
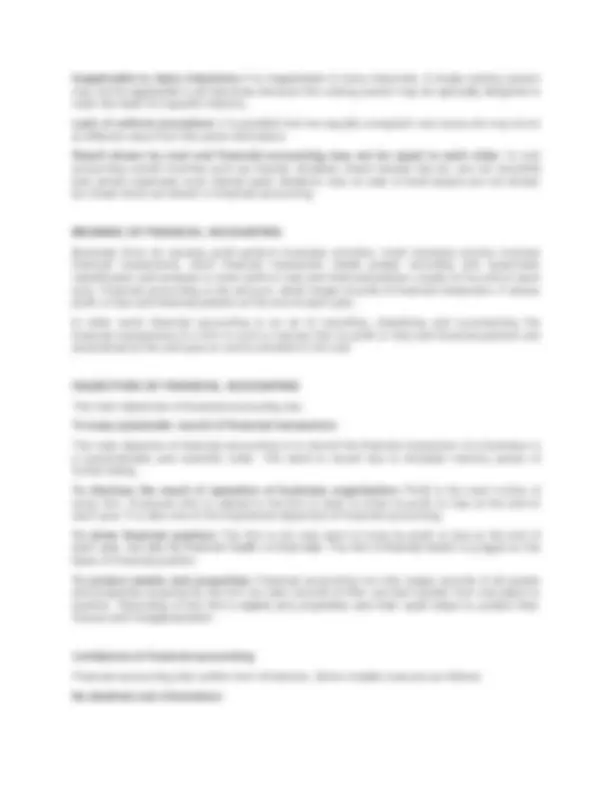
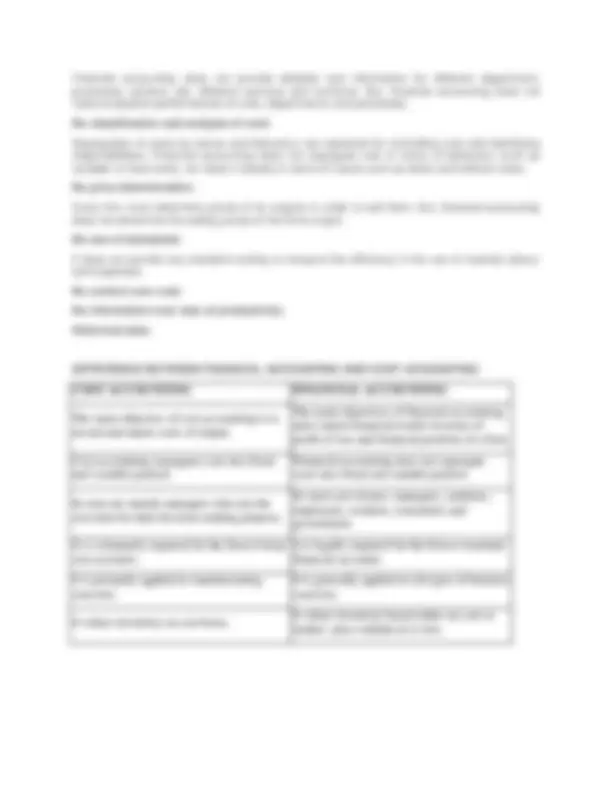
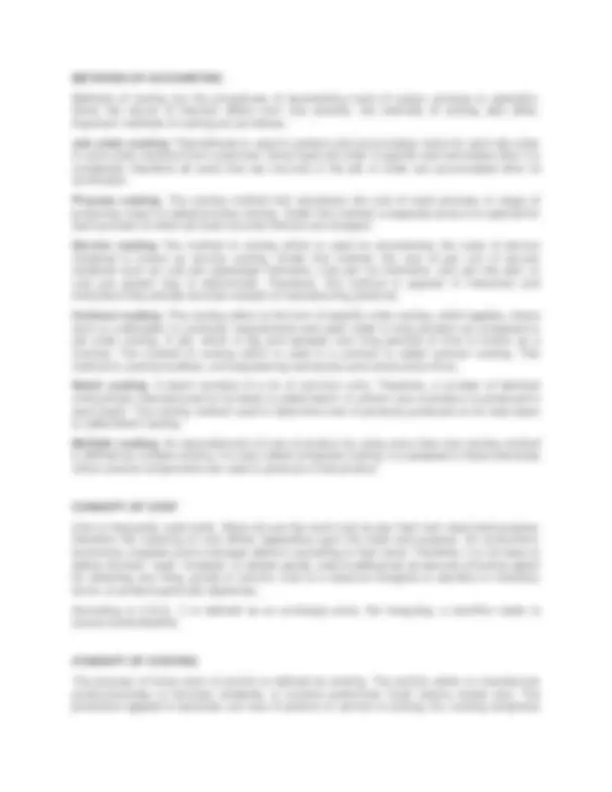
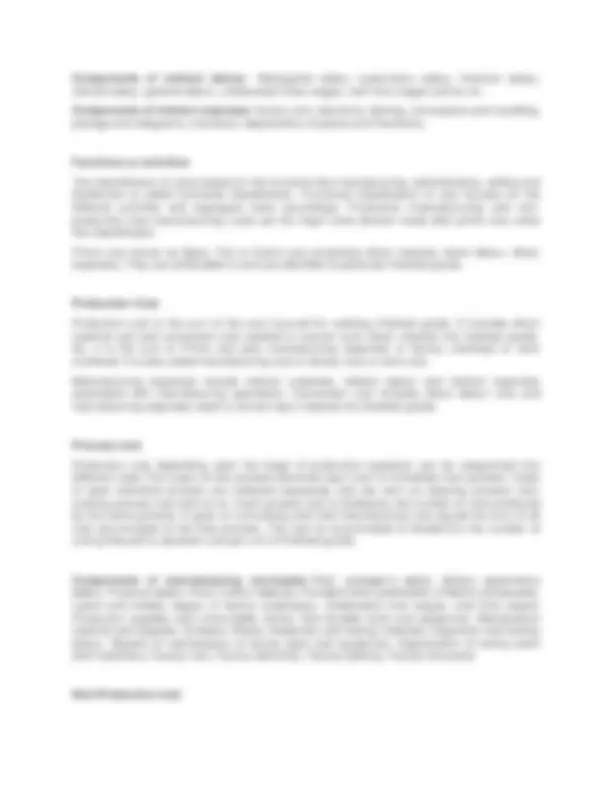
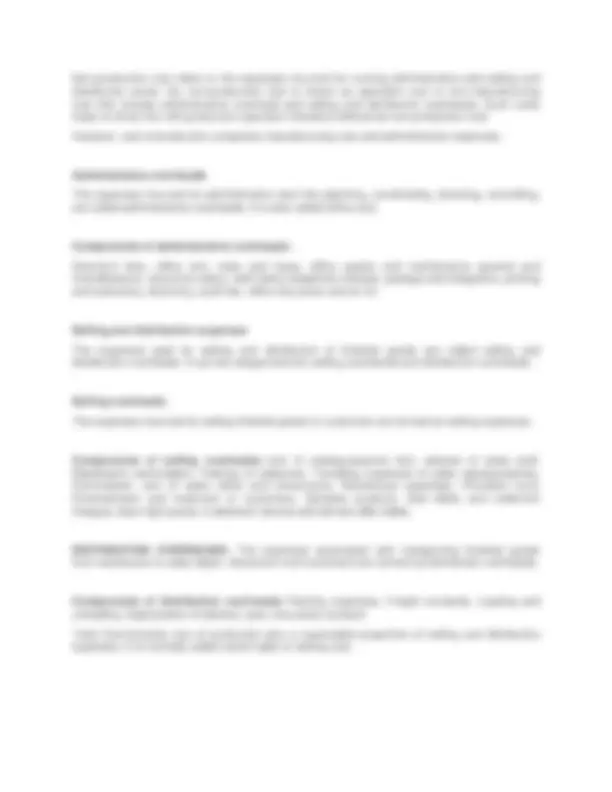
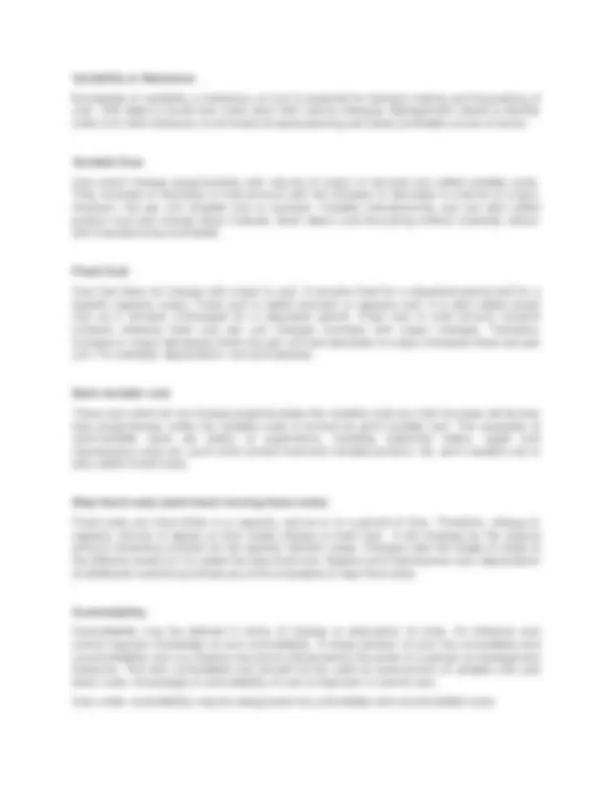
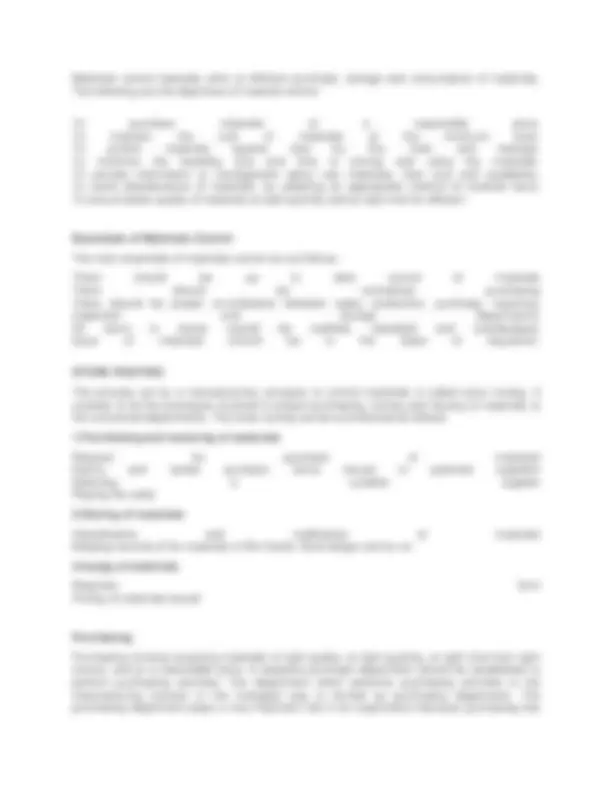
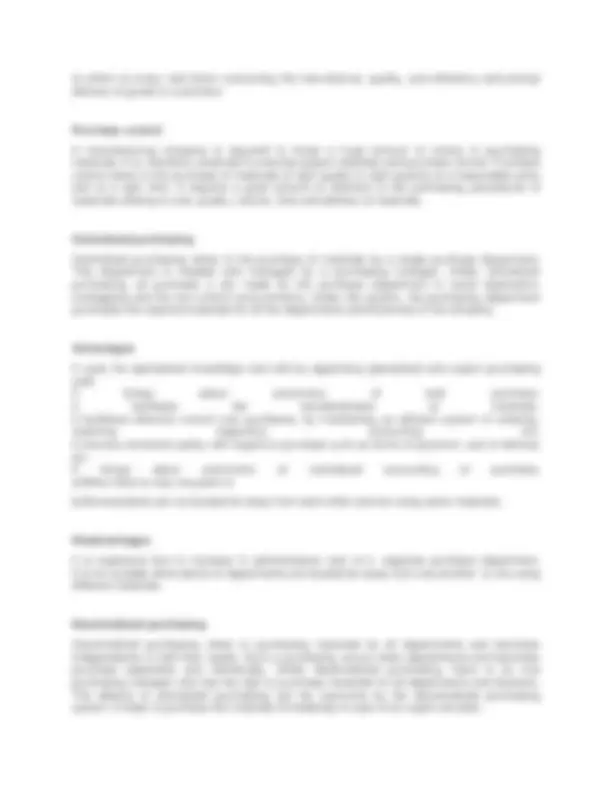
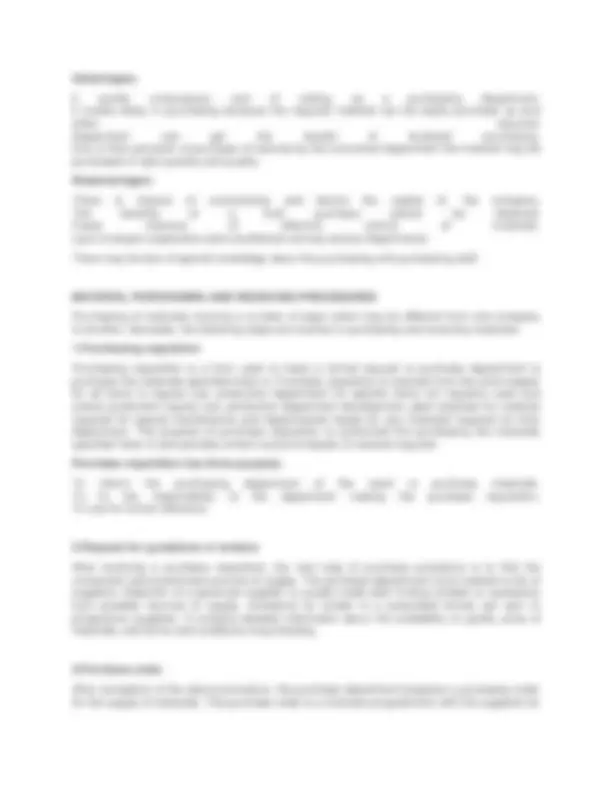
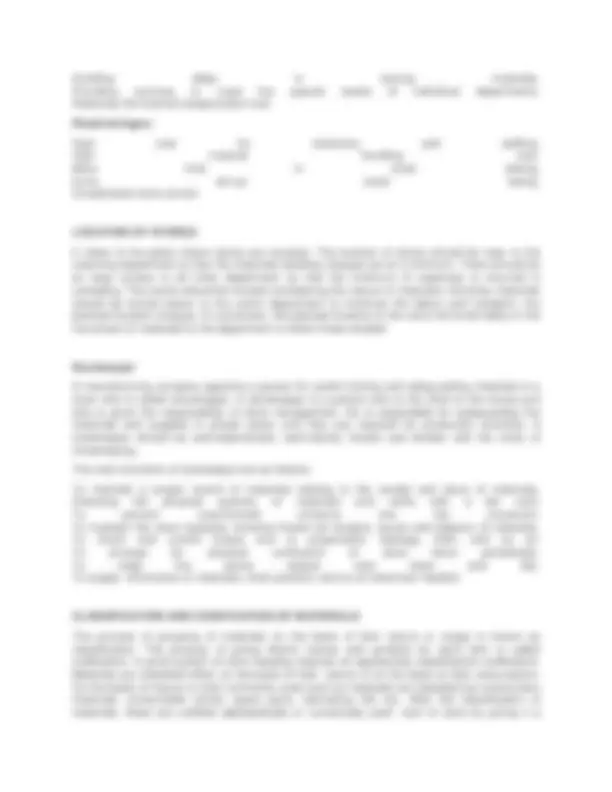
