
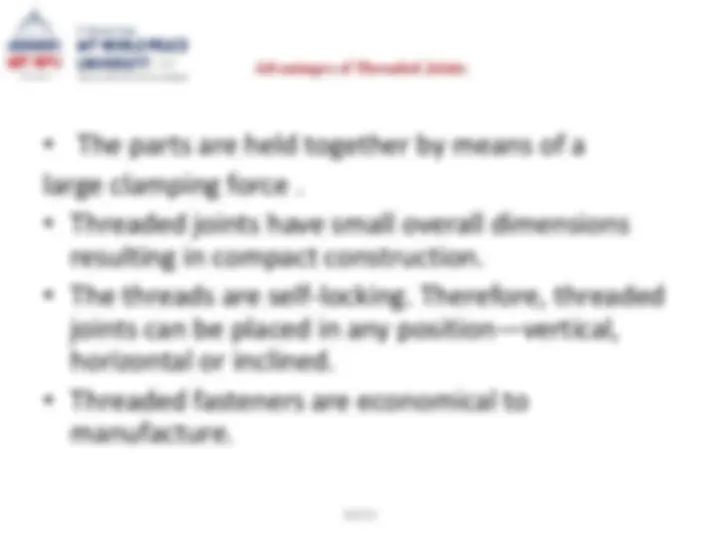
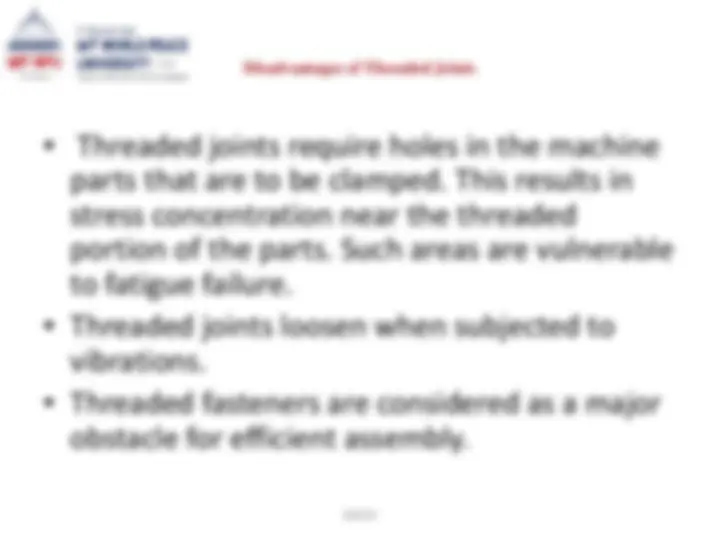
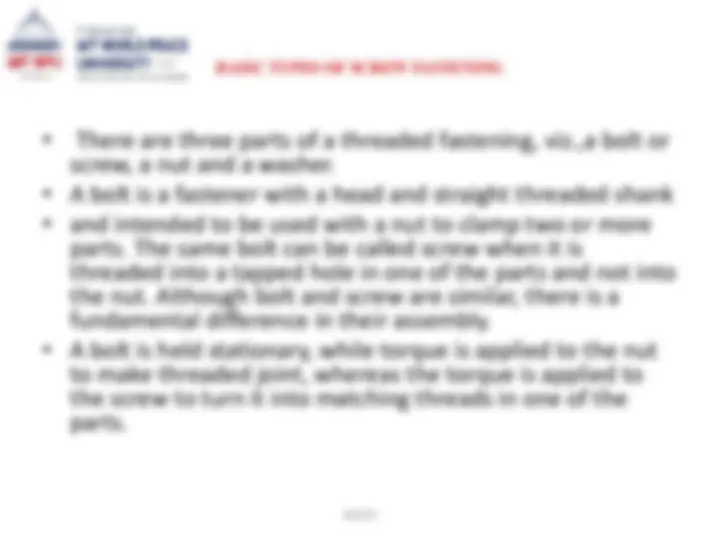
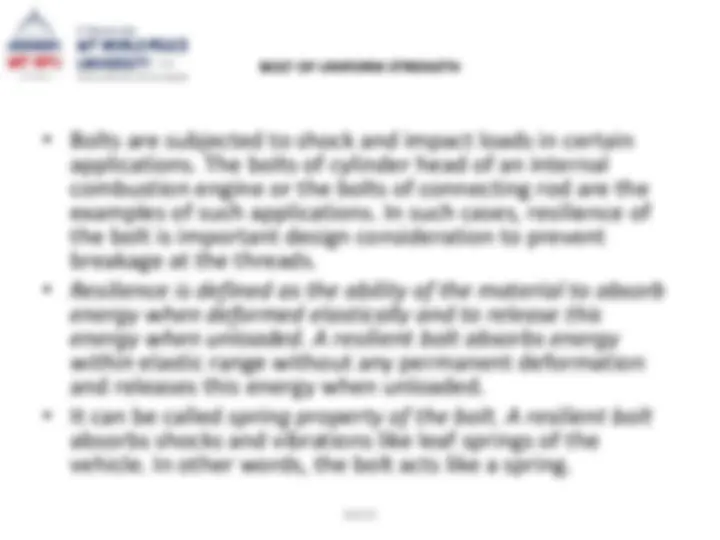
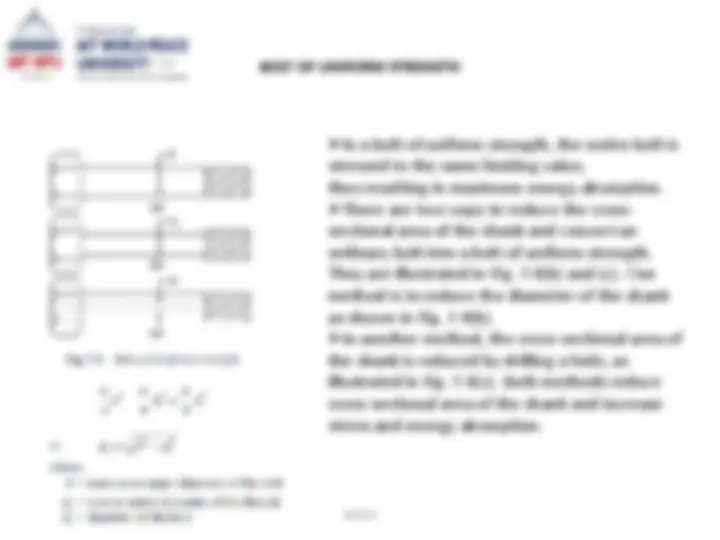
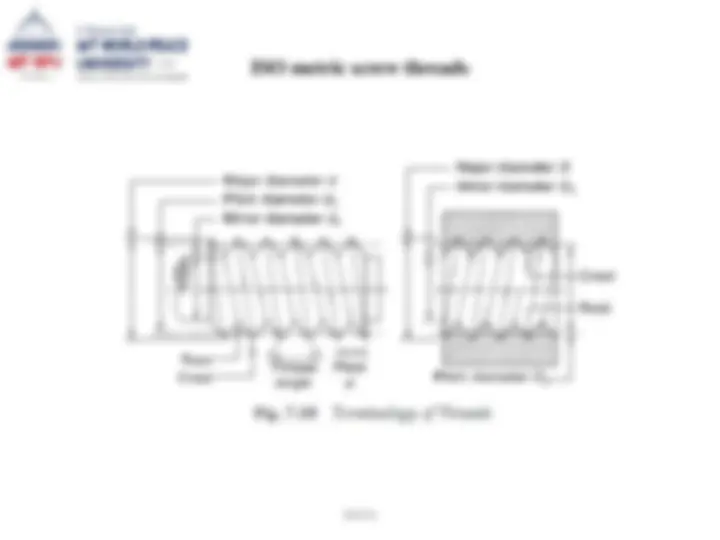
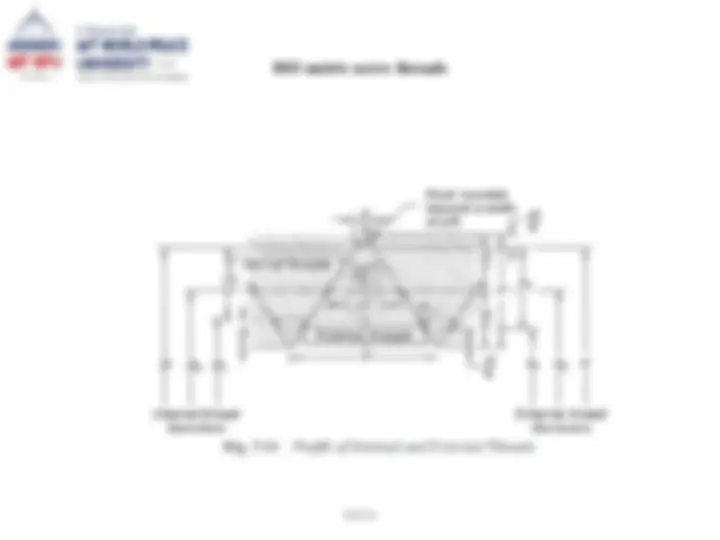
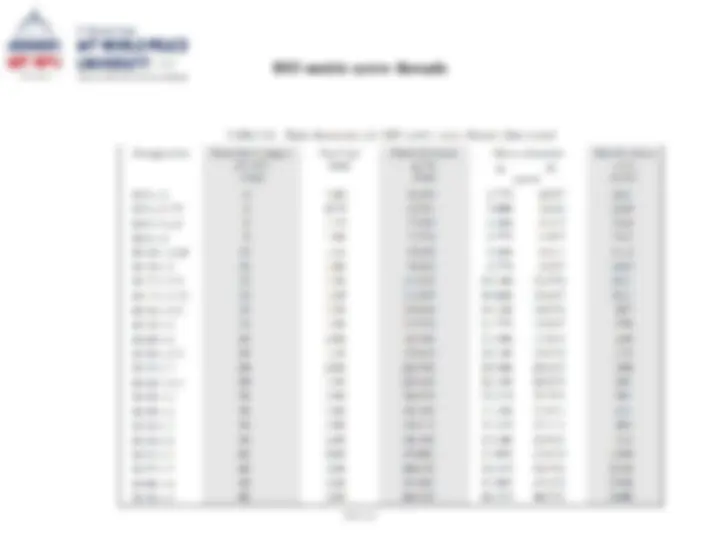
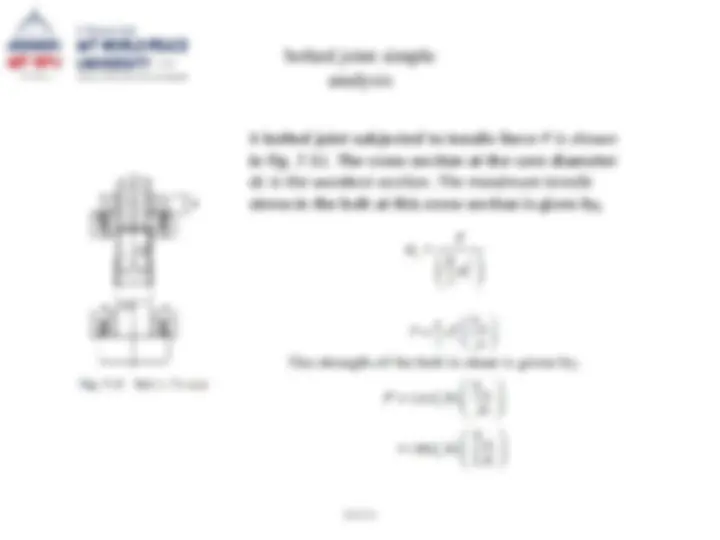
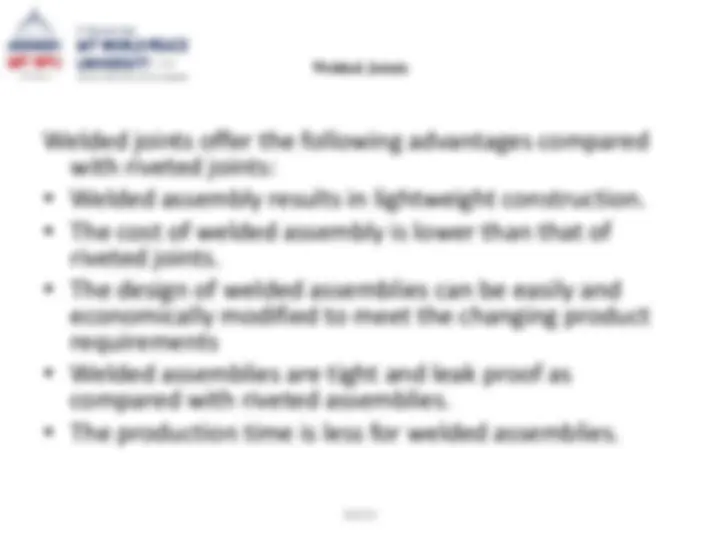
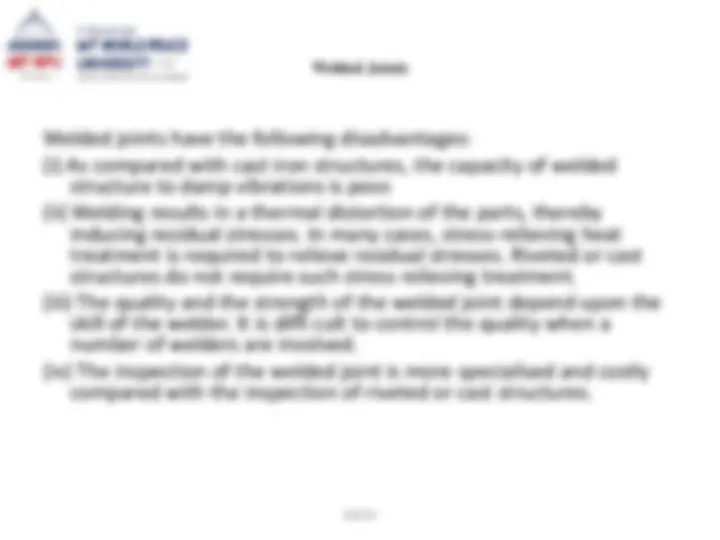
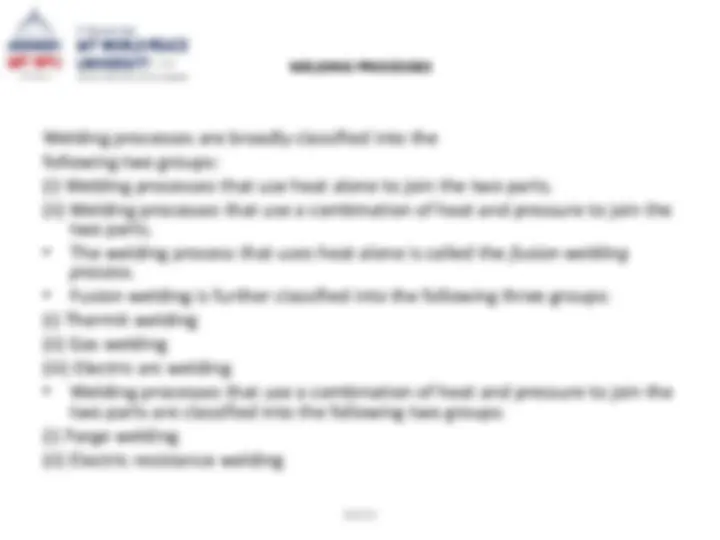
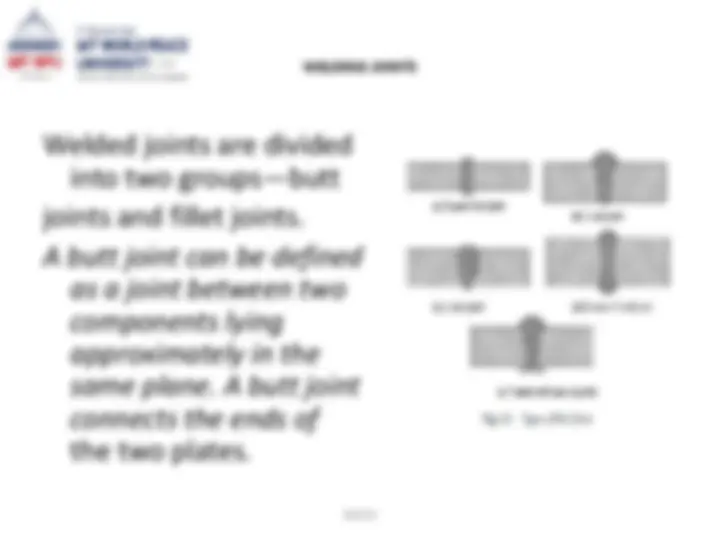
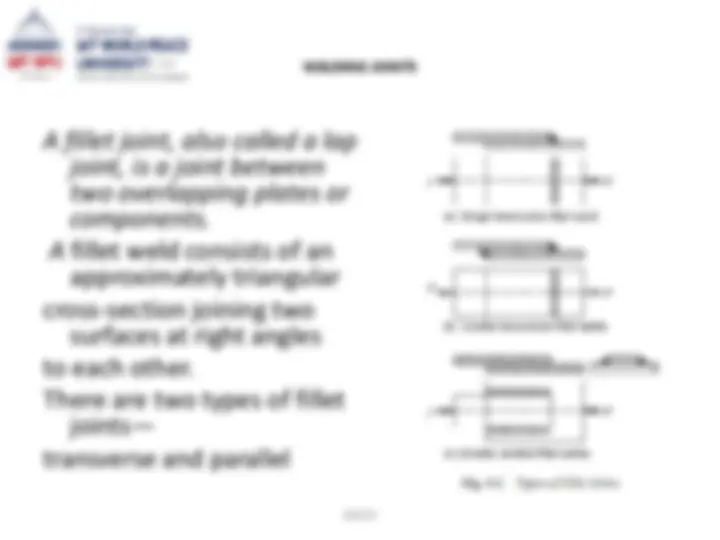
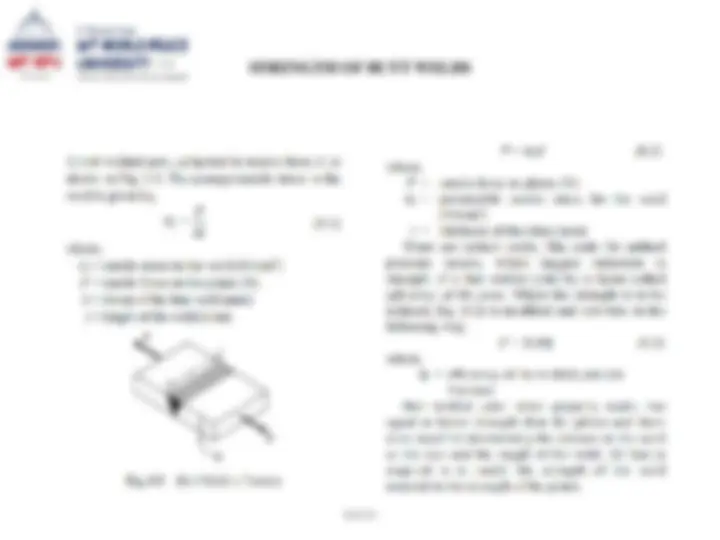
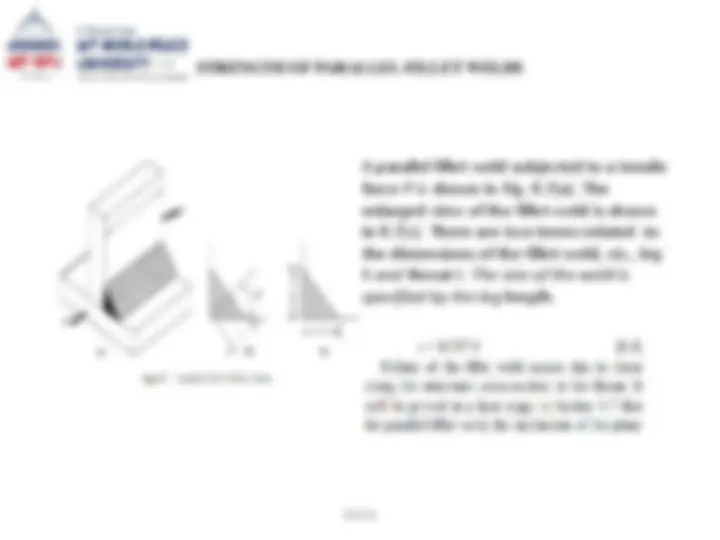
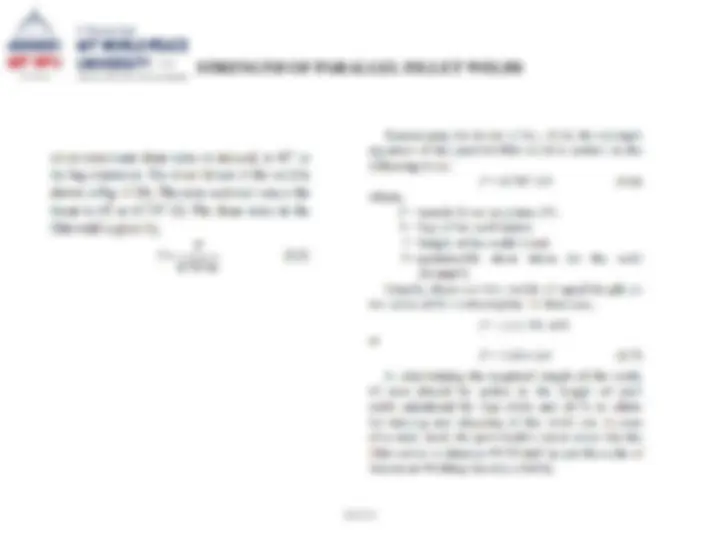

