
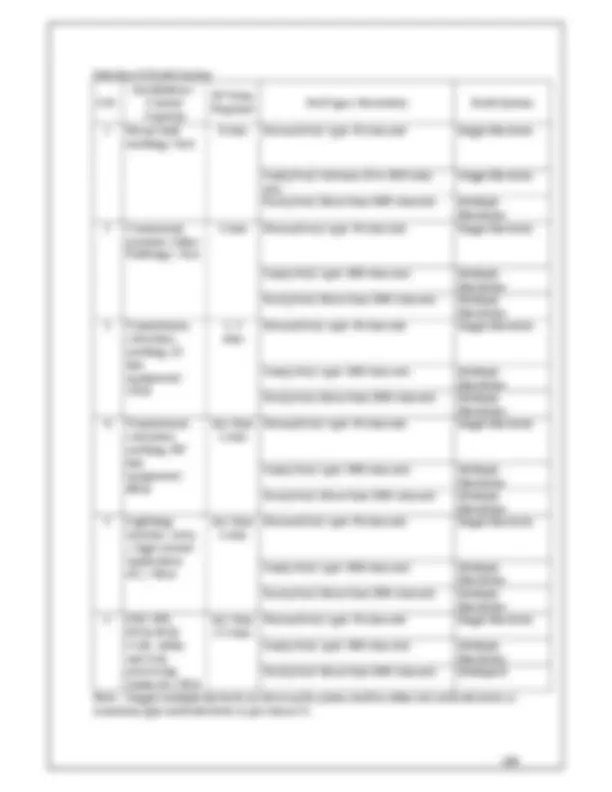
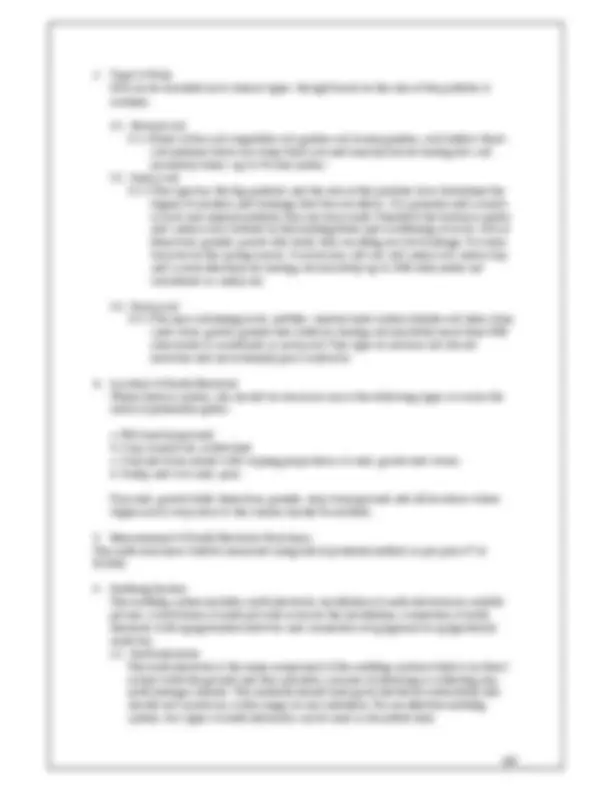
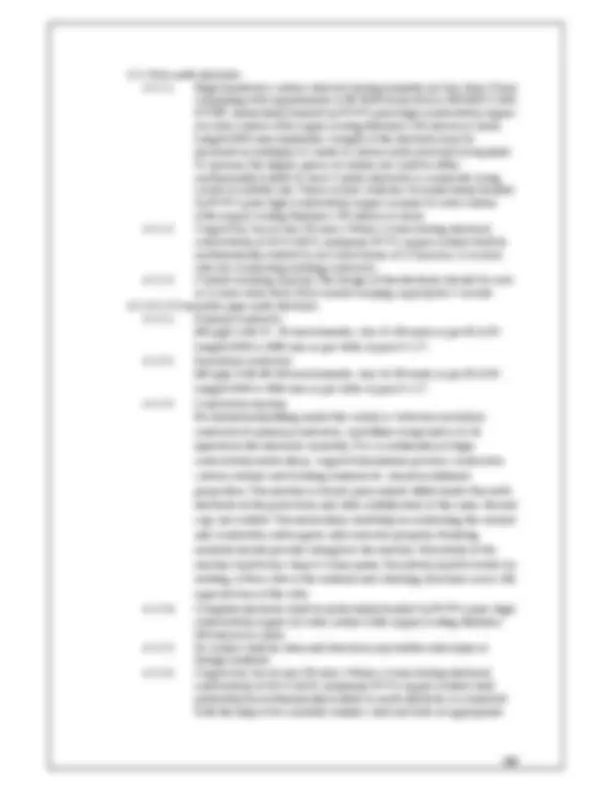
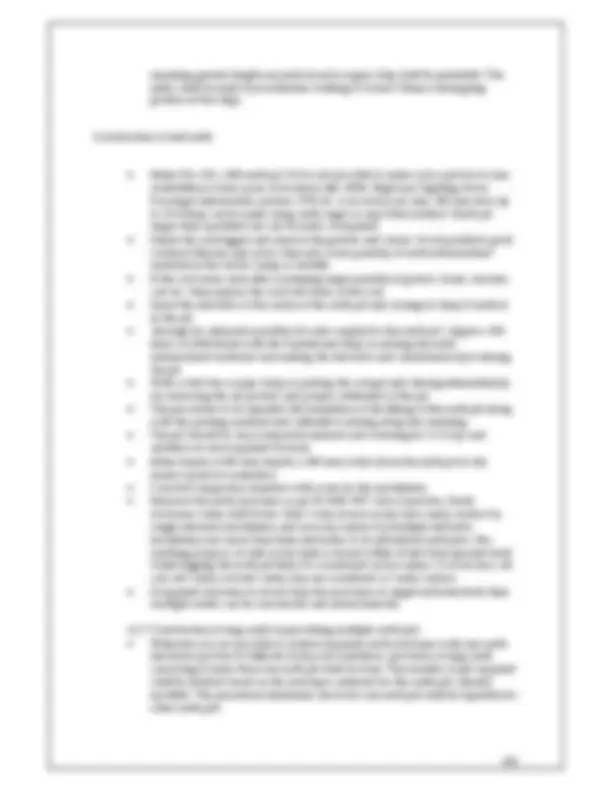
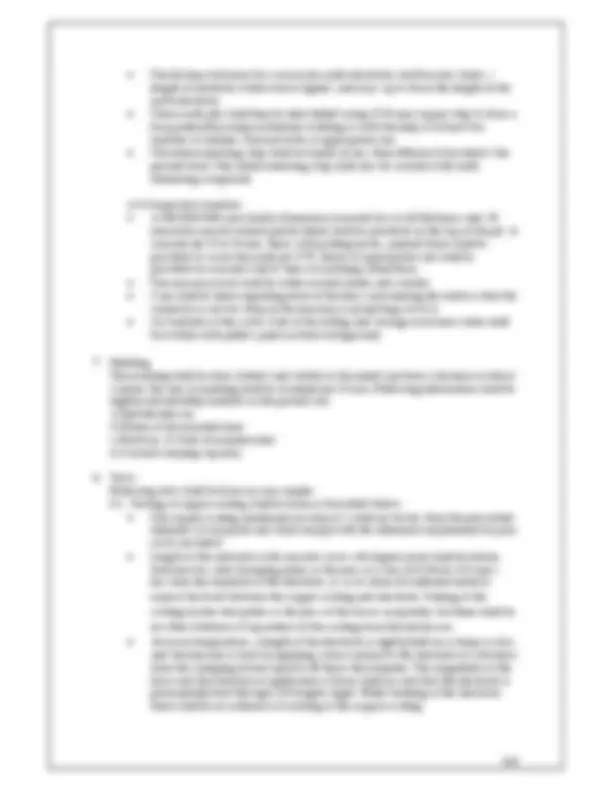
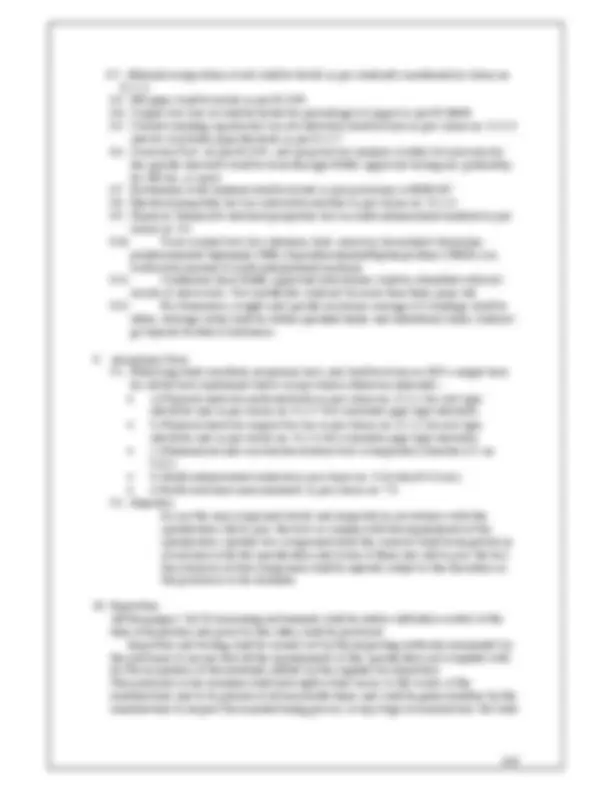
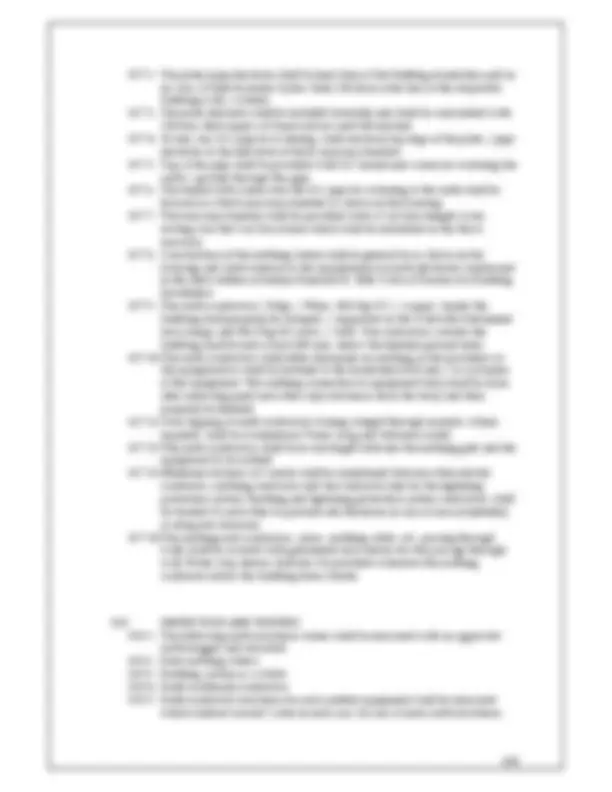
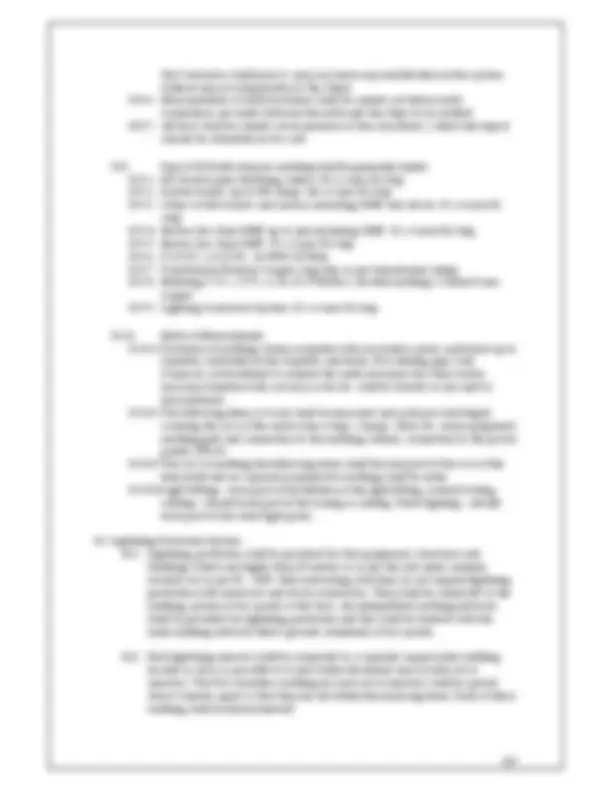
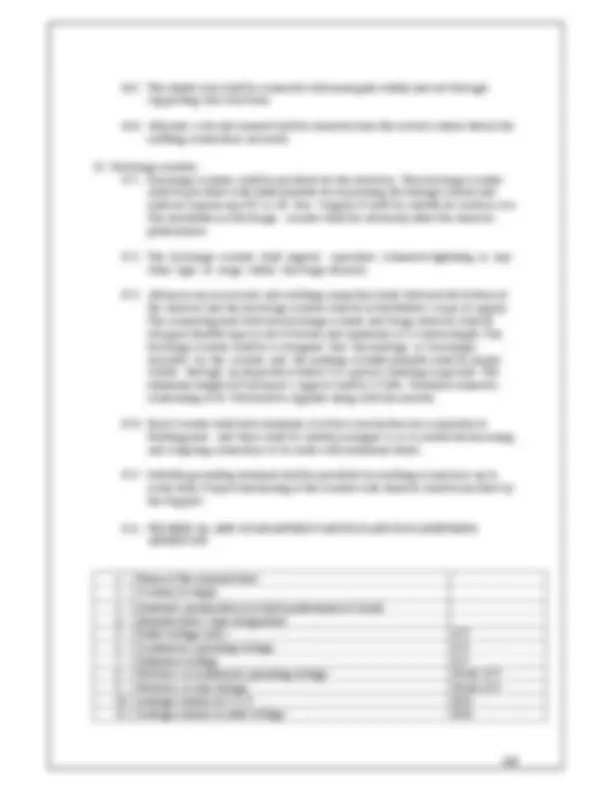
Study with the several resources on Docsity
Earn points by helping other students or get them with a premium plan
Prepare for your exams
Study with the several resources on Docsity
Earn points to download
Earn points by helping other students or get them with a premium plan
Community
Ask the community for help and clear up your study doubts
