
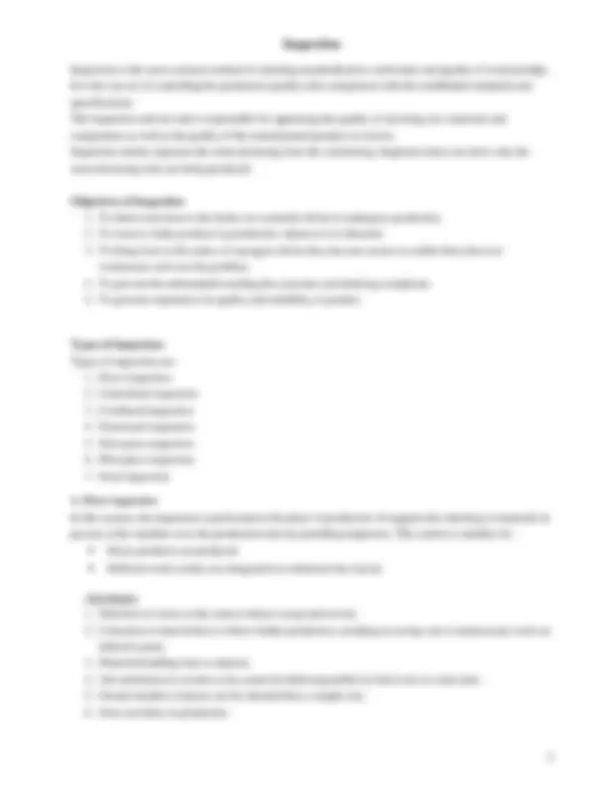
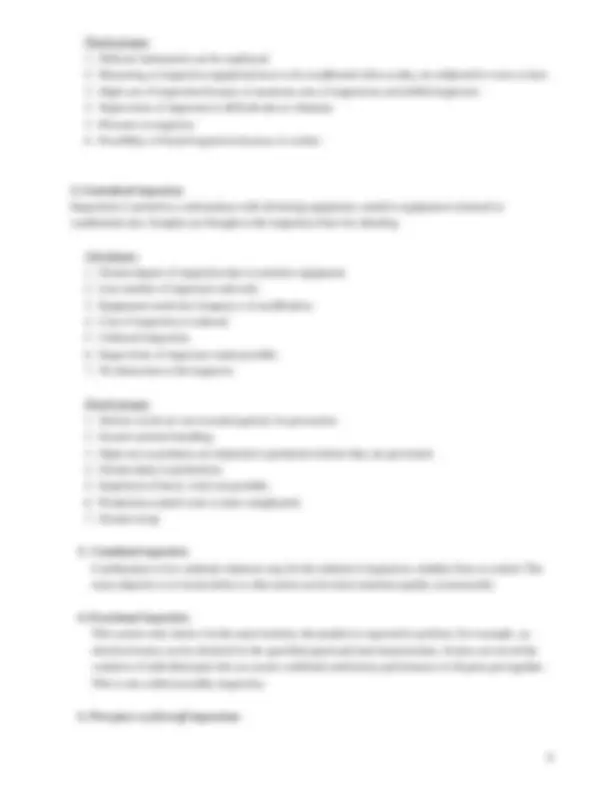
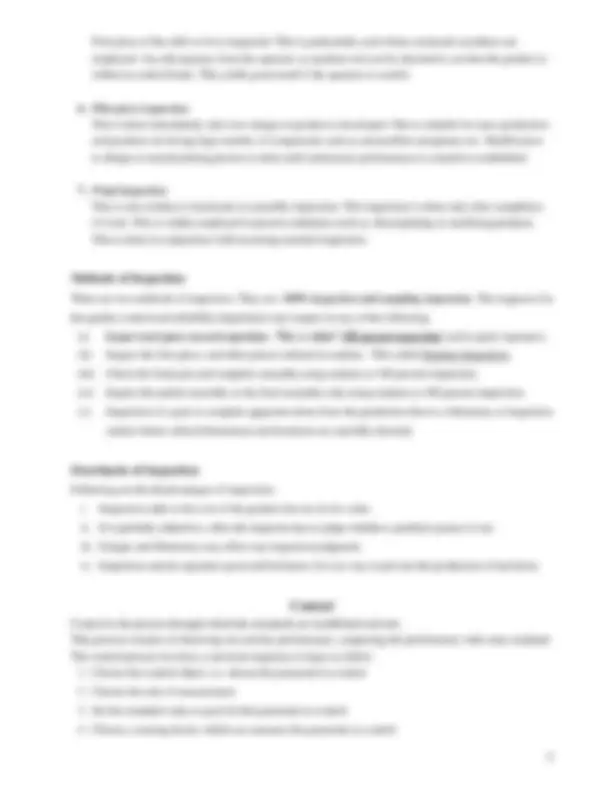
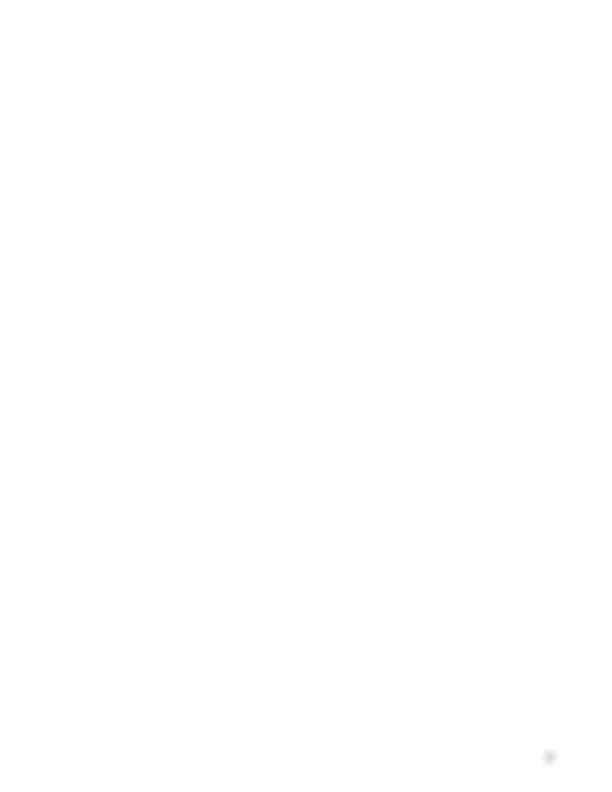
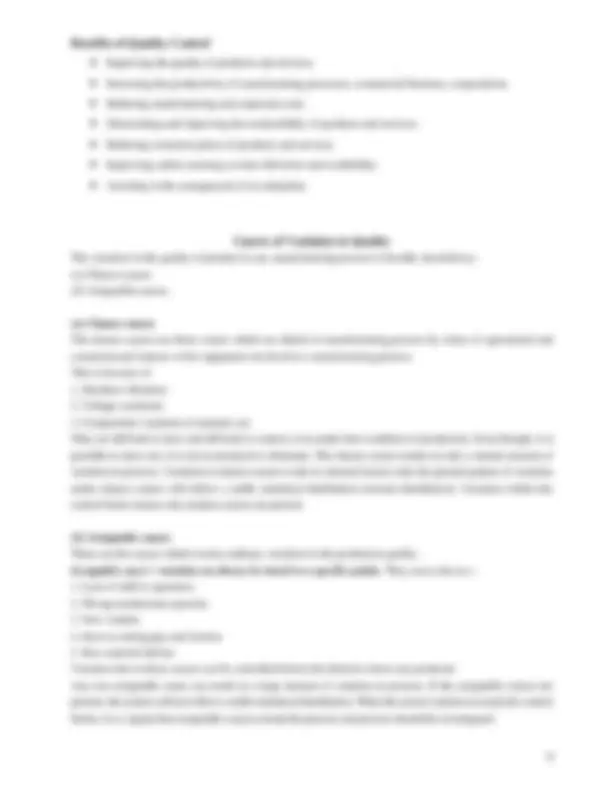
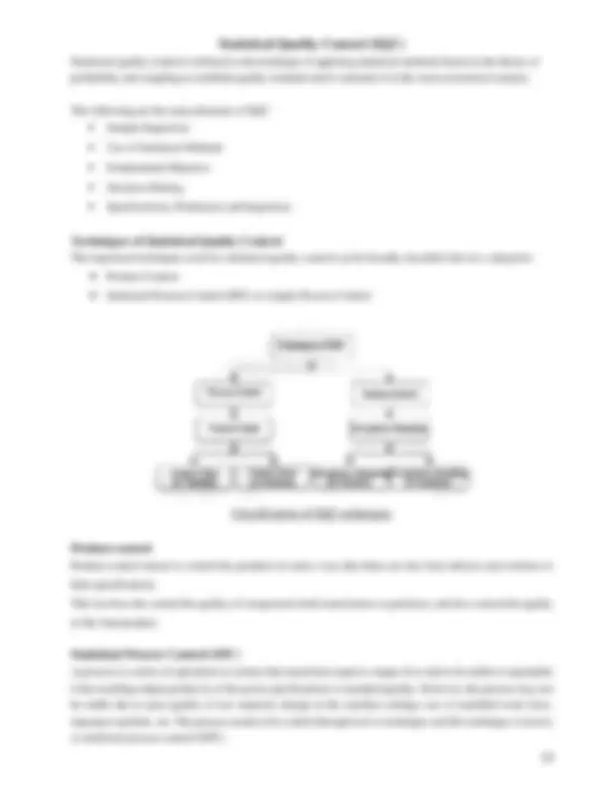
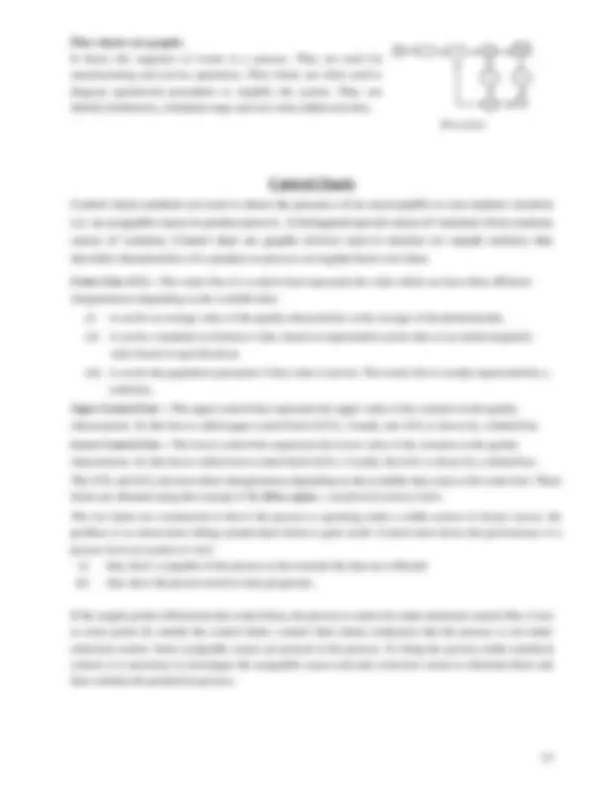
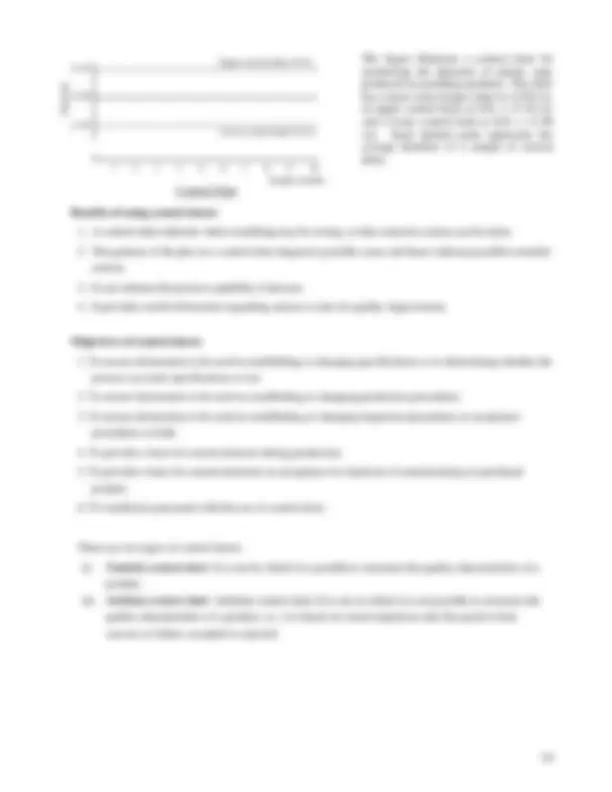
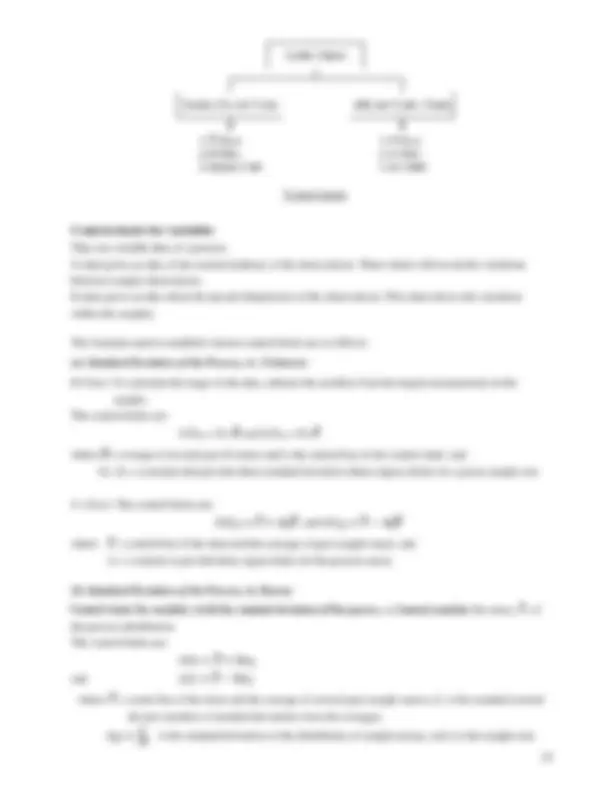
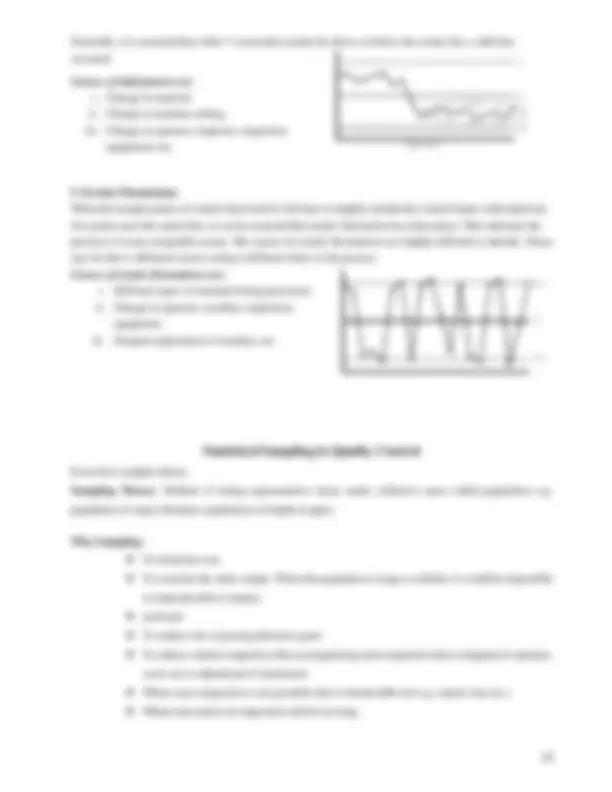
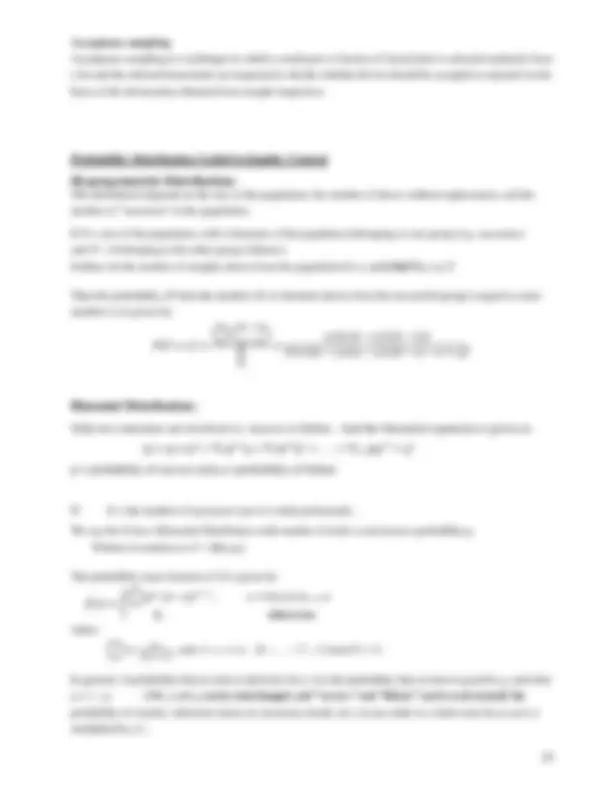
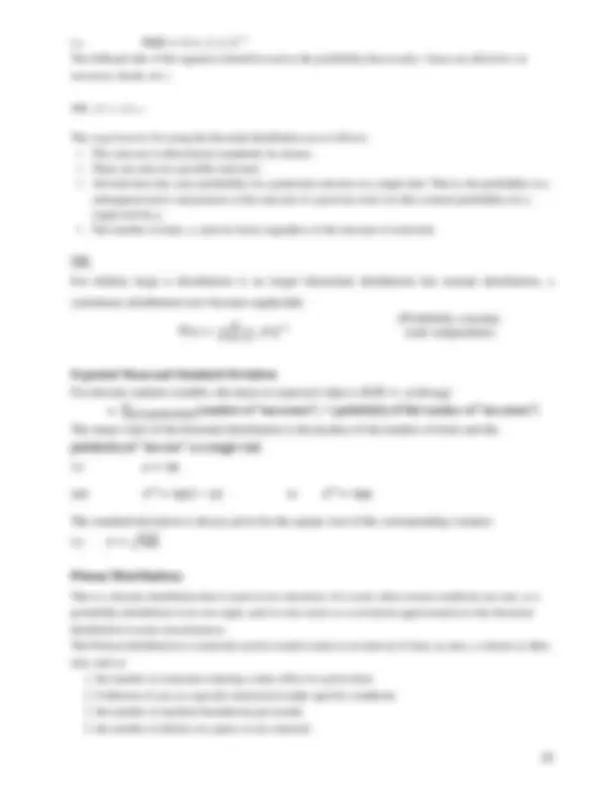
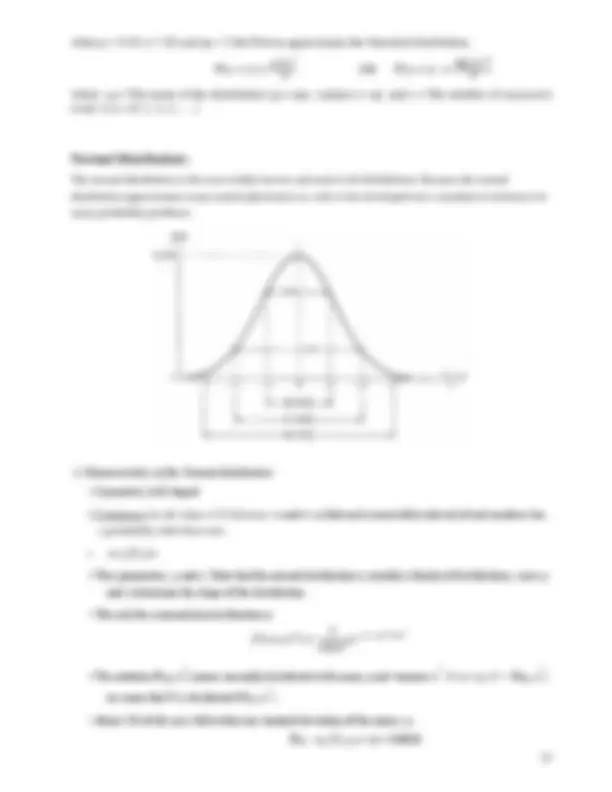
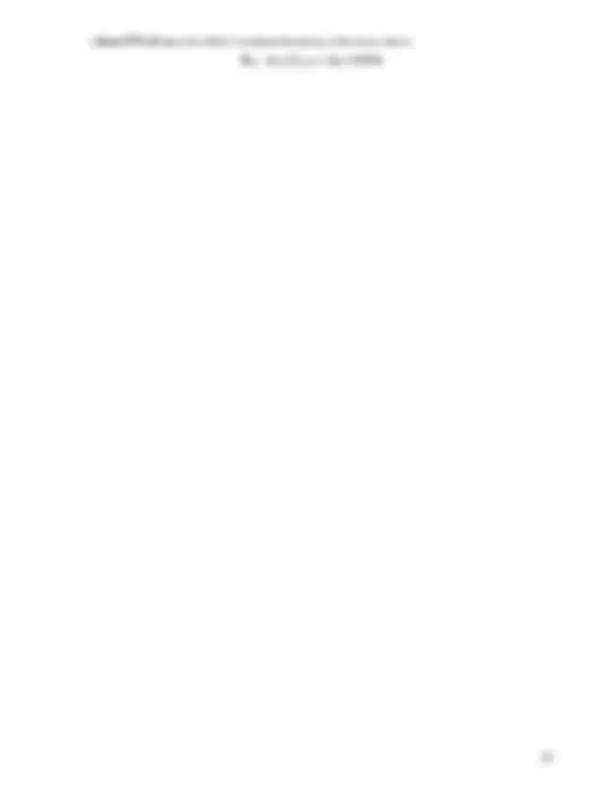
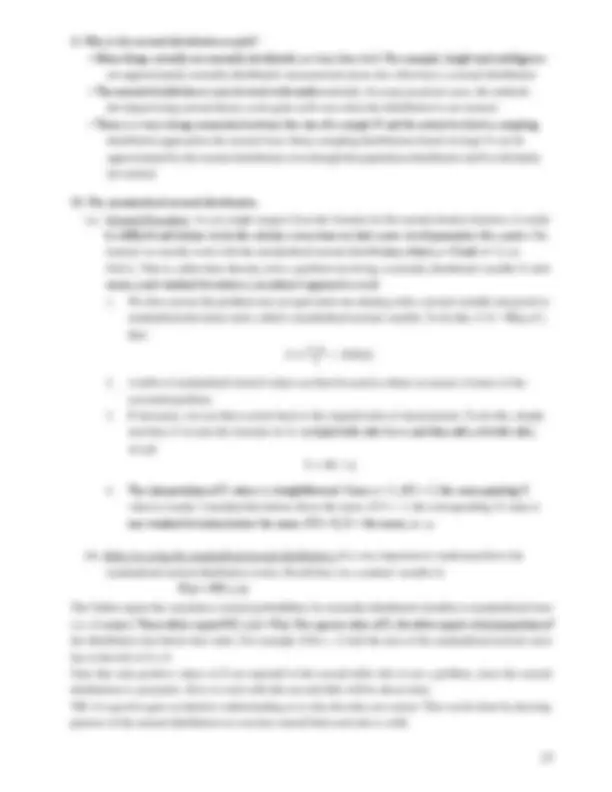
