
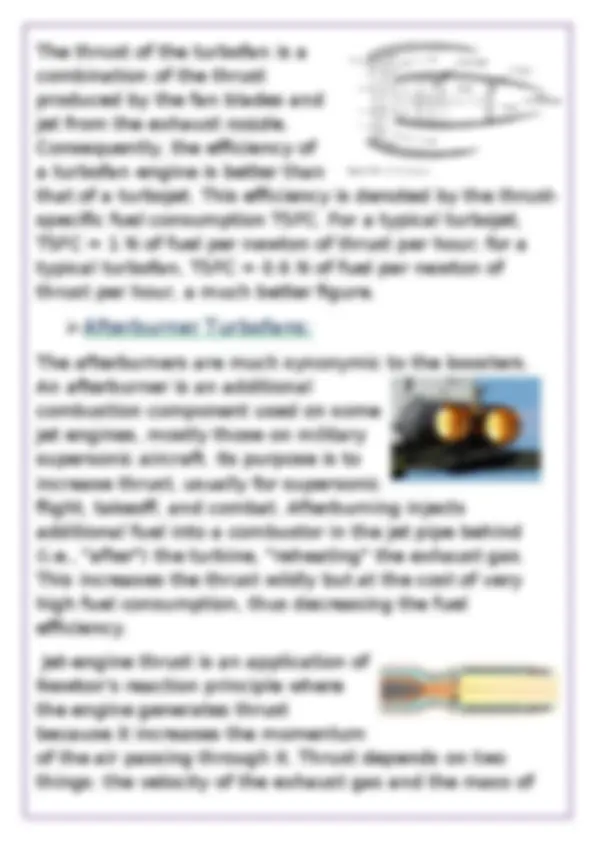
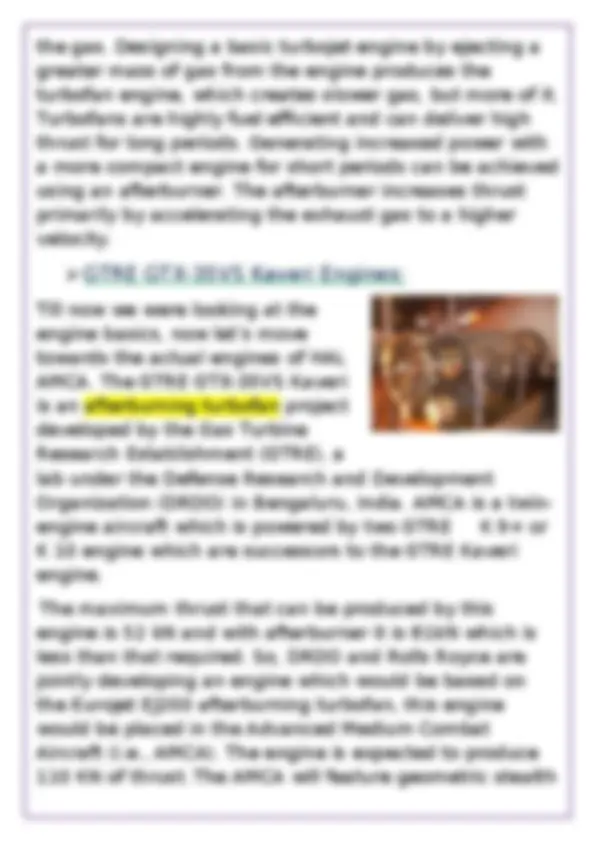
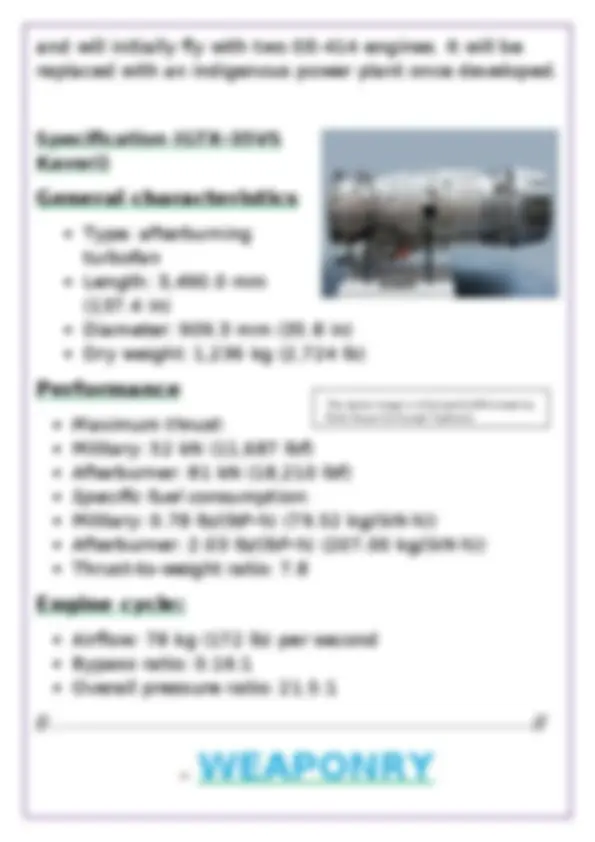
Study with the several resources on Docsity
Earn points by helping other students or get them with a premium plan
Prepare for your exams
Study with the several resources on Docsity
Earn points to download
Earn points by helping other students or get them with a premium plan
Community
Ask the community for help and clear up your study doubts
Discover the best universities in your country according to Docsity users
Free resources
Download our free guides on studying techniques, anxiety management strategies, and thesis advice from Docsity tutors
Explore the world of jet engines powering HAL AMCA with a focus on turbofans and afterburners. Learn about their functions, differences, and advantages. Discover the role of bypass ratios, specific fuel consumption, and thrust-to-weight ratio in turbofan engines. Understand the concept of afterburners and their impact on fuel efficiency and thrust.
