
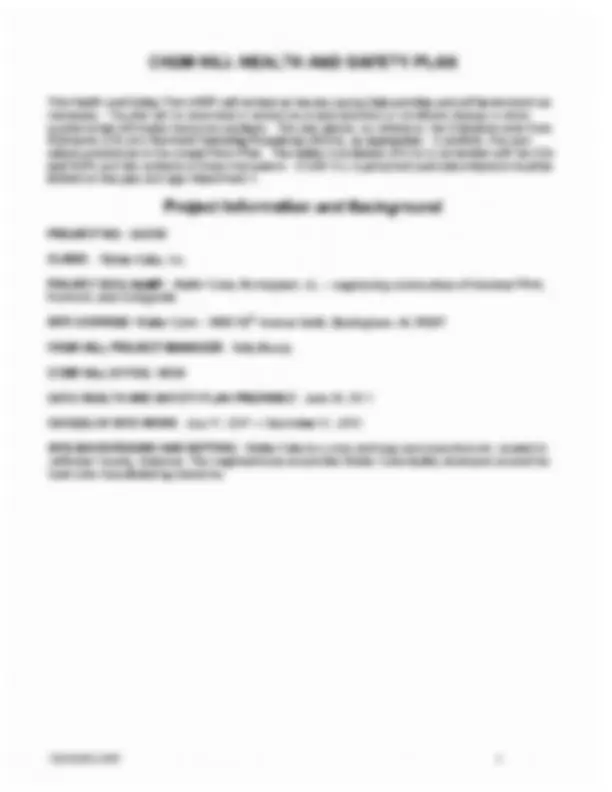
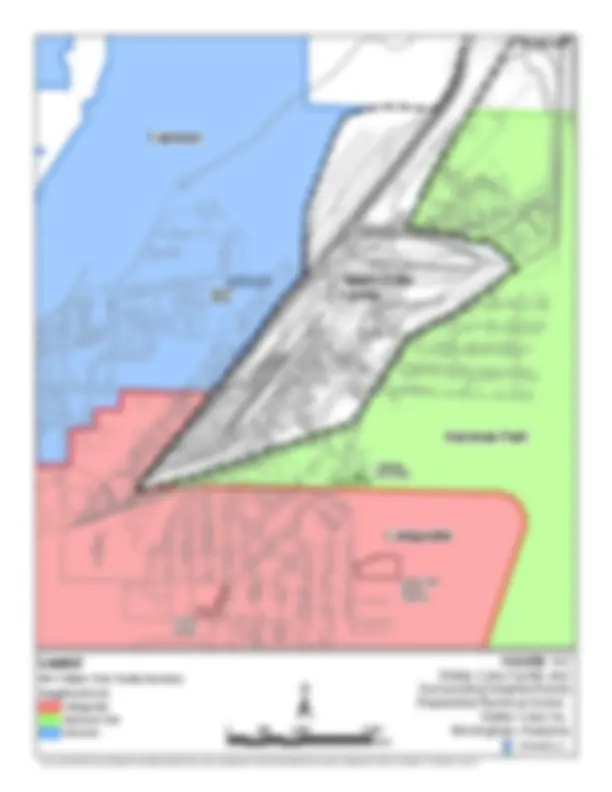
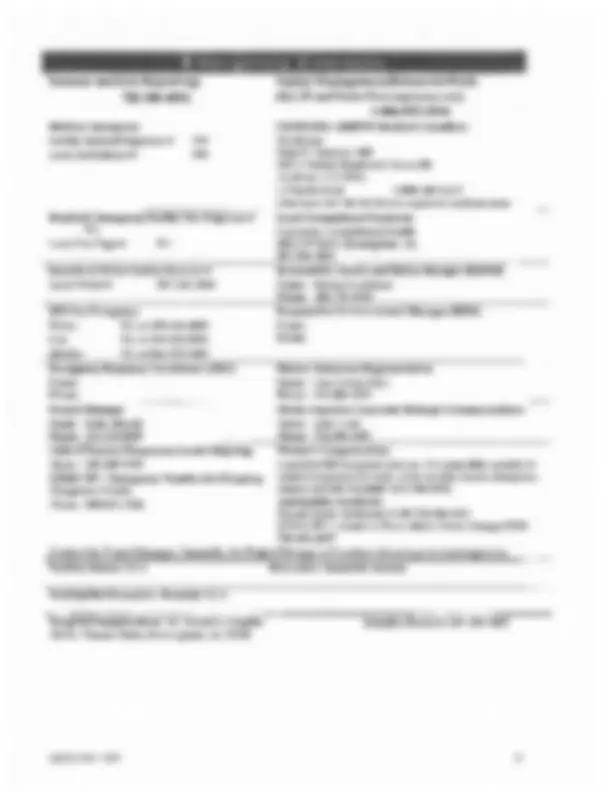
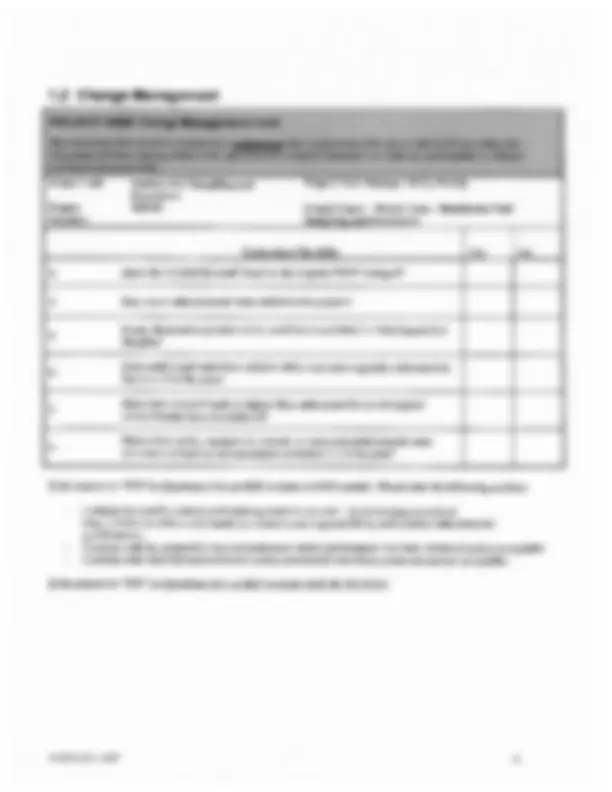
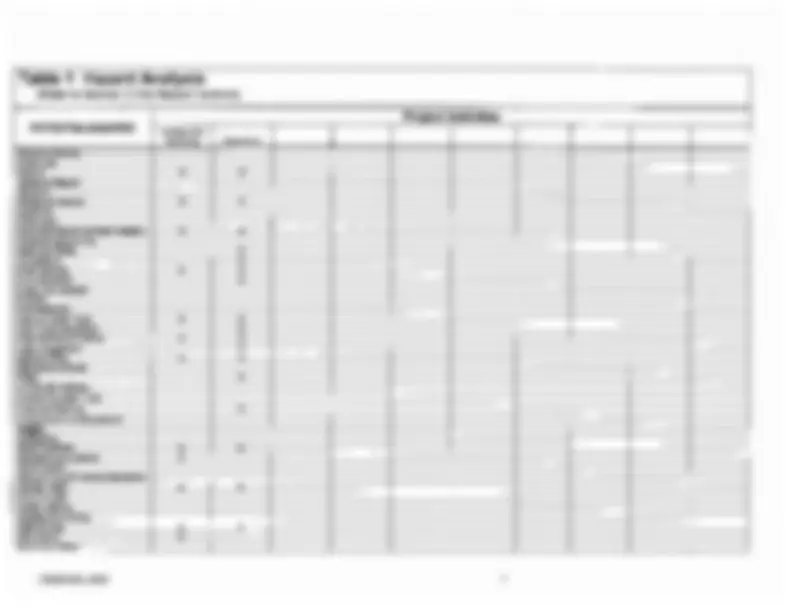
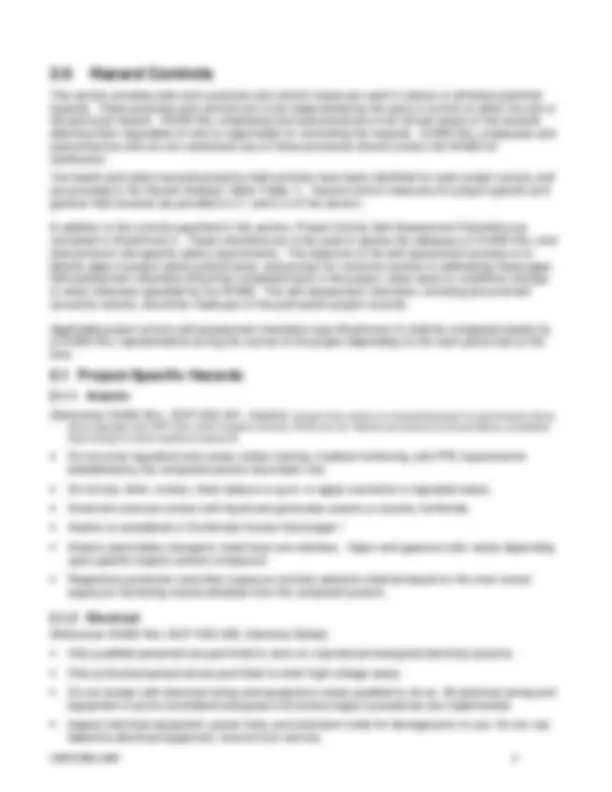
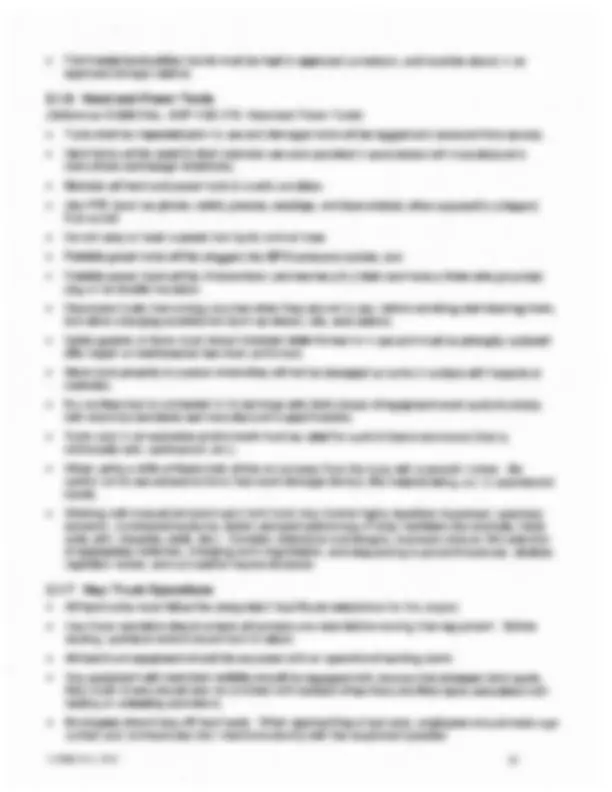
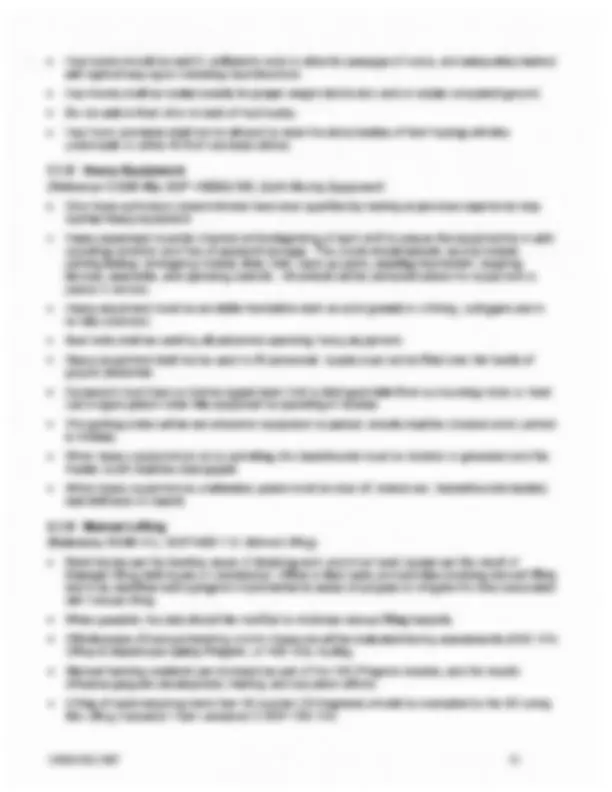
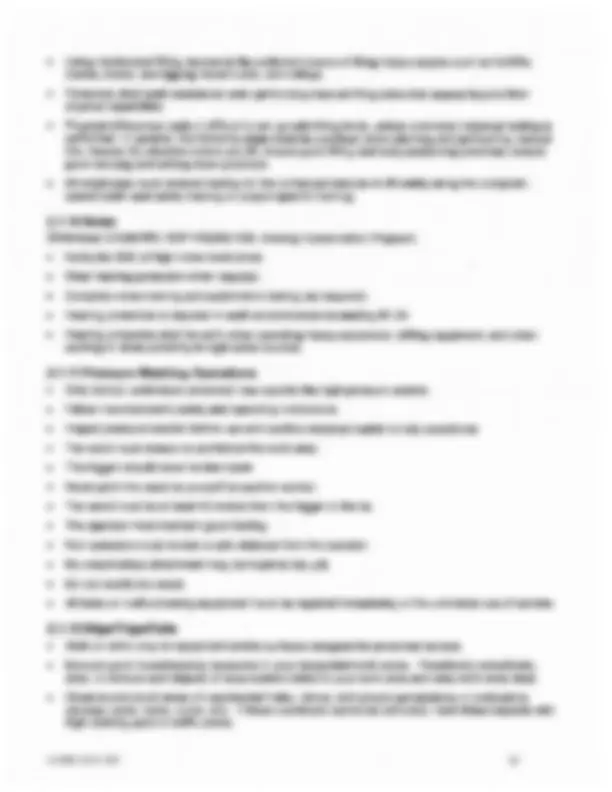
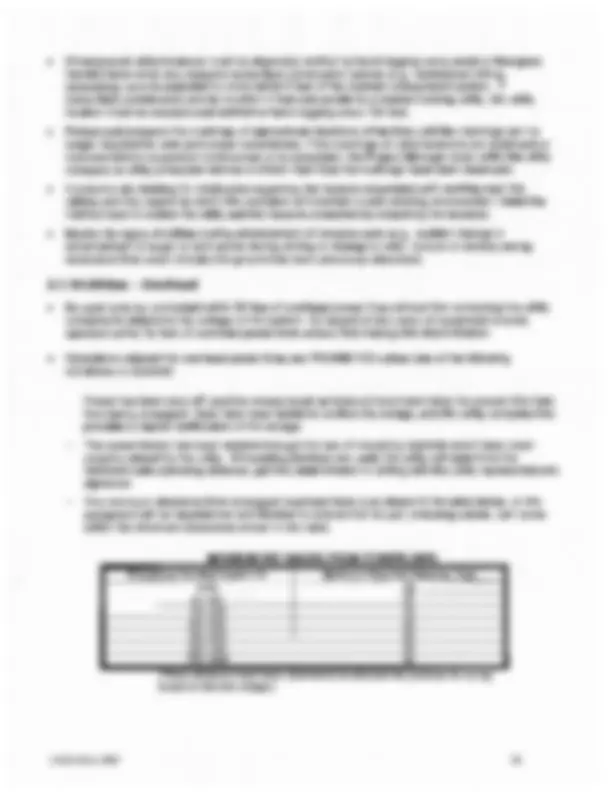
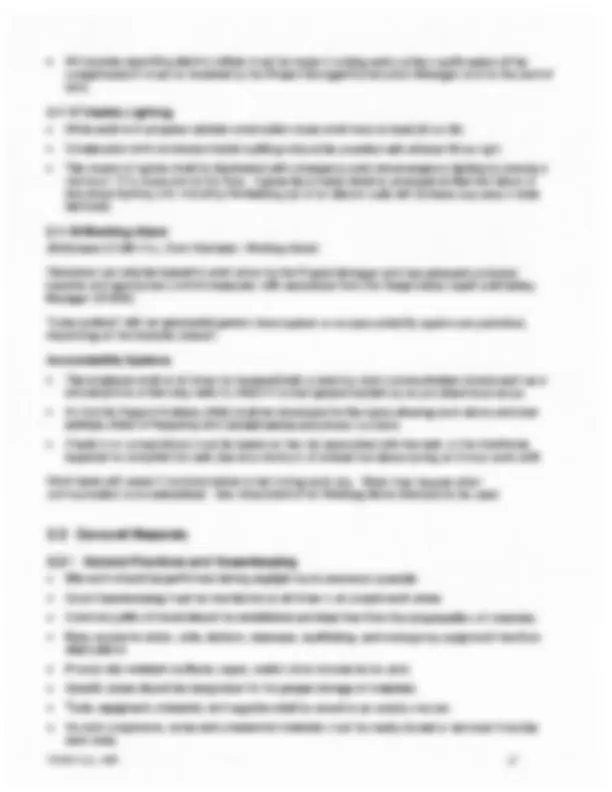
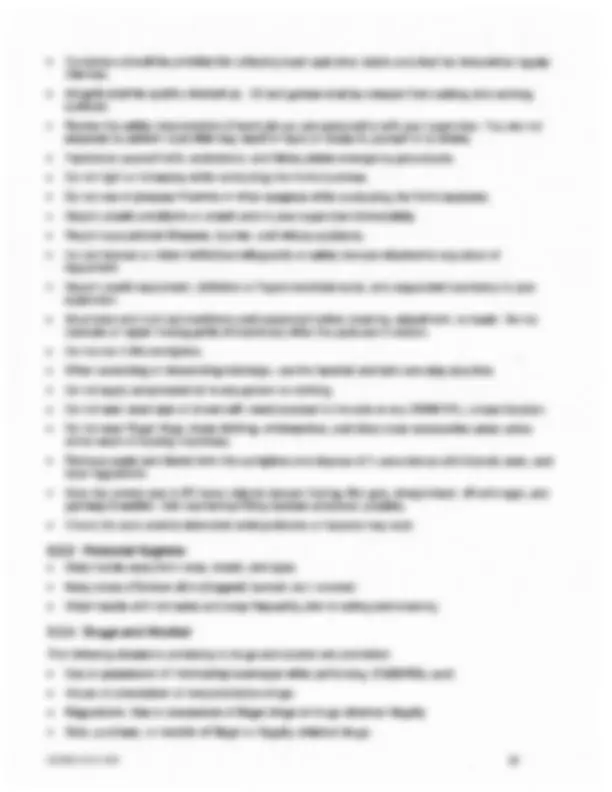
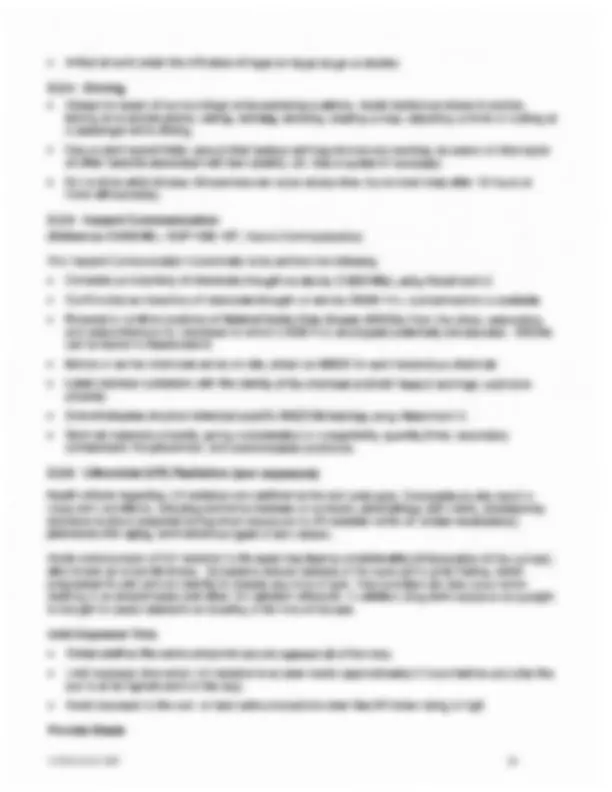
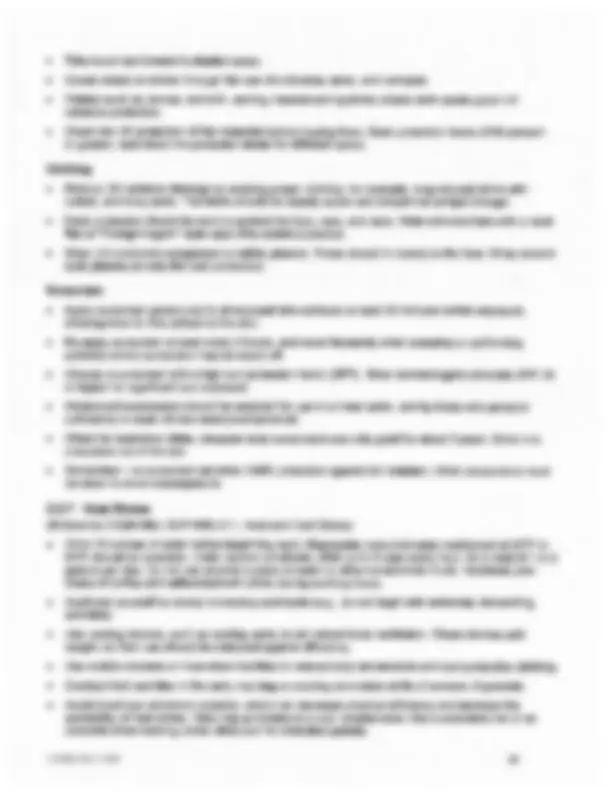
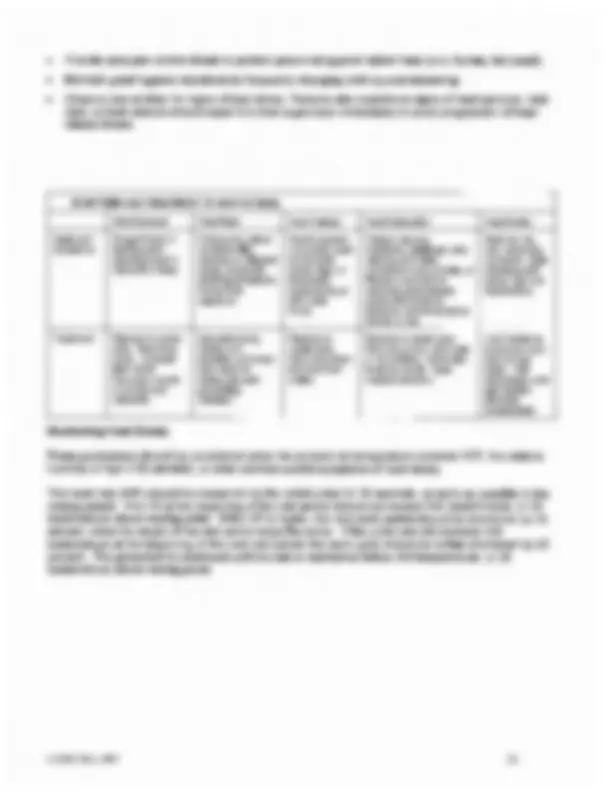
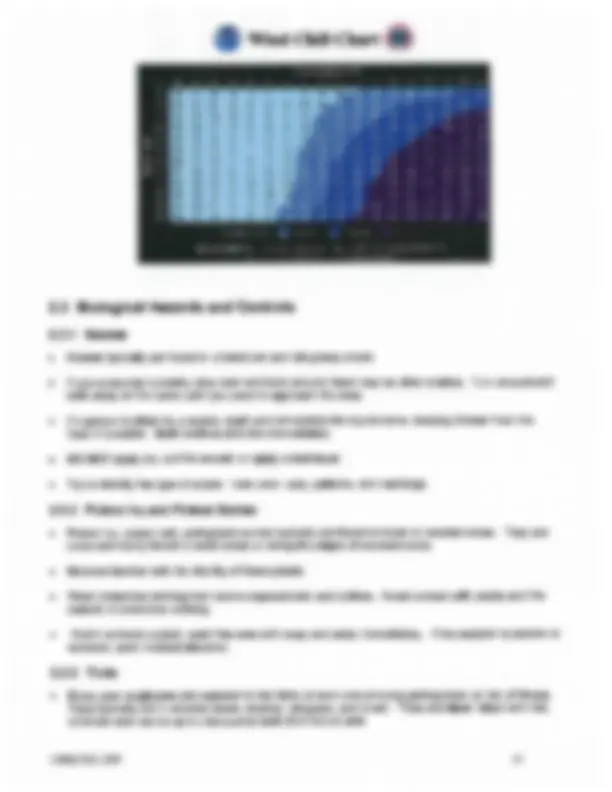