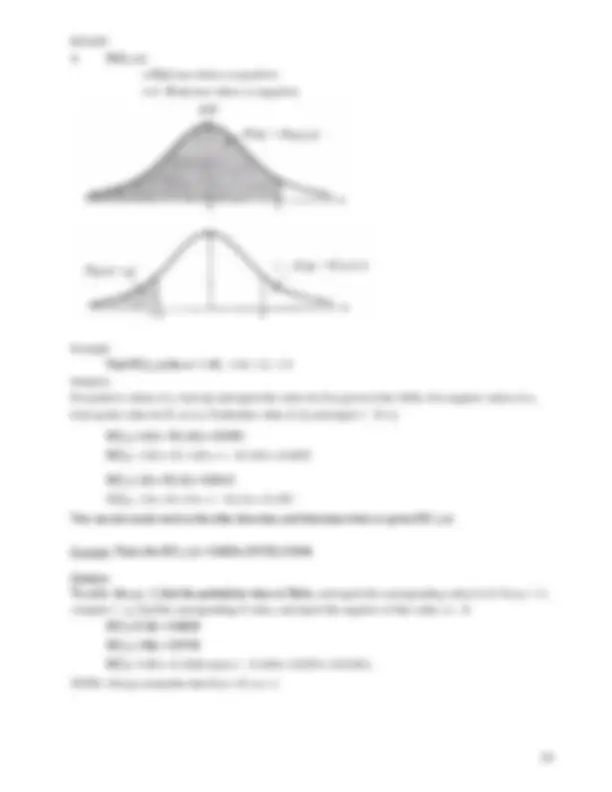
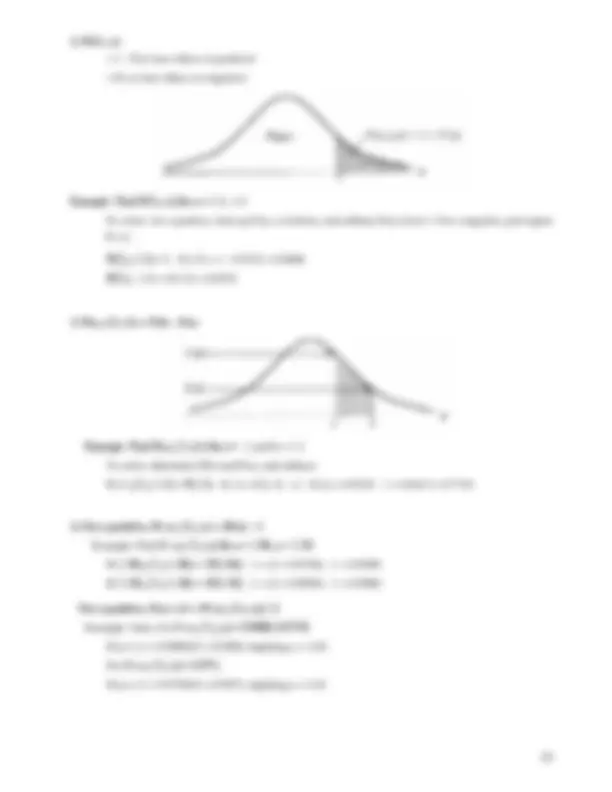
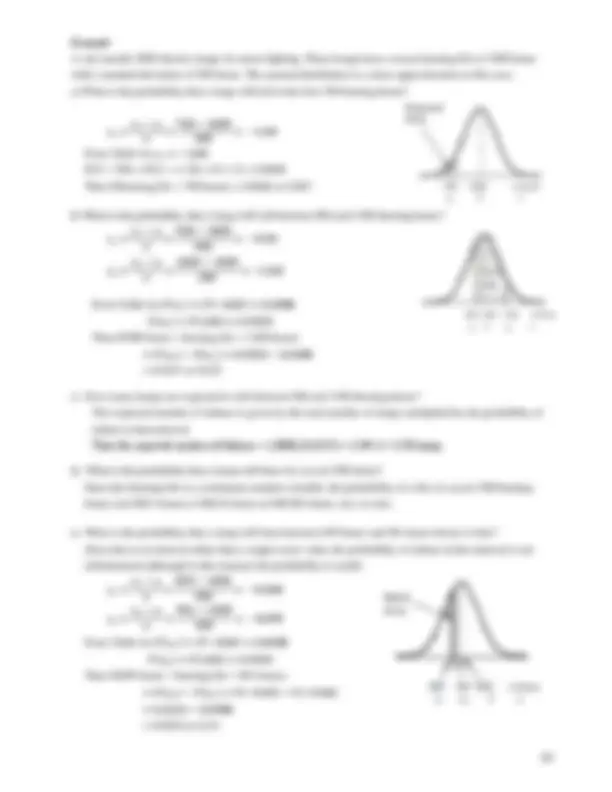
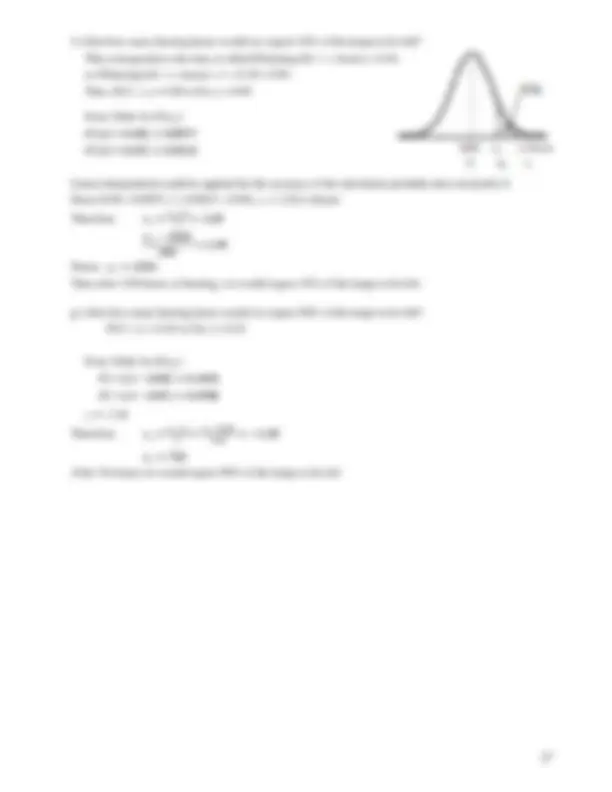

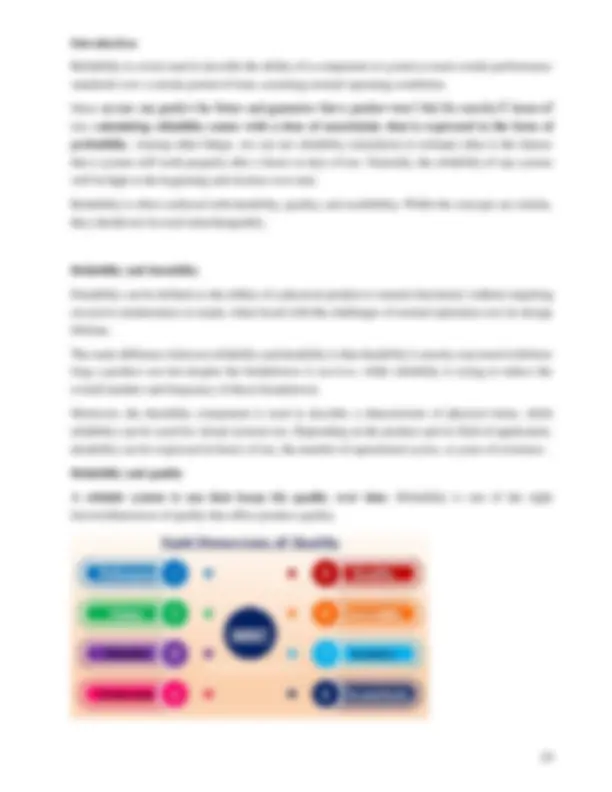
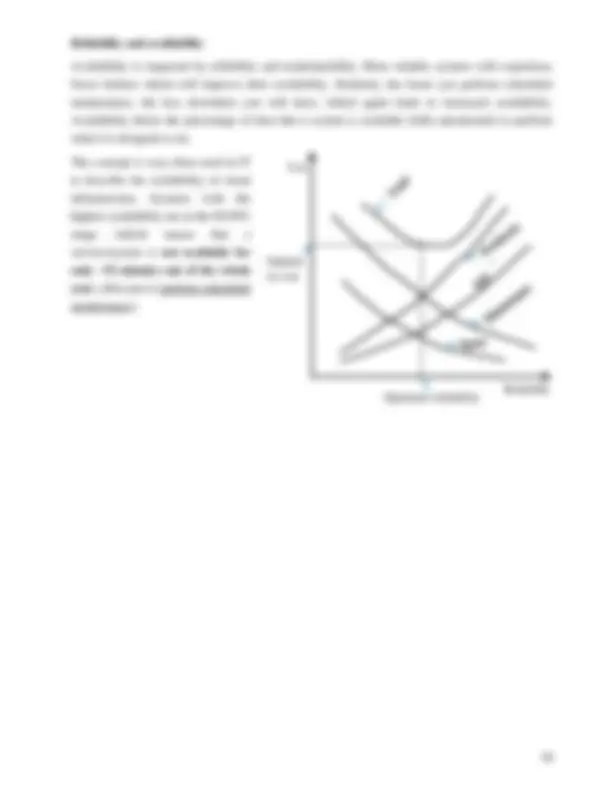
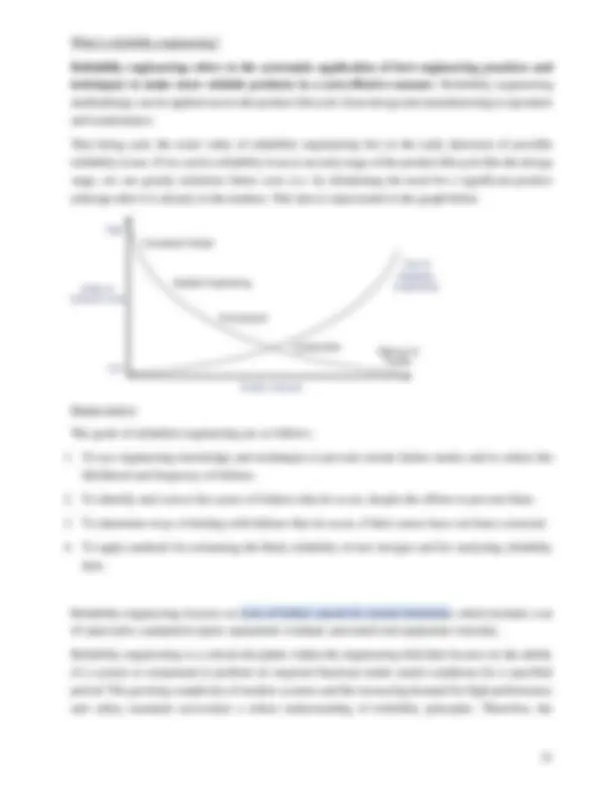
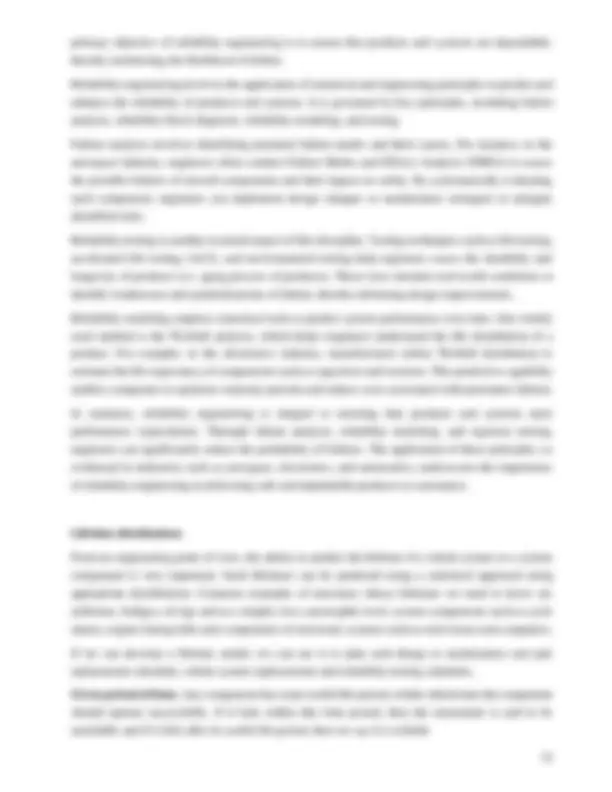
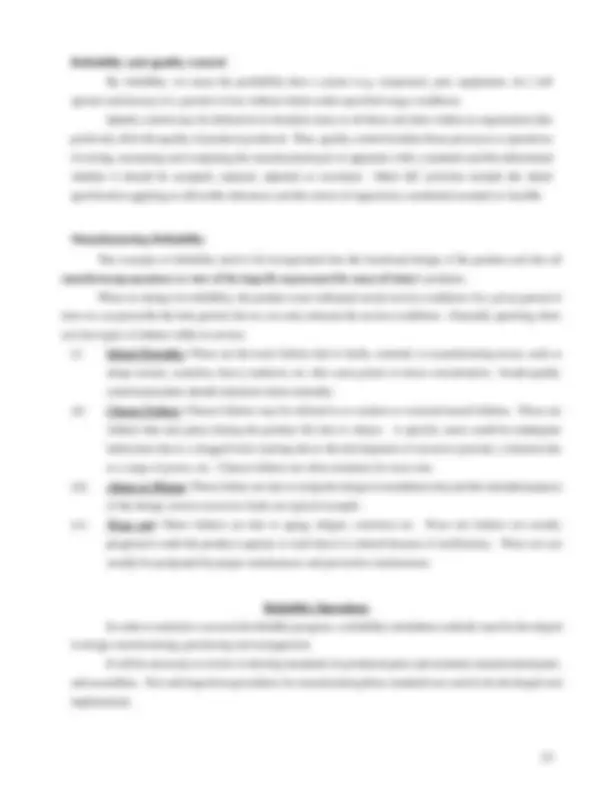
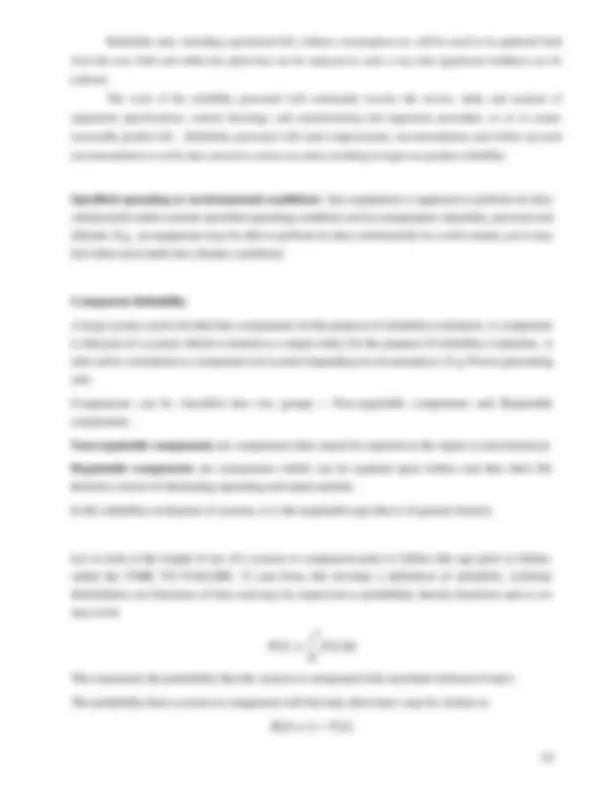
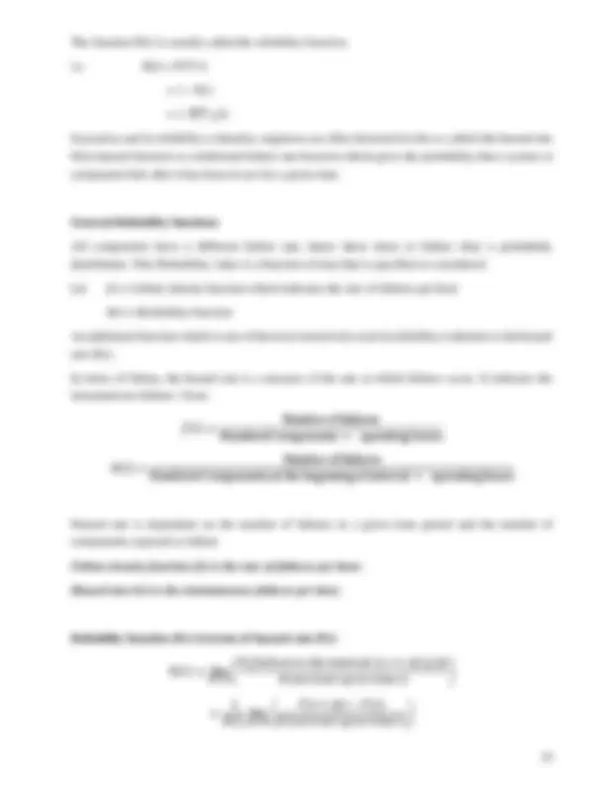
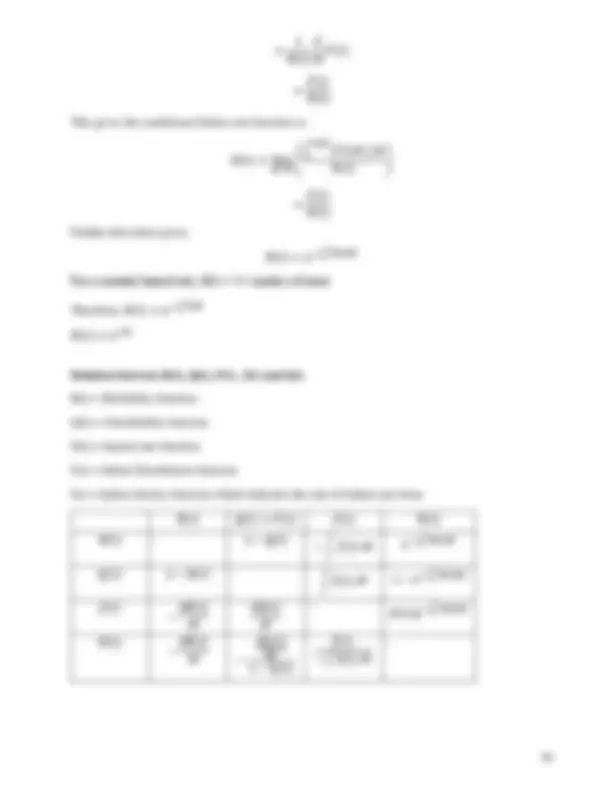
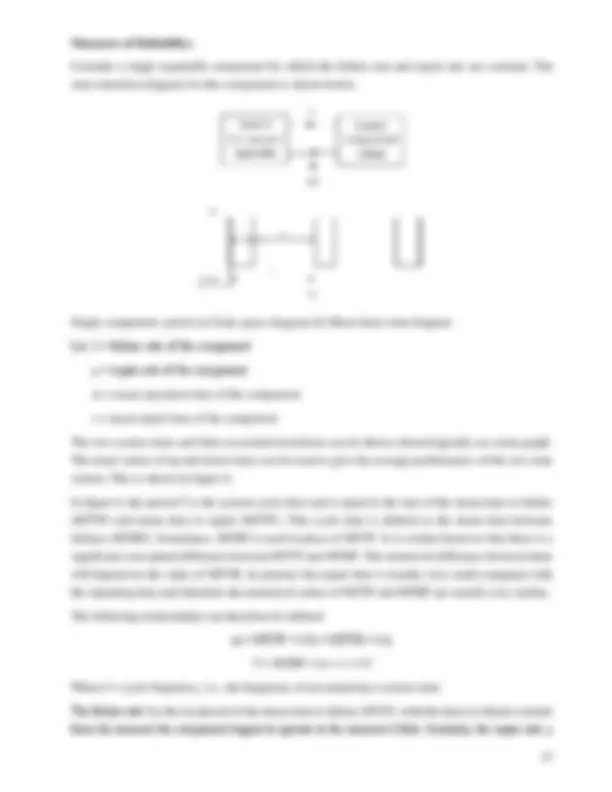
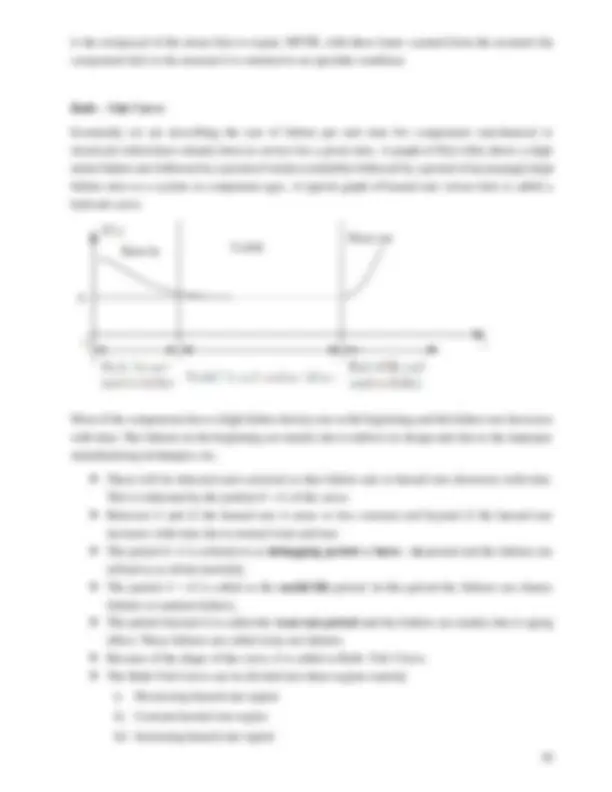
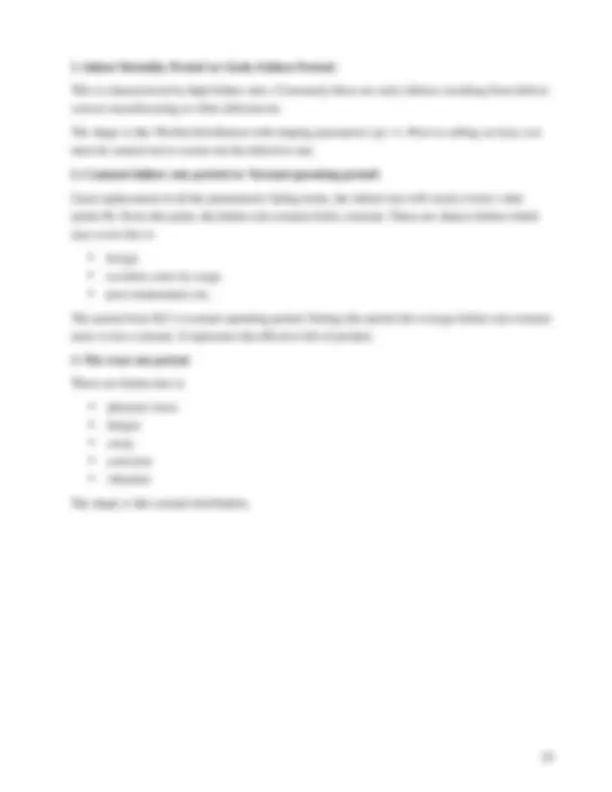
