
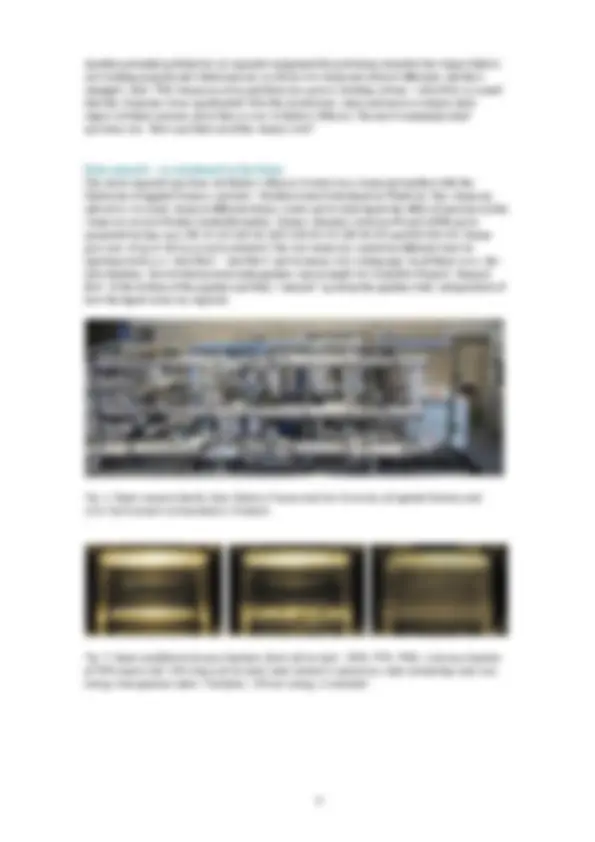
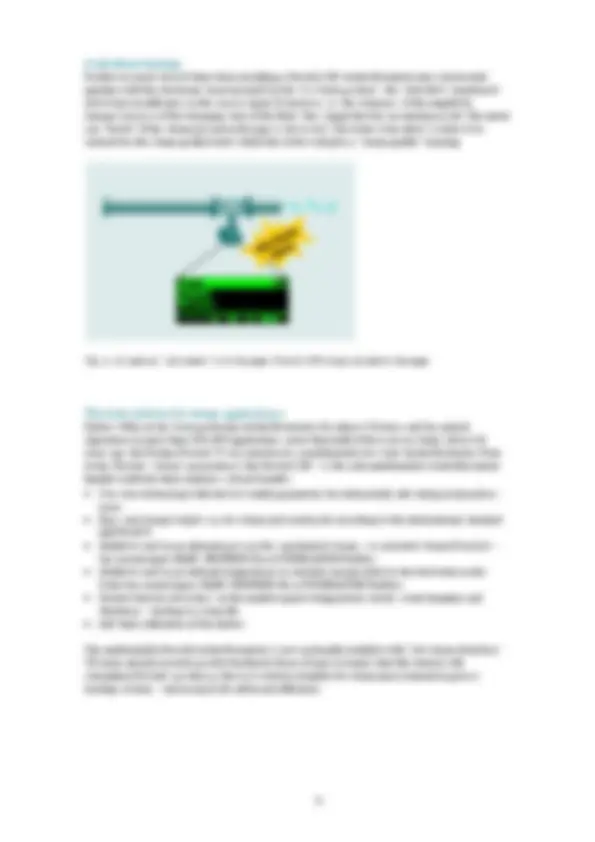
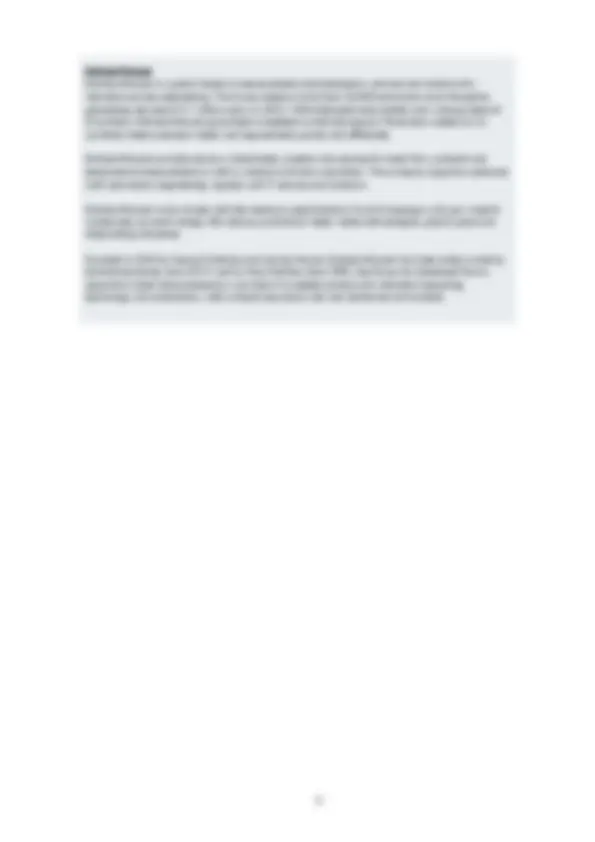
Study with the several resources on Docsity
Earn points by helping other students or get them with a premium plan
Prepare for your exams
Study with the several resources on Docsity
Earn points to download
Earn points by helping other students or get them with a premium plan
Community
Ask the community for help and clear up your study doubts
Discover the best universities in your country according to Docsity users
Free resources
Download our free guides on studying techniques, anxiety management strategies, and thesis advice from Docsity tutors
Endress+Hauser's new Proline vortex flowmeter family is designed for steam applications and offers multivariable solutions for steam mass and energy measurement. The innovative feature of this flowmeter is the ability to detect wet steam on a continuous basis, which helps increase safety and improve efficiency in steam systems. the challenges of determining the dryness fraction of steam by measuring pressure and temperature alone and discusses the problems caused by wet steam in steam piping and heat exchangers.
What you will learn
Typology: Lecture notes
1 / 5
This page cannot be seen from the preview
Don't miss anything!
Endress+Hauser has recently introduced its new Proline vortex flowmeter family. This highly robust flowmeter has been mainly developed for steam applications, and it offers a broad scope of multivariable solutions for steam mass and energy measurement. An innovation that helps to increase safety and improve the efficiency of steam systems is the new optional feature designed to detect wet steam on a continuous basis.
