
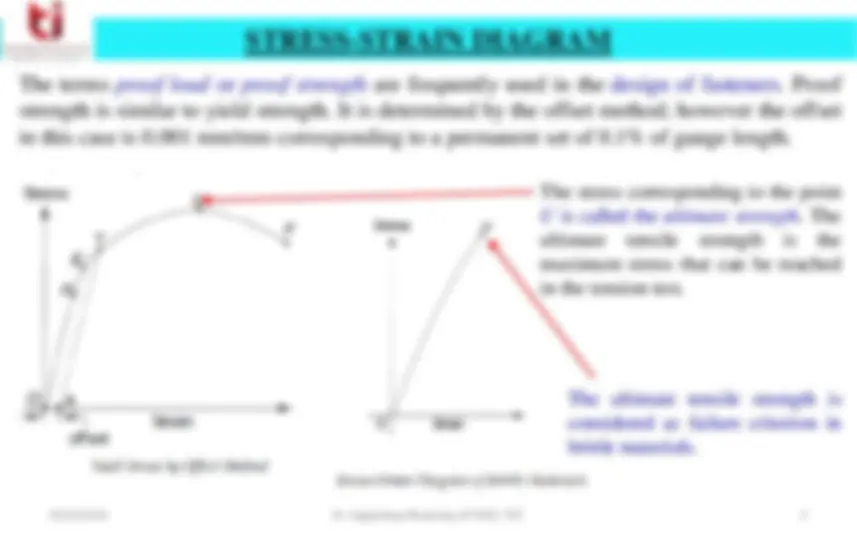
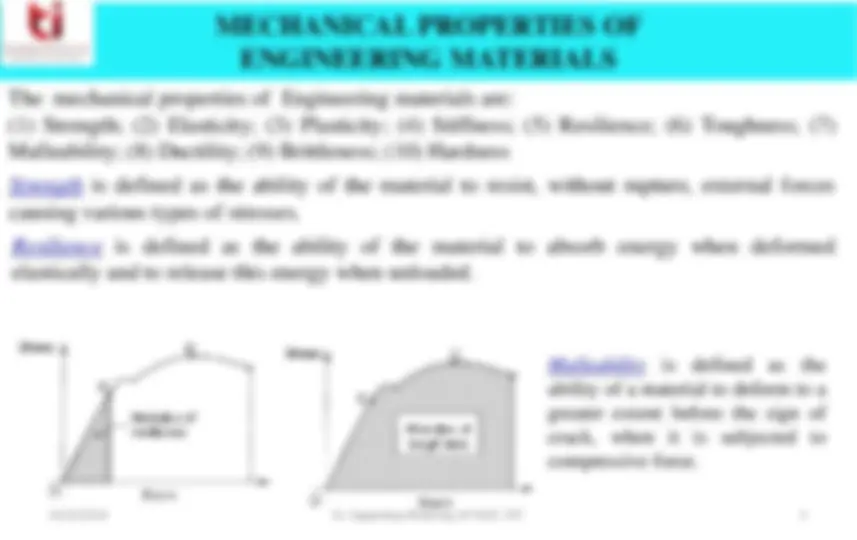
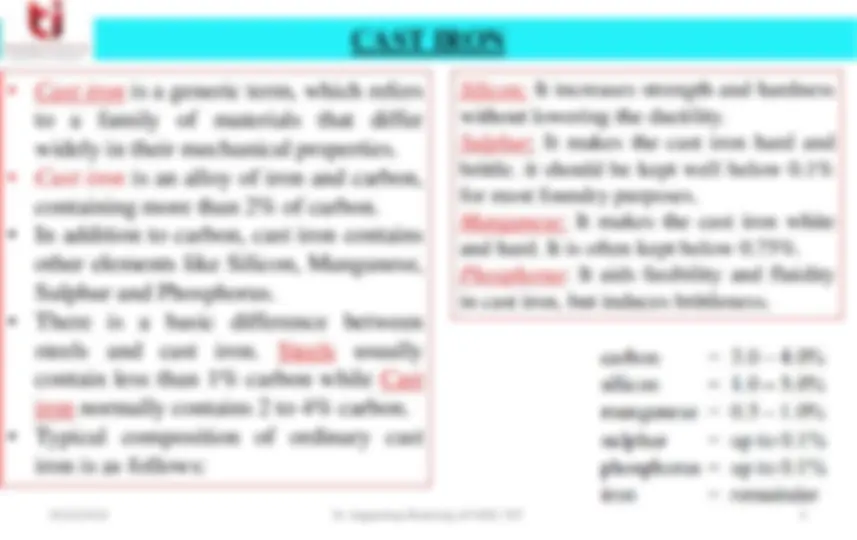
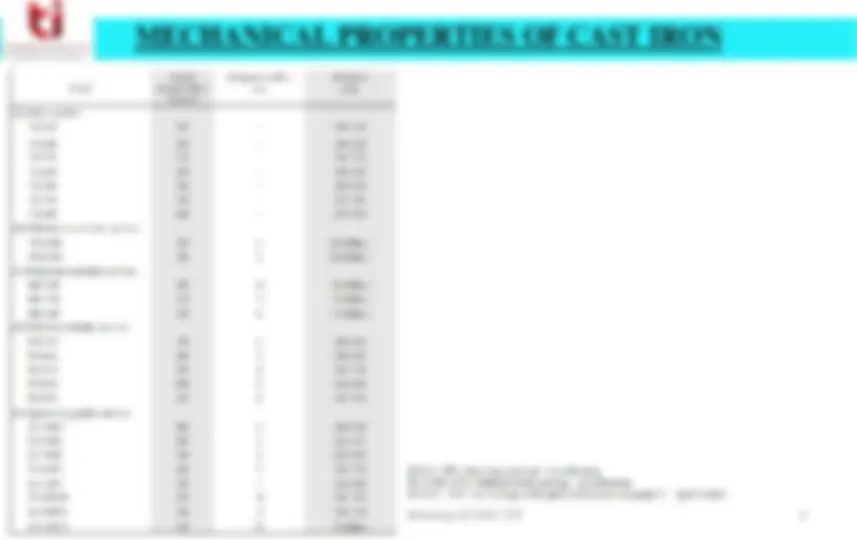
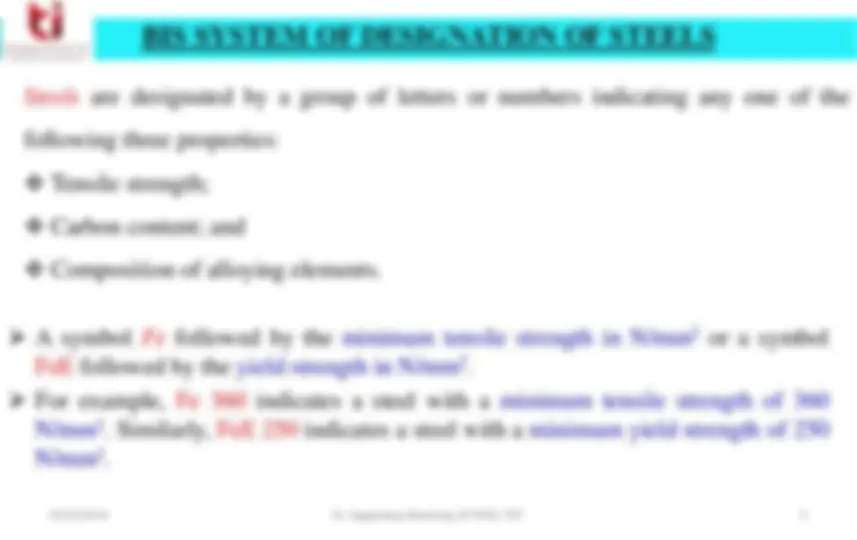
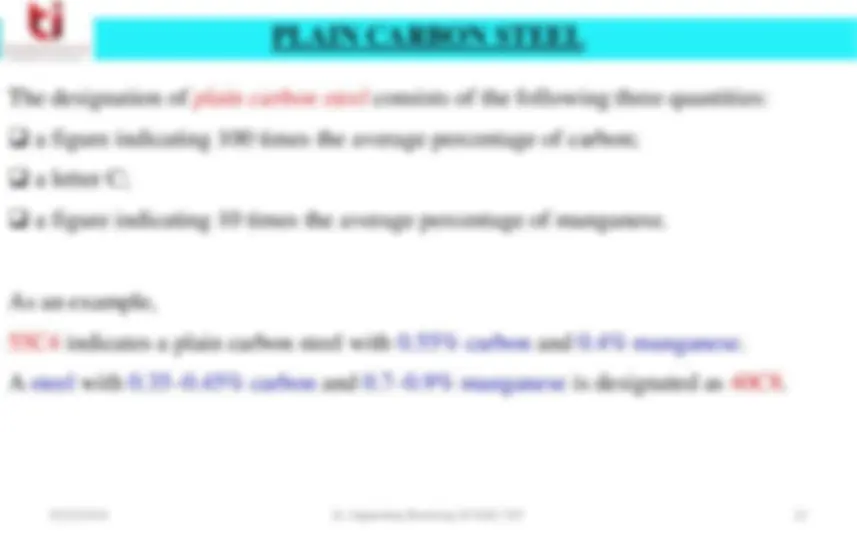
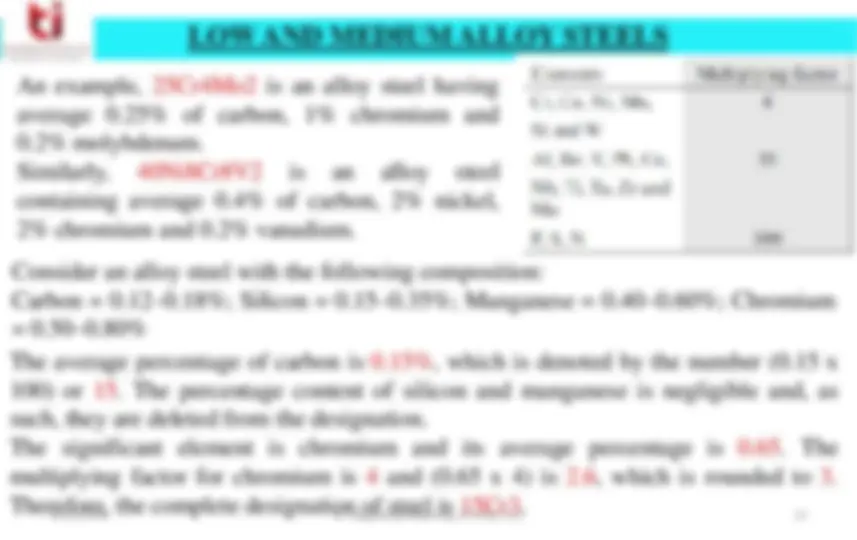
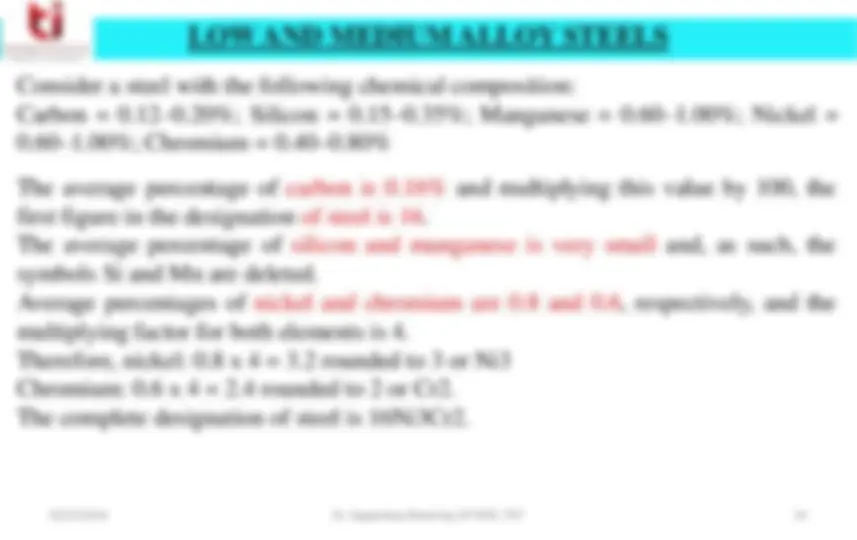
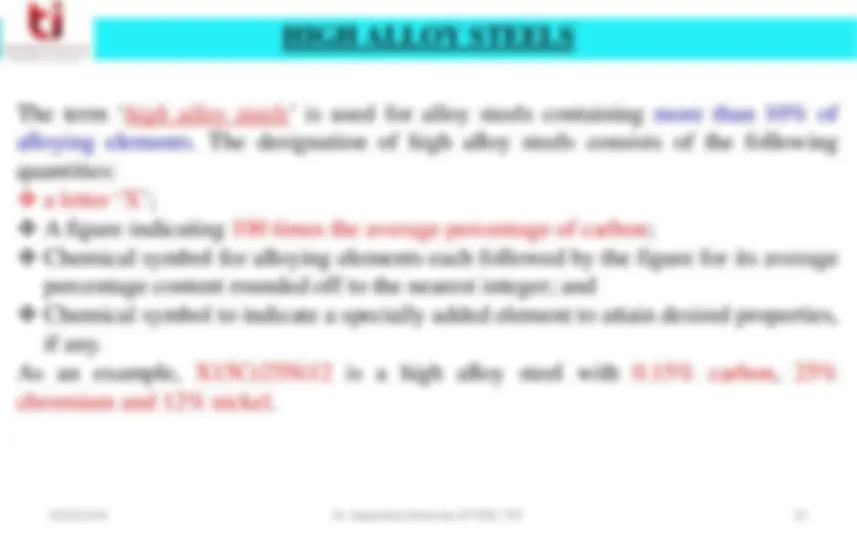
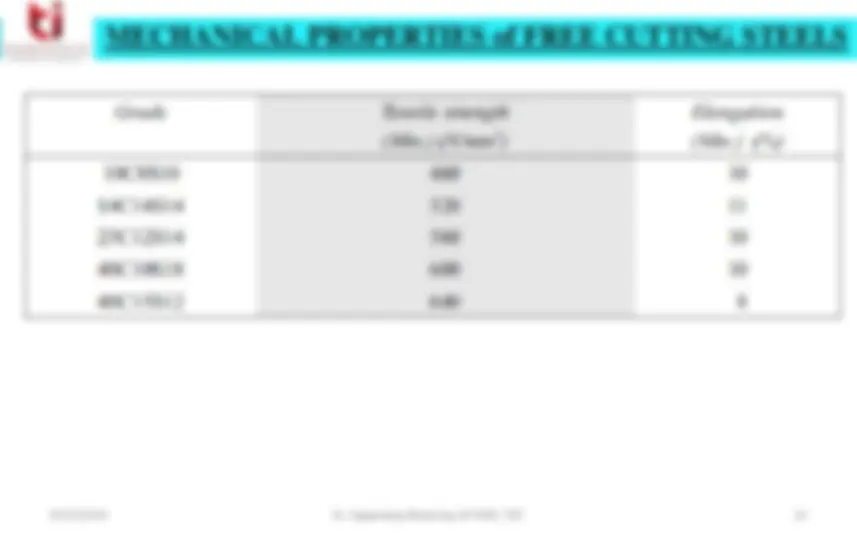
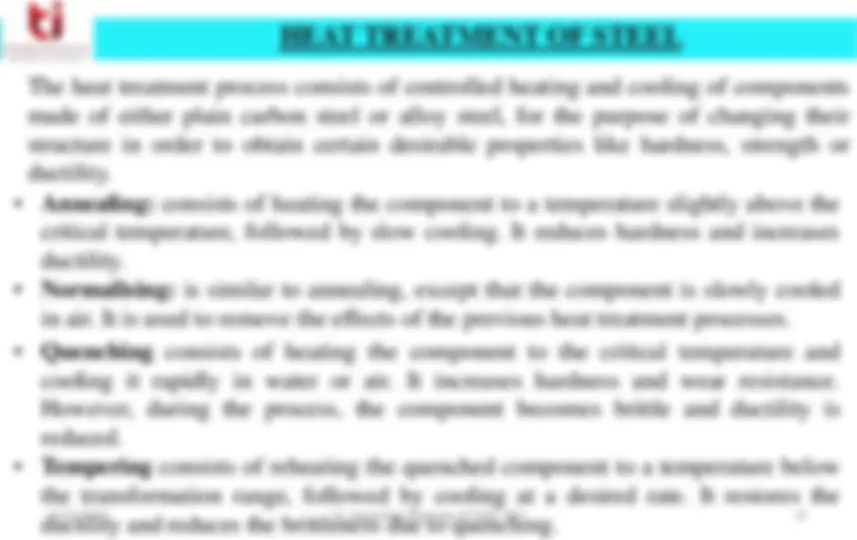
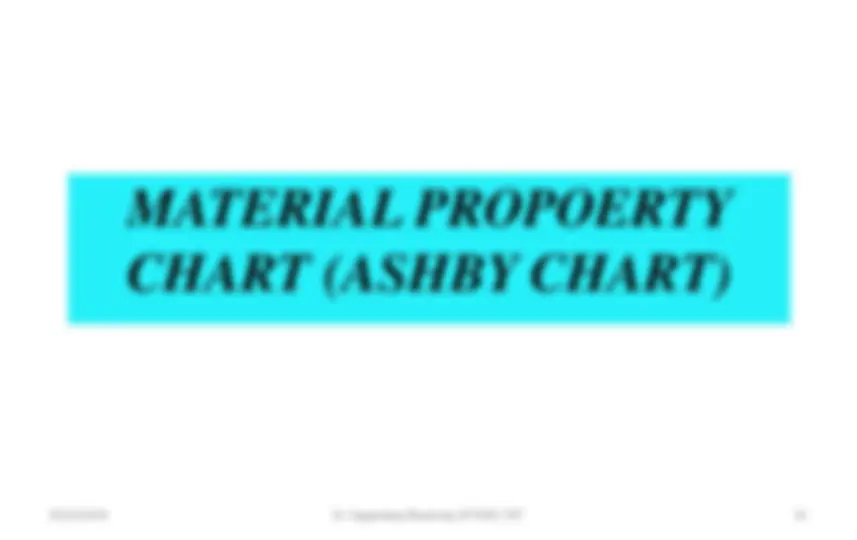
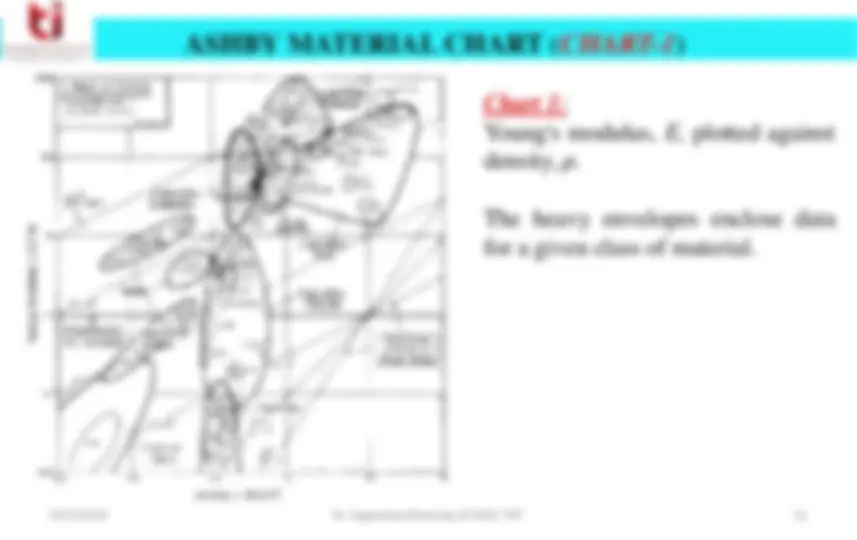
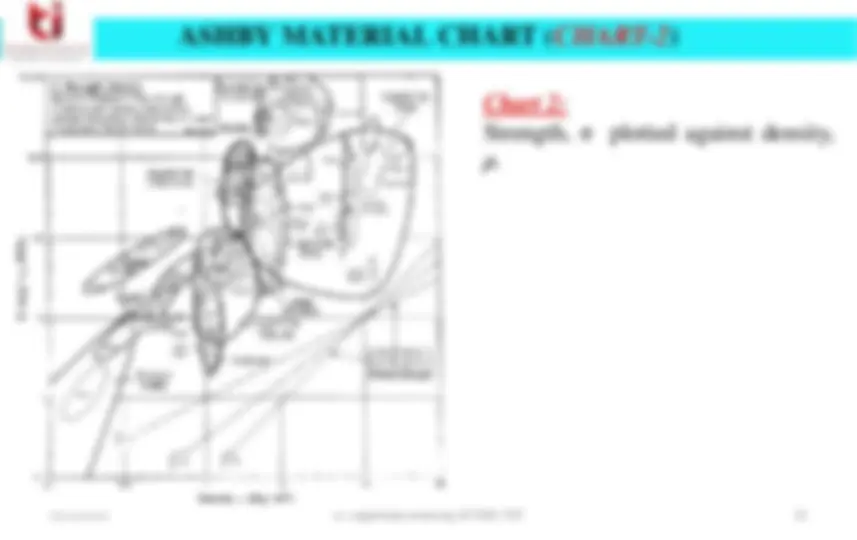
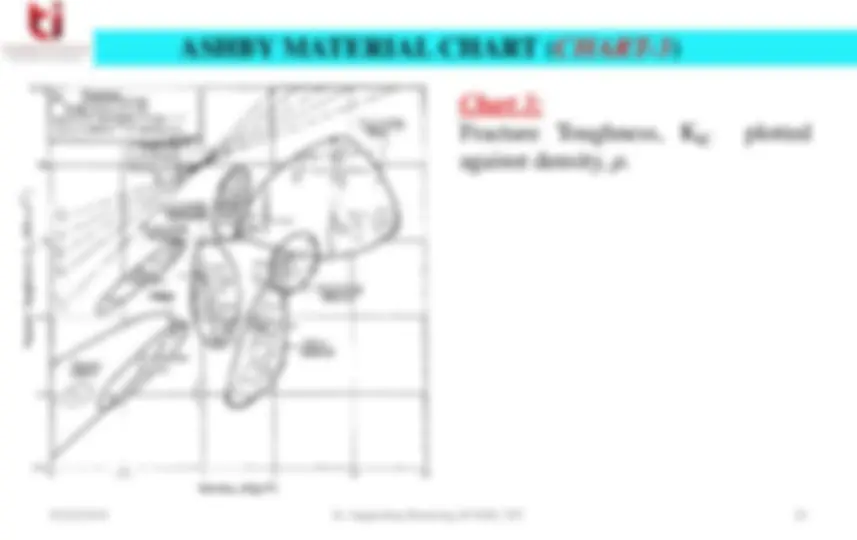
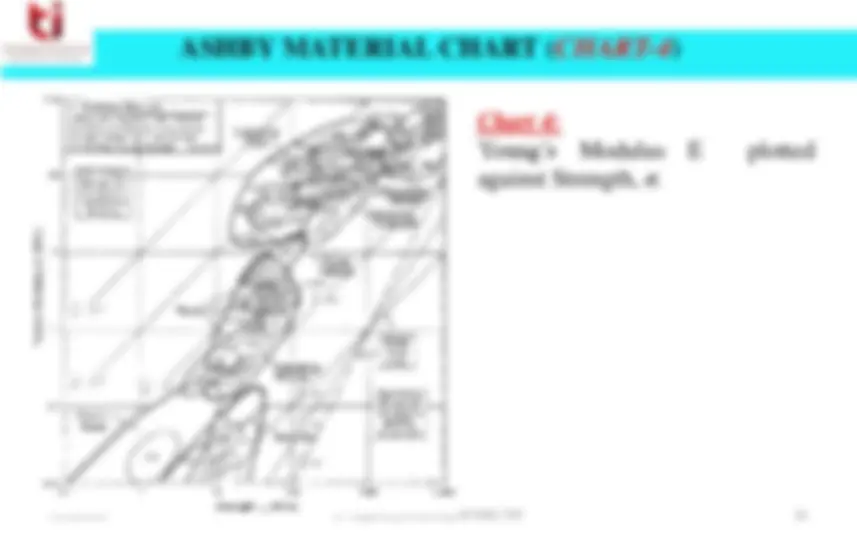
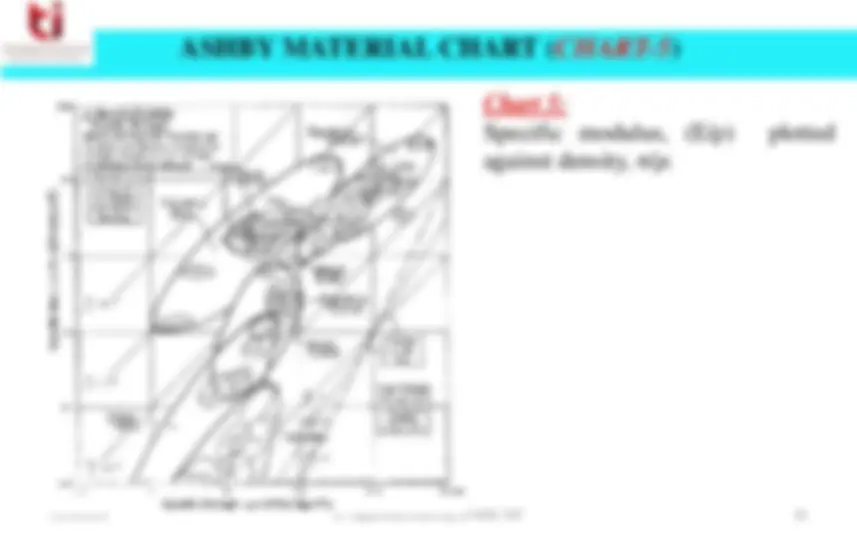
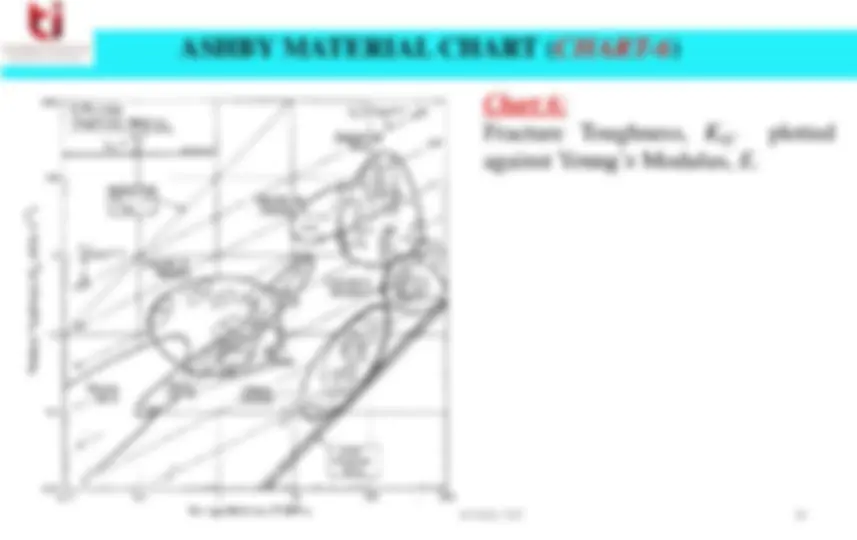
