
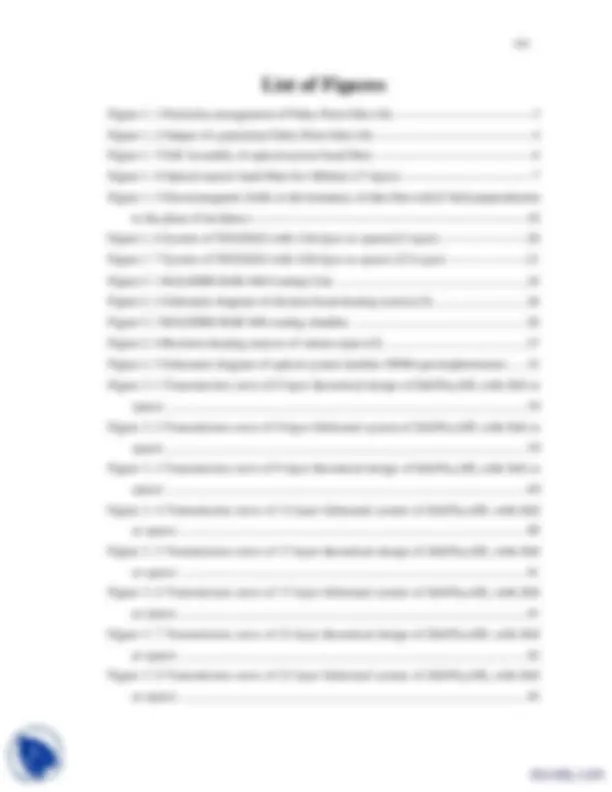
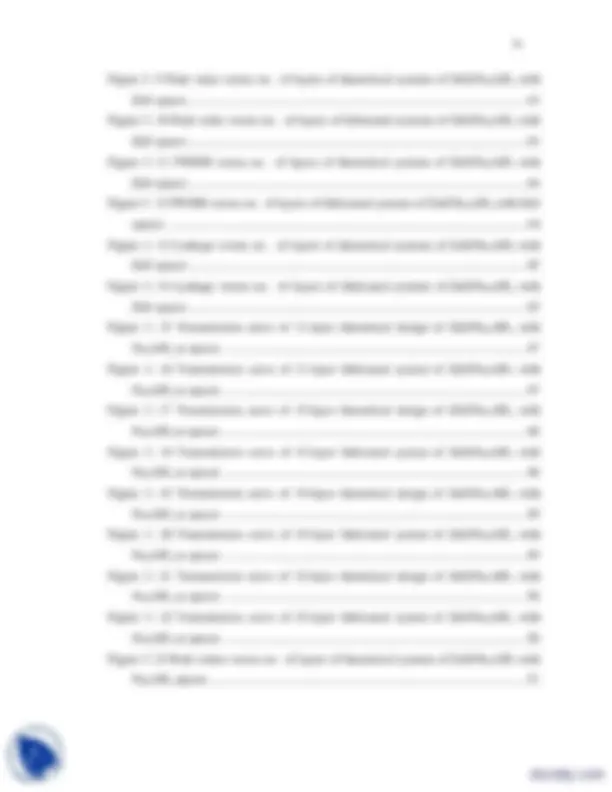
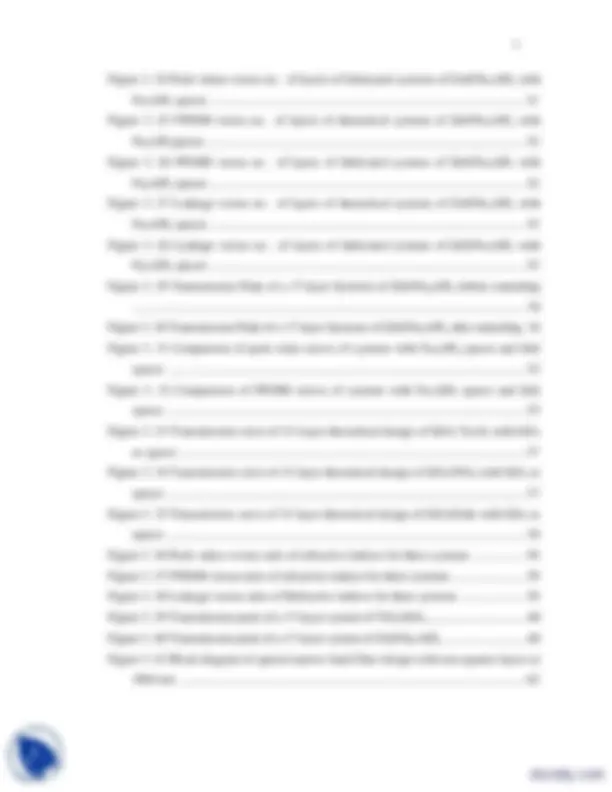
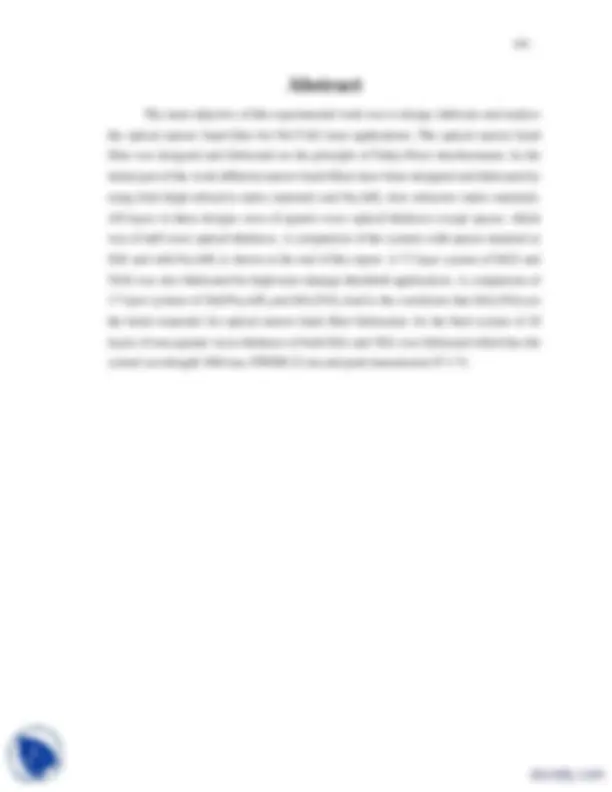
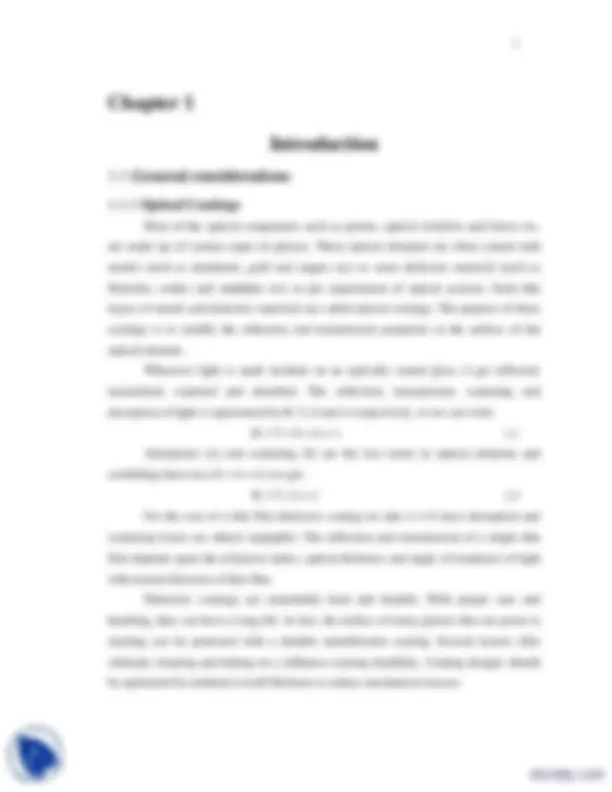
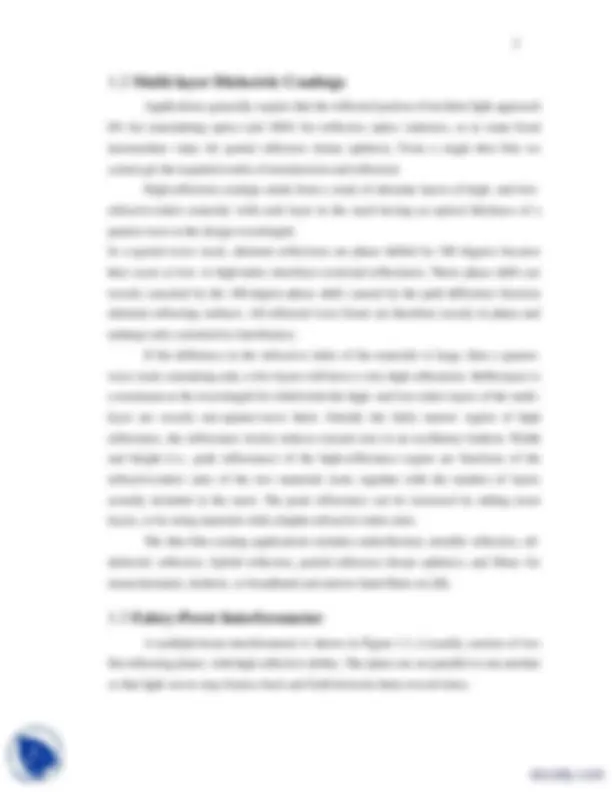
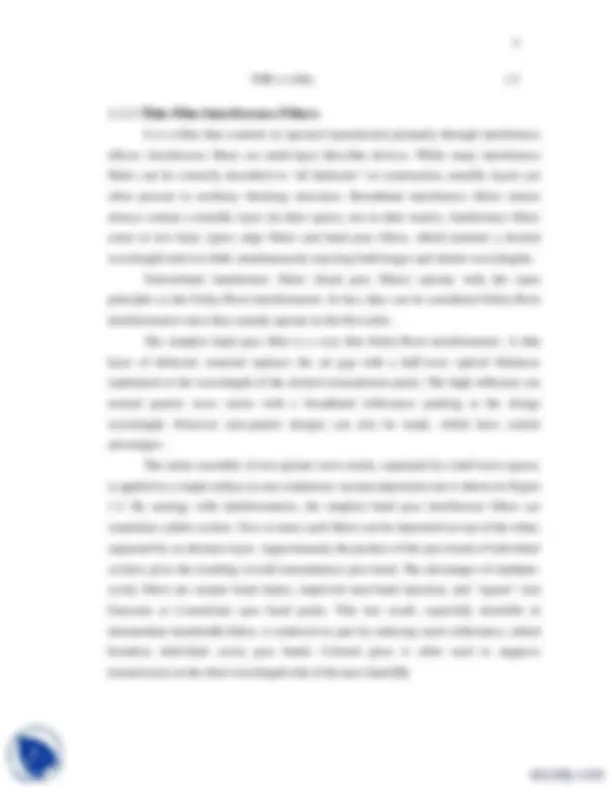
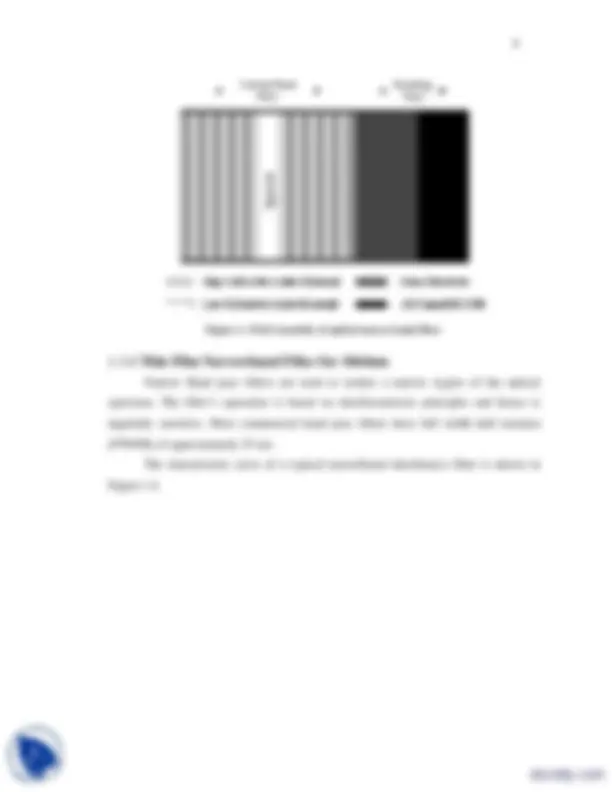
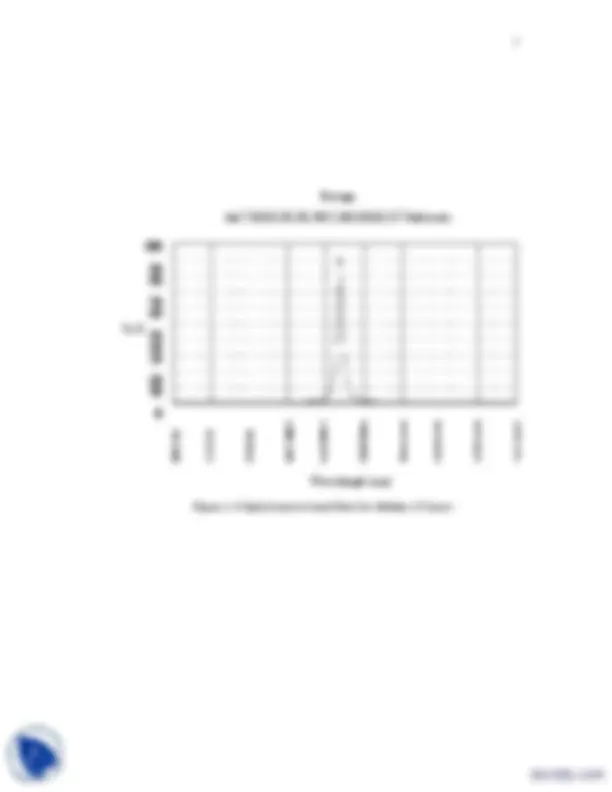
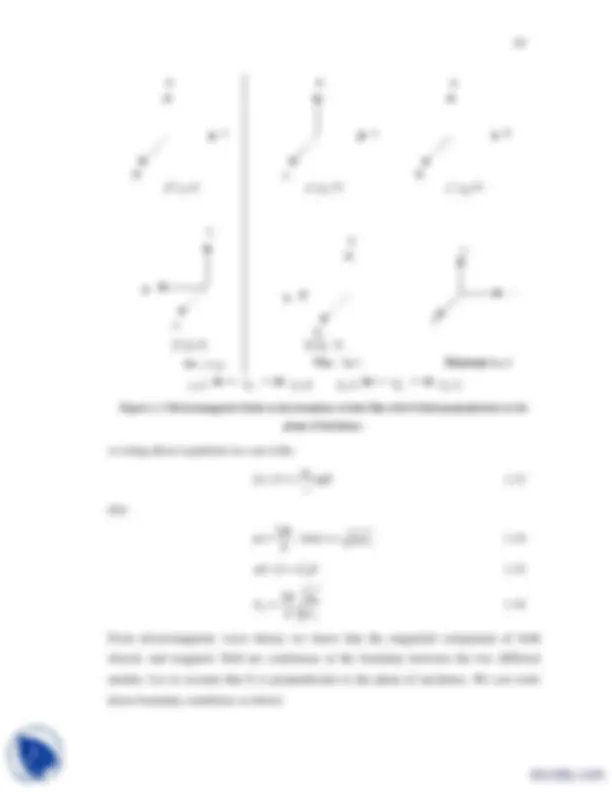
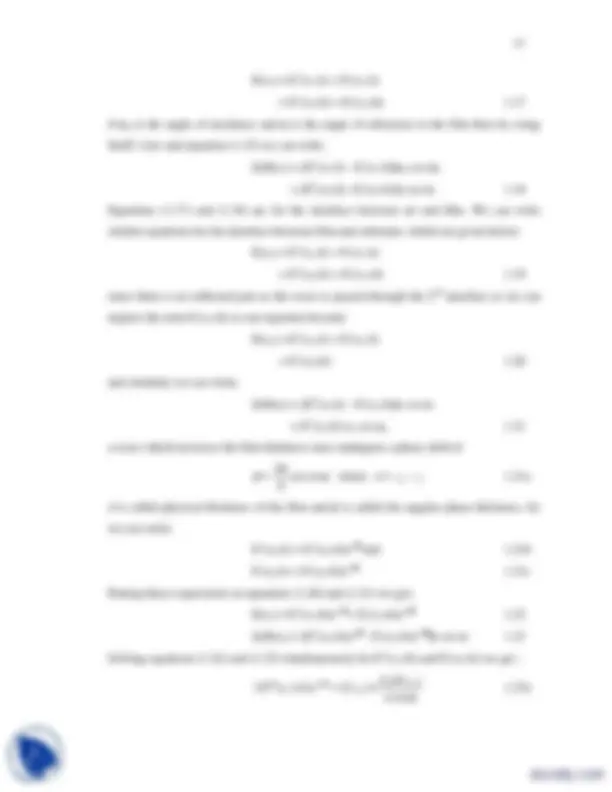
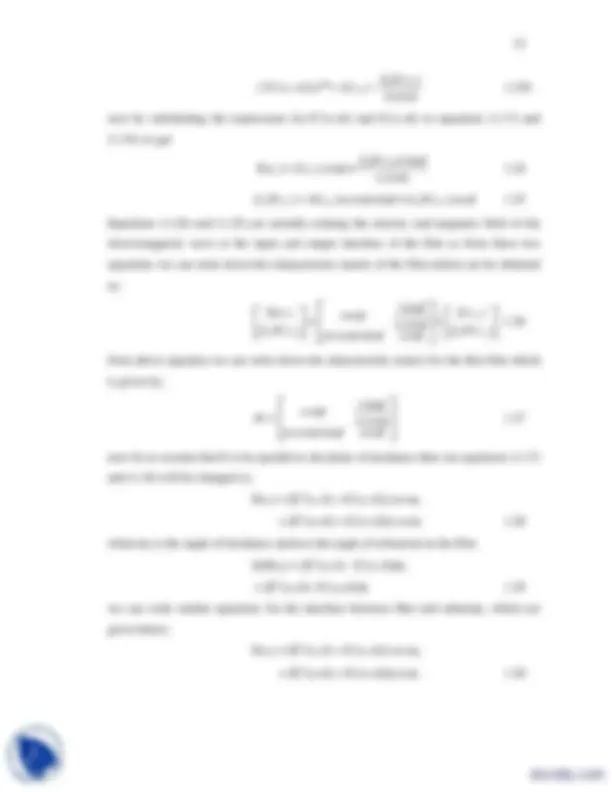
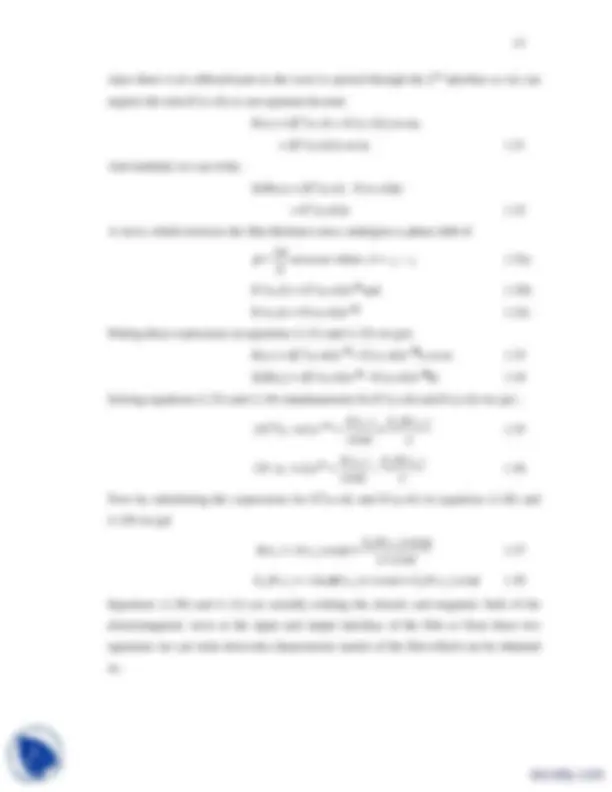
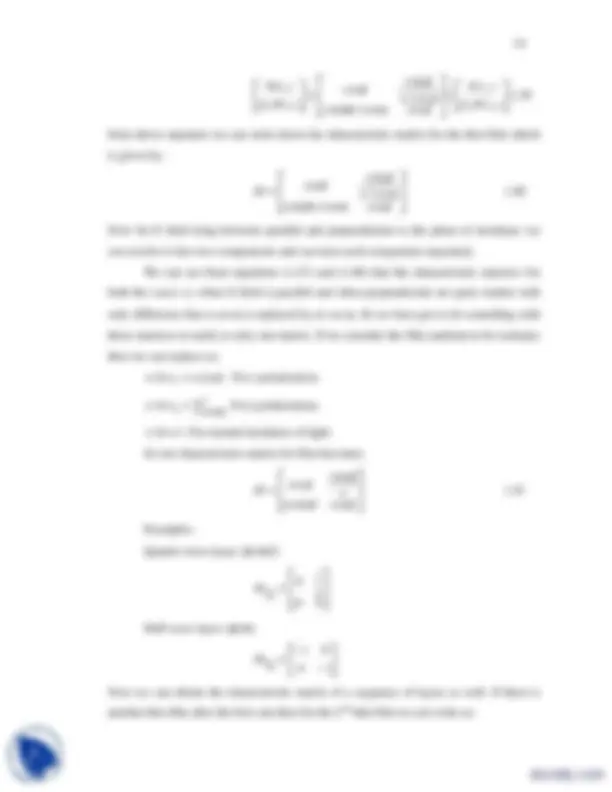
