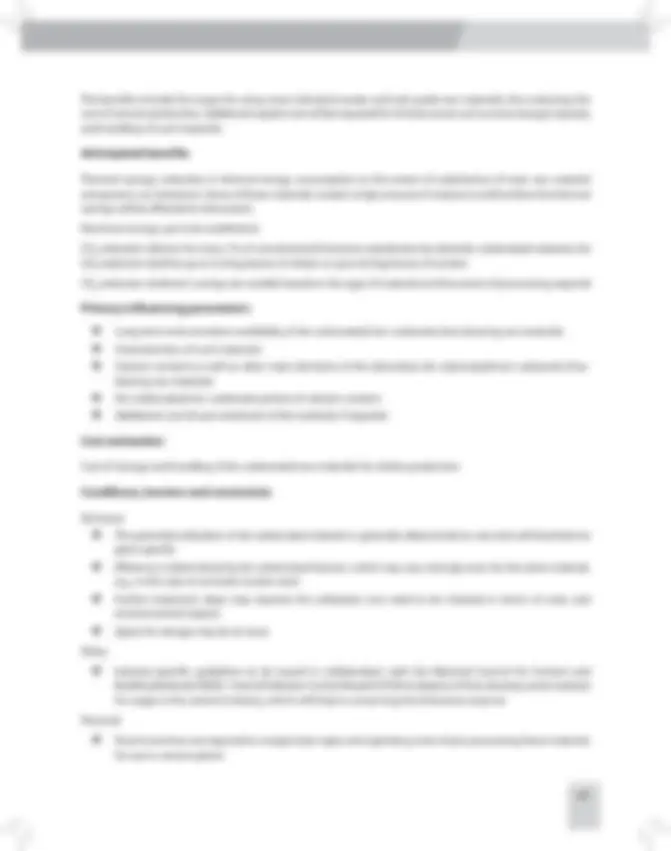
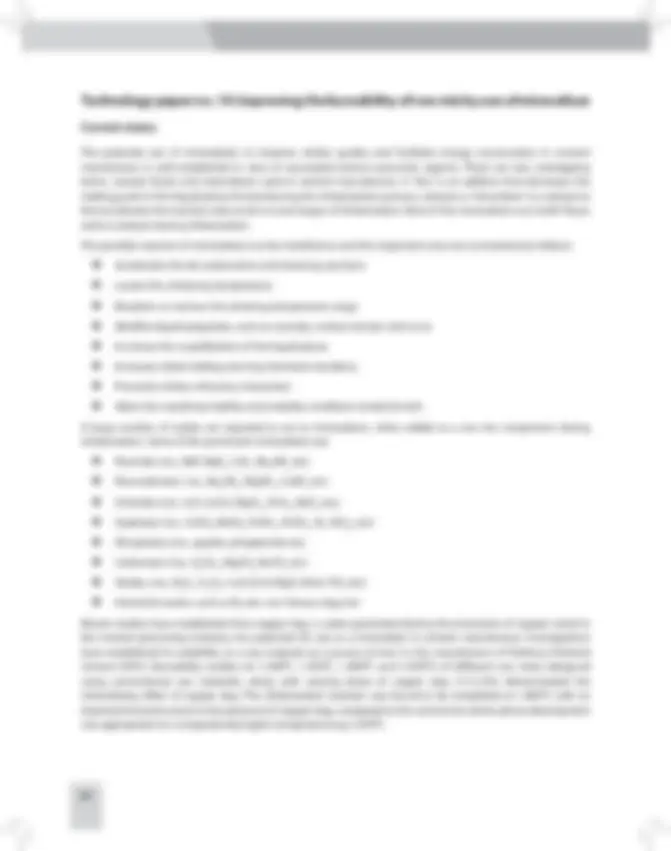
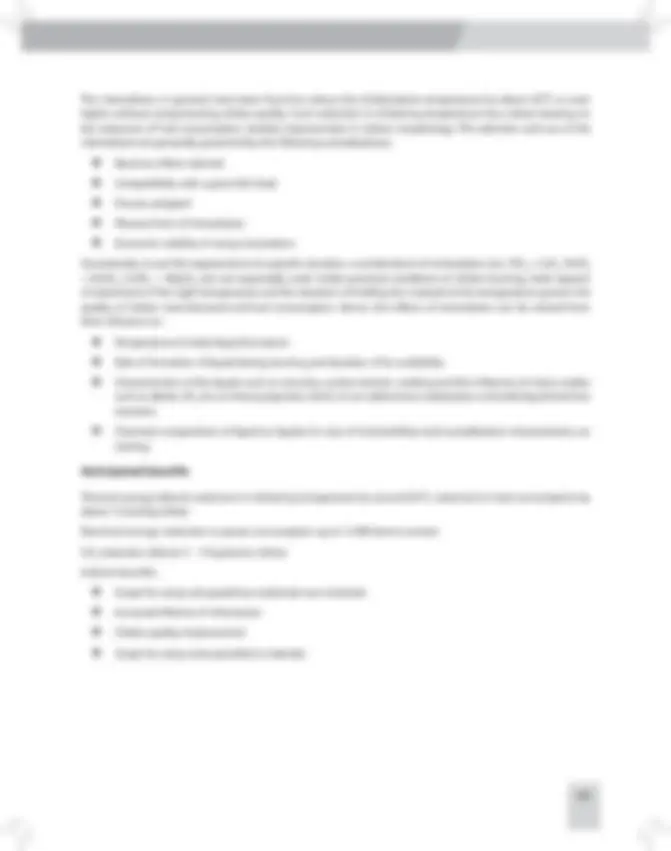
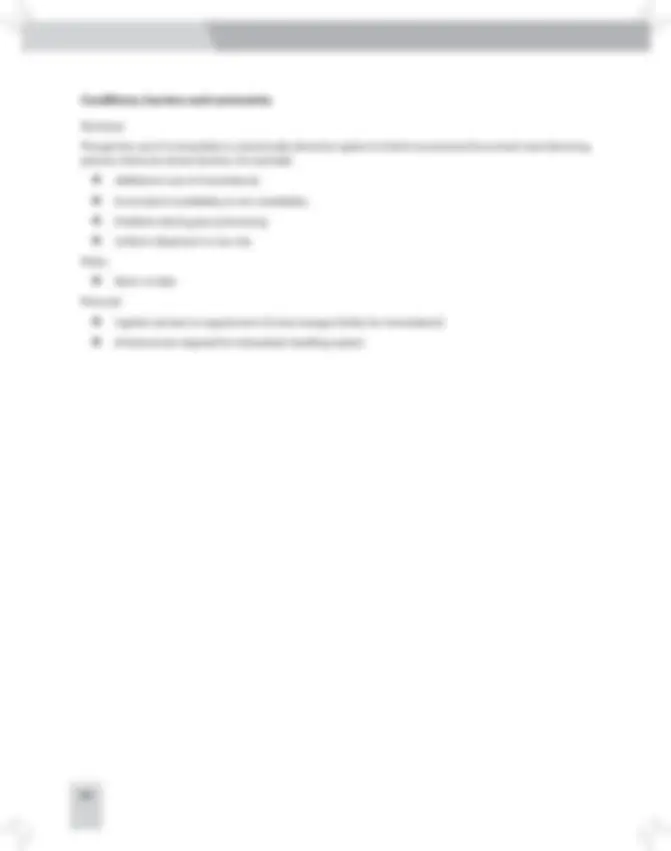

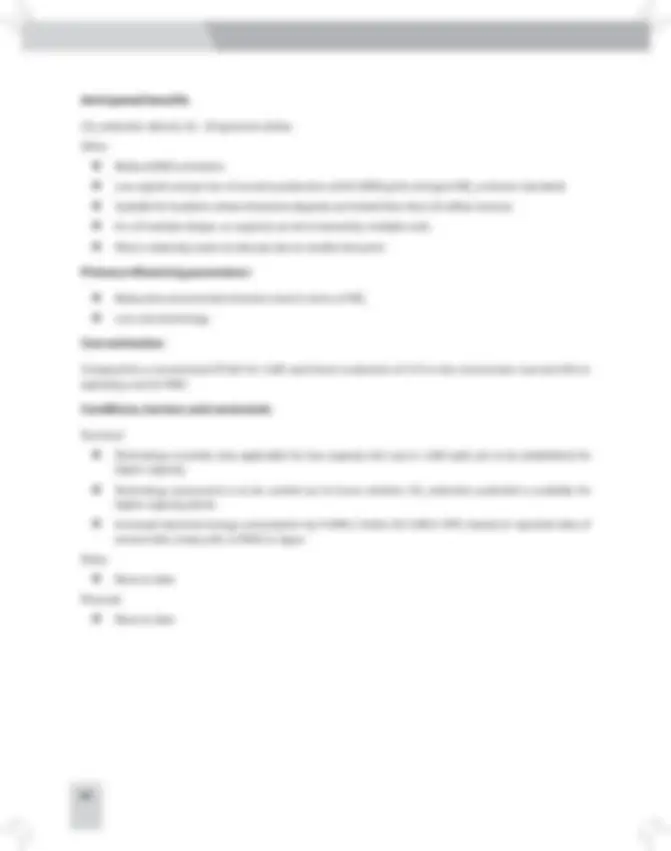
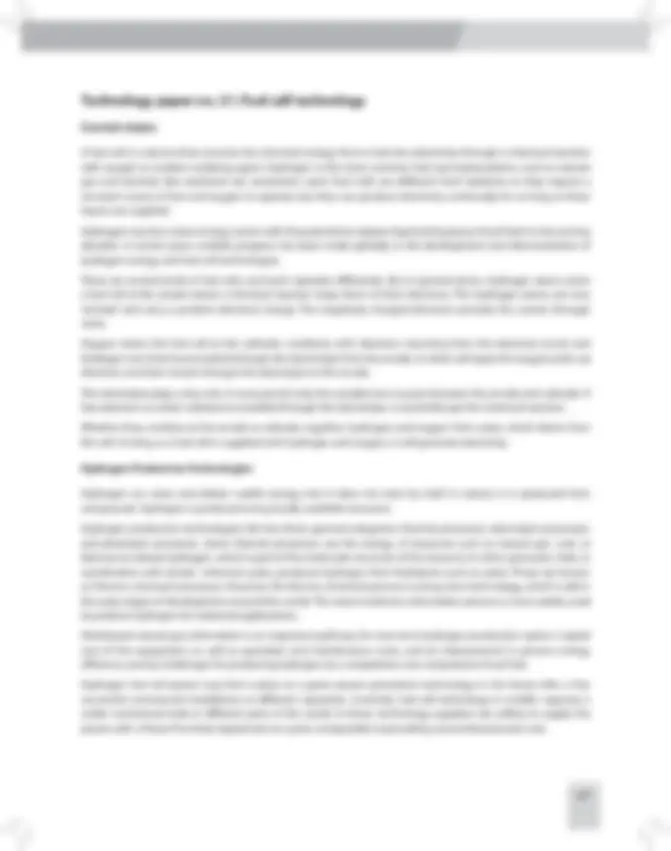
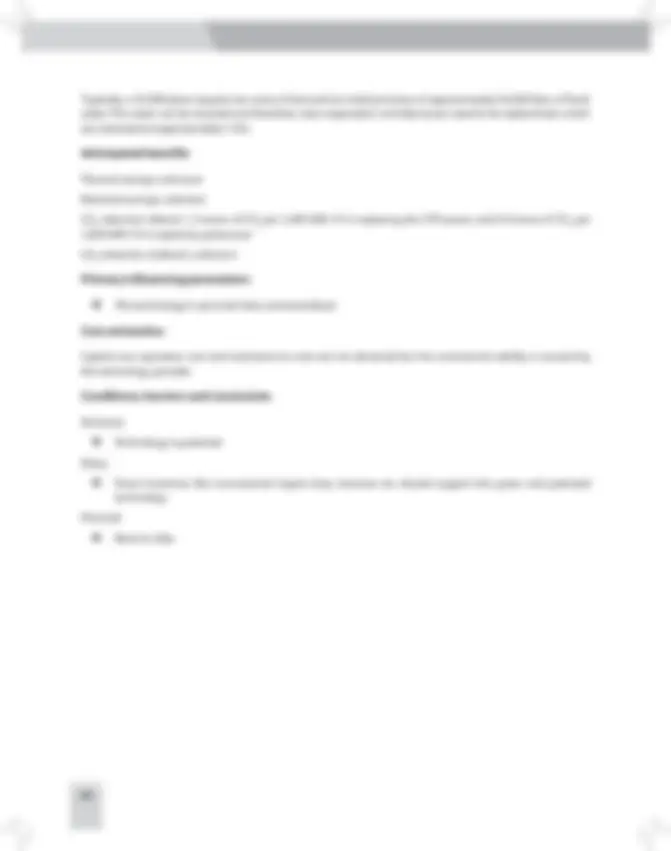

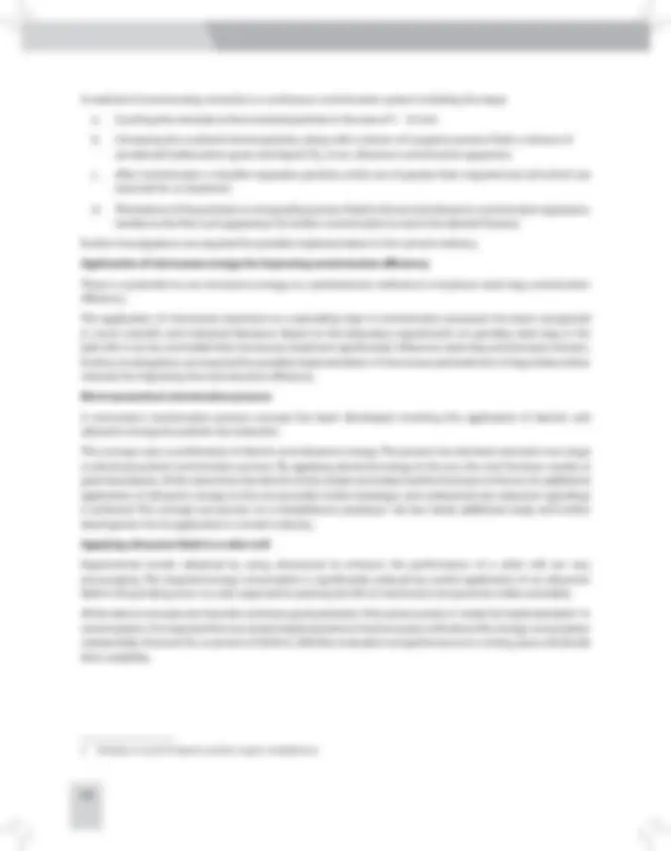
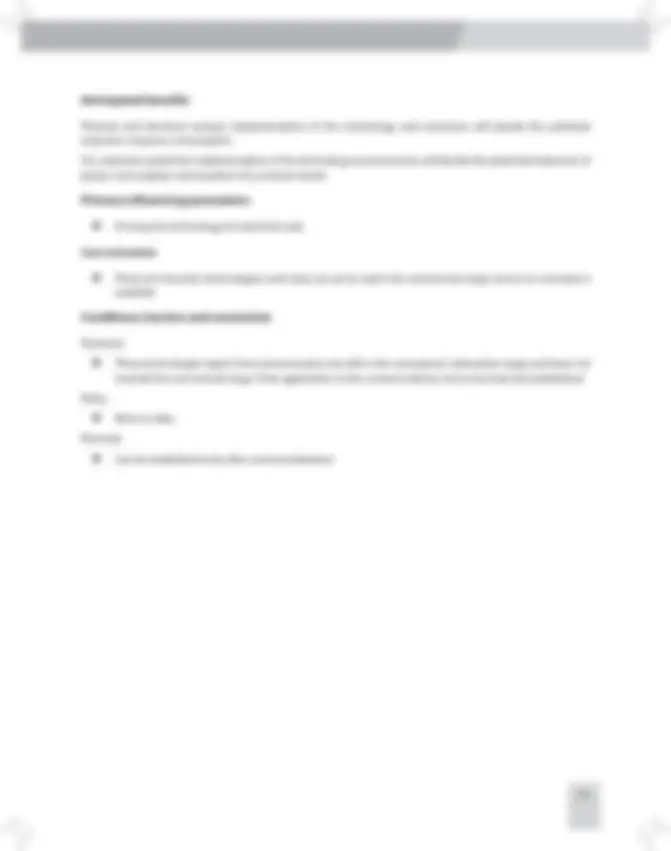
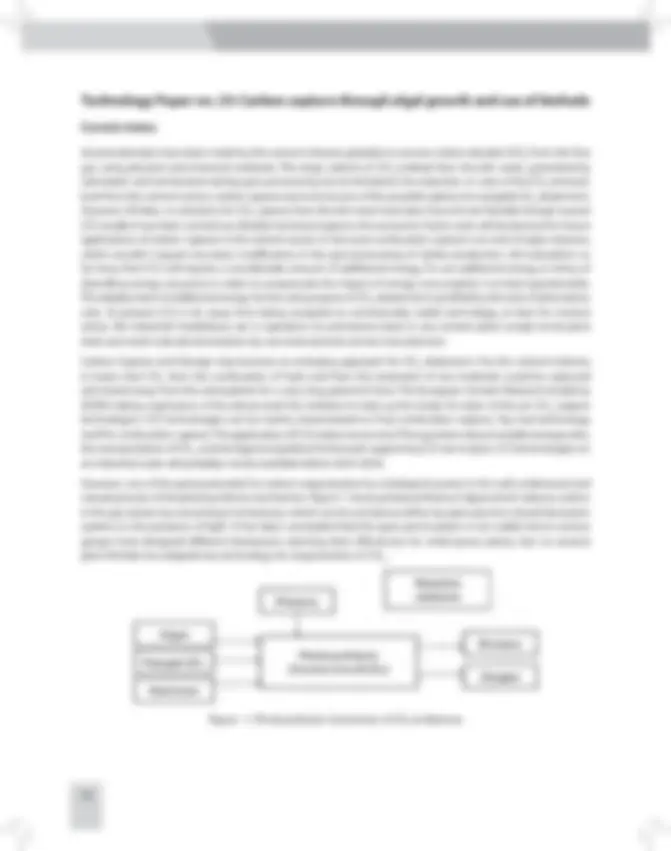
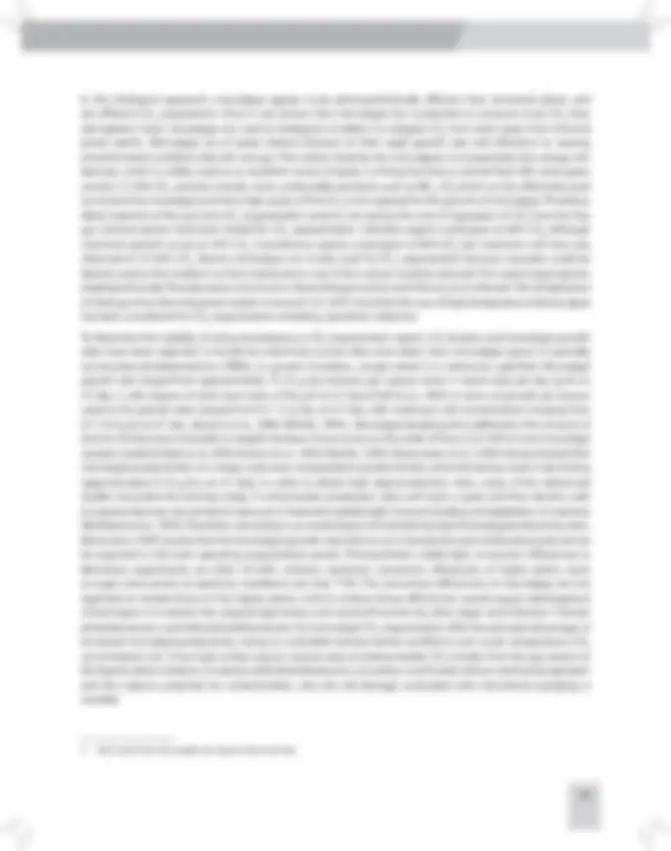
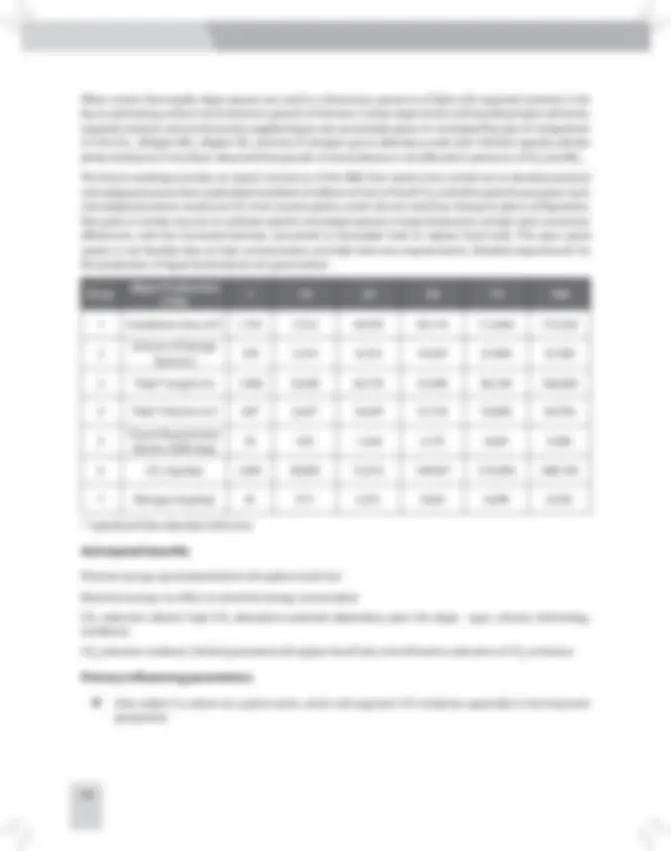
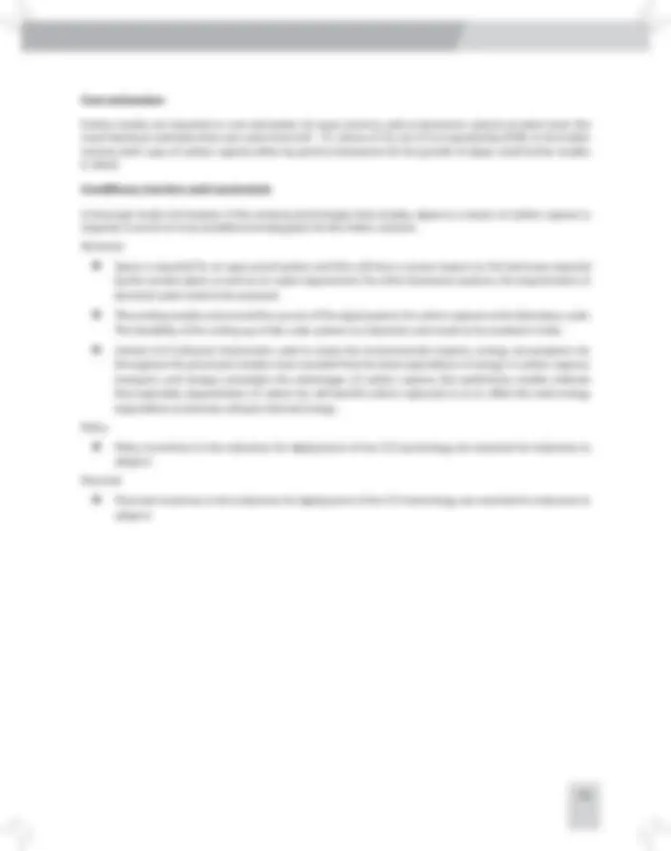
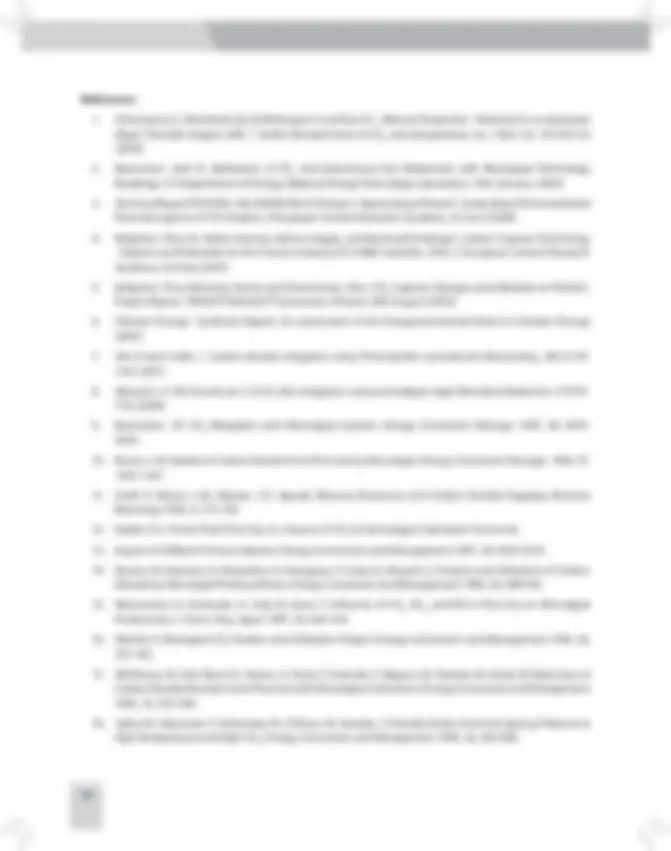
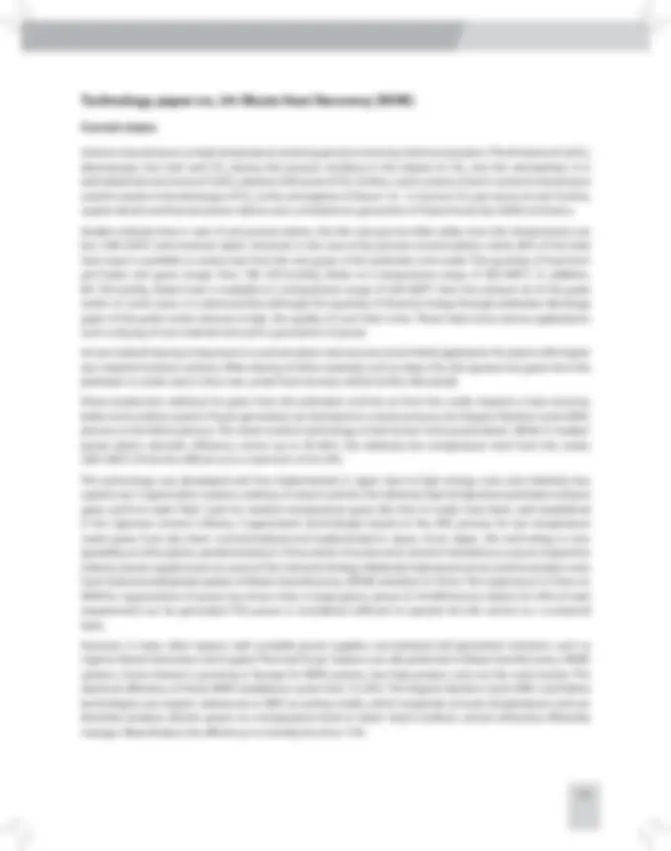
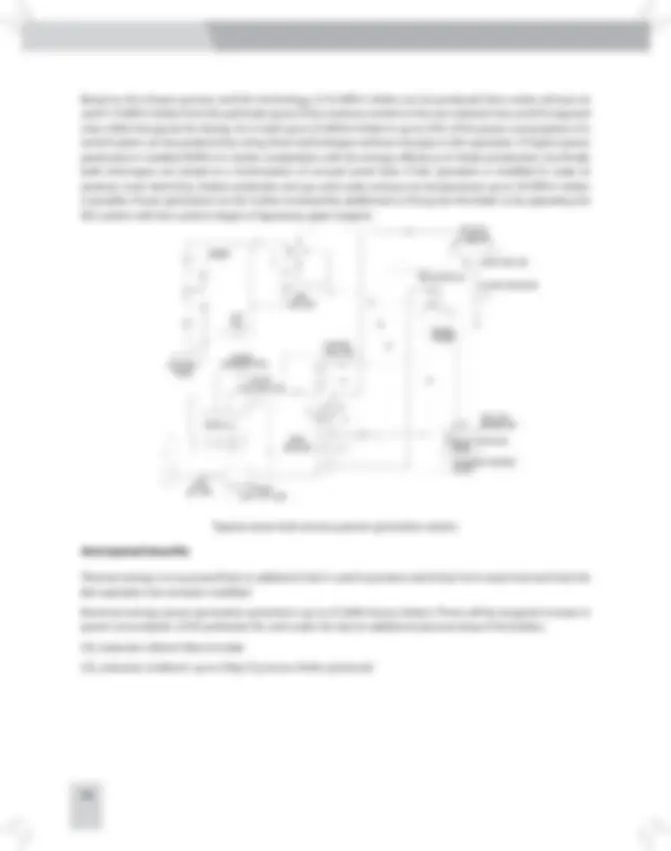
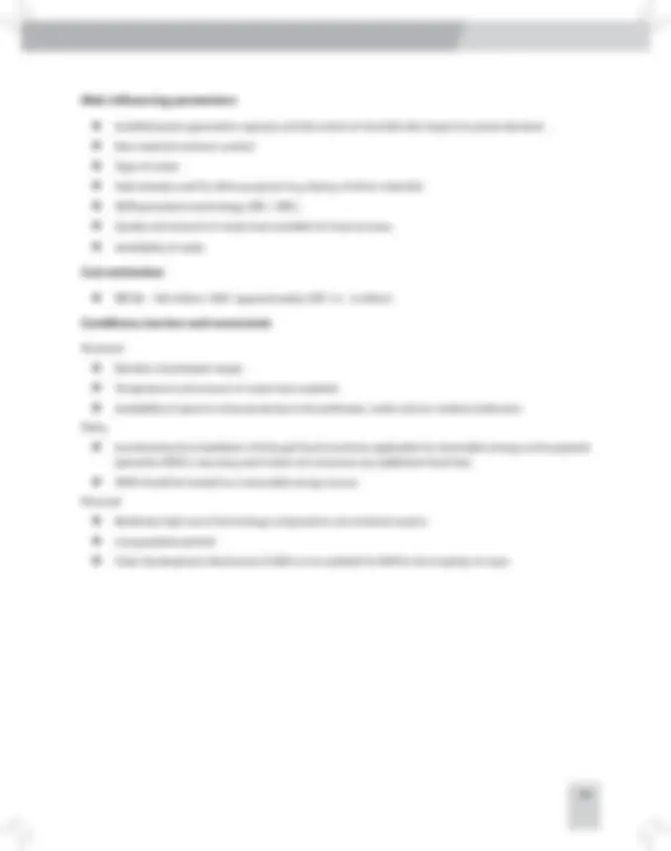
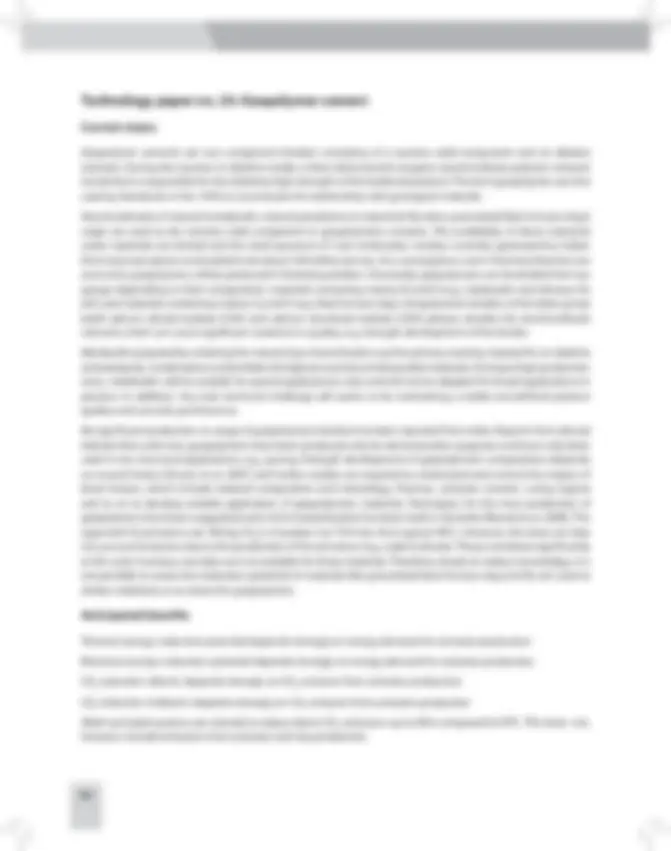
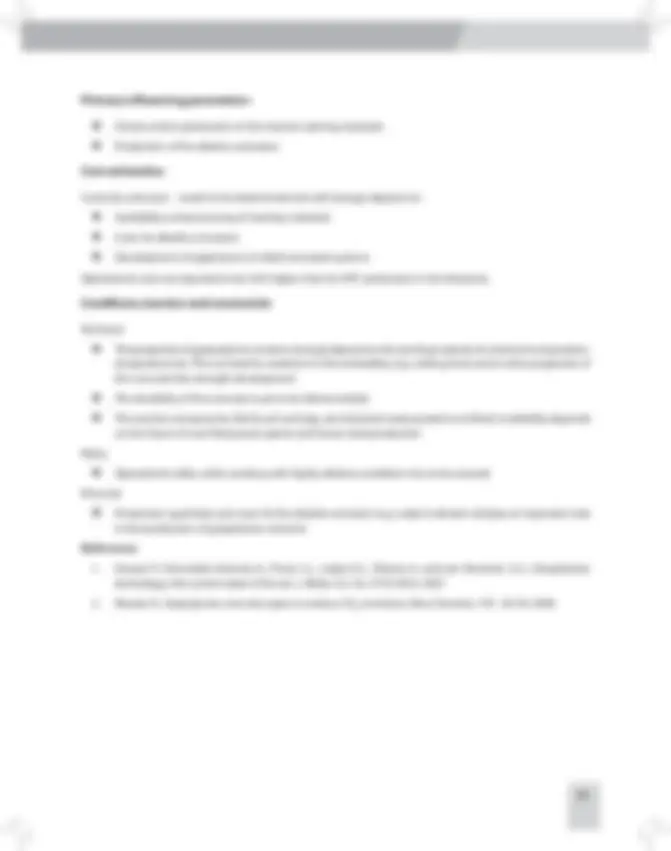
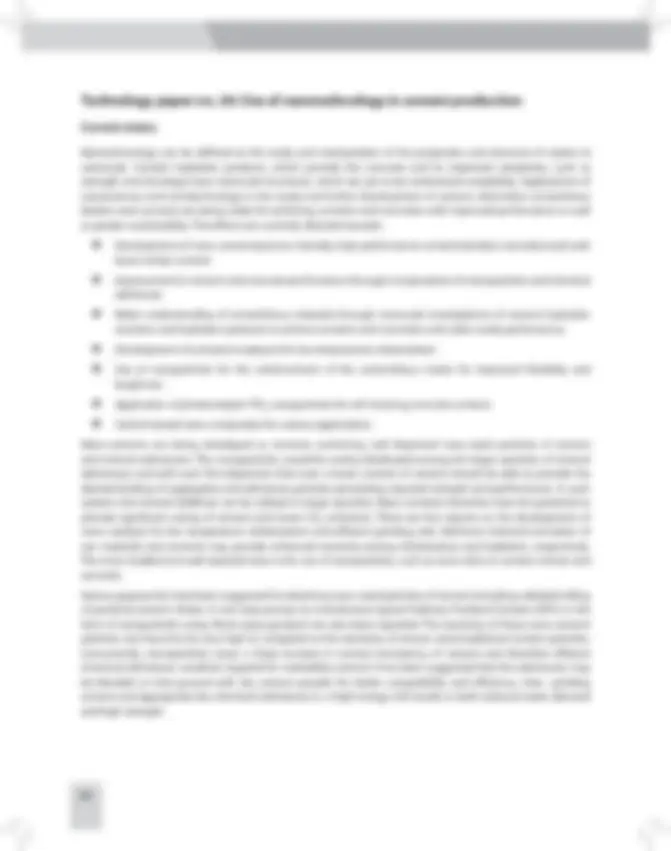

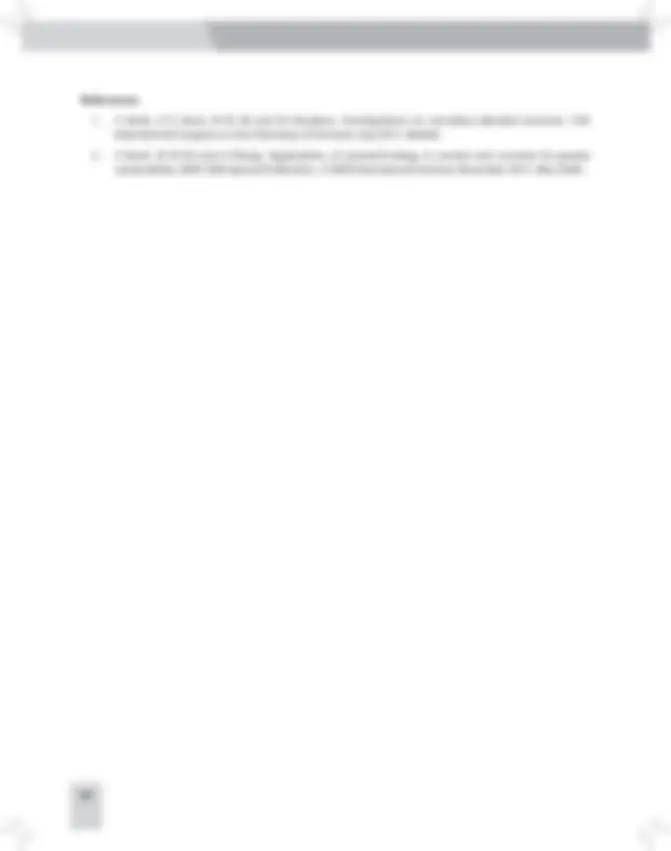