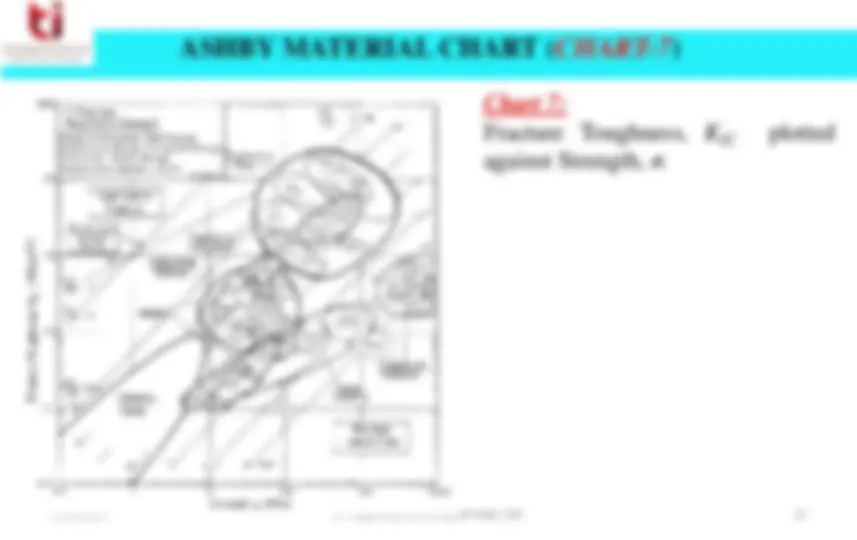
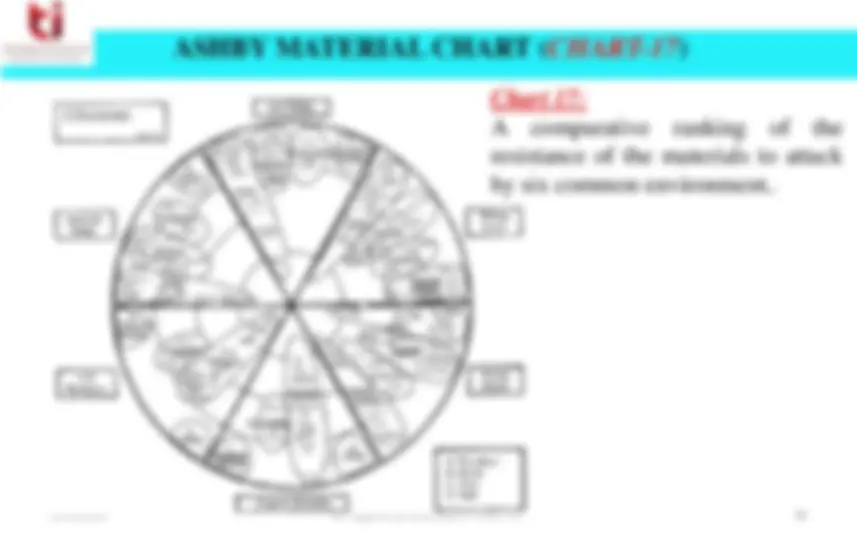
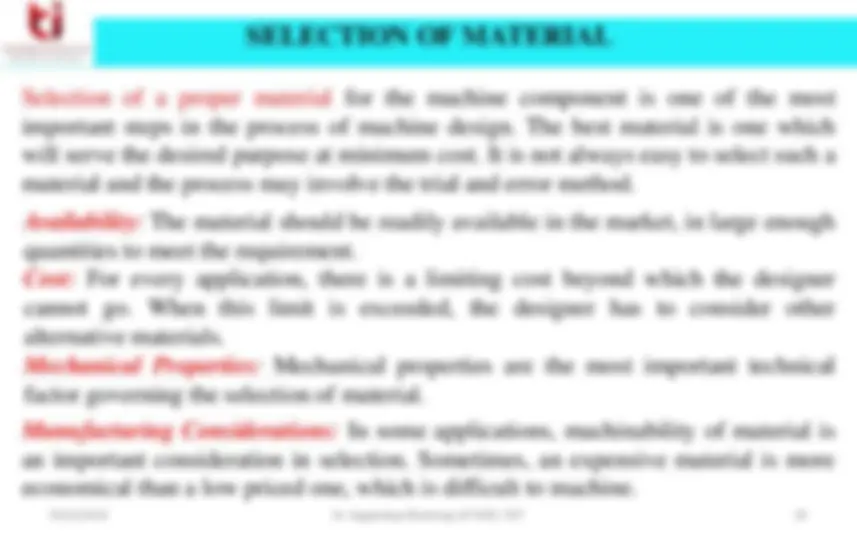
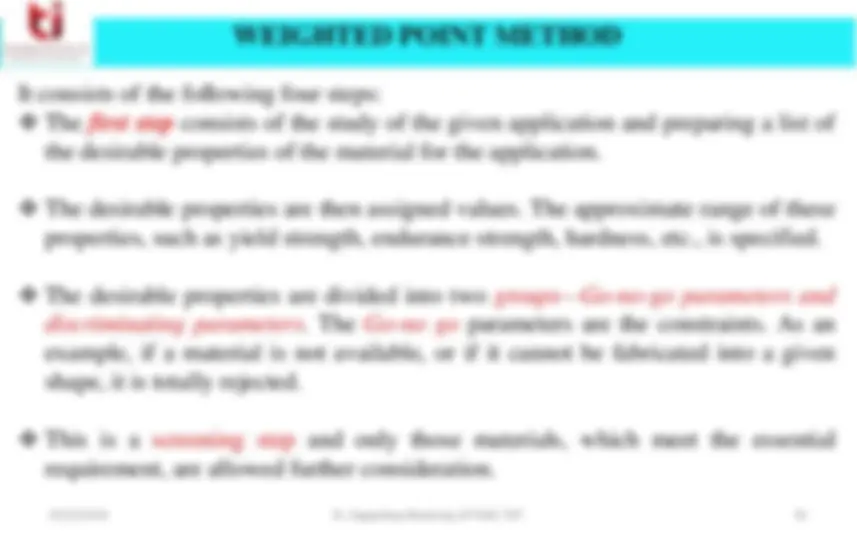
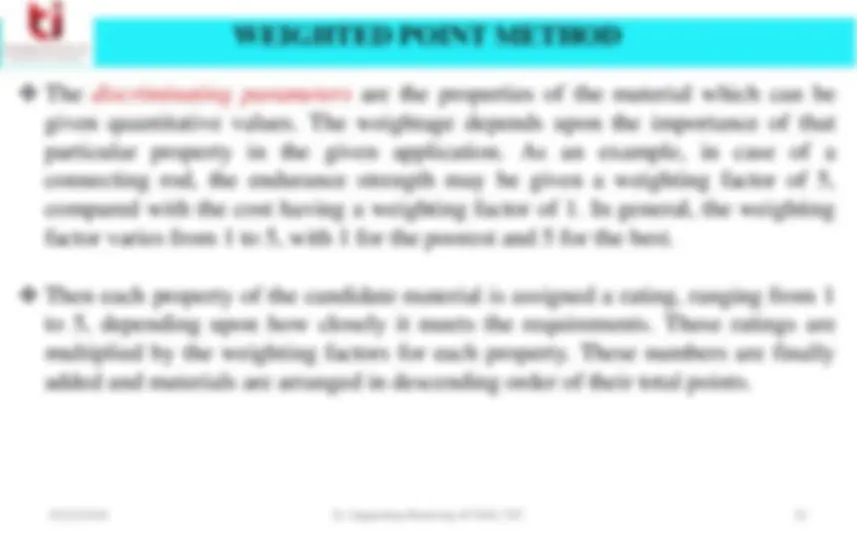
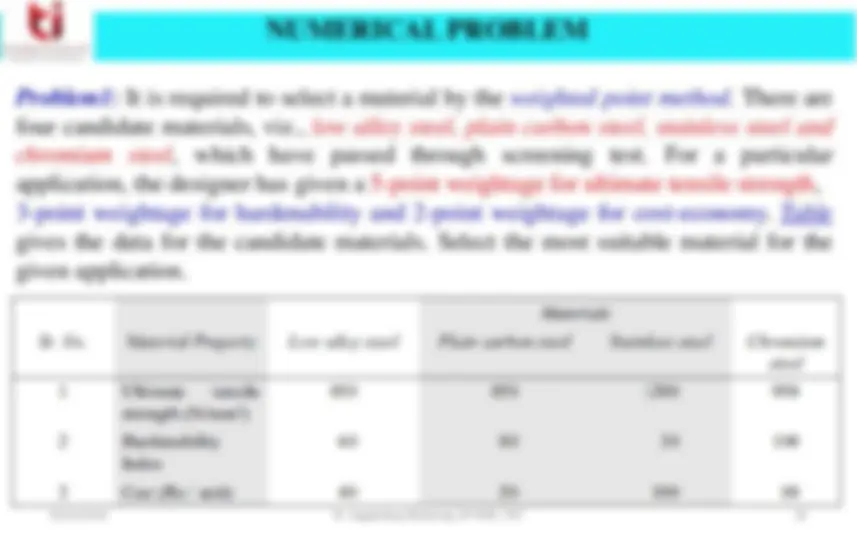
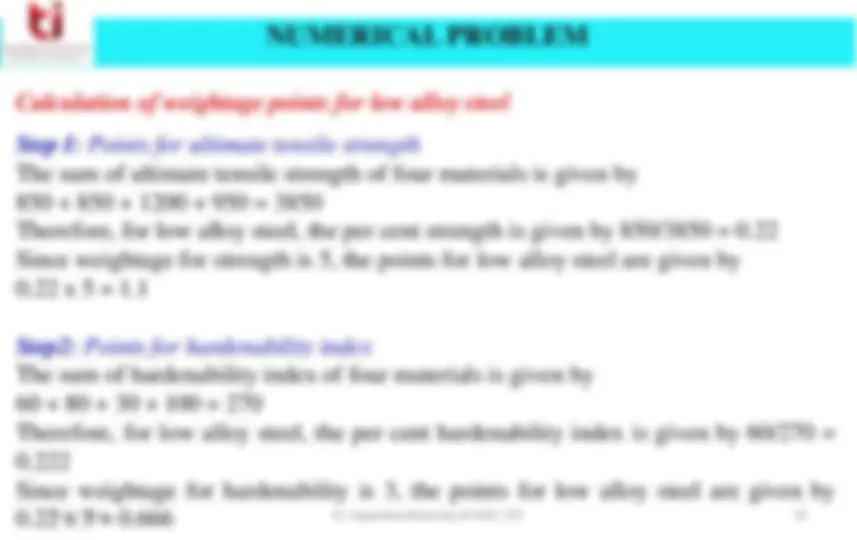
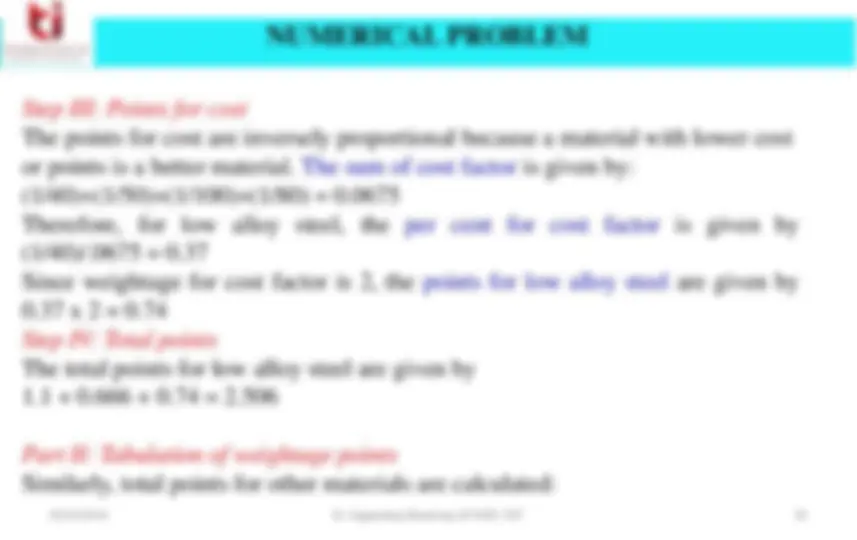
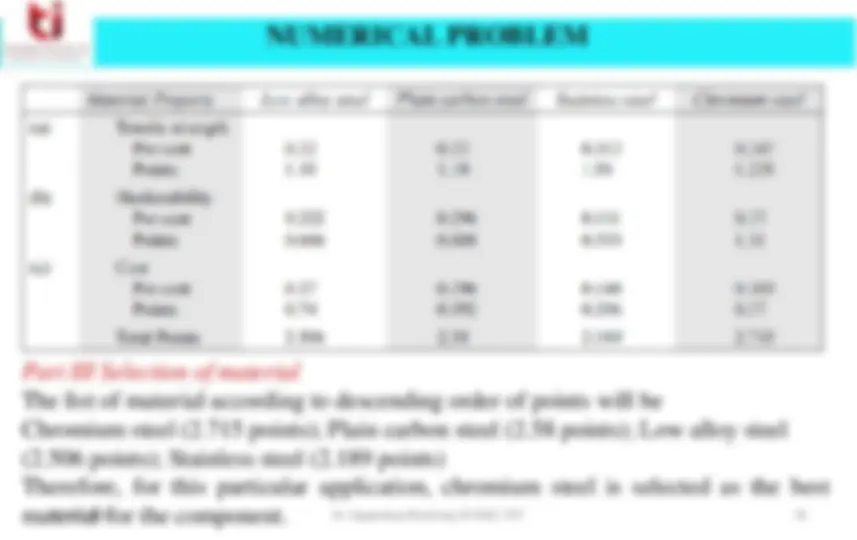
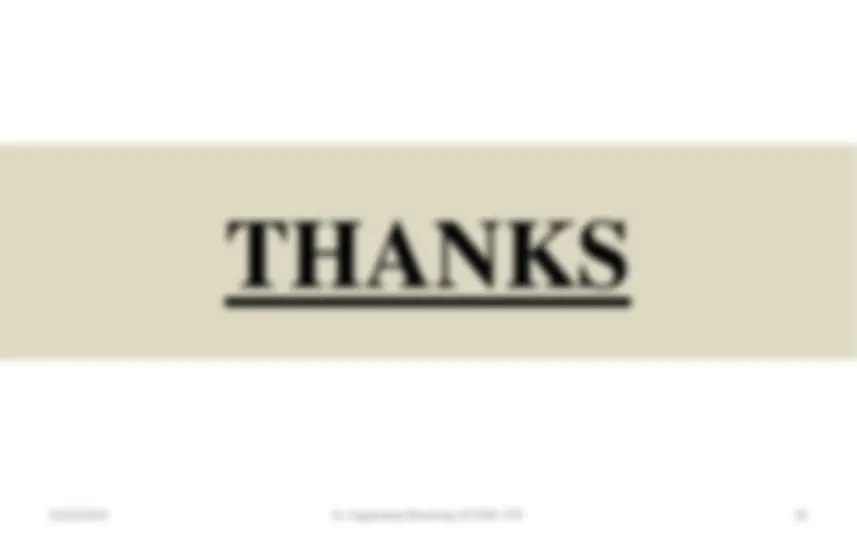
Study with the several resources on Docsity
Earn points by helping other students or get them with a premium plan
Prepare for your exams
Study with the several resources on Docsity
Earn points to download
Earn points by helping other students or get them with a premium plan
Community
