
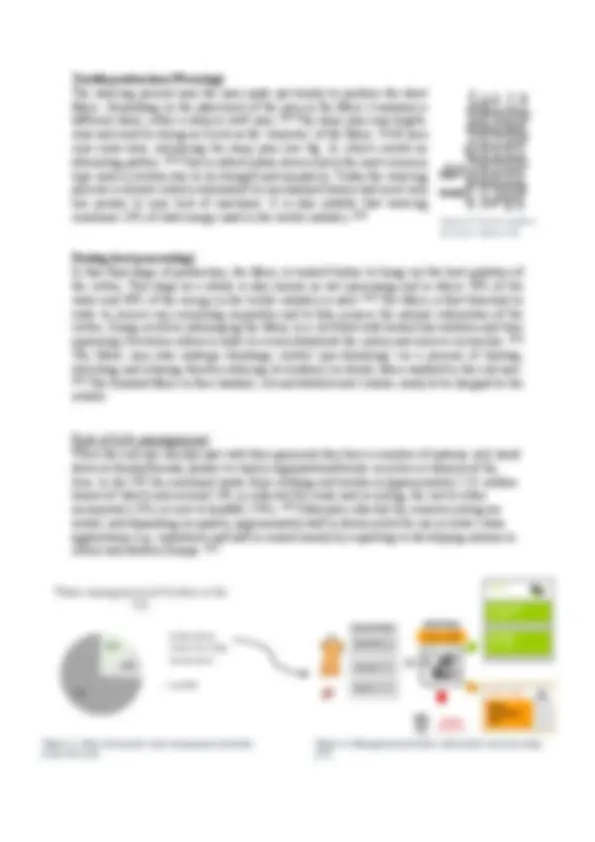
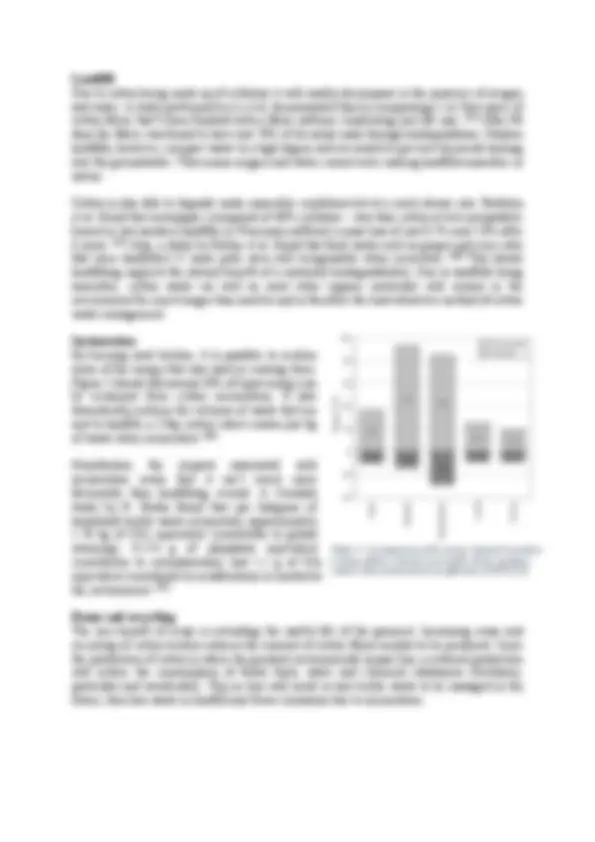
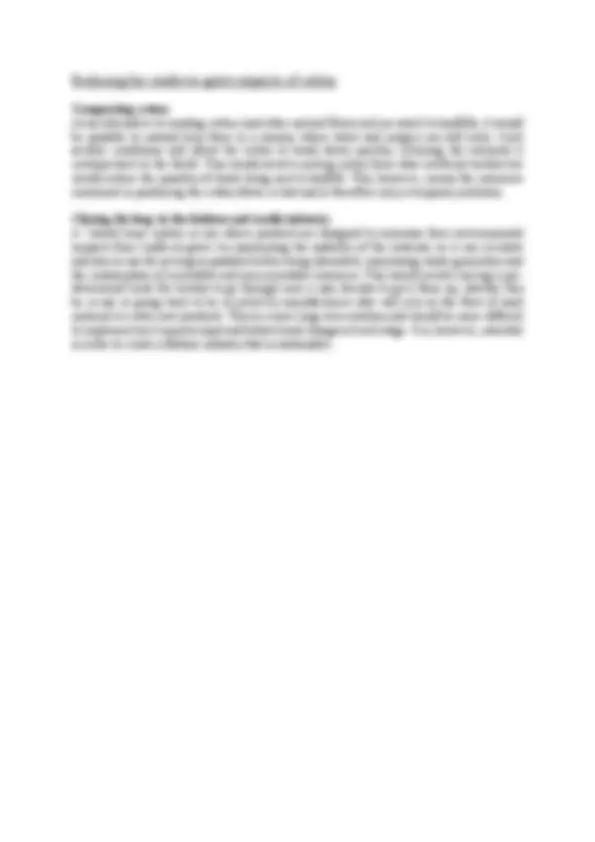
Study with the several resources on Docsity
Earn points by helping other students or get them with a premium plan
Prepare for your exams
Study with the several resources on Docsity
Earn points to download
Earn points by helping other students or get them with a premium plan
Community
Ask the community for help and clear up your study doubts
Discover the best universities in your country according to Docsity users
Free resources
Download our free guides on studying techniques, anxiety management strategies, and thesis advice from Docsity tutors
An in-depth analysis of the environmental impact of cotton production, from cultivation to disposal. It covers topics such as the leading cotton-producing countries, the environmental burdens of cotton production, the composition of cotton, the stages of cotton production, and the end-of-life management of cotton textiles. The document also discusses the environmental benefits and drawbacks of various methods for managing cotton waste, such as composting, incineration, and reuse/recycling.