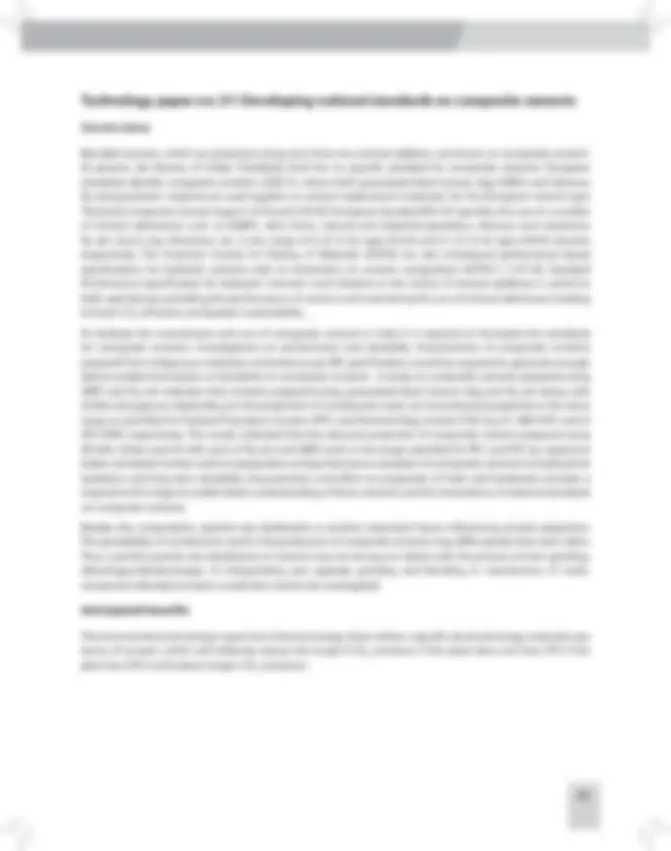
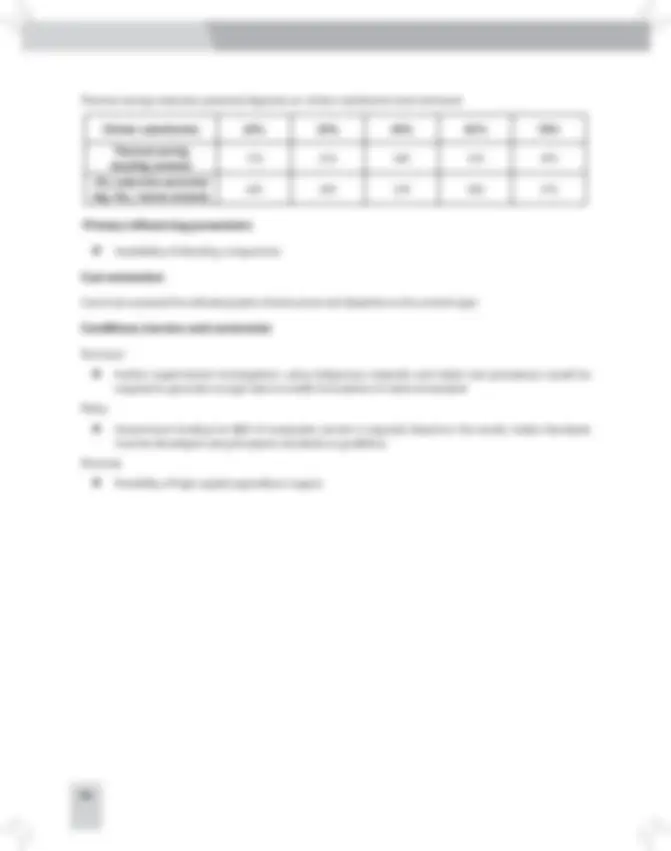
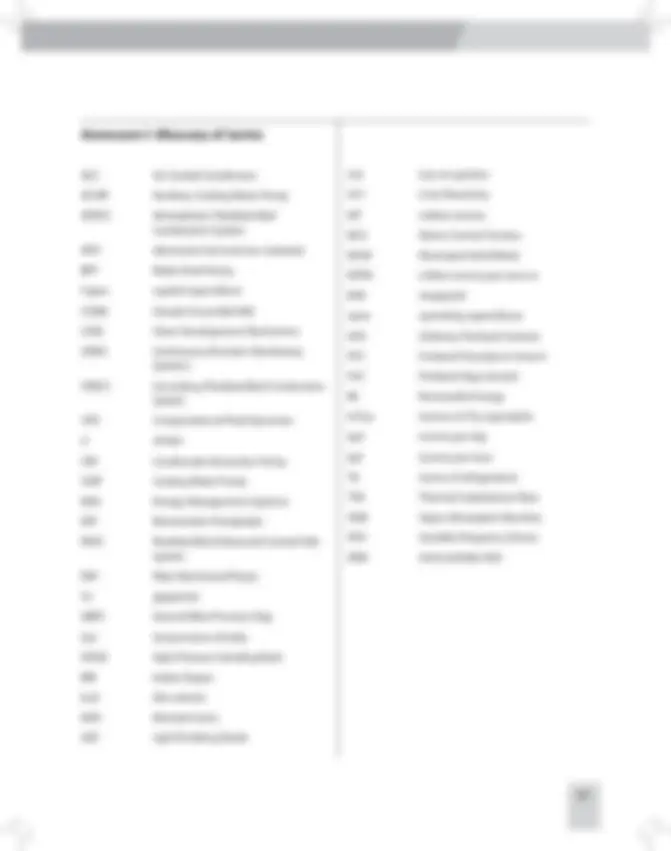
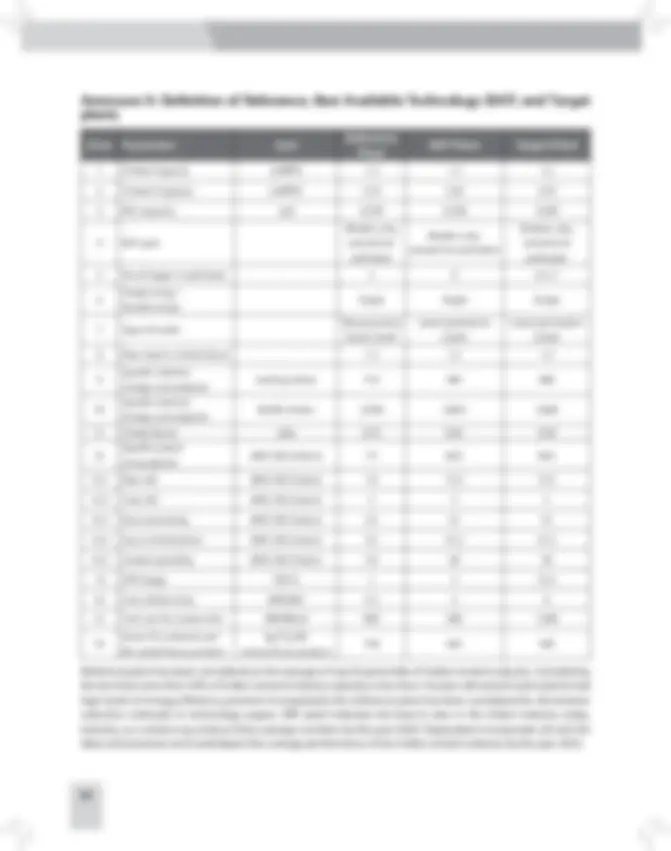
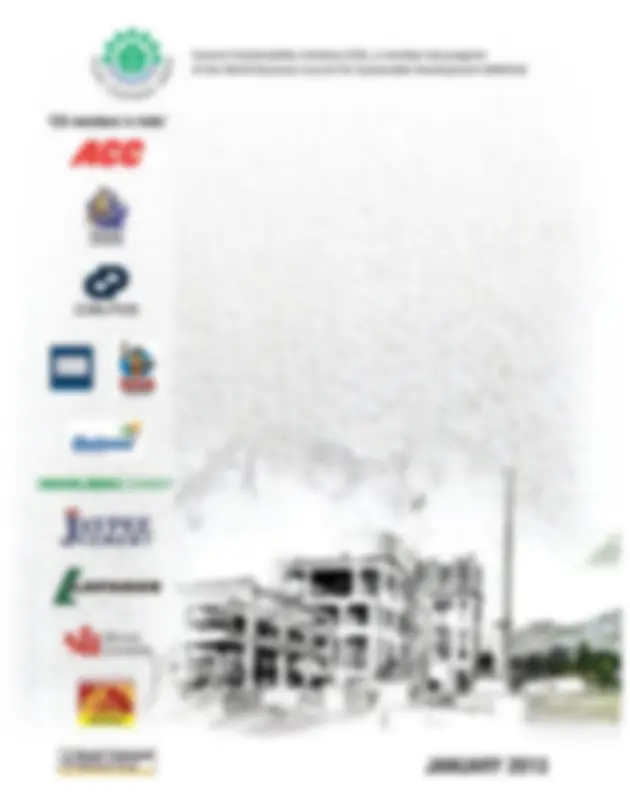
Study with the several resources on Docsity
Earn points by helping other students or get them with a premium plan
Prepare for your exams
Study with the several resources on Docsity
Earn points to download
Earn points by helping other students or get them with a premium plan
Community
Ask the community for help and clear up your study doubts
Discover the best universities in your country according to Docsity users
Free resources
Download our free guides on studying techniques, anxiety management strategies, and thesis advice from Docsity tutors
The potential benefits and challenges of co-processing alternative fuels and raw materials in cement manufacturing. Topics include the impact