
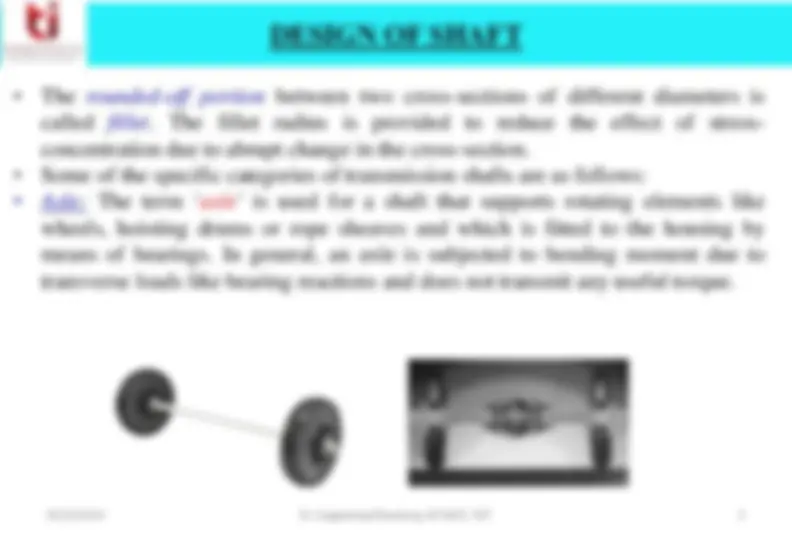
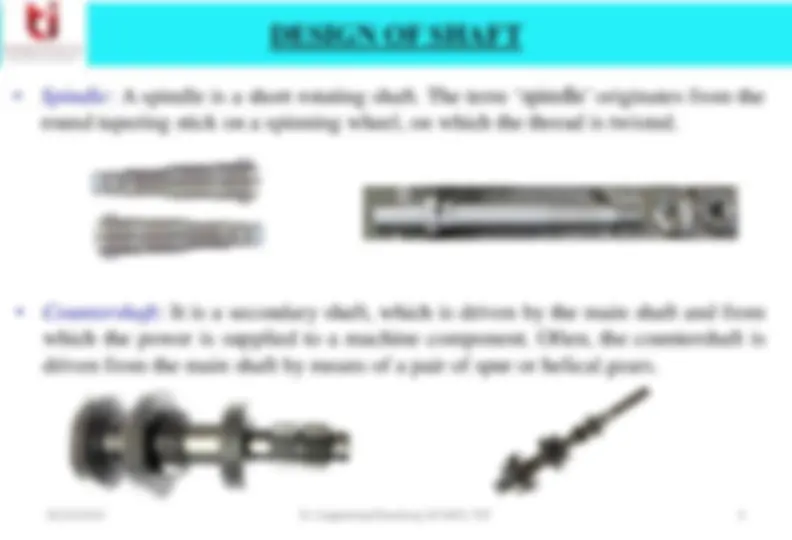
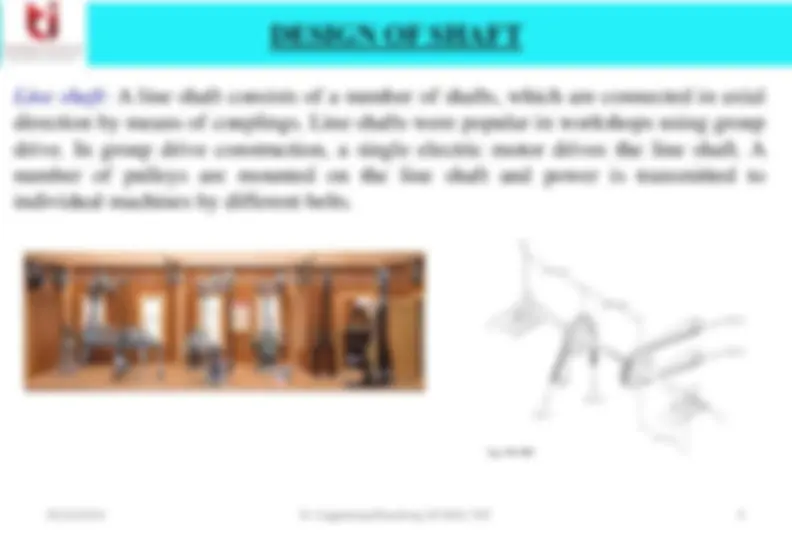
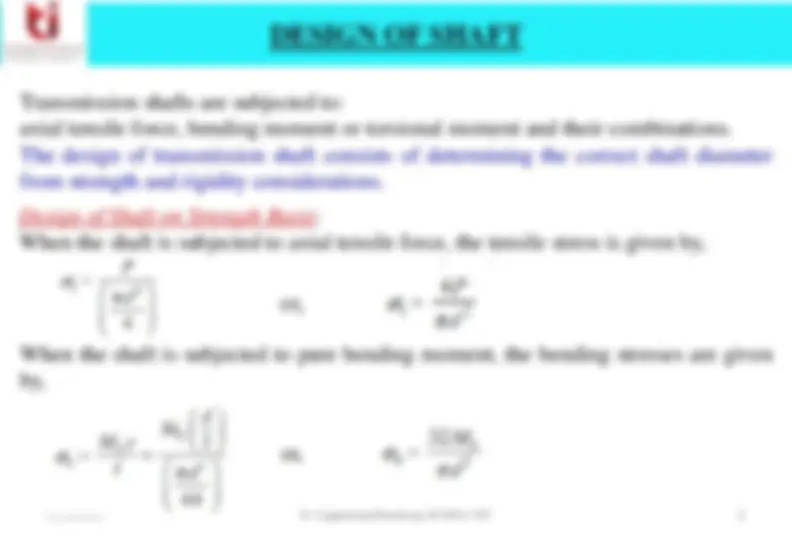
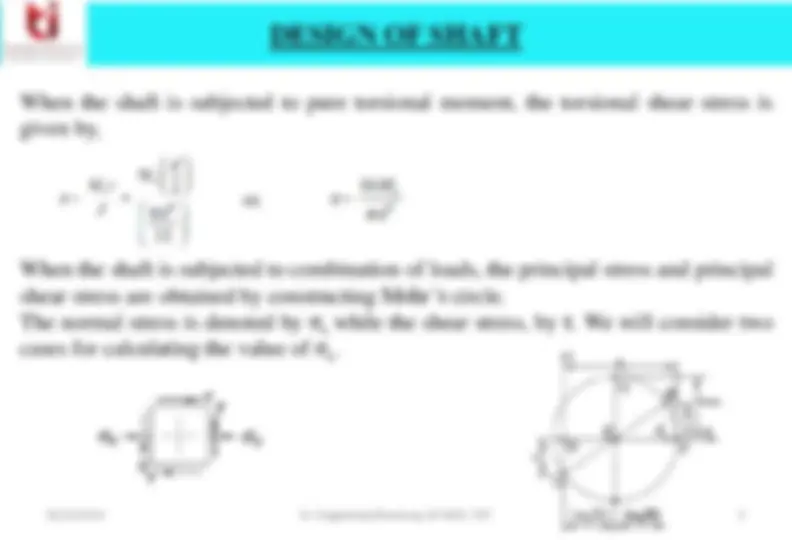
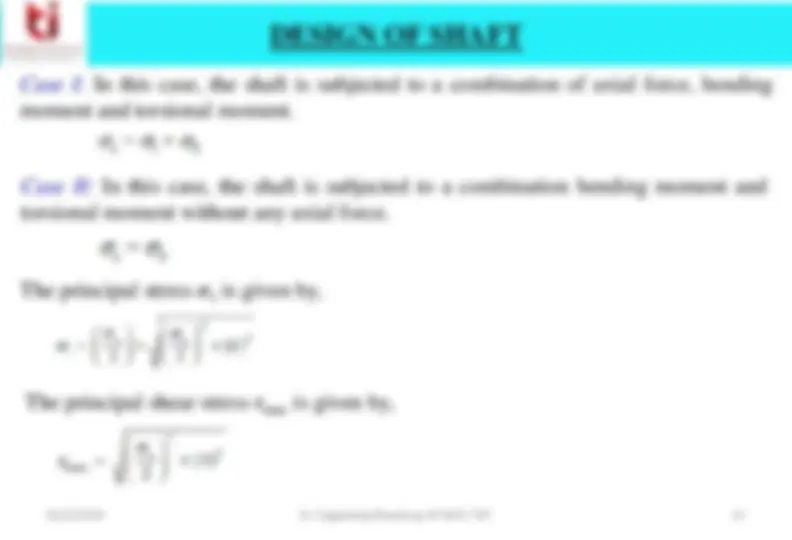
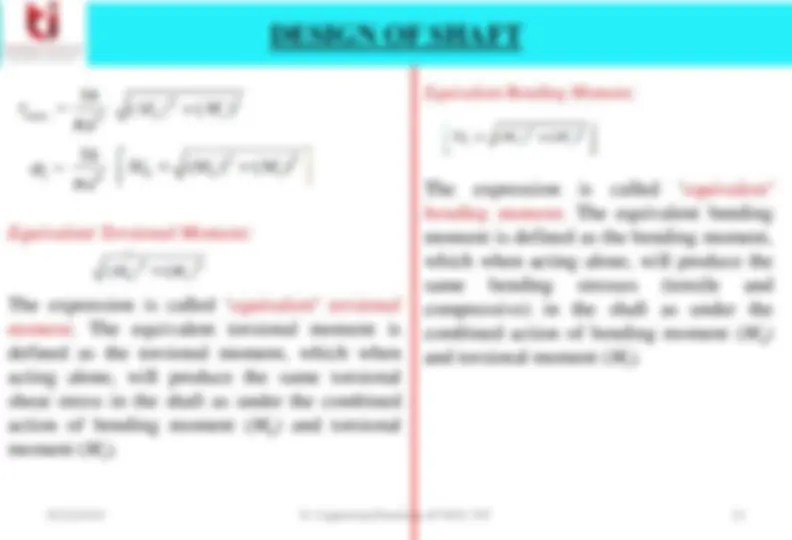
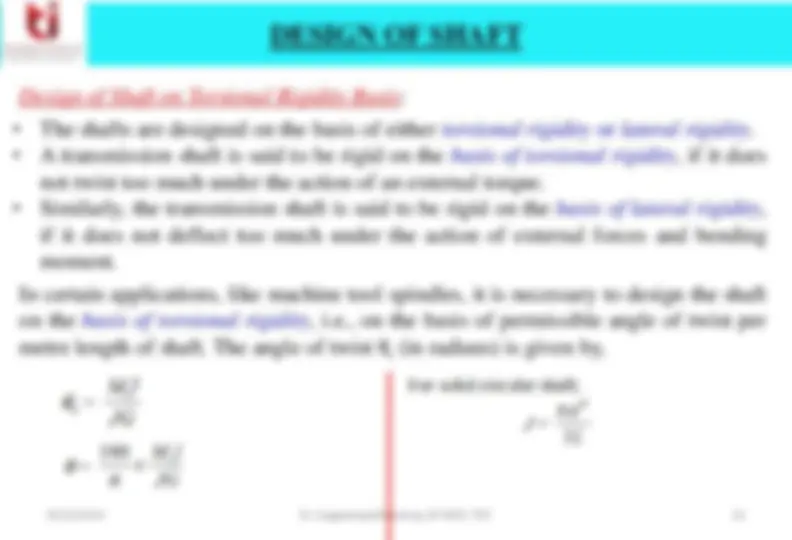
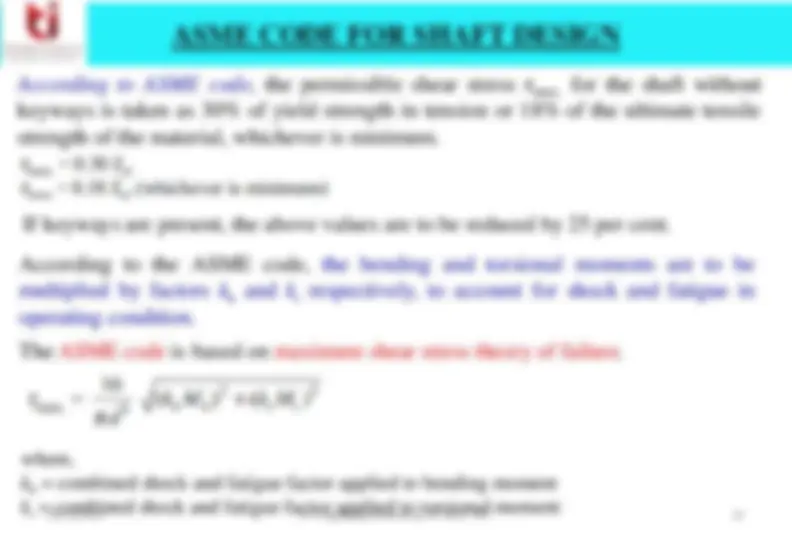
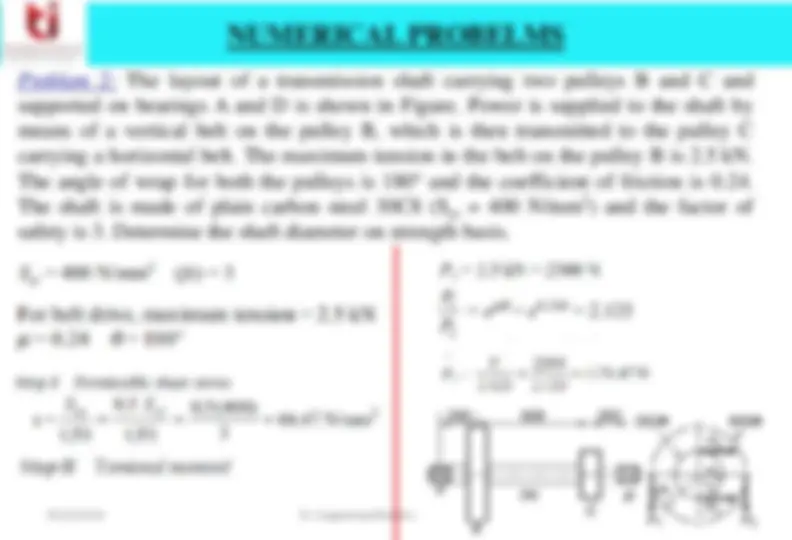
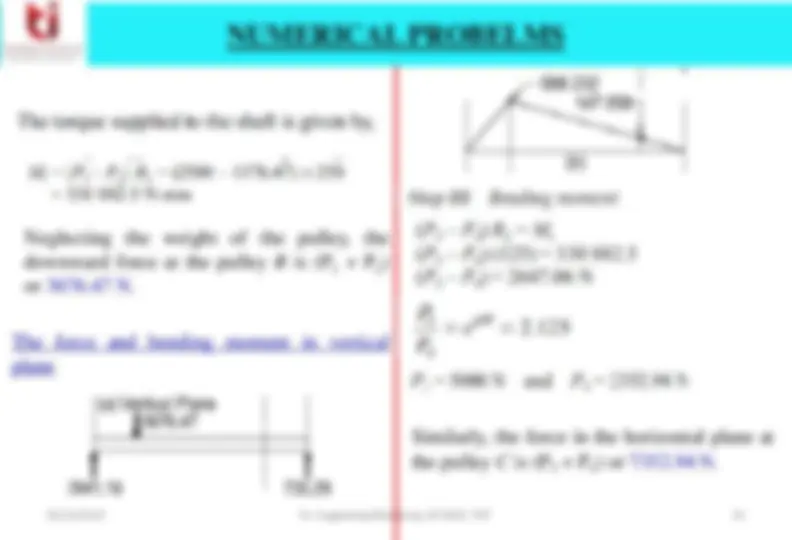
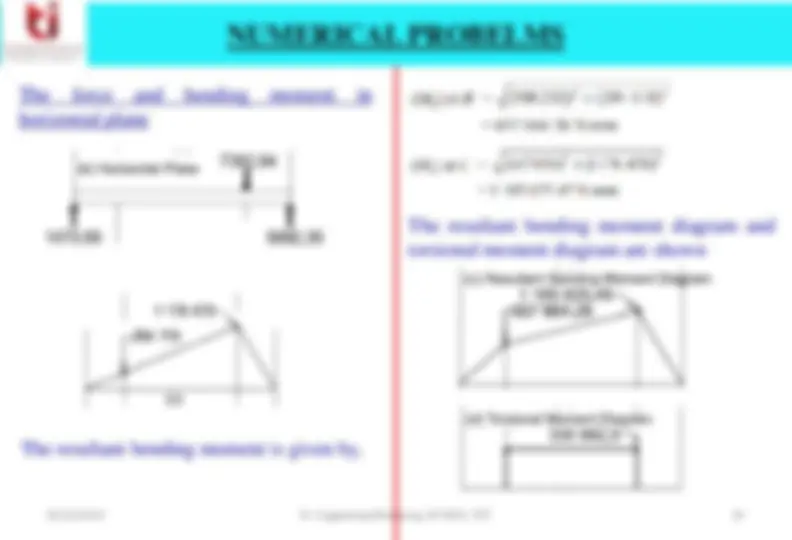
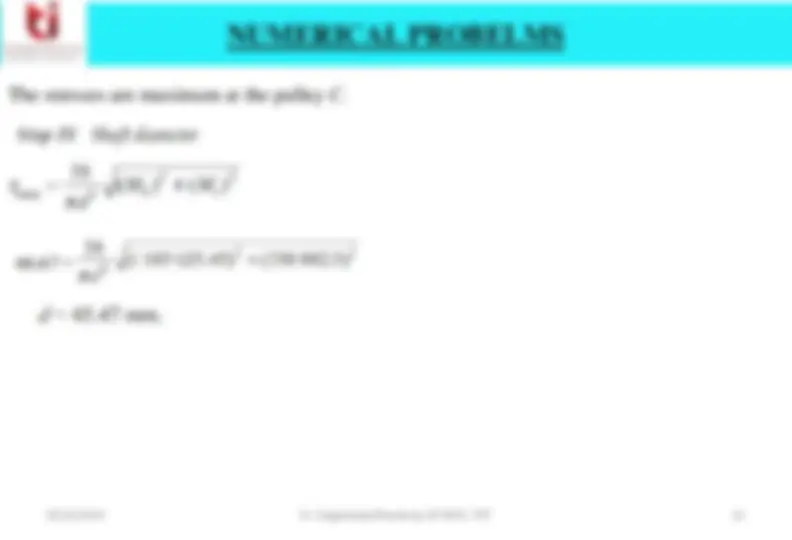
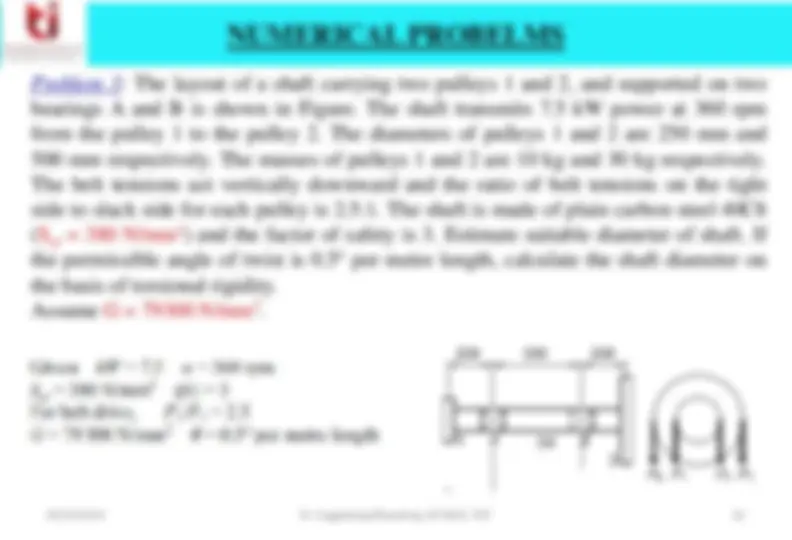
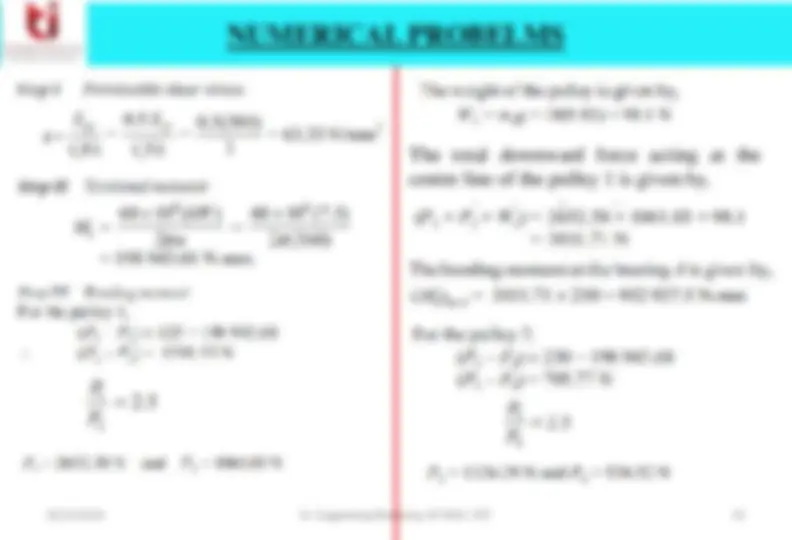
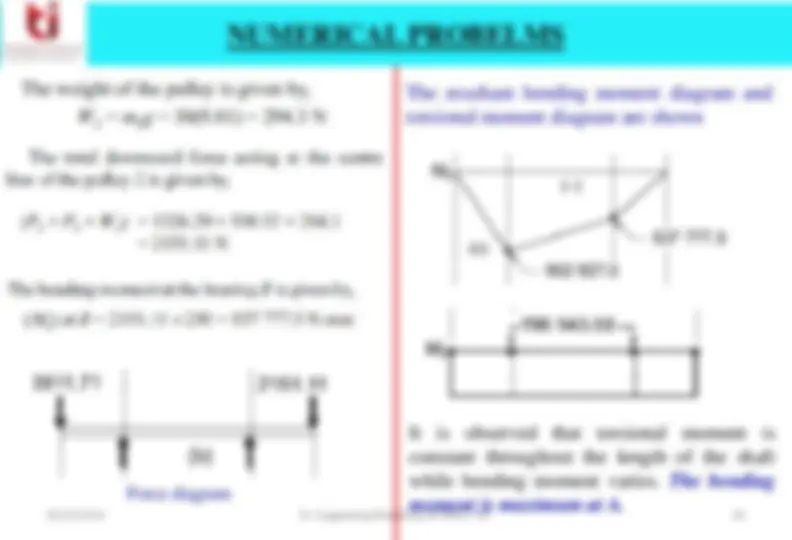
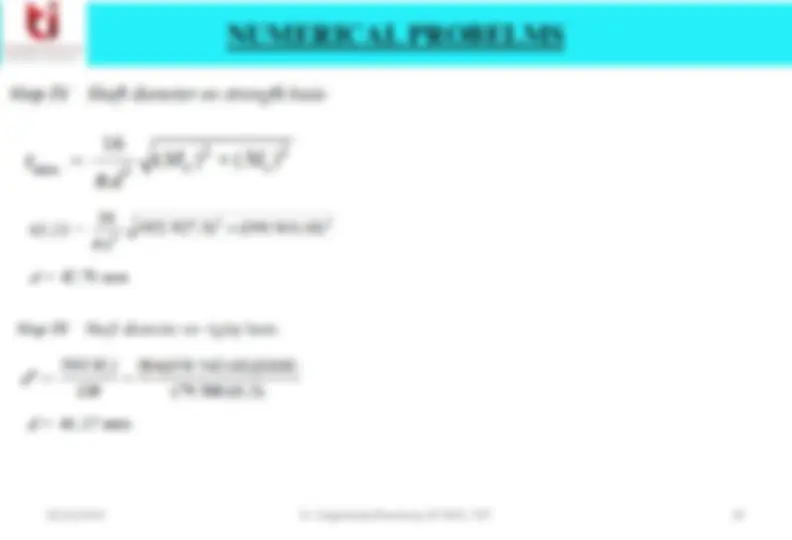
