
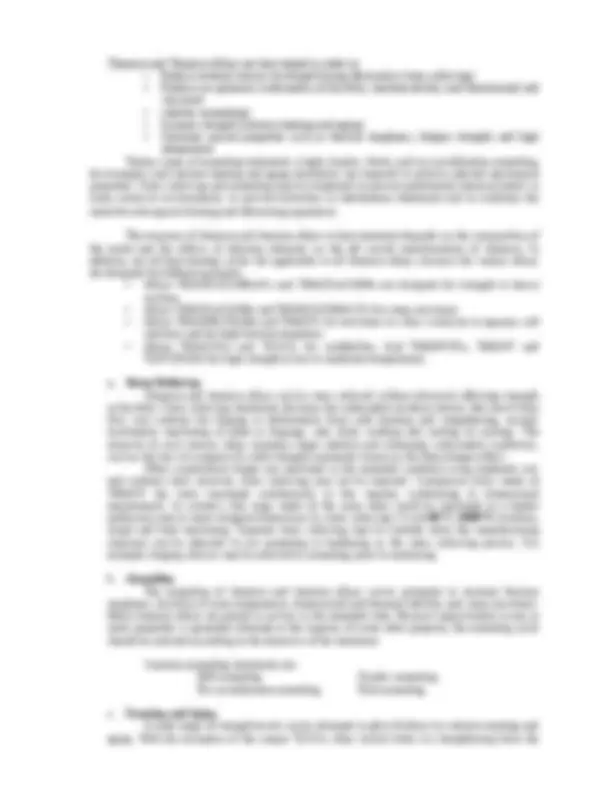
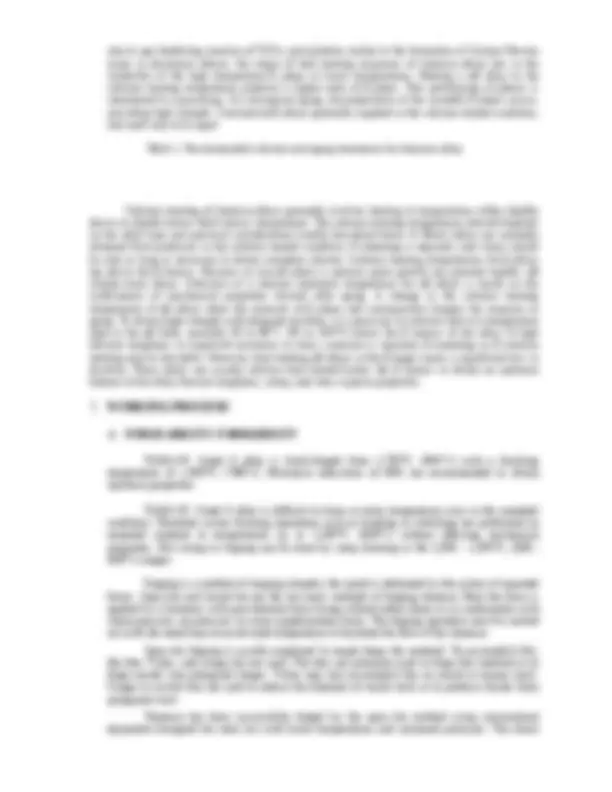
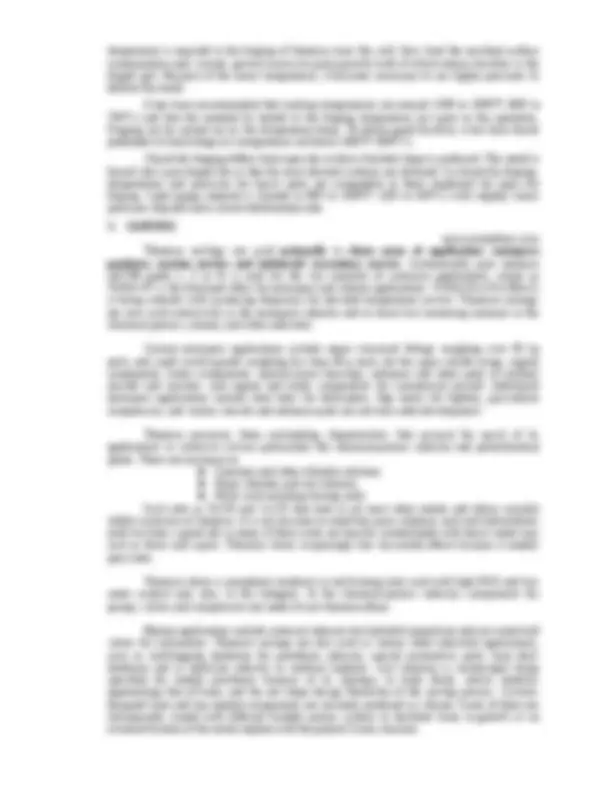
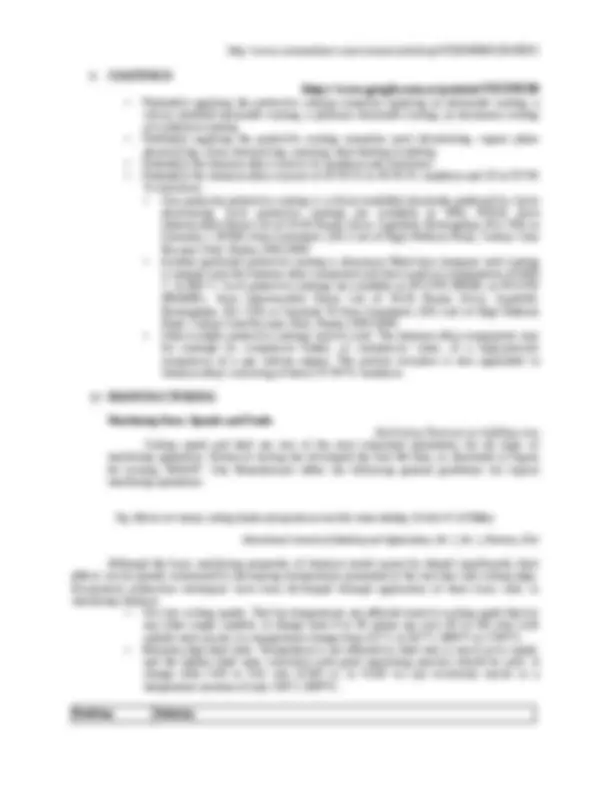
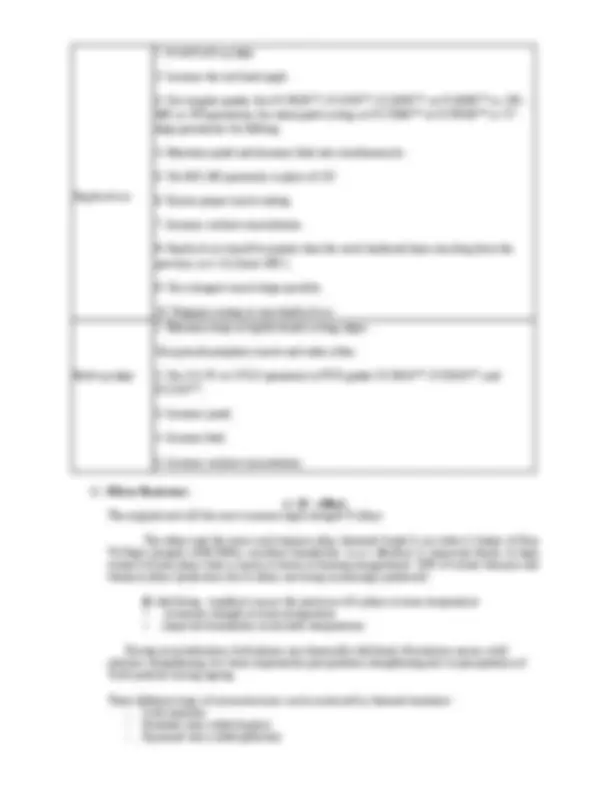
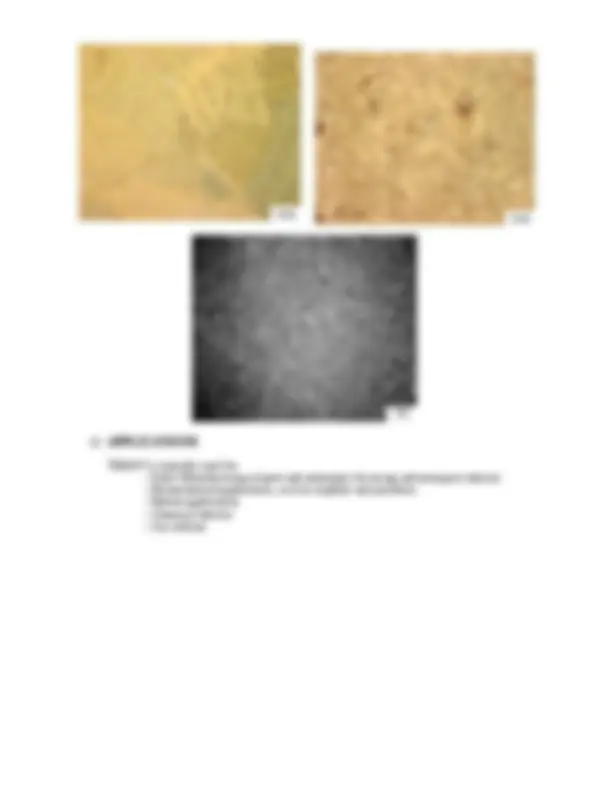
Study with the several resources on Docsity
Earn points by helping other students or get them with a premium plan
Prepare for your exams
Study with the several resources on Docsity
Earn points to download
Earn points by helping other students or get them with a premium plan
Community
Ask the community for help and clear up your study doubts
Discover the best universities in your country according to Docsity users
Free resources
Download our free guides on studying techniques, anxiety management strategies, and thesis advice from Docsity tutors
Titanium Grade %
Typology: Study Guides, Projects, Research
1 / 10
This page cannot be seen from the preview
Don't miss anything!
Ti-6Al-4V, Grade 5 alloy (UNS R56400) is the most widely used titanium grade. It is a two phase α+β titanium alloy, with aluminum as the alpha stabilizer and vanadium as the beta stabilizer. This high- strength alloy can be used at cryogenic temperatures to about 800°F (427°C). ATI Ti-6Al-4V, Grade 5 alloy is used in the annealed condition and in the solution treated and aged condition. Some applications include: compressor blades, discs, and rings for jet engines; airframe and space capsule components; pressure vessels; rocket engine cases; helicopter rotor hubs; fasteners; critical forgings requiring high strength-to-weight ratios. This alloy is produced by primary melting using vacuum arc (VAR), electron beam (EB), or plasma arc hearth melting (PAM). Re-melting is achieved by one or two vacuum arc steps.