Typology: Essays (university)
1 / 7
This page cannot be seen from the preview
Don't miss anything!
Cotton is a soft fibre that grows in tufts on the cotton plant (which belongs to the genus Gossypium ). [1]^ Due to it offering excellent properties including high durability, low weight and breathability (to name a few), cotton is the most used natural fibre in the clothing and textile industry. [2]^ Most recent estimates place worldwide cotton production at approximately 24.5 million tonnes, with China, India and America being the leading producers. [2]^ This figure is also steadily increasing, likely due in part to the current popularity of âfast clothingâ where consumers are spending less on clothes yet buying more. Producing this much cotton burdens the environment with vast amounts of land occupation, water consumption, emissions and chemical usage (pesticides and fertilisers). [2]^ For this reason, the item chosen to be investigated here is the cotton t-shirt. The environmental impacts of cotton production will be analysed as well as the fate of the material after disposal.
The t-shirt being investigated here is a âMenâs Supima cotton crew neck short sleeve t-shirtâ from Uniqlo. [3]^ Composed of 100% Pima cotton, âSupimaâ being a trademarked marketing name used to promote the extra-long staple (ELS) cotton grown in western America. [4]^ Pima cotton or Gossypium barbadense is a species of cotton known for its softness and unusually long fibres of over 1.5 inches in length, compared to around 1 inch for conventional cotton. [4] Pima cotton represents less than 1% of cotton grown worldwide and the long fibres make for a fabric that is more resistant to tearing and breaking. [4] Cotton fibres are composed almost entirely of cellulose as shown in Table 1 below. The specific chemical composition is dependant on the species, growing conditions (temperature, soil, water) and the level of maturity. [^6 ]^ Due to the presence of cellulose in the cotton plant, its cultivation acts as a carbon sink for the environment. However, when accounting for the emissions due to fertilisers and fuel/electricity (consumed by harvesting machinery), there is a net carbon dioxide emission of around 2.5kg equivalent per kg fibre harvested. [7] Component Amount (%) Cellulose 88 - 96. Proteins 1.0 - 1. Waxes 0.4 â 1. Pectins 0.4 â 1. Inorganics 0.7 â 1. Other substances 0.5 â 8.
Manufacturing cotton textiles is a complex procedure and involves skilled workers and intricate machinery. Production is split into five key stages: Cultivation, ginning, spinning, textile production and dyeingâ these are discussed in more detail below. Adding on to these the usage Figure 1 : Cotton fibres shown bursting from a seed capsule [5]. Table 2 : Composition of cotton on a dry basis [6].