What you will learn
Typology: Assignments
1 / 7
This page cannot be seen from the preview
Don't miss anything!
The turbofan or fanjet is a type of jet engine that is widely used in aircraft propulsion. The turbo portion refers to a gas turbine engine which achieves mechanical energy from combustion, and the fan, a ducted fan that uses the mechanical energy from the gas turbine to accelerate air rearwards. Shown beside is the animation of how the engine functions. Thus, whereas all the air taken in by a turbojet passes through the turbine (through the combustion chamber), in a turbofan some of that air bypasses the turbine. A turbofan thus can be thought of as a turbojet being used to drive a ducted fan, with both of these contributing to the thrust. Here turbofans are not to be confused with turbojets they are different. On one hand where the turbojets are used for generating very high speeds and the propellers are used for low speeds, the so-called turbofans are used for generating speeds in between them. The bypass ratio (BPR) of a turbofan engine is the ratio between the mass flow rate of the bypass stream to the
mass flow rate entering the core. This BPR is kept high in order to decrease the SFC i.e., specific fuel consumption rate. A higher BPR provides a lower fuel consumption for the same thrust. Turbofans retain an efficiency edge over pure jets at low supersonic speeds up to roughly Mach 1.6 (2,000 km/h).
the gas. Designing a basic turbojet engine by ejecting a greater mass of gas from the engine produces the turbofan engine, which creates slower gas, but more of it. Turbofans are highly fuel efficient and can deliver high thrust for long periods. Generating increased power with a more compact engine for short periods can be achieved using an afterburner. The afterburner increases thrust primarily by accelerating the exhaust gas to a higher velocity.
Till now we were looking at the engine basics, now let’s move towards the actual engines of HAL AMCA. The GTRE GTX-35VS Kaveri is an afterburning turbofan project developed by the Gas Turbine Research Establishment (GTRE), a lab under the Defense Research and Development Organization (DRDO) in Bengaluru, India. AMCA is a twin- engine aircraft which is powered by two GTRE K 9+ or K 10 engine which are successors to the GTRE Kaveri engine. The maximum thrust that can be produced by this engine is 52 kN and with afterburner it is 81kN which is less than that required. So, DRDO and Rolls Royce are jointly developing an engine which would be based on the Eurojet EJ200 afterburning turbofan, this engine would be placed in the Advanced Medium Combat Aircraft (i.e., AMCA). The engine is expected to produce 110 KN of thrust. The AMCA will feature geometric stealth
and will initially fly with two GE-414 engines. It will be replaced with an indigenous power plant once developed. Specification (GTX-35VS Kaveri)
Type: afterburning turbofan Length: 3,490.0 mm (137.4 in) Diameter: 909.3 mm (35.8 in) Dry weight: 1,236 kg (2,724 lb)
Maximum thrust : Military: 52 kN (11,687 lbf) Afterburner: 81 kN (18,210 lbf) Specific fuel consumption : Military: 0.78 lb/(lbf•h) (79.52 kg/(kN·h)) Afterburner: 2.03 lb/(lbf•h) (207.00 kg/(kN·h)) Thrust-to-weight ratio: 7.
Airflow: 78 kg (172 lb) per second Bypass ratio: 0.16: Overall pressure ratio: 21.5: //………………………………………………………………………//
The above image is of Eurojet EJ200 (made by Rolls Royce for Eurojet Typhoon)
gondhalekar.sc20b165@ug.iist. ac.in
REFERENCES: https://en.wikipedia.org/wiki/HAL_AMCA https://en.wikipedia.org/wiki/GTRE_GTX-35VS_Kaveri https://en.wikipedia.org/wiki/Turbofan https://en.wikipedia.org/wiki/Afterburner Introduction to flight by John D. Anderson. Made by: NAME: JAYESH S GONDHALEKAR BRANCH: ENGINEERING PHYSICS (DD) MAIL: ID: SC20B NAME: JAYESH S GONDHALEKAR BRANCH: ENGINEERING PHYSICS (DD) MAIL: ID: SC20B gondhalekar.sc20b165@ug.iist. ac.in