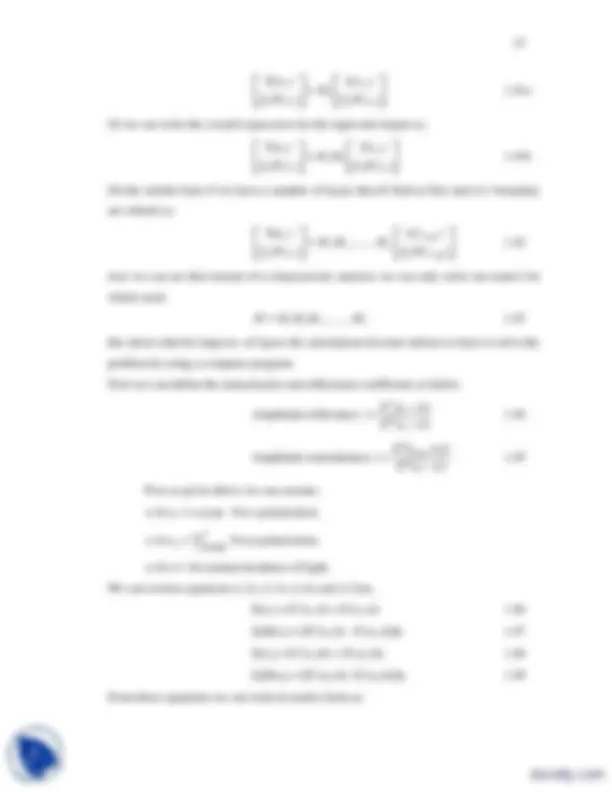
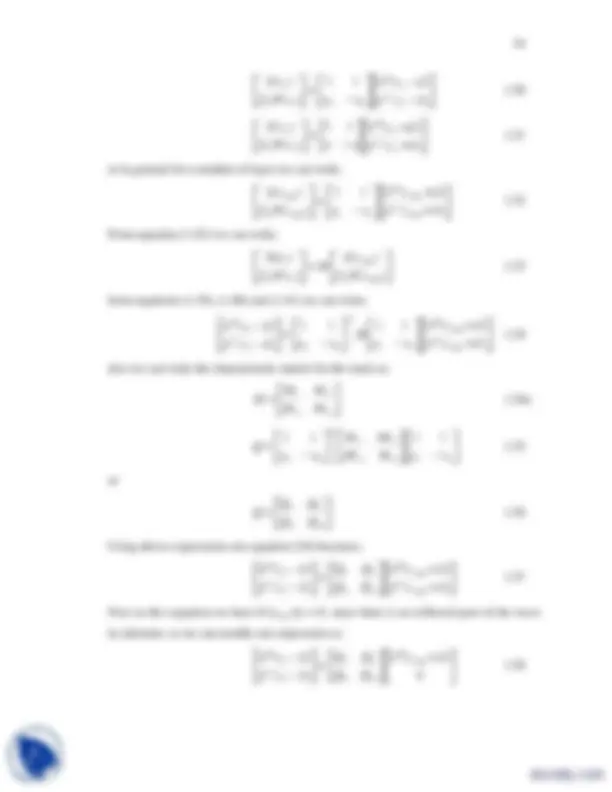
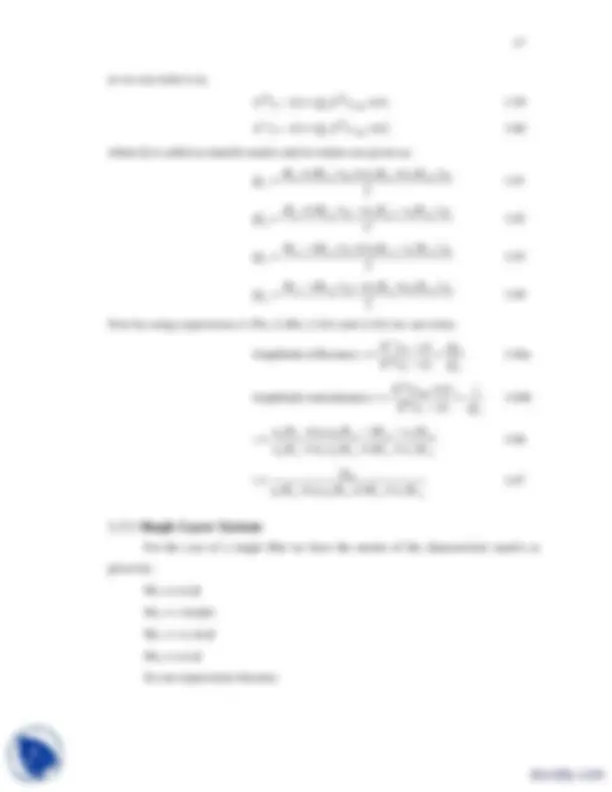
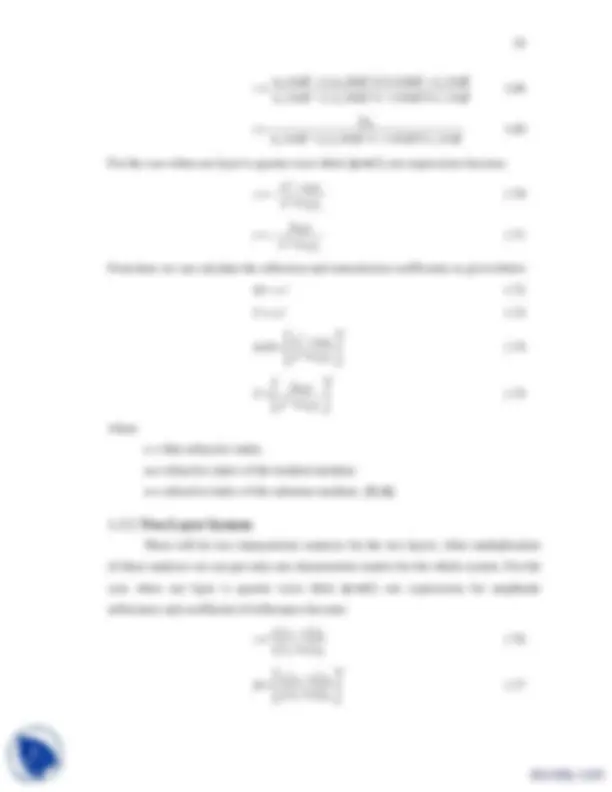
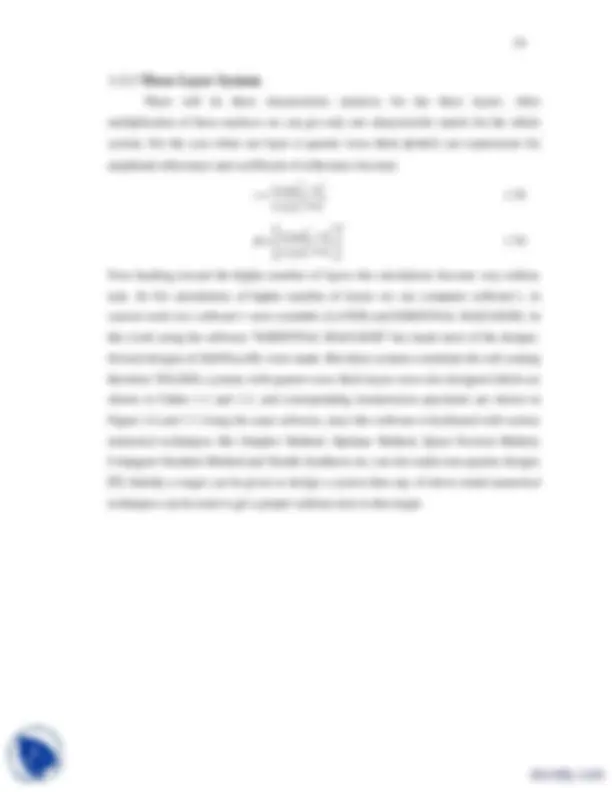
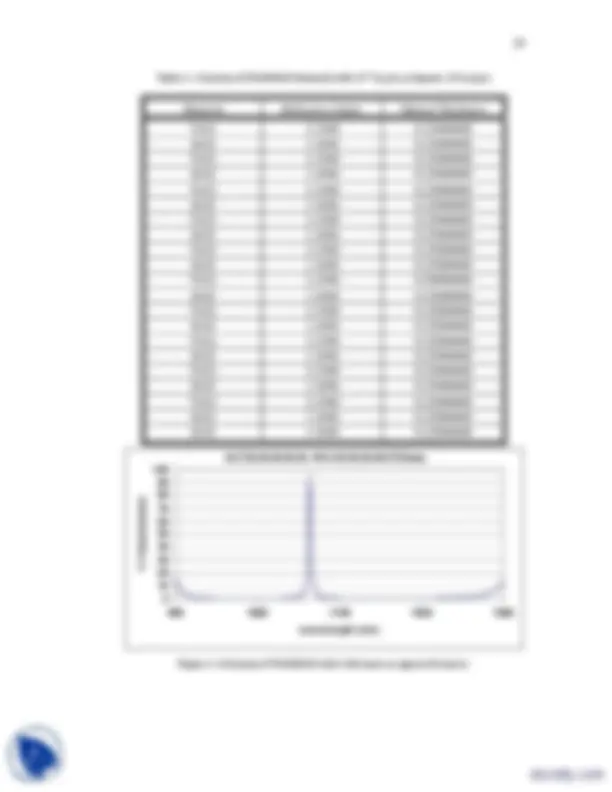
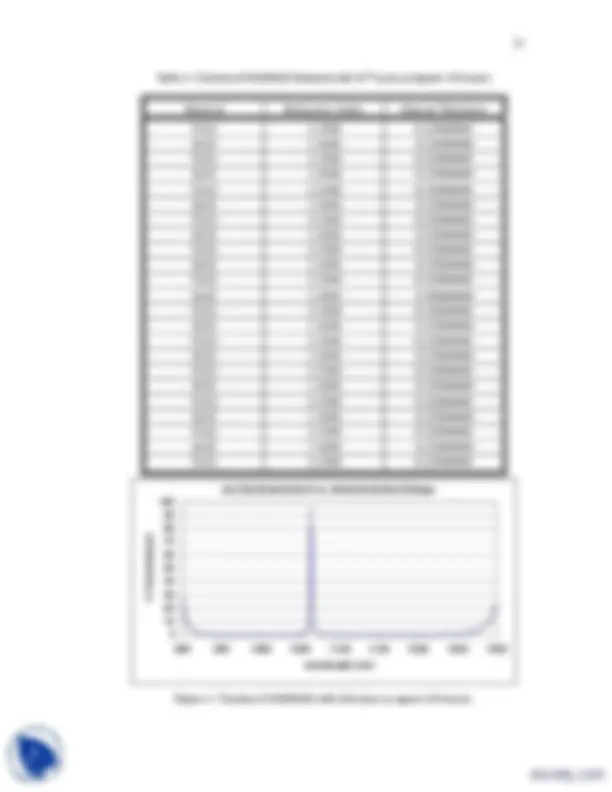
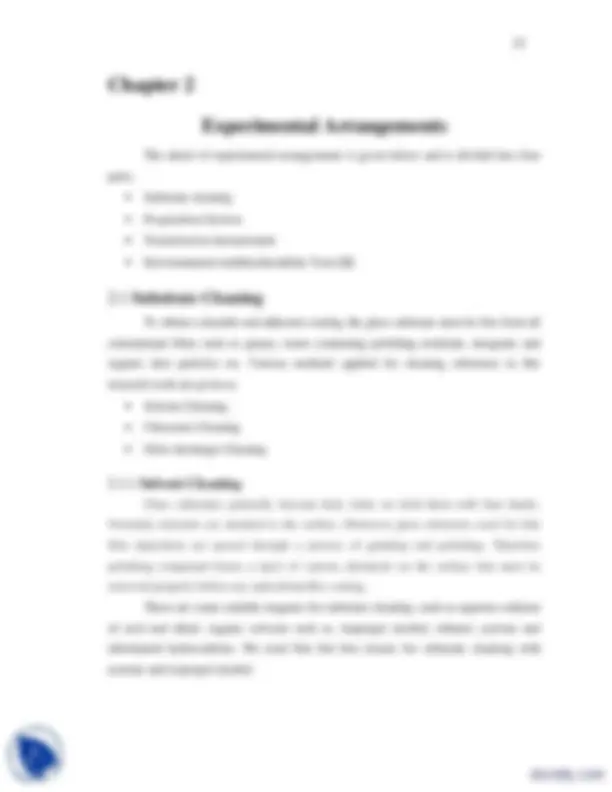
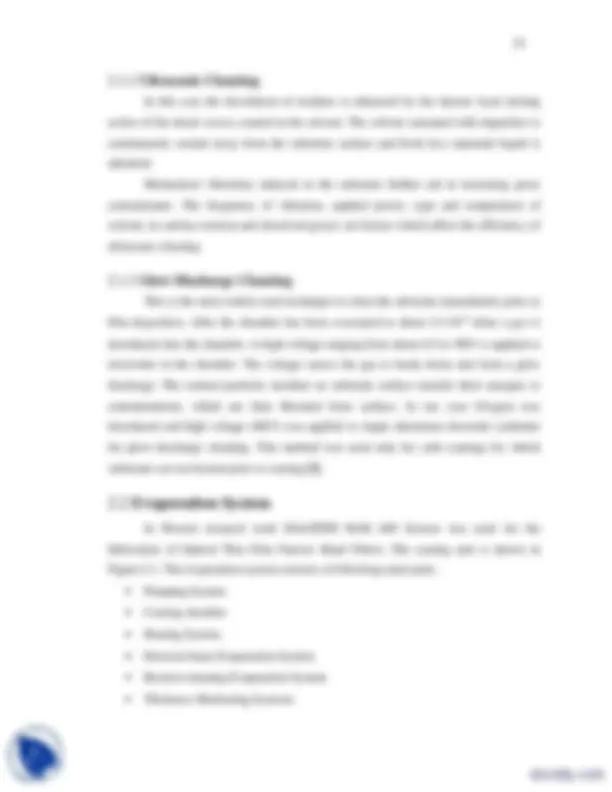
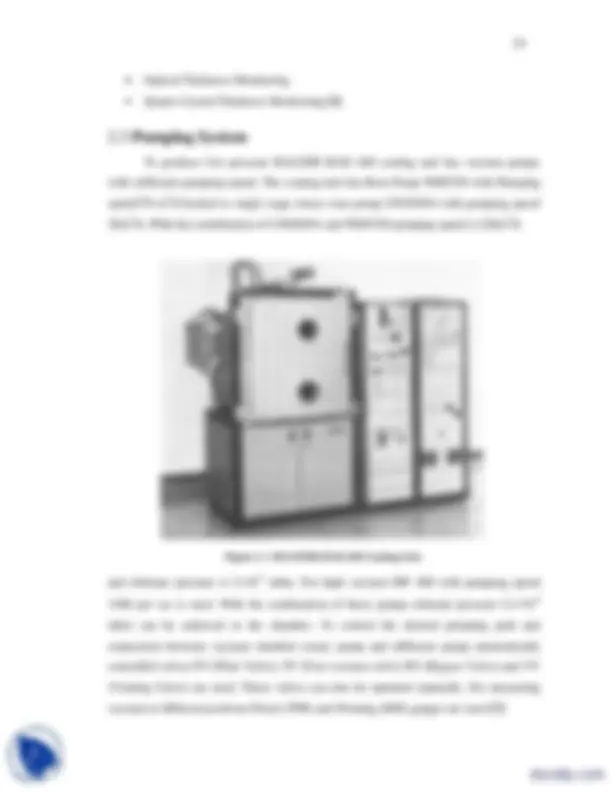
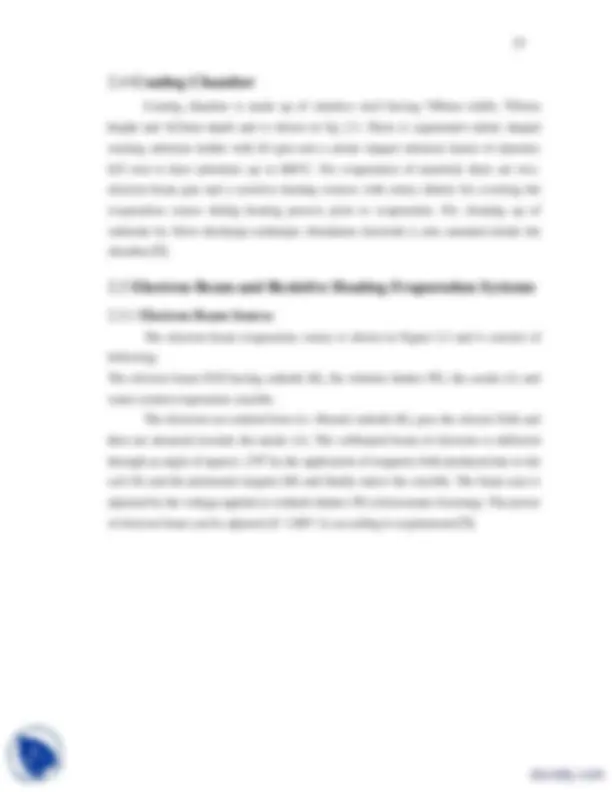
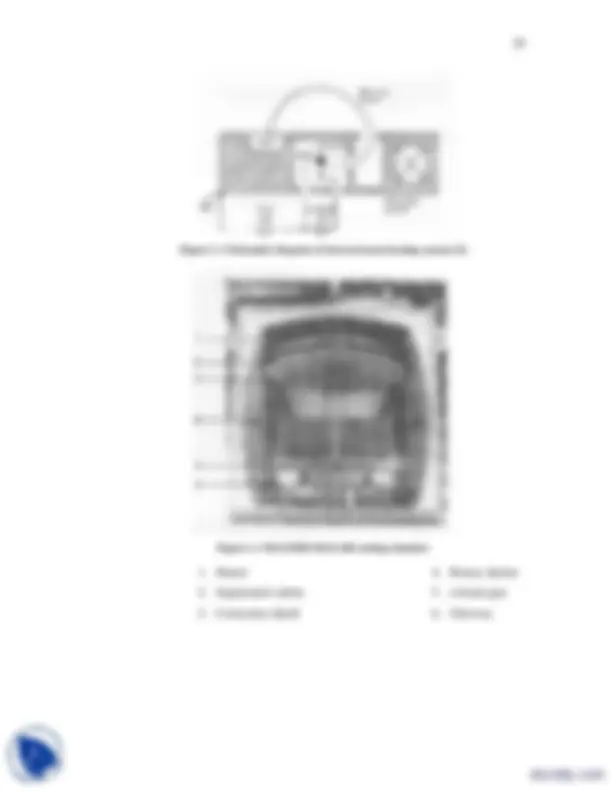
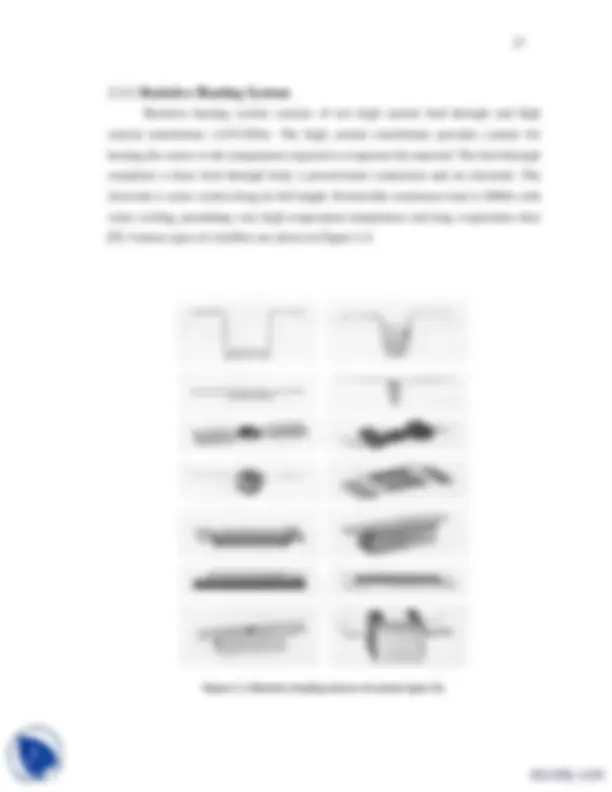
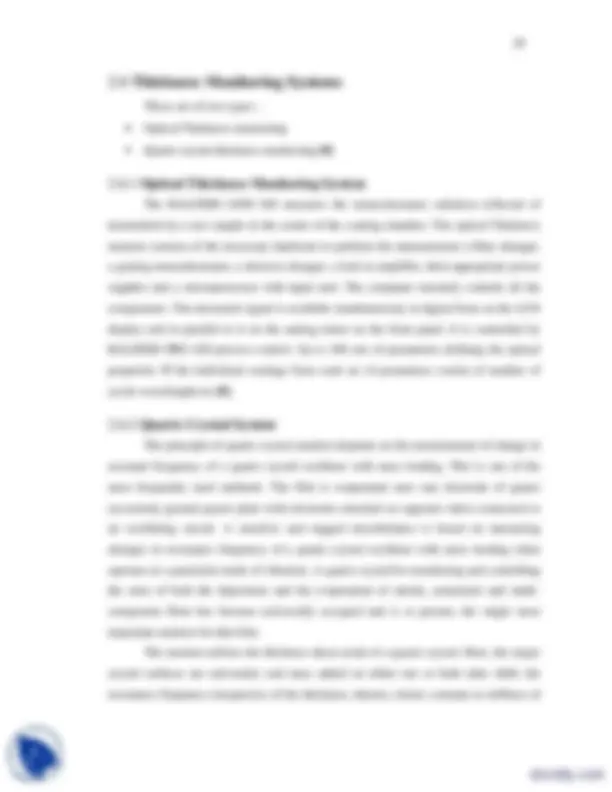
