
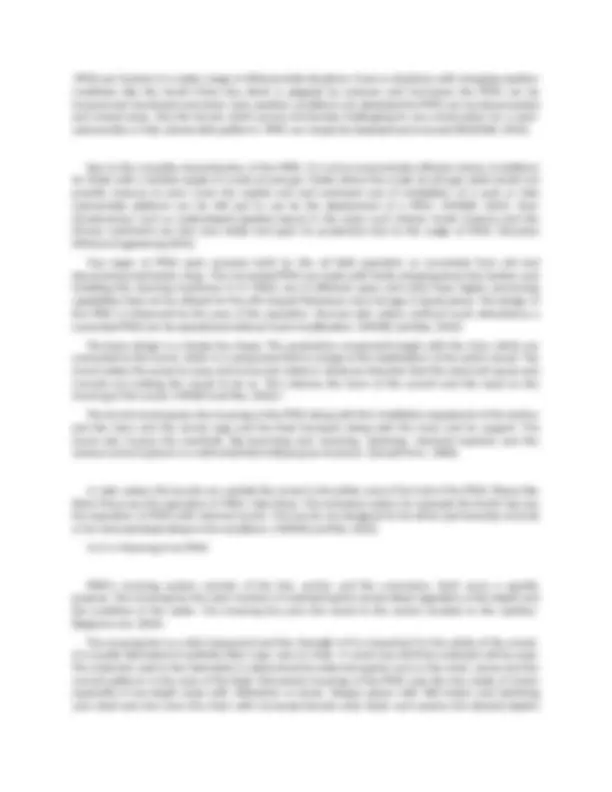
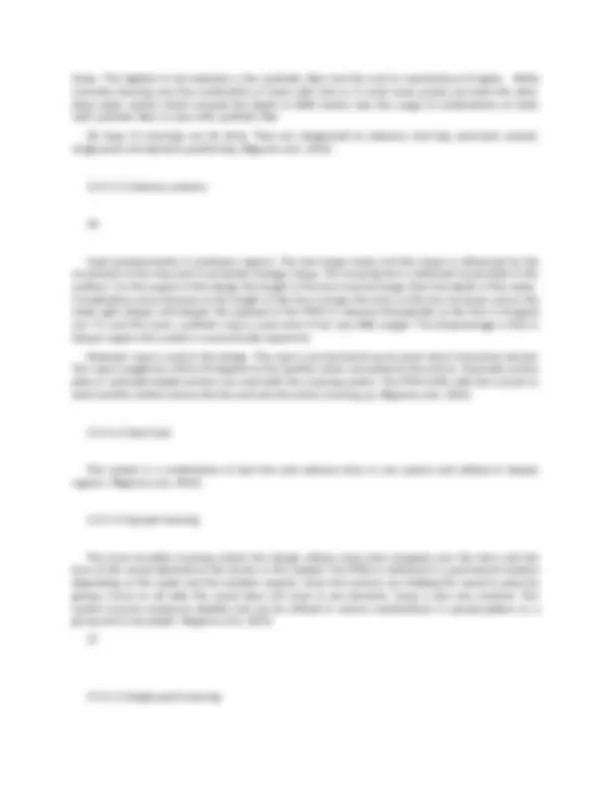
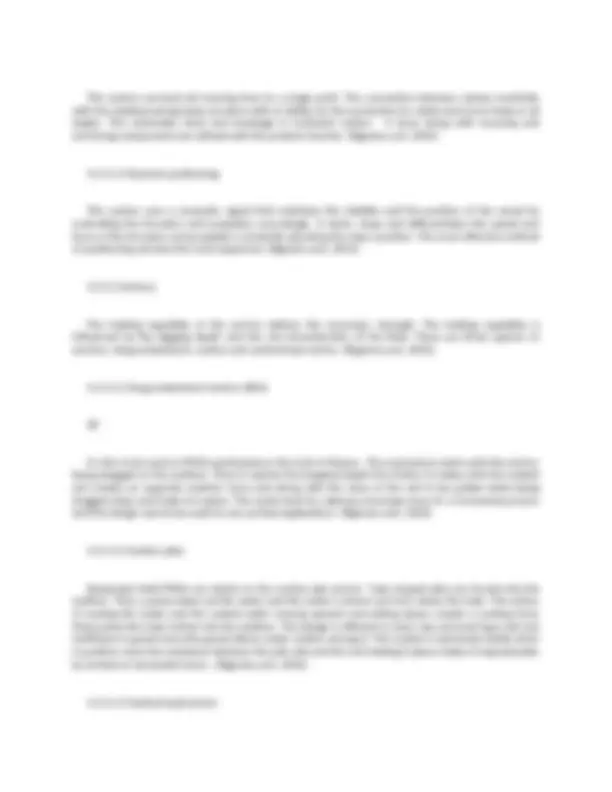
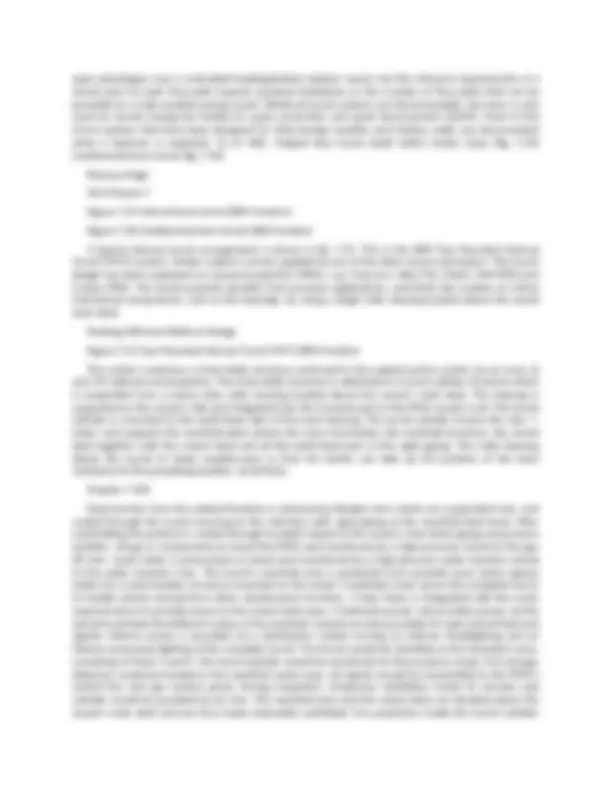
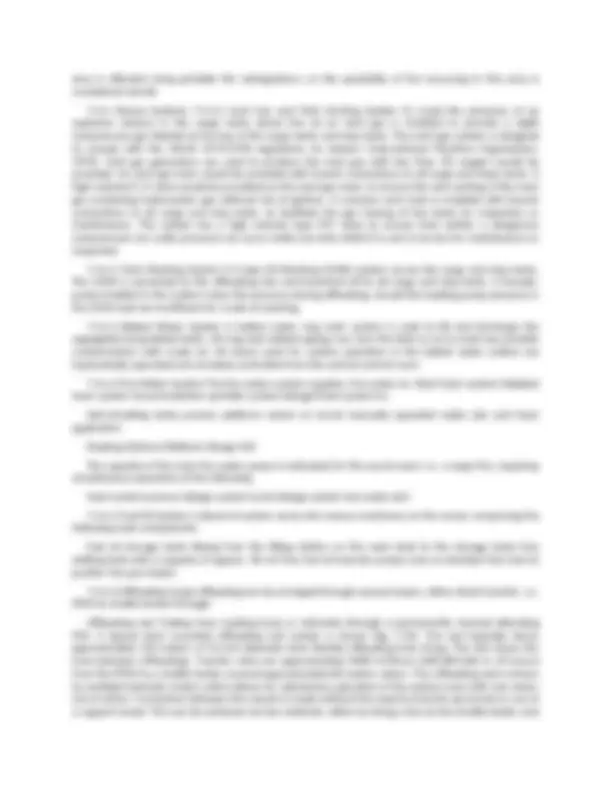
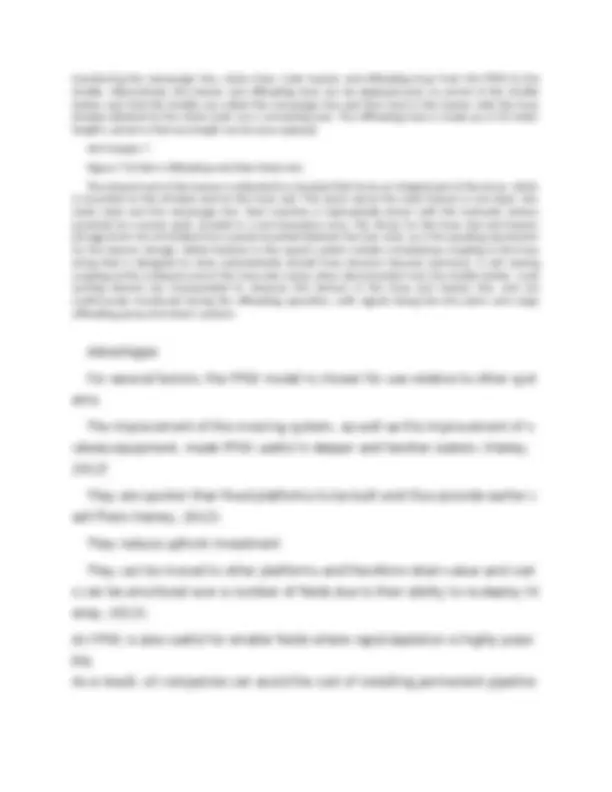
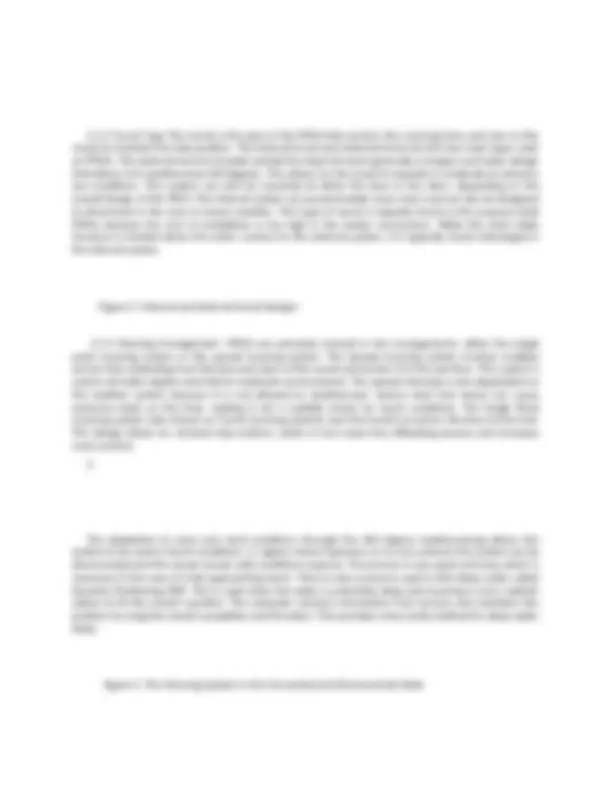
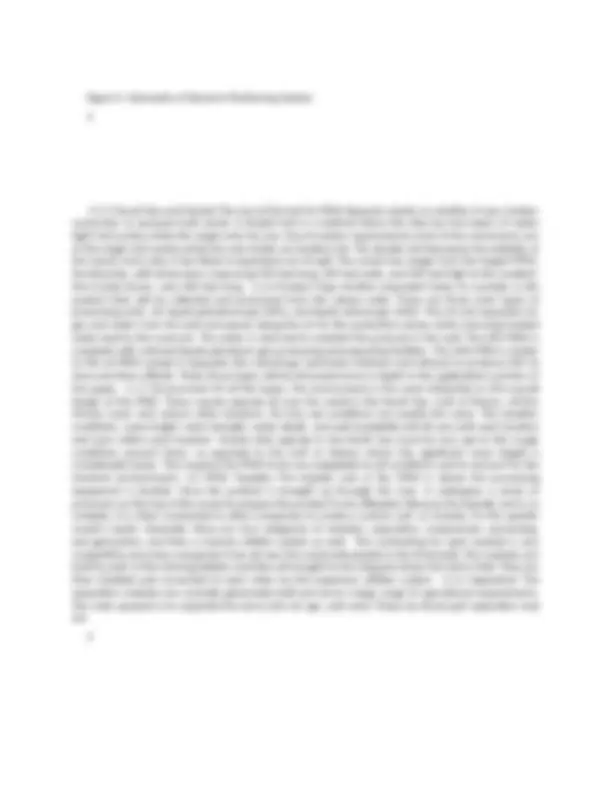
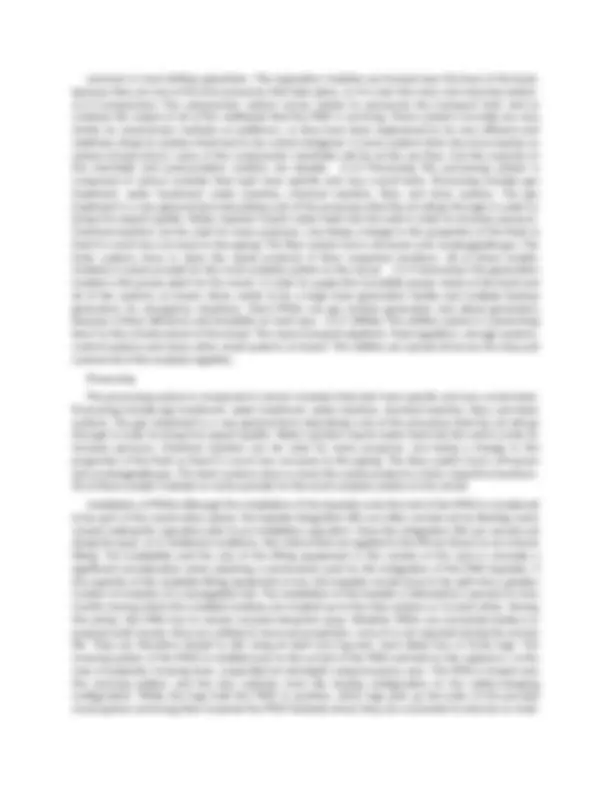
Study with the several resources on Docsity
Earn points by helping other students or get them with a premium plan
Prepare for your exams
Study with the several resources on Docsity
Earn points to download
Earn points by helping other students or get them with a premium plan
Community
Ask the community for help and clear up your study doubts
Discover the best universities in your country according to Docsity users
Free resources
Download our free guides on studying techniques, anxiety management strategies, and thesis advice from Docsity tutors
floating production storage and offloading
Typology: Assignments
1 / 16
This page cannot be seen from the preview
Don't miss anything!
Introduction The industry of oil and gas involves the usage of various machineries and platforms to derive the many functions needed to run the industry from the ground up (LUKOIL, 2013). The demand for fossil fuel based energy along with other energy sources has continued to increase drastically. (Islam Saiful A.B.M, 2012) To simplify the entire process of turning the crude petroleum into usable oil and gas products several types of oil processing platforms are utilized. Among them are the semi-submersible, floating production, storage and offloading (FPSO), conventionally fixed platforms, compliant tower, spar, vertically moored tension leg and mini tension leg platform and finally sub-sea completion and tie-back to host facility (Devold Harvard, 2013) Floating production, storage and offloading platform is an oil and gas facility also known as FPSO. FPSO are widely used ever since the 1970s. The parts of the oil wells that has seen the operation of FPSO are Angola, Offshore Brazil, Asia Pacific, the Equatorial Guinea (FPSO.com, 2015) An FPSO is an offshore floating production, storage and offloading vessel and is one of a range of floating systems used by the offshore oil and gas industry today. FPSO is a type of floating tank system designed to receive all the crude oil from wells, process it and store it until the oil can be offloaded to shuttle tankers or be transported through pipelines to shore. The FPSOs are generally ship shaped floaters with provisions for storing and offloading of oil simultaneously An FPSO is commonly a converted oil tanker but can also be a purposely built vessel. It is often similar in appearance to a ship and carries all the necessary production and processing facilities normally associated with a fixed oil and gas platform including accommodation aboard what is know as the "topside". An FPSO also has storage capacity within the hull for crude oil recovered from the reservoir. The FPSO is usually moored permanently on location during production and is connected to the wells on the seabed by flexible risers.^1 The 35 percent of FPSO are from converted cargo ships while the other 65 percent are newly built units. The hull of the vessel in lined with all the machineries required to produce, store and offload the oil and gas product derived from the oil wells (Potthurst Rob 2003). The first tanker based FPSO was installed by Shell in its Castellon field offshore Spain in 1977.^3 There are currently approximately 70 FPSOs in operation worldwide, including seven in Australia. The FPSO can be compared with a range of different offshore floating systems that, like the FPSO, are not fixed permanently to the seabed but are designed to be moored on location for a long period of time. Some of these floating systems include:^2 (a) The floating storage and offloading system (FSO), which is a ship or barge-shaped floating hull incorporating tanks for storage of produced oil, and a method of loading the oil into offtake tankers. These installations do not have any production or processing facilities. (b) The floating production system (FPS) which is a general term to describe any floating facility designed to receive crude oil from producing wells and process it. It may not have facilities for storage, in which case export would be by pipeline to shore or to a nearby FSO. (c) The floating storage unit (FSU) which is a floating facility intended only for storage of oil. Export may be by pipeline to an onshore facility or by shuttle tankers.
During the recent years FPSOs have become the major production unit both for shallow and deep waters either in mild or harsh environments (Eide, 2008). Advantages They eliminate the need for costly long-distance pipelines to an onshore terminal
faster. The lightest of all materials is the synthetic fiber but the cost to manufacture it higher. While normally mooring uses the combination of chain with wire or in some cases purely just chain the ultra- deep water section which exceeds the depth of 2000 meters sees the usage of combinations of chain with synthetic fiber or wire with synthetic fibe Six ways of moorings can be done. They are categorized as catenary, taut leg, semi-taut, spread, single point and dynamic positioning. (Rigzone.com, 2015) 4.2.3.1.1 Catenary systems. 56 Used predominantly in shallower regions. The line hangs freely and the shape is influenced by the movement of the ship and it constantly changes shape. The mooring line is stationed horizontally in the seafloor. For this aspect of the design the length of the line must be longer than the depth of the water. Complications arise because as the length of the line is longer the mass of the line increases and as the water gets deeper and deeper the payload of the FPSO is reduced dramatically as the line is dropped out. To curb this issue, synthetic rope is used since it has very little weight. The disadvantage is that in deeper regions this system is economically expensive. Polyester rope is used in this design. The rope is pre tensioned up to point when it becomes tensed. The rope is angled at a 30 to 45 degrees to the seafloor when connected to the anchor. Normally suction piles or vertically loaded anchors are used with this mooring system. The FPSO drifts with the current or wind and this motion tenses the line and sets the entire mooring up. (Rigzone.com, 2015) 4.2.3.1.2 Semi taut This system is a combination of taut line and catenary lines in one system and utilized in deeper regions. (Rigzone.com, 2015) 4.2.3.1.3 Spread mooring The most versatile mooring system this design utilizes many lines dropped over the stern and the bow of the vessel attached to the anchor in the seabed. The FPSO is stationed in a permanent location depending on the water and the weather aspects. Since the anchors are holding the vessel in place by giving a force on all sides the vessel does not move in any direction. Sway is also very minimal. This system ensures maximum stability and can be utilized in various combinations in spread pattern or a group and in any depth. (Rigzone.com, 2015) 57 4.2.3.1.4 Single point mooring
This system connects all mooring lines to a single point. The connection between subsea manifolds with the weathervaning tanks are done with an ability for the connection to rotate and move freely in all angles. This eliminates twist and breakage in turbulent waters. A buoy along with mooring and anchoring components are utilized with the product transfer. (Rigzone.com, 2015) 4.2.3.1.5 Dynamic positioning This system uses a computer signal that maintains the stability and the position of the vessel by controlling the thrusters and propellers accordingly. It starts, stops and differentiates the speed and force of the thrusters and propellers constantly adjusting the ship’s position. The most effective method of positioning and also the most expensive. (Rigzone.com, 2015) 4.2.3.2 Anchors The holding capability of the anchor defines the mooring’s strength. The holding capability is influenced by the digging depth and the soil characteristics of the field. There are three species of anchors: drag embedment, suction and vertical load anchor. (Rigzone.com, 2015) 4.2.3.2.1 Drag embedment anchor (DEA) 58 It’s the most used on FPSOs particularly in the Gulf of Mexico. The mechanism starts with the anchor being dragged on the seafloor. Once it reaches the targeted depth the friction it makes with the seabed soil creates an opposite reaction force and along with the mass of the soil it has pulled while being dragged stops and holds it in place. This works best for catenary moorings since it’s a horizontal process and this design cannot be used for any vertical applications. (Rigzone.com, 2015) 4.2.3.2.2 Suction piles Deepwater field FPSOs are reliant on the suction pile anchor. Tube shaped piles are forced into the seafloor. Then a pump takes out the water and this water is driven out from above the tube. This action of sucking the water and the sucked water moving upward and exiting above creates a sucking force that pushes the tube further into the seafloor. This design is efficient in sand, clay and mud type soils but inefficient in gravel since the gravel allows water motion among it. This system is extremely stable when in position since the resistance between the pile side and the soil holding it place makes it impenetrable by vertical or horizontal forces. (Rigzone.com, 2015) 4.2.3.2.3 Vertical load anchor
systems that new fabrication allows. The design modifications to the hull are assumed to be minimal, hence no changes are made to the hull framing, plate thickness or welds on the basis that the proposed duty will not exceed that of a tanker working on worldwide duty. Secondly, the main changes in duty are configured through the turret and the topsides process loads, which are both accounted for via supplementary stiffening 7.4.4 Deck Structure Advantages Lifeboats deploy away from smoke in process fire. 7.4.4.1 Accommodation The position of the accommodation facilities can both dictate the position of the turret and potentially reduce the cargo carrying capacity of the tanker. The basic premise that accommodation should be placed forward on a weathervaning vessel is a compromise between safety issues and construction/design issues: Disadvantages Higher motions at stern, crew discomfort factor. BOW Accommodation: /Advantages 1 Disadvantages
opex advantages over a controlled headingJimited rotation vessel, but the inherent requirements of a swivel joint for each flow path imposes practical limitations on the number of flow paths that can be provided for a fully weathervaning vessel. Whilst all turret systems are disconnectable, the term is only used for turrets having the facility for quick connection and quick disconnection (QCDC). Most of the turret systems that have been designed for fairly benign weather and shallow water are disconnected when a typhoon is expected. 15 to 18%. Integral bow turret (built within tanker bow) (fig. 7.29) Cantilevered bow turret (fig. 7.30) Previous Page 456 Chnprer 7 Figure 7.29 Internal bow turret (SBM-Imodco) Figure 7.30 Cantilevered bow turret (SBM-Imodco) A typical internal turret arrangement is shown in fig. 7.31. This is the SBM Top Mounted Internal Turret (TMIT) system. Similar systems can be supplied by any of the other turret contractors. This turret design has been employed on several production FPSOs, e.g. Chevron’s Alba FSU, Shell’s CNS FPSO and Curlew FPSO. The turret presents benefits from previous applications, and limits the number of critical mechanical components, such as the bearings, by using a single roller bearing located above the vessel main deck. Floating Offshore Platform Design Figure 7.31 Top Mounted Internal Turret TMIT (SBM-Imodco) The system comprises a chain-table structure anchored to the seabed anchor points via an array of nine (9) catenary mooring lines. The chain-table structure is attached to a turret cylinder structure which is suspended from a heavy duty roller bearing located above the vessel’s main deck. The bearing is supported on the vessel’s side and integrated into the forward part of the FPSO vessel’s hull. The turret cylinder is mounted to the earth-fixed side of the main bearing. The turret cylinder houses the riser ‘I- tubes’ and supports the manifold deck (where the risers terminate), the manifold structure, the swivel deck together with the swivel stack and all the earth-fixed part of the rigid piping. The roller bearing allows the turret to freely weathervane so that the tanker can take up the position of the least resistance to the prevailing weather, at all times. Chapter 7 458 Fluid transfer from the seabed flowlines is achieved by flexible risers which are suspended from, and routed through the turret mooring to the interface with rigid piping at the manifold deck level. After manifolding the product is routed through toroidal swivels to the vessel’s main deck piping and process facilities. Lift gas is compressed on board the FPSO and transferred by a high-pressure swivel to the gas lift riser. Inject water is pressurized on board and transferred by a high-pressure water injection swivel to the water injection riser. The turret’s manifold area is protected from possible wave action (green water) by a wave breaker structure mounted on the vessel. A pedestal crane serves the complete turret to handle swivels and perform other maintenance functions. A stair tower is integrated with the crane superstructure to provide access to the swivel stack area. A hydraulic power unit provides power via the swivel to activate the different valves in the manifold. Swivels are also provided for well control fluid and signals. Electric power is provided via a distribution system serving an exterior floodlighting and an interior accessway lighting of the complete turret. The turret would be classified as the hazardous area, consisting of Zones 1 and 2. The turret cylinder would be monitored for the presence of gas. Fire and gas detectors would be located in the manifold swivel area. All signals would be transmitted to the FPSO’s central fire and gas control panel. During inspection, temporary ventilation inside its annulus and cylinder would be provided by air fans. The manifold area and the swivel stack are situated above the vessel’s main deck and are thus freely (naturally) ventilated. Fire protection inside the turret cylinder
transferring the messenger line, chafe chain, main hawser and offloading hose from the FPSO to the shuttle. Alternatively, the hawser and offloading hose can be deployed prior to arrival of the shuttle tanker such that the shuttle can collect the messenger line and then haul in the hawser with the hose already attached to the chafe chain via a connecting wire. The offloading hose is made-up of 10 meter lengths, joined so that any length can be easy replaced. 464 Chapter 7 Figure 7.32 Stern offloading reel (Aker Kvaerner) The inboard end of the hawser is attached to a bracket that forms an integral part of the drum, which is mounted on the aft deck next to the hose reel. This drum stores the main hawser in one layer, the chafe chain and the messenger line. Each machine is hydraulically driven with the hydraulic motors powered by a power pack, located in a non-hazardous area. The drives for the hose reel and hawser storage drum are controlled from a panel mounted between the two units, as is the spooling mechanism for the hawser storage. Safety features in the export system include a breakaway coupling in the hose string that is designed to close automatically should hose tensions become excessive. A self closing coupling at the outboard end of the hose also closes when disconnected from the shuttle tanker. Load sensing devices are incorporated to measure the tension in the hose and hawser line, and are continuously monitored during the offloading operation, with signals being fed into alarm and cargo offloading pump shut-down systems.
The external turret mooring system includes a turret system that is located at the extreme end of an outrigger structure attached to the bow of the vessel. This turret contains one large-diameter 3-race roller main bearing that transfers both the vertical and the horizontal loads from the riser and mooring system to the outrigger structure. In addition, it transfers the own weight of the turret and the turntables above the main bearing to the outrigger. The turntables include the process facilities for commingling fluids from the risers using manifolds, as well as pigging facilities and/or chemical injection facilities to assure the flow in the risers. The swivel stack is located at the highest deck of these turntables and transfers fluid and electrical power to the turret access structure located on the outrigger. This access structure also provides support access to the different turntable decks. The external turret including (a part of) the outrigger can be installed as one integrated structure on the vessel bow, minimising the scope of work for the integration of the turret into the vessel. Furthermore this integration work can be executed while the vessel is afloat. Typically the cantilever type outrigger structure is integrated above the main deck of the vessel. However, depending on the departure angle of the mooring lines and on the size of the outrigger structure, part of the bow might need to be removed to avoid clashes between the vessel and the mooring lines. Optionally, risers are available that allow for fast disconnection from the turret. This disconnectable turret uses a buoy to keep the risers afloat when disconnected. Typically the disconnectable option is required when the vessel operates on dynamically positioned (DP) station keeping. Disconnection within minutes is required to avoid damage to the risers during failures in the DP system causing drift-off or drive-off conditions. The internal turret mooring system includes a turret system that is integrated into the hull structure at the bow of the vessel. The internal turret is a slender structure that is connected to the vessel structure via a large-diameter 3-race roller main bearing at the top and via a large-diameter sliding bearing at the bottom. The slender turret shaft ensures that the horizontal loads from the risers and mooring lines are transferred via the sliding bearing to the vessel, while the remaining forces from the turret and the vertical loads from the risers and mooring lines are transferred via the 3-race roller bearing. The supports of the bearings are integrated into the turret casing, which is part of the modified vessel hull structure. Typically the turret casing is a cylindrical structure that is integrated between the bottom and the deck of the vessel and transfers the turret loads via the vessel web frames to the vessel hull structures. The turntable decks are positioned on top of the 3-race roller bearing. The turntables include the process facilities for commingling fluids from the risers using manifolds, as well as pigging facilities and/or chemical injection facilities to assure the flow in the risers. In addition, the turntables provide space for subsea control facilities, to enable safe operation of the subsea manifolds and well heads. The highest deck level of the turntables provides space for the swivel stack, which transfers fluid and electrical power to the turret access structure that is located on the vessel main deck. This access structure also provides support access to the different turntable decks. CONCLUSION All the studies done has proven that FPSO is the future for oil and gas developments. The various advantage of lower cost of manufacturing, the ease of travel and relocation and lower cost of abandonment of the platform further pushes major oil companies to see FPSO as the alternative. The lowering fuel prices which pushes these major companies to cut cost and downsize due to imbalanced political and economic situations added with the fossil fuel reservoirs that are being depleted to excessive usage pushes explorations to new and untouched rural areas of the globe. The journey to new oil fields would mean a platform that is versatile and flexible as well as reliant and capable to output a high production rate to supply the demand of the users. The FPSO is the only such platform with the said advantages and features. No other platform can be even moved and stationed without taking up as much as twice the time and the cost. The further fact that FPSOs can be manufactures from a used cargo ship and after being used to the maximum the topsides can be converted into another ship also gives a much needed culling in manufacturing costs. The factor that permits the platform 69 to be re used in more than one particular oil field also increases the dependability on FPSO. The capital investment is reimbursed and the platform continues to provide revenue to the owners in its years of service. This is a long term investment and continues to provide advantages for the company. FPSOs are also stable and safer compared to the other platforms and can work in hazardous and treacherous waters. Areas of the globe where it is impossible to construct and build any kind of
2.1.3 Turret Type The turret is the part of the FPSO that anchors the mooring lines and riser to the vessel to maintain the ship position. The internal turret and external turret are the two main types used on FPSOs. The external turret is located outside the ship hull and is generally a cheaper and faster design that allows it to weathervane 360 degrees. This allows for the vessel to operate in moderate to extreme sea conditions. This system can also be mounted at either the bow or the stern, depending on the overall design of the FPSO. The internal system can accommodate more risers and can also be designed to disconnect in the case of severe weather. This type of turret is typically found in the purpose build FPSOs because the cost of installation is too high in the tanker conversions. While the chain table structure is located above the water surface for the external system, it is typically found submerged in the internal system. Figure 3. Internal and external turret designs 2.1.4 Mooring Arrangement FPSOs are primarily moored in two arrangements: either the single point mooring system or the spread mooring system. The Spread mooring system involves multiple anchor lines extending from the bow and stern of the vessel and anchor it to the sea floor. This system is used in all water depths and mild to moderate environments. The spread mooring is very dependent on the weather system because it is not allowed to weathervane. Severe wind and waves can cause excessive loads on the lines, making it not a suitable choice for harsh conditions. The Single Point mooring system (also known as Turret mooring system) uses the turrets to anchor the lines to the hull. This design allows for minimal ship motions, which in turn eases the offloading process and increases crew comfort. 