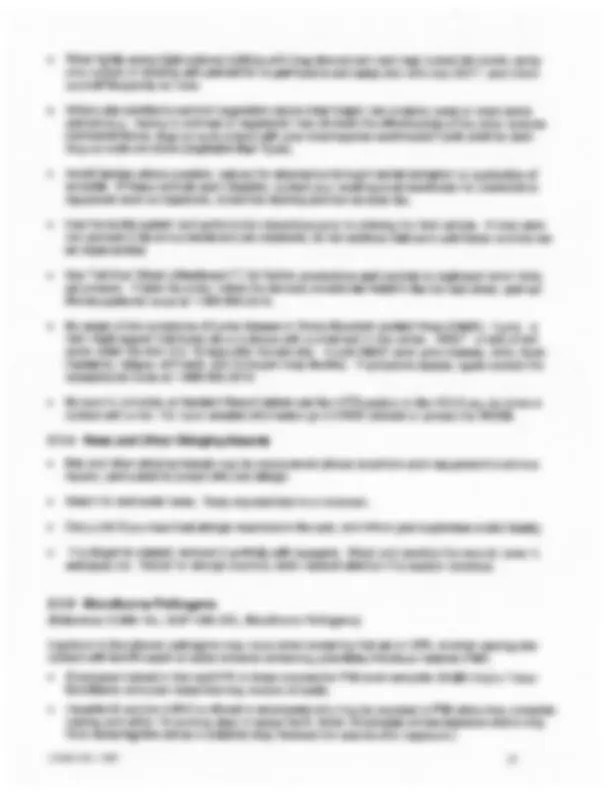
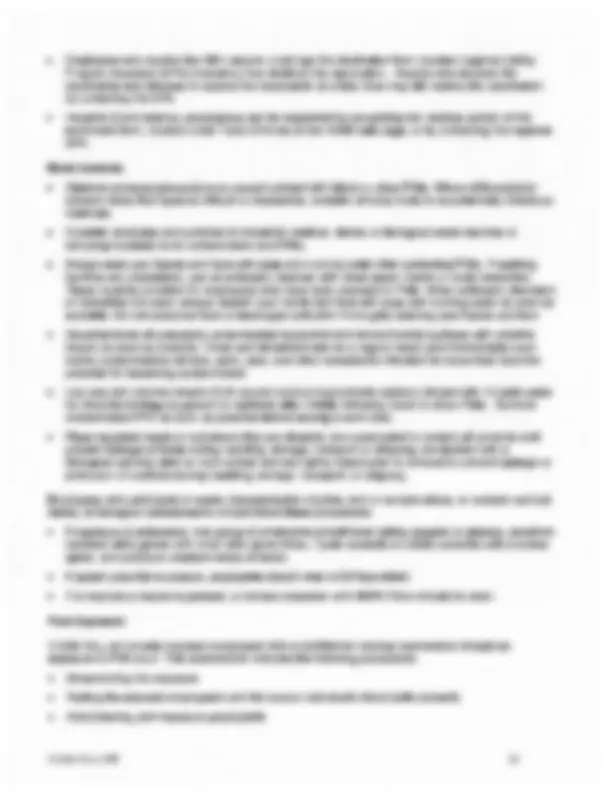
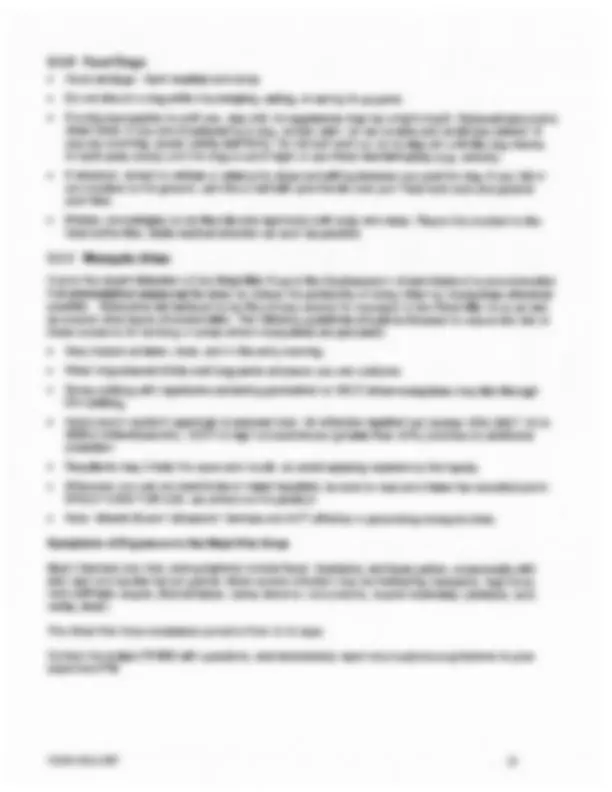
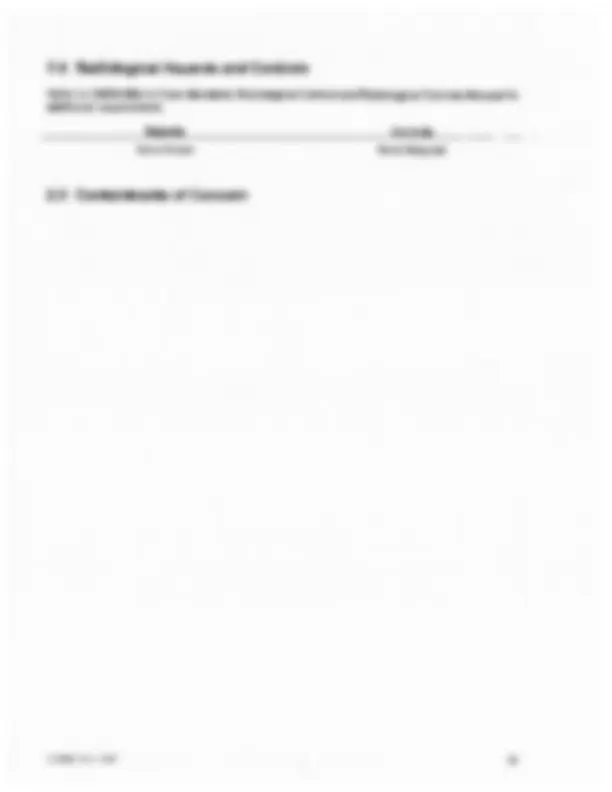
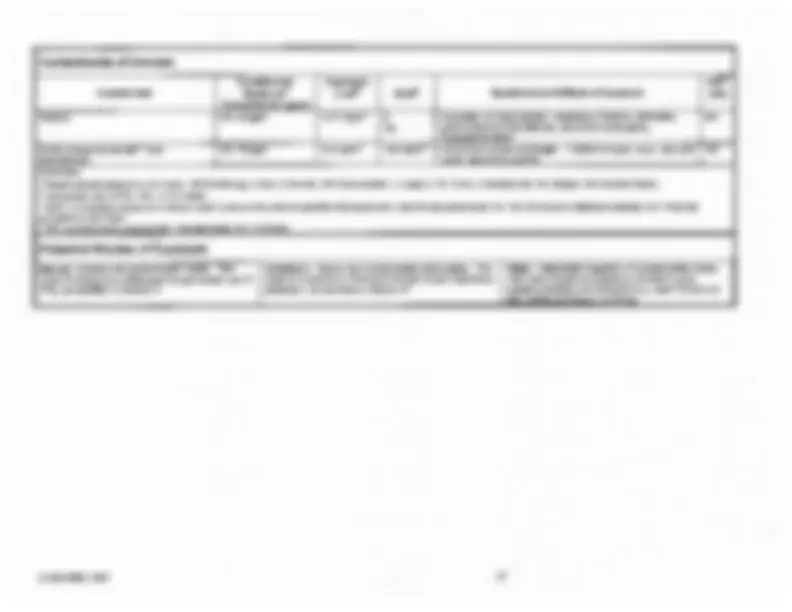
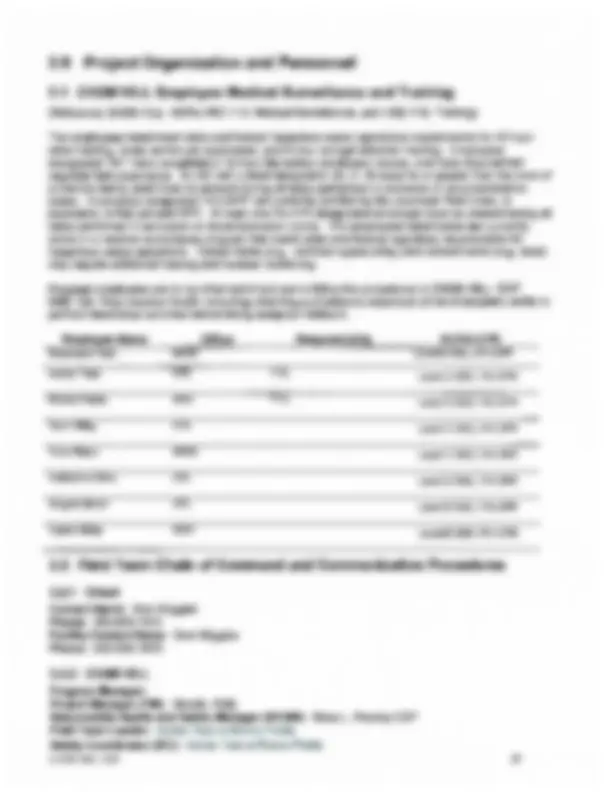
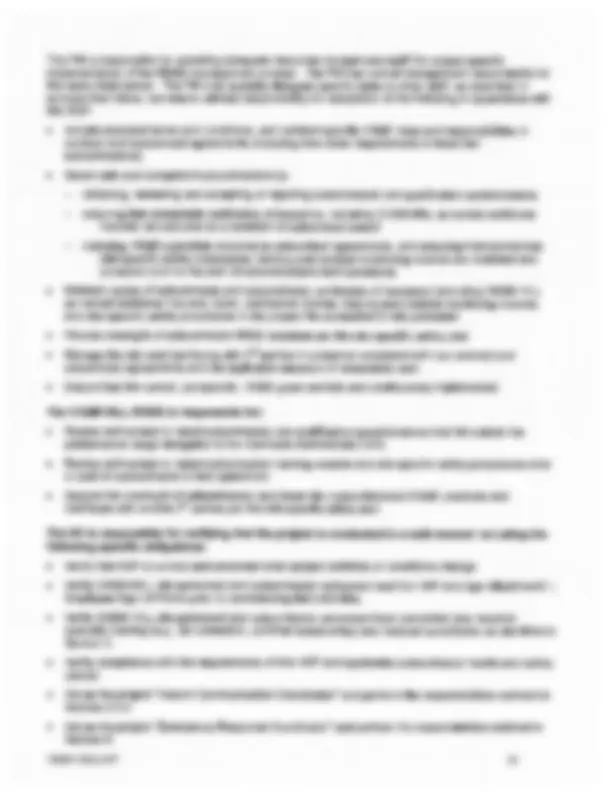
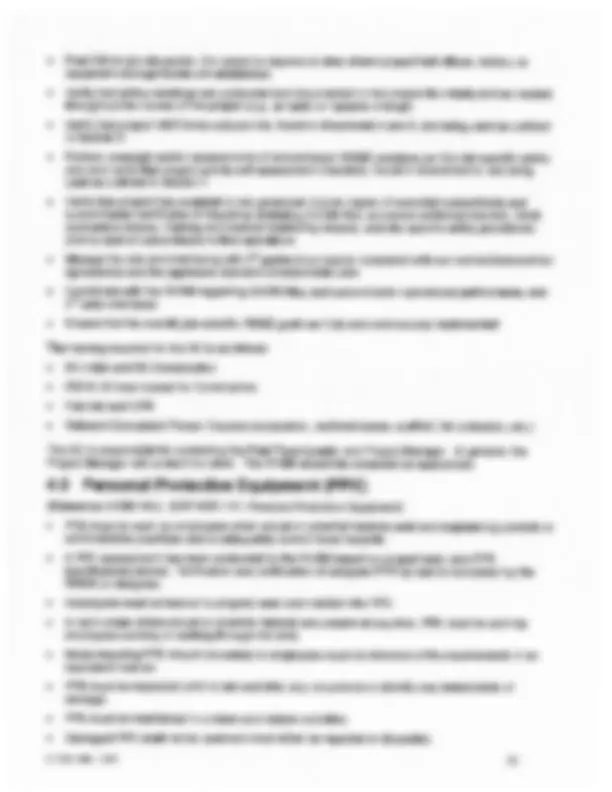
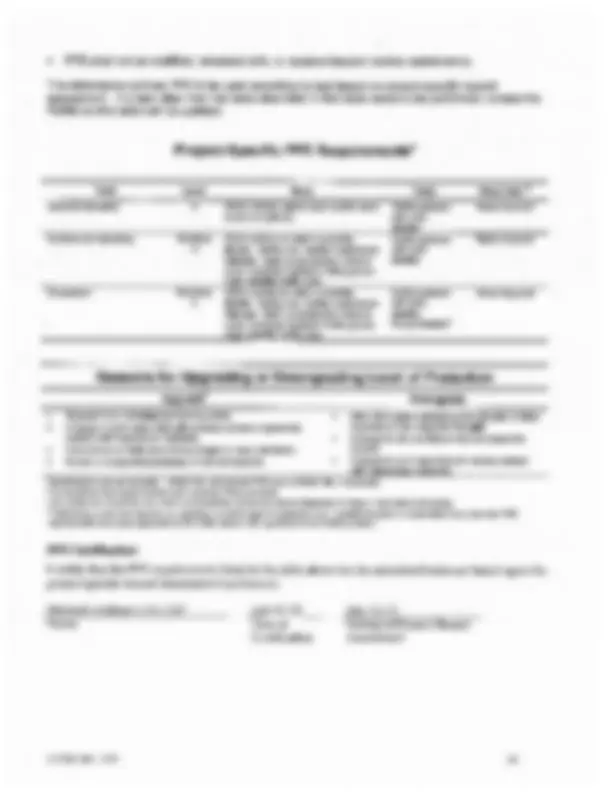
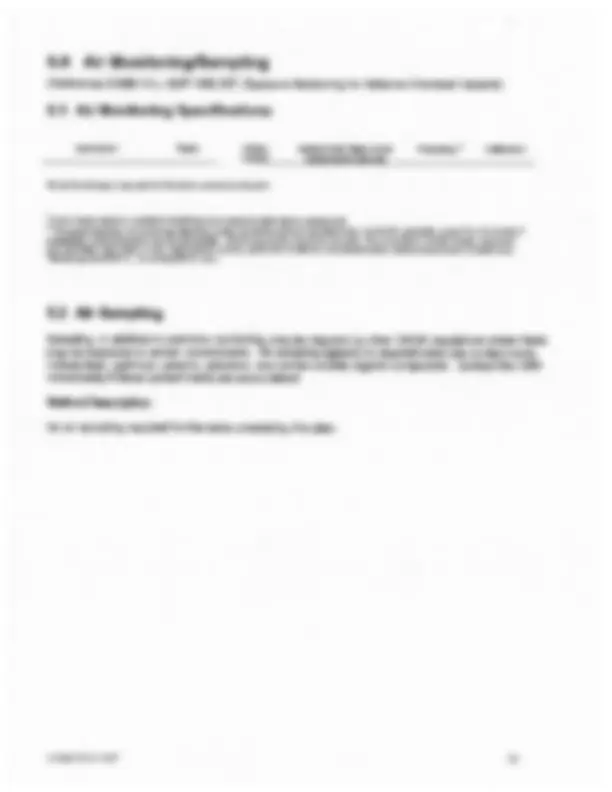
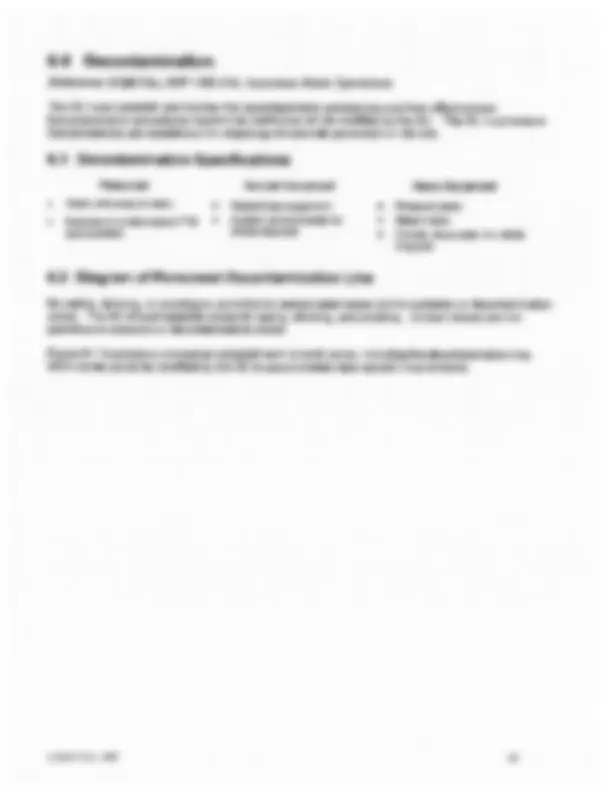
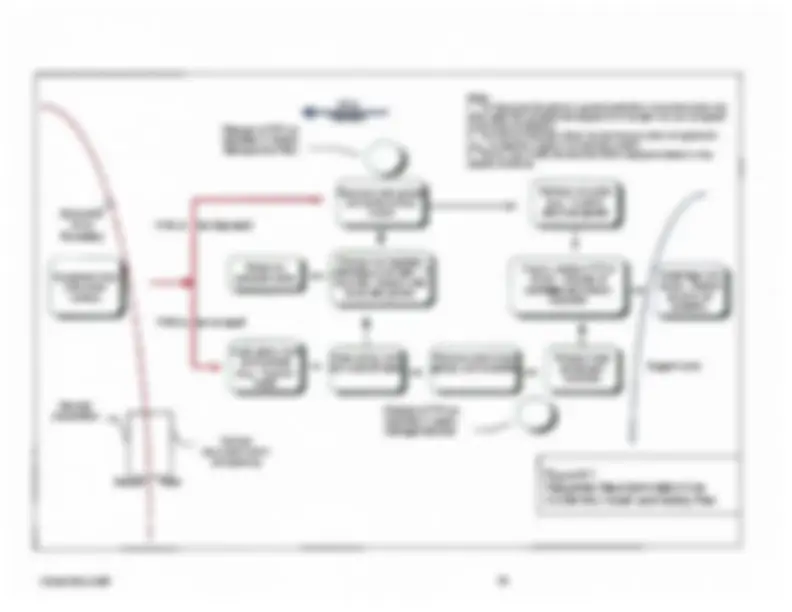
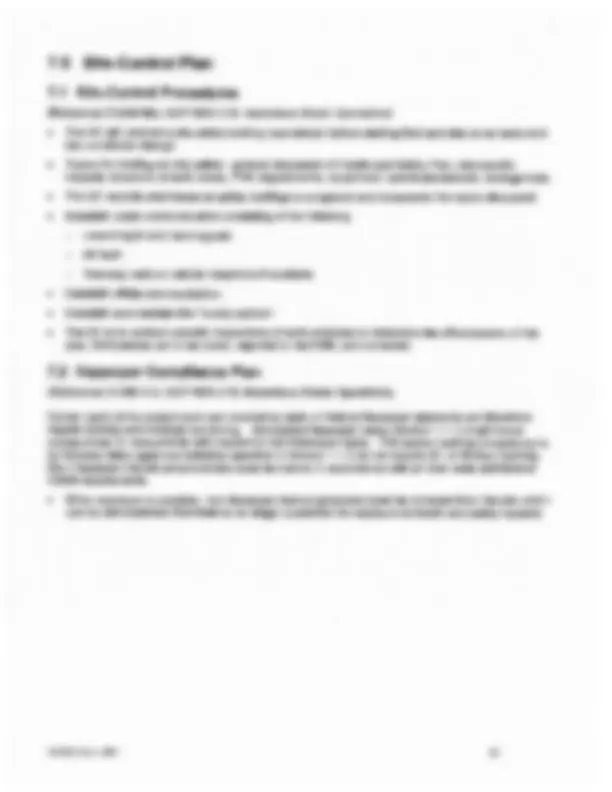
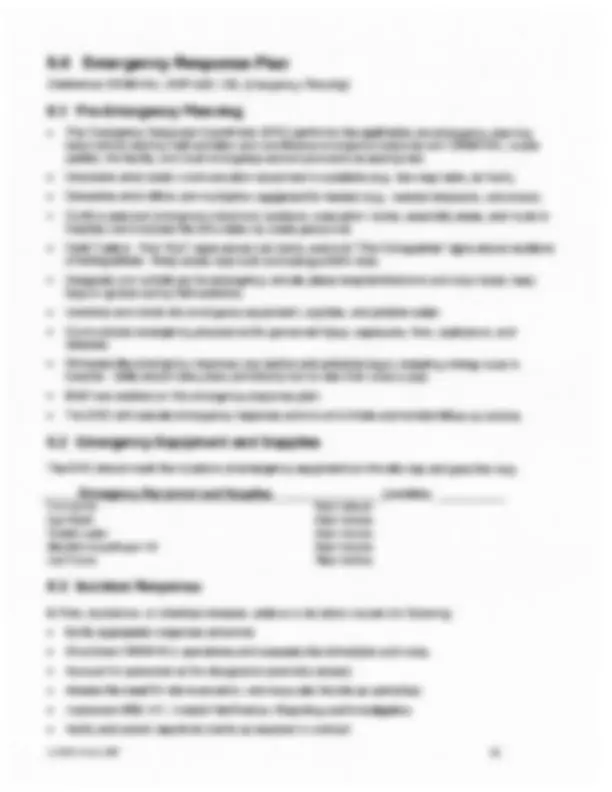
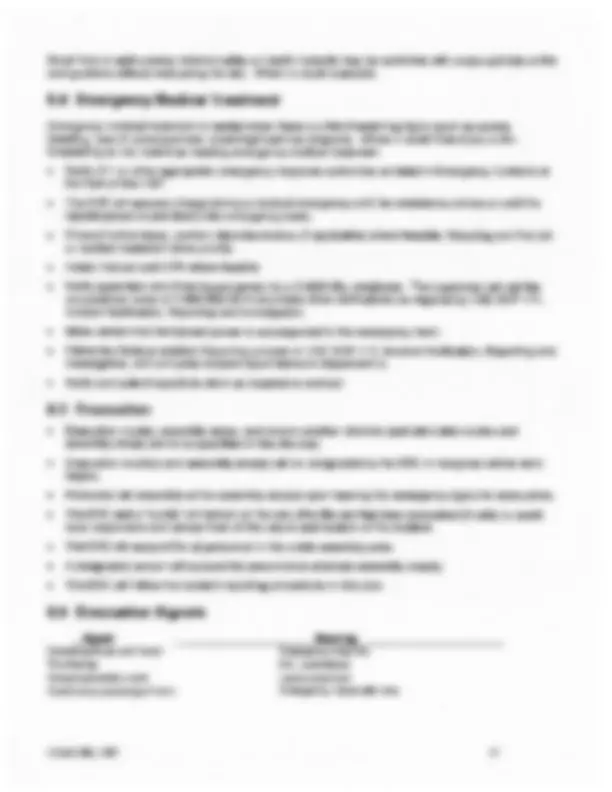
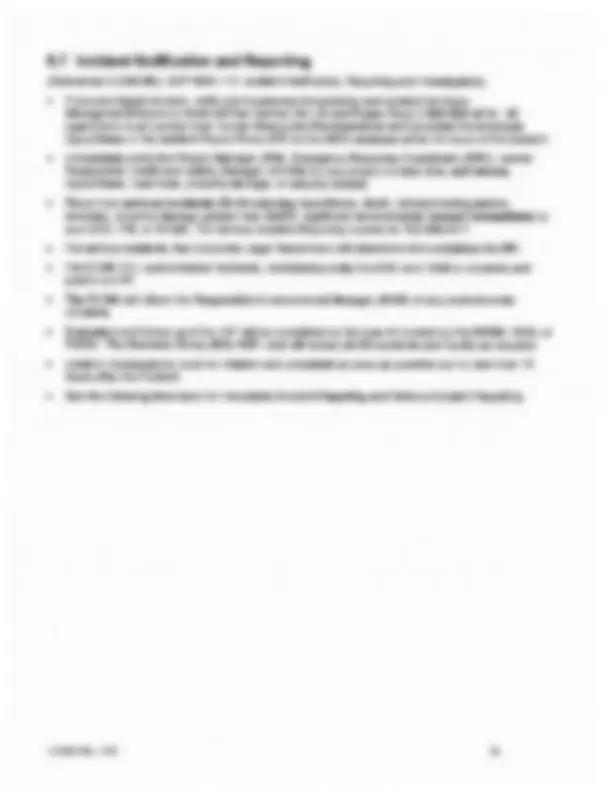
