
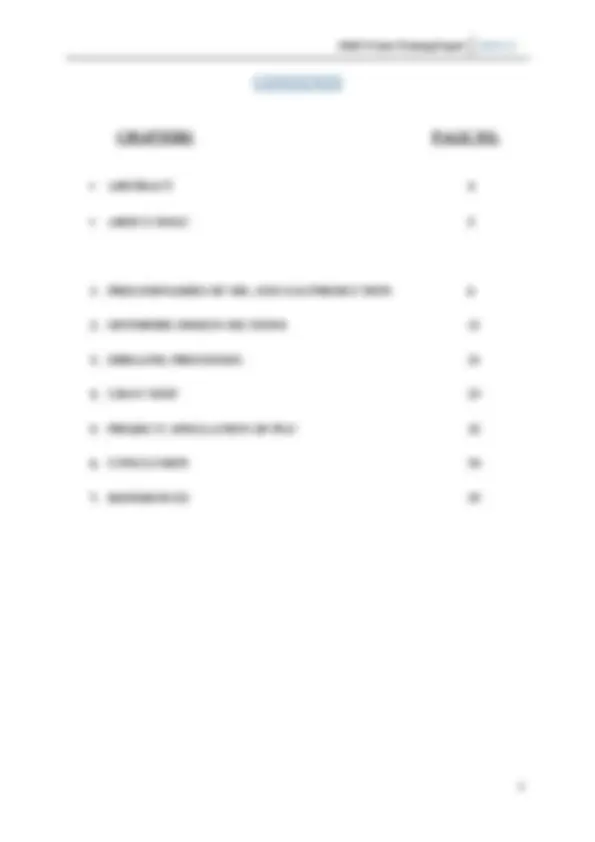
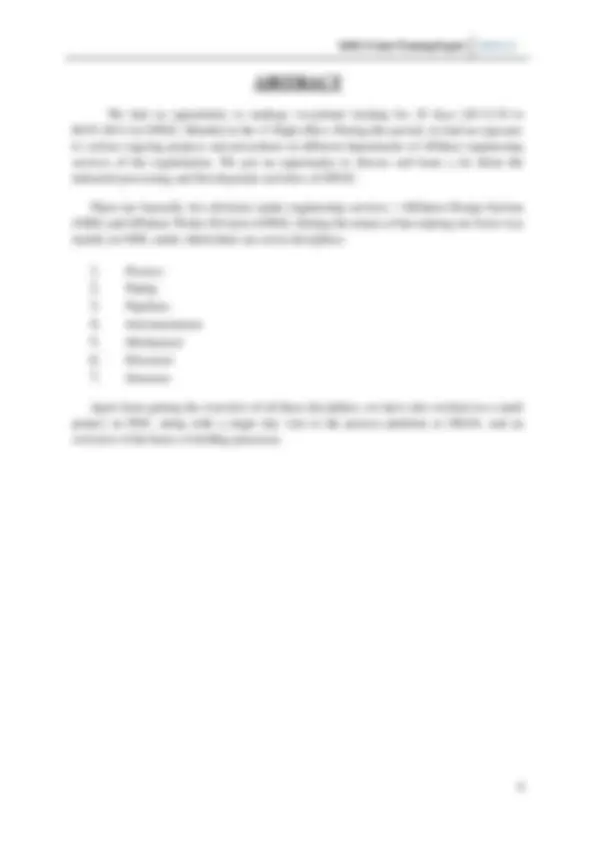
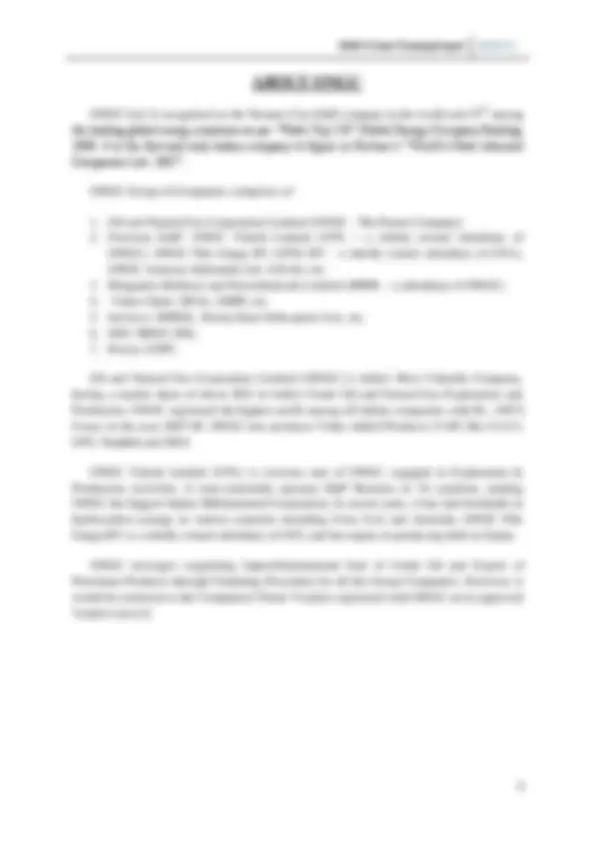
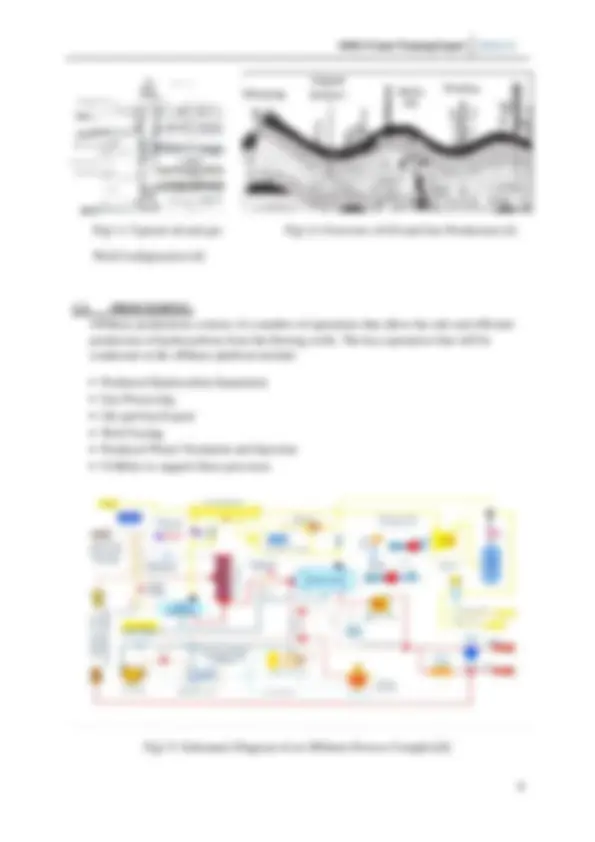
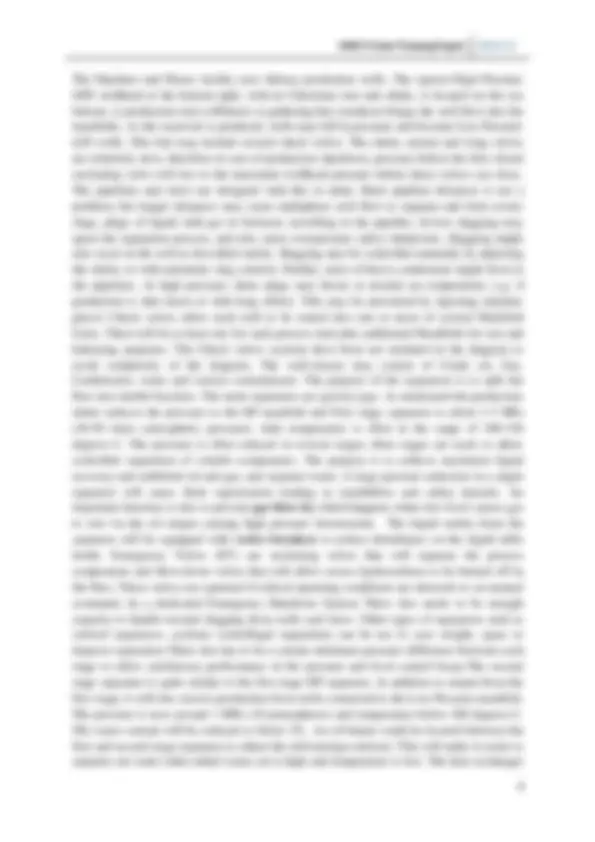
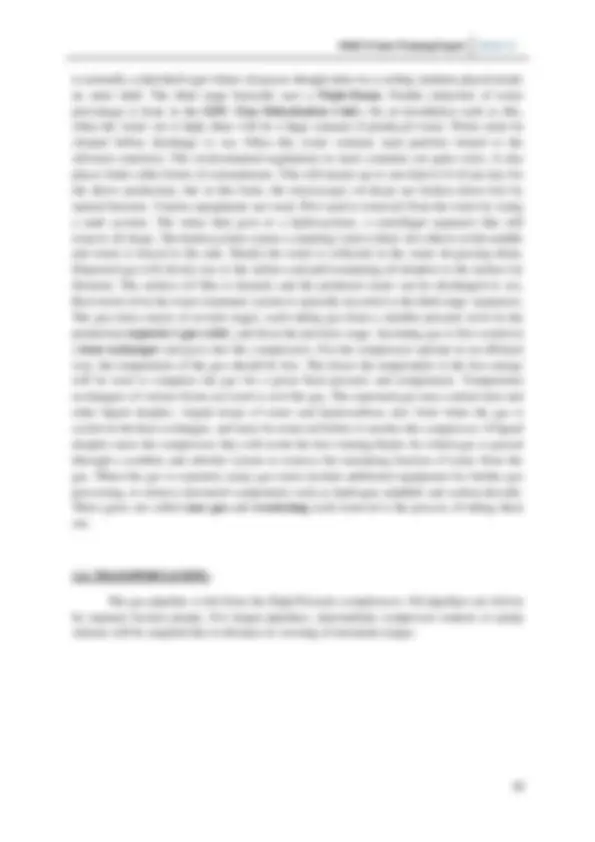
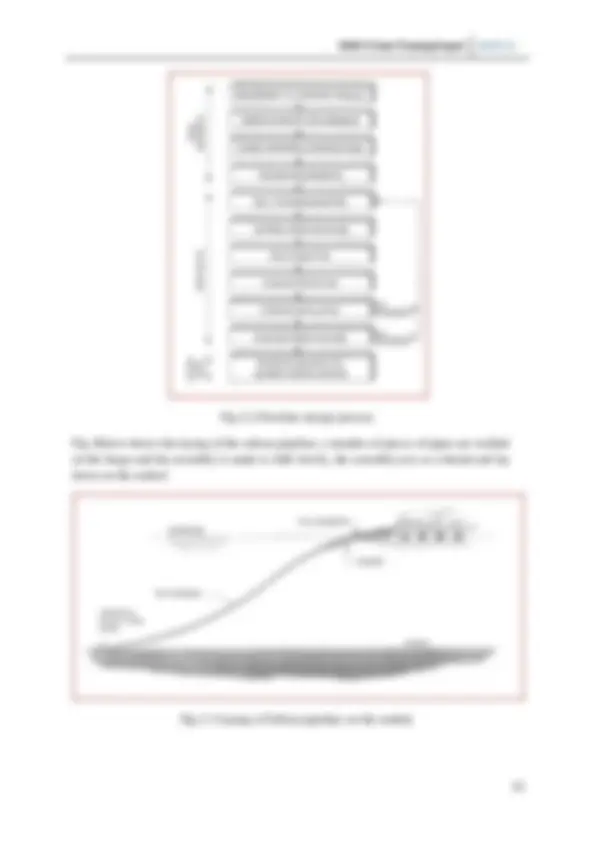
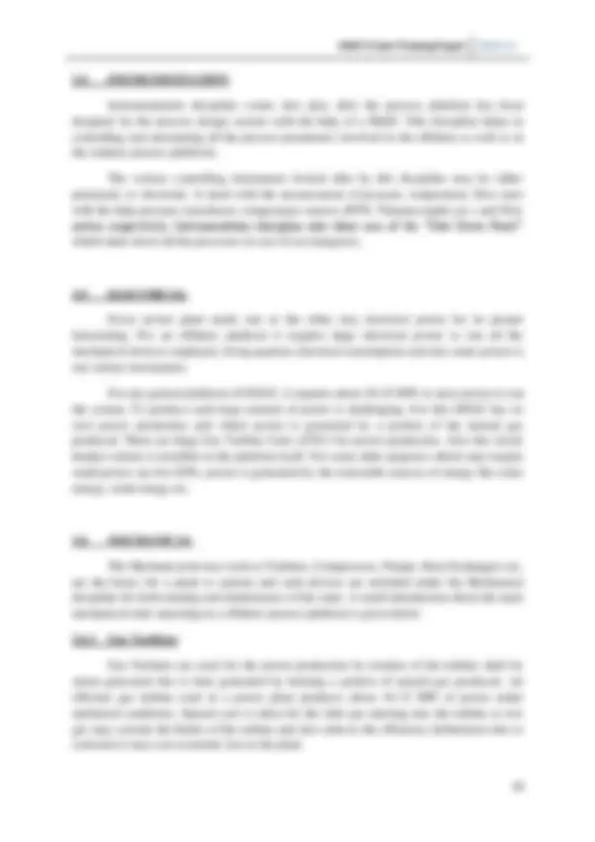
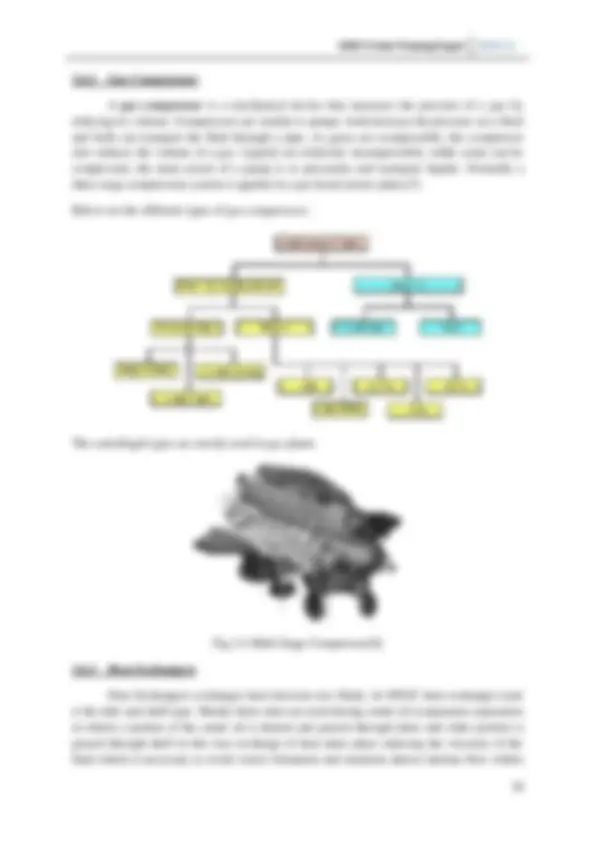
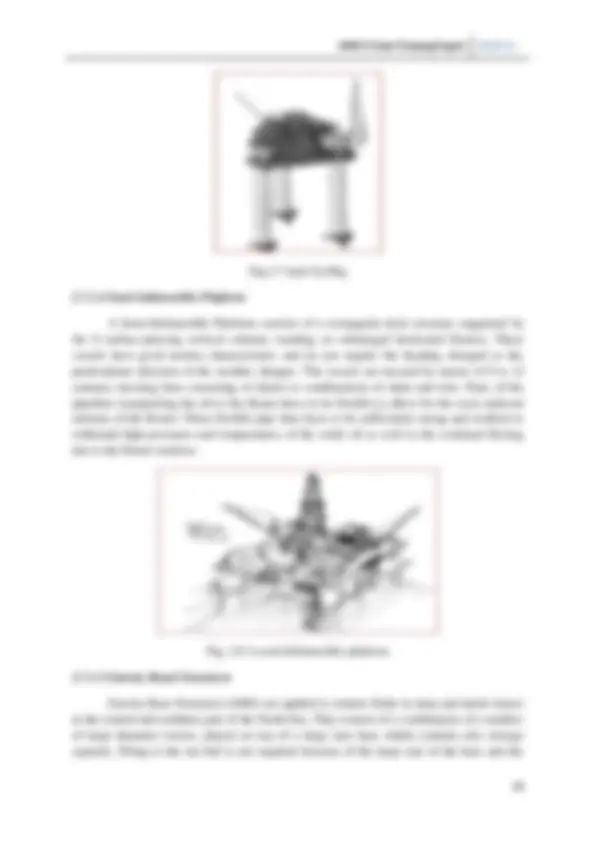
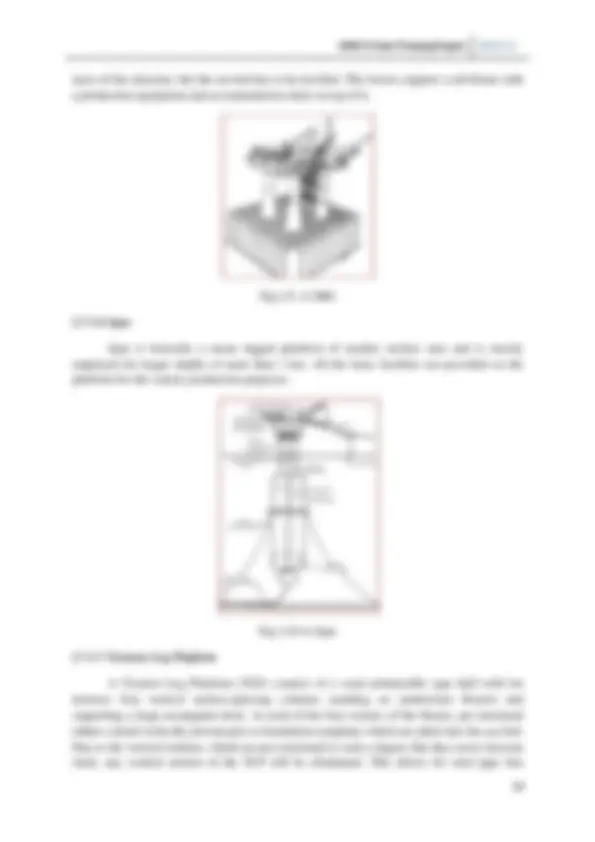