on clinker quality, energy consumption, early strength development, market acceptance, and the use of de-carbonated raw materials. Technologies such as mineralizers and fuel cell technology are also discussed.
Typology: Exercises
1 / 90
This page cannot be seen from the preview
Don't miss anything!
Annexures ............................................................................................................................................. 87
Annexure I Glossary of terms ............................................................................................................................................... 87
Annexure II Definition of Reference, Best Available Technology (BAT) and Target plants .............................. 88
*To see further papers on the potential of carbon emissions reductions through carbon capture technologies in the cement industry, see ‘Development of State of the Art Techniques in Cement Manufacturing: Trying to Look Ahead’, developed by the European Cement Research Academy (ECRA) in
Authors: Confederation of Indian Industry (CII) lead-authored paper 1 to 12 and paper on Best Available Technologies, and National Council for Cement and Building Material (NCB) lead-authored paper 13 to 27.
The Cement Sustainability Initiative (CSI) is a global effort by 25 major cement producers with operations in more than 100 countries who believe there is a strong business case for the pursuit of sustainable development. Collectively these companies account for about one-third of the world’s cement production and range in size from very large multinationals to smaller local producers. The purpose of the initiative is to:
( Explore what sustainable development means for the cement industry ( Identify actions and facilitate steps cement companies can take, individually and as a group, to accelerate progress toward sustainable development ( Provide a framework for other cement companies to become involved ( Create the content and context for further stakeholder engagement
To date the CSI remains one of the largest global sustainability programs ever undertaken by a single industry sector. To find out more, visit www.wbcsdcement.org
In India, nine member companies collaborated on the development of these papers. They are: ACC Ltd (project Co-Chair), Ambuja Cements Ltd, HeidelbergCement India Ltd, Lafarge India Private Ltd, My Home Industries Ltd / CRH, Shree Cement (project Co-Chair), Shree Digvijay Cement Co Ltd – Cimpor Group, UltraTech Cement (project Co-Chair) and Zuari Cement. Since the roadmap project began, Dalmia Bharat Cement and Jaypee Cement have has also joined CSI.
The International Energy Agency (IEA) works to ensure reliable, affordable and clean energy for its 28 member countries and beyond. Founded in response to the 1973/4 oil crisis, the IEA’s initial role was to help countries co- ordinate a collective response to major disruptions in oil supply through the release of emergency oil stocks to the markets. While this continues to be a key aspect of its work, the IEA has evolved and expanded to help enable the transition to a sustainable low-carbon energy future. It is at the heart of global dialogue on energy, providing reliable and unbiased research, statistics, analysis and recommendations. www.iea.org
The Confederation of Indian Industry (CII) works to create and sustain an environment conducive to the growth of industry in India, partnering industry and government alike through advisory and consultative processes.
