
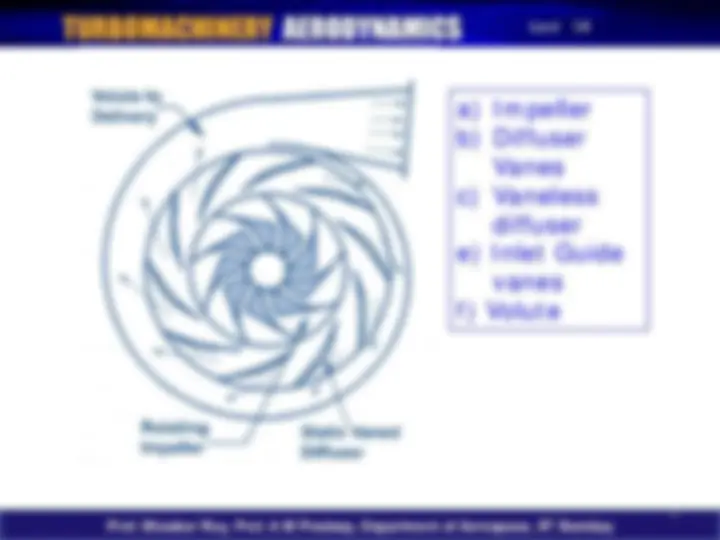
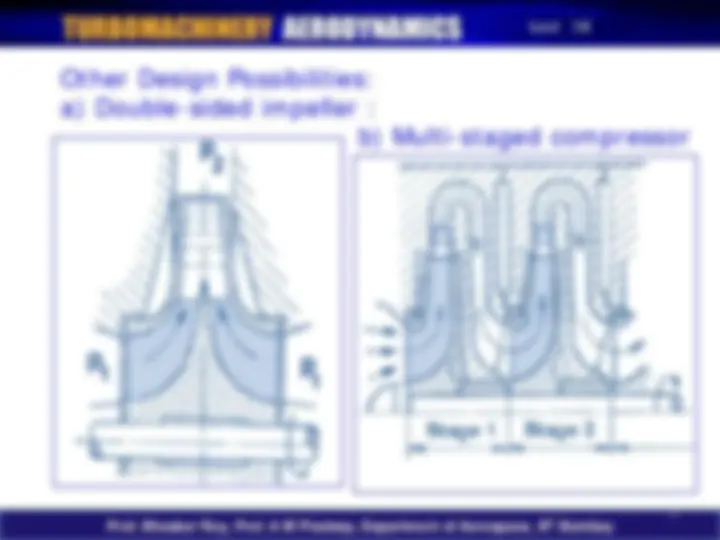
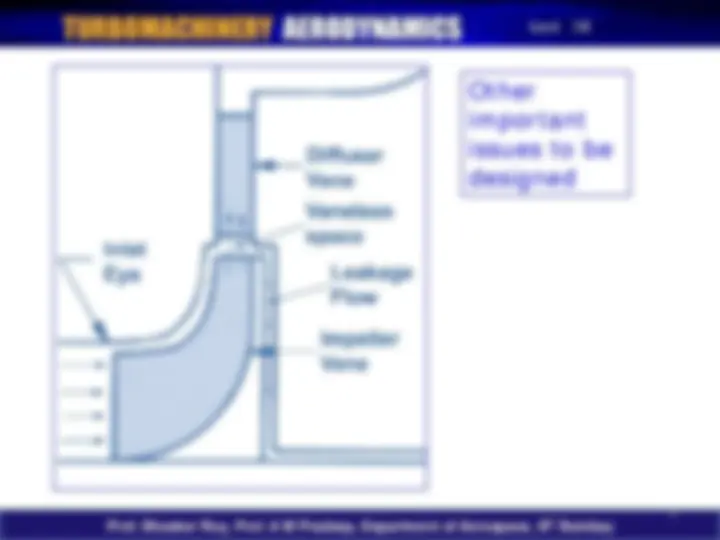
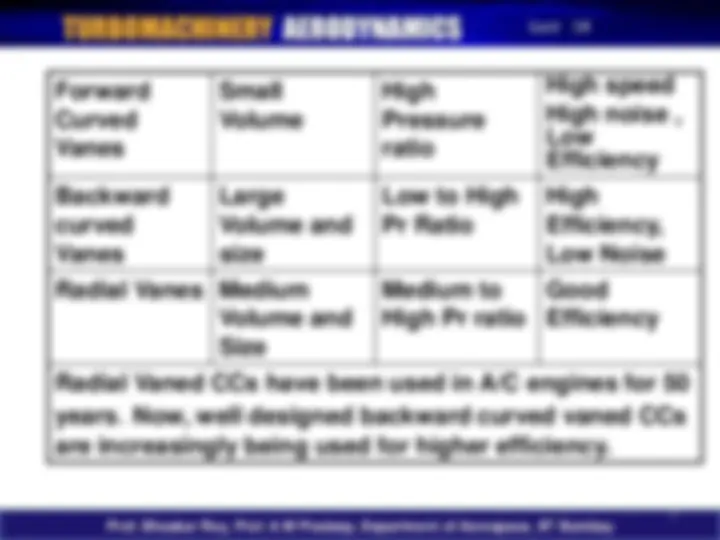
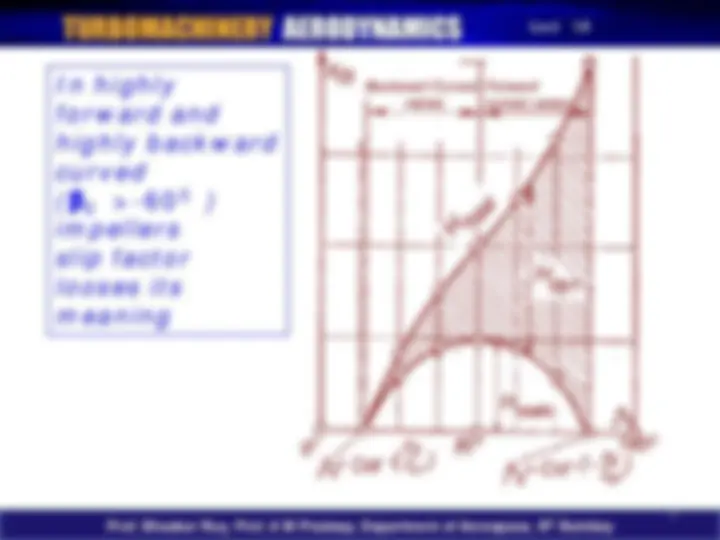
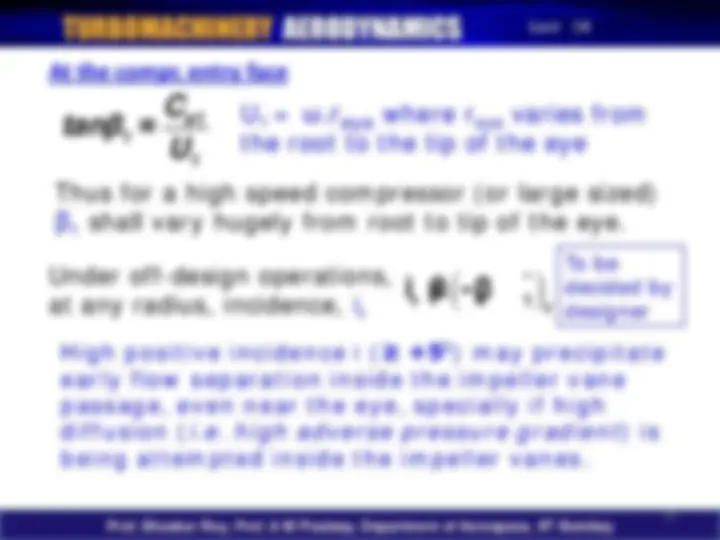
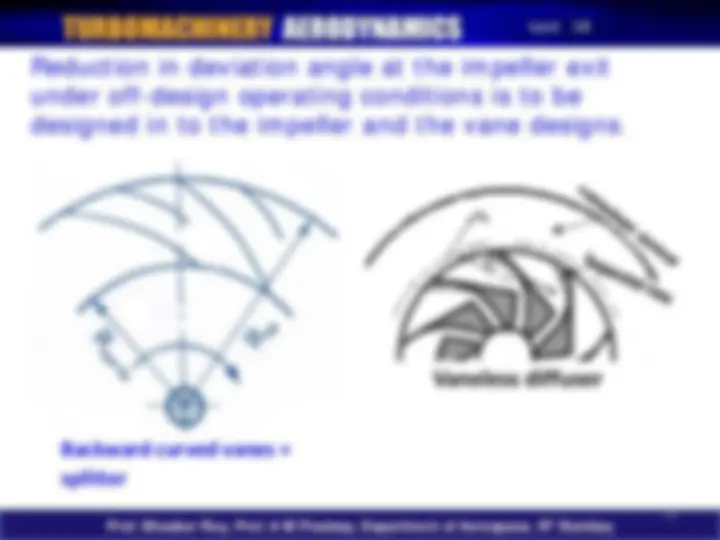
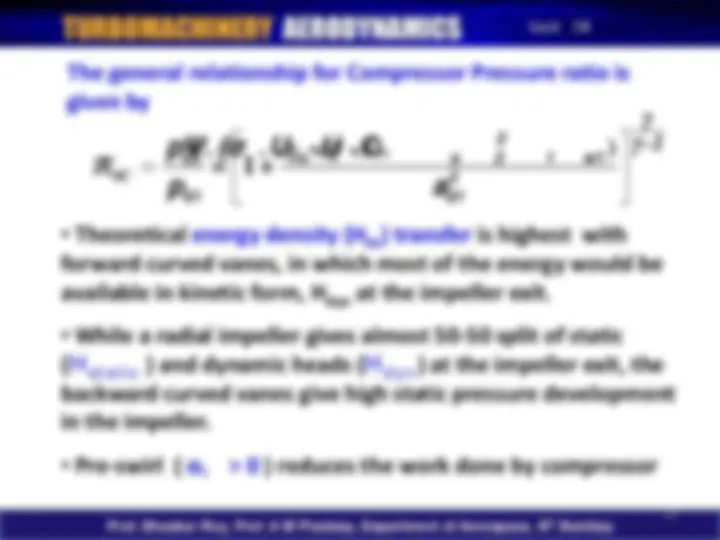
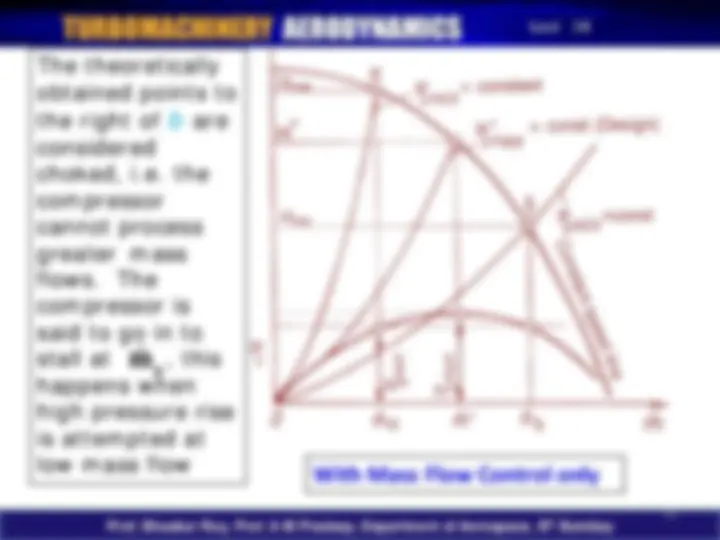
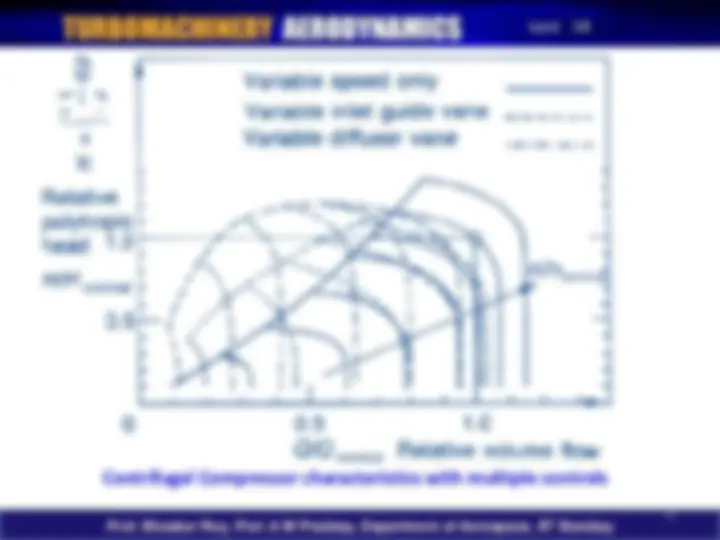
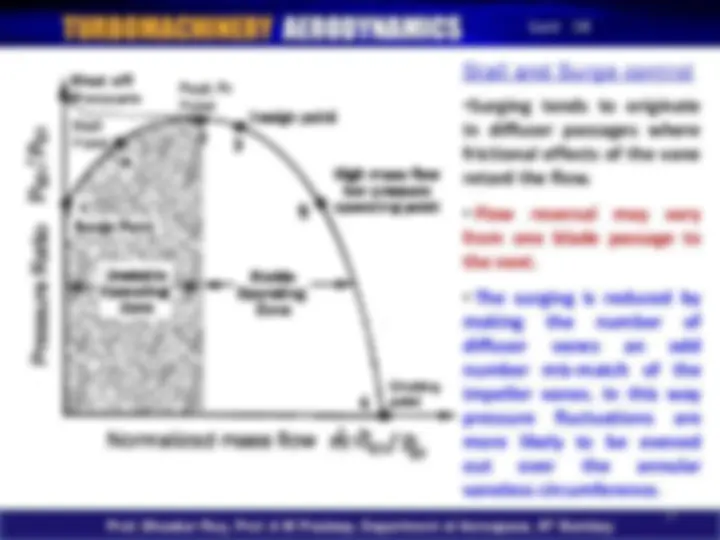
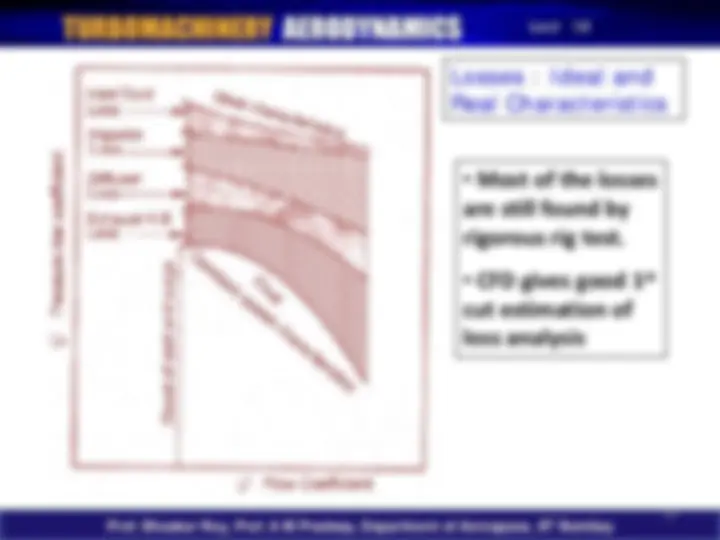
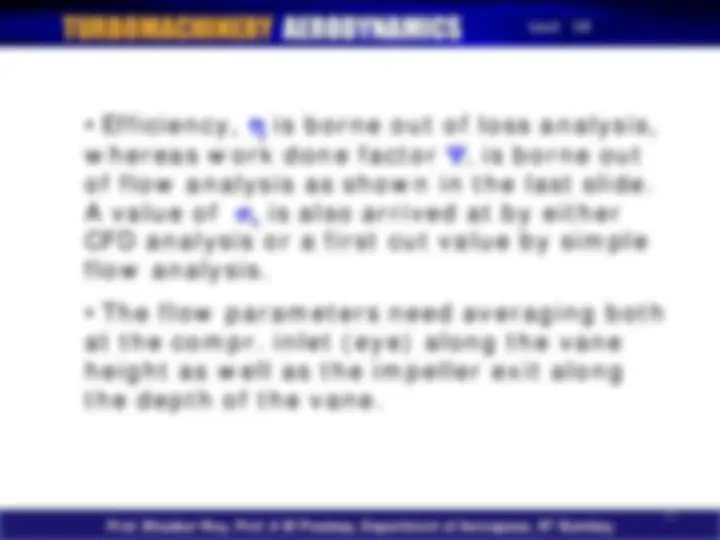
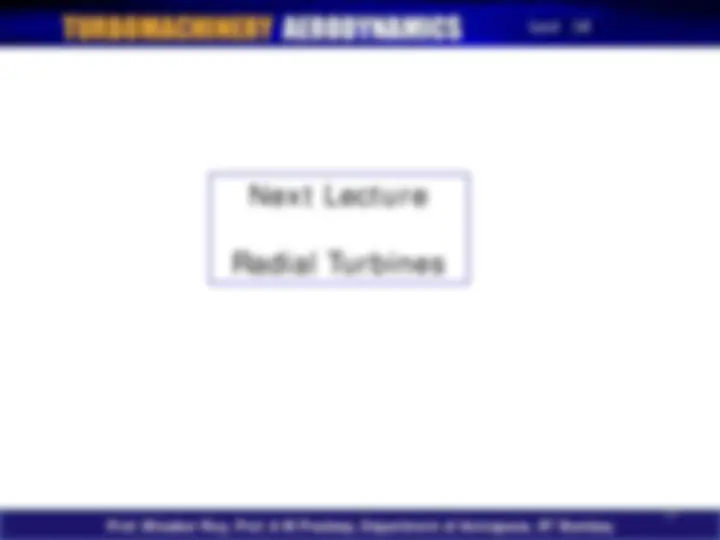
Study with the several resources on Docsity
Earn points by helping other students or get them with a premium plan
Prepare for your exams
Study with the several resources on Docsity
Earn points to download
Earn points by helping other students or get them with a premium plan