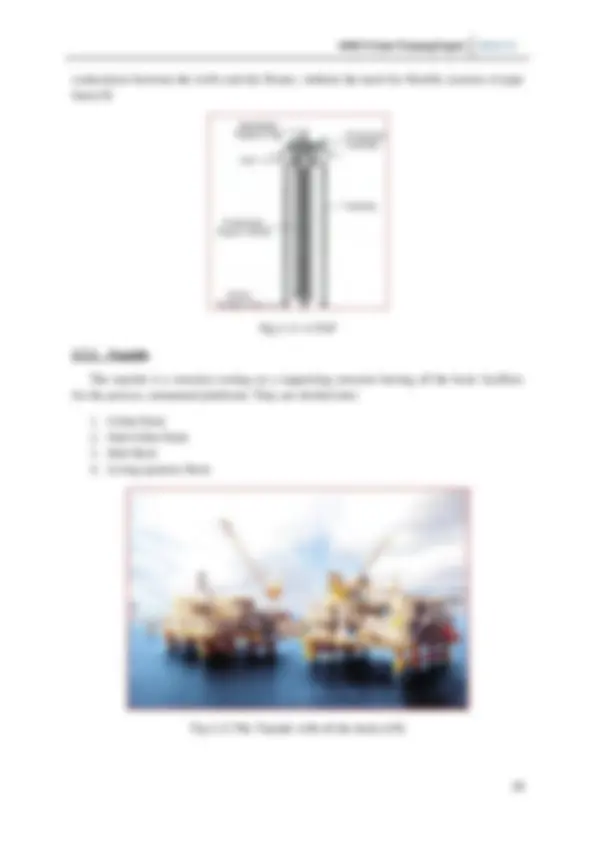
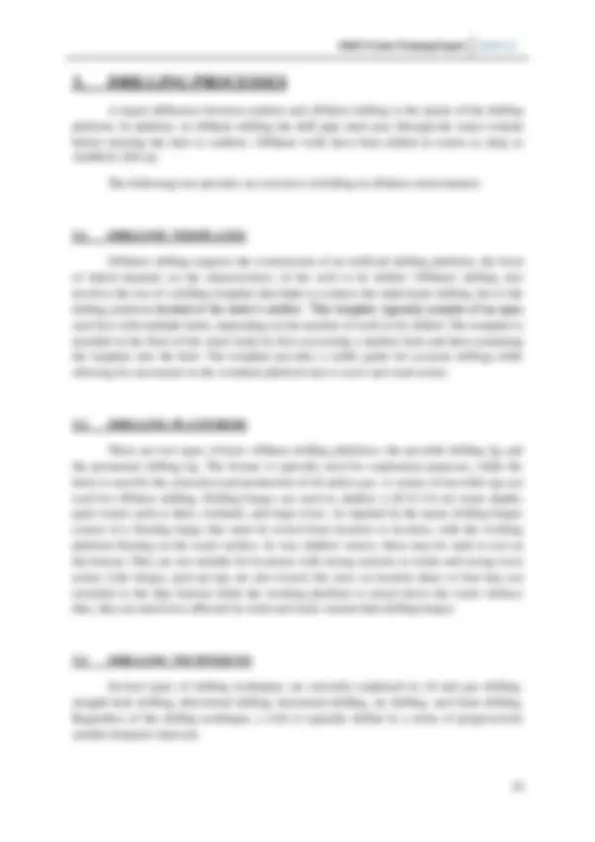
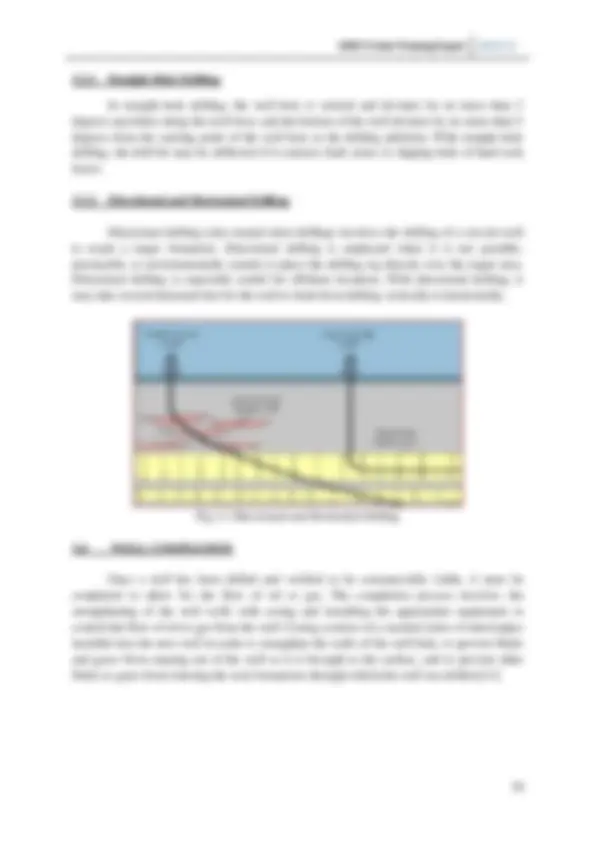
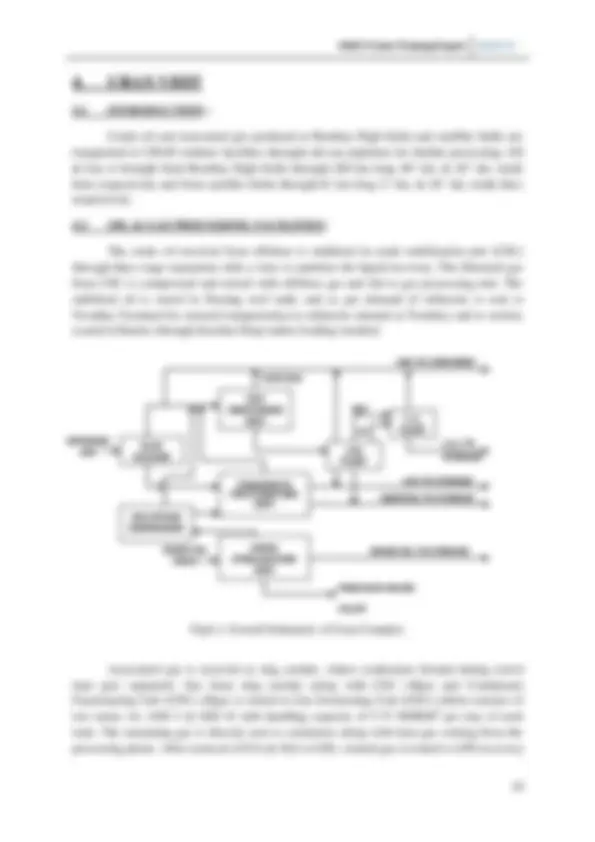
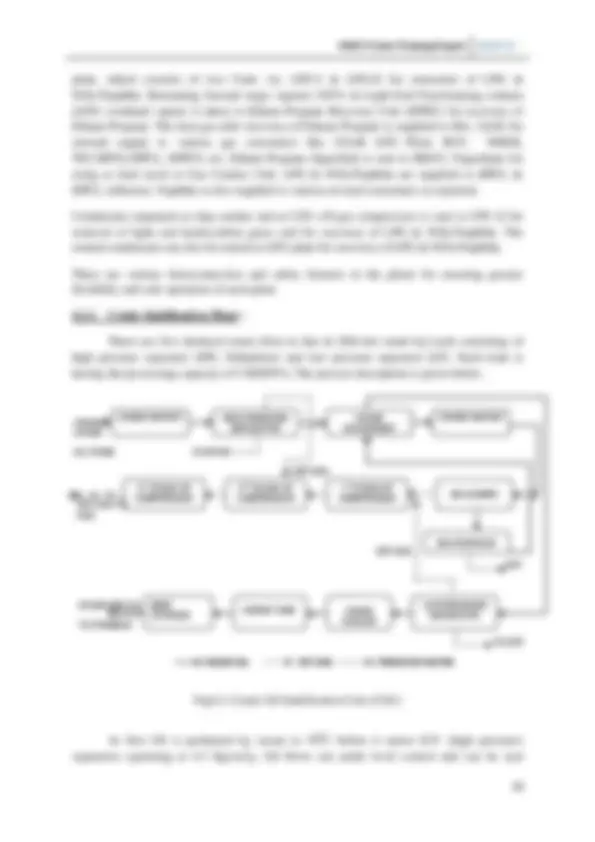
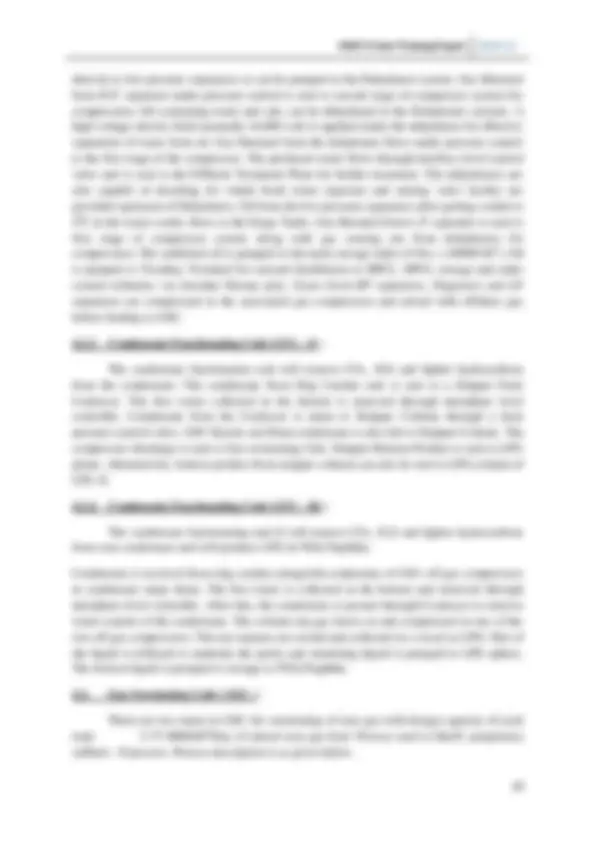
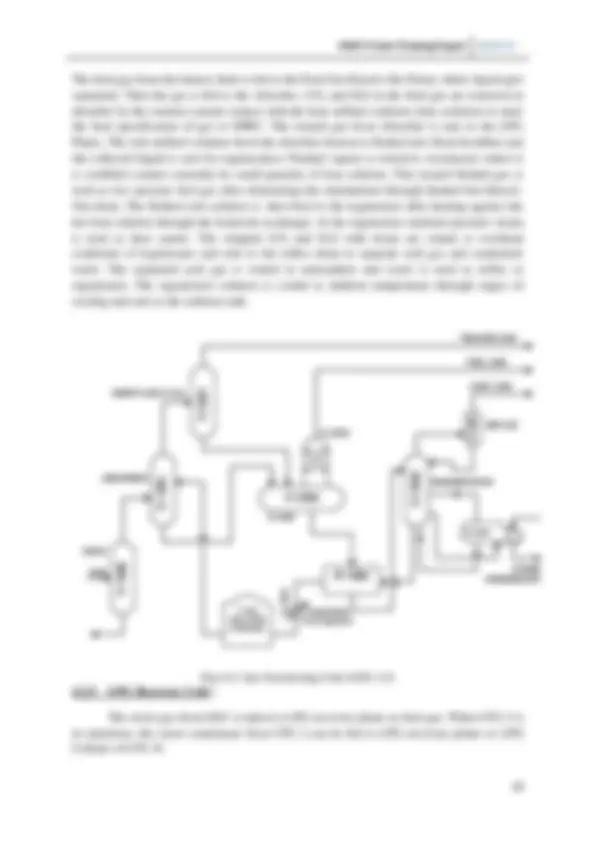
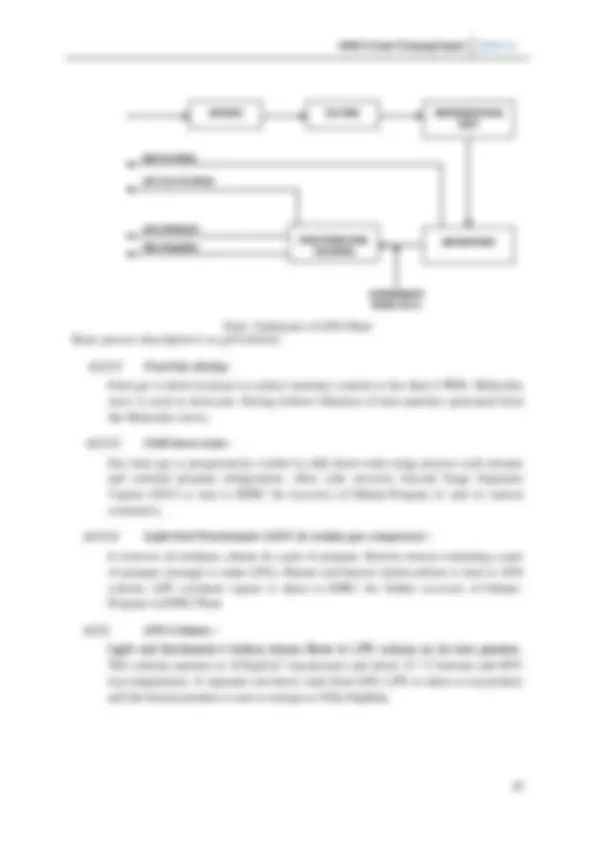
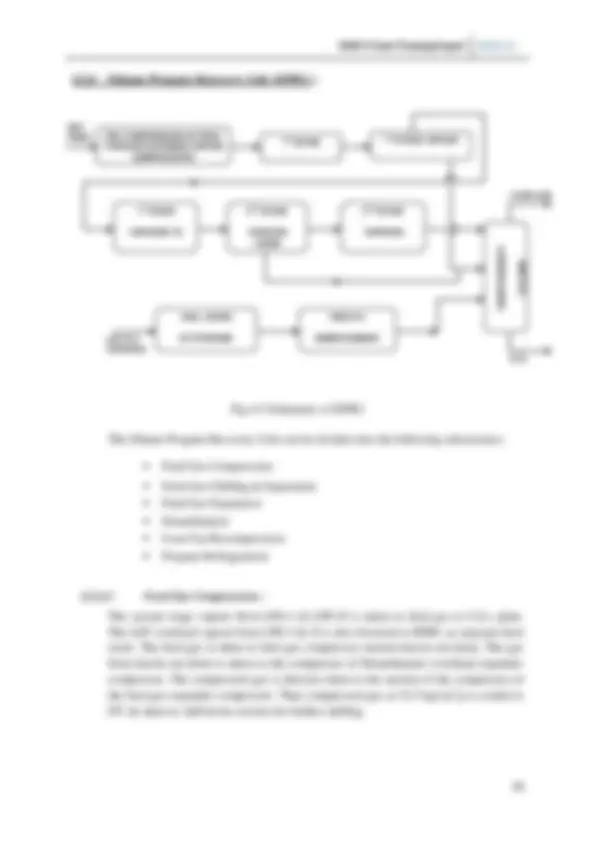
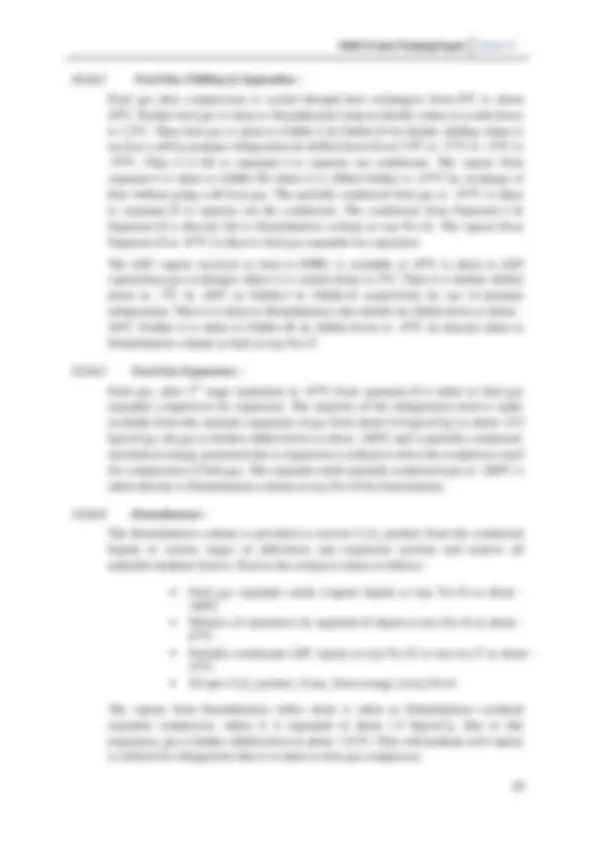