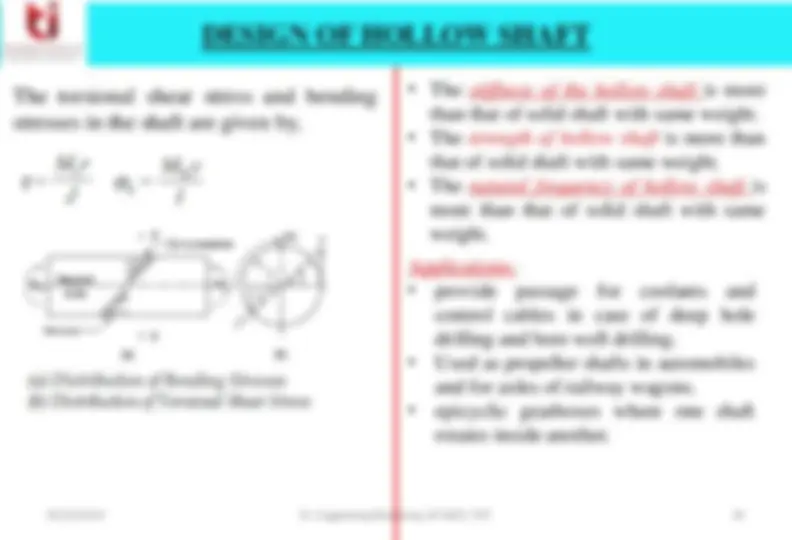
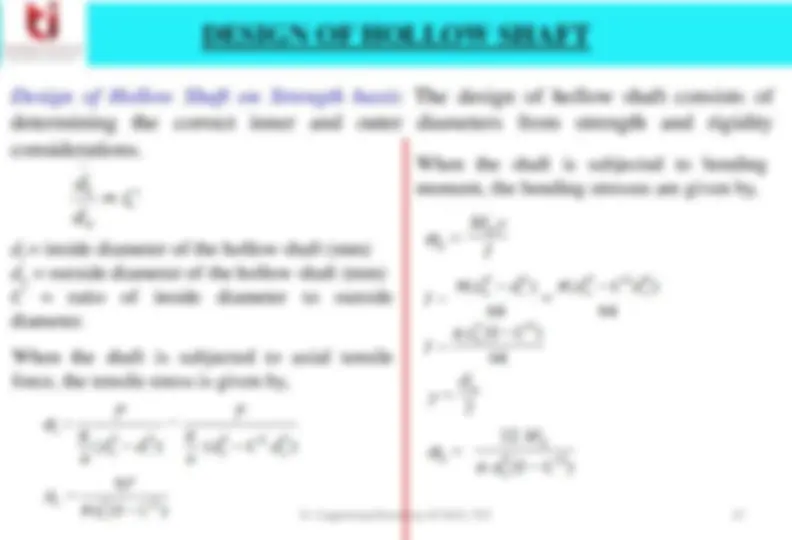
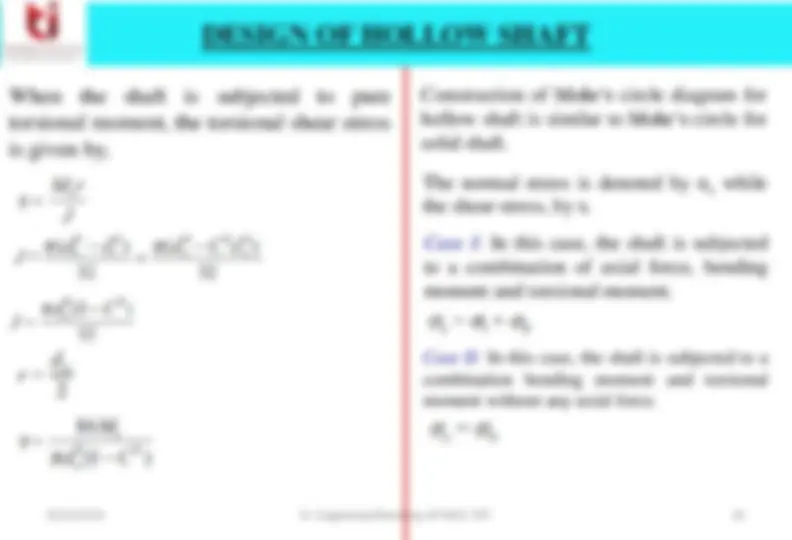
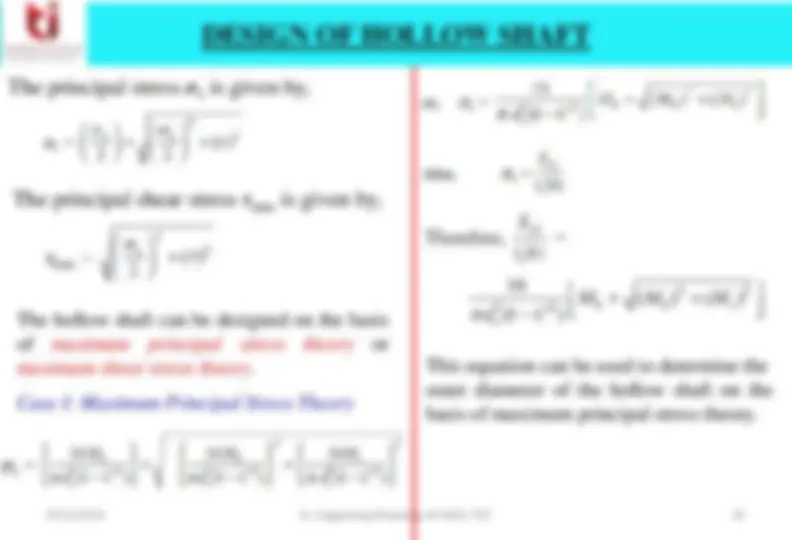
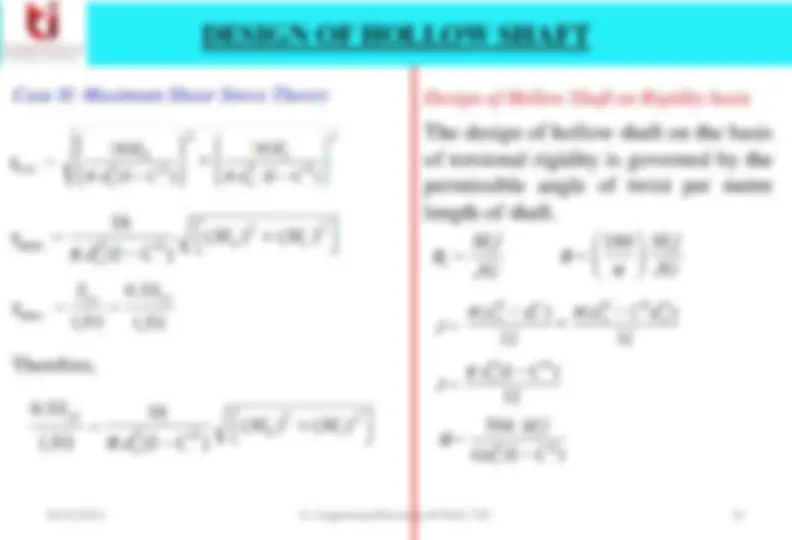
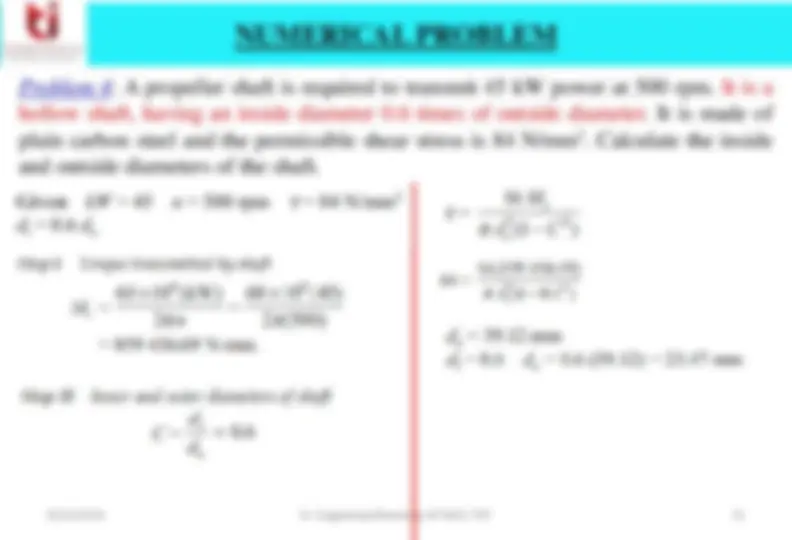
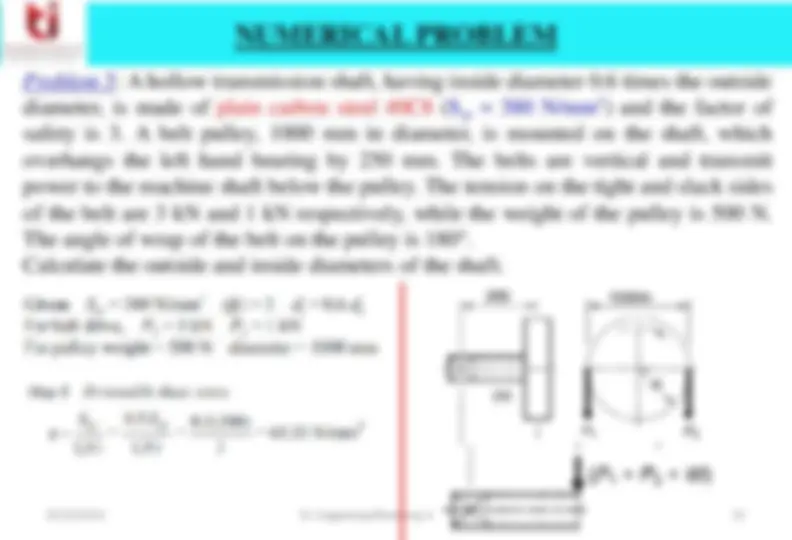
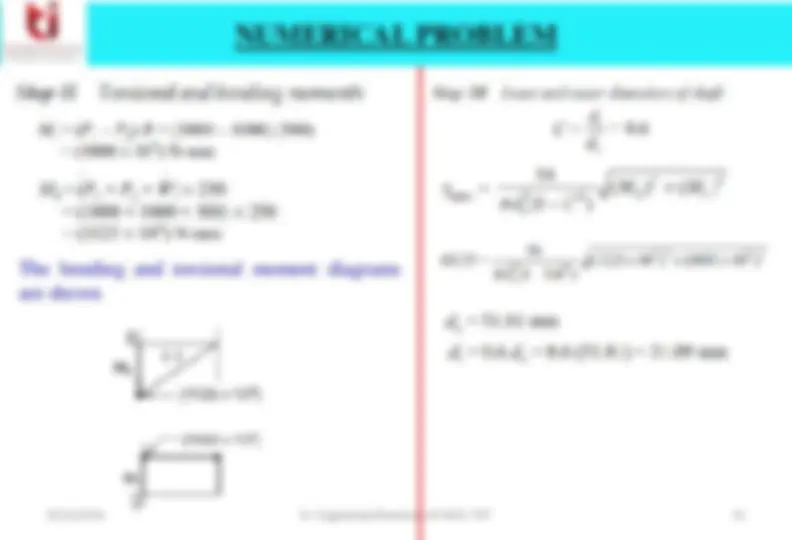
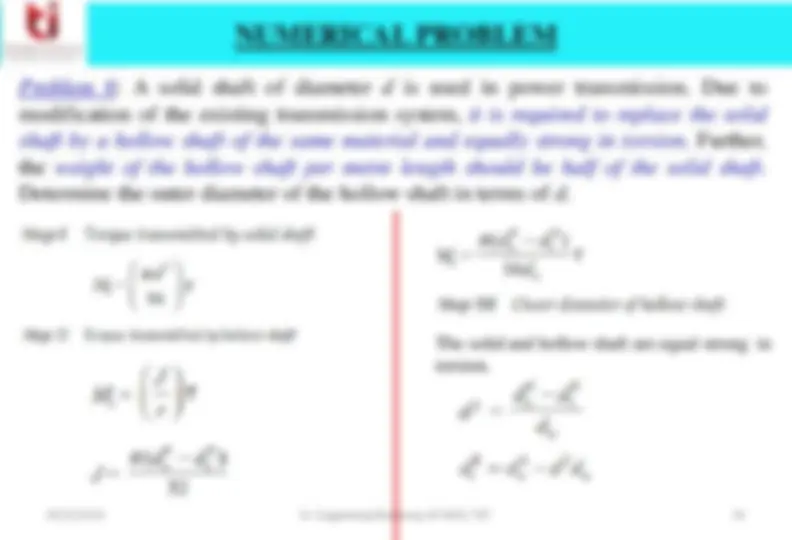
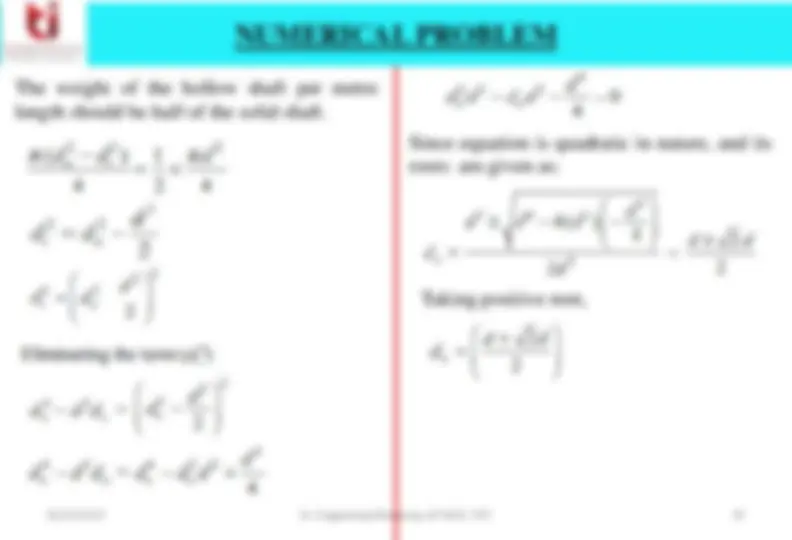
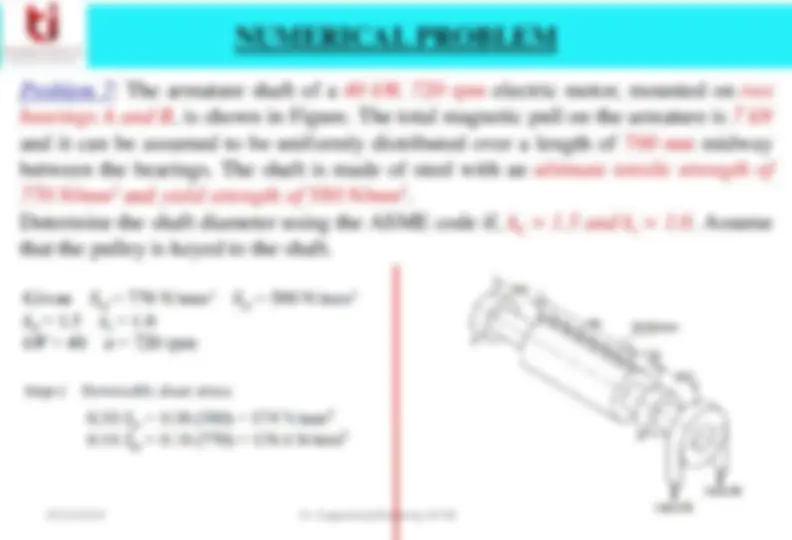
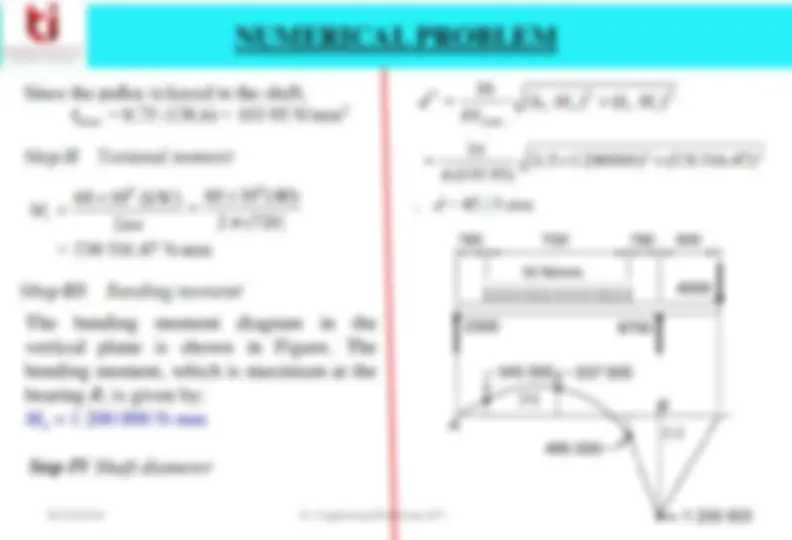
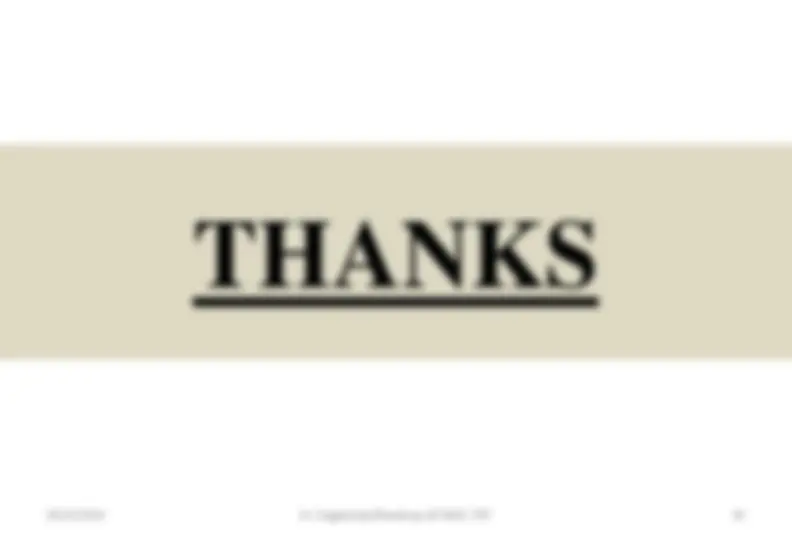
Study with the several resources on Docsity
Earn points by helping other students or get them with a premium plan
Prepare for your exams
Study with the several resources on Docsity