http://www.titaniummet.com/product/show_product.php?id= Shape: Round, Square, Hex, Sheet/Plate Material: Titanium Gr1, Gr2, Gr3, Gr4, Gr5 ( ELI), Gr7, Gr9, etc. Specification: Bar : Dia: 6.0 - 350mm Length: ≤6000mm Rod : Dia: 0.8 - 40mm Length: ≤6000mm Standards: ASTM B348, ASTM F67, ASTM F136, AMS Application: Chemical industry, petroleum chemical industry, medical etc Sheet : Thickness: 0.5 - 4.0mm Width ≤ 1250mm Length ≤ 3000mm Plate : Thickness: 4.0 -100mm Width ≤ 2600mm Length ≤ 1000mm Application: Aerospace, spaceflight, chemical industry, marine engineering. Standards: ASTM B265, ASTM F67/ F136, AMS 4911
Quality and Test: Strict test is indispensible, because we must ensure our clients get the best product. The Third Party Inspection --- EN 10204 3.1 is available. Quality Certification: ISO9001-2008)
http://www.tmstitanium.com Shape: Round, Square, Hex, Sheet/Plate Material: Titanium Gr1, Gr2, Gr3, Gr4, Gr5 (ELI), Gr7, Gr9, etc. Specification: Rod : Dia: 0.25 - 355mm Length: ≤6000mm Standards: 6-4, 6-4 Eli, 6-2-4-2, 6-2-4-6, CP Grades 1,2,3, Application: Chemical industry, petroleum chemical industry, medical etc Sheet: Thickness: 0.4 - 4.8mm Width ≤ 1250mm Length ≤ 3000mm Plate: Thickness: 6.4 -100mm Width ≤ 2600mm Length ≤ 1000mm Application: Racing, Medical, Aerospace, Commercial Standards: 6AL-4V, 6AL-4V Eli, CP Grades 1, 2, 3, 4
http://www.king-titanium.com Grades: CP, Gr.5 (Ti-6Al-4V), Gr.6 (Ti-5Al-2.5Sn), Gr.7 (Ti-0.2Pb), Gr.9 (Ti-3Al-2.5V ), Specifications: ASTM B348, ASME SB348, ASTM F67, AMS 4928, MIL-T- Bar Sizes: Dia. 4mm ~ 350mm Sheet Sizes: Thickness: 0.8 ~ 60mm
classic age hardening reaction of Ti2Cu precipitation similar to the formation of Guinier Preston zones in aluminum alloys), the origin of heat treating responses of titanium alloys lies in the instability of the high temperature β phase at lower temperatures. Heating a αβ alloy to the solution treating temperature produces a higher ratio of β phase. This partitioning of phases is maintained by quenching; On subsequent aging, decomposition of the unstable β phase occurs, providing high strength. Commercial β alloys generally supplied in the solution treated condition, and need only to be aged.
Table 1. Recommended solution and aging treatments for titanium alloy
Solution treating of titanium alloys generally involves heating to temperatures either slightly above or slightly below the β transus temperature. The solution treating temperature selected depends on the alloy type and practical considerations briefly described below. β (Beta) alloys are normally obtained from producers in the solution treated condition. If reheating is required, soak times should be only as long as necessary to obtain complete solution. Solution treating temperatures for β alloys are above the β transus; Because no second phase is present, grain growth can proceed rapidly. αβ (Alpha beta) alloys. Selection of a solution treatment temperature for αβ alloys is based on the combination of mechanical properties desired after aging. A change in the solution treating temperature of αβ alloys alters the amounts of β phase and consequently changes the response to aging. To obtain high strength with adequate ductility, it is necessary to solution treat at a temperature high in the αβ field, normally 25 to 85°C (50 to 150°F) below the β transus of the alloy. If high fracture toughness or improved resistance to stress corrosion is required, β annealing or β solution treating may be desirable. However, heat treating αβ alloys in the β range causes a significant loss in ductility. These alloys are usually solution heat treated below the β transus to obtain an optimum balance of ductility, fracture toughness, creep, and stress rupture properties.
Ti-6Al-4V, Grade 5 alloy is finish-forged from 1,750°F; (954°C) with a finishing temperature of 1,450°F; (788°C). Minimum reductions of 35% are recommended to obtain optimum properties.
Ti-6Al-4V, Grade 5 alloy is difficult to form at room temperature even in the annealed condition. Therefore severe forming operations such as bending or stretching are performed on annealed material at temperatures up to 1,200°F; (649°C) without affecting mechanical properties. Hot sizing or shaping can be done by creep forming in the 1,000 - 1,200°F; (538 - 649°C) ranges.