CII is a non-government, not-for-profit, industry led and industry managed organization, playing a proactive role in India's development process. Founded over 116 years ago, it is India's premier business association, with a direct membership of over 8,100 organizations from the private as well as public sectors, including Small and Medium Enterprises (SMEs) and multinationals, and an indirect membership of over 90,000 companies from around 400 national and regional sectoral associations. www.cii.in
CII - Sohrabji Godrej Green Business Centre (CII - Godrej GBC), a division of CII is India's premier developmental institution, offering advisory services to the industry on environmental aspects and works in the areas of green buildings, energy efficiency, water management, environment management, renewable energy, green business incubation and climate change activities. www.greenbusinesscentre.com
National Council for Cement and Building Materials (NCB) is an apex R&D organization functioning under the administrative control of Department of Industrial Policy and Promotion (DIPP), Ministry of Commerce and Industry, Government of India (GoI). NCB, in the service of the nation, is devoted to technology development and transfer, testing and calibration, human resource development and consultancy services for the benefit of Cement and Construction Industry for the last about 50 years. Its multi-disciplinary activities are performed in an integrated and coordinated manner through its two larger units located at Ballabgarh (near Delhi) and Hyderabad (Both ISO: 9001-2008 Certified) and the third unit at Ahmedabad, guided by the six corporate centers. www.ncbindia.com
IFC, a member of the World Bank Group is the largest global development institution focused exclusively on the private sector. We help developing countries achieve sustainable growth by financing investment, providing advisory services to businesses and governments, and mobilizing capital in the international financial markets. In fiscal 2011, amid economic uncertainty across the globe, we helped our clients create jobs, strengthen environmental performance, and contribute to their local communities - all while driving our investments to an all-time high of nearly $19 billion.
For more information, visit www.ifc.org
To grow opportunities for the underserved, IFC in South Asia has concentrated on low-income, rural, and fragile regions while building infrastructure and assisting public-private-partnerships; facilitating renewable energy generation; promoting cleaner production, energy and water efficiency; supporting agriculture; creating growth opportunities for small businesses; reforming investment climate; encouraging low-income housing; and making affordable healthcare accessible.
Through these strategic interventions in the region, IFC aims to promote economic inclusion at the base of the pyramid, particularly in the low income states of India; help address climate change impacts; and encourage global and regional integration including promoting investments from South Asia into Africa. In South Asia, IFC works in low-income and frontier regions where our work results in quick outcomes and strong impacts. To promote inclusive growth at the base of the pyramid, we built on previous years experiences to engage in working with the private sector in the region to develop measures that will increase incomes for the poor and small businesses.
IFC tries to support projects that are difficult in nature, first of its kind and reform oriented. We are increasingly being engaged by governments when they see we bring unique knowledge, experience and access to a wide network of investors, and sector expertise.
IFC's Sustainable Business Advisory promotes sustainable business practices specifically among firms in infrastructure, extractive industries, manufacturing, agribusiness, and services sectors. We offer these programs to companies to promote sustainable management and investment practices to create value and growth while addressing climate change through encouraging mitigation and building resilience. IFC's Resource Efficiency teams work with firms to save costs, prevent waste, and reduce green house gas emissions through more efficient use of energy, water, and materials. At the sector level, we promote broader adoption of good practices through case studies and benchmarking energy, water, and material use.
The Indian cement industry, the second largest after China, has achieved an installed capacity of around 300 million tonnes (2011) and is anticipated to reach 320 million tonnes by 2012 and 600 million tonnes by 2020. With 99% of the installed capacity using dry process manufacturing, the Indian cement industry has been adopting latest technologies for energy conservation and pollution control as well as online process and quality control based on expert systems and laboratory automation.
On the energy conservation front, the best levels achieved by the Indian cement industry, at about 680 kcal/kg clinker (cli) (2.85 GJ/ton clinker) and around 66 kWh per tonne cement, are comparable with the best achieved levels in the world. However, a large number of plants installed before the 1990s are operating at relatively high energy consumption levels. Although some of these legacy plants have been modernized to a limited extent by retrofitting new technologies, they should, on priority, bring their energy consumption levels closer to the best achieved levels in the industry by further modernization and adoption of best available processes and technologies.
On the technological front, India’s cement industry has largely adopted the state-of-the-art manufacturing technologies. However, systems for cogeneration of power through waste heat recovery and technologies for low NOx and SOx emissions have not penetrated significantly.
The industry’s efforts towards emissions control, preservation of ecology and voluntary initiatives, such as Corporate Responsibility for Environmental Protection (CREP) are laudable. The Indian cement industry deserves commendation for its long-standing efforts towards reduction of its carbon footprint by adopting the best available technologies and environmental practices. This is reflected in the industry’s achievement of reducing CO₂ emissions to an industrial average of about 0.719 tonne CO₂ per tonne of cement (direct and indirect emissions from Scope I and Scope II) from a substantially higher level of 1.12 tonne CO₂ in 1996.
The initiatives adopted by the Indian cement industry towards utilization of secondary materials are evident from the fact that production of blended cements (Portland Pozzolana Cement (PPC) and Portland Slag Cement (PSC)) in the country in the year 2010-11 was as high as 67%, as against only 36% in 2000-01. India’s cement industry annually consumes around 45 million tonnes of fly ash from thermal power plants, as well as consuming the entire quantity of around 10 million tonnes of granulated blast furnace slag generated by steel plants in the country.
The cement industry has also sharpened its focus on the utilization of alternative fuels by increasingly using newer industrial, municipal and agricultural wastes. There is a substantial scope to enhance waste utilization, particularly hazardous and combustible wastes, and the industry is soon expected to achieve international best practices of waste utilization.
Possibilities of implementation of the technologies covered in these technical papers will depend on existing plant technology, layout and site constraints. The extent of reduction by implementing these technologies will also depend on several influencing parameters such as availability and quality of AFR, raw materials properties, etc. Therefore all the technical papers may not be applicable to any given facility. The maximum greenhouse gas emission reduction potential of each lever is only indicative and may or may not be fully achievable for all facilities. Therefore simply adding up the reduction potential of each technology in order to calculate total potential may not be appropriate
Best Available Technologies (BAT) for a modern cement plant
India is the world’s second largest cement producing country after China. In 2000, the country’s annual capacity was around 120 million tonnes, and, a decade later in 2011, it is estimated to be around 300 million tonnes. This shows a cement capacity growth rate of approximately 10% every year. The Indian cement industry is far more advanced than many other countries in specific energy consumption in both thermal and electrical energy (energy use per unit of production). (Best achieved numbers being 680 kcal/kg of clinker (2.85 GJ/ton clinker) and 66 kWh / tonne of cement). Many plants have already retrofitted or have chosen a better design at the commissioning stage itself, thereby creating a better platform for enhancing energy efficiency. For a modern cement plant with the best available technology, the following features have to be taken into consideration:
For medium and soft materials, a surface miner with single stage impact crusher and wobblers can be chosen, whereas for hard materials, conventional mining with two-stage crushing can be selected. Advanced mining with mine plan software would result in reduced raw material additives, over-burden handling and enhanced mine life. Overland conveyors to transport crushed limestone will be beneficial for long distance transport between mines and plants.
Other mine management measures are the installation of mobile crushers for productivity improvement, and radio controlled mines machinery monitoring system for better control and optimization.
Stacker and reclaimer with higher blending ratio (of 10:1) can be adopted by design.
( For limestone with a moisture content of more than 5% and hardness classified as medium to soft, Vertical Roller Mills (VRM) with the latest generation classifier are being installed with the following: ( Mechanical recirculation system ( High efficiency fans with High Tension (HT) Variable Frequency Drive (VFD) ( Automatic sampler and cross-belt analyzer in the mill feed for better quality control ( Adaptive predictive control for mill operation
For limestone with low moisture content (less than 3%), roller press with separator in finished mode can be installed with the following:
( High efficiency separators and cyclones ( Automatic sampler and cross-belt analyzer in the mill feeding for better quality control ( Adaptive predictive control for mill operation
( Continuous blending silo with high blending ratio (10:1) ( Mechanical conveying system for all material transport ( For silo extraction, gravimetric feeding system for all fine material with an accuracy of over 1%
1 In India, 'Mine' refers to both open cast / surface mine (in Europe, this is 'quarry') and underground mine
Technical paper no.1: Electrical and thermal energy efficiency improvements in kilns and preheaters
Kiln and preheater system in Indian cement industry has achieved very high levels of technology adoption and energy efficiency levels. With significantly higher productivity levels and installation of latest energy efficiency and automation control devices, these systems are operating at one of the best performance measures in the world.