Discover the best universities in your country according to Docsity users
Free resources
Download our free guides on studying techniques, anxiety management strategies, and thesis advice from Docsity tutors
earthing & lightning protection installation details
Typology: Study Guides, Projects, Research
1 / 17
This page cannot be seen from the preview
Don't miss anything!
1. Foreword 1.1. Earthing is essential in any electrical installation to provide safety. The conventional GI pipe earthing system employing charcoal & salts are provided for various applications as per IS: 3043. Corrosion of metallic parts is comparatively fast besides maintenance by way of watering of earth pits and chiseling of corrosion prone parts & their replacement require monitoring which may not always be feasible in certain crowded and inaccessible areas. 1.2. This document is intended to provide guide lines for installation & testing of long lasting earthing system for various applications to meet requirement of rules 51, 61 of Indian Electricity Rule, 1956.
Scope: 1.1. This specification covers components, enhancing material & jointing used and procedure for constructing the earth pit for maintenance free earthing system to ensure that the resistance to earth is near zero consistent throughout the year.
Codes & standards 1.1.1. The design, material, assembling, inspection and testing shall comply with all currently applicable statutes, regulations and safety codes in the locality where the system will be installed. The equipment shall also confirm to the latest applicable standards and codes of practice as mentioned below
Sr. Item
Relevant is
1 Code of practice for earthing
2 Insulation co-ordination application guide IS 3716
3
Code of practice for protection of buildings and allied structures against lightning
IEEE guide for safety in AC sub-station grounding IEEE 80 Standard for qualifying permanent connections used in Substation grounding.
4 Indian electricity rules, 1956 with latest amendments 5 Indian electricity act, 1910 6 National electrical code
Wherever, reference to any specification appears in this document, it shall be Taken as a reference to the latest version of that specification unless the year of issue of the specification is specifically stated.