Forging is a method of shaping whereby the metal is deformed by the action of repeated blows. Open die and closed die are the two basic methods of forging titanium. Here the force is applied by a hammer, with gravitational force being utilized either alone or in combination with steam pressure, air pressure, or some supplementary force. The forging operation must be carried out with the metal kept at an elevated temperature to facilitate the flow of the titanium. Open die forging is usually employed to rough-shape the material. To accomplish this, flat dies V-dies, and swage die are used. Flat dies are primarily used to forge flat material or to forge rounds into polygonal shapes. V-dies may also accomplish this on round or square stock. Swage or curved dies are used to reduce the diameter of round stock or to produce rounds from polygonal stock. Titanium has been successfully forged by the open die method using conventional equipment designed for steel, but with lower temperatures and increased pressures. The lower
temperature is required in the forging of titanium since this will, first, limit the resultant surface contamination and, second, prevent excessive grain growth, both of which reduce ductility in the forged part. Because of the lower temperature, it becomes necessary to use higher pressures to deform the metal.
It has been recommended that soaking temperatures are around 1200 to 1300°F (650 to 700°C) and that the material be heated to the forging temperature just prior to the operation. Forging can be carried out as the temperature drops. To obtain good ductility, it has been found preferable to finish-forge at a temperature not below 1550°F (840°C).
Closed die forging differs from open die in that a finished shape is produced. The metal is forced into a pre-shaped die so that the exact desired contours are obtained. In closed die forging, temperatures and pressures for heavy parts are comparable to those employed for open die forging. Light gauge material is formed at 800 to 1000°F (425 to 540°C) with slightly lower pressures required and a slower deformation rate.
www.acmealloys.com Titanium castings are used primarily in three areas of application: aerospace products, marine service and industrial (corrosion) service. Commercially pure titanium (ASTM grade 1, 2 or 3) is used for the vast majority of corrosion applications, where as Ti-6Al-4V is the dominant alloy for aerospace and marine applications. Ti-6Al-2Sn-4Zr-2Mo-Si is being selected with increasing frequency for elevated temperature service. Titanium castings are now used extensively in the aerospace industry and to lesser but increasing measure in the chemical-process, marine, and other industries.
Current aerospace applications include major structural fittings weighing over 45 kg each, and small switch guards weighing less than 30 g each, for the space shuttle wings, engine components, brake components, optical-sensor housings, ordnance and other parts of military aircraft and missiles; and engine and brake components for commercial aircraft. Additional aerospace applications include rotor hubs for helicopters, flap tracks for fighters, gas-turbine compressors, and various missile and ordnance parts are actively under development.
Titanium possesses three outstanding characteristics that account for much of its applications in corrosive service particularly the chemical-process industry and petrochemical plants. These are resistance to ■ Seawater and other chloride solutions ■ Hypo chlorites and wet chlorine ■ Nitric acid including fuming acids Such salts as FeCl3 and CuCl2 that tend to pit most other metals and alloys actually inhibit corrosion of titanium. It is not resistant to relatively pure sulphuric acid and hydrochloric acids but does a good job in many of these acids are heavily contaminated with heavy metal ions such as ferric and cupric. Titanium shows surprisingly low two-metal effects because it readily passivates.
Titanium shows a pyrophoric tendency in red fuming nitric acid with high NO2 and low water content and, also, in dry halogens. In the chemical-process industry, components for pumps, valves and compressors are made of cast titanium alloys.
