
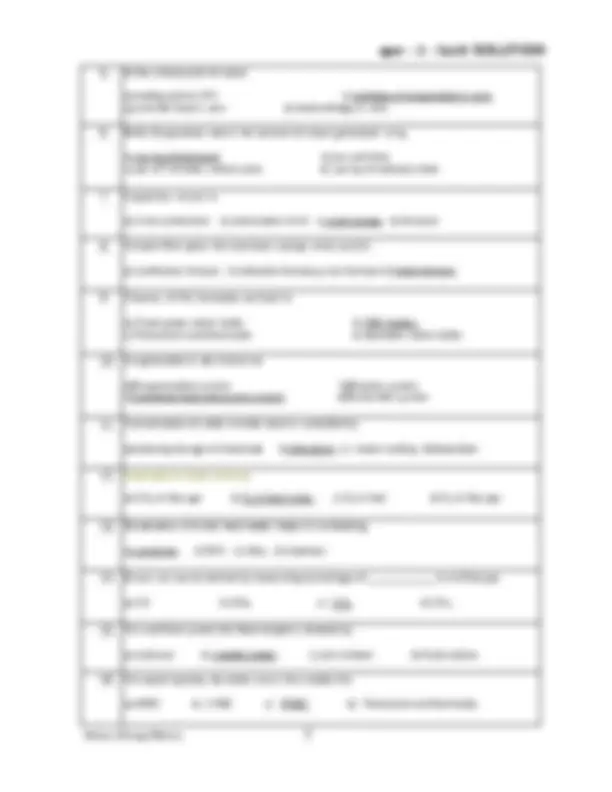
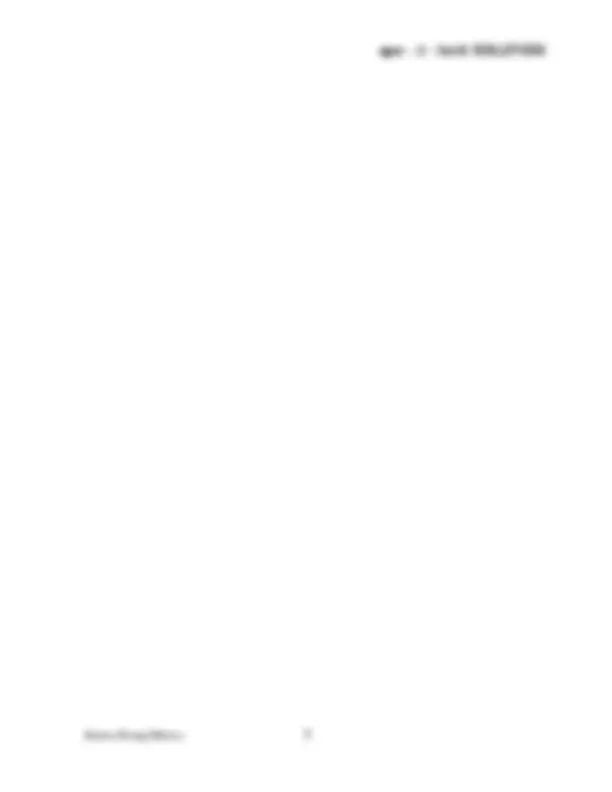
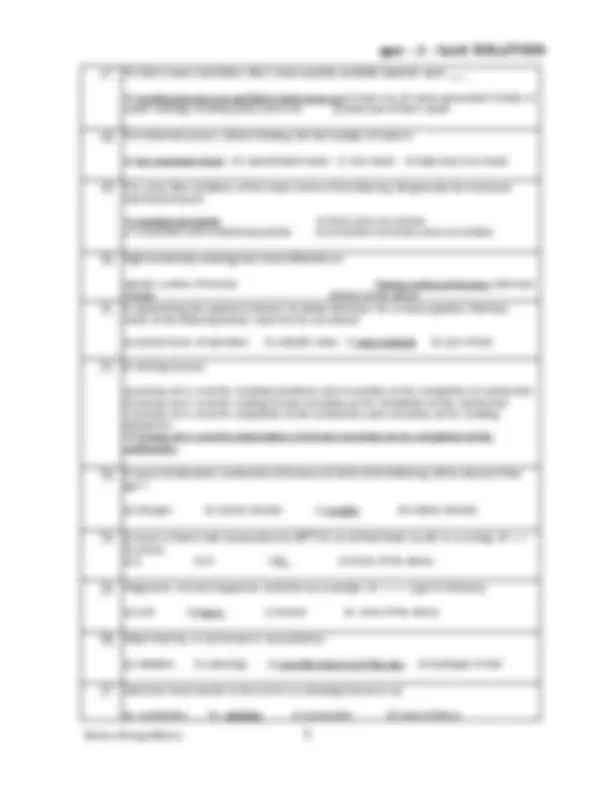
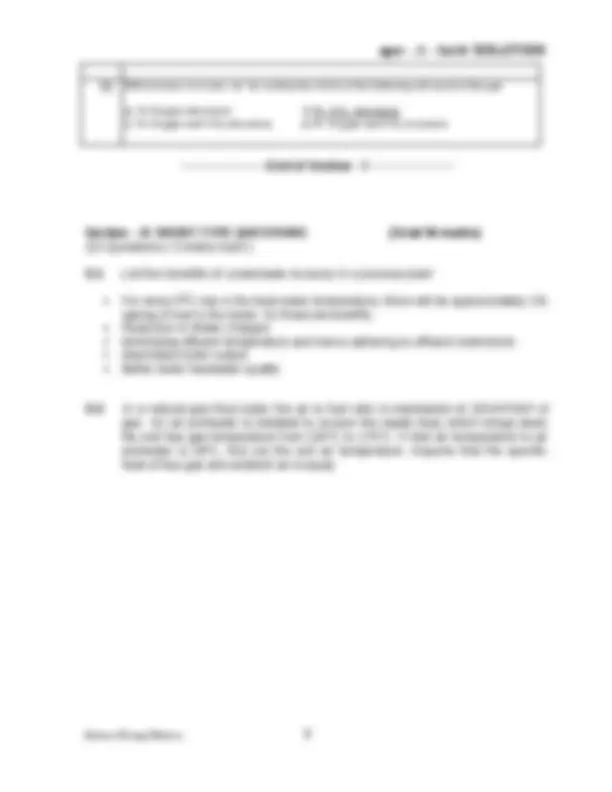
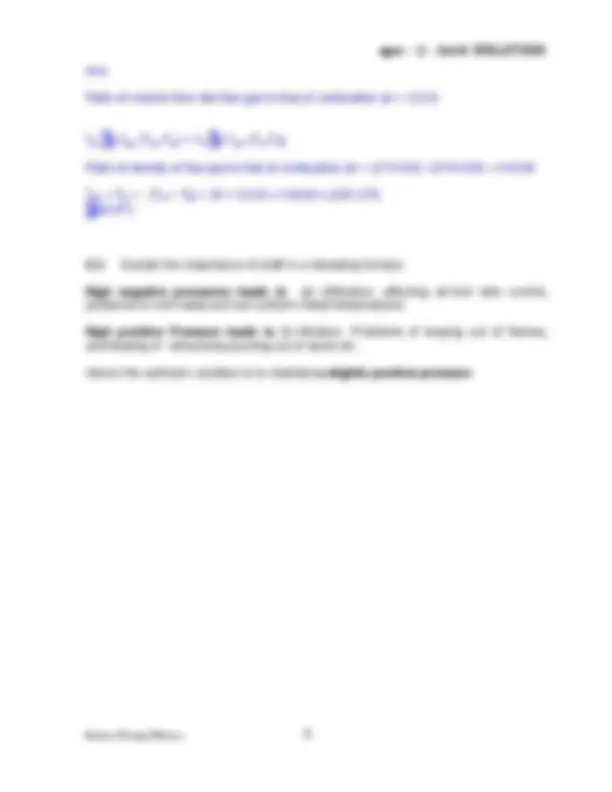
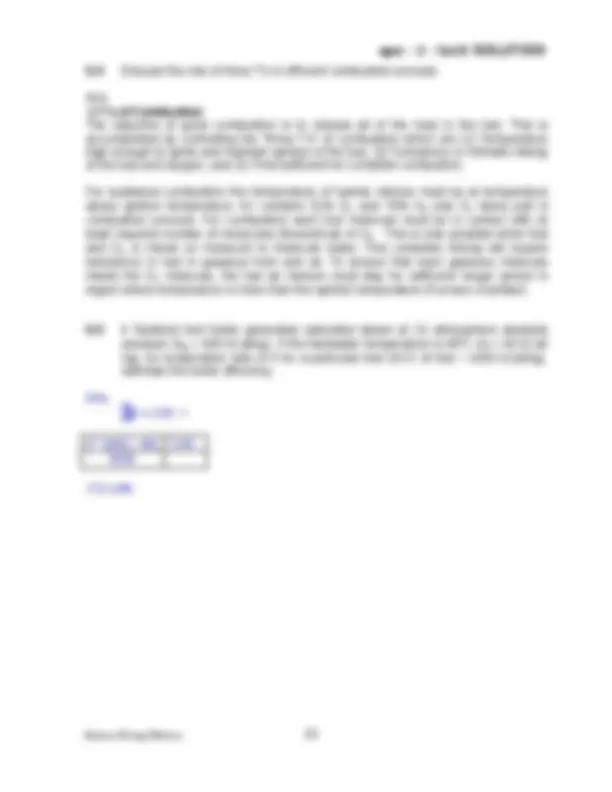