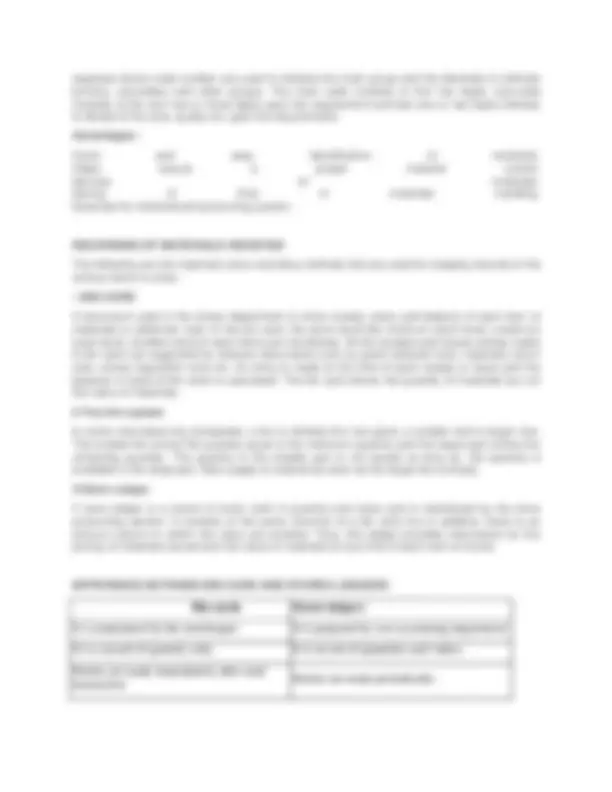
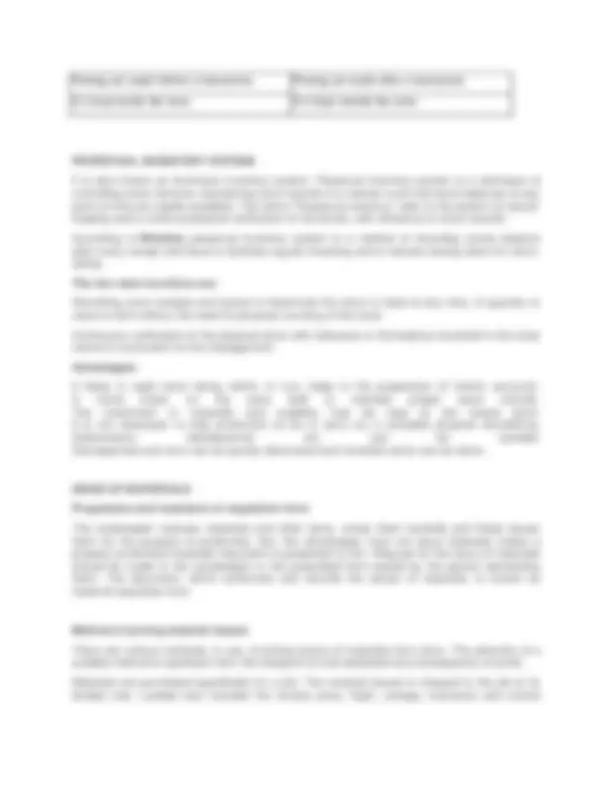
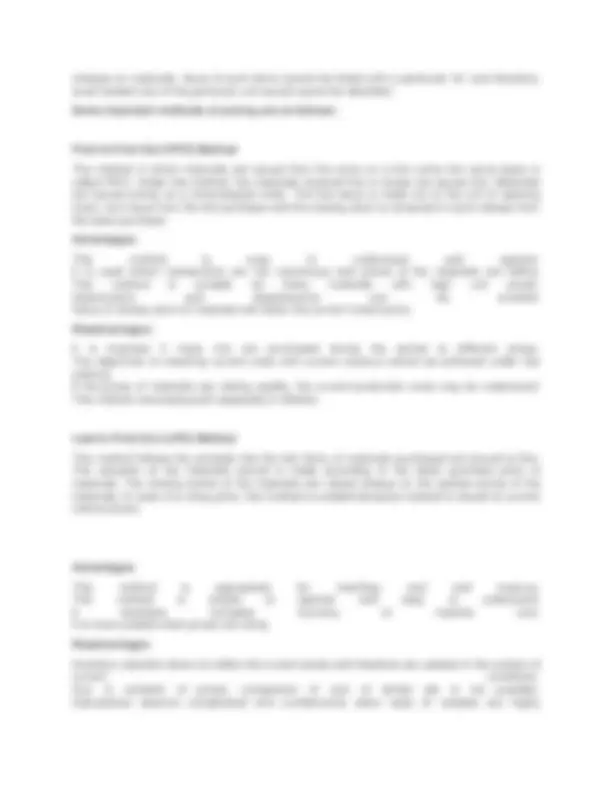
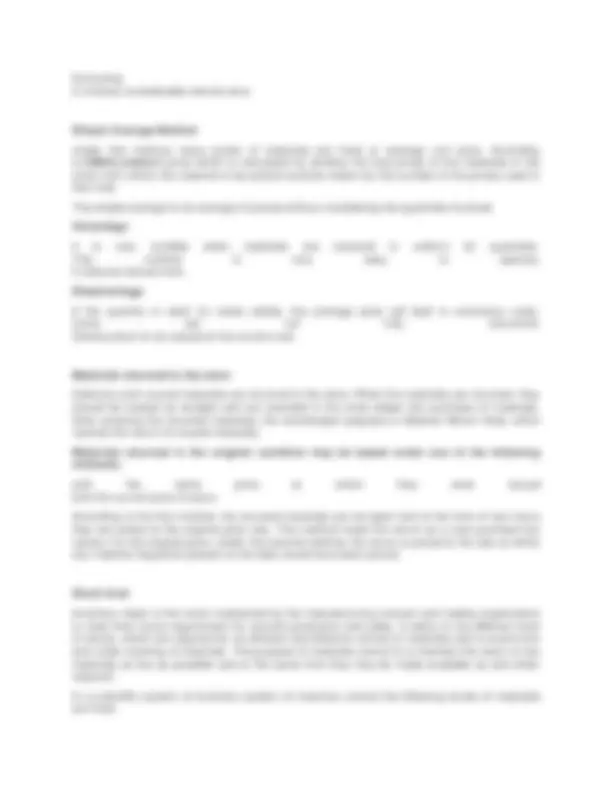
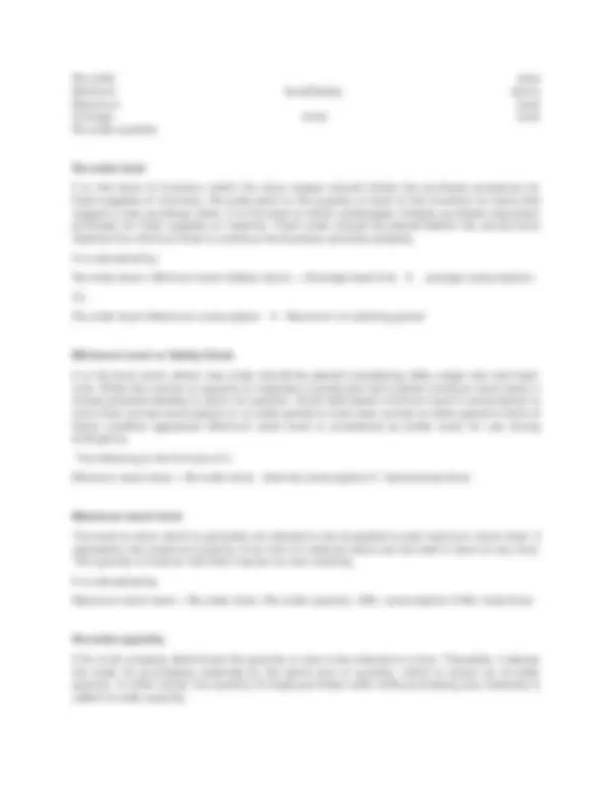
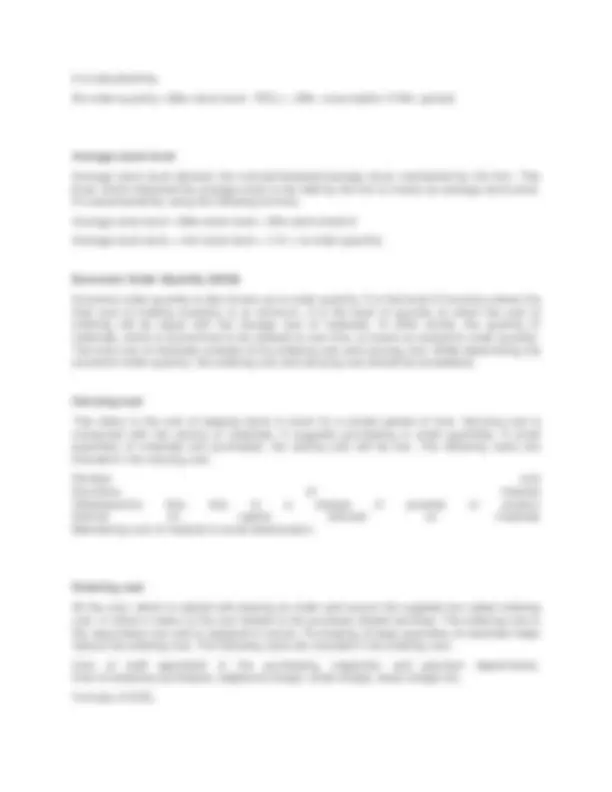
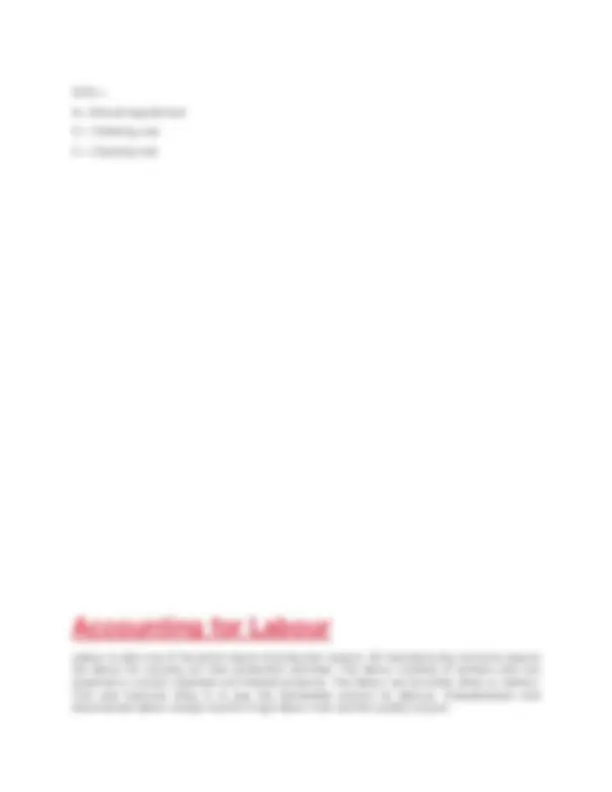
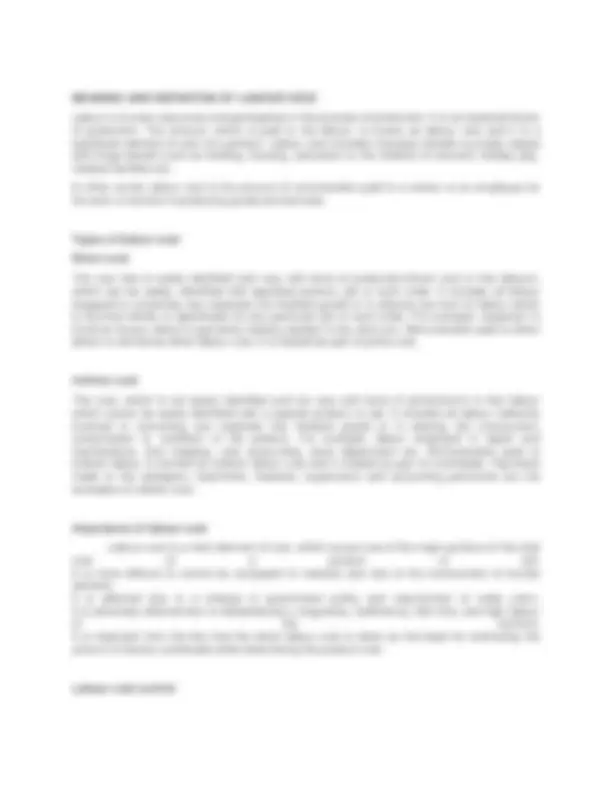
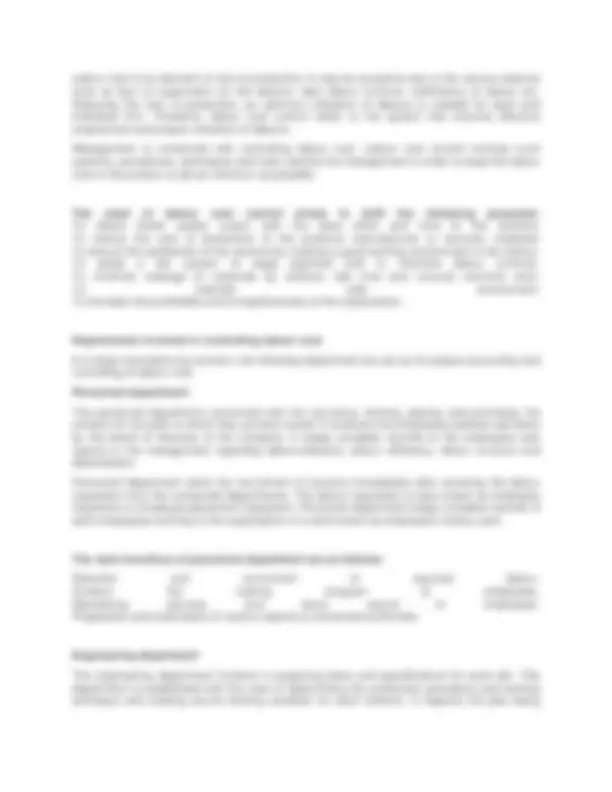
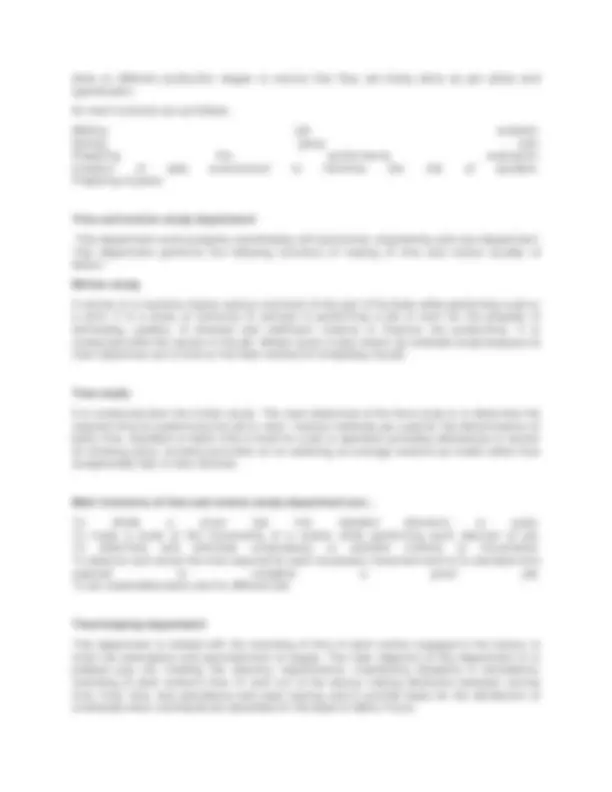