Marine applications include water-jet inducers for hydrofoil propulsion and sea water ball valves for submarines. Titanium castings are also used in various other industrial applications, such as well-logging hardware for petroleum industry, special automotive parts, boat deck hardware and in medicine industry as medical implants. Cast titanium is increasingly being specified for medial prostheses because of its inertness to body fluids, elastic modulus approaching that of bone, and the net shape design flexibility of the casting process. Custom- designed knee and hip implant components are routinely produced in volume. Some of them are subsequently coated with diffused bonded porous surface to facilitate bone in-growth or an eventual fixation of the metal implant with the patient’s bone structure.
a source of weld contamination. Before starting an arc in welding titanium, it is good practice to pre- purge the torch, trailing shield and backup shield to be sure all air is removed. Whenever possible, high frequency arc starting should be used. Scratch starting with tungsten electrodes is a source of tungsten inclusions in titanium welds. On extinguishing the arc, the use of current down slope and a contractor, controlled by a single foot pedal, is encouraged. Torch shielding should be continued until the weld metal cools below 800°F (427°C). Secondary and backup shielding should also be continued. A straw or blue colour on the weld is indicative of premature removal of shielding gas. Preheating is not generally needed for titanium shop welds. However, if the presence of moisture is suspected, due to low temperature, high humidity, or wet work area, preheating may be necessary. Gas torch heating (slightly oxidizing flame) of weld surfaces to about 150°F (66°) is generally sufficient to remove moisture. The arc length for welding titanium without filler metal should be about equal to the electrode diameter. If filler metal is added, maximum arc length should be about 1-1/2 times the electrode diameter. Filler wire should be fed into the weld zone at the junction of the weld joint and arc cone. Wire should be fed smoothly and continuously into the puddle. An intermittent dipping technique causes turbulence and may result in contamination of the hot end of the wire on removal from the shield. The contaminants are then transferred to the weld puddle on the next dip. Whenever the weld wire is removed from the inert gas shielding, the end should be clipped back about 1/2-inch to remove contaminated metal. Inter pass temperatures should be kept low enough, such that additional shielding is not required. Cleaning between passes is not necessary if the weld bead remains bright and silvery. Straw or light blue weld discoloration can be removed by wire brushing with a clean stainless steel wire brush. Contaminated weld beads, as evidenced by a dark blue, grey or white powdery colour, must be completely removed by grinding. The joint must then be carefully prepared and cleaned before welding again. Irregularities in weld colour and corresponding treatments
Weld Colour Probable Cause and Treatment
Light Straw, Dark Straw, Light Blue Surface oxide. Remove by wire brushing with new stainless steel wire brush. Dark Blue, Grey Blue, Grey Metal contamination. Welds should be removed and done over after corrections in shielding are made. White (loose deposit) Metal contamination. Welds should be removed and done over after corrections in shielding are made
d. Brazing Titanium Several brazing techniques are applicable to titanium. These include induction brazing, resistance brazing and furnace brazing in an argon atmosphere or in vacuum. Torch brazing is not applicable to titanium. Since brazing techniques have the potential for contaminating titanium surfaces, cleanliness is important and consideration should be given to argon or helium gas shielding. Alloys for brazing titanium to itself or other metals are titanium-base (70Ti-15Cu-15Ni), silver-base (various), or aluminium-base (various). The titanium base alloy requires temperatures in the vicinity of 1700°F (927°C), whereas the silver and aluminium-base alloys require 1650°F (899°C) and 1100°-1250°F (593°-677°C) respectively. If corrosion resistance is important, tests should be run on brazed joints in the intended environment prior to use. The titanium-base alloy reportedly offers superior resistance to atmospheric corrosion and saline environments.
http://www.sciencedirect.com/science/article/pii/S025405841201053X
Machining Data: Speeds and Feeds Machining Titanium on JobShop.com Cutting speed and feed are two of the most important parameters for all types of machining operations. Extensive testing has developed the tool life data, as illustrated in Figure for turning Ti6Al4V. One Manufacturer offers the following general guidelines for typical machining operations.
Fig: Effects of various cutting fluids and speeds on tool life when drilling Ti-6Al-4V (375Bhn)
International Journal of Modeling and Optimization, Vol. 2, No. 1, February 2012
Although the basic machining properties of titanium metal cannot be altered significantly, their effects can be greatly minimized by decreasing temperatures generated at the tool face and cutting edge. Economical production techniques have been developed through application of these basic rules in machining titanium:
Problem Solution
Ti6Al4V is typically used for: