
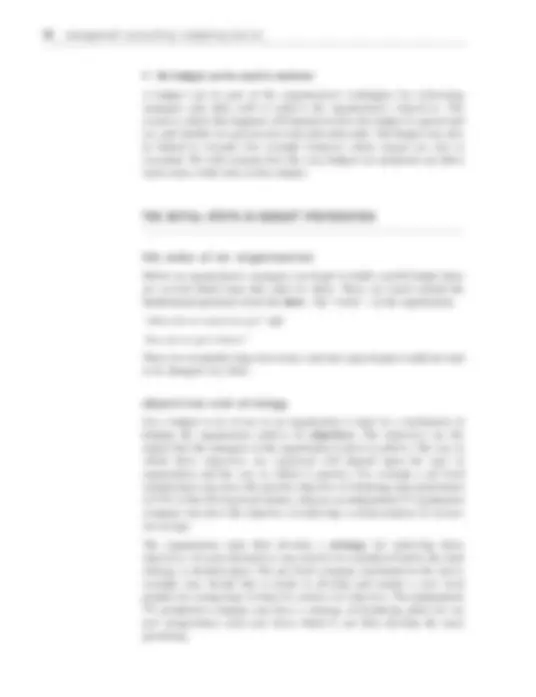
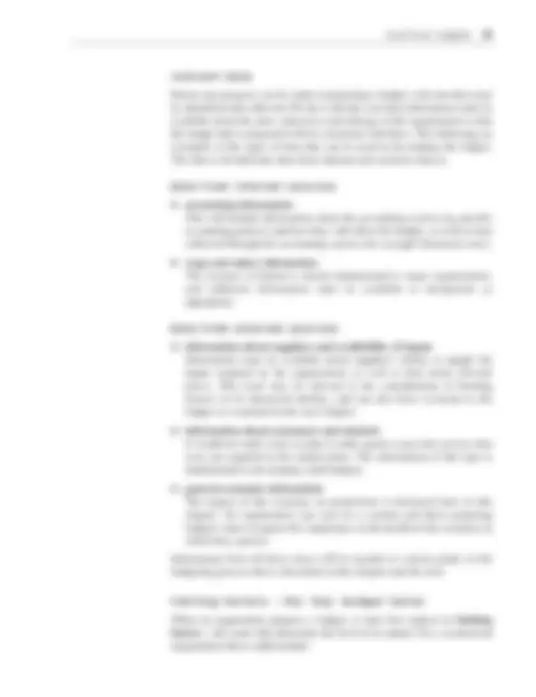
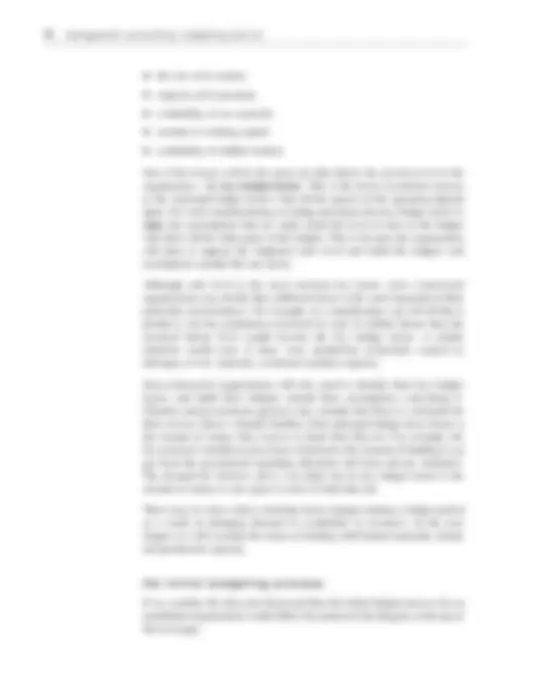
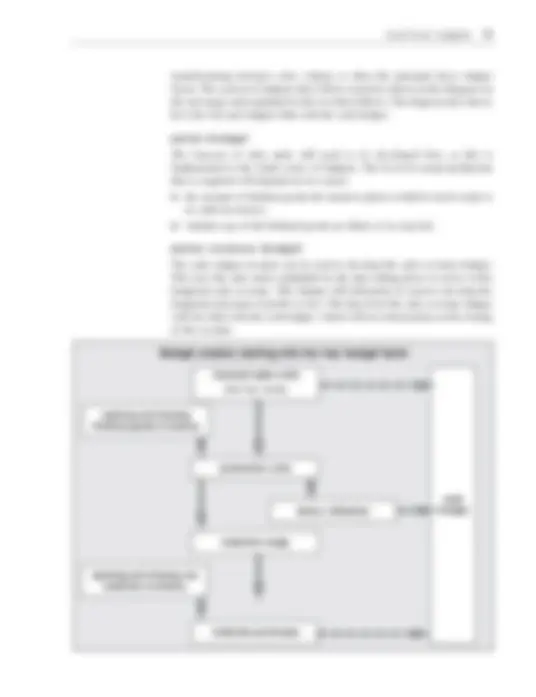
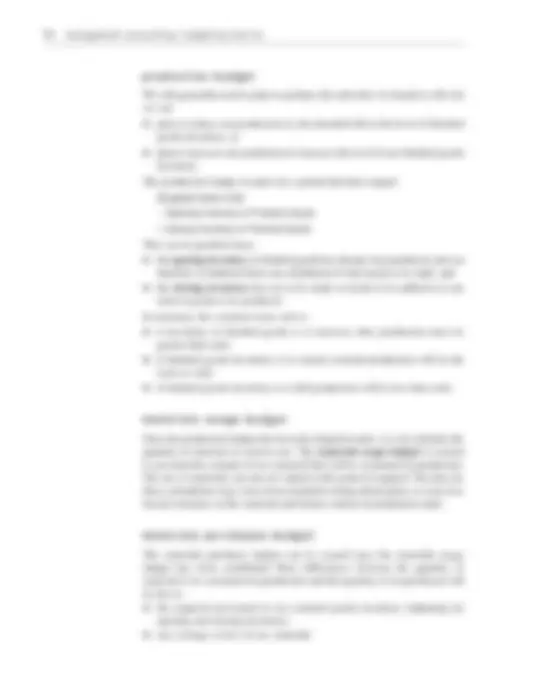
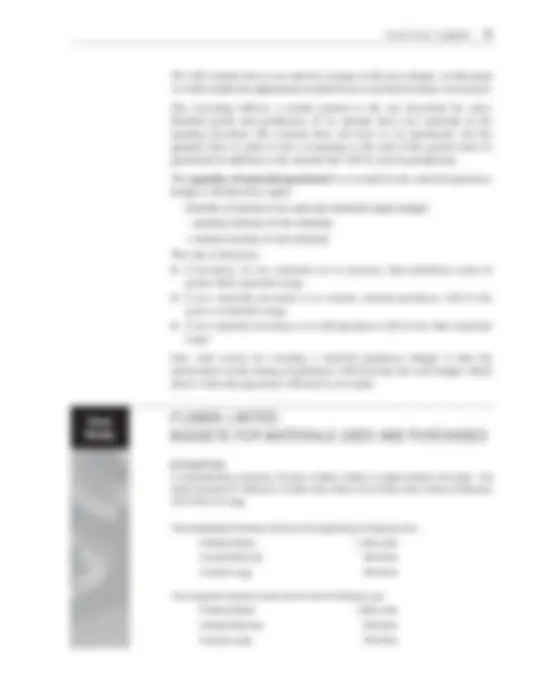
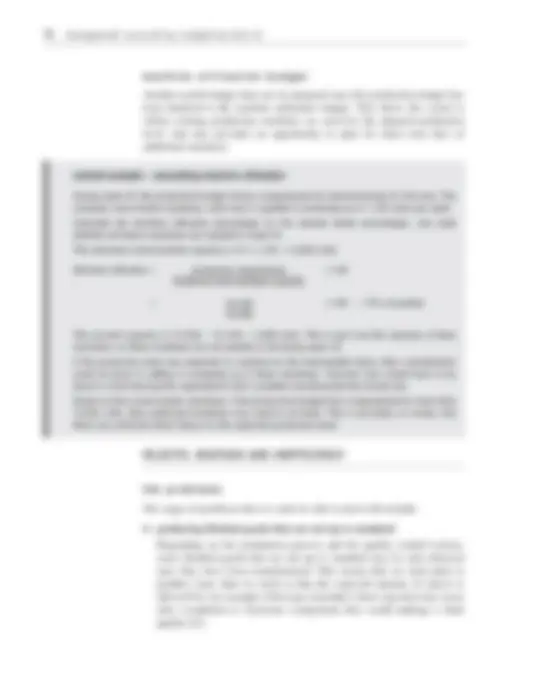
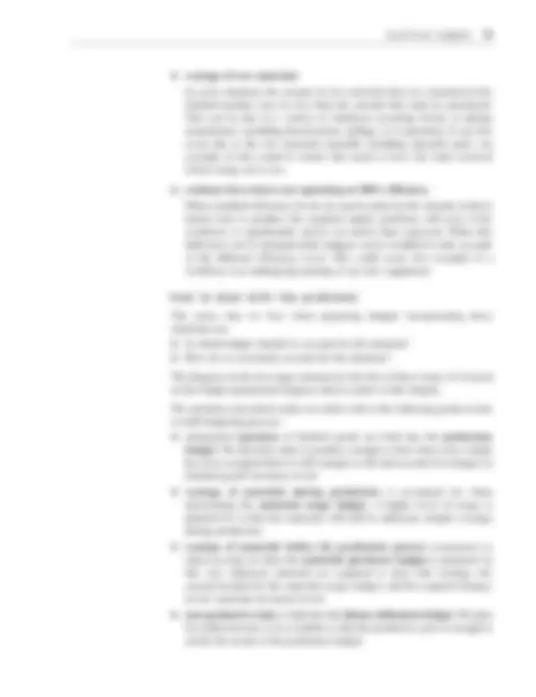
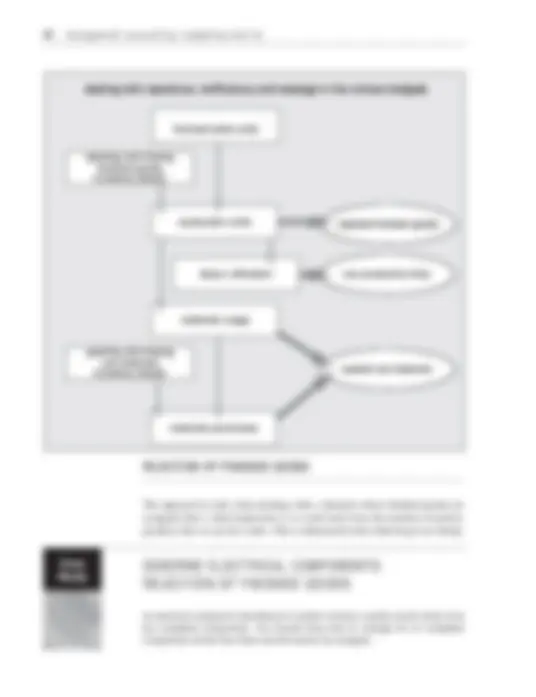
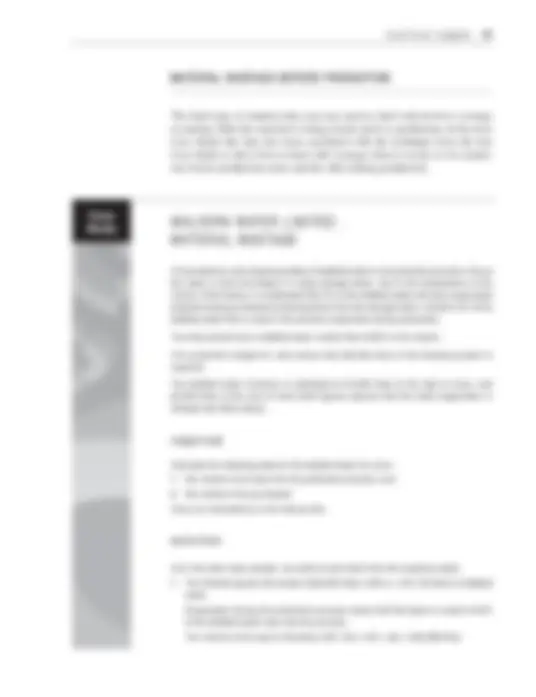
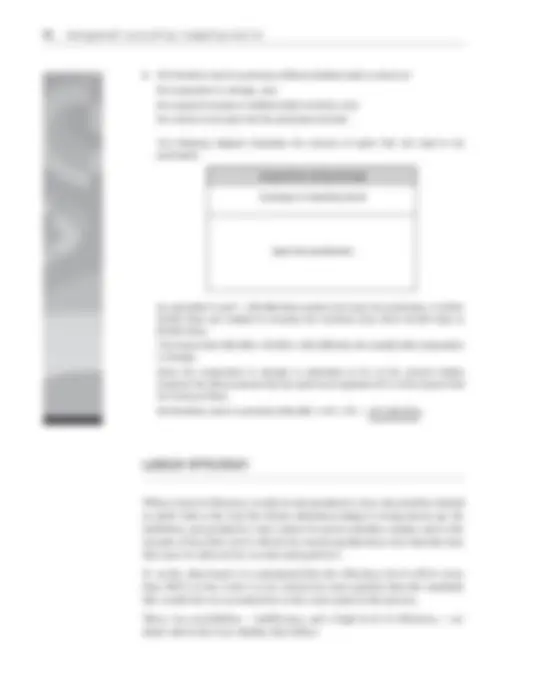
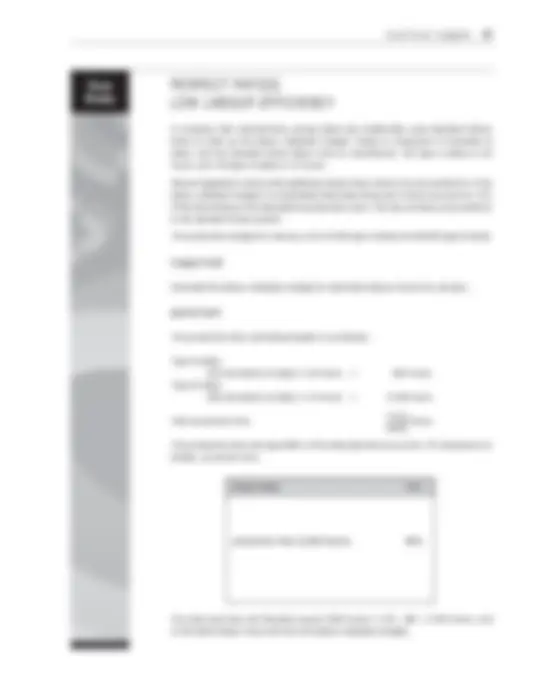
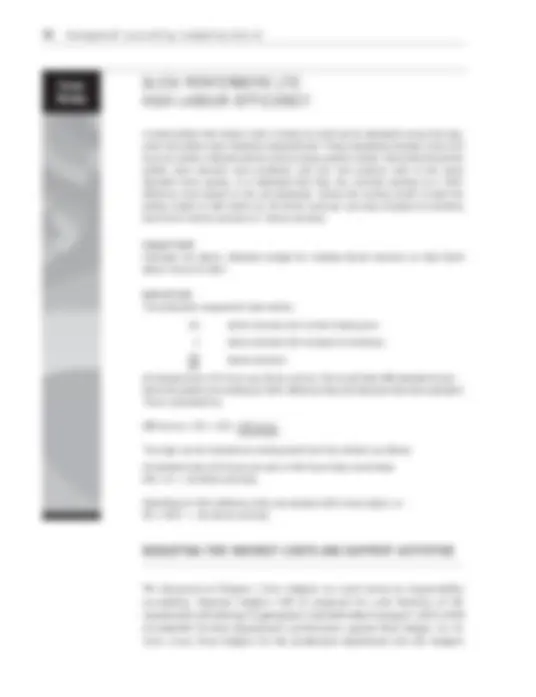
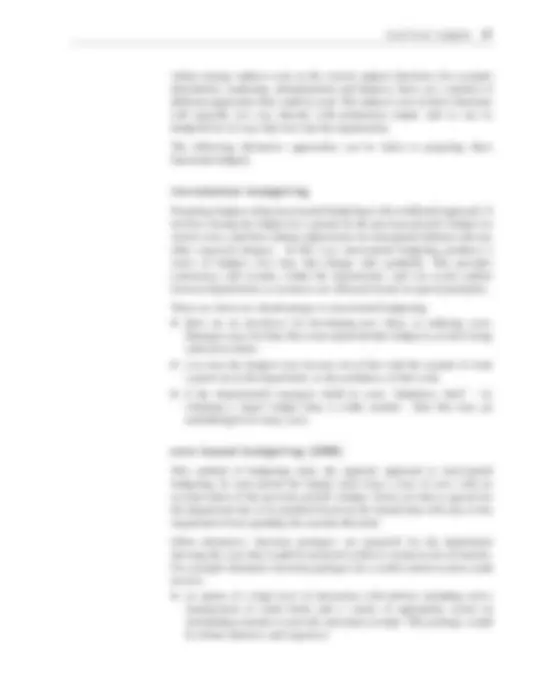
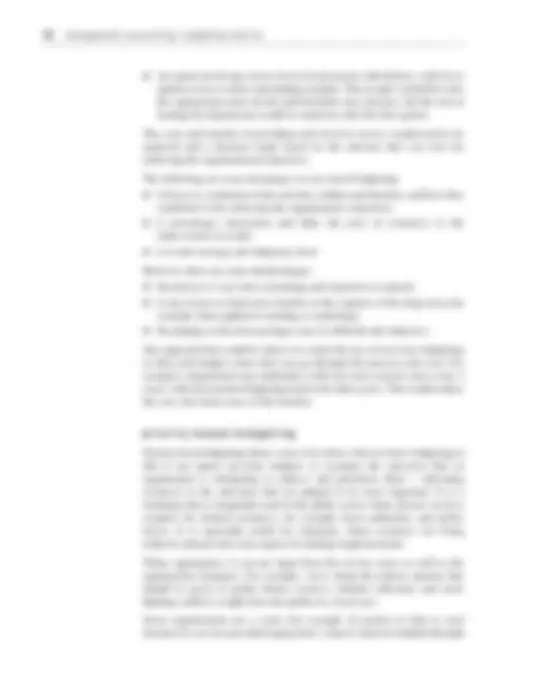