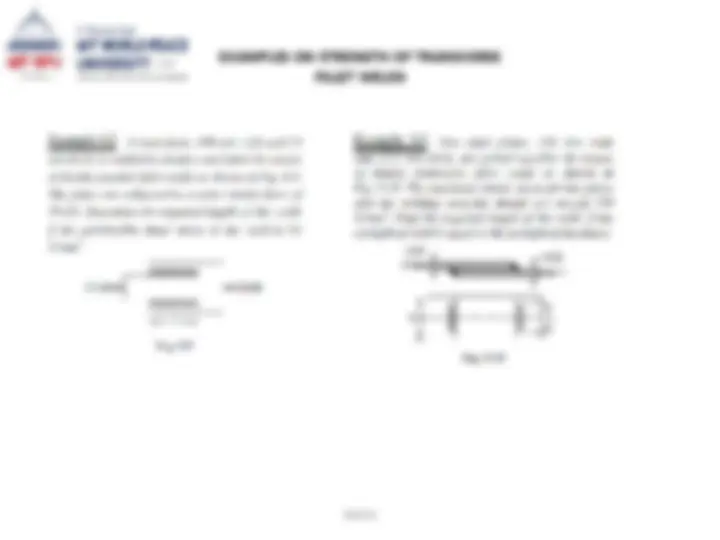
Study with the several resources on Docsity
Earn points by helping other students or get them with a premium plan
Prepare for your exams
Study with the several resources on Docsity
Earn points to download
Earn points by helping other students or get them with a premium plan
Community
Ask the community for help and clear up your study doubts
Discover the best universities in your country according to Docsity users
Free resources
Download our free guides on studying techniques, anxiety management strategies, and thesis advice from Docsity tutors
For 3D printing mechanisms you need understand how gears, shafts, bearings, linkages, joints etc works