Community
Ask the community for help and clear up your study doubts
Discover the best universities in your country according to Docsity users
Free resources
Download our free guides on studying techniques, anxiety management strategies, and thesis advice from Docsity tutors
Some concept of Turbomachinery Aerodynamics are Axial Flow Compressors, Axial Turbine Design Considerations, Blade Performance, Engine Performance Significantly, Flows Through Axial Compresso. Main points of this lecture are: Centrifugal Compressors, Impellers, Diffuser, Vanes, Inlet Guide, Volute, Design Possibilities, Double-Sided Impeller, Multi-Staged Compressor, Velocity
Typology: Slides
1 / 22
This page cannot be seen from the preview
Don't miss anything!
1
Centrifugal Compressors
Design of Centrifugal Compressor elements – Impellers, Vanes etc.
Other Design Possibilities: a) Double-sided impeller : b) Multi-staged compressor
Other important issues to be designed
Slip factor
In a real compressor relative velocity vector V 2 is at angle β 2 because of non-radial exit from the impeller tip as the real viscous flow detaches near the tip from the impeller vane (trailing) surface
0.63.π / N σ = 1 - 1 -. tanβ
s
0.63.π σ = 1- N
Stanitz formula ,
which, for a radial vane,
φ 2 r^2 2
U_**
2
r2 2 σ 1 ( / )cosβ
1 (V /U )
σ 1 ( / )
N
N
π
π
= −
−
= − 2
2 tanβ
cosβ
Wisner’s definition
Stodola Definition
Where & N= no. of blades
No dependence on backsweep
β 2 <-45^0 ; N>
β 2 >-45^0 ; N>
00 < β 2 <-60^0
Forward Curved Vanes
Small Volume
High Pressure ratio
High speed High noise , Low Efficiency
Backward curved Vanes
Large Volume and size
Low to High Pr Ratio