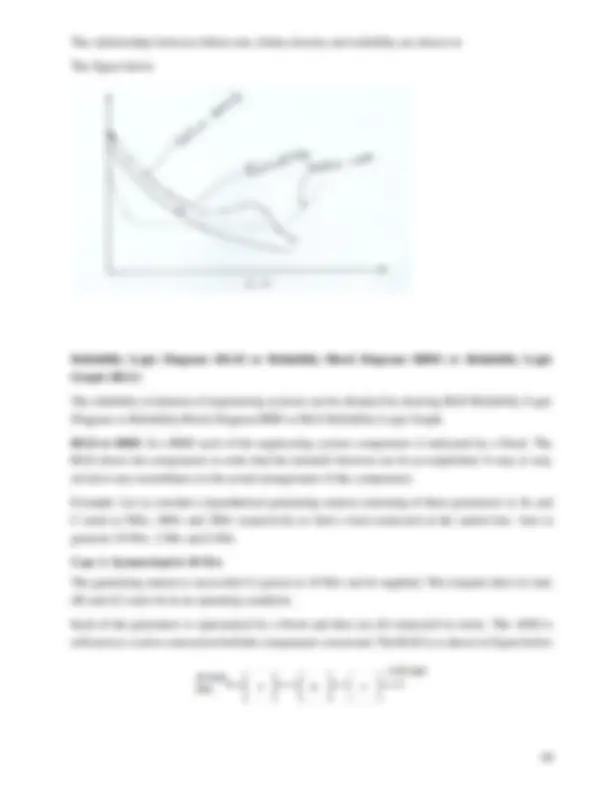
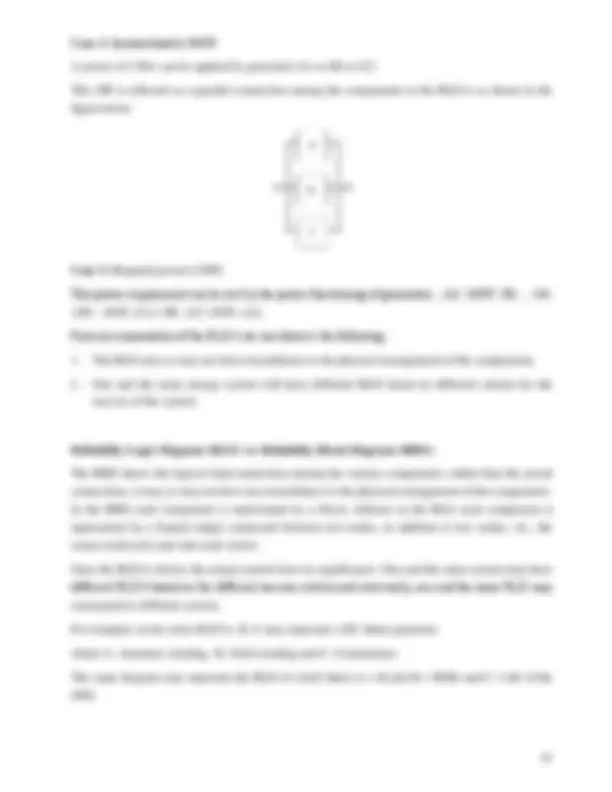
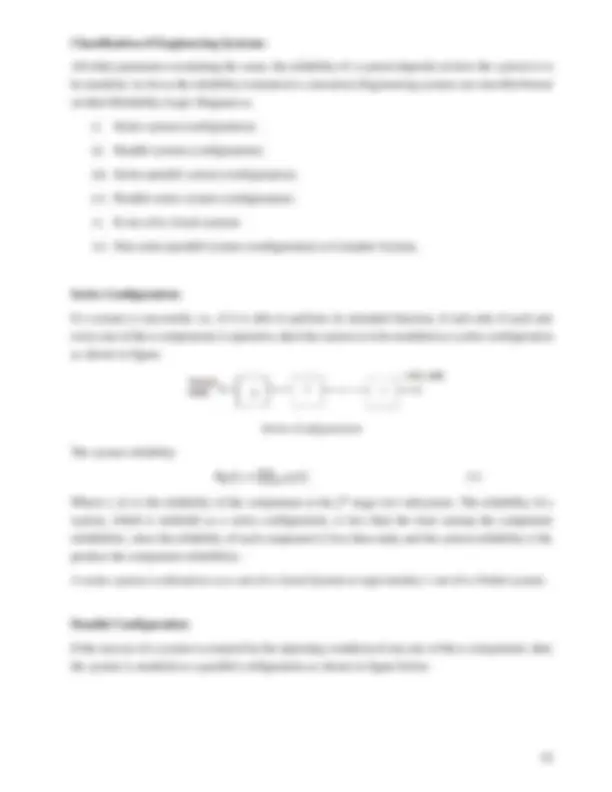
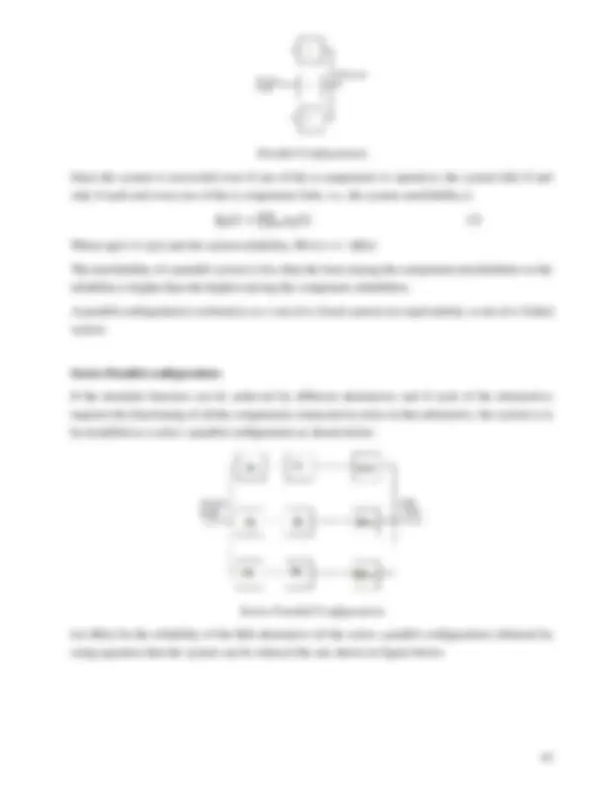
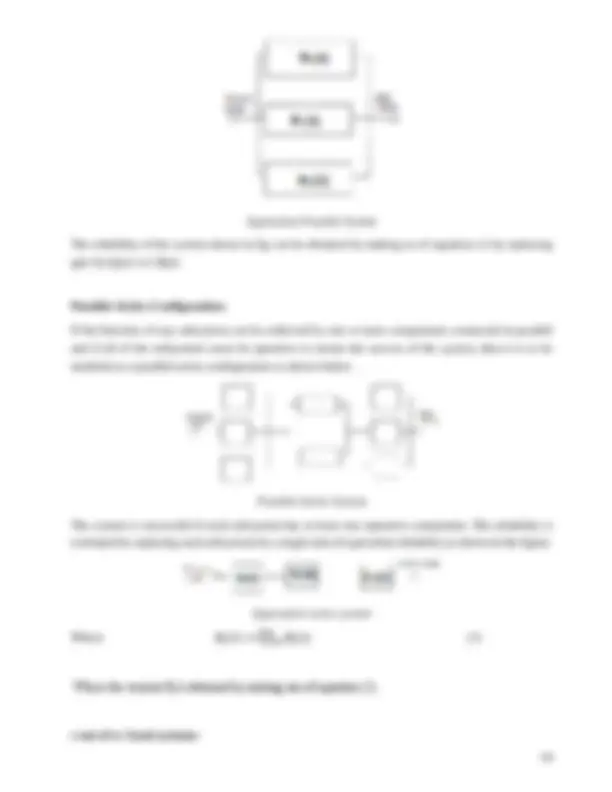
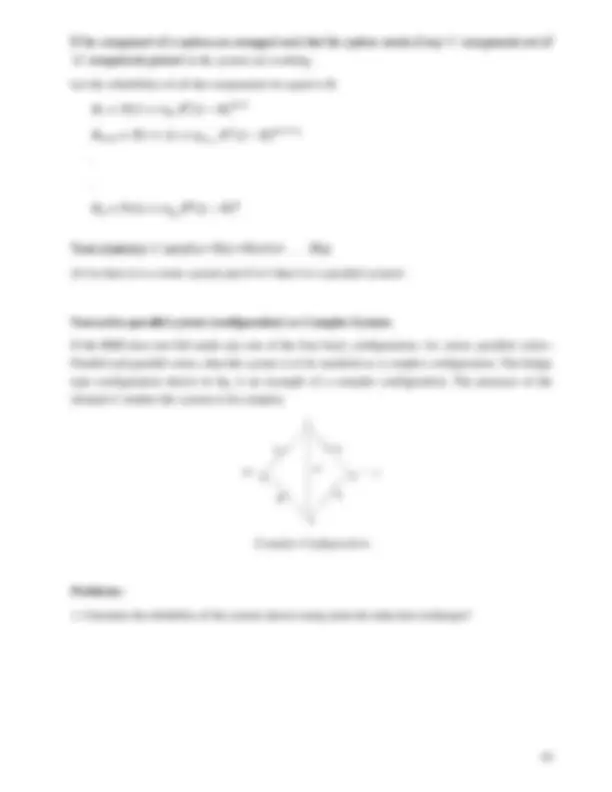
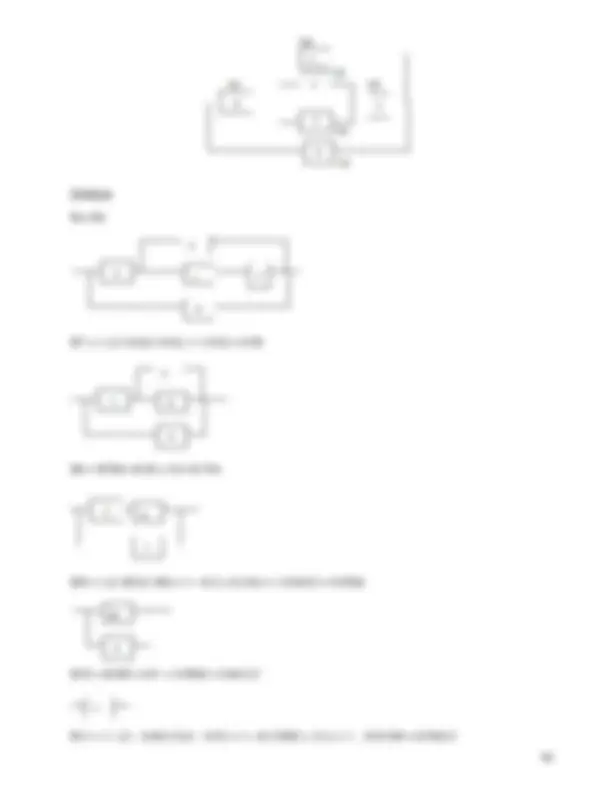
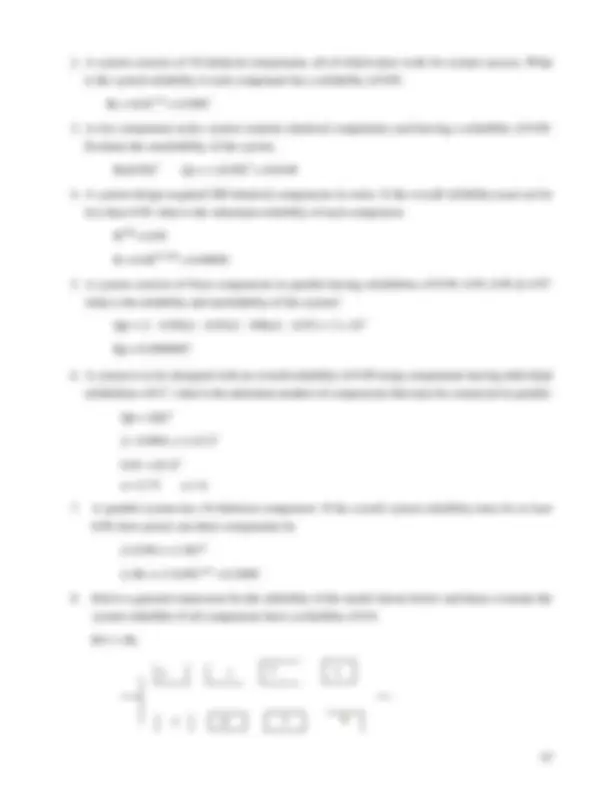
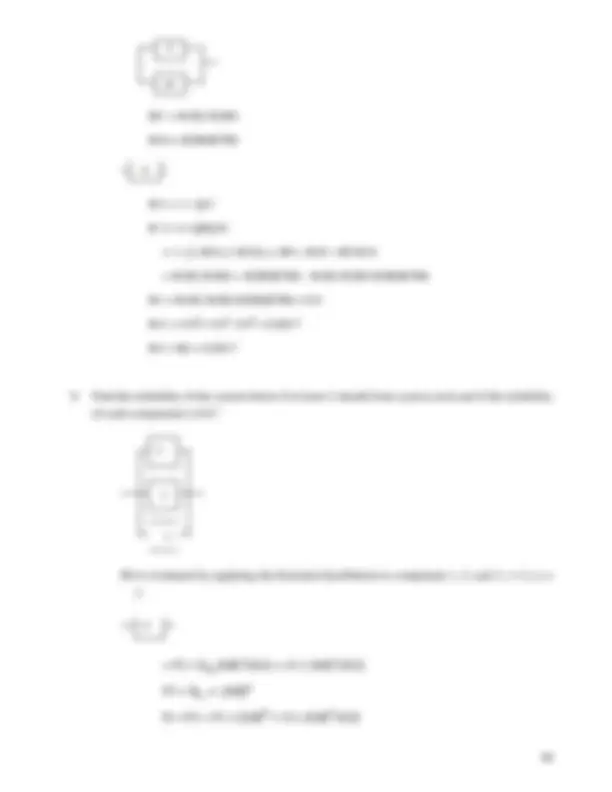
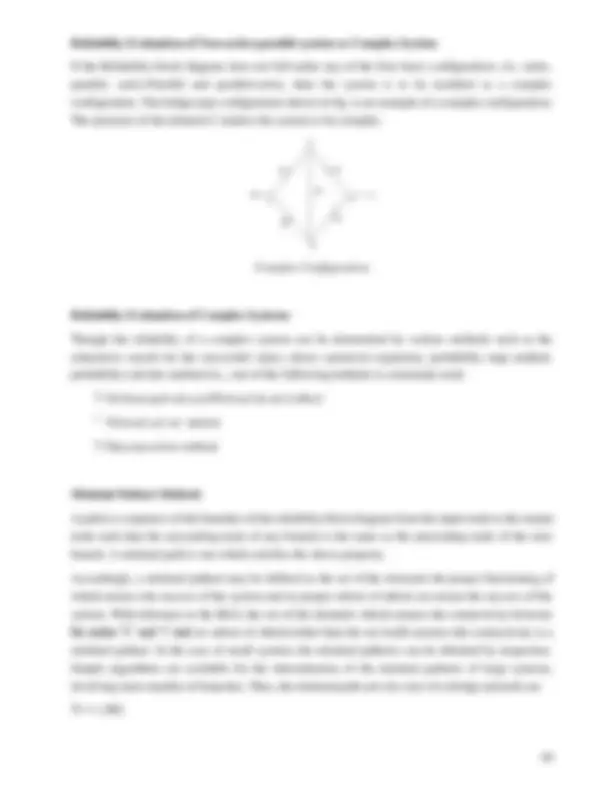
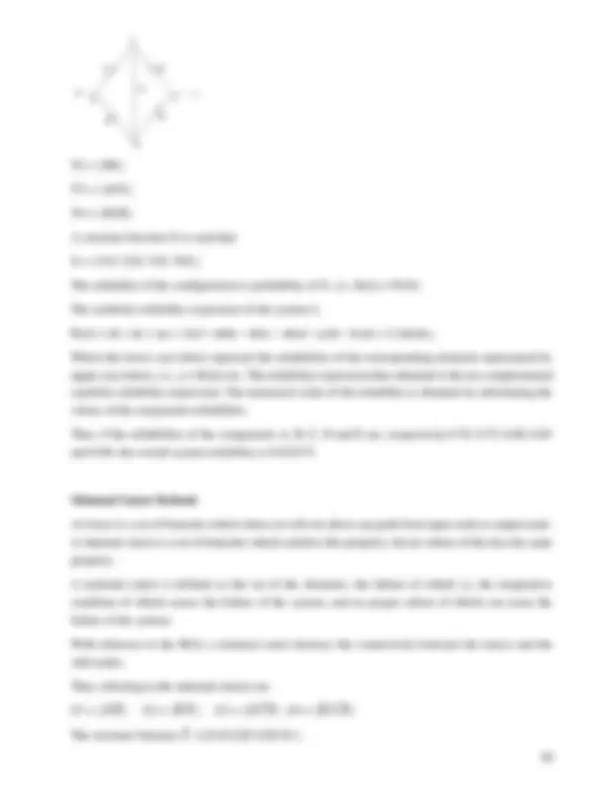
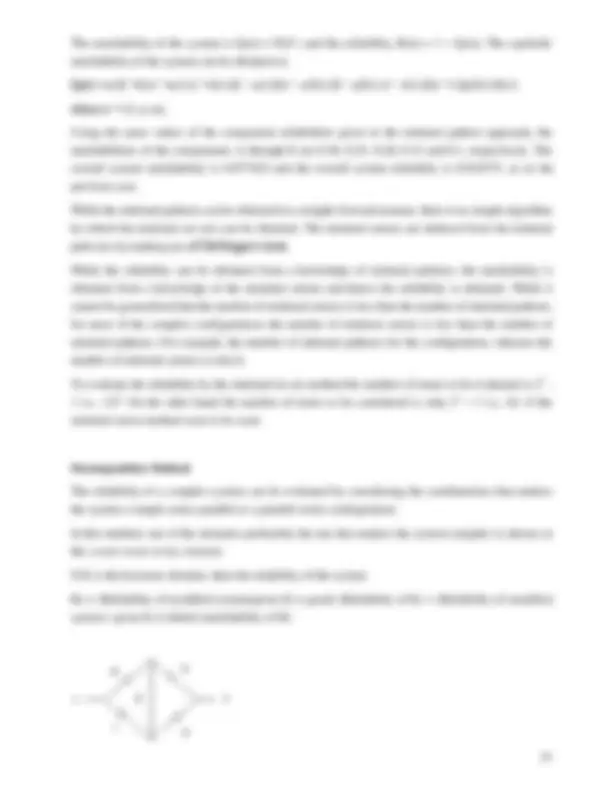

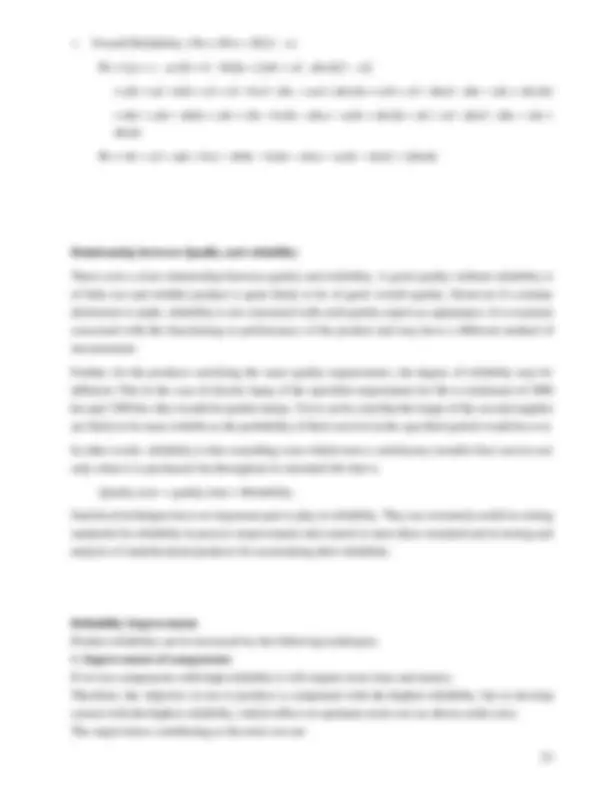
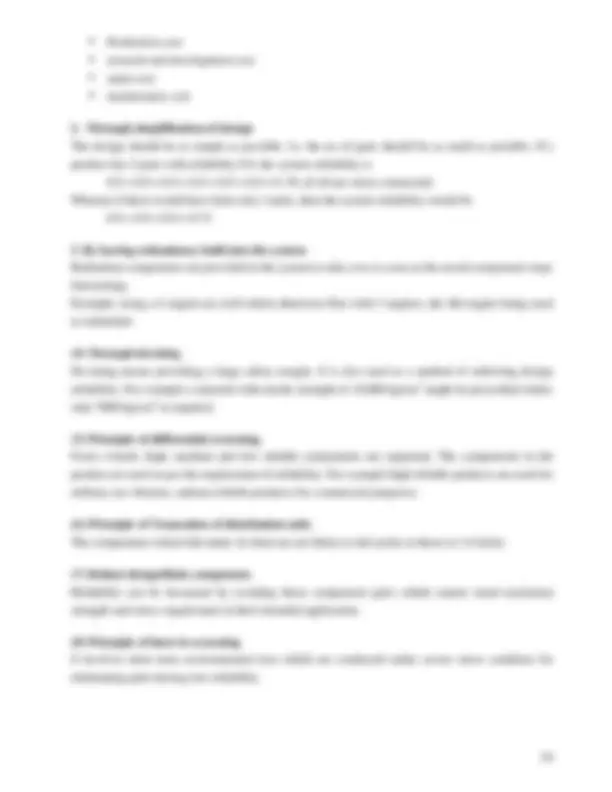
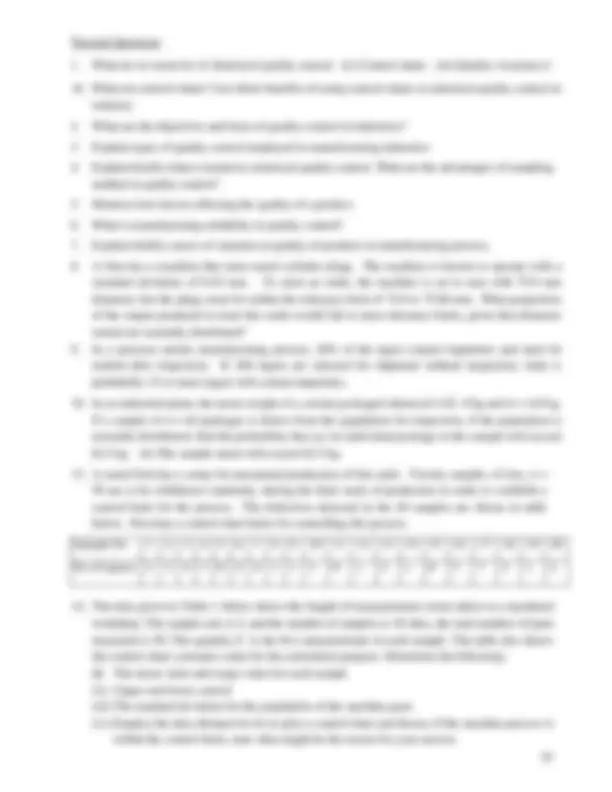
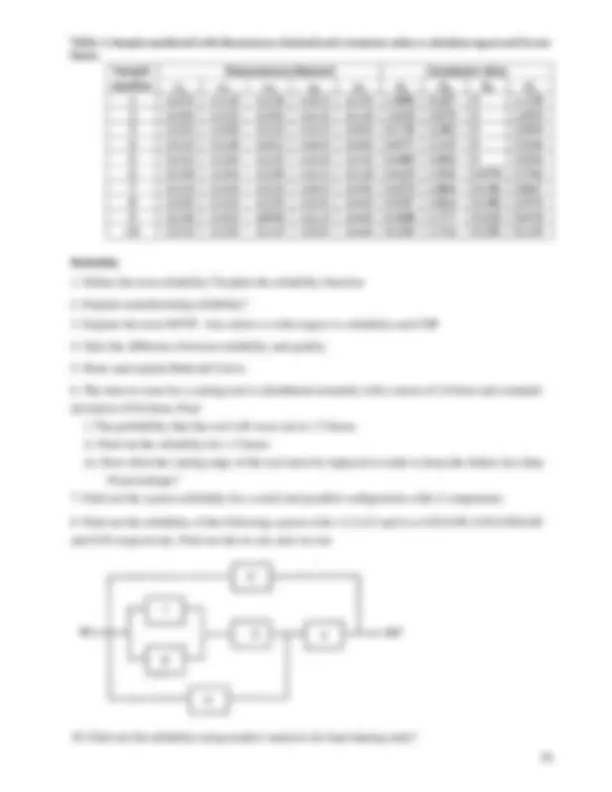