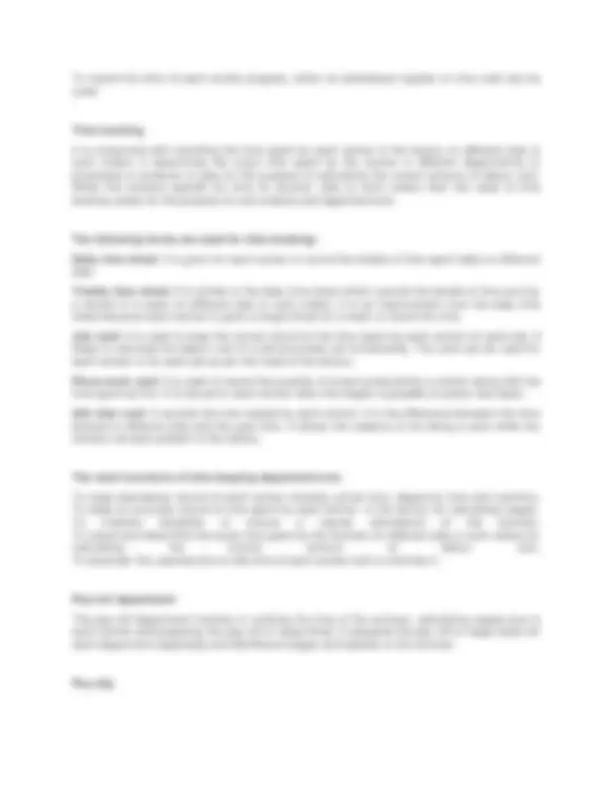
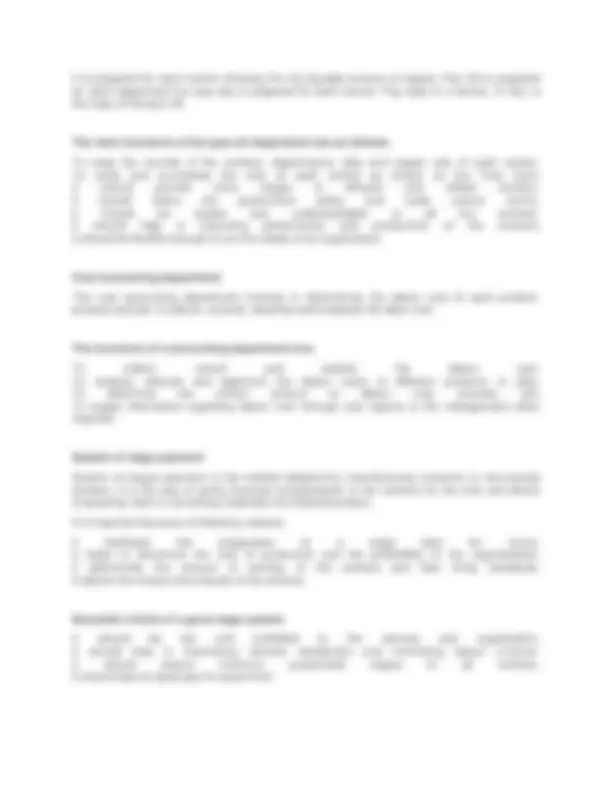
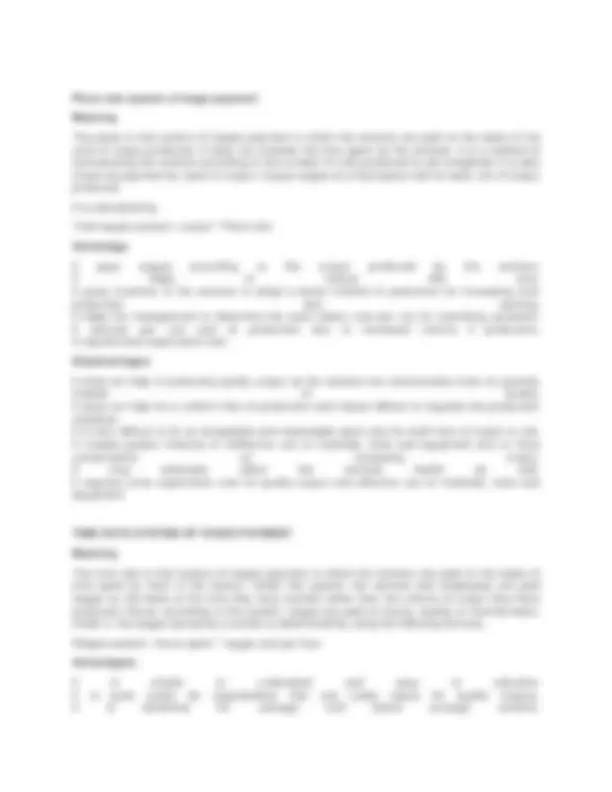
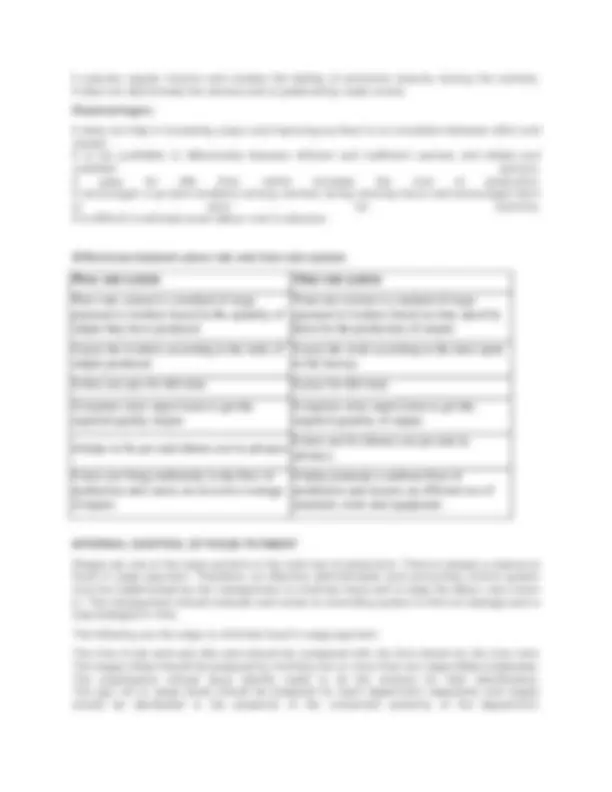
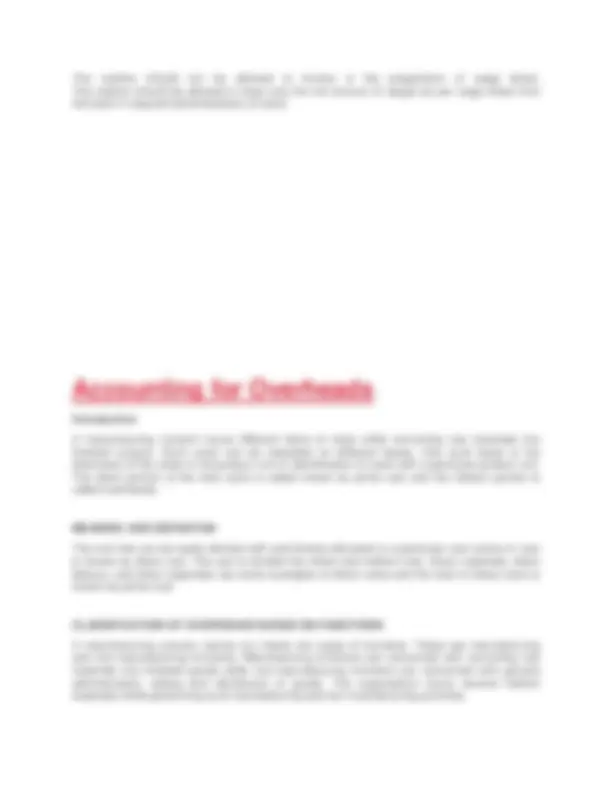
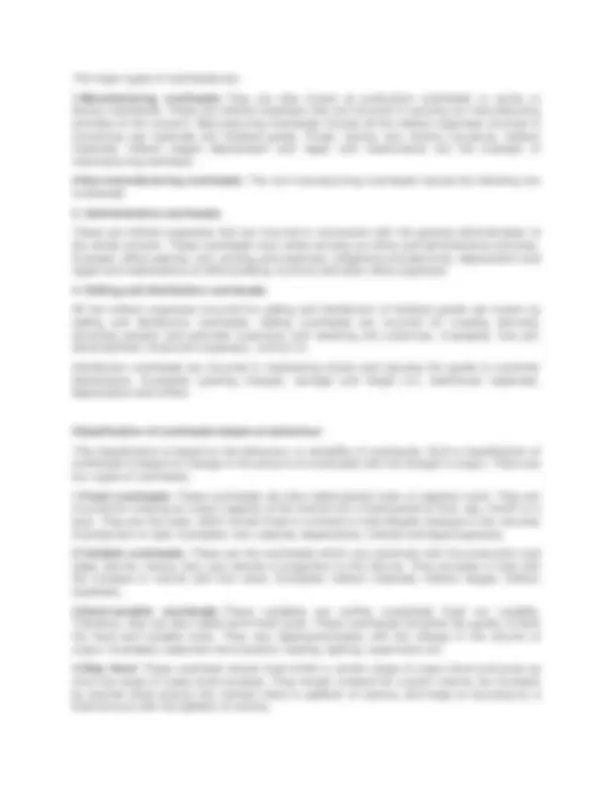
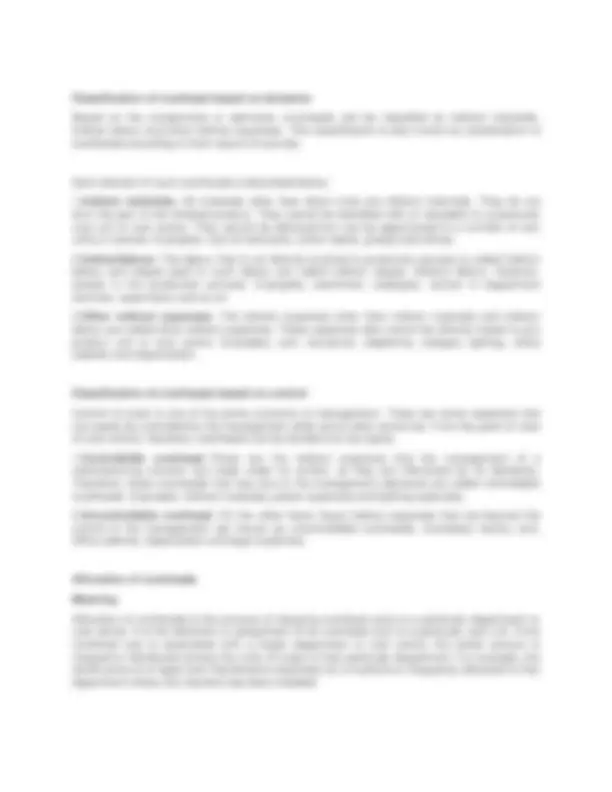
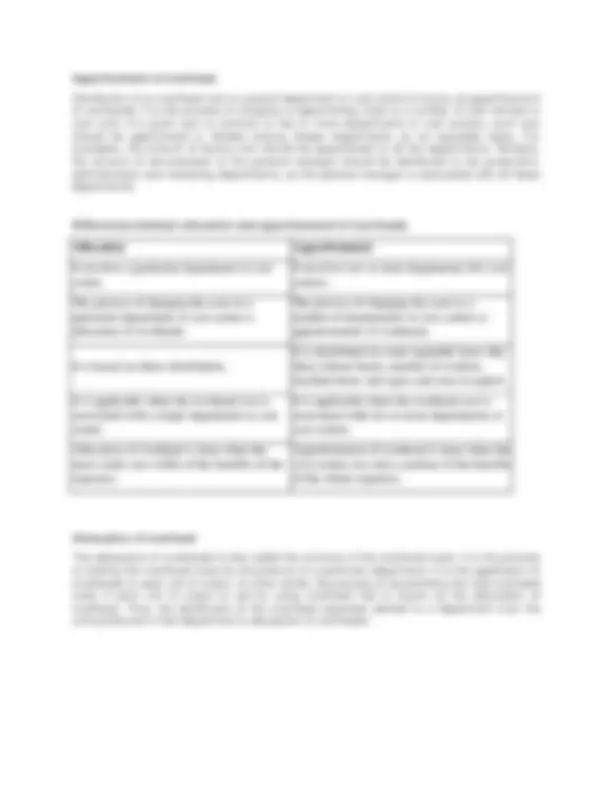
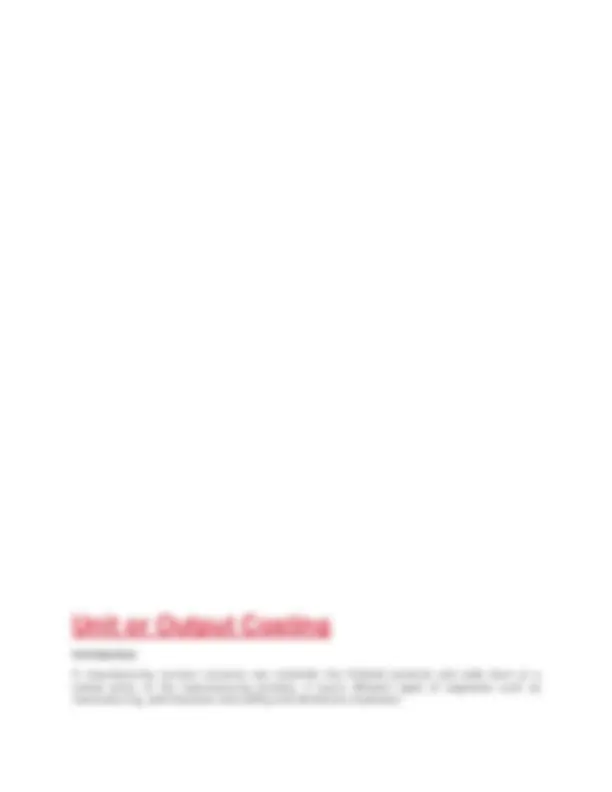
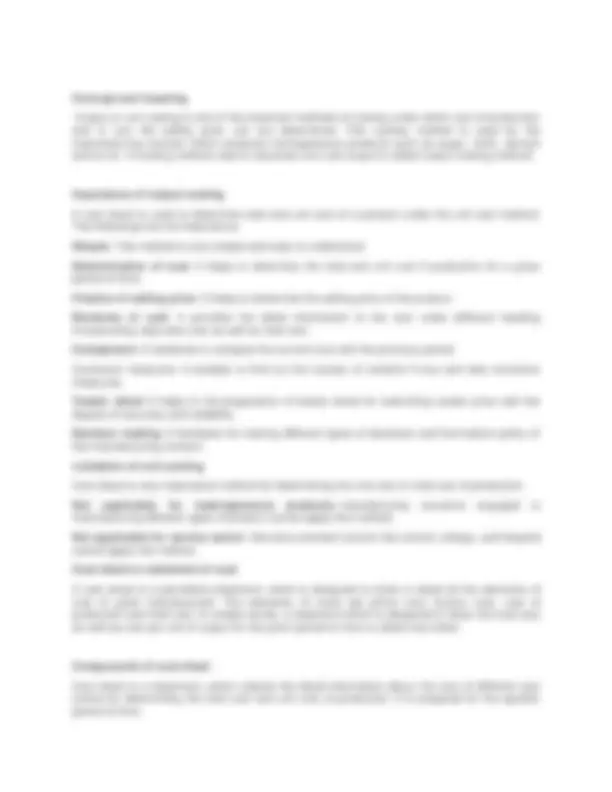