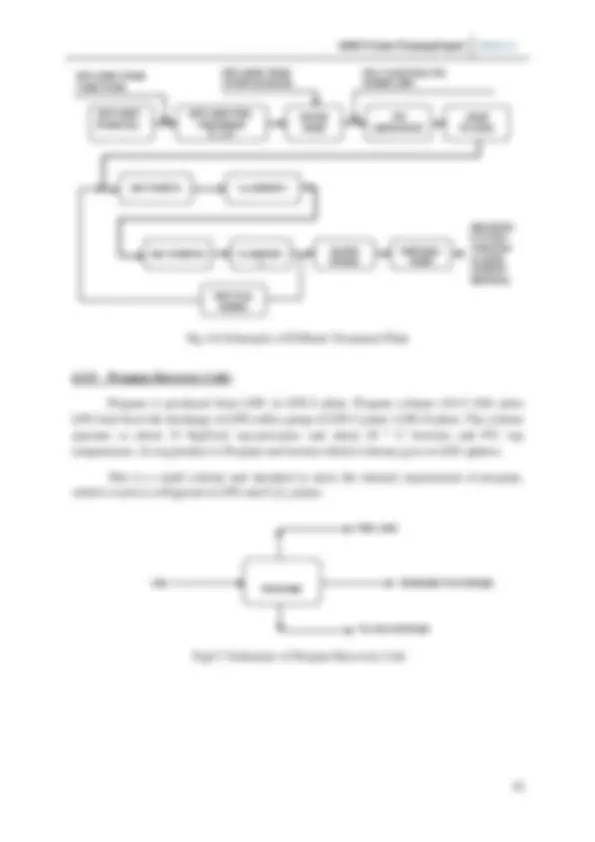
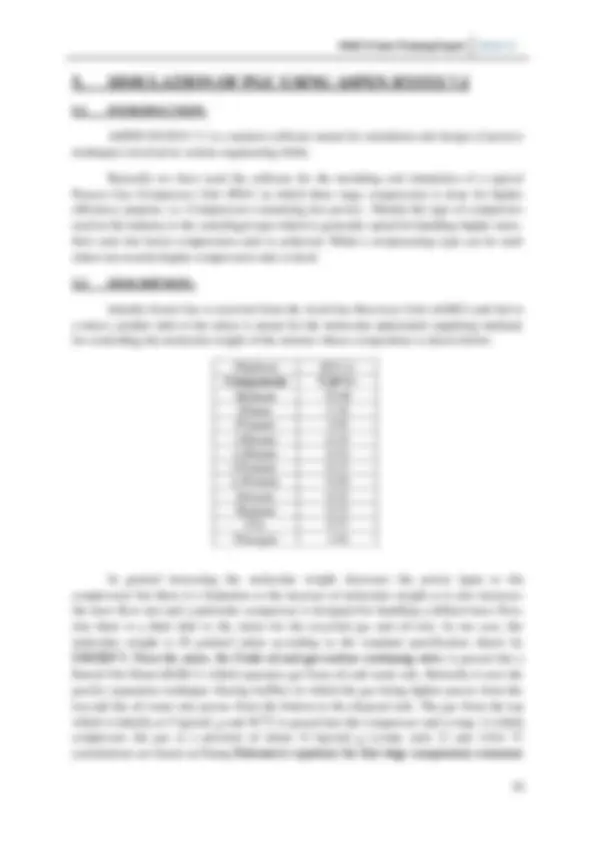
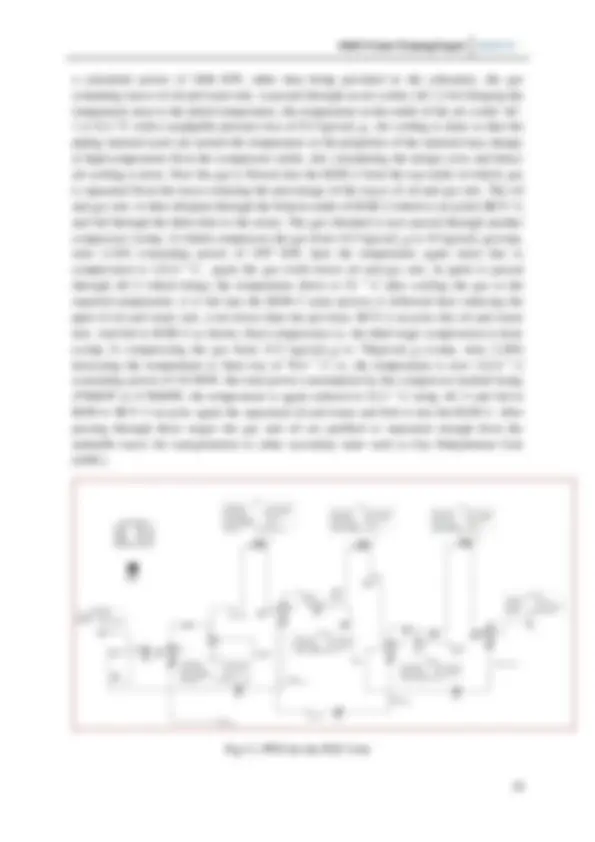
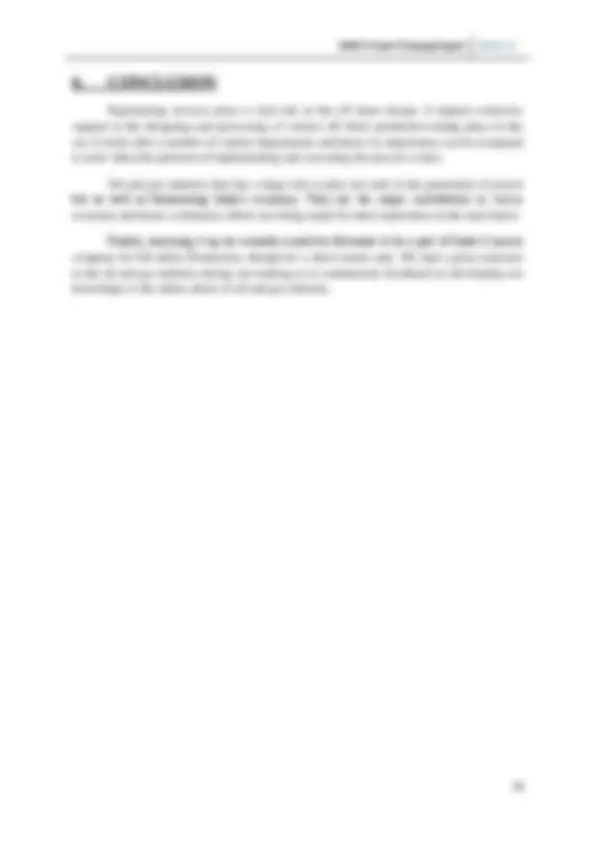
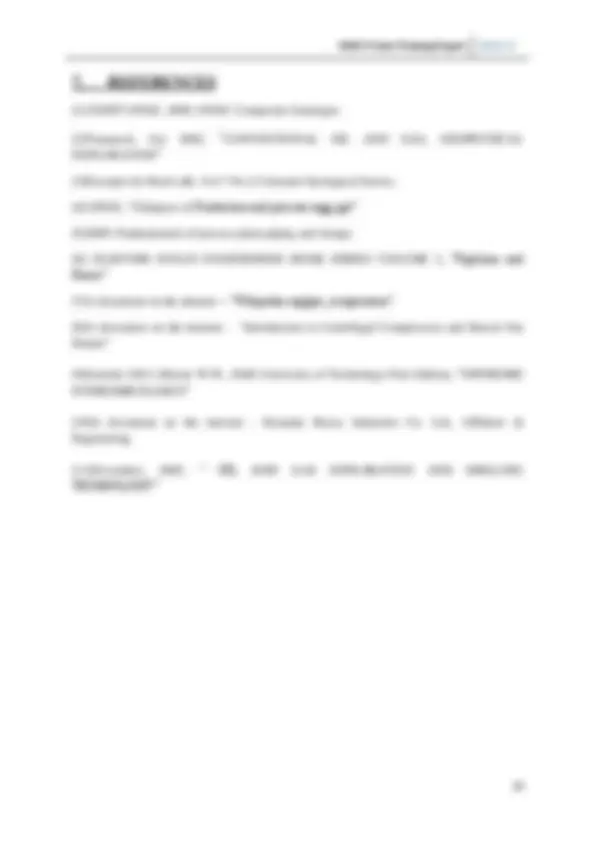
Study with the several resources on Docsity
Earn points by helping other students or get them with a premium plan
Prepare for your exams
Study with the several resources on Docsity
Earn points to download
Earn points by helping other students or get them with a premium plan
Community
Ask the community for help and clear up your study doubts
Discover the best universities in your country according to Docsity users
Free resources
Download our free guides on studying techniques, anxiety management strategies, and thesis advice from Docsity tutors
An overview of the key steps involved in the production of crude oil and natural gas. It covers the exploration and extraction processes, including drilling techniques, well completion, and the various processing units used to separate and refine the crude oil and natural gas. The document delves into the specific operations at the uran onshore facilities, which receive the crude oil and associated gas from the bombay high fields through subsea pipelines. It describes the different stages of the crude oil stabilization, gas sweetening, lpg recovery, and other processing units, highlighting the equipment and technologies used. The information presented in this document would be valuable for students and professionals interested in understanding the upstream oil and gas industry, the production processes, and the associated infrastructure and operations.
Typology: Cheat Sheet
1 / 35
This page cannot be seen from the preview
Don't miss anything!
CE(P), 11 High,
ONGC (MUMBAI).