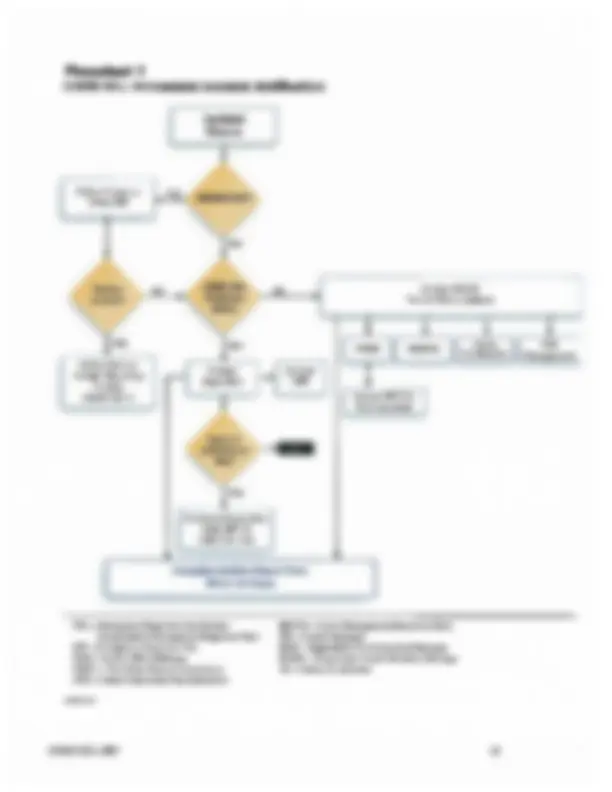
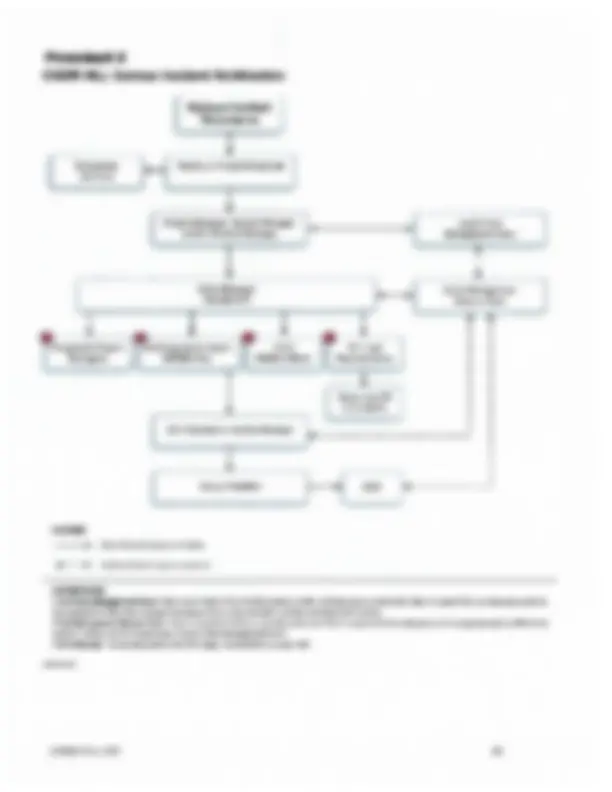
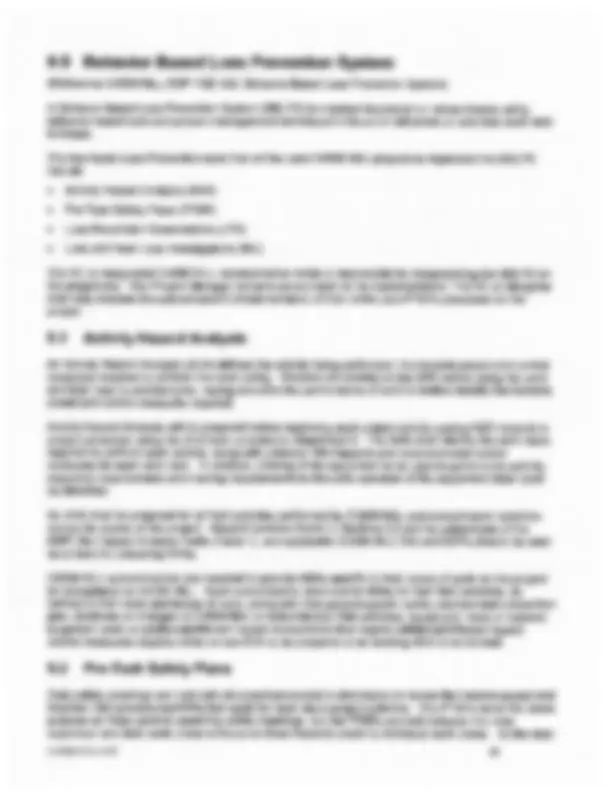
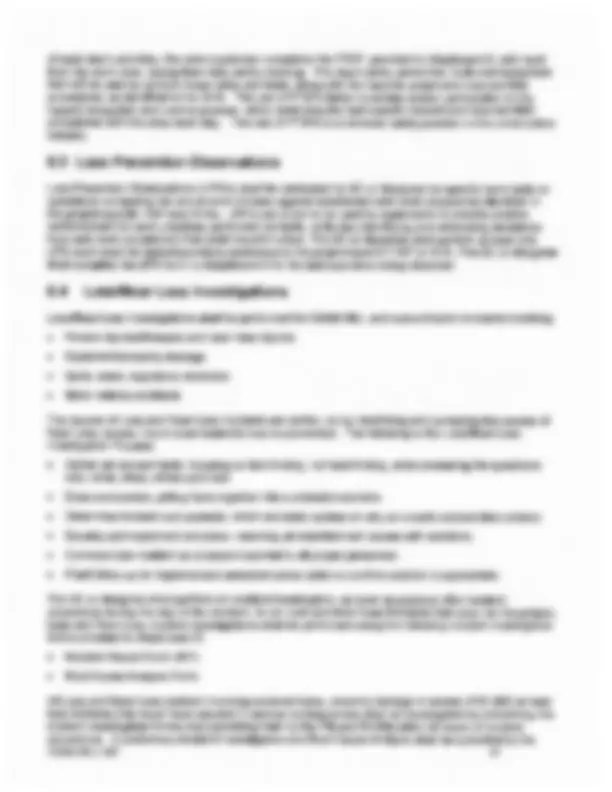
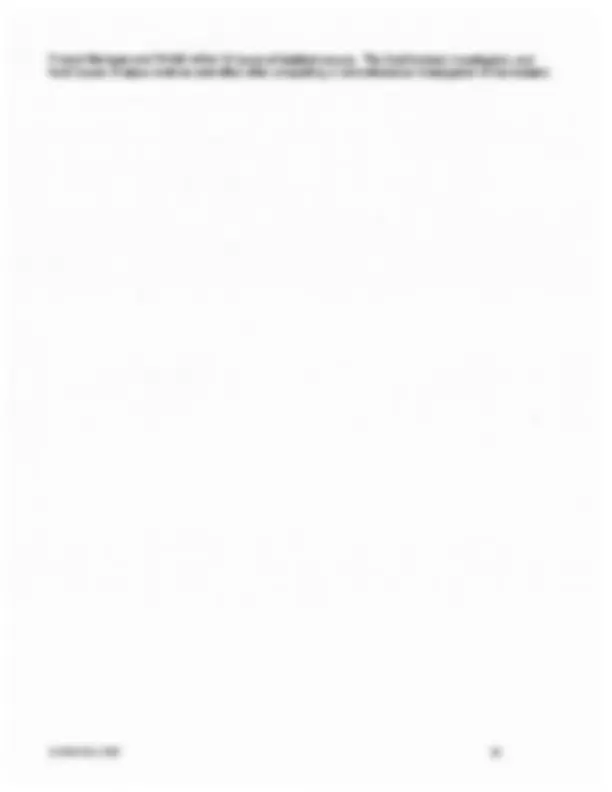
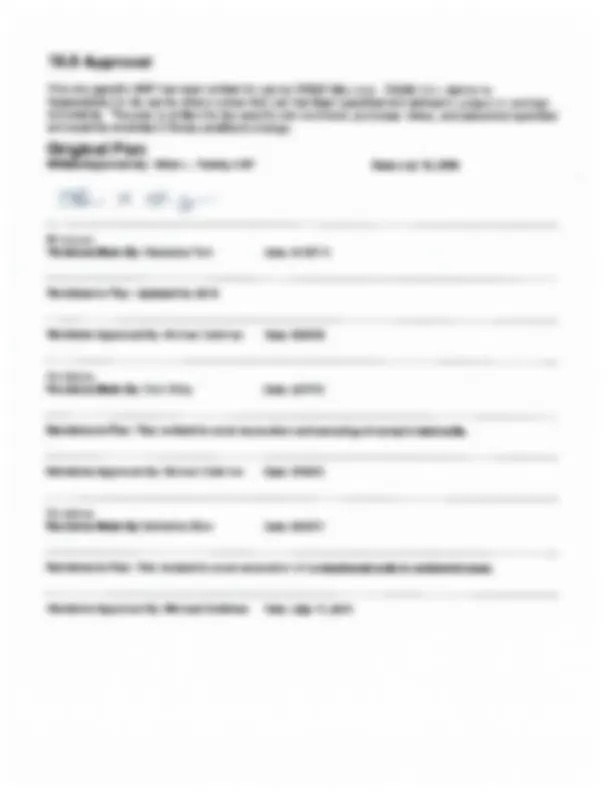
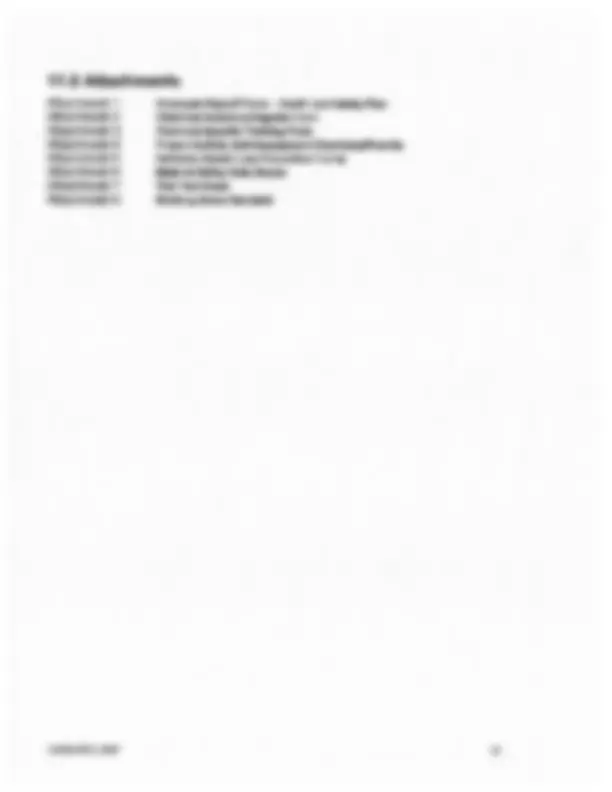
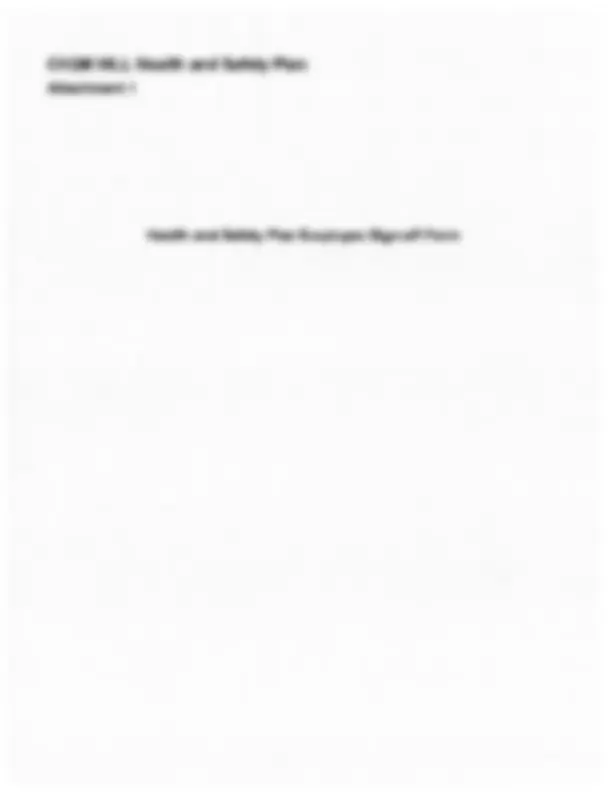
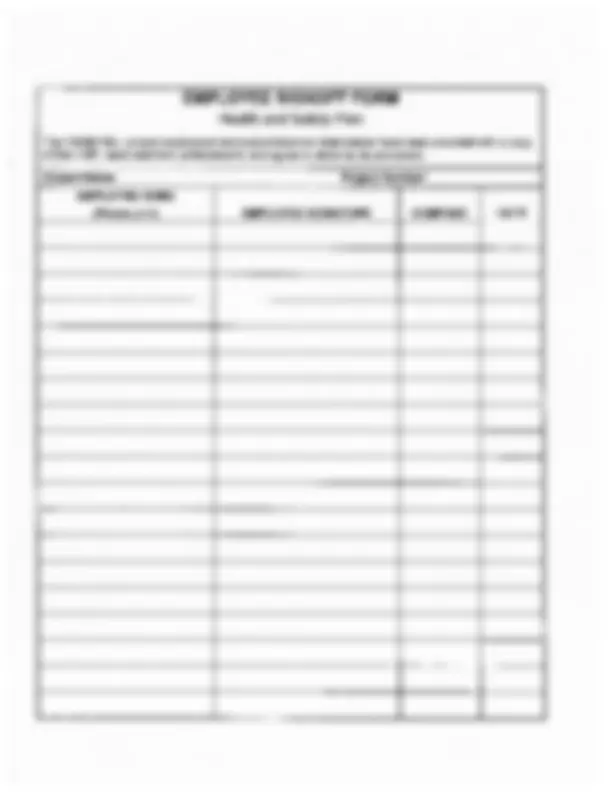
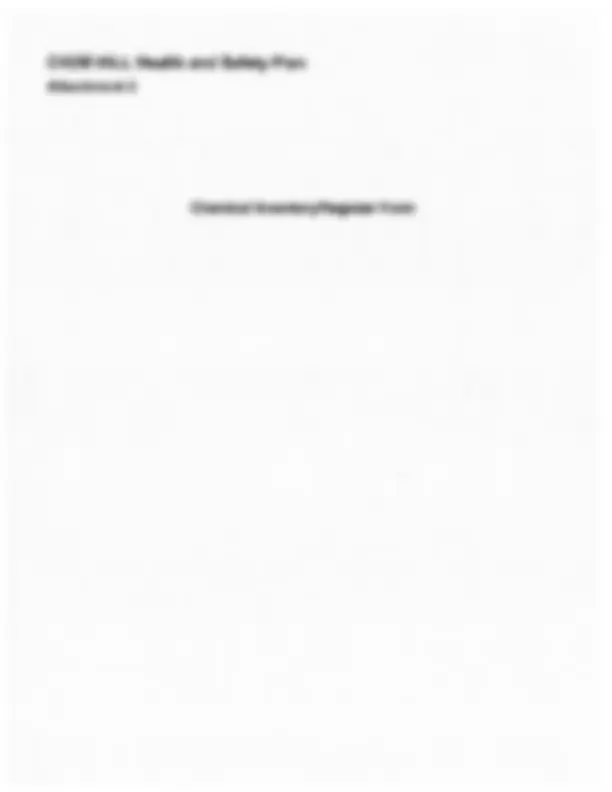
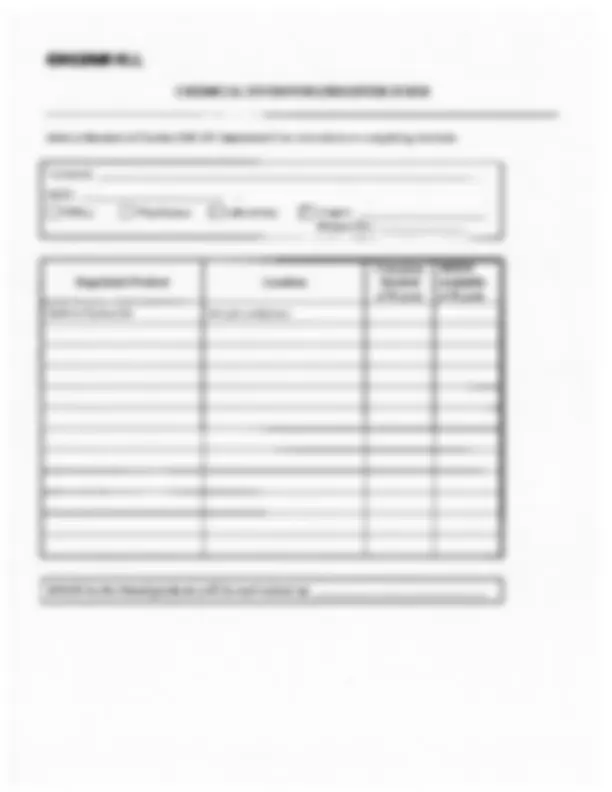
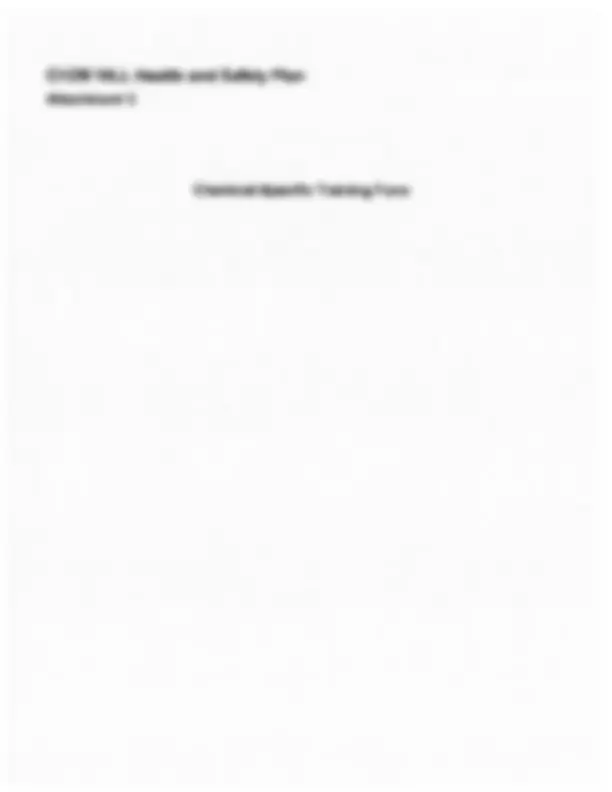
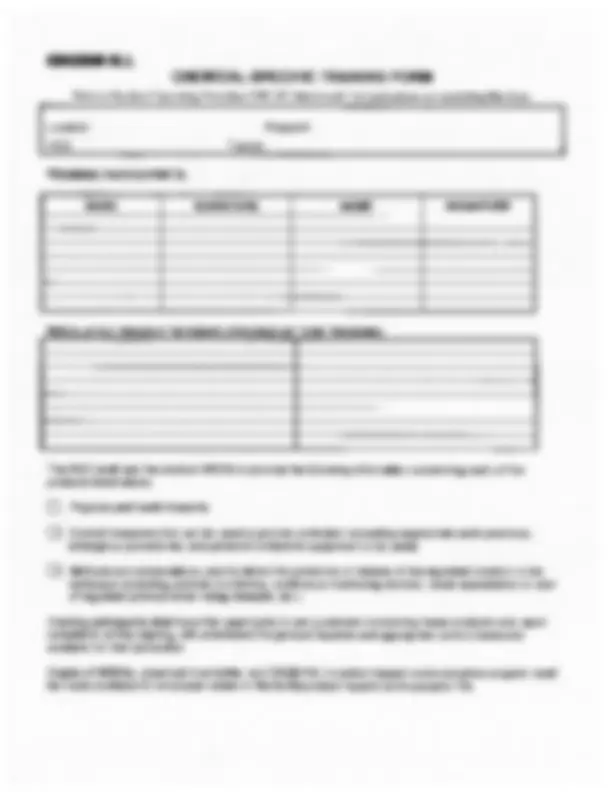
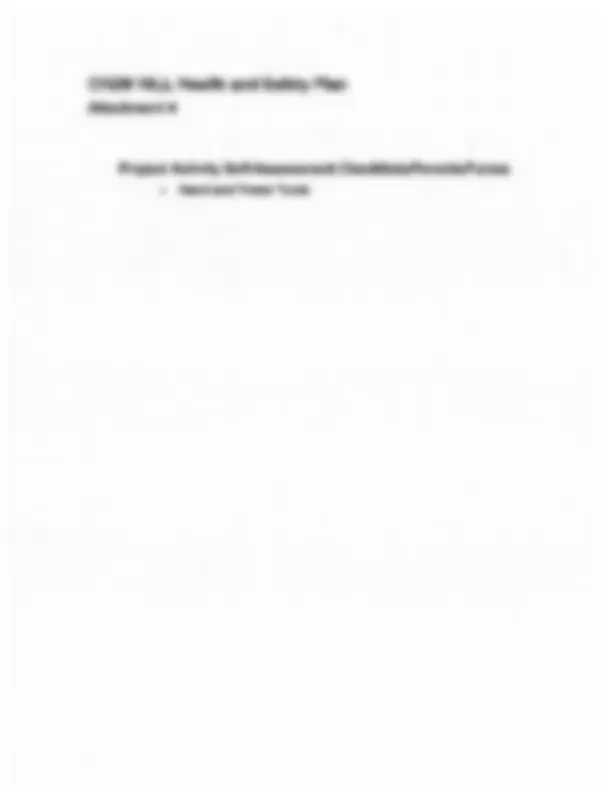
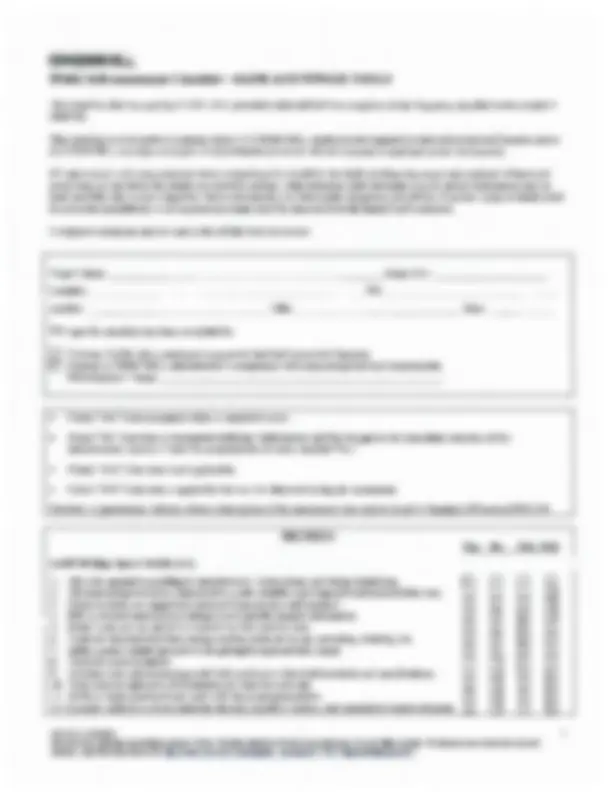