High Efficiency, Low Noise
Radial Vanes Medium Volume and Size
Medium to High Pr ratio
Good Efficiency
Radial Vaned CCs have been used in A/C engines for 50
years. Now, well designed backward curved vaned CCs are increasingly being used for higher efficiency.
At the compr. entry face
a 1 1
C tanβ = U
U 1 = ω.reye where r (^) eye varies from the root to the tip of the eye
Thus for a high speed compressor (or large sized) β 1 shall vary hugely from root to tip of the eye.
Under off-design operations,
i =r β - β** (^1 1) r
High positive incidence i (≥ +5^0 ) may precipitate early flow separation inside the impeller vane passage, even near the eye, specially if high diffusion ( i.e. high adverse pressure gradient ) is being attempted inside the impeller vanes.
To be decided by designer
At the exit plane of the impeller, the exiting flow deviates from the trailing edge and lag behind in rotational mode. This is often referred to as the lag or deviation angle.
av 2 2
δ = β - β
which is an average at the passage exit, and β 2 * is the impeller vane exit angle set by design
Diffusion Limit :
An upper limit of realistic diffusion limit V 2 /V 1 ≈ 0. In rotating diffuser V 2 /V 1 < 0. In Impeller design, ρ 1 A 1 / ρ 2 A 2 > 2.
Backward curved vanes + splitter
Reduction in deviation angle at the impeller exit under off-design operating conditions is to be designed in to the impeller and the vane designs.
Vaneless diffuser
.( - 1). ) 0C = 1 +^ 0c
γ η γ γ - π
= (^)
2 03 s 2 1 w 2 01 01
pΨ. (σ. U - U .C p a
The general relationship for Compressor Pressure ratio is given by
With Speed Control and Flow Control
Stall and Surge control
Losses : Ideal and Real Characteristics