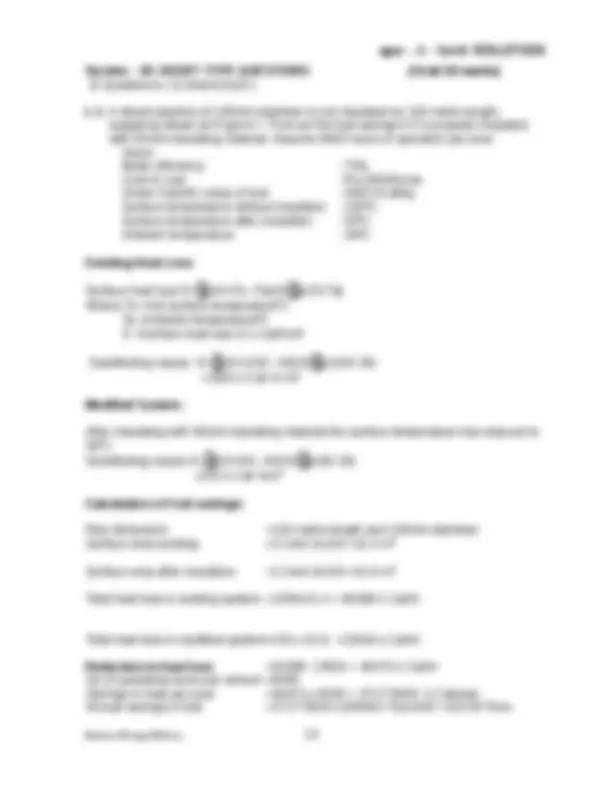
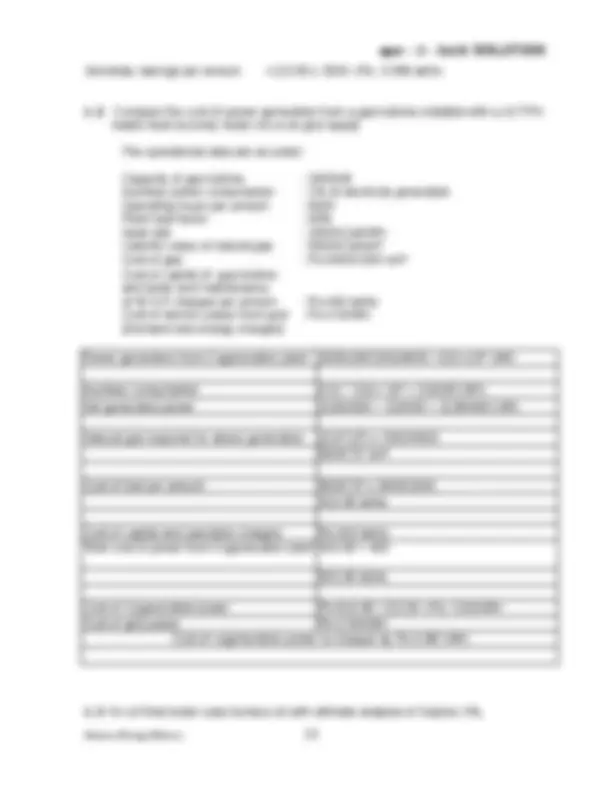
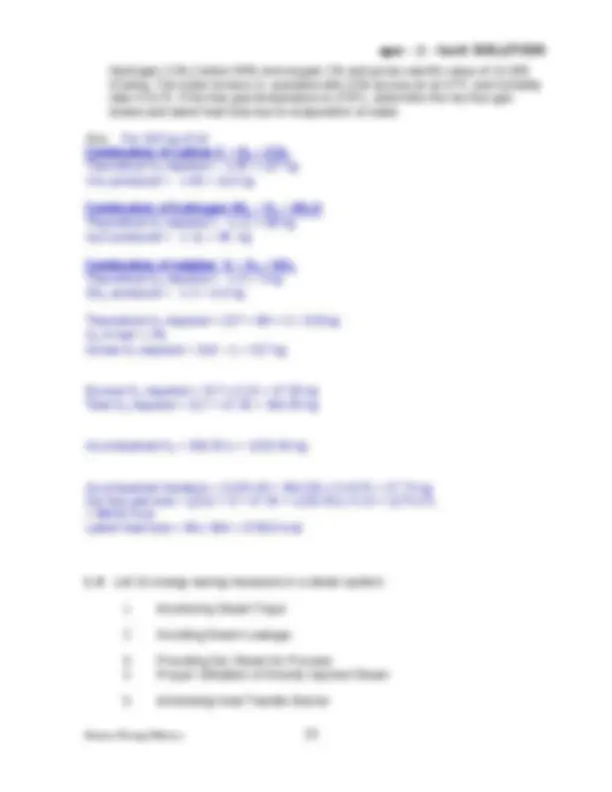
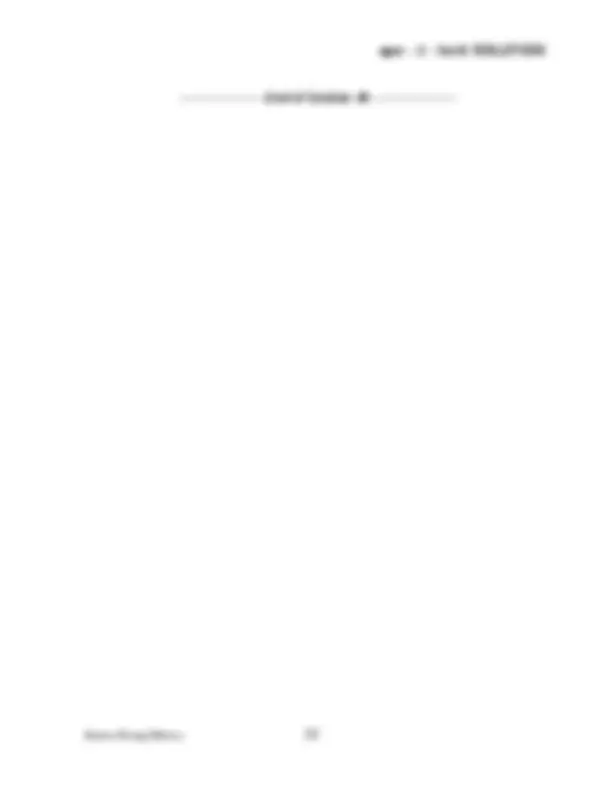
Study with the several resources on Docsity
Earn points by helping other students or get them with a premium plan
Prepare for your exams
Study with the several resources on Docsity
Earn points to download
Earn points by helping other students or get them with a premium plan
Community
Ask the community for help and clear up your study doubts
Discover the best universities in your country according to Docsity users
Free resources
Download our free guides on studying techniques, anxiety management strategies, and thesis advice from Docsity tutors
Furnace - Furnace
Typology: Exams
1 / 18
This page cannot be seen from the preview
Don't miss anything!