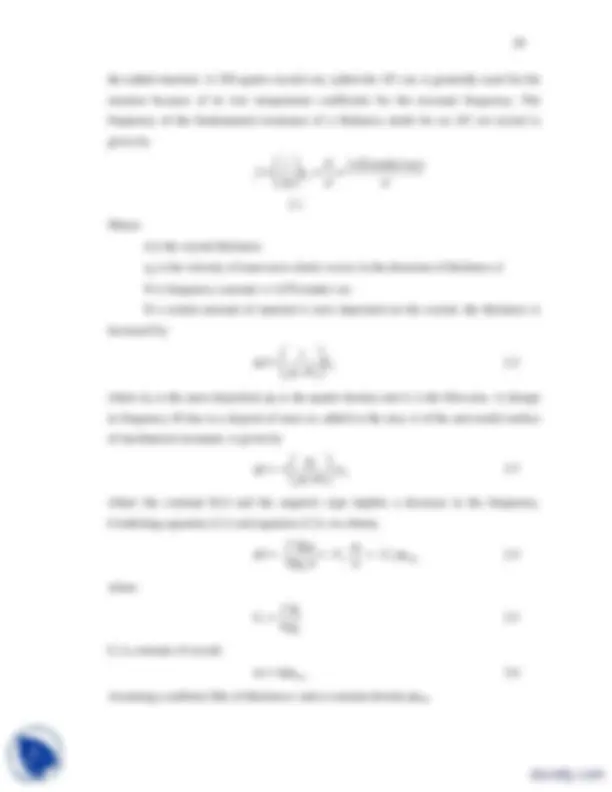
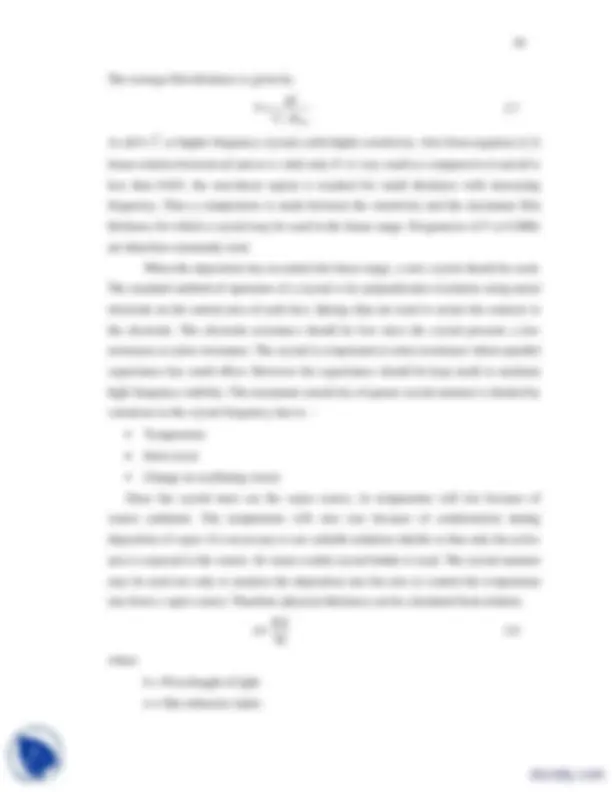
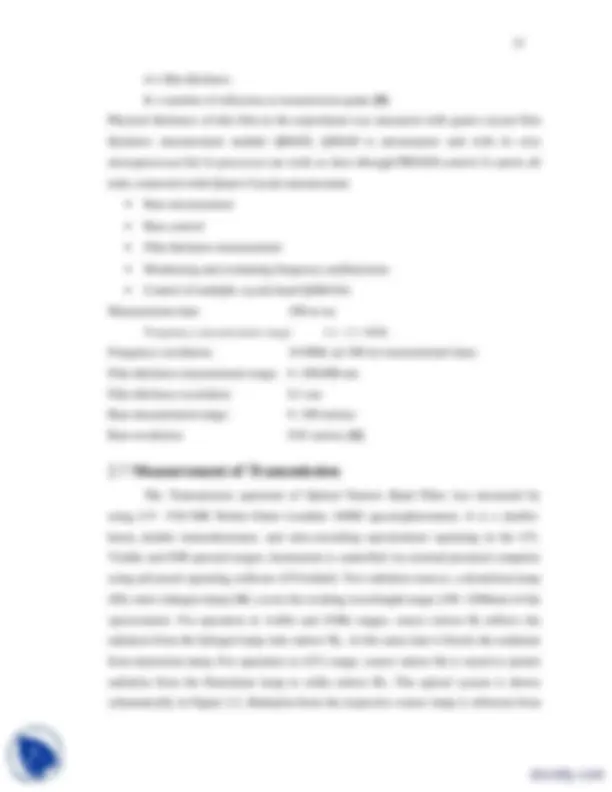
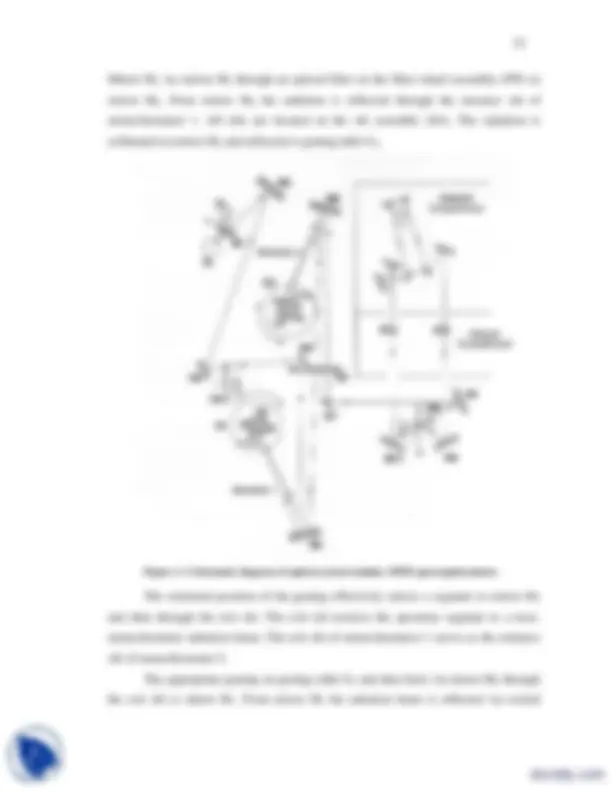
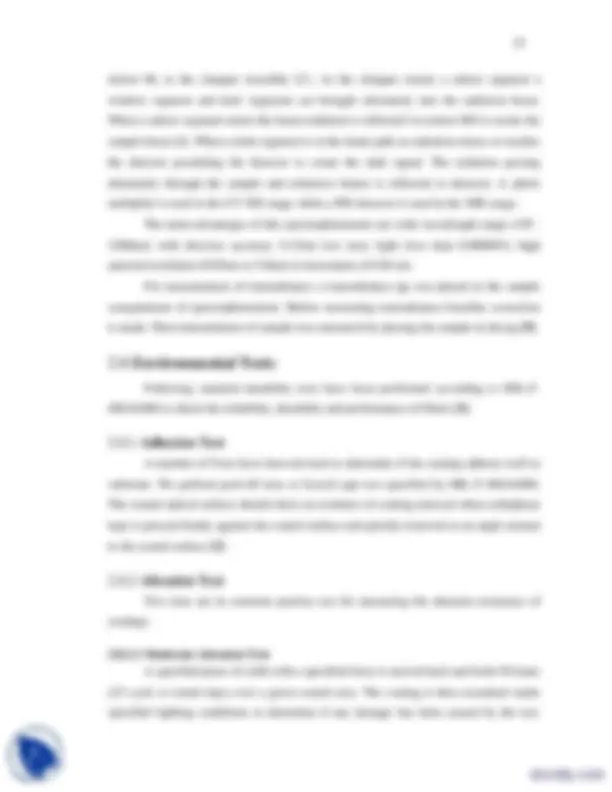
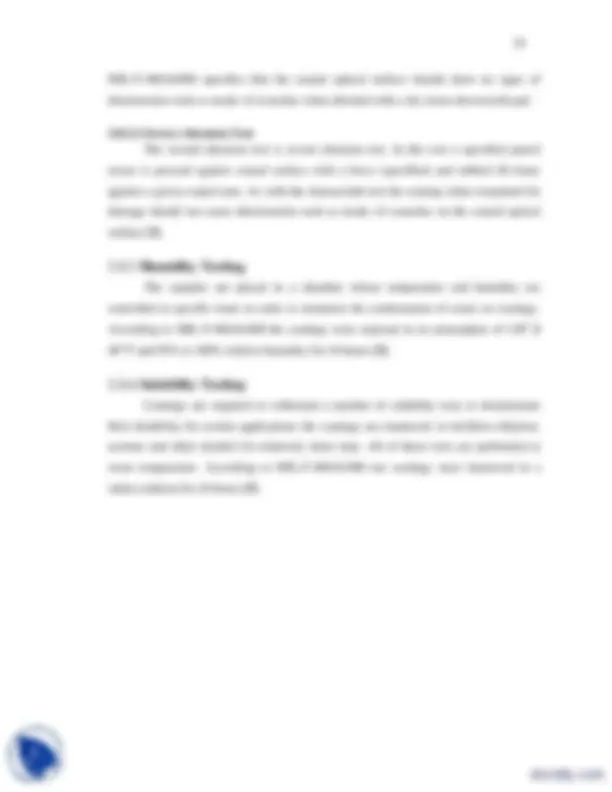
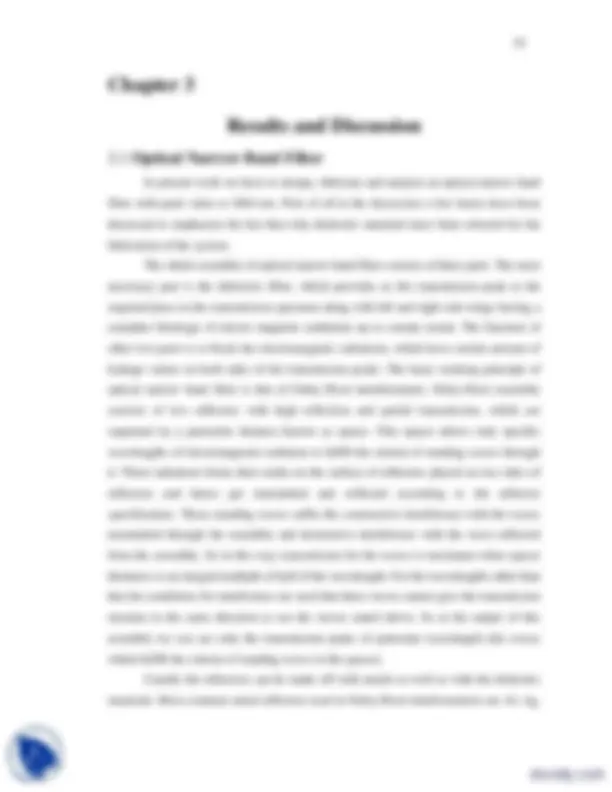
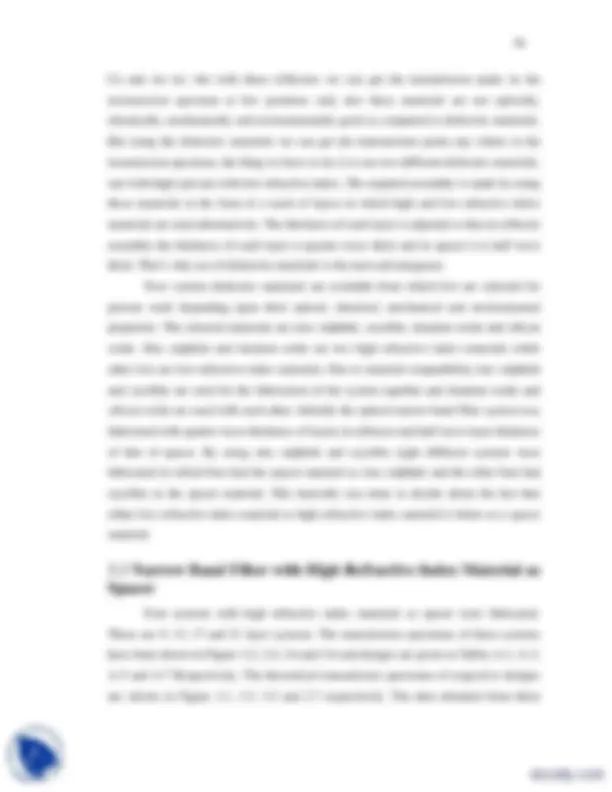
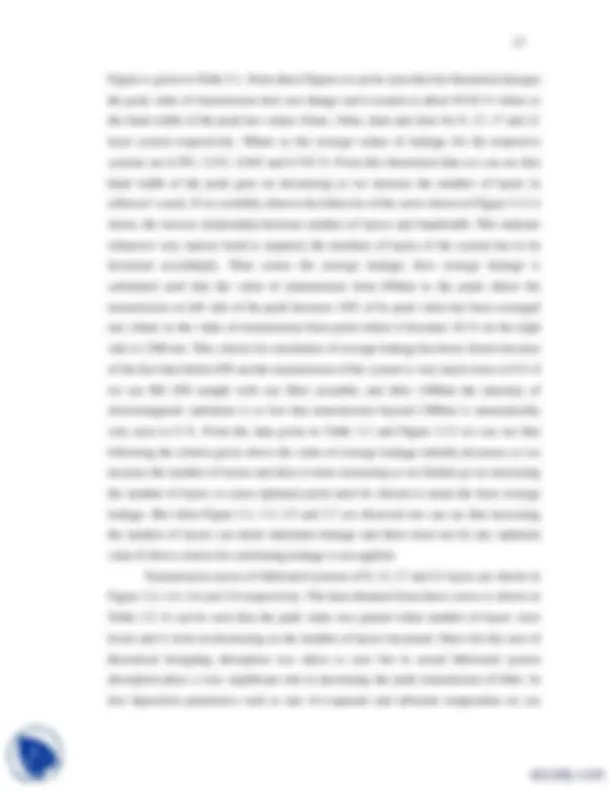
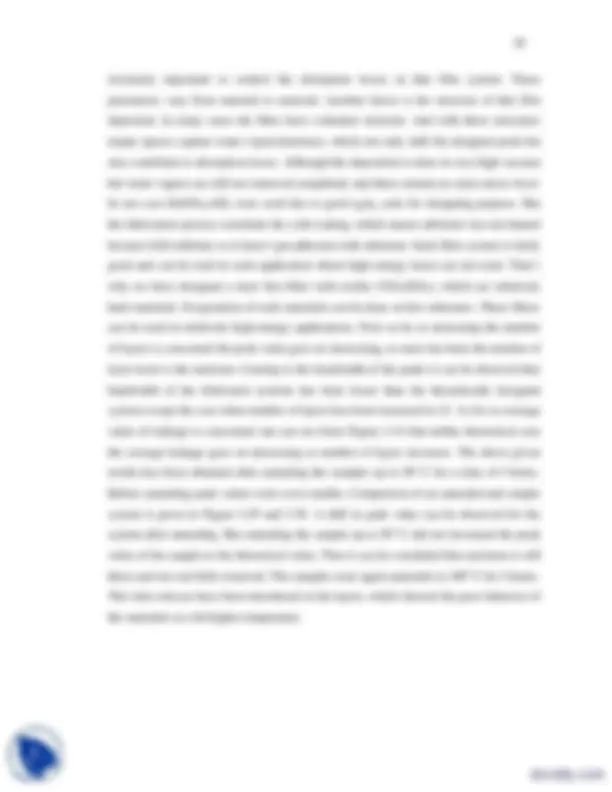
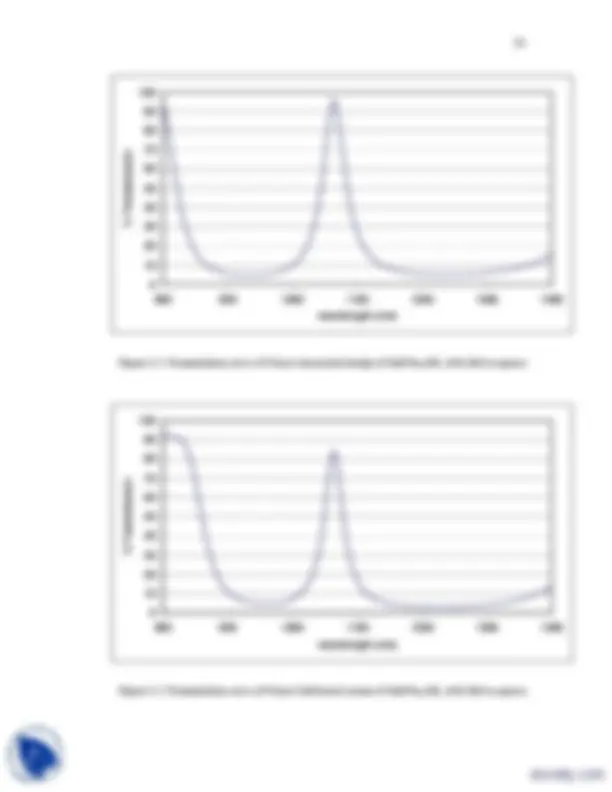
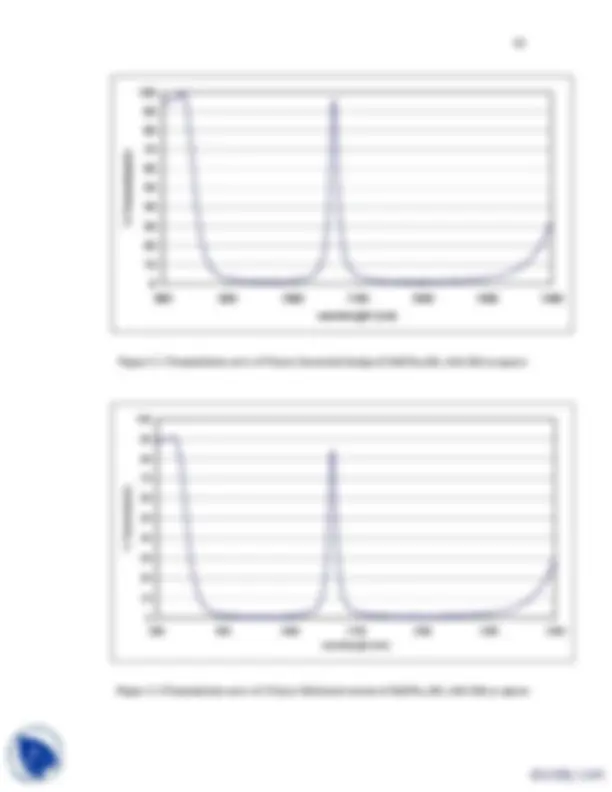
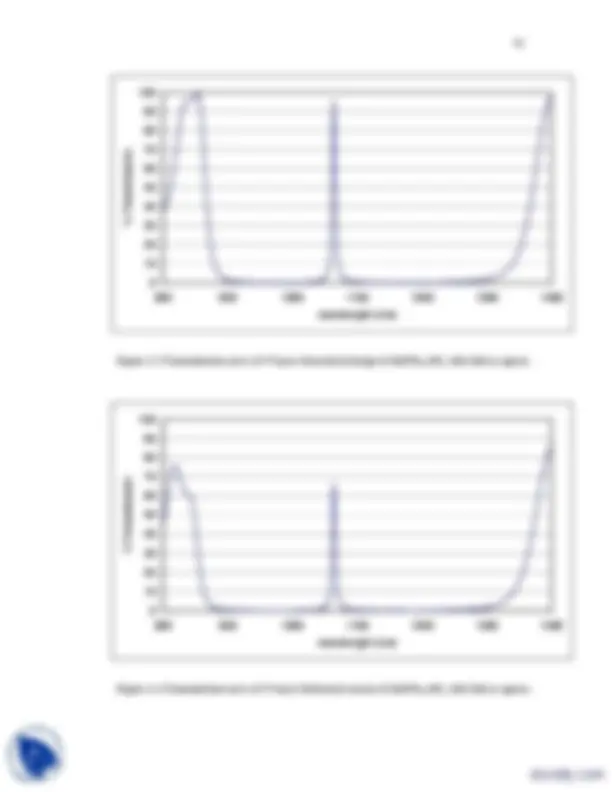
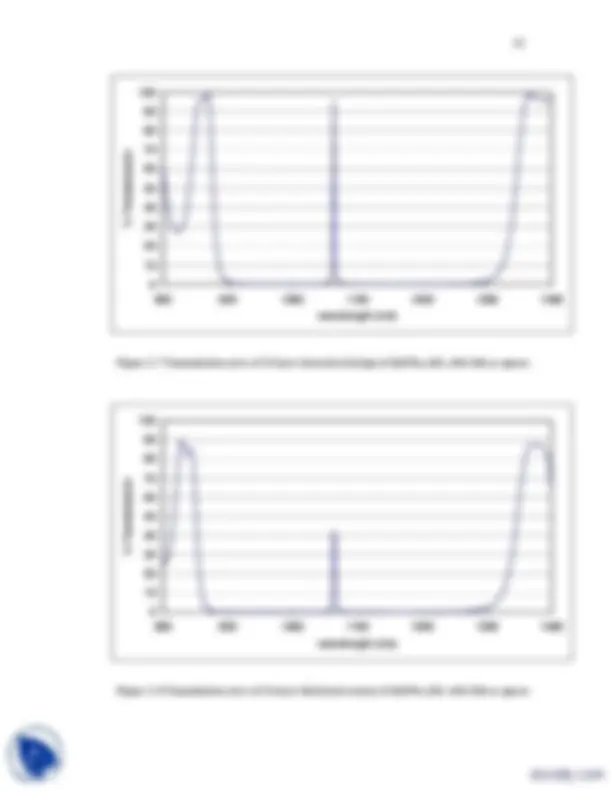
