
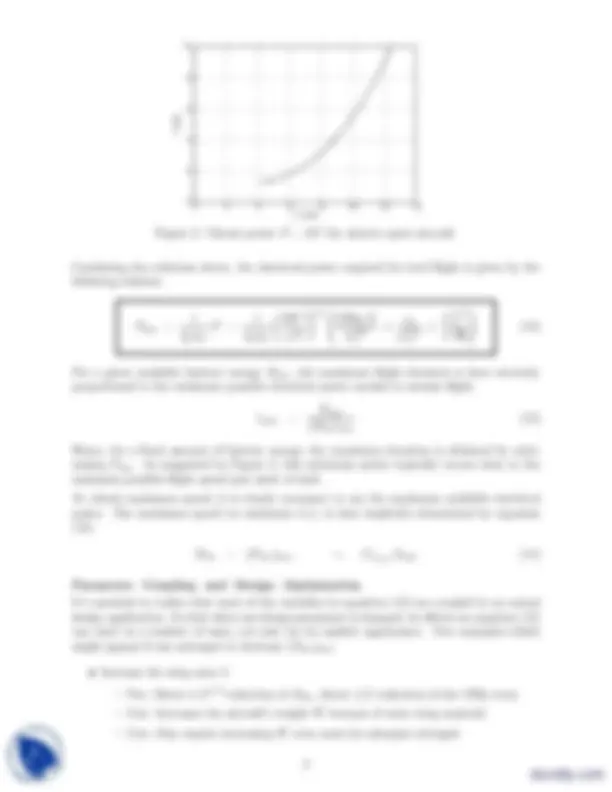
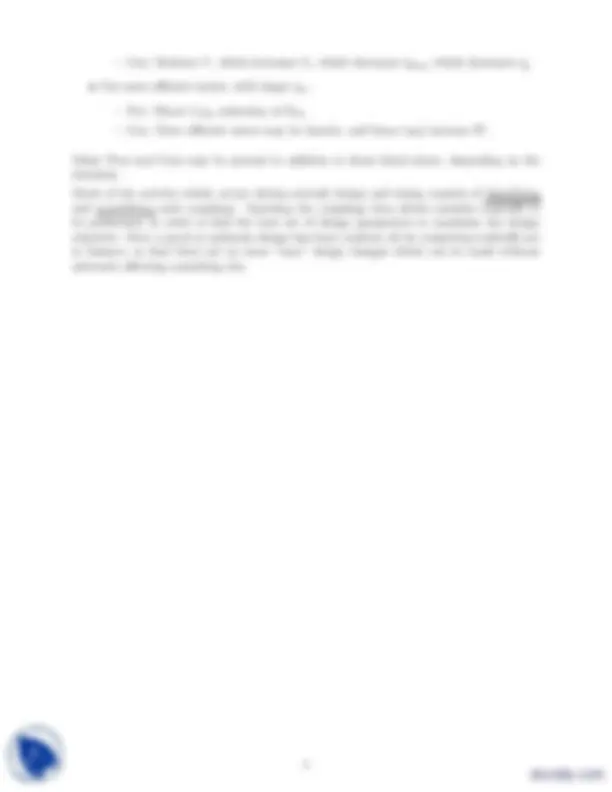
Study with the several resources on Docsity
Earn points by helping other students or get them with a premium plan
Prepare for your exams
Study with the several resources on Docsity
Earn points to download
Earn points by helping other students or get them with a premium plan
Community
Ask the community for help and clear up your study doubts
Discover the best universities in your country according to Docsity users
Free resources
Download our free guides on studying techniques, anxiety management strategies, and thesis advice from Docsity tutors
Lecture notes on the topic of flight power relations. It covers the generation of thrust during flight, the drag power, and the contribution of different components to the total drag. The document also discusses the relationship between flight power and duration in an electric aircraft, and the importance of parameter coupling and design optimization.
Typology: Exercises
1 / 4
This page cannot be seen from the preview
Don't miss anything!
( )
Nomenclature
c
c
D aircraft drag L aircraft lift W aircraft weight T propeller thrust V flight speed S reference area (wing area) b wing span AR wing aspect ratio L lift coefficient D drag coefficient CDA 0 drag area of non-wing components ā wing-airfoil profile lift coefficient d wing-airfoil profile drag coefficient Ļ air density t
Ī·
Ī·
Ī·
P thrust power ( ā” T V ) shaft motor shaft power elec electric power (Volts^ Ć^ Amps) m electric motor efficiency p overall propeller efficiency ideal ideal propeller efficiency R propeller radius c thrust coefficient m motor rotation rate Ī© propeller rotation rate Ī» propeller advance ratio Re chord Reynolds number elec electrical (battery) energy max maximum flight duration
Thrust Power Generation of thrust during flight requires the expenditure of power. In steady level flight, T = D, and hence the thrust power is equal to the drag power.
P ā” T V = DV (steady level flight) (1)
In steady level flight we also have W = L, which gives the velocity in terms of other relevant parameters.
1 W = L = ĻV 2 S CL (2) 2 ( ) 1 / 2 2 W V = (3) Ļ S CL
The drag power can then be given as follows. 1 DV = ĻV 3 S CD (4) 2 2 W 3 C 1 / 2 DV = D (5) Ļ S (^) C^3 /^2 L We will assume that the typical wing airfoil sees the same local cā as the overall aircraft CL, so we can employ 2D airfoil cd(cā, Re) data.
cā = CL (6)
The aircraft drag coefficient can now be broken down into three basic components.
1
The last term is the induced drag, which directly depends on the aspect ratio of the wing. This is defined in terms of the wing span and area.
b^2 AR = (8) S
Figure 1 shows the three CD components versus CL for a typical 1.5 m span light RC sport aircraft.
CL
1.4 CDAo/S^ cd^ CDi^ CD
0.0 0.00 0.02 0.04 0.06 0.08 0.10 0.12 0.14 0. CD Figure 1: Drag polar and drag polar components for electric sport aircraft. AR = 9. 0
For a typical operating point at CL = 1.0 (low speed) and CL = 0.3 (high speed), indicated by the symbols in Figure 1, the three components contribute roughly the following percentages to the total drag:
CL
cd
37 % 52 %
L/Ļ^ AR
45 % 9 %
The corresponding flight power is shown in Figure 2.
Flight Power and Duration
In an electric aircraft, the flight power is provided by an electric motor, driving a propeller with some efficiency Ī·p.
P = Ī·p Pshaft (9)
The motor itself has efficiency Ī·m, and is supplied by a battery which outputs electrical power Pelec.
Pshaft = Ī·m Pelec (10) P = Ī·p Ī·m Pelec (11)
Other Pros and Cons may be present in addition to those listed above, depending on the situation.
Much of the activity which occurs during aircraft design and sizing consists of identifying and quantifying such couplings. Knowing the couplings then allows suitable tradeoffs to be performed, in order to find the best set of design parameters to maximize the design objective. Once a good or optimum design has been reached, all its competing tradeoffs are in balance, so that there are no more āeasyā design changes which can be made without adversely affecting something else.