Oliver Seifert Product Manager, Endress+Hauser Flowtec AG, Reinach (Switzerland)
Steam is commonly used for process heating. Typically, saturated steam is produced in shell and tube (fire tube) boilers. Its advantages are obvious: The heat content is high and temperature can be regulated by controlling pressure. When looking at the properties of saturated steam it can be seen that it is exactly at the border line between liquid water and gaseous steam (vapor).
When dry saturated steam passes on its energy to a process, its “latent” energy is released. This energy can be found in steam tables as enthalpy (hfg). Whilst this energy is released, the steam becomes wetter, i.e. its dryness fraction (x) is reduced from 1 down to 0. What doesn’t change, however, is the combination of pressure and temperature during this process. This means that ideally steam enters a heat exchanger at 3 bar g and +144 °C and condensate can be found at the exit at exactly the same pressure and temperature – but the steam has lost 2138 kJ/kg of latent heat (hf). The problem now is: If both liquid and steam, and any state in-between, can exist at the same pressure and temperature, it is impossible to determine the dryness fraction by just measuring pressure and temperature. Therefore, today there is no solution available to easily determine if water is present in the steam line or not.
Fig.1: Mollier diagram for water. Example: Heating liquid water from 20 °C (A) to 100 °C (B) requires about 4.2 kJ/kg K of energy. In order to convert the water (B) to steam (C) at 100 °C and 1.013 bar abs., 2255 kJ/kg are required (hf). During this process, the dryness (x-factor) is increased from 0 to 1.