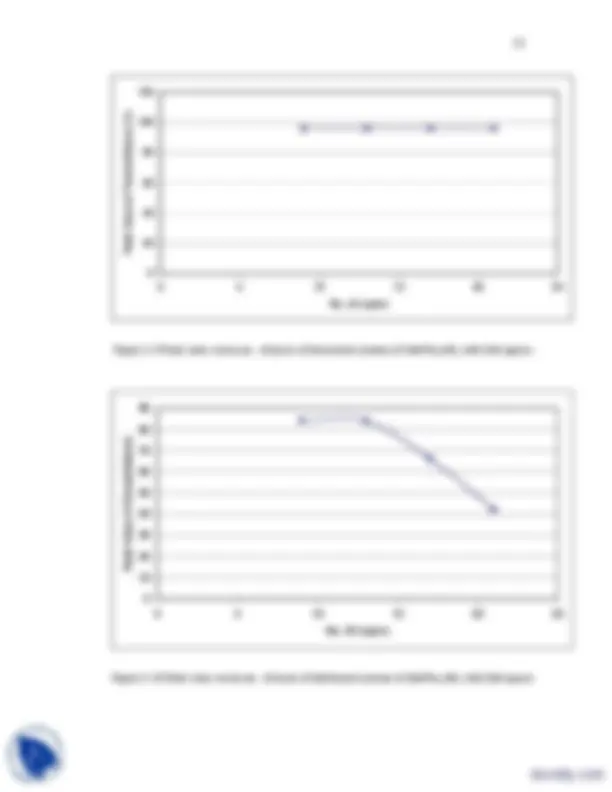
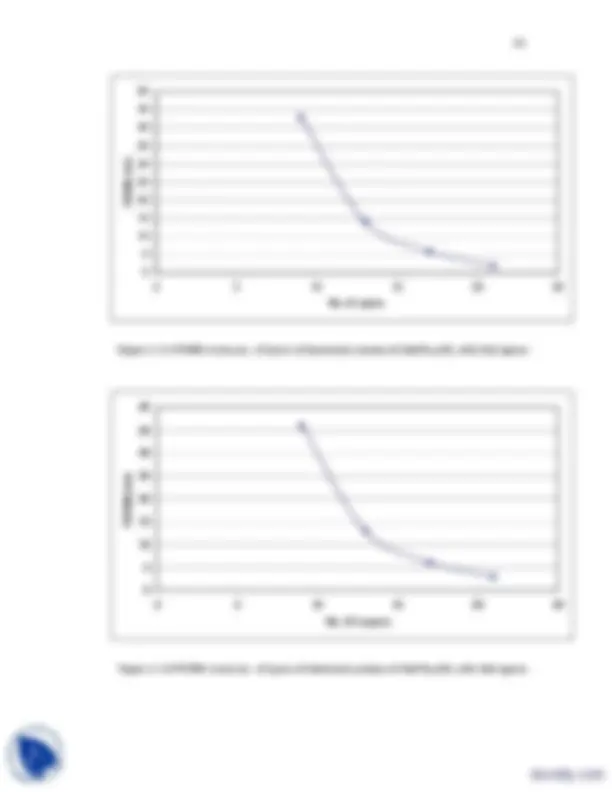
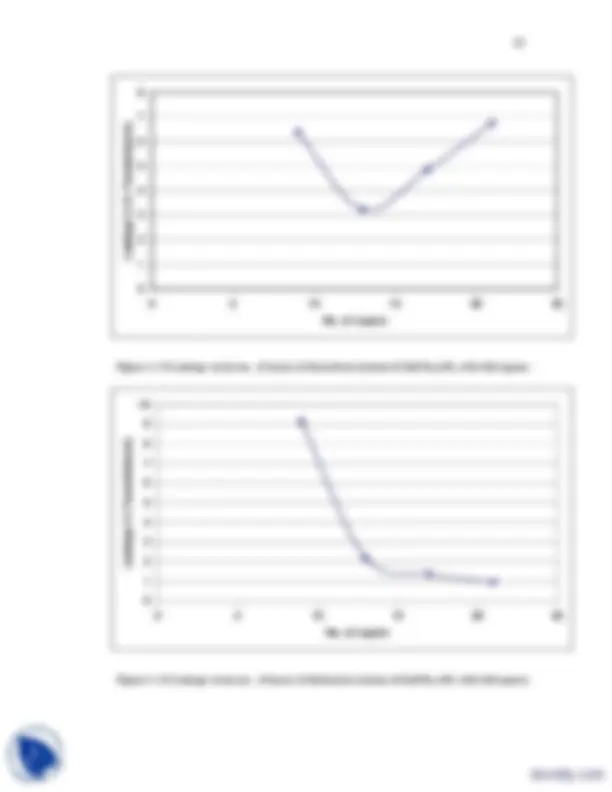
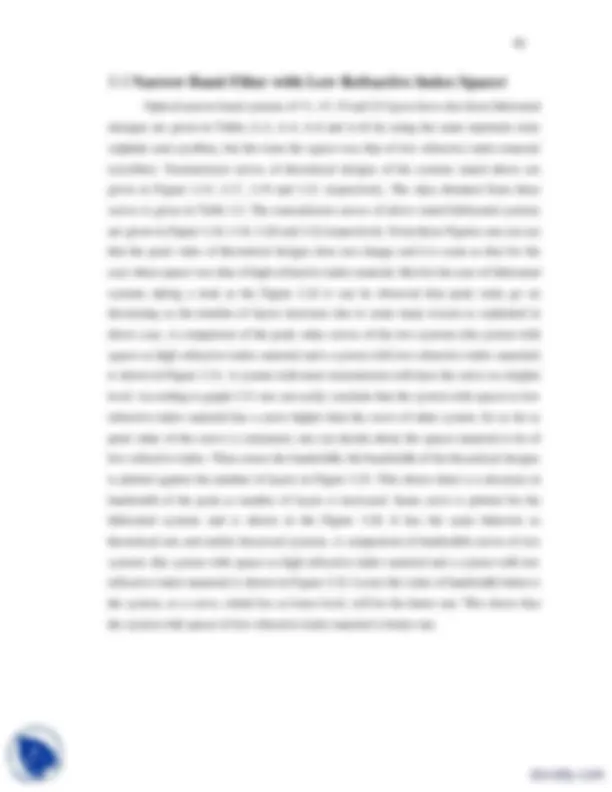
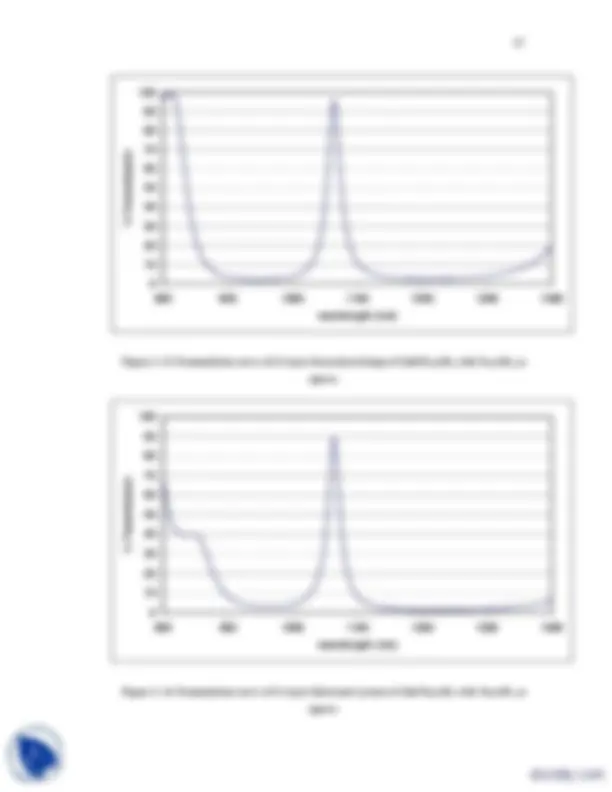
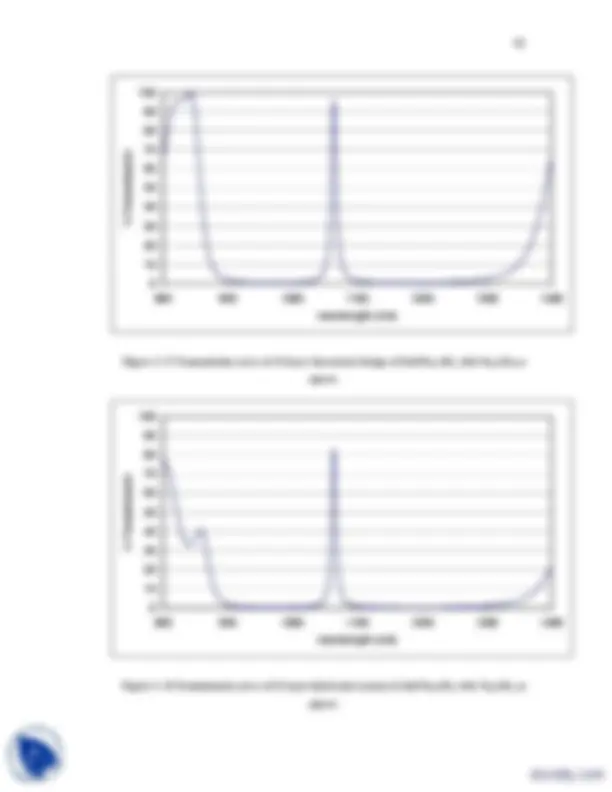
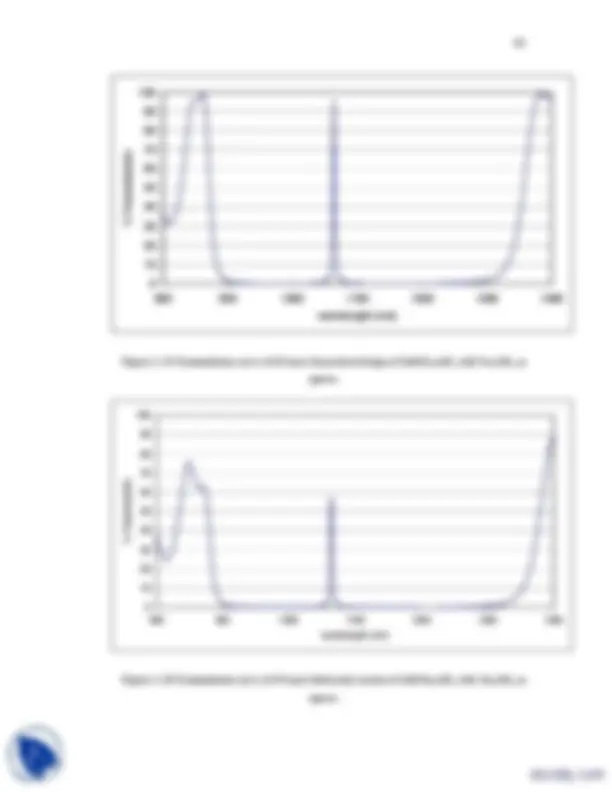
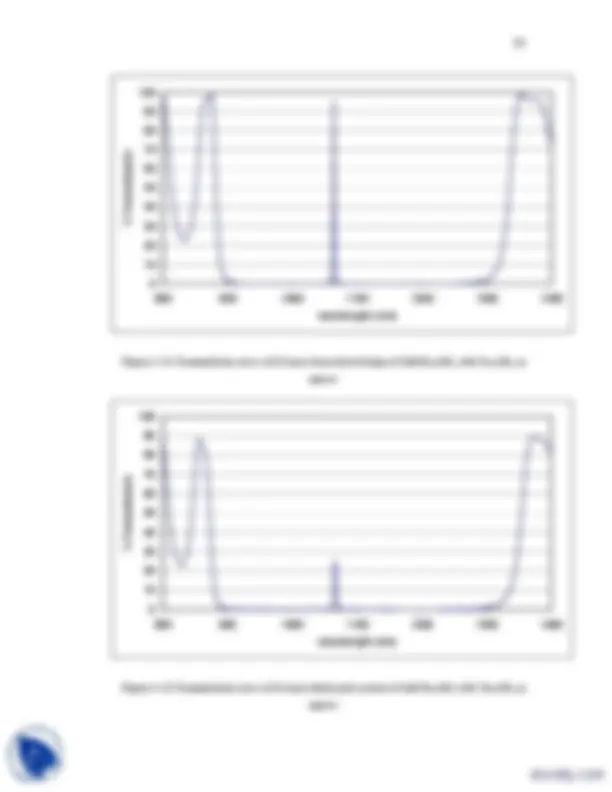
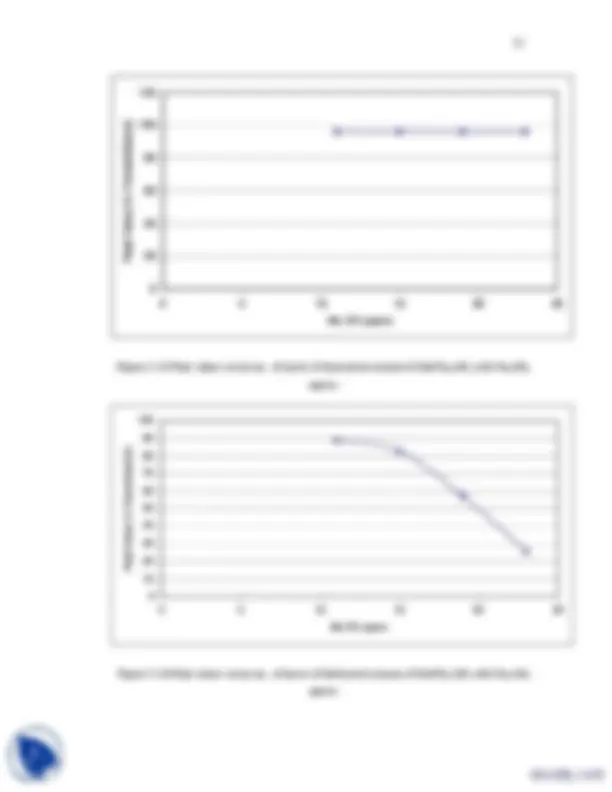
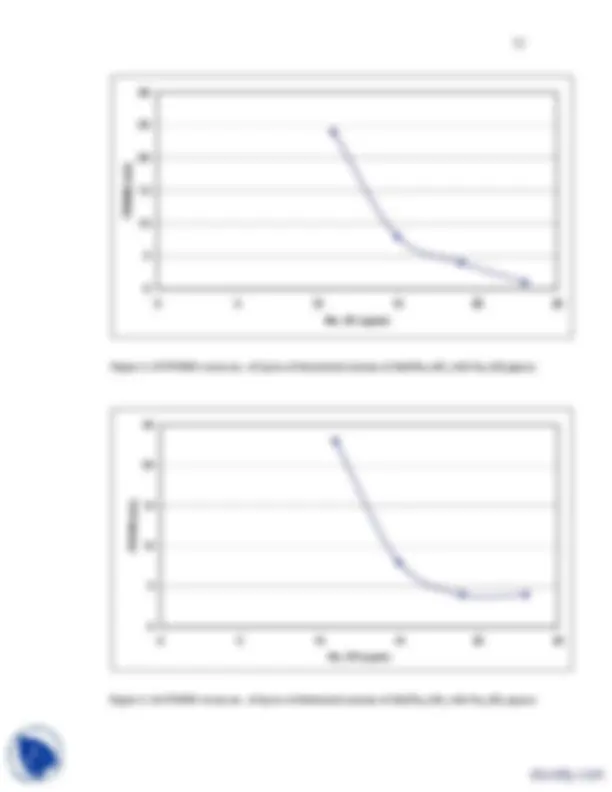
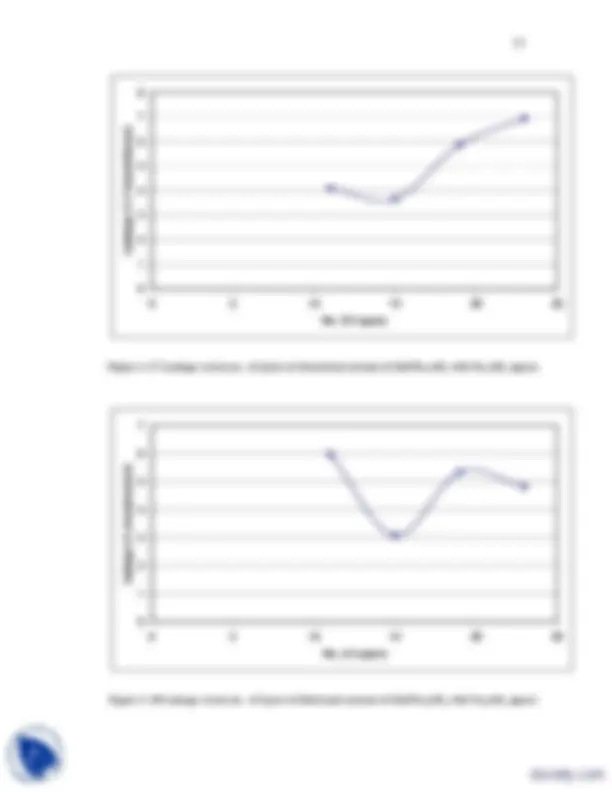
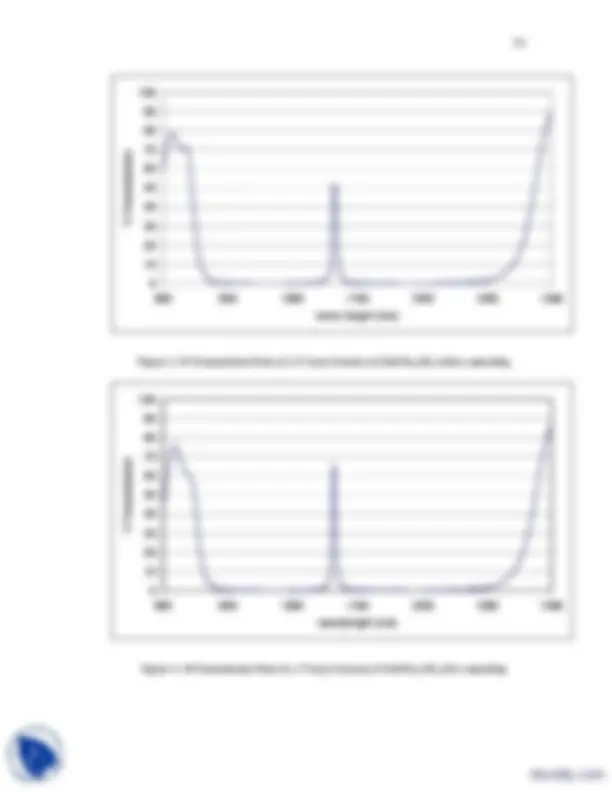
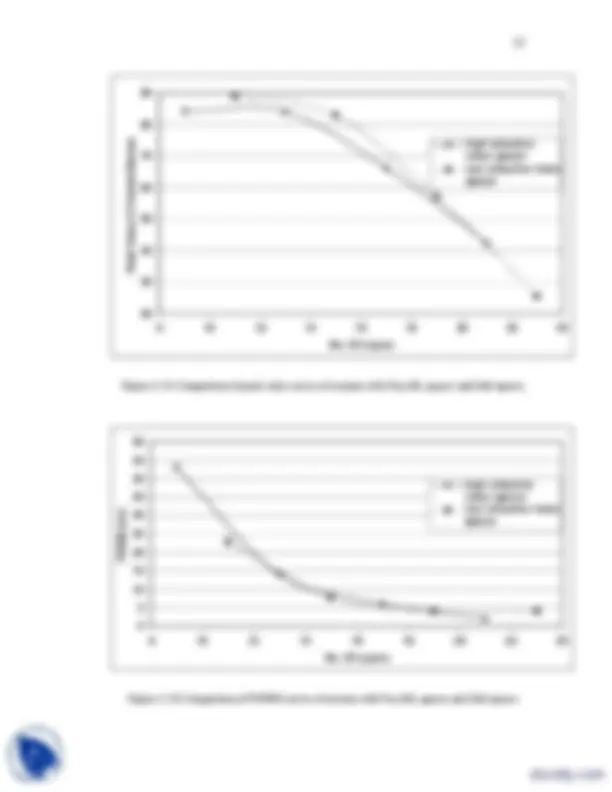
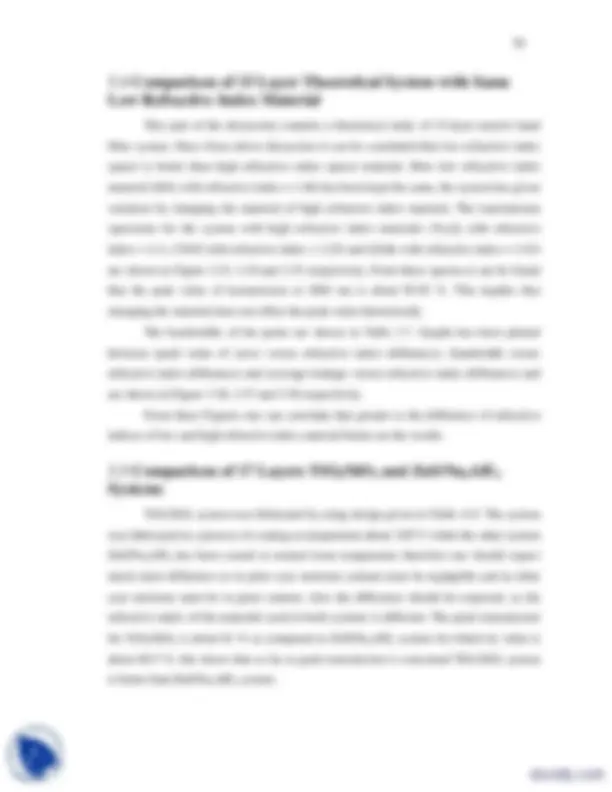