Regn No: _________________
Name: ___________________
(To be written by the candidates)
NATIONAL CERTIFICATION EXAMINATION 2007 FOR ENERGY MANAGERS & ENERGY AUDITORS
PAPER – 2: ENERGY EFFICIENCY IN THERMAL UTILITIES
Date: 21.04.2007 Timings: 1400-1700 HRS Duration: 3 HRS Max. Marks: 150
General instructions:
Section – I: OBJECTIVE TYPE Marks: 50 x 1 = 50 (i) Answer all 50 questions (ii) Each question carries one mark (iii) Please hatch the appropriate oval in the OMR answer sheet with HB Pencil, as per instructions
a) air to fuel b) maximum fuel input to actual fuel input c) maximum fuel input over minimum fuel input d) maximum air input over minimum air input
a) float trap b) thermodynamic c) thermostatic d) inverted bucket
a) It reduces partial pressure of steam and decreases thermal resistance to heat transfer b) It increase partial pressure of steam and decrease thermal resistance to heat transfer c) It increases saturation temperature of steam and increases thermal resistance to heat transfer d) It reduce saturation temperature of steam and increase thermal resistance to heat transfer
a) Back pressure steam turbine b) Gas turbine c) Condensing turbine d) none of the above
a) condensate pressure and flash steam pressure b) pressure of steam generated in boiler c) steam enthalpy at atmospheric pressure d) total heat of flash steam
a) dry saturated steam b) superheated steam c) wet steam d) high pressure steam
a)outer surface of furnace b)inner surface of furnace c)furnace charge d)none of the above
a) primary air is used for creating turbulence and secondary air for completion of combustion b) primary air is used for cooling oil and secondary air for completion of the combustion c) primary air is used for completion of the combustion and secondary air for creating turbulence d) Primary air is used for atomizations of oil and secondary air for completion of the combustion.
a) nitrogen b) carbon dioxide c) oxygen d) sulphur dioxide
a) acid b) basic c) neutral d) none of the above
a) radiation. b) openings. c) sensible heat in exit flue gas d) hydrogen in fuel
a) conduction b) radiation c) convection d) none of these
c) be independent of loading d) none of the above
a) number of bends b) length of pipe c) specific volume of steam d) none of the above
a) increasing the calorific value of the coal b) keeping boiler grate cooled c) increasing the furnace draft velocity d)stopping coal fines to fall through grate and being carried away with furnace draft
a) high pressure steam with super heat b) dry saturated low pressure steam c) dry saturated steam with high pressure d) wet steam with very high pressure
a) 79% b) 100% c) 21% d) 0%
a)blow down quantity b)calorific value of fuel c)excess air level d)flue gas temperature
a) pulverised coal b) bagasse c)fuel oil d) natural gas.
a) low thermal conductivity b) light weight c) high heat storage d) thermal shock resistant
a) complete combustion with minimum excess air b) waste heat recovery from the flue gases c) optimum capacity utilization d) heat recovery from furnace openings
a) highest specific heat and latent heat b) low heat transfer coefficient c) easy to control and distribute d) cheap and inert
a) fluidized bed boiler b) spreader stoker boiler c) pulverized coal fired boiler d) manually fired boiler
a) naphtha b) LPG c) LSHS d) natural gas
a) % Oxygen decreases b) % CO 2 decreases c) % Oxygen and CO 2 decreases d) % Oxygen and CO 2 increases
----------------------End of Section - I----------------------
Section – II: SHORT TYPE QUESTIONS (Total 50 marks) (10 Questions x 5 Marks Each )
S-1 List five benefits of condensate recovery in a process plant
S-2 In a natural gas fired boiler the air to fuel ratio is maintained at 10Nm 3 /Nm 3 of gas. An air preheater is installed to recover the waste heat, which brings down the exit flue gas temperature from 220 oC to 170^ oC. If inlet air temperature to air preheater is 30ºC, find out the exit air temperature. Assume that the specific heat of flue gas and ambient air is equal.