ACKNOWLEDGEMENTS
We sincerely thank Mr. Basudeb Sarkar,CE(P) for taking us under his able mentorship. We also thank specially Mr. Sudip Gupta,CE(P) and Mr. K.C. Deka,CE(CIVIL) for helping us throughout this period .We also give sincere thanks to Mr. P.L.N. Laxminarayan,CE(M) , Mr. Pranjal Sarma,SE(M) , Mr. A. Sezhian,DGM(E) , Mrs. Elizabeth,SE(I), Mr. K. Thakuria,SE(M),Mr. Dilip Mondal,SE(E&T), Mr. Maruti Viswakarma,AEE(E), Mr. V.N. Mathur,DGM(Civil) ,Mr. Samar Das,CE(D) Mr. N.M. Ghavri,Senior Drawing Officer and Mr. R.V. Gawande,EE(M), for giving us their valuable time and sharing their knowledge with us.
We also thank Mr. B.B. Nayak,DGM(P) and Mr. S.R. Chowdhury,CE(P) for guiding us on our visit to the URAN plant.
We also express our gratitude towards Mr. Alok Bali, Supdtg. Geologist and RTI, ONGC(Mumbai) without the help of whom it would not have been possible for us to undergo this training.
We thank Oil and Natural Gas Corporation Limited, Mumbai for giving us an opportunity to have an industrial exposure under the guidance of the experts.
We also thank all of them who have directly or indirectly helped us during the tenure of our training.
Sincerely thanking all of the above once again, we hope to continue to take the guide from the aforementioned in near future. It has been a great experience for all of us.
Department of Mechanical Engineering, National Institute of Technology Silchar.
ABSTRACT
We had an opportunity to undergo vocational training for 18 days (20.12.10 to 06.01.2011) in ONGC, Mumbai at the 11 High office. During this period, we had an exposure to various ongoing projects and procedures in different departments of offshore engineering services of the organization. We got an opportunity to discuss and learn a lot about the industrial processing and Development activities of ONGC.
There are basically two divisions under engineering services – Offshore Design Section (ODS) and Offshore Works Division (OWD). During the tenure of the training our focus was mainly on ODS, under which there are seven disciplines-
Apart from getting the overview of all these disciplines, we have also worked on a small project on PGC, along with a single day visit to the process platform at URAN, and an overview of the basics of drilling processes.
ABOUT ONGC
ONGC Ltd. Is recognized as the Numero Uno E&P company in the world and 25th^ among the leading global energy measures as per ―Platts Top 250‖ Global Energy Company Ranking
ONGC Group of Companies comprises of
Oil and Natural Gas Corporation Limited (ONGC) is India's Most Valuable Company, having a market share of above 80% in India's Crude Oil and Natural Gas Exploration and Production. ONGC registered the highest profit among all Indian companies with Rs. 19872 Crores in the year 2007-08. ONGC also produces Value-Added Products (VAP) like C2-C3, LPG, Naphtha and SKO.
ONGC Videsh Limited (OVL) is overseas arm of ONGC, engaged in Exploration & Production Activities. It trans-nationally operates E&P Business in 10 countries, making ONGC the biggest Indian Multinational Corporation. In recent years, it has laid footholds in hydrocarbon acreage in various countries including Ivory Cost and Australia. ONGC Nile Ganga BV is a wholly owned subsidiary of OVL and has equity in producing field in Sudan.
ONGC envisages organizing Import/International Sale of Crude Oil and Export of Petroleum Products through Tendering Procedure for all the Group Companies. However, it would be restricted to the Companies/ Firms/ Vendors registered with ONGC on its approved Vendor Lists.[1]
geological time. Three conditions must be present for oil reservoirs to form: a source rock rich in hydrocarbon material buried deep enough for subterranean heat to cook it into oil; a porous and permeable reservoir rock for it to accumulate in; and a cap rock (seal) or other mechanism that prevents it from escaping to the surface. Within these reservoirs, fluids will typically organize themselves like a three-layer cake with a layer of water below the oil layer and a layer of gas above it according to their densities, although the different layers vary in size between reservoirs. Because most hydrocarbons are lighter than rock or water, they often migrate upward through adjacent rock layers until either reaching the surface or becoming trapped within porous rocks (known as reservoirs) by impermeable rocks above. However, the process is influenced by underground water flows, causing oil to migrate hundreds of kilometers horizontally or even short distances downward before becoming trapped in a reservoir. When hydrocarbons are concentrated in a trap, an oil field forms, from which the liquid can be extracted by drilling and pumping.[3]
Fig1.2: Hydrocarbon trapping in an anticline structure[4]
Prospects must be well defined in order to obtain oil and gas leases from landowners prior to the drilling of a wildcat well after the necessary land work has been completed, the drilling rig is moved on site and crews work 24 hours a day to drill a hole for the calculated depth.
Once the hole has been drilled to the target formation, the well is logged with electronic downhole measurement tools to record the characteristics of the subsurface rock formations. If logging indicates the well is productive, it is cased with steel pipe and a wellhead of shutoff valves is installed to prepare for production. The well is completed by perforating holes in the casing at the depth of the producing formation. Once a successful test well or series of wells has been drilled, the economic potential of the hydrocarbon discovery must be determined. This step includes estimating how much oil and gas is present (reserves), the probable selling price, the cost of continuing the exploration effort as well as the cost of full field development, and the taxes, royalties, and other expenses associated with producing the oil field. If the venture looks promising, the final step is taken—development of a newly discovered field.[3]
Fig1.3: Typical oil and gas Fig1.4: Overview of Oil and Gas Production [2]
Well Configuration [4]
Offshore productions consists of a number of operations that allow the safe and efficient production of hydrocarbons from the flowing wells. The key operations that will be conducted at the offshore platform include:
Produced Hydrocarbon Separation Gas Processing Oil and Gas Export Well Testing Produced Water Treatment and Injection Utillities to support these processes
Fig1.5: Schematic Diagram of an Offshore Process Complex[4]
is normally a tube/shell type where oil passes though tubes in a cooling medium placed inside an outer shell. The third stage basically uses a Flash-Drum. Further reduction of water percentage is done in the GDU (Gas Dehydration Unit). On an installation such as this, when the water cut is high, there will be a huge amount of produced water. Water must be cleaned before discharge to sea. Often this water contains sand particles bound to the oil/water emulsion. The environmental regulations in most countries are quite strict, It also places limits other forms of contaminants. This still means up to one barrel of oil per day for the above production, but in this form, the microscopic oil drops are broken down fast by natural bacteria. Various equipments are used, First sand is removed from the water by using a sand cyclone. The water then goes to a hydrocyclone, a centrifugal separator that will remove oil drops. The hydrocyclone creates a standing vortex where oil collects in the middle and water is forced to the side. Finally the water is collected in the water de-gassing drum. Dispersed gas will slowly rise to the surface and pull remaining oil droplets to the surface by flotation. The surface oil film is drained, and the produced water can be discharged to sea. Recovered oil in the water treatment system is typically recycled to the third stage separators. The gas train consist of several stages, each taking gas from a suitable pressure level in the production separator’s gas outlet, and from the previous stage. Incoming gas is first cooled in a heat exchanger and goes into the compressors. For the compressor operate in an efficient way, the temperature of the gas should be low. The lower the temperature is the less energy will be used to compress the gas for a given final pressure and temperature. Temperature exchangers of various forms are used to cool the gas, The separated gas may contain mist and other liquid droplets. Liquid drops of water and hydrocarbons also form when the gas is cooled in the heat exchanger, and must be removed before it reaches the compressor. If liquid droplets enter the compressor they will erode the fast rotating blades for which gas is passed through a scrubber and reboiler system to remove the remaining fraction of water from the gas. When the gas is exported, many gas trains include additional equipment for further gas processing, to remove unwanted components such as hydrogen sulphide and carbon dioxide. These gases are called sour gas and sweetening /acid removal is the process of taking them out.