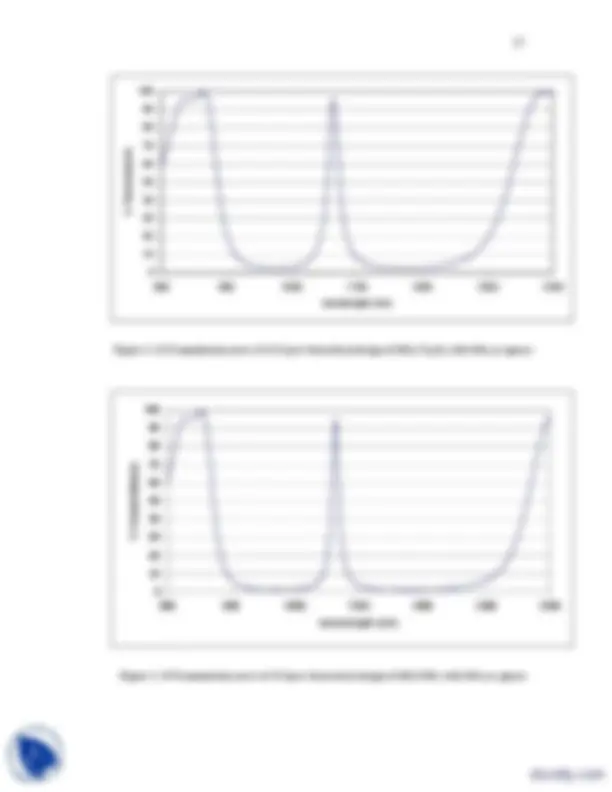
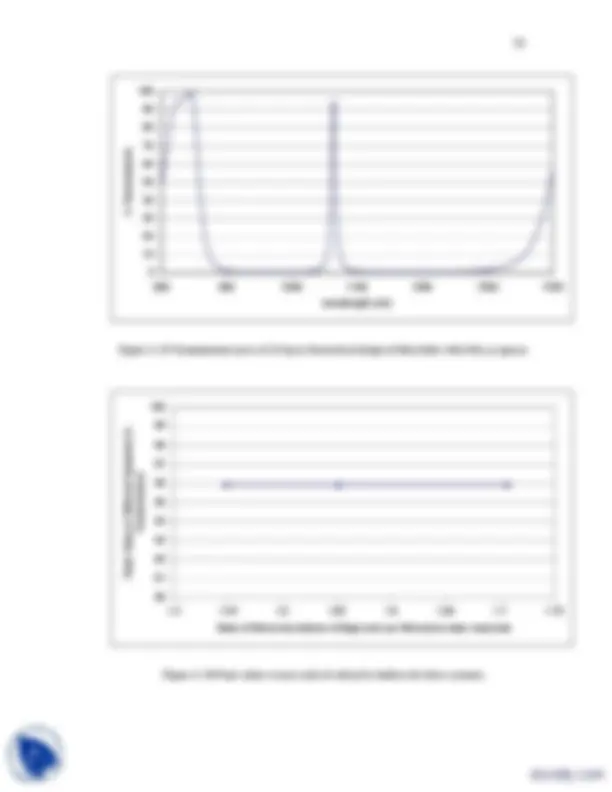
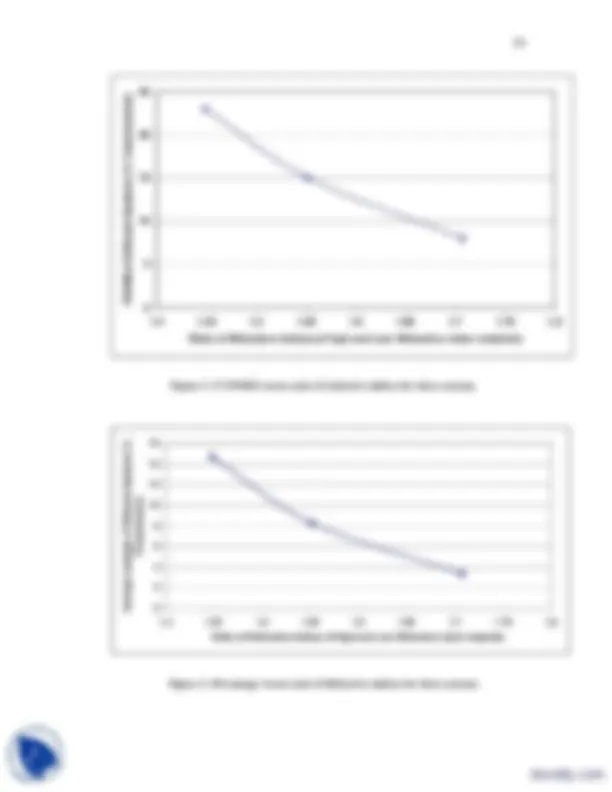
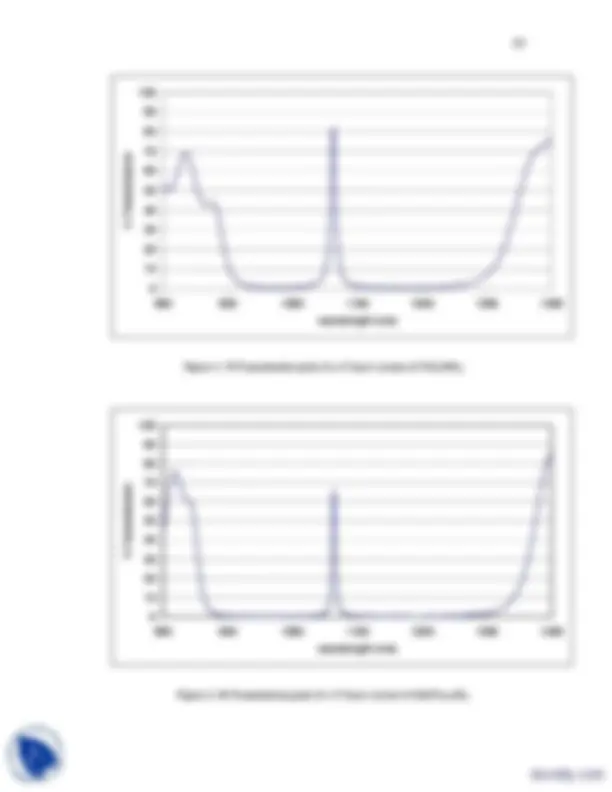
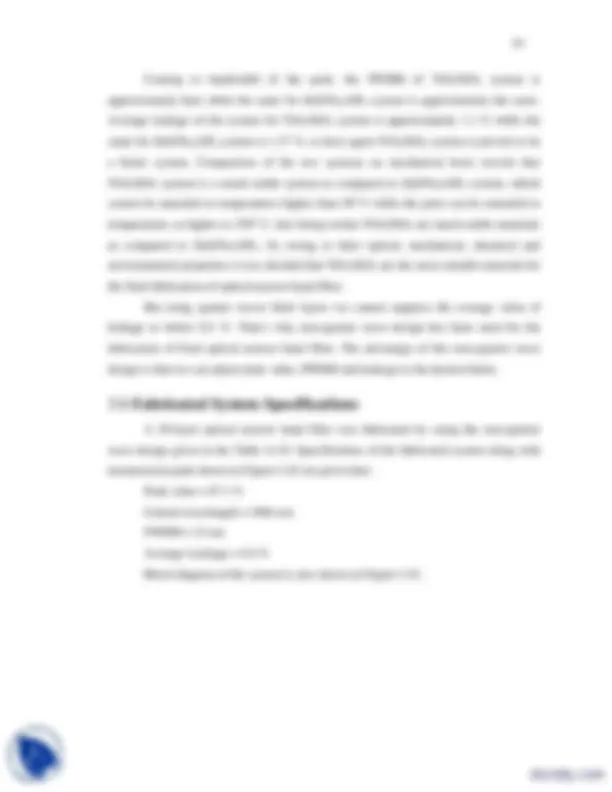
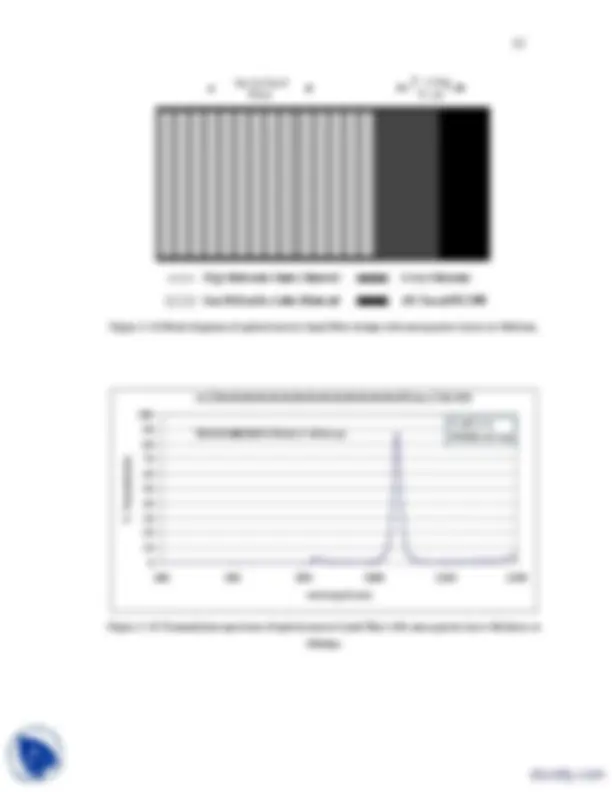
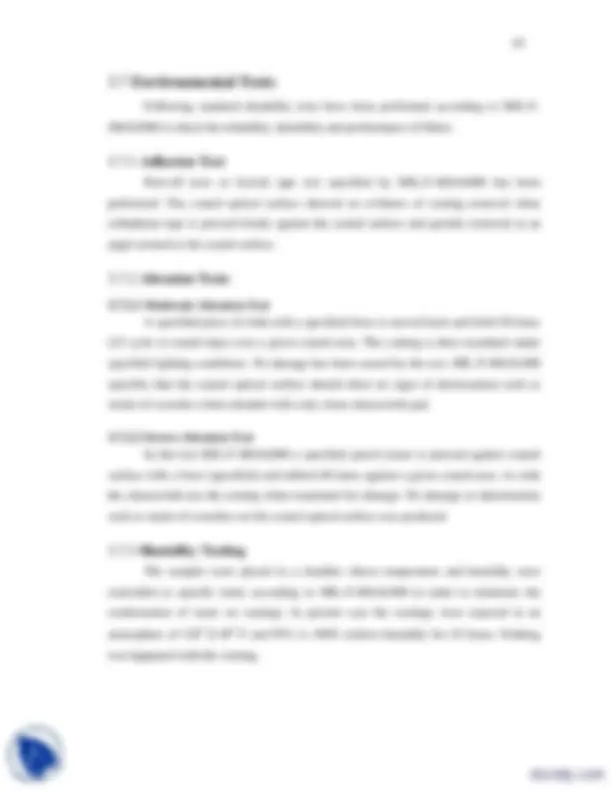
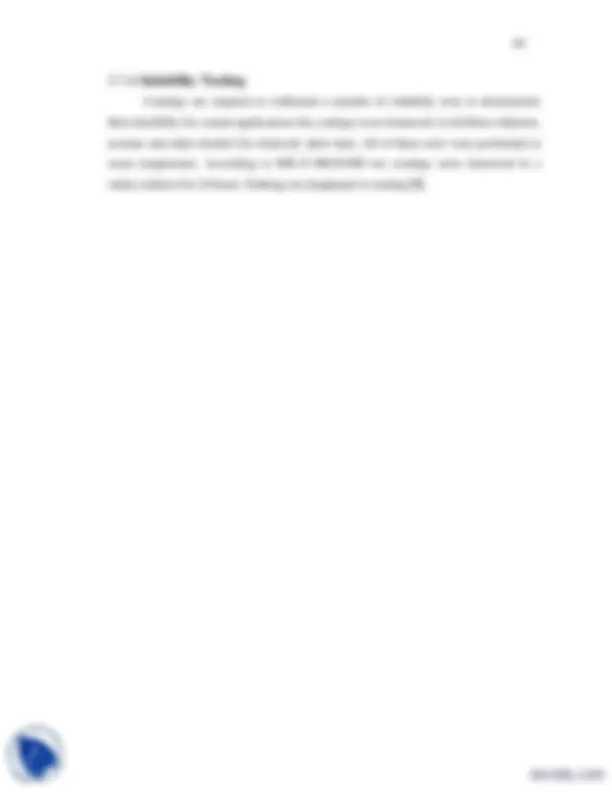
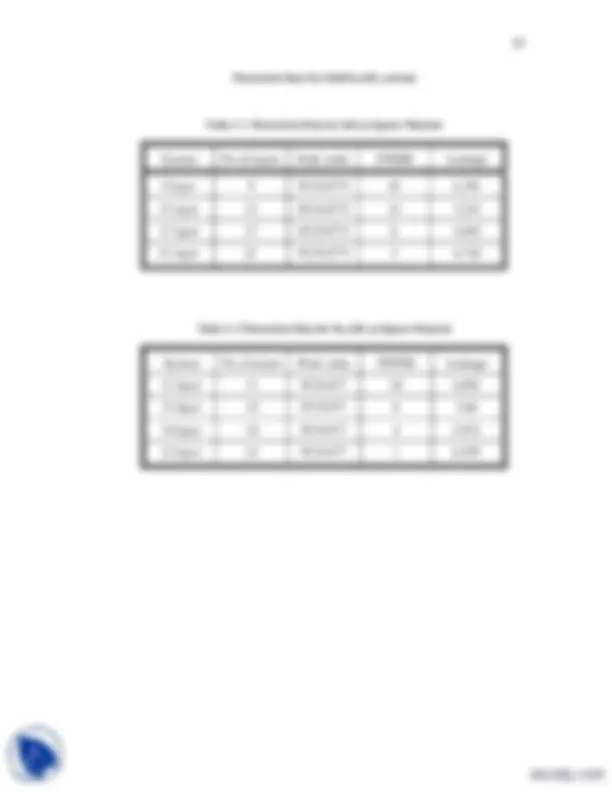
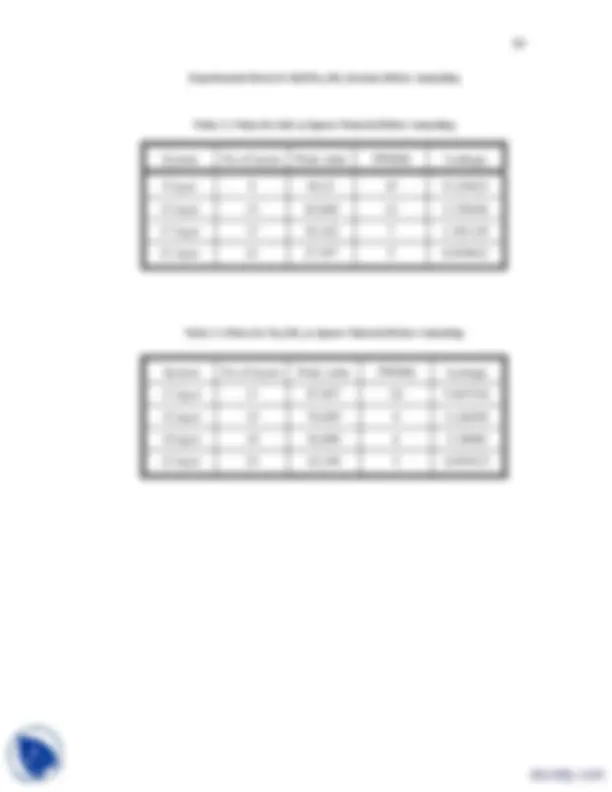
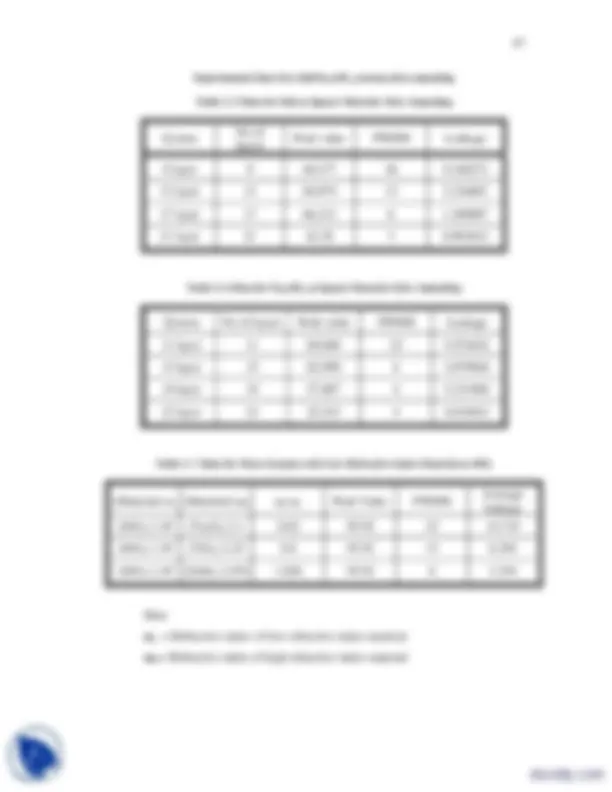
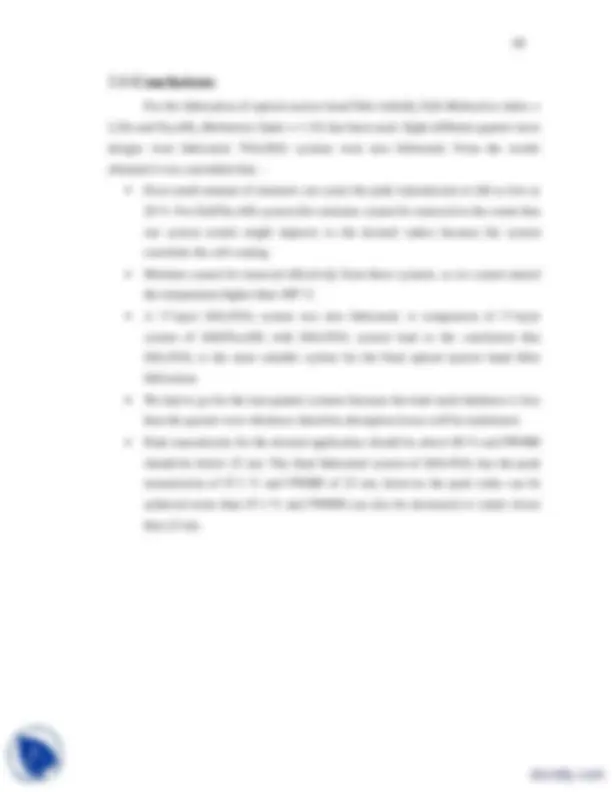
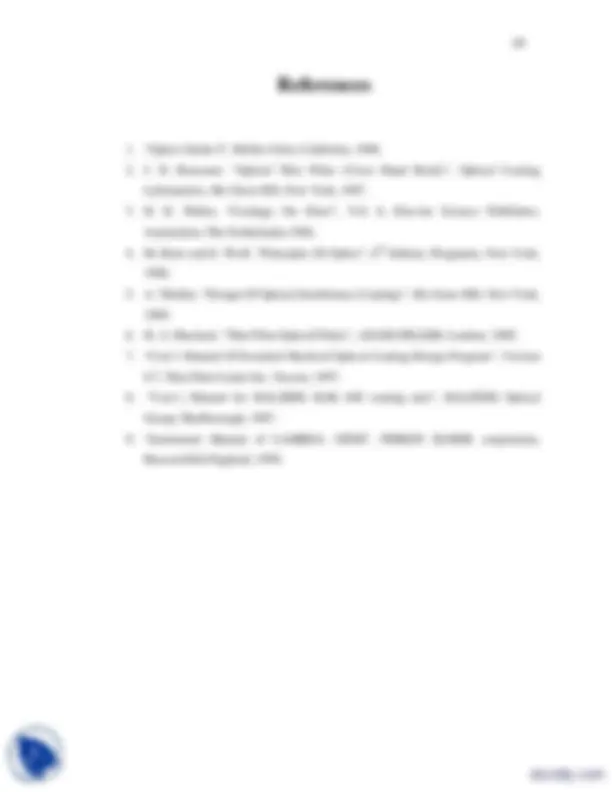
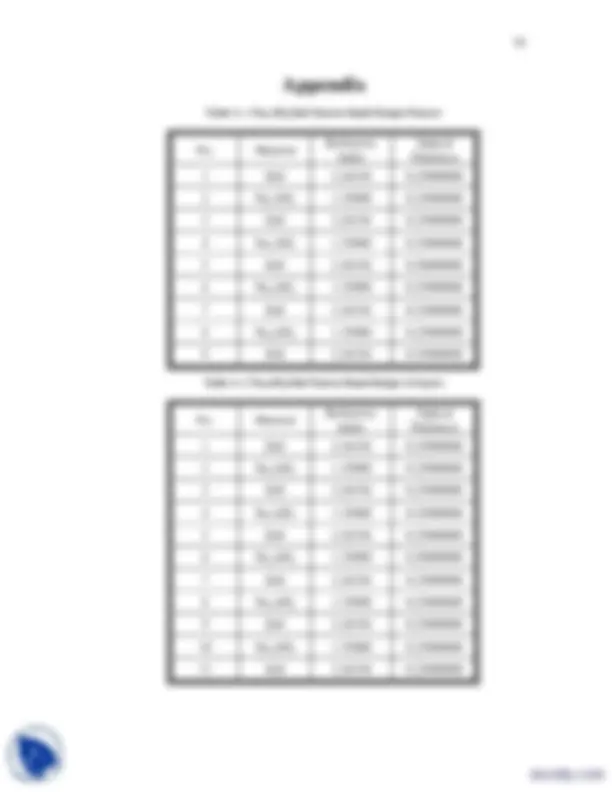