2. Applications 2.1.1. Earthing systems covered in this document shall be for providing effective grounds for 2.1.1.1. Sub-Stations 2.1.1.2. RTUs, supply control posts 2.1.1.3. Transformer and Generator neutral & Body earths 2.1.1.4. Lightning arrester earths 2.1.1.5. Equipment earths including panels
3. Type Of Soils Soil can be classified in to various types, though based on the size of the particles it contains:
3.1. Normal soil 3.1.1. Black cotton soil, vegetable soil, garden soil, loamy garden, soil shallow black , soil medium black soil ,deep black soil and marshy soil etc having low soil resistivity value ( up to 50 ohm meter) 3.2. Sandy soil 3.2.1. This type has the big particles and the size of the particles does determine the degree of aeration and drainage that the soil allows. It is granular and consists of rock and mineral particles that are very small. Therefore the texture is gritty and sandy soil is formed by the disintegration and weathering of rocks such as limestone, granite, quartz and shale, thus resulting in over-drainage. It warms very fast in the spring season. Coastal area, silt soil, red sandy soil, sandy clay and coastal alluvium etc having soil resistivity up to 2000 ohm-meter are considered as sandy soil.
3.3. Rocky soil 3.3.1. The area containing rocks, pebbles, uneven hard surface laterite soil, lime stone, sand stone, gravel, granite and chalk etc having soil resistivity more than 2000 ohm-meter is considered as rocky soil. This type of soil does not absorb moisture and are extremely poor conductor.
4. Location Of Earth Electrode Where there is option, site should be chosen in one of the following types of soil in the order of preference given:-
a. Wet marshy ground; b. Clay, loamy soil, arable land. c. Clay and loam mixed with varying proportions of sand, gravel and stones; d. Damp and wet sand, peat.
Dry sand, gravel chalk, limestone, granite, very stony ground and all locations where virgin rock is very close to the surface should be avoided,
5. Measurement Of Earth Electrode Resistance The earth resistance shall be measured using fall of potential method as per para 37 of IS:3043. 6. Earthing System The earthing system includes earth electrode, installation of earth electrode in suitable pit size, construction of earth pit with cover for the installation, connection of earth electrode with equipotential earth bus and connection of equipment to equipotential earth bus. 6.1. Earth electrode The earth electrode is the main component of the earthing system which is in direct contact with the ground and thus provides a means of releasing or collecting any earth leakage currents. The material should have good electrical conductivity and should not corrode in a wide range of soil conditions. For an effective earthing system, two types of earth electrodes can be used as described here:
6.1.1. Rod earth electrode 6.1.1.1. High tensile-low carbon steel rod having diameter not less than 17mm complying with requirements of BS 4360 Grade 43A or EN10025:2- S275JR, molecularly bonded by 99.99% pure high conductivity copper on outer surface with copper coating thickness 250 micron or more, Length 3000 mm (minimum). Length of the electrode may be increased in multiple of 1 meter to reduce earth resistance if required. To increase the length, pieces of similar rod shall be either exothermally welded to basic 3 meter electrode or connected using socket of suitable size. These sockets shall also be molecularly bonded by 99.99% pure high conductivity copper on inner & outer surface with copper coating thickness 250 micron or more. 6.1.1.2. Copper bus bar of size 250 mm x 50mm x 6 mm having electrical conductivity of 101% IACS, minimum 99.9% copper content shall be exothermically welded to rod with 4 holes of 12 mm dia. (2 on each side) for connecting earthing conductor. 6.1.1.3. Current carrying capacity: The design of the electrode should be such as to have more than 15kA current carrying capacity for 1 second. 6.1.2. 8.1.2 Concentric pipe earth electrode: 6.1.2.1. Primary conductor MS pipe with 25 - 50 mm diameter, class B, ISI mark as per IS-1239, Length 2000 or 3000 mm as per table at para 8.1.2.7. 6.1.2.2. Secondary conductor MS pipe with 40-100 mm diameter, class B, ISI mark as per IS-1239, Length 2000 or 3000 mm as per table at para 8.1.2.7. 6.1.2.3. Conductive mixture For hermetically filling inside the cavity i.e. between secondary conductor & primary conductor, crystalline compound is to be injected in the electrode assembly. It is a combination of high conductivity metal alloys, copper &aluminium powder, conductive carbon/cement and bonding material etc. mixed in different proportion. The mixture is forced (pressurized) filled inside the earth electrode in the paste form and after solidification of the same, the end caps are welded. The metal alloys shall help in conducting the current and conductive carbon gives anti corrosive property. Bonding material should provide strength to the mixture. Resistivity of the mixture shall be less than 0.2 ohm-meter. Resistivity shall be tested by making a 20cm cube of the material and checking resistance across the opposite face of the cube. 6.1.2.4. Complete electrode shall be molecularly bonded by 99.99% pure, high conductivity copper on outer surface with copper coating thickness 300 micron or more. 6.1.2.5. Its surface shall be clean and free from any visible oxide layer or foreign material. 6.1.2.6. Copper bus bar of size 250 mm x 50mm x 6 mm having electrical conductivity of 101% IACS, minimum 99.9% copper content shall preferably be exothermically welded to earth electrode or connected with the help of two number stainless steel nut bolts of appropriate
6.2.14. It should be diffuses into soil pores and creates conductive roots enlarging conductive zone of earth pit. 6.2.15. It shall be permanent & maintenance free and in its “set form”, maintains constant earth resistance with time. 6.2.16. It shall not require periodic charging treatment or replacement. 6.2.17. It shall be suitable for any kind of electrode and all kinds of soils of different resistivity. 6.2.18. It shall not cause burns, irritation to eye, skin etc. 6.2.19. Minimum quantity of earth enhancement material to be supplied : 6.2.20. For 5’ x5’x 10’ earth pit – Min. 75 kgs per pit 6.2.21. For 300mm bore type earth pit – Min 50 kgs per pit 6.2.22. The Earth enhancement material shall be supplied in sealed, moisture proof bags. These bags shall be marked with Manufacturer’s name or trade name, quantity, batch no & date of manufacture.