Fig. 2: The dryness of steam is defined by the “x-factor”. If x = 0: water is fully saturated. If x = 1, there is dry saturated steam. If x = 0.8, 80% of the mass of water is in a gaseous state and 20% in a liquid state.
Wet steam Heat losses in steam piping, e.g. because of lack of isolation, will lead to a reduced dryness fraction. This wet steam can lead to the following problems: Water hammer/slug flow caused by the water entering the steam line Reduced efficiency of the steam system because wet steam contains less energy than dry saturated steam
If the wet steam is a result of carry-over from the boiler itself, stress corrosion cracking may result. Wet steam, however, is also an issue at the point of end-use. If the condensate trap at the outlet of a boiler does not work, the heat exchanger may drown, thus reducing the heat transfer efficiency drastically.
Fig. 3: Drowned heat exchanger (left) resulting in poor steam quality upstream
A wet steam warning Further research showed that when installing a Prowirl 200 vortex flowmeter into a horizontal pipeline with the electronics head mounted in the “6 o’clock position”, the “river flow” mentioned above had an influence on the sensor signal. Its kurtosis, i.e. the steepness of the amplitude, changes because of the changing state of the fluid. This simple fact has an exciting result: The meter can “decide” if the steam present in the pipe is dry or wet. The device even allows a value to be entered for the steam quality below which the device will give a “steam quality” warning.
Fig. 6: As soon as “wet steam” is in the pipe, Prowirl 200 issues an alarm message.
Endress+Hauser has been producing vortex flowmeters for almost 30 years and has gained experience in more than 300,000 applications; more than half of these are in steam. About 10 years ago, the Proline Prowirl 73 was introduced, a multivariable two-wire vortex flowmeter. Even today, Prowirl – today’s generation is the Prowirl 200 – is the only multivariable vortex flowmeter family worldwide that combines several benefits:
Two-wire technology with the best entity parameters for intrinsically safe wiring in hazardous areas Mass and energy output, e.g. for steam and condensate according to the international standard IAPWS-IF Ability to read in an external pressure for superheated steam – or saturated steam if desired – via current input, HART, PROFIBUS PA or FOUNDATION Fieldbus Ability to read in an external tempertaure to calculate energy added to the feedwater in the boiler via current input, HART, PROFIBUS PA or FOUNDATION Fieldbus Greatest known robustness on the market against temperature shocks, water hammer and vibrations – leading to a long life Life-time calibration of the meters
The multivariable Prowirl vortex flowmeter is now optionally available with “wet steam detection”. We have already received positive feedbacks from several customers that this feature will strengthen Prowirl’s position as the best solution available for steam measurement in process heating systems – increasing both safety and efficiency.
Endress+Hauser Endress+Hauser is a global leader in measurement instrumentation, services and solutions for industrial process engineering. The Group employs more than 10,000 personnel across the globe, generating net sales of 1.7 billion euros in 2012. With dedicated sales centers and a strong network of partners, Endress+Hauser guarantees competent worldwide support. Production centers in 11 countries meet customers’ needs and requirements quickly and effectively.
Endress+Hauser provides sensors, instruments, systems and services for level, flow, pressure and temperature measurement as well as analytics and data acquisition. The company supports customers with automation engineering, logistics and IT services and solutions.
Endress+Hauser works closely with the chemical, petrochemical, food & beverage, oil & gas, water & wastewater, power & energy, life science, primaries & metal, renewable energies, pulp & paper and shipbuilding industries.
Founded in 1953 by Georg H Endress and Ludwig Hauser, Endress+Hauser has been solely owned by the Endress family since 1975. Led by Klaus Endress since 1995, the Group has developed from a specialist in level measurement to a provider of complete solutions for industrial measuring technology and automation, with constant expansion into new territories and markets.