Ask the community for help and clear up your study doubts
Discover the best universities in your country according to Docsity users
Free resources
Download our free guides on studying techniques, anxiety management strategies, and thesis advice from Docsity tutors
overview of different materials and their use in design
Typology: Lecture notes
1 / 36
This page cannot be seen from the preview
Don't miss anything!
Prepared by: Dr. Gagandeep Bhardwaj, Assistant Professor, MED Email: gagandeep.med@thapar.edu Contact No. 8954388548
The following information can be obtained from a tension test: (i) Proportional limit; (ii) Elastic limit; (iii) Modulus of elasticity; (iv) Yield strength; (v) Ultimate tension strength; (vi) Modulus of resilience; (vii) Modulus of toughness; (viii) Percentage elongation; (ix) Percentage reduction in area The shape and dimensions of this specimen are standardised. They should conform to IS 1608.
The mechanical properties of Engineering materials are: ( 1 ) Strength; ( 2 ) Elasticity; ( 3 ) Plasticity; ( 4 ) Stiffness; ( 5 ) Resilience; ( 6 ) Toughness; ( 7 ) Malleability; ( 8 ) Ductility; ( 9 ) Brittleness; ( 10 ) Hardness Strength is defined as the ability of the material to resist, without rupture, external forces causing various types of stresses. Resilience is defined as the ability of the material to absorb energy when deformed elastically and to release this energy when unloaded. Malleability is defined as the ability