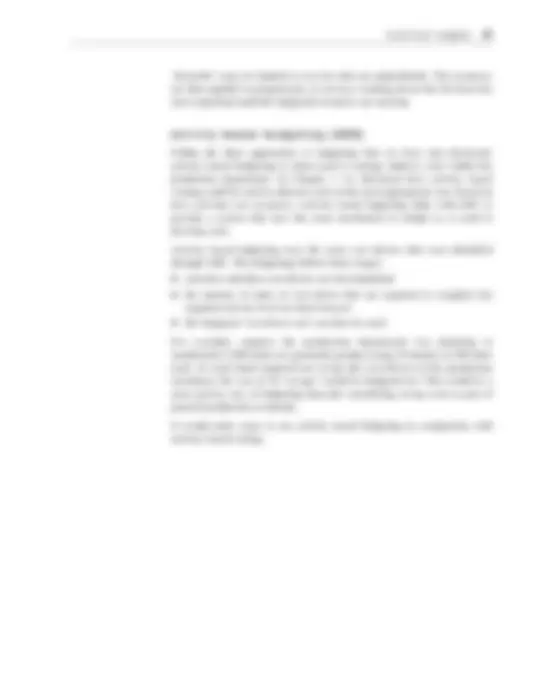
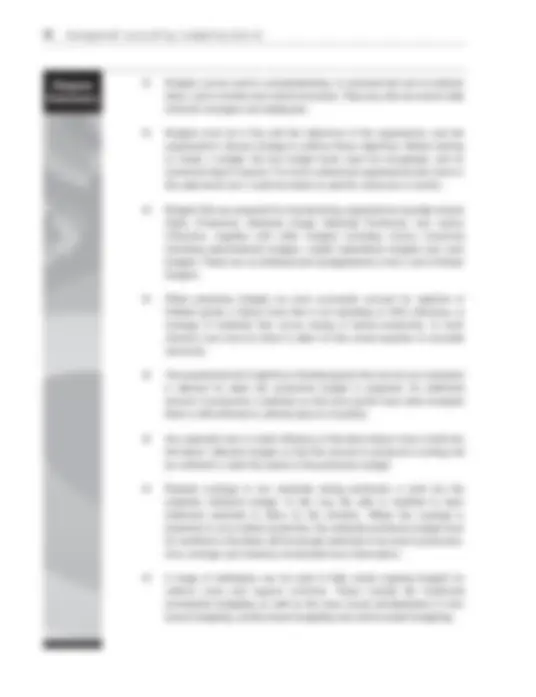
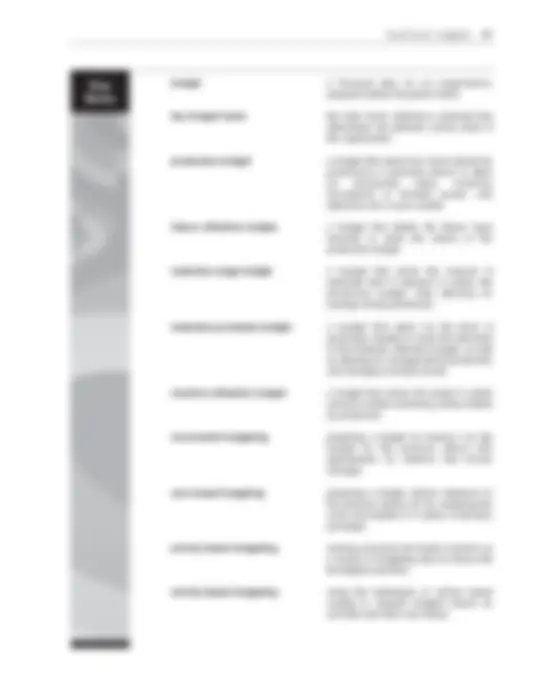
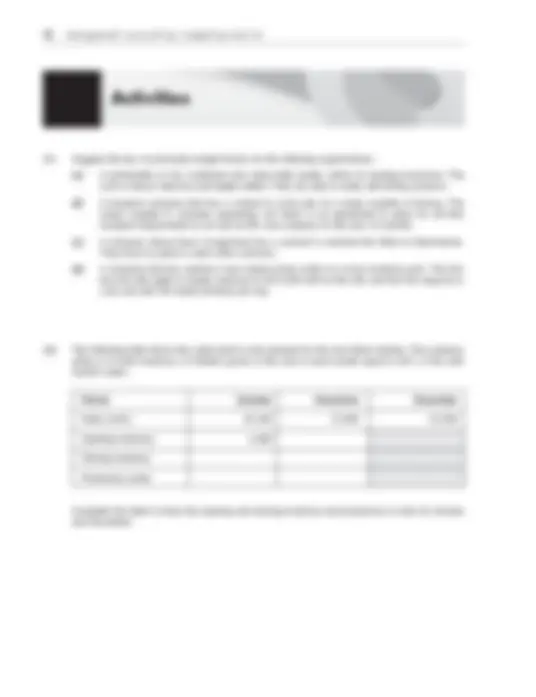
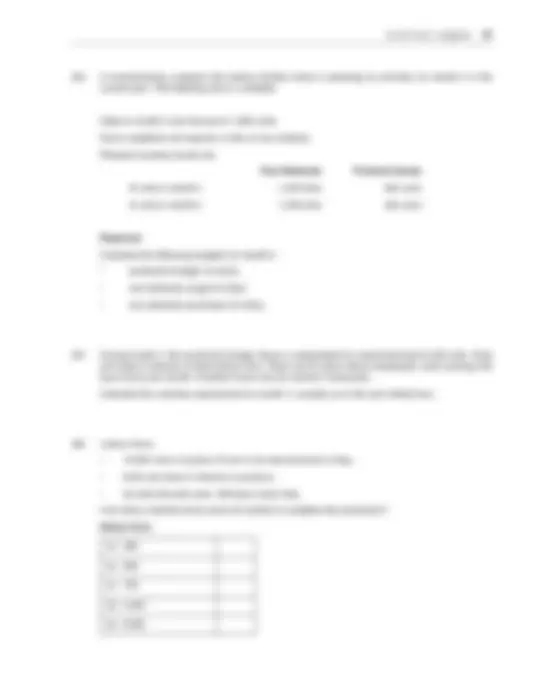
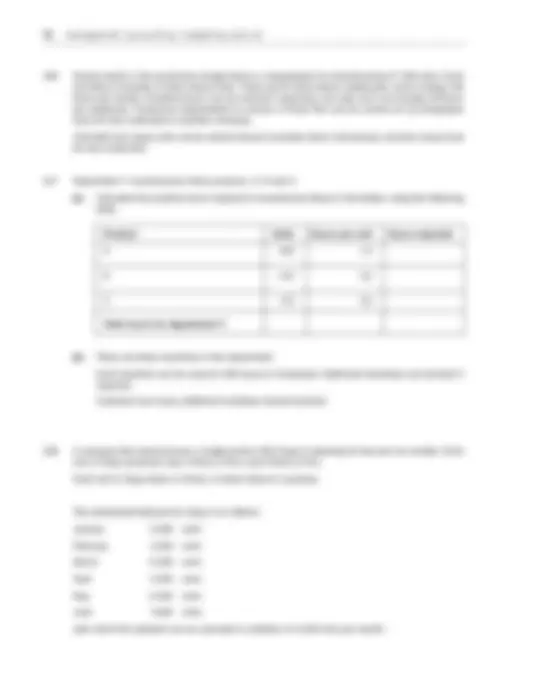
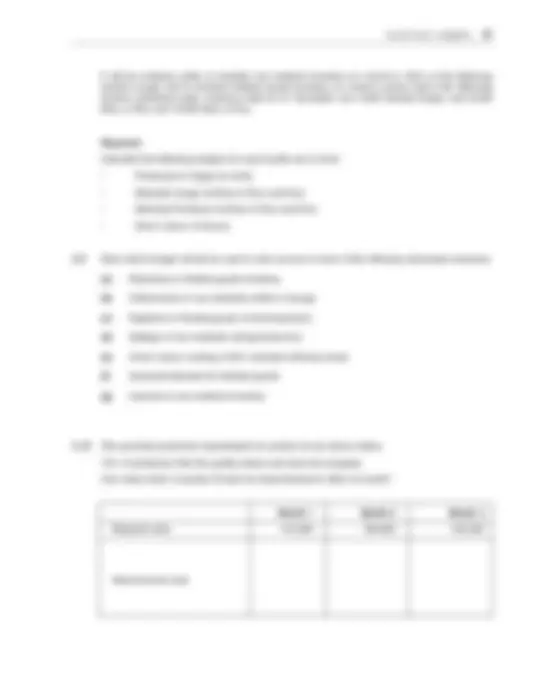
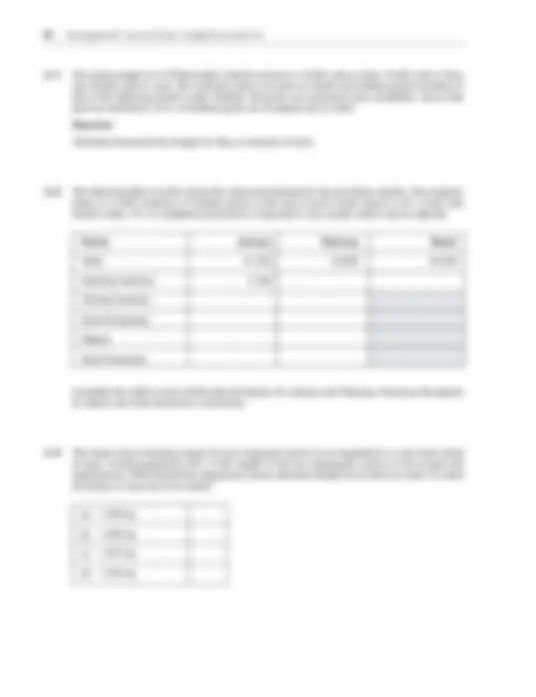
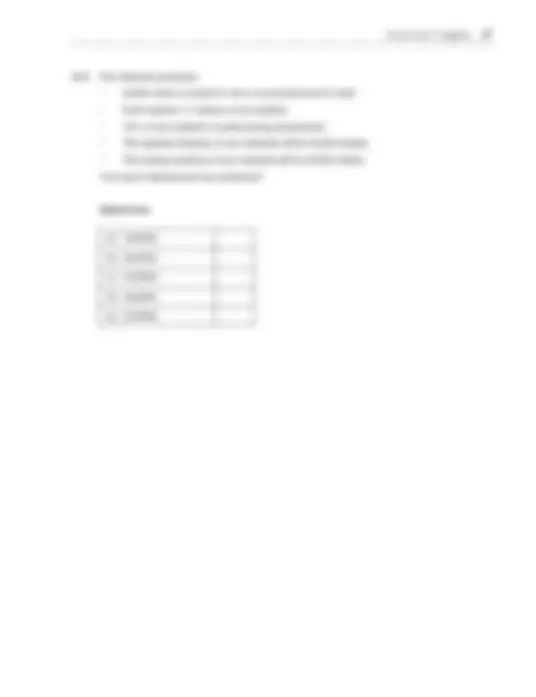
Study with the several resources on Docsity
Earn points by helping other students or get them with a premium plan
Prepare for your exams
Study with the several resources on Docsity
Earn points to download
Earn points by helping other students or get them with a premium plan