S.4 Discuss the role of three T’s in efficient combustion process
Ans 3 T’s of Combustion The objective of good combustion is to release all of the heat in the fuel. This is accomplished by controlling the "three T's" of combustion which are (1) Temperature high enough to ignite and maintain ignition of the fuel, (2) Turbulence or intimate mixing of the fuel and oxygen, and (3) Time sufficient for complete combustion.
For sustained combustion the temperature of fuel/air mixture must be at temperature above ignition temperature. Air contains 21% O 2 and 79% N 2 only O 2 takes part in combustion process. For combustion each fuel molecule must be in contact with at least required number of molecules (theoretical) of O 2.^ This is only possible when fuel and O 2 is mixed on molecule to molecule basis. This complete mixing will require turbulence in fuel in gaseous from and air. To ensure that each gaseous molecule meets the O 2 molecule, the fuel air mixture must stay for sufficient longer period in region where temperature is more than the ignition temperature (Furnace chamber).
S-5 A fluidized bed boiler generates saturated steam at 15 atmosphere absolute pressure (hg = 666 kCal/kg). If the feedwater temperature is 60ºC (hf = 60 kCal/ kg), for evaporation ratio of 5 for a particular fuel (GCV of fuel = 4200 kCal/kg), estimate the boiler efficiency.
Ans. F 0 6 8 = x 100 =
5 * (666 – 60) * 100 4200
=72.14%
S-6 Draw a schematic diagram of a combined cycle power plant
S-7 A boiler is generating steam at 5500 kg/hr. The maximum permissible limit of TDS in the boiler is 3000 ppm. If the make up water is 40% at a TDS level of 200 ppm, calculate the blowdown percentage and blow down rate.
200 * 40 = 2.67% 3000 Ans. Blow down percentage =
Blow down rate = 5500 x .0267 = 146.85 kg/hr.
S-8 Explain the working of a float trap with a sketch.
or
Float traps operate in a very similar way to a ball cock. A float contained within the trap body is raised or lowered by the volume of condensate delivered to the trap. As increasing levels of condensate raise the ball float, the mechanism lifts a valve allowing condensate to discharge thus lowering the level of condensate within the trap. The trap eventually closes preventing the further passage of steam.
The trap will remain closed and partially flooded unless there is a sufficient level of condensate within the trap. At start up any air ahead of the steam and condensate will not therefore be vented. Consequently it is necessary to incorporate an air cock or a balanced pressure device (as described above) to release air in the trap.
S-9 For a oil containing 9% hydrogen (GCV = 10,200 kCal/kg), estimate the percentage of sensible and latent heat loss due to evaporation of water formed due to hydrogen in the fuel, if the flue gas temperature is 180ºC and combustion air temperature is 40ºC. (latent heat of vapours = 584 kCal/kg, specific heat of vapours = 0.45 kCal/kg/ 0 C)
Section – III: SHORT TYPE QUESTIONS (Total 50 marks) (5 Questions x 10 Marks Each )
L-1 A steam pipeline of 100mm diameter is not insulated for 100 metre length, supplying steam at 8 kg/cm 2. Find out the fuel savings if it is properly insulated with 50mm insulating material. Assume 8000 hours of operation per year. Given: Boiler efficiency : 75% Cost of coal : Rs.2500/tonne. Gross Calorific value of fuel : 4000 kCal/kg Surface temperature without insulation : 150 0 C Surface temperature after insulation : 50 0 C Ambient temperature : 30 0 C
Existing Heat Loss :
Surface heat loss S= F 05 B 10+(Ts –Ta)/20 F 05 D x(Ts-Ta) Where Ts =Hot surface temperature 0 C Ta =Ambient temperature 0 C S =Surface heat loss in k.Cal/hrm^2
Substituting values S= F 05 B 10+(150 –30)/20 F 05 D x(150-30) =1920 k.Cal/ hr-m^2
Modified System :
After insulating with 50mm insulating material the surface temperature has reduced to 500 C Substituting values S= F 05 B 10+(50 –30)/20 F 05 D x(50-30) =220 k.Cal/ hrm 2
Calculation of Fuel savings:
Pipe dimension =100 metre length and 100mm diameter Surface area existing =3.14x0.1x100 =31.4 m 2