of a material to deform to a greater extent before the sign of crack, when it is subjected to compressive force.
๏ It has a poor tensile strength compared to steel. ๏ Cast iron parts are section-sensitive. Even with the same chemical composition, the tensile strength of a cast iron part decreases as the thickness of the section increases. This is due to the low cooling rate of thick sections. ๏ For thin sections, the cooling rate is high, resulting in increased hardness and strength. ๏ Cast iron does not offer any plastic deformation before failure and exhibits no yield point. The failure of cast iron parts is sudden and total. Cast iron parts are, therefore, not suitable for applications where permanent deformation is preferred over fracture. ๏ Cast iron is brittle and has poor impact resistance. ๏ The machinability of cast iron parts is poor compared to the parts made of steel.
The designation of plain carbon steel consists of the following three quantities: ๏ฑ a figure indicating 100 times the average percentage of carbon; ๏ฑ a letter C; ๏ฑ a figure indicating 10 times the average percentage of manganese. As an example, 55C4 indicates a plain carbon steel with 0.55% carbon and 0.4% manganese. A steel with 0.35โ0.45% carbon and 0.7โ0.9% manganese is designated as 40C8.
The designation of unalloyed free cutting steels consists of the following quantities: ๏ผ A figure indicating 100 times the average percentage of carbon; ๏ผ A letter