India’s modern cement plant is equipped with six stage (or five stage in certain clusters having higher moisture levels in limestone) preheater with in-line or separate-line calciner (depending on the rated kiln output), kilns with volumetric loading of about 5--6.5 tpd/cu.m and advanced automation systems. Continuous Emission Monitoring Systems (CEMS) are also being increasingly adopted in new as well as existing kilns. However, while the productivity levels of existing kilns have been increased to meet growing demand, enhanced energy consumption due to increased velocity resulting in higher pressure drop and reduced heat transfer offers potential areas for improvement.
The installation of high efficiency (and low pressure drop) cyclones offers significant energy efficiency improvement opportunity in cement kilns. With several design innovations, a six-stage preheater system offers pressure drop of about 300 mmWC in latest designs. For existing plants, installation of additional preheater stages (wherever civil structures permit from 4/5 stages to 6/7 stages) for increased heat recovery and computational fluid dynamics (CFD) studies for reducing the pressure drop in preheater cyclones, along with necessary modifications offer further electrical and thermal energy efficiency improvement opportunities.
With several advancements in refractory properties, such as thermo-mechanical and alkali resistance, cement kilns today can minimize the radiation losses as well as handle increased AFR substitution rates. The kiln main drive is also undergoing substantial improvements with better gears and lubrications system. Automation and control systems, such as adaptive-predictive control systems and online control systems for flame, free-lime, inlet NOx are very effective for better throughput, smooth operation and control.
Oxygen enrichment as an option for energy efficiency (by reducing the combustion air requirements) as well as increased alternative fuel utilization (for kiln firing fuels, by providing better flame temperature and ensuring complete combustion) can offer significant energy efficiency, as well as assist in increased substitution rates. Higher investment costs for installing oxygen separation system from air, storage and handling systems and the related safety issues are the deterrents, affecting the economics of increased adoption of oxygen enrichment in the Indian cement industry today.
Technical
( Layout constraints/civil structural capability for stage addition ( High moisture limestone restricts the number of stages in the preheater ( Burnability of raw mix
Policy
( India’s stringent environmental norms, necessitating installation of additional equipment, might increase future energy consumption ( Logistics/availability and quality concerns of coal, and quality concerns of raw materials and power among others
Financial
( Longer shutdown time for major modifications ( Extended return on investments for certain initiatives, if only energy efficiency benefits are taken into account ( Higher investment and operating costs for oxygen enrichment
Technical paper no. 2: Latest generation high efficiency clinker coolers
The Indian cement industry, over the last several years, has increasingly adopted reciprocating grate coolers with great success. While rotary coolers have been completely phased out, several installations with planetary coolers are still in vogue. With more than 50% of cement produced from kilns less than 10 years old, reciprocating grate coolers have become common practice in the industry today, with cooler loading of about 45–50 tpd/square metre (m 2 ) of cooler area. Enthalpy from hot clinker is recovered to preheat the incoming secondary and tertiary air to improve thermal efficiency. Based on the cooling efficiency, technology adopted, and desired clinker temperature, the amount of air used in this cooling process is approximately 2.5–3 kg/kg of clinker.
Conventional grate coolers provide a recuperation efficiency of 50–65%, depending on the mechanical condition and process operation of the cooler. This corresponds to a total heat loss from the cooler of about 120–150 kcal/ kg clinker. Several cement kilns in India, as a result of continuous productivity increase measures, are operating at significantly higher cooler loading range than rated, with a range of 50–65 tpd/m² of cooler area; increasing the total heat loss from the cooler.
The reciprocating cooler has undergone significant design developments; the latest generation clinker coolers offering better clinker properties, and significantly lower exit gas and clinker temperatures. As a direct consequence, secondary and tertiary air temperatures offered by latest generation coolers have also increased to about 1,250⁰C and 1,000⁰C, respectively. The cooling air requirements of such coolers have also gradually reduced to about 2. –2.4 kg/kg clinker.
While it is very attractive to adopt latest generation coolers for new plants by design, retrofitting existing conventional reciprocating coolers with latest generation coolers also offers a significant potential for electrical and thermal energy saving in the Indian cement industry. The total heat loss of latest generation clinker coolers is less than 100 kcal/kg clinker, and has a recuperation efficiency in the range of 75–80%.
Future technologies under development
With increasing thermal efficiency in the kiln and preheater system, it is necessary for clinker coolers to be capable of supplying reduced secondary and tertiary air volumes with higher recuperation efficiency. Several improvements in clinker cooler technology in terms of better air distribution for reduced cooling air requirement, effective conveying system for better transport of clinker and mechanical stability of cooler, optimum under-grate pressure and heat shields, are under development. Vertical shaft coolers with recuperation efficiencies of more than 80% are under development which could further result into specific heat and CO₂ reduction. The Indian cement industry can therefore expect further reductions in cooler heat loss and increased energy efficiency.
Thermal savings: 10–30 kcal/kg clinker
Electrical savings: 0–1 kWh/mt clinker
CO₂ reduction potential (direct and indirect): 8–10 kg CO 2 /mt clinker
Technical paper no. 3: Energy efficiency in grinding systems
Material grinding is the largest electrical energy consumer in cement manufacture. Therefore the Indian cement industry, where energy costs contribute to a majority share in overall cement manufacturing costs, has adopted the most energy efficient technology for its grinding requirements.
For raw material grinding, the most commonly used grinding technology is Vertical Roller Mills (VRM), while few older facilities still operate with either ball mills alone or ball mills with pregrinder (the most commonly used pregrinder is the mechanical crusher). Coal grinding has also gradually shifted to VRM use, while a few older facilities still operate with air-swept ball mills. With an increased use of petroleum coke and imported coal and, therefore, enhanced coal fineness requirements, VRMs are gradually becoming the most preferred option for coal mills.
India’s cement grinding uses has multiple grinding systems: ball mills; ball mills with pregrinder (the commonly used pregrinders are High Pressure Grinding Rolls (HPGR) followed by vertical mills as a pregrinder to ball mills); VRM for clinker grinding and, in certain grinding locations, ball mills and VRM (grinding clinker and additive materials separately and blending).
The newest plants in the Indian cement industry (installed in the last 10 years and contributing over 50% of cement manufacturing capacity) have VRM for raw material and coal grinding and VRM/ball mill with HPGR for cement grinding.
The selection of grinding mill type depends mostly on the moisture content and material hardness. VRM, widely accepted for the combined drying and grinding of moist raw materials and coal and for low energy consumption, has been widely used for all three grinding requirements. Several improvements in design and operation of the mill and other equipment in the grinding circuit are resulting in less energy consumption and improved reliability.
The introduction of an external re-circulation system for material, adjustable louvre ring, latest generation classifier and modification of mill body to improve the air and material trajectories are examples of such changes which increase throughput and improve energy efficiency.
While VRM has been the preferred option for raw material and coal grinding, clinker grinding still provides several options for Indian cement manufacturers. The closed circuit ball mill with high efficiency separator is the most common type of clinker grinding system used. A comparative analysis of various options available for cement grinding compared to a closed circuit ball mill is provided below:
Comparative analysis
Closed Circuit Ball Mill (CCBM)
Semi finish grinding – ball mill and HPGR pregrinder
HPG finish mode VRM
Impactand attrition with the grinding balls
Compression in RP. Attrition in ball mill
Compression Compression
90% passing 25 mm sieve
Up to 2 times the gap width
Up to 2 times the gap width Up to 75 mm
Air flow requirement Low Low Low High
No. of auxiliary equipment More More Less Less
Maintenance Low High High Medium
Expected specific power consumption, kWh/t OPC @ 3,400 cm²/gm
Thermal savings: nil
Electrical savings: 6 – 10 kWh/mt cement
CO₂ reduction (indirect): 7 – 12 kg CO₂/mt cement
( Material (raw material, coal and clinker) properties ( Output size requirement (fineness and particle size distribution and so on) ( Material science and grinding technology ( Durability of construction material (reliability and maintenance, among others)
Since cost estimation for individual mills for various grinding requirement is difficult, a typical cost estimate is compared below:
( Ball mill with closed circuit: X (X given as an example unit) ( Vertical roller mill (VRM): 2.3 – 2.5 X (that is to say, 2.3–2.5 times more than ball mill) ( Roller press in finish mode: 1.8 – 2 X (that is to say, 1.8–2 times more than ball mill) ( Roller press with ball mill: 2 – 2.2 X (that is to say, 2–2.2 times more than ball mill)