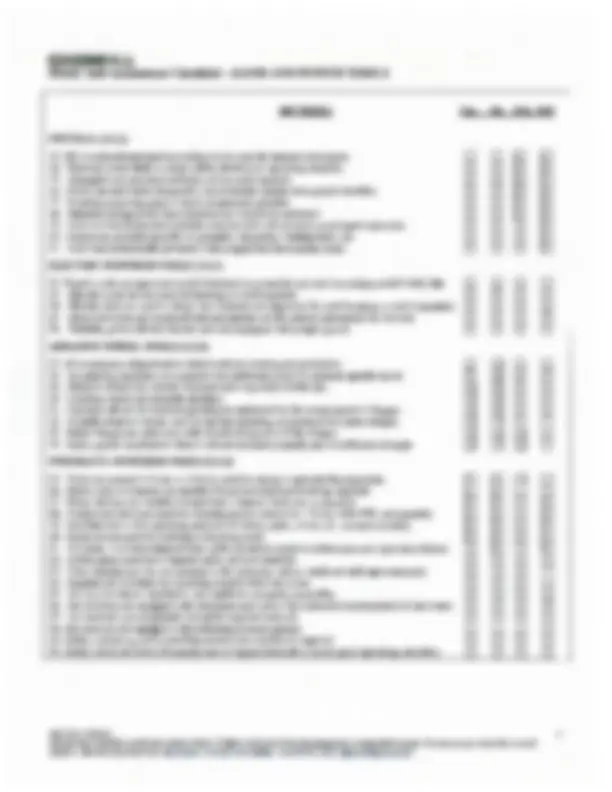
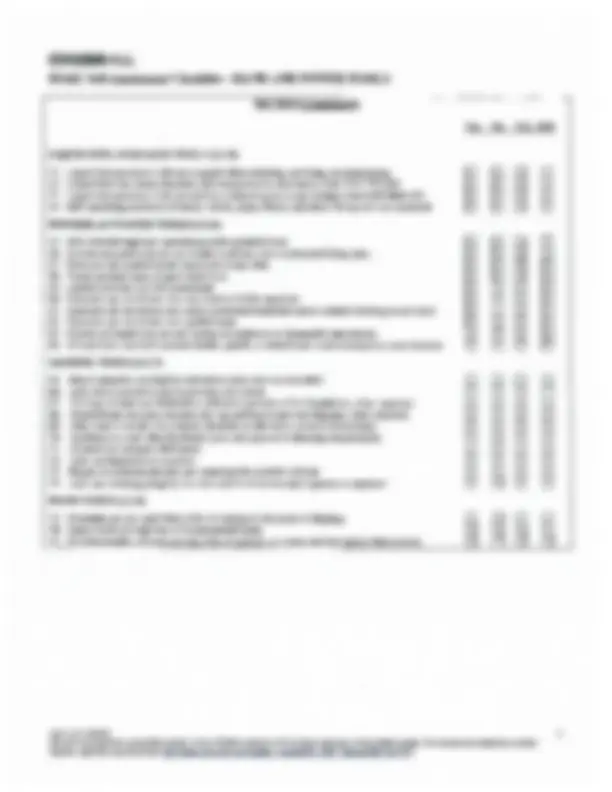
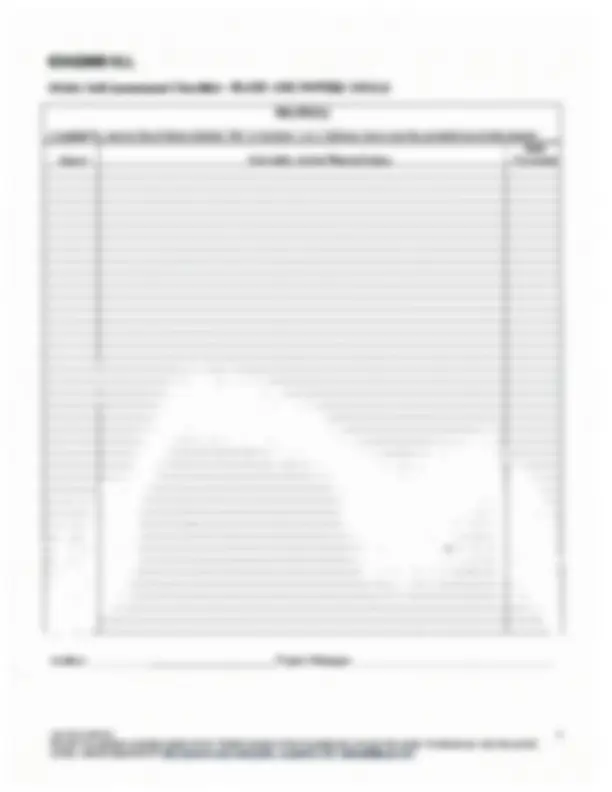
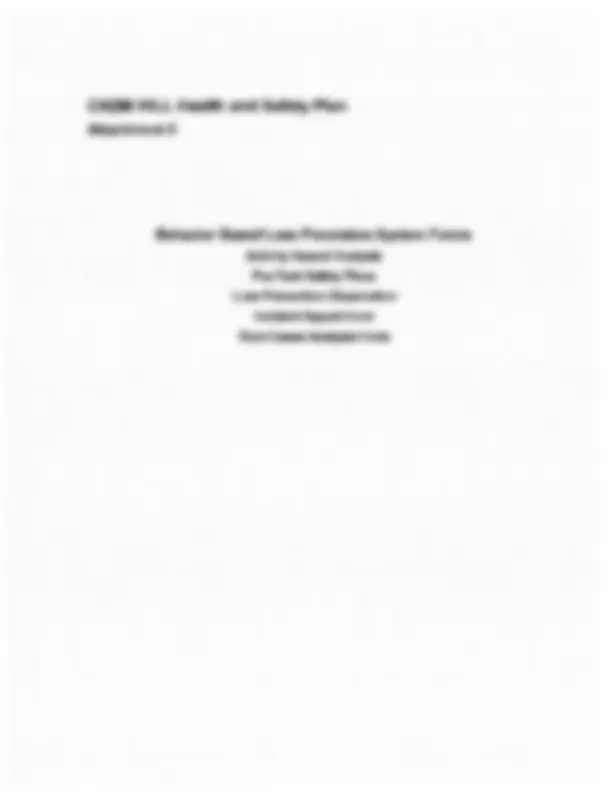
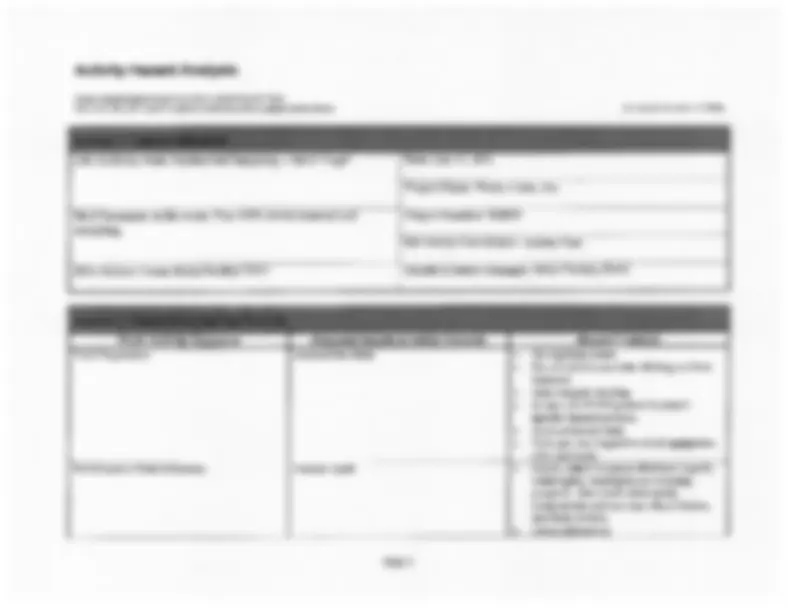
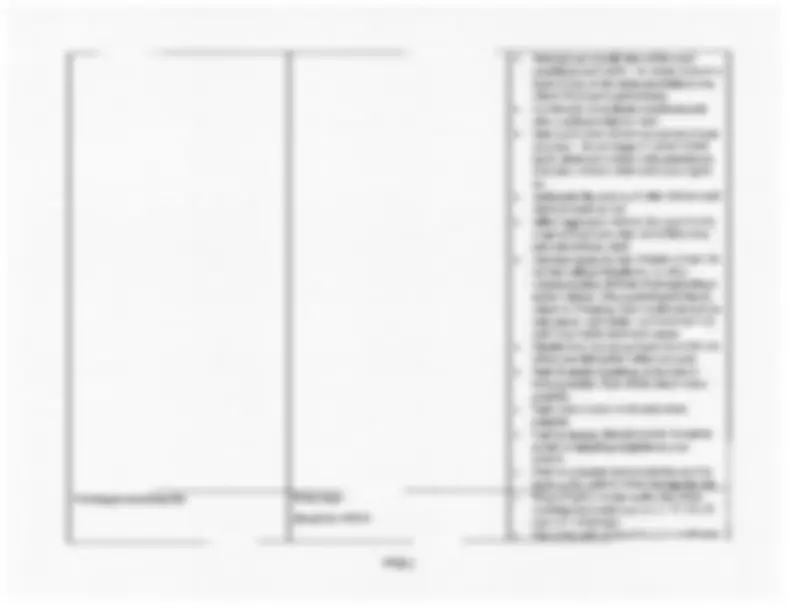
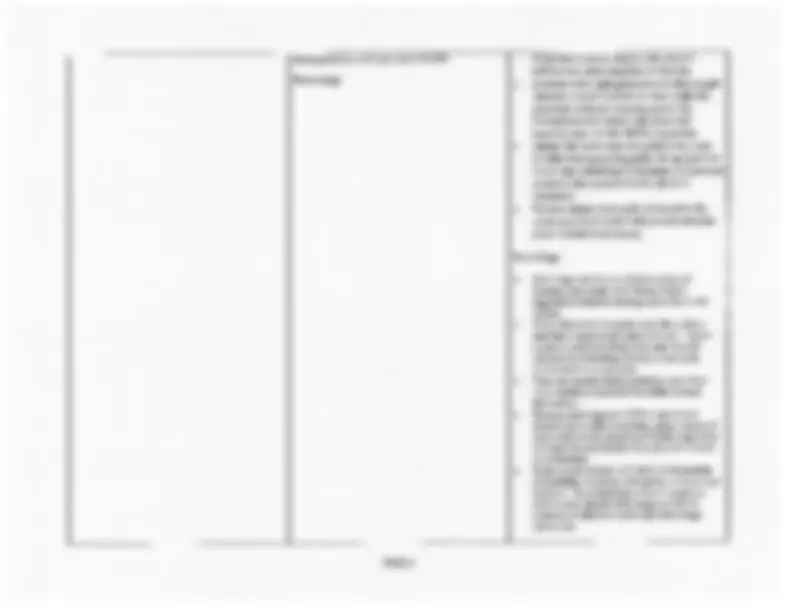
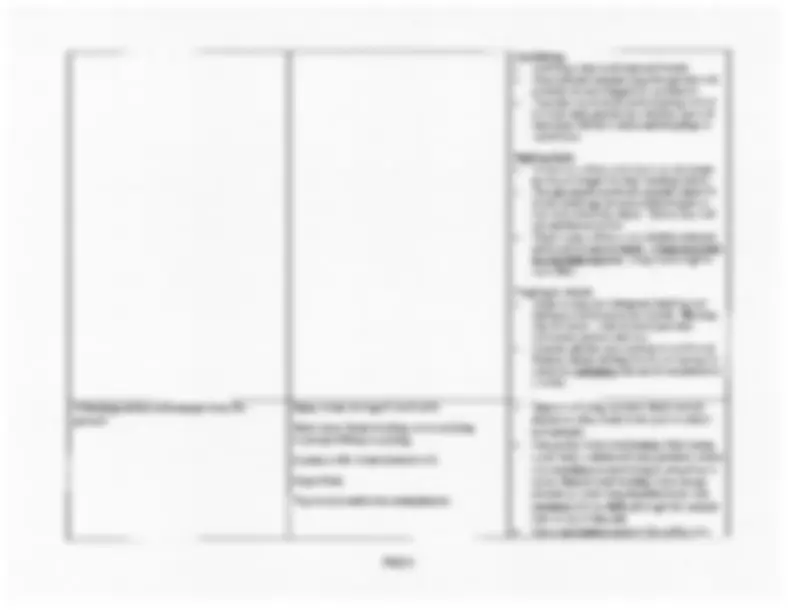
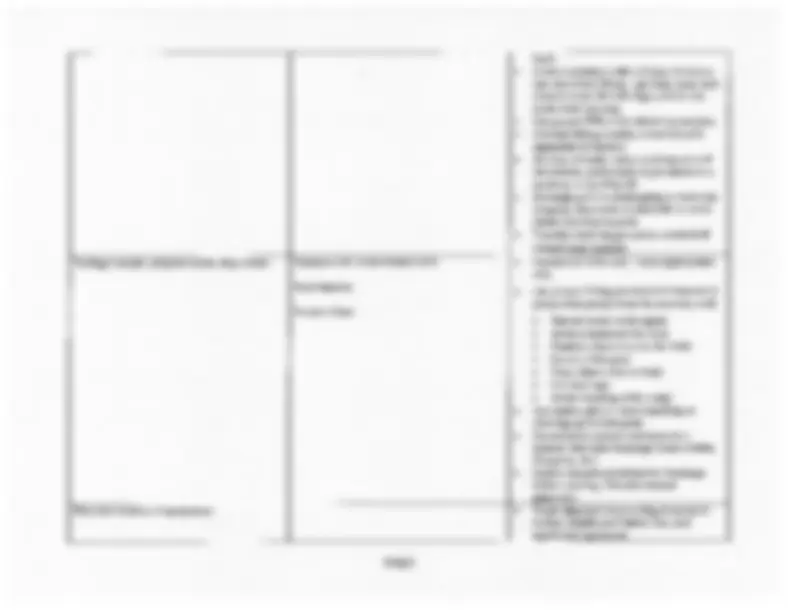
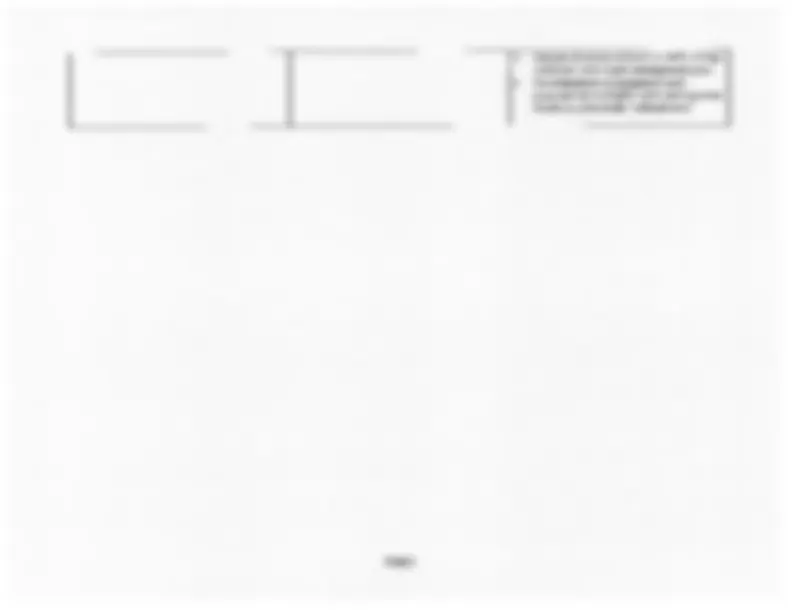
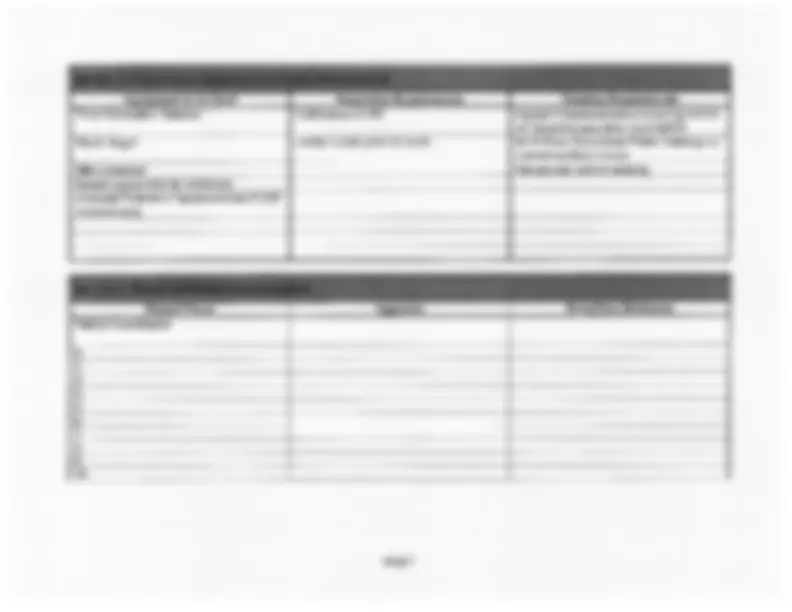
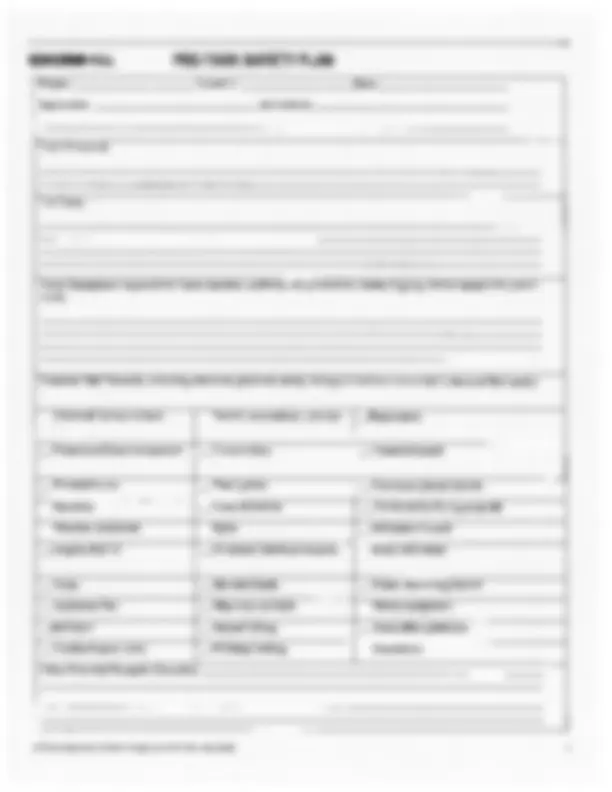
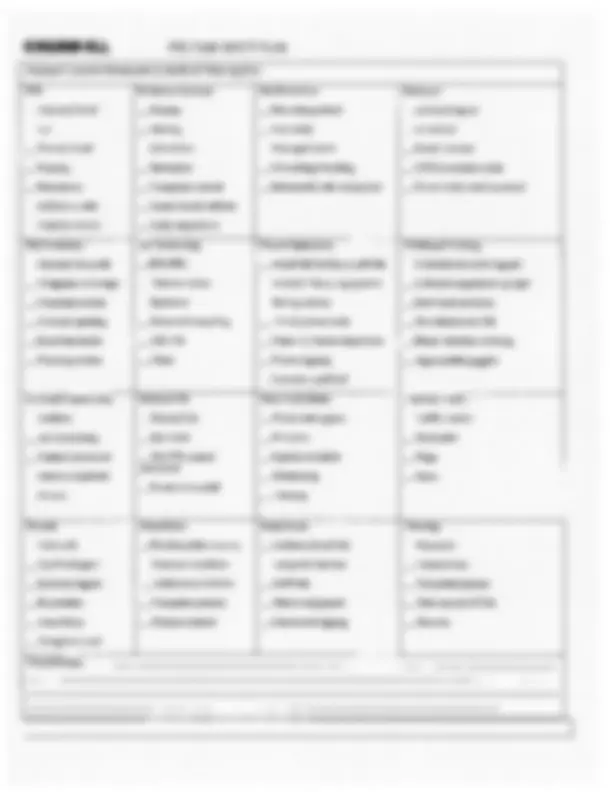
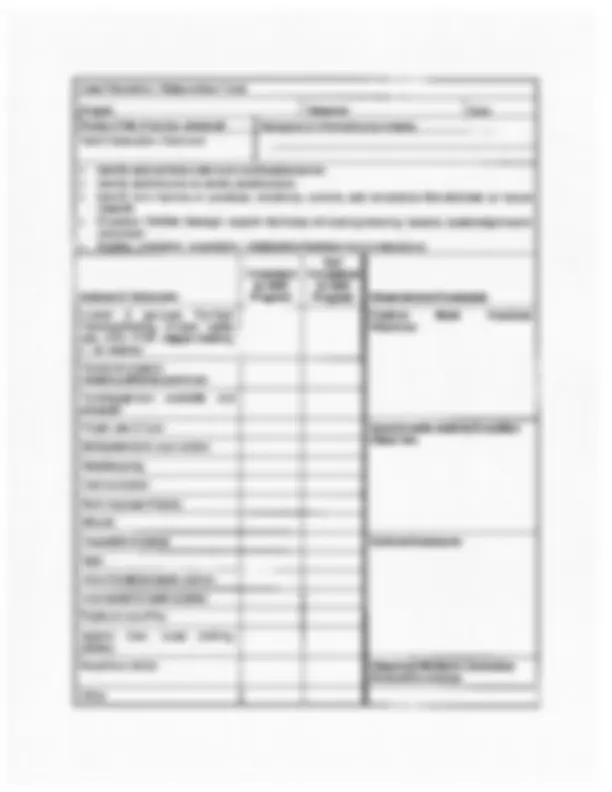
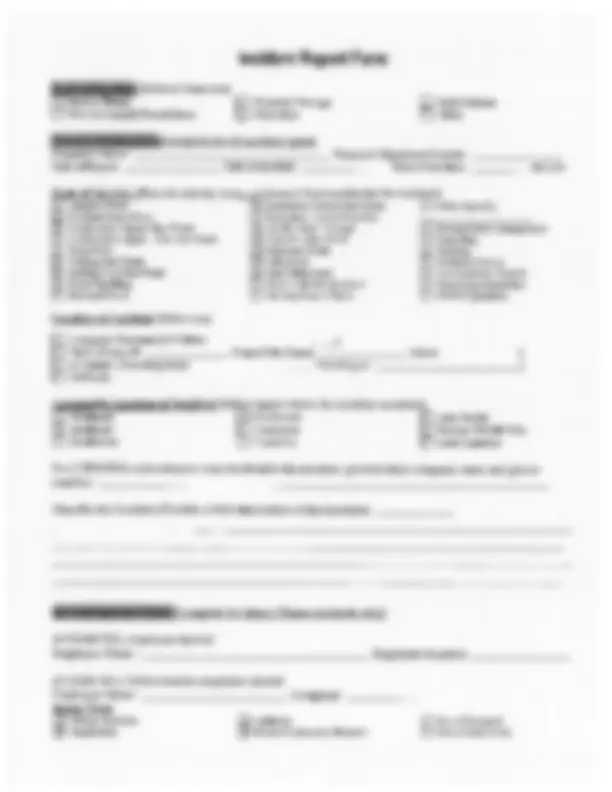
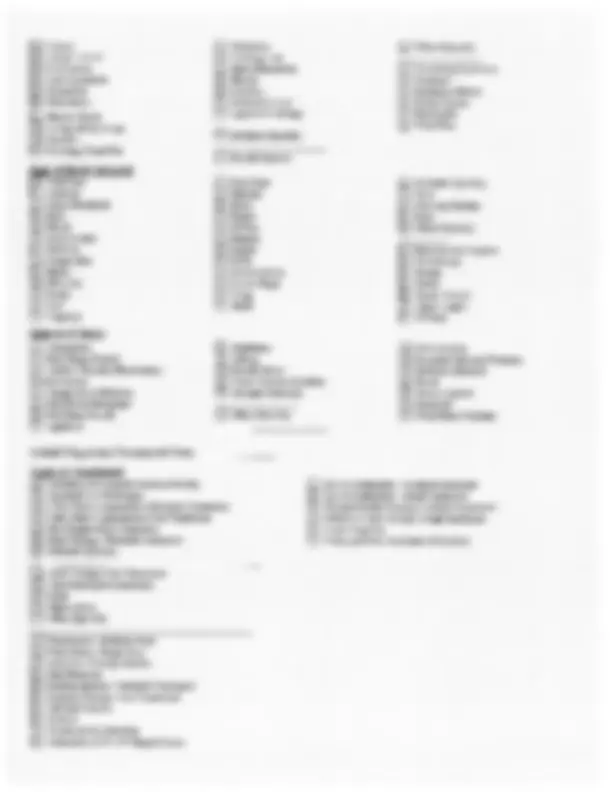