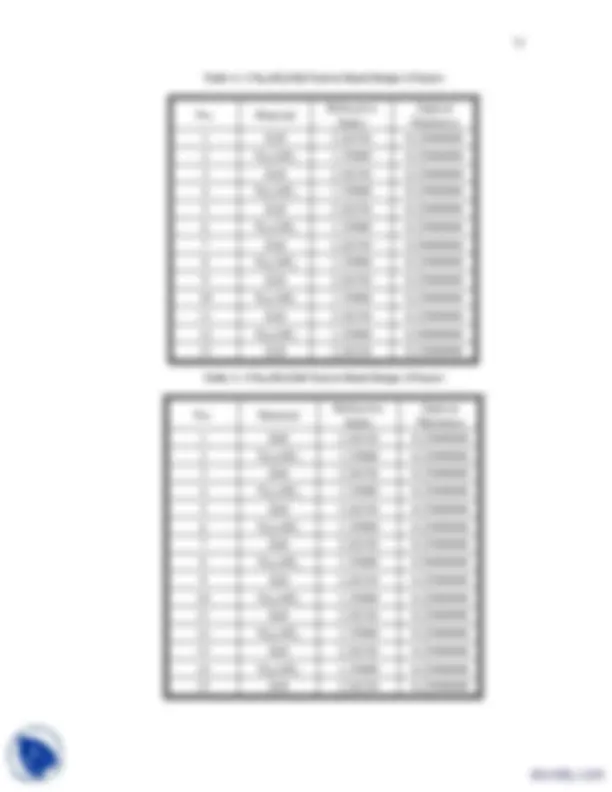

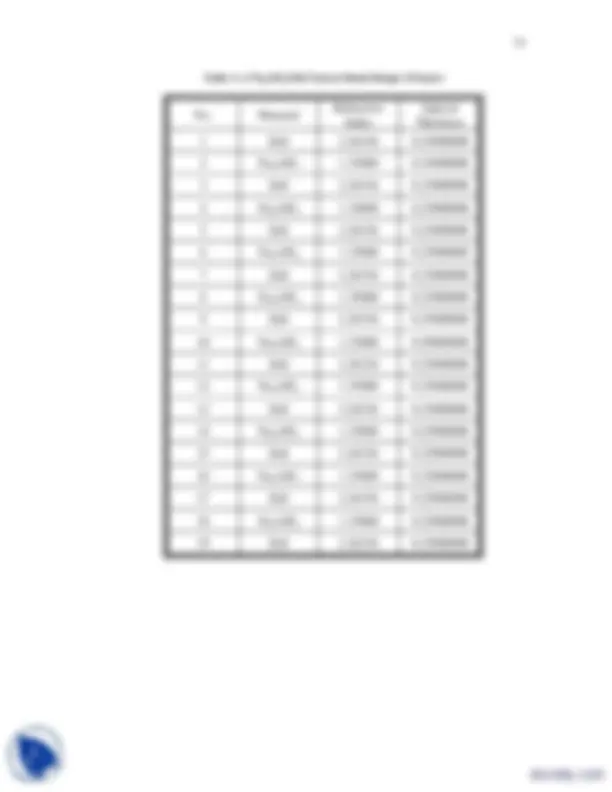
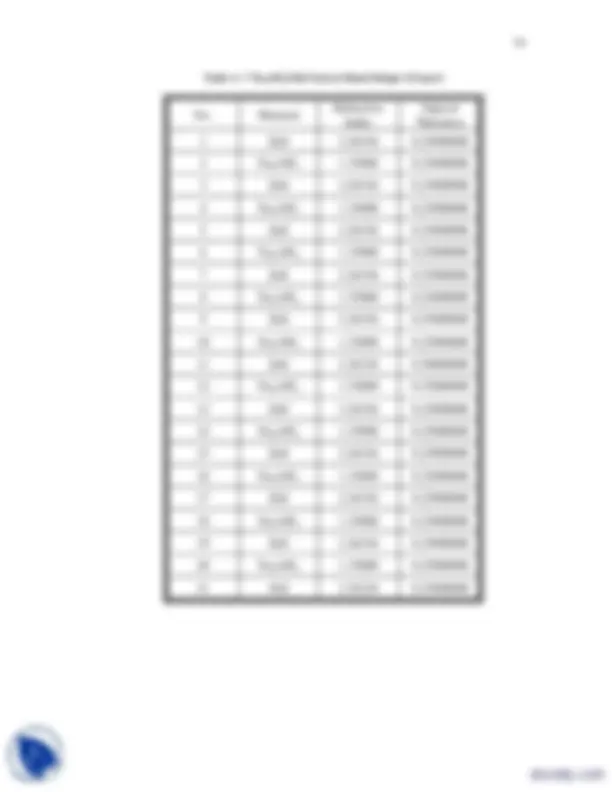
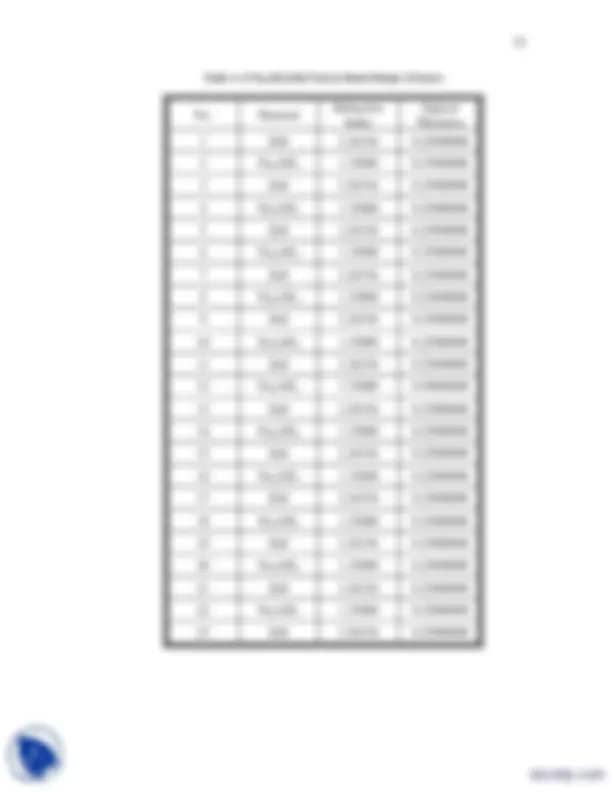
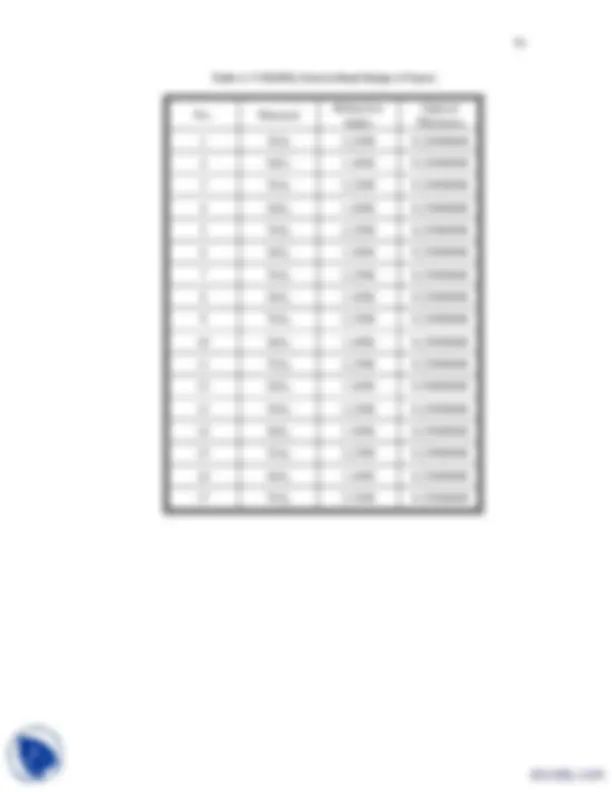
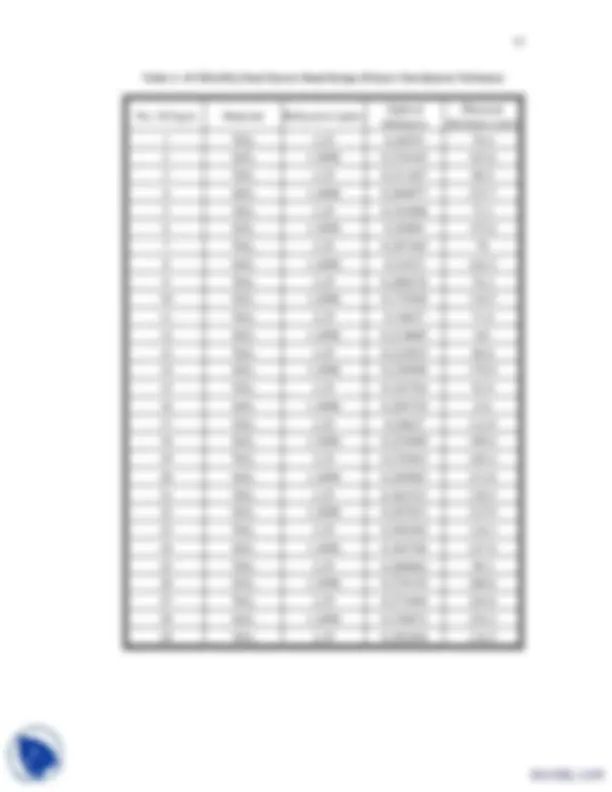
Study with the several resources on Docsity
Earn points by helping other students or get them with a premium plan
Prepare for your exams
Study with the several resources on Docsity
Earn points to download
Earn points by helping other students or get them with a premium plan
Community
Ask the community for help and clear up your study doubts
Discover the best universities in your country according to Docsity users
Free resources
Download our free guides on studying techniques, anxiety management strategies, and thesis advice from Docsity tutors
This project report was submitted to Prof. Aghanashini Yadavendra at University of Kerala for Advanced Physics course. It includes: General, Considerations, Fabry, Perot, Interferometer, Free, Spectral, Range, Thin, Film, Narrowband, Filter
Typology: Study Guides, Projects, Research
1 / 85
This page cannot be seen from the preview
Don't miss anything!
