
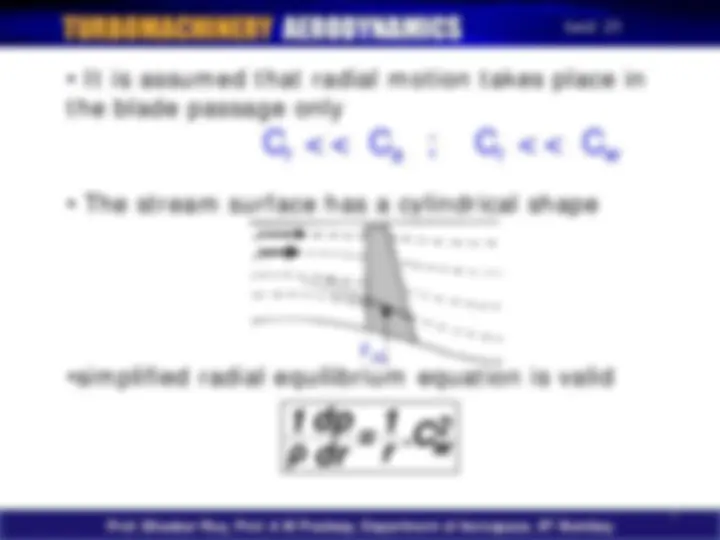
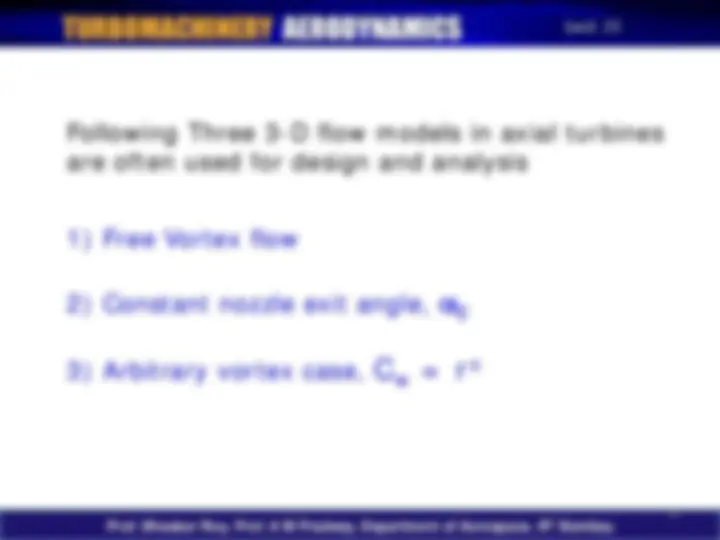
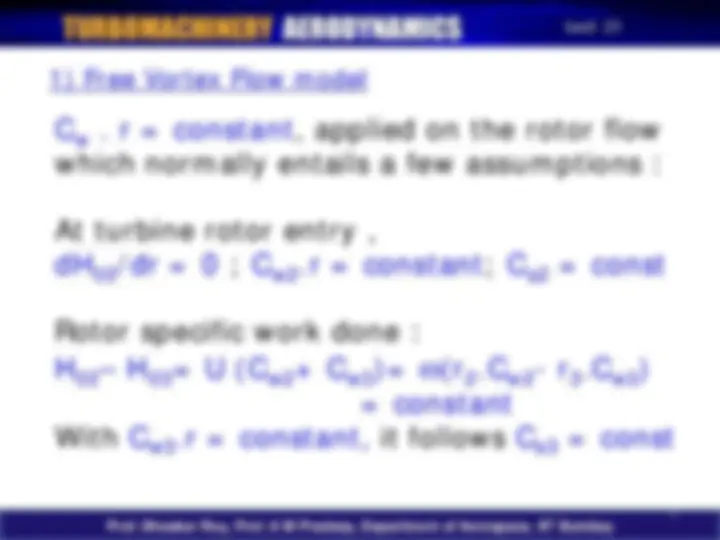
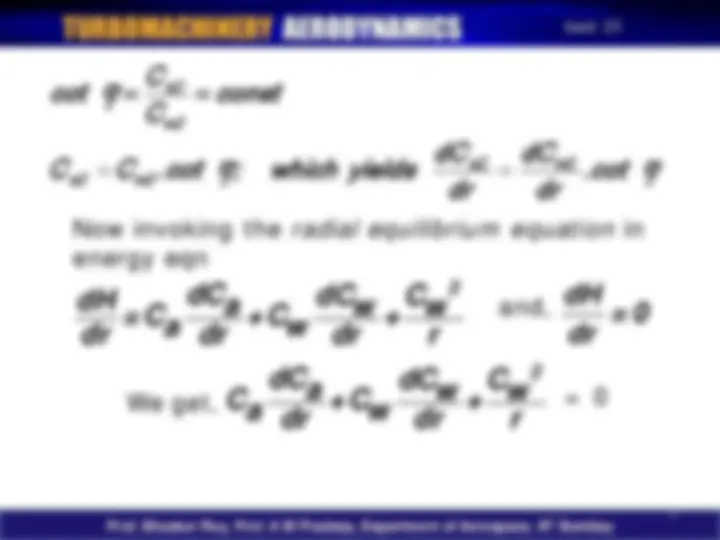
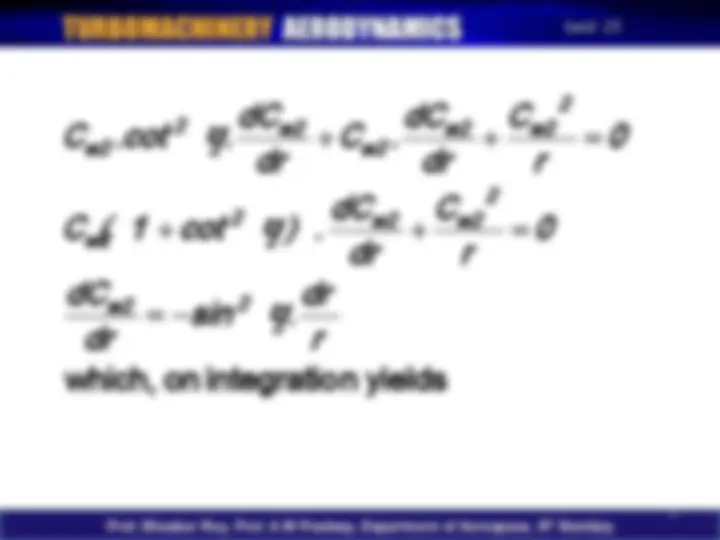
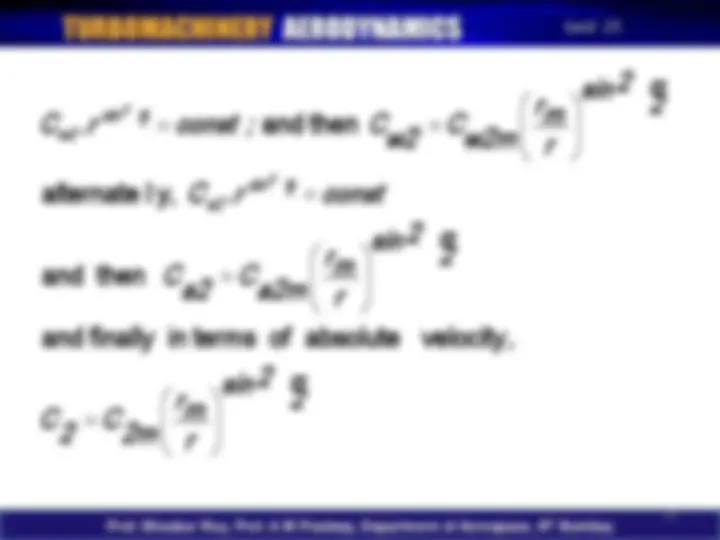
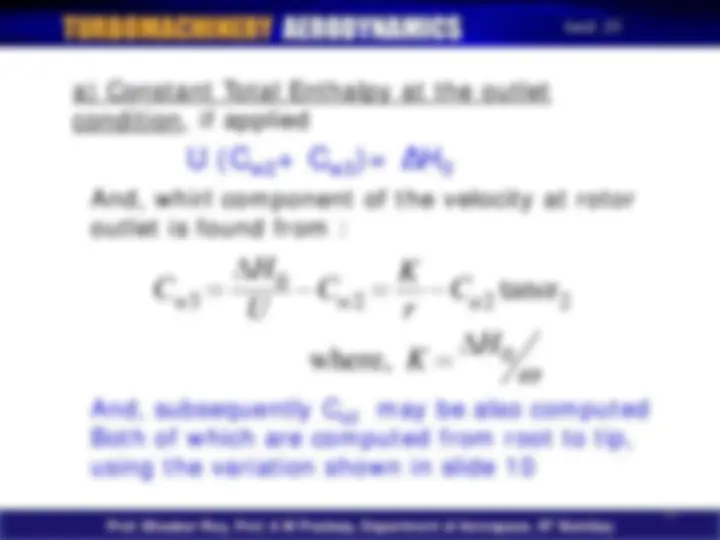
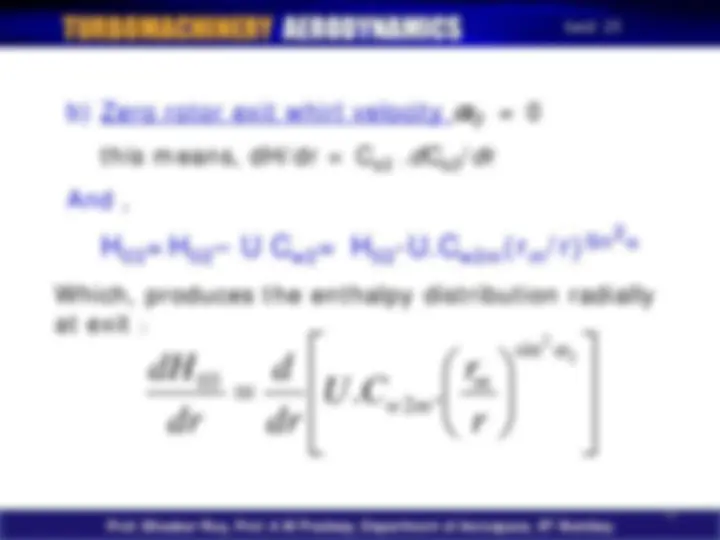
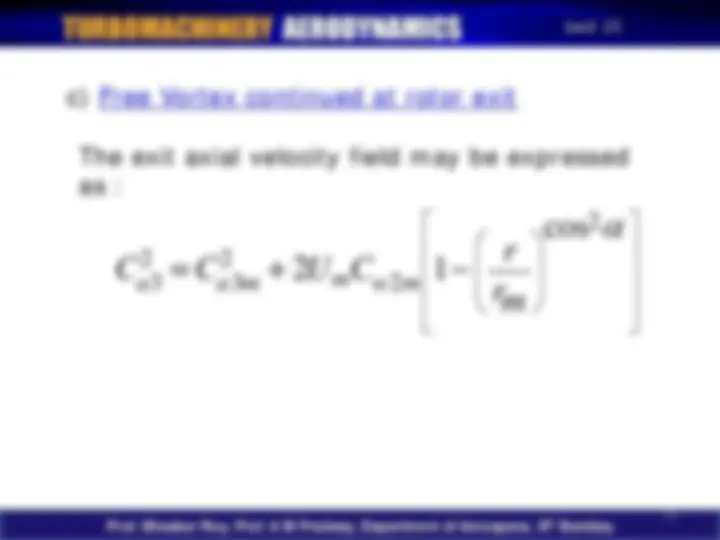
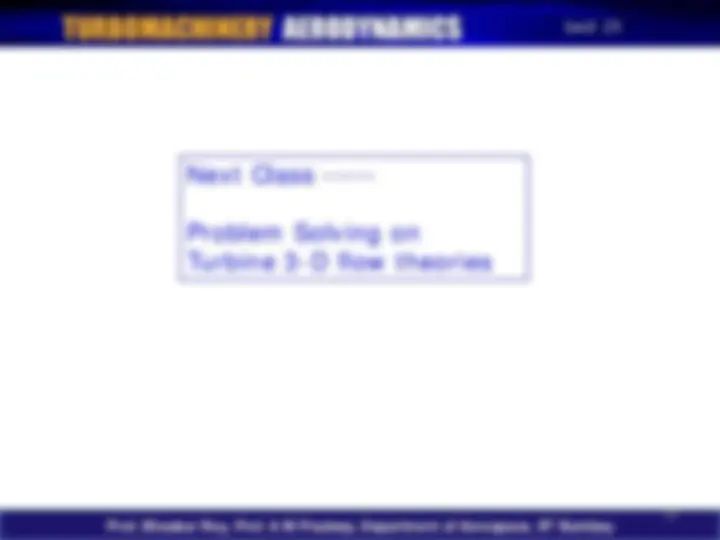
Study with the several resources on Docsity
Earn points by helping other students or get them with a premium plan
Prepare for your exams
Study with the several resources on Docsity
Earn points to download
Earn points by helping other students or get them with a premium plan
Community
Ask the community for help and clear up your study doubts
Discover the best universities in your country according to Docsity users
Free resources
Download our free guides on studying techniques, anxiety management strategies, and thesis advice from Docsity tutors