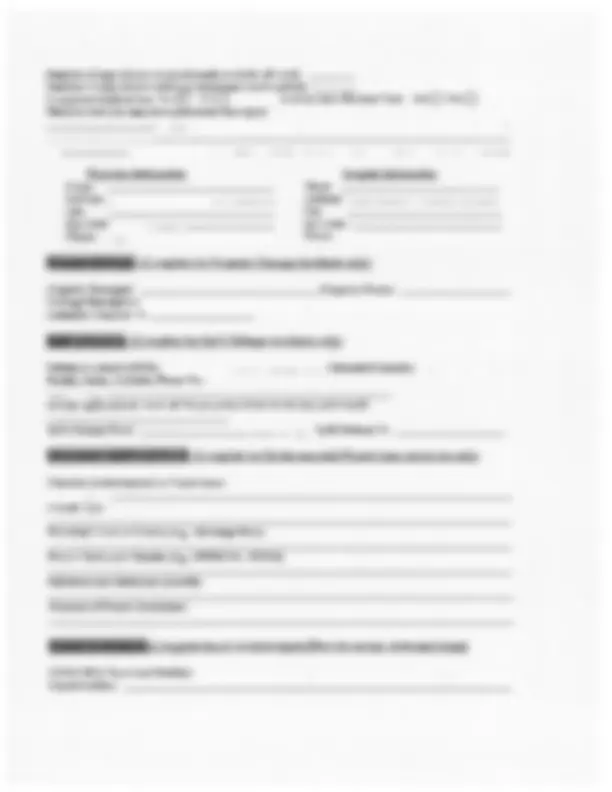
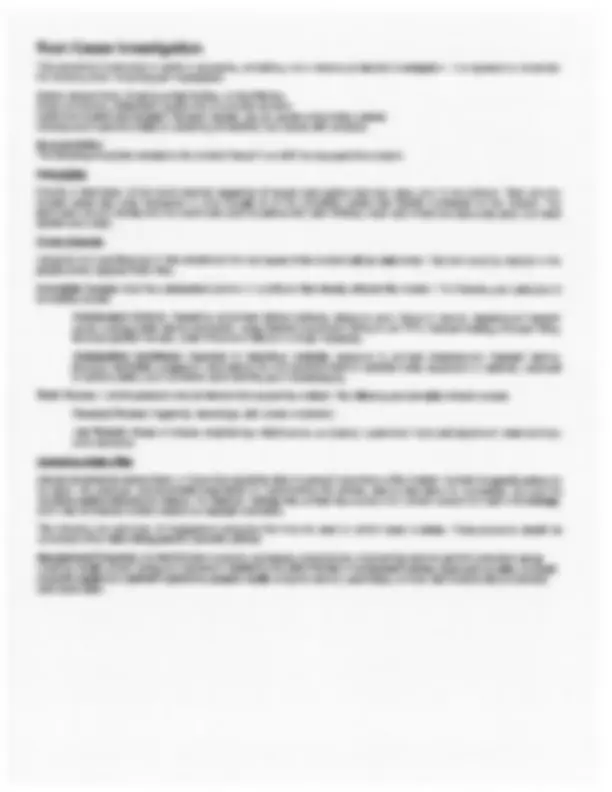
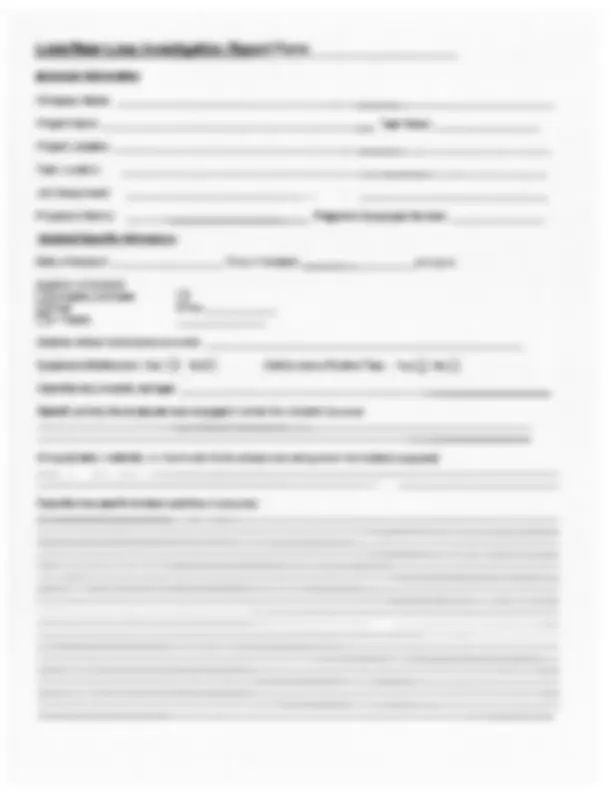
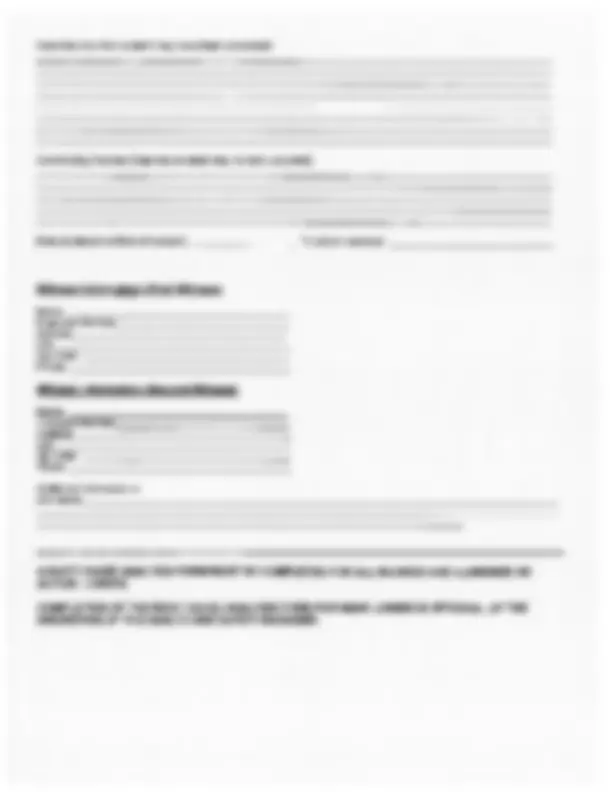
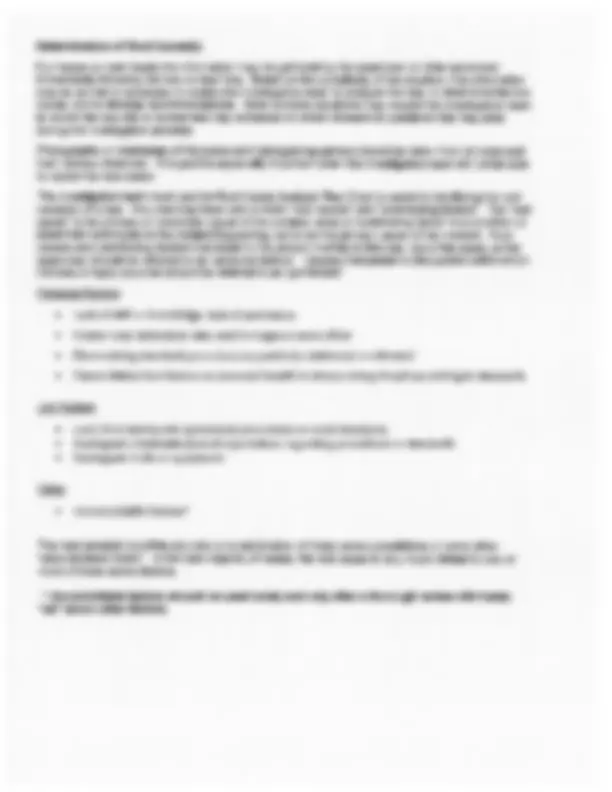
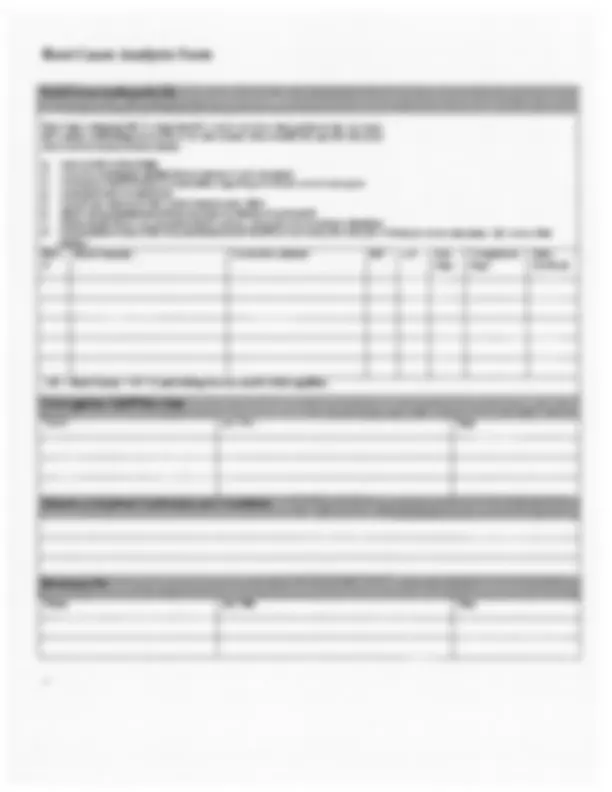
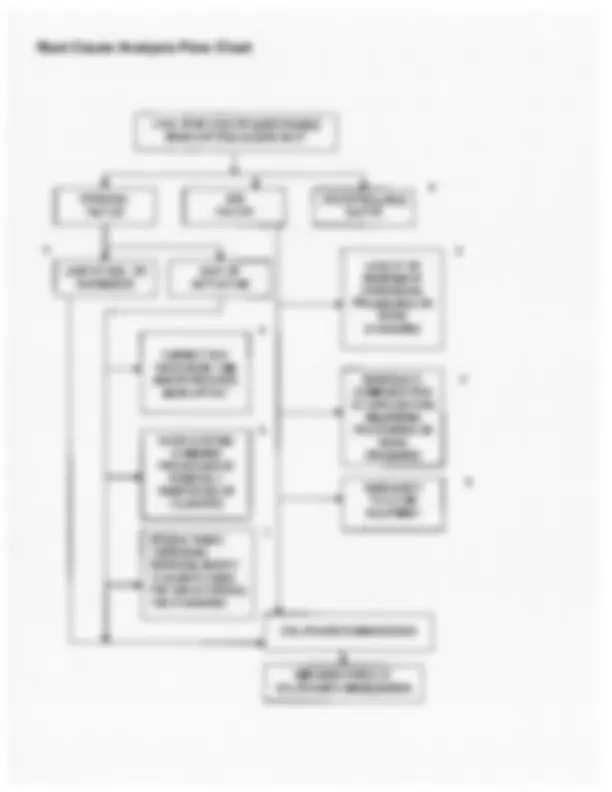
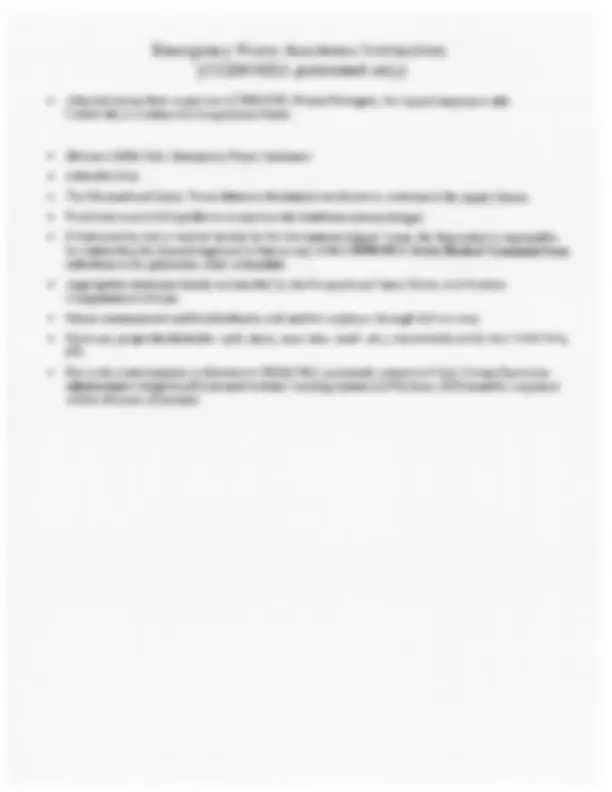

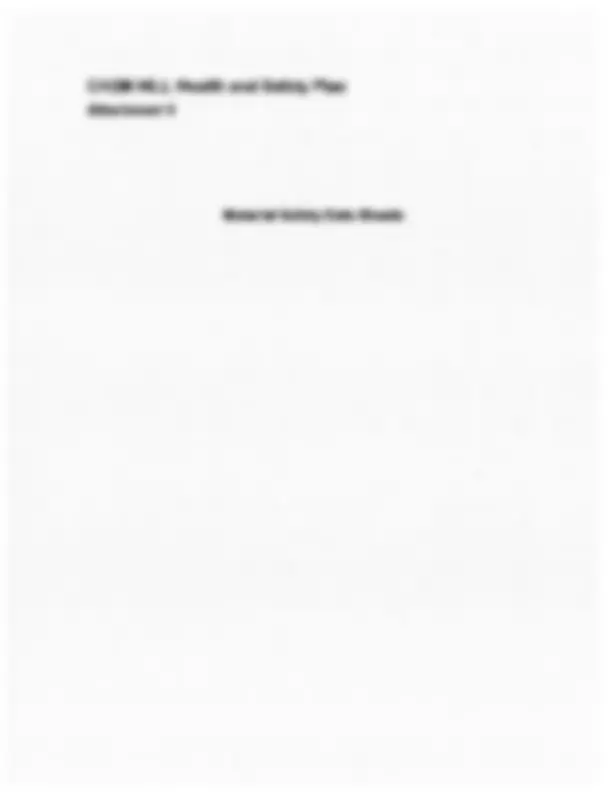
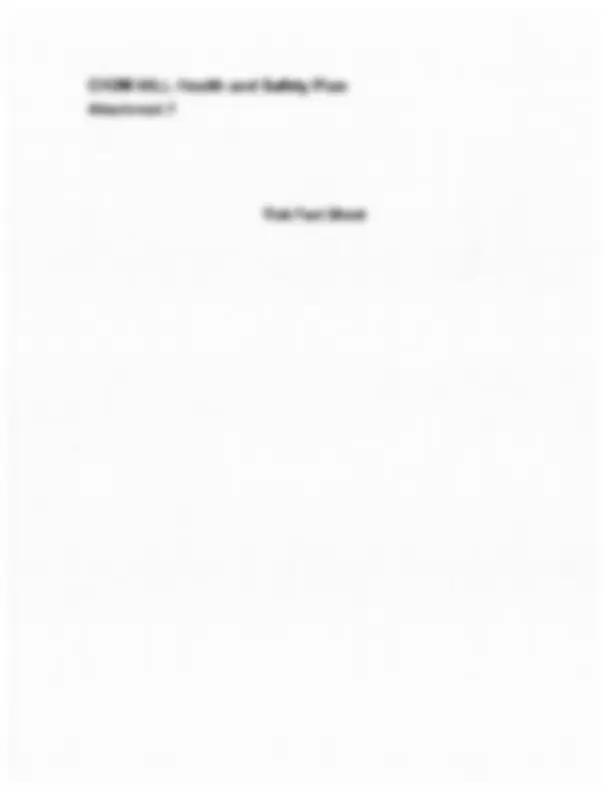
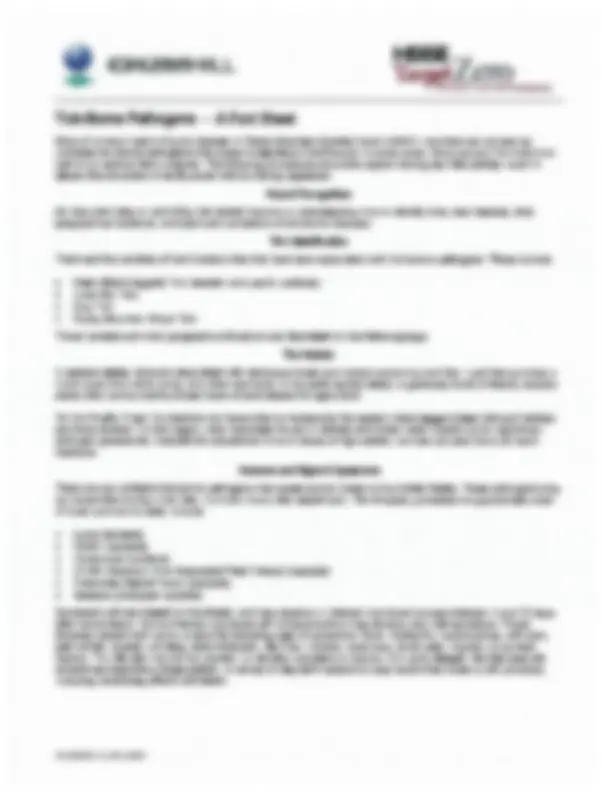
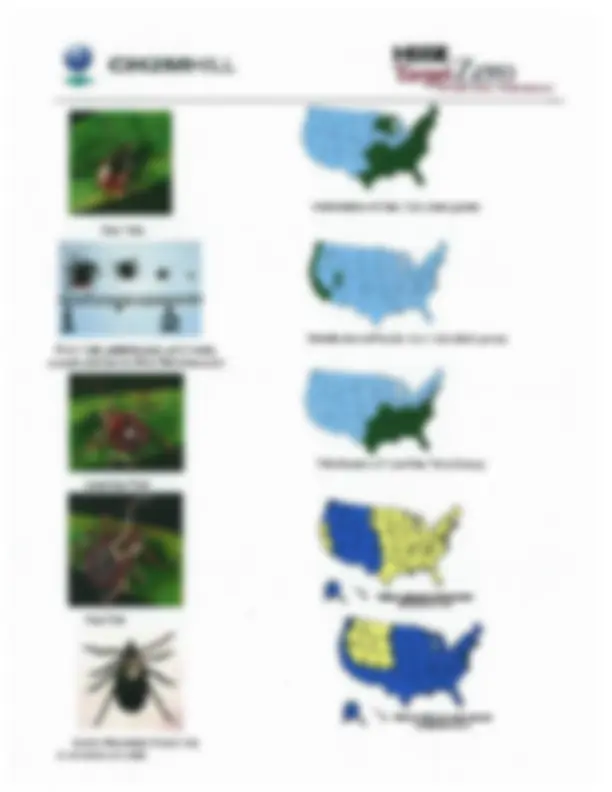
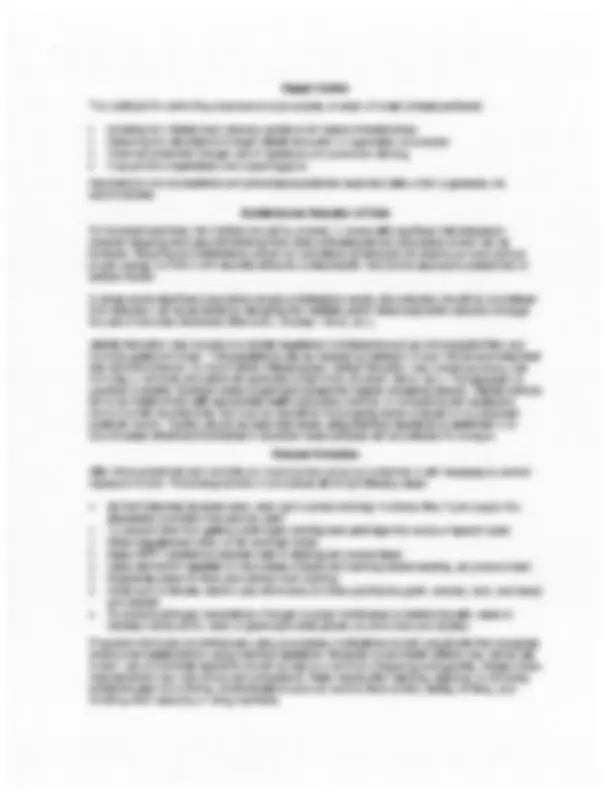
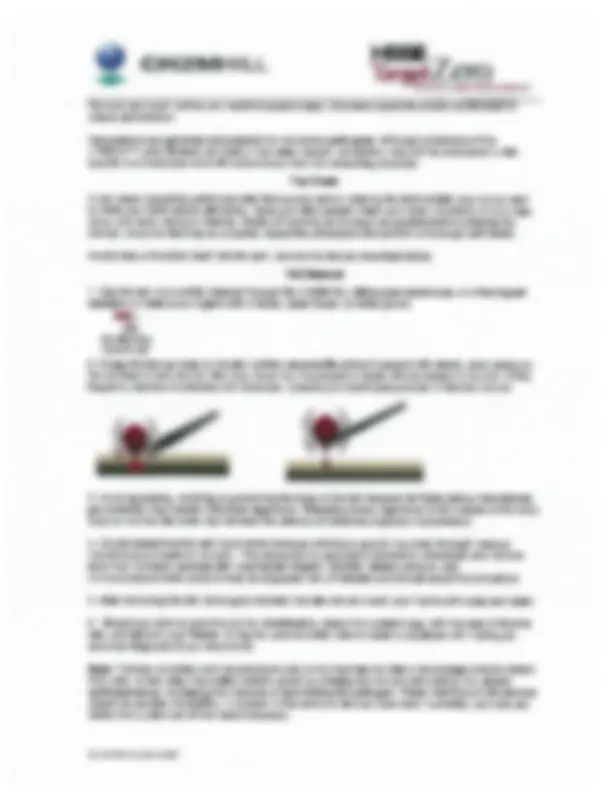

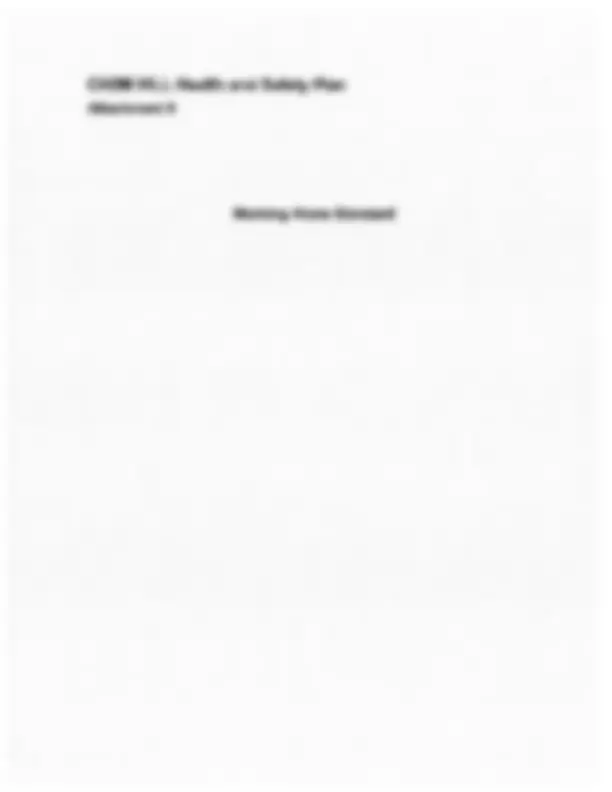


Study with the several resources on Docsity
Earn points by helping other students or get them with a premium plan
Prepare for your exams
Study with the several resources on Docsity
Earn points to download
Earn points by helping other students or get them with a premium plan
Community
Ask the community for help and clear up your study doubts
Discover the best universities in your country according to Docsity users
Free resources
Download our free guides on studying techniques, anxiety management strategies, and thesis advice from Docsity tutors
SITE ADDRESS: Walter Coke - 3500 35th Avenue North, Birmingham, AL 35207 ... performance range delegated to the Contracts Administrator (KA).