6.2.23. Backfill material Normally the excavated soil shall be used if it is free from sand, gravel and stones. In case the excavated soil contains sand, gravel and stones these shall be removed by appropriate methods such as hand picking, sieving etc. Small proportion of sand in the soil may be permissible. Material like sand, salt, coke breeze, cinders and ash shall not be used because of its acidic and corrosive nature. If the excavated soil contains sand, gravel and stone in large proportion and it is not feasible to remove these economically, good quality soil from other place may be used for backfilling. While backfilling the soil shall be thoroughly compacted with at least 5 kg compactor. In case the soil is dry, small quantity of water may be sprinkled only to make it moist enough suitable for compacting. Large quantity of water may make the soil muddy which is not suitable for compacting and after drying the soil may contain voids which may permanently increase earth resistance.
6.3. Equipotential bus & Earthing Conductor 6.3.1. A copper bus bar of size 300mm x 25mm x 6mm to be installed in the equipment room as equipotential bus and must be connected with preferably copper strip of 25mm x 3mm (suitable length) from instrument to the bus bar. The connecting terminal of the earth electrode to the bus bar must be connected by copper strip of 25mm x 3mm (suitable length) buried inside a trench of 300mm width x 600mm depth (from the earth pit to the nearest wall) .It shall be duplicated. However, it shall be ensured that only minimum required length is used and any extra length is cut away to keep the earth impedance minimum. 6.3.2. It shall be high conductivity copper having electrical conductivity of 101% IACS i.e. minimum 99.9% copper content The maximum specific resistance of the copper strip earthing conductor shall be 17.241 x 10-7 ohm cm at 20ºC. 6.3.3. At a temperature of 20ºC, its density shall be 8.89 gm/cm 6.3.4. Its surface shall be clean and free from any visible oxide layer or foreign materials. 6.3.5. It shall preferably be connected to earth electrode and earth bus bar with the help of exothermic welding or at least two number stainless steel nut bolts of appropriate size. 6.3.6. Normally a single length of copper strip shall be used for each duplicate copper strip earthing conductor and no joint should be used. However in situation
requiring greater length one joint in each copper strip shall be permitted. The joints shall be made by exothermic welding of at least 10mm overlapping portion of the strips.
Construction of unit earth.
6.3.7. Construction of ring earth by providing multiple earth pits
8.2. Material composition of rod shall be tested as per standards mentioned in clause no. 8.1.1.1. 8.3. MS pipes shall be tested as per IS:1239. 8.4. Copper bus bars of shall be tested for percentage of copper as per IS:14644. 8.5. Current carrying capacity test on rod electrode shall be done as per clause no. 8.1.1. and for concentric pipe electrode as per 8.1.2.7. 8.6. Corrosion Test :As per IS:2119, salt spray test for analysis of effect of corrosion for the specific electrode shall be done through NABL approved testing lab, preferably for 500 hrs. or more. 8.7. Exothermic weld material shall be tested as per provisions of IEEE 837. 8.8. Electrical properties test on conductive mixture as per clause no. 8.1.2.3. 8.9. Physical, chemical & electrical properties test on earth enhancement material as per clause no. 8.2. 8.10. Toxic content tests for cadmium, lead, mercury, hexavalent chromium, polybrominated biphenyls (PBBs) &polybrominateddiphenyl ethers (PBDEs) on conductive mixture & earth enhancement material. 8.11. Certificates from NABL approved laboratories shall be submitted with test results of above tests. Test certificates shall not be more than three years old. 8.12. For dimension, weight and specific resistance average of 3 readings shall be taken. Average value shall be within specified limits and individual values shall not go beyond double of tolerances.