Community
Ask the community for help and clear up your study doubts
Discover the best universities in your country according to Docsity users
Free resources
Download our free guides on studying techniques, anxiety management strategies, and thesis advice from Docsity tutors
This chapter explores the preparation of budgets for organizations, discussing their purposes, techniques for construction, and specific budgets such as sales, production, materials usage, materials purchases, labor utilization, functional, capital expenditure, and cash budgets. the relationship between inventory levels and budgets, the importance of accounting for wastage and non-productive time, and various budgeting methods including incremental, zero-based, priority-based, and activity-based budgeting.
What you will learn
Typology: Study notes
1 / 32
This page cannot be seen from the preview
Don't miss anything!
In this chapter we begin our examination of the preparation of budgets.
We start by learning the purposes of budgets, and see how some organisations view particular purposes as more important than others. We examine how budget setting links with the organisation’s objectives and strategy, and must be built around the key (or principal) budget factor – which is often sales.
Next we examine the various budgets that are usually prepared, and how they are sequenced. The key budget factor is normally forecast first, and the other budgets are based around this important data.
We examine in detail how the budgets for a manufacturing organisation are prepared, including dealing with rejection rates, wastage and inefficiency.
Finally we discuss some techniques that can be applied to the construction of budgets for indirect costs and support functions.
A budget is a financial plan for an organisation, prepared in advance.