3 The adaptation to wave and wind conditions through the 360 degree weathervaning allows this system to be used in harsh conditions. In regions where typhoons or ice are common the system can be disconnected and the vessel moved until conditions improve. The process is very quick and easy which is necessary in the case of a fast approaching storm. There is also a process used in ultra-deep water called Dynamic Positioning (DP). This is used when the water is extremely deep and mooring is not a realistic option to fix the vessel’s position. The computer receives information from sensors and maintains the position by using the vessel’s propellers and thrusters. This provides a less costly method for deep water fields. Figure 4. The Mooring System in the Connected and Disconnected State
Figure 5. Schematic of Dynamic Positioning System 4 2.1.5 Vessel Size and Variety The size of the hull for FPSO depends mainly on whether it was a tanker conversion or purpose built vessel. A double hull is a method where the ship has two layers of water tight hull surface while the single only has one. Due to tanker requirements most of the conversions are of the single hull variety while the new builds are double hull. The double hull decreases the stability of the vessel, but is also is less likely to experience an oil spill. The vessel size ranges from the largest FPSO, the Kizomba, with dimensions measuring 935 feet long, 207 feet wide, and 105 feet high to the smallest, the Crystal Ocean, only 450 feet long. 2.1.6 Product Type Another important factor to consider is the product that will be collected and processed from the subsea wells. There are three main types of processing units: oil, liquid petroleum gas (LPG), and liquid natural gas (LNG). The oil unit separates oil, gas and water from the well and passes along the oil for the production phase while returning treated water back to the reservoir. The water is returned to maintain the pressure in the well. The LPG FPSO is complete with onboard liquid petroleum gas processing and exporting facilities. The LNG FPSO is similar to the oil FPSO except it separates the natural gas (primarily methane and ethane) to produce LNG to store and then offload. These three types will be discussed more in depth in the applications portion of the paper. 2.1.7 Environment Of all the topics, the environment is the most influential on the overall design of the FPSO. These vessels operate all over the world in the North Sea, Gulf of Mexico, off the African coast, and various other locations. No two sea conditions are exactly the same. The weather conditions, wave height, wind strength, water depth, and well availability will all vary with each location and even within each location. Vessels that operate in the North Sea must be very apt to the rough conditions present there, as opposed to the Gulf of Mexico where the significant wave height is considerably lower. This requires the FPSO to be very adaptable to all conditions and to account for the harshest environments. 2.2 FPSO Topsides The topside unit of the FPSO is where the processing equipment is located. Once the product is brought up through the riser, it undergoes a series of processes on the top of the vessel to prepare the product to be offloaded. Because the topside unit is so complex, it is often contracted to other companies to create a custom unit, or module, for the specific vessel’s needs. Generally, there are four categories of modules; separation, compression, processing, and generation, and then a massive utilities system as well. The contracting for each module is very competitive and many companies from all over the world will partake in the final build. The modules are built by each of the winning bidders and then all brought to the shipyard where the hull is held. They are then installed and connected to each other by the expansive utilities system. 2.2.1 Separation The separation modules are normally generically built and serve a large range of operational requirements. The main purpose is to separate the slurry into oil, gas, and sand. These are three part separators and are 5
jacks that are installed on the FPSO. The tugs are released when a sufficient number of lines are connected. The mooring line hook-up operation continues until all the lines are connected and tensioned All the studies done has proven that FPSO is the future for oil and gas developments. The various advantage of lower cost of manufacturing, the ease of travel and relocation and lower cost of abandonment of the platform further pushes major oil companies to see FPSO as the alternative. The lowering fuel prices which pushes these major companies to cut cost and downsize due to imbalanced political and economic situations added with the fossil fuel reservoirs that are being depleted to excessive usage pushes explorations to new and untouched rural areas of the globe. The journey to new oil fields would mean a platform that is versatile and flexible as well as reliant and capable to output a high production rate to supply the demand of the users. The FPSO is the only such platform with the said advantages and features. No other platform can be even moved and stationed without taking up as much as twice the time and the cost. The further fact that FPSOs can be manufactures from a used cargo ship and after being used to the maximum the topsides can be converted into another ship also gives a much needed culling in manufacturing costs. The factor that permits the platform 69 to be re used in more than one particular oil field also increases the dependability on FPSO. The capital investment is reimbursed and the platform continues to provide revenue to the owners in its years of service. This is a long term investment and continues to provide advantages for the company. FPSOs are also stable and safer compared to the other platforms and can work in hazardous and treacherous waters. Areas of the globe where it is impossible to construct and build any kind of platforms due to the geographical reasons and lack of facilities can utilize a FPSO because the platform is built elsewhere and moved to the field and moored. This reduces the risks involved and in terms of safety of the workers involved is guarded since there is very little underwater and subsea maintenance and infrastructure operation done when it involves this platform. FPSOs is the future of the oil and gas industry and various new technological advancements must be integrated into this platform to further increase its efficiency to benefit the energy market globally.