ix
Figure 3. 9 Peak value versus no. of layers of theoretical systems of ZnS/Na 2 AlF 6 with ZnS spacer................................................................................................................. 43 Figure 3. 10 Peak value versus no. of layers of fabricated systems of ZnS/Na 2 AlF 6 with ZnS spacer................................................................................................................. 43 Figure 3. 11 FWHM versus no. of layers of theoretical systems of ZnS/Na 2 AlF 6 with ZnS spacer................................................................................................................. 44 Figure 3. 12 FWHM versus no. of layers of fabricated systems of ZnS/Na 2 AlF 6 with ZnS spacer. ....................................................................................................................... 44 Figure 3. 13 Leakage versus no. of layers of theoretical systems of ZnS/Na 2 AlF 6 with ZnS spacer................................................................................................................. 45 Figure 3. 14 Leakage versus no. of layers of fabricated systems of ZnS/Na 2 AlF 6 with ZnS spacer................................................................................................................. 45 Figure 3. 15 Transmission curve of 11-layer theoretical design of ZnS/Na 2 AlF 6 with Na 2 AlF 6 as spacer. .................................................................................................... 47 Figure 3. 16 Transmission curve of 11-layer fabricated system of ZnS/Na 2 AlF 6 with Na 2 AlF 6 as spacer. .................................................................................................... 47 Figure 3. 17 Transmission curve of 15-layer theoretical design of ZnS/Na 2 AlF 6 with Na 2 AlF 6 as spacer...................................................................................................... 48 Figure 3. 18 Transmission curve of 15-layer fabricated system of ZnS/Na 2 AlF 6 with Na 2 AlF 6 as spacer. .................................................................................................... 48 Figure 3. 19 Transmission curve of 19-layer theoretical design of ZnS/Na 2 AlF 6 with Na 2 AlF 6 as spacer. .................................................................................................... 49 Figure 3. 20 Transmission curve of 19-layer fabricated system of ZnS/Na 2 AlF 6 with Na 2 AlF 6 as spacer. .................................................................................................... 49 Figure 3. 21 Transmission curve of 23-layer theoretical design of ZnS/Na 2 AlF 6 with Na 2 AlF 6 as spacer. .................................................................................................... 50 Figure 3. 22 Transmission curve of 23-layer fabricated system of ZnS/Na 2 AlF 6 with Na 2 AlF 6 as spacer. .................................................................................................... 50 Figure 3. 23 Peak values versus no. of layers of theoretical systems of ZnS/Na 2 AlF 6 with Na 2 AlF 6 spacer.......................................................................................................... 51
x
Figure 3. 24 Peak values versus no. of layers of fabricated systems of ZnS/Na 2 AlF 6 with Na 2 AlF 6 spacer.......................................................................................................... 51 Figure 3. 25 FWHM versus no. of layers of theoretical systems of ZnS/Na 2 AlF 6 with Na 2 AlF 6 spacer........................................................................................................... 52 Figure 3. 26 FWHM versus no. of layers of fabricated systems of ZnS/Na 2 AlF 6 with Na 2 AlF 6 spacer.......................................................................................................... 52 Figure 3. 27 Leakage versus no. of layers of theoretical systems of ZnS/Na 2 AlF 6 with Na 2 AlF 6 spacer.......................................................................................................... 53 Figure 3. 28 Leakage versus no. of layers of fabricated systems of ZnS/Na 2 AlF 6 with Na 2 AlF 6 spacer.......................................................................................................... 53 Figure 3. 29 Transmission Peak of a 17-layer Systems of ZnS/Na 2 AlF 6 before annealing ................................................................................................................................... 54 Figure 3. 30 Transmission Peak of a 17-layer Systems of ZnS/Na 2 AlF 6 after annealing 54 Figure 3. 31 Comparison of peak value curves of systems with Na 2 AlF 6 spacer and ZnS spacer. ....................................................................................................................... 55 Figure 3. 32 Comparison of FWHM curves of systems with Na 2 AlF 6 spacer and ZnS spacer. ....................................................................................................................... 55 Figure 3. 33 Transmission curve of 15-Layer theoretical design of SiO 2 / Ta 2 O 5 with SiO 2 as spacer. ................................................................................................................... 57 Figure 3. 34 Transmission curve of 15-layer theoretical design of SiO 2 /TiO 2 with SiO 2 as spacer. ....................................................................................................................... 57 Figure 3. 35 Transmission curve of 15-layer theoretical design of SiO 2 /ZnSe with SiO 2 as spacer. ....................................................................................................................... 58 Figure 3. 36 Peak values versus ratio of refractive indices for three systems. ................. 58 Figure 3. 37 FWHM versus ratio of refractive indices for three systems......................... 59 Figure 3. 38 Leakage versus ratio of Refractive indices for three systems. ..................... 59 Figure 3. 39 Transmission peak of a 17-layer system of TiO 2 /SiO 2 ................................. 60 Figure 3. 40 Transmission peak of a 17-layer system of ZnS/Na 2 AlF 6 ............................ 60 Figure 3. 41 Block diagram of optical narrow band filter design with non-quarter layers at 1064 nm. ................................................................................................................... 62
xiii
The main objective of this experimental work was to design, fabricate and analyze the optical narrow band filter for Nd-YAG laser applications. The optical narrow band filter was designed and fabricated on the principle of Fabry-Perot interferometer. In the initial part of the work different narrow band filters have been designed and fabricated by using ZnS (high refractive index material) and Na 2 AlF 6 (low refractive index material). All layers in these designs were of quarter wave optical thickness except spacer, which was of half wave optical thickness. A comparison of the systems with spacer material as ZnS and with Na 2 AlF 6 is shown at the end of this report. A 17-layer system of SiO2 and TiO2 was also fabricated for high laser damage threshold applications. A comparison of 17 layer systems of ZnS/Na 2 AlF 6 and SiO 2 /TiO 2 lead to the conclusion that SiO 2 /TiO 2 are the better materials for optical narrow band filter fabrication. So the final system of 29 layers of non-quarter wave thickness of both SiO 2 and TiO 2 was fabricated which has the central wavelength 1064 nm, FWHM 23 nm and peak transmission 87.1 %.
1.2 Multi-layer Dielectric Coatings
Applications generally require that the reflected portion of incident light approach 0% for transmitting optics and 100% for reflective optics (mirrors), or at some fixed intermediate value for partial reflectors (beam splitters). From a single thin film we cannot get the required results of transmission and reflection High-reflection coatings made from a stack of alternate layers of high- and low- refractive-index material, with each layer in the stack having an optical thickness of a quarter wave at the design wavelength. In a quarter-wave stack, alternate reflections are phase shifted by 180 degrees because they occur at low- to high-index interfaces (external reflections). These phase shifts are exactly canceled by the 180-degree phase shifts caused by the path difference between alternate reflecting surfaces. All reflected wave fronts are therefore exactly in phase and undergo only constructive interference. If the difference in the refractive index of the materials is large, then a quarter- wave stack containing only a few layers will have a very high reflectance. Reflectance is a maximum at the wavelength for which both the high- and low-index layers of the multi- layer are exactly one-quarter-wave thick. Outside the fairly narrow region of high reflectance, the reflectance slowly reduces toward zero in an oscillatory fashion. Width and height (i.e., peak reflectance) of the high-reflectance region are functions of the refractive-index ratio of the two materials used, together with the number of layers actually included in the stack. The peak reflectance can be increased by adding more layers, or by using materials with a higher refractive index ratio. The thin film coating applications includes antireflection, metallic reflectors, all- dielectric reflectors, hybrid reflectors, partial reflectors (beam splitters), and filters for monochromatic, dichroic, or broadband and narrow band filters etc [1].
1.3 Fabry-Perot Interferometer
A multiple-beam interferometer is shown in Figure 1.1, it usually consists of two flat reflecting plates, with high reflective ability. The plates are set parallel to one another so that light waves may bounce back and forth between them several times.
The Fabry-Perot relies on the interference of multiple reflected beams. Incident light undergoes multiple reflections between coated surfaces, which define the cavity. Each transmitted wave front has undergone an even number of reflections (0, 2, 4,.. .). Whenever there is no phase difference between emerging wavefronts, interference between these wavefronts produces a transmission maximum [1]. This occurs when the optical path difference is an integral number of whole wavelengths, i.e., when mλ = 2t (^) op cosθ 1.
Figure 1. 1 Particular arrangement of Fabry-Perot filter [4].
where m is an integer, often termed the order, top is the optical thickness, and θ is the angle of incidence. At other wavelengths, destructive interference of transmitted wavefronts reduces transmitted intensity toward zero (i.e., most, or all, of the light is reflected back toward the source). Transmission peaks can be made very sharp by increasing the reflectivity of the mirror surfaces. In some Fabry-Perot interferometers, air is the medium between high reflectors; therefore, the optical thickness, t (^) op , is essentially equal to d, the physical thickness. The air gap may vary from a fraction of a millimeter to several centimeters. The Fabry-Perot is a useful spectroscopic tool. It provided much of the early motivation to develop quality thin films for the high-reflectance mirrors needed for high finesse.
FSR = c/4nL 1.
It is a filter that controls its spectral transmission primarily through interference effects. Interference filters are multi-layer thin-film devices. While many interference filters can be correctly described as "all dielectric" in construction, metallic layers are often present in auxiliary blocking structures. Broadband interference filters almost always contain a metallic layer (in their spacer, not in their stacks). Interference filters come in two basic types; edge filters and band pass filters, which transmit a desired wavelength interval while simultaneously rejecting both longer and shorter wavelengths. Narrowband interference filters (band pass filters) operate with the same principles as the Fabry-Perot interferometer. In fact, they can be considered Fabry-Perot interferometers since they usually operate in the first order. The simplest band pass filter is a very thin Fabry-Perot interferometer. A thin layer of dielectric material replaces the air gap with a half-wave optical thickness (optimized at the wavelength of the desired transmission peak). The high reflectors are normal quarter wave stacks with a broadband reflectance peaking at the design wavelength. However non-quarter designs can also be made, which have certain advantages. The entire assembly of two-quarter wave stacks, separated by a half-wave spacer, is applied to a single surface in one continuous vacuum deposition run is shown in Figure 1.3. By analogy with interferometers, the simplest band pass interference filters are sometimes called cavities. Two or more such filters can be deposited on top of the other, separated by an absentee layer. Approximately the product of the pass bands of individual cavities gives the resulting overall transmittance pass band. The advantages of multiple- cavity filters are steeper band slopes, improved near-band rejection, and "square" (not Gaussian or Lorentzian) pass band peaks. This last result, especially desirable in intermediate bandwidth filters, is achieved in part by reducing stack reflectance, which broadens individual cavity pass bands. Colored glass is often used to suppress transmission on the short wavelength side of the pass band [2].
Figure 1. 3 Full Assembly of optical narrow band filter.
Narrow Band pass filters are used to isolate a narrow region of the optical spectrum. The filter’s operation is based on interferometeric principles and hence is angularly sensitive. Most commercial band pass filters have full width half maxima (FWHM) of approximately 25 nm. The transmission curve of a typical narrowband interference filter is shown in Figure 1.4.
1.4 Applications of Optical Narrow Band Filters
The fabricated system has its specific applications in electro-optic systems such as: -
1.5 Theoretical Considerations
Let us consider a thin film of non-absorbing, homogeneous, isotropic medium having uniform thickness as shown in Figure 1.5. Let n be the refractive index of the film and n (^) o, ns are the refractive indices of the incident (air) and substrate (glass) medias respectively. The incident beam undergoes internal reflection and transmission at various different interfaces. Here we will be dealing with two types of wave functions, which are given below:
t
E (^) c ∂ ∇ × =−^1 ∂ 1.
so simplifying we can write,
t
E (^) c ∂
Since solutions of electromagnetic equations are, E = E 0 ei ( kr −^ ω^ t ) 1. H = H 0 ei ( kr −^ ω^ t ) 1.
so we can write, ∇ × E = ik × E 1.
E(z 1 ) = E+(z 1 - δ) + E-(z 1 - δ) = E+(z 1 +δ) + E-(z 1 +δ) 1. if α 0 is the angle of incidence and α is the angle of refraction in the film then by using Snell’s law and equation (1.15) we can write, Z 0 H(z 1 ) = [E+(z 1 - δ) - E-(z 1 - δ)]n 0 cos α 0 = [E+(z 1 +δ) -E-(z 1 +δ)]n cos α 1. Equations (1.17) and (1.18) are for the interface between air and film. We can write similar equations for the interface between film and substrate, which are given below; E(z 2 ) = E+(z 2 - δ) + E-(z 2 - δ) = E+(z 2 +δ) + E-(z 2 +δ) 1. since there is no reflected part as the wave is passed through the 2nd^ interface so we can neglect the term E-(z 2 +δ) so our equation become E(z 2 ) = E+(z 2 - δ) + E-(z 2 - δ) = E+(z 2 +δ) 1. and similarly we can write; Z 0 H(z 2 ) = [E+(z 2 - δ) - E-(z 2 - δ)]n cos α = E+(z 2 +δ) ns cos αs 1. a wave which traverses the film thickness once undergoes a phase shift of
d is called physical thickness of the film and φ is called the angular phase thickness. So we can write; E+(z 2 - δ) = E+(z 1 +δ)e -iφ^ and 1.21b E-(z 2 - δ) = E-(z 1 +δ)e +iφ^ 1.21c Putting these expressions in equations (1.20) and (1.21) we get; E(z 2 ) = E+(z 1 +δ)e -iφ^ + E-(z 1 +δ)e +iφ^ 1. Z 0 H(z 2 ) = [E+(z 1 +δ)e -iφ^ - E-(z 1 +δ)e +iφ]n cos α 1. Solving equations (1.22) and (1.23) simultaneously for E+(z 1 +δ) and E-(z 1 +δ) we get ;
φ cos 2 E (z 1 ) ( 2 )^0 (^2 ) n
φ cos
now by substituting the expressions for E+(z 1 +δ) and E-(z 1 +δ) in equations (1.17) and (1.18) we get
cos E(z ) ( )cos^0 (^2 )sin (^1 2) n = E z + ZH z i 1.
Equations (1.24) and (1.25) are actually relating the electric and magnetic field of the electromagnetic wave at the input and output interface of the film so from these two equations we can write down the characteristic matrix of the film which can be obtained as;
⎥⎦
cos sin cos
cos cos sin ( )
E(z) 0 2
2 0 1
1 ZH z
E z in
n
i
from above equation we can write down the characteristic matrix for the thin film which is given by;
cos sin cos
cos cos sin in
n
i M 1.
now let us assume that E to be parallel to the plane of incidence then our equations (1.17) and (1.18) will be changed as; E(z 1 ) = [E+(z 1 - δ) + E-(z 1 - δ)] cos α 0 = [E+(z 1 +δ) + E-(z 1 +δ)] cos α 1. where α 0 is the angle of incidence and α is the angle of refraction in the film. Z 0 H(z 1 ) = [E+(z 1 - δ) - E-(z 1 - δ)]n 0 = [E+(z 1 +δ) -E-(z 1 +δ)]n 1. we can write similar equations for the interface between film and substrate, which are given below; E(z 2 ) = [E+(z 2 - δ) + E-(z 2 - δ)] cos α 0 = [E+(z 2 +δ) + E-(z 2 +δ)]cos α 1.