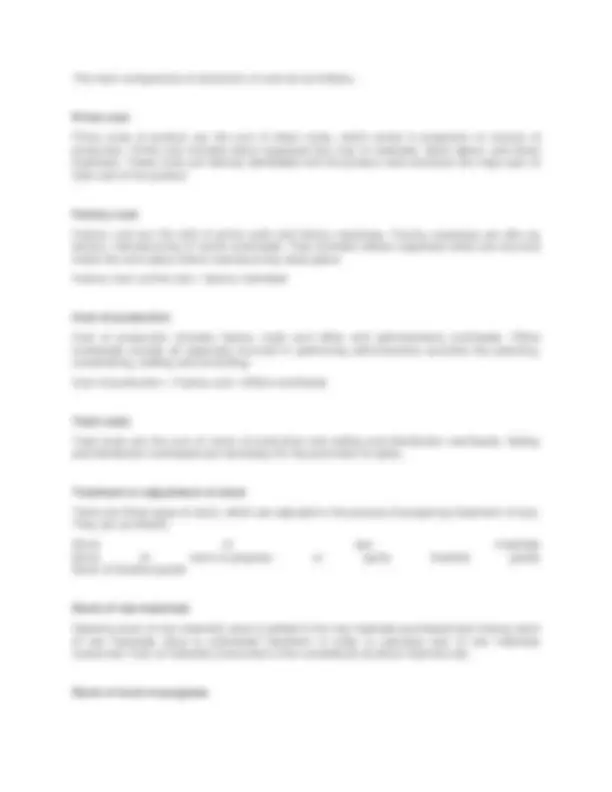
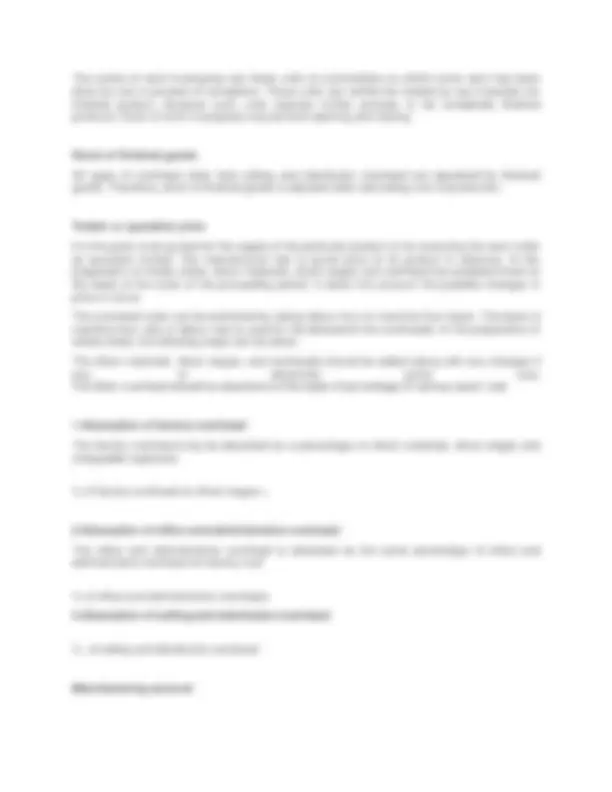
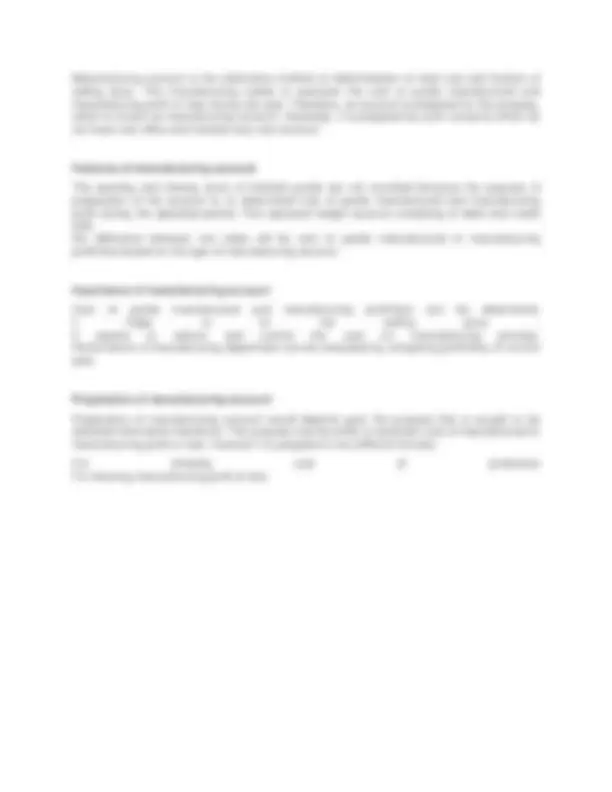
Study with the several resources on Docsity
Earn points by helping other students or get them with a premium plan
Prepare for your exams
Study with the several resources on Docsity
Earn points to download
Earn points by helping other students or get them with a premium plan
Community
Ask the community for help and clear up your study doubts
Discover the best universities in your country according to Docsity users
Free resources
Download our free guides on studying techniques, anxiety management strategies, and thesis advice from Docsity tutors
Concept of cost accounting There are three branches of accounting. i.e Financial Accounting, cost accounting and management accounting. Cost accounting is one of the branches of accounting, which has been developed due to the limitation of financial accounting. Financial accounting communicates economic information of an organization as a whole and that is used for external reporting purpose. The reporting of financial accounting may not be sufficient for internal reporting i.e for the formulati
Typology: Lecture notes
1 / 41
This page cannot be seen from the preview
Don't miss anything!