and final disposal stages results in a total of seven stages the t-shirt will go through from cradle- to-grave, as shown in figure 2. Cultivation The first step is the preparation of the soil which involves ploughing and adding compost. Seeds are then planted whilst leaving adequate spacing between each plant. They are most commonly watered via drip irrigation as this eliminates water stress and reduces wastage. [^8 ] Due to the cotton plant being an ideal food source for some weevils and aphids, pesticide use is very common and so are weedicides for minimising weed growth. Fertiliser use also plays a big role in maximising cotton yield; where on average approximately 100kg Nitrogen, 60kg Phosphorus and 80kg Potassium fertiliser is used per hectare. [^8 ]^ Harvesting seed cotton is then performed either by hand or machine, manual picking being the slower option but better preserving the characteristics of the cotton. [^8 ] Ginning Seed cotton is then put into nearby cotton gins â machines that separate cotton from seeds and major debris. First the cotton goes through dryers to reduce the moisture content, facilitating the ginning process and inhibiting mildew growth. During ginning, revolving circular saws grab the cotton and pull it through closely spaced ribs that are too small for seeds to pass (see fig. 3). [^9 ]^ A blade then detaches the seeds from the cotton and the seeds are brushed away. [^9 ] The cotton that remains is then compressed into bales of around 220kg, [^9 ]^ ready for storage and transport. Spinning Once the bales of cotton have been transported from their origin to the place of textile manufacture yarn production can begin (In the case of the t-shirt under investigation, the pima cotton is imported from America to be manufactured in India). This starts off with separating the bales so that fibres can be gathered into loose strands. Strands are then combed, removing the shortest fibres in order to create a stronger yarn. The strands, which naturally vary in thickness along the length are then combined with up to eight other strands in order to create a more consistent thickness in a process called drawing. [1^1 ]^ This leads to the spinning stage where drawn strands enter a rotor to be spun into a yarn and are then finally wound up onto a bobbin. [1^1 ]^ The spinning stage consumes approximately 34% of total energy used in textile manufacture. [13] Figure 3 : A simple cotton gin. [ 10 ] Figure 2: A summary of the key stages in the life cycle of a cotton t-shirt as it goes from cradle-to-grave. [2]
Landfill Due to cotton being made up of cellulose it will readily decompose in the presence of oxygen and water. A study performed by Li et al. demonstrated this by composting a 1 x1 foot piece of cotton fabric thatâs been finished with a fabric softener (replicating real life use). [16]^ After 90 days the fabric was found to have lost 78% of its initial mass through biodegradation. Modern landfills, however, compact waste to a high degree and are sealed to prevent chemicals leaking into the groundwater. This means oxygen and water cannot enter making landfills anaerobic in nature. Cotton is also able to degrade under anaerobic conditions but at a much slower rate. Baldwin et al. found that newspaper (composed of 60% cellulose â less than cotton at but comparable) buried in two sanitary landfills in Wisconsin suffered a mass loss of just 8.5% and 5.6% after 6 years. [17]^ Also, a study by Rathje et al. found that food waste such as grapes and corn cobs that were landfilled 25 years prior were still recognisable when excavated. [18]^ This shows landfilling neglects the natural benefit of a materials biodegradability. Due to landfills being anaerobic, cotton waste (as well as most other organic materials) will remain in the environment for much longer than need be and is therefore the least attractive method of cotton waste management. Incineration By burning used textiles, it is possible to reclaim some of the energy that was used in creating them. Figure 7 shows that around 28% of input energy can be reclaimed from cotton incineration. It also dramatically reduces the volumes of waste that are sent to landfill; a 250g cotton t-shirt creates just 3g of waste when incinerated. [2^0 ] Nonetheless, the impacts associated with incineration mean that it isnât much more favourable than landfilling overall. A Swedish study by R. Bodin found that per kilogram of household textile waste incinerated, approximately 1.78 kg of CO 2 equivalent (contributes to global warming), 0.154 g of phosphate equivalent (contributes to eutrophication) and 1.1 g of SO 2 equivalent (contributes to acidification) is emitted to the environment. [21] Reuse and recycling The key benefit of reuse is extending the useful life of the garment. Increasing reuse and recycling of cotton textiles reduces the amount of cotton fibres needed to be produced. Since the production of cotton is where the greatest environmental impact lies, a reduced production will reduce the consumption of fossil fuels, water and chemical substances (fertilisers, pesticides and weedicides). This in turn will result in less textile waste to be managed in the future, thus less waste in landfill and fewer emissions due to incineration. Figure 7: A comparison of the energy required to produce a range of fibres with the recoverable energy (negative values) when incinerated at an efficiency of 60%. [19]
Composting cotton As an alternative to sending cotton (and other natural fibres such as wool) to landfills, it would be possible to instead bury them in a manner where water and oxygen can still enter. Such aerobic conditions will allow the cotton to break down quickly, returning the nutrients it contains back to the Earth. This would involve sorting cotton from other artificial textiles but would reduce the quantity of waste being sent to landfill. This, however, means the resources consumed in producing the cotton fabric is lost and is therefore only a temporary solution. Closing the loop in the fashion and textile industry A âclosed loopâ system is one where products are designed to minimise their environmental impacts from cradle-to-grave by maximising the usability of the material, so it can circulate and stay in use for as long as possible before being discarded, minimising waste generation and the consumption of renewable and non-renewable resources. This would involve having a pre- determined route for textiles to go through once a user decides to give them up, whether this be re-use or going back to be recycled by manufacturers who will rely on the flow of used material to create new products. This is a more long-term solution and would be more difficult to implement as it requires input and behavioural changes at each stage. It is, however, essential in order to create a fashion industry that is sustainable.
[16] Biodegradability Study on Cotton and Polyester Fabrics https://www.jeffjournal.org/papers/Volume5/5- 4 - 6Frey.pdf [17] Decomposition of specific materials buried within sanitary landfill. Baldwin et al. [18] Rubbish! The Archeaology of Garbage. William Rathje & Cullen Murphy ISBN 0- 06 - 016603 - 7; Harpercollins (hardback, 1992) [19] Waste: A Handbook for Management. Trevor M. Letcher and Daniel A. Vallero. 2011. 978 - 0 - 12 - 381475 - 3 [20] Well dressed? The present and future sustainability of clothing and textiles in the United Kingdom [21] To Reuse or to Incinerate? Robert Bodin