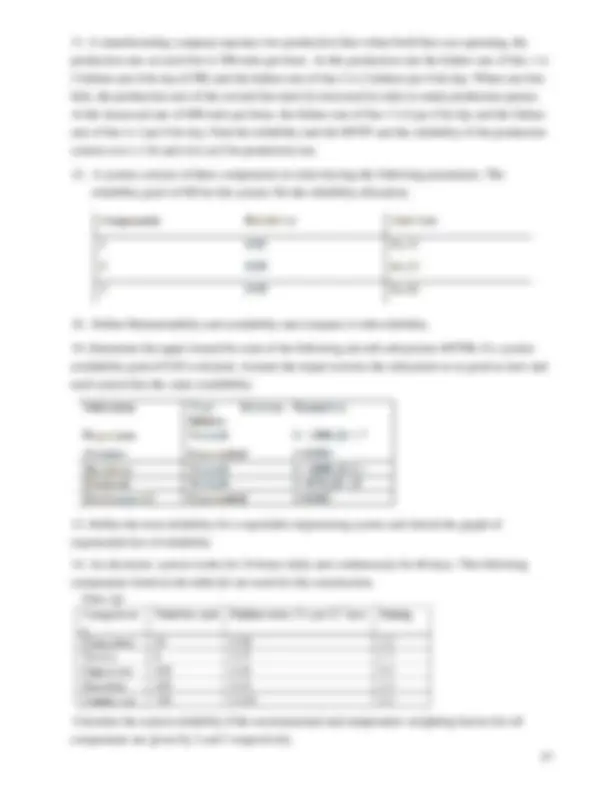
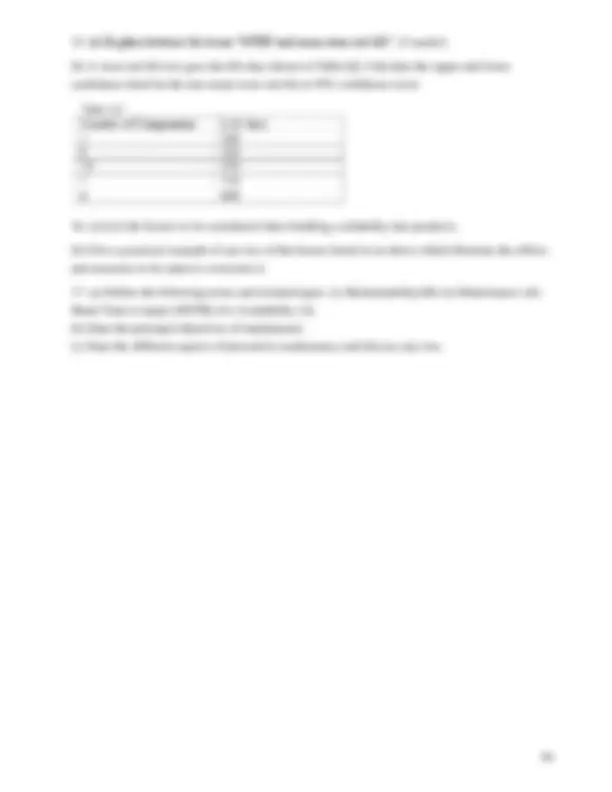
Study with the several resources on Docsity
Earn points by helping other students or get them with a premium plan
Prepare for your exams
Study with the several resources on Docsity
Earn points to download
Earn points by helping other students or get them with a premium plan
Community
Ask the community for help and clear up your study doubts
Discover the best universities in your country according to Docsity users
Free resources
Download our free guides on studying techniques, anxiety management strategies, and thesis advice from Docsity tutors
