
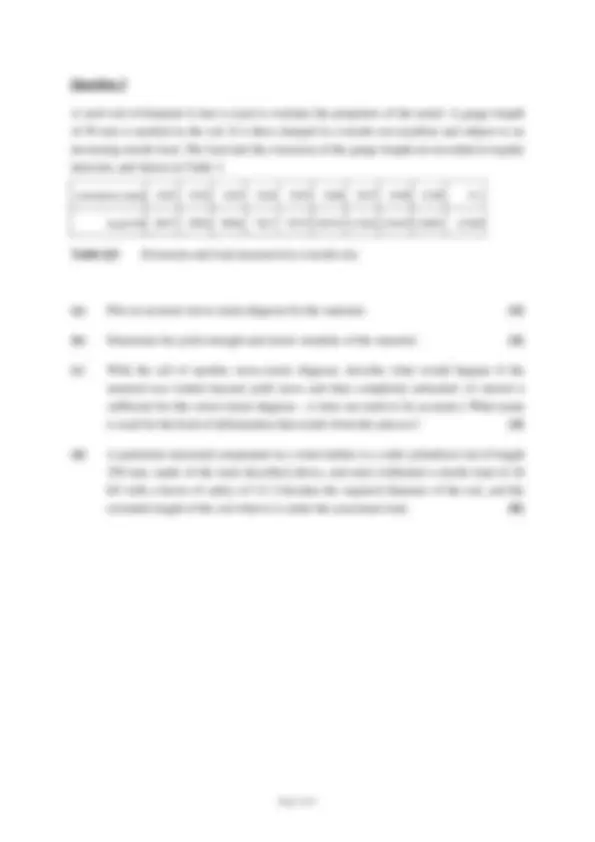
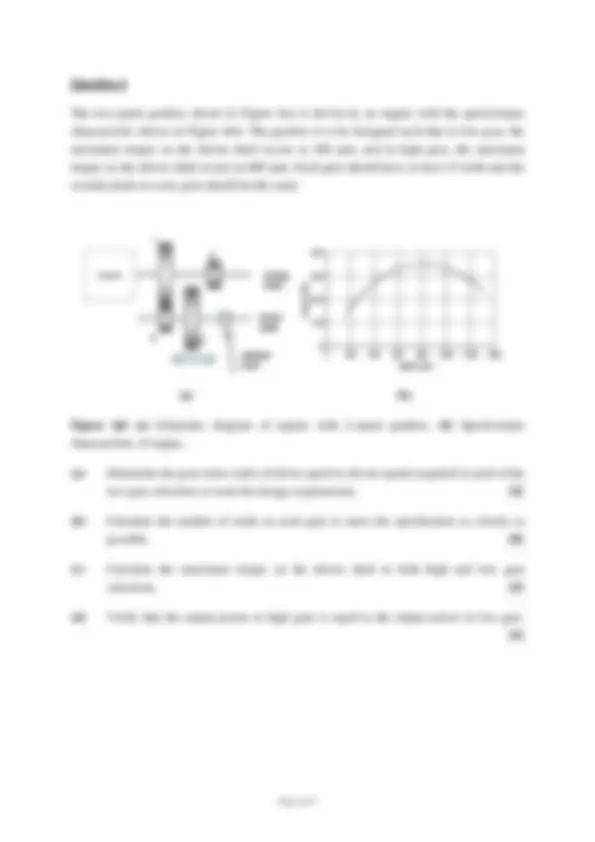
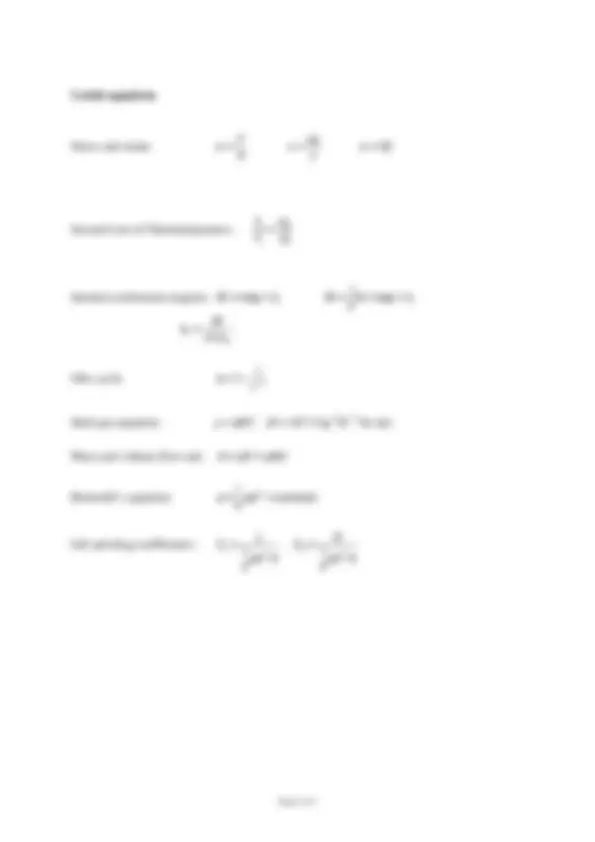
Study with the several resources on Docsity
Earn points by helping other students or get them with a premium plan
Prepare for your exams
Study with the several resources on Docsity
Earn points to download
Earn points by helping other students or get them with a premium plan
Community
Ask the community for help and clear up your study doubts
Discover the best universities in your country according to Docsity users
Free resources
Download our free guides on studying techniques, anxiety management strategies, and thesis advice from Docsity tutors
Information about the semester 2 examinations for mechanical and biomedical engineering in the academic year 2010/2011. It includes exam codes, modules, questions, instructions, and requirements. Topics such as the destruction of space shuttle columbia, aerodynamics, stress-strain analysis, and gearbox design.