In any organisation the budget provides the mechanism by which the objectives of the organisation can be achieved. In this way it forms a link between the current position and the position that the organisation’s managers are aiming for. By using a budget firstly to plan and then to monitor, the managers can ensure that the organisation’s progress is co- ordinated to achieve the objectives of the organisation. The specific purposes and benefits of using budgets are as follows.
1 the budget compels planning
By formalising the agreed objectives of the organisation through a budget preparation system, an organisation can ensure that its plans are achievable. It will be able to decide what resources are required to produce the desired outputs, and to make sure that they will be available at the right time.
2 the budget communicates and co-ordinates
Because a budget will be agreed by an organisation, all the relevant personnel will be working towards the same ends. During the budget setting process any anticipated problems should be resolved and any areas of potential confusion clarified. All the organisation’s departments should be in a position to play their part in achieving the overall goals. This objective of all parts of the organisation working towards the same ends is sometimes referred to as ‘ goal congruence ’.
3 the budget can be used to authorise
For organisations where control of activities is deemed to be a high priority the budget can be used as the primary tool to ensure conformity to agreed plans. Once the budget is agreed it can effectively become the authority to follow a particular course of action or spend a certain amount of money. Public sector organisations, with their necessary emphasis on strict accountability, will tend to take this approach, as will some commercial organisations that choose not to delegate too much authority.
4 the budget can be used to monitor and control
An important reason for producing a budget is that management is able to monitor the actual results against the budget. This is so that action can be taken to modify the operation of the organisation as time passes, or possibly to change the budget if it becomes unachievable. This is similar to the way that standard costing is used to monitor and control costs, and can be used alongside that technique.
f u n c t i o n a l b u d g e t s 6 7
r e l e v a n t d a t a
Before any progress can be made in preparing a budget, relevant data must be identified and collected. We have already seen that information must be available about the aims, objectives and strategy of the organisation so that the budget that is prepared will be consistent with these. The following are examples of the types of data that can be used in developing the budget. The data is divided into data from internal and external sources.
d a t a f r o m i n t e r n a l s o u r c e s
n accounting information This will include information about the accounting system (eg specific accounting polices) and how they will affect the budget, as well as data collected through the accounting system (for example historical costs).
n wage and salary information The resource of labour is clearly fundamental to many organisations, and sufficient information must be available to incorporate as appropriate.
d a t a f r o m e x t e r n a l s o u r c e s
n information about suppliers and availability of inputs Information must be available about suppliers’ ability to supply the inputs required by the organisation, as well as data about relevant prices. This issue may be relevant to the consideration of limiting factors (to be discussed shortly), and can also force revisions to the budget as examined in the next chapter.
n information about customers and markets It would not make sense to plan to make goods or provide services that were not required in the market place. The information of this type is fundamental to developing valid budgets.
n general economic information The impact of the economy on projections is discussed later in this chapter. No organisation can exist in a vacuum and those preparing budgets must recognise the importance of the health of the economy in which they operate.
Information from all these areas will be needed at various points in the budgeting process that is described in this chapter and the next.
l i m i t i n g f a c t o r s – t h e ‘ k e y ’ b u d g e t f a c t o r
When an organisation prepares a budget, it must first analyse its limiting factors – the issues that determine the level of its output. For a commercial organisation these could include:
f u n c t i o n a l b u d g e t s 6 9
n the size of its market n capacity of its premises n availability of raw material n amount of working capital n availability of skilled workers
One of the factors will be the main one that affects the activity level of the organisation – the key budget factor. This is the factor (sometimes known as the ‘principal budget factor’) that all the aspects of the operation depend upon. For most manufacturing or trading operations the key budget factor is sales ; the assumptions that are made about the level of sales in the budget will affect all the other parts of the budget. This is because the organisation will plan to support the budgeted sales level and build the budgets and assumptions around this one factor.
Although sales level is the most common key factor, some commercial organisations may decide that a different factor is the most important in their particular circumstances. For example, if a manufacturer can sell all that it produces, but has production restricted by lack of skilled labour then the assumed labour level would become the key budget factor. A similar situation would arise if there were production restrictions caused by shortages of raw materials, or limited machine capacity.
Non-commercial organisations will also need to identify their key budget factor, and build their budgets around their assumptions concerning it. Charities and government agencies may consider that there is a demand for their services that is virtually limitless; their principal budget (key) factor is the amount of money they receive to fund what they do. For example, the Government’s healthcare provision is limited by the amount of funding it can get from the government spending allocation and from private enterprise. The demand for Oxfam’s aid is very high, but its key budget factor is the amount of money it can expect to raise to fund that aid.
There may be times when a limiting factor changes during a budget period as a result of changing demand or availability of resources. In the next chapter we will examine the issues of dealing with limited materials, labour and production capacity.
t h e i n i t i a l b u d g e t i n g p r o c e s s If we combine the ideas just discussed then the initial budget process for an established organisation would follow the pattern in the diagram at the top of the next page.
7 0 m a n a g e m e n t a c c o u n t i n g : b u d g e t i n g t u t o r i a l
cash flow budget this would take account of all the other budgets and their effect on the organisation’s liquidity – note that this is not a functional budget, but is a part of the master budget master budget the calculations from all the revenue and capital budgets contribute to the master budget which takes the form of a budgeted statement of profit or loss (income statement) and a budgeted statement of financial position (balance sheet) together with a cash budget The choice and format of the main budgets will need to be appropriate to the organisation. In Chapter 1 we examined responsibility accounting, and how responsibility centres can be used. Appropriate cost centres, profit centres and investment centres will need to be defined, and the budgets will need to be structured accordingly. For example, if there are separate cost centres for ‘administration’ and ‘marketing’ then there needs to be administration and marketing budgets. In this way managers can be held to account for their department’s performance.
t h e e f f e c t o f c h a n g i n g i n v e n t o r y l e v e l s You will have noticed several references in the list of budgets to inventory levels. Where inventory levels are to remain constant the situation is simple. For example the production budget will be identical to the sales budget if the finished goods inventory level is to remain unchanged, ie the amount you will produce will be the amount you estimate you are going to sell. However if the inventory level is to increase then the extra units of goods that will go into inventory will need to be produced in addition to the units that are to be sold in the budget period. This is a concept that we will return to frequently.