Earn points to download
Earn points by helping other students or get them with a premium plan
Community
Ask the community for help and clear up your study doubts
Discover the best universities in your country according to Docsity users
Free resources
Download our free guides on studying techniques, anxiety management strategies, and thesis advice from Docsity tutors
design of shaft against different loadings
Typology: Lecture notes
1 / 38
This page cannot be seen from the preview
Don't miss anything!
Prepared by: Dr. Gagandeep Bhardwaj, Assistant Professor, MED Email: gagandeep.med@thapar.edu Contact No. 8954388548
Line shaft: A line shaft consists of a number of shafts, which are connected in axial direction by means of couplings. Line shafts were popular in workshops using group drive. In group drive construction, a single electric motor drives the line shaft. A number of pulleys are mounted on the line shaft and power is transmitted to individual machines by different belts.
Transmission shafts are subjected to: axial tensile force, bending moment or torsional moment and their combinations. The design of transmission shaft consists of determining the correct shaft diameter from strength and rigidity considerations.
Design of Shaft on Strength Basis : When the shaft is subjected to axial tensile force, the tensile stress is given by,
When the shaft is subjected to pure bending moment, the bending stresses are given by,
Case I: In this case, the shaft is subjected to a combination of axial force, bending moment and torsional moment.
Case II: In this case, the shaft is subjected to a combination bending moment and torsional moment without any axial force.
The principal stress σ 1 is given by,
The principal shear stress τ max is given by,
The shaft can be designed on the basis of maximum principal stress theory or maximum shear stress theory. We will apply these theories to transmission shaft subjected to combined bending and torsional moments.
(i) Maximum Principal Stress Theory: The maximum principal stress is σ 1. Since the shaft is subjected to bending and torsional moments without any axial force,