Typology: Study notes
1 / 90
This page cannot be seen from the preview
Don't miss anything!
Submitted
(^) to:
Prepared
(^) by:
Birmingham,
(^) Alabama
(^) 30,
(^2011)
BrianPrepared By:
L. Parsley
(^) CSP
Responsible
(^) Health
and Safety Manager^
Date
Project Approved By:
(^) Manager
Date
Client
(^) Acceptance:
Responsible
(^) Authority
Date
CH2M HILL
(^) HSP
Riggins School
Callaway Elementary
Carver High School (Closed)
Hudson School
0 500 1,000 2, Feet
Walter Coke Facility Boundary
Neighborhood Collegeville Harriman Park Fairmont
\HOLLISTER\PROJ\SLOSS\MAPFILES\NEIGHBORHOOD_MAP_COMMUNITY.MXD NEIGHBORHOOD_MAP_COMMUNITY.MXD FLONDON 11/10/2009 11:00:
Emergency
Contacts
Serious Incident Reporting:
Medical
(^) Emergency
Local AmbulanceFacility Medical Response #:
(^) #:
911911
Fire/Spill
(^) Emergency Facility Fire Response #:
911
Local Fire
(^) Dept
(^) #:
911
Security
(^) & Police Facility Security #:
Local Police
(^) #:
205-254-
Utilities
(^) Emergency
Water:
911 (^) or (^) 205-244-
Gas:
911 (^) or (^) 205-326-
Electric:
911 (^) or (^) 866-553-
Emergency
(^) Response
(^) Coordinator
(^) (ERC)
ProjectPhone:Name:
(^) Manager
Name:
Kelly
(^) Moody
Federal ExpressPhone: 334-215-
(^) Dangerous
(^) Goods
(^) Shipping
Phone:
800-238-
CH2M
(^) HILL
(^) Emergency
(^) Number
(^) for (^) Shipping
Dangerous
(^) Goods
Phone:
(^) 800-255-
Injury
(^) .Management/Return-to-Work
(For (^) US (^) and
(^) Puerto
(^) Rico
(^) employees
(^) only)
CH2M
(^) HILL
(^) IMRTW
(^) Medical
(^) Consultant
300 Peter P. Greaney, MDWorkCare (^) S. (^) Harbor
(^) Boulevard, Suite 600
Anaheim,
(^) CA (^92805)
1-714-456-
1-800--455-
Local(After hours calll-866-893-2514 for response by oncall physician)
(^) Occupational
(^) Physician
Carraway
(^) Occupational
(^) Health
3001
(^) 27th (^) St (^) N, (^) Birmingham, AL
Responsible205-502-
(^) Health
(^) and
(^) Safety
(^) Manager
(^) (RHSM)
Name:
Michael
(^) Goldman
Phone:
404-790-
Responsible
(^) Environmental
(^) Manager
(^) (REM)
HumanPhone:Name:
(^) Resources
(^) Representative
Name:
Lisa (^) Covey
/SAC
Phone:
916-286-
Media
(^) Inquiries
(^) Corporate
(^) Strategic
(^) Communications
Name:
(^) John Corsi
Phone:
(^) 720-286-
Worker's
(^) Compensation:
Complete
(^) IRF to initiate process. For
(^) immediate
(^) assistance
contact Regional
(^) HR (^) Dept.
(^) or (^) for (^) an (^) after
(^) hours
(^) emergency
contact Jennifer Rindahl:
(^) 303/918/
Automobile
(^) Accidents:
Rental:
(^) Linda
(^) Anderson/COR
(^) 720-286-
CH2M
(^) HILL
(^) owned
(^) or (^) fleet vehicle: Linda
(^) George/DEN
720-286-
Contact the Project Manager. Generally,
(^) the (^) Project
(^) Manager
(^) will contact relevant
(^) government
(^) agencies.
Facility-Alarms:
(^) N/ (^) A
Evacuation
(^) Assembly
(^) Area(s):
Facility/Site
(^) Evacuation
(^) Route(s):
(^) N/ (^) A
Hospital
(^) Name/Address:
(^) St. (^) Vincent's
(^) Hospital
810 (^) St. (^) Vincent Drive, Birmingham, AL 35205
CH2M HILL
(^) HSP
Hospital
(^) Phone#:
(^) 205-939-
3
Tasks
to
be Performed
(^) under
(^) this
Plan
Description
of Tasks
Refer to project documents (i.e.,
(^) Work
(^) Plan)
(^) for (^) detailed
(^) task information.
(^) health
(^) and safety risk
analysis
(^) (Table
(^) 1) has been performed
for each task and is incorporated in this
(^) plan
(^) through task-
specific hazard
(^) controls
(^) and requirements
(^) for (^) monitoring and protection.
Tasks other than
t~ose
listed
below
(^) require an approved amendment
or revision to this
(^) plan
(^) before tasks
(^) l:)egin.
Refer to Section
for (^) procedures
(^) related
(^) to (^) "clean"
(^) tasks that do not
(^) involve
(^) hazardous waste operations and emergency
1.1.1response (Hazwoper).
Hazwoper-Regulated Tasks
Surface
(^) soil (^) sampling
Excavation
1.1.
Non-Hazwoper-Regulated Tasks
Under specific circumstances, the training and
(^) medical
(^) monitoring requirements
of federal
(^) or state
Hazwoper
(^) regulations
(^) are not
(^) applicable.
It (^) must be demonstrated that the tasks can be performed
without the
(^) possibility
of exposure in order to use non-Hazwoper-trained
(^) personnel.
Prior
(^) approval
from
(^) the
Responsible
(^) Health
(^) and
(^) Safety
(^) Manager
is required
(^) before
(^) these
tasks
are
conducted
(^) on
regulated
(^) hazardous
(^) waste
(^) sites.
CH2M HILL HSP^ N/A
5
1.
Change Management
tt
(^) Change
Manag~ment
Form
'Iihis
jo1im
slfpuld
reviewed
oft a continuous
basis
to
ijthe
site heaUJi
and safef;y
plan
adtq Ult tely, addresses
ongoing
and shoul
d! be complete
d
new tasks
are aontemplated
or^1 (^) changed
conditions
are eneountered.
Project Task:
Surface
(^) Soil
(^) Sampling
and
Project/Task Manager: Kelly
(^) Moody
Excavation
Project
392539
Project Name:
Walter
Coke-
Residential
(^) Soil
Number:
Sampling
and Excavation
' Evaluation
(^) Checklist
Yes
No
Have
(^) the CH2MHILLstaff listed
in the original HASP changed?
Has a
new
subcontractor
(^) been
added
to the project?
Is (^) any (^) chemical
(^) or (^) product
(^) to (^) be used
(^) that
is not listed
in Attachment 2 of
the plan?
Have
(^) additional tasks
(^) been
added
which
(^) were
(^) not (^) originally
(^) addressed
(^) in
Section 1.1 of the plan?
Have
(^) new
(^) contaminants
(^) or (^) higher
(^) than
(^) anticipated levels of original
contaminants been encountered?
Have
(^) other safety, equipment, activity
(^) or (^) environmental
(^) hazards
(^) been
encountered
that
are (^) not (^) addressed
(^) in (^) Section
(^) 2. (^) of the plan?
If the answer is
(^) "YES"
(^) to Questions 1-3, an
(^) HSP
(^) revision is
(^) NOT
(^) needed. Please take the following actions:
Confirm
(^) that
(^) staff's medical
and training status
(^) is (^) current
(^) - check training records at:
http:/
(^) fwww.int.ch2m.com/hands
(^) (or contact
(^) your
(^) regional SPA),
(^) and (^) confirm subcontractor
Confirmqualifications.
(^) with
(^) the project KA
(^) that
(^) subcontractor safety performance has
(^) been
reviewed^
(^) and
(^) is (^) acceptable
Confirm
(^) with
(^) H&S
(^) that
(^) subcontractor safety procedures have
(^) been
(^) reviewed
(^) and (^) are acceptable.
If the answer is
(^) ''YES"
(^) to Questions 4-6, an
(^) HSP
(^) revision
(^) MAY
(^) BE (^) NEEDED.
CH2M HILL
(^) HSP
6
CH2M HILL HSP 8
2.0 Hazard Controls
This section provides safe work practices and control measures used to reduce or eliminate potential hazards. These practices and controls are to be implemented by the party in control of either the site or the particular hazard. CH2M HILL employees and subcontractors must remain aware of the hazards affecting them regardless of who is responsible for controlling the hazards. CH2M HILL employees and subcontractors who do not understand any of these provisions should contact the RHSM for clarification.
The health and safety hazards posed by field activities have been identified for each project activity and are provided in the Hazard Analysis Table (Table 1). Hazard control measures for project-specific and general H&S hazards are provided in 2.1 and 2.2 of this section.
In addition to the controls specified in this section, Project-Activity Self-Assessment Checklists are contained in Attachment 4. These checklists are to be used to assess the adequacy of CH2M HILL and subcontractor site-specific safety requirements. The objective of the self-assessment process is to identify gaps in project safety performance, and prompt for corrective actions in addressing these gaps. Self-assessment checklists should be completed early in the project, when tasks or conditions change, or when otherwise specified by the RHSM. The self-assessment checklists, including documented corrective actions, should be made part of the permanent project records.
Applicable project activity self-assessment checklists (see Attachment 4) shall be completed weekly by a CH2M HILL representative during the course of the project depending on the work performed at the time.
2.1 Project-Specific Hazards
(Reference CH2M HILL, SOP HSE-501, Arsenic ) *project note: arsenic is included because it is governed by stand- alone regulation [29 CFR 1910.1018 Inorganic Arsenic]; PAHs are not. Neither are present at concentrations considered high enough to cause significant exposure.
(Reference CH2M HILL SOP HSE-206, Electrical Safety )
(^) has
(^) selected
(^) Ground
(^) Fault
(^) Circuit
(^) Interrupters
(^) (GFCis)
(^) as the standard method for
protecting
(^) employees
(^) from the
(^) hazards
(^) associated with
(^) electric
(^) shock.
GFCis
(^) shall
(^) be used on
(^) all (^) 120-volt,
(^) single
(^) phase 15 and 20-amphere
(^) receptacle
(^) outlets
(^) which
are not part
(^) of (^) the permanent wiring
(^) of (^) the (^) building
(^) or (^) structure·.
An assured equipment grounding conductor program may be required under the
(^) following
(^) cannot be
(^) utilized
Client
(^) requires such a program to be
(^) implemented
Business group decides to
(^) implement
(^) program in addition to
(^) protection
Extension cords must be equipped with third-wire grounding.
Cords
(^) passing through work areas
must be covered,
(^) elevated
(^) or protected from damage.
Cords
(^) should
not be routed through^
doorways
(^) unless
(^) protected from pinching.
Cords
(^) should
(^) not be fastened with
(^) staples,
(^) hung from
nails,
(^) or (^) suspended with wire.
Electrical
(^) power
(^) tools
(^) and equipment must be
(^) effectively
(^) grounded or
(^) double-insulated
approved.
Operate
(^) and maintain
(^) electric
(^) power
(^) tools
(^) and equipment according to manufacturers' instructions.
Maintain safe
(^) clearance
(^) distances between overhead power
(^) lines
(^) and any
(^) electrical
(^) conducting
material
(^) unless
(^) the power
(^) lines
(^) have been de-energized and grounded,
(^) or (^) where
(^) insulating
(^) barriers
have been
(^) installed
(^) to prevent
(^) physical
(^) contact. Maintain at
(^) least
(^1) (^0) feet from overhead power
(^) lines
for (^) voltages
(^) of (^) 50 kV
(^) or (^) less,
(^) and 1
feet (^) plus
(^) % (^) inch for every 1 kV over 50 kV.
Temporary
(^) lights
(^) shall
(^) not be suspended by their
(^) electric
(^) cord
(^) unless
(^) designed for suspension.
Lights
(^) shall
(^) be protected from
(^) accidental
(^) contact or breakage.
Protect
(^) all (^) electrical
(^) equipment,
(^) tools,
(^) switches, and
(^) outlets
(^) from
(^) environmental
(^) elements.
(Reference
(^) Excavation
(^) & (^) Trenching
(^) Safety)
All (^) underground
(^) installations
(^) (i.e.,
(^) utilities,
(^) fuel
(^) lines)
(^) shall
(^) be (^) located
(^) and protected from damage
prior to opening an excavation.
The excavation, adjacent areas, and protective systems must be inspected
(^) daily,
(^) as needed
throughout the work shifts, and after every rainstorm or other hazard-increasing event.
If a
potentially
(^) hazardous condition is identified, exposed workers
(^) shall
(^) be removed from the hazard and
all (^) work in the area
(^) shall
(^) be stopped
(^) until
(^) necessary precautions have been
(^) implemented.
Excavated
(^) material
(^) shall
(^) be (^) placed
(^) at (^) least
2 feet. (0.6 meter) from the edge of excavation^
(^) or
greater distance as necessary to prevent excessive
(^) loading
(^) (and
(^) potential
(^) collapse)
(^) of (^) the
excavation face(s).
Sloping,
(^) benching, shoring,
(^) shielding,
(^) or (^) other protective systems are required to protect
(^) personnel
from cave-ins except when the excavation is made
(^) entirely
(^) in (^) stable
(^) rock or
(^) is (^) less
(^) than 5 feet deep
and there is no indication
(^) of (^) possible
(^) cave-in, as determined by the excavation competent person.
registeredProtective systems for excavations deeper than 20 feet must be designed or approved by a
(^) professional
(^) engineer.
Trenches greater than 4 feet deep
(^) shall
(^) be provided with a
(^) ladder,
(^) stairway, or ramp positioned so
that the maximum
(^) lateral
(^) travel
(^) distance is no more than 25 feet.
Do not enter the excavations
(^) unless
(^) completely
(^) necessary, and
(^) only
(^) after the excavation competent
person has
(^) completed
(^) their
(^) daily
(^) inspection and has authorized entry.
CH2M HILL
(^) HSP
9
Flammable/combustible
(^) liquids
(^) must be kept in approved containers, and must be stored
(^) in (^) an
approved storage cabinet.
(Reference CH2M
(^) Hand and Power Tools)
Tools
(^) shall
(^) be inspected prior to use and damaged
(^) tools
(^) will (^) be tagged and removed from service.
Hand
(^) tools
(^) will (^) be used
(^) for (^) their intended use and operated
(^) in (^) accordance with manufacturer's
instructions and design
(^) limitations;
Maintain
(^) all (^) hand and power
(^) tools
(^) in (^) a safe condition.
Use PPE (such as
(^) gloves,
(^) safety
(^) glasses,
(^) earplugs,
(^) and face
(^) shields)
(^) when exposed to a hazard
from a
(^) tool.
Do not carry or
(^) lower
(^) a power
(^) tool
(^) by its cord
(^) or (^) hose.
Portable
(^) power
(^) tools
(^) will (^) be (^) plugged
(^) into
(^) GFCI
(^) protected
(^) outlets;
(^) and
Portable
(^) power
(^) tools
(^) will (^) be Underwriters Laboratories (UL)
(^) listed
(^) and have a three-wire grounded
plug
(^) or (^) be (^) double
(^) insulated.
Disconnect
(^) tools
(^) from energy sources when they are not in use, before servicing and
(^) cleaning
(^) them,
and when changing accessories (such as
(^) blades,
(^) bits, and cutters).
Safety
(^) guards
(^) on (^) tools
(^) must remain
(^) installed
(^) while
(^) the (^) tool
(^) is (^) in (^) use and must be
(^) promptly
(^) replaced
after repair or maintenance has been performed.
Store
(^) tools
(^) properly
(^) in (^) a (^) place
(^) where they
(^) will (^) not be damaged or come
(^) in (^) contact with hazardous
materials.
If a cordless
(^) tool
(^) is connected to its recharge unit, both pieces
(^) of (^) equipment must conform
(^) strictly
with (^) electrical
(^) standards and manufacturer's specifications.
Tools
(^) used
(^) in (^) an (^) explosive
(^) environment must be rated for work
(^) in (^) that environment (that is,
intrinsically
(^) safe, spark-proof, etc.).
When using a knife
(^) or (^) blade
(^) tool,
(^) stroke
(^) or (^) cut away from the body with a smooth motion.
Be
careful
(^) not to use excessive force that
(^) could
(^) damage the
(^) tool,
(^) the (^) material
(^) being cut, or unprotected
hands.
Working with
(^) manual
(^) and
(^) pistol-grip
(^) hand
(^) tools
(^) may involve
(^) hig~ly
(^) repetitive movement, extended
elevation,
(^) constrained postures, and/or awkward positioning
(^) of (^) body members (for
(^) example,
(^) hand,
wrist, arm,
(^) shoulder,
(^) neck, etc.).
Consider
(^) alternative
(^) tool
(^) designs, improved posture, the
(^) selection
of (^) appropriate
(^) materials,
(^) changing work organization, and sequencing to prevent
(^) muscular,
(^) skeletal,
repetitive motion, and
(^) cumulative
(^) trauma stressors;
All (^) haul
(^) trucks must
(^) follow
(^) the designated
(^) Haul
(^) Route
(^) established
(^) for the project.
Haul
(^) truck operators
(^) should
(^) ensure
(^) all (^) persons are
(^) clear
(^) before moving their equipment.