Concept of cost accounting There are three branches of accounting. i.e Financial Accounting, cost accounting and management accounting. Cost accounting is one of the branches of accounting, which has been developed due to the limitation of financial accounting. Financial accounting communicates economic information of an organization as a whole and that is used for external reporting purpose. The reporting of financial accounting may not be sufficient for internal reporting i.e for the formulation of policy and strategy, decision making and control. According to C.Gilespie “cost accounting is a set of producers for determining the cost of a product and various activities involved in its manufacture and sales and for planning and measuring performance. FEATURES OF COST ACCOUNTING The following are the main features of cost accounting Nature : Cost accounting is a branch of accounting. It is concerned with recording and reporting costs of output to the firm’s management. Objective : Its main objectives are to accumulate costs of output, job, process, unit and department and report them for different uses. Status : It is complementary to financial accounting as it provides cost data of different kinds of stock for preparing financial statements. Basis : It is the basis for cost estimate, cost control, and price determination of output. Usefulness : It is useful for decision making and performance evaluation as it uses absorption or valuation costing technique in preparing income statements. Objectives of cost accounting There can be several objectives of cost accounting. However, the following are its important objectives: To ascertain cost: The important objective of cost accounting is to ascertain cost of a product or services or jobs. Ascertainment of cost is process of determining cost after they have been incurred. Generally, there are two methods of determining the cost i.e job costing and process costing. Due to the different in the nature of activity of industry, different methods of cost may be applied. To control cost: The objectives of cost accounting is to control over the cost by using various techniques such as standard costing, inventory control, marginal costing etc. To provide information for decision making: Cost accounting is the formal system of accounting and provides information for various managerial decisions like
i. Whether to accept or reject the offer ii.Whether to make or buy a product iii.Whether to continue or replace the existing machine and iv.Whether to drop or continue the product or services To fix the selling price: Cost accounting can beprovide the detailed information about the cost of a product or service to determine the selling price. To ascertain costing profit or loss: Cost accounting ascertains total cost and total revenue of every product or services or job and calculates profit or loss by comparing with revenue and cost. To provide information in preparation of financial statements: Inventory should be valued for preparation of financial statements by comparing cost price and market price. Importance and advantages of cost accounting Cost accounting provides immense advantages to a firm. It also can be explained in terms of importance: Helping in ascertaining of cost: Cost accounting uses different methods of costing such as job costing, process costing etc. applying this costing method cost of each product, process or job is ascertained. Helps in inventory control: It helps in inventory control using various techniques like ABC analysis, economic order quantity, stock level etc. Helps in measurement of efficiency: It helps in measurement of efficiency of operations through establishment if standards and various analysis. Helps in preparation of budget: It helps in preparation of various budgets such as sales budget, production budget, material purchase budget, flexible budget etc. LIMITATIONS OF COST ACCOUNTING Cost accounting also suffers from a number of limitations such as follows: Unnecessary : It is unnecessary because it involves duplication of work, many good enterprise are functioning without any costing system. Expensive: It is expensive because the installation of cost accounting system involves additional cost.
Financial accounting does not provide detailed cost information for different department, processes, product, job, different services and functions. But, financial accounting does not make evaluation performances of units, departments, and processes. No classification and analysis of cost: Segregation of costs by nature and behaviour are essential for controlling cost and identifying responsibilities. Financial accounting does not segregate cost in terms of behaviour such as variable or fixed costs, nor does it classify in terms of nature such as direct and indirect costs. No price determination: Every firm must determine prices of its outputs in order to sell them. But, financial accounting does not determine the selling prices of the firms output. No use of standards: It does not provide any standard costing to measure the efficiency in the use of material, labour and expenses. No control over cost: No information over loss of productivity: Historical data: DIFFERENCE BETWEEN FINANCIAL ACCOUNTING AND COST ACCOUNTING
Methods of costing are the procedures of ascertaining costs of output, process or operation. Since the nature of industry differs from one another, the methods of costing also differ. Important methods of costing are as follows: Job order costing: Thismethods is used to gathers and accumulates costs for each job order or work order received from customers. Since each job order is specific and terminates after it is completed, therefore all costs that are incurred in the job or order are accumulated after its termination. Process costing : The costing method that ascertains the cost of each process or stage of producing output is called process costing. Under this method, a separate account is opened for each process to which all costs incurred thereon are charged. Service costing: The method of costing which is used for ascertaining the costs of service rendered is known as service costing. Under this method, the cost of per unit of service rendered such as cost per passenger kilometre, cost per ton kilometre, cost per kilo-watt, or cost per patient day is determined. Therefore, this method is popular in industries and institutions that provide services instead of manufacturing products. Contract costing: This costing refers to the form of specific order costing, which applies, where work is undertaken to customer requirements and each order is long duration as compared to job order costing. A job, which is big and spreads over long periods of time is known as a contract. The method of costing which is used in a contract is called contract costing. This method is used by builders, civil engineering contractors and construction firms. Batch costing : A batch consists of a lot of common units. Therefore, a number of identical units/articles manufactured on lot basis is called batch. A uniform size of product is produced in each batch. The costing method used to determine cost of products produced on lot wise basis is called batch costing. Multiple costing: An ascertainment of cost of product by using more than one costing method is defined as multiple costing. It is also called composite costing. It is adopted in those industries where several components are used to produce a final product. CONCEPT OF COST Cost is frequently used word. Since all use the word cost as per their own need and purpose, therefore the meaning of cost differs depending upon the need and purpose. An accountant, economist, engineer and a manager define it according to their need. Therefore, it is not easy to define the term “cost”. However, in simple words, cost is defined as an amount of money spent for obtaining any thing, goods or service. Cost is a resource foregone or sacrifice in monetary terms, to achieve particular objectives. According to U.S.A., it is defined as an exchange price, the foregoing, a sacrifice made to source some benefits. CONCEPT OF COSTING The process of fixing costs of activity is defined as costing. The activity refers to manufacture products/articles or services rendered, or function performed. Each activity needs cost. The procedure applied to ascertain unit cost of product or service is costing. So, costing comprises
All the three elements of cost can further be divided or grouped into two types based on their nature such as direct and indirect costs. Direct costs Direct costs are those materials, labour and other expenses which can easily be attributed or identified with a unit of product, process or operation. The cost of raw materials, productive labour, and carriage of materials paid are the examples of direct cost. The total of direct cost is termed as prime cost. Indirect costs Indirect costs are those types of cost, which cannot easily be attributed to or identified with a unit of product, process or operation. Therefore, the total of costs of indirect materials, indirect labour and indirect expenses is referred to as indirect costs. They are also called overhead costs. The examples of indirect costs are repair charges, salaries, rent, telephone and water. Direct materials cost: The cost of materials having physical identity with the end product is defined as direct materials cost. Main raw materials and necessary components are a few examples of direct materials. Indirect materials cost: Materials are not used as inputs of product are called indirect materials. Cost of materials incurred for repair of a machine used for printing of textbook is defined as indirect materials cost. Direct labour cost: Labour or wages incurred for the operative workers engaged in production process are categorized as direct labour cost. Wages paid to the workers involved in production and handling materials, workers engaged in productive operation by way of supervision and maintenance etc is direct labour costs. Indirect labour cost: Smooth operation of an organization needs operation of account department, marketing department, and internal transport also besides production department. Indirect labour cost mean salary paid to staff. Direct expenses: Direct expenses are charged directly to finished product like direct materials cost. It is also called designed chargeable expenses. These include special layout cost, drawing and designed charges, royalties and so on. Indirect expenses: The cost which is not directly connected with finished product but occur on account of operation are termed as indirect expenses. Indirect expenses are also more frequently called on cost or overheads and include expenses such as canteen expenses, lighting, heating charge, rent, insurance and so on. Components of indirect materials: Production supplies and consumable stores, greases, waste, Non-durable tools and equipment, maintenance material and supplies, inspection and testing materials.
Components of indirect labour: Managerial salary, supervisory salary, foremen salary, clerical salary, general labour, unallocated times wages, over-time wages and so on. Components of indirect expenses: factory rent, electricity, lighting, conveyance and travelling, postage and telegrams, insurance, depreciation of plants and machinery. Functions or activities The classification of costs based on the functions like manufacturing, administrative, selling and distribution is called functional classification. Functional classification of cost focuses on the different activities and segregate costs accordingly. Production (manufacturing) and non- production (non-manufacturing) costs are the major costs division made after prime cost under this classification. Prime cost known as Basic, Flat or Direct cost comprises direct material, direct labour, direct expenses. They are attributable to and are identified to particular finished goods. Production Cost Production cost is the sum of the cost incurred for realizing finished goods. It includes direct material cost and conversion cost needed to convert such direct material into finished goods. So, it is the sum of Prime cost plus manufacturing expenses or factory overhead or work overhead. It is also called manufacturing cost or factory cost or work cost. Manufacturing expenses include indirect materials, indirect labour and indirect expenses associated with manufacturing operations. Conversion cost includes direct labour cost and manufacturing expenses need to convert input material into finished goods. Process cost Production cost depending upon the stage of production operation can be categorized into different costs.The output of one process becomes input cost of immediate next process. Costs of each individual process are collected separately and are term as cleaning process cost, cooking process cost and so on. Each process cost is divided by the number of units produced by the same process. It goes on cumulating and total manufacturing cost equals the sum of all cost accumulated at the final process. The cost so accumulated is divided but the number of units produced to ascertain cost per unit of finished goods. Components of manufacturing overheads: Work manager’s salary, factory supervisory salary, Foremen salary, Work Clerks’ salaries, Provident fund contribution of factory employees, Leave and holiday wages of factory employees, Unallocated time wages, over-time wages, Production supplies and consumable stores, Non-durable tools and equipment, Maintenance material and supplies, Greases, Waste, Inspection and testing materials, Inspection and testing labour, Repairs of maintenance of factory plant and equipment, Depreciation of factory plant and machinery, Factory rent, Factory electricity, Factory lighting, Factory insurance. Non-Production cost
Variability or Behaviour Knowledge of variability or behaviour of cost is essential for decision making and forecasting of cost. This helps to study how costs react with volume changes. Management needs to identify costs from their behaviour to formulate forward planning and select profitable course of action. Variable Cost Cost which change proportionality with volume of output or services are called variable costs. They increase or decrease in total amount with the increase or decrease in volume of output. However, the per unit variable cost is constant. Variable manufacturing cost are also called product cost and include direct material, direct labour and fluctuating indirect materials, labour and manufacturing overheads. Fixed Cost Cost that does not change with output is cost. It remains fixed for a stipulated period and for a specific capacity output. Fixed cost is called constant or capacity cost. It is also called create cost as it remains unchanged for a stipulated period. Fixed cost in total amount remains constant whereas fixed cost per unit changes inversely with output changes. Therefore, increase in output decreases fixed cost per unit and decrease in output increases fixed cost per unit. For example: depreciation, rent and salaries. Semi-variable cost Those cost which do not change proportionately like variable costs but their increase will be less than proportionate unlike the variable costs is termed as semi-variable cost. The examples of semi-variable costs are salary of supervisors, travelling salesman salary, repair and maintenance costs etc. such costs contain fixed and variable portions. So, semi variable cost is also called mixed costs. Step-fixed costs (semi-fixed/ moving fixed costs) Fixed costs are fixed either to a capacity volume or to a period of time. Therefore, change in capacity volume or lapses of time create change in fixed cost. It will changes by the original amount remaining constant for the specific relevant range. Changes take the shape of steps at the different levels so it is called the step fixed cost. Repairs and maintenance cost; depreciation of additional machine purchase are some examples of step fixed costs. Controllability Controllability may be defined in terms of change or alternation of costs. An effective cost control requires knowledge of cost controllability. A sharp division of cost into controllable and uncontrollability cost is a relative one and is influenced by the action of a person at management hierarchy. The term controllable cost should not be used as synonymous of variable cost and direct costs. Knowledge of controllability of cost is important to control cost. Cost under controllability may be categorized into controllable and uncontrollable costs.