9. Acceptance Tests 9.1. Following shall constitute acceptance tests and shall be done on 100% sample basis for all the tests mentioned below except where otherwise indicated–
have the right to reject whole or part of any work or material that does not conform to the terms of this specification or any other specification or requirement applicable and may order the same to be removed / replaced or altered at the expense of the manufacturer. All reasonable/complete facilities considered necessary by the inspecting authorities for the inspection shall be supplied by the manufacturer free of cost. The manufacturer shall at his own cost prepare and furnish the necessary test pieces and appliances for such testing as may be carried out at his own premises in accordance with the specification. Failing the existence of facilities at his own premises for the prescribed tests, the manufacturer shall bear the cost of carrying out the tests in an approved laboratory, workshop or test house.
11. Completion Report & Certification: 11.1. 13.1 The last documents for the completion of the procedure will be submission of the work completion report to the concern Railway authority. After testing the earth values of the pits and proper recording in presence of Railway authority, certified grounding self-adhesive certificate shall be provided for all installations and the same will be displayed / pasted at the place of installation. 11.2. 13.2 The complete layout with dimensions of the earthing & bonding system shall be submitted by the supplier in appropriate size (in three copies) after commissioning showing commissioning date, earth resistance, specification no. and manufacturer’s name. 12. Infringement Of Patent Rights: Indian railways shall not be responsible for infringement of patent rights arising due to similarity in design, manufacturing process, use of the components, used in design, development and manufacturing of escalator and any other factor which may cause such dispute. The responsibility to settle any issue lies with the manufacturer. 13. Funnel Type Earthing 13.1. Scope: 13.2. Plate Earthing 13.2.1. Supply and erecting of funnel type earthing having earth plate of following size buried in specifically prepared earth pit 3.00 meter below ground with 40 kg charcoal and salt with alternate layer of charcoal and salt, 20 mm diameter GI pipe with funnel with a wire
13.3. Material Specification & Workmanship 13.3.1. The earthing system complete in all respect with all equipment, fittings and accessories for efficient and trouble-free operation. The material to be supplied by the contractor and work to be carried out by the contractor shall be in general, but not limited to, conforming to the specification laid down for each item.
13.4. Codes & standards 13.4.1. The design, material, assembling, inspection and testing shall comply with all currently applicable statutes, regulations and safety codes in the locality where the system will be installed. The equipment shall also confirm to the latest applicable standards and codes of practice as mentioned below
13.7.2. The plate/pipe electrode shall be kept clear of the building foundation and in no case, it shall be nearer by less than 2 M from outer face of the respective building wall / column 13.7.3. The plate electrode shall be installed vertically and shall be surrounded with 150 mm. thick layers of Charcoal dust and Salt mixture 13.7.4. 20 mm. dia. G.I. pipe for watering, shall run from top edge of the plate / pipe electrode to the mid level of block masonry chamber 13.7.5. Top of the pipe shall be provided with G.I. funnel and screen for watering the earth / ground through the pipe 13.7.6. The funnel with screen over the G.I. pipe for watering to the earth shall be housed in a block masonry chamber as shown in the drawing 13.7.7. The masonry chamber shall be provided with a Cast Iron hinged cover resting over the Cast Iron frame which shall be embedded in the block masonry 13.7.8. Construction of the earthing station shall in general be as shown in the drawing and shall conform to the requirement on earth electrodes mentioned in the latest edition of Indian Standard IS: 3043, Code of Practice for Earthing Installation 13.7.9. The earth conductors ( Strips / Wires, Hot dip G.I. / copper ) inside the building shall properly be clamped / supported on the wall with Galvanized Iron clamps and Hot Dip GI screws / bolts. The conductors outside the building shall be laid at least 600 mm. below the finished ground level 13.7.10.The earth conductors shall either terminate on earthing