Before
moving, operators
(^) should
(^) sound horn or
(^) alarm.
All (^) haul
(^) truck equipment
(^) should
(^) be equipped with an
(^) operational
(^) backing
(^) alarm.
Any equipment with restricted
(^) visibility
(^) should
(^) be equipped with devices that
(^) eliminate
(^) blind
(^) spots.
Haul
(^) truck drivers
(^) should
(^) also
(^) be provided with spotters when there are
(^) blind
(^) spots associated with
loading
(^) or (^) unloading
(^) operations.
Employees
(^) should
(^) stay off
(^) haul
(^) roads.
When approaching a
(^) haul
(^) area,
(^) employees
(^) should
(^) make eye
contact and communicate their intentions
(^) directly
(^) with the equipment operator.
CH2M
(^) lllLL
(^) HSP
11
Haul
(^) roads
(^) should
(^) be (^) well
(^) lit, (^) sufficiently
(^) wide to
(^) allow
(^) for passage
(^) of (^) trucks, and
(^) adequately
(^) marked
with right-of-way signs indicating
(^) haul
(^) directions.
Haul
(^) trucks
(^) shall
(^) be (^) loaded
(^) evenly
(^) for proper weight distribution and on
(^) stable
(^) competent ground.
Do not
(^) walk
(^) in (^) front
(^) of (^) or (^) in back
(^) of (^) haul
(^) trucks.
Haul
(^) truck operators
(^) shall
(^) not be
(^) allowed
(^) to raise the dump bodies
(^) of (^) their
(^) hauling
(^) vehicles
underneath
(^) or (^) within 1
ft (^) of (^) overhead
(^) utilities.
(Reference CH2M
(^) Earth Moving Equipment)
Only
(^) those authorized
(^) personnel
(^) who have been
(^) qualified
(^) by training or previous experience may
operate heavy equipment.
Heavy equipment must be checked at the beginning
(^) of (^) each shift to ensure the equipment is
(^) in (^) safe
operating condition and free
(^) of (^) apparent damage.
The check
(^) should
(^) include:
(^) service brakes,
parking brakes, emergency brakes, tires, horn, back-up
(^) alarm,
(^) steering mechanism,
(^) coupling
devices, seat
(^) belts,
(^) and operating
(^) controls.
All (^) defects
(^) will (^) be corrected before the equipment is
placed
(^) in (^) service.
Heavy equipment must be on
(^) stable
(^) foundation such as
(^) solid
(^) ground
(^) or (^) cribbing; outriggers are to
be (^) fully
(^) extended.
Seat
(^) belts
(^) shall
(^) be used by
(^) all (^) personnel
(^) operating heavy equipment.
Heavy equipment
(^) shall
(^) not be used to
(^) lift (^) personnel.
Loads must not be
(^) lifted
(^) over.the heads
(^) of
ground
(^) personnel.
Equipment must have a reverse
(^) signal
(^) alarm
(^) that is distinguishable from surrounding noise
(^) or (^) must
use a
(^) signal
(^) person when the equipment is operating
(^) in (^) reverse.
The parking brake
(^) will (^) be set whenever equipment is parked;
(^) wheels
(^) must be chocked when parked
in (^) inclines.
When heavy equipment is not
(^) in (^) operating, the
(^) blade/bucket
(^) must be
(^) blocked
(^) or (^) grounded and the
master
(^) clutch
(^) must be disengaged.
When heavy equipment is unattended, power must be shut off, brakes set, blades/buckets
(^) landed,
and shift
(^) lever
(^) in (^) neutral.
(Reference CH2M
(^) Manual Lifting)
Back injuries are the
(^) leading
(^) cause
(^) of (^) disabling
(^) work and most back injuries are the
(^) result
(^) of
improper
(^) lifting
(^) techniques
(^) or (^) overexertion.
(^) Office
(^) or (^) field
(^) tasks and activities
(^) involving
(^) manual
(^) lifting
are to be identified and a program
(^) implemented
(^) to assist
(^) employees
(^) to mitigate the risks associated
with (^) manual
(^) lifting.
When
(^) possible,
(^) the task
(^) should
(^) be modified to minimize
(^) manual
(^) lifting
(^) hazards.
Effectiveness
(^) of (^) manual
(^) handling
(^) control
(^) measures
(^) will (^) be (^) evaluated
(^) during assessments (HSE-114,
Office
(^) & Warehouse
(^) Safety
(^) Program, or
(^) Audits).
Manual
(^) handling
(^) incidents are reviewed as part
(^) of (^) the (^) HSE
(^) Program reviews, and the
(^) results
influence
(^) program
(^) development,
(^) training, and education efforts.
Lifting
(^) of (^) loads
(^) weighing more than
(^) pounds (
(^) kilograms)
(^) should
(^) be (^) evaluated
(^) by the
(^) using
the Lifting
(^) Evaluation
(^) Form contained
(^) in (^) SOP
(^) HSE-112.
CH2M HILL
(^) HSP
12
Whenever
(^) possible,
(^) work from areas with
(^) flat,
(^) stable
(^) surfaces and do not enter steep-sided ditches
or (^) excavations.
Wear
(^) ~turdy
(^) hard-toe boots that provide sufficient
(^) ankle
(^) support.
(^) Stairways
(^) and
(^) Ladders)
Stairway
(^) or (^) ladder
(^) is (^) generally
(^) required when a break in
(^) elevation
(^) of (^) 19 inches
(^) or (^) greater exists.
Personnel
(^) should
(^) avoid using both hands to carry objects
(^) while
(^) on (^) stairways; if
(^) unavoidable,
(^) use
extra precautions.
Personnel
(^) must not use pan and
(^) skeleton
(^) metal
(^) stairs
(^) until
(^) permanent
(^) or (^) temporary treads and
landings
(^) are provided the
(^) full (^) width and depth
(^) of (^) each step and
(^) landing.
Ladders must be inspected by a competent person for
(^) visible
(^) defects prior to each day's use.
Defective
(^) ladders
(^) niust be tagged and removed from service.
Ladders must be used
(^) only
(^) for the purpose for which they were designed and
(^) shall
(^) not be
(^) loaded
beyond their rated capacity.
Only
(^) one person at a time
(^) shall
(^) climb
(^) on (^) or work from an
(^) individual
(^) ladder.
User must face the
(^) ladder
(^) when
(^) climbing;
(^) keep
(^) belt
(^) buckle
(^) between side
(^) rails
Ladders
(^) shall
(^) not be moved, shifted,
(^) or (^) extended
(^) while
(^) in use.
User must use both hands to
(^) climb;
(^) use rope to raise and
(^) lower
(^) equipment and
(^) materials
Straight and extension
(^) ladders
(^) must be tied off to prevent
(^) displacement
Ladders that may be
(^) displaced
(^) by work activities
(^) or (^) traffic must be secured
(^) or (^) barricaded
Portable
(^) ladders
(^) must extend at
(^) least
(^) 3 feet above
(^) landing
(^) surface
Straight and extension
(^) ladders
(^) must be positioned at such an
(^) angle
(^) that the
(^) ladder
(^) base to the
(^) wall
is one-fourth
(^) of (^) the working
(^) length
(^) of (^) the (^) ladder
Stepladders
(^) are to be used
(^) in (^) the·
fully
(^) opened and
(^) locked
(^) position
Users are not to stand on the top two steps
(^) of (^) a (^) stepladder;
(^) nor are users to sit on top or
(^) straddle
(^) a
stepladder
Fixed
(^) ladders
(^) ~ (^) 24 feet in height must be provided with
(^) fall (^) protection devices.
Fall (^) protection
(^) should
(^) be considered when working from extension, straight, or fixed
(^) ladders
(^) greater
than six feet from
(^) lower
(^) levels
(^) and both hands are needed to perform the work, or when reaching
(^) or
working outside
(^) of (^) the (^) plane
(^) of (^) ladder
(^) side
(^) rails.
(Reference CH2M
(^) Traffic Control)
The (^) following
(^) precautions must be taken when working around traffic, and in or near an area where
traffic
(^) controls
(^) have been
(^) established
(^) by a contractor.
Exercise caution when exiting
(^) traveled
(^) way or parking
(^) along
(^) street - avoid sudden stops, use
flashers,
(^) etc.
Park in a manner that
(^) will (^) allow
(^) for safe exit from
(^) vehicle,
(^) and where
(^) practicable,
(^) park
(^) vehicle
(^) so
that it can serve as a barrier.
All (^) staff working adjacent to
(^) traveled
(^) way
(^) or (^) within work area must wear
(^) reflective/high-visibility
safety vests.
CH2M
(^) lllLL
(^) HSP
Eye protection
(^) should
(^) be worn to protect from
(^) flying
(^) debris.
Remain aware
(^) of (^) factors that influence traffic
(^) related
(^) hazards and required
(^) controls-
(^) sun
(^) glare,
rain, wind,
(^) flash
(^) flooding,
(^) limited
(^) sight-distance,
(^) hills,
(^) curves,
(^) guardrails,
(^) width
(^) of (^) shoulder
(^) (i.e.,
breakdown
(^) lane),
(^) etc.
Always
(^) remain aware
(^) of (^) an escape route -- behind an
(^) established
(^) barrier, parked
(^) vehicle,
(^) guardrail,
etc.
Always
(^) pay attention to moving traffic - never assume drivers are
(^) looking
(^) out for you
Work
(^) as far from
(^) traveled
(^) way as
(^) possible
(^) to avoid creating confusion for drivers.
When workers must face away from traffic, a
(^) "buddy
(^) system"
(^) should
(^) be used, where one worker is
looking
(^) towards traffic.
When working on highway projects, obtain a copy
(^) of (^) the contractor's traffic
(^) control
(^) plan.
Work area
(^) should
(^) be protected by a
(^) physical
(^) barrier-
(^) such as a
(^) K-rail
(^) or Jersey barrier.
Review traffic
(^) control
(^) devices to ensure that they are adequate to protect your work area. Traffic
control
(^) devices
(^) should:
(^) 1) convey a
(^) clear
(^) meaning, 2) command respect
(^) of (^) road users, and 3) give
adequate time for proper traffic response. The adequacy
(^) of (^) these devices are dependent
(^) on (^) limited
sight distance, proximity to ramps or intersections, restrictive width, duration
(^) of (^) job, and traffic
volume,
(^) speed, and proximity.
Either a barrier
(^) or (^) shadow
(^) vehicle
(^) should
(^) be positioned a
(^) considerable
(^) distance ahead of the work
area. The
(^) vehicle
(^) should
(^) be equipped with a
(^) flashing
(^) arrow sign arid truck-mounted
(^) crash
(^) cushion
(^) All (^) vehicles
(^) within
(^) feet
(^) of (^) traffic
(^) should
(^) have an orange
(^) flashing
(^) hazard
(^) light
(^) atop the
vehicle.
Except on highways,
(^) flaggers
(^) should
(^) be used when 1) two-way traffic is reduced to using one
common
(^) lane,
(^) 2) driver
(^) visibility
(^) is impaired or
(^) limited,
(^) 3) project
(^) vehicles
(^) enter or exit traffic
(^) in (^) an
unexpected manner,
(^) or (^) 4) the use
(^) of (^) a (^) flagger
(^) enhances
(^) established
(^) traffic warning systems.
Lookouts
(^) should
(^) be used when
(^) physical
(^) barriers are not
(^) available
(^) or (^) practical.
(^) The
(^) lookout
continually
(^) watches approaching
(^) traffic·
(^) for signs
(^) of (^) erratic driver behavior and warns workers.
Vehicles
(^) should
(^) be parked at
(^) least
(^40) (^) feet away from the work zone and traffic. Minimize the
amount
(^) of (^) time that you
(^) will (^) have your back to oncoming traffic.
(^) - Underground
The survey contractor
(^) shall
(^) determine the most appropriate
(^) geophysical
(^) technique
(^) or (^) combinations
of (^) techniques to identify the buried
(^) utilities
(^) on (^) the project, based on the survey contractor's
experience and expertise, types
(^) of (^) utilities
(^) anticipated to be present and specific site conditions.
The survey contractor
(^) shall
(^) employ
(^) the same
(^) geophysical
(^) techniques used on the project to identify
the buried
(^) utilities,
(^) to survey the proposed path of subsurface construction work to confirm no buried
utilities
(^) are present.
Identify
(^) customer specific permit and/or
(^) procedural
(^) requirements for excavation and
(^) drilling
activities.
For (^) military
(^) installations
(^) contact the Base
(^) Civil
(^) Engineer and obtain the appropriate form
to begin the
(^) clearance
(^) process.
Contact
(^) utility
(^) companies
(^) or (^) the (^) state/regional
(^) utility
(^) protection service at
(^) least
(^) two (2) working days
prior to excavation activities to advise
(^) of (^) the proposed work, and ask them to
(^) establish
(^) the (^) location
of (^) the (^) utility
(^) underground
(^) installations
(^) prior to the start
(^) of (^) actual
(^) excavation.
Schedule
(^) the independent survey.
Obtain
(^) utility
(^) clearances
(^) for (^) subsurface work on both
(^) public
(^) and private property.
Clearances
(^) are to be
(^) in (^) writing, signed by the party conducting the
(^) clearance.
CH2M HILL
(^) HSP
15
All (^) inquiries regarding
(^) electric
(^) utilities
(^) must be made
(^) in (^) writing and a written confirmation
(^) of (^) the
outage/isolation must be received by the Project Manager/Construction Manager prior to the start
(^) of
work.
While
(^) work is
(^) in (^) progress outside construction areas
(^) shall
(^) have at
(^) least
(^) lux (^) (lx).
Construction work conducted inside
(^) buildings
(^) should
(^) be provided with at
(^) least
(^55) (^) lux (^) light.
The means
(^) of (^) egress
(^) shall
(^) be (^) illuminated
(^) with emergency and non-emergency
(^) lighting
(^) to provide a
minimum
(^) lx (^) measured at the
(^) floor.
Egress
(^) illumination
(^) shall
(^) be arranged so that the
(^) failure
(^) of
any (^) single
(^) lighting
(^) unit,
(^) including
(^) the burning out
(^) of (^) an (^) electric
(^) bulb
(^) will (^) not (^) leave
(^) any area
(^) in (^) total
darkness.
(Reference
(^) Core
(^) Standard,
(^) Working Alone)
Personnel
(^) can
(^) only
(^) be tasked to work
(^) alone
(^) by the Project Manager who has assessed
(^) potential
hazards and appropriate
(^) control
(^) measures, with assistance from the
(^) Responsible
(^) Health
(^) and
(^) Safety
Manager
"Lone
(^) workers" with an automated person down system or an
(^) accountability
(^) system are permitted,
depending
(^) on (^) the hazards present.
The (^) employee
(^) shall
(^) at (^) all (^) times be equipped with a working voice communication device such as a
cellular
(^) phone or two-way radio to check-in to
(^) th~ir
(^) project contact (s) at pre-determined times.
An Activity Hazard
(^) Analysis
(^) shall
(^) be (^) developed
(^) for the tasks
(^) allowing
(^) work
(^) alone
(^) and
(^) shall
address check
(^) in (^) frequency and contact names and phone numbers.
Check-in
(^) or (^) contact times must be based
(^) on (^) the risk associated with the task, or the timeframe
expected to
(^) complete
(^) the task, but at a minimum of at
(^) least
(^) two times during an 8 hour work shift.
Work tasks
(^) will (^) cease if communication is
(^) lost
(^) during work day.
Work may resume when
communication is
(^) re-established.
See (^) Attachment 8 for Working
(^) Alone
(^) Standard to be used.
2.
General
(^) Hazards
Site (^) work
(^) should
(^) be performed during
(^) daylight
(^) hours whenever
(^) possible.
Good housekeeping must be maintained at
(^) all (^) times
(^) in (^) all (^) project work areas.
Common paths
(^) of (^) travel
(^) should
(^) be (^) established
(^) and kept free from the
(^) accumulation
(^) of (^) materials.-
Keep access to
(^) aisles,
(^) exits,
(^) ladders,
(^) stairways,
(^) scaffolding,
(^) and emergency equipment free from
obstructions.
Provide
(^) slip-resistant
(^) surfaces, ropes, and/or other devices to be used.
Specific areas
(^) should
(^) be designated for the proper storage
(^) of (^) materials.
Tools,
(^) equipment,
(^) materials,
(^) and
(^) supplies
(^) shall
(^) be stored in an
(^) orderly
(^) manner.
As (^) work progresses, scrap and
(^) unessential
(^) materials
(^) must be
(^) neatly
(^) stored or removed from the
work area.
CH2M HILL HSP
17
Containers
(^) should
(^) be provided for
(^) collecting
(^) trash and other debris and
(^) shall
(^) be removed at
(^) regular
intervals.
All (^) spills
(^) shall
(^) be (^) quickly
(^) cleaned
(^) up.
Oil (^) and grease
(^) shall
(^) be (^) cleaned
(^) from
(^) walking
(^) and working
surfaces.
Review the safety requirements
(^) of (^) each job you are assigned to with your
(^) S.!.Jpervisor.
(^) You are not
expected to perform a
(^) job (^) that may
(^) result
(^) in (^) injury or
(^) illness
(^) to (^) yourself
(^) or (^) to others.
Familiarize
(^) yourself
(^) with, understand, and
(^) follow
(^) jobsite emergency procedures.
Do not fight
(^) or (^) horseplay
(^) while
(^) conducting the firm's business.
Do not use
(^) or (^) possess firearms
(^) or (^) other weapons
(^) while
(^) conducting the firm's business.
Report unsafe conditions or unsafe acts to your supervisor
(^) immediately.
Report
(^) occupational
(^) illnesses,
(^) injuries, and
(^) vehicle
(^) accidents.
Do not remove
(^) or (^) make ineffective safeguards
(^) or (^) safety devices attached to any piece
(^) of
equipment.
Report unsafe equipment, defective
(^) or (^) frayed
(^) electrical
(^) cords, and unguarded machinery to your
supervisor.
Shut
(^) down and
(^) lock
(^) out machinery and equipment before
(^) cleaning,
(^) adjustment,
(^) or (^) repair. Do not
lubricate
(^) or repair moving parts
(^) of (^) machinery
(^) while
(^) the parts are in motion.
Do not run in the
(^) workplace.
When ascending
(^) or (^) descending stairways, use the
(^) handrail
(^) and take one step at a time.
Do not
(^) apply
(^) compressed air to any person
(^) or (^) clothing.
Do not wear
(^) steel
(^) taps
(^) or (^) shoes with
(^) metal
(^) exposed to the
(^) sole
(^) at any CH2M
(^) project
(^) location.
Do not wear finger rings,
(^) loose
(^) clothing,
(^) wristwatches, and other
(^) loose
(^) accessories when within
arm's reach of moving machinery.
Remove waste and debris from the
(^) workplace
(^) and dispose of
(^) in (^) accordance with
(^) federal,
(^) state, and
local
(^) regulations.
Note the correct way to
(^) lift (^) heavy objects (secure footing, firm grip, straight back,
(^) lift (^) with
(^) legs),
(^) and
get (^) help
(^) if needed. Use
(^) mechanical
(^) lifting
(^) devices whenever
(^) possible.
Check the work area to determine what
(^) problems
(^) or (^) hazards may exist.
Keep hands away from nose, mouth, and eyes.
Keep areas of broken skin (chapped, burned, etc.) covered.
Wash hands with hot water and soap
(^) frequently
(^) prior to eating and smoking.
The (^) following
(^) situations pertaining to drugs and
(^) alcohol
(^) are prohibited:
Use or possession
(^) of (^) intoxicating beverages
(^) while
(^) performing CH2M
(^) work
Abuse
(^) of (^) prescription
(^) or (^) nonprescription drugs
Regulations.
(^) Use or possession of
(^) illegal
(^) drugs or drugs obtained
(^) illegally
Sale,
(^) purchase, or transfer of
(^) illegal
(^) or (^) illegally
(^) obtained drugs
CH2M HILL
(^) HSP
18