The permissible value of maximum principal stress is given by,
The maximum principal stress theory gives good predictions for brittle materials. Shafts are made of ductile material like steel and therefore, this theory is not applicable to shaft design.
Equivalent Torsional Moment:
The expression is called ‘ equivalent ’ torsional moment. The equivalent torsional moment is defined as the torsional moment, which when acting alone, will produce the same torsional shear stress in the shaft as under the combined action of bending moment ( Mb ) and torsional moment ( Mt ).
Equivalent Bending Moment:
The expression is called ‘ equivalent ’ bending moment. The equivalent bending moment is defined as the bending moment, which when acting alone, will produce the same bending stresses (tensile and compressive) in the shaft as under the combined action of bending moment ( Mb ) and torsional moment ( M t ).
Design of Shaft on Torsional Rigidity Basis :
Equivalent Torsional Moment
The expression is called ‘ equivalent ’ torsional moment when the shaft is subjected to fluctuating loads.
Equivalent Bending Moment
The expression is called ‘ equivalent ’ bending moment when the shaft is subjected to fluctuating loads.
Problem 1 : A solid circular shaft is subjected to a bending moment of 3000 N-m and a torque of 10000 N-m. The shaft is made of 45C8 steel having ultimate tensile stress of 700 MPa and a ultimate shear stress of 500 MPa. Assuming a factor of safety as 6, determine the diameter of the shaft.
Given: M = 3000 N-m = 3 × 106 N-mm; T = 10 000 N-m = 10 × 106 N-mm; σ tu = 700 MPa = 700 N/mm^2 ; τ u = 500 MPa = 500 N/mm^2
Neglecting the weight of the pulley, the downward force at the pulley B is (P 1 + P 2 ) or 3676.47 N.
Similarly, the force in the horizontal plane at the pulley C is (P 3 + P 4 ) or 7352.94 N.
The force and bending moment in vertical plane
The force and bending moment in horizontal plane
The resultant bending moment is given by,
The resultant bending moment diagram and torsional moment diagram are shown