Surface area after insulation =3.14x0.2x100 =62.8 m 2
Total heat loss in existing system =1920x31.4 = 60288 k.Cal/hr
Total heat loss in modified system=220 x 62.8 =13816 k.Cal/hr
Reduction in heat loss =60288 -13816 = 46472 k.Cal/hr No of operating hours per annum = Savings in heat per year =46472 x 8000 = 371776000 k.Cal/year Annual savings in fuel =371776000 /(4000x0.75)x1000 =123.93 Tons
Monetary savings per annum =123.93 x 2500 =Rs. 3.098 lakhs
L-2 Compare the cost of power generation from a gas turbine installed with a 10 TPH waste heat recovery boiler vis-a-vis grid supply
The operational data are as under:
Capacity of gas turbine : 3000kW Auxiliary power consumption : 1% of electricity generated Operating hours per annum : 8000 Plant load factor : 90% Heat rate : 3050kCal/kWh Calorific value of natural gas : 9500kCal/sm 3 Cost of gas : Rs.6000/1000 sm 3 Cost of capital of gas turbine and boiler and maintenance of W.H.R charges per annum : Rs.400 lakhs Cost of electric power from grid : Rs.4.5/kWh (Demand and energy charges)
Power generation from Cogeneration plant 3000x(90/100)x8000 =216 x10 5 kWh
Auxiliary consumption 0.01 * 216 x 10 5 = 216000 kWh
Net generated power 21600000 – 216000 = 21384000 kWh
Natural gas required for above generation (216*10 5 ) x 3050/ 6934737 sm 3
Cost of fuel per annum 6934737 x 6000/ 416.08 lakhs
Cost of capital and operation charges Rs 400 lakhs Total cost of power from Cogeneration plant 416.08 + 400
816.08 lakhs
Cost of Cogenerated power Rs 816.08 / 213.84 =Rs. 3.82/kWh Cost of grid power Rs 4.50/kWh Cost of cogeneration power is cheaper by Rs 0.68/ kWh
L-3 An oil fired boiler uses furnace oil with ultimate analysis of Sulphur 3%,
L-5 Explain briefly the principles of operation of a) Heat pipe b) Radiation Recuperator c) Plate Heat Exchanger
)a Heat pipe
The Heat Pipe comprises of three elements – a sealed container, a capillary wick structure and a working fluid. The capillary wick structure is integrally fabricated into the interior surface of the container tube and sealed under vacuum. Thermal energy applied to the external surface of the heat pipe is in equilibrium with its own vapour as the container tube is sealed under vacuum. Thermal energy applied to the external surface of the heat pipe causes the working fluid near the surface to evaporate instantaneously. Vapour thus formed absorbs the latent heat of vapourisation and this part of the heat pipe becomes an evaporator region. The vapour then travels to the other end the pipe where the thermal energy is removed causing the vapour to condense into liquid again, thereby giving up the latent heat of the condensation. This part of the heat pipe works as the condenser region. The condensed liquid then flows back to the evaporated region.
b) Radiation Repuperator
A metallic radiation recuperator consists of two concentric lengths of metal tubing. The inner tube carries the hot exhaust gases while the external annulus carries the combustion air from the atmosphere to the air inlets of the furnace burners. The hot gases are cooled by the incoming combustion air which now carries additional energy into the combustion chamber. Radiation recuperator gets its name from the fact that a substantial portion of the heat transfer from the hot gases to the surface of the inner tube takes place by radiative heat transfer.
c) Plate Heat Exchanger Ans.
A plate type heat exchanger consists of a series of separate parallel plates forming thin flow pass. Each plate is separated from the next by gaskets and the hot stream passes in parallel through alternative plates whilst the liquid to be heated passes in parallel between the hot plates. To improve heat transfer the plates are corrugated.
Hot liquid passing through a bottom port in the head is permitted to pass upwards between every second plate while cold liquid at the top of the head is permitted to pass downwards between the odd plates. When the directions of hot & cold fluids are opposite, the arrangement is described as counter current.