Controllable cost: The cost subject to control or substantial influence of a particular manager or individual is called controllable cost. In controllable cost, the cost can be changed or altered by the action of a specific managers. Example; direct materials, direct labour, other overheads such as indirect labour, factory supplies, cutting tools, power costs, repair and maintenance etc are controllable costs. Uncontrollable costs: Costs that are not subject to influence by the action of manager is called uncontrollable costs. These costs remain unchanged or unaltered. Example: managerial salaries, staff salaries, depreciation after purchase of equipment, rent. Some costs may be controllable in the short run but not in the long run.
Materials control basically aims at efficient purchase, storage and consumption of materials. The following are the objectives of material control; To purchase materials at a reasonable price. To maintain the cost of materials at the minimum level. To protect materials against loss by fire, theft, and leakage. To minimize the handling cost and time in storing and using the materials. To provide information to management about raw materials, their cost and availability. To avoid obsolescence of materials by adopting an appropriate method of material issue. To ensure better quality of materials at right quantity and at right time for efficient Essentials of Materials Control The main essentials of materials control are as follows; There should be up to date record of materials There should be centralized purchasing There should be proper co-ordination between sales, production, purchase, receiving, inspection and storage departments. All items in stores should be codified, classified and standardised. Issue of materials should be in the basis of requisition. STORE ROUTING The process set by a manufacturing company to control materials is called store routing. It consists of all the processes involved in proper purchasing, storing and issuing of materials to the concerned departments. The store routing can be summarized as follows: 1.Purchasing and receiving of materials Request for purchase of materials Inquiry and tender quotation forms issued to potential suppliers Selecting a suitable supplier Placing the order 2.Storing of materials Classification and codification of materials Keeping records of the materials in Bin Cards, Store ledger and so on. 3.Issuig of materials Requition form Pricing of materials issued Purchasing Purchasing involves acquiring materials of right quality, at right quantity, at right time from right source, and at a reasonable price. A separate purchase department should be established to perform purchasing activities. The department which performs purchasing activities in the manufacturing concern in the managed way is termed as purchasing department. The purchasing department plays a very important role in an organization because purchasing has
its effect on every vital factor concerning the manufacture, quality, cost efficiency and prompt delivery of goods to customers. Purchase control A manufacturing company is required to invest a huge amount of money in purchasing materials. It is, therefore, essential to exercise proper materials and purchase control. Purchase control refers to the purchase of materials of right quality in right quantity at a reasonable price and at a right time. It requires a good amount of attention to the purchasing procedures of materials relating to cost, quality, volume, time and delivery of materials. Centralized purchasing Centralized purchasing refers to the purchase of materials by a single purchase department. This department is headed and managed by a purchasing manager. Under centralized purchasing, all purchase s are made by the purchase department to avoid duplication, overlapping and the non-uniform procurements. Under this system, the purchasing department purchases the required materials for all the departments and branches of the company. Advantages It uses the specialized knowledge and skill by appointing specialized and expert purchasing staff. It brings about economics of bulk purchase. It facilitates the standardization of materials. It facilitates effective control over purchases, by maintaining an efficient system of ordering, receiving inspection, accounting etc. It ensures consistent policy with regard to purchase such as terms of payment, cost of delivery etc. It brings about economics of centralized accounting of purchase. a)When there is only one plant or b)Several plants are not located far away from each other and are using same materials. Disadvantages It is expensive due to increase in administration cost of a separate purchase department. It is not suitable when plants of departments are located far away from one another or are using different materials. Decentralized purchasing Decentralized purchasing refers to purchasing materials by all departments and branches independently to fulfil their needs. Such a purchasing occurs when departments and branches purchase separately and individually. Under decentralized purchasing, there is no one purchasing manager who has the right to purchase materials for all departments and divisions. The defects of centralized purchasing can be overcome by the decentralized purchasing system. It helps to purchase the materials immediately in case of an urgent situation.
the supply of materials. It is prepared in five copies, the original copy is sent to the supplier, the second copy for receiving department, third for account department, fourth for imitating department and the fifth one is retained in the purchasing department for reference. 4.Receiving and inspecting materials The receiving department should perform the unction of unloading and receiving of material dispatched by the suppliers. The receiving department verifies the materials with the help if delivery note and the copy of the purchase order after receiving the delivery of goods. The suppliers sends detailed information and an invoice of the materials supplied by it. It has to verify and check the quantity and physical condition of materials by making a comparison of the purchase order and the materials received in large companies, an inspector is appointed to inspect all the materials received and to prepare an inspection report. 5.Checking and passing of bills for payment When the invoices are received from the supplier, they are sent to the stores and accounting departments for the verification of the quantity and price of materials mentioned in the invoices. After checking the required documents, the store department requests the accounting department for making the payment of the invoice to the suppliers. Store-keeping Store keeping refers to the act of storing materials for their safe custody till these are issued to the production and other departments. It involves receiving, storing and issuing of materials. The place where materials are kept is known as 'store'. The term 'stores' has wide meaning and includes raw materials used in production, consumable store such as oil, grease etc, tools, patterns, maintenance materials etc, stock of work in progress and stock of finished goods. Objectives of storekeeping All of proper place for every item of store Keep every item of store in fixed place Maintain proper and upto date records Issuing materials quickly to department Classify and codify the materials for easy identification Types of stores
Economy in cost Better supervision of store Better layout and control of stores Minimum investment in store Less space is occupied Better safety and security of stock Disadvantages: Delay in sending materials to the department and branch. increase in the material handling cost. Greater risk of loss by fire. Not suitable for a large company.
separate stores code number are used to indicate the main group and the decimals to indicate primary, secondary and other groups. The main code consists of first two digits, sub-code consists of the next two or three digits upon the requirement and last one or two digits indicate to details of the size, quality etc upon the requirements. Advantages : Quick and easy identification of materials. Helps ensure a proper material control. Secrecy of materials. Saving of time in materials handling. Essential for mechanized accounting system. RECORDING OF MATERIALS RECEIVED The following are the important store recording methods that are used for keeping records of the various items to store:
It is also known as Automatic inventory system. Perpetual inventory system is a technique of controlling stock items by maintaining store records in a manner such that stock balances at any point of time are readily available. The terms "Perpetual inventory" refer to the system of record- keeping and a continue physical verification of the stocks, with reference to store-records. According to Wheldon, perpetual inventory system is a method of recording stores balance after every receipt and issue to facilitate regular checking and to obviate closing down for stock- taking. The two main functions are: Recording store receipts and issues to determine the stock in hand at any time, in quantity or value or both without the need for physical counting of the stock. Continuous verification of the physical stock with reference to the balance recorded in the store record is convenient for the management. Advantages: It helps in rapid stock taking which, in turn, helps in the preparation of interim accounts. A moral check on the store staff to maintain proper stock records. The investment in materials and supplies may be kept at the lowest point. It is not necessary to stop production so as to carry out a complete physical stocktaking. Deterioration, obsolescence etc, can be avoided. Discrepancies and error can be quickly discovered and remedial action can be taken. ISSUE OF MATERIALS Preparation and treatment of requisition form The storekeeper receives materials and other items, stores them carefully and finally issues them for the purpose of production. But, the storekeeper must not issue materials unless a properly authorized materials requisition is presented to him. Request for the issue of materials should be made to the storekeeper in the prescribed form signed by the person demanding them. The document, which authorizes and records the issues of materials, is known as material requisition from. Method of pricing material issued There are various methods, in use, of pricing issues of materials form store. The selection of a suitable method is significant from the viewpoint of cost absorbed and consequently on profit. Materials are purchased specifically for a job. The material issued is charged to the job at its landed cost. Landed cost includes the invoice price, fright, cartage, insurance and control