C; ๏ผ A figure indicating 10 times the average percentage of manganese; ๏ผ A symbol โSโ(Sulphur), โSeโ (Selenium), โTeโ (Tellurium) or โPbโ (Lead) depending upon the element that is present and which makes the steel free cutting; ๏ผ A figure indicating 100 times the average percentage of the above element that makes the steel free cutting. For example: 25 C 12 S 14 indicates a free cutting steel with 0. 25 % carbon, 1. 2 % manganese and 0. 14 % sulphur. Similarly, a free cutting steel with an average of 0. 20 % carbon, 1. 2 % manganese and 0. 15 % lead is designated as 20 C 12 Pb 15.
An example, 25 Cr 4 Mo 2 is an alloy steel having average 0. 25 % of carbon, 1 % chromium and
Consider a steel with the following chemical composition: Carbon = 0. 12 โ 0. 20 %; Silicon = 0. 15 โ 0. 35 %; Manganese = 0. 60 โ 1. 00 %; Nickel =
Low Carbon Steel: Low carbon steel contains less than 0. 3 % carbon. It is popular as โ mild steel โ. Low carbon steels are soft and very ductile. However, due to low carbon content, they are unresponsive to heat treatment. Medium Carbon Steel: Medium carbon steel has a carbon content in the range of
05/02/2019 Dr. Gagandeep Bhardwaj, AP MED, TIET 19
The heat treatment process consists of controlled heating and cooling of components made of either plain carbon steel or alloy steel, for the purpose of changing their structure in order to obtain certain desirable properties like hardness, strength or ductility.