Modern programmes for assuring quality, productivity and lower cost, statistical engineering techniques for process control and product acceptance are emphasized, recognized methods are also presented for defects reductions, product liability prevention, inspection improvement, traceable calibration and tender/customer relations.
Typology: Lecture notes
1 / 58
This page cannot be seen from the preview
Don't miss anything!
In the manufacturing and services sector, definition of quality incorporate in the following: conforming to requirement and specifications, fitness for use, customer satisfaction, delighting the customer, and enchanting the customers.
i) Performance It refers to the primary operating characteristics of a product. E.g., a product can be judged by its clarity of sound, weight, size, functions, or by speed, pick-up, fuel efficiency, etc. ii) Features : These constitute the second dimension of quality. These refer to additional characteristics available in products along with the primary operating characteristics. iii) Reliability Reliability refers to the probability of a product’s failure within a specified time period. If a product fails frequently, we say that it is an unreliable product. iv) Conformance (Agreement) Conformance means meeting specifications that customers want that the product should meet.
v) Durability Durability refers to the measure of product life. It can also be understood as the operational life of the product, i.e., how long the product can be used without replacement. vi) Serviceability Serviceability is concerned with how readily a product can be serviced back into operational mode. vii) Aesthetics This means how a product looks, sounds, feels, etc. The aesthetic value of a product is purely subjective. viii) Reputation Reputation is related to the past performance of the company.