Earlier in this chapter we examined the methods and implications of creating budgets and using budgetary control. We will now look at the numerical work that is needed to produce a budget. This will involve co-ordinating the various budgets so that they are all based on the same assumptions and fit together in a logical sequence. In any tasks involving the preparation of budgets, you may be requested to state the assumptions that they are based on. The procedure that we will need to follow when creating budgets is based on the system described in the earlier section on co-ordinated budgets. Limiting factors need to be considered and the ‘key’ factor identified. For a
7 2 m a n a g e m e n t a c c o u n t i n g : b u d g e t i n g t u t o r i a l
manufacturing business sales volume is often the principal (key) budget factor. The system of budgets that will be created is shown in the diagram on the next page and explained in the text that follows. The diagram also shows how the relevant budgets link with the cash budget.
s a l e s b u d g e t The forecast of sales units will need to be developed first, as this is fundamental to the whole series of budgets. The level of actual production that is required will depend on two issues: n the amount of finished goods the business plans to hold in stock ready to be sold (inventory) n whether any of the finished goods are likely to be rejected.
s a l e s r e v e n u e b u d g e t The sales budget in units can be used to develop the sales revenue budget. This uses the sales units multiplied by the unit selling prices to arrive at the budgeted sales revenue. This budget will ultimately be used to develop the budgeted statement of profit or loss. The data from the sales revenue budget will also link with the cash budget, which will use information on the timing of the receipts.
f u n c t i o n a l b u d g e t s 7 3
materials purchases
labour utilisation
cash budget
production units
materials usage
opening and closing raw materials inventory
forecast sales units (the ‘key’ factor)
opening and closing finished goods inventory
We will examine how to account for wastage in the next chapter. At this point we will consider the adjustments needed for raw material inventory movements. The reasoning follows a similar pattern to the one described for sales, finished goods and production. If we already have raw materials in the opening inventory this amount does not have to be purchased, but the quantity that we plan to have remaining at the end of the period must be purchased in addition to the amount that will be used in production. The quantity of material purchased (as recorded in the material purchases budget) will therefore equal: Quantity of material to be used (per materials usage budget)
_- opening inventory of raw materials,
F l u m e n l i m i t e d : B u d G e t S F O R m At e R i A l S u S e d A n d P u R C H A S e d
s i t u a t i o n A manufacturing company, Flumen limited, makes a single product, the Wye. the sales forecast for February is 5,900 units. each unit of Wye uses 5 kilos of monnow and 3 kilos of lugg.
the anticipated inventory levels at the beginning of February are: Finished Wyes 1,400 units unused monnow 350 kilos unused lugg 200 kilos
the required inventory levels at the end of February are: Finished Wyes 1,800 units unused monnow 250 kilos unused lugg 450 kilos
f u n c t i o n a l b u d g e t s 7 5
Case Study
r e q u i r e d Produce the following budget figures for the month of February: (a) Production of Wye (in units) (b) materials usage of monnow and lugg (in kilos) (c) materials purchases of monnow and lugg (in kilos) s o l u t i o n
(a) Production units = Budgeted Sales units 5,
(b) materials usage monnow: 6,300 x 5 kilos = 31,500 kilos lugg: 6,300 x 3 kilos = 18,900 kilos (c) materials purchases: monnow: Quantity of material to be used 31,500 kilos
l a b o u r u t i l i s a t i o n b u d g e t ( s u b h e a d i n g ) This budget (also known as the direct labour budget) is developed based on the production requirements (in units) shown in the production budget. The labour utilisation budget is usually based on direct labour time in hours, but could be converted into full time equivalent employees. At this point it will be determined whether there are sufficient basic labour hours available for the production requirements, or whether overtime will be needed to be worked. Sometimes the amount of labour time available is a limiting factor (as discussed earlier) and it may be that sub-contractors can be used to make up any shortfall. This is an example of the benefits of good budgeting – so that the labour resources can be planned to ensure that production can go ahead as required.
7 6 m a n a g e m e n t a c c o u n t i n g : b u d g e t i n g t u t o r i a l
m a c h i n e u t i l i s a t i o n b u d g e t Another useful budget that can be prepared once the production budget has been finalised is the machine utilisation budget. This shows the extent to which existing production machines are used for the planned production level, and also provides an opportunity to plan for short term hire of additional machines.
7 8 m a n a g e m e n t a c c o u n t i n g : b u d g e t i n g t u t o r i a l
worked example – calculating machine utilisation
during week 52, the production budget shows a requirement for manufacturing 10,120 units. the company owns twelve machines, each one is capable of producing up to 1,125 units per week. Calculate the machine utilisation percentage (to the nearest whole percentage), and state whether all twelve machines are needed in week 52. the maximum total machine capacity is 12 x 1,125 = 13,500 units
machine utilisation = production requirement x 100 maximum total machine capacity
= 10,120 x 100 = 75% (rounded) 13,
the unused capacity is (13,500 – 10,120) = 3,380 units. this is just over the capacity of three machines, so three machines are not needed at all during week 52. if this production level was expected to continue for the foreseeable future, then consideration could be given to selling or scrapping up to three machines. However care would have to be taken to avoid leaving the organisation with a problem should production levels rise. Based on the current twelve machines, if the production budget had a requirement for more than 13,500 units, then additional machines may need to be hired. this is provided, of course, that there was sufficient direct labour for the expected production level.
t h e p r o b l e m s The range of problems that we must be able to deal with include:
n producing finished goods that are not up to standard Depending on the production process and the quality control system, some finished goods that are not up to standard may be only detected once they have been manufactured. This means that we must plan to produce more than we need so that the expected number of rejects is allowed for. An example of the type of product where rejection may occur after completion is electronic components that would undergo a final quality test.
n wastage of raw materials
In some situations the amount of raw materials that are contained in the finished product may be less than the amount that must be purchased. This can be due to a variety of situations occurring before or during manufacture, including deterioration, spillage, or evaporation. It can also occur due to the raw materials naturally including unusable parts. An example of this could be timber that needs to have the bark removed before being cut to size.
n a labour force that is not operating at 100% efficiency
When standard efficiency levels are used to plan for the amount of direct labour time to produce the required output, problems will arise if the workforce is significantly slower (or faster) than expected. When this difference can be anticipated the budgets can be modified to take account of the different efficiency level. This could occur (for example) if a workforce was undergoing training to use new equipment.
h o w t o d e a l w i t h t h e p r o b l e m s
The issues that we face when preparing budgets incorporating these situations are:
n In which budget should we account for the situation? n How do we accurately account for the situation?
The diagram on the next page summarises the first of these issues. It is based on the budget preparation diagram shown earlier in this chapter.
The problems described earlier are dealt with at the following points in the overall budgeting process:
n anticipated rejections of finished goods are built into the production budget. We therefore plan to produce enough so that when some output has been scrapped there is still enough to sell and account for changes in finished goods inventory levels
n wastage of materials during production is accounted for when determining the materials usage budget. A higher level of usage is planned for so that the materials will still be sufficient, despite wastage during production
n wastage of materials before the production process commences is taken account of when the materials purchases budget is prepared. In this way sufficient materials are acquired to deal with wastage, the amount needed for the materials usage budget, and the required changes in raw materials inventory levels
n non-productive time is built into the labour utilisation budget. We plan for sufficient time to be available so that the productive part is enough to satisfy the needs of the production budget
f u n c t i o n a l b u d g e t s 7 9
the forecast sales volume for the month of march is 5,200 components, and the production budget is to incorporate an increase in finished goods inventory from 1, components to 1,440 components, as well as the typical failure rate.
r e q u i r e d
Calculate the production budget (in numbers of components) for march.
s o l u t i o n
Both the sales forecast and the finished goods inventory increase must be based on ‘good’ components. it would not make sense to sell or place into inventory any units that had failed the quality inspection.
the number of ‘good’ components required is therefore:
Budgeted Sales units 5,
But actual production must be greater than this amount to account for rejects. Since the rejection rate is assumed to be 6%, the 5,640 ‘good’ units must equal 94% of the required production level, as demonstrated in this diagram.
the production budget must therefore equal 5,640 x 100 ÷ 94 = 6,000 units.
You should be careful to note that the calculation does not involve simply adding 6% to the good production, but is effectively adding 6/94, because the good production is 94% of the total production. this technique is often examined, and is a frequent source of confusion amongst students.
notice that you can always check your answer. if 6% of 6,000 units are rejected, ie 360 are rejected, 5,640 units are left.
f u n c t i o n a l b u d g e t s 8 1
reject units 6% of production
‘good’ units (5,640) 94% of production
Wastage during manufacture is a common problem, and occurs in industries as diverse as food production and house building. There can also be situations where one material incurs wastage, while another adds to the weight of the finished product. The next case study examines this problem.
C O O l C H i P C O m PA n Y : m At e R i A l W A S tA G e
A frozen potato chip manufacturer purchases whole potatoes with skins. these are then peeled, any imperfections are removed, and the potatoes are sliced into chips and fried before freezing. the average wastage that occurs during peeling and imperfection removal is 20% of the weight of the whole potatoes. no further wastage occurs during slicing, or frying. the production budget for july is for 100,000 kilos of frozen chips, based on their weight immediately prior to freezing.
r e q u i r e d
Calculate the materials usage budget (in kilos) for july for whole raw potatoes.
s o l u t i o n
in order to calculate the usage we must work back from the production budget:
to produce 100,000 kilos of uncooked chips we need to start with a larger weight of whole potatoes. the uncooked chips represent 80% of the weight of the whole potatoes, since 20% is lost as skin and imperfections. therefore whole potatoes will equal 100,000 x 100 ÷ 80 = 125,000 kilos.
the materials utilisation budget will therefore be: 125,000 kilos whole potatoes.
it is worth double-checking our calculation. this can be done as follows: 125,000 kilos whole potatoes used, less 20% wastage at the peeling stage, leaving 100,000 (80%) chips.
8 2 m a n a g e m e n t a c c o u n t i n g : b u d g e t i n g t u t o r i a l
Case Study
2 We therefore need to purchase sufficient distilled water to allow for: the evaporation in storage, plus the required increase in distilled water inventory, plus the volume to be input into the production process.
the following diagram illustrates the amount of water that will need to be purchased:
As calculated in part 1, 365,368 litres needs to be input into production. A further 30,000 litres are needed to increase the inventory level (from 50,000 litres to 80,000 litres). this means that (365,368 + 30,000) = 395,368 litres are needed after evaporation in storage. Since the evaporation in storage is estimated at 3% of the amount initially acquired, the above amount that we need must represent 97% of the amount that we must purchase. We therefore need to purchase (395,368 x 100 ÷ 97) = 407,596 litres
When a lack of efficiency results in non-productive time, the problem should be dealt with at the time the labour utilisation budget is being drawn up. By definition, non-productive time cannot be used to produce output, and so the amount of time that can be effectively used in production is less than the time that must be allowed for in total (and paid for). If, on the other hand, it is anticipated that the efficiency level will be more than 100% (ie the work is to be carried out more quickly than the standard) this would also be accounted for at the same point in the process. These two possibilities – inefficiency and a high level of efficiency – are dealt with in the Case Studies that follow.
8 4 m a n a g e m e n t a c c o u n t i n g : b u d g e t i n g t u t o r i a l
evaporation during storage
increase in inventory level
input into production
P e R F e C t PAt i O S : l O W l A B O u R e F F i C i e n C Y
A company that manufactures paving slabs has traditionally used standard labour times to build up the labour utilisation budget. Output is measured in hundreds of slabs, and the standard direct labour time to manufacture 100 type A slabs is 3. hours, and 100 type B slabs is 4.2 hours. Recent legislation means that additional break times need to be accounted for in the labour utilisation budget. it is estimated that break times will in future account for 12% of the direct labour time allocated to production work, this has not been accounted for in the standard times quoted. the production budget for january is for 24,000 type A slabs and 58,000 type B slabs.
r e q u i r e d
Calculate the labour utilisation budget (in total direct labour hours) for january.
s o l u t i o n
the productive time (excluding breaks) is as follows:
type A slabs: 240 (hundreds of slabs) x 3.6 hours = 864 hours type B slabs: 580 (hundreds of slabs) x 4.2 hours = 2,436 hours
total productive time 3,300 hours
this productive time will equal 88% of the total paid time due to the 12% allowance for breaks, as shown here.
the total paid time will therefore equal 3,300 hours x 100 ÷ 88 = 3,750 hours, and 3,750 direct labour hours will form the labour utilisation budget.
f u n c t i o n a l b u d g e t s 8 5
Case Study
break times 12%
productive time (3,300 hours) 88%