Typology: Exams
1 / 5
This page cannot be seen from the preview
Don't miss anything!
Exam Code(s) 1BM, 1BG, 1BLE, 1BP, 1EG, 1BSE, 1BEI, 1BEE Exam(s) 1 st Engineering: Mechanical Biomedical Electrical and Electronic Electronic and Computer Undenominated Energy Systems Engineering Innovation – Electronic, Sports and Exercise) Module Code(s) ME Module(s) Fundamentals of Mechanical Engineering External Examiner(s) Prof. Noel O’Dowd Internal Examiner(s) Prof. Sean Leen *Dr. Nathan Quinlan
Duration 2 hours No. of Pages 5 Discipline(s) Mechanical and Biomedical Engineering Course Co-ordinator(s) Dr. Nathan Quinlan Requirements : Statistical/ Log Tables Graph paper Release to Library Yes
Question 1 (a) Explain the series of physical events that led to the destruction of the Space Shuttle Columbia in 2003. [ 6 ] (b) Explain the measures that were taken afterwards to prevent a recurrence of the incident. [ 6 ] (c) Consider the spacecraft in flight at velocity u 0 through air of density a when a fragment of debris breaks away from it. The fragment is a sphere of diameter d , density d and drag coefficient CD. Derive a differential equation that governs v ( t ), the velocity of the debris fragment relative to the spacecraft, as a function of time. [8] Question 2 Consider a racing car with a mass of 600 kg, a frontal area of 1.3 m 2 , a drag coefficient of 0.8, and a zero lift coefficient. The car’s engine’s maximum power is 440 kW and the coefficient of friction between the tyres and the road is 0.9. The car has detachable front and rear inverted wings to increase downforce. The two wings are identical, each with a planform area of 1.4 × 0.4 m, drag coefficient of 0.8 and lift coefficient of 2.6. (The “lift” on the wings is downward.) Ambient pressure and temperature are 101 kPa and 22°C. Assume that rolling resistance is negligible, that there are no energy losses in the car’s transmission, and that an optimal gear ratio is always selected so that 440 kW is transmitted to the roadwheels at all times. (a) Calculate the density of air around the car. [2] (b) What is the maximum possible speed of the car when driven in a straight line, with no wings attached? [6] (c) What is the maximum possible speed of the car (without skidding) through a corner of radius 110 m, with no wings attached? [4] (d) What is the maximum possible speed of the car (without skidding) through a corner of radius 110 m, with the wings attached? [8]
Question 4 The two-speed gearbox shown in Figure 4 (a) is driven by an engine with the speed-torque characteristic shown in Figure 4(b). The gearbox is to be designed such that in low gear, the maximum torque on the driven shaft occurs at 200 rpm, and in high gear, the maximum torque on the driven shaft occurs at 600 rpm. Each gear should have at least 15 teeth and the circular pitch on every gear should be the same. driving shaft driven shaft selector lever 1 (^3 ) 2 engine driving shaft driven shaft selector lever 1 (^3 ) 2 engine (a) 0 200 400 600 800 1000 1200 1400 0 100 200 300 400 speed (rpm) torque (Nm) 0 200 400 600 800 1000 1200 1400 0 100 200 300 400 speed (rpm) torque (Nm) (b) Figure Q 4 (a) Schematic diagram of engine with 2 - speed gearbox. (b) Speed-torque characteristic of engine. (a) Determine the gear ratios (ratio of driver speed to driven speed) required in each of the two gear selections to meet the design requirements. [ 4 ] (b) Calculate the number of teeth on each gear to meet the specification as closely as possible. [ 8 ] (c) Calculate the maximum torque on the driven shaft in both high and low gear selections. [ 4 ] (d) Verify that the output power in high gear is equal to the output power in low gear. [ 4 ]
Useful equations Stress and strain: A F L L E Second Law of Thermodynamics: L H L H Q Q T T Internal combustion engines: W mep Vd W Nmep Vd 2 ^1 f RP o mh W Otto cycle: (^1) 1 1 r Ideal gas equation: p = RT ( R = 287 J kg