socket provided on the equipment or shall be fastened to the foundation bolt and / or on frames of the equipment. The earthing connection to equipment body shall be done after removing paint and other oily substances from the body and then properly be finished 13.7.11.Over lapping of earth conductors during straight through in joints, where required, shall be of minimum 75mm. long and bitumen coated 13.7.12.The earth conductors shall be in one length between the earthing grid and the equipment to be earthed 13.7.13.Minimum distance of 2 meter shall be maintained between other electric conductor, earthing conductor and the conductor laid for the lightning protection system. Earthing and lightning protection system conductors shall be bonded to each other to prevent side flashover in case of non-availability of adequate clearance 13.7.14.The earthing met conductors, risers, earthing cables, etc. passing through walls shall be covered with galvanized iron sleeves for the passage through wall. Water stop sleeves shall also be provided wherever the earthing conductor enters the building from outside
13.8.1. The following earth resistance values shall be measured with an approved earth megger and recorded. 13.8.2. Each earthing station 13.8.3. Earthing system as a whole 13.8.4. Earth continuity conductors 13.8.5. Earth conductor resistance for each earthed equipment shall be measured which shall not exceed 1 ohm in each case. In case of more earth resistance,
the Contractor shall have to carry out necessary modification in the system without any cost implication to the Client 13.8.6. Measurements of earth resistance shall be carried out before earth connections are made between the earth and the object to be earthed 13.8.7. All tests shall be carried out in presence of the consultant / client and report should be submitted in two sets
13.9. Size of GI Earth-strip for earthing shall be generally under: 13.9.1. HT Switch-yard/Earthing station: 50 x 6 mm GI strip 13.9.2. Switch-boards up to 800 Amps: 40 x 6 mm GI strip 13.9.3. Other switch-boards and motors including 50HP and above: 32 x 6 mm GI strip 13.9.4. Motors less than 50HP up to and including 20HP: 32 x 3 mm GI strip 13.9.5. Motors less than 20HP: 25 x 3 mm GI strip 13.9.6. P.S.D.B.’s L.S.D.B’s: 10 SWG GI Wire 13.9.7. Transformer Neutral: Copper strip Size as per transformer rating 13.9.8. Metering C.T’s / P.T’s, L.A’s & TVM Box: (double earthing): 25mmx5 mm copper 13.9.9. Lighting Conductor System: 32 x 6 mm GI strip
13.10. Mode of Measurement 13.10.1.Provision of earthing station complete with excavation, plate, earth lead up to chamber, earth link in the chamber, electrode, GI watering pipe, Salt, Charcoal, soil treatment to achieve the earth resistance less than 4 ohm, masonry chamber with cast iron cover etc. shall be treated as one unit of measurement. 13.10.2.The following items of work shall be measured and paid per unit length covering the cost of the earth wires/strips, clamps, labor etc. main equipment earthing grid and connection to the earthing stations, connection to the power panels, DB etc. 13.10.3.The cost of earthing the following items shall become part of the cost of the item itself and no separate payment for earthing shall be made. 13.10.4.Light fittings - form part of installation of the light fitting, conduit wiring, cabling - should form part of the wiring or cabling. Street lighting - should form part of the street light poles.
14. Lightning Protection System 14.1. Lightning protection shall be provided for the equipment, structures and buildings which are higher than 20 meters or as per the risk index analysis worked out as per IS – 2309. Self-conducting structures do not require lightning protection with aerial rod and down conductors. They shall be connected to the earthing system at two points of the base. An independent earthing network shall be provided for lightning protection and this shall be bonded with the main earthing network below ground, minimum at two points.
14.2. Each lightning arrestor shall be connected to a separate copper plate earthing located as close as possible to it and within the fenced area of each set of arrestors. The Two numbers earthing for each set of arrestors shall be spaced about 5 meters apart so that they are all within the enclosing fence. Each of these earthing shall be interconnected.
KV(Peak) KV(Peak) KV(Peak)
Micro second.
mm mm
Earthing Schedule
Earthing Schedule
S. No. Item Description GI^ Copper^ Unit
1 Earthing & Lightning Protexction
Total GI Safe earth Electrode (^) 16 Copper Plate Earthing (^) 19