The gas pipeline is fed from the High Pressure compressors. Oil pipelines are driven by separate booster pumps. For longer pipelines, intermediate compressor stations or pump stations will be required due to distance or crossing of mountain ranges.
2. OFFSHORE DESIGN SECTIONS
There are basically two divisions under engineering services – Offshore Design Section (ODS) and Offshore Works Division (OWD). During the tenure of the training our focus was mainly on ODS, under which there are seven disciplines-
This discipline lays out the initial specifications required for the process platform in the offshore. Any process platform is the gathering and distribution point for all the pipelines i.e. well fluid lines, lift gas lines and oil export line for tanker loading. All the processing facilities i.e. separation, produced water treatment, gas compression and dehydration, gas sweetening is installed on this platform. In addition there are testing facilities for testing of production coming from individual platforms.
Therefore, using many softwares like ASPEN HYSYS, SMARTPLANT etc. the process discipline under ODS drafts out the basic plans for any offshore process platform. The various diagrams like PFDs (Process Flow Diagram) and P&IDs (Piping and instrumentation diagram) are being designed by the people of this discipline. After the process design is completed the feasibility study for the designed process is carried out for future bidding and finalisation for the design.
The piping discipline under ODS looks after the pipes on the process platform. Plant layout and design of piping systems constitutes a major part of the design and engineering effort. Basically the following are the main tasks carried out by this discipline:
Piping and instrumentation diagrams (P&IDs) Piping design and engineering principles Terminology, symbols and abbreviations used in piping design Piping materials Piping specifications and piping codes Components of piping systems - fittings, flanges and valves[5]
Fig 2.2 Flowline design process
Fig. Below shows the laying of the subsea pipeline, a number of pieces of pipes are welded on the barge and the assembly is made to shift slowly, the assembly acts as a thread and lay down on the seabed
Fig 2.3 Laying of Subsea pipeline on the seabed.
Instrumentation discipline comes into play after the process platform has been designed by the process design section with the help of a P&ID. This discipline helps in controlling and automating all the process parameters involved in the offshore as well as in the onshore process platforms.
The various controlling instruments looked after by this discipline may be either pneumatic or electronic. It deals with the measurement of pressure, temperature, flow-rates with the help pressure transducers, temperature sensors (RTD, Thermocouples etc.) and flow meters respectively. Instrumentation discipline also takes care of the ―Shut Down Panel‖ which shuts down all the processes in case of an emergency.
Every power plant needs one or the other way electrical power for its proper functioning. For an offshore platform it requires huge electrical power to run all the mechanical devices employed, living quarters electrical consumption and also some power to run various instruments.
For any general platform of ONGC, it requires about 20-25 MW or more power to run the system. To produce such large amount of power is challenging. For this ONGC has its own power production unit where power is generated by a portion of the natural gas produced. There are huge Gas Turbine Units (GTU) for power production. Also the circuit breaker station is installed on the platform itself. For some other purposes which may require small power say few KWs, power is generated by the renewable sources of energy like solar energy, wind energy etc.
The Mechanical devices such as Turbines, Compressors, Pumps, Heat Exchangers etc. are the basics for a plant to operate and such devices are included under the Mechanical discipline for both running and maintenance of the same. A small introduction about the main mechanical units operating in a offshore process platform is given below
2.6.1 Gas Turbines
Gas Turbines are used for the power production by rotation of the turbine shaft by steam generated due to heat generated by burning a portion of natural gas produced. An efficient gas turbine used in a power plant produces about 10-15 MW of power under optimized conditions. Special care is taken for the inlet gas entering into the turbine as wet gas may corrode the blades of the turbine and also reduces the efficiency furthermore due to corrosion it may cost economic loss to the plant.
the pipes which helps in avoiding condensate formation. Also since compressors require the temperature of the entering gas to be low for its efficient working temperature exchangers of various forms are used to cool the gas.
2.6.4 Knock Out Drums (KOD)
The knock out drums is used for the separation of gas and oil from the saline water. Mainly the principle involved is the gravity separation (baffle plates are present inside them) in which the components are separated depending on their density.
2.6.5 Pumps
Pumps are basically used for transporting incompressible fluids like crude oil by creating large pressure difference for its transportation along pipelines. Presently in ONGC centrifugal type pumps are used for general purposes.
Structure discipline designs the supporting structure of the platform and the topside considering the stress analysis criteria. They use many softwares like SACS, MicroStation etc. for the design purposes.
2.7.1 Supporting Structures
The supporting structure on which the platform rests is divided into:
2.7.1.1 Jackets
Jackets are broadly classified into 3/4/6/8 legged, depending upon the surface area of the platform required. A jacket can be used only for smaller depth say 60-70 metres as the jacket structure rests on the seabed, a typical four legged jacket is shown below. The jacket supports a sub-frame with production equipment and accommodation deck on top of it. The jacket has to be transported on a barge to its installation site at sea. While installing jacket on the seabed steam hammering is done while piling them for stability. Sometimes skirt piles are also given for providing support to the bigger jacket structure. The other processes which are involved while installing the jacket are: cementing of legs of jacket, provision of the mud mat at the base, battering of the legs (single batter on one side and double batter on the other side, this is done in order to let the barge approach to the platform to install the drill rigs), provision for the riser is also included in the design.
Fig.2.5 A Four Legged Jacket[9]
2.7.1.2 FPSO
A Floating Production, Storage and Off-loading vessel (FPSO) is generally based on the use of a tanker hull, which has been converted for the purpose. Such vessels have a large storage capacity and deck area to accommodate the production equipment and accommodation. When converting old tankers for this purpose, special attention has to be paid to the fatigue life of the vessel.
Fig.2.6 FPSO[9]
2.7.1.3 Jack-Up Rigs
A jack-up is a mobile drilling unit that consists of a self-floating, flat box-type deck structure supporting the drilling rig, drilling equipment and accommodation. It stands on 3 or 4 vertical legs along which the platform can be self-elevated out of the water to a sufficient height to remain clear of the highest waves. Drilling operations take place in the elevated condition with the platform standing on the sea bed. This type of platform is used for drilling operations in water depths up to about 100 m. Jack-ups spend part of their life as floating structures. This is when such platforms are towed to a new location by means of ocean-going tugs. In this mode, the legs are lifted up and extend upwards over the platform.
mass of the structure, but the sea bed has to be levelled. The towers support a sub-frame with a production equipment and accommodation deck on top of it.
Fig 2.9. A GBS
2.7.1.6 Spar
Spar is basically a mono legged platform of smaller surface area and is mostly employed for larger depths of more than 1 km. All the basic facilities are provided on the platform for the various production purposes.
Fig 2.10 A Spar
2.7.1.7 Tension Leg Platform
A Tension Leg Platform (TLP) consists of a semi-submersible type hull with for instance four vertical surface-piercing columns standing on underwater floaters and supporting a large rectangular deck. At each of the four corners of the floater, pre tensioned tethers extend vertically downwards to foundation templates which are piled into the sea bed. Due to the vertical tendons, which are pre-tensioned to such a degree that they never become slack, any vertical motion of the TLP will be eliminated. This allows for steel pipe line
connections between the wells and the floater, without the need for flexible sections of pipe lines.[9]
Fig 2.11 A TLP
2.7.2 Topside
The topside is a structure resting on a supporting structure having all the basic facilities for the process, unmanned platforms. They are divided into:
Fig 2.12 The Topside with all the decks.[10]