The nine fundamental factors ( 9 M’s ),
Disadvantages
Advantages
Disadvantages
First piece of the shift or lot is inspected. This is particularly used where automatic machines are employed. Any discrepancy from the operator as machine tool can be checked to see that the product is within in control limits. This yields good result if the operator is careful.
6. Pilot piece inspection This is done immediately after new design or product is developed. This is suitable for mass production and products involving large number of components such as automobiles aeroplanes etc. Modification to design or manufacturing process is done until satisfactory performance is assured or established. 7. Final inspection This is also similar to functional or assembly inspection. This inspection is done only after completion of work. This is widely employed in process industries such as, electroplating or anodizing products. This is done in conjunction with incoming material inspection.
There are two methods of inspection. They are: 100% inspection and sampling inspection. The inspector for
the quality control and reliability department may inspect in any of the following;
(i) Inspect each piece on each operation. This is called ‘100 percent inspection’ and is quite expensive. (ii) Inspect the first piece, and other pieces selected at random. This called Random Inspection. (iii) Check the final part and complete assembly using random or 100 percent inspection. (iv) Inspect the partial assembly or the final assembly only using random or 100 percent inspection. (v) Inspection of a part or complete apparatus taken from the production line to a laboratory or inspection station where critical dimensions and functions are carefully checked.
Following are the disadvantages of inspection:
i. Inspection adds to the cost of the product but not for its value. ii. It is partially subjective, often the inspector has to judge whether a products passes or not. iii. Fatigue and Monotony may affect any inspection judgment. iv. Inspection merely separates good and bad items. It is no way to prevent the production of bad items.
Control Control is the process through which the standards are established and met. This process consists of observing our activity performance, comparing the performance with some standard. The control process involves a universal sequence of steps as follow:
Following are the steps in quality control process: i. Formulate quality policy. ii. Set the standards or specifications on the basis of customer’s preference, cost and profit. iii. Select inspection plan and set up procedure for checking. iv. Detect deviations from set standards of specifications. v. Take corrective actions or necessary changes to achieve standards. vi. Decide on salvage method i.e ., to decide how the defective parts are disposed of, entire scrap or rework. vii. Coordination of quality problems. viii. Developing quality consciousness both within and outside the organization. ix. Developing procedures for good vendor-vendee relations.
The broad areas of application of quality control are incoming material control, process control and product control.
Statistical Quality Control (SQC) Statistical quality control is defined as the technique of applying statistical methods based on the theory of probability and sampling to establish quality standard and to maintain it in the most economical manner.
The following are the main elements of SQC: Sample Inspection Use of Statistical Methods Fundamental Objective Decision Making Specifications, Production and Inspection
The important techniques used for statistical quality control can be broadly classified into two categories:
Product Control. Statistical Process Control (SPC) or simply Process Control.
Product control means to control the products in such a way that these are free from defects and conform to
their specifications.
This involves the control the quality of components both manufacture or purchase, and also control the quality
of the final product.
A process is a series of operations or actions that transforms input to output. It is said to be stable or repeatable if the resulting output product is of the given specifications or standard quality. However, the process may not be stable due to poor quality of raw material, change in the machine settings, use of unskilled work force, improper machine, etc. The process needs to be control through tool or technique and this technique is known as statistical process control (SPC).
Statistical process control is a technique used for understanding and monitoring the process by collecting data on quality characteristics periodically from the process, analysing them and taking suitable actions whenever there is a difference between actual quality and the specifications or standard.
Tools for Statistical Process Control
Pareto charts Pareto charts help prioritize by arranging them in decreasing order of importance. In an environment of limited resources, these diagrams help companies decide on the order in which they should address problems. The Pareto analysis can be used to identify the problem in several forms: ( a ) Analysis of losses by material (number or part number). ( b ) Analysis of losses by process i.e. , classification of defects or lot rejections in terms of the process. ( c ) Analysis of losses by product family. ( d ) Analysis by supplier across the entire spectrum of purchases. ( e ) Analysis by cost of the parts. Pareto chart for poor quality ( f ) Analysis by failure mode.
Check sheets A check sheet is a form used systematically to record the frequency of occurrence of certain product or service characteristics related to quality as they happen which reveals patterns or trends. The characteristics may be measurable on a continuous scale such as weight, diameter, time, or length.
Check list
Flow charts (or) graphs It shows the sequence of events in a process. They are used for manufacturing and service operations. Flow charts are often used to diagram operational procedures to simplify the system. They can identify bottlenecks, redundant steps and non-value added activities. Flowchart
Control Charts
Centre Line (CL) – The centre line of a control chart represents the value which can have three different interpretations depending on the available data:
(i) it can be an average value of the quality characteristic or the average of the plotted points. (ii) it can be a standard or reference value, based on representative prior data or an aimed (targeted) value based on specifications. (iii) it can be the population parameter if that value is known. The centre line is usually represented by a solid line.
Upper Control Line – The upper control line represents the upper value of the variation in the quality characteristic. So this line is called upper control limit (UCL). Usually, the UCL is shown by a dotted line.
Lower Control Line – The lower control line represents the lower value of the variation in the quality characteristic. So this line is called lower control limit (LCL). Usually, the LCL is shown by a dotted line.
The UCL and LCL also have three interpretations depending on the available data same as the centre line. These limits are obtained using the concept of 3σ (three sigma – standard deviation) limits.
The two limits are constructed so that if the process is operating under a stable system of chance causes, the problem of an observation falling outside these limits is quite small. Control chart shows the performance of a process from two points of view: (i) they show a snapshot of the process at the moment the data are collected. (ii) they show the process trend as time progresses.
If the sample points fall between the control lines, the process is said to be under statistical control. But, if one or more points lie outside the control limits, control chart alarms (indicates) that the process is not under statistical control. Some assignable causes are present in the process. To bring the process under statistical control, it is necessary to investigate the assignable causes and take corrective action to eliminate them and then continue the production process.
The figure illustrates a control chart for monitoring the diameter of plastic cups produced on moulding machines. The chart has a mean value (target value) at 12.00 cm, an upper control limit at UCL = 12.10 cm and a lower control limit at LCL = 11. cm. Each plotted point represents the average diameter of a sample of several disks.
Benefits of using control charts
Objectives of control charts
There are two types of control charts: (i) Variable control chart : It is one by which it is possible to measures the quality characteristics of a product. (ii) Attribute control chart : Attribute control chart: It is one in which it is not possible to measures the quality characteristics of a product, i.e., it is based on visual inspection only like good or bad, success or failure, accepted or rejected.
Upper control limit (UCL)
Lower control limit (LCL)
Control Chart
Sample number
Diameter
(^1 2 3 4 5 6 7 8 9 )
Procedures to construct X-chart and R-chart
P-charts and C-charts are charts used for attributes. This chart shows the quality characteristics rather than measurements.
P -chart A p -chart is a commonly used control chart for attributes, whereby the quality characteristic is counted, rather than measured, and the entire item or service can be declared good or defective. The standard deviation of the proportion defective, p , is:
Using the normal approximation to the binomial distribution, which is the actual distribution of p ,
where Z is the normal deviation (number of standard deviations from the average).
A control chart having a natural pattern of variation has the following three characteristics: i. Most points lie near the centre line of the chart. ii. Very few points lie near the control limits. iii. None of the points fall outside the control limits.
In a typical control chart with 3σ limits, 99.73% observations lie between the 3σ limits while only 0.27 observations may lie outside the 3σ limits
1. Extreme Variation If one or more sample points are significantly different from the other points and lie outside the control limits of the control chart then there is an extreme variation in the chart. Some assignable causes are present in the process and corrective action is necessary to bring the process under control. Causes of extreme variation are: i. Error in measurement, recording and calculations, ii. Wrong setting and defective machine tools or erroneous use, iii. Power failures for short time, iv. Use of a new tool, failure of the component at the time of test, etc. 2. Trend If consecutive points on the control chart tend to move upward or downward as shown in the figure, it can be assumed that the process indicates a trend. If proper care or corrective action is not taken, the process may go out of control.
Causes of trend pattern are: i. Tool or die wear, ii. Gradual change in temperature or humidity, iii. Gradual wearing of operating machine parts, iv. Gradual deterioration of equipment, etc.
3. Cycles When consecutive points exhibit a cyclic pattern, it is also an indication that assignable causes are present in the process which affect it periodically.
Causes of cyclic pattern are: i. Rotation of operators, ii. Periodic changes in temperature and humidity, iii. Periodicity in the mechanical or chemical properties of the material, iv. Seasonal variation of incoming component, etc.
4. Shifts When a series of consecutive points falls above or below the centre line of the chart, it can be assumed that a shift in the process has taken place. This indicates the presence of some assignable causes.
Acceptance sampling Acceptance sampling is a technique in which a small part or fraction of items/units is selected randomly from a lot and the selected items/units are inspected to decide whether the lot should be accepted or rejected on the basis of the information obtained from sample inspection.
Hypergeometric Distribution: The distribution depends on the size of the population, the number of draws without replacement, and the number of "successes" in the population.
If N = size of the population, with k elements of the population belonging to one group (e.g. successes) and N − k belonging to the other group (failures). Further, let the number of samples drawn from the population be n , such that 0 ≤ n ≤ N.
Then the probability ( P ) that the number ( X ) of elements drawn from the successful group is equal to some number ( x ) is given by:
Binomial Distribution:
We say the X has a Binomial Distribution with number of trials n and success probability p. Written in notation as 𝑋 ~ 𝐵(𝑛, 𝑝)
The probability mass function of X is given by
𝑓(𝑥) = {(
0, otherwise where
(𝑛𝑥) = (^) 𝑥!(𝑛−𝑥)!𝑛! , and x! = x × (x - 1) × … × 2 × 1 (note 0! = 1)
In general, if probability that an item is defective be p. Let the probability that an item is good be q , such that q = 1 – p (NB: p and q can be interchanged, and “success” and “failure” can be used instead) the probability of exactly r defective items (or successes, heads, etc.) in any order in n trials must be pr q ( n – r ) multiplied by (^) nCr ,
i.e. Pr[𝑅 = 𝑟] = (^) n Cr pr^ q(n-r) The lefthand side of this equation should be read as the probability that exactly r items are defective (or successes, heads, etc.).
NB: (^) n Cr = (^) n C(n-r)
The requirements for using the binomial distribution are as follows:
P(x) = pxqn-x
Poison Distribution:
This is a discrete distribution that is used in two situations. It is used, when certain conditions are met, as a probability distribution in its own right, and it is also used as a convenient approximation to the binomial distribution in some circumstances. The Poisson distribution is commonly used to model counts in an interval of time, an area, a volume or other unit, such as