Typology: Summaries
1 / 27
This page cannot be seen from the preview
Don't miss anything!
Disadvantages of Threaded Joints
BASIC TYPES OF SCREW FASTENING
BASIC TYPES OF SCREW FASTENING
BOLT OF UNIFORM STRENGTH
Basic Definitions (i)Major Diameter : The major diameter is the diameter of an imaginary cylinder that bounds the crest of an external thread ( d). (ii) Minor Diameter : The minor diameter is the diameter of an imaginary cylinder that bounds the roots of an external thread ( dc) or the crest of an internal thread ( Dc). The minor diameter is the smallest diameter of the screw thread. It is also called core or root diameter of the thread. (iii) Pitch Diameter : The pitch diameter is the diameter of an imaginary cylinder, the surface of which would pass through the threads at such points as to make the width of the threads equal to the width of spaces cut by the surface of the cylinder. It is also called the effective diameter of the thread. (iv) Pitch : Pitch is the distance between two similar points on adjacent threads measured parallel to the axis of the thread. It is denoted by the letter p. (v) Lead : Lead is the distance that the nut moves parallel to the axis of the screw, when the nut is given one turn. (vi) Thread Angle: Thread angle is the angle included between the sides of the thread measured in an axial plane. Thread angle is 60o for ISO metric threads.
ISO metric screw threads
ISO metric screw threads
Examples Example 1: An electric motor weighing 10 kN is lifted by means of an eye bolt as shown in Fig. 7.13. The eye bolt is screwed into the frame of the motor. The eye bolt has coarse threads. It is made of plain carbon steel 30C8 (Syt = 400 N/mm2) and the factor of safety is 6. Determine the size of the bolt. Example 7.2 Two plates are fastened by means of two bolts as shown in Fig. 7.14. The bolts are made of plain carbon steel 30C8 (Syt = 400 N/mm2) and the factor of safety is 5. Determine the size of the bolts if,
Welded Joints
Welded Joints Welded joints have the following disadvantages: (i) As compared with cast iron structures, the capacity of welded structure to damp vibrations is poor. (ii) Welding results in a thermal distortion of the parts, thereby inducing residual stresses. In many cases, stress-relieving heat treatment is required to relieve residual stresses. Riveted or cast structures do not require such stress relieving treatment. (iii) The quality and the strength of the welded joint depend upon the skill of the welder. It is diffi cult to control the quality when a number of welders are involved. (iv) The inspection of the welded joint is more specialised and costly compared with the inspection of riveted or cast structures.
WELDING PROCESSES