Some concept of Turbomachinery Aerodynamics are Axial Flow Compressors, Axial Turbine Design Considerations, Blade Performance, Engine Performance Significantly, Flows Through Axial Compresso. Main points of this lecture are: Free Vortex Flow, Stream Surface, Cylindrical Shape, Simplified Radial, Radial Equilibrium, Equilibrium Equation, Nozzle Exit, Exit Angle, Free Vortex Flow, Arbitrary Vortex Case
Typology: Slides
1 / 18
This page cannot be seen from the preview
Don't miss anything!
1
Axial Flow Turbines
3-D Flow theories
Following Three 3-D flow models in axial turbines are often used for design and analysis
Free Vortex flow
Constant nozzle exit angle, α 2
Arbitrary vortex case, C (^) w = rn
C (^) w. r = constant, applied on the rotor flow which normally entails a few assumptions :
At turbine rotor entry , dH 02 /dr = 0 ; C (^) w2 .r = constant; C (^) a2 = const
Rotor specific work done :
= constant With C (^) w3 .r = constant, it follows C (^) a3 = const
Constant Nozzle exit angle model
This model has been utilized for the practical purpose of creating stator-nozzle blades with zero twist. When stator-nozzles are facing very high inlet temperature elaborate cooling mechanism is embedded inside the blades; to facilitate efficient cooling of the blades, it is thought that such blades may not be twisted at all.
2 a2 w a2 w2 2
w
2 a
.cot^ α dr
dC dr
C C .cot^ α; which yields dC
const C
cot^ α
= =
= =
Now invoking the radial equilibrium equation in energy eqn dH = 0 dr
and,
We get,
sin^2 α
r
rm C 2 C2m
sin^2 α
r
rm Ca2 Ca2m
, C .r const
sin^2 α
r
rm C .r const ; Cw2 Cw2m
(^22)
(^22)
sin^ α a
sin^ α w
=
=
=
= =
and finally in terms of absolute velocity
and then
alternate ly
and then
So, at the rotor inlet station one can say,
α 2 = constant
then,
r m
r C2m
C 2 Ca2m
Ca Cw2m
Cw2 (^) = = =
if
U (C (^) w2 + C (^) w3 )= ΔH (^0)
a) Constant Total Enthalpy at the outlet condition, if applied
ω
α
0
2 2 2
0 3
where,
tan
K^ H
C r
K C U
H C (^) w w a
=^ ∆
− = −
And, whirl component of the velocity at rotor outlet is found from :
And, subsequently C (^) a3 may be also computed Both of which are computed from root to tip, using the variation shown in slide 10
b) Zero rotor exit whirl velocity α 3 = 0 this means, dH/dr = C (^) a3. d C (^) a3 / d r And , H 03 =H 02 – U C (^) w2 = H 02 -U.C (^) w2m(r (^) m /r)Sin (^2) α
sin^22
2
α
w m
Which, produces the enthalpy distribution radially at exit :
Depending on the value of n there are four flow variation possibilities
i) n = -1 -- resolves to Free Vortex Model
ii) n= 0 ----- resolves to constant free vortex
iii) n= 1 ---- gives ‘solid body rotation’ model
iv) n= -2 --- produces ‘strong vortex flow’
All